Swegon SILVER C User manual

GB.EXCHSILV2.141119
We reserve the right to alter specifications. www.swegon.com 1
Instructions for the heat exchanger control system SILVER C
RX, RECOnomic, sizes 100/120, RECOsorptic, sizes 50-120
1. General
The heat exchanger control system is a control system for
380 W step motors. It is designed for precise and quiet
control of rotary heat exchangers in the SILVER C RX
ventilation units with standard rotor (RECOnomic) in size
100/120, and with sorption rotor (RECOsorptic) in sizes
05-120.
Integrated functions:
• 0 - 10 V DC analogue input for controlling the speed.
• Alarm for overloading, over-voltage and under-voltage.
• Protective motor switch with integrated current limit-
ing function.
• Short-circuit protected inputs and outputs.
• Digital input for start/stop.
• Digital input for alarm resetting.
• Integrated EMC filter.
In the size 50-80 SILVER C units the heat exchanger
control system is located inside the filter section in the
lower level. In the size 100/120 SILVER C units the heat
exchanger control system is located inside the fan or filter
section to the left of the centre section in the lower level
(viewed from the inspection side). For access, open the
inspection door.
Forbidden to start operation
It is absolutely forbidden to start operation until the
entire air handling unit, where the above-mentioned heat
exchanger control system is integrated, has been declared
to conform to relevant regulations in Machinery Directive
98/37/EEC and to existing national legislation, if applica-
ble.
The heat exchanger control system must not be energized
until the entire installation conforms to the provisions in
ALL relevant EU Directives. If the heat exchanger control
system has been damaged, for instance during transport,
it must be inspected and repaired by qualified personnel
before the voltage is connected.
Safety functions
The heat exchanger control system is protected against
phase-to-phase short.circuiting, and has integrated cur-
rent limiting function for protection of the motor.
The electrician is accountable for ensuring correct earth-
ing as well as protection according to local standards
and regulations. An earth fault circuit breaker, multiple
protective earthing or ordinary earthing can be used as
extra protection, provided that the local regulations are
complied with. The earth leakage currents exceed 3.5 mA.
Therefore a fixed, permanent installation and heavy-duty
protective earthing are required.
NOTE! If an earth fault occurs, there can be a direct cur-
rent component in the leakage current. Earth fault circuit
breakers should therefore be designed to be able to detect
this and be installed according to applicable national and
international regulations, where they are used.

GB.EXCHSILV2.141119
We reserve the right to alter specifications.
2 www.swegon.com
2. Technical data
Power supply 50-60 Hz,
1x230 V AC
-10%/+15 %
Rated motor shaft power: 0.38 kW
Motor current cons. (max. load) 4.5 A
Maximum fuse protection 10 A
Ambient air temp., operation -40/+40 °C
Ambient air temperature, storage -40/+70 °C
Enclosure class IP54
Control voltage 0-10 V DC
Weight 4.9 kg
3. Function
General
The motor control system advantageously replaces the
traditional solution with gear motor. The step motor has
uniform torque across the entire rpm range, in contrast
to gear motors that lose torque at low and high speeds
of rotation respectively. The step motor's constant torque
curve provides an essentially greater operating range
where the speed of rotation can be controlled with preci-
sion. It is therefore possible to control the heat recovery in
an energy-optimum manner and achieve a more accurate
temperature.
The heat exchanger control system is controlled with 0 –
10 V signals.
The step motor is controlled in micro steps with sinusoidal
constant current for ensuring motor shaft rotation with
uniform torque throughout the revolution. This prevents
torque pulses and at the same time provides quieter
operation.
Rotation monitor
The rotation monitor consists of an inductive sensor.
When the rotation monitor is mounted correctly, the sen-
sor's LED flashes yellow each time the detection surface
passes the rotation monitor.
Operation
LED indications
The junction box has 2 integrated LEDs located under the
cover. They are therefore not visible when the cover is
mounted.
The green LED is constantly lit when voltage is supplied..
The red LED is lit if at least one active alarm has been initi-
ated.
Warning The chassis on the heat exchanger control
system can become very warm!
Warning! Do not repair the heat exchanger con-
trol system at the site. Never attempt to repair a
defective control system unit.
Contact the supplier to obtain a replacement unit.
Fig. 1. Dimensions

GB.EXCHSILV2.141119
We reserve the right to alter specifications. www.swegon.com 3
Control with 0 – 10 V DC
The heat exchanger control system can be controlled via
external input signals. The heat exchanger control system
needs a start/stop signal in order to start. The start/stop
signal is transmitted by short-circuiting Terminals 7 (Start/
stop) and 8. ( ) (See Fig. 2).
The heat exchanger control system regulates the speed
linearly between 0 % and 100 %, however it is limited to
the regulation range between the preset lowest and high-
est speeds (See Fig. 3) 100 % speed is defined as an input
voltage of "0-10 V in" (Terminal 13) at 9.5 V (100 % at
9.5 V, +/-2 %).
Compensation for non-linear heat transfer
The 0 – 10 V signal is compensated internally in the heat
exchanger control system with a contrary rotor character-
istic to provide far more linear heat transfer than compara-
ble systems and better regulation (See Fig. 4).
The function selector switch positions (Factory
preset):
4 = Sizes 100/120, standard rotor
5 = Sizes 50/60, sorption rotor
6 = Sizes 70/80, sorption rotor
7 = Sizes 100/120, sorption rotor
To reverse the direction of rotation
The direction of motor rotation is reversible so that the
rotor always has the correct direction of rotation in rela-
tion to the purging sector.
To reverse the motor's direction of rotation, transpose two
optional conductors to Motor Terminal V - U - W (See Fig.
6).
Automatic restart after alarm
The heat exchanger control system automatically attempts
to start again following an alarm, such as over or under-
voltage alarm. This automatic restart is carried out maxi-
mally 3 times (rotation monitor alarm: 1 restart) After that,
the heat exchanger control system will remain in the error
mode, and must be restarted by resetting the alarm.
Alarm resetting: See Section on "Alarm resetting".
Alarm relay/output
The heat exchanger control system is equipped with an
alarm output in the form of an alarm relay. The alarm relay
is activated if an alarm arises in the heat exchanger control
system or if alarms are discovered in motors or fans. Con-
nect the alarm signal cable leads to Terminals 16 (C) and
17 (normally closed). The relay contact is closed in deener-
gized condition and if there are active alarms.
Alarm reset
The heat exchanger control system is equipped with a
digital input for resetting alarms. The alarm input is reset
by short-circuiting Terminals 11 (Alarm reset) and 12 ( )
(See Fig. 2). The alarm output can also be reset by switch-
ing off the supply voltage to the heat exchanger control
system for more than 60 seconds.
Fig. 2. Junction box, overview of the wiring terminals
Fig. 3. The ratio between the speed and the min./max. speed setting
.
.
.
,
Fig. 4. Compensation for non-linear heat transfer.

GB.EXCHSILV2.141119
We reserve the right to alter specifications.
4 www.swegon.com
4. Electrical connections
The heat exchanger control system has a junction box installed in the
lower part of the heat exchanger section. For access, open the inspec-
tion cover in front of the heat exchanger.
To connect control signal wiring
• Insert the control cables into the junction box through the cable
grommets fitted with rubber gaskets. Clip an appropriately large
hole in the gaskets to enable the gasket to seal tightly around the
cable. Only by doing so can the stated Enclosure class IP54 be com-
plied with.
• Connect the 0 – 10 V DC control signal from an external regula-
tor in the junction box to Terminals 13 (0 - 10 V in) and 14 (See
Fig. 5). The heat exchanger control system regulates the speed in
a capacity linear manner between 0 % and 100 % (100 % at 9.5
V +/- 2 %), however according to the preset times for up ramp
and down ramp, and limited to the regulation range between the
preset lowest and highest speeds (See Fig. 3 and 4). The ”Control
with 0-10 V DC” function is described in Section 3. Function.
• Connect the start/stop signal cable leads in the junction box to Ter-
minals 7 (Start/stop) and 8 ( ) (See Fig. 5). This should be a poten-
tial-free digital contact. The ”Start-/stop” function is described in
Section 3. Function.
• Connect the Alarm Reset signal cable leads to the heat exchanger
control system's junction box to Terminals 11 (Alarm reset) and 12 (
) (See Fig. 5). This should be a potential-free digital contact. The
"Alarm Reset" function is described in Section 3. Function.
• The heat exchanger control system is equipped with an alarm
relay output with normally-open contact function in the event of
a malfunction or alarm. The alarm signal cable is marked "Alarm
relay", and should be connected in the junction box to Terminals
16 (C) and 17 ( ) (See Fig. 5). This should be a potential-free digi-
tal contact. The "Alarm Relay" function is described in Section 3.
Function.
• Connect the sensor cable of the rotation monitor to Terminals 9
(digital in), 10 ( ) and 15 (+10 V out, power supply to sensor).
Fig. 5. Junction box, overview of the wiring terminals
.
.
.
Blue
Black
Brown
.
,

GB.EXCHSILV2.141119
We reserve the right to alter specifications. www.swegon.com 5
Electric Power Connections
In the size 50-80 SILVER C units the heat exchanger
control system is located inside the filter section in the
lower level. In the size 100/120 SILVER C units the heat
exchanger control system is located inside the fan or filter
section to the left of the centre section in the lower level
(viewed from the inspection side). For access, open the
inspection door.
For appropriate connection, see Fig. 6.
For electrical data, see Section 2.
Fig. 6. To connect power supply wiring to the heat exchanger control system.
To change the rotor's direction of rotation, transpose
two optional conductors to Motor Terminal V - U - W.

GB.EXCHSILV2.141119
We reserve the right to alter specifications.
6 www.swegon.com
5. Trouble shooting
To open the heat exchanger control system
Before you open the heat exchanger control system, isolate the line voltage and wait at least 2 minutes. Failure to do so
will expose you to the risk of coming into contact with harmful residual voltage inside the unit.
Troubleshooting when the heat exchanger control system is controlled with external (A/D) signals:
Symptoms Cause Action
The motor is not rotating
There is no power supply
Check whether there is voltage on the heat exchanger control system's ”L” and ”N” terminals on
the models for 230 V.
(Operating voltage is specified on the rating plate, affixed to the side of the heat exchanger control
system.)
Poor electrical connections Check the connectors and other electrical connections
There is no in-operation signal Short-circuit Terminals 7 and 8 in the heat exchanger control system junction box marked (GND)
and ”Start/Stop” (Fig. 5).
There is no 0 – 10 V DC control
signal
Check that the 0 - 10 V DC control signal is correctly connected to Terminals 13 and 14 in the heat
exchanger control system junction box marked (GND) and ”0-10 V in” (Fig. 5).
The motor has been stopped by the
internal protective motor switch 3
times due to overloading or some
other alarm.
Reset the alarm by short-circuiting Terminals 11 and 12 in the heat exchanger control system
junction box marked (GND) and ”Alarm reset” (Fig. 5).
You can also reset the alarm by switching off the supply voltage to the heat exchanger control
system and switching it back on after 60 seconds.
Defective heat exchanger control
system Replace the heat exchanger control system
Defective motor Replace the motor
The heat exchanger control
system switches off.
¤) Remember to reset the
alarm by short-circuiting
Terminals (GND) and
"Alarm Reset".
At least two phases are short-circuit-
ed on the motor wiring terminals. Eliminate the short-circuit on the motor wiring terminals ¤)
Defective motor Replace the motor ¤)
Overloaded motor Remedy the overload condition of the motor ¤)
Defective motor Replace the motor ¤)
Overloaded motor Remedy the overload condition of the motor ¤)

GB.EXCHSILV2.141119
We reserve the right to alter specifications. www.swegon.com 7
6. Service and maintenance
No particular maintenance is required. Contact Swegon if
any problem arises.
To troubleshoot the unit: See Section 5. Troubleshooting.
7. Alarm
The integrated alarm relay in the junction box has nor-
mally-closed contacts and is marked "Alarm Relay". The
alarm relay contacts are closed in deenergized condition
and open in faultless condition. The alarm relay contacts
close in the event of an alarm. The heat exchanger control
system stops and an alarm indicating LED is lit. If the fault
ceases to exist, the alarm is reset automatically and the
heat exchanger control system starts up.
8. Environment and waste disposal
Help to protect the environment by ensuring correct
disposal of the packaging and use the products in accord-
ance with applicable environmental regulations.
Disposal of the product
Products with this mark must not be disposed as
ordinary household refuse. They must be collected
in separate containers according to applicable local
rules.
9. Applicable standards.
GB-61800-2 ”Electric motor operation with variable
speed, General Requirements”
EN-61800-3 ”General electromagnetic compatibility”
10. CE marking
Swegon AB certifies under its own sole responsibility
that this product conforms to the Commission's Directive
92/31 with subsequent modifications concerning electric
compatibility as well as the Commission's Directive 73/23
dealing with electric material for use within certain voltage
limitations.
APPROVALS
EMC EN 61800-3
LVD EN 61800-2
PRODUCT STANDARD EN 61800 PART
2 & 3
THE ROHS DIRECTIVE YES
PRODUCT
APPROVALS CE

GB.EXCHSILV2.141119
We reserve the right to alter specifications.
8 www.swegon.com
Other manuals for SILVER C
2
This manual suits for next models
3
Table of contents
Other Swegon Control System manuals
Popular Control System manuals by other brands

Igema
Igema SMLC 1 Installation and operating instructions
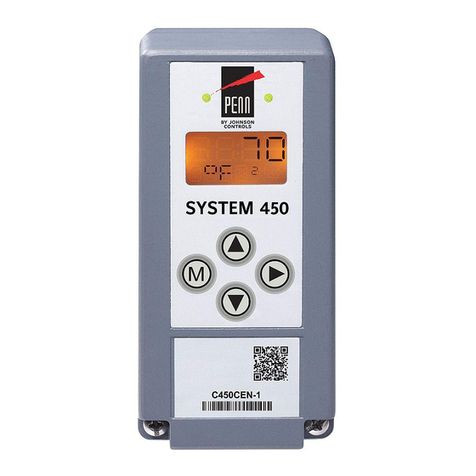
Johnson Controls
Johnson Controls Penn System 450 Series Technical bulletin
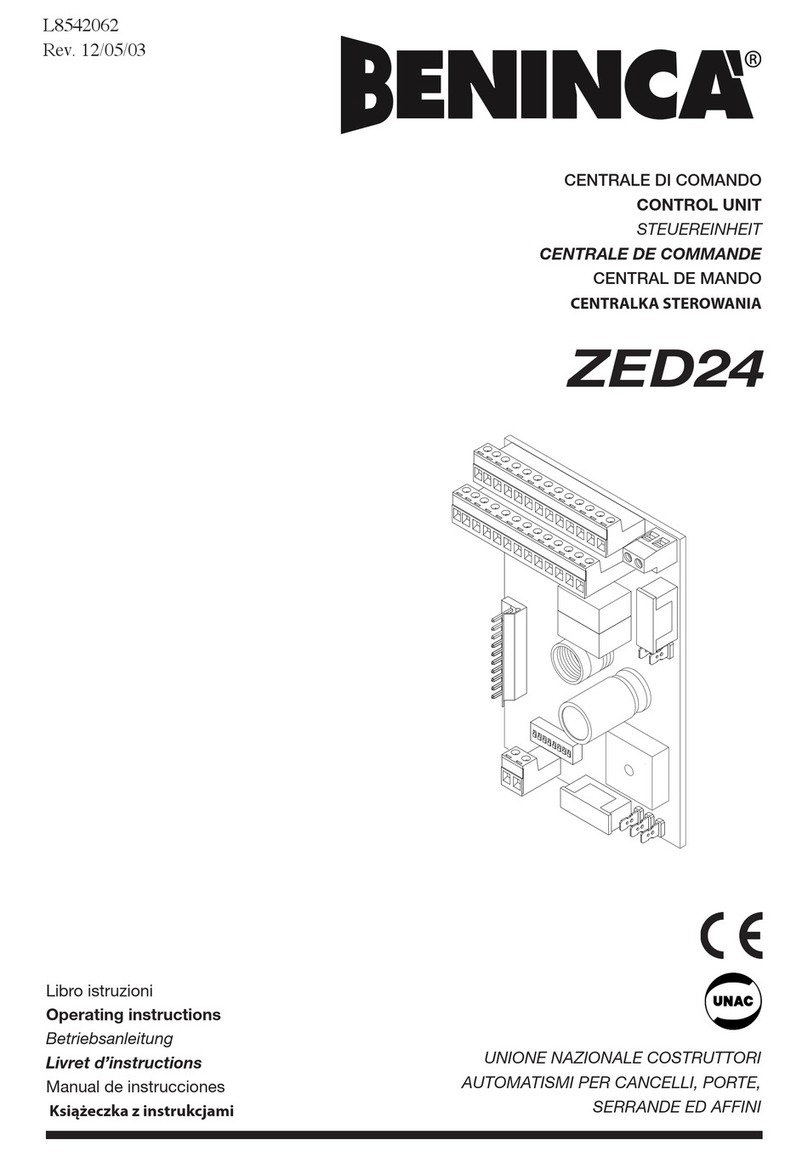
Beninca
Beninca ZED24 operating instructions
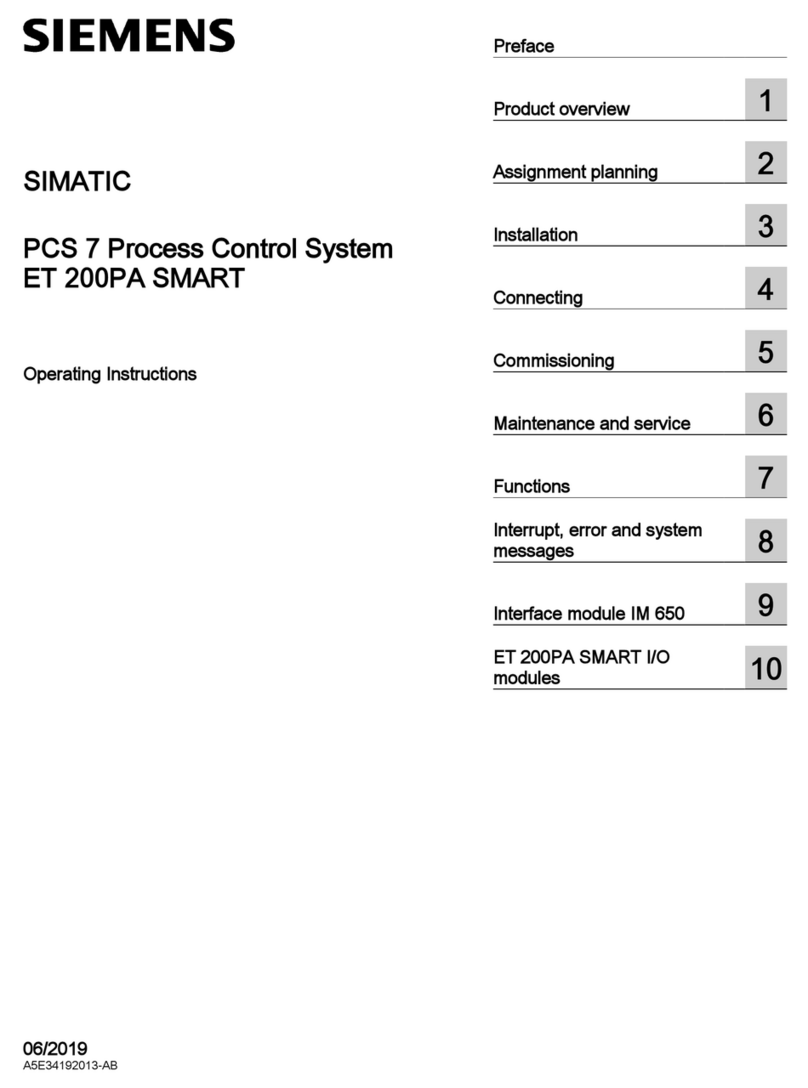
Siemens
Siemens SIMATIC ET 200PA SMART operating instructions
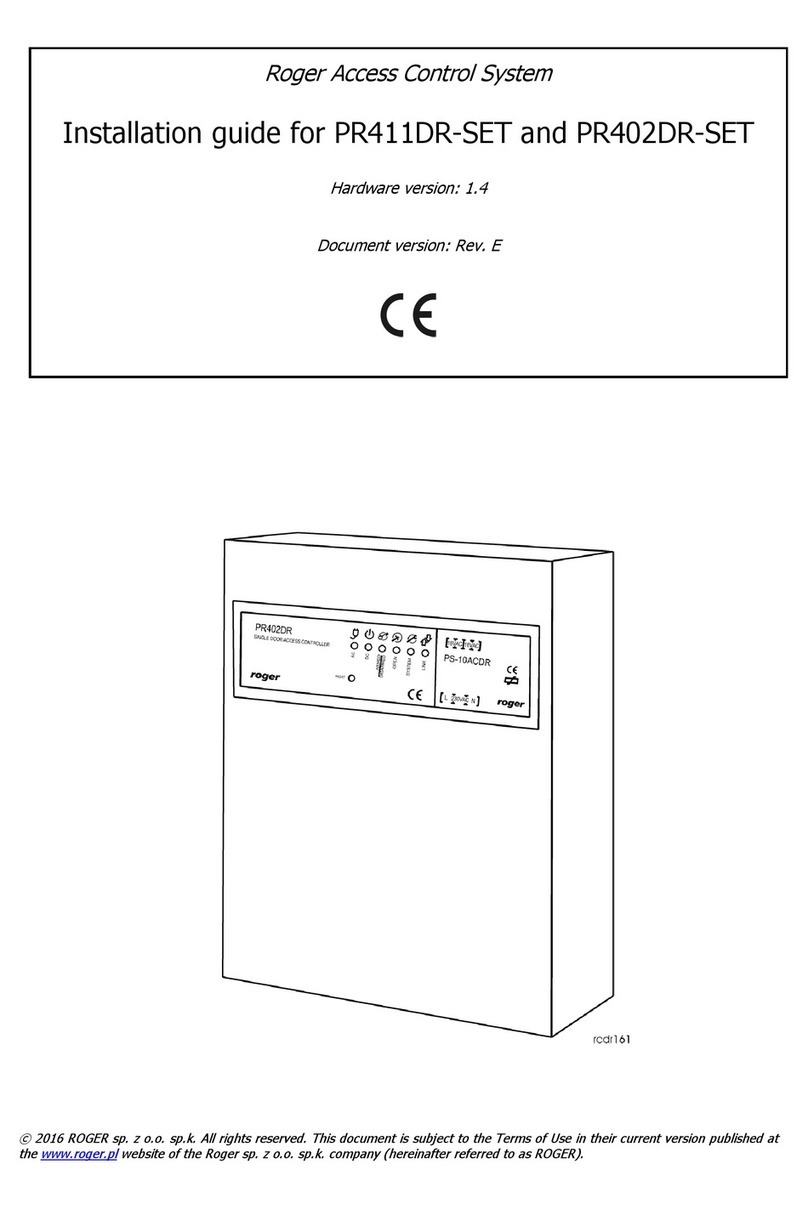
Roger
Roger PR411DR-SET installation guide

WEIHONG
WEIHONG NK280B manual