SLEIPNER MOTOR AS SIDE-POWER SX35 User manual

Made in Norway
©Sleipner Motor AS 2020
SLEIPNER MOTOR AS
P.O. Box 519
N-1612 Fredrikstad
Norway
www.side-power.com
Document id:
Revision:
Date:
5630
10
Installation Manual
2020
SX
- 35
- 50
For installing SX thruster with the
Hydro-pod modication please use the
SX-Hydro pod installation guide.
SX-Hydro pod
NEW

25630 10 2020
-
SX35 & SX50
DECLARATION OF CONFORMITY
Sleipner Motor AS
P.O. Box 519, Arne Svendsensgt. 6-8
N-1612 Fredrikstad, Norway
Declare that this product with accompanying standard control systems complies with
the essential health and safety requirements according to:
DIRECTIVE 2013/53/EU
DIRECTIVE 2014/30/EU
DIRECTIVE 2014/35/EU
MC_0020
Bow Installation Instructions
Bow Installation Considerations and Precautions ..................... 3
Thruster Measurements ........................................................... 4
Thruster Specications.............................................................. 5
Technical Specications ........................................................... 5
Control Box Technical Specications......................................... 6
Positioning the Stern Truster ..................................................... 7
Stern Thruster Cowls/ Grids ...................................................... 8
Thruster Installation Instructions
Thruster Installation Considerations and Precautions............... 9
Grids or Cowls Assembly......................................................... 10
Tunnel Installation ................................................................... 11
SX Spacer ............................................................................... 12
Motor Installation ..................................................................... 13
Control Box Installation............................................................ 14
Thruster Electrical Installation ......................................... 15 - 16
Electrical Specications .......................................................... 17
Control Panel Cable Installation ............................................. 18
Control Panel Installation ........................................................ 19
Pre-delivery Checklist .......................................................... 20
Spare Parts ............................................................................ 21
Warranty statement .............................................................. 21
Contents
EN
Products
SE20/110S - SE20 Tunnel thruster, 12V
SE25/110S - SE25 Tunnel thruster, 12V
SE30/125S2 - SE30 Tunnel thruster, 12V
SE40/125S2 - SE40 Tunnel thruster, 12V
MC_0257
Thruster Installation Considerations and Precautions
EN
Before installation, it is important that the installer reads this guide to ensure necessary acquaintance with this product.
• The electromotor must be handled with care. Do not lift it by internal cable connections, main terminals or placed down on the driveshaft.
• The thruster power supply circuit must include the recommended sized fuse and a battery isolation switch.
• Never run the thruster out of water.
• It is important to follow the guidelines in this manual. Failure can result in severe damage to the thruster.
MC_0267
NEVER
Disassemble any part of the Ignition Protected stern thruster assembly. Tampering with the Ignition Protected stern thruster assembly or any attempt
to disassemble anything on this thruster assembly inside the boat can cause an explosion with severe consequences. If there is a problem with your
Ignition Protected stern thruster, please contact your dealer.
MC_0071
Installation Considerations and Precautions
EN
• Do not install the thruster in a position where you need to cut a stiff ener/ stringer/ support for the hull integrity without checking with the boat builder
this can be done safely.
• Contacts/ plugs or other joints in the control cables must be mounted so they remain dry at all times.
• We advise painting the gear house and propellers with antifouling. (NB: Do not paint the sealings/ rubber fi ttings or propeller shafts.)
• Do not nish the inside of the tunnel with a layer of gelcoat/ topcoat or similar. There is only room for a thin coat of primer and two layers of anti-fouling
between the tunnel and the propellers.
• keep installation within advised measurements. The entire surface is hard coated seawater resistant aluminium. Do not damage/penetrate the coat.
• The external stern thruster assembly and controller unit are ignition protected and can be installed in areas with the chance of explosive gases in
accordance to ISO 8846 and ABYC c1500. (Certi cation pending)
• Ensure that the external stern thruster assembly does not disturb the water fl ow under the hull. At higher speeds, if the thruster is installed to
low it can cause damage to the thruster and/ or add additional drag and unwanted water splashing.
• The recommended minimum tunnel depth from the water surface is 140mm (5,51‘) to the centre of tunnel diameter. Place the Thruster as deep as
possible for better performance and reduced noise.
• When installing the thruster ensure it does not foul existing equipment inside the boat like motor bedding etc.
• If able ensure that sterndrives/ trimtabs do not interfere with the water fl ow from the thruster as this can reduce the thrust eff ectiveness considerably.
We recommend the use of our Side-Power cowls to enhance the performance and allow installation in shallow draft boats. Side-Power cowls will also
minimise the eff ect if sterndrives/ trimtabs obstruct the thruster.
• Ensure there is enough space both inside and outside the transom of the boat and the thruster does not get in confl ict with existing equipment
inside the boat like steerage links etc. (NB: It is possible to mount the tunnel off set from the boat’s centre line if necessary.)
• Heat protection cut off is calculated from the thruster motor. To avoid cable overheating do not install place the volt cables from the thruster to the
control box near any heat sources.

3
5630 10 2020
-
SX35 & SX50
It is the installers responsibility
When installing Side-Power equipment to follow the outlined regulations/ classi cation rules (electrical/ mechanical) according to
international or special national regulations. Instructions in this guide cannot be guaranteed to comply with global electric/ mechanic
regulations/ classi cation rules.
To follow all health and safety laws in accordance with their local outlined regulations/ classi cation rules.
Before installation, it is important that the installer reads this guide to ensure necessary acquaintance with this product.
The recommendations made in this manual are guidelines ONLY, and Sleipner Motor AS (Side-Power) strongly recommend that
before installation, advice is obtained from a naval architect familiar with the particular vessel and regulations/ classi cations.
This manual is intended to support educated/ experienced staff and is therefore not suffi cient in all details for professional
installation. (NB: These instructions are only general instruction. If you are not skilled to do this work, please contact professional
installers for assistance.)
All electrical work must be done by a licensed professional.
Faulty installation of the tunnel, thruster or panel will render all warranty given by Sleipner Motor AS void. MC_0038
MC_0257
Thruster Installation Considerations and Precautions
EN
Before installation, it is important that the installer reads this guide to ensure necessary acquaintance with this product.
• The electromotor must be handled with care. Do not lift it by internal cable connections, main terminals or placed down on the driveshaft.
• The thruster power supply circuit must include the recommended sized fuse and a battery isolation switch.
• Never run the thruster out of water.
• It is important to follow the guidelines in this manual. Failure can result in severe damage to the thruster.
MC_0267
NEVER
Disassemble any part of the Ignition Protected stern thruster assembly. Tampering with the Ignition Protected stern thruster assembly or any attempt
to disassemble anything on this thruster assembly inside the boat can cause an explosion with severe consequences. If there is a problem with your
Ignition Protected stern thruster, please contact your dealer.
MC_0071
Installation Considerations and Precautions
EN
• Do not install the thruster in a position where you need to cut a stiff ener/ stringer/ support for the hull integrity without checking with the boat builder
this can be done safely.
• Contacts/ plugs or other joints in the control cables must be mounted so they remain dry at all times.
• We advise painting the gear house and propellers with antifouling. (NB: Do not paint the sealings/ rubber fi ttings or propeller shafts.)
• Do not nish the inside of the tunnel with a layer of gelcoat/ topcoat or similar. There is only room for a thin coat of primer and two layers of anti-fouling
between the tunnel and the propellers.
• keep installation within advised measurements. The entire surface is hard coated seawater resistant aluminium. Do not damage/penetrate the coat.
• The external stern thruster assembly and controller unit are ignition protected and can be installed in areas with the chance of explosive gases in
accordance to ISO 8846 and ABYC c1500. (Certi cation pending)
• Ensure that the external stern thruster assembly does not disturb the water fl ow under the hull. At higher speeds, if the thruster is installed to
low it can cause damage to the thruster and/ or add additional drag and unwanted water splashing.
• The recommended minimum tunnel depth from the water surface is 140mm (5,51‘) to the centre of tunnel diameter. Place the Thruster as deep as
possible for better performance and reduced noise.
• When installing the thruster ensure it does not foul existing equipment inside the boat like motor bedding etc.
• If able ensure that sterndrives/ trimtabs do not interfere with the water fl ow from the thruster as this can reduce the thrust eff ectiveness considerably.
We recommend the use of our Side-Power cowls to enhance the performance and allow installation in shallow draft boats. Side-Power cowls will also
minimise the eff ect if sterndrives/ trimtabs obstruct the thruster.
• Ensure there is enough space both inside and outside the transom of the boat and the thruster does not get in confl ict with existing equipment
inside the boat like steerage links etc. (NB: It is possible to mount the tunnel off set from the boat’s centre line if necessary.)
• Heat protection cut off is calculated from the thruster motor. To avoid cable overheating do not install place the volt cables from the thruster to the
control box near any heat sources.

45630 10 2020
-
SX35 & SX50
MG_0110
H
WL
+L
++L
(a)
(b)
(c)
(d)
(e)
* Extended tube for
thicker hull models
(Hull thickness >50mm to <150mm)
* Standard tube
(Hull thickness <50mm)
MC_0239
Thruster Measurements
EN
Measurement
code Measurement description mm inch mm inch
H Motor Height 374 14.72 374 14.72
W Width 183 7.20 183 7.20
L Length 171 6.7 171 6.7
+L Standard tube length 108 4.3 108 4.3
++L Extended tube length for thicker hulls 276 10.9 276 10.9
(a) Height of support bolts from tube 35.8 1.4 35.8 1.4
(b) Main tube diameter 50 2 50 2
(c) Support bolts diameter 18 0.7 18 0.7
(d) Distance of support bolts from tube 65 2.6 65 2.6
(e) Distance of support bolts 130 5.1 130 5.1
*35
12v *50
12v
*Valid for SX & SXP

5
5630 10 2020
-
SX35 & SX50
MC_0073
Technical Speci cations
EN
Motor: Custom made reversible DC-motor.
Gearhouse: Seawater resistant aluminium. Ballbearing and ceramic axial seals at propeller shaft and a combination of ball bearing/ slide bearing
at driveshaft. (Pre- lled and sealed for life)
Motor bracket: Seawater resistant aluminium, galvanically insulated from the motor..
Tunnel: Hydrodynamic breglass reinforced snap on composite.
Propeller: 5-blade skewback “Q-prop” propeller, breglass reinforced composite.
Batteries: Minimum recommended battery capacity (cold crank capacity by DIN/SAE standard)
Contact a battery supplier for more information.
Max. use: 2 - 3 min. duty cycle at 20°
Safety features: - Electronic time-lapse device protects against sudden change of drive direction.
- The electric thermal cut-off switch in electromotor protects against overheating (auto-reset when electro motor cools down).
- Flexible coupling between electro-motor and driveshaft protects electromotor and gear system if propeller jams.
- Original Sidepower panels shut off automatically 6 minutes after last use.
- Original Sidepower panels use child-safe double ON buttons.
- An integrated microprocessor monitors solenoids, reduce wear and risk of solenoid lock-in.
- Auto-stop of the thruster occurs when an undesirable solenoid lock-in occurs or when continuous operation cut-off timer exceeds
3 minutes.
MG_0110
H
WL
+L
++L
(a)
(b)
(c)
(d)
(e)
* Extended tube for
thicker hull models
(Hull thickness >50mm to <150mm)
* Standard tube
(Hull thickness <50mm)
MC_0149
Thruster Speci cations
EN
description * 35 * 50
Available DC System (v) 12v 12v
Thrust 12v or 24v (kg * lbs) 43 kg * 94 lbs 62 kg * 136 lbs
Thrust 10.5v or 21v (kg * lbs) 35 kg * 77 lbs 50 kg * 110 lbs
Typical Boat Size (m * ft) 6m - 10m * 19ft - 32ft 8m - 11m * 27ft - 37ft
Propulsion System Single Single
Power (kw * Hp) 1.8kw * 2hp 2.8kw * 3.75hp
Weight (kg * lbs) 15.3 kg * 33.73 lbs 15.3 kg * 33.73 lbs
Minimum Battery Capacity (CCA) 12v * 24v * 48v 300 380
*Valid for SE / SE IP & SEP / SEP IP

65630 10 2020
-
SX35 & SX50
MC_0082
Control Box Technical Speci cations
EN
SX35 SX50
Operation volts: 12v. 12v
Max Current: 250A 380A
Duty Cycle: S2. S2
Max ambient temp: 50ºc 50ºc
Min ambient temp: -25ºc -25ºc
Power supply cable: 35 - 70mm²/ AWG 2 - 00 35 - 70mm²/ AWG 2 - 00
Mount direction : Any Any
MG_0132
121 mm
4’76”
187 mm
7’36”
170 mm
6’69”
136 mm
5’35”
110 mm
4’33”

7
5630 10 2020
-
SX35 & SX50
MC_0072
Positioning the stern truster
EN
For best performance, the thruster must be installed as deep on the stern as possible and the thrusters water fl ow must not obstruct any objects.
The thruster should be installed as deep under the waterline as possible for two reasons:
1. So it does not suck air from the surface which will reduce performance and increase noise levels.
2. To receive maximum effi ciency and thrust.
The thruster must be installed to ensure the propulsion water fl ow must not be obstructed by other objects. Objects that obstruct the water fl ow will
greatly reduce the thrust output.
Position
The thruster can be installed in multiple locations on the boat transom. Installing the thruster slightly off centre will not aff ect the overall eff ectiveness of
the thruster. Installing the thruster off centre may be required to avoid any obstructions externally or internally on the vessel.
Ensure that the external stern thruster assembly does not disturb the water fl ow under the hull. At higher speeds, if the thruster is installed to
low can cause damage to the thruster, additional drag and unwanted water splashing.
Alignment
The thruster can be installed at a slight angle if required for the water fl ow to avoid obstructions. These obstructions can include propellers systems, trim
tabs or the hull. The average force the thruster propels water is 5-7 meters per sec, therefore angled installations must be as deep as possible under the
water to minimise spray breaking beyond the water surface. (NB: install the truster at an angle only if no other suitable location can be found.)
Max hull thickness 50mm include spacer
MG_0109
Thruster tunnel is clear
from obstruction.
Ensure the attachment bolts and
wiring are not obstructing objects
internally in the boat such as
steering legs or motors
Steering Arm
Installing the thruster at an angle
close to the water line will blast
water beyond the water surface.
Engine
The thruster can be installed in multiple
locations based on object obstructions
on the stern.
Engine
Water line Water line
Water line
Engine
Engine
Thruster assembly does not disturb
the water flow under the hull.
Water flow
MC_0082
Control Box Technical Speci cations
EN
SX35 SX50
Operation volts: 12v. 12v
Max Current: 250A 380A
Duty Cycle: S2. S2
Max ambient temp: 50ºc 50ºc
Min ambient temp: -25ºc -25ºc
Power supply cable: 35 - 70mm²/ AWG 2 - 00 35 - 70mm²/ AWG 2 - 00
Mount direction : Any Any
MG_0132
121 mm
4’76”
187 mm
7’36”
170 mm
6’69”
136 mm
5’35”
110 mm
4’33”

85630 10 2020
-
SX35 & SX50
MC_0072
Stern Thruster Cowls/ Grids
EN
Installing a stern thruster cowl for stern thrusters that will allow installations in boats with shallow drafts or due to other obstructions on the stern. These
can include obstacles such as trim tabs, jets or surface drive propeller systems where shallow installation of a stern thruster is the only option.
Cowls:
Designed to aid in water redirection and reduce air entering the tunnel in shallow installations.
Grides:
Designed to protect the thruster from objects while in use.
MG_0017
Shallow installation
Cowl water flow redirection
An angled edge further
preventing air attraction into
the tunnel
Composite material with smooth
inner walls for optimal water flow
and strength
A standard Sidepower stern
thruster tunnel with add-on cowls
for shallow installation
cowls to change the
water flow direction to
avoid obstructions on the
stern
cowls help prevent air
from the water surface
entering the tunnel in
shallow installations
Radiused corners prevent
turbulence
Easy installation for easy
bolt-on fitting
A
B
C
D
IMPORTANT
Angled cowls out of horizontal, must
be installed deeper to avoid air entry
in the thruster tunnel
Model # 90126 90080 90077 90136 90130 90220 90560
A (mm/ in) 528/ 20.8 681/ 26.6 823/ 32.4 850/ 33.5 1010/ 39.75 1208/ 47.6 1580/ 62.2
B (mm/ in) 166/ 6.5 172/ 6.8 243/ 9.6 260/ 10.2 330/ 13 393/ 15.5 515/ 20.3
C (mm/ in) 130/ 5.1 240/ 9.4
D (mm/ i n) 170/ 6.7 256/ 10.1 256/ 10.1 288/ 11.3 340/ 13.4 419/ 16.5 540/ 21.3
IMPORTANT
Install the cowls/ grids before mounting the tunnel to the SX thruster.
100mm
177mm
537mm
174mm

9
5630 10 2020
-
SX35 & SX50
MC_0072
Stern Thruster Cowls/ Grids
EN
Installing a stern thruster cowl for stern thrusters that will allow installations in boats with shallow drafts or due to other obstructions on the stern. These
can include obstacles such as trim tabs, jets or surface drive propeller systems where shallow installation of a stern thruster is the only option.
Cowls:
Designed to aid in water redirection and reduce air entering the tunnel in shallow installations.
Grides:
Designed to protect the thruster from objects while in use.
MG_0017
Shallow installation
Cowl water flow redirection
An angled edge further
preventing air attraction into
the tunnel
Composite material with smooth
inner walls for optimal water flow
and strength
A standard Sidepower stern
thruster tunnel with add-on cowls
for shallow installation
cowls to change the
water flow direction to
avoid obstructions on the
stern
cowls help prevent air
from the water surface
entering the tunnel in
shallow installations
Radiused corners prevent
turbulence
Easy installation for easy
bolt-on fitting
A
B
C
D
IMPORTANT
Angled cowls out of horizontal, must
be installed deeper to avoid air entry
in the thruster tunnel
Model # 90126 90080 90077 90136 90130 90220 90560
A (mm/ in) 528/ 20.8 681/ 26.6 823/ 32.4 850/ 33.5 1010/ 39.75 1208/ 47.6 1580/ 62.2
B (mm/ in) 166/ 6.5 172/ 6.8 243/ 9.6 260/ 10.2 330/ 13 393/ 15.5 515/ 20.3
C (mm/ in) 130/ 5.1 240/ 9.4
D (mm/ i n) 170/ 6.7 256/ 10.1 256/ 10.1 288/ 11.3 340/ 13.4 419/ 16.5 540/ 21.3
IMPORTANT
Install the cowls/ grids before mounting the tunnel to the SX thruster.
100mm
177mm
537mm
174mm
It is the installers responsibility
When installing Side-Power equipment to follow the outlined regulations/ classi cation rules (electrical/ mechanical) according to
international or special national regulations. Instructions in this guide cannot be guaranteed to comply with global electric/ mechanic
regulations/ classi cation rules.
To follow all health and safety laws in accordance with their local outlined regulations/ classi cation rules.
Before installation, it is important that the installer reads this guide to ensure necessary acquaintance with this product.
The recommendations made in this manual are guidelines ONLY, and Sleipner Motor AS (Side-Power) strongly recommend that
before installation, advice is obtained from a naval architect familiar with the particular vessel and regulations/ classi cations.
This manual is intended to support educated/ experienced staff and is therefore not suffi cient in all details for professional
installation. (NB: These instructions are only general instruction. If you are not skilled to do this work, please contact professional
installers for assistance.)
All electrical work must be done by a licensed professional.
Faulty installation of the tunnel, thruster or panel will render all warranty given by Sleipner Motor AS void. MC_0038
MC_0257
Thruster Installation Considerations and Precautions
EN
Before installation, it is important that the installer reads this guide to ensure necessary acquaintance with this product.
• The electromotor must be handled with care. Do not lift it by internal cable connections, main terminals or placed down on the driveshaft.
• The thruster power supply circuit must include the recommended sized fuse and a battery isolation switch.
• Never run the thruster out of water.
• It is important to follow the guidelines in this manual. Failure can result in severe damage to the thruster.
MC_0267
NEVER
Disassemble any part of the Ignition Protected stern thruster assembly. Tampering with the Ignition Protected stern thruster assembly or any attempt
to disassemble anything on this thruster assembly inside the boat can cause an explosion with severe consequences. If there is a problem with your
Ignition Protected stern thruster, please contact your dealer.
MC_0071
Installation Considerations and Precautions
EN
• Do not install the thruster in a position where you need to cut a stiff ener/ stringer/ support for the hull integrity without checking with the boat builder
this can be done safely.
• Contacts/ plugs or other joints in the control cables must be mounted so they remain dry at all times.
• We advise painting the gear house and propellers with antifouling. (NB: Do not paint the sealings/ rubber fi ttings or propeller shafts.)
• Do not nish the inside of the tunnel with a layer of gelcoat/ topcoat or similar. There is only room for a thin coat of primer and two layers of anti-fouling
between the tunnel and the propellers.
• keep installation within advised measurements. The entire surface is hard coated seawater resistant aluminium. Do not damage/penetrate the coat.
• The external stern thruster assembly and controller unit are ignition protected and can be installed in areas with the chance of explosive gases in
accordance to ISO 8846 and ABYC c1500. (Certi cation pending)
• Ensure that the external stern thruster assembly does not disturb the water fl ow under the hull. At higher speeds, if the thruster is installed to
low it can cause damage to the thruster and/ or add additional drag and unwanted water splashing.
• The recommended minimum tunnel depth from the water surface is 140mm (5,51‘) to the centre of tunnel diameter. Place the Thruster as deep as
possible for better performance and reduced noise.
• When installing the thruster ensure it does not foul existing equipment inside the boat like motor bedding etc.
• If able ensure that sterndrives/ trimtabs do not interfere with the water fl ow from the thruster as this can reduce the thrust eff ectiveness considerably.
We recommend the use of our Side-Power cowls to enhance the performance and allow installation in shallow draft boats. Side-Power cowls will also
minimise the eff ect if sterndrives/ trimtabs obstruct the thruster.
• Ensure there is enough space both inside and outside the transom of the boat and the thruster does not get in confl ict with existing equipment
inside the boat like steerage links etc. (NB: It is possible to mount the tunnel off set from the boat’s centre line if necessary.)
• Heat protection cut off is calculated from the thruster motor. To avoid cable overheating do not install place the volt cables from the thruster to the
control box near any heat sources.

10 5630 10 2020
-
SX35 & SX50
MC_0074
Grids or Cowls assembly
EN
1. Install the cowls or grids before mounting the new tunnel to the thruster. (NB: Remember the tunnel can not be removed without being
destroyed.)
2. Drill 4 holes in the mould marking on the tunnel.
3. Attach the cowls or grids with included bolts and washers. (NB: Ensure the appropriate twist of the cowl to direct water away from obstacles)
4. Attach the compleated tunnels.
For retro t
1. Remove propeller and the old tunnel. (NB: the tunnel is not designed to be removed non-destructively. Break off the snaplocks between the
tunnel half ends by pushing a small screwdriver through the holes from the outside.)
2. Follow the above installation process.
IMPORTANT
Cowls or Grids must be tted to each tunnel half before you assemble the tunnel to the thruster unit.
MG_0145
S
naplock from
o
ppositetunnel half
not be
owls or grid a new tunnel is required.
Detail #1
Drill 4 xØ5,5mmholes
BEFORETUNNELIS MOUNTED ONTHRUSTE
R!

11
5630 10 2020
-
SX35 & SX50
MC_0074
Grids or Cowls assembly
EN
1. Install the cowls or grids before mounting the new tunnel to the thruster. (NB: Remember the tunnel can not be removed without being
destroyed.)
2. Drill 4 holes in the mould marking on the tunnel.
3. Attach the cowls or grids with included bolts and washers. (NB: Ensure the appropriate twist of the cowl to direct water away from obstacles)
4. Attach the compleated tunnels.
For retro t
1. Remove propeller and the old tunnel. (NB: the tunnel is not designed to be removed non-destructively. Break off the snaplocks between the
tunnel half ends by pushing a small screwdriver through the holes from the outside.)
2. Follow the above installation process.
IMPORTANT
Cowls or Grids must be tted to each tunnel half before you assemble the tunnel to the thruster unit.
MG_0145
Snaplock from
oppositetunnel half
not be
owls or grid a new tunnel is required.
Detail #1
Drill 4 xØ5,5mmholes
BEFORETUNNELIS MOUNTED ONTHRUSTER!
MG_0112
Align two ends of the tunnel.
Push two tunnel
ends together.
Check snap lock
positions around the
tunnel.
Ensure top lips tabs
into the motor
inserts.
1
2
Tunnel Installation
EN
1. Ensure grids or cowls are installed if in use.
2. Connect both ends of the tunnel to the thruster motor. All hooks must be completely interlocked making the inside of the tunnel smooth. (NB:
Ensure tunnel moulding around the gear leg and tunnel top align.)
MC_0074
!Please refer to the graphic for special considerations relating to your model !
IMPORTANT
Ensure all snap-lock positions are correctly connected into place.

12 5630 10 2020
-
SX35 & SX50
SX Spacer
EN
Follow the installation of the SX thruster in the Motor Installation to step 3. see next page
1. De ne the location to install the thruster. (NB: Ensure the thruster does not protrude past the transom profi le on any side and there is no
obstruction to the thrusters water fl ow. Also, check internally the thruster will not obstruct any objects.)
2. Mark the locations of the three drill holes using the de ned measurements in this manual or from a template. (NB: Maximum hull thickness is
50mm including optional spacer or 150mm for extended hull thickness models.)
3. Drill main hole, then two support bolt holes. Clean the area from dust for installation of the thruster. (NB: Hull holes must be drilled fi rst before
attaching the spacer as the top support holes are larger than the spacers.)
---------
4. Drill out the two support bolt holes in the spacer.
5. Apply MS Polymer sealant or equal to the back surface face of the spacer.
6. Place the spacer to the hull.
Continue the installation of the SX thruster from step 4 in the Motor Installation.
MC_0074
!Please refer to the graphic for special considerations relating to your model !
IMPORTANT
If using the 50mm spacer ensure you have the extended tube SX model.
MG_0262
Hull
Hull
12mm
Spacer
Apply MS Polymer sealant or
equal to back surface face
50mm
Spacer
Drill
8.5 / 9 mm
Drill
8.5 / 9 mm
4 65 IMPORTANT
The spacer and hull have different hole
diameters for the support bolts. This is to
allow the compression rings to be
inserted into the hull only.
The spacer and hull for the main tube
have the same hole diameter so
compression rings can be inserted for
the total length of the hole.
Compression
ring
Compression
ring

13
5630 10 2020
-
SX35 & SX50
SX Spacer
EN
Follow the installation of the SX thruster in the Motor Installation to step 3. see next page
1. De ne the location to install the thruster. (NB: Ensure the thruster does not protrude past the transom profi le on any side and there is no
obstruction to the thrusters water fl ow. Also, check internally the thruster will not obstruct any objects.)
2. Mark the locations of the three drill holes using the de ned measurements in this manual or from a template. (NB: Maximum hull thickness is
50mm including optional spacer or 150mm for extended hull thickness models.)
3. Drill main hole, then two support bolt holes. Clean the area from dust for installation of the thruster. (NB: Hull holes must be drilled fi rst before
attaching the spacer as the top support holes are larger than the spacers.)
---------
4. Drill out the two support bolt holes in the spacer.
5. Apply MS Polymer sealant or equal to the back surface face of the spacer.
6. Place the spacer to the hull.
Continue the installation of the SX thruster from step 4 in the Motor Installation.
MC_0074
!Please refer to the graphic for special considerations relating to your model !
IMPORTANT
If using the 50mm spacer ensure you have the extended tube SX model.
MG_0262
Hull
Hull
12mm
Spacer
Apply MS Polymer sealant or
equal to back surface face
50mm
Spacer
Drill
8.5 / 9 mm
Drill
8.5 / 9 mm
4 65 IMPORTANT
The spacer and hull have different hole
diameters for the support bolts. This is to
allow the compression rings to be
inserted into the hull only.
The spacer and hull for the main tube
have the same hole diameter so
compression rings can be inserted for
the total length of the hole.
Compression
ring
Compression
ring
MG_0113
130 mm
5,12”
65 mm
2,56”
35,80 mm
1,41”
50 mm
1,97”
Drill holes in hull
Hole size
for hull
Sealant (MS Polymer)
Thruster and attachment bolts
18 mm
0,71”
All rings need
+15% compression
All rings need
+15% compression
Bolt and Washer
Hull thickness
Maximum hull thickness
is 50 mm or 150mm
Cover the
entire surface
1 - 3
6
7 - 8
4 - 5
Motor Installation
EN
1. De ne the location to install the thruster. (NB: Ensure the thruster does not protrude past the transom profi le on any side and there is no
obstruction to the thrusters water fl ow. Also, check internally the thruster will not obstruct any objects. Ensure cables internally do not
obstruct any objects. Do not place cables or control box close to high heat radiating parts EG. Turbo/ exhaust manifolds etc.)
2. Mark the locations of the three drill holes using the de ned measurements in this manual or from a template. (NB: Maximum hull thickness is
50mm including optional spacer or 150mm for extended hull thickness models.)
3. Drill main hole, then two support bolt holes. Clean the area from dust for installation of the thruster.
4. Install a bolt and washer to ensure top bolts contact surface area is level with the main tube. Temporally place the thruster through the holes to
ensure correct tting. Using the cable leads from the thruster de ne the location within the vessel for the installation of the control box. (NB: If
using a spacer the support bolt and washer are not required.)
5. Check the length of the compression rings. Compression rings must be longer than hull thickness to allow for compression (NB: Cut compression
sealants to length top achieve 15% compression.)
6. The thruster assembly must sit fl ush on the transom. Grind and sand the area if required to ensure a secure t. (NB: Use caution when grinding/
sanding surfaces as to not remove too much fi breglass.)
7. Ensure both bolts and washers to the support bars on the thruster are attached.
Apply a sealant (MS Polymer) to:
- the inside surface of the cutout holes on the hull.
-To the surface of the washer to the thread and
- in the recess of the main tube to the thread.
- 1cm deep inside all compression ring.
place all compression rings to bolt threads. (NB: Ensure ample sealant (MS Polymer) around the bolts and centre tube for a watertight
fi tting.)
8. Insert the thruster with compression rings into the hole.
9. Fasten the thruster
MC_0074
!Please refer to the graphic for special considerations relating to your model !

14 5630 10 2020
-
SX35 & SX50
MG_0114
BAT. -
5, 6 Nm
Control Box
hose clamp
Hose claps
BAT. +
5, 6 Nm
MOTOR CABLE -
5Nm
# SX35 CONTROL BOX
6 1232i
TORQUE 8Nm
MOTOR CABLE +
5Nm
BAT. -
5, 6 Nm
BAT. +
5, 6 Nm
MOTOR CABLE -
5Nm
# SX50 CONTROL BOX
6 1232i
TORQUE 8Nm
MOTOR CABLE +
5Nm
Control Box Installation
EN
The control box is the central component that can be connected to several other control panels. The control box can be mounted in any orientation,
preferably with cables facing down. (NB: The control box must be positioned within 0,75 meters from the thruster assembly with the provided
cables and not near any object that radiate high temperatures.)
1. De ne the location to install the control box. (NB: Ensure cables will not obstruct any objects.)
2. Mark the locations of the four drill holes and drill the holes.
3. Attach cables to the control box (NB: the control box internal components can be removed via its attachment screws for easier installation
using thick battery cables.)
4. Tighten hose clamps in order to ensure Ignition Protection as illustrated.
5. Fasten the control box to the hull.
MC_0075
!Please refer to the graphic for special considerations relating to your model !
IMPORTANT
It is the installers full responsibility to follow instructions and ensure total Ignition Protection.

15
5630 10 2020
-
SX35 & SX50
MG_0114
BAT. -
5, 6 Nm
Control Box
hose clamp
Hose claps
BAT. +
5, 6 Nm
MOTOR CABLE -
5Nm
# SX35 CONTROL BOX
6 1232i
TORQUE 8Nm
MOTOR CABLE +
5Nm
BAT. -
5, 6 Nm
BAT. +
5, 6 Nm
MOTOR CABLE -
5Nm
# SX50 CONTROL BOX
6 1232i
TORQUE 8Nm
MOTOR CABLE +
5Nm
Control Box Installation
EN
The control box is the central component that can be connected to several other control panels. The control box can be mounted in any orientation,
preferably with cables facing down. (NB: The control box must be positioned within 0,75 meters from the thruster assembly with the provided
cables and not near any object that radiate high temperatures.)
1. De ne the location to install the control box. (NB: Ensure cables will not obstruct any objects.)
2. Mark the locations of the four drill holes and drill the holes.
3. Attach cables to the control box (NB: the control box internal components can be removed via its attachment screws for easier installation
using thick battery cables.)
4. Tighten hose clamps in order to ensure Ignition Protection as illustrated.
5. Fasten the control box to the hull.
MC_0075
!Please refer to the graphic for special considerations relating to your model !
IMPORTANT
It is the installers full responsibility to follow instructions and ensure total Ignition Protection.
MC_0035
Thruster Electrical Installation
EN
!Please refer to the graphic for special considerations relating to your model !
WARNING
Check the following with the main switch is set to off :
After all electrical connections have been completed check with an ohm meter that there is no electrical connection between
1. electro-motor fl ange and the positive terminal on the motor
2. electro-motor fl ange and the battery negative terminal on the motor
If unsure contact skilled personnel.
1. Information of electrical table. see next page
- All power cable lengths represent the total length of the combined (+) and (-) cables.
- Battery capacity is stated as minimum cold crank capacity, (CCA).
- Use slow blow rated fuses to hold stated Amp-Draw for min. 5 minutes.
- Consider the AMP hours (Ah) for your speci c duty cycle.
2. Use appropriate sized cables and batteries with high cranking capacity to feed the thruster. The actual voltage at the motor while running the
thruster decides the motors output RPM and thrust. Use larger cables and stronger batteries for better results.
- See electrical speci cations for advised minimum cables and batteries (CCA).
3. Connect the battery supply to the control unit (PPC).
- Install a main manual/ automatic switch from the positive lead terminal on the battery PPC unit). The main switch must be accessible to turn
off the thruster independently from the rest of the electrical operation of the vessel when not onboard or in emergencies. (NB: It is advised
to install a fuse on the positive cable for protection against short-circuiting of the main cables. The fuse should ensure no voltage
decrease, slow-blow and sized to take the amperage draw for at least 5 minutes.)
- A circuit breaker can be used instead of the fuse and main power switch If the functionality is the same.
(NB: For Ignition Protected installations remember to use ignition protected fuses and switches if fi tted in areas that require this feature.
Ensure to follow your national regulations)
5. Cable lugs must have adequate electrical and mechanical isolation and tted with cable lug covers.
6. Fasten cables to the required torque.
MG_0039
Control Cables
Minimum and recommended cable dimensions can be identical due to safety margins and cable heat considerations for short cable lenghts.
* Minimum or recommended cable cross section in mm2
To control panel(s)/remote.
A1
A2
Temp switch NC
NTC
B+
B-
CONTROLLER
++
*C
BLUE HOSE
(900mm/ 35”)
THRUSTER
(MUST BE IGNITION PROTECTED IF
LOCATED IN IP REQUESTED AREA)
Automatic MAIN
SWITCH
THRUSTER
BATTERY
12V B-
B+
*D
MAIN FUSE
CONTROLLER CONNECTIONS:
<<B+>>: Power supply pos from thruster battery/ Main switch/ Main fuse
<<B->>: Power supply neg from thruster battery
2 Motor cables from thruster
4 wires from thruster overtemp switch
2 Control cables from control panel(s)/ remote

16 5630 10 2020
-
SX35 & SX50
MG_0320
Thruster Electrical Installation
EN
A1
A2
Temp switch NC
NTC
Temp switch NC
Temp switch NC
(BLUE HOSE)
# SX50 CONTROL BOX
# SX35 CONTROL BOX
B-B+
Tighten to
5, 6 NM
4,13 lb/ft
Blue Hose
Blue Hose
Tighten to
5 NM
3,69 lb/ft
Tighten to
5 NM
3,69 lb/ft
Tighten to
5, 6 NM
4,13 lb/ft
Tighten to
5 NM
3,69 lb/ft
Tighten to
5 NM
3,69 lb/ft
A1
A1
A2
A2
B+
B-
(BLUE HOSE)
B-B+
*Only used for PRO systems
Control Cables

17
5630 10 2020
-
SX35 & SX50
MG_0320
Thruster Electrical Installation
EN
A1
A2
Temp switch NC
NTC
Temp switch NC
Temp switch NC
(BLUE HOSE)
# SX50 CONTROL BOX
# SX35 CONTROL BOX
B-B+
Tighten to
5, 6 NM
4,13 lb/ft
Blue Hose
Blue Hose
Tighten to
5 NM
3,69 lb/ft
Tighten to
5 NM
3,69 lb/ft
Tighten to
5, 6 NM
4,13 lb/ft
Tighten to
5 NM
3,69 lb/ft
Tighten to
5 NM
3,69 lb/ft
A1
A1
A2
A2
B+
B-
(BLUE HOSE)
B-B+
*Only used for PRO systems
Control Cables
Electrical Speci cations
EN MC_0077
Model Size System
Voltage
Nominal
current
draw
Min. battery
CCA Rec. fuse
<7m total + & - 7-14m total + & - 15-21m total + & - 22-28m total + & - 28-35m total + & - 36-45m total + & -
Min. Rec. Min. Rec. Min. Rec. Min. Rec. Min. Rec. Min. Rec.
AWG 3 2 1/0 1/0 2/0 2/0 3/0 3/0 4/0 4/0 2 x 2/0 2 x 2/0
*35/140 12 V 245 A
DIN: 200
SAE: 380
EN: 330
ANL 150
mm2 35 50 50 70 70 95 95 120 120 2 x 70 2 x 70 2 x 95
AWG 2 1/0 1/0 2/0 2/0 3/0 3/0 4/0 4/0 2 x 2/0 2 x 2/0 2 x 3/0
*50/1400
12 V 370 A
DIN: 350
SAE: 665
EN: 600
ANL 325
mm2 50 50 70 95 120 2 x 70 2 x 70 2 x 95 2 x 95 2 x 120 2 x 120 2 x 120
AWG 1/0 1/0 2/0 3/0 4/0 2 x 2/0 2 x 2/0 2 x 3/0 2 x 3/0 2 x 4/0 2 x 4/0 2 x 4/0
24 V 170 A
DIN: 175
SAE :332
EN: 280
ANL 150
mm2 25 25 25 35 35 50 35 50 50 70 70 70
AWG 3 3 3 2 2 1/0 2 1/0 1/0 2/0 2/0 2/0

18 5630 10 2020
-
SX35 & SX50
Control Panel Cable Installation
EN
• All Sidepower control panels can be used in any combination.
• All control panels can be installed using:
• Y-connectors - for standard on/off
• T-connectors - for S-link proportional power system.
(NB: If two or more control panels are operated at the same time in opposite directions, the electronic control box will stop the thruster until
it receives a single signal or thrust in one direction.)
• Sidepower on/off equipment it is entirely “plug & play” and require no additional con guration setup.
See the Control pannel manual for more information.
MC_0041
!Please refer to the graphic for special considerations relating to your model !
MG_0115
Thuster
Motor
Automatic Main switch
Manual Main switch
Ext. cable
5-lead
Y cable
5-lead
* 5 LEAD EXTENSION
CABLES
* 4 OR 5 LEAD EXTENSION
CABLES
Ext. cable
5-lead
Thuster
Motor Ext. cable
4- or 5-lead
Y cable
4- or 5-lead
Ext. cable
4- or 5-lead
Option: Automatic main switch. connects the battery to
the thruster. Operated from the control panel(s).
Requires 5-lead control cables.

19
5630 10 2020
-
SX35 & SX50
Control Panel Cable Installation
EN
• All Sidepower control panels can be used in any combination.
• All control panels can be installed using:
• Y-connectors - for standard on/off
• T-connectors - for S-link proportional power system.
(NB: If two or more control panels are operated at the same time in opposite directions, the electronic control box will stop the thruster until
it receives a single signal or thrust in one direction.)
• Sidepower on/off equipment it is entirely “plug & play” and require no additional con guration setup.
See the Control pannel manual for more information.
MC_0041
!Please refer to the graphic for special considerations relating to your model !
MG_0115
Thuster
Motor
Automatic Main switch
Manual Main switch
Ext. cable
5-lead
Y cable
5-lead
* 5 LEAD EXTENSION
CABLES
* 4 OR 5 LEAD EXTENSION
CABLES
Ext. cable
5-lead
Thuster
Motor Ext. cable
4- or 5-lead
Y cable
4- or 5-lead
Ext. cable
4- or 5-lead
Option: Automatic main switch. connects the battery to
the thruster. Operated from the control panel(s).
Requires 5-lead control cables.
Control Panel Installation
EN
Find a suitable location for the control panel where it does not obstruct or is obstructed by other devices. Install the control panel on a fl at surface where
it is easy to use.
1. Use the supplied cut-out template to mark the area to remove on your control dash.
2. Cut out the area per template for the control panel. (NB: If the front surface around your cut out is jagged or chipped, use a sealant
to assist the gasket.)
3. Place the gasket to the back face of the panel
4. Plug cables into the connectors at the rear of the control panel.
5. Insert the control panel in place and fasten screws.
6. Insert the control panels covering caps.
MC_0042
!Please refer to the graphic for special considerations relating to your model !
MG_0026
(4) COVERING CAPS
Example of control
panels
(4) COVERING CAPS
COVERING CAP
GASKET
CABLES
CABLES
CABLES
GASKET
GASKET
(4) SCREWS
(4) SCREWS
(4) SCREWS

20 5630 10 2020
-
SX35 & SX50
MC_0081
Pre-delivery Checklist
EN
�.......... Propeller is fastened correctly to the shaft.
�.......... Propeller turns freely in tunnel.
�.......... Primer and anti-fouling have been applied to the gearhouse and propeller but NOT on the
anode or the gearhouse lid where the propeller is fastened.
�.......... Correct drive direction as per controlpanel.
�.......... The bolts holding the thruster are tightened correctly.
�.......... The bolts holding the motor to its bracket are tightened correctly.
�.......... All electrical connections are clean, dry and tight, and the correct cable, fuse and main
switch size.
�.......... No water leakage around hull penetrated studs
�.......... Check that there is no electrical connection between the electromotor body and positive
terminal on the motor, and between the electromotor body and the negative (A1) terminal on
the motor with an ohm meter.
The thruster has been installed as per the instructions in this manual and all points in checklist above have been controlled.
Signed: .........................................................................................
Date: .............................................................................................
Extra pre-delivery tests by installer / yard who does not use other quality control systems !
Thruster type: ................................................................................................................................................................................................
Serial number:...............................................................................................................................................................................................
Date of delivery:.............................................................................................................................................................................................
Correct drive direction as per controlpanel: ..................................................................................................................................................
The compartment for the thruster has been isolated from general bilge water and has no obvious or suspected risks for fl ooding:
......................................................................................................................................................................................................................
......................................................................................................................................................................................................................
......................................................................................................................................................................................................................
Other comments by installer: ........................................................................................................................................................................
.......................................................................................................................................................................................................................
.......................................................................................................................................................................................................................
......................................................................................................................................................................................................................
Other manuals for SIDE-POWER SX35
1
This manual suits for next models
3
Table of contents
Popular Controllers manuals by other brands
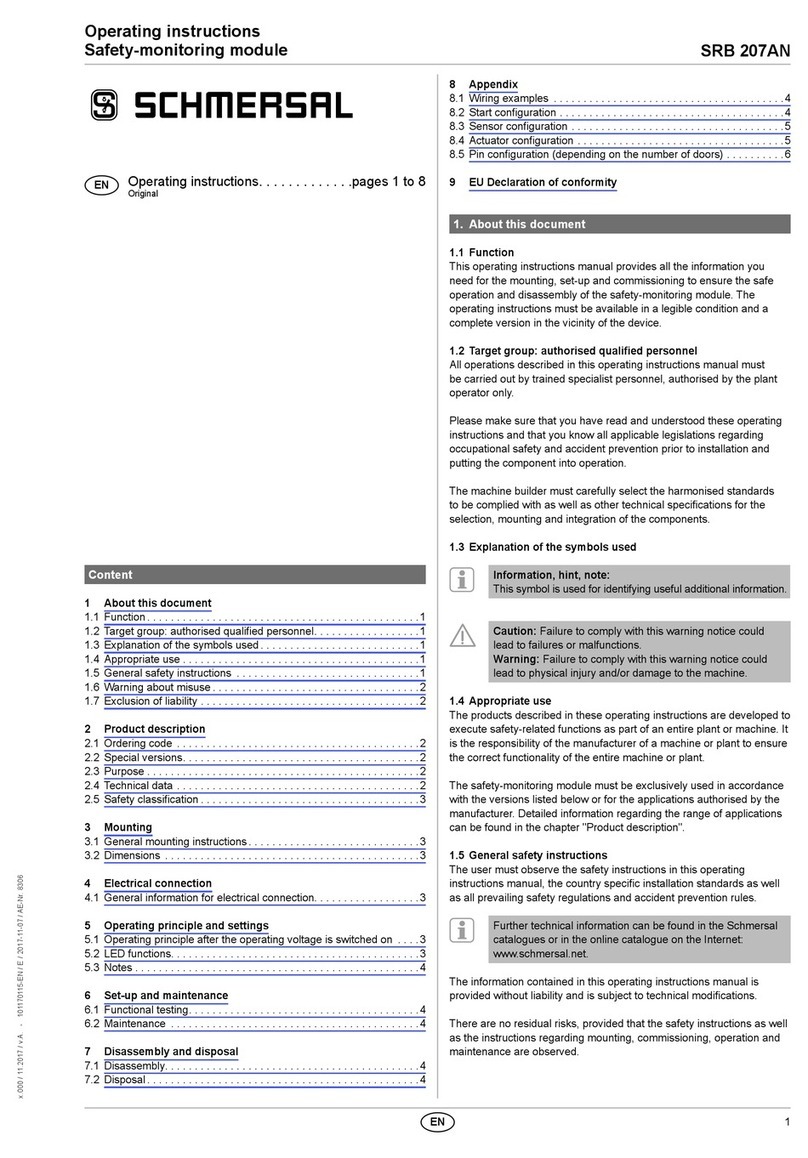
schmersal
schmersal SRB 207AN operating instructions
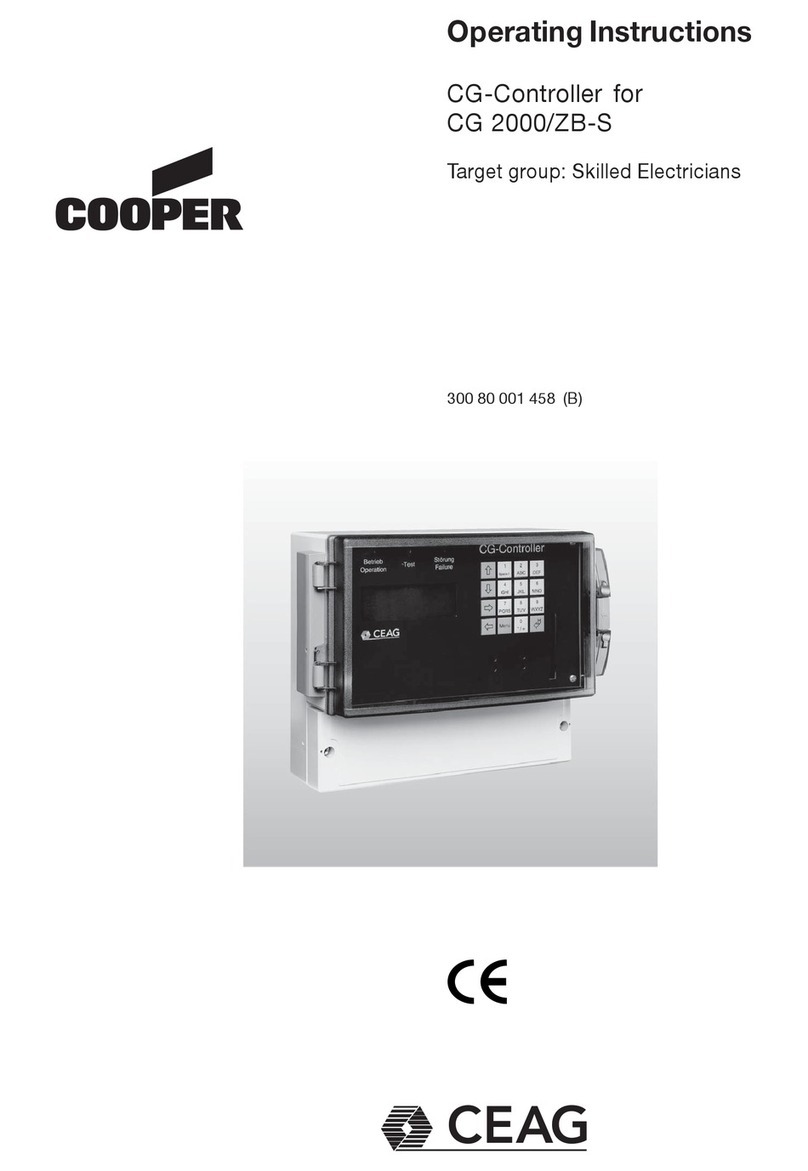
CEAG
CEAG COOPER CG-Controller operating instructions
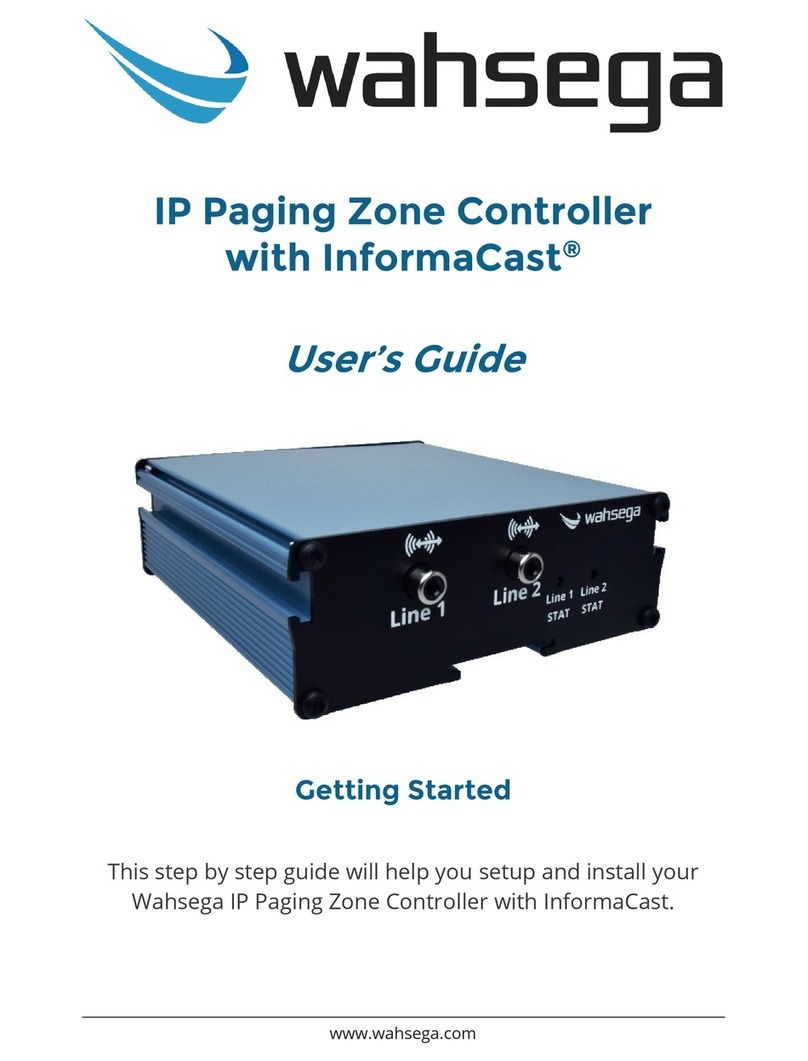
Wahsega
Wahsega InformaCast user guide
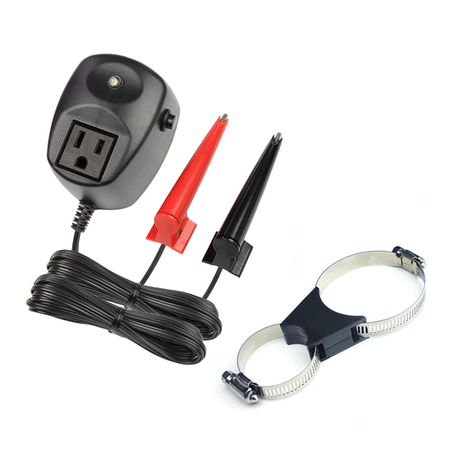
HydroCheck
HydroCheck HC6000v2 Hi-Lo quick start guide
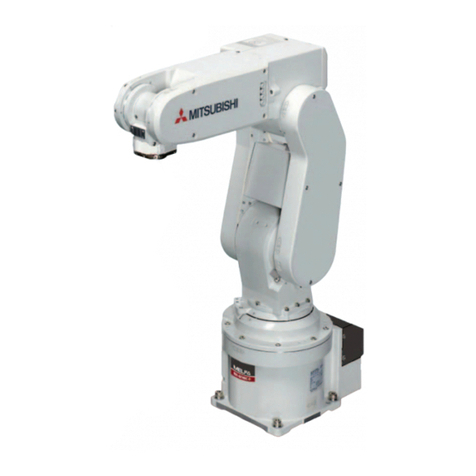
Mitsubishi
Mitsubishi MELFA SQ Series Special Specifications Manual
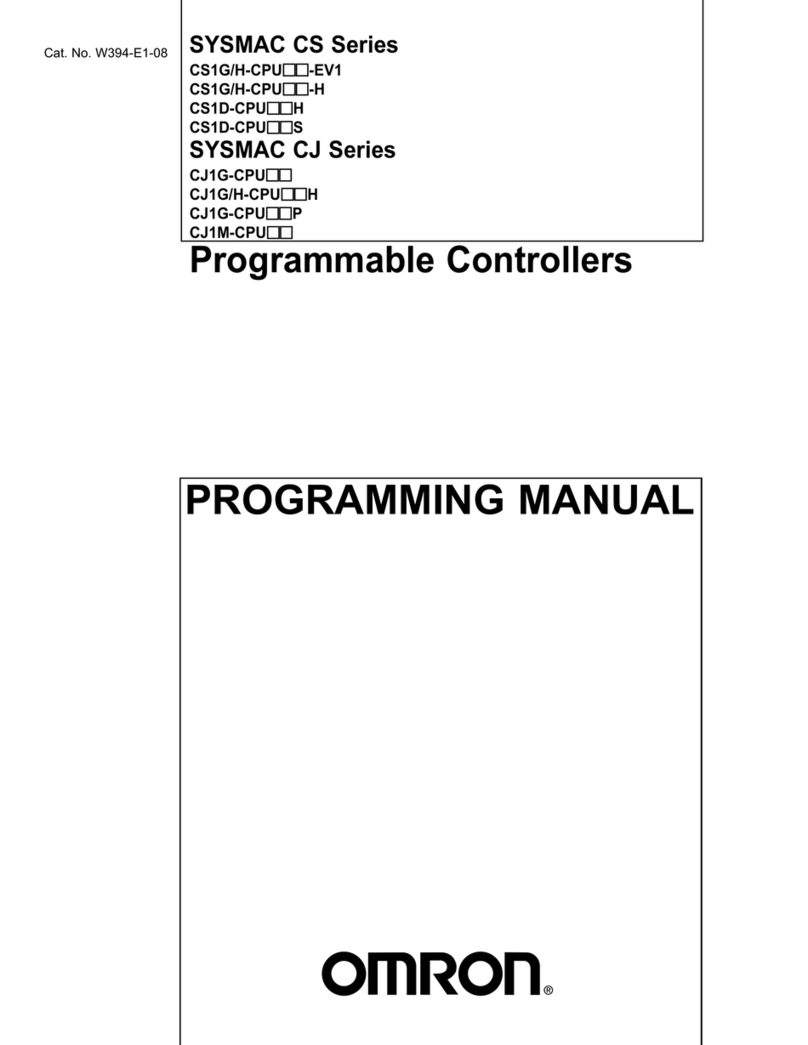
Omron
Omron CS1G/H-CPUxx-EV1 Programming manual