TC Communications TC1630R User manual

Notice!
Althougheveryefforthasbeenmadetoinsurethatthismanualiscurrent
and accurate as of date of publication, no guarantee is given or implied
that this document is error free or accurate with regard to any specifica-
tion. TC Communications, Inc. reserves the right to change or modify
the contents of this manual at any time without prior notification.
TC1630R/S
RACK MOUNT/STAND ALONE
T1/E1 FIBER OPTIC MODEM
User's Manual
© COPYRIGHT 1992-2007. ALL RIGHTS RESERVED.
MODEL:
S/N:
DATE:
TC Communications, Inc. 17881 Cartwright Road - Irvine, CA 92614

- 2 -
TC1630R/S User's Manual
Rev. 2.5
This unit has been setup at the factory as follows:
LINE CODE LINE LENGTH
AMI B8ZS HDB3 T1/E1 0 -133 133-266 266-399 399-533 533-655
( ) ( ) ( )
Factory Default Configuration
SW1: Line Code/Line Length switch setting (Only one setting should be marked):
ON
LEN2
LOCLB
RMTLB
LEN1HDB3
LEN0
B8ZS
AMI
1234
1 2 3 4
1
2
3
4
5
6
7
8
ON
LEN2
LOCLB
RMTLB
LEN1HDB3
LEN0
B8ZS
AMI
1234
1 2 3 4
1
2
3
4
5
6
7
8
ON
LEN2
LOCLB
RMTLB
LEN1HDB3
LEN0
B8ZS
AMI
1234
1 2 3 4
1
2
3
4
5
6
7
8

- 3 -
TC1630R/S User's Manual
Rev. 2.5
Table Of Contents
Factory Default Configuration ................................................................................................................ 2
Chapter 1 - Overview ............................................................................................................................... 4
Description.......................................................................................................................................... 4
Front Panel.......................................................................................................................................... 5
LEDs Functions ............................................................................................................................ 5
DIP Switch Functions .................................................................................................................. 6
Fiber Optic Specifications ................................................................................................................ 6
Transmission Distances (typical) .............................................................................................. 6
Launch Power & Sensitivity ....................................................................................................... 6
Rear Panel........................................................................................................................................... 7
Functional Description ...................................................................................................................... 8
Chapter 2 - Installation ............................................................................................................................ 9
Unpacking the Unit ............................................................................................................................ 9
Equipment Location .......................................................................................................................... 9
Power Supply...................................................................................................................................... 9
T1/E1 Connection .............................................................................................................................. 9
Dry Contact Alarm Switch (optional) .............................................................................................. 9
Installation Procedure....................................................................................................................... 9
TC1630R/S's Configuration ...........................................................................................................10
System Start Up ...............................................................................................................................11
Chapter 3 - Troubleshooting ................................................................................................................. 12
General ..............................................................................................................................................12
All LEDs are Off................................................................................................................................12
Alarm LED .........................................................................................................................................12
Optic Cable Types............................................................................................................................12
Calculating the Fiber Optic Loss Budget .....................................................................................12
Cable Connection Verification .......................................................................................................13
Dry Contact Alarm Relay.................................................................................................................13
Chapter 4 - Bench Tests ........................................................................................................................ 14
General ..............................................................................................................................................14
Test Equipment Requirements ......................................................................................................14
Pre-Installation Tests.......................................................................................................................14
Local Loopback Test ........................................................................................................................14
Optical Loopback Test .....................................................................................................................15
Remote Optic Loopback Test .........................................................................................................15
Chapter 5 - Component Placement ...................................................................................................... 16
Chapter 6 - Specifications ..................................................................................................................... 17
Appendix A.............................................................................................................................................. 18
Setting the E1 Interface Impedance .............................................................................................18
Appendix B.............................................................................................................................................. 19
Electrical Signal Cable Connection...............................................................................................19
Appendix C.............................................................................................................................................. 20
19" Rack with Dual Power Cards ...................................................................................................20
Appendix D.............................................................................................................................................. 22
Return Policy ....................................................................................................................................22
Warranty ............................................................................................................................................22

- 4 -
TC1630R/S User's Manual
Rev. 2.5
Chapter 1 - Overview
Description
The Model TC1630R/S is a T1/E1 Fiber Optic Modem that converts analog T1 or E1 signals to digital fiber
optic signal and vice versa. TC1630R is for 19" rackmount and TC1630S is for standalone unit. Both have
the same functions and features, the only difference is power connectors. For convenience, TC1630R/S and
TC1630 will be used interchangeably throughout this manual.
TC1630 offers advanced features such as digital transmission, jitter removal and a field replaceable Line
Interface Module. Because it is based on modern FPGA (Field Programmable Gate Array) technology, the
IC chip counts are reduced to a minimum, hence offering extremely low power consumption (less than 3
watts) and higher reliability.
Transparent to the framing format, the TC1630R/S’s T1/E1 interface shapes the transmit pulse to support
CCITT G.703, or, for connecting to DSX-1 cross connects, copper line distances are from 0 to 655 feet. The
internal elastic buffer removes jitter from transmit data.
The TC1630R/S has multiple LED indicators to ease installation and troubleshooting. These LEDs indicate
power,operatingvoltage,alarmstatus,localandremoteT1/E1signalloss,bipolarviolations,alloneswarning,
Optic signal sync active and more. Eight DIP switches, accessible from the front panel, control settings for
Line Code, Line Length, Local Loopback and Remote Loopback. The dry contact alarm relay switch
provides remote alarm monitoring capability.
The TC1630R/S is compatible with all types and sizes of fiber optic cable. Fiber optic connectors are ST
(optional FC). T1 or E1 signal can be connected to two pairs feed-thru detachable terminals or a RJ-48C
connectorat the rearpanel. Inputpower is 12V DCor 115/230V AC withanexternalpower cube. Alternate
power sources are available as an option (see Chapter 6 - Specifications).
Note: The terms "TC1630R/S" and "TC1630" are used interchangeably in this manual.
Figure 1. Typical Point-to-Point T1/E1 Application
CSU/DSU
TC1630R/S
TC1630R/S
CHANNEL
BANK/
CUSTOMER
TERMINATION
DEVICE
T
1
/
E
1
T
1
/
E
1
T
1
/
E
1
T
1
/
E
1
OPTIC
Tx
OPTIC
Tx
OPTIC
Rx
OPTIC
Rx

- 5 -
TC1630R/S User's Manual
Rev. 2.5
Figure 2. TC1630R/S's Front Panel
LAIS
T1/E1 LINE LEN
LEN2
LOCLB
RMTLB
LEN1HDB3
LEN0
B8ZS
AMI
L
L
O
S
R
L
O
S
B
A
P
W
R
V
c
c
S
Y
N
C
RMT LOC
AMI
B8ZS
HDB3
CSU133
266
399
MadeinU.S.A.
TCCOMM.COM
T1/E1 FIBER OPTIC MODEM
A
L
M
655
533
1
2
3
R
x
T
x
O
P
T
I
C
LINECODE
LOOP BACK TEST
R
x
O
P
T
1234
1 2 3 4
1 2 3 4
5 6 7 8
LEDs Functions
Alarm-
ALM: Alarm indicator. The Alarm LED will light when following conditions occur:
The unit is in a diagnostic mode.
When an invalid line code or line length is set.
Optic signal is lost.
Local T1/E1 signal is lost or all ones signal is received from customer's device.
Remote T1/E1 signal is lost.
When the "Line Distance" setting is set as "1 0 0" (when SW5 is on, and both SW4 and SW3 are
Off).
Power Supply Status-
Power A/B: These LEDs indicate which power source on the rear panel the unit is drawing from. If power redundancy is
utilized, both LEDs will light.
Vcc: +5V Voltage indicator. This LED should light whenever power is connected to the unit. It indicates the
correct operating voltage is being derived from the power source.
Optic Signal Status-
RxOPT: Solidly lit, it indicates optical signal received.
Flashes when the optical signal is lost.
SYNC: Indicates a valid composite signal is being received.
Configuration Setting-
AMI/B8ZS/HDB3: These LEDs indicate the T1/E1 line code setting (SW6, 7, 8).CSU: Channel Service Unit indicator. This
LED will be lit whenever the minimum T1 Line Length is set (see Configuration Table - page 10).
133-655/CSU: These LEDs indicate the T1 Line Length distance setting (SW3, 4, 5).
Local T1/E1 status and warning-
LAIS: When flashing, it indicates "all ones" signal received from user's equipment.
LLOS: When flashing, it indicates the loss of the T1/E1 signal from local user's equipment.
BPV: Bipolar Violation LEDs. These LEDs light when bipolar violations (Line Code violations) are detected. The
severity of the violation is represented by three LEDs. Higher BPV rates cause more LEDs to light.
LOC: Indicates the Local Loopback function is enabled (SW2 is On).
Remote T1/E1 status and warning-
RLOS: When flashing, it indicates the loss of the T1/E1 signal from remote user's equipment. This LED will be Off
when no fiber cable is connected or the fiber cable is bad.
RMT: Indicates the Remote Loopback function is enabled (local SW1 is On).
Front Panel

- 6 -
TC1630R/S User's Manual
Rev. 2.5
DIP Switch Functions
Slide switch to the Right (On) position to activate the function.
AMI/B8ZS/HDB3: These switches select the Line Code (see Figure 5).
LEN0/LEN1/LEN2: These switches define the DSX-1 cross connect distance. There are 5 partitions to
choose from. In a T1 application, this is the length of twisted pair cable connecting the TC1630R/S to the
user's equipment, which may be a CSU or DSU. The cable lengths can be from 0 to 655 feet (see Figure
5).
Local LBT: This switch initiates the Local Loopback function. The T1/E1 signal is received and decoded,
then looped back to the T1/E1 "out" terminals for diagnostic testing.
Remote LBT: This switch activates remote unit into Remote Loopback function. The composite optic
signal is transmitted to remote unit and decoded, then looped back to local unit.
Fiber Optic Specifications
Transmission Distances (typical)
The TC1630R/S is compatible with all popular sizes and types of fiber. Transmission distances up to 3km*
are typical over Multimode fiber at 850nm and 4km* at 1310nm. Distances to 35km* are typical over Single
Mode fiber at 1310nm.
Launch Power & Sensitivity
Transmitter: LED/ELED; typical Launch Power - -19dBm* (850nm/1310nm MM, @62.5/125µm)
-15dBm* (1310nm Single Mode, @9/125µm)
Receiver: PIN Diode; typical Sensitivity - -35dBm* (850nm/1310nm MM, @62.5/125µm)
-35dBm* (1310nm Single Mode, @9/125µm)
*Launch power, sensitivity and distance are listed for reference only. These numbers may vary. Contact factory for
higher loss budget requirements.
ON
LEN2
LOCLB
RMTLB
LEN1HDB3
LEN0
B8ZS
AMI
1 2 3 4
1234
1
2
3
4
5
6
7
8

- 7 -
TC1630R/S User's Manual
Rev. 2.5
Figure 3. TC1630S Rear Panel
Rear Panel
* Note 1: The T1/E1 signal can be connected to either the terminal block connectors or the RJ-45F
connector as shown above on the rear panel, but not on bothat the same time.
* Note 2: The T1/E1 signal is bipolar, independent of the polarity. Polarity on the "IN" & "OUT" terminal
block connector shown above is shown for reference only.
TC1630S Rear Panel
T1/E1 Signal Input, Output
Terminal Blocks
T1/E1 Signal Input, Output
RJ-48C Female Connector
Power
Dry Contact (Alarm)
+-+-
PWR A PWR B
IN OUT
Normalopen
Rating:50 VDC @500mama
x
1 2 34567 8
NOTE: TC1630 STAND-ALONE
VERSIONSHOWN
24VDC12VDC 125VDC48VDC
+-+-
Rating: 12VDC @250mA (typical)
24VDC @125mA
48VDC @63mA
125VDC @25mA
(typical)
(typical)
(typical)

- 8 -
TC1630R/S User's Manual
Rev. 2.5
Functional Description
As shown in figure 4, the TC1630 consists of five basic function blocks: DIP switches, LEDs, T1/E1
interface, T1/E1 signal processor and optic interface.
DIP switches are used to configure the TC1630 according to a customer's application such as line code and
line distances. LEDs are used to display corresponding DIP switches settings, power supply status, optic
signal status, signal warnings, alarm, etc... the T1/E1 interface converts T1/E1 analog signals to digital
signals and provides local and remote loopback function. The signal processor composes T1/E1's timing and
data to a bit stream. The optic interface converts the electrical bit stream to an optic signal and vice versa.
Figure 4. TC1630R/S Functional Diagram
T1/E1 Signal Processor
Optic interface
AMI or
B8ZS/HDB3 LineLength
1,2,3
Remote
Loop
Test
LED Indicators on front panel
to optic
cable
Replaceable T1/E1
line Interface Module
Elastic Buffer
to T1/E1 line
from T1/E1 line
Line Driver Line Receiver
TC1630R/S
External DIP Switches (accessible from front panel)
TxA
RxA
Local
Loop
Test
Power
A,B Vcc Alarm Optic
Sync Local
Loss Remote
Loss Local
Loop
back
Remote
Loop
back
All
Ones
Warning
Bipolar
Violation
Line
Code
Setting
Line
length
Setting

- 9 -
TC1630R/S User's Manual
Rev. 2.5
Chapter 2 - Installation
Unpacking the Unit
Before unpacking any equipment, inspect all shipping containers for evidence of external damage caused
during transportation. The equipment should also be inspected for damage after it is removed from the
container(s). Claimsconcerning shipping damage shouldbemade directly tothepertinent shipping agencies.
Any discrepancies should be reported immediately to the Customer Service Department at TC Communi-
cations, Inc.
Equipment Location
TheTC1630R/S shouldbe located in an areathat provides adequate light, work space,and ventilation. Avoid
locating it next to any equipment that may produce electrical interference or strong magnetic fields, such as
elevator shafts or heavy duty power supplies. As with any electronic equipment, keep the unit from excessive
moisture, heat, vibration, and freezing temperatures.
Power Supply
The TC1630S is powered by an external DC power adapter rated 12VDC @250mA. There are two power
jacks at the rear panel for power redundancy. TC1630R is the rackmount version of the TC1630S. It can
be inserted into the card slot when power is on (hot swapable).
T1/E1 Connection
Two pairs of terminal block connectors and/or an RJ-45F connector are provide for the connection of the
T1/E1wire pairs. Whenviewing the rear panel,the left pairof terminal block connectorsareforT1/E1 signal
going into the TC1630R/S (receive), while the right pair of terminal block connectors are for the transmit
signal coming out of the unit. Note: The T1/E1 signal can be connected to either the terminal block connectors
or the RJ-45F connector, but not on both at the same time, refer to page 7.
Dry Contact Alarm Switch
A terminal block connector at the rear panel provides for the Dry Contact Relay Alarm. Normally in the
CLOSED position, any alarm condition will force the switch to the OPEN position. This relay can be
configured by the user if necessary (see Chapter 3 - Troubleshooting).
Installation Procedure
The TC1630R/S is designed for quick and easy installation. First, configure the modem for your specific
application by setting the Line Code and Line Length DIP switches. Once configured, you can connect the
optical, T1/E1 signal source and power.
Installation Procedure:
1. Select the Line Code (SW6, 7, 8).
2. For T1, select the Line Length (SW3, 4, 5).
3. Connect the T1/E1 signal source, either terminal blocks or RJ-48C connector.
4. Connect the optic cables. Verify single mode or multimode optic cable according to your TC1630
ordered. Using incorrect optic cables will result in a malfunction. Verify optic connections.
5. Connect the power. All the LEDs should flash for approximately three seconds.
After installation is completed, it is an excellent idea to verify the optical cable loss. This reading will both
verify the integrity of the circuit and provide a benchmark for future troubleshooting efforts.

- 10 -
TC1630R/S User's Manual
Rev. 2.5
Figure 5. TC1630R/S Configuration Table
TC1630R/S's Configuration
1. Select the application's Line Code: SW6, 7 or 8. Slide the appropriate switch to the Down (On) position.
AMI: set SW8 to the Down (On) position.
B8ZS: set SW7 to the Down (On) position.
HDB3: set SW6 to the Down (On) position.
Only one of the above switches should be selected, as any two switches in the Down (On) position will cause
the "Alarm" LED to flash.
2. Select the Line Length setting for T1: SW3, 4, 5 (see Figure 5). Slide the appropriate switches to the
Down position.
Depending on the distance between the TC1630R/S and the T1 cross connect, set the Line Length for the
T1 transmit line driver according to the table below. When connecting to DSX-1 cross-connects for Line
Lengths ranging from 0 to 655 feet, see DIP Switch Functions on page 6. There is no need to set the Line
Length for E1 applications; set SW3, 4, and 5 to the Up (Off) position.
Note: The “Line Length” setting “1 0 0” is invalid. If “Line Length” is set as (1 0 0), then the Alarm
LED will flashes, indicating the setting is invalid.
Legend:
0 = Off 1 = On
AMI
B8ZS
HDB3
DSX-1
ABAM
0-133 feet
133-266 feet
266-399 feet
399-533 feet
533-655 feet
CSU
NETWORK
INTERFACE
DSX-1
ABAM
CSU
NETWORK
INTERFACE
PCM-30,
G.703
0-655 feet
0-133 feet
133-266 feet
266-399 feet
399-533 feet
533-655 feet
0-655 feet
0-655 feet
L I N E C O D E
SW8 SW7 SW6 L I N E L E N G T H
SW5 SW4 SW3 LOCAL & REMOTE
LOOPBACK TESTS
1
1
1
1
1
0
0
0
0
0
0
0
0
0
0
1
10
00
0
1
1
1
1
1
0
0
0
0
0
0
0
0
0
0
1
10
0
0
0
0 0 1
1
0
1
0
1
1
0
0
1
1
0
1
1
1
1
0
11
10
0
1
0
0
1
1
0
1
1
1
1
1
0
1
0
1
1
10
0
0
1
0 0 0
0
0
0
0
0
0
0
0
0
0
0
00
0
0
0
0
0
0
0
0
0
0
0
0
00
0
0 0

- 11 -
TC1630R/S User's Manual
Rev. 2.5
3. Connect the T1 or E1 signal.
T1 signal connection for100 ohm line:Connect the incoming T1 signal (from your equipment) to the "in"
terminal blocks on the rear panel; they are not polarity sensitive. A valid T1 signal will cause the "LLOS"
LED turn to off. Connect the outgoing T1 signal (received from the optical cable) to the "out" terminal blocks.
E1 signal connection(The E1 interface can be used for either 75 or 120 ohm line - see Appendix A):
75 ohm line: Connect the incoming signal (from your equipment) to the "in" BNC adapter. Connect the
outgoing signal (received from optical cable) to the "out" BNC adapter.
120 ohm line:If twisted-pairs are used, connect the wires in the same way as the T1's wire. If dual coaxial
is used, connect the cores to the "in" terminal blocks for the incoming signal and to the "out" terminal blocks
for the outgoing signal (each cable has two cores & a shield).
4. Verify optical connections:
Make sure the local TC1630's optic "Tx" is connected to the remote TC1630's optic "Rx" (and vice-versa).
5. Connect power to both units.
System Start Up
When power is initially connected, the following conditions should be observed:
1. The "POWER A" and/or "B" LED is lit.
2. The "LLOS" LED is Off, indicating a valid T1 or E1 signal input.
3. The "ALARM" LED should be Off.
Start the T1/E1 signal transmission:
4. The "POWER A" and/or "B" LED stays lit.
5. The "SYNC" LED should be lit, indicating a valid received optic signal.
6. One of the line length LED should be lit. If "133" is selected, "CSU" LED should be lit too.
Note: If the modem is not functioning properly at this point, please refer to Chapter 3 - Troubleshooting.

- 12 -
TC1630R/S User's Manual
Rev. 2.5
Chapter 3 - Troubleshooting
General
Alarm conditions occur whenever an optical problem or "fault" condition is detected by the TC1630.
All LEDs are Off
If no LEDs are lit on the unit, check the DC power supply, terminal block connector plug, change to alternate
powerjack onthe rear panel,fuses A and/or B indicatedon page 17, and/or thepower source. If theproblem
persists, contact the Technical Support Department at TC Communications, Inc.
Alarm LED
When an alarm condition is detected, the Alarm LED will flash. The following fault conditions will cause
the alarm to be triggered:
1. Optic signal lost from optic "Rx."
2. Optic signal is marginal, which causes invalid data packets to be received; the "SYNC" LED will be "Off."
3. Received "space" or "mark" from local T1/E1 device.
4. An invalid Line Code setting exists.
5. The Line Length setting does not match the Line Code.
6. The local or remote T1/E1 signal is lost; the "LLOS" or "RLOS" LED will be also be flashing.
Note: The "RLOS" LED will be Off when there is no fiber cable connected or the fiber cable is bad.
Optic Cable Types
Conventionally, fiber optic cable withyellow-coloredinsulation is used for Single Mode applications;gray
or orange-coloredinsulated cable is for Multimode use. If Multimode cable is used in a Single Mode
application, the test results could be erroneous and confusing.
Calculating the Loss on the Fiber
The fiber optic link and/or connectors are frequently the source of various problems. Check out the
connectors and the integrity of the link first. Ideally, the link should be calibrated for total loss after the
installation has been completed. This will accomplish two things: (1) it will verify that the total loss of the
link is within the loss budget of the device and (2) it will provide a benchmark for future testing. For example,
a system that has been tested as having 6dB total loss when installed and suddenly tests out as having a loss
of 10dB probably has a connector or link problem.
*Thesenumbersarelistedforreferenceonly. WerecommendanOTDRreadingbeusedtodetermineactuallinkloss.
These are the reference values we used to calculate loss on the fiber :
Multimode 850nm :3 dB loss per km on 62.5/125µm cable*
Multimode 1310nm :2 dB loss per km on 62.5/125µm cable*
Single Mode 1310nm :0.5 dB loss per km on 9/125µm cable*
Single Mode 1550nm :0.25 dB loss per km on 9/125µm cable*

- 13 -
TC1630R/S User's Manual
Rev. 2.5
Cable Connection Verification
Electrical Cables:
1. Make sure all electrical signal connections match the pin assignments (I/O) for the device (check User's
Manual if necessary).
2. Verify signal connections by checking the status LEDs on the front panel of the TC1630R/S. If the
"LLOS" LED is flashing, a transmit signal is not being detected from the local device. If the "RLOS"
LED is flashing, no response signal is being detected from the remote device.
3. Verify that the correct Line Code setting (and Line Length setting for T1) has been configured and that
the appropriate LEDs light to match the setting selected.
4. Conduct a Local Loopback Test to help isolate an electrical interface problem (see Chapter 4 - Bench
Tests).
Optic Cables:
If the "SYNC" LED on the front panel is flashing or Off, this is an indication that the optic signal is not being
correctly received. Usually, unsecured fiber optic connectors or faulty cable are to blame. A good
connection is indicated by the "SYNC" LED on the front panel being solidly lit. This indicates that the
receiving cable is correctly connected to Remote unit's optic "Tx."
Dry Contact Alarm Relay
TC1630 has built-inDry contact relay switch. The status is for the relay switch is "normal open". It is
triggered by following major alarm conditions:
Optic signal lost
Local T1/E1 signal lost
Local user's T1/E1 device is sending "mark" data pattern
Local user's T1/E1 device's signal is causing bipolar violations
Invalid line code setting
Invalid line length setting
The electrical rating for the dry contact relay switch is
50VDC max
500 mA max.
switching power is 10 watts max.

- 14 -
TC1630R/S User's Manual
Rev. 2.5
Chapter 4 - Bench Tests
General
It is highly recommended to conduct bench tests before actual installation. Bench testing allows the user to
become familiar with all the functions and features of the TC1630 in a controlled environment. Knowledge
of the TC1630's functions and features will ease installation and troubleshooting efforts later on.
Test Equipment Requirements
End-user equipment required for testing:
1. Model 5575A T1 Micro BERT (Bit Error Rate Tester) Test Set with Terminal Block Connectors.
2. Two optical cable jumpers (patch cords) with appropriate connectors.
Pre-Installation Tests
1. Make sure the appropriate power supply accompanies the TC1630R/S unit (see page 9).
2. To verify that the unit functions properly, connect power to the unit's "PWR A" or "B" terminal blocks
(be sure to observe correct polarity) without connecting any other cables to the unit.
3. Onthe front panel,the appropriate greenPower "A" orPower "B" LEDshould be illuminated(depending
on whether you plug into the "A" or "B" terminal on the back of the unit). Both lights should be on if you
utilize power redundancy (power is plugged into both "A" and "B" on the rear panel).
4. The "ALARM" and "LLOS" LEDs should be flashing.
5. The "Vcc" LED should be illuminated. Please note: all other LEDs can be in a random state (flashing,
solidly lit, or off) as only upon proper receipt and transmission of a signal will the TC1630R/S unit set its
LEDs appropriately for normal operation. Proceed to the Local Loopback Test.
Local Loopback Test
The purpose of this test is to verify 1) the signal source recognition and 2) the connection between the
incoming signal and the TC1630R/S's terminal blocks.
1. Make sure your BERT tester is turned on and configured with the same setup as the TC1630R/S (and
your application).
2. Plug in the terminal blocks from the BERT tester to the TC1630R/S’s connectors on the rear panel.
When the input and output are connected correctly, the "LLOS" LED on the TC1630R/S will turn Off.
3. Slide SW2 (LOCAL LBT) to the Down (On) position. The "LOC" LED should flash on the front panel.
4. Make sure the "TERM" or "BRIDGE" LED on the tester is lit, and that the tester is in the "RUN" mode.
The tester should indicate a "SYNC" signal.
5. If any other LEDs illuminate or flash, make sure that all
DIP switches on the TC1630R/S are in the correct
position,thenresettheBERT tester. You should notsee
any bit errors. To verify this, inject an error using the
BERT tester to see if it will be recorded by the tester,
then verify that no additional errors appear after the user
injected error. Proceed to the Optical Loopback Test.
Local Loopback
IN
Optic Rx
Optic Tx
T1/E1
BERT
Tester
Local loopback
OUT
T1/E1 Line
Interface

- 15 -
TC1630R/S User's Manual
Rev. 2.5
Optical Loopback Test
At any time you may use a short optic cable to loopback the unit's Optic "Tx" to "Rx." The "SYNC" LED
on the front panel should light (solid) when a good optic signal is received. This test verifies the optic
transmitter's function as well as the receiver's. Upon successful completion of this test, proceed to the
Remote Loopback Test.
Remote Optic Loopback Test
1. Connect a second TC1630R/S unit. As with the first unit, follow the bench test steps on the previous
page. When you have completed the Local Loopback & Optical Loopback tests for the second unit,
proceed to the next step.
2. Remove the optical jumper cable from the local unit's "Rx" and connect it to the second unit's optic "Rx."
Add a second optical jumper cable to connect the local unit's "Rx" to the second unit's "Tx."
3. Verify that both TC1630R/S units have the same Line Code and Line Length settings.
4. On the local TC1630R/S, slide SW1 (Remote Loopback) to the Down (On) position. The "RMT" LED
on the remote TC1630R/S's front panel should flash, as well as the "LLOS" and "ALM" LEDs.
5. Make sure the "TERM" LED on the tester is lit, and that the tester is in the "RUN" mode. The tester
should indicate a "SYNC" signal.
6. IfanyotherLEDsilluminate or flash ontheunit,makesurethatallDIPswitchesonbothof the TC1630's
are in the correct position, then reset the BERT tester. You should not see any bit errors.
7. At this point, both units tested will have passed all electrical and optical tests and will have been verified
that they are functioning properly. Proceed to the next TC1630 unit to be tested or begin verifying other
equipment and cabling in your application (if you have not already done so).
Local Optic Loopback
IN
Optic Rx
Optic Tx
T1/E1
BERT
Tester
Optic Local loopback
OUT
T1/E1 Line
Interface
Remote Optic Loopback
IN
IN
Optic Rx
Optic Tx
Optic Rx
Optic Tx
T1/E1
BERT
Tester
Remote Optic loopback
OUT OUT
T1/E1 Line
Interface
T1/E1 Line
Interface

- 16 -
TC1630R/S User's Manual
Rev. 2.5
Chapter 5 - Component Placement
Figure 6. TC1630R/S's Internal PCB
U4
F1
POWER APOWER B
F2
JP2
FPGA
chip
1
2
3
4
5
6
7
8
O
N
4
3
2
1
SW1
INTERFACE MODULE
+
+
--
TERMINAL
BLOCK
CONNECTORS
Dry contact alarm relay
terminal block connector
T1/E1 Line interface
module
T1/E1 input and output
terminal block connectors
T1/E1 RJ-48C
connector Power A and B Terminal
block connectors
Fuses A, B
FPGA
FPGA configuration
EPROM
Optic transmitter
and receiver
LED indicators LED indicators
External
DIP switch
TxA RxA
SW2
DIP switch 2
(not used)
8
765

- 17 -
TC1630R/S User's Manual
Rev. 2.5
Chapter 6 - Specifications
Data Rates
T1 (per channel) ........................................................................................... 1.544 Mbps
E1 (per channel) ........................................................................................... 2.048 Mbps
Line Code .......................................................................................AMI, B8ZS, or HDB3
Optical
Transmitter ...................................................................................................... LED/ELED
Receiver ..........................................................................................................PIN Diode
Wavelength ............................................................................850nm/1310nm Multimode
.......................................................................................................1310nm Single Mode
Fiber Optic Connectors ..................................................................... ST* (FC optional)
Loss Budget ........................................... 15dB Multimode 850nm/1310nm @62.5/125µm
......................................................................................20dB** Single Mode @9/125µm
Electrical
Interface ..................................................................................................................T1/E1
T1 Connector (100 ohm) ......................................................................... Terminal Block
E1 Connector (120 ohm) ......................................................................... Terminal Block
E1 Connector (75 ohm) .............................................Terminal Block with BNC Adapter
System
Bit Error Rate ...................................................................................... 1 in 1010 or better
Visual Indicators ..............................................POWER A, POWER B, ALM, Vcc, SYNC,
.....................................................................AMI, B8ZS, HDB3, 133, 266, 399, 533, 655,
.....................................................LAIS, LLOS, LOC, RLOS, RMT, BPV (3 LEDs), CSU.
Dry Contact Alarm.................................................................... 50VDC, 500ma (10watts)
Power Source
Standard................................................................. 12V DC(9-14VDC) @250ma (typical)
Optional ......................................................115V or 230V AC with external power cube
Optional ..........................................24VDC (18-36VDC), 48VDC (36-75VDC), or 125VDC
Temperature
Operating ................................................................................................... -10oC to 50oC
Hi-Temp...................................................................................................... -20oC to 70oC
Storage....................................................................................................... -40oC to 90oC
Humidity........................................................................................ 95% non-condensing
Physical
*ST is a trademark of AT&T
**Contact factory for requirements higher than 20dB.
Rack Mountable Card
Height ........................... (17.7 cm) 7.0"
Width ............................ (3.2 cm) 1.25"
Depth .......................... (14.8 cm) 5.75"
Weight ..................... (192 gm) 5.44 oz
Stand Alone Unit
Height ........................... (18.2 cm) 7.2"
Width ..............................(3.5 cm) 1.4"
Depth .......................... (16.6 cm) 6.60"
Weight ..................... (512 gm) 14.5 oz

- 18 -
TC1630R/S User's Manual
Rev. 2.5
Appendix A
TheE1interfaceimpedanceontheTC1630R/S is user configurable by changing thejumpersontheinterface
module. Please follow the instructions below to set the E1 impedance appropriately.
Setting the E1 Interface Impedance
1. Unscrew the 2 front panel screws and slide the unit out of it's housing.
2. Locate the interface module at board location JP2 (the board plugs vertically into the main board's socket).
3. For 75 ohm impedance, the jumpers on the interface module should be set as follows:
JP2------- removed
JP1,3,4,5,6------- installed
Figure 7. TC1630R/S's E1 (75 ohm) Interface Module Configuration
4. For 120 ohm impedance, the jumpers on the interface module should be set as follows:
JP1------- installed
JP2,3,4,5,6------- removed
5. Slide the unit back into the housing and secure the 2 front panel screws.
Figure 8. TC1630R/S's E1 (120 ohm) Interface Module Configuration

- 19 -
TC1630R/S User's Manual
Rev. 2.5
Appendix B
Electrical Signal Cable Connection
The user's device may have a DB15 or RJ45 connector. The following connection diagrams illustrate the
signal flow direction and pin assignments typically used with these connectors.
Note: The polarity of the T1/E1 signal is bipolar, independent of the polarity. Polarity is shown for reference
only.
Figure 9. DB15 Connection Diagram
Figure 10. RJ45 Connection Diagram
Note:Pins7, 8,12,14 and15are notusedon theDB15connector. Pins 5,6,10 and13are reservedforTelco use.
Note:Pins3and6arenotusedontheRJ45connector. Pins7and8areusedforoptionalshieldconnections.
(TransmittoNetwork)
User's Device
12345678
9101112131415
DB15 Connector
(TransmittoNetwork)
(Receive from Network)
(Receive from Network)
TC1630
Terminal Block
Connectors
IN
OUT
(TransmittoNetwork)
TC1630
Terminal Block
Connectors
User's Device
1
2
3
4
5
6
7
8
RJ45 Connector
(TransmittoNetwork)
(Receive from Network)
(Receive from Network)
IN
OUT

- 20 -
TC1630R/S User's Manual
Rev. 2.5
Appendix C
19" Rack with Dual Power Cards
The picture shows the 19" rack with dual power supply cards. It consists of two subassemblies; TCRM192-
D-48 which is the 19" rack with dual 48VDC to 12VDC power cards and the TCRM192-BKPL, which is
the power back plane. The power card can be ordered for universal AC input or 24VDC input. The output
of each kind of power card is 12VDC, different input voltage has different output power rating. They are
listed as following:
TCRM192-D-48: 19" rack with dual power cards, each has 48VDC(36-75VDC) input, 12VDC output and
150 Watts.
TCRM192-D-24: Same as above but with 24VDC(18-36VDC) input, 12VDC output and 100 Watts output
power.
TCRM192-D-01: 19" rack with dual power cards, each has universal AC input (90VAC to 240VAC, 50Hz
to 60Hz) with 12VDC output. Maximum output power is 65 Watts. The diagram on the next page shows
the equivalent circuits.
Theadd-onsubassembly to the 19"rackisTCRM-bkpl, which is apowerstripPCB connected to bothpower
cards via two pair cable assembly. This power back plane has built-in fuses and power indicators to ease
installation and trouble-shooting.
Fuse A,B
for primary
power card
48(24)VDC input
for primary
power card
48(24)VDC input
for secondary
power card
AC power input
for secondary
power card
AC power input
for primary
power card
Fuse A,B
for secondary
power card
Power indicators
for power A,B
Primary power card
Secondary power card
Power indicators
for power A,B
This manual suits for next models
1
Table of contents
Other TC Communications Modem manuals
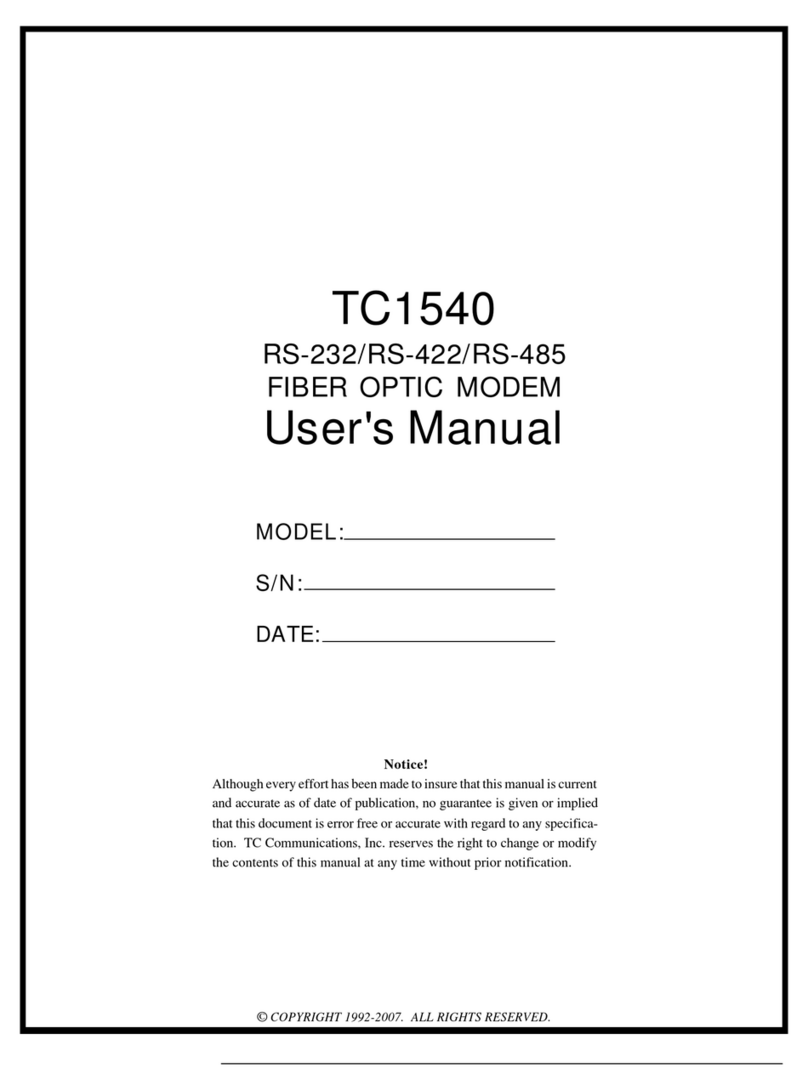
TC Communications
TC Communications TC1540 User manual

TC Communications
TC Communications TC2100 User manual
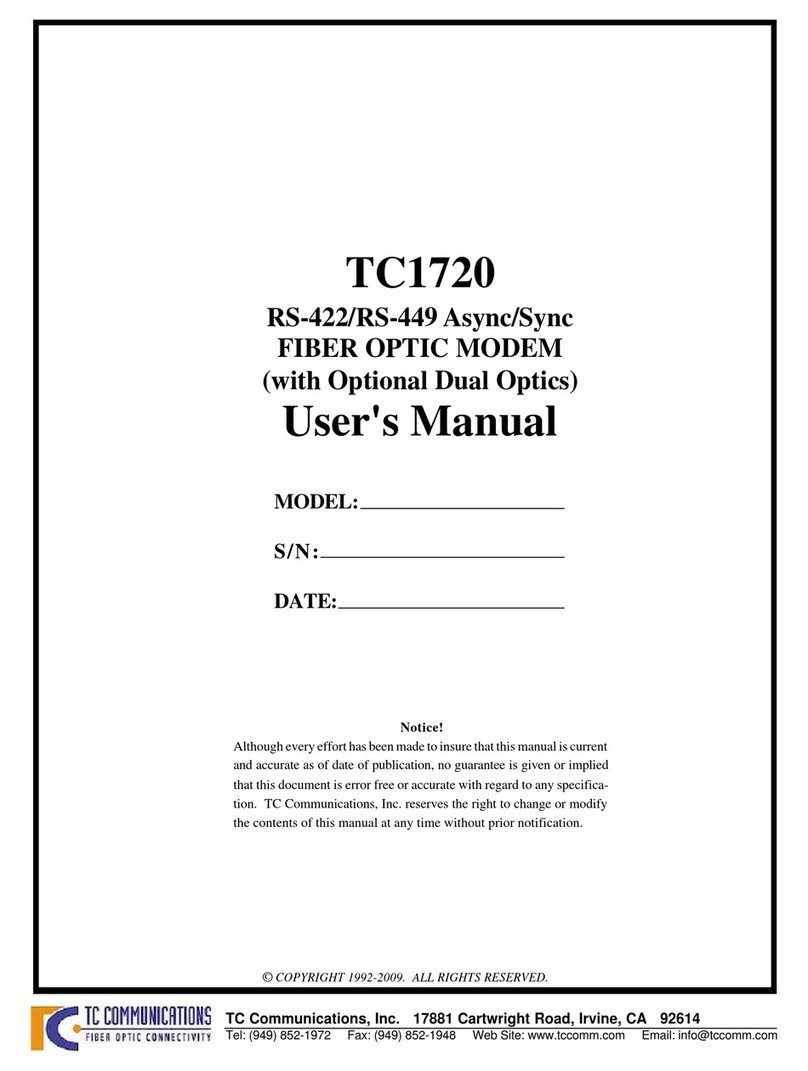
TC Communications
TC Communications TC1720 User manual
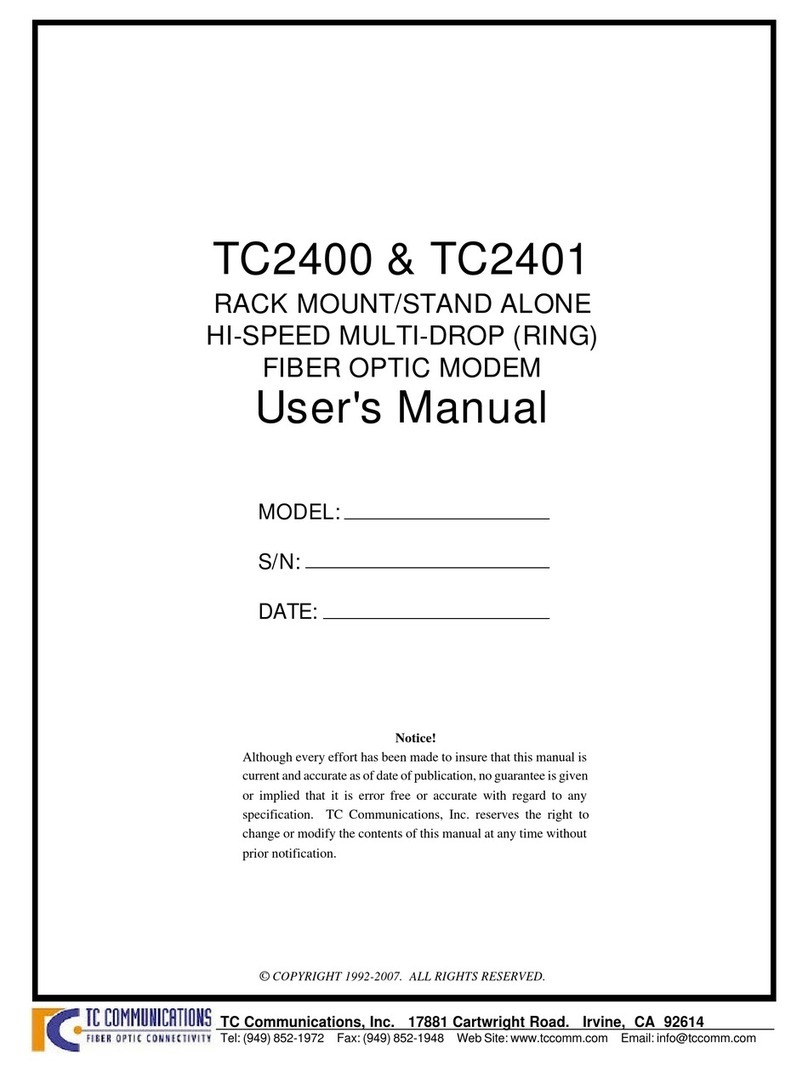
TC Communications
TC Communications TC2400 User manual
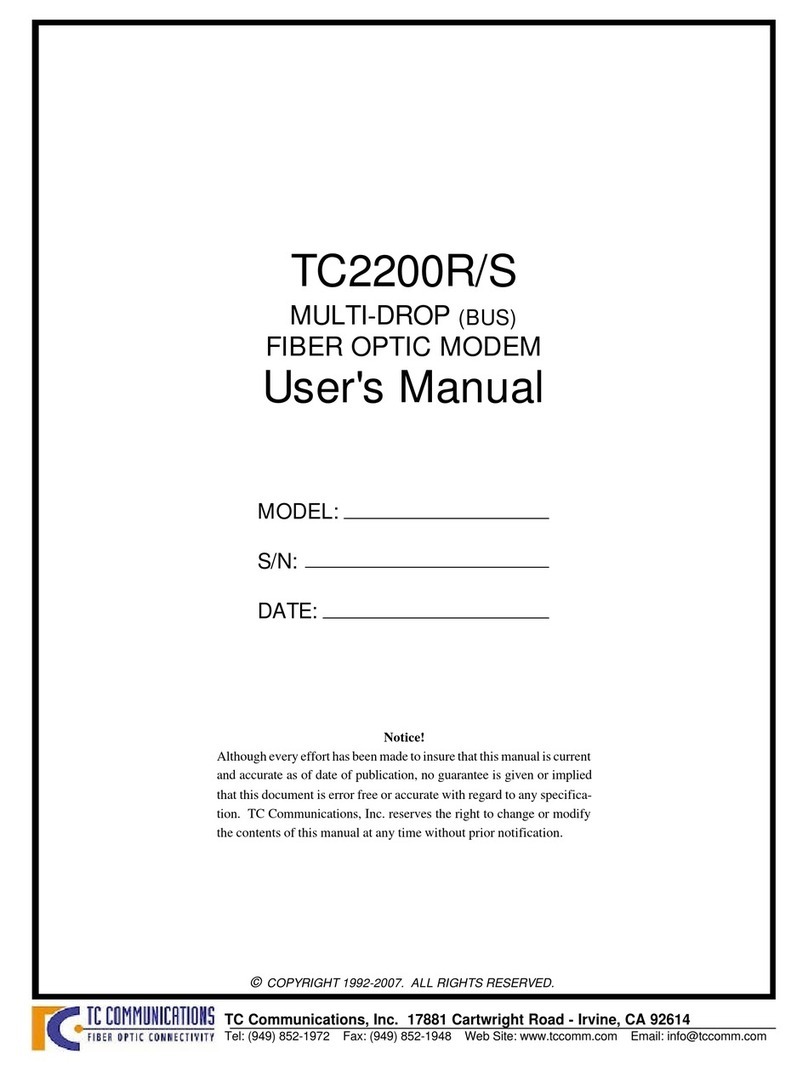
TC Communications
TC Communications TC2200R User manual

TC Communications
TC Communications TC1710 User manual
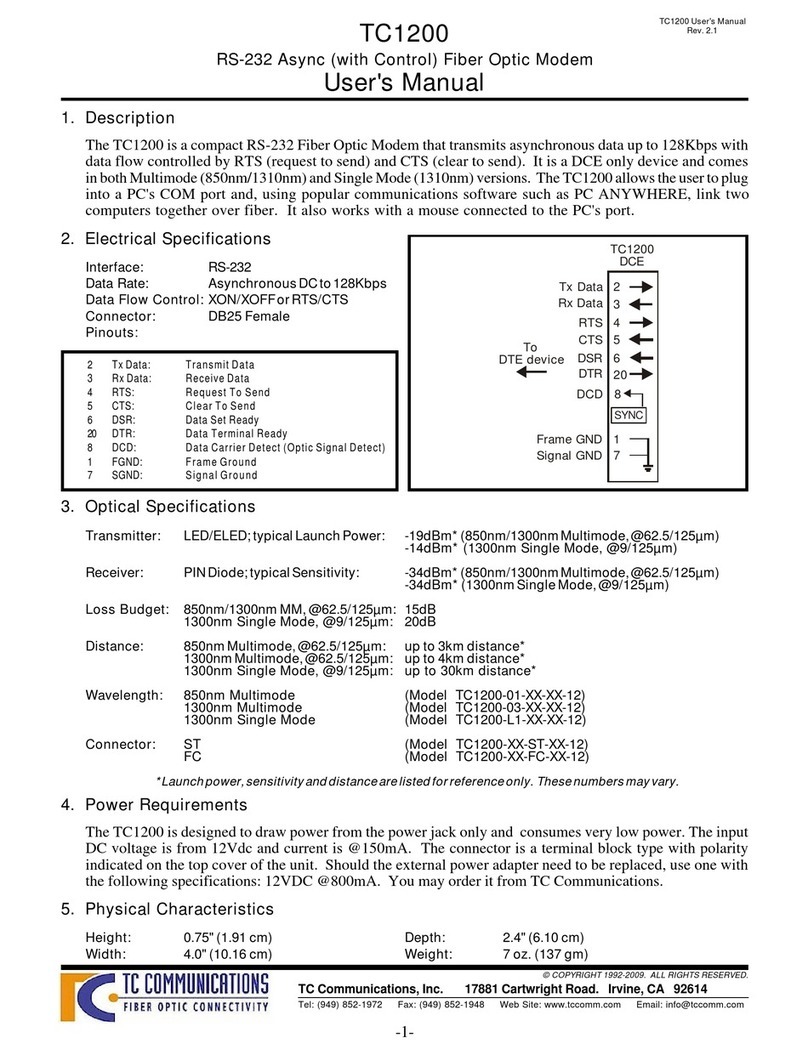
TC Communications
TC Communications TC1200 User manual
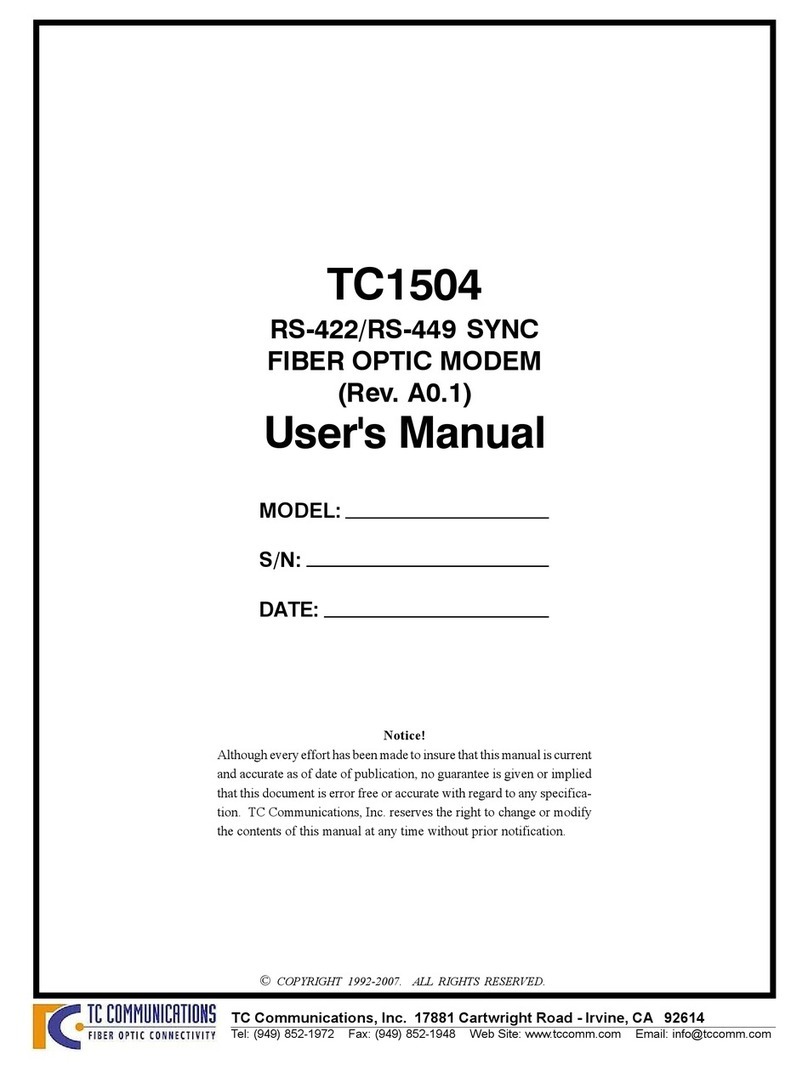
TC Communications
TC Communications TC1504 User manual
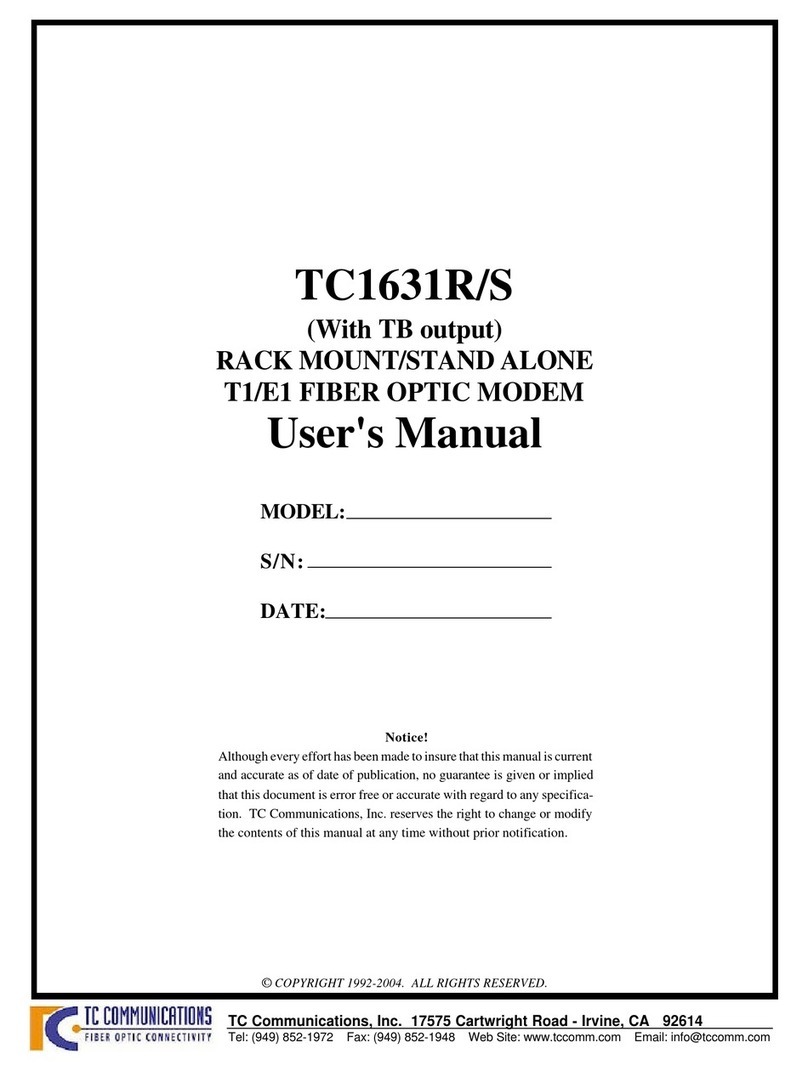
TC Communications
TC Communications TC1631R User manual