Tech West ACL2S2 Manual

2625 N. Argyle Ave. • Fresno, CA 93727
(559) 291-1650 • (800) 428-7139 • FAX (559) 348-9677
T
ECH
W
EST
I
NC.
Manufacturers of Dental Vacuum
and Air Systems
ULTRA CLEAN
LUBRICATED COMPRESSOR
INSTALLATION
AND SERVICE
MANUAL
Revised 4-15


1
ULTRA CLEAN
LUBRICATED COMPRESSOR
INSTALLATION AND SERVICE MANUAL
This manual is for the installation and service of Tech West’s Ultra Clean Lubricated Compressors.
CONTENTS
Installation
Location Requirements 3
Figure 1: Wire and Breaker Size 3
Installation Steps 4
Figure 2: Compressor Connections 5
Start Up 6
Maintenance 6
Figure 3: Checking and Changing the Oil 7
Figure 4: Replacing Oil Indicator Lens 7
Parts Breakdown 8-11
Dessicant Dryer Parts Breakdown 12
Coalescing Filter Parts Breakdown 13
Single Ultra Clean Lubricated Compressor Assembly 14
Dual Ultra Clean Lubricated Compressor Assembly 15
Triple Ultra Clean Lubricated Compressor Assembly 16
Compressor Wiring Diagram 17
TROUBLE SHOOTING
Single Compressor Trouble Shooting 18-19
Dual Compressor Trouble Shooting 20-21
Triple Compressor Trouble Shooting 22-23
Air Line Sizing Chart 24
Maintenance & Service / Notes Sheet 24-25

Maintenance & Service / Notes
2

ULTRA CLEAN LUBRICATED COMPRESSOR
INSTALLATION
1. ULTRA CLEAN LUBRICATED COMPRESSOR LOCATION REQUIREMENTS
The Ultra Clean Lubricated Compressor location should be level, accessible and well ventilated.
If the Ultra Clean Lubricated Compressor will be located in a confined space, provide adequate ventilation.
Electrical
(1) Line voltage must be within the limits of Figure 1 below. (Install a “buck-boost
transformer” if line voltage is not between these values.) Circuit breaker switches
must be 20 - 30 amp depending on model and voltage necessary.
(2) Local code may require you to provide one quick disconnect (safety switch) for the
compressor.
(3) See Figure 1 below for breaker size and line voltage.
CAUTION - Voltage must be 110/128 v or motor damage may occur.
CAUTION - Voltage must be 208/240 v or motor damage may occur.
3
Figure 1: Recommended Wire and Breaker Size
Single Head Compressors
Model Voltage Amperage Wire Size Recommended
(Gauge) Breaker Size
ACL2S2 230 7.2 12 20
ACL2S1 115 13.6 12 20
ACL4D2 230 14.4 12 20
ACL6T2 230 21.6 10 30
Dual Head Compressors
Triple Head Compressors

ULTRA CLEAN LUBRICATED COMPRESSOR
INSTALLATION
2
2. INSTALLATION STEPS
This dental Compressor should only be installed by qualified personnel. Should any questions arise
during the installation, call Tech West Technical Support between the hours of 7:00 a.m. to 4:00 p.m.
(Pacific Standard Time).
Place the compressor in a clean, dry, well ventilated area, on a solid, level surface. Consider sound
level and insulate as needed. Be sure that adequate ventilation is available as the compressor is air
cooled. Ambient temperature in the equipment room should be within the temperature range of 40
degrees Fahrenheit minimum to 100 degrees Fahrenheit maximum.
(a) Check the shipping carton for damage. This could detect damage to the unit which might
otherwise be overlooked. Remove cardboard shipping carton.
(b) Remove the Lubricated Compressor from its shipping skid. Inspect the unit for damage.
Lubricated Compressors are shipped bolted to a pallet. This pallet is intended for shipping
only and should be discarded.
(c) Remove installation kit attached to pallet. It should contain the following:
(4) Isolation Feet
(1) Alternate Air Hookup Hose
(1) Bottle of Tech West Compressor Oil per Motor
(1) 5’ Flexible Air Hose
(d) Install isolation feet on tank legs.
(e) Remove shipping tape from spring-hinged oil filler cap(s).
(f) Install flexible hose to outlet on the compressor shut-off valve.
(g) Move compressor into place and level the motor platform.
(h) Install flexible hose to office air supply line.
(i) Install flexible hose to alternate fresh air supply.
(j) Wiring instructions:
1 Have all electrical connections made by qualified personnel only. All connections
should be in accordance with local codes.
2 Use the chart on page 1 to help determine the proper line and breaker size for
the unit that is being installed.
4

5
ULTRA CLEAN LUBRICATED COMPRESSOR
INSTALLATION
2
3. CONNECTIONS
Electrical Connection
to disconnect and
electrical panel
220 v
(110 v / 220 v ) on the
single models only.
Air Out
Connection to building
supply line.
Alternate Air
Connection
to fresh air supply.
Figure 2
Dryer Purge
Connection

5. PERIODIC SERVICING
WEEKLY SERVICING
(a) Check the oil level. Refer to figure 2. Use only Tech West oil specially formulated for Tech
West Compressors.
DO NOT OVERFILL. Add oil only when the oil level remains below the center line of the oil-level
sight glass after the compressor has been idle for at least 5 minutes.
(b) Empty condensate drain bucket under the dryer.
MONTHLY SERVICING
(a) Crack the drain petcock on the bottom of the storage tank to check for water and drain if needed.
(b) Check pump-up times.
(c) Check the moisture indicator to see that it is still “blue”. If it is pink it is time to service the air dryer.
YEARLY SERVICING
(a) Repeat all of the monthly servicing.
(b) Change oil (part # CO-100).
(c) Replace the dessicant air dryer (part # RDC-100).
(d) Replace the ultra clean coalescing filter. (part # CFEO-375). This keeps drying system efficient.
(e) Replace alternate air filter (part # TIF-100). Reduces oil consumption and lengthens
compressor life and efficiency.
(f) Replace the moisture indicator on the compressor (part # MI-100).
6
ULTRA CLEAN LUBRICATED COMPRESSOR
INSTALLATION
4. START-UP STEPS
(a) Make sure the shut-off valve from the compressor tank is closed.
(b) Turn the breaker from the panel to the “ON” position.
(c) Turn power “ON” from the toggle switch on the compressor. Compressor should run quietly
and vibration free. The storage tank should start to build pressure.
(d) The compressor will run until the pressure gauge reads 100 psi. The compressor then will
automatically shut off and the dryer will purge with a quick blast of air.
(e) Using soapy water, check the compressor plumbing hook ups for leaks. Repair leaks if needed.
(f) Pressure test the entire plumbing system for leaks. Use the storage tank pressure gauge to
monitor a pressure drop. After the plumbing system has been pressurized for 30 minutes,
re-check the gauge for pressure drop. If there is a drop in pressure, find and repair all leaks
in the office plumbing.
AIR LEAKS ARE THE MAIN CAUSE OF COMPRESSOR FAILURES.
(g) Complete and mail in the warranty card for the compressor within ten days of installation.

7
Figure 3: Checking and Changing the Oil
D
O
N
O
T
O
V
E
R
F
I
L
L
K
E
E
P
F
U
L
L
Oil Filler Spout
Indicator Lens
Oil Drain Plug
Keep full to here.
Alternate
Drain Spout
Instructions
Add oil to compressor through
oil filler spout. Do not overfill.
Keep filled to level as shown
below. Oil should be changed
annually or when oil becomes
discolored.
Check oil level with compressor
off and compressor sitting level.
Figure 4: Replace Oil Indicator Lens
Important!
Drain oil from compressor head
before removing lens.
Indicator Lens
Retaining Ring Gasket
Note:
Replace only if damaged
or discolored.
part #OSG-100

8
6
5
3
KEY PART NO. DESCRIPTION UNIT
1 CCH-115 115 V COPELAND COMPRESSOR HEAD 1HP 1
2 CCH-230 230 V COPELAND COMPRESSOR HEAD 1 HP 1
3 CF-115 115 V COOLING FAN 1
4 CF-230 230 V COOLING FAN 1
5 CFS-100 COMPRESSOR FAN SHROUD 1
6 CFG-100 FINGER GUARD 1
7 OSG-100 OIL SIGHT GLASS 1
HEAD COVER AND FAN ASSEMBLY
4
12
7

9
Figure 4: AIR COMPRESSOR STARTER ASSEMBLY
KEY PART NO. DESCRIPTION UNIT
1 CRA-115 115 V CAP AND RELAY ASSEMBLY, COMPLETE 1
2 CRA-208 208-230 V CAP AND RELAY ASSEMBLY, COMPLETE 1
3 CRA-230 230 V ONLY CAP AND RELAY ASSEMBLY, COMPLETE 1
4 PR-115 115 V POTENTIAL RELAY 1
5 PR-208 208-230 V ONLY POTENTIAL RELAY 1
6 RCC-115 115 V RUN CAPACITOR 1
7 RCC-208 208-230 V RUN CAPACITOR 1
8 RCC-230 230 V ONLY RUN CAPACITOR 1
9 SCC-115 115 V START CAPACITOR 1
10 SCC-230 208-230 V / 230 V ONLY START CAPACITOR 1
ULTRA CLEAN AIR COMPRESSOR STARTER ASSEMBLY
123
678
910
45

0
10
20
30 40 50 60
7
8
90
100
psi
100
90
80
70
60
50
0
0
20
10
0
10
2
4
4
3
3
2
5
5
8
6
7
7
1
1
KEY PART NO. DESCRIPTION UNIT
1 CPG-250 COMPRESSOR GAUGE 1
2 BV-250 1/4” BALL VALVE 1
3 MI-100 MOISTURE INDICATOR 1
4 FA-4-4 1/4” FLARE HOSE FITTING 1
5 BN-250-CL 1/4” BRASS CLOSE NIPPLE 1
6 BT-250 1/4” BRASS TEE 1
7 BSE-250 1/4” BRASS ELBOW 1
8 BPC-4 1/4” BRASS CROSS 1
GAUGE AND CUT-OFF ASSEMBLY
SINGLE COMPRESSOR CONFIGURATION
DUAL AND TRIPLE
COMPRESSOR CONFIGURATION

11
REAR VIEW ASSEMBLY AND PARTS LIST
KEY PART NO. DESCRIPTION UNIT
1 CV-375MF-100 3/8 CHECK VALVE MALE TO FEMALE CONNECTION 1
2 CPT-100 COMPRESSOR PURGE TANK 1
3 CV-375D-100 3/8 CHECK VALVE 1-3
4 HA-12-250 1/4 HOSE ASSEMBLY - 12” LONG 1
5 DPC-1 DRYER PRE COOLER SINGLE COMPRESSOR 1
6 DPC-2 DRYER PRE COOLER DUAL & TRIPLE COMPRESSOR 1
7 RFV-100 RUBBER MOUNTING FEET 4
4
3
2
1
7
5
6
3

12
KEY PART NO. DESCRIPTION UNIT
1 DSV-115 115V PURGE SOLENOID VALVE 1
2 DSV-230 230V PURGE SOLENOID VALVE 1
3 AS-500 1/2 FILTER ASSY 1
4 RDC-100 REPLACEMENT DESSICANT TANK 1
5 MV-250 METERING VALVE 1
6 SN-250-CL STAINLESS STEEL NIPPLE 1/4 3
7 FE-4-6 FLAIR FITTING 1/4 X 3/8 1
8 BV-250 BALL VALVE 1/4 1
9 BT-250 BRASS TEE 1/4 2
10 PFH-375 CLEAR DRAIN HOSE PER FOOT
11 MSD-100 MOLECULAR-SIEVE 1 LB 2LBS
12 MSD-200 ACTIVATED ALUMINA 1 LB 2LBS
13 CV-250D 1/4 CHECK VALVE 1
NEW DESICCANT AIR DRYER ASSEMBLY
4
3
5
6
9
7
8
9
1
2
13
12
11
INSIDE
TANK
ELEMENT
10

13
FILTER ASSEMBLY
1
2
3
KEY PART NO. DESCRIPTION UNIT
1 CFAO-375 COALESCING FILTER ASSEMBLY 3/8 1
2 CFEO-375 COALESCING FILTER ELEMENT 3/8 1
3 CFBP-375 COALESCING FILTER BOWL 1

14
14
17
6
16
15
18
2
7
5
13
11
9
4
10
1
3
12
KEY PART NO. DESCRIPTION UNIT
1 SBHA-21-375 STEEL BRAID HOSE ASSEMBLY 1
2 SBHA-7.5-375E STEEL BRAID HOSE ASSEMBLY 1
3 SBHA-21-375E STEEL BRAID HOSE ASSEMBLY 1
4 FPH-375 PURGE FLEX HOSE CLEAR PER FT
5 ZZACS61 1/4 HOSE ASSEMBLY 1
6 PFT-500 POLY FLO TUBE 1/2 PER FT
7 CFAO-375 COALESCING FILTER 3/8 1
9 DPB-100 DRYER PURGE BUCKET 1
10 CPT-100 COMPRESSOR PURGE TANK 1
11 RDC-100 REPLACEMENT DESICCANT CARTRIDGE 1
12 DSV-115 1/4 CHECK VALVE 1
13 DSV-230 PURGE VALVE SOLENOID VALVE 230V 1
14 CCH-115 LUBRICATED COMPRESSOR HEAD 115V 1
15 CCH-230 LUBRICATED COMPRESSOR HEAD 230V 1
16 RFV-100 RUBBER MOUNTING FEET 4
17 PSC-3 PRESSURE SWITCH 1
18 POVA-100 SAFETY POP OFF VALVE 1
SINGLE ULTRA CLEAN LUBRICATED COMPRESSOR

15
KEY PART NO. DESCRIPTION UNIT
1 SBHA-21-375 STEEL BRAID HOSE ASSEMBLY 1
2 SBHA-10-375E STEEL BRAID HOSE ASSEMBLY 1
3 SBHA-9-375E STEEL BRAID HOSE ASSEMBLY 1
4 FPH-375 PURGE FLEX HOSE CLEAR PER FT
5 ZZACS61 1/4 HOSE ASSEMBLY 1
6 PFT-500 POLY FLO TUBE 1/2 PER FT
7 CFAO-375 COALESCING FILTER 3/8 1
9 DPB-100 DRYER PURGE BUCKET 1
10 CPT-100 COMPRESSOR PURGE TANK 1
11 RDC-100 REPLACEMENT DESICCANT CARTRIDGE 1
12 CV-375D-100 3/8 CHECK VALVE 2
13 DSV-230 PURGE VALVE SOLENOID VALVE 230V 1
14 SBHA-18-375 STEEL BRAID HOSE ASSEMBLY 2
15 CCH-230 LUBRICATED COMPRESSOR HEAD 230V 2
16 RFV-100 RUBBER MOUNTING FEET 4
17 PSC-3 PRESSURE SWITCH 1
18 POVA-100 SAFETY POP OFF VALVE 1
DUAL ULTRA CLEAN LUBRICATED COMPRESSOR
14
17
6
16
15
18
2
7
5
13
11
9
4
10
1
3
12

16
KEY PART NO. DESCRIPTION UNIT
1 SBHA-21-375 STEEL BRAID HOSE ASSEMBLY 1
2 SBHA-10-375E STEEL BRAID HOSE ASSEMBLY 1
3 SBHA-9-375E STEEL BRAID HOSE ASSEMBLY 1
4 FPH-375 PURGE FLEX HOSE CLEAR PER FT
5 ZZACS61 POLY FLO TUBE 1/4 1
6 PFT-500 POLY FLO TUBE 1/2 PER FT
7 CFAO-375 COALESCING FILTER 3/8 1
9 DPB-100 DRYER PURGE BUCKET 1
10 CPT-100 COMPRESSOR PURGE TANK 1
11 RDC-100 REPLACEMENT DESICCANT CARTRIDGE 1
12 CV-375D-100 3/8 CHECK VALVE 3
13 DSV-230 PURGE VALVE SOLENOID VALVE 230V 1
14 SBHA-18-375 STEEL BRAID HOSE ASSEMBLY 3
15 CCH-230 LUBRICATED COMPRESSOR HEAD 230V 3
16 RFV-100 RUBBER MOUNTING FEET 4
17 PSC-3 PRESSURE SWITCH 1
18 POVA-100 SAFETY POP OFF VALVE 1
TRIPLE ULTRA CLEAN LUBRICATED COMPRESSOR
14
17
6
16
15
18
2
7
5
13
11
9
4
10
1
312

17
Figure 5: Compressor Wiring Diagram

18
NO
GO ON TO
THE NEXT
PAGE.
Are there leaks in
compressor or in
office piping system?
Does purge
valve seal while
running?
Clean
or
replace.
YES
NO
Is intake filter
clogged?
Trouble Shooting Chart
Single Ultra Clean Lubricated Compressor
Single Ultra Clean Lubricated Compressor Diagram
NO
YES
Is there sufficient
pressure build-up
with head
discharge line
removed?
NO
Defective
head,
contact
Tech West.
NOTE: Close
shut off valve.
Pump up tank to
100 psi. If pres-
sure is main-
tained for 15-20
min., leak is in
office lines.
YES
Locate
and repair.
NO
Does air leak
from unloader
valve until unit
cycles again?
Examine the check
valve and the
purge valve for
leaks.
YES
NO
YES
YES
Replace
intake
filter.
Contact
Tech West.
YES
Does
unloader
valve system
function
properly?
YES
Does com-
pressor run
too hot or too
frequent?
1. Locate and repair
leaks.
2. Ventilate if room is
above
100 deg. F.
3. Contact compressor
may be undersized.
YES
Is head
level?
YES
NO
Level
head.
YES
Does com-
pressor run
too hot or too
frequent?
YES
NO
Contact
Tech West.
Contact
Tech West.
1. Ensure that
unloader valve
& pressure
switch close on
pump-up, &
open on purge
cycle.
2. Ensure that
drain line is not
clogged.
NO
DOES AIR
COMPRESSOR
RUN?
Does compressor run
for a few
seconds, “chugs”, then
stops?
Does compressor pres-
surize from 80 to 100
psi in less than 1
minute with no air
being used?
YES NO
Does compressor
cycle with no air
being used?
YES NO
Is the moisture
indicator pink?
Is there excessive
oil usage?
NO
YES
Check voltage
supplied to the
compressor.
This manual suits for next models
3
Table of contents
Other Tech West Air Compressor manuals
Popular Air Compressor manuals by other brands
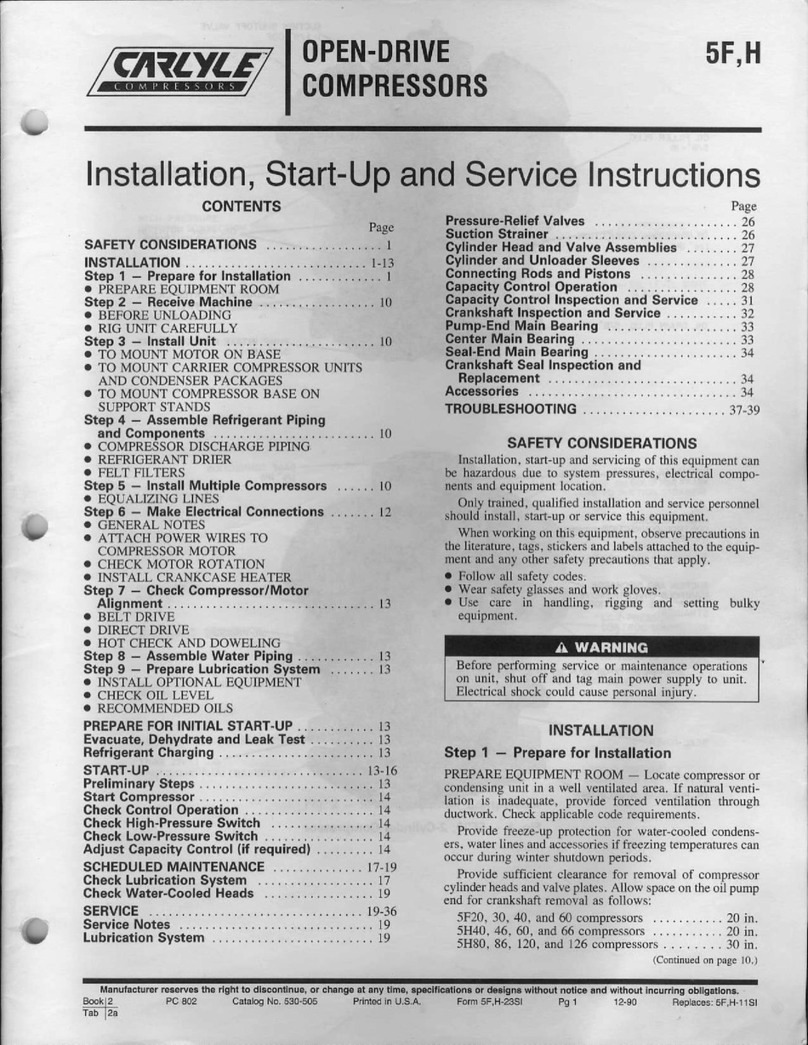
Carlyle
Carlyle 5F Series Installation and service manual
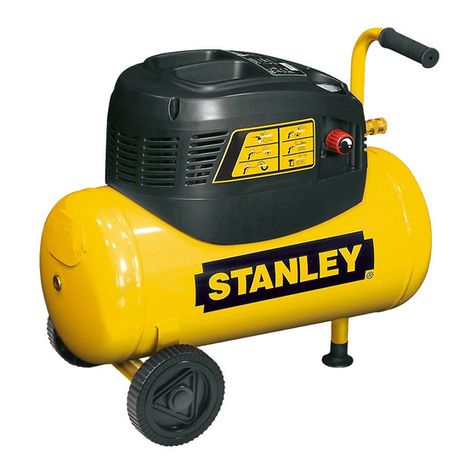
Stanley
Stanley 8216035SCR011 instruction manual
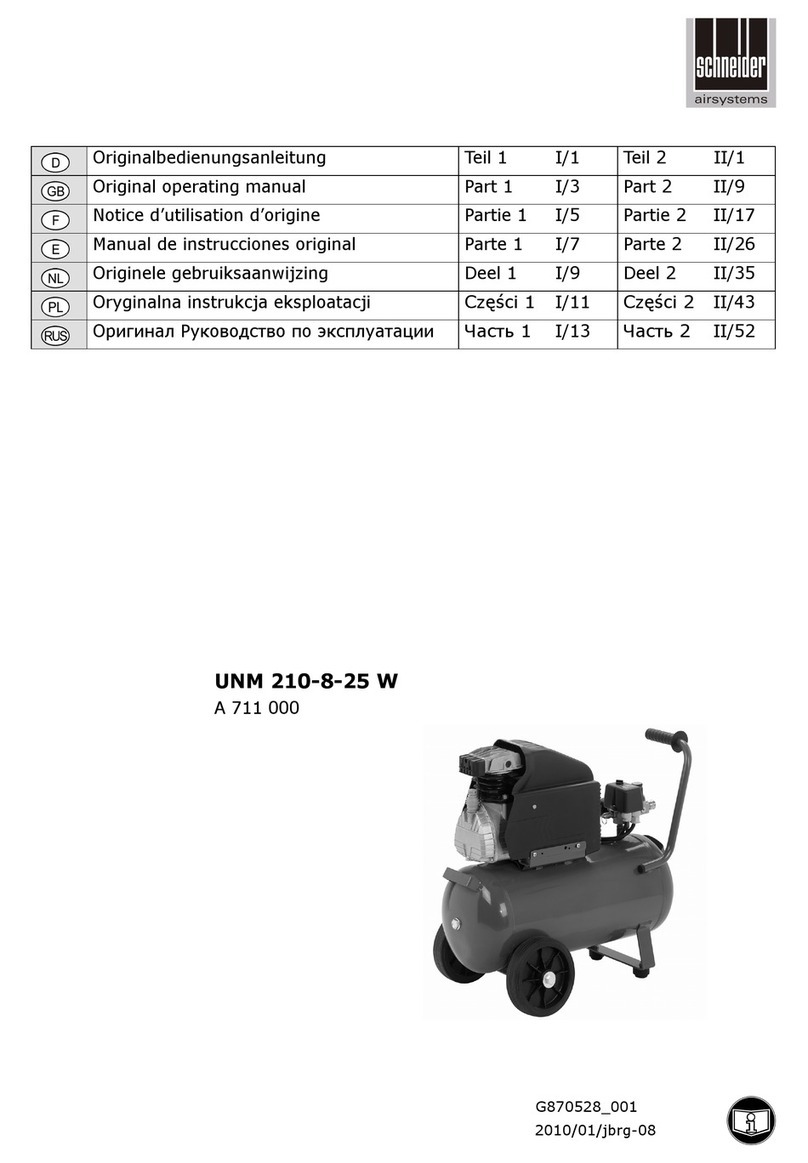
Schneider Airsystems
Schneider Airsystems UNM 210-8-25 W operating manual

Vmac
Vmac V400015 installation manual
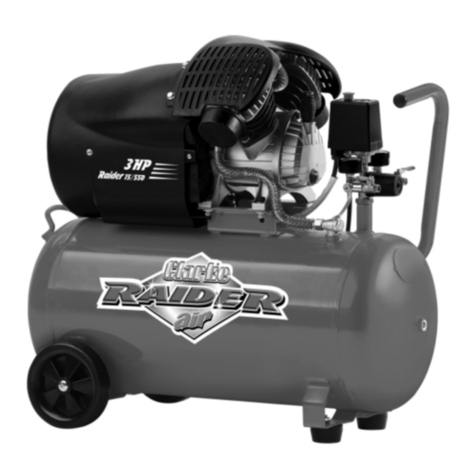
Clarke
Clarke RAIDER 15/550 Operation & maintenance instructions

Stealth
Stealth SAQ-1815 Operator's manual

Ingersoll-Rand
Ingersoll-Rand EP 20 SE Operators/Instruction Manual Options
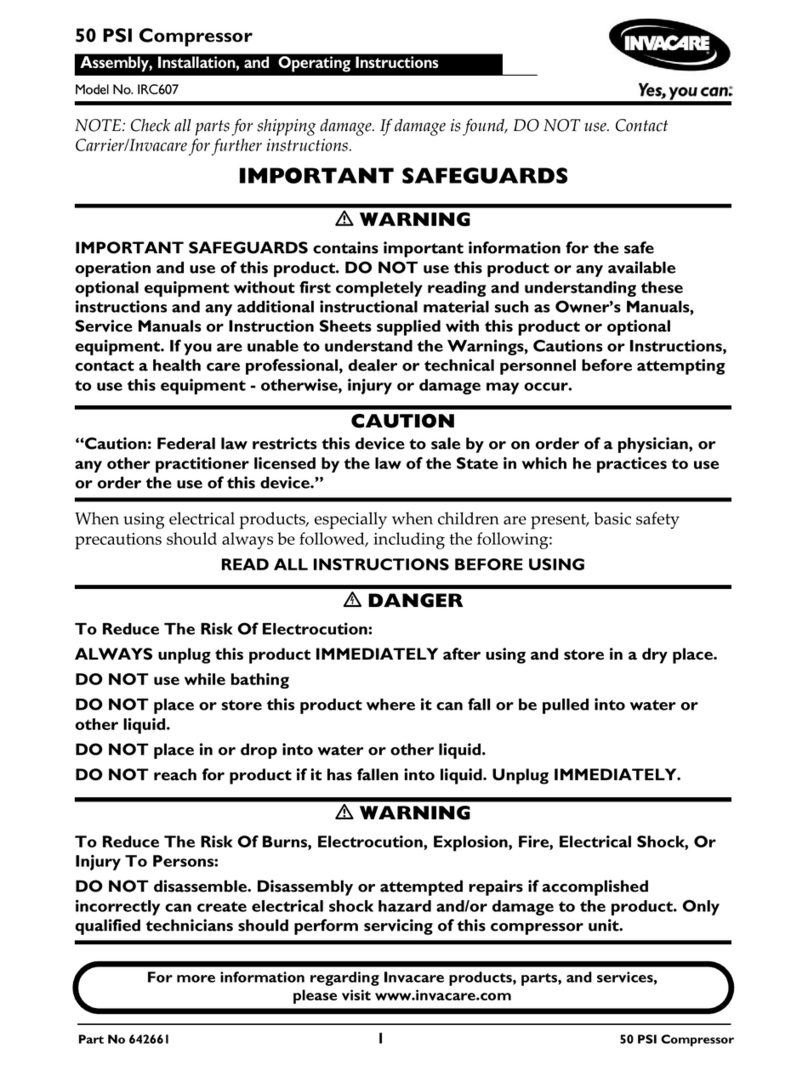
Invacare
Invacare 50 psi Compressor IRC607 Assembly, installation and operating instructions
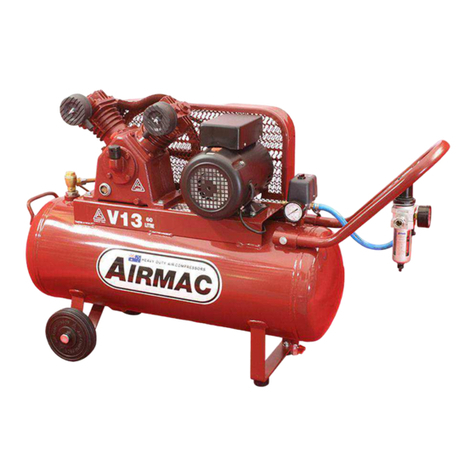
AIRMAC
AIRMAC T20D instruction manual
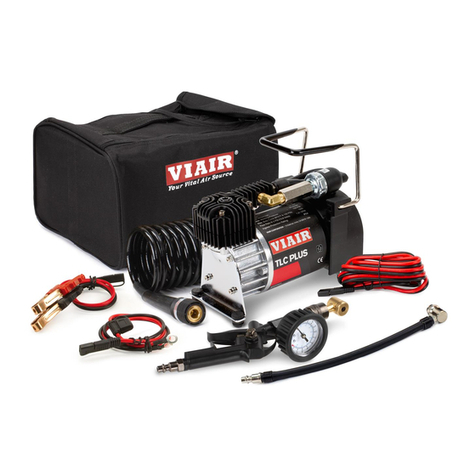
VIAIR
VIAIR 00190 user manual
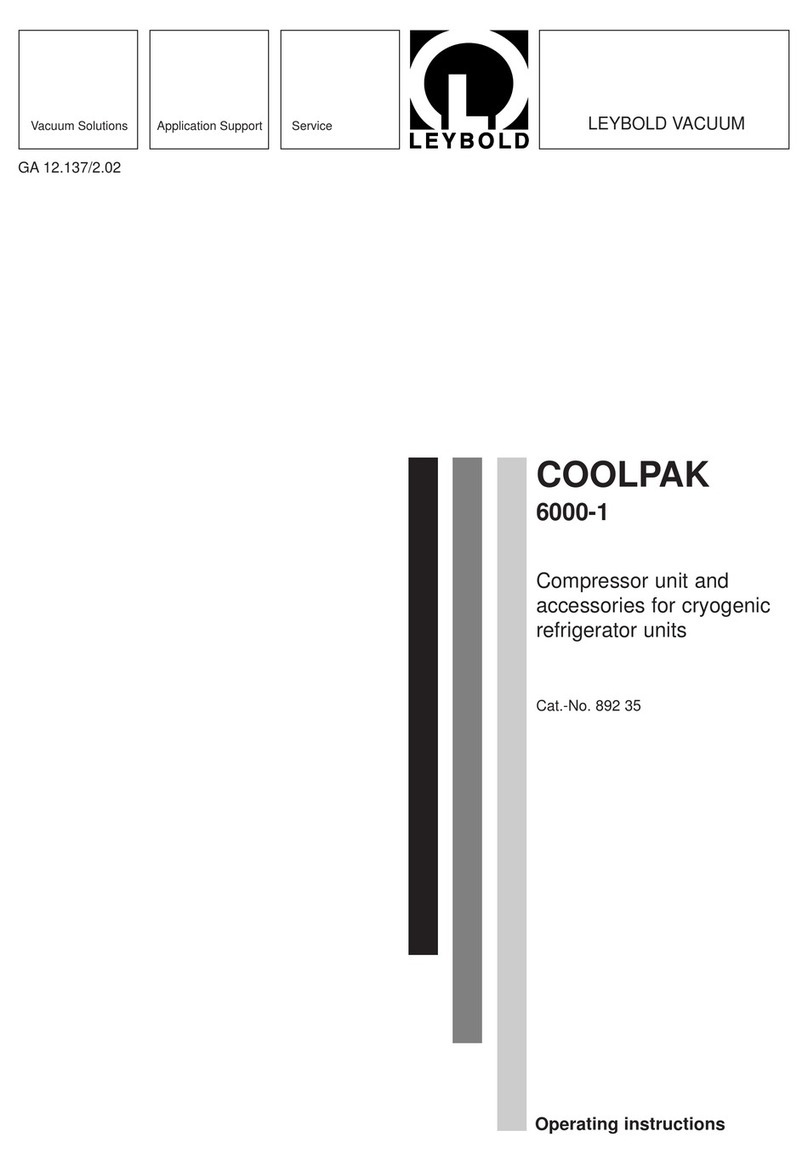
LEYBOLD
LEYBOLD COOLPAK 6000-1 operating instructions
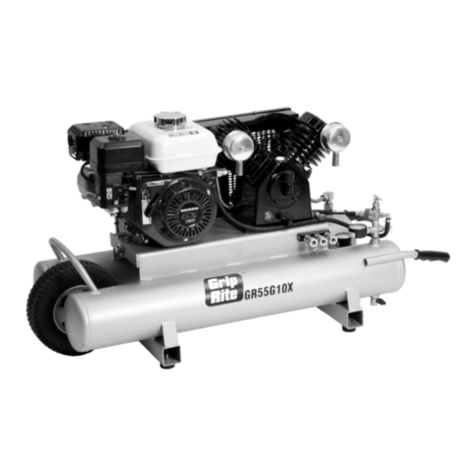
Grip Rite
Grip Rite GR55G10X Operating manual and parts list