Status Instruments SEM1750 User manual

D2533-01-07
SEM1750
USER INSTRUCTIONS
Important - Please read this document before installing.
Every effort has been taken to ensure the accuracy of this document; however, we do
not accept responsibility for damage, injury, loss or expense resulting from errors and
omissions, and we reserve the right of amendment without notice.
IMPORTANT – CE, UKCA & SAFETY REQUIREMENTS
Product must be DIN rail mounted, inside a suitable enclosure providing environmental
protection to IP65 or greater.
To maintain CE EMC requirements, input and supply wires must be less than 30
metres.
The product contains no serviceable parts, or internal adjustments. No attempt must be
made to repair this product. Faulty units must be returned to supplier for repair.
Before attempting any electrical connection work, please ensure all supplies are
switched off.
ABSOLUTE MAXIMUM CONDITIONS (To exceed may cause damage to the unit).
Working voltage terminals Inputs
± 75 V dc @ 75 mA dc
Working voltage terminals Outputs
± 30 V dc @ 50 mA dc
Supply voltage
(20 to 240) Vac 50/60 Hz or (20 to 240) Vdc,3 W
Input (SELV)
±50 Vdc or ±50 mAdc
Output (SELV)
Current (0 to 20) mA, Voltage (0 to 10) V
Ambient
Temperature (-20 to 70) °C
Approvals EN61010_1, EN61326
External supply
1 A anti-surge fuse recommended
Isolation supply to input/output
4250 V
Any input to output
3750 V
Output to output, input to input
3750 V
Important – Read this
document before installing.
---------------------------------------------------------------------------------------------------------------
1~DESCRIPTION.
SEM1750 is a dual channel signal conditioner designed to accept mA or voltage inputs
and provide isolated, industrial process output signals in mA or Volts. Each output
channel may be linked to either an input signal or to a maths function of both input
signals. This powerful feature allows the device to operate in several different modes.
The output signal can also be adjusted over the full working ranges (0 to 20) mA or (0 to
10) V, to provide common or custom process signals, examples (4 to 20) mA, (0 to
1)mA, (1 to 5) V. The SEM1750 is configured using the free software that allows the
user to configure the device without requiring calibration equipment. Maths functions on
each channel can be set up using the software as well as a 22-segment profile tool.
Input/output simulation tools for diagnostic purposes are also available.
2~RECEIVING AND UNPACKING.
Please inspect the packaging and instrument thoroughly for any signs of transit
damage. If the instrument has been damaged, please notify your supplier immediately.
3~SPECIFICATION.
Refer to data sheet for full specification. Download at www.status.co.uk
Factory defaults
Basic mode, dual channel operation, 420 ms update,
(Ch1, Ch2) = (4 to 20) mA input, (4 to 20) mA output
4~INSTALLATION AND WIRING.
Important safety requirements
This equipment is suitable for environment Installation category II pollution degree 1 and
is classed as "PERMANENTLY CONNECTED EQUIPMENT". The equipment is intended
for industrial and commercial application only and not suitable for domestic or medical
use.
The equipment must be mounted inside an enclosure that provides protection >= IP65.
In NORMAL USE, the equipment will only be accessed for maintenance by qualified
personnel. Please ensure the equipment is mounted vertically with terminals (101 to 204)
at the bottom. This will provide maximum ventilation. This equipment may generate heat:
ensure the enclosure size is adequate to dissipate heat. Be sure to consider any other
equipment inside the enclosure.
The equipment surfaces may be cleaned with a damp cloth. Use a mild detergent/water.
Ensure the supply is off before cleaning and on completion of cleaning the equipment is
completely dry before the supply is turned back ON.
This equipment must be installed by a qualified person. All electrical wiring must be
carried out in accordance with the appropriate regulations for the place of installation.
DC supply must be derived from a local supply and not a distribution system.
Supply (20 to 240) Vac 50/60 Hz (20 to 240) Vdc. If supply is a HAZARDOUS VOLTAGE,
a supply isolation switch must be installed close to the equipment with the “OFF”
position clearly marked. Also, the supply must be fused with a suitable 1 A (T) fuse
(circuit breaker) installed close to the equipment.
USB configuration can be performed without the supply being connected. For safety
reasons, use 24 Vdc for a functional test of the unit prior to fixed installation. The
following operations should only be carried out on a disconnected device and under
ESD safe conditions: General mounting, connection and disconnection of wires.
4.1~MECHANICAL.
The equipment must be mounted on a DIN rail style DIN EN50022 inside a plastic or
metal enclosure with a protection level >= IP65. All wiring must be secured. Maximum
cable sizes 2.5 mm. Connection two-part screw terminals.
4.2~ELECTRICAL
CONNECTIONS
For wiring connections, refer to the side label on the SEM1750 and this document.
For channel one use pins 101 to 108, for channel two use pins 201 to 208
SUPPLY
(20 to 240) V dc 50/60 Hz
(20 to 240) V dc
Ma x Powe r 3W
S1 -
S2 +
INPUTS
(4 to 20) mA TX
Tx
202102
204104
+
-
mA
202
102
201101
+
-
Vdc
201101
203103
+
-
Volts
208108
OUTPUTS
Vdc
LOAD
207107
External Powered mA
+
-
205105
207107
Internal Powered mA
LOAD
207107
Vout
206106
Voltage Output
+
-
205105
+
-
+
-
LI NK P IN 107 AND 106 (207, 206)
Input connections for cable length >3 metres: use screen or twisted pair cables. Max
cable run 30 metres.
Output connections for cable length >3 metres: use screen or twisted pair cables. For
current outputs max cable run 1000 metres, Voltage output 30 metres.
Supply maximum cable run 30 metres. As stated in the IMPORTANT SAFETY
REQUIREMENTS the supply must be fused with a 1A (T) fuse and provision provided
to isolate the circuit when hazardous voltages are being switched.
LED front panel indication.
Channel 1 and channel 2 LEDs show green for in range input condition.
Channel 1 and channel 2 LEDs show red for out of range input condition.

D2533-01-07
5~USER CONFIGURATION.
Read the Important safety requirements
PC CONFIGURATION
During configuration the equipment takes its power from the USB port, therefore no
power connection is required. The equipment can be configured whilst powered but the
computer used must be isolated from the supply earth to avoid grounded earth loop
effects.
Device
U SBSP EED LI NK s oftwa r e
USB CABLE
COMPUTER
Configuration steps using USBSpeedLink
Download install and run USBSpeedLink
Connect device to PC using an A to mini B USB lead
Upload device set-up into the configuration software, “Basic” and “Advanced”
options are available for configuring the device
Adjust settings as required
Send new configuration to the device
USBSpeedLink software configuration screen for SEM1750
Note: When the device is correctly connected, the “Send” and “Receive” menu buttons
will turn black and the “data” section of the screen will open on the right.
Advanced configuration screen shown
Sample Rate
Select: (420, 140, 70) ms update rate. A faster response time will reduce accuracy.
Input (Ch1 and Ch2)
Select: input type mA or V
Input Pre-set (Ch1 and Ch2)
This will open a box to enter a value for the input (mA or V) that the device will take as
its input condition. The actual input will be ignored while this input pre-set is selected.
The device will respond accordingly to the pre-set input value on its output.
Damping seconds mA/V (Ch1 and Ch2)
User-adjustable damping of the analogue output is provided for both rising and falling
signals. The adjustable range is (0 to 3600) s for a 1 mA or 1 V swing.
Example: If the damping value is set at 2 s (per mA) then a 5 mA change on the input
will take 10 s on the output to respond fully.
Segments (Ch1 and Ch2)
Controls the number of mA/V input to output points
This will normally be used to range the electrical input mA/V to the relevant engineering
unit °C, bar, lt/min for example.
For a straight-line alignment only 3 points need to be used.
More segments can be used if required to control out of limit conditions.
Up to 22 user-segments can be used to create a user curve or non-linear relationship
table, for example to represent the volume in a non-linear tank. This can also be used
to correct or calibrate an input sensor.
Units (Ch1 and Ch2)
This allows the user to enter the engineering units for the input to output relationship
Tag (Ch1 and Ch2)
This allows the user to enter text description that is saved to the device.
OUTPUT (Ch1 and Ch2)
A list of output options is available from a drop-down box.
The most common selection will be to match channel input to channel output, however,
both output channels can have the same input selected, making the device into a signal
splitter
Other options are available including maths functions and a fixed output option that may
be used as a diagnostics tool.
OUTPUT Units (Ch1 and Ch2)
Select the range in engineering units that is to be scaled to the analogue output signal.
OUTPUT SIGNAL (Ch1 and Ch2)
Select mA or V and the output range to be scaled to the engineering range. This can be
any value within the physical capability of the device.
For a voltage output, the output load value, if known, can also be entered.
OUTPUT SIGNAL (Ch1 and Ch2)
Select mA or V and the output range to be scaled to the engineering range. This can be
any value within the physical capability of the device.
For a voltage output, the output load value, if known, can also be entered.
Menu Options
The configuration can be saved to PC file for back up and re-use as required.
The USBSpeedLink software will allow live readings to be taken from the device
showing input and output conditions.
For diagnostic use, the device can save live readings to a text file on the PC.
USBSpeedLink configuration software is available online at www.status.co.uk
This guide is also available online at www.status.co.uk
Status Instruments Ltd, Status Business Park, Gannaway Lane, Tewkesbury, Gloucestershire, UK, GL20 8FD,
Web Page: www.status.co.uk,
Technical Support: support@status.co.uk
Tel: +44 (0) 1684 296818, Fax: +44 (0) 1684 293746
Other Status Instruments Test Equipment manuals
Popular Test Equipment manuals by other brands
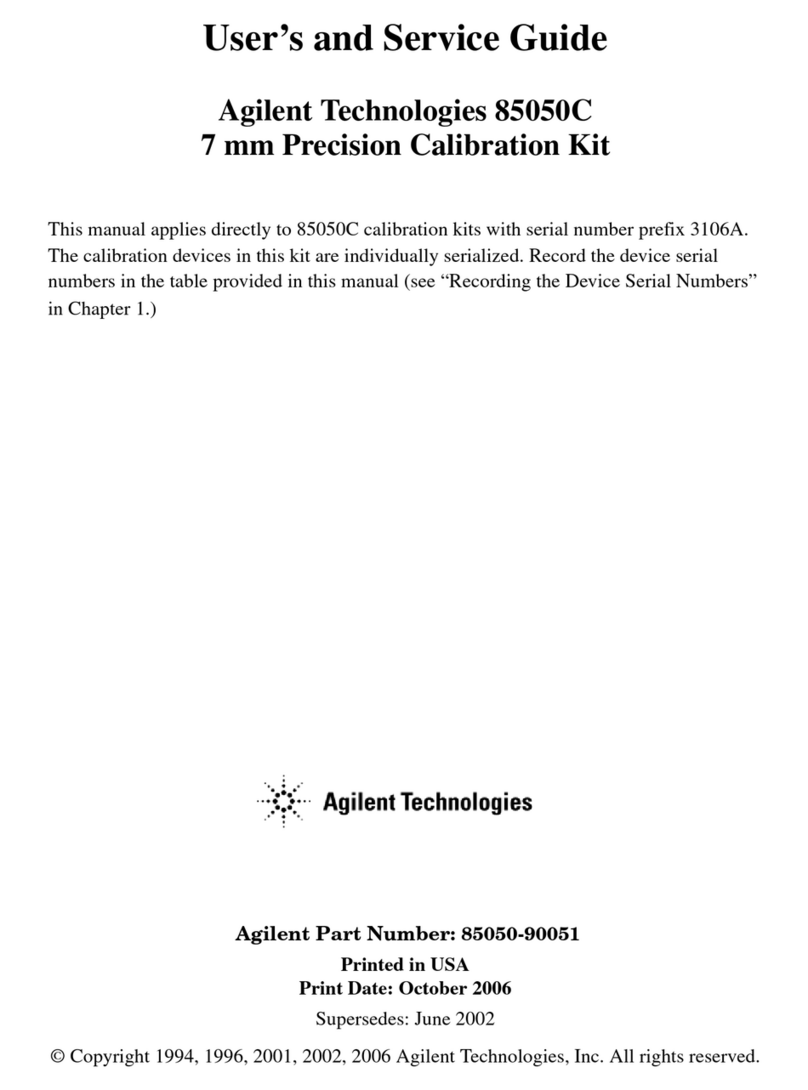
Agilent Technologies
Agilent Technologies 85050C User's and service guide
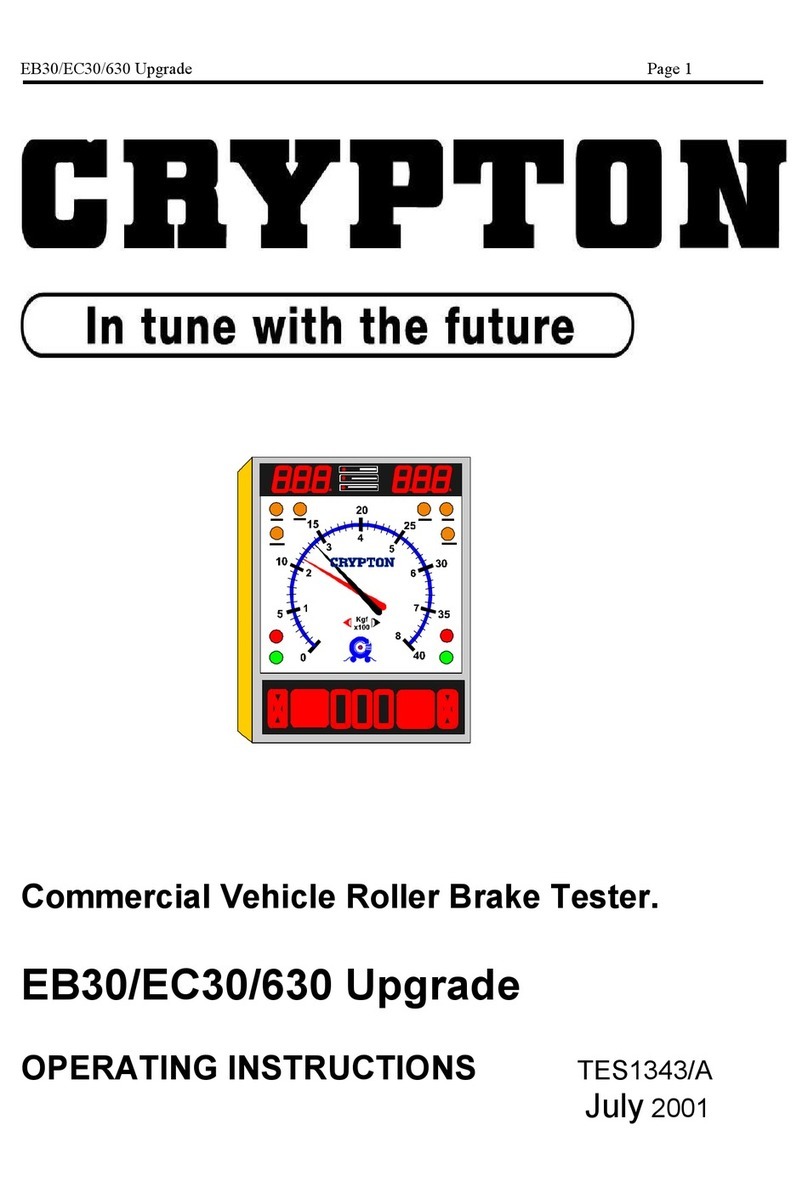
CryptOn
CryptOn EB30 operating instructions
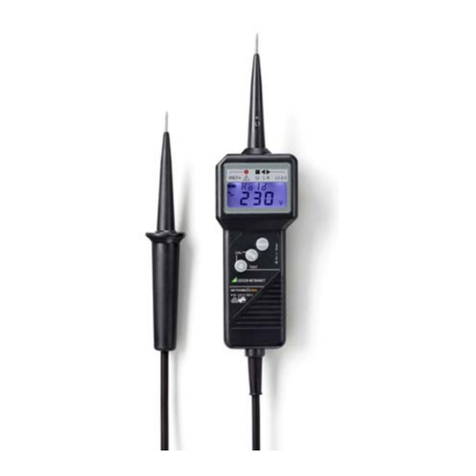
Gossen MetraWatt
Gossen MetraWatt METRAVOLT 12D+L operating instructions
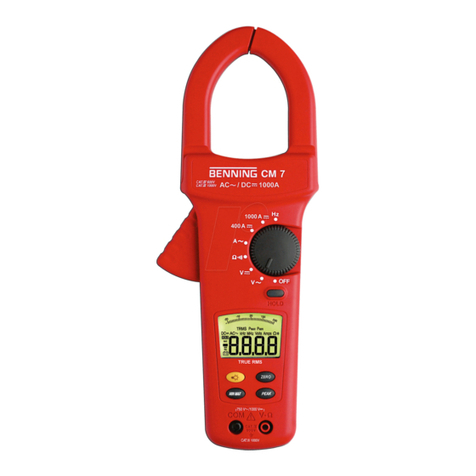
Benning
Benning CM 7 Service information
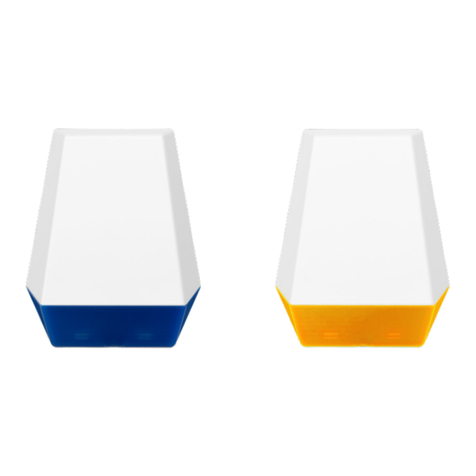
Rosslare
Rosslare SA-95L installation manual
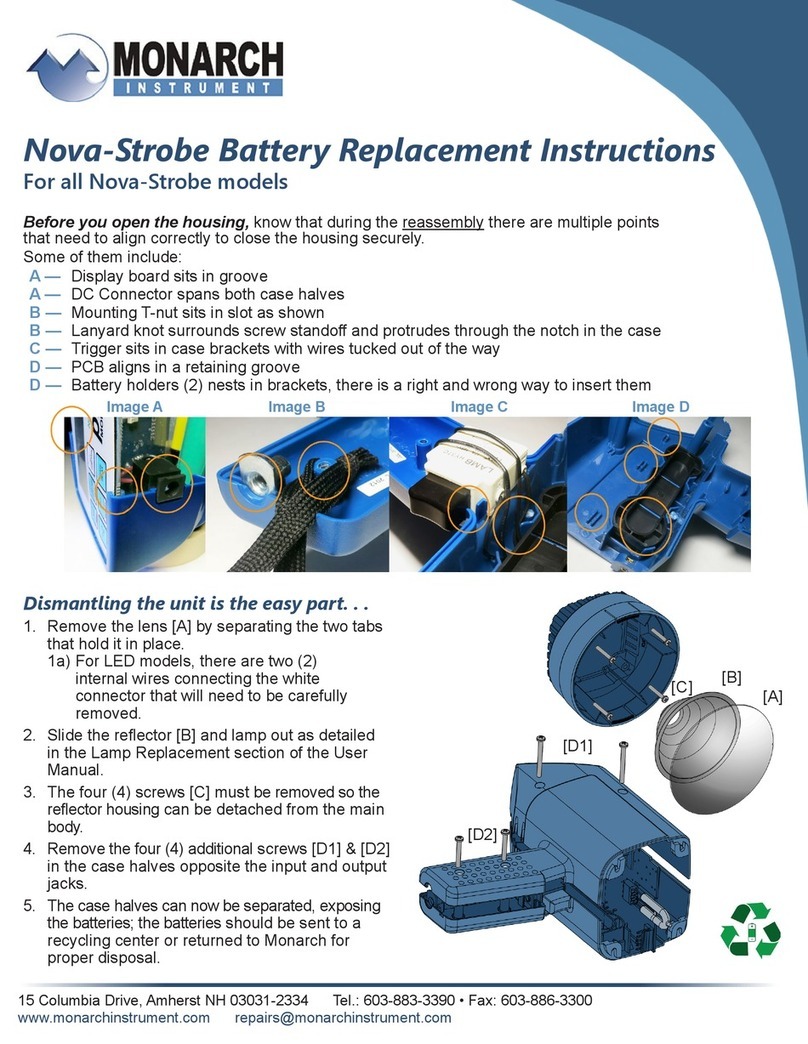
MONARCH INSTRUMENT
MONARCH INSTRUMENT Nova-Strobe BATTERY REPLACEMENT INSTRUCTIONS