Sortimat SMS 150 User manual

Operating Instructions
for
Controller SMS 150 / 151

2
Contents
Controller SMS 150 / 151..................................... 1
Contents..................................................... 2
Reserve...................................................... 2
1. Safety instructions for users............................. 3
2. Application............................................... 4
3. Warnings.................................................. 5
4. Installation.............................................. 5
4.1 Overview and dimensions.................................. 7
4.2 Technical data........................................... 8
4.3 Connection possibilities................................. 9
4.4 Starting................................................ 11
5. Operating tips........................................... 11
6. Repairs.................................................. 11
7. Troubleshooting.......................................... 12
Declaration of conformity................................... 13
Reserve
General informations und data contained in this documentation can changed
without announcement. Errors and omissions excepted.
The users are committed to observe all applicably copyright laws. Without
explicit permission in written form of the company RUG Regler- und Geräte-
bau GmbH no part of this documentation may copied or communicate for any
purposes, independently in which kind or with any instruments, electroni-
cally or mechanically, this happens.

3
1. Safety instructions for users
These instructions contain the necessary information for the correct use of
the products described. They are for use by technically qualified persons.
Qualified personnel are those persons whose vocational training, experience
and internal training and their knowledge of the relevant standards, regu-
lations, accident prevention regulations and plant operating conditions has
led the person responsible for operational safety to authorise them to car-
ry out the necessary work, and are able to recognise and avoid potential
risks (definition of skilled workers as per IEC 364).
Risk information
The following information serves not only the personal safety of the oper-
ating personnel but also the safety of the products described herein and
appliances connected to them.
DANGER !
High-voltage operations.
Non-compliance can lead to death, serious injury or damage to property.
-
-
-
-
-
-
Always disconnect the supply voltage before assembly or dismantling
work, when replacing fuses or altering the structure.
The relevant Accident Prevention and Safety at Work Regulations must be
complied with at all times.
Before commissioning, make sure that the appliance's nominal voltage
conforms to the local mains voltage.
EMERGENCY SWITCHES must remain operational in all working modes. Unlock-
ing EMERGENCY SWITCHES must not lead to uncontrolled.
Electrical connections must be covered at all times!
After assembly, check all protective conductor systems for correct func-
tioning!
Proper use
The appliance described here is an electrical device for use in feeder
equipment or automation plant.
The appliance has been planned for use in oscillation conveyors, in control
and automation technology.

4
This appliance conforms to the relevant Low-Voltage and EMC Guidelines.
2. Application
The SMS 150/151 electronic controller is used for stepless control of in-
ductive loads such as spiral conveyors, linear conveyors and hoppers.
The controller works on the phase control system, the conveyor output is
carried out by setting the magnet voltage via the setpoint potentiometer
integrated in the casing cover. The control curve of the setpoint value
voltage can be restricted by means of two trimming potentiometers, Umin and
Umax, on the board in such a way that the complete range of the setpoint
value can always be used.
The ignition impulses can be displaced infinitely in the range of the posi-
tive or negative mains voltage half-wave through the setpoint voltage ad-
justable with the setpoint, which then sets the voltage-time area of the
output voltage is set. With feeder appliances with 50 Hz oscillation fre-
quency both (positive and negative) mains voltage half-waves are con-
trolled, and with feeders with 25 Hz oscillation frequency only one mains
voltage half-wave is controlled. The switchover between full-wave and half-
wave mode is carried out as a standard with a sliding switch on the board
(see Connection Possibilities).
After the working voltage has been switched on the integrated variable
soft-start is started and guarantees smooth acceleration of the output vol-
tage to the preset voltage value. This eliminates possible switching peaks.
In addition, the soft-start, and the soft-stop, become effective when the
output voltage is switched on and off via the controller input for the lev-
el control system and serves to increase or decrease the conveyor output on
a time-controlled basis so that bulk material does not change its position.
Both these times can be set separately.
The controller input controls the running time of the oscillation conveyor
in such a way that unnecessary running time are avoided. Internal variable
times (GAN and GAB) are used to turn the oscillation conveyor ON or OFF in
dependency on the material level measured via a material sensor.
The controller input enables the turn On and OFF of the controller load
output through another system (SPS, initiator, sensor and other). The con-
troller has an integrated power supply for +24VDC. A turn ON and OFF
through a external +24VDC voltage is possible. The controller input takes
affect to the ignition pulses.
Measurements of the output voltage (arithmetic value measurements) enable
changes to the voltage to be registered immediately an compensated by means
of a controller stage. This guarantees even running of the bulk material.

5
Miniature magnets can also be operated safely at the controller !
Setting the ON and OFF time delay for the level controller
The level of the material in the filling section is measured by the GAN and
GAB trimmers. To increase the material back-up downstream from the sensor,
use the GAB trimmer to lengthen the controller's OFF delay time. Reduce the
GAB time to reduce the back-up of material. The GAN trimmer can now be used
to determine the time that passes from when the last part of the material
leaves the sensor position until the feeder appliance is switched on
The diagram shows the time sequence in operations with the controller input
low active:
t
t
0
X
V
0
1
G
AN
SA G
AB
SS
0,1-10s 0,5-5s 0,1-10s
0,1-5s
Output voltage
Signal at
control input
3. Warnings
!
!
!
In the case of applications that require the oscillation conveyor
to be switched ON and OFF constantly (e.g. dust switched off, hop-
per control system, etc.), the prescribed controller input must be
used. If the load circuit is disconnected with a switch or a relay
the controller may be damaged.
If the controller is switched on, never insert or remove the plug
at the vibration conveyor being operated. This can damage the ap-
pliance.
Repair work must be carried out by qualified personnel only. We
recommend that repairs are carried out on our premises.
4. Installation

6
For mounting of the controller there is a hole and a long hole accessibly
from the outside. These holes are separated from the interior of the hous-
ing.
-
-
Mounting on a vibration free background.
Please notice, the interior ribbon cables may not squeezed against the
housing. When the ribbon cables are squeezed there can be a short-
circuit and the controller can be destroyed !

7
4.1 Overview and dimensions

8
4.2 Technical data
Type SMS 150 / SMS 151
Mains voltage 230V AC / +-10% / 115V AC / +-10%
Mains frequency 50Hz / 60Hz
Output frequency 25Hz/50Hz / 30Hz/60Hz
Output voltage 30 - 228 V AC / 30 - 113 V AC
Setup to 200 VAC
Output current 0,01 - 6 A AC
Type of protection IP 54 at mounting hanging
(fitting show down)
Fuse 1 x 6,3 A F flink
Ambient temperature 0 .. 50°C
Setpoint Internal potentiometer
Mains connection 2m with gated Schuko-plug 90°
Connection conveyor 2m witht Contact HA3-BS plug
Housing Al-background + Al-Strand casting +
Plastic cover
Dimensions (l x b x h) ca. 175 x 80 x 94 mm
Features:
Oscillation frequency Reversible
Controller input isolated
Switching level HI: 6 - 24 VDC
Switching level LO: 0 - 4 VDC
+24 V DC / max. 50mA / PNP
Opener mode:
Output voltage 0 V with applied
switching voltage of + 24 V DC
Preset output voltage with applied
switching of 0 V DC
Closer mode :
Output voltage 0 V with applied
switching voltage of 0 V DC
Preset output voltage with applied
switching voltage of + 24 V DC
Twin timer (GAN/GAB) GAN turn ON delay : 0-10 seconds
GAB turn OFF delay : 0-10 seconds
Soft-start t1 ca. 0.5 - 5 sec. Variable
Soft-stop t2 ca. 0.1 - 5 sec. Variable
Mains voltage compensation
(arithmetic measurement)
Compensation of mains voltage fluctu-
ations at output.
With preset output voltage of e.g.
170 V AC a max. voltage change of
3,5
V AC arises, with changes of the in-
put voltage from 230 V AC to 200 V AC
or from 230 V AC to 260 V AC.
Standards complied with DIN EN 50 081 Part 1
Residential, commercial and trade and
light industry, industry.
DIN EN 50 082 Part 2
Industry
VDE 0160

9
4.3 Connection possibilities
Connection conveyor
Pin 1 - Load
Pin 2 – Load
Pin 3 - NotConnected
PE - Protective earth

10
Connection
s
ensor /
control input
Pin 1 - +24 VDC / max.50mA / PNP
Pin 2 – NotConnected
Pin 3 - ground
Pin 4 - Input 1
The +24VDC supply is isolated to 230VAC und +5VDC side
of the CPU !
Programmi
ng
Dip 1 – Frequency 50/25Hz
OFF – 50Hz
ON – 25Hz
Dip 2 – Setpoint fixed
OFF - Setpoint-potentiometer active
ON - Setpoint-potentiometer inactive
Value fixed by switching
Dip 3 - Control
OFF - Output has reaction on control input and
Closer/opener
ON - Output always ON, no reaction on control
Input and closer/opener
Dip 4 - Input 1
OFF – value opener
ON - value closer (input 1 inverted)
Right rotary
Min – left limit stop
Max - right limit stop
Values
Umin – Low limit of the output
Umax – High limit of the output
SA – Soft start
SS – Soft stop
GAN 1 – Turn ON delay input 1
GAB 1 – Turn OFF delay input 1

11
4.4 Starting
1.
2.
3.
4.
5.
6.
7.
Before connecting the controller, check the working voltage and working
frequency of the conveyor and compare them with the technical data for
the controller. The output current of 6A should not be exceeded.
Depending on the working frequency of the conveyor, set the slide
switch on the board:
Full-wave operations 50/60 Hz (slide switch above)
Half-wave operations 25/30 Hz (slide switch below)
Check the programming on the board in dependence on the type of switch-
ing and set.
Connect the conveyor to the controller.
Insert the controller's plug into the mains.
Switch the controller on.
Set the required control range with the Umin and Umax potentiometers.
5. Operating tips
1.
2.
3.
Before switching on, check that the controller is correctly plugged
into the conveyor.
Switch the controller on with a mains switch.
If required, adjust the setpoint until the vibration conveyor reaches
the desired output.
6. Repairs
Replacing fuse
1. Replace defective fuse with a 6,3 A F fuse.
Fuse is available over fuseholder in the cover.

12
7. Troubleshooting
Appliance not working
-
-
Check the mains voltage, check the fuse and replace if necessary.
Is the controller input set correctly, programming correct?
No output from conveyor
-
-
-
Check whether the correct oscillation frequency has been set, change
setting where necessary.
Check the mains frequency (50/60 Hz). The oscillation frequency and the
mains voltage must agree.
Umax trimmer set too low. Set Umax.
Conveyor vibrates too much, magnet knocking (noises)
-
-
Oscillation frequency setting incorrect. CAUTION! Magnet may have been
destroyed by overheating or damaged mechanically by knocking.
Umax trimmer set too high. Set Umax if necessary.
Magnet heats up
-
-
Magnet has incorrect mains voltage, check.
Incorrect oscillation frequency set, change if necessary.
Controller input not working
-
-
Control voltage polarity reversal, check.
Correct jumper for controller input? Check.

13
Declaration of conformity
The company RUG Regler- und Gerätebau GmbH
Karl-Ehmann-Str.50
73037 Göppingen
hereby declares in its own responsibility that the product
control appliance for oscillation conveyor systems
with the type designation SMS 150/151 (incl. derivatives)
to which this declaration refers conforms to the following standards
Basic standards for transient emissions : DIN EN 50 081 Teil 1
living quarters, business
and trade area plus small
companys
Basic standards for interfernce resistancet : DIN EN 50 082 Teil 2
Industrial
in accordance to the appointments of the
EC Directive 2004/108/EG
.
This manual suits for next models
1
Table of contents
Popular Controllers manuals by other brands
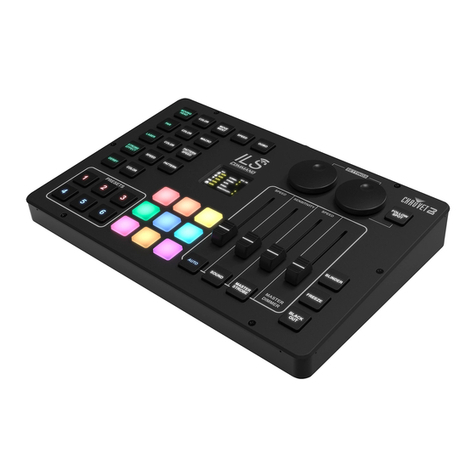
Chauvet DJ
Chauvet DJ ILS Command Quick reference guide
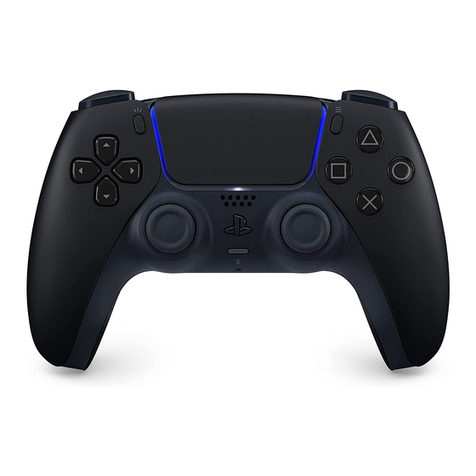
Sony
Sony DualSense CFI-ZCT1W instruction manual
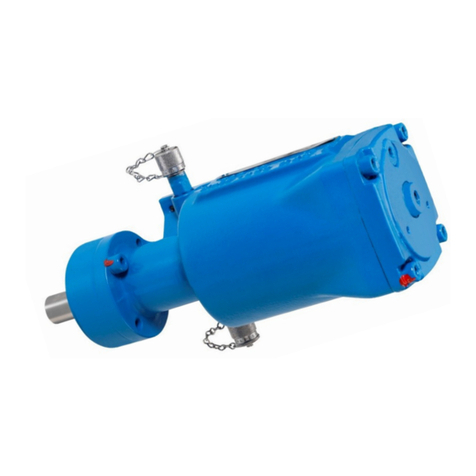
Econ
Econ Fig. 21401 Installation & operation manual
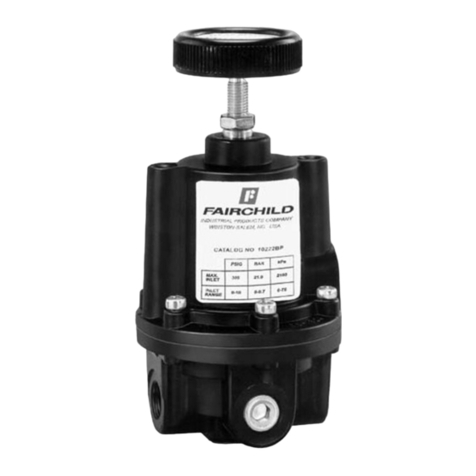
Fairchild
Fairchild 10BP Installation, operation and maintenance instructions
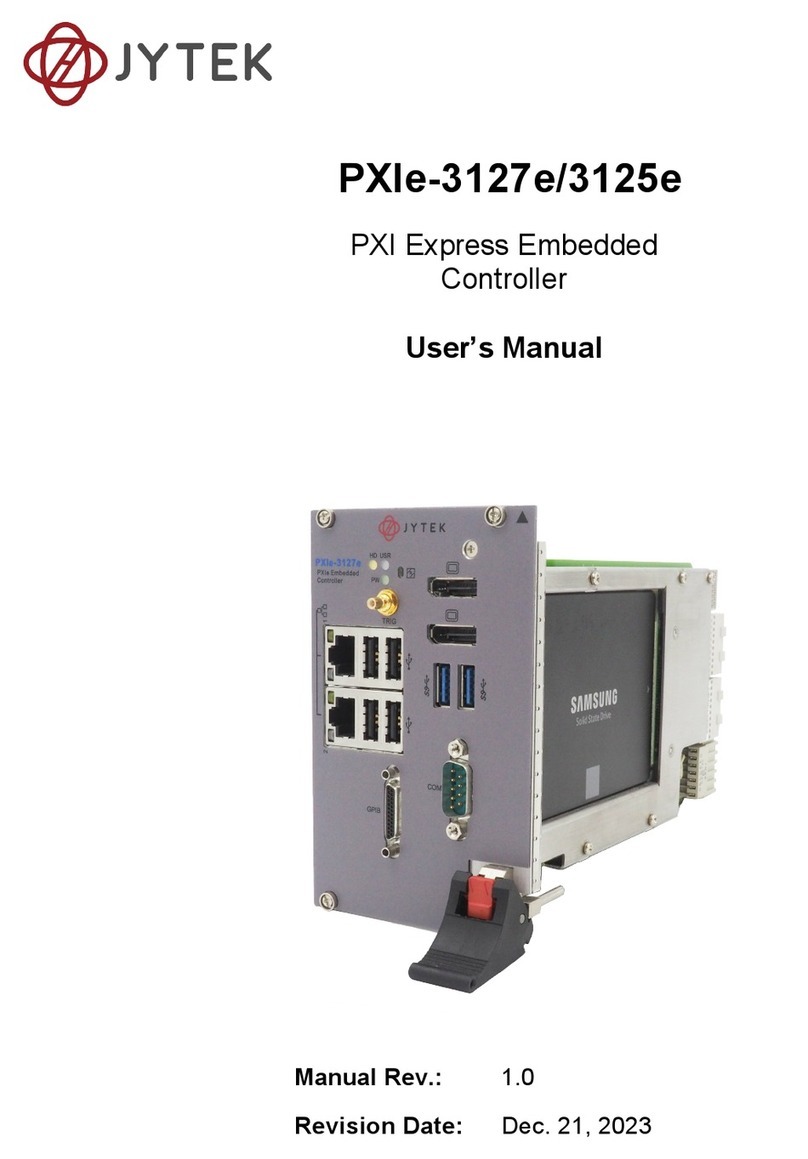
JYTEK
JYTEK PXIe-3127e user manual
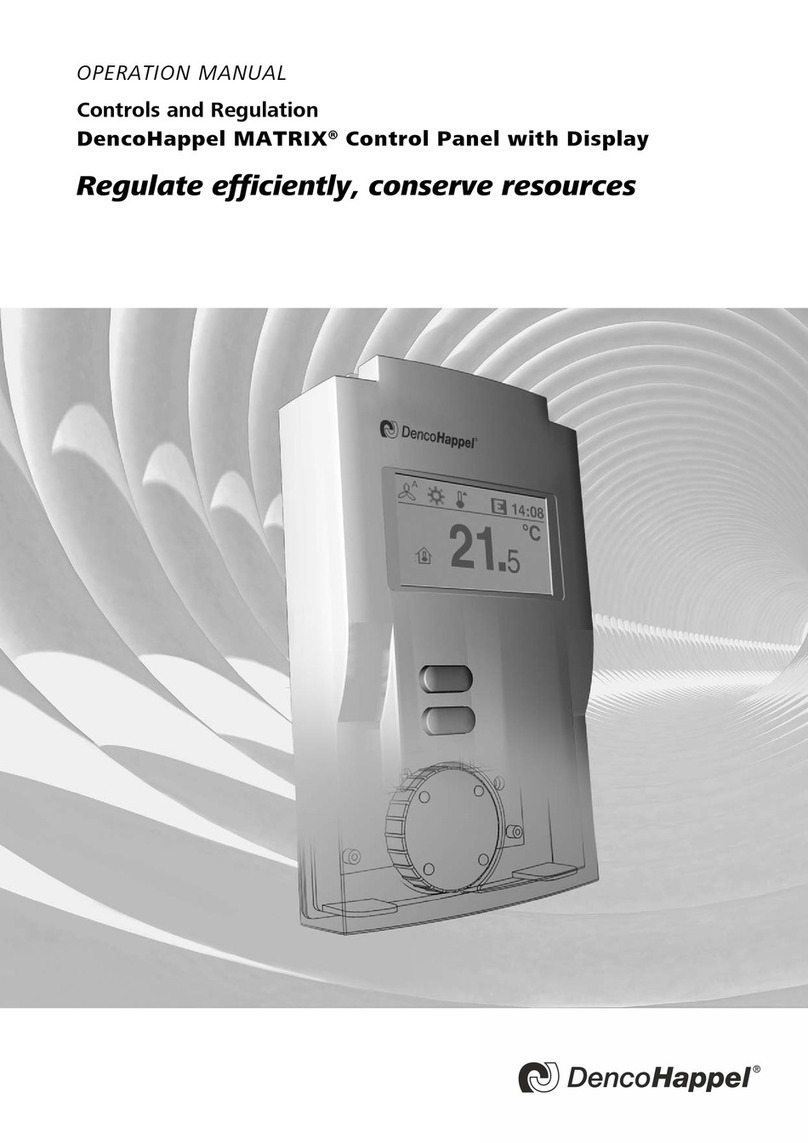
DencoHappel
DencoHappel MATRIX OP21C Operation manual
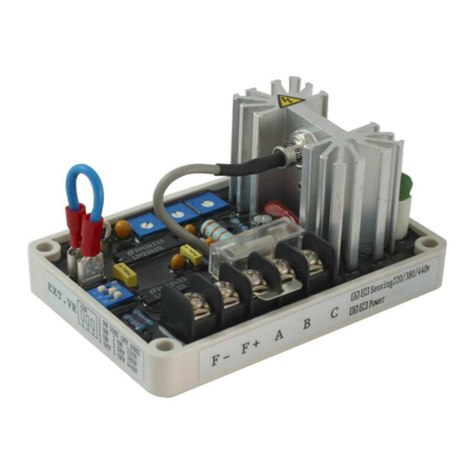
Kutai electronics
Kutai electronics EA05A Operation manual
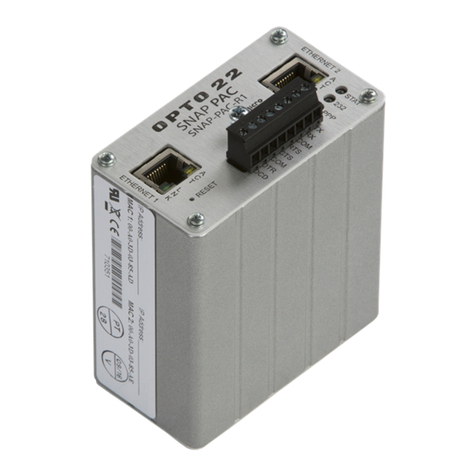
OPTO 22
OPTO 22 SNAP-PAC-R1 user guide
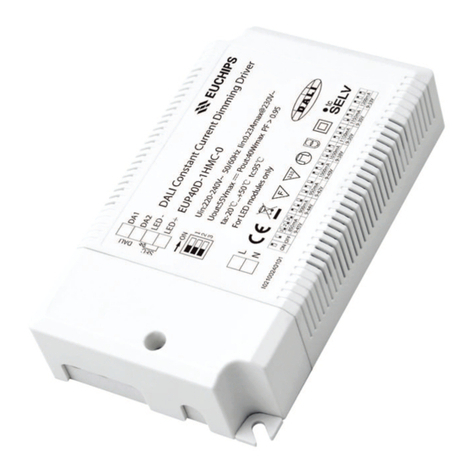
EUCHIPS
EUCHIPS EUP40D-1HMC-0 manual

Duff-Norton
Duff-Norton SK-2389 Installation, operation & maintenance instructions
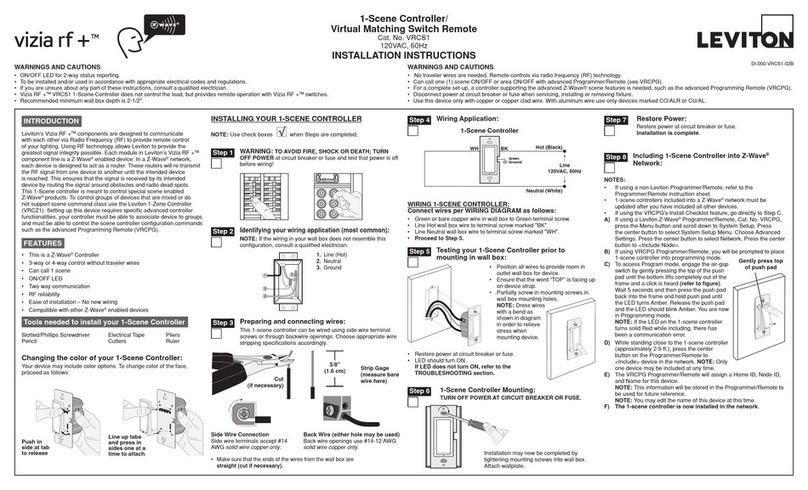
Leviton
Leviton vizia rf+ VRCS1 installation instructions
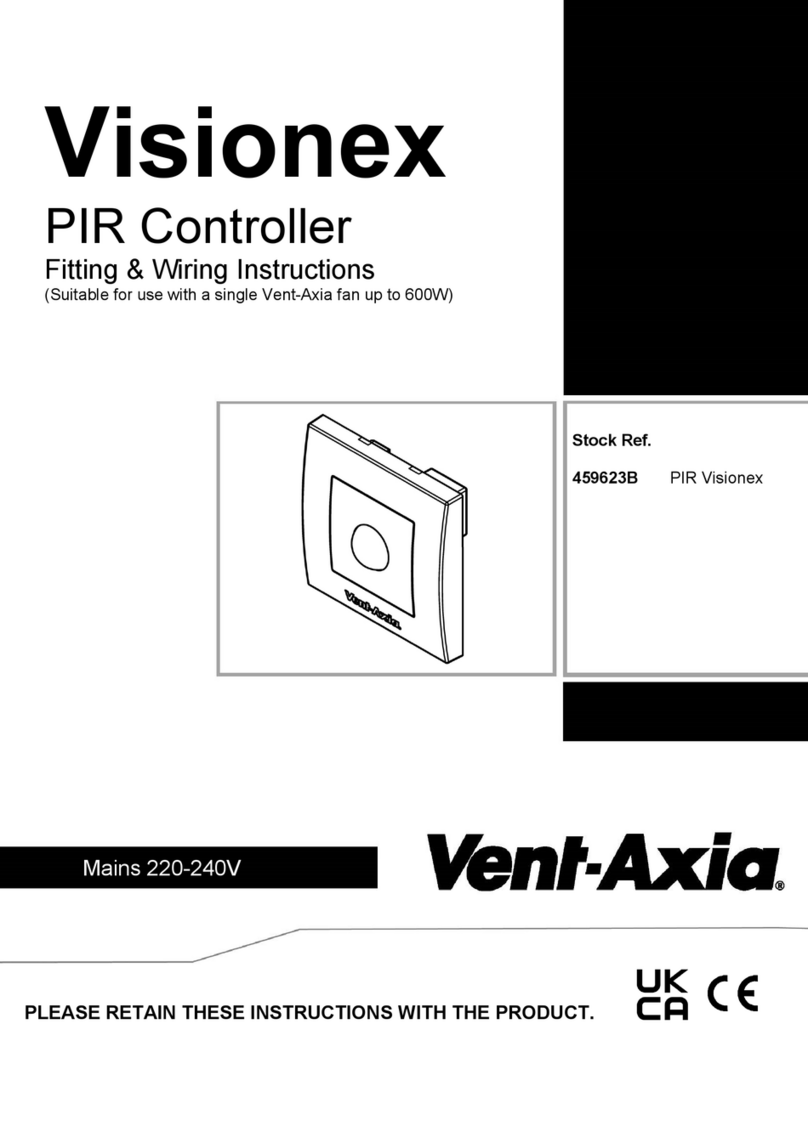
Vent-Axia
Vent-Axia Visionex Fitting & Wiring Instructions