Solutions UWT NivoGuide 8100 User manual

NivoGuide® 8100
Two-wire 4 … 20 mA/HART
Coax probe
With SIL qualication
TDR sensor for continuous level and interface
measurement of liquids
Technical information / Instruction manual
Document ID: 61893

2
NivoGuide® 8100 • Two-wire 4 … 20 mA/HART
Contents
61893-EN-190911
Contents
1 About this document ............................................................................................................... 4
1.1 Function ........................................................................................................................... 4
1.2 Target group ..................................................................................................................... 4
1.3 Symbols used................................................................................................................... 4
2 For your safety ......................................................................................................................... 5
2.1 Authorised personnel ....................................................................................................... 5
2.2 Appropriate use ................................................................................................................ 5
2.3 Warning about incorrect use ............................................................................................. 5
2.4 General safety instructions ............................................................................................... 5
2.5 EU conformity ................................................................................................................... 6
2.6 SIL qualication according to IEC 61508 .......................................................................... 6
2.7 NAMUR recommendations .............................................................................................. 6
2.8 Installation and operation in the USA and Canada ........................................................... 6
3 Product description ................................................................................................................. 8
3.1 Conguration .................................................................................................................... 8
3.2 Principle of operation........................................................................................................ 9
3.3 Packaging, transport and storage ................................................................................... 11
3.4 Accessories.................................................................................................................... 11
4 Mounting................................................................................................................................. 12
4.1 General instructions ....................................................................................................... 12
4.2 Mounting instructions ..................................................................................................... 13
5 Connecting to power supply................................................................................................. 16
5.1 Preparing the connection ............................................................................................... 16
5.2 Connecting ..................................................................................................................... 17
5.3 Wiring plan, single chamber housing.............................................................................. 18
5.4 Wiring plan, double chamber housing ............................................................................ 19
6 Functional safety (SIL) .......................................................................................................... 21
6.1 Objective ........................................................................................................................ 21
6.2 SIL qualication .............................................................................................................. 21
6.3 Application area ............................................................................................................. 21
6.4 Safety concept of the parameterization .......................................................................... 22
6.5 Setup process ................................................................................................................ 23
7 Set up with the display and adjustment module ................................................................ 26
7.1 Insert display and adjustment module ............................................................................ 26
7.2 Adjustment system ......................................................................................................... 27
7.3 Parameter adjustment - Extended adjustment................................................................ 29
7.4 Saving the parameterisation data ................................................................................... 49
8 Diagnostics and servicing .................................................................................................... 50
8.1 Maintenance .................................................................................................................. 50
8.2 Diagnosis memory ......................................................................................................... 50
8.3 Status messages ............................................................................................................ 50
8.4 Rectify faults ................................................................................................................... 53
8.5 Exchanging the electronics module ................................................................................ 56
8.6 How to proceed if a repair is necessary .......................................................................... 57
9 Dismount................................................................................................................................. 58

3
NivoGuide® 8100 • Two-wire 4 … 20 mA/HART
Contents
61893-EN-190911
9.1 Dismounting steps.......................................................................................................... 58
9.2 Disposal ......................................................................................................................... 58
10 Supplement ............................................................................................................................ 59
10.1 Technical data ................................................................................................................ 59
10.2 Dimensions .................................................................................................................... 68
10.3 Trademark ...................................................................................................................... 71
Safety instructions for Ex areas
Take note of the Ex specic safety instructions for Ex applications.
These instructions are attached as documents to each instrument
with Ex approval and are part of the operating instructions.
Editing status: 2019-07-30

4
NivoGuide® 8100 • Two-wire 4 … 20 mA/HART
1 About this document
61893-EN-190911
1 About this document
1.1 Function
This operating instructions provides all the information you need for
mounting, connection and setup as well as important instructions for
maintenance, fault rectication, the exchange of parts and the safety
of the user. Please read this information before putting the instrument
into operation and keep this manual accessible in the immediate
vicinity of the device.
1.2 Target group
This operating instructions manual is directed to trained personnel.
The contents of this manual must be made available to the qualied
personnel and implemented.
1.3 Symbols used
Information, note, tip: This symbol indicates helpful additional infor-
mation and tips for successful work.
Note: This symbol indicates notes to prevent failures, malfunctions,
damage to devices or plants.
Caution: Non-observance of the information marked with this symbol
may result in personal injury.
Warning: Non-observance of the information marked with this symbol
may result in serious or fatal personal injury.
Danger: Non-observance of the information marked with this symbol
results in serious or fatal personal injury.
Ex applications
This symbol indicates special instructions for Ex applications.
• List
The dot set in front indicates a list with no implied sequence.
→ Action
This arrow indicates a single action.
1 Sequence of actions
Numbers set in front indicate successive steps in a procedure.
Battery disposal
This symbol indicates special information about the disposal of bat-
teries and accumulators.

5
NivoGuide® 8100 • Two-wire 4 … 20 mA/HART
2 For your safety
61893-EN-190911
2 For your safety
2.1 Authorised personnel
All operations described in this documentation must be carried out
only by trained, qualied personnel authorised by the plant operator.
During work on and with the device, the required personal protective
equipment must always be worn.
2.2 Appropriate use
NivoGuide 8100 is a sensor for continuous level measurement.
You can nd detailed information about the area of application in
chapter "Product description".
Operational reliability is ensured only if the instrument is properly
used according to the specications in the operating instructions
manual as well as possible supplementary instructions.
2.3 Warning about incorrect use
Inappropriate or incorrect use of this product can give rise to applica-
tion-specic hazards, e.g. vessel overll through incorrect mounting
or adjustment. Damage to property and persons or environmental
contamination can result. Also, the protective characteristics of the
instrument can be impaired.
2.4 General safety instructions
This is a state-of-the-art instrument complying with all prevailing
regulations and directives. The instrument must only be operated in a
technically awless and reliable condition. The operator is responsi-
ble for the trouble-free operation of the instrument. When measuring
aggressive or corrosive media that can cause a dangerous situation
if the instrument malfunctions, the operator has to implement suitable
measures to make sure the instrument is functioning properly.
During the entire duration of use, the user is obliged to determine the
compliance of the necessary occupational safety measures with the
current valid rules and regulations and also take note of new regula-
tions.
The safety instructions in this operating instructions manual, the na-
tional installation standards as well as the valid safety regulations and
accident prevention rules must be observed by the user.
For safety and warranty reasons, any invasive work on the device
beyond that described in the operating instructions manual may be
carried out only by personnel authorised by the manufacturer. Arbi-
trary conversions or modications are explicitly forbidden. For safety
reasons, only the accessory specied by the manufacturer must be
used.
To avoid any danger, the safety approval markings and safety tips on
the device must also be observed and their meaning read in this oper-
ating instructions manual.

6
NivoGuide® 8100 • Two-wire 4 … 20 mA/HART
2 For your safety
61893-EN-190911
2.5 EU conformity
The device fulls the legal requirements of the applicable EU direc-
tives. By axing the CE marking, we conrm the conformity of the
instrument with these directives.
The EU conformity declaration can be found on our homepage.
Electromagnetic compatibility
Instruments in four-wire or Ex-d-ia version are designed for use in an
industrial environment. Nevertheless, electromagnetic interference
from electrical conductors and radiated emissions must be taken into
account, as is usual with class A instruments according to EN 61326-
1. If the instrument is used in a dierent environment, the electromag-
netic compatibility to other instruments must be ensured by suitable
measures.
2.6 SILqualicationaccordingtoIEC61508
The Safety Integrity Level (SIL) of an electronic system is used to as-
sess the reliability of integrated safety functions.
For detailed specication of the safety requirements, multiple SIL
levels are specied according to safety standard IEC 61508. You can
nd detailed information in chapter "Functional safety (SIL)" of the
operating instructions.
The instrument meets the specications of IEC 61508: 2010 (Edi-
tion 2). It is qualied for single-channel operation up to SIL2. The
instrument can be used homogeneously redundant up to SIL3 in
multi-channel architecture with HFT 1.
2.7 NAMUR recommendations
NAMUR is the automation technology user association in the process
industry in Germany. The published NAMUR recommendations are
accepted as the standard in eld instrumentation.
The device fulls the requirements of the following NAMUR recom-
mendations:
• NE 21 – Electromagnetic compatibility of equipment
• NE 43 – Signal level for fault information from measuring transduc-
ers
• NE 53 – Compatibility of eld devices and display/adjustment
components
• NE 107 – Self-monitoring and diagnosis of eld devices
For further information see www.namur.de.
2.8 Installation and operation in the USA and
Canada
This information is only valid for USA and Canada. Hence the follow-
ing text is only available in the English language.
Installations in the US shall comply with the relevant requirements of
the National Electrical Code (ANSI/NFPA 70).

7
NivoGuide® 8100 • Two-wire 4 … 20 mA/HART
2 For your safety
61893-EN-190911
Installations in Canada shall comply with the relevant requirements of
the Canadian Electrical Code
A Class 2 power supply unit has to be used for the installation in the
USA and Canada.

8
NivoGuide® 8100 • Two-wire 4 … 20 mA/HART
3 Product description
61893-EN-190911
3 Product description
3.1 Conguration
The type label contains the most important data for identication and
use of the instrument:
2
1
12
13
14
15
11
10
5
3
6
4
7
8
9
Fig. 1: Layout of the type label (example)
1 Instrument type
2 Product code
3 Approvals
4 Power supply and signal output, electronics
5 Protection rating
6 Probe length (measurement accuracy optional)
7 Process and ambient temperature, process pressure
8 Material wetted parts
9 Order number
10 Serial number of the instrument
11 Symbol of the device protection class
12 Reminder to observe the instrument documentation
13 NotiedauthorityforCEmarking
14 Approval directives
15 MarkingofthesafetyfunctioninSIS
This operating instructions manual applies to the following instrument
versions:
• Hardware from 1.0.0
• Software from 1.2.0
• DTM from version 1.67.2
The instrument and the electronics version can be determined via the
product code on the type label as well as on the electronics.
• Standard electronics: Type FX80H.-SIL
The scope of delivery encompasses:
• Sensor
• Optional accessory
• Documentation
Type label
Scope of this operating
instructions
Versions
Scope of delivery

9
NivoGuide® 8100 • Two-wire 4 … 20 mA/HART
3 Product description
61893-EN-190911
– Quick setup guide NivoGuide 8100
– Instructions for optional instrument features
– Ex-specic "Safety instructions" (with Ex versions)
– If necessary, further certicates
Information:
Optional instrument features are also described in this operating
instructions manual. The respective scope of delivery results from the
order specication.
3.2 Principle of operation
The NivoGuide 8100 is a level sensor with coax probe for continuous
level or interface measurement, suitable for applications in liquids.
Due to the qualication up to SIL2 or homogeneous redundant up to
SIL3 (IEC 61508) the NivoGuide 8100 is suitable for the use in safety-
instrumented systems (SIS).
The safety function (SIF) can be a monitoring of the max. or min. level
or a combination of both.
High frequency microwave pulses are guided along a steel cable or
a rod. Upon reaching the product surface, the microwave pulses are
reected. The running time is evaluated by the instrument and output
as level.
d
h
1
Fig. 2: Level measurement
1 Sensorreferenceplane(sealsurfaceoftheprocesstting)
d Distance to the level
h Height - Level
High frequency microwave impulses are guided along a steel cable or
rod. Upon reaching the product surface, a part of the microwave im-
pulses is reected. The other part passes through the upper product
and is reected by the interface. The running times to the two product
layers are processed by the instrument.
Application area
Functional principle -
level measurement
Functional principle - in-
terface measurement

10
NivoGuide® 8100 • Two-wire 4 … 20 mA/HART
3 Product description
61893-EN-190911
TS
d1
h1
h2
d2
1
L2
L1
L3
Fig. 3: Interface measurement
1 Sensorreferenceplane(sealsurfaceoftheprocesstting)
d1 Distance to the interface
d2 Distance to the level
TS Thicknessoftheuppermedium(d1-d2)
h1 Height - Interface
h2 Height - Level
L1 Lower medium
L2 Upper medium
L3 Gas phase
Upper medium (L2)
• The upper medium must not be conductive
• The dielectric constant of the upper medium or the actual distance
to the interface must be known (input required). Min. dielectric
constant: 1.6.
• The composition of the upper medium must be stable, no varying
products or mixtures
• The upper medium must be homogeneous, no stratications
within the medium
• Min. thickness of the upper medium 50 mm (1.97 in)
• Clear separation from the lower medium, emulsion phase or detri-
tus layer max. 50 mm (1.97 in)
• If possible, no foam on the surface
Lower medium (L1)
• The dielectric constant must be 10 higher than the dielectric
constant of the upper medium, preferably electrically conductive.
Example: upper medium dielectric constant 2, lower medium at
least dielectric constant 12.
Gas phase (L3)
• Air or gas mixture
• Gas phase - dependent on the application, gas phase does not
always exist (d2 = 0)
Prerequisites for inter-
face measurement

11
NivoGuide® 8100 • Two-wire 4 … 20 mA/HART
3 Product description
61893-EN-190911
The instrument is always preset to the application "Level measure-
ment".
For the interface measurement, you can select the requested output
signal with the setup.
3.3 Packaging, transport and storage
Your instrument was protected by packaging during transport. Its
capacity to handle normal loads during transport is assured by a test
based on ISO 4180.
The packaging consists of environment-friendly, recyclable card-
board. For special versions, PE foam or PE foil is also used. Dispose
of the packaging material via specialised recycling companies.
Transport must be carried out in due consideration of the notes on the
transport packaging. Nonobservance of these instructions can cause
damage to the device.
The delivery must be checked for completeness and possible transit
damage immediately at receipt. Ascertained transit damage or con-
cealed defects must be appropriately dealt with.
Up to the time of installation, the packages must be left closed and
stored according to the orientation and storage markings on the
outside.
Unless otherwise indicated, the packages must be stored only under
the following conditions:
• Not in the open
• Dry and dust free
• Not exposed to corrosive media
• Protected against solar radiation
• Avoiding mechanical shock and vibration
• Storage and transport temperature see chapter "Supplement -
Technical data - Ambient conditions"
• Relative humidity 20 … 85 %
With instrument weights of more than 18 kg (39.68 lbs) suitable and
approved equipment must be used for lifting and carrying.
3.4 Accessories
The instructions for the listed accessories can be found in the down-
load area on our homepage.
The display and adjustment module is used for measured value indi-
cation, adjustment and diagnosis.
Screwed anges are available in dierent versions according to the
following standards: DIN 2501, EN 1092-1, BS 10, ASME B 16.5,
JIS B 2210-1984, GOST 12821-80.
Output signal
Packaging
Transport
Transport inspection
Storage
Storage and transport
temperature
Lifting and carrying
Display and adjustment
module
Flanges

12
NivoGuide® 8100 • Two-wire 4 … 20 mA/HART
4 Mounting
61893-EN-190911
4 Mounting
4.1 General instructions
On devices with a threaded tting, the hexagon on the process tting
must be tightened with a suitable wrench.
See chapter "Dimensions" for wrench size.
Warning:
The housing or the electrical connection may not be used for screw-
ing in! Depending on the device version, tightening can cause dam-
age, e. g. to the rotation mechanism of the housing.
Protect your instrument against moisture ingress through the following
measures:
• Use a suitable connection cable (see chapter "Connectingto
power supply")
• Tighten the cable gland or plug connector
• Lead the connection cable downward in front of the cable entry or
plug connector
This applies mainly to outdoor installations, in areas where high
humidity is expected (e.g. through cleaning processes) and on cooled
or heated vessels.
Note:
Make sure that the degree of contamination specied in chapter
"Technical data" meets the existing ambient conditions.
Note:
Make sure that during installation or maintenance no moisture or dirt
can get inside the instrument.
To maintain the housing protection, make sure that the housing lid is
closed during operation and locked, if necessary.
Metric threads
In the case of instrument housings with metric thread, the cable
glands are screwed in at the factory. They are sealed with plastic
plugs as transport protection.
You have to remove these plugs before electrical connection.
NPT thread
In the case of instrument housings with self-sealing NPT threads, it is
not possible to have the cable entries screwed in at the factory. The
free openings for the cable glands are therefore covered with red dust
protection caps as transport protection. The dust protection caps do
not provide sucient protection against moisture.
Prior to setup you have to replace these protective caps with ap-
proved cable glands or close the openings with suitable blind plugs.
Note:
For safety reasons, the instrument must only be operated within the
permissible process conditions. You can nd detailed information on
Screwing in
Protection against mois-
ture
Cable glands
Process conditions

13
NivoGuide® 8100 • Two-wire 4 … 20 mA/HART
4 Mounting
61893-EN-190911
the process conditions in chapter "Technical data" of the operating
instructions or on the type label.
Make sure before mounting that all parts of the instrument exposed to
the process are suitable for the existing process conditions.
These are mainly:
• Active measuring component
• Process tting
• Process seal
Process conditions in particular are:
• Process pressure
• Process temperature
• Chemical properties of the medium
• Abrasion and mechanical inuences
4.2 Mounting instructions
In vessels with conical bottom it can be advantageous to mount the
sensor in the center of the vessel, as measurement is then possible
nearly down to the lowest point of the bottom. Keep in mind that
measurement all the way down to the tip of the probe may not be pos-
sible. The exact value of the min. distance (lower dead zone) is stated
in chapter "Technical data".
Fig. 4: Vessel with conical bottom
Before beginning the welding work, remove the electronics module
from the sensor. By doing this, you avoid damage to the electronics
through inductive coupling.
Do not mount the instruments in or above the lling stream. Make sure
that you detect the product surface, not the inowing product.
Installation position
Welding work
Inowingmedium

14
NivoGuide® 8100 • Two-wire 4 … 20 mA/HART
4 Mounting
61893-EN-190911
Fig.5:Mountingofthesensorwithinowingmedium
The reference plane for the measuring range of the sensors is the
sealing surface of the thread or ange.
Keep in mind that a min. distance must be maintained below the refer-
ence plane and possibly also at the end of the probe - measurement
in these areas is not possible (dead zone). These dead zones are
listed in chapter "Technical data". Keep in mind for the adjustment that
the default setting for the measuring range refers to water.
The process tting must be sealed if there is gauge or low pressure in
the vessel. Before use, check if the seal material is resistant against
the measured product and the process temperature.
The max. permissible pressure is specied in chapter "Technical
data" or on the type label of the sensor.
If there is a risk of the coaxial probe touching the vessel wall during
operation due to product movements or agitators, etc., the measuring
probe should be securely xed.
Avoid undened vessel connections, i.e. the connection must be
either grounded reliably or isolated reliably. Any undened change of
this condition can lead to measurement errors.
If there is a danger of the coaxial probe touching the vessel wall, then
the probe must be fastened at the bottom end.
Keep in mind that measurement is not possible below the fastening
point.
Measuring range
Pressure
Fasten

15
NivoGuide® 8100 • Two-wire 4 … 20 mA/HART
4 Mounting
61893-EN-190911
1
2
1
2
Fig. 6: Fasten the probe
1 Coaxprobe
2 Retaining sleeve

16
NivoGuide® 8100 • Two-wire 4 … 20 mA/HART
5 Connecting to power supply
61893-EN-190911
5 Connecting to power supply
5.1 Preparing the connection
Always keep in mind the following safety instructions:
• Carry out electrical connection by trained, qualied personnel
authorised by the plant operator
• If overvoltage surges are expected, overvoltage arresters should
be installed
Warning:
Only connect or disconnect in de-energized state.
Power supply and current signal are carried on the same two-wire
cable. The operating voltage can dier depending on the instrument
version.
The data for power supply are specied in chapter "Technical data".
Provide a reliable separation between the supply circuit and the
mains circuits according to DIN EN 61140 VDE 0140-1.
Power the instrument via an energy-limited circuit acc. to IEC 61010-
1, e.g. via Class 2 power supply unit.
Keep in mind the following additional factors that inuence the operat-
ing voltage:
• Lower output voltage of the power supply unit under nominal load
(e.g. with a sensor current of 20.5 mA or 22 mA in case of fault)
• Inuence of additional instruments in the circuit (see load values in
chapter "Technical data")
The instrument is connected with standard two-wire cable without
screen. If electromagnetic interference is expected which is above the
test values of EN 61326-1 for industrial areas, screened cable should
be used.
Use cable with round cross section for instruments with housing and
cable gland. Use a cable gland suitable for the cable diameter to
ensure the seal eect of the cable gland (IP protection rating).
Metric threads
In the case of instrument housings with metric thread, the cable
glands are screwed in at the factory. They are sealed with plastic
plugs as transport protection.
Note:
You have to remove these plugs before electrical connection.
NPT thread
In the case of instrument housings with self-sealing NPT threads, it is
not possible to have the cable entries screwed in at the factory. The
free openings for the cable glands are therefore covered with red dust
protection caps as transport protection.
Safety instructions
Voltage supply
Connection cable
Cable glands

17
NivoGuide® 8100 • Two-wire 4 … 20 mA/HART
5 Connecting to power supply
61893-EN-190911
Note:
Prior to setup you have to replace these protective caps with ap-
proved cable glands or close the openings with suitable blind plugs.
On plastic housings, the NPT cable gland or the Conduit steel tube
must be screwed into the threaded insert without grease.
Max. torque for all housings, see chapter "Technical data".
If screened cable is required, we recommend connecting the cable
screening on both ends to ground potential. In the sensor, the cable
screening must be connected directly to the internal ground terminal.
The ground terminal on the outside of the housing must be connected
to the ground potential (low impedance).
In Ex systems, the grounding is carried out according to the installa-
tion regulations.
In electroplating plants as well as plants for cathodic corrosion protec-
tion it must be taken into account that signicant potential dierences
exist. This can lead to unacceptably high currents in the cable screen
if it is grounded at both ends.
Information:
The metallic parts of the instrument (process tting, sensor, concen-
tric tube, etc.) are connected with the internal and external ground
terminal on the housing. This connection exists either directly via
the conductive metallic parts or, in case of instruments with external
electronics, via the screen of the special connection cable.
You can nd specications on the potential connections inside the
instrument in chapter "Technical data".
5.2 Connecting
The voltage supply and signal output are connected via the spring-
loaded terminals in the housing.
Connection to the display and adjustment module or to the interface
adapter is carried out via contact pins in the housing.
Information:
The terminal block is pluggable and can be removed from the
electronics. To do this, lift the terminal block with a small screwdriver
and pull it out. When reinserting the terminal block, you should hear it
snap in.
Proceed as follows:
1. Unscrew the housing lid
2. If a display and adjustment module is installed, remove it by turn-
ing it slightly to the left
3. Loosen compression nut of the cable gland and remove blind
plug
4. Remove approx. 10 cm (4 in) of the cable mantle, strip approx.
1 cm (0.4 in) of insulation from the ends of the individual wires
5. Insert the cable into the sensor through the cable entry
Cable screening and
grounding
Connection technology
Connection procedure

18
NivoGuide® 8100 • Two-wire 4 … 20 mA/HART
5 Connecting to power supply
61893-EN-190911
1 2
Fig.7:Connectionsteps5and6
1 Single chamber housing
2 Double chamber housing
6. Insert the wire ends into the terminals according to the wiring plan
Information:
Solid cores as well as exible cores with wire end sleeves are insert-
ed directly into the terminal openings. In case of exible cores without
end sleeves, press the terminal from above with a small screwdriver,
the terminal opening is then free. When the screwdriver is released,
the terminal closes again.
You can nd further information on the max. wire cross-section under
"Technicaldata-Electromechanicaldata".
7. Check the hold of the wires in the terminals by lightly pulling on
them
8. Connect the screen to the internal ground terminal, connect the
external ground terminal to potential equalisation
9. Tighten the compression nut of the cable entry gland. The seal
ring must completely encircle the cable
10. Reinsert the display and adjustment module, if one was installed
11. Screw the housing lid back on
The electrical connection is nished.
5.3 Wiring plan, single chamber housing
The following illustration applies to the non-Ex, Ex-ia and Ex-d-ia
version.

19
NivoGuide® 8100 • Two-wire 4 … 20 mA/HART
5 Connecting to power supply
61893-EN-190911
5
12
+
( ) (-)
678
4...20mA
2
3
4
1
Fig.8:Electronicsandconnectioncompartment-singlechamberhousing
1 Voltage supply, signal output
2 For display and adjustment module or interface adapter
3 For external display and adjustment unit
4 Ground terminal for connection of the cable screening
5.4 Wiring plan, double chamber housing
The following illustrations apply to the non-Ex as well as to the Ex-ia
version.
5678
4...20mA
12
+
( ) (-)
2
1 1
Fig.9:Electronicscompartment-doublechamberhousing
1 Internal connection to the connection compartment
2 For display and adjustment module or interface adapter
Electronics and connec-
tion compartment
Electronics compartment

20
NivoGuide® 8100 • Two-wire 4 … 20 mA/HART
5 Connecting to power supply
61893-EN-190911
5
12
+
( ) (-)
678
4...20mADisplay
2
3
4
1
Fig.10:Connectioncompartment-doublechamberhousing
1 Voltage supply, signal output
2 For display and adjustment module or interface adapter
3 For external display and adjustment unit
4 Ground terminal for connection of the cable screening
Connection compartment
Table of contents
Other Solutions Security Sensor manuals
Popular Security Sensor manuals by other brands
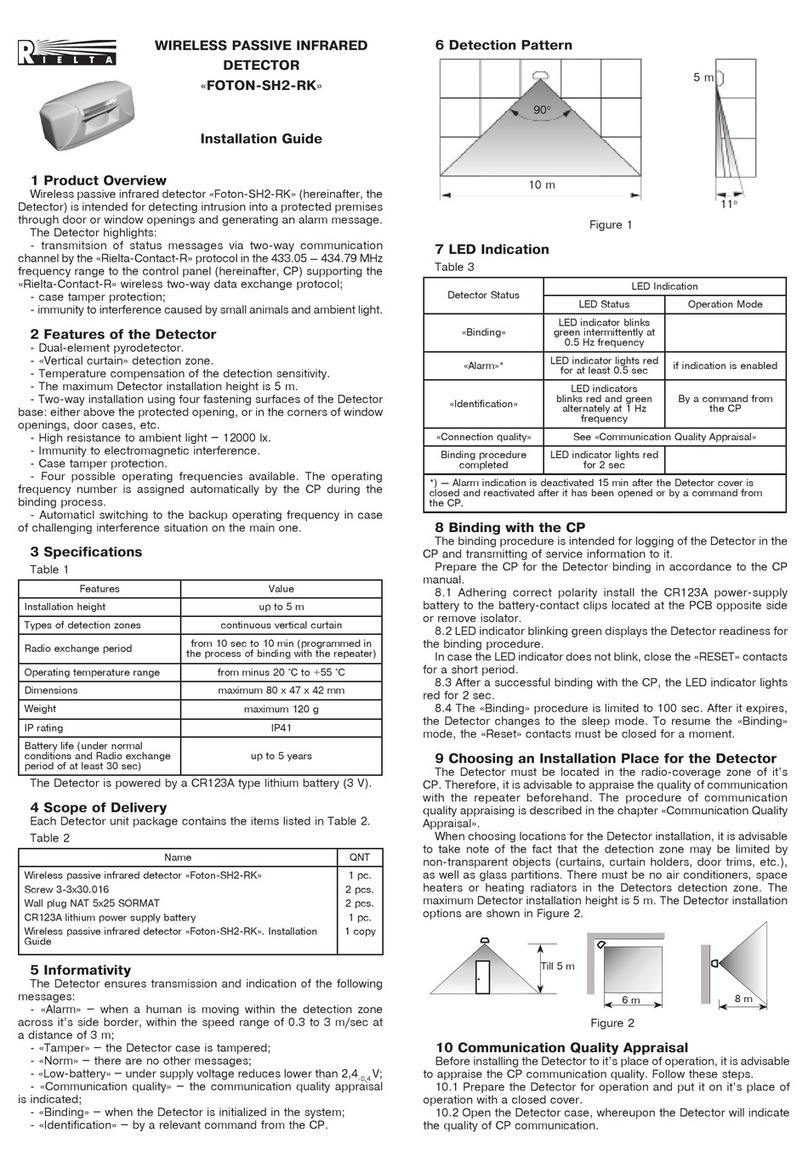
Rielta
Rielta FOTON-SH2-RK installation guide
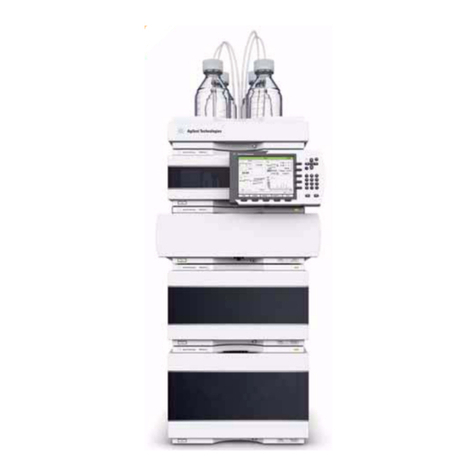
Agilent Technologies
Agilent Technologies 1200 Infinity Series user manual
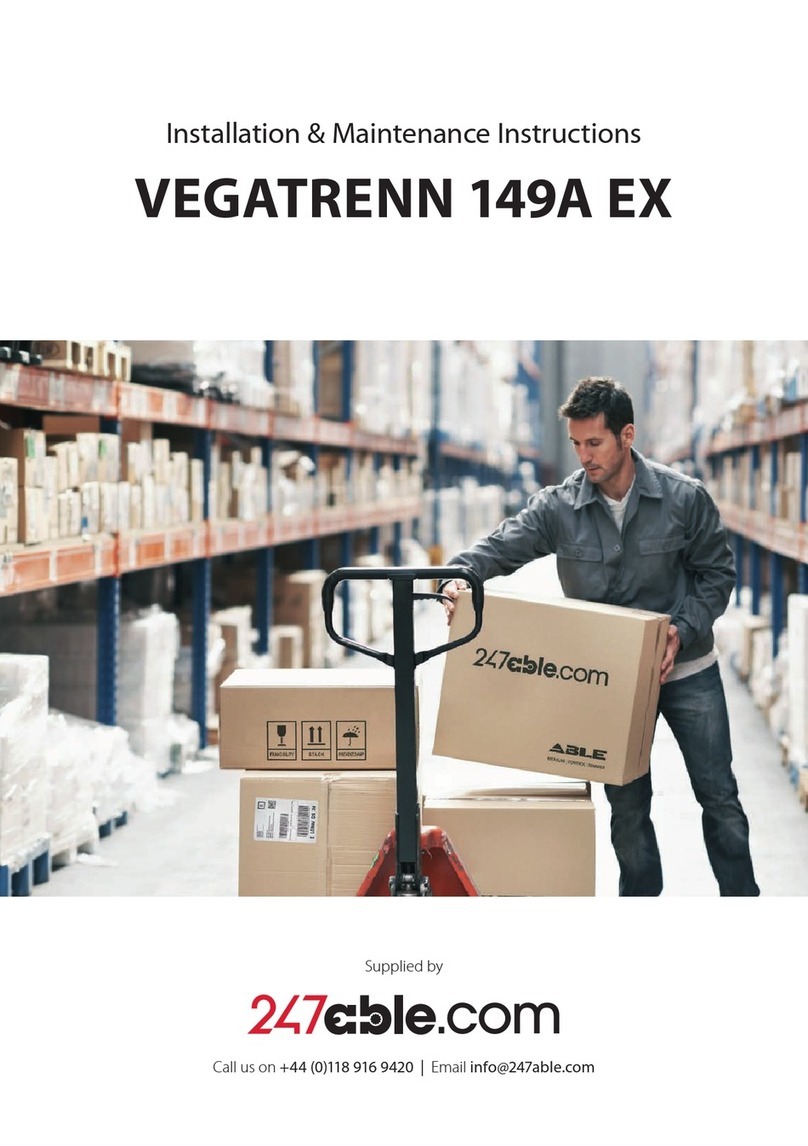
Vega
Vega VEGATRENN 149A EX operating instructions

Industrial Scientific
Industrial Scientific Ventis Pro Series product manual
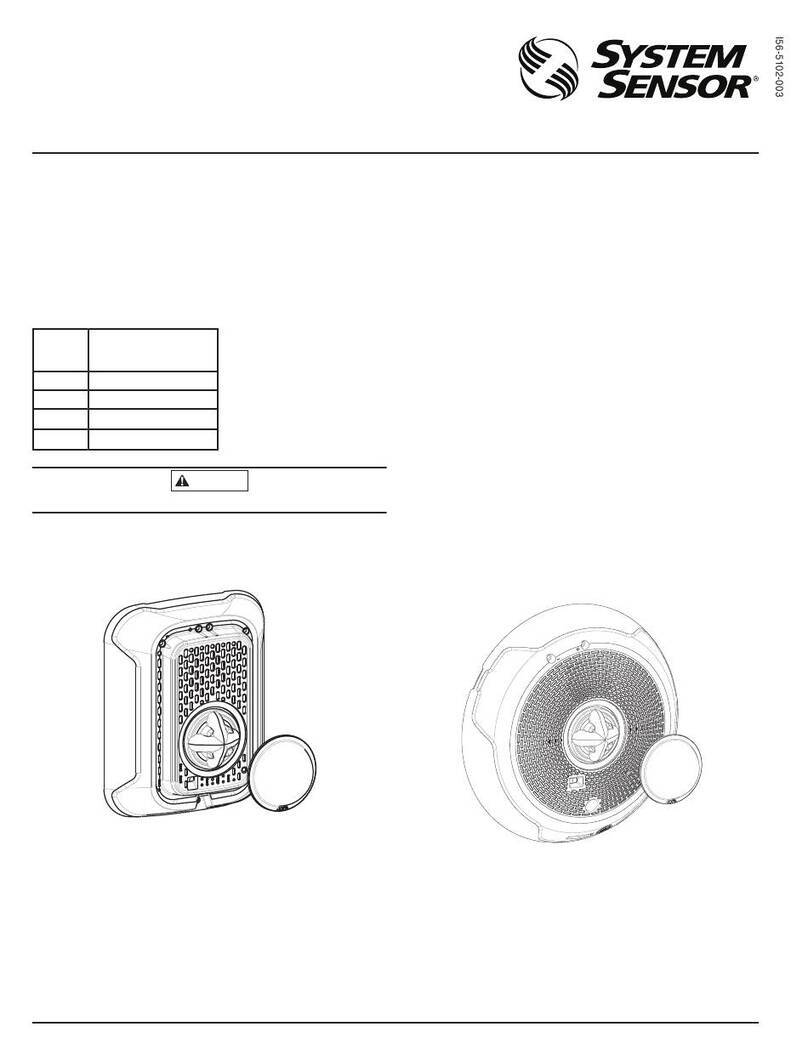
System Sensor
System Sensor L-Series Installation and maintenance instructions

Linde
Linde G-TECTA 4G operating manual