Himoinsa M6 User manual

INSTRUCTION MANUAL
PROFESIONAL
M6 CONTROL UNIT

| PAG. 2
INDEX
3 1. Introduction
4 2. Front of the control unit
7 3. Connections
10 4. Operation
13 5. Dimensions, wiring and mechanical parts
17 6. Table of parameters

INTRODUCTION | PAG. 3
1. INTRODUCTION
The M6 control unit is an electronic monitoring, control and protection controller
for generator sets.
The general characteristics are as described below:
1. Supply voltage 8/36V.
2. Start and mode selection key.
•“AUTO” mode. Start activated through an external start input via volt
free contact ( LT)
•“MAN” mode. Start activated by the user.
3. 14 LEDs for visual indication of the status of the control unit.
4. 2 control unit command buttons:
•Push button to “start” / “stop” the generator set.
•“RESET” button to reset the control unit when an alarm is detected.
5. Start by voltage free contact ( LT ) in “AUTO mode”.
6. Motor protection features:
•Fuel reserve.
•Battery charging failure.
•High motor coolant temperature.
•Low oil pressure.
•Auxiliary motor alarm.
•Overspeed eding:
•Due to electrical signal frequency of generator.
•Due to motor pick up.
7. Shortcircuit and temperature selfprotected transistor outputs:
•3 power outputs (40A).
•4 signal outputs (1A).
8. USB port.

FRONT OF THE CONTROL UNIT| PAG. 4
2. FRONT OF THE CONTROL UNIT
On the front of the M6 control unit you can nd:
•2 buttons for control unit operation in manual mode (START/RESET)
•Operating mode selection key (MAN STOP AUT)
•14 LEDs to indicate status:
Start button. It is used to engage the starting and stopping of
the control unit in manual mode (mode selection key in the
MAN position):
- Start motor: with the engine stopped and in manual mode,
press once to start the engine.
- Stop motor with cooling: with motor running and in manual
mode, press once to stop the motor with cooling.
- Stop motor without cooling: with motor running and in manual
mode, press twice to stop the motor without cooling.

FRONT OF THE CONTROL UNIT| PAG. 5
Overspeeding LED. Light signal via the ashing overspeeding
alarm detection LED. The light indicator will remain active until
the motor has been stopped and the control unit has been re-
set by pressing the RESET button.
The overspeeding alarm causes the motor to stop immediately
without cooling.
The overspeeding alarm is only managed if the nominal motor
speed has been adjusted (sec. 3.3). The overspeeding LED
also indicates if the nominal speed of the control unit has not
been adjusted, via the ashing of.
Low oil pressure LED. Light signal via the ashing low oil pres-
sure alarm detection LED. The light indicator will remain active
until the motor has been stopped and the control unit has
been reset by pressing the RESET button. The low oil pressure
alarm causes the motor to stop immediately without cooling.
High water temperature LED. Light signal via the ashing high
water temperature alarm detection LED. The light signal will
remain active as long as the alarm condition continues (control
unit ATA input). The control unit is reset by pressing the RESET
button. The high water temperature alarm causes the motor to
stop immediately without cooling.
Motor failure LED. Light signal via the ashing motor failure
alarm detection LED. The light signal will remain active as long
as the alarm condition continues. The control unit is reset by
pressing the RESET button.
Starting failure LED. Light signal via the ashing start motor
failure alarm detection LED. The light signal will remain active
as long as the alarm condition continues. The control unit is
reset by pressing the RESET button.
Power supply LED. Light signal via an LED on the control unit.
Operating mode selection key (MAN/STOP/AUT). The mode
selection key of the M6 control unit allows to select the operat-
ing mode of the control unit:
-STOP: stops the motor and turns off the control unit.
-MAN: activates the control unit and sets the manual operating
mode (control of genset via buttons).
-AUTO: activates the control unit and sets the auto operating
mode; performs a switch on of the switchboard and congures
the auto work mode to comand the engine start input by con-
tact free of tension (LT).
RESET button. It allows the user to reset the generator set af-
ter an alarm has been detected.
Fuel reserve LED. Light signal via the ashing fuel reserve
alarm detection LED. The light signal will remain active as long
as the alarm condition continues (RC input of the control unit).
Battery charging alternator failure LED. Light signal via the
ashing alarm LED detecting a failure in the battery charger via
the input D+. The LED will remain active until the control unit is
reset by pressing the RESET button.
Auxiliary motor LED. Light signal via the ashing auxiliary mo-
tor alarm detection LED. The light signal will remain active as
long as the alarm condition continues (control unit AUX input).
The control unit is reset by pressing the RESET button. The
auxiliary motor alarm causes the motor to stop immediately
without cooling.
Emergency stop LED. Light signal via the ashing emergency
stop alarm detection LED. The light signal will remain active as
long as the alarm condition continues (control unit PEM input).
The control unit is reset by pressing the RESET button. The
emergency stop alarm causes the motor to stop immediately
without cooling.

FRONT OF THE CONTROL UNIT| PAG. 6
Preheating LED. Light signal via an LED ashing during the
preheating phase of starting the motor.
Cooling and motor stop LED. Light signal via an LED ashing
during the cooling phase of stopping the motor.
Starting free of voltage LED. Light signal via an LED ashing
with the activation of the genset’s external start input via volt-
free contact (LT).
Motor running LED. Light signal via the ashing of the motor
running detection LED.

CONNECTIONS| PAG. 7
3. CONNECTIONS
3.1 OUTPUTS
3.1.1 PREHEATING OUTPUT (PR)
The preheating output (PR) of the M6 control unit is a high power shortable out-
put (40 A) which regulates the heating process of the motor’s spark plugs during
the starting process. The activation time of the preheating output can be set
(parameter 4). The preheating output can also be used to control stopping due to
the excitation of motors which use PE/PS type control (parameter 15 value 2).
3.1.2 CONTACTOR ACTIVATION OUTPUT (CON)
The contactor output (CON) activates a programmable time (parameter 5) after
detecting the motor is running in order to ensure stabilisation of the motor before
enabling the charging of the generator set.
3.1.3 EXCITATION OUTPUT OF THE BATTERY CHARGE ALTERNATOR (D+)
The battery charge alternator excitation output (D+) of the M6 control unit is
responsible for driving the battery charge alternator during the starting process
via a starting pulse at a programmable time interval (parameter 14).
3.1.4 ALARM OUTPUT (AL)
The M6 control unit activates the alarm output (AL) upon the detection of any
active error and remains active until the system has been reset by pressing the
RESET key. Furthermore, the M6 control unit also activates the alarm output (AL)
before starting the motor in automatic operation mode by means of the external
start via voltfree contact (LT).

CONNECTIONS| PAG. 8
3.1.7 IGNITION (PD)
The IGNITION output (PD) is activated 500 ms after the preheating output has
been deactivated and remains active while the motor is running. The IGNITION
output (PD) is interconnected with the emergency stop input (PEM) of the control
unit.
For motors congured with the starting control mode PULL/HOLD (parameter 15
value 3), the IGNITION output (PD) is also activated during starting in the motor
preheating phase.
3.2 INPUTS
3.2.1 ALTERNATOR VOLTAGE INPUT (GEN)
The alternator voltage input is used to calculate the electrical signal frequency of
the generator (parameter 16 value 0). To do this 2-phases of the alternator are
connected between the GEN and GCOM inputs of the control unit in gensets with
more than one phase or 1 phase and the neutral of the alternator between the
GEN and GCOM inputs of the control unit in single phase gensets.
3.2.2 PICK-UP INPUT (PCK)
The pickup input is used to calculate the motor rotation speed (parameter 16
value 1). To do this, the motor pickup signal is connected to the PCK and GCOM
terminals of the control unit.
3.2.3 VOLTAGE INPUT OF THE ALTERNATOR AND PICK-UP (GCOM)
Same input for reading the alternator voltage frequency and motor speed, accord-
ing to the programming of the control unit (parameter 16). Only one of the two
signals can be wired to the terminal of the GCOM input of the M6 control unit.
3.1.5 STARTING OUTPUT (ARR)
The motor starting output (ARR) of the M6 control unit is a high power shortable
output (40 A) which activates the starter. The motor starting output (ARR)
remains active until a condition is detected while the motor is running for a pro-
grammable maximum time (parameter 3).
3.1.6 CONFIGURABLE STOP (PC)
The congurable motor stop output (PC) of the M6 control unit is a high power
shortable output (40 A) that controls the stopping of the motor and is intercon-
nected with the emergency stop input (PEM) of the control unit. The congurable
motor stop output (PC) can be congured so that it controls motors according to
four different start/stop modes (parameter 15):
•PR/PD (parameter 15 value 0): The congurable motor stop output
(PC) for motors with PR/PD control is activated 500 ms after the
preheating output has been deactivated, and remains active while the
motor is running.
•PR/PE (parameter 15 value 1): The congurable motor stop output
(PC) for motors with PR/PE control is activated during a programmable
time interval (parameter 7) when the motor stop command has been
given. In this conguration, the emergency stop input (PEM) of the
control unit must be wired to the negative terminal of the battery and
the emergency stop button must be wired to the auxiliary input of the
(AUX) alarm.
•PE/PD (parameter 15 value 2): The congurable motor stop output
(PC) for motors with PE/PD control is activated 500 ms after the
preheating output (PR) has been deactivated, which occurs when the
motor stop command has been given. This output is used to enable
the motor sensors. The preheating output (PR) of the control unit is
responsible for executing the motor stop by activating the stop by
excitation process.
•PULL/HOLD (parameter 15 value 3): The motor start control set in
PULL/HOLD mode uses the congurable output (PC) as PULL signal
(40 A) which is activated for a xed time of 1 second during starting.
The IGNITION output (PD) is used as HOLD signal (2 A) which remains
active while the motor is running.

CONNECTIONS| PAG. 9
3.2.9 EMERGENCY STOP INPUT (PEM)
Digital input to connect an emergency stop for inmediately motor stop without
cooling. The emergency stop alarm has a visual signal on the front of the M6
control unit.
3.3 USB PORT
It allows the programming of certain parameters, in addition to the reading of the
internal hour counter (total and partial) and alarm history through a PC.
3.2.4 WATER TEMPERATURE INPUT (ATA)
Input connected to the motor coolant temperature thermostat that is used to
detect a high water temperature alarm condition. The polarity of the ATA input is
congurable (parameter 23). The high motor temperature alarm has a visual sig-
nal on the front of the M6 control unit. The high motor temperature alarm causes
the motor to stop immediately
3.2.5 LOW OIL PRESSURE INPUT (BPA)
Input connected to the engine oil pressure switch, indicating to the control unit
that a low oil pressure alarm has ocurred. Polarity of the BPA input is congur-
able (parameter 24). The low oil pressure alarm has a visual signal on the front
of the M6 control unit. The low oil pressure alarm causes the motor to stop
immediately.
3.2.6 FUEL RESERVE INPUT (RC)
Input connected to the fuel tank gaug ethat is used to detect a fuel reserve
alarm condition. The polarity of the RC input is congurable (parameter 27). The
fuel reserve alarm has a visual signal on the front of the M6 control unit. The
action taken by the M6 control unit after detecting the fuel reserve alarm is pro-
grammable (parameter 18).
3.2.7 AUXILIARY ALARM INPUT (AUX)
Input connected to any sensor which tells the control unit that is used to detect a
motor auxiliary alarm condition. The polarity of the AUX input is congurable
(parameter 25). The motor auxiliary alarm has a visual signal on the front of the
M6 control unit. The auxiliary engine alarm causes an immediate stop motor.
3.2.8 ENTRADA ARRANQUE EXTERNO (LT)
Digital signal for connecting a volt-free contact forcing the starting of the genset
when the M6 control unit is in automatic mode. The polarity of the LT input is
congurable (parameter 26). The external start input has a visual signal on the
front of the M6 control unit.

OPERATION| PAG. 10
4. OPERATION
4.1 STARTING THE MOTOR
With motor stopped, and without alarms, when starting the motor, the M6 control
unit proceeds to perform the following operations:
•Preheating of the motor. With the preheating process enabled
(parameter 19 value 1), the control unit activates the preheating
output (PR) in motors for PR/PD and PR/PE control (parameter 15
values 0 and 1) for the set time (parameter 3) with visual indication
via the LED on the front of the control unit.
•Enabling the starting of the motor. Enabling the starting of the motor
is done via the IGNITION output (PD) of the M6 control unit and the
CONFIGURABLE STOP output (PC) for motor congurations PR/PD and
PE/PD (parameter 15 value 0 and 2).
•Starting the motor (ARR). The starting output (ARR) of the M6 control
unit is activated until some of the enabled starting conditions have
been detected, for a maximum time (parameter 3):
•Generator frequency (parameter 16 value 0). The motor is
considered started when the generator frequency exceeds a
certain percentage (parameter 11) of the nominal frequency of
the genset.
•Motor speed (parameter 16 value 1). The motor is considered
started when the motor speed exceeds a certain percentage
(parameter 11) of the nominal motor speed.
•Alternator voltage (parameter 21 value 1). The motor is
considered started when a certain battery charging alternator
voltage (60% of the battery voltage) is exceeded.
Control unit waits for a time (parameter 2) before starting the motor again if no
motor running condition is detected during cranking time. Unit control activates
the STARTING FAILURE alarm led if the maximum starts attemps is exceeded.
Excitation of the battery charger is set on by the D+ output for a time (parameter
14) during motor starting process. Controller checks the battery charger voltage
after the battery charger excitation time.
The Alternator Failure alarm is activated with a visual signal via the Battery charg-
ing failure LED on the front of the control unit if a fault is detect in the battery
charging alternator, .

OPERATION| PAG. 11
4.3 OPERATING MODES
The M6 control unit is turned on by turning the key on the control panel to either
the “MAN” or “AUT”O position. Controller checks leds by setting on sequentially
during power on.
4.3.1 STOP MODE (STOP)
By selecting the “STOP mod”e, the control unit orders the generator set motor to
stop in a controlled manner if it is in operation and, after checking that it has
stopped, proceeds to switch off the control unit.
4.3.2 MANUAL MODE (MAN)
Selecting “MAN mode”, starting and stopping the generator set is controlled via
the START button on the control panel. By pressing “START” the motor is ordered
to start immediately if the motor is stopped, indicated by the Motor running LED
not being lit.
If “START button” is pressed while the genset is in operation, indicated by the
Motor running LED lit at the front of the M6 control unit, the genset is stopped by
disconnecting the genset load via the deactivation of the contactor output (CON)
of the control unit and proceeding to engage the cooling process indicated by the
Cooling and stop LED lit at the front of the M6 control unit.
If “START button” is pressed when the motor is in the process of cooling, indicat-
ed by the Cooling and stop LED at the front of the M6 control unit, an immediate
stop is carried out, cancelling the motor cooling process.
4.3.3 AUTOMATIC MODE (AUTO)
When selecting “AUTO mode”, the starting and stopping of the generator set is
controlled by means of the external start input via voltage free contact (LT) of the
M6 control unit.
With the closure of the voltage free contact, the control unit commands the
generator set motor to start.
With the opening of the voltage free contact, the control unit commands the
generator set motor to stop with cooling.
The congurable stop output (PC) of the control unit is used in motors for PR/
PULL control (parameter 15 value 3) to energize the motor solenoid by activating
a pulse for a duration of 1 second during the start process.
•Generator load activation: Once any motor starting condition has
been detected, the control unit waits for a set time (parameter 5) for
the activation of charging through the contactor output (CON) of the
control unit.
4.2 STOPPING THE MOTOR
With the motor started, when stopping the motor, the M6 control unit proceeds to
perform the following operations:
•Deactivating charging. The M6 control unit deactivates the contactor
output (CON) to release the charging of the generator set.
•Cooling the motor. Motor will continue running without load for a
programmable. If any alarm is detected, the M6 control unit performs
an immediate stop without cooling the motor.
•Motor stop. After the motor cooling time has passed, the IGNITION
output (PD) of the M6 control unit is deactivated and, depending on
the motor conguration (parameter 15) the following occurs:
•Deactivation of the CONFIGURABLE STOP output (PC) for motor
congurations PR/PD and PE/PD (parameter 15 value 0 and 2).
•Activation of the CONFIGURABLE STOP output (PC) for motor
congurations PR/PE (parameter 15 value 1) for a congurable
time (parameter 7).
•Activation of the PREHEATING output (PR) for motor
congurations PE/PD (parameter 15 value 2) for a congurable
time (parameter 7).
•Motor is stopped if no start condition is detected. The following start
condition can be selected:
•Generator frequency (parameter 16 value 0). The motor is
considered stopped when the generator frequency is zero.
•Motor speed (parameter 16 value 1). The motor is considered
stopped when the motor speed is zero.
•Low Oil Pressure Input (parameter 22). The motor is considered
stopped when the motor oil pressure switch connected to the
low oil pressure input (BPA) is closed.
•Battery charging alternator voltage (parameter 21 value 1).
The motor is considered stopped when the battery charging
alternator voltage is less than a certain voltage (60% of the
battery voltage).

OPERATION| PAG. 12
4.4 NOMINAL SPEED ADJUSTMENT
It is necessary to set up the nominal motor speed that is used for detecting over-
speed alarm and motor running condition:
1. The Overspeed LED on the M6 control unit is ashing to indicate that the
control unit has no nominal motor speed programmed.
2. Start the motor and wait for it to stabilise until it reaches its nominal speed.
3. Hold down “RESET button” for 5 seconds.
4. The Overspeed LED on the M6 control unit turns off to indicate that the
process is complete.
5. Management of the overspeed alarm is enabled (parameter 17 value 1).
6. To reset the setting to nominal speed, it is necessary to hold down “RESET
button” for 5 seconds with the motor stopped. Performing this process, over-
speed alarm management is disabled (parameter 17 value 1).
The described process is valid, both for speed detection by frecuency of generator
as per motor pick-up.

DIMENSIONS, WIRING AND MECHANICAL PARTS | PAG. 13
5. DIMENSIONS, WIRING AND MECHANICAL
PARTS
Fig.1
M6 Control Unit

DIMENSIONS, WIRING AND MECHANICAL PARTS | PAG. 14
The equipment must be isolated or disconnected before connecting the voltage
input for the generator, as there is a risk of danger. The USB connector complies
with the standard 2.0.
To power the control panel, it is recommended to use a 1mm2 section cable. A
cable with a diameter of 2.5 mm2 must be used for +BAT, ARR, PR and PC con-
nections. For all other connections, it is recommended to use a 1mm2 cable
diameter.
5.1 INPUTS AND OUTPUTS
Signal Description Type Characteristics
Powe supply
8÷36V Positive battery terminal Power supply Tensión alimentación módulo de 8 a 36V
-BAT Negative battery terminal Power supply Module supply negative
Digital Inputs
RC Fuel reserve Input NPN digital input
BPA Low oil pressure Input NPN digital input
ATA High water temperature Input NPN digital input
LT External start Input NPN digital input
PEM Emergency stop Input NPN digital input
AUX Motor auxiliary input Input NPN digital input
Pick-up/generator input
GCOM Common Input Pick-up and alternator voltage common input
PCK Pick-up Input PICK-UP input
GEN Generator Input Alternator voltage input
High voltage PNP outputs
+BAT Positive battery terminal Power supply Digital outputs supply voltage
ARR Starting Output PNP digital output of power
PR Preheating Output PNP digital output of power
PC Congurable stop Output PNP digital output of power
PNP outputs
D+ Alternator excitation Output PNP digital output
AL Alarm Output PNP digital output
CON Contactor Output PNP digital output
PD Ignition Output PNP digital output
Fig.2
M6 Control Unit Connections

DIMENSIONS, WIRING AND MECHANICAL PARTS | PAG. 15
The control unit must be mounted at the front of an electrical panel, if possible in
the centre to allow easy wiring.
There are no special ventilation requirements due to the low power consumed by
the control unit.
All outputs must be provided with the corresponding inductive current disconnec-
tion devices (diodes, varistors, RC lters, etc…).
The wiring for manoeuvres should be kept at a sufcient distance from high elec-
tric elds: at least two metres of power lines of up to 600A and 1 metre of power
lines over 600A.
5.3 CHARACTERISTICS AND INSTALLATION OF THE EQUIPMENT
EThe equipment is included within the measurement category CAT III 600V for
measurements performed in the building installation.
Disconnection means should be incorporated to the xed installation in accord-
ance with instalation regulations.
Such means must have contact separation for all poles that provide full discon-
nection in category III overvoltage conditions.
The disconnecting means, must be accessible by the user. The negative terminal
of the battery, electrical panel chassis and generator chassis must all be earthed.
After installation, the connection terminals of the Pick Up / Generator sensor in-
put (terminals GCOM, PCK, GEN) should not be accessible.
If the equipment is handled in a way not specied by the manufacturer, the equip-
ment’s protection devices could become compromised.
The surface areas of the equipment and the external face should be cleaned with
a damp cloth.
This equipment can generate the risk of danger if handled improper-
ly. It must be installed by qualied personnel. It is necessary to
consult the equipment’s documentation.
ATTENTION: risk of danger.
5.2 ELECTRICAL CHARACTERISTICS
Symbol Parameter Conditions Minimum Typical Maximum Unit
Power supply (terminals 8÷36V, –BAT, +BAT)
8÷36V Module supply voltage 8 36 VDC
+BAT Power supply of the outputs 8 36 VDC
IBAT Supply current 8÷36V=12V 20 60 mA
IBAT Supply current 8÷36V=24V 10 50 mA
PBAT Power consumption 1 W
NPN digital inputs (terminals RC, BPA, ATA, LT, PEM, AUX)
VIN Input voltage -0,7 40 V
VIL Low level input voltage 1 V
VIH High level input voltage 5 V
IIL Low level input current VIN = 0V 2 2,5 mA
IIH High level input current VIN = 24V 0 100 uA
Pick-Up / Generator input sensor (terminals GCOM, PCK, GEN)
VIN Pick-Up input voltage 4 30 VDC
FIN Pick-Up input frequency 200 2500 8000 Hz
VIN Generator input voltage 180 480 VAC
FIN Generator input frequency 45 66 Hz
Power PNP outputs (terminals ARR, PR, PC)
VOOutput voltage +BAT V
IOOutput current T = 1s 40 A
IOOutput current T = 10s 20 A
IOOutput current de salida T = ∞ 15 A
PNP outputs (terminals D+, AL, PD, CON)
VOOutput voltage +BAT V
IOOutput current 1 A
RD+ Output resistance D+ 49,5 Ω
Environmental conditions and protection of the enclosure
Tª Operating temperature -40 +85 ºC
HRRelative humidity No
condensation 80 %
IP Degree of Protection *see note 1 65
Note 1: IP 65 on the front of the control unit when installed on the control panel with the sealing gasket-
provided.

DIMENSIONS, WIRING AND MECHANICAL PARTS | PAG. 16
5.4 DIMENSIONS OF THE EQUIPMENT 5.5 SYMBOLS
Attention. Consult the manufacturer’s documentation.
Equipment with Class II protection against electric shock. Equipment
protected by double insulation or reinforced insulation.
Direct current.
5.6 CERTIFICATIONS
Electromagnetic Compatibility Directive 2004/108/EEC. Product Standard UNE
EN 61326 1
Low Voltage Directive 2006/95/EEC. Product Standard 61010 11
Fig.3
M6 dimensions

TABLE OF PARAMETERS | PAG. 17
6. TABLE OF PARAMETERS
Parameter Description Value Range
1
Number of starts
Number of starting retries automatically performed by the
control unit before signalling a starting failure.
4 1..10
2Time between starts
Time between starting retries.
5” 3”..15”
3
Start time
Maximum activation time of the motor start output before
any motor starting condition is detected.
5” 2”..30”
4
Preheating time
Maximum activation time of the motor preheating output
(PR) during the motor starting process. Special case with
3 second delay between activation of the congurable
stop (PC) and start (ARR) outputs for motors with control
type PR/PD: preheating process enabled by programming
a value of 0 for the preheating time.
8” 0”..180”
5
Contactor activation time.
Motor stabilization time from the moment the motor is
detected in operation until the activation of the genset
contactor output (CON).
5” 1”..30”
6
Cooling time
Time that the motor remains in operation without load
after the genset has been commanded to stop.
120” 2”..1800”
7
Stop time.
Activation time of the solenoid used to stop the motor
in order to cause the stopping of the generator set with
motor conguration type PR/PE and PE/PD.
10” 1”..30”
8
Low oil pressure delay
Time interval from the moment the starting of the motor
is detected until the low oil pressure alarm is managed to
ensure the stabilisation of the oil pressure switch.
15” 0”..60”
9
High temperature water delay
Time interval from the moment the starting of the motor is
detected until the high temperature water alarm is mana-
ged to ensure the stabilisation of the coolant temperature
thermostat.
1” 0”..60”
10
Motor auxiliary alarm input delay.
Time interval from the moment the starting of the motor
is detected until the motor auxiliary alarm is managed for
the stabilisation of the motor sensor connected to the
motor auxiliary alarm input (AUX) of the M6 control unit.
5” 0”..60”
11
Frequency threshold for starting detection
Percentage of genset nominal speed at which point the
motor is considered to be started. If the process of ad-
justing the nominal frequency of the genset has not been
completed, the control unit will consider the motor to be
started from a frequency of 20 Hz.
30 0..100%
12
Overspeeding detection threshold
Percentage of genset nominal speed at which point the
genset overspeeding alarm is detected.
16 0..100%
13
Alarm activation time.
Activation time of the AL output upon detection of a
genset alarm. If set to zero, the output will remain active
indenitely until the genset is reset by pressing the RESET
button or by turning off the control unit.
0 0..600
14
Excitation time of the battery charging alternator
Excitation time of the battery charging alternator during
the motor starting process. At the end of this time,
controls will begin to check the level of voltage supplied by
the battery charging alternator, the detection of the
motor starting condition and to verify the proper functio-
ning of the generator set’s battery charging regulator.
3
1”..29’’
(Always less
than the
starting time)
15
Motor configuration
Conguration of the preheating (PR) and congurable stop
(PC) outputs of the motor control unit.
0
0..3
0:PR/PD
1:PR/PE
2:PE/PD
3:PR/PULL
16
Selection of motor speed reading
Method for calculating the motor speed by generator
frequency or motor pickup.
00:Generador
1: Pickup
17 Enabling the motor overspeeding alarm
0
0..1
0: Not active
1: Active
18 Motor stop due to low fuel reserve alarm
Management of the fuel reserve alarm.
19
Enabling preheating
Special case with 3 second delay between activation of
the congurable stop (PC) and start (ARR) outputs for PR/
PD type motors: preheating process enabled by program-
ming a value of 0 for the preheating time.
20 Enabling cooling time
21 Detection of motor in operation for battery charging
alternator 1
22 Detection of stop due to low oil pressure 0
23 Polarity of high water temperature input (ATA)
0
0..1
0: Normally open
(NO)
1: Normally closed
(NC)
24 Polarity of low oil pressure input (BPA)
25 Polaridad entrada auxiliar de motor (AUX)
26 Polarity of volt-free input (LT)
27
Polarity of fuel reserve input (RC)

HIMOINSA reserves the right to modify any characteristic without prior
notice. Illustrations may include optional equipment and/or accessories.
Non contractual images. The technical information described in this
manual corresponds to the information available at the time of printing.
HIMOINSA ® - 2019 ©All rights reserved.
© HIMOINSA - 2019W33
FACTORIES
SPAIN • FRANCE • INDIA • CHINA • U.S.A. • BRAZIL • ARGENTINA
SUBSIDIARIES
PORTUGAL | SINGAPORE | POLAND | ARAB EMIRATES | PANAMA | GERMANY
ARGENTINA | ANGOLA | UNITED KINGDOM | DOMINICAN REPUBLIC | SOUTH AFRICA
HEADQUARTERS
Ctra. Murcia - San Javier, km 23.6
30730 SAN JAVIER (Murcia) SPAIN
TEL. +34 968 19 11 28 | +34 902 19 11 28
Fax +34 968 19 12 17 | Export Fax +34 968 33 43 03
www.himoinsa.com
Table of contents
Other Himoinsa Control Unit manuals
Popular Control Unit manuals by other brands
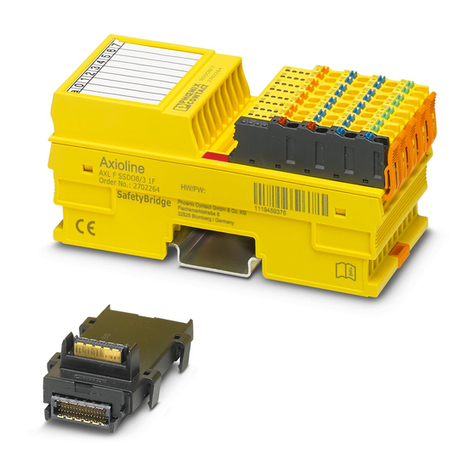
Phoenix Contact
Phoenix Contact Axioline F user manual
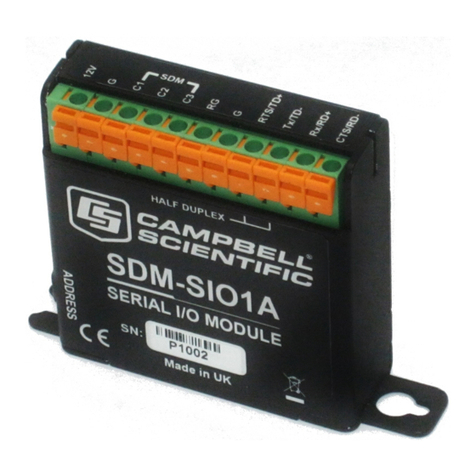
Campbell
Campbell SDM-SIO1A instruction manual
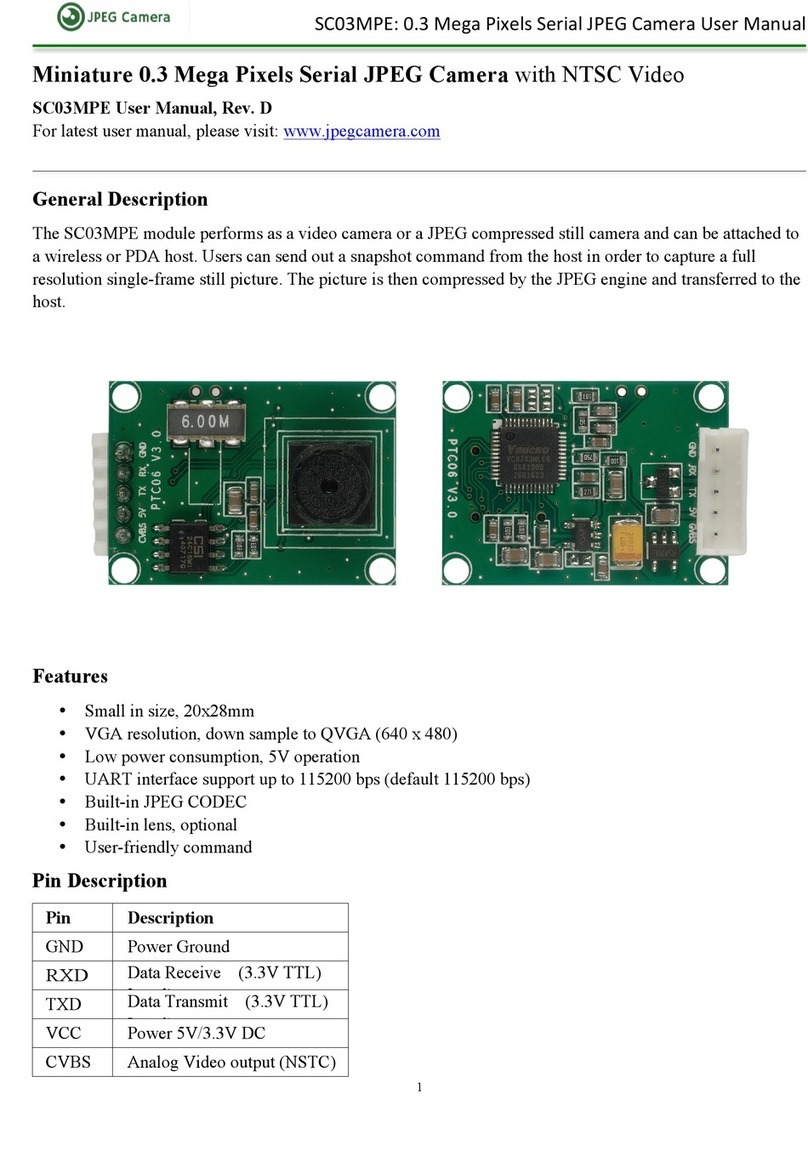
JPEG Camera
JPEG Camera SC03MPE user manual

Viavi
Viavi COSA-4055 user manual
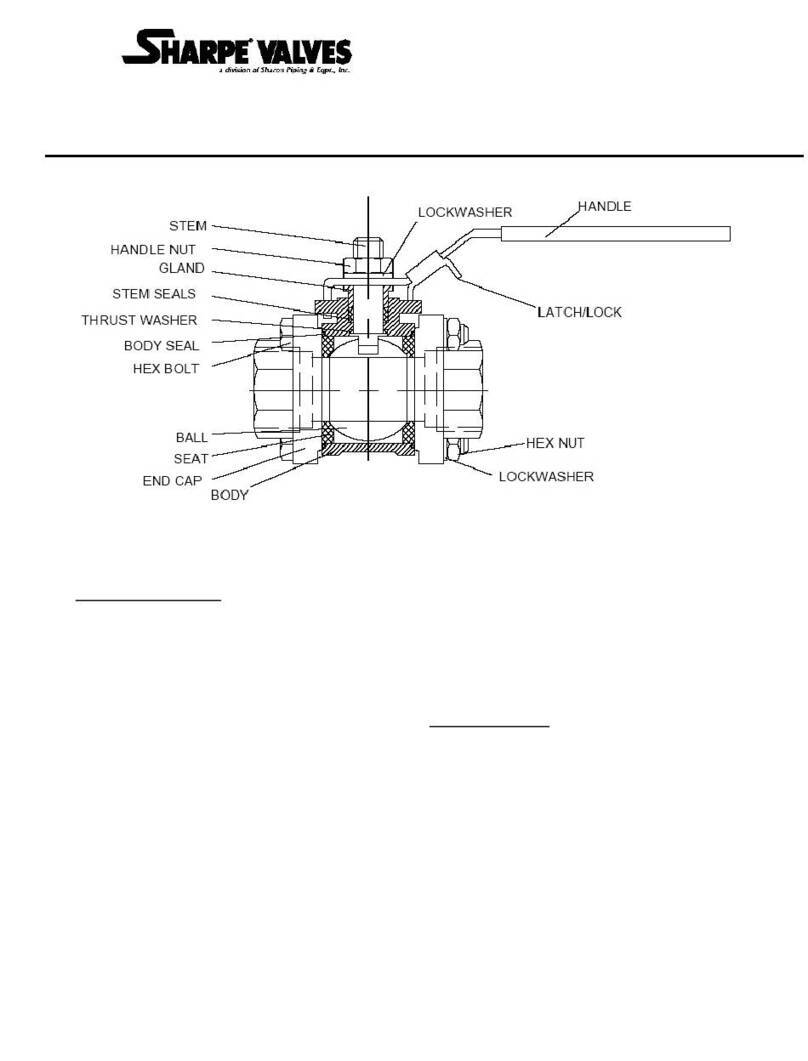
Sharon Piping & Eqpt
Sharon Piping & Eqpt Sharpe Valves 53034 Installation, operation and maintenance instructions
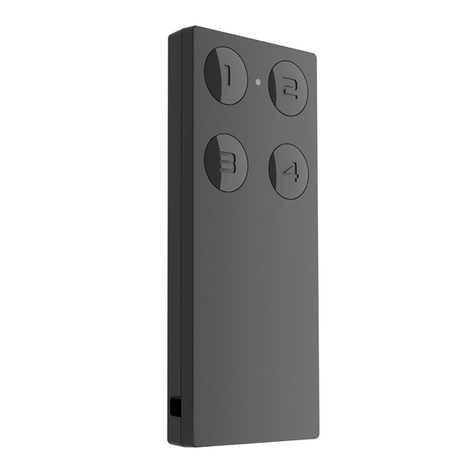
iNels
iNels RF KEY-40/W manual