SOR echosonix U71 Instruction manual

Form 1034 (05.13) ©SOR Inc.
1/40
DISCONTINUED
echOsonix is a non-contact, ultrasonic level sensing device. It provides several
product-handling functions in one device.
n
Isolated 4-20 mA reversible analog output
scaled over the range entered by the user
n
Modbus digital communications
n
Switch - Two (model U71 integral mount)
or four (model U73 remote mount)
programmable Form C SPDT relays
n
Switch function choices of energize on
high or low level, fail-safe or disabled
n
Switch settings fully independent of level transmitter range and other relays
n
All values entered in engineering units
n
Push-button setup, no ranging or calibration required
n
Field selected application type from liquid, slurry or solid
n
Simulate mode to test parameter settings and relay/analog outputs
n
Automated false echo handling
n
Diagnostics - Features to aid installation/setup and provide testing and diagnostic functions
General Instructions
Registered Quality System to ISO 9001
Design and
specifications are
subject to change
without notice.
For latest revision, go to
www.sorinc.com
NOTE: If you suspect that a product is
defective, contact the factory or the
SOR
®
Representative in your area for
a return authorization number (RMA).
This product should only be installed
by trained and competent personnel.
Table of Contents
Safety.............................................3
Quick Start Installation Guide.................4
Mounting the Transducer ......................6
Focusing Cone and Flange Assembly...... 10
Electronic Housing Installation ............. 11
Transducer Cable Installation............... 12
Integral Electronics Wiring.................. 12
Wiring Diagram ............................... 14
Integral Terminal Block Diagram........... 16
Remote Terminal Block Diagram........... 16
Modbus Wiring Diagram..................... 17
Modbus Network .............................. 18
Keypad Interface .............................. 20
LCD Display.................................... 21
Field Programming ........................... 22
User Dened Values.......................... 23
Menu Structure................................ 26
Dimensions .................................... 28
Product Specications ....................... 33
Troubleshooting ............................... 34
U71-U73 Ultrasonic Transmitter
U73
U71

2/40
Form 1034 (05.13) ©SOR Inc.
DISCONTINUED
These instructions provide information for Mounting, Process and Electrical connections
and Field Programming of the echOsonix transmitter.
The echOsonix incorporates a transducer for sending and receiving an ultrasonic signal and
an electronics processing package. The ultrasonic signal is very powerful and may cause
hearing damage - refer to the safety instructions on page 3. The electronics package is either
mounted on top of the transducer or in a remote location connected by a shielded cable.
Prior to installation, review these instructions entirely. Transducer mounting location is
critical to proper operation. Most settings can be programmed prior to installation.
The PC boards are serialized to each unit and should not be removed
except by the factory. Removing the PC board will render the warranty
null and void.

Form 1034 (05.13) ©SOR Inc.
3/40
DISCONTINUED
Safety
Electrical Safety
The echOsonix is an electrically powered transmitter. Common electrical safety procedures
must be followed when working with this equipment. All wiring should be per local and
national standards. Do not remove the enclosure cover unless the area is known to be non-
hazardous. Do not handle circuit boards when energized.
Sound Protection
The echOsonix produces intense sound pulses. SOR recommends checking local safety
standards for Applicable hearing protection regulations.
Do not aim the transducer of an operating echOsonix at anyone’s head.
Permanent hearing damage may result. Use proper hearing protection when
operating in an enclosed space.
These values are based on dB (Lin) Peak, unweighted. Consult local sound protection
standards for conversions and limits.
Electrostatic Discharge (ESD) Handling Procedure
The SOR electronics instruments are designed to the highest quality standards. These
products use highly sensitive electronic components that are affected by static electricity,
that is present in most work environments. The following procedure is recommended to
reduce the possibility of component failure caused by static electricity damage.
n
Use a grounded wrist strap when installing or removing electronic boards. A grounded
workstation is recommended.
n
Ensure that all electrical connections are made and none are partial or floating. Ground
all equipment properly.
n
To prevent ignition from static charge buildup, use a damp cloth when cleaning the unit.
*Sound Pressure Level
Transducer
Model/Frequency
SPL* at 3 ft. (1 m)
in front of transducer
SPL* at 3 ft. (1 m)
to side of unit
SPL* at 3 ft. (1 m)
behind unit
A - 5kHz 137 dB 113 dB 100
B - 10kHz 138 dB 111 dB
K - 15kHz 135 dB 107 dB
C - 20kHz 135 dB 108 dB
D - 30kHz 133 dB 102 dB

4/40
Form 1034 (05.13) ©SOR Inc.
DISCONTINUED
Quick Start Installation Guide
This guide is intended to be a quick reference only. Please refer to each section of this form
for details on installation, wiring, set-up and operation. Contact the factory or your local
representative if you have any questions or concerns.
Install the transducer away from obstructions. Do not mount in the center of domed or
conical roof tanks. See page 6 for minimum mounting distance from tank walls.
Wire the unit according to local and national safety codes. Power and signal wiring must be
run as a minimum. Refer to pages 11-17 for more wiring details.
NOTE: Proper earth grounding of electronics is critical!
Flanged Mounting
Avoid mounting end of transducer
assembly inside standpipe.
Use a shorter standoff so
end of transducer assembly
is inside vessel, or...
Extend standpipe into
the vessel and cut the
end at a 45
o
angle.
Use a threaded coupling
directly on top of the
vessel, or...
Extend standpipe into
the vessel and cut the
end at a 45
o
angle.
See page 9
for standoff details.
Inlet Pipe
Test
GND
+DC
GND
Neutral
Active
RL1NO
RL1C
RL1NC
RL2NO
RL2C
RL2NC
GND
l+
l-
ICOM
B
A
22-27 VDC
Power Supply
100-126 VAC or
200-230 VAC
Power Supply
PLC/DCS
or Indicator
PLC/DCS
Powered Card
+
+- -
250Ω
250Ω
And/Or
Or
Threaded Mounting
Avoid mounting end of transducer
assembly inside standpipe.

Form 1034 (05.13) ©SOR Inc.
5/40
DISCONTINUED
Black
Red
White
Blue
Green
Yellow
Black
***
Red
White
Blue
Green
Y
ellow
Black
***
Red
White
Blue
Green
Y
ellow
Wire Shield (Drain)
Cable
Insulation
*** = Orange, Brown or Red/Black, depending on cable.
White & Black
If supplied, cut this
wire – do not use
Black
***
Red
White
Blue
Green
Y
ellow
Wire Shield (Drain)
Cable
Insulation
White & Black
To splice remote transducer cables, follow the diagram below. See page 12 for details.
*** Brown or Red/Black, depending on cable.
* Yellow or Orange
*
*
*
*
Relay Point
Highest Level
High Level
100%
Relay Point
Lowest Level
Low Level
0%
Blanking
(No detection)
High Level
(20 mA)
L1 Level
(Any relay)
L2 Level
(Any relay)
Lo Level
(4mA)
Calculate the level distances for
the vessel. These will be entered
when programming the unit.
All values are measured from
the transducer face down to the
desired level. See pages 23-24
for details of each value.
NOTE: All values are measured
from the transducer face down.
Hi Level will be a smaller number
than Lo Level.
Program the basic parameters in the setup menu. Press CAL to access the menu. Enter the
Application Type, Hi Level, Lo Level and relay settings using the values calculated in the
above step. See pages 26 and 27 for menu structure and description.
NOTE: Push-button interface is the
same for integral and remote units.
To change number values fast,
hold down the arrow key and
press CAL.
This guide is intended to be a quick reference only. Please refer to each section of this form
for details on installation, wiring, set up and operation. Contact the factory or your local
representative if you have any questions or concerns.
Return to normal operation Enter menus, change
menu selection,
accept changes
Change numeric values and move
between menu options
{
Distance
12.34 ft.
DistanceDistance
12.34 ft.12.34 ft. cal
run
NOTE: Do not exceed loft of cable added or taken off

6/40
Form 1034 (05.13) ©SOR Inc.
DISCONTINUED
Mounting the Transducer
For all applications the transducer is mounted above the process pointing directly down at
the measured surface. In open or flat topped vessels the transducer should be mounted
so that the primary cone of sound does not intersect the wall of the vessel, if possible. The
table below lists typical guidelines for minimum mounting distances from the wall. If the
radius of the vessel is less than the minimum distance, consult the factory for assistance.
Vessel Height
For vessels taller than 40 feet (12m), use:
Minimum Distance = Vessel Height x 0.087
0
1 foot
(0.3 m)
2 feet
(0.6 m)
3 feet
(0.9 m)
4 feet
(1.2 m)
10 feet
(3 m)
20 feet
(6 m)
30 feet
(9 m)
40 feet
(12 m)
0
Minimum Mounting Distance
Minimum Mounting
Distance
Transducer mounting placement is critical. The
transducer assembly generates both the sound
pulse and monitors the echoes. The sound pulses
travel away from the face of the transducer in a
cone-shaped pattern. This area should be free of
obstructions and away from inlets.
The transducer should be mounted in a position
that allows unobstructed access between the
face and the process to be measured.
Inlet Pipe
NOTE: A good rule of thumb is to look down
inside the vessel through the mounting
location. You should be able to see a clear
path to the process material without any
physical objects or ll streams in the way.

Form 1034 (05.13) ©SOR Inc.
7/40
DISCONTINUED
Alternative Mounting
echOsonix units may be mounted inside a stilling well or bridle to avoid excessive
obstructions or turbulence in the process. Follow the guidelines shown below for the
stilling well or bridle, then see page 38 for special instructions.
Bridle
Stilling Well
Inlet Pipe
Min. 2”
Min. 4”
Diamete
r
Min. 4”
Diamete
r
Minimum
Holes
echOsonix units are designed to read solids materials and ignore the angle of repose. The
angle of repose is the angle between horizontal and the side of the pile of material. For
processes where the angle of repose is greater than 45 degrees, the echOsonix may require
some special tuning or setup. Contact the factory for these situations.
For solids installations, the echOsonix should be mounted in a vertical position according to
the diagram below. Do not “aim” the transducer to the angle of repose, this is not necessary.
Mount the transducer 1/3 of the distance from the vessel wall to the vessel centerline, away
from any internal obstructions.
For vessels that fill and discharge from the center, this mounting location will provide a
good average level measurement. As solids pile up they form a cone, and as they
discharge they form a conical pit. By measuring the level at the 1/3 radius position
shown, an average level is obtained for both situations. For vessels that do not fill and/or
discharge from the center, a mounting location should be chosen that will provide the best
possible average level.

8/40
Form 1034 (05.13) ©SOR Inc.
DISCONTINUED
1
3
2
3
1
3
2
3
Average
Level

Form 1034 (05.13) ©SOR Inc.
9/40
DISCONTINUED
echOsonix transducers may be mounted using a threaded connection or a flanged
connection. Some units require flange mounting. There are two options for thread
mounting which are detailed below. In all cases, the transducer should be installed in
a stable, permanent mounting fixture.
Focusing Cones
All units are supplied with some form of focusing cone to be mounted on the transmitting
end of the transducer. These cones should always be installed according to the instructions
in this manual. If the mounting method inhibits this cone, the mounting should be modified
to account for it. The cones are vital to proper performance and should not be modified
or removed.
Thread Mounting
Short-range transducers (30, 20 and 15kHz) may be supplied with a 3” NPT mounting
thread. All remote transducers are also supplied with a 1” NPT/BSP cable nipple that can be
used for either conduit connection or mounting.
Flange Mounting
When mounting a unit with a flange, we recommend using non-metallic bolts. The
mounting bolts should be hand-tight only. Do not over-tighten the bolts, this can affect
performance of the echOsonix transducer.
Most flange mounts use a standpipe. It is important to follow the guidelines below for
standpipe design. Methods are shown in order of preference - Method 1 preferred, etc.
Method 1 Method 2 Method 3
End of transducer
assembly extends past
end of standpipe
End of standpipe
is cut at a 45°
angle, transducer
is inside pipe End of transducer is
inside standpipe.
Ratio of H / D = 1 or less
DisMinimum 4”
H
D

10/40
Form 1034 (05.13) ©SOR Inc.
DISCONTINUED
Focusing Cone and Flange Assembly
Units supplied with focusing cones and flanges are shipped disassembled. Follow the
directions below to assemble these units prior to installation.
Transducer
(Sensor)
Mounting
Flange
Focusing
Cone
Locking
Ring
For 10kHz (BBP, RBP, BEP), screw locking ring
down tight onto top of focusing cone
Or
For 5kHz (BAP, RAP) locking ring is not
moveable, screw transducer down until locking
ring is tight onto top of focusing cone
Mount transducer
into flange assembly.
Thread focusing cone
into mounting flange.
NOTE: All threaded connections
should be sealed with either Teon
tape or a thread sealer that is
compatible with Polypropylene.
Install mounting
flange / focusing
cone assembly into
process.
NOTE:
Mount ange
as shown; small
threaded ange
MUST be pointing up.

Form 1034 (05.13) ©SOR Inc.
11/40
DISCONTINUED
Electronic Housing Installation
For integral units, the electronic housing assembly is permanently attached to the
transducer and mounted at the same time. This design unit is not considered here.
For remote units, the electronic housing is a separate assembly from the transducer. The
two are attached by a 7-conductor, 22-gage shielded cable. The electronics enclosure
should be mounted in a location that is protected from physical damage, will stay within
the temperature limits of the electronics and is convenient to plant operators.
One cable gland is supplied with the unit for
the transducer cable. Power and signal wiring
must be routed through a customer supplied
cable gland. Customer connections should be
installed in the same housing surface as the
supplied factory cable gland.
Customer Cable Gland Installation
Locate where the cable gland will be installed
and mark the center of the hole. Clamp the
enclosure to a secure surface. Drill the required hole size.
NOTE: Backing is NOT required when drilling the echOsonix
remote electronics enclosure.
Open cover.
Remove all machining debris from inside the enclosure. Install the new cable gland.
Mounting Remote Electronics Box
Mount the remote electronics enclosure so that the hinged cover is upright and opens from
right to left. Mount the box using four threaded screws through the holes provided on the
back (hole size 3/16”).

12/40
Form 1034 (05.13) ©SOR Inc.
DISCONTINUED
Transducer Cable Installation
On remote mount units the electronics housing may be mounted up to 330 feet (100m)
away from the transducer. Transducer cable is supplied with each unit to the length
requested in the model number. The cable is sealed in the transducer and has six
conductors at the electronics end.
Transducer cable should be mounted in conduit, but it is not required. Mount the cable
so that it is free from physical damage and electrical interference from outside sources.
The transducer cable should always be mounted away from high-energy AC power lines.
Splices in the cable must be protected from weather. If conduit is used, it is NOT necessary
to use grounded, metal conduit.
If the cable is too short, it can be lengthened in the eld. Extend the cable length using
6-conductor, 22-gage shielded cable. The new cable may be attached with an in-line splice
or using a junction box. Be sure to maintain color continuity.
If the cable is too long, it can be shortened in the eld. Follow the diagram below very
carefully to ensure proper termination of the cable. This is critical to the functioning of the
transducer.
Black
Red
White
Blue
Green
Yellow
Black
***
Red
White
Blue
Green
Y
ellow
Black
***
Red
White
Blue
Green
Y
ellow
Wire Shield (Drain)
Cable
Insulation
*** = Orange, Brown or Red/Black, depending on cable.
White & Black
If supplied, cut this
wire – do not use
Black
***
Red
White
Blue
Green
Y
ellow
Wire Shield (Drain)
Cable
Insulation
White & Black
*** Brown or Red/Black, depending on cable.
* Yellow or Orange
*
*
*
*
Integral Electronics Wiring
Remote transducer cables must be attached to the terminal block provided inside the remote
electronics housing. The terminals are labeled on the PCB according to the wire colors:
black, red, white, blue, green, yellow or orange. Thread the transducer cable through the
factory supplied cable gland. Firmly attach each transducer wire lead to the corresponding
terminal block point. Provide enough cable slack inside the housing to keep all stress off of
the terminal connections. Tighten the cable gland nut securely – DO NOT OVERTIGHTEN.
NOTE: To ensure proper and secure wiring, back each terminal block screw out to the fully open
position before inserting the appropriate wire. After tightening the terminal screw, check the
connection by gently tugging on the wire to see if it comes out of the terminal block.

Form 1034 (05.13) ©SOR Inc.
13/40
DISCONTINUED
Integral Housing Wiring
Loosen cover locking screw A1 and remove cover A2 to access display board B.
Remove the display board by removing the three screws at its outer edge C. DO NOT
remove the four screws at the corners of the LCD display. Pull the display board up and
lay it out of the way.
Remove the terminal blocks D by rocking them back and forth gently while pulling
straight up. Run the supply wires through conduit opening E and attach them to the
terminal blocks per the wiring diagram selected from pages 14 & 15.
After wiring is complete, align the respective terminal block with its socket and push
firmly into place. The entire block must be fully seated for proper connections.
For explosion proof locations, install the proper conduit seals per local and national
codes and standards.
Electrical power must be disconnected from explosion proof models before
the cover is removed. Failure to do so could result in severe personal injury or
substantial property damage.
Drawing 0390733
NOTE: Minimum recommended wire gage should be 14 AWG. Conductors are rated for
100°C minimum.
The echOsonix may be powered by 24 VDC, 110/220 VAC or both at the same time. The
most common method of powering the unit is to use 110 VAC line power with a 24 VDC
battery backup. The unit has an optically isolated 4-20mA analog output signal, RS485
Modbus digital communications output and two or four relays.

14/40
Form 1034 (05.13) ©SOR Inc.
DISCONTINUED
Wiring Diagram
All echOsonix units may be powered by either AC or DC external supplies. The analog
4-20mA circuit may either be powered from the echOsonix internally or by a user-supplied
external DC power supply. The wiring diagrams below specify the wiring options for either
3-wire DC, 4-wire DC or AC external power supplies.
The analog 4-20mA circuit is a self-powered, optically isolated negative side current control
loop. The current is actually controlled between the “I COM” and “I-” terminals of the unit.
The “I+” terminal is the internally regulated voltage source for self powering the current
loop. The loop is approximately +17V above the output common “I COM”.
Terminal Connections for DC Supply
a) 3-Wire DC – 4-20mA driven from Common User Supply (RL to +DC)
b) 3-Wire DC – 4-20mA driven from Common User Supply (RL to GND)
c) 4-Wire DC – 4-20mA driven from Internal Isolated Supply (I+)

Form 1034 (05.13) ©SOR Inc.
15/40
DISCONTINUED
Terminal Connections for AC Supply
d) 4-20mA driven from User’s External DC Supply (RL to Pos.)
e) 4-20mA driven from User’s External DC Supply (RL to Neg.)
f) 4-20mA driven from Internal Isolated Supply (I+)

16/40
Form 1034 (05.13) ©SOR Inc.
DISCONTINUED
Integral Terminal Block Diagram
Terminal Description
Test Test port (factory only)
GND -DC power
+DC +DC power
GND AC ground
Neutral AC neutral
Active AC hot wire
RL1NC Relay 1 normally closed
RL1C Relay 1 common
RL1NO Relay 1 normally open
RL2NC Relay 2 normally closed
RL2C Relay 2 common
RL2NO Relay 2 normally open
Terminal Description
A RS485 Comm Port
B RS485 Comm Port
GND Ground point
I+ 4-20 mA loop positive pole
I- 4-20 mA loop negative pole
ICOM 4-20 mA loop common
Terminal
Description
1 Relay 1 normally open
2 Relay 1 common
3Relay 1 normally closed
4 Relay 2 normally open
5 Relay 2 common
6Relay 2 normally closed
7 Relay 3 normally open
8 Relay 3 common
9Relay 3 normally closed
10 Relay 4 normally open
11 Relay 4 common
12 Relay 4 normally closed
13 AC hot wire
14 AC neutral
15 AC ground
Remote Terminal Block Diagram
Terminal
Description
BLK Black transducer wire
RED Red transducer wire
WHT White transducer wire
BLU Blue transducer wire
GRN Green transducer wire
YLW Yellow transducer wire
485A RS485 Comm Port
485B RS485 Comm Port
GND Ground point
Terminal
Description
ICOM 4-20 mA loop common
I-
4-20 mA loop negative pole
I+
4-20 mA loop positive pole
TST Test port (factory only)
GND -DC power
+DC +DC power

Form 1034 (05.13) ©SOR Inc.
17/40
DISCONTINUED
Modbus Wiring Diagram
All line-powered echOsonix units are provided with Modbus communications. One advan-
tage of this feature is the ability to connect units in series, reducing cabling requirements.
Up to 128 echOsonix units may be connected through a single I/O point using the Modbus
communications network. The wiring diagram below describes how to do this.
Materials Required
n
Three conductor shielded cable
n
An RS485 compatible computer control system with external AC or DC power supply
- OR -
n
An ADAM RS485 to RS232 converter (or equivalent) and PC with available Serial port
NOTE: This wiring diagram is for the Modbus communications ONLY. Either AC or DC power must
be provided separately. Power circuits may be connected in series as well; each echOsonix unit
will draw approximately 0.3A.
A
B
GND
I+
I-
ICOM
24V DC
A
B
GND
I+
I-
ICOM
A
B
GND
I+
I-
ICOM
A
B
GND
I+
I-
ICOM
Leave shield wire
open at this end
Unit 1 Unit 2 Unit 3
Last Unit (128 max.)
Repeat this wiring
scheme for every
unit in the network.
Chassis
Ground
Shielded 22-gage
3-conductor cable
ADAM
RS485 to RS232
Converter
R + Vs
B Gnd
Data+
Data-
+
–
To PC Serial Port

18/40
Form 1034 (05.13) ©SOR Inc.
DISCONTINUED
Modbus Network
Each echOsonix has a communications address that must be unique. The Modbus protocol
uses this address to identify each unit. The default address “1” must be changed before
connecting more than one unit to the network. This can be done either through the
on-board menus or the Modbus interface. Follow one of the procedures below to address
each unit before connecting them all to the network.
On-Board Menu Procedure
Provide power to the unit.
At the normal operations screen on the LCD, press CAL once. The screen will change to
“UnLock: 0”.
Use the up arrow to enter “195” for the unlock code. Press CAL once. The screen will
change to “Setup”.
Press the up arrow twice to change the screen to “Tracking”. Press CAL once.
Press CAL until the screen says “CommAdds: 1”. This is the communications
address value.
Press the up arrow to enter the unique communications address for this unit –
range is 1 to 255.
NOTE: Do not use addresses 3 or 6.
Press RUN to save the communications address.
Repeat this procedure for every unit in the network, making sure each one has a
unique address.
Modbus Interface Procedure
Connect one unit to both the power supply and the Modbus network per the prior
wiring diagram.
Set up the controlling computer software to write to the Comms Address parameter per
the chart on page 19.
Write a unique communications address to this unit. This address must be between
“2” and “255”.
Connect one more unit to both the power supply and the Modbus network.
Repeat steps 3 and 4 until all units have been connected to the network and given a
unique address.
Modbus Address Denitions
Many users will want to connect echOsonix units to their pre-existing Modbus compatible
control system. To do this, they must know what information is available over the Modbus
network, where it is located, and how to manipulate it. The chart below defines the most
commonly used addresses on the echOsonix unit. It is not the intention of this document
to educate users on the fundamentals of Modbus protocols. More information can be
found at www.modbus.org.

Form 1034 (05.13) ©SOR Inc.
19/40
DISCONTINUED
echOsonix
Parameter
Command
Address Location Decimal
Min.
Decimal
Max.
Conversion
Factor Description
Read Only Parameters
Distance 75 High byte
Low byte
0 46562 See below
Current output of the
unit as distance from
the face of the trans-
ducer to the process
material.
Noise Level 79 Low byte 1 255 X 0.3922
The background
noise detected by the
transducer
Temp 70 High byte
Low byte
0 1760 Divide by
10
Currently monitored
temperature in °F or
°C (based on units of
measure selected).
Temp Sign 18 High byte NA NA NA
If bit 3 = 1, temperature
is positive, if bit 3 = 0,
temperature is negative.
Read/Write Parameters
Comms
Address
65 High byte 1 255 1
Communications
address for the unit as
described above.
Units of
Measure
18 High byte NA NA NA
If bit 0 = 1, units is
feet, if bit 0 = 0, units is
meters.
Display 35 High byte 0 2 NA
0 = distance, 1 = level,
2 = level %
Application 22 High byte 0 2 NA
0 = solids, 1 = liquids, 2
= slurries
Application
Speed
22 Low byte 2 255 X 0.1 (ft)
X 0.03 (m)
The maximum speed
the process is expected
to move.
Damping 20 Low byte 0 240 1 Damping value
Blanking 33 High byte
Low byte
0 46562 See below Programmed blanking
distance
NOTE: Additional echOsonix parameter address information is available from the factory.
Distance Conversion Factors
To convert distance values from decimal form to engineering units, multiply the reported
result by the following factors.
Transducer Frequency/Model Conversion to Feet Conversion to Meters
5 & 10kHz (RAP, BAP, RBP, BBP) 0.001501333 0.0004576
15, 20 & 30kHz (RKP, BKP, RCP, BCP, RDP, BDP) 0.00011439 0.0003753

20/40
Form 1034 (05.13) ©SOR Inc.
DISCONTINUED
Keypad Interface
The echOsonix requires a minimal amount of parameter
setup. The units, display, process type and range must be set
for each application. All other parameters should be set as
required or desired. The large picture below shows the setup
interface for an integral unit. The remote unit controls are
shown in the inset. The next section shows the menu choices
as well as a brief description of each feature.
NOTE: When changing numerical values, hold down the arrow but-
ton and push the CAL button to make the numbers change faster.
But be careful – if you let go of the arrow while pushing the CAL
button the display will move to the next programming step.
LCD Display
RUN button- used to exit menus
and return to normal operation
CAL button - used to
enter menus and select/
save menu choices
UP and DOWN arrow buttons -
used to move between menu
options and change values
Pulse indicator light
Echo Indicator LED–
Readable Echo Received
Relay Indicator LEDs –
Status of Relays
(LED on, relay is energized)
Remote Unit Controls
This manual suits for next models
1
Table of contents
Other SOR Transmitter manuals
Popular Transmitter manuals by other brands

APG
APG PT-500 Series user manual

Rosemount
Rosemount 848T quick start guide
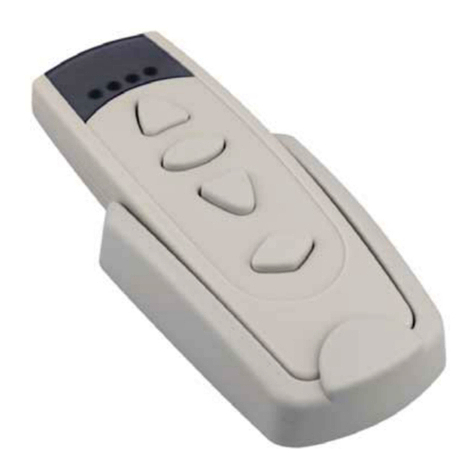
Eldat
Eldat Easywave RT24 Series operating instructions

ARTEX AIRCRAFT SUPPLIES
ARTEX AIRCRAFT SUPPLIES ME406 ELT Description, operation, installation and maintenance manual
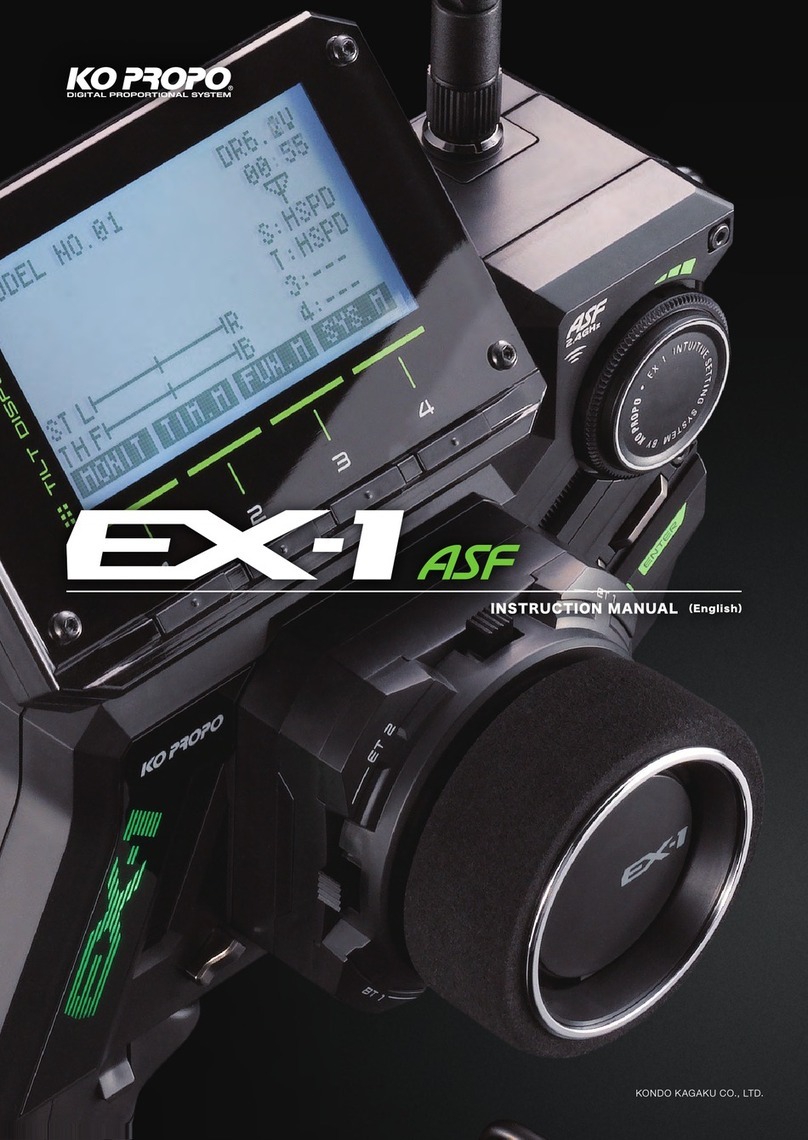
Ko Propo
Ko Propo EX-1 ASF instruction manual
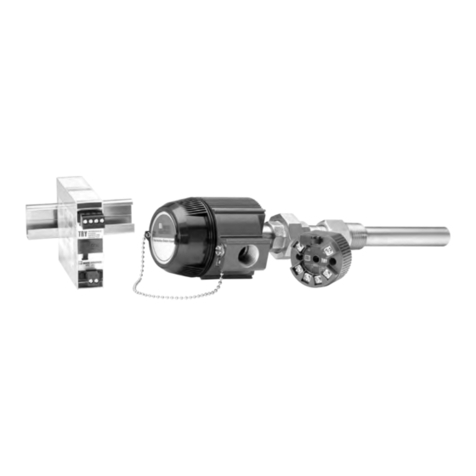
Moore Industries
Moore Industries TRY quick start guide