TEM PSD Reader User manual

PSD Reader User Manual
2/ 23
Table of Contents
1Introduction .................................................................................................................... 4
2Block Diagram PSD Reader........................................................................................... 4
3Description of the Front Panel Elements ........................................................................ 5
3.1 RS232 Version (optional) ........................................................................................ 5
3.2 RS422 Version (optional) ........................................................................................ 6
3.3 Version with DAC output (optional).......................................................................... 6
4Connection of the PSD Reader ...................................................................................... 7
4.1 Aligna Con (optional)............................................................................................... 7
4.2 PSD Reader with DAC (optional)............................................................................. 8
5Software Installation....................................................................................................... 8
5.1 Installing the Kangoo Software................................................................................ 8
5.2 Installing USB driver...............................................................................................10
6Upgrading the Firmware................................................................................................10
7Interfacing with a PC.....................................................................................................11
7.1 Variables................................................................................................................11
7.2 Commands.............................................................................................................14
8Using the Kangoo Software...........................................................................................15
8.1 Basic Kangoo Features..........................................................................................15
8.1.1 Buttons and Devices .......................................................................................15
8.1.2 Sections..........................................................................................................16
8.1.3 Further Kangoo Functions...............................................................................16
8.2Kangoo Configuration “CrossHair 4D” ....................................................................17
8.3 Pulsed Lasers ........................................................................................................18
8.4 Automatic Pointing data output...............................................................................20
8.5 Optional: DAC output .............................................................................................20
9Delivery Content............................................................................................................20
10 Pinout........................................................................................................................21
10.1 RJ45 for RS422 (optional)......................................................................................21
10.2 SUB-D 9 for RS232 (optional) ................................................................................21
10.3 DAC output (optional).............................................................................................22
11 Electrical Specification...............................................................................................22
11.1 Environmental Conditions.......................................................................................22
11.2 PSD Reader Device...............................................................................................22
11.3 USB COM Interface................................................................................................22
11.4 RS232 or RS422 Interface (optional)......................................................................22
11.5 Mains Power Connection........................................................................................22
12 Customer Service......................................................................................................23

PSD Reader User Manual
3/ 23

PSD Reader User Manual
4/ 23
1 Introduction
The PSD Reader from TEM Messtechnik is a multi-purpose device for measuring physical
values (optical power, voltage, current) and display them on a PC. In standard application the
sensor is a PSD4Dc (or derivatives like PSD2D or PSDe) and the device displays the four
degrees of freedom of a laser´s beam pointing (angle phi and theta, position x and y, or just
two degrees of freedom in case of using a PSD2D).
In customized applications the device is able to act as a digital regulator which measures a
value, compares it to a setpoint and provides an output to feed it to an actuator.
Since the signal processing is exclusively done by a microcontroller, the PSD Reader device
shows great flexibility. All important parameters and settings are accessible by interfacing the
device with a PC, either using the dedicated program Kangoo or user-supplied software
2 Block Diagram PSD Reader
At the heart of the PSD Reader device lies a microcontroller, which handles all
communications over the USB interface and over the I2C or SPI bus. For reading input
signals or acquiring data, the PSD Reader is equipped with an 8-channel, 16-bit ADC with an
input range of +/-10V.
Figure 1 Block diagram, optional components shown semi-transparent
The standard configuration of the PSD Reader electronics features one 8-channel input
connector for feeding in PSD- or photodiode-signals.
Optionally the controller can do signal processing, such as the implementation of PID-
regulators, the generation of control signals for micro-stepper motors or digital filtering.
Optional signal output is provided by a 4-channel, 16-bit digital-to-analog converter (DAC).
The output range of this DAC is +/-10V.

PSD Reader User Manual
5/ 23
3 Description of the Front Panel Elements
Figure 2 Top view of the PSD Reader
Table 1 Function of the front panel elements
1
PSD input
HD-15 connector: PSD input, I2C, SPI, supply voltages
2
Power plug
Input for coaxial power connector (5,5/2,5 mm)
3
Status LED
LED indicator for intensity status:
Slow “breathing”: intensity OK
Fast “breathing”: intensity too high or too low
4
USB port
USB port for the connection to a PC and the Kangoo software
5
Prog Key
Hold key and switching on power supply: Enter program mode
In normal use: Perform Autogain
3.1 RS232 Version (optional)
Figure 3 Top view of the PSD Reader
Table 2 Function of the front panel elements
1
RS232 port
SUB-D 9 Connector for the communication via RS232 to a PC
and the Kangoo software
2
PSD input
HD-15 connector: PSD input, I2C, SPI, supply voltages
3
Power plug
Input for coaxial power connector (5,5/2,5 mm)
4
Status LED
LED indicator for microcontroller activity
5
USB port
USB port for flashing the microcontroller
6
Prog Key
Hold key and switching on power supply: Enter program mode
In normal use: Perform Autogain

PSD Reader User Manual
6/ 23
3.2 RS422 Version (optional)
Figure 4 Top view of the PSD Reader
Table 3 Function of the front panel elements
1
RS422 port
RJ45 Connector for the communication via RS422 to a PC and
the Kangoo software
2
PSD input
HD-15 connector: PSD input, I2C, SPI, supply voltages
3
Power plug
Input for coaxial power connector (5,5/2,5 mm)
4
Status LED
LED indicator for microcontroller activity
5
USB port
USB port for flashing the microcontroller
6
Prog Key
Hold key and switching on power supply: Enter program mode
In normal use: Perform Autogain
3.3 Version with DAC output (optional)
Figure 5 Top view of the PSD Reader
Table 4 Function of the front panel elements
1
DAC output
HD-15 connector: Pointing and trigger signals output
Pin1: DacA, Pin2, DacB, Pin 3: DacC, Pin 4: DacD, Pin 8: SG,
Pin11: Trigger out, Pin 12: DAC update, Pin 13: Sampling
(Pulsed Mode)
2
PSD input
HD-15 connector: PSD input, I2C, SPI, supply voltages
3
Power plug
Input for coaxial power connector (5,5/2,5 mm)
4
Status LED
LED indicator for microcontroller activity
5
USB port
USB port for flashing the microcontroller
6
Prog Key
Hold key and switching on power supply: Enter program mode
In normal use: Perform Autogain

PSD Reader User Manual
7/ 23
4 Connection of the PSD Reader
The PSD Reader is commonly used to set the gain of the PSD detectors and read out the
position and angle data. For this purpose the PSD detector is connected via Sub-D 15 HD
cable (1:1 Pin connection) to the PSD Reader. This configuration is shown in Figure 6. The
12 Volt power supply of the PSD Reader is used to supply the electronics and the PSD
detector. For the communication to the PC a UBS cable is included.
Figure 6 Connection of the PSD Reader
4.1 Aligna Con (optional)
TEM Messtechnik GmbH offers an Aligna Con module to get access to the raw signals of the
PSD via BNC connector. This allows a monitoring of the signal with e.g. an oscilloscope
without limitation of the bandwidths. The Aligna Con is either inserted into the connection
between the PSD and the PSD Reader or connected to the PSD reader with a y-adapter
cable (see Figure 7 and Figure 8).
Figure 7 In-Line configuration

PSD Reader User Manual
8/ 23
Figure 8 Y-configuration
4.2 PSD Reader with DAC (optional)
If ordered the PSD Reader can equip with a 4 channel digital-to-analog converter, providing
+/-10 volts per channel. The output voltages can be controlled via Kangoo Software or
coupled to the measured pointing data. As pointing output the voltages correspond to the
measured position in mrad or mm (mrad or mm / Volt). The four pointing signals can be
connected at the DAC output via AlignaCon module to an oscilloscope.
5 Software Installation
5.1 Installing the Kangoo Software
To install the Kangoo software, start the program “Install.exe” in the root directory of the
installation CD. The installer will show a welcome screen with several options.

PSD Reader User Manual
9/ 23
Figure 9 Kangoo installation: Welcome screen
“Details” informs you about the installation procedure.
“Source path” indicates the source path of the installation.
“Destination Path”: Here, you can choose the desired destination path. The standard
directory is “TEM” in the "ProgramFiles" folder. On Windows Visa or Windows 7 systems,
please avoid the "Program Files" folder and choose the path "C:/TEM”!
The button “OK, install now!” starts copying all required files from the source path to the
destination path.
During the installation procedure, the installation program checks all required files.
Figure 10 Kangoo installation: Progress
The program then creates a list of file copy commands. When this list is complete, you can
check the list and start the copy procedure.

PSD Reader User Manual
10 / 23
Figure 11 Kangoo installation: Start copy procedure
Figure 12 Kangoo installation: Summary
Figure 13 Kangoo installation: Successful installation
5.2 Installing USB driver
Typically, when the USB connection between the micro-controller and a PC is first made,
Windows will open the Found New Hardware Wizard. Here, choose to install drivers from a
user-specified location. The necessary driver file is located in the directory
“TEM/Service/USB Driver” in the Kangoo installation directory (or on the USB Stick). The
Hardware Wizard will now finish the installation and no further configuration will be
necessary. Once the installation is complete, Windows will assign a COM-port. To find out
which COM-port has been assigned, check for a new entry in the section “Ports (COM &
LPT)” of the device manager.
6 Upgrading the Firmware
Please contact TEM Messtechnik for details about firmware upgrades.

PSD Reader User Manual
11 / 23
7 Interfacing with a PC
The microcontroller of the PSD Reader is accessed via USB using ASCII-formatted text
strings. Each string has to be terminated by a carriage return character (‘\r’ or ASCII 13).
These strings separate into two general categories, namely variables and commands. A
variable represents a user-accessible parameter which can be set, queried and stored.
Examples of variables are the maximum speed of a motor, the regulator status and the serial
number of the device. Commands execute single actions, such as an analog-to-digital
conversion or the sending of output to the PC.
7.1 Variables
If the text string sent to the microcontroller contains an equal sign, it is interpreted as a
variable. If this equal sign is followed by a space and an integer number, the text string is an
assignment and the current value of the variable is updated. If the string ends after the equal
sign (trailing spaces are irrelevant), the string represents a query and the microcontroller
echoes the current value of the queried variable. Echoes can be suppressed by prefacing the
variable name by a backslash.
Table 5 Examples of setting and requesting variables
Text string
Type
Answer from microcontroller
SerialNumber= 7012
Assignment
SerialNumber= 7012
SerialNumber=
Query
SerialNumber= 7012
\SerialNumber= 7012
Assignment, no echo
Each variable has a maximum and a minimum value. If assignments lie outside this range,
the assigned value is clipped and this clipped assignment is echoed back to the PC.
The following list shows all variables which are available in the PSD Reader.
Table 6 List of variables
Variable name
Values
Description
SerialNumber
0 to 100000000
the serial number of the device
Build
Actual Firmware version
uCApplication
0 to 1000
tells the PC which application program is active
PCBVersion
Actual Hardware version
DacA, Dacb, DacC,
DacD
-10000 to 10000
optional: Voltage at the DacA/B/C/D output in mV
DacA_output,
DacB_output,
DacC_output,
DacD_output
0 to 6
optional:
0: manual setting
1: Pointing Ax
2: Pointing Ay
3: Pointing Bx
4: Pointing By
5: Sum A
6: Sum B
PsdAgain
100 to 1000000
gain in percent for a TEM angle PSD
PsdAdx
-9999 to 9999
gain offset factor in x-direction for a TEM angle
PSD
PsdAdy
-9999 to 9999
gain offset factor in y-direction for a TEM angle
PSD
PsdBgain
100 to 1000000
gain in percent for a TEM position PSD
PsdBdx
-9999 to 9999
gain offset factor in x-direction for a TEM position
PSD
PsdBdy
-9999 to 9999
gain offset factor in y-direction for a TEM position

PSD Reader User Manual
12 / 23
PSD
PsdUnitsA
0 t0 3
physical units for displaying the angle PSD
0: ADC units (-32768 to 32767)
1: Volts (-10 to 10)
2: mm @ PSD
3: mrad
PsdUnitsB
0 t0 3
physical units for displaying the position PSD
0: ADC units (-32768 to 32767)
1: Volts (-10 to 10)
2: mm @ PSD
3: mrad
AxScale, AyScale
0 to 10000
scaling factor, active when PsdUnitsA = 2
BxScale, ByScale
0 to 10000
scaling factor, active when PsdUnitsB = 2
BL_AdcScale(0)=
-1000000 to 1000000
Scaling of Pointing signal Ax
BL_AdcScale(1)=
-1000000 to 1000000
Scaling of Pointing signal Ay
BL_AdcScale(2)
-1000000 to 1000000
Scaling of Pointing signal Bx
BL_AdcScale(3)
-1000000 to 1000000
Scaling of Pointing signal By
BL_AdcScale(4)
-1000000 to 1000000
Scaling of SumA
BL_AdcScale(5)
-1000000 to 1000000
Scaling of SumB
AdcOffsetAx
-10000 to 10000
offsets
AdcOffsetAy
-10000 to 10000
AdcOffsetBx
-10000 to 10000
AdcOffsetBy
-10000 to 10000
AdcOffsetSumA
-10000 to 10000
AdcOffsetSumB
-10000 to 10000
FocalLengthPsdA
100 to 10000000
FocalLengthPsdB
100 to 10000000
PsdDiffGainSwitch
A
0 to 1
gain boost for the angle PSD
PsdDiffGainSwitch
B
0 to 1
gain boost for the position PSD
PsdDiffGainAx
1 to 1000000
PsdDiffGainAy
1 to 1000000
PsdDiffGainBx
1 to 1000000
PsdDiffGainBy
1 to 1000000
MinIntens
-1000 to
12000
minimum intensity for the measured PSD signals
(below this threshold, scope view wont´t work)
MaxIntens
-1000 to
12000
maximum intensity for the measured PSD sigals
(over this threshold, scope view wont´t work)
AutoGainAset
1000 to 9000
set value for autogain procedure
BL_PowerPortion
0 to
100000000
Calibration factor for the power display
Psd_DiagonalA
0 to 1
switch for rotating angle PSD by 90°
Psd_DiagonalB
0 to 1
switch for rotating position PSD by 90°
BL_AvailableAB
0 to 3
0: no detector
1: Detector A only
2: Detector B only
3: Detector A + B
IclABx
-8192 to 8192
Crosslink matrix element
IclABy
-8192 to 8192
Crosslink matrix element
IclBAx
-8192 to 8192
Crosslink matrix element
IclBAy
-8192 to 8192
Crosslink matrix element
Norm
0 to 1
switch on/off the normalization of the differential

PSD Reader User Manual
13 / 23
signals
LaserCwPulsed
0 or 1
0: cw mode
1: activate Trigger for Pulsed mode
LaserRepRate
0 to 80000000
sec. 8.3 for details
below 4000: double sample
above 4001; single sample
Delay1
1 to 65535
Delay in µs between trigger event and first sample
Delay2
1 to 65535
Delay in µs between first and second sample for
“LaserPepRate” below 4000
UcUsartBaudrate
Default 57600. For the (optional) serial
communication higher baud rates might be
necessary like e.g. 921600
Datasendperiod
0 to 10000
Automatic Data output option (same format than
the “BL_PrntVars 1” answer).
Define the delay (ms) between two Datasets.
0: sending off
< 8: sending data with maximum speed of 8ms
8: data output with defined speed
For Pulsed mode the datasets are sending after
each new trigger event but not faster than the
defined delay.
BL_LowPassOn
0 to 1
activates a digital low-pass filter for PSD signals
BL_LowPassTime
1 to 5000
time constant for the low-pass filter

PSD Reader User Manual
14 / 23
7.2 Commands
Text strings which do not contain equal signs are interpreted as commands. The possible
formats are single words, a word followed by an argument or a word followed by an
argument and a value. Examples are shown in the following table.
Table 7 Examples of using commands
Text string
Type
Microcontroller action
varDump
Single word command
Print all variable values
varLoad 1
Command with argument
Set variables to default
da 3 7888
Cmd with arg and value
Set DAC channel 3 to 7888 mV
ad 5
Cmd with arg
Print the value of ADC CH5 in mV
What follows is a comprehensive list of all commands which the PSD Reader can
understand.
Table 8 List of commands
Command name
Arg
Values
Description
Com
Hello
answers with "Hi there!"
Help
VarSave
save all current variable values to the EEPROM
VarLoad
flag
load variable values from EEPROM (0) or from
the program memory (1) and print all
varDefault
set all variables to default values
VarDump
print all variables with their current values
CmdDump
print all command names
uCtype
echo the μController type
AD
channel
ADC value of the desired channel
DA
channel
val
DAC output (if DAC-option)
AutoGain
automatically adjust the gains of TEM detectors
BL_PrntVars 1
Answers with the 4D laser pointing
Ax, Ay, Bx, By, SumA, SumB
Reset
resets the controller

PSD Reader User Manual
15 / 23
8 Using the Kangoo Software
The alignment of the parameters of the system is most easily done with the supplied
software package Kangoo.
Since the PSD Reader is controlled by plain-text commands, it can be configured with any
control software like LabView, TestPoint, or other programs written in VisualBasic, VisualC,
C++, C#, etc. However, to become familiar with the system it is highly recommended to use
Kangoo and benefit from the built-in functions.
8.1 Basic Kangoo Features
"Kangoo" is a comprehensive measurement and controlling software system, which can be
adapted to control completely different applications. (Controlling a PSD Reader or Aligna®
are just two systems of a long list). Kangoo will not be described in complete detail here; just
the basic use and the configuration for use of the PSD Reader will be covered.
In this chapter we will describe very briefly some elementary features and the basic common
usage of Kangoo. In a following chapter we will describe the usage of the standard
configuration, related to the PSD Reader.
8.1.1 Buttons and Devices
The interaction between the user and the program is mainly realized by "buttons" and
"devices" (with the exception of the menu bar). A short explanation ("ToolTip") of the
meaning and sense of a button or device is displayed in the status line, when the mouse
pointer is located over the button or device position.
A "button" forces an activity. This may be the
loading of another configuration (application-specific user surface) ,
starting a measurement or analyzing process ,
display a help text and many more.
A "device" may represent a parameter, either of the Kangoo program, or of the control
software inside the PSD Reader device's microcontroller (µC) firmware.
The appearances of devices can be very different:
There are keys or LEDs ,
numerical parameters, displayed as simple digital value ,
digital and/or analog display , and many more.
To change the value of these parameters there are different options:
The most convenient way is to use the mouse wheel, when the mouse is hovering over
the device. Even very fine or coarse changes can be realized:
The sensitivity of the mouse wheel can be controlled by pressing additional keyboard keys
while moving the mouse wheel
- pressing the "shift" key: factor of 10 higher resolution

PSD Reader User Manual
16 / 23
- pressing the "ctrl" key: factor of 100 higher resolution
- pressing the "alt" key: factor of 10 stronger variation.
In the absence of a mouse wheel you can click and hold the mouse at the device and
move the pointer horizontally. Even here the "shift", "control" and "alt" keys will increase or
decrease the sensitivity.
Many devices have predefined values, which are displayed by a pop-up menu when left-
clicking the device. Selecting the item "others…" allows input of any user-defined value.
A right-click to the device opens a pop-up menu with the option "set value" (even if no
"toggle" pull-up menu is defined with this device.)
8.1.2 Sections
The configurations are usually separated into sections for clarity and convenience. Some
sections contain parameters which are used very infrequently. By clicking the upper right
"close" button the section window will be shrunk to a small button at the bottom line or the left
side of the user screen. The section window can be re-sized by clicking on the minimized
button.
.
8.1.3 Further Kangoo Functions
There are reams of additional features of the Kangoo program, such as calculations,
analyses of measured data sets, import and export of data or the creations of custom
configurations. In this manual however we concentrate just on the description of those
configurations needed for the use of the PSD Reader.
Many of the features are described in the help files, available in the menu items "Help / ...".
(If you have questions regarding further use of Kangoo, please don't hesitate to ask TEM for
additional information.)

PSD Reader User Manual
17 / 23
8.2 Kangoo Configuration “CrossHair 4D”
The standard configuration for using the PSD Reader is the configuration “CrossHair 4D”.
This configuration is located in the folder C:\TEM\Kangoo\Data\CrossHair. Figure 14 shows a
screenshot of this configuration.
3
Figure 14 Kangoo Configuration Cross Hair 4D
First you have to connect to the microcontroller of the PSD Reader: Left-click on the “check”-
button, then choose the matching COM-port (if you´re not sure which channel is correct,
please have a look in the device manager). Open the COM-port by left-click on “ComPort”-
Button. The Kangoo-LED should light up yellow.
Figure 15 Section "COM Port"
If the PSD Reader and the PSD4Dc/PSD2D have just powered up, the photocurrent-
amplifiers may have an incorrect gain. The effect would be a very high or low intensity level.
To set the gains correctly, just change the devices “PSD A gain” or “PSD B gain” or do an
“Auto gain” (The Auto gain procedure try to set the gains in a way that the sum-signals of A-
and B-detector are the –“setintens” – e.g. 5V). Furthermore the gains have to be in the
range between 5…10000.
If the beam hits the detector and the sum-signals are in the correct range, you can observe
the beam movement on the Kangoo screen. The laser beam position is shown in the scope
view. If you have a PSD4Dc the green dot stands for the laser beam position and the red dot
stands for the laser beam angle. If the beam changes the position/angle this causes a
movement of the green/red dot in Kangoo.
If you have a PSD2D then just one dot (the green or the red, depending on the detector) is
moving by varying the beam position.

PSD Reader User Manual
18 / 23
To save your new settings like gain of the PSD, click on the “VarSave”-Button.
The new values will be saved and at the next power cycle or reset, they will be load
automatically.
To log the beam pointing, please open the section “Recorder”. In the window you can choose
some different record options. By clicking “run” the chart recorder starts to record the beam-
pointing.
Figure 16 Section "Recorder"
To save these values to your computer choose in the menu bar: Data->Data export… Here
you can choose several export options and save the recorded data to a *.txt file.
8.3 Pulsed Lasers
If you work with pulsed lasers, you have to choose the pulsed option in the section “Pulsed
Laser Parameters” (Figure 17).
Figure 17 Section "Pulsed Laser Parameters"
Usually if a short pulse is applied to a photodiode (or the PSD), the photodiode will be
saturated. Thus the electric signal of the photodiode is stretched by a low pass filter to
spread the energy over a bigger time section. This stretched pulse is processed by the
microcontroller.

PSD Reader User Manual
19 / 23
In pulsed mode the rising edge of the sum of the PSD is detected and the signal is sampled.
There are two different pulsed modes available depending on the repetition rate: If the
repetition rate is below 4 kHz, the pulse is sampled twice: One sample at the peak and one
sample at idle level. The difference is the resulting photodetector value. This way DC offsets
like background light and also 50 Hz hum will be ignored. Figure 18 shows the principle.
The time between detection and the first sample is set with the Kangoo device “Delay 1”. The
time between the first and the second sample is set with the device “Delay 2”.
Figure 18 Pulsed mode below 4 kHz
At higher repetition rates, the pulses are getting closer to each other and a double sampling
like in Figure 18 is not appropriate. If you choose a repetition rate above 4 kHz, the pulse is
just sampled once, see Figure 19. The beam pointing may vary if you change between the
two sampling modes.
Figure 19 Pulsed mode above 4 kHz
Note: To set the correct delay, please set a repetition rate in Kangoo of 4 kHz or higher.
(That means the controller just samples once. The laser may have another repetition rate).
Set the device “Delay1” the way that the sum signal is at its maximum. The chart recorder
may be a good help for that task (see Figure 20). For the time “Delay2” the standard time is
100 µs. In normal case you don´t have to change this value. To be on the save side, you can
variate the “Delay 2” value and check, that the intensity signal of the PSDs don’t increase.
Figure 20 Power displayed in the chart recorder
too low good too high
time [s]
Delay1 [µs]
Delay1:

PSD Reader User Manual
20 / 23
8.4 Automatic Pointing data output
If needed the PSD Reader can send the actual pointing data to the PC. The data format is
the same than the answer from the “BL_PrntVars 1” request. To activate this feature the
variable “Datasendperiod” must be set to a value > 0. This defines the timeout (in ms)
between two datasets. To avoid problems the minimum time between two dataset is limited
to 8 ms. Values between 1 and 8 will cause a minimum delay of 8 ms. The variable can be
found at the Crosshair 4D Configuration at the hidden parameter section. For CW mode the
data output is time controlled. For Pulsed mode the data output is additional trigger by the
optical pulse. In this mode a data set will be send after an trigger event and the given
timeout. For repetition rates up to 100 Hz and the minimum timeout (“Datasendperiod = 8”)
the pointing data of each pulse can measured.
Notice!
The Auto gain function or high communication load might slow down the data output speed.
8.5 Optional: DAC output
The DAC output voltages can be controlled by the devices DacA…DacD via Kangoo
Software. For manual setting of the voltages please set the corresponding “DAC Output” to
Manual (value 0).
Figure 21 Menu of the DAC output
Alternatively the DAC voltages can be coupled the Pointing signals by Software
Figure 22 Option for the DAC outputs.
In this case the DAC values were updated with about 5 kHz for CW mode. The DAC update
moment can be monitored via oscilloscope at DAC output pin 12. The rising signal edge is
connected to the start of the DAC write while the falling edge is connected to the end of the
DAC write process. For Pulsed mode the DAC values were updated after each optical pulse.
The maximum repetition rate depends on the DAC write process time (about 25 µs per
channel) and the delays. For repetition rates above a few kHz please monitor the electrical
trigger signal (Pin 11 at the DAC output connector) and the update signal of the DAC (Pin 12
at the DAC output) to check that the DAC is updated after each pulse.
9 Delivery Content
Please check the device on delivery for damaged or missing items.
Delivery content:
- PSD Reader
- 12V Power supply
- HD15 and USB cable
It is recommended to keep the packaging material for future storage and transportation.
Table of contents
Popular Measuring Instrument manuals by other brands
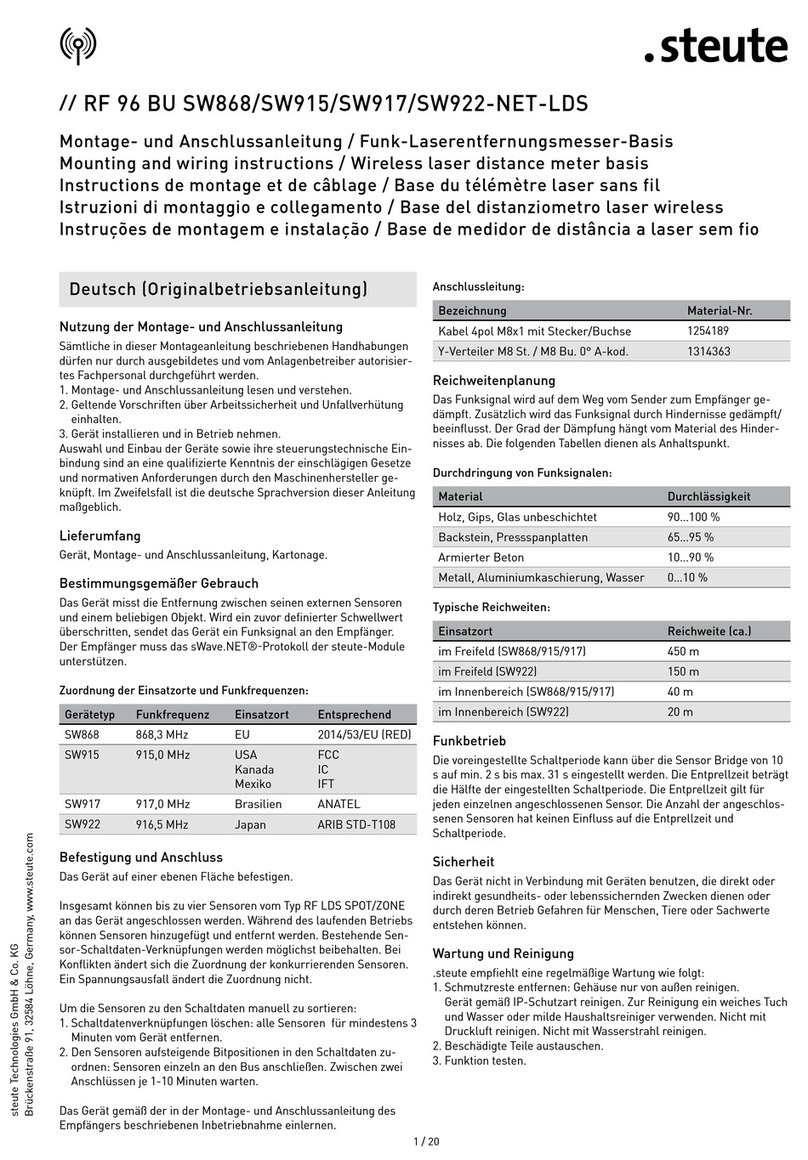
steute
steute RF 96 BU SW868-NET-LDS Mounting and wiring instructions
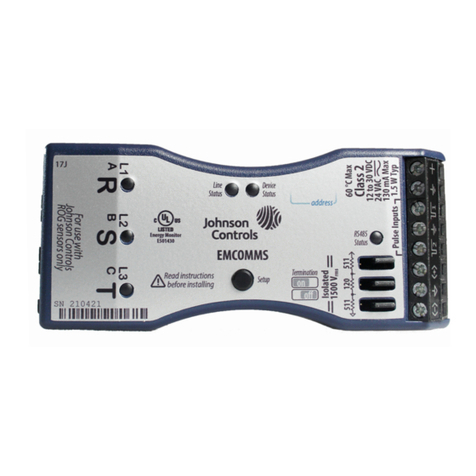
Johnson Controls
Johnson Controls EMCOMMS Series installation instructions
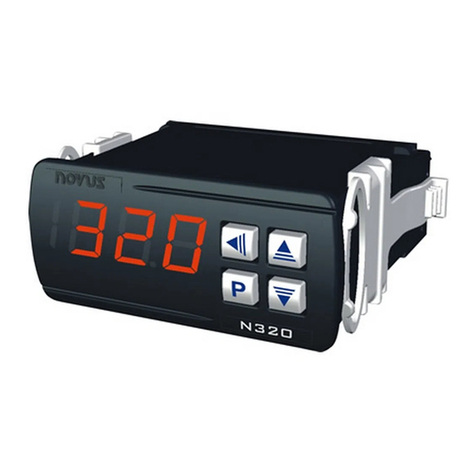
Novus
Novus N320 operating manual
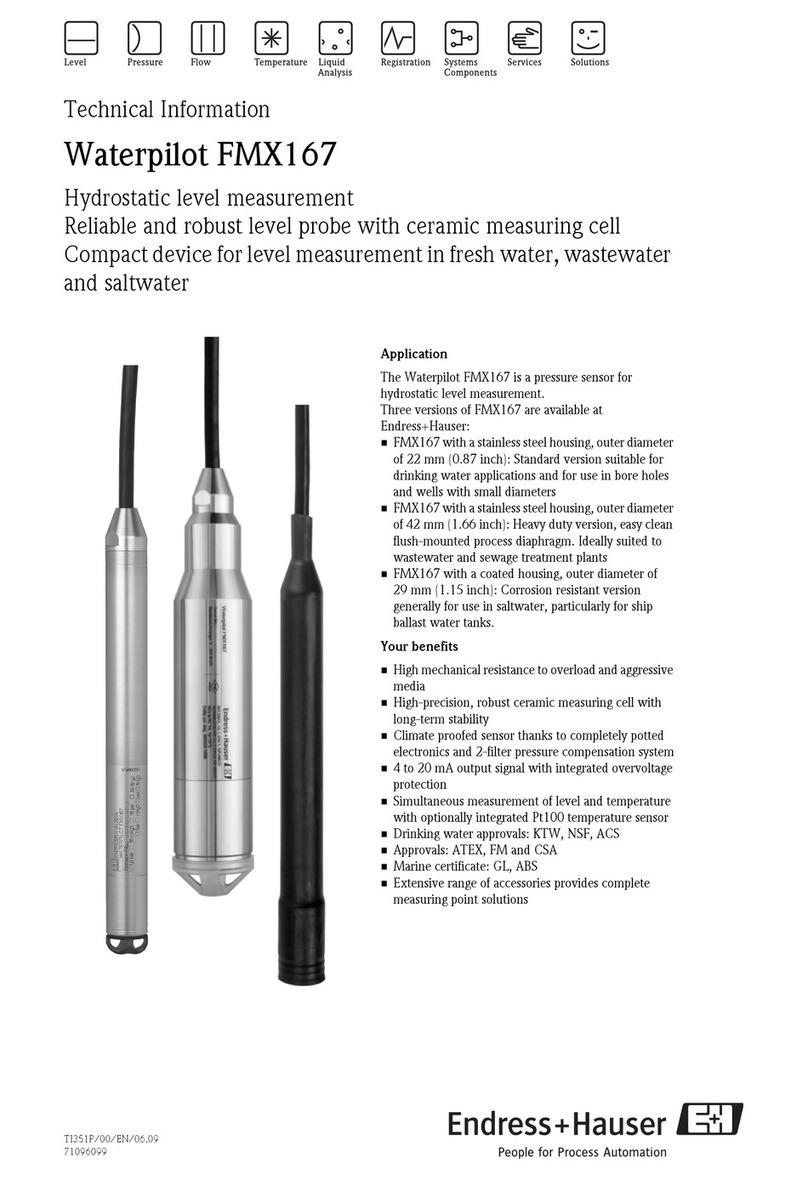
Endress+Hauser
Endress+Hauser Waterpilot FMX167 technical information
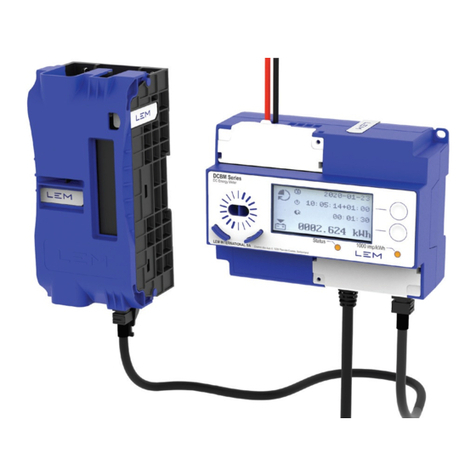
LEM
LEM DCBM Series installation manual
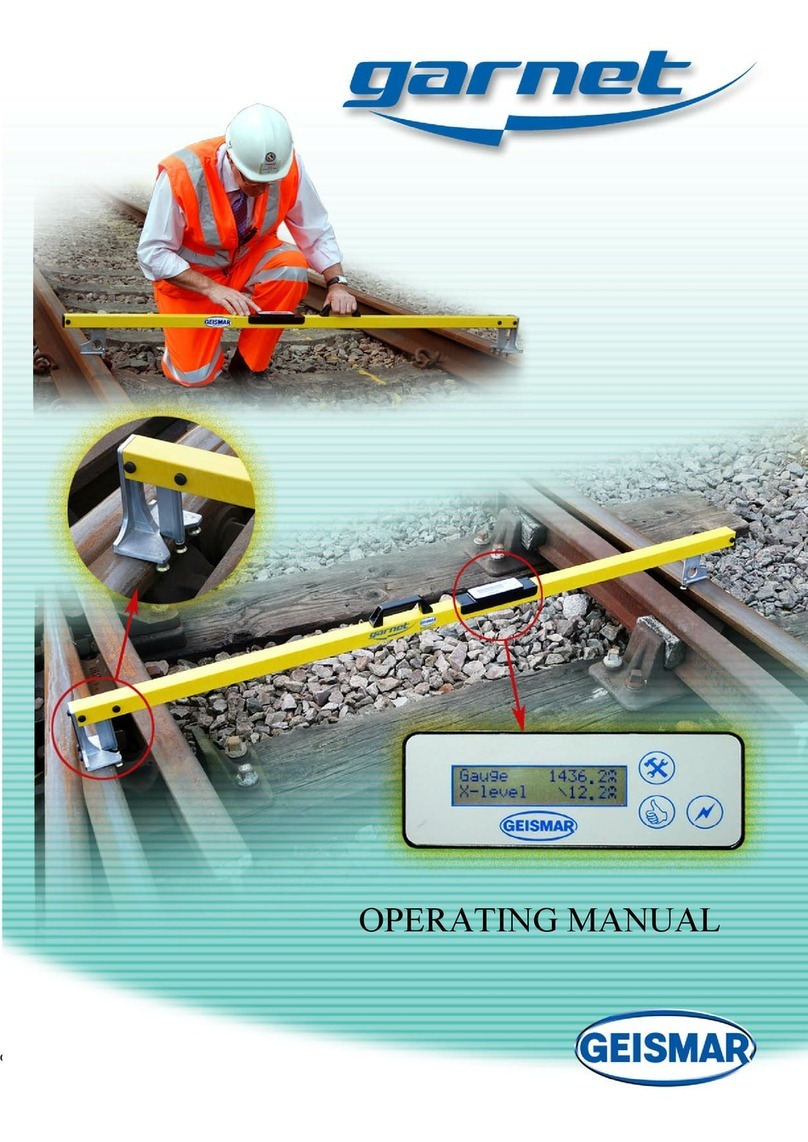
GEISMAR
GEISMAR Garnet P8 operating manual
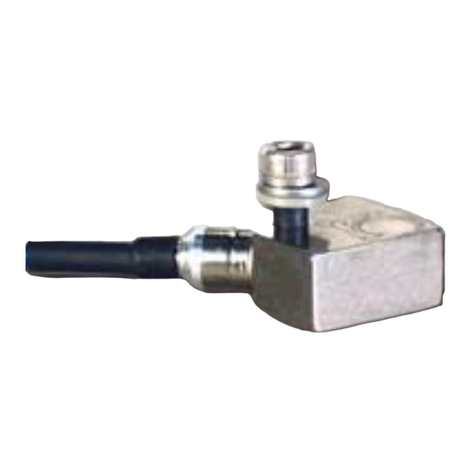
PCB Piezotronics
PCB Piezotronics 354C10 Installation and operating manual
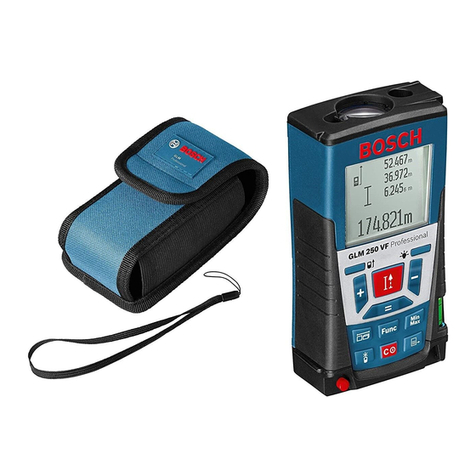
Bosch
Bosch GLM Professional 250 VF Original instructions
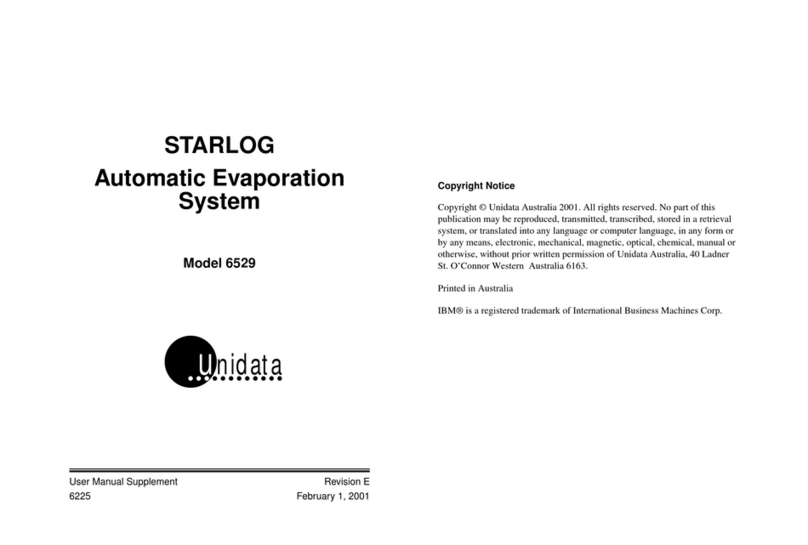
UniData Communication Systems
UniData Communication Systems STARLOG 6529 User's manual supplement
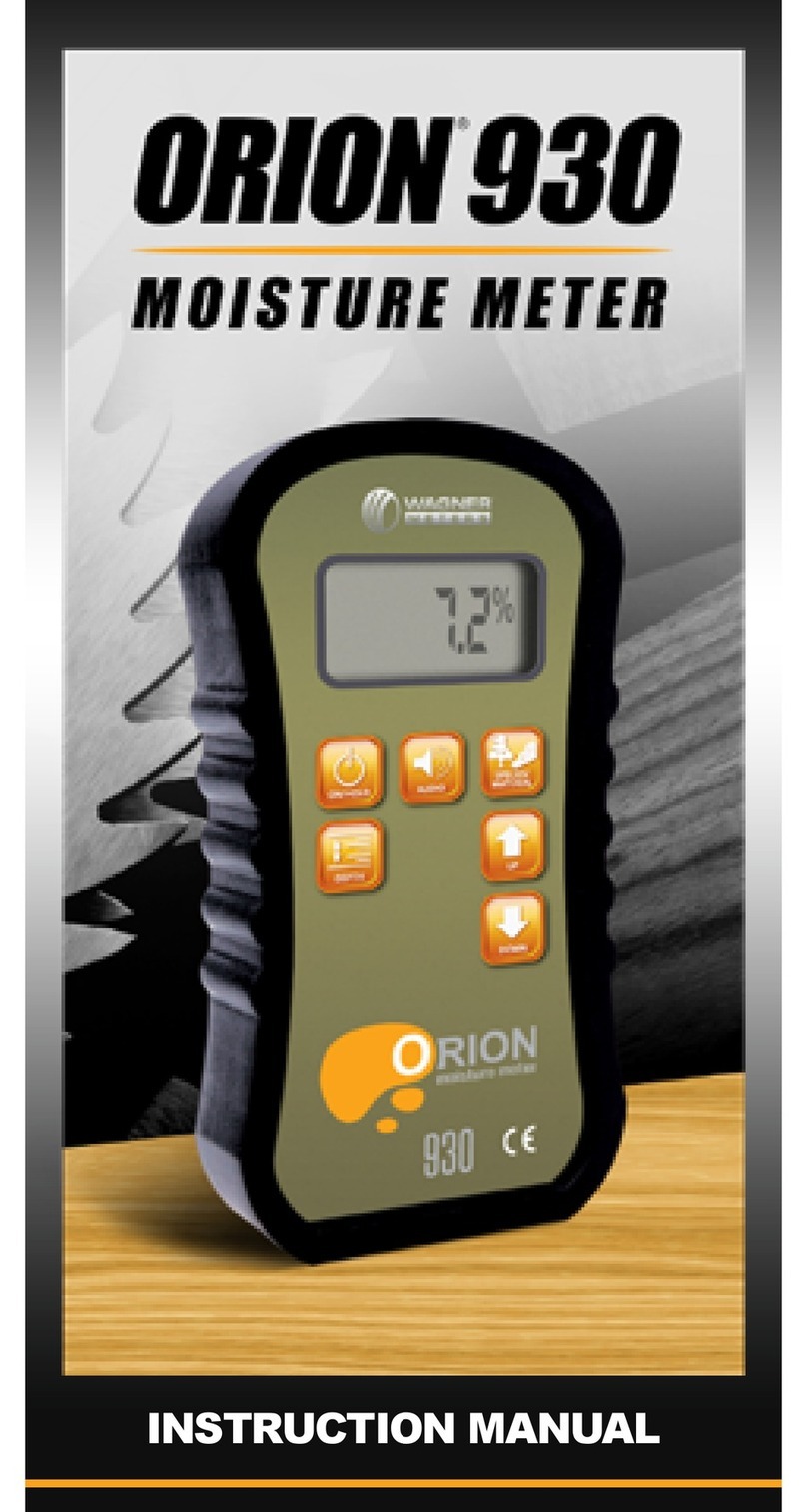
Wagner Meters
Wagner Meters Orion 930 instruction manual

Maxwell
Maxwell 25602 user manual
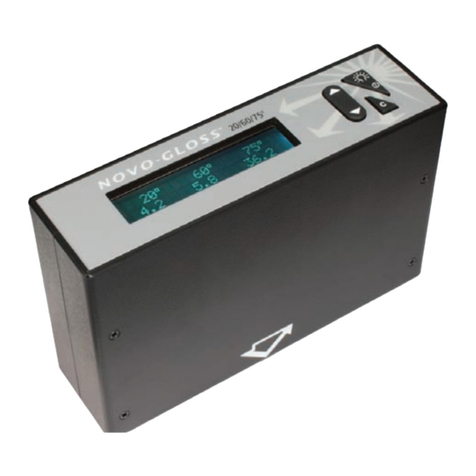
Rhopoint
Rhopoint Novo-Gloss 20/60/75 Operation manual