stellar labs STA2000 Series User manual

Antenna Mount Amplifier
For Satellite Communications
Operation Manual
Type STA2000 Series
Whilst e2v technologies has taken care to ensure the accuracy of the
information
contained herein it accepts no responsibility for the consequences of any use thereof
and also reserves the right to change the specification of goods without notice. e2v technologies accepts no liability beyond the set out in its standard conditions of sale in
respect of infringement of third party patents arising from the use of tubes or other devices in accordance with information contained herein.
e
2v technologies (uk) limited, Waterhouse Lane, Chelmsford, Essex CM1 2QU United Kingdom Holding Company: e2v technologies plc
T
elephone: +44 (0)1245 493493 Facsimile: +44 (0)1245 492492
Contact e2v by e-mail: enquiries@e2v.com or visit www.e2v.com for global sales and operations centres.
© e2v technologies (uk) limited 2010 DAS768892AA Version 1, March 2010
108210

This Operation Manual covers the following amplifier
type numbers:
STA2175, STA2275, STA2375, STA2T45, and
STA2450 Series (including all derivatives).
SAFETY NOTES
The following warnings and precautions are for your safety and the prevention of injury. Please read
them carefully and observe at all times when installing or operating a Stellar Travelling Wave Tube
Amplifier. Hazard warning signs, as defined in BS5378 Safety Signs and Colours, are used on the
equipment to highlight any possible hazards.
Earthing
The mains supply connection cable to the amplifier must include an electrical safety protective earth
conductor, installed and connected to the local distribution system earthing point in conformance with
local regulations. The electrical safety protective earth conductor must be capable of carrying 20A
and must be from an approved manufacturer (2.5 mm2/12 AWG).
An external protective earth, also providing protection against RF and transient currents, must be
connected between the amplifier and an adjacent earth point before applying the mains supply and
should only be removed after disconnecting the amplifier from the supply. The external protective
earth conductor must be a flat copper strap, braided or plain, and must be capable of carrying 30A.
The length of external protective earth conductor must not exceed 400mm.
Mains Supply
A mains supply disconnection device must be provided to isolate this amplifier from the mains supply
source. Either a plug/socket outlet or a two-pole isolation switch must be used as the mains supply
disconnection device, and it must be easily accessible. The connector on the amplifier is NOT
suitable, and must not be used to disconnect the amplifier when powered.
Toxic Material
The Travelling Wave Tube (TWT) within the amplifier contains beryllium oxide. Dust created by
breakage, or fumes from a beryllium oxide fire, are highly toxic if inhaled, or if particles enter the body
via a cut or abrasion.
Consult e2V technologies and the appropriate national authorities for details regarding the disposal of
damaged or old TWTs and amplifiers.
© e2v technologies (uk) limited 2010 DAS768892AA Version 1, page 2

High Voltage
High voltages in excess of 11.5kV are present within the amplifier. However, the equipment is
designed so that personnel cannot come into contact with high voltage circuits unless the covers are
removed.
Access inside the amplifier is restricted to suitably skilled engineers.
RF Radiation
Exposure of the human body to microwave radiation can constitute a hazard (ANSI/IEEE C95-1-
1992). Personnel must be protected from microwave energy produced by the TWT.
All RF connectors must be correctly fitted before operation, so that there is no leakage of RF energy.
The amplifier must not be operated unless the RF output connection is correctly terminated. It is
particularly hazardous to look into open waveguides, coaxial feeders, or transmitter antennae when
the amplifier is operating.
Input Drive
Damage to the amplifier may occur if the RF input drive level or the input frequency are outside the
limits given in the specification for the model (see section 1.1).
Environmental
•Do not block, or poke objects through, the amplifier ventilation slots.
•Do not spray aerosol cleaners directly on to the amplifier surfaces when cleaning.
•or unsafe surface.
pped over or damaged by furniture or movable
equipment.
•
STA
provided if
necessary.
•EEC Directive 89/336/EEC Electromagnetic compatibility.
•EEC Directive 73/23/EEC Low voltage directive.
•CETLus listed to ANSI/UL 60950-1-2002 & CAN/CSA22.2 No. 60950-1-03.
e2v technologies’ quality management system is certificated to the requirements of ISO9001:2000.
Do not operate the amplifier on an unstable
•Ensure that all cables cannot be walked on, tri
•Do not place objects inside the waveguide.
Ensure exhaust air is not re-circulated.
NDARDS COMPLIANCE
Stellar amplifiers comply with the following requirements. Further details may be
© e2v technologies (uk) limited 2010 DAS768892AA Version 1, page 3

CUSTOMER CARE
Stellar 24-Hour Hotline
In the event of a Stellar product operational problem or urgent application enquiry:
1. Complete a Product Service Report Form before calling the Hotline. A copy can be found at the
back of this manual.
2. Contact the Stellar Hotline on +44 (0)1245 355398, where your enquiry will be dealt with.
Return Procedure
In the event of a Stellar product requiring return to e2v technologies:
1. Have as many of the following details as possible to hand before contacting e2v technologies.
This will help us to respond promptly to your request.
•Type number (found on the panel adjacent to the RF output).
•Serial number (found on the panel adjacent to the RF output).
n damaged?
ting
lure. The form must be returned
4. ing is in good condition, use it to return the product. If the original packaging
ologies can supply suitable replacement packaging for a small charge.
5. ackaging with the following information:
Type number
•Serial number
•Return address.
For further details, refer to the e2v technologies Standard Conditions of Warranty, a copy of
which can be found at the back of this manual.
•Has the product bee
•Description of any operational fault or problem.
•Return address.
2. The Customer Service Team will issue you a Reference Number for the return.
t the back of this manual), no
3. Complete a Product Service Report Form (a copy can be found a
in particular any unusual occurrences before or at the time of fai
with the product.
If the original packag
is damaged, e2v techn
Clearly mark the outer p
•Reference number.
•
© e2v technologies (uk) limited 2010 DAS768892AA Version 1, page 4

CONTENTS
1THANK YOU FOR BUYING STELLAR......................................................................................................7
1.1 RANGE OF OPTIONS ........................................................................................................................7
2CARE OF YOUR AMPLIFIER ....................................................................................................................9
2.1 STORAGE...........................................................................................................................................9
2.2 HANDLING..........................................................................................................................................9
2.3 UNPACKING .......................................................................................................................................9
2.4 CLEANING ..........................................................................................................................................9
2.5 MAINTENANCE ..................................................................................................................................9
3INSTALLATION CONSIDERATIONS ..................................................................................................... 10
3.1 MOUNTING...................................................................................................................................... 10
3.2 RF CONNECTIONS ......................................................................................................................... 11
3.3 COOLING CONSIDERATIONS ....................................................................................................... 11
3.3.1 Some Cooling Facts and Figures ............................................................................................ 11
3.3.2 Ducting Considerations ........................................................................................................... 12
3.3.3 Equipment Housing ................................................................................................................. 12
3.3.4 Commissioning the Installation................................................................................................ 13
3.4 MAINS SUPPLY CONNECTION ..................................................................................................... 13
3.4.1 Mains Supply Cable Connection ............................................................................................. 13
3.4.2 Earthing ................................................................................................................................... 14
3.4.3 Mains Supply Distribution ........................................................................................................ 14
3.5 USER INTERFACE CONNECTIONS .............................................................................................. 14
3.6 REDUNDANT SWITCH CONFIGURATION .................................................................................... 14
4BASIC OPERATION OF THE AMPLIFIER ............................................................................................. 16
4.1 APPLYING THE MAINS VOLTAGE................................................................................................. 16
4.2 MAINS SUPPLY INTERRUPTIONS ................................................................................................ 16
4.3 FUNCTIONS .................................................................................................................................... 16
4.3.1 Amplifier Off State ................................................................................................................... 16
4.3.2 Amplifier Warm-up State ......................................................................................................... 16
4.3.3 Amplifier Standby State ........................................................................................................... 16
4.3.4 Amplifier Transmit State .......................................................................................................... 17
4.4 UP-CONVERTER OPERATION ...................................................................................................... 17
4.5 RF SAMPLE PORT .......................................................................................................................... 17
5USER INTERFACES............................................................................................................................... 18
5.1 PIN IDENTIFICATION...................................................................................................................... 18
5.2 USER INTERFACE FEATURES...................................................................................................... 19
5.2.1 Indicator Outputs – Type 1 ...................................................................................................... 19
5.2.2 Indicator Outputs – Type 2 ...................................................................................................... 20
5.2.3 Analogue Outputs.................................................................................................................... 20
5.2.4 Control Inputs – Type 1 ........................................................................................................... 20
5.2.5 Control Inputs – Type 2 ........................................................................................................... 21
5.2.6 Control Inputs – Type 3 ........................................................................................................... 21
5.2.7 Miscellaneous Functions. ........................................................................................................ 22
6RS-485 SERIAL BUS .............................................................................................................................. 23
6.1 GENERAL DESCRIPTION AND FEATURES ................................................................................. 23
6.1.1 HPA Type? .............................................................................................................................. 23
6.1.2 Status?..................................................................................................................................... 23
6.1.3 General Amplifier Control ........................................................................................................ 25
6.1.4 Redundancy Mode .................................................................................................................. 25
6.1.5 Power Alarms .......................................................................................................................... 25
6.1.6 Warm-up Time?....................................................................................................................... 25
6.1.7 Attenuator Control ................................................................................................................... 25
6.1.8 RF Control ............................................................................................................................... 26
6.1.9 Helix Current Monitoring.......................................................................................................... 26
6.1.10 Elapsed Hours? ....................................................................................................................... 26
6.1.11 Forward Power? ...................................................................................................................... 26
6.1.12 Interface set-up........................................................................................................................ 26
6.1.13 RF band selection.................................................................................................................... 27
6.2 PROTOCOL ..................................................................................................................................... 28
6.2.1 Interface and Termination........................................................................................................ 28
6.2.2 Data Format............................................................................................................................. 28
6.2.3 Data Rate................................................................................................................................. 28
6.2.4 Generalised Message Format ................................................................................................. 28
6.2.5 Command Message Format .................................................................................................... 29
6.2.6 Response Message Format .................................................................................................... 29
© e2v technologies (uk) limited 2010 DAS768892AA Version 1, page 5

6.2.7 Message Timing ...................................................................................................................... 29
6.2.8 Summary of Command Messages .......................................................................................... 29
6.3 EXAMPLES OF COMMAND AND RESPONSE MESSAGES......................................................... 30
6.3.1 Simple Command Message (no return of data) ...................................................................... 30
6.3.2 Command Messages Requesting data ................................................................................... 31
6.3.3 Universal Command Messages Requesting Data................................................................... 31
6.3.4 Command Messages Requesting Longer Data Strings .......................................................... 33
6.3.5 Command Messages Passing Parameters ............................................................................. 33
6.3.6 Response to an invalid command message............................................................................ 33
6.4 APPLICATION NOTES .................................................................................................................... 34
7RELATED DOCUMENTS........................................................................................................................ 35
8APPENDICES ......................................................................................................................................... 36
8.1 APPENDIX A.................................................................................................................................... 36
8.2 APPENDIX B.................................................................................................................................... 37
8.3 APPENDIX C.................................................................................................................................... 38
8.4 APPENDIX D.................................................................................................................................... 39
8.5 APPENDIX E.................................................................................................................................... 40
© e2v technologies (uk) limited 2010 DAS768892AA Version 1, page 6

1 THANK YOU FOR BUYING STELLAR
Thank you for buying a Stellar Travelling Wave Tube Amplifier (TWTA). This antenna mount amplifier
range from e2v technologies provides RF power outputs up to 750W and operates in the frequency
bands shown in figures 1 and 2. The amplifier is:
•Compact.
Lightweight.•
•Portable – can run off a wide range of mains input voltages and frequencies.
•Designed for high reliability.
Before using your new amplifier, we recommend that you spend
familiarise yo eration and features.
a little time to read this manual to
If y s, or recommendations about this manual, please contact your
dist
In addition to this manual your amplifier should be supplied with:
•Test results.
B (for Ku, DBS and Tri band).
ble mains cable, connecting plug and residual
1.1 RA E
he STA2000 series of antenna mount amplifiers includes the following RF system options (see
gures 1 and 2).
•Low gain (no solid-state pre-amplifier).
•Integral solid-state pre-amplifier (fixed gain).
•Integral solid-state pre-amplifier (digitally variable gain) using serial bus.
•Integral linearizer.
•Internal L-band block up converter.
•Breakout link (for use with internal up converter).
urself with its op
ou have any further question
ribu or.
t
•A mains connector.
•A control connector plug.
•Air cowl.
•Waveguide screws, 8 off 10-32 UNF-2B (for C-band), 8 off 8-32 UNC-2B (for X-band), 4 off 6-
32 UNC-2
•Note: for installation you will require a suita
current circuit breaker (RCCB) (see section 3.4).
NG OF OPTIONS
T
fi
© e2v technologies (uk) limited 2010 DAS768892AA Version 1, page 7

Figure 1
Figure 2
© e2v technologies (uk) limited 2010 DAS768892AA Version 1, page 8

2 CARE OF YOUR AMPLIFIER
2.1 STORAGE
•Store the amplifier in its normal horizontal orientation.
xes to support the weight of any other item.
•amplifier boxes for future use.
ing to lift or carry it.
2.4
s. A maintenance
(this can be seasonal,
t pending) enables the unit to
perate in extreme environmental conditions, from direct rain to direct sunlight.
t use detergents or other cleaners without consulting e2v technologies. The
.
2.5
e checked regularly for blockages (see section 2.4).
depending upon environmental conditions. The
pical life of desiccant is 5 years in sub-tropical conditions, assuming that the seal on the lid has not
een disturbed.
heck the mains cable for damage.
•.Storage temperature is from –40 to –80˚C
•Do not use amplifier bo
Retain the
•Avoid severe shocks.
2.2 HANDLING
The amplifier nominally weighs 34 kg, so care must be taken when attempt
2.3 UNPACKING
Only install and use the amplifier within the specified environmental limits.
CLEANING
The amplifier is designed for use in harsh environments without additional protective covers. The
internal forced-air cooling system relies on the internal and external airways being free from
blockages. The cooling air enters and exits the unit through slotted panels designed to prevent large
items of foreign matter from entering and potentially blocking the internal airway
plan should be developed to check and clean the amplifier slotted panels regularly. The frequency of
cleaning will be dependent upon the installation and the environment. The maintenance plan should
be regularly reviewed and modified according to changes in the environment
e.g. airborne seed pods can cause regular blockages at certain times of the year).
he advanced packaging and cooling techniques (Stellar Cool TM, paten
T
o
When cleaning, do no
amplifier must be disconnected from the mains supply before cleaning
MAINTENANCE
Airways should b
D
ty
esiccant should be replaced every 3 to 5 years,
b
C
© e2v technologies (uk) limited 2010 DAS768892AA Version 1, page 9

3 INS ATIONS
M T
chosen platform (see figure 3). Suitable load spreading
ashers, locking nuts and/or locking washers should be used to prevent the amplifier from working
ose under vibration and shock conditions that each installation may impose. This is especially
nto the
ntation of
amplifier is
TALLATION CONSIDER
3.1 OUN ING
The amplifier can be:
•Used free standing.
•Mounted in a flight case.
•Mounted on the roof of a vehicle.
•Mounted to an antenna system.
The amplifier has six M6 mounting points (three each side, 10 mm maximum depth), which can be
used to mount the amplifier solidly to the
w
lo
important for mobile applications.
Where possible, the amplifier should be positioned to avoid the direct entry of rainwater i
ventilation slots. The amplifier is provided, as standard, with an air cowl, the normal orie
which is pointing towards the base of the unit avoiding the direct entry of driving rain.
Note: There is a drainage hole in the cover to prevent the build-up of water if the
inadvertently mounted or left upside-down.
Figure 3
l 5 mm clearance from any adjacent equipment or
mechanical interference due to tolerances on equipment parts and/or
mini
If the am in cover is used, the air cowl may be removed.
When de
bend rad les (see figure 3).
The amplifier should be mounted with a nomina
surface. This will avoid
movement under operational vibration.
If the amplifier is to be fitted against a flat surface, a flexible gasket material should be used to
mise excessive noise in mobile applications.
plifier is to be installed where a secondary ra
signing the installation, a space at the end should be allowed for the disconnection and the
ius of connection cab
© e2v technologies (uk) limited 2010 DAS768892AA Version 1, page 10

3.2 RF C N
RF i
amp
•
•
Waveguide type WG17 or WG75 may be used. The RF output is UBR120, with
four tapped holes 6-32 UNC requiring four bolts (6-32 UNF-2B, maximum internal thread
d with sufficient bolts for this flange.
sufficient
rain or subjected to condensation,
ll attempts should be made to prevent moisture ingress into the waveguide system. It is
guide joints are made using flanges fitted with ‘O’ rings to prevent
iven is only general. Any
3.3.1
....................................................................................... 1600W
r cooling system and is equipped with two thermal
continuously
fan will rotate
at th s llector.
When th
change
red d
cooling ecessary. When normal
irflow is confirmed, the amplifier can be placed back into the transmit state.
he amplifier is automatically placed in the off state if the over-temperature condition exists for more
than 4 minutes. The mains supply should be removed and the amplifier isolated before a full
O NECTIONS
nput and output connections are made via waveguide connectors on opposite ends of the
lifier.
C-Band. Waveguide type WG14 should be used. The RF output is CPR 137F, with eight
tapped holes 10-32 UNF-2B (maximum internal thread depth 8mm). The amplifier is
provided with sufficient bolts for this flange.
X-Band. Waveguide type WG15 should be used. The RF output is CPR 112G, with eight
tapped holes 8-32 UNC-2B requiring eight bolts. The amplifier is provided with sufficient
bolts for this flange.
•Ku-Band.
depth 8mm). The amplifier is provide
•DBS-Band. Waveguide type WG18 should be used. The amplifier is provided with sufficient
bolts for this flange, (4 off 6-32 UNC-2B).
•Tri-Band. Waveguide type WRD580 should be used. The amplifier is provided with
bolts for this flange, (4 off 6-32 UNC-2B).
RF input signals applied must be within the frequency range specified for the particular amplifier type
(see figure 1and 2). The maximum RF input drive level should not exceed +10dBm for pre-amplifier
option C and -10dBm for pre-amplifier options A, D or Z.
f the amplifier is to be used in applications where it is exposed to
I
a
recommended that all external wave
moisture ingress.
3.3 COOLING CONSIDERATIONS
Temperature affects the life and reliability of high power electronic devices. As the temperature of the
device increases, generally reliability and life expectancy decrease; TWTAs are no exception. Please
follow the cooling considerations for your amplifier to ensure many trouble free years of use.
Engineers at e2v technologies have many years of experience working with customers to integrate
equipment successfully and to ensure that long and reliable product lives are achieved. The
information contained within this section has been gained from both field experience and theoretical
cooling system design knowledge. As most installations differ, the advice g
specific aspects of installation design can be discussed further by contacting (by telephone, fax or e-
mail) the Stellar Product Support Team at e2v technologies.
Some Cooling Facts and Figures
Minimum air flow................................................................................................ 112 litre/sec 240 ft3/min
Minimum duct area .........................................................................................................250 cm2(39 in2)
Typical internal power dissipation (no RF drive):
C- or X-band.......................................
Ku- or DBS band ....................................................................................................................... 1500W
Tri-band ................................................................................................................................... 1800W
The amplifier utilises an efficient, integral, forced-ai
sensors to protect it in the event of an over-temperature condition. The cooling fan has a
variable speed of rotation so that, when the amplifier is operating normally, the cooling
e lowest speed consistent with adequate cooling of the TWT co
e temperature of either thermal sensor exceeds preset levels, the amplifier will automatically
state from transmit to fault. In the fault state, the dissipation within the amplifier is greatly
uce and if the airflow is normal, the amplifier will rapidly cool. At this stage, the installation
system should be visually inspected for blockages and cleaned as n
a
T
© e2v technologies (uk) limited 2010 DAS768892AA Version 1, page 11

inspection is made of the installation cooling system. The amplifier should be left for 20 minutes
e sections 5 and 6).
e air exhaust.
•event hot exhaust air from re-circulating to the cooling
n designing common ducting systems for multiple amplifiers.
e
3.3.2
ction 3.1). The cowl can be turned through 180° for
lternative mounting configurations. The cowl is designed to avoid driving rain entering the unit if a
ed.
•
•re restrictive to airflow.
•
•Do not use ducting adaptors that reduce the internal cross-sectional area of the ducting.
ct systems, install additional external fans to provide adequate
3.3.3 Equ m
All equ light cases, roof mount enclosures, cabins and air-
con
•Maintain an adequate supply of air to the inlet; a 250 cm (39 in2) unimpeded aperture should
be provided into any enclosure for each Stellar amplifier.
nation of cooling air should be ideally be common, to avoid back-
Housings that are exposed to environmental wind effects should use a common face inlet for
st vents should be of a design that prevents direct
environmental wind effects, whilst avoiding creating additional restriction to airflow.
before any attempt is made to restart.
Following an over-temperature condition, the TWT COLLECTOR TOO HOT or CASE TOO HOT fault
conditions are set. These conditions can be monitored via the user interface or accessed through the
serial communications port (se
When deciding on the location of the amplifier the following points should be observed:
•It is important not to obstruct the air inlet or th
In any system, it is mandatory to pr
inlet, otherwise the air temperature will increase, resulting in potential thermal runaway. This
is a prime consideration whe
•In any other instance, if there is significant additional obstruction to the airflow, then it may b
necessary to provide externally forced or cooled air to the amplifier.
Ducting Considerations
The amplifier is provided as standard with one air cowl, the normal orientation of which is pointing
owards the base of the amplifier (see se
t
a
secondary cover is not us
Any ducting connected to the air inlet or exhaust will create additional back-pressure, reduce the
airflow and increase the internal temperature of the amplifier. Additional ducting should be avoided if
possible, but if it is essential for the application then:
•Keep ducting lengths to a minimum. Check the amplifier maximum operating temperature de-
rating for the length of duct required.
•Route ducting directly, avoid sharp bends and ensure that the minimum bend radius is three
times the ducting diameter.
Use the largest cross-sectional area of ducting possible.
Use smooth walled ducting and avoid corrugated ducting, as it is mo
Transitions in ducting sizes should be smooth, so avoid step changes.
If the installation dictates restrictive du
airflow and counteract the effects of ducting. The additional fans should be installed on the air input to
the amplifier, where the air is at its coolest.
ip ent Housing
ipment housings, including basic f
ditioned rooms, have common cooling system design requirements:
2
•The local source and desti
pressure caused by differential pressure effects.
•exhaust vents, to avoid back-pressure caused by differential wind effects.
•Terminations of inlet and exhau
•If a sealed cooling system with re-circulating air-conditioners is used, an over temperature
alarm should be fitted to the cabin to detect air conditioner failures.
© e2v technologies (uk) limited 2010 DAS768892AA Version 1, page 12

•In any system, prevent hot exhaust air from re-circulating to the air inlet, otherwise the inlet air
temperature will increase, resulting in potential thermal runaway. This is a prime
consideration when designing common ducting systems for multiple amplifiers.
3.3.4 Commissioning the Installation
When commissioning the across each amplifier should be
checked to assess the suitability of the cooli ure measurements should be taken
as follows:
•Under the worse case op transmit state, no RF drive
applied (beam only) an bilised (typically 2 hours after
transmit (XMIT) has bee
•As close to the amplifi (to reduce the effects of
inaccuracies caused by un
3.4 MAINS SUPPLY CONNECTION
notes at the start of this manual should be read before connecting the amplifier to the
240V ac without any user adjustments.
e
he connection of
installation, the temperature difference
ng system. Temperat
erating conditions with the amplifier in the
d after the amplifier has thermally sta
n selected).
er air inlet and exhaust as possible
even temperature distribution).
The safety
mains supply.
The amplifier can be operated from mains supplies of 200 to
Both the live and neutral connections on the amplifier are fully rated and isolated for maximum lin
voltage, full transient and noise immunity.
The amplifier is supplied with one mains cord and a connecting plug. A residual current circuit breaker
(RCCB) must be used, approved for any local wiring regulations and rated for the environmental and
operational conditions. A cord size of 3x2.5mm2(12 AUG) minimum must be used. T
the wiring cord to the amplifier connector must be made by a suitably qualified person. The pin
configuration is shown in figure 4.
3.4.1
It is important to ensure that the required voltage is available at the input connector of the amplifier
drop is less than 10Vrms.
Figure 4.
The plug connecting to the local mains distribution is the emergency disconnect device and must be
kept accessible at all times during operation of the amplifier.
It is recommended that the mains supply to the amplifier is fed via a double pole 30A RCCB.
Mains Supply Cable Connection
under conditions of maximum current demand (as stated on the RATINGS LABEL).
It is also important to ensure that for any supply selected, the mains supply no load to full load voltage
© e2v technologies (uk) limited 2010 DAS768892AA Version 1, page 13

Under the conditions of a low voltage power source and long power connections leads, it may be
necessary to select a cable for its low voltage drop rather than a selection based on the nominal
current rating requirement (refer to local wiring regulations).
3.4.2
sient currents, must be
g the mains supply and
hould only be removed after disconnecting the amplifier from the supply. The connections must
l protective earth conductor must be a flat copper strap,
30A. The length of external protective earth
3.4.3
Earthing
An external protective earth conductor providing protection against RF and tran
onnected between the amplifier and an adjacent earth point before applyin
c
s
conform to local regulations. The externa
braided or plain, and must be capable of carrying
conductor must not exceed 400 mm.
Mains Supply Distribution
A mains supply disconnection device must be provided to isolate the amplifier from the mains supply
source. Either a socket outlet or a two-pole isolation switch (rated for the maximum current condition)
must be used as the mains supply disconnection device. It must be installed near the amplifier and
be easily accessible. The mains connector on the amplifier must not be used as the mains supply
disconnection device. It is provided for convenience during installation and for ease of operation.
It is strongly recommended that the mains supply for the amplifier is fed via a double pole residual
current circuit breaker (RCCB). The amplifier earth leakage current is <6 mA rms under nominal
operating conditions.
On low voltage 3-phase systems (e.g. 115 V line to neutral and 200V line to line), the unit may be
operated bi-phase. In this case, the amplifier may be connected across any two lines of the 3-phase
system to obtain what is effectively a 200 V single-phase source.
Under these circumstances the neutral of the 3-phase generator is not connected to the amplifier, this
may offer a method of partially balancing a number of low power single phase loads operated from
small generators.
If the amplifier is connected bi-phase, an external 2-pole protection device must be provided that
disconnects both line connections in the event of a fault on either line.
This equipment has not been designed for connection to an IT power system.
3.5 USER INTERFACE CONNECTIONS
Note: Refer to the appendices at the end of manual for examples of wiring.
The amplifier is supplied with a user interface connector plug, but no cable. Additional connectors are
available from e2v technologies. Please contact your distributor.
If the amplifier is to be used in applications where it is exposed to rain or subjected to condensation,
all attempts must be made to prevent moisture ingress into the connector and cable loom. The
onnector plug accepts cable diameters up to a maximum of 15m
c m.
r is assembled.
nts.
3.6
itch position and amplifier operation
or further details on the N6143, contact your distributor).
For use with cable diameters less than 15 mm the effective cable diameter should be increased to
proximately 14 to 15 mm to allow an effective seal to be made when the connecto
ap
Self-amalgamating tape or layers of adhesive heat shrink cable are recommended. Connector back
shells that accept adhesive heat shrink boots are available, please contact your distributor.
ully screened cable should be used for interface requireme
F
REDUNDANT SWITCH CONFIGURATION
If two amplifiers are to be connected to a redundant switched system, the control circuitry within the
amplifiers can be used to implement a cost-effective switch control solution. Figure 5 on the following
page shows the wiring connections required to implement a basic redundant switched system using
the N6143 as the controlling device. The N6143 control unit is connected to the serial interface of
oth amplifiers, allowing remote switching and monitoring of sw
b
(f
© e2v technologies (uk) limited 2010 DAS768892AA Version 1, page 14

As the amplifiers do eguide switch is pre-
selected by the use control unit. The low
power alarms on b amplifiers placed in the
transmit state. The via the user interface
or from the N6143
With both amplifiers ope RF output power, the
waveguide switch will remain as the other amplifier for
potential faults on, or its RF output
power drops below alarm level), the other
amplifier takes co t is used, an audible
alarm will indicate the fault
The amplifiers will remai not recover and a fault
ccurs on the second amplifier it will not result in switching of the waveguide switch.
a 24V type and a closed tell-back contact within the waveguide
ould be used for the amplifier whose output is switched to the load. An open contact tell-back
e switch selected but will be typically 50-100ms.
1-pin amplifier control
onnector. Termination of the serial communications bus is dependent upon the length and type of
e used, and should follow normal transmission line practice.
not have a master/slave relationship, the position of the wav
r either manually, via the user interface or from the N6143
oth amplifiers should be set if required and then both
automatic mode enable (AUTO ENA) input is then selected
control unit to pass control of the switch to the amplifiers.
rating normally in the transmit state with >1W of
set. Each amplifier monitors the status of
. If the amplifier routed to the antenna develops a fault conditi
the low power alarm setting (1W minimum low power
ntrol, switching the waveguide switch. If the N6143 control uni
condition to the operator.
n in the automatic mode, but if the faulty amplifier does
o
he waveguide switch coil should be
T
switch sh
should be used for the amplifier switched to the antenna.
witching time is dependent upon the waveguid
S
The interface between the control unit and the amplifiers is via the local serial communications bus.
As the amplifiers do not contain transmitter or receiver termination, the local serial communications
bus should be fitted with 120R ±1%, ¼W carbon film or similar termination resistors between pin d
X+) and pin e (RX-), also between pin b (TX+) and pin c (TX-) of the 4
(R
c
cabl
Figure 5 Redundant switch operation
Notes:
A wiring schematic diagram is given in the appendices for the connection of two amplifiers, the N6143
control unit and a waveguide switch.
If the amplifier AUTO ENA line is not asserted, the RED FLT O/P will not be enabled. Consequently, if
an external controlling device other than the N6143 is used, the RED FLT O/P cannot be used to
trigger the amplifier switch-over. As an alternative, the SUM FLT IND multiplexed fault lines or
inverted XMIT IND outputs can be used as the trigger for the switch-over.
© e2v technologies (uk) limited 2010 DAS768892AA Version 1, page 15

4 BASIC OPERATION OF THE AMPLIFIER
4.1 APPLYING THE MAINS VOLTAGE
Before applying the mains supply to the amplifier, the operator must be satisfied that:
•Both the RF input and RF output connections are correctly terminated (see section 3.2).
es and section 3.3).
is good practice to allow the TWT to cool for three to four minutes after leaving the transmit state,
m the mains supply.
4.2
on some mains or local generator derived supplies, for the supply to be temporarily
er these conditions when it is
nd the
ected and the amplifier will
ave the transmit state. When the mains supply returns, the amplifier will remain in the off state until
other operating state either manually or automatically.
4.3 FUNCTIONS
s the control functions available to the user.
4.3.1
ntil another state is
off state can be requested to remove the amplifier from the transmit state.
4.3.2
rm-up timer period will be 10 minutes.
uring the warm-up period the standby or transmit states can be requested, to select the state that
e end of the warm-up period.
4.3.3
ready to enter the
ollowing transmission, the standby state can be requested to remove the amplifier from the transmit
tate.
•Safety and cooling requirements are complied with (see safety not
•The correct type of mains cable is in use (see section 3.4).
Once the above has been verified apply the mains supply to the amplifier. The fans will be heard to
start.
It
before disconnecting the amplifier fro
MAINS SUPPLY INTERRUPTIONS
t is common
I
interrupted. This section details the behaviour of the amplifier und
ransmitting.
t
Interruption < 30 mS – the amplifier will continue to operate normally.
nterruption > 30mS < 3 Seconds – a degradation of RF performance can be expected a
I
amplifier will leave the transmit state. When the mains supply returns, the amplifier will automatically
re-enter the transmit state within 1 second. All operating parameters will be as previously set.
terruption > 3 Seconds – a degradation of RF performance can be exp
In
le
the user selects an
This section describe
Amplifier Off State
pplying prime power to the unit results in the amplifier entering the off state u
A
selected. In this state, only the amplifier control, auxiliary circuits and fans are operational. The
ooling fan will operate at maximum speed for the first 3 seconds after switch-on.
c
Following transmission, the
Amplifier Warm-up State
Requesting either the standby or transmit state from the off state will result in the TWT cathode heater
power being applied and the warm-up timer (180 seconds) being initiated.
ote: If the ambient temperature is less than -10ºC, the wa
N
D
the amplifier will enter at th
Amplifier Standby State
this state the TWT cathode is at its operating temperature and the amplifier is
In
transmit state. Power is applied only to the TWT cathode heater. Unless the transmit state has been
requested, the amplifier will enter standby state when the warm-up is complete.
F
s
© e2v technologies (uk) limited 2010 DAS768892AA Version 1, page 16

Amplifier Transmit State
With the amplifier in the standby state, selecting the transmit state results in the application of helix
and collector voltages to the TWT, allowing RF transmission
4.3.4
. In the transmit state, the RF output
ower and the TWT helix current monitor features are operational and the control of gain is possible
he cooling fans will alter speed (depending on internal temperature) to maintain adequate cooling to
e TWT.
4.4
used without an external 10 MHz. This feature is activated when the external 10 MHz
cking signal is too low or not present. The BUC must be used in conjunction with either the D or Z
put options.
Table 1 Single Band BUC Basic Parameters
LIMITS
p
using the (optional) Digital Electronically Variable Attenuator.
T
th
UP-CONVERTER OPERATION
Products in the C and Ku ranges with a U suffix in the type number (see figure 1) contain an integral
L-band block up-converter (BUC). Inclusion of the BUC enables the input signal to be in the L-band
range as defined in table 1 overleaf. The BUC may be synchronised with an external 10 MHz that
enables it to be
lo
in
AMPLIFIER PARAMETER UNITS N
Min om Max
STA2175 – CC1xU GHz 5.85 - 6.425
STA2375 – KU1xU GHz 13.75 - 14.5
STA2375 – KU3xU
Output Frequency
GHz 14.0 - 14.5
STA2175 – CC1xU MHz 950 - 1520
STA2375 – KU1xU MHz 950 1700-
STA2375 – KU3xU
Input Frequency
9 1450
MHz 50 -
STA2175 – CC1xU GHz - 4.9 -
STA2375 – KU1xU GHz - 12.8 -
STA2375 – KU3xU
Local Oscillator Frequency
GHz - 13.05 -
umn, x indicates either the D or Z input option.
4.5
ge. It allows external monitoring of the output power,
roviding a signal approximately 50 dB lower than the RF output power. It is provided with calibration
data across the amplifier’s frequency range.
Note : In the Amplifier col
RF SAMPLE PORT
The RF sample port is provided as an optional N-type (female) connector, mounted at the opposite
end of the amplifier to the waveguide flan
p
© e2v technologies (uk) limited 2010 DAS768892AA Version 1, page 17

5 USER INTERFACES
The amplifier is provided with two control interfaces, the user port and the serial communications
interface (RS-485, 2 or 4-wire). All interfaces are available on the 41-pin control connector, located
next to mains supply connector. This section identifies each control connector pin and describes the
function of each pin, including the electrical specification.
5.1 PIN IDENTIFICATION
Code Function Pin
OFF IND Off indicator output A
WARMUP IND Warm-up indicator output B
STBY IND Standby indicator output C
XMIT IND Transmit indicator output D
SUM FLT IND Summary fault indicator output E
Spare F
RF INHIB RF inhibit control input G
INV RF INHIB Inverted RF inhibit control input H
OFF Off control input J
STBY Standby control input K
XMIT Transmit control input L
MUX 4 Multiplexed fault line 4 indicator output M
FWD PW MON Forward power monitor analogue output N
GND Ground P
EXT INTLK External interlock input R
ADD 0 Address select 0 S
ADD 1 Address select 1 T
+ 15V + 15V output U
ADD SEL Address select V
CTRL O/R Control override select W
MUX 0 Multiplexed fault line 1 indicator output X
MUX 1 Multiplexed fault line 2 indicator output Y
MUX 2 Multiplexed fault line 3 indicator output A
MUX 3 Multiplexed fault line 4 indicator output a
RS TX + Serial interface TX + b
RS TX- Serial interface TX - c
RS RX+ Serial interface RX + d
RS RX- Serial interface RX - e
HX I MON Helix current monitor analogue output f
ADD 2 Address select 2 g
ADD 3 Address select 3 h
2/4 BUS SEL 2/4 wire serial bus select i
Spare j
RED FLT O/P Redundancy fault indicator output k
RED SW 1 Redundancy RF switch drive 1 – this HPA
to antenna
m
RED SW 2 Redundancy RF switch drive 2 – this HPA
to load
n
RS GND Serial interface signal return p
SWITCH
SENSE
Redundancy RF switch sense input q
AUTO ENA Redundancy automatic mode enable
input
r
RED SEL Redundancy select input s
RED FLT I/P Redundancy fault input t
© e2v technologies (uk) limited 2010 DAS768892AA Version 1, page 18

5.2 USER INTERFACE FEATURES
5.2.1 Indicator Outputs – Type 1
Normally open relay contact outputs switched to GND (pin P on the user interface connector) when
condition is true.
Example 1 Amplifier in the off state is indicated by pin A on the user interface connector
closing to pin ‘P’.
Example 2 MUX 0 fault line is at binary 1 when pin X on the user interface connector
closes to pin P.
OFF IND Indicates power is applied and that the unit is in the off state.
WARMUP IND Indicates the TWT cathode three minute warm-up timer is operating and that
the unit is in the warm-up state.
STBY IND Indicates the TWT cathode warm-up is complete, the unit is in the standby
state and ready to enter the transmit state.
XMIT IND Indicates the unit is in the transmit state.
SUM FLT IND Indicates the unit has detected a fault condition.
MUX 0
MUX 1 Five binary coded discrete lines that indicate the fault conditions;
MUX 2 the following list gives a breakdown of these fault conditions with a
MUX 3 brief description of reset conditions.
MUX 4
MUX fault code Fault Reset code
00001 Peak helix overcurrent A
00010 Mean helix overcurrent A
00011 Excessive reflected power A
00100 Power factor correction P
00101 DC bus supply P
00110 HV overload A
00111 External interlock open M
01000
01001
01010 Cooling fan failure P
01011 TWT collector too hot M
01100
01101
01110 Case too hot M
01111
10000
10001 Heater voltage outside limits M
10010
10011 Collector voltage outside limits M
10100 Cathode voltage outside limits M
Reset Code Description
A (automatic reset). Units that exhibit faults with this reset code will be immediately removed from the
transmit state and placed into the fault state. The unit will automatically attempt to reset to the
transmit state after 3 seconds and if this fails the unit will attempt a further two reset cycles. If after
the three reset attempts the amplifier still exhibits the fault condition, the unit will remain in the fault
state for 4 minutes before returning to the off state, unless the fault clears and the transmit state is
reselected.
M (manual reset). Units that exhibit faults with this reset code will be immediately removed from the
transmit state and placed into the standby state. The unit will remain in this state for the period of 4
minutes before returning to the off state, unless the fault clears and the transmit state is reselected.
P (prime power reset). Units that exhibit faults with this reset code will be immediately removed from
the transmit state and placed into the fault state. If the fault is seen to clear, the mains supply should
be removed for nominally 10 seconds before re-applying to reset the trip.
© e2v technologies (uk) limited 2010 DAS768892AA Version 1, page 19

5.2.2 Indicator Outputs – Type 2
Normally open relay contact outputs switched to GND (pin P on the user interface connector) when
conditions is false.
Example Unit is operating normally with no fault condition when pin k on the user
interface connector is closed to pin P.
RED FLT O/P Part of the redundant switch control facility. Indicates that the unit has
suffered a low power alarm or a fault condition that has resulted in removal
from the transmit state. This output would normally be connected to the RED
FLT I/P (pin t on the user interface connector) of the other amplifier in the
redundant switch system.
Note: Only active if the AUTO ENA input has been asserted.
5.2.3 Analogue Outputs
The following analogue outputs are provided to allow the user to implement a simple and cost
effective monitoring system. These outputs are also available in digital form via the RS-422 or RS-485
serial communications interface (see section 6). These outputs are referenced to GND (pin P on the
user interface connector).
It is recommended that a screened cable is utilised to avoid RFI effects.
FWD PW MON Provides a 0 to +10Vdc analogue output that corresponds to a RF output
power range of 0 to 750 W. This output is a linear 50 W/V. Maximum output
impedance 100 Ω
HX I MON Provides a 0 to +10Vdc analogue output that corresponds to a TWT Helix
current range of 0 to 10mA. This output is a linear 1 mA/V. Maximum output
impedance 100 Ω
5.2.4 Control Inputs – Type 1
The following control inputs are of the momentary edge-triggered type. The inputs are internally pulled
up to +12V by 3k3 resistors. The input is asserted on the falling edge i.e. as the input is switched to
GND (pin P on the user interface connector). Only one input should be asserted at a time and should
be relinquished for at least 10mS prior to asserting another type 1 input.
Note: The operation of the XMIT control input is modified while the CTRL O/R input is asserted.
See section 5.2.6.
Minimum pull down time ........................................................................................................... 1mS
Maximum external switch ‘on’ resistance .................................................................................100 Ω
OFF Selects the off state directly from any of the other four operating states
(warm-up, standby, transmit and fault).
STBY Selects the standby state directly from the transmit state. When selected
from the off state the unit is placed into the warm-up state for three minutes
before automatically entering the standby state.
XMIT Selects the transmit state directly from the standby state. When selected
from the off or warm-up states the transmit state is automatically entered after
the end of the three minute heater warm-up time.
RED SEL Part of the redundant switch control facility, selecting the amplifier to be
routed to the antenna.
© e2v technologies (uk) limited 2010 DAS768892AA Version 1, page 20
This manual suits for next models
5
Table of contents
Other stellar labs Amplifier manuals
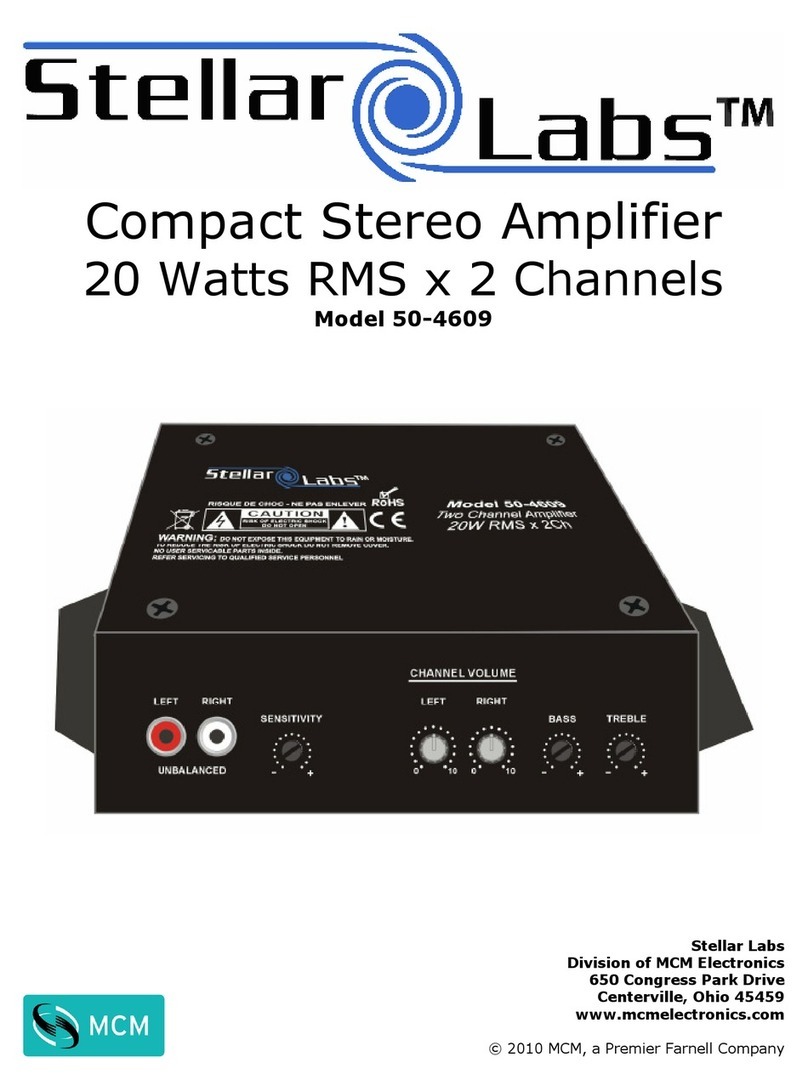
stellar labs
stellar labs 50-4609 User manual

stellar labs
stellar labs DA-250 User manual
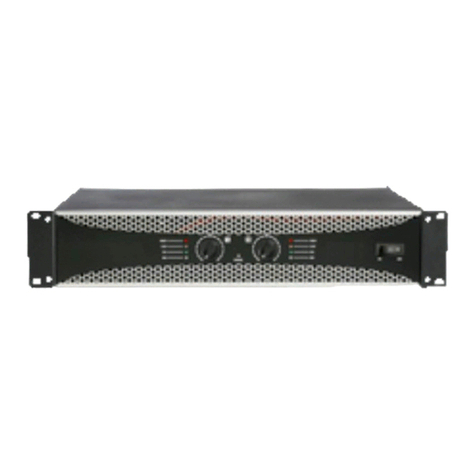
stellar labs
stellar labs SLP-200 100W x 2 CH User manual
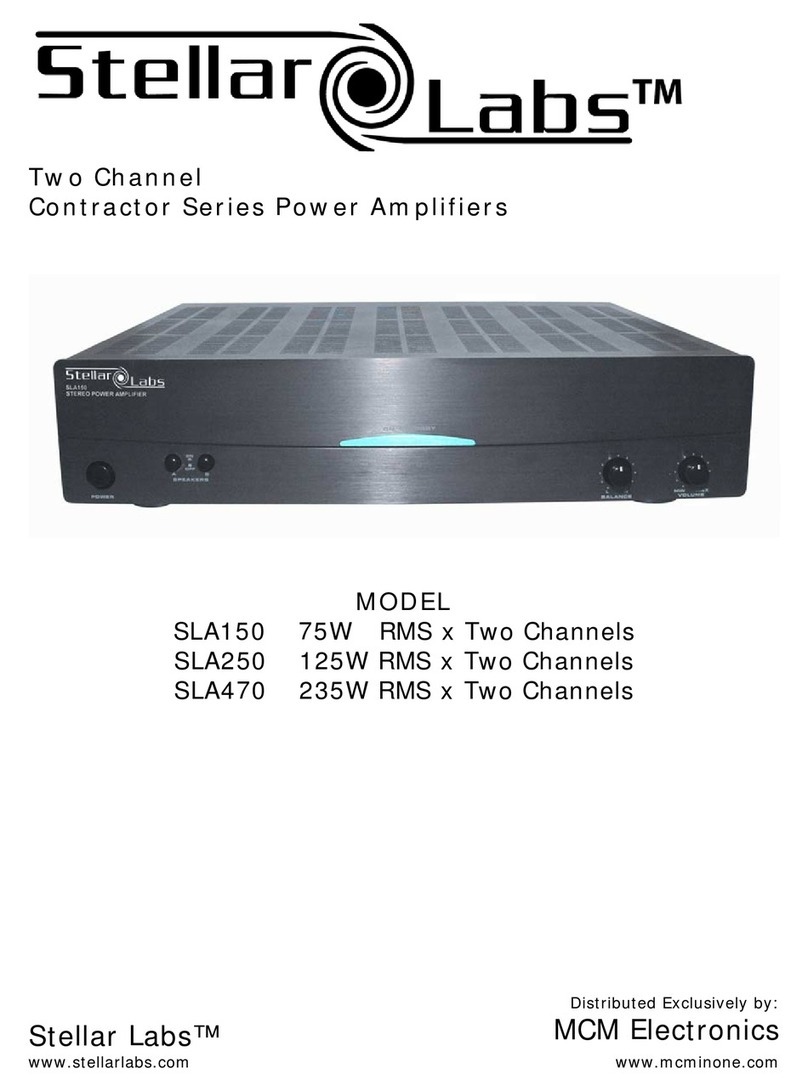
stellar labs
stellar labs SLA150 User manual

stellar labs
stellar labs 30-2471 User manual
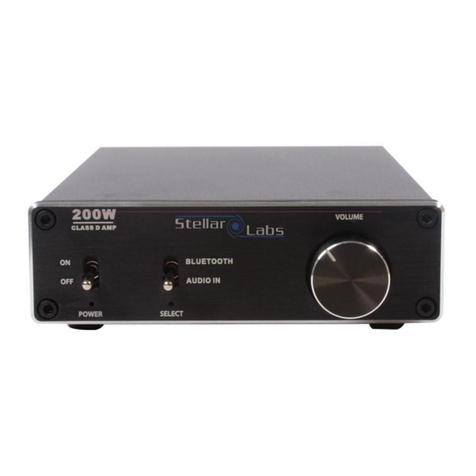
stellar labs
stellar labs 50-20810 User manual
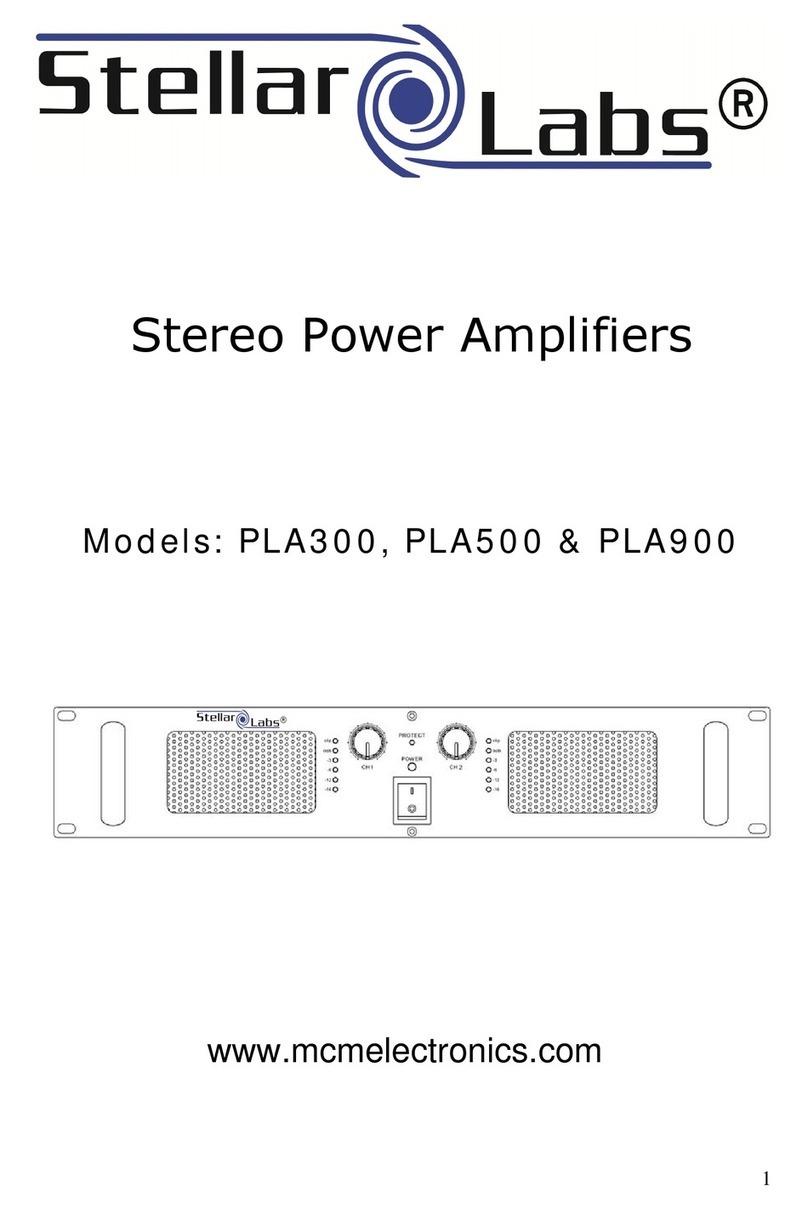
stellar labs
stellar labs PLA300 User manual