tae TA-15/6P Manual

Pikatron GmbH •division TAE Antriebstechnik •Raiffeisenstrasse 10 •D-61250 Usingen
http://www.tae-antriebstechnik.de TA_BA TA-15-200_6P_EN.PDF
The German text applies in cases of doubt
TA-15/6P…200/6P
Instruction and Operation Manual
Caution:
There is always a risk involved in the handling of electrical machinery!
Therefore mounting and maintenance should only be done by authorized personnel.

2
missprints and technical changes reserved Instruction & Operating Manual
TA-15/6P...200/6P
rFull controlled three phase bridge
rField Current control
rPhase control
rBlocking control
rCurrent Output Impulse controlled
2. Connection of the drive control (refer to connection diagram TA-15/6P...200/6P)
Ensure that your line voltage corresponds to the voltage indicated on the type marking of the unit.
2.1 Terminal Strip KL. 3 (at TA-15/6P KL.3=KL.1)
L1 - L2 - L3 Three phase a.c. line input and voltage according to type marking on unit.
Frequency see the selector switch on the upper printed circuit board.
A+ A- Armature
2.2 Terminal Strip KL. 1
F+ F- Field
Terminal 1 and 9 Drive ON - (Closing contact)
(Drive remains switched on until contacts open)
Terminal 4 and 9 Jog Speed ON - (Closing contact)
(Drive remains switched on until contacts open)
1. Technical Data
rMotor-Zero Speed Indicator
rCurrent Limit control
rTachometer Signal control
rElectronic circuit galvanically seperated from line
when tachometer feedback is utilized
Drive Type TA-15/6P TA-40/6P TA-60/6P TA-100/6P TA-200/6P
Line Voltage 230VAC 400VAC 230VAC 400VAC 230VAC 400VAC 230VAC 400VAC 230VAC 400VAC
Power 10KW 15KW 24KW 40KW 35KW 60KW 60KW 100KW 120KW 200KW
Armature Voltage 240V 440V 240V 440V 240V 440V 240V 440V 240V 440V
Armature Current 45A 45A 100A 100A 180A 180A 280A 280A 560A 560A
Field Voltage 155V 270V 155V 270V 155V 270V 155V 270V 155V 270V
Field Current max 4A 4A 4A 4A 10A 10A 10A 10A 10A 10A
Ambient Temp. 0 - 40 °C
Speed Accuracy Armature feedback controlled 3% - Tachometer feedback controlled a.c 2% ; d.c 0,5%
Read these instructions carefully before installation,
adjustment and operation of the drive control.

3
missprints and technical changes reserved Instruction & Operating Manual
TA-15/6P...200/6P
Terminal 7 and 8 Terminals for contacts of all malfunction signals. (Contacts open in event of fault)
Terminal 2, 5, 6 Speed potentiometer
With this potentiometer the speed is infinite variable from minimum to maximum
speed.
Poti-connect: KL. 5 = Beginning
KL. 6 = End
KL. 2 = Connect center
Terminal 13 Current reference signal output
Terminal 18 Current reference signal input
Terminal 13 and 18 For speed control these terminals must be jumpered
Terminal 17 Reference signal (negative) 0-max. 200V
depending on value of resistor R83
General input voltage 0-10V
Terminal 19 and 20 Terminals for connection of a.c. tachometer
Output voltage of tachometer approximately 100-150V at rated motor speed.
rWhen tachometer feedback is utilized jumpersIand VII and resistor R82 must
be removed.
rJumpers IX and Xmust be installed and jumper VIII must be removed.
rThe adaption of the tachometer signal is achived by changing the value of
resistor R91.
Terminal 11 and 20 Terminals for connection of d.c. tachometer
KL. 11 = Negative
KL. 20 = Positive
rJumpers IX and Xmust be removed and jumper VIII must be installed.
rThe adaption of the tachometer signal is achieved by changing the value of
resistor R91.
R91 is calculated as follows:
R91 in kOhm = tachometer voltage at rated motor speed minus 50
Terminal 22 and 23 Relay contacts (normally open, no potential)
(for operation of auxiliary armature solenoid.)
Terminal 24 and 25 Terminals for quick-stop (normally closed)
Terminal L1 and N Terminals for connection of fan 230V VAC, 50/60Hz at TA-60/6P
2.3 Terminal Strip KL. 2 (Only at TA-40/6P available)
Terminal 3 and 4 Terminals for connection of fan 230V VAC, 50/60Hz

4
missprints and technical changes reserved Instruction & Operating Manual
TA-15/6P...200/6P
3. Drive control adjustments
Phaseballance P1 Adjustments of the triggering angeles of the individual Thyristors in order to
obtain equal currents for all Thyristors. Do not adjust.
(This potentiometer is adjusted and sealed by the manufacturer)
Accelerationrate P2 Adjustment of the linear acceleration time of the motor from min. to max.
speed (2-15 sec.)
IxRCompensation P3 This potentiometer enables to compensate for the voltage drop in the
armature and in the supply line when armature feedback is utilized.
When tachometer feedback is used set this potentiometer fully counter
clockwise.
Deceleration P4 Adjustment of the linear deceleration time of the motor (provided: positive
torque) from max. to min. speed (adjustable from 2-15 sec.) This
potentiometer is only operative when jumper VI is installed or when the
reference speed is changed.
Current limit P5 Adjustment of the requested max. armature current.
(adjust the nominal motor current)
Minimum Speed P6 Adjustment of min. speed during operation.
(set potentiometer fully counter clockwise)
Jogspeed P7 Speed adjustment for jog speed
Stability P8 Adjustment for the dynamical adaption to the load.
Maximumspeed P9 Adjustment of max. speed during operation.
(set potentiometer fully counter clockwise)
Delay time P10 Adjustment of the control relay from approx.2-10sec.
(other delay times on request)
4. Indicators
LED 1clear Thyristor triggering
LED 2green Power supply -15V
LED 3red Indication of malfunction of field, Blocking protection, Phase control, current
output control
LED 4red Triggering pulse fault, Current output control
LED 5green Power supply +15V
LED 6red Current limit/Over-speed
LED 7yellow Jog speed, relay d2
LED 8green Line voltage
LED 9green D.C supply ON, drive release
LED 10 yellow Speed control indication (from 10 to 100%), operative only if jumper VI is
installed.
LED 11 yellow Operation, relay d1

5
missprints and technical changes reserved Instruction & Operating Manual
TA-15/6P...200/6P
5.1 Armature feedback control (UA-controlled)
1) Jumper VI must be installed if a controlled decelaration at drive stop is requested. For Emergency
off the connection between terminals 24 and 25 must be opened (Quick-stop). The drive will be
locked immidiately.
2) Check all connections with an Ohm-meter for grounds.
3) Install jumpers Iand VII and also resistor R82 (22 KOhm).
4) Check if line voltage corresponds with voltage indicated on the type marking. Select applicable
frequency, 50 Hz or 60 Hz with frequency-switch.
5) Switch on line voltage. The following LED must light up:
LED 8 green Line on
LED 5 green +15V
LED 2 green -15V
The diodes LED 4 (red) and the six diodes LED 1 (clear) will only light up briefly.
6) Measure field voltage at terminal F+ and F- with a Multimeter (moving coil meter with at least 330
Ohm/Volt) 270V at 400V or 155V at 230V line-voltage. Measure voltage at potentiometer (terminal
5- and 6+) 10 V d.c. Set min. speed potentiometer during this measurement fully counter
clockwise.
7) Potentiometer P4 Acceleration time, set in center position
Potentiometer P2 Deceleration time, set in center position
Potentiometer P3 IxR Compensation, set fully counter clockwise
Potentiometer P8 Stability, set in center position
Potentiometer P7 Jog speed, set fully counter clockwise
Potentiometer P10 Delay time, set fully clockwise
8) Switch on the drive, LED 11 yellow (Drive on) and LED 9, green (drive release) will light up. When
the speed potentiometer is turned in clockwise direction, the armature voltage and the motor
speed respectively, will increase. This causes the six clear diodes LED 1 (Thyristor triggering) to
light up. Adjust potentiometer P9 (max. speed) for the requested armature voltage/motor speed.
Now set speed potentiometer fully counter clockwise, the output voltage must drop back to 0V.
Now adjust potentiometer P6 for the requested minimum speed.
9) Switch off drive, Jog speed switch on.(LED 7 and LED 9 will light up). Adjust the requested jog
speed with potentiometer P7 (Jog speed).
10) Adjust I x R compensation. Check for an apoprox equal speed with and without motor load in the
lower speed range. If the potentiometer is turned in clockwise direction the speed under load will
increase.
If the compensation potentiometer is set too high, the drive will become unstable.
Caution!
Do not useany Mega-Ohm-meter, buzzer or similar test instruments.
Test instruments must be galvanically seperated from a.c. line.
5. Functional tests and preliminary adjustments before operation

6
missprints and technical changes reserved Instruction & Operating Manual
TA-15/6P...200/6P
11) Current limit: In order to check the current limit the field must be disconnected, the motor must be
blocked and the field control (jumper XI) must be jumpered. Switch on drive and preselect speed
and adjust the requested current with P5 (current limit). The red LED 6 (current limit) must light up.
This adjustment should be performed with in 10 sec., otherwise the blocking control will become
effective. If the adjustment takes longer than 10 sec. and the bolcking control is actuated, press the
key TA to confirm the blocking. The drive will then immidiately operate at the current limit.
12) Zero-speed control: If a controlled deceleration after normal switch-off (provided the machine
operates with positive torque) is required, jumper VI must be installed to make the zero speed
control operative. (zero speed control is effective above approximately 10% of the speed.)
13) Stability potentiometer P8. This potentiometer must be adjusted so that the drive operates without
overshoot in the presset speeds.
5.2 Tachometer feedback control:
1) Check all connections with an Ohm-meter for grounds
2) Install required jumpers for tachometer feedback control (depending if a.c. or d.c. tachometer is
used (see page 2) terminals 19 and 20 or 11 and 20 respectively.
3) Remove resistor R82 and also remove jumpers VII and I. The electronic circuit is now without any
potential.
4) For all further adjustments refer to the adjustments as previously described for the armature
feedback control, however, I x R compensation (P3) must be set fully counter clockwise.
6. Troubleshooting
For fast and effective troubleshooting and for the location of defective components proceed as follows.
Check the drive for:
a) Intermittent or loose connections
b) Defective insulation of the connection leads
c) Defective motor (brushes etc.)
Caution!
Do not useany Mega-Ohm-meter, buzzer or similar test instruments.
Test instruments must be galvanically seperated from a.c. line. The electronic circuit
carries a voltage potential against ground when the drive is armature feedback
controlled (UA-controlled).

7
missprints and technical changes reserved Instruction & Operating Manual
TA-15/6P...200/6P
Drive does not run when switched to "DRIVE
ON"
6.1 Fault location
Symptom
LED 8 (Power on) does not light up.
+/- 15V (LED 5, LED 2) does not light up.
Possible causes
a) Defective fuse Si 1 on the upper PC-board
b) One phase is missing
c) No supply voltage (115V) for relays d1 and d2.
Check voltage (115V) between terminals 9 and
16
d) LED 8 or D37 defect.
a) One phase is missing
b) Check power supply, measure +/- 24V
a) Motor load too high.
b) Drive operates at the current limit, LED 6 lights
up.
c) Current limit is adjusted too low, drive switches
off after short operation.
d) Defective speed potentiometer.
a) Check switch-on contact (terminals 1 and 9)
b) Defective fuse Si 1 on the upper PC-board
c) LED 8 (Power on) does not light up
d) LED 9 does not light up however LED 11 lights
up, jumper or quick-stop contacts terminals 24
and 25 not closed.
e) No reference voltage (terminal 2) voltage is
variable by speed potentiometer from 0 to 10V
f) Relay d6 (malfunction) not energised. LED 3,
red, lights up. Confirmation of malfunction is
only possible if LED 4 and LED 6 do not light
up and if the field control is not activated.
g) Check three phase line input.
h) Defective fuses Si 1, Si 2 or Si 3 on lower PC-
board.
i) Check field voltage and field current.
a) I x R compensation P3 is set too high.
b) Defective tachometer or tachometer leads.
c) Stability potentiometer P8 is wrong adjusted.
d) Auxiliary winding of the d.c. motor is wrong
connected
e) Triggerinig of one Thyristor temporarely
interrupted.
Output voltage does not increase when
speed potentiometer is turned up
Drive does not run stable

8
missprints and technical changes reserved Instruction & Operating Manual
TA-15/6P...200/6P
Defective line fuse
a) Defective tachometer or interrupted
tachometer feedback, R91 missing
b) Interruptedarmature feedback. Check jumpers
Iand VII, R82 missing.
c) Maximum speed potentiometer P9 intermittent.
d) Minimum speed potentiometer P6 intermittent.
e) Interrupted potentiometer connection from
terminal 5 to start of speed-potentiometer.
f) Wrong polarity +/- on d.c. tachometer
connection. (Check terminal connection 11-20)
Drive runs at maximum speed, however
speed potentiometer is set for zero speed or
low speed
This concludes the preliminary preparation and adjustment of the
Thyristor-Drive-Control Type TA-15/6P...200/6P
a) Too low adjustment of current limit.
b) Motor is overloaded, mechanical defect on
machine or motor. Check motor brushess
c) Supply voltage +/- 15V for electronic circuit
incorrect or missing. Reference voltage + 10V
incorrect or missing. Check LED 5 and LED 2
d) Triggering of one Thyristor temporarely
interrupted. Defective tachometer or
tachometer leads. Defective minimum speed
potentiometer.
e) Defective speed potentiometer
a) Armature connections shorted or grounded.
Check power Thyristors.
b) Defective motor or armature. Check brushes.
a) Defective power supply
b) Jumper on the terminals 13-18 is missing
c) Check relay and relay supply
d) Defective speed potentiometer
e) Defective armature fuse
f) Check motor and motor brushes
g) Defective fuses Si 1, Si 2 or Si 3
Speed varies without change of the setting
of the speed potentiometer
Symptom
Drive does not run
Possible causes

9
missprints and technical changes reserved Instruction & Operating Manual
TA-15/6P...200/6P
7. Connection diagram
220VAC
220VAC
A
0 bis max. 200V
Sollwerteingang
ND3
ND2
ND1
AC-DYNAMO TACHYMETRIQUE
AC-Tachometer
Schnell-STOP
BLOWER
VENTILATEUR
Lüfter
Lüfter
VENTILATEUR
BLOWER
E.-STOP
AC-TACHOMETER
~
G
REF: INPUT
DC-DYNAMO TACHYMETRIQUE
DC-Tachometer
POTENTIOMETRE DE VITESSE
SPEED POTENTIOMETER
VITESSE D`ACCROCHAGE
Reglerfreigabe
ALTERNATIF
FIELD
DC-TACHOMETER
Sollwertpotentiometer
Schleichgang
JOG SPEED
DEBLOCAGE
RUN
EXCITATION
Feld
Anker
Netz
INDUIT
ARMATURE
ALIMENTATION EN
LINE
FAULT DOCKET
Störmeldung
-
G
+-
d2
E
d1
S
B2
E1/F1
A1
M
(Starting at TA-60/6P)
(ab TA-60/6P)
(Only by TA-40/6P availble)
(Nur bei TA-40/6P vorhanden)
Strom-Istwert
+15V
CURRENT FEEDBACK
24
L1
N
25
4
Kl.2
3
23
22
21
20
19
18
17
16
15
14
13
12
d3
Motor EIN
MOTEUR MARCHE
MOTOR ON
(bei TA-15/6P ist Kl.3=Kl.1)
(at TA-15/6P is Kl.3=Kl.1)
-15V
11
10
F+
d6
9
7
8
6
4
5
3
1
2
F-
A-
A+
L3
L2
L1
E2/F2
Kl.3
Kl.1
TA-15/6P...200/6P

10
missprints and technical changes reserved Instruction & Operating Manual
TA-15/6P...200/6P
8. Mounting template
TA-40/6P
TA-60/6P...200/6P
TA-15/6P
310
270
1
6
5
7 x 13
2
7
0
3
5
0
KL1
310
270
1
6
5
7 x 13
4
0
0
2
7
0
4
6
0
4
0
KL3
KL1
KL2
530
486
ø10,5
2
5
0
1
2
4
8
6
5
1
0
KL3
KL1
This manual suits for next models
4
Table of contents
Other tae Power Supply manuals
Popular Power Supply manuals by other brands
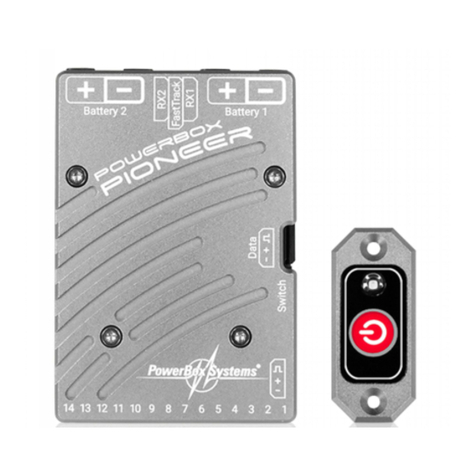
PowerBox Systems
PowerBox Systems PowerBox Pioneer instruction manual
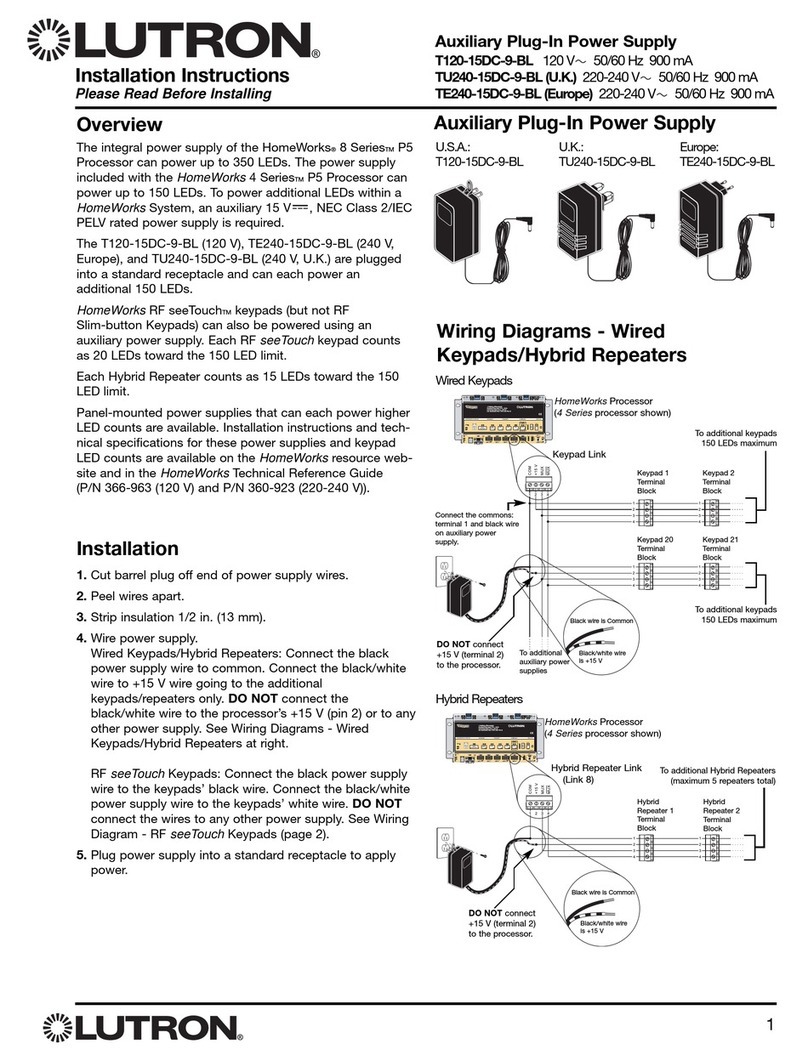
Lutron Electronics
Lutron Electronics T120-15DC-9-BL installation instructions
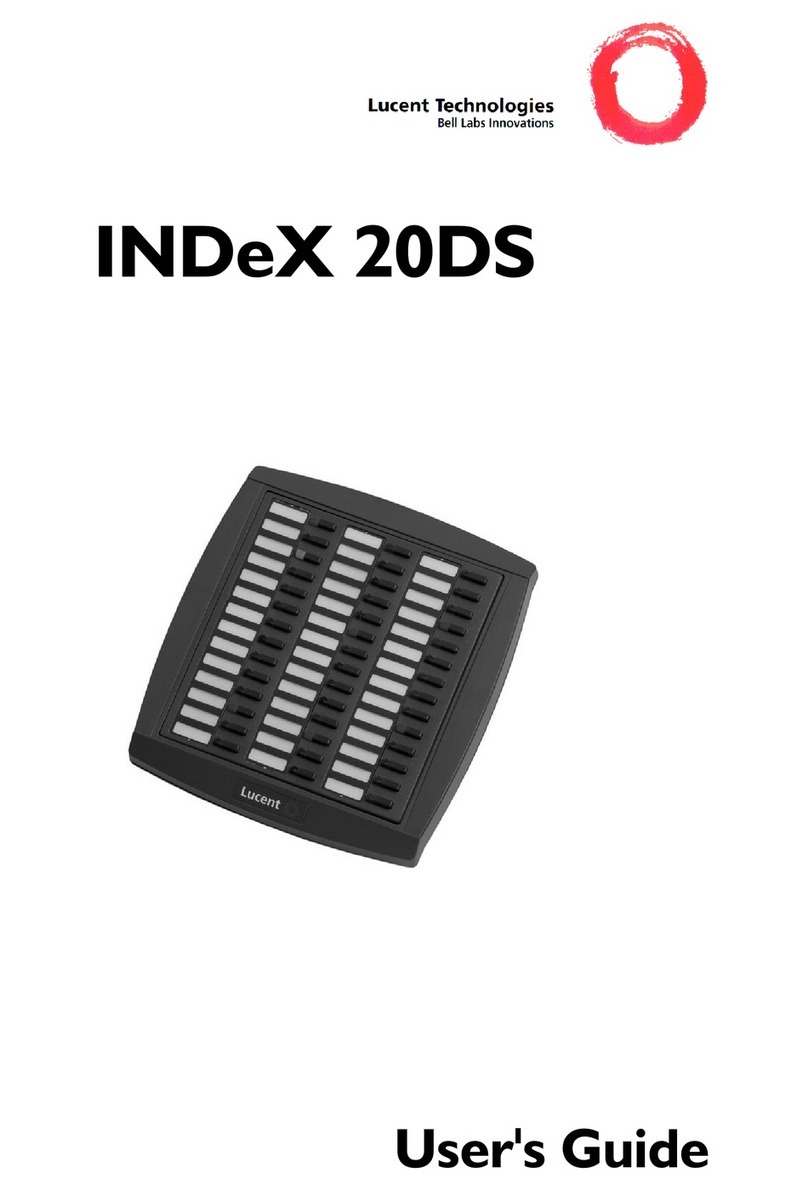
Lucent Technologies
Lucent Technologies INDeX 20DS Turret user guide

Elektro-Automatik
Elektro-Automatik PS 9080-50 operating guide
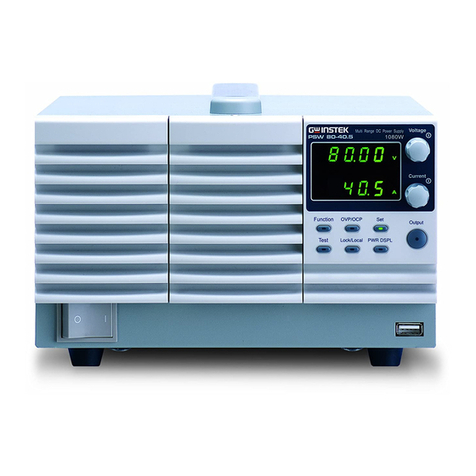
GW Instek
GW Instek PSW 30-36 user manual
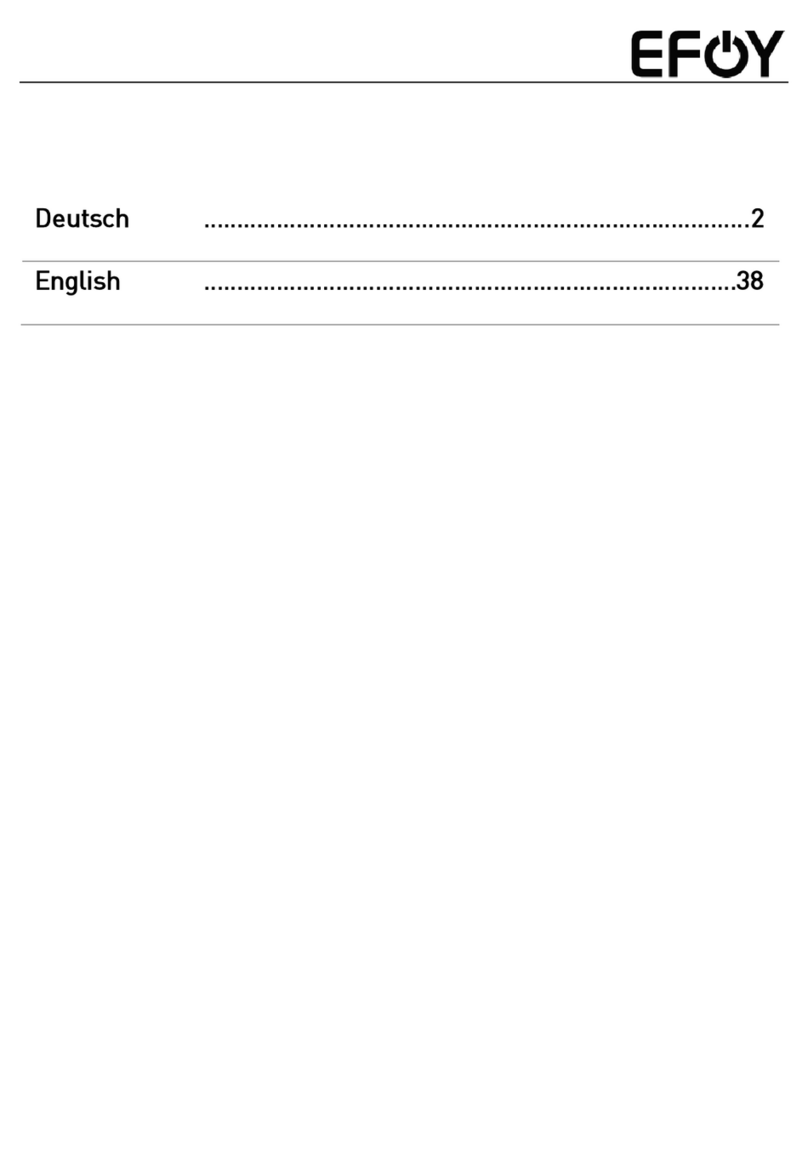
EFOY
EFOY ProEnergyCase 2020P-3 user manual