Tanco Autowrap 1814 User manual

Innovation in Agricultural Machinery
manual
1814 Autowrap
Operator’s

Tanco Autowrap -
Operator’s Manual
1
Chapter Contents Page
1 SAFETY DECALS
2 INTRODUCTION 3
3 TECHNICAL SPECIFICATIONS 5
4 SAFETY PRECAUTIONS 6
5 BALE WRAPPING 10
6 MACHINE SETUP 12
7 EH CONTROLLER INFORMATION 16
8 OPERATIONAL FEATURES 28
9 ELECTRO-HYDRAULICS 31
10 TROUBLESHOOTING 40
11 MAINTENANCE 45
12 GUARANTEE 46
13 DECLARATION OF CONFORMITY 47
TABLE OF CONTENTS

Tanco Autowrap -
Operator’s Manual
2
1. SAFETY DECALS

Tanco Autowrap -
Operator’s Manual
3
2. INTRODUCTION

Tanco Autowrap -
Operator’s Manual
4
2. INTRODUCTION
Tanco Autowrap Ltd congratulates you on your choice of the TANCO AUTOWRAP bale wrapping machine. We are certain you will be satised with the machine,
and that you will have the pleasure of your investment for many years.
There are three models on the 1814 Autowrap range. The ARC and S models are designed for static operation; the LA model is self-loading to operate in the eld.
All models can be operated fully automatically. The static models have the controller mounted in an enclosure on the machine;
this can be operated by radio remote control from the loading tractor.
The LA model has the controller in the tractor cab.
The 1814 is equipped with a patented, special mounting for the rollers, which enables the machine to wrap round* & square bales.
The 1814 can wrap both square and rectangular bales, from 47 x 80 to 120 x 120 x 190 cm long.
It can take bales of up to 1500 kg. It can also wrap round bales of up to ø1500 mm.
This machine has been in operation since 2007; customer demand has enabled us to develop this well adapted machine for the market.
This manual is meant to explain how the 1814 is prepared, mounted, operated and how it works, and along with the spare part’s list be a reference for
maintenance and troubleshooting. So take good care of this book, it is a part of the machine.
Read carefully through this manual, and specially chapter 4, safety precautions, before starting the machine, and follow the instructions thoroughly.
If problems should occur, ask your dealer for advice before you make the problem worse than it is. See also chapter 12, guarantee.
TANCO AUTOWRAP LTD. reserves the right to alter the product and/or its technical specications without prior notice and without this entitling any
alterations to previously supplied products.
© All rights in pursuance of the Copyright Act shall apply, and any reproduction of the contents of this booklet, in whole or in part, is forbidden without the permission of
TANCO AUTOWRAP LTD.
Reservation is made for possible printing errors.
*Optional ’round bale kit’ required for wrapping round bales.

Tanco Autowrap -
Operator’s Manual
5
Technical Specications Arc, S LA
Height 3400 mm 3400 mm
Width 2440 / 3215 mm 2440 /6950 mm
Length 2540 / 3425 mm 2540 / 3425 mm
Weight 2550kg 4500 kg
Wrapping Arm Speed (Recomended) 25 rev. per minute 25 rev. per minute
Wrapping Arm Speed (max) 30 rev. per minute 30 rev. per minute
Wheel Size 480/45-17 500/50-17
Maximum Bale Size 120x120x190 120x120x190
Maximum Bale Weight 1500 kg 1500 kg
Capacity Approx. 50 bales per hour Approx. 50 bales per hour
Pre-Stretcher(s) 750 mm 750 mm
Hydraulic Connection
Oil Pressure 175 bar / 50 litres/minute 175 bar / 50 litres/minute
Oil Amount (Max / Min)
Maximum Counter Pressure
Eltectrical Connection 12 V DC 12 V DC
NB: Tanco Autowrap Ltd. reserves the right to modify the construction and/or technical specications without warning and without rights to changes on already delivered products.
3. TECHNICAL SPECIFICATIONS

Tanco Autowrap -
Operator’s Manual
6
4. SAFETY PRECAUTIONS
TANCO AUTOWRAP LTD. does not take the responsibility for damages that may occur on machine, persons or other equipment, because of the machine NOT being used as described in
this manual, or because of the safety precautions NOT being followed.
Safety Equipment
Before using the machine, make sure that all guards and covers are securely tted. The machine must not be operated if a function does not work as described later in this manual.
The AutoWrap 1814 is equipped with an "EMERGENCY STOP" on the wrapping arm. This device stops all functions as quickly as possible, but is by denition not an emergency stop,
because it does not interrupt the feed. Nevertheless it has an equivalent function, so we have decided to call it an EMERGENCY STOP in this book.
Become Familiar with the Operations of the Machine
If you are unsure how to operate the machine properly, either use of or maintenance to your Tanco Autowrap, please contact your Tanco Autowrap dealer.
IMPORTANT!
Always make sure that nobody is inside the hazard area of the wrapping arm when the machine is in use. Safety distance is 5 metres
The machine must not be operated by persons who do not know enough about how to safely operate the machine, or by persons under the age of 16 years.
Dangerous Areas
TANCO AUTOWRAP LTD. has given the safety to the operator the highest priority, but it is still impossible to secure oneself of every danger area on the machine. Therefore we will now go
through some of the dangers that can occur when using the Auto Wrap bale wrapper. The 1814 is a large machine with many moving parts. As such there are signicant danger area’s
associated with it and it is vitally important that the operator is conscious of these and remains vigilant at all times when operating the 1814.
- Impact of The Wrapping Arm
During the wrapping process the arm rotates with a speed of 20-27 revolutions per minute around the bale. On the arm
there is mounted a lm Dispenser unit with a plastic roll. The Dispensers can give a person serious injuries if one comes to
close to the working area of the wrapping arm. To reduce this danger we have mounted an emergency stop* device on the
wrapping arm, this stops output for the wrap arm and should stop the wrap arm within two feet of movement when
something comes in the way of it.
It is very important that this protection always works and that it should not under any circumstances be disconnected.
Fig.4.1

Tanco Autowrap -
Operator’s Manual
7
- Crush Hazard Between the Tower/Chassis and the Wrapping Arm
As earlier explained, we have a wrapping arm with a Dispenser and a plastic roll. The wrapping arm passes the main frame during
each rotation. Here there is a risking of crushing if a person stands to close to the main frame when the wrapping arm passes.
The distance between the main frame and the wrapping arm is not large enough to give room for a person.
The clearance between the Dispenser and the Chassis there is also be a crush hazard.
- Crush Hazard Between the Tower and the Wrapping Arm
During the main wrapping process the wrapping arm rotates around the bale. Every time the wrapping arm passes
the tower/chassis, there is a crush hazard that can be dangerous for the ngers/ arms or bodies.
The distance between the stationary and the wrapping arm is between 25-40 mm.
4. SAFETY PRECAUTIONS
Fig. 4.3
Fig. 4.2

Tanco Autowrap -
Operator’s Manual
8
Crush Hazard Between the Rollers and the Main Frame
When adjusting the width of the rollers there is a danger of being trapped and squashed. Keep away from this area, ngers and feet also.
(See g. 4.3).
- Crush Hazard Cause by Cut and Start System
At the end of the wrapping process the plastic is held tight & cut from the bale. It’s held ready for the start of the next wrapping process.
When the cutter arm moves down to hold the plastic, there can occur a trap danger between the cutter arm and the cutter holder.
The cutter blade that perforates the plastic is very sharp, so keep hands away from the cutter. (See g. 4.4).
- Crush Hazard Between the Rollers
When the rollers on the machine are moved together, there is not enough space for a person between the rollers. Here there is a danger of being squeezed, so make sure that nobody is
between the rollers when they are moved together.
Note that the rocking rollers can rotate and even if they are in the level position they can drop suddenly. There is a serious risk of crushing associated with this. Never stand on the roll-
ers or stand between or lie under them. If you need to work in this area always ensure that everything is in a safe position. i.e rollers are dropped and fully opened and power supply is
disconnected
- Crush Hazard on the Load Arm
Always ensure that when you are operating the load arm there is nobody in the operating area of it as it could cause serious injury, either by crushing or squeezing.
- Hazard on the Conveyor
Always ensure that when you are operating the unloading conveyor there is nobody in the operating area of it as it could cause serious injury. If the optional rotate conveyor is tted
there is a risk of getting crushed when it is closing.
Note: The rollers on the conveyors and the two mounted on the chassis between the rocking rollers and the conveyor are free rolling. Never stand or sit on them as you are likely to loose
your balance and cause injury to yourself.
4. SAFETY PRECAUTIONS
Fig. 4.4

Tanco Autowrap -
Operator’s Manual
9
Locking the Conveyor
When the machine is not in use, make sure the unloading conveyor is raised and the parking bracket is connected. If this bracket is not connected, the conveyor can creep down, causing
a hazard on the road or to items the beside the machine.(See g. 4.5)
Connecting heavy working implements often has an overall negative eect on the tractor’s driving and braking capacity. When transporting on the road always ensure the machines
hydraulic brakes are connected to the tractor and that they are functioning correctly.
Transporting
When transported on a public road there are certain safety measures that must be taken:
1. Move the wrapping arm into the transport position using the controller. (See 10.)
2. Close the grab fully and raise the load arm fully. (See 10.9)
3. Raise the unloading conveyor and secure with the parking bracket. (See section 2.7)
4. Ensure machines lights are connected and working correctly.
5. Cut the ow of oil to the machine by disengaging the tractors spool valve and cut the power to the controller by pressing the Red Button on the controller.
Fig. 4.5
4. SAFETY PRECAUTIONS

Tanco Autowrap -
Operator’s Manual
10
Bale Wrapping Principles
The advantages of round bale silage are many, and include fewer feed units, a exible harvesting system, large capacity and the possibility of selling feed units.
In principle, the same fermentation processes occur whether the fodder is placed in a silo or pressed into bales and packed in plastic, i.e. lactic acid fermentation in anaerobic conditions.
The oxygen in the bale must be exhausted before fermentation begins.
The grass should be dried to approximately 30-40% solid content. The solid content can be determined by twisting the grass by hand. If drops of liquid are forced out of the grass, the
solid content is less than 25%. Low solid content (wet grass) can lead to increased butyric acid fermentation if preservatives are not added to the grass. If the solid content is too high,
(over 50%), normal fermentation will not take place and there will be enough oxygen in the bale to produce mould fungus.
The Baler
It is vital that the baler produces compact, well-formed bales, as misshapen bales can be dicult to wrap. Wrapping will also often take longer, thereby increasing the amount of plastic
used.
Dicult Bales
When a misshapen bale is wrapped, it will have a tendency to move outwards or inwards on the roller. If the bale begins to move outwards, the machine must be lifted slightly at the rear
edge to get the bale to rest against the support roller on the main frame. It can therefore be useful to use a hydraulic top link to make this adjustment easier.
If the bale to be wrapped is conical you must ensure that the sharp end is pointed at the tractor. It will then be easier to get the bale to lie correctly during packing. It is easy for such a
bale to“turn”forward in the direction in which it is pointing, and therefore lie against the support rollers. If the bale is lying on a slope it must be picked up from the lower side.
A hydraulic top link will again be advantageous.
Types of Plastic
A good type of plastic with good adhesive properties, and which is recommended for bale wrapping, must be used. The thickness of the plastic foil should be at least 25 µ. (25/1,000 mm).
In order that the plastic tightens suciently around the bale, it is stretched before being wrapped, so it is somewhat thinner when it is put on the bale. With short-term storage (up to
eight weeks) it is recommended that bales have a minimum of four layers of plastic at the thinnest points, with at least 52-53% overlap.
For long-term storage, or when the grass is wet when it is wrapped, the bale should have 90-100 µ plastic (six layers) and the same amount of overlap. If thinner plastic is used, more lay-
ers should be applied. If it is very hot the plastic will be stretched further, and more layers should be applied. It is better to have slightly too much than too little plastic on the bale.
From experience, light colored plastic produces slightly lower temperatures within the bale, and tends to improve feed quality.
5. BALE WRAPPING

Tanco Autowrap -
Operator’s Manual
11
Storage Location
Care should be taken in nding a suitable location for the storage of bales. The storage location should preferably be prepared before the bales are laid out. An elevation close to
well-drained roads is recommended. If the wrapped bales are simply placed on stubble there is a danger of the plastic being pierced. A tarpaulin or a thin layer of sand should
therefore be laid where the bales are to be stored over the winter.
Bales should be stored in the shade as far as possible. This reduces the danger of air leakage in the bales. A bale which is stored in sunlight and which therefore undergoes greater swings
in temperature“pumps in”a great deal of air in comparison to a bale stored in the shade. According to“Teknik for Lantbruket”[Technology for Agriculture] in Sweden, a bale stored in the
shade has only 40% of the air leakage of a bale which is stored in sunlight.
Stacking / Protection
If bales are hard and well formed, they can be stacked vertically, but loose and misshapen bales with low solid content should not be stacked higher than one layer, as this could easily
cause deformity and the danger of runo will be increased.
Bales can also be stored on their sides. The layer of plastic is thicker here, providing greater protection against piercing.
Bales should be covered with a tarpaulin or a ne-mesh net to protect against birds and small rodents. If the plastic is pierced, it must be sealed with weatherproof, hard-wearing tape,
preferably under the outermost layer of plastic. Ensure that the hole is adequately sealed.
For Best Wrapping Results...
1. Harvest the grass early.
2. Ensure the grass is dried out to 30-40% solid content. If there is a danger of rain, bale and wrap the
grass anyway.
3. Take care not to mix any earth in with the grass.
4. Use a baler that produces even, rm bales. Bales 1.2mtrs in width and with a diameter of 1.2-1.5mtrs
are preferred sizes.
5. Wrap the bales as soon after baling as possible; never more than two hours afterwards.
6. Use a good plastic type, applying six layers of plastic. This removes the need to use preservatives.
7. Store bales in the shade to reduce the danger of air leakage.
5. BALE WRAPPING

Tanco Autowrap -
Operator’s Manual
12
Mounting of the Machine
Be careful! There is a danger of being crushed when working implements are mounted and connected. Carry out the mounting procedures slowly and carefully, and use separate
and approved lifting equipment to make the work easier. See section 2 on safety regulations and pay attention to the various safety decals displayed on dierent parts of the bale
wrapper.
Hinged Tower
Because of the freighting of the machine, AUTO WRAP 1814 is sometimes delivered with the tower hinged down. Raise tower by lifting using the lifting eyes. Fit 10 M16 x 50 bolts but do
not tighten. Fit the dispenser to the wrap arm. Measure the height from the bottom of the dispenser to the chassis. Rotate the arm around ½ a turn and measure again. Raise or lower
the tower until the wrap arm is parallel to the chassis. Tighten up the top links on the back of the tower. Lower the lifting mechanism and check again. If necessary lift again and tighten
top links. Then t the tower support going to the front of the machine.
Tighten all bolts and lock top links and after several hours’use, tighten all the bolts once again.
Mounting of Dispensers
The dispensers are mounted using two M12 bolts. The dispenser height should be such
that the plastics is being applied as close to the centre of the bale on the end as possible. Generally we recommend that they
should be tted in the lowest position possible (where the plastic just passes over the cut and starts).
The height of the bale can then be decided by the width between the rocking rollers.
Mounting of Emergency Stop* Arm
The machine is equipped with emergency stop-arms on each of the wrap arms.
The releasing arm for the emergency stop component must be mounted.
Put the arm into the bracket and mount the hinge bolt.
Replace the washers and tighten the locking nuts. (See g. 5.1).
The return spring is to be fastened between the eye bolt on the arm and the eye bolt on the bracket.
Fig. 5.1
6. MACHINE SETUP

Tanco Autowrap -
Operator’s Manual
13
Electrical supply
The electric supply for the machine’s control unit and electro-hydraulic components should come directly from the tractors’12 volt battery .
The electric wires from the battery must have an area measurement of min. 2,5 mm².
Connection of other contacts on the tractor can cause risk of malfunction, and is not recommended.
Never tamper or remove fuses tted. Replace fuses with ones of the same rating.
Brown Leader Goes to Battery Plus Pole
Blue Leader Goes to Battery Minus Pole
EMERGENCY STOP.
The machine is equipped with a safety arm (2) on the wrapping arm (3), and its operation must be tested before work itself is started.
The safety arm is designed to stop the wrapping arm injuring operators or objects, when starting up or during the wrapping process.
The emergency stop* is constructed with a“positive”connection, i.e. it has to be in full order before the machine can be started. Note that if there is a fault with the system, the wrap arm
will work in manual mode but the controller will not go into automatic.
This consists of an electrical switch (1) mounted on the arm. This is wired normally open, and the actuating plate attached to the E-Stop arm rests on this and keeps it closed. The signal
from the two switches and the lm break sensors are fed through the centre of the wrap arm by means of a small electrical coupling.
If the electrical circuit is broken, the hydraulic oil ow is cut o and all functions stop immediately. This is indicated on the control box display by‘EMERGENCY STOP’
Before use, this function must be tested. Start the wrapping arm, hold out an arm or any obstacle, the wrapping arm must stop within 700mm.
To restart the machine the obstacle must be removed and the safety guard must return to its original position. If “STOP” is pressed before“RESTART”, the wrapping continues from the
point in the program at which the emergency stop was activated.
IMPORTANT!
GIVEN THE VELOCITY AND MOMENTUM OF THE ARM IT IS IMPOSSIBLE TO STOP THE WRAP ARM IMMEDIATELY.
THE EMERGENCY STOP ARM IS PROVIDED TO HELP REDUCE THE RISK OF SERIOUS INJURY AND GREAT CARE MUST BE
TAKEN WHEN OPERATING THIS MACHINE
Fig. 5.2
6. MACHINE SETUP

Tanco Autowrap -
Operator’s Manual
14
Mounting of Plastic Film (See Fig. 5.3 & 5.4)When loading a plastic roll, rst ensure the Top Cone is pushed up to the latched position,
then push back the Dispenser Insert until held in position by the Bottom Latch.
Place the Roll on the Bottom Cone and release the Top Latch.
BEWARE OF FINGERS!
Pull the lm between the rollers on the Dispenser Insert in the direction of the arrow, as shown below. (See also the sticker on the dispenser).
Release the Bottom Latch and allow the rollers to lie against the roll of lm.
Pull the lm from the roll and tie it to the bale.
Adjusting the Height of the Dispenser
The standard lm dispenser is designed for 750mm lm. If using 500 mm lm an adaptor is required which must be ordered separately. See parts
book and contact your dealer.
The plastic lm should hit at the middle of the bale wrapped and therefore it can be necessary to adjust the height of the pre-stretcher.
Top Latch
Bottom Latch
Dispenser Insert
Bottom Cone
Top Cone
Fig. 5.4
Fig. 5.3
Height Adjustment
Fig. 5.5
6. MACHINE SETUP

Tanco Autowrap -
Operator’s Manual
15
Tanco Dual Stretch Dispenser
All Tanco Autowrap machines are supplied with a patented dual stretch gear system. This system enables a quick change of stretch levels on the Film Dispenser.
If the Gear Bolt is tted in Position 1 (See Fig. 5.6), the top set of gears provide the stretch @ 70%. By removing the Gear Bolt from Position 1 and tting it in Position 2,
the bottom set of gears become the stretch gears giving 32% (for pre-stretched lm) or optionally 55% (for use in hotter climates or with square bales).
Fig. 5.6
Gear Bolt
Pos. 1 Pos. 2
Inner Gear Outer Gear % Stretch
60 Tooth 35 Tooth 70%
58 Tooth 37 Tooth 55%
54 Tooth 41 Tooth 32%
6. MACHINE SETUP

Tanco Autowrap -
Operator’s Manual
16
The Tanco Autowrap Bale Wrap Controller enables the operator to monitor and control the operation of the bale wrapper at any stage of the wrapping cycle. The controller is designed for
models : 1814 rotating-arm type wrappers.
There are 2 operating modes – Automatic and Manual. The automatic mode permits‘one-touch wrapping’to ease the workload on the operator.
The controller is fully programmable to optimise wrapping performance. Bale counts are automatically logged in any one of 10 selectable memory stores,
in addition to a grand total memory store.
IMPORTANT SAFETY INFORMATION!
Please read and understand the instructions for using this controller before operating the machine.
This controller is tted with a pushbutton type On/O Emergency Stop switch.
Always ensure the controller is switched OFF via this switch before attempting any adjustment or maintenance to the machine.
Please follow ALL other safety instructions given in the manufacturers’Operator Handbook for this machine.
Main operating Functions and Display
The principal instrument features and operating functions are shown in gure 7.1.
7. EH CONTROLLER INFORMATION

Tanco Autowrap -
Operator’s Manual
17
4-way Menu switch to
Set No. of wraps
- Change/reset bale sub-total
- Access Operator Setup menu
- Access Technician Setup menu
- Press ESC to switch between normal (N) and
secondary function (S)
L1 - Pause bale rotation
(during auto-wrap cycle)
L2 - Cut and grip lm
L3 - Slow wrap
L4 - Reverse wrap arm
L5 - Bale load Cycle (A)
Starts Continuous Cycle
LOAD/WRAP/OFFLOAD
(If Continuous is On)
Power On/O
/Emergency Stop
L6 - Select Operating Mode
A 2-line, 32 character dot matrix ,
back-lit display shows in the normal
operating mode:
- Current No. of wraps
- Target No. of wraps
- Wrapping speed (rpm)
- Bale total (10 separate
R1 - Pause wrapping (Auto)
Rotate rollers (Manual)
Level Bale manually for ooading
(if not auto leveled)
R2 - Release lm grip
R3 - Fast wrap / Resume wrap after
manually pausing
R4 - Add 1 wrap to current
(or next) bale
R5 - Bale unload. Discharges the
bale from the conveyor (A).
Tips & rotates rollers (M)
R6 - Start Auto Wrapping cycle
(Press STOP switch to stop cycle e.g.
in an emergency, otherwise press to
pause the cycle)
Fig. 7.1
7. EH CONTROLLER INFORMATION

Tanco Autowrap -
Operator’s Manual
18
Operation
Operation in Automatic mode
The controller is generally used in automatic mode for‘one touch wrapping’.
The complete cycle can be broken into three main parts, Loading, Wrapping and Unloading. The default setting of the controller is for each of these tasks to be performed and then wait
for the operator to activate the next operation. If Continuous (in Operator Setup) is set to ON, then the machine will run the complete cycle without operator intervention
Note: In Continuous operation the machine loads and unloads simultaneously, take great care that rotate conveyor has sucient room to operate safely.
‘A’ on the display indicates that the controller is set in Automatic mode. If not, press L6 to select.
Place a bale on top of the machine. Pressing the L5 button or with the controller in N(see 2.5) mode it can be done using the Hand controller.
If Continuous is set to On (Operator Setup) then this button will start Loading, then when the load arm reaches down sensor Wrapping automatically starts and ooading automatically
starts at the end of the wrapping cycle.
Press the R6 switch to commence the automatic wrapping cycle. The cycle is completed when the target number of wraps has been reached.
Once wrapping is complete the bale will be discharged onto the unload conveyors. You can now load the next bale or if you like press the R5 switch to unload the bale. Note if your ma-
chine has a non-rotate conveyor you must be stationary when doing this.
7. EH CONTROLLER INFORMATION

Tanco Autowrap -
Operator’s Manual
19
Manually interrupting an automatic wrapping cycle
Press the Stop switch to bring the wrapper to a controlled stop. Pressing the R6 switch will continue the auto-wrap cycle from where it stopped.
For safety reasons, if it is necessary to work on the machine (e.g. in the event of a lm break or the lm running out), then it is strongly recommended that you then switch the
controller o via the red stop button and disengage the machine power source. Pressing the R6 switch after switching the controller back on will resume the auto-wrap cycle
from where it stopped.
Unless it is an emergency situation, do not bring the machine to a stop by pressing the red stop button as this will impose unnecessary strain on the machine.
Manual options in Automatic mode
With the controller in automatic mode, the following manual functions are possible.
- Slow Wrap (L3): (not during the wrapping sequence). Press R3 to resume the normal fast wrap.
- Reverse Wrap Arm (L4): (only enabled outside of the wrapping sequence). Press this button to nudge the wrap arm backwards to the desired position.
- Pause Bale Rotation (L1): (function active during auto-wrap cycle). Hold this button to add more lm to a particular part of the bale. Release the button when sucient additional lm
has been applied.
- Bale Indexing (R1): (function active in manual mode). Press and hold this button to index the bale. Release the button when the bale is at the desired position.
Rectangular bales are automatically rotated till level at the end of wrapping before ooading. If the controller thinks the bale is not level then Bale Not Level message ashes on the
screen and the sequence will stop. To continue, hold this button down until the bale is level and when the button is released the bale will automatically ooad.
NOTE: The R5 button can also be used to rotate the rollers in manual mode but note that it also unloads the bale!
Add 1 Wrap (R4): Each time you press this button an additional wrap will be put on the current bale if the wrapping sequence is in progress, or onto the next bale if the automatic cycle
has not yet been started. You can add as many wraps as required.
Operation in Manual mode
‘M’on the display indicates that the controller is set in manual mode. If not, press L6 to select. In manual mode you have total control of every stage of the wrapping cycle.
The software logic determines which manual functions can be activated at any point in the wrapping cycle.
Should the operator incorrectly select a function at a certain stage during the wrapping cycle, then that operation will not be performed.
7. EH CONTROLLER INFORMATION
Table of contents
Other Tanco Autowrap Stretch Wrapping System manuals
Popular Stretch Wrapping System manuals by other brands
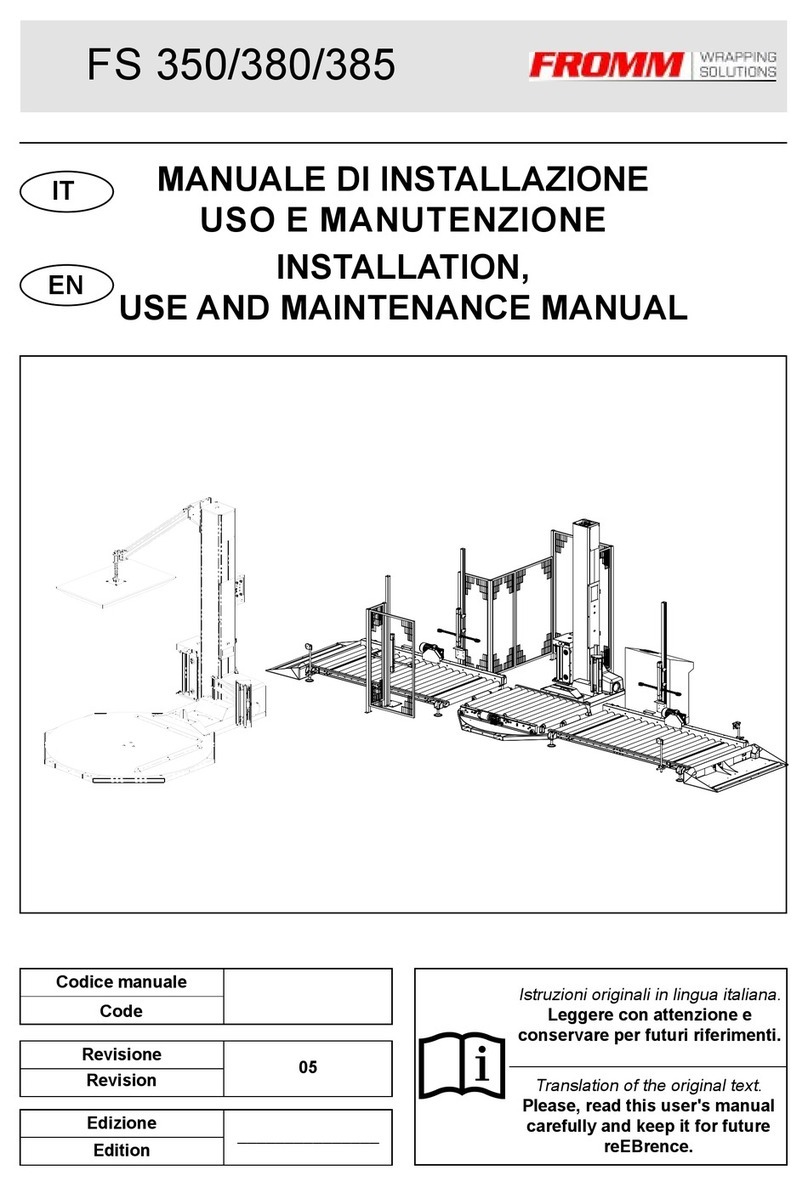
Fromm
Fromm FS350 Instructions for installation, use and maintenance manual
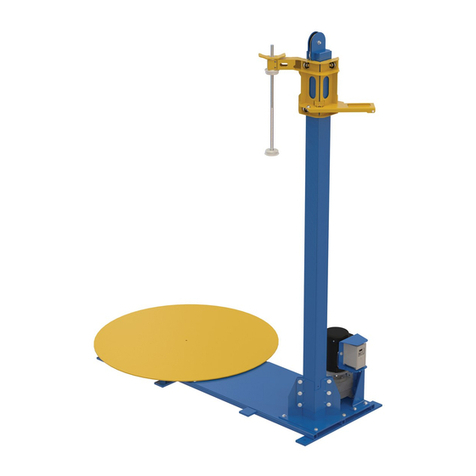
Vestil
Vestil SWA-48 owner's manual

SealerSales
SealerSales U-450 operating instructions
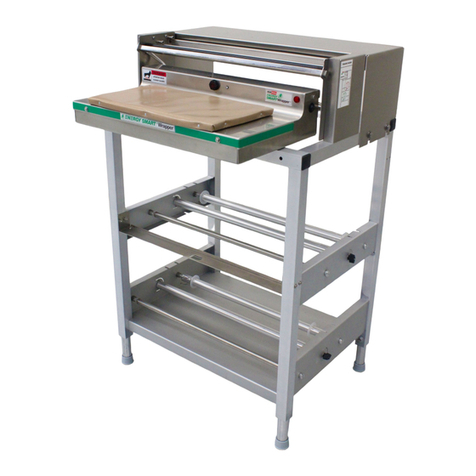
Heat Seal
Heat Seal 200ES Operating & service parts manual
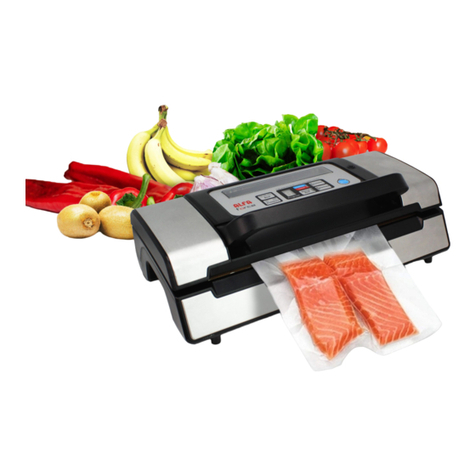
Alfa Network
Alfa Network FORCE Instructions and Safety
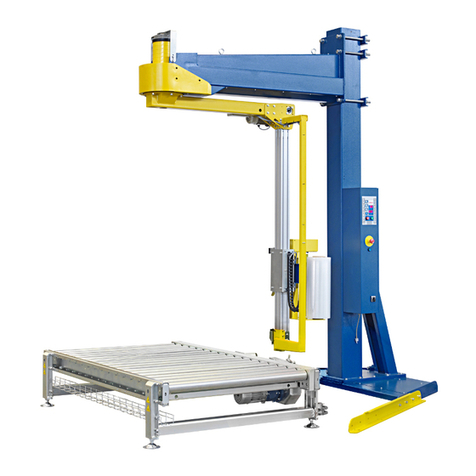
Fromm
Fromm FS 540 Installation, use and maintenance manual