Simu DMI5 Hz User manual

DMI5Hz - DMI6Hz
Tubular operators with integrated radio and manual
override for blinds, awnings & roller shutters.
USA
S.A.S. au capital de 5 000 000 !- Z.I. Les Giranaux - BP71 - 70103 Arc-Les-Gray CEDEX - RCS GRAY B 425 650 090 - SIRET 425 650 090 00011 - n° T.V.A CEE FR 87 425 650 090
5047058D
IMPORTANT - Review instruction
throughly before installing Hz motors
1/8
A4 x ØB / 90°
ØB
D
C
AØ min.
T min.
Ø 3/16
STEEL SAE5 or higher
Ø 1/4
For Compos
i
te Dr
i
ve
For the Aluminum
Drive use the 5mm X
6mm screws supplied
with the drive
4 X
or
4 X
ASSEMBLY
1
- This device complies with part 15 of the FCC Rules. Operating is subject to the following
two conditions:
(1) This device may not cause harmful interference.
(2) This device must accept any interference received, including interference that may
cause undesired operation.
- Caution: Changes or modications not expressly approved by the party responsible for
compliance could void the user’s authority to operate the equipment.
1.1 - TUBE PREPARATION
Warning: do not cut or drill the tube with the motor installed.
- Cut the tube to the required length.
- Remove all burrs from the tube.
- If using a round tube, cut a notch (D wide by C long) into one end of the tube.
- On round tubes measure length (A) and drill 4 holes around the tube. For octagonal
tubes 1 hole is sufcient (see dimension chart next page).
12 max. d2 > 8 inches min.
1 ft. < d1 < 65 ft.
d1 d2
WARNING

1 2
4 3
Nm ≥ 60 & ALUMINIUM DRIVE
DMI5 : 9910004
DMI6 : 9910062
For the aluminum drive Ais 20mm less than shown
-
-
26 4.2
-
8
-
36
mm
BC D
5
5
75625-18 30-12 35-18 50-12
83660-14 80-14 100-14
A
71615-18
DMI5 Hz
120V / 60Hz
Ø / T min. = 47
DMI6 Hz
120V / 60Hz
Ø / T min. = 60
1.2 - INSTALLING THE TUBULAR MOTOR
1- Fit the adaptor over the crown. Align the slot in the adaptor with the raised key and rmly t the
adaptor over the crown. A crown adaptor is not necessary with 47mm (2") tubes.
2- Snap the drive wheel onto the drive shaft. Screw on the drive stop if needed (60 Nm+ operators).
3- Slide the tubular motor into the tube. Do not force or hammer on the head of the motor. If the
motor does not insert smoothly, remove the motor and le smooth the edge of the tube. On round
tubes conrm the raised key on the crown ts snugly into the cut slot on the end of the tube.
4- Secure the drive wheel to the tube. For the composite drive, use four 3/16" dia. steel pop rivets
or four 1/4" dia. screws with steel grade SAE 5 or higher. For the aluminum drive, use the three
5mm X 6mm cheese head screws provided.
1.3 - MOUNTING THE TUBULAR MOTOR
The DMI5Hz / DMI6Hz motor use standard T5 / T6 accessories.
- Mount the motor as shown using only SIMU accessories.
- Mount the motor heads at least 8" apart from each other to prevent RF interference.
- Always install the power cable with a drip loop to prevent water penetration.
- SIMU motors conform to IP44 requirements and as such must be protected against
direct weather elements such as rain, sleet, ...etc. Failure to do so could result in voiding
the warranty.
2/8
85 Nm max.

MOTOR
CABLE
POWER
120VAC
BLACK
WHITE
GREEN
HOT
NEUTRAL
GROUND
OPERATOR
WIRING CHART
3/8
1
2
10 Nm max.
(DMI 6 120 : 20Nm max.)
WIRING
2
2.1 - DMI Hz PERMANENT WIRING (shutter, shade or awning)
Warning: All wiring must conform to the National Electric Code and local codes.
- (1) The motor must be installed with a drip loop to prevent water intrusion.
- (2) Connect the motor to power using a listed junction box with appropriate cable strain reliefs.
- It is recomended a method of power disconnect for each motor be placed within sight of the motor to
cut power during servicing and facilitate reprogramming.
- Do not use the motor cable to penetrate building walls. Connect the motor to power in a listed junction
box and from the listed junction box run power in the manner proscribed by NEC. and local codes.

MOTOR
CABLE
POWER
120VAC
BLACK
WHITE
GREEN
HOT
NEUTRAL
GROUND
OPERATOR
WIRING CHART
Hand Held Transmitters Color Multi & Timer MultiWall switch Transmitter
Decoflex wall switch transmitterHz Timer
single channelfive channels
PROGRAM BUTTON
PROGRAM BUTTON
(back of transmitter)
PROGRAM BUTTON
(back of transmitter)
PROGRAM BUTTON
2.2 - DMI Hz PLUG-IN WIRING (shade or awning)
Warning: All wiring must conform to the National Electric Code and local codes.
- (1) The motor must be installed with a drip loop to prevent water intrusion.
- (2) If used outdoors, a GFCI receptacle with an outdoor cover is required.
- Do not use the motor cable to penetrate building walls.
The molded-on attachment plug can be removed when permanent installation is
required by National or Local Codes.
- Cut the exible cord at 10 mm from the start of the molded-on plug.
- Strip the cord jacket to required length in order to connect the motor to the Mains power
supply in a listed junction box according to National Electric Code and local codes.
- Strip the insulated insulation of the conductors and use the appropriate listed eld-wiring
wire nuts as per local and National codes in order to make the permanent wiring of the
operator.
COMPATIBLE TRANSMITTERS
3
4/8

>>>
ON
ON
>>>
>>>
>>> >>>
GO TO 4.3
OR
3+ sec.
4.1 - WAKING UP THE MOTOR
Before programming, changing direction of rotation, setting the limits, etc…you
must wake the motor up. If using a multi-channel transmitter, conrm you are on
the desired channel. Press and hold the up and down together until the motor
gives a short up/down bounce. The motor is now awake.
4.3 - PROGRAMMING A TRANSMITTER CHANNEL TO A MOTOR
If using a multi-channel transmitter, conrm you are on the desired channel.
Press the Program Button and the motor will give a short up/down bounce.
Conrm the transmitter now controls the motor. A short push on the up of down
button should make the motor run until you stop it or the motor stop at its limits.
You should not have to hold the button down.
4.2 - DIRECTION OF ROTATION
You must check the direction of rotation before programming. If the direction
of rotation is not correct, press and hold the stop Button until the motor gives a
short up/down bounce. Conrm the direction of rotation is now correct.
PROGRAMMING
4
5/8

>>> >>> >>>
>>> >>> >>>
OFF
8s
OFF
8s
8s
ON ON
5s.
>>>
4.4 - ADDING ADDITIONAL TRANSMITTERS (CHANNELS) TO THE MOTOR.
Use the transmitter that currently controls the motor and conrm it is on the correct channel.
Press and hold the Program Button until the motor gives a short up/down bounce. Conrm
transmitter is on the channel you wish to add and press the Program Button. The motor will
give a short up/down bounce. The new channel is now added. Repeat for any additionnal
transmitter channels you wish to add.
4.5 - DELETING A TRANSMITTER CHANNEL TO A MOTOR.
Use a transmitter that currently controls the motor and conrm it is on the correct channel
to control the motor. Press and hold the Program Button until the motor gives a short up/
down bounce. Press the Program Button of the second transmitter until the motor gives a
short up/down bounce. The second transmitter is now deleted.
4.6 - CLEARING THE MEMORY OF OLD TRANSMITTERS AND ADDING NEW TRANSMITTERS.
If all a motor transmitters are lost or damaged it is possible to clear the old memorized codes from
memory and add the new transmitter. Perform a double power cut in the following sequence:
1- Power off for at least 8 seconds
2- Power on for 8 seconds
3- Power off for at least 8 seconds
4- Power on. The motor will try and run for 5 seconds but will not run past its limits.
The motor is now in a temporary mode for 2 minutes. NOTE: this is not the "factory mode".
If a motor or motors are entered into temporary programing mode by mistake it can be cancelled
by pressing for a second on the UP, STOP or DOWN of any transmitter that motor has memorized.
The motor will also return to normal operating mode if left for 2 minutes.
5- Press and hold the Program Button of any unmemorized transmitter for more than 8 seconds.
When the motor gives a short up/down bounce release the button. The memory of the motor’s
receiver is now cleared of the old transmitters and the new transmitter has been added.
6/8

LIMIT ADJUSTMENT SCREWS ON OPPOSITE SIDE FROM MOTOR CABLE
5.1 - Identify which limit adjustment screw controls the up limit and which controls the
down limit (see above diagrams). It is important to note that the arrows by the
limits adjustments screws refer to the tube’s rotation. Thus if the material comes
off the tube on the back side and you are adjusting the limits from the side that the
motor cable is not on (as per diagram 2), the limit adjustment screw with the arrow
facing up controls the down limit and vice-versa.
5.2 - Turning an adjustment screw positive (+) will increase the maximum travel in the
direction that it controls and turning it negative (-) will decrease the maximum tra-
vel. For the adjustment screws on the side without the motor cable, turning counter
clockwise is positive (+) and clockwise is negative (-).
5.3 - To set a limit, run the motor in the selected direction.
5.4 - If the motor stops on its own before reaching the desired stop, turn the appropriate
limit screw positive (+). Every 2 or 3 turns of the limit adjustment screw will allow
the motor to travel about 1 inch further. After every few turns of the limit adjustment
screw use the control switch to move the motor to the new limit position. If the mo-
tor does not stop on its own before reaching the desired stop, go to step 5.6.
5.5 - When you are approximately at the desired stop, use the control switch to run the
motor away from the limit 2 or 3 feet and then back. This will allow you to see pre-
cisely where the limit is set. Make small adjustments and repeat.
5.6 - If the motor does not stop on its own at least 6 inches before the desired limit posi-
tion, stop the motor with the control switch. Then turn the adjustment screw in the
negative (-) direction. Conrm that the motor is stopped at the limit and set the limit
as in step 5.4 and 5.5. If the motor is not stopped at the limit, continue turning the
limit adjustment screw (up to 120 turns may be required).
NOTE: The motor has a built-in thermal cut-off. If after several minutes of use the motor
will not run in either direction allow the motor to cool approximately 20 minutes.
7/8
SETTING THE LIMITS
5
DOWN LIMIT ADJUSTMENT SCREW
MATERIAL ROLLS DOWN ON SAME SIDE AS LIMITS
UP ADJUSTMENT SCREW
1
MATERIAL ROLLS DOWN ON OPPOSITE SIDE AS LIMITS
2
UP LIMIT ADJUSTMENT SCREWDOWN LIMIT ADJUSTMENT SCREW

LIMIT ADJUSTMENT SCREWS ON SAME SIDE FROM MOTOR CABLE
6.1 - Identify which limit adjustment screw controls the up limit and which controls the
down limit (see above diagrams). It is important to note that the arrows by the
limits adjustments screws refer to the tube’s rotation. Thus if the material comes
off the tube on the back side and you are adjusting the limits from the side that the
motor cable is not on (as per diagram 4), the limit adjustment screw with the arrow
facing up controls the down limit and vice-versa.
6.2 - Turning an adjustment screw positive (+) will increase the maximum travel in the
direction that it controls and turning it negative (-) will decrease the maximum
travel. For the adjustment screws on the side with motor cable, turning counter
clockwise is negative (-) and clockwise is positive (+).
6.3 - To set a limit, run the motor in the selected direction.
6.4 - If the motor stops on its own before reaching the desired stop, turn the appropriate
limit screw positive (+). Every 2 or 3 turns of the limit adjustment screw will allow
the motor to travel about 1 inch further. After every few turns of the limit adjustment
screw use the control switch to move the motor to the new limit position. If the mo-
tor does not stop on its own before reaching the desired stop, go to step 6.6.
6.5 - When you are approximately at the desired stop, use the control switch to run the
motor away from the limit 2 or 3 feet and then back. This will allow you to see pre-
cisely where the limit is set. Make small adjustments and repeat.
6.6 - If the motor does not stop on its own at least 6 inches before the desired limit posi-
tion, stop the motor with the control switch. Then turn the adjustment screw in the
negative (-) direction. Conrm that the motor is stopped at the limit and set the limit
as in step 6.4 and 6.5. If the motor is not stopped at the limit, continue turning the
limit adjustment screw (up to 120 turns may be required).
NOTE: The motor has a built-in thermal cut-off. If after several minutes of use the motor
will not run in either direction allow the motor to cool approximately 20 minutes.
8/8
SETTING THE LIMITS
6
UP LIMIT ADJUSTMENT SCREW
MATERIAL ROLLS DOWN ON SAME SIDE AS LIMITS
DOWN LIMIT ADJUSTMENT SCREW
MATERIAL ROLLS DOWN ON OPPOSITE SIDE AS LIMITS
34
DOWN LIMIT ADJUSTMENT SCREWUP LIMIT ADJUSTMENT SCREW
MOTOR CABLE MOTOR CABLE MOTOR CABLEMOTOR CABLE
Other manuals for DMI5 Hz
3
This manual suits for next models
1
Table of contents
Other Simu Control Unit manuals
Popular Control Unit manuals by other brands
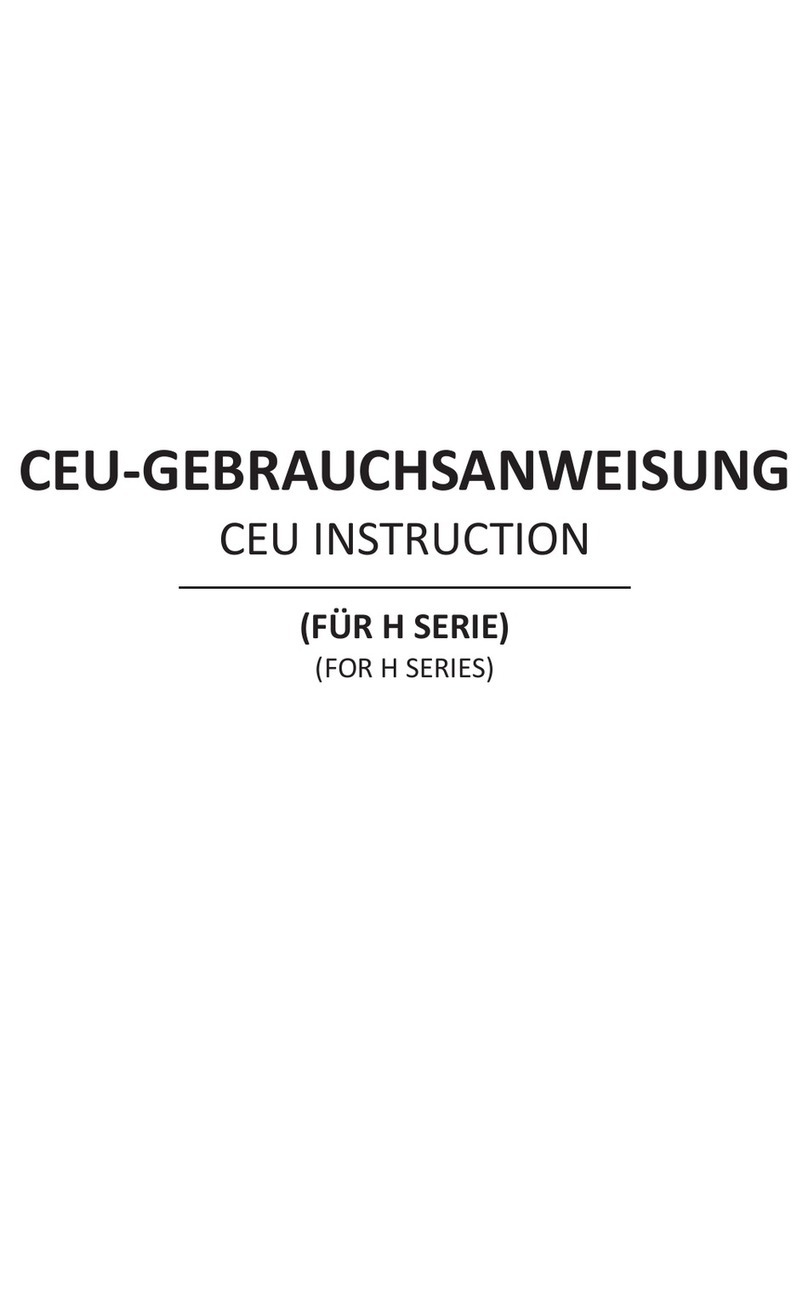
GO Europe
GO Europe H Series instruction manual
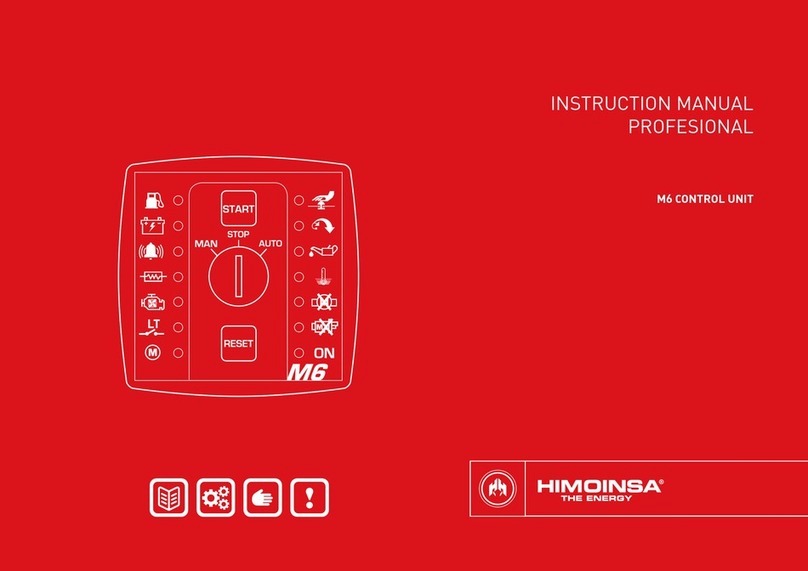
Himoinsa
Himoinsa M6 instruction manual
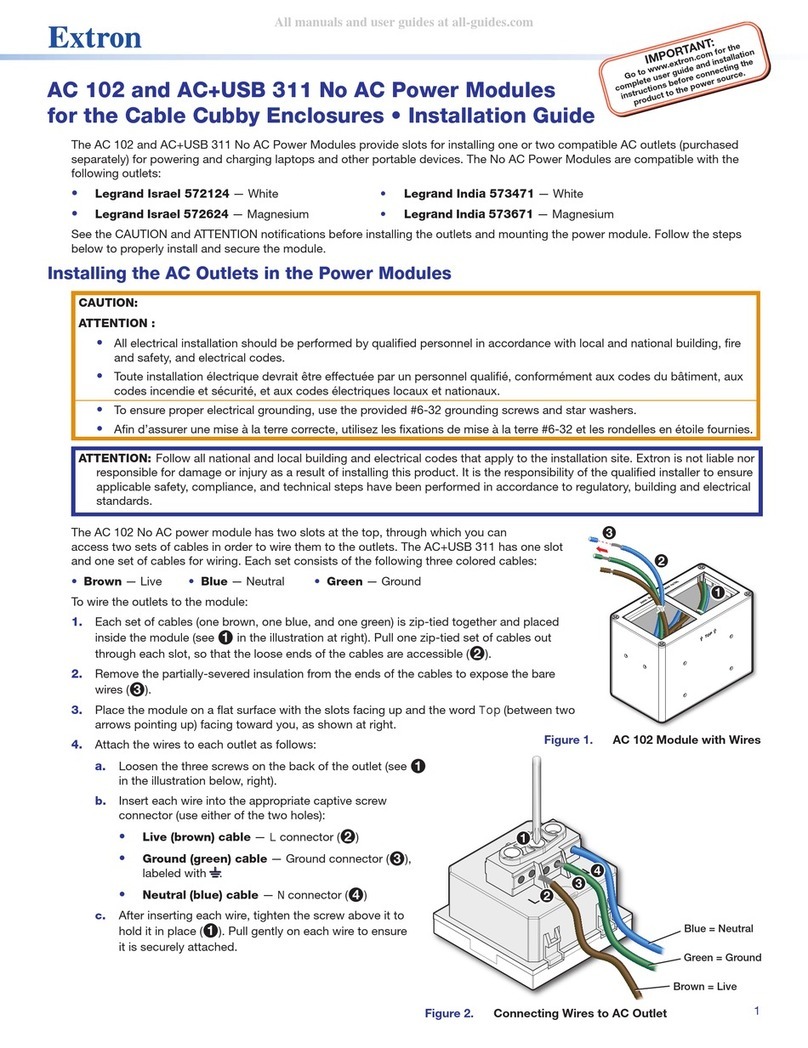
Extron electronics
Extron electronics AC+USB 311 installation guide
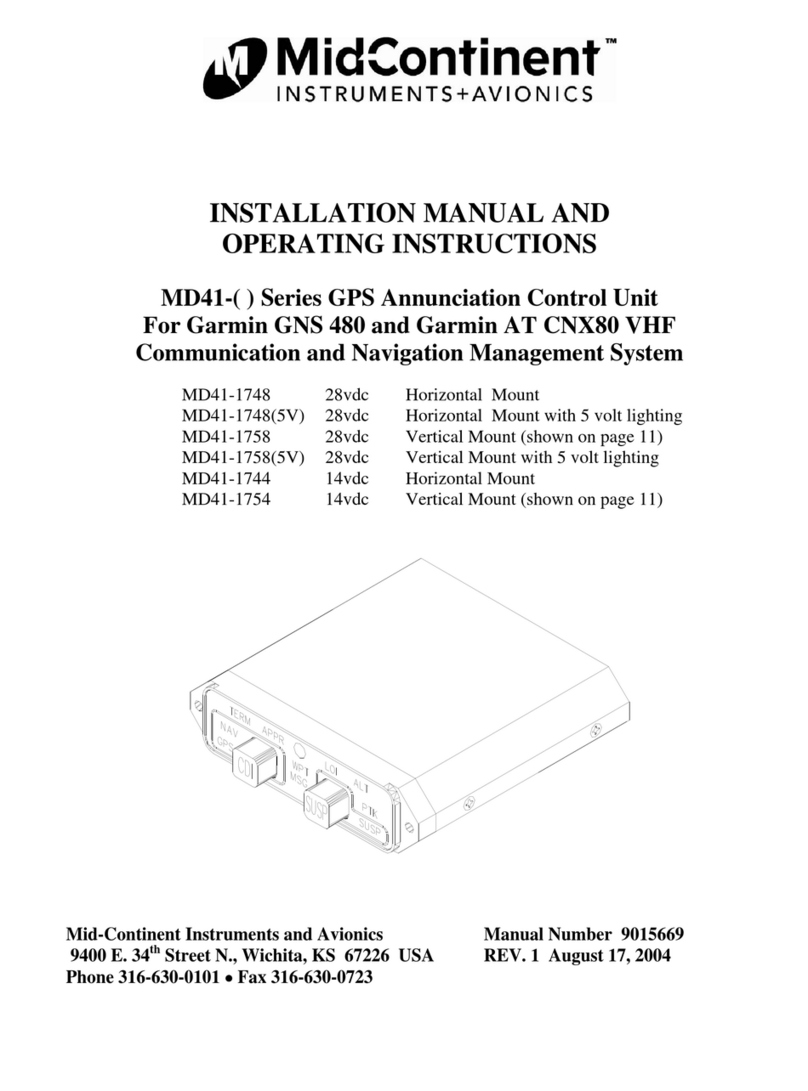
Midcontinent
Midcontinent MD41 Series Installation manual and operating instructions
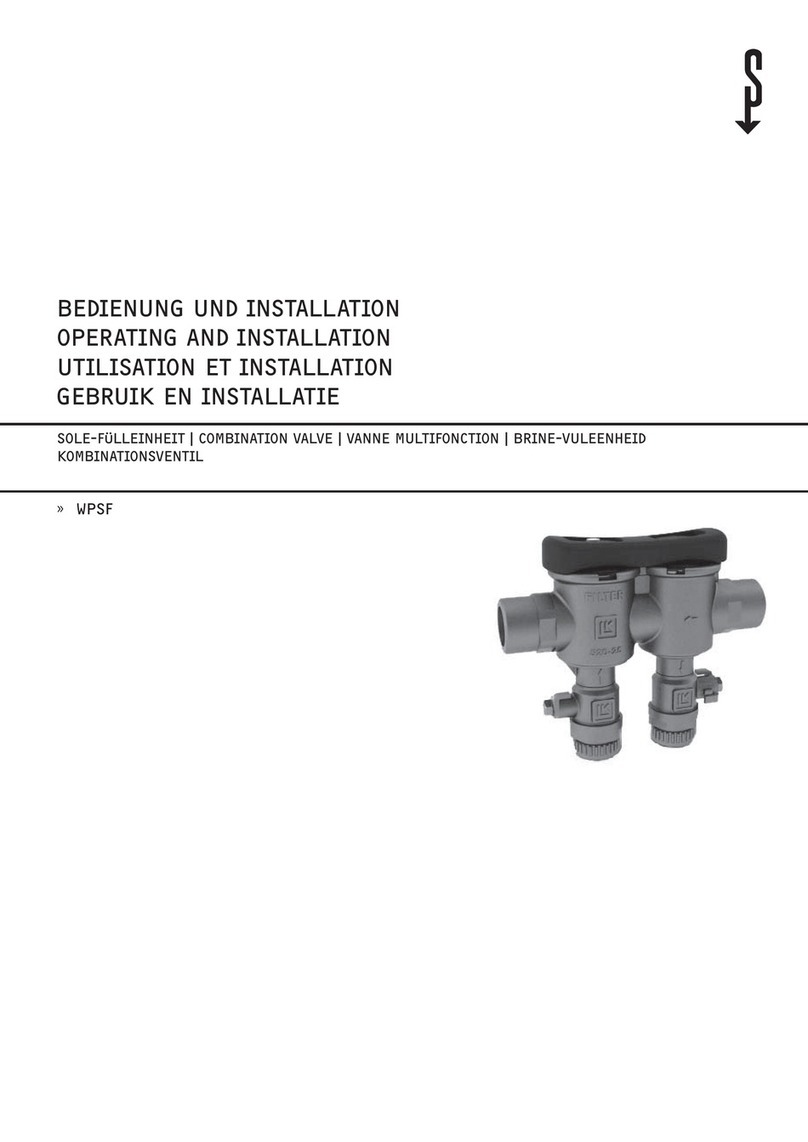
STIEBEL ELTRON
STIEBEL ELTRON WPSF Operating and installation instructions
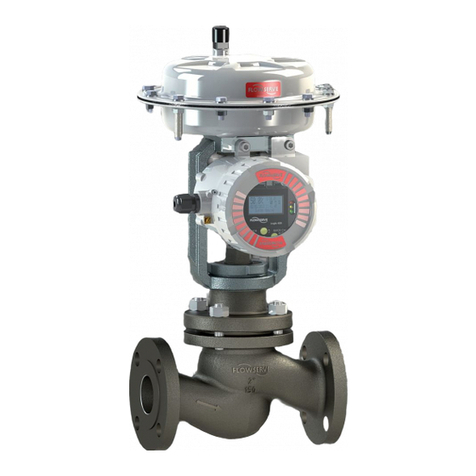
Flowserve
Flowserve Valtek GS User instructions