TECHNO-AC SUCCESS TPT-522N Manual


2
Table Page of Contents
Introduction ..........................................................................................................3
1. Components and Operating Principle......................................................................4
2. Receiver AP-027 Appearance and Controls ...........................................................5
2.1 Preparing Receiver AP-027 for operation.......................................................5
3. Acoustic sensor AD-247......................... ........................................................7
4. Operation sequence in liquids leak detection mode .........................................9
4.1 Connection of sensors and check the receiver operability ................................9
4.2 Acoustic sensor AD-227 set contents ...........................................................9
4.3 Conduct fine tuning of receiver filter.............................................................11
5. Operation sequence in liquids leak detection mode ...........................................13
6. Transmitter AG-144.1 ........................................................................................16
6.1 Appearance. Controls ................................................................................16
6.2 Transmitter Operating Procedure ...............................................................17
6.3 Transmitter Connection .............................................................................18
6.4 Powering on the transmitter ........................................................................19
6.5 Transmitter parameter setting ....................................................................20
6.6 Changing the Set Transmitter Parameters ...................................................21
6.7 Operation with the Inductive Antenna .........................................................21
6.8 Operation with the Inductive Clamp ............................................................21
6.9 Operation in Conditions of Atmospheric Precipitations .................................21
6.10 Operation from the External Source ..........................................................21
6.11 Internal accumulators charge....................................................................22
7. Active Route Detection ........................................................................................25
7.1 Incorporated equipment .............................................................................25
7.2 Operation sequence in active cable route detection mode ............................25
7.3 Operation sequence in acoustic cable route detection mode.........................28
8. In direct electromagnetic mode of measuring depth ...........................................30
9.Detecting the pipeline and utility lines intersection point.....................................30
10.Transportation and Storage.................................................................................30
Appendix A
Receiver AP-027. Technical specifications............................................................. 31
Technical Characteristics of the Transmitter .................................................... 32
Appendix B
Control and indication of the generator AG-144.1....................................................35
Appendix C
Receiver AP-027. Indication............................................................................ 37

3
Introduction
Metal and non-metal pipeline Locator with water leak detection function «Success
TPT-522N»:
- non-metal pipeline location underground
- water leak detection from metal or non-metal pipelines underground up to 6 m depth
- water leak detection inside the house
- detection of cables underground up to 6 m depth
- detection of any metal pipelines underground up to 6 m depth
- survey the ground before the ground works ( BB mode )
- distance of tracing from the place of transmitter connection is up to 3 km.
- min and max method of tracing
- indirect measurement of the depth
Kit components are:
7
21 – Receiver AP-027
2 – Transmitter AG-144.1
3 – Acoustic sensor AD-227
4 – Electromagnetic sensor EMD-247
5 – Headphones
6 – Inductive antenna IEM - 301.3
7 – Impact device UM - 112
Operation conditions
- Ambient temperature, °С ...........................................................-20 to +50
- Relative humidity, % ................................................................. up to 90
1
4
6
3
5
1 – Acoustic sensor AD-227
2 – Magnet for AD-227
3 – Contact rod for AD-227, (70 mm)
4 – Contact rod for AD-227, (150 mm)
5 – Carrying rod for AD-227
6 – Extention carrying rod for AD-227
7 – Allen key, 2 pcs
8 – Key (attached to cable)
9 – Handle
23 4 58
1
8
9
6

4
1. Components and Operating Principle
Cable route and leak detector «Success TPT-522N» is a multi-purpose, integrated,
multifunctional set. Functionally, the set joins three devices:
1. Route detector with the electromagnetic sensor;
2. Route detector with the acoustic sensor;
3. Leak detector with the acoustic sensor.
The set consists of the transmitter providing for electromagnetic field radiation and generation
of impact (audio) pulses in the utility under examination (when using the impact device), and the
receiver with electromagnetic and acoustic sensors.
Transmitter AG-144.1 is intended for electromagnetic and acoustic methods of underground
utilities detection.
The maximum transmitter power in sinusoidal mode is 180 W.
Using the transmitter enables the following:
- Route location of utilities by electromagnetic (cables, metal pipelines) and acoustic methods
(metal and NON-METAL pipelines).
- Conduct gas pipeline diagnostics and locate breaks in protective cable covering
The transmitter can be connected to the load either directly (with connecting wires) or with the
use of the inductive antenna or inductive clamp providing for noncontact (inductive) connection
of the utility under examination.
Use of the inductive antenna as a load is only possible at the 8192 Hz frequency (selected
automatically at antenna connection).
The electromagnetic sensor connected to the receiver converts the electromagnetic signal into
the electric one. The electric signal is delivered to the receiver where it is amplified and filtered.
According to the signal in headphones and LCD-indicator, the operator determines the route
location.
In the route location mode, the receiver is also able of receiving a signal from industrial frequency
radiation sources (50/60 Hz) and cathode protection systems (100/120 Hz).
The leak detector consists of the acoustic pre-amplifying converter and receiver where the
received signal is subject to amplification and filtering. Noise of a hole through the ground is
perceived by the converter, amplified in the pre-amplifier and fed to the receiver. The receiver
filters the hole noise of unwanted sounds, amplifies the signal and forwards it to headphones and
indicator. According to the maximum signal or specific hole noise, the operator determines the
leak location.

5
2. Receiver AP-027
Appearance and Controls
Fig. 2.1
932
1
6
5
7
84
10 11
12
13
14
15
1 power on/off button 9▲/▼ selected parameter adjustment
buttons (up/down)
2visual indication type button 10 frequency button (filter frequency
adjustment on/off)
3sound indication type button 11 LCD screen
4◄/► parameter selection buttons (left/
right) 12 headphones jack
5filter button (broadband on/off) 13 sensors connector
6memory button 14 protective insert
7start/pause button
(measurement mode) 15 external power supply socket
8 / sensitivity buttons (higher/lower)
Technical specifications of the Receiver are listed in Appendix A.
Screen controls are listed in Appendix B.
*Set of external PowerBank (for
example, Xiaomi Mi Power Bank
20000 mAh with protective case and
power adaptor питания SAMSUNG
ART-U90EWE 5.0 V/2.0 A)
2.1 Preparing Receiver AP-027 for operation
1. Insert 4 AA elements in battery compartment of the receiver, observing the polarity. Pic
2.1 p.14 If accumulators are used, they should be fully charged with charger, supplied
separately.
Receiver cab also work from external PowerBank, supplied separately*.
NOTE
AP-027 automatically switches to external power supply, when connected to PowerBank.
Some models of PowerBanks should be activated by pressing separate button on their body.
When working at negative temperatures (to -20°С) place PowerBank under clothes.

6
2. Set the receiver on the holder
3. Put one end of the holder below protective rubber of the receiver.
4. Put other end of the holder below the second rubber
5. The receiver is ready for the operation.
It is recommended to adjust the length of the neck strap for more comfort during operation.

7
Acoustic sensor AD-227 is made with threaded
holes for installation of removable rods (magnet
pos.2, rods pos.3 and pos.4) and extension
handle pos.5. The set of sensor includes
plastic plug-screws (for protection of threaded
holes from dust and water) and a key (pos.8).
3.1. Set content of acoustic sensor
threaded
hole plug
While working with acoustic sensor without removable elements for handling, use the handle
on sensor cable to position the sensor (pos.9) .
Using of magnet allows to attach the acoustic sensor to metal pipes and isolation valves. While
preparing the sensor for the operation with removable handle and (or) rods, these plugs should
be removed. After finishing the location the accessories should be removed and the plugs should
be placed back.
3. Acoustic sensor AD-227
3.2. Structural and operation features of acoustic sensor
Sensitive element of acoustic sensor is placed on steel sensing base (later on – base). The
base is hanging at snap diaphragm made of sound-proof rubber and protected from external
noise with safety cuff. Overall design of the sensor reduces the distortion of external noise and
prevents mechanical damage of body.
Best protection from external noise is provided when cuff is placed fully on ground surface.
(also when using rods).
When working with sensor, the cuff is placed fully against the surface, and the base of sensor
should touch the ground surface.
1 – Acoustic sensor AD-227
2 – Magnet for AD-227
3 – Contact rod for AD-227, (70 mm)
4 – Contact rod for AD-227, (150 mm)
5 – Carrying rod for AD-227
6 – Extention carrying rod for AD-227
7 – Allen key, 2 pcs
8 – Key (attached to cable)
9 – Handle
23 4 58
1
8
9
6
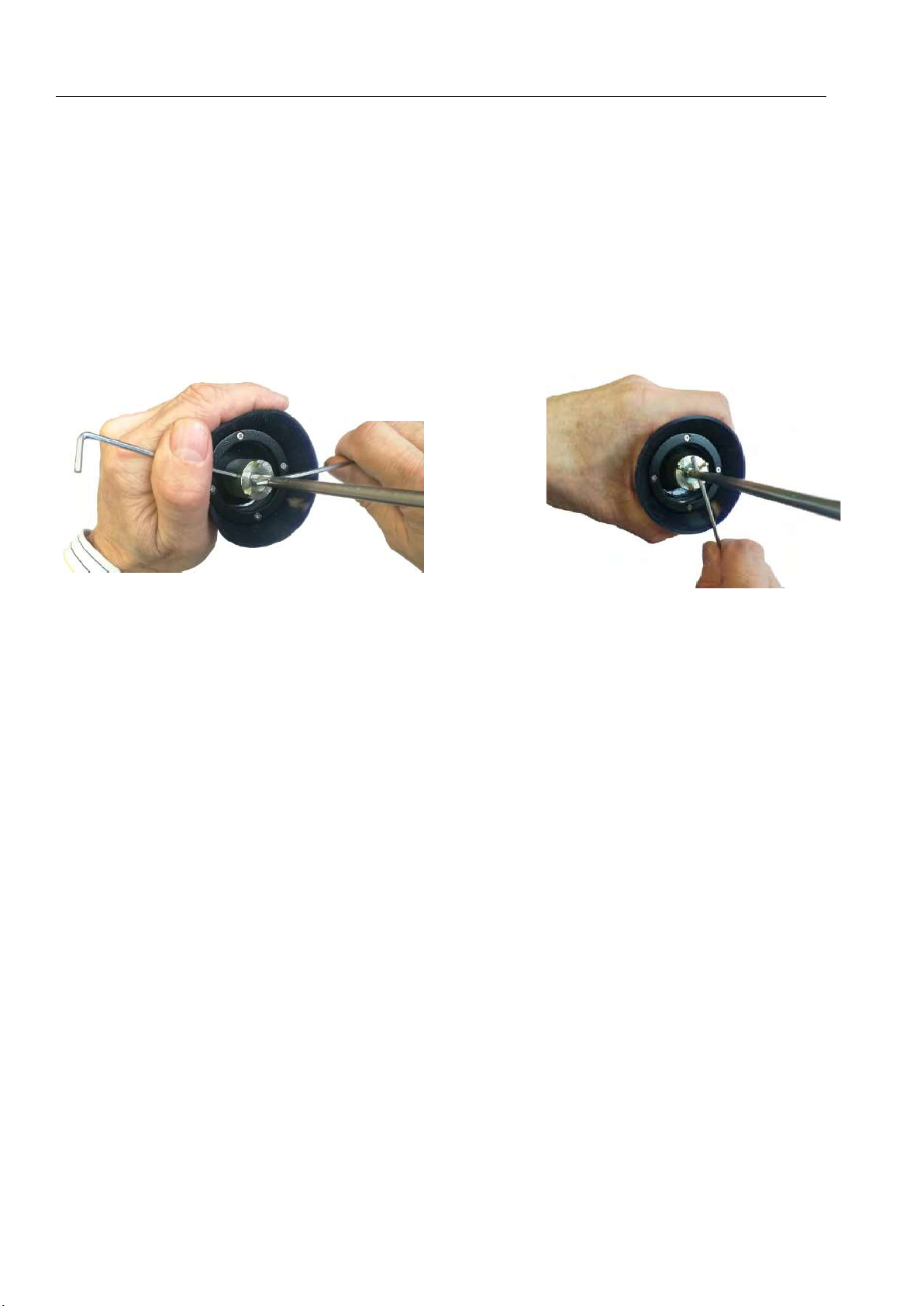
8
While working with sensor, please, make sure you are not pressing it too hard. The sensitive
base may strike of vertical movement mechanical stopper. It may cause the unwanted noise in
headphones and distorted signal. The distortion of signal may happen when sensitive base is
placed incorrectly due to roughness of ground surface. When placing the sensor, choose as flat
surface as possible.
When working on soft soil or in high grass or snow, use removable rods.
The rods are installed and removed manually. If necessary Allen keys (supplied) can be used to
install and remove the rods. (one key is put into the hole of the rod, the second – into the hole in
the base of sensor to prevent cranking of the base and damaging of the sensor)
WARNING! Using one key to install the rod is prohibited!
When using the rods, please, make sure that protective cuff fully touches the surface of the
ground. This helps to exclude the influence of unwanted noise. (Pic. 3.1).
If it is impossible to place the cuff so it fully touched the ground, provide as much silence as
possible. (Pic.3.2).
Pic. 3.1 Pic. 3.2
Indicated useful signal level fully depends on the position of the sensor. Comparison of signal
levels can be done only when the sensor is placed in multiple points at similar conditions..
Moreover, the signal level in each point should be measured several times and average value
should be considered as true.
Some elements of sensor are made of rubber, that is why it is restricted to clean the sensor with
sharp tools. It is also restricted to bash the sensor over hard surfaces in order to clean it off the
dirt. In order to clean the sensor rinse some water on it.

9
4. Operation sequence in liquids leak detection mode
Fig. 4.1
CAUTION!!
During leak detection works one should have a detailed diagram of underground
utilities. If there is no diagram, a preliminary pipeline route location should be
conducted. The level of valid signal and signal interference depends on the accuracy
of acoustic sensor placement over the pipeline axis.
Check the charge status of the batteries (the charge
should be no less than 4,0 V). If the battery charge is low,
replace the batteries
Check the accuracy of
sensor connection. If a «no
sensor» symbol is lit on the
display ,,check if the
sensor is connected
Select the received
signal type «leak»
by any of ▲/▼buttons
Set the necessary
level of receiver display
backlighting, using
◄/► buttons
Equipment used:
3.In the start window on the receiver display:
2. Turn on the
Receiver AP-027
1. Connect acoustic sensor and
headphones to the corresponding
receiver connections
4.1 Connection of sensors and check the receiver operability
Acoustic sensor
AD-227
Receiver
AP 027 Headphones

10
4.2 Preliminary route inspection
1.Place the acoustic sensor over
the supposed pipeline location
2. Switch on the
measurement mode
using the button
3. Set the
broadband mode
, by pressing
the filter button.
4. Set input signal level using
sensitivity buttons и
Narrow scale indicator
readings should be preferably
at 50…90% of maximum value
5. Set the headphones to
required volume u s i n g
buttons◄/►
6. As you move along the route, move the acoustic sensor
in increments of approx.1 m. and place markers in the
spots where the signal level is the highest
7. We recommend you to record
the points where signal level is the
highest into the memory of the
device by pressing the memory
button
7.1. Browse the saved memory (Appendix B), select the
areas with the highest signal and search for leaks in the
marked spots If on the extraneous background sounds you
can hear the distinctive sound of the leak, set the filter
(p.4.3). If not - move the sensor to another proposed
location
The receiver has an ability
to record/view 30 saved
signal levels Output signal
level values are recorded every time
by pressing the memory button
valid value signal leve
Number of the
memory cell.
Selection of the
required memory
cell is made by
◄/► buttons
levels of useful signal, fixed by memory buttons
pressings
Signal level МAX

11
NOTES:
- It is recommended to turn off the measurement mode by pressing the button
before moving the sensor, in order to save the receiver settings and eliminate unpleasant
noise in the headphones.
- During leak detection it is not recommended to move the sensor and use the memory
functionary earlier than 10 seconds after placing the sensor on the ground and turning on
the measurement mode
- Do not change control settings as you move along the route, in order to save the relative
value of signal level.
In order to enter the review mode:
1. Turn off measurement
mode by pressing
2. Press the memory
button
3. Review memorized fields
using the◄/► buttons
In order to leave memory mode press button - you enter the launch window, and then to
return to the measurement mode press «start»
When the receiver is powered off, the recorded data is not saved!
4.3 Conduct fine tuning of receiver filter
General principle of the filter setting is the gradual narrowing of band pass in order to isolate the
sound of leakage and maximum suppression of all other sounds.
1. Place the acoustic sensor
over the suspected leak point
and commence filter setup.
2. On hearing a sound like
the sound of fluid leakage turn
on the band pass filter by the
button
3. Switch to Spectrum
window by pressing visual
indication type button
twice
Suspected
leak point

12
5. Turn on the filter by pressing
the frequency button . A
symbol of low frequencies
suppressing will appear on the
display
6. Using the buttons ◄/►
increase the frequency of the
lower «cut-off» as
long as it is not detrimental to
the intelligibility of the sound
in the headphones
7. Press the frequency
button . A symbol of higher
frequencies will appear on the
display
8. Using the buttons ◄/►
decrease the frequency of the
«cut-off» as long
as it is not detrimental to the
intelligibility of the sound in the
headphones.
9. Check the filtered signal
quality shown in the Spectrum
graph (see p. 4). Highest
number of black stripes (valid
signal) and lowest number
of light stripes (interference)
signifies correct choice of filter
10. Switch to Scale mode
by pressing visual indication
button . Without changing
the settings, examine the
suspected leak area as
described above in sections
3.2 paragraphs 5-8
Frequencies where light segments prevail over the dark ones, are the most likely the
interference frequencies that should be suppressed by pass band filter
4. Conduct an analysis of the generated spectrum
dark segments
correspond
to the frequency
components of valid
(continuous) signal
light to the frequency
components of accidental
interference
Leak point usually corresponds to a point where valid
signal level is the highest.(fig.4.2).
If the same intensity of the signal level is observed at a
distance of 2 to 5 m, then the leak point is located in the
middle of such a segment.
11. Mark the suspected leak location.
12. Turn off the device
Fig.4.2

13
5. Operation sequence in passive cable route detection mode
Fig. 5.1
Used equipment:
1. Connect the electromagnetic sensor and
headphones to the corresponding receiver
connections headphones (if necessary)
5.1 Connection of sensors and check of the receiver operability
2.1 To set the electromagnetic sensor from
transport to operating position. In order to do
that: loosen the locking nut (1), extend the
bar (2) to a required length and fix with the
locking nut
2.2
Loosen the locking nut (1) and install the electromagnetic sensor
(2) in a position used in route detection. Fix the position with the
locking nut. Horizontal position – is used for route detection by
maximum method, and transport position for route detection by
minimum method
3. Turn on
the receiver
AP-027
electromagnetic
sensor EMD-247
receiver
AP-027
1. 2.
1. 2.
headphones

14
4. In the start window of the receiver display:
Check the charge status of the batteries the charge
should be no less than 4,0 V). If the battery charge is low,
replace the batteries.
Check accuracy of the
sensor connection. If a
«no sensor» symbol ,
is lit on the display, check
if the sensor is connected
correctly.
Check the received signal type
as «continuous» (by any of
buttons ▲/▼)
Set the necessary level of receiver
display backlighting, using ◄/► buttons
Fig.5.2
If it necessary, change the
frequency of the second filter
by changing the number of
harmonic component «f
HRM
» to
another by buttons or .
№2
5.2 Conduct receiver setup
For tracing of energized
cables please set
frequency 50 Hz.
1. Switch on the
measurement mode
using the button
5. Set input signal level using
sensitivity buttons and
Level (at the bottom of the scale)
must be within 50 ... 90% of the
maximum
2.
To select the necessary
frequency press the frequency
button . symbol will appear
3. Using buttons ◄/►, set
the desired frequency in the
filtration zone
for example, 50 Hz
4.
Leave the filter adjustment
mode by pressing the frequency
button .
Indicator
will appear in the volume
adjustment zone
6.
Set an acceptable volume
level volume using
◄/►
buttons
7. Moving along the route,
it is necessary to move the
electromagnetic sensor across
the route in one and the other side
to maintain a maximal level of the
signal.
Attention! input overload can lead
to the wrong interpretation of data

15
8. Set the required gain factor of filtered signal to
«×1/2/4/8», by pressing buttons ▲/▼
9. Commence detection or tracing according to the
method set in p.4.3, avoiding prolonged input/output
overloads
5.3 Route location methods
1.The Maximum method
This method consists of positioning the electromagnetic sensor in the direction of the magnetic
field created by the utility radiation (fig.4.3). EMD antenna must be positioned horizontally and
the sensor placed in a plane perpendicular to the cable route. In this case the maximum signal
level is observed when the sensor antenna
passes directly above the utility line. The
maximum method is intended for a quick
route location. Flat peaks of the signal
level curve do not allow for high location
accuracy, but enables a quick route
location.
2. The Minimum method
When the EMD antenna in a vertical (transport) position is placed directly above the route
the signal is at its lowest level fig. 4.4. As the distance from the point directly above the pipeline
increases, the signal level first rises sharply then slowly decreases. This is the minimum method,
which is used to determine a more precise
route location (after quick route tracing
using maximum method.
Horizontal
position
Fig. 5.4
Fig. 5.3
Vertical
position
The Maximum method
The Minimum method

16
1 Source (transmission, charging) switch
2 Internal source voltage selector switch
3 Selector switch of external source power delivery method
4 Selector switch of transmission modes «sin»
5 Selector switch of transmitted signal frequencies
6 Source status and charging process indicator
7 Output status indicator
8 «Dangerous» mode field
9 Plug sealing the external source connector (open)
10 External source connector
11 Output connector for connecting the utility, inductive antenna or clamp (the
sealing plug is closed)
Fig. 6.1
6. Transmitter AG-144.1
6.1 Appearance. Controls
12345
8
7
69
10
11

17
6.2 Transmitter Operating Procedure
Transmitter AG-144.1 transmits sinusoidal current for electromagnetic method of route
location, either continuously or as short trains, for route location of cables and metal pipelines, or
impact device control pulses for acoustic route detection.
High output current of the sine signal (up to 10 A) allows route location of extremely «low-
resistance» utilities (for example, let the output current between «earthed» pipeline and earth loop
bus). High output voltage (more than 330 V) and large power margin (up to 180 W) allow obtaining
the sufficient route location current in long-distance «high-resistance» utilities.
Three sinusoidal transmission modes are provided:
- pulsed;
- continuous;
- three-frequency.
The selected power values are output automatically and are equal to the following values in
autonomous mode: 7,5/15/30/60 W – CONTINUOUSLY, or 15/30/60/120 W - PULSES. Low power
provides for energy saving and low «induction» towards adjacent objects, high power provides for
long distance of signal translation and detection.
Resonant transmitting antenna (a shunt circuit) produces rather powerful radiation at relatively
low energy consumption.
Several stages of protection against various impressible factors ensure high reliability.
«By default» increase of output voltage is limited at the level safe for man (24 V). When
required (for cable route location), the limitation can be cancelled in on-line mode (temporarily till
the session end), provided that relevant safety measures have been taken. Potentially «hazardous»
unlimited mode of transmission is displayed as a special «warning» indicator « ».
SAFETY REQUIREMENTS
There may be dangerous voltage (24 to 400 V) at the transmitter output (including
terminals). The route location method is based on grounding one of the transmitter output
terminals.
NEVER! Touch terminals of output connecting cables and elements of the utility being examined
while the transmitter is operating.
NEVER! Connect and disconnect connector cables while the transmitter is on.
Persons who have taken briefing and are physically qualified are allowed for handling the
instrument.
Transmitter operation mode ensuring personnel safety at connection to the route:
-make sure that no works are carried out or planned along or near the utility being examined,
which may cause intentional or unintentional touching the alive current-carrying part;
- make sure that the transmitter is off;
- earth the cable conductions which is opposite to the transmitter connection end and hang out
the table «Earthed» («High voltage»);
- if the first three conditions are infeasible, use contactless connection by means of the inductive
antenna or inductive clamp;
- make sure that the instrument cannot be unintentionally switched on by another person during
connection of the output cable;
- connect the output cable terminal to the utility being examined (cable cord, pipeline,
communication cable);
- connect the second output cable terminal to earth, cable armature, or to the grounded pin;
- connect the output cable terminal to the output jack of the de-energized transmitter;
- if there are other people near current-carrying parts, warn them about power supply saying
«Power on».
CAUTION!!
During work on connecting the transmitter, the transmitter itself must be turned OFF!!

18
Transmitter operation mode ensuring personnel safety at disconnection from the
route:
-switch the transmitter off;
- disconnect the output cable from the transmitter, then close the connector with a rubber plug;
-repair works (digging the cable out, sleeve mounting, etc.) are allowed only AFTER the
transmitter is off and disconnected from the utility.
6.3 Transmitter Connection
6.3.1 Contact method of transmitter connection
This method provides for interference-free signal
transmission and allows using low frequencies.
Connection to utilities is carried out through attachment of
the transmitter output connector to the utility and ground pin
(Fig. 6.2).
Attachment is carried out at any appropriate place, the
attachment point shall be cleaned from dirt with a file or
abrasive paper till the metal can be seen. It provides for more
reliable electrical contact of the terminal and utility.
Earth contact mounting:
- To obtain maximum route location distance at transmitter
connection to the utility, place the earth contact at an angle
approaching 90оand at a maximum distance from the route
towards the supposed detection direction.
- Bury the earth pin to the height of not less than 2/3.
- To obtain the highest efficiency from grounding, do the following at the place of grounding pin
mounting: strip contacts at the point of contact wire connection to the pin, ram the soil, moisten
the soil using salt solution.
Methods of transmitter connection to the utility
Follow the below rules to ensure the proper detection of route location:
The longest range at route location is provided by direct connection of the transmitter to the
load.
There are several methods for route location of an
underground cable or a pipeline at direct connection
to the utility:
1) return conductor – ground (Fig. 5.3)
For this purpose connect the transmitter to one
cable end and ground the other cable end.
2) return conductor – cable armature (Fig. 5.4)
Using this method, connect the transmitter to
cable ends, join other cable ends.
3) return conductor – cable cord (Fig. 5.5)
Using this route location method, connect the
transmitter to two cords from one cable end and join
cords from the other end.
Fig.6.3
Fig.6.2
Fig.6.4
Fig.6.5

19
6.3.2 Contactless method with the use of - inductive antenna IEM-301.3
Connection to the utility is performed in inductive way. To this end, take the antenna from
the package and insert the antenna active part into the base body. Connect the antenna to the
transmitter output connector and install it above the place of supposed route location so that the
antenna and the route are in the same plane (Fig. 6.6).
6.3.3 Contactless method with the use of inductive clamp.
This method allows route location of utilities, loaded and unloaded cables. Clamp must be
closed around the conductor subject to route location (Fig. 6.7).
NEVER!
Touch terminals of output connector cables and components of the utility subject to
route location while the transmitter is on.
NEVER!
Connect and disconnect connector cables while the transmitter is on.
6.4 Powering on the transmitter
Connect onnect the load to the socket on the transmitter back panel in
accordance with the method of transmitter connection
to the route (see section 6.3). The load may be the route
being detected (pipeline, cable), induction antenna or
inductive clamp.
In order to ensure safety, it is strongly recommended
to complete all connection work before transmission is
commenced.
Turn on the power supply by positioning the power
on switch (Pt. 1 Fig 6.8) into one of the «I» positions,
depending on selected power. If the «Power» indicator
(Pt. 6 Fig 6.8) glows yellow, charge the internal batteries;
if it glows green, you may commence the work.
Fig.6.8 12345
8
7
6
Fig.6.6 Fig.6.7

20
6.5 Transmitter parameter setting
6.5.1 Open the cover. Using selector switch «FREQ» (Pt. 5, Fig Fig 6.8), select the required
frequency of sinusoidal transmission (512/1024/8192 Hz).
6.5.2 Using selector switch «MODE SIN» (Pt. 4, Fig 6.8), select the required type of sinusoidal
transmission («CONT»/« »/»3 FREQ»).
- continuous mode is required for most multi-sensor digital receiving systems;
- pulsed mode – highly economical mode with high legibility against the interference background
for interface with analogue (mainly, one-sensor) receiving systems;
- three-frequency mode provides for selection of optimum frequency at the remote receiver
without changing the transmitter frequency.
6.5.3 Using selector switches «SOURCE» («EXTERN»/»INTERN»), select the required operation
mode.
Set the selector switch (Pt. 3, Fig 6.8) to position «OPER».
Using the internal source voltage selector switch (Pt. 2, Fig.6.8), set the first factor of the
transmission power selection.
Power is selected based on the following principle: «minimum power which is sufficient for
obtaining the output current producing the electromagnetic field allowable for route location».
Follow the below principles when selecting the transmission power and frequency:
- «lower power, lower frequency» – «repeated induction» towards adjacent objects are rarer,
power supply life is longer
- «higher frequency» – receiver sensitivity is higher, lower power is enough, energy saving is
possible, recommended for «high-resistance» utilities, but the degree of signal penetration into
surrounding objects is higher, and due to greater attenuation the signal spreads to a shorter
distance.
- «higher power, lower frequency» – transmission and route detection distance is longer but the
power supply life is shorter.
6.5.4 Switch on power supply setting the power on-key (Pt. 1, Fig 6.8) to the position
corresponding to the second factor of power selection.
6.5.5 Transmission and automatic matching will start with gradual output voltage increase.
Watch the colour of indicator «OUT» (Pt. 7, Fig 6.8). If automatic matching ends with green light, the
preset power has been reached. If automatic matching ends with yellow light, the load resistance
is too high for the preset power while the output power is limited
«by default» at the «safe» level of 24 V.
Here a decision shall be made whether the detection procedure is possible (for example,
through trial route location). If the current in the line is obviously insufficient for producing an
allowable level of the identification field, increase the output voltage higher than the 24 V «safe»
level. After taking the respective safety precautions, the operator can start automatic matching in
«unlimited mode» on his own responsibility.
To start «unlimited» mode, switch on power supply (using the selector switch «START»), with
the red button « » pressed (pos 8, Fig 6.8) and held pressed till the red indicator « »lights up.
Blinking light of this indicator means possible «danger». Continuous light signals about actual
presence of output voltage ≥24 V.
6.5.6 Operation in mode of shock pulses generation «SHOCK»
- Fasten the shock device on the facility (pipeline) under examination, using a chain fastener
with a detent lever.
- Connect the shock device to the transmission output connector. When the energy is on, the
instrument switches over to mode «SHOCK» (Pt. 5 Fig 6.8) automatically, where one of the three
repetition rates of shock pulses (30-60-120 shocks per minute) can be selected, and the shock
force is directly proportional to the supply voltage.
- Using the selector switch «SOURCE INTERN» (Pt. 2 Fig 6.8), select the shock force («12 V» –
lower, «24 V» - higher).
Table of contents
Other TECHNO-AC Security Sensor manuals
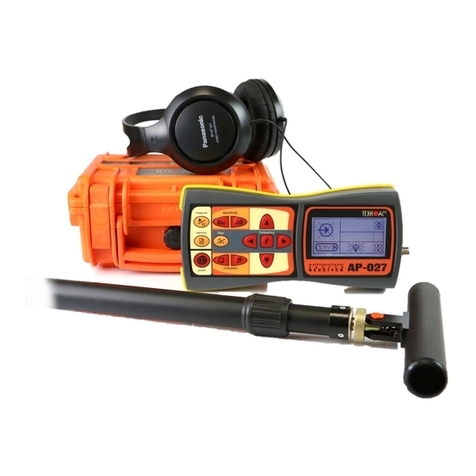
TECHNO-AC
TECHNO-AC SUCCESS-438.15N Manual
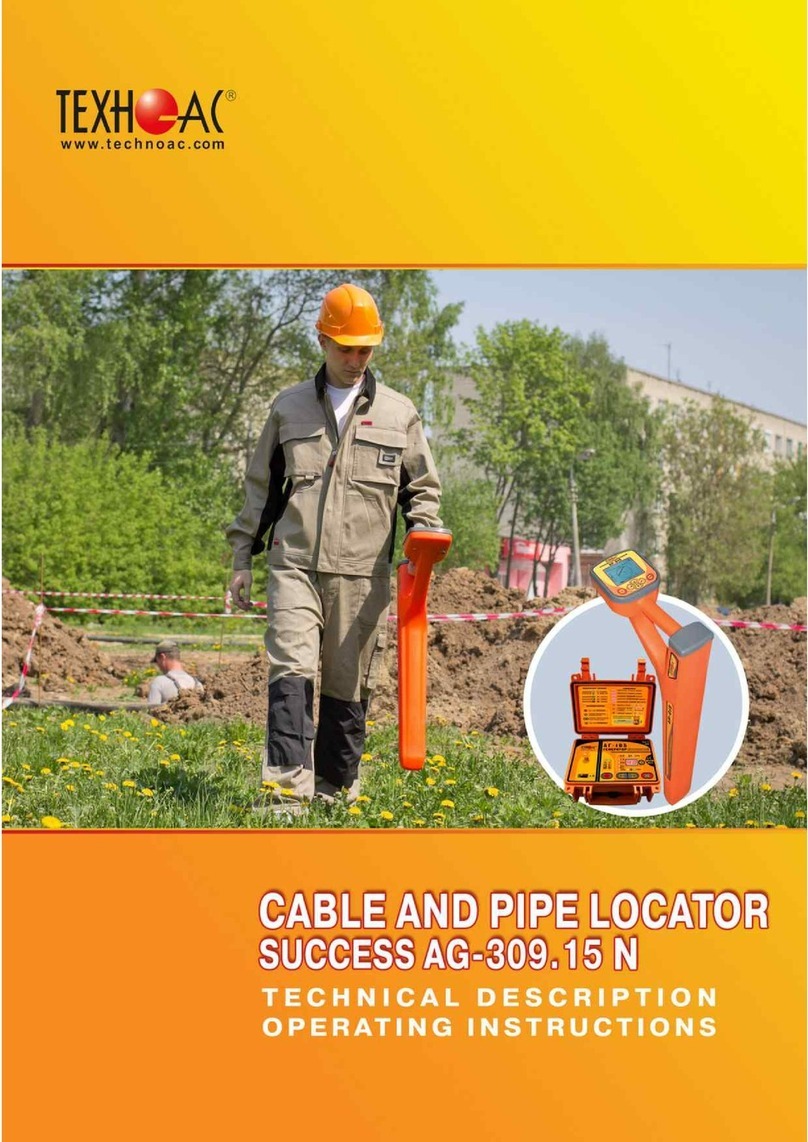
TECHNO-AC
TECHNO-AC Success AG-309.15 N User manual
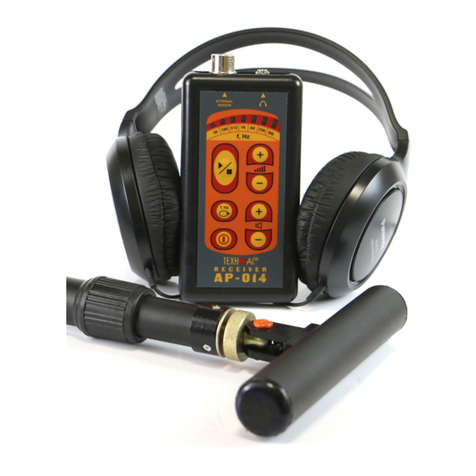
TECHNO-AC
TECHNO-AC Success CBI-116N User manual
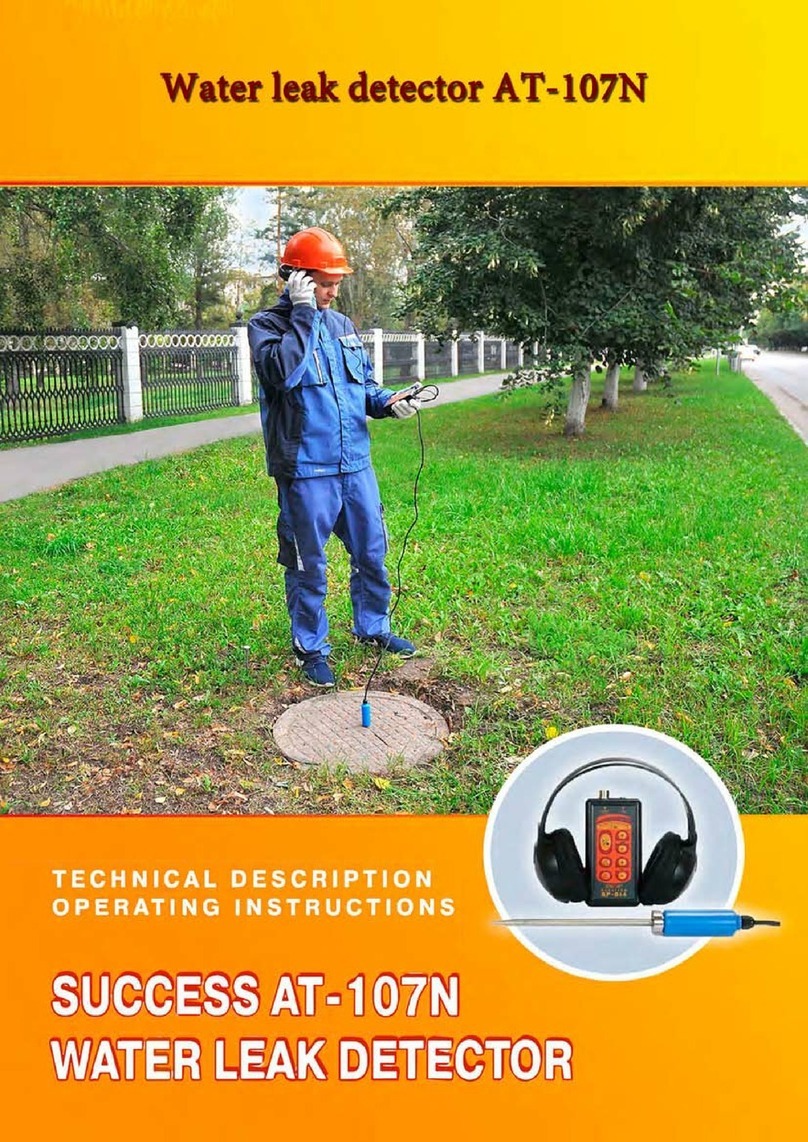
TECHNO-AC
TECHNO-AC Success AT-107N Manual
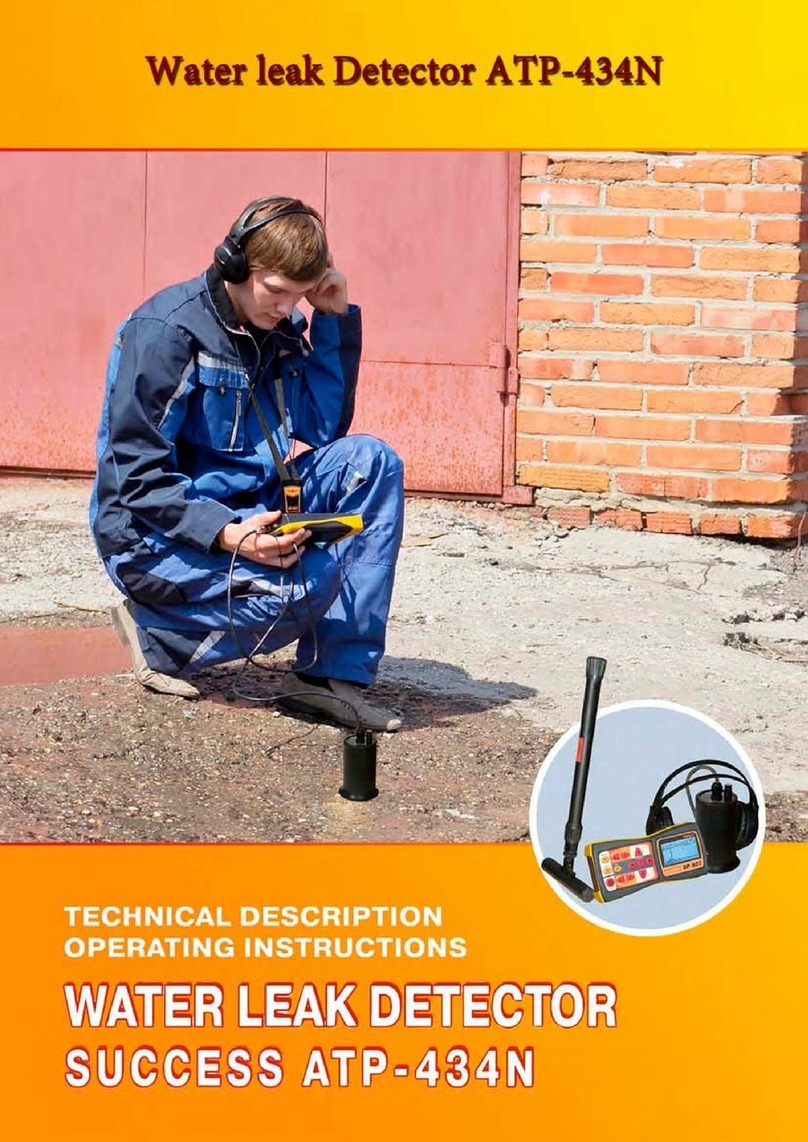
TECHNO-AC
TECHNO-AC SUCCESS ATP-434N User manual
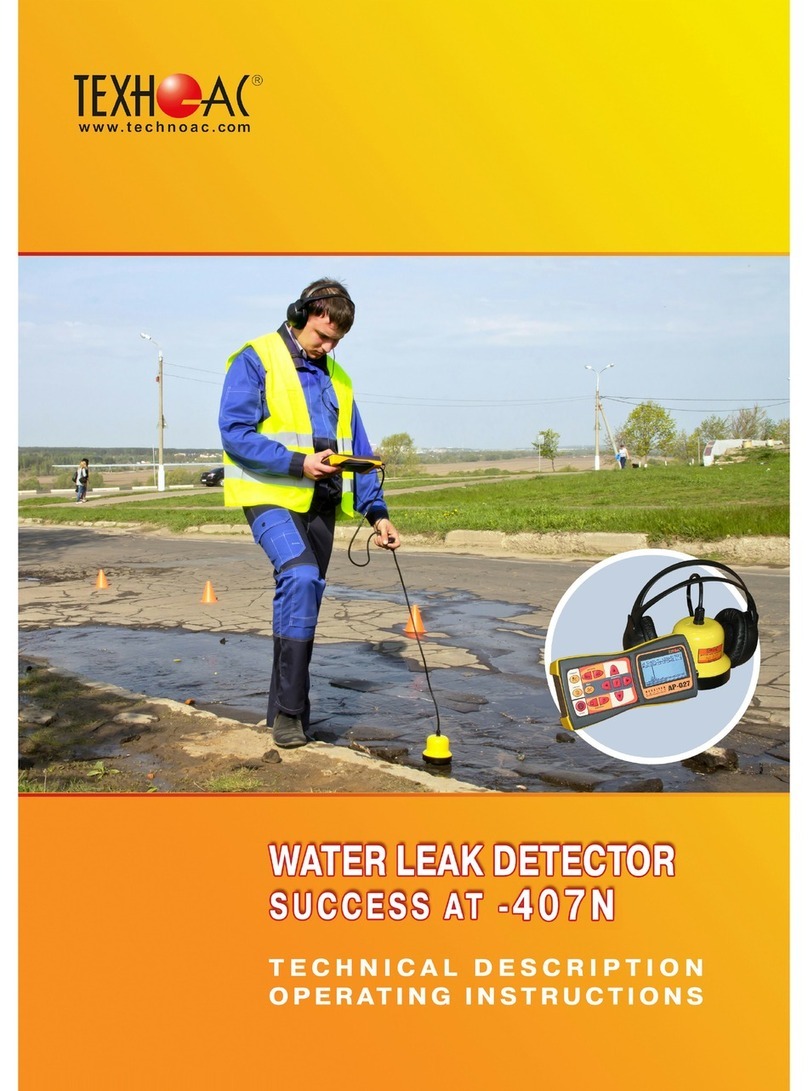
TECHNO-AC
TECHNO-AC Success AT-407N Parts list manual
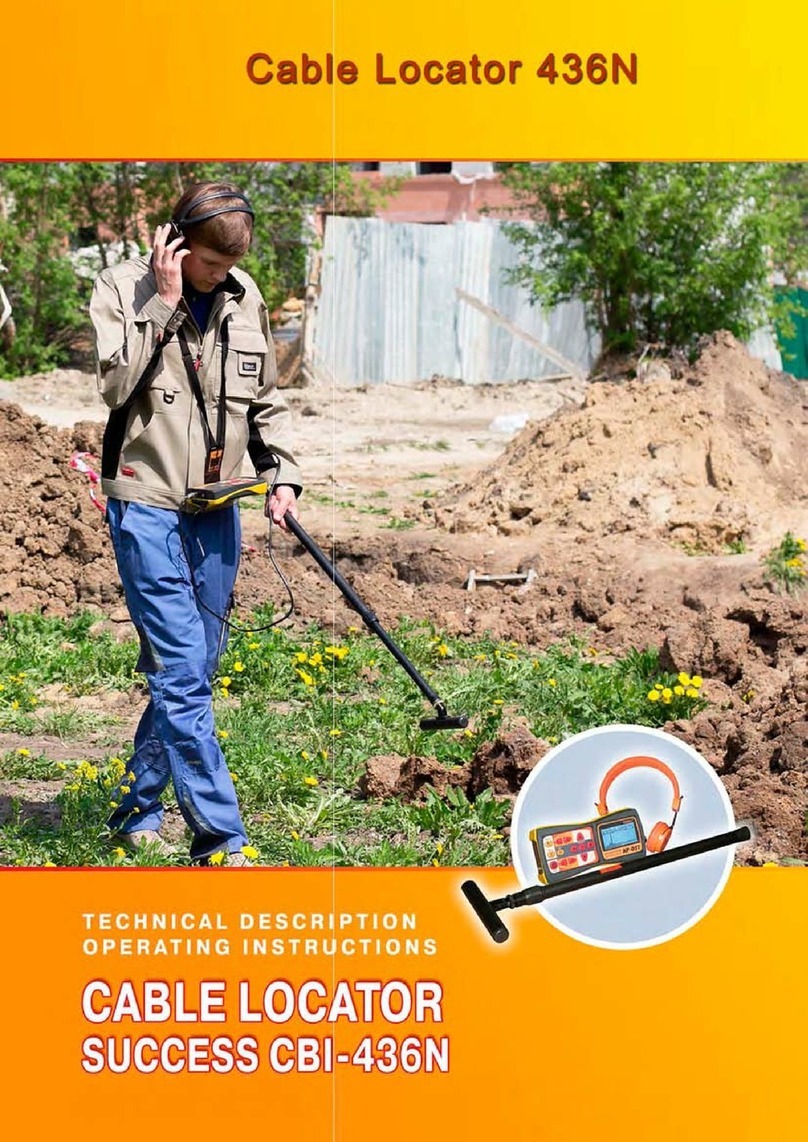
TECHNO-AC
TECHNO-AC SUCCESS CBI-436N Manual
Popular Security Sensor manuals by other brands
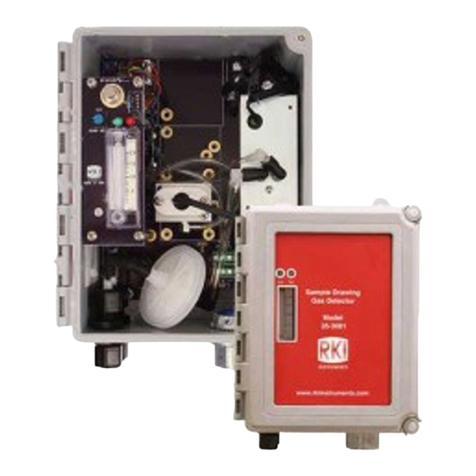
RKI Instruments
RKI Instruments 35-3001A-09 Operator's manual
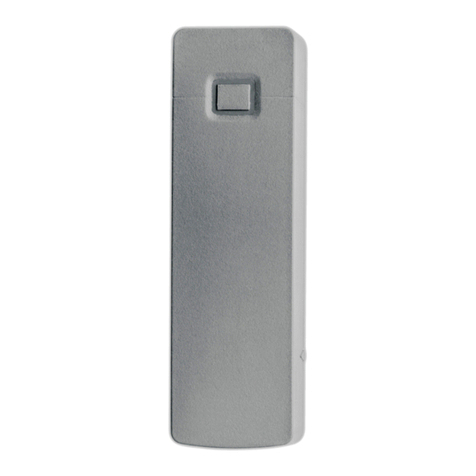
UTC Fire and Security
UTC Fire and Security interlogix RF-DC101 Series Installation sheet
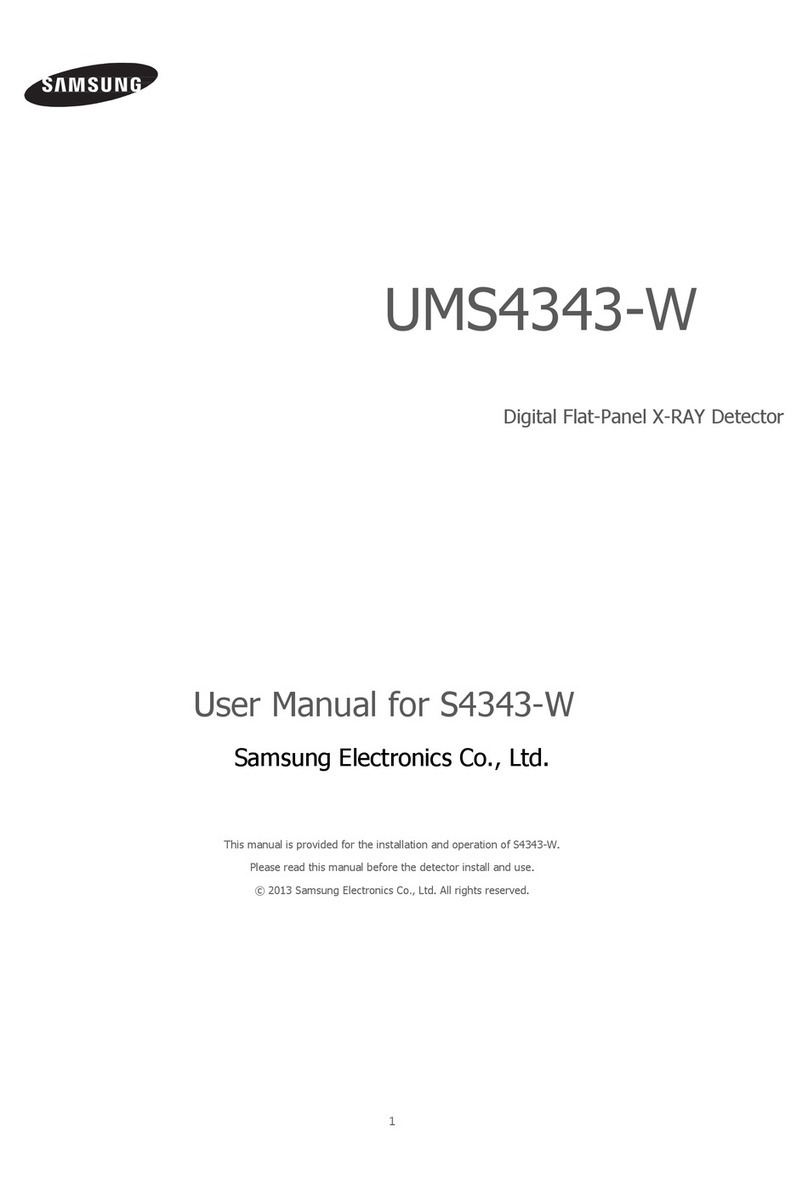
Samsung
Samsung S4343-W user manual
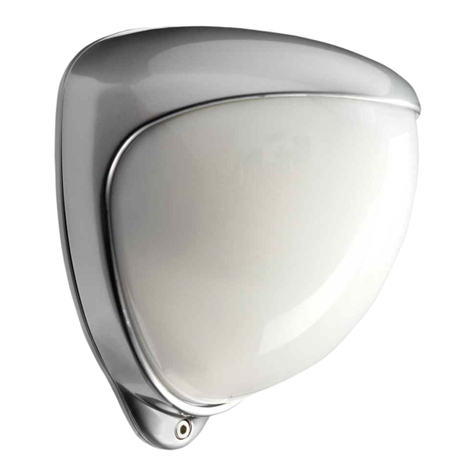
GJD
GJD D-TECT Universal GJD630 manual
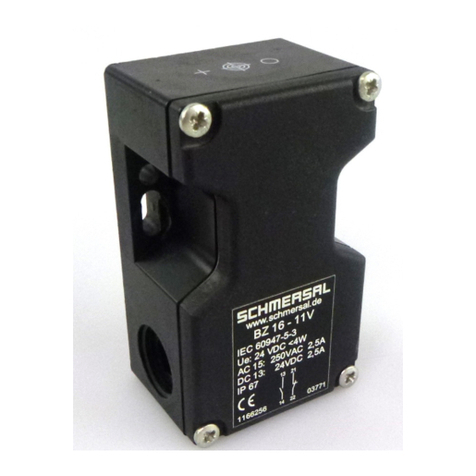
schmersal
schmersal BZ 16 operating instructions
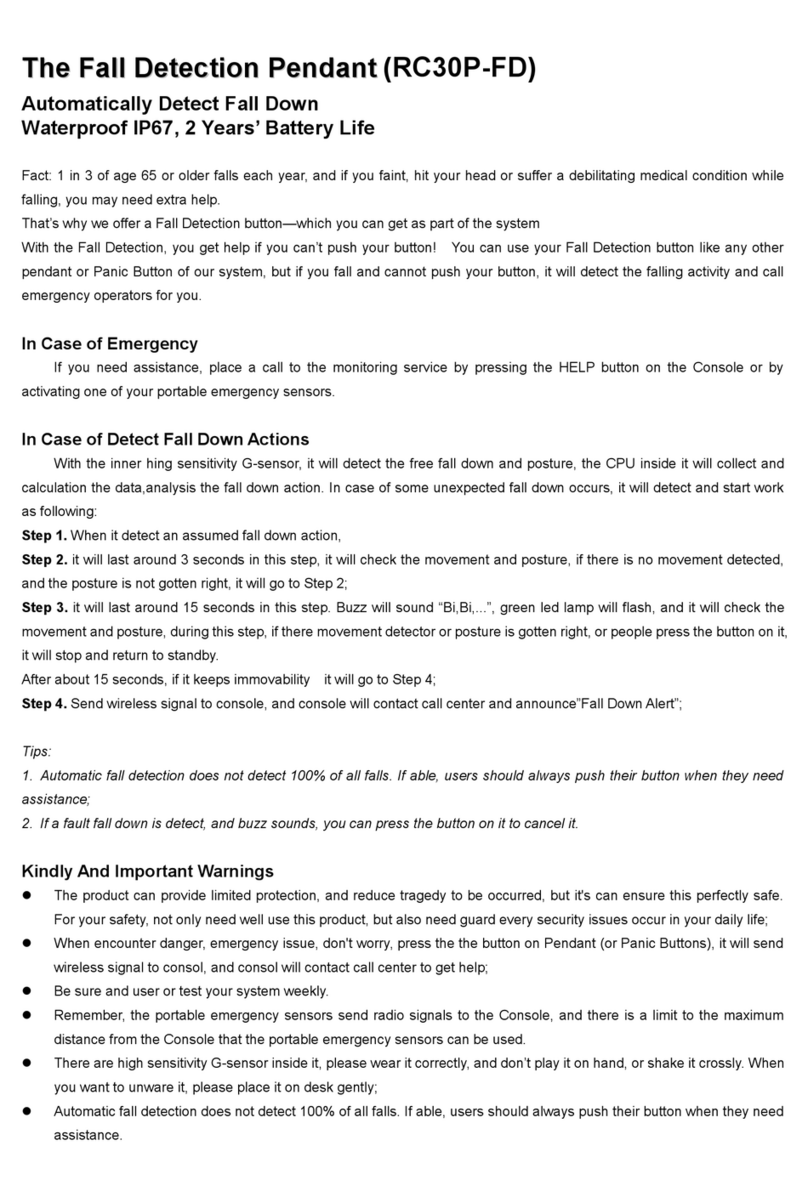
Shenzhen Joy Technology
Shenzhen Joy Technology RC30P-FD user manual