Teral NX-VFC User manual

TERAL INC.
Instruction Manual
Estimated Terminal Pressure
Constant Control of Water
Supply Unit
Thank you very much for purchasing the TERAL water supply unit.
In order to use the water supply unit appropriately, read this instruction manual
before using, and do not perform operation, maintenance and inspection before
understanding the description in this manual thoroughly.
For safety purpose, observe the cautions and warnings in this instruction manual
and those on the labels affixed on the water supply unit.
Keep this manual carefully at hand where it can be consulted at any time of
operation, maintenance and inspection of the water supply unit.
To whom performing utility work:
Be sure to submit this manual to the customer performing
operation, maintenance and inspection of the water supply unit.
Important Notice
Estimated Terminal Pressure Constant
Control of Water Supply Unit
NX-VFC/NX-VFC-e Multiple pump control

Limited warranties
1. In the event of failure or breakage under proper use of the product during the warranty period, equipment
supplied by Teral Inc. shall be repaired or replaced free of charge within the scope of the relevant part,
provided that such failure or breakage is attributable to inadequacy of the design or workmanship of the
equipment.
2. The warranty mentioned in the above clause shall be only the mechanical warranty of the defective part,
and shall not cover any expenses or other damage arising from the failure or breakage.
3. In the event of the following failures and breakage, the costs of the repairs and consumables (i.e. parts
whose consumption or wear is expected at the beginning of purchase) shall be borne by the user.
(1) Failures and breakage attributable to equipment that was not delivered by Teral Inc.
(2) Failures and breakage after the expiration of the warranty period
(3) Failures and breakage caused by disasters or force majeure, such as fire, acts of God or earthquakes
(4) Failures and breakage resulting from repairs, disassembly or modifications made without the consent
of Teral Inc.
(5) Failures and breakage when parts other than those designated by Teral Inc. are used
(6) Failures and breakage caused by any use outside the specification limit of the equipment
4. Teral Inc. shall not be liable for any damage caused by incorrect or reckless use of the water supply unit
even if such damage occurs within the warranty period. Cost and expenses incurred for sending engineer(s)
in such a case shall be borne by the user.
5. If the cause of the failure is unclear, necessary actions shall be determined through mutual consultation.
6. In order to improve performance, some parts and/or components of the product may be changed without
prior notice.
In addition, upon repairs of the product, Teral Inc may use recycled parts that conform to our quality
standards or may use substitutes that are functionally equivalent.
Purpose of this manual / Notice to users
1. The purpose of this manual is to provide the user with detailed information necessary to operate, maintain
and inspect the water supply unit (or “the unit”) properly.
This manual does not cover work that requires highly specialized knowledge (disassembly, repairs, etc.). If
the unit needs to be repaired, be sure to contact Teral Inc. or its relevant service company.
2. This manual is intended for:
xpersons experienced in the operation of water supply units, or those who have been trained by such
experienced operators
xqualified persons, such as licensed electrical engineers, for the content regarding electric wiring work
3. This manual mainly covers standard products. If you have purchased a customized product, some part of
this manual may not be applicable to your unit. In such a case, refer to other documents such as the
delivery specifications to confirm the product specifications.
4. The product specifications and information in this manual are subject to change without prior notice.
5. In the illustrations of this manual, some part of the product is omitted or simplified to make it easy to
understand. Therefore, the illustrations may look different from the actual product you use.

Contents
1. Safety precautions ············································································································1-1
1.1 Explanation of safety indications and graphic symbols························································1-1
1.2 Safety precautions······································································································1-1
2. Before using the water supply unit························································································2-1
2.1 Points to be checked···································································································2-1
2.2 Model type description·································································································2-1
3. Configuration and overview of the water supply unit ·································································3-1
3.1 Specifications of the water supply unit·············································································3-1
3.2 Names and functions of each part··················································································3-2
3.3 Specifications of control panel·······················································································3-6
3.4 Specification tables·····································································································3-7
4. Installation ······················································································································4-1
4.1 Precautions for installation ···························································································4-1
4.2 Precautions for piping work ··························································································4-2
4.3 Precautions for wiring work···························································································4-3
5. Preparation for operation····································································································5-1
5.1 Points to be checked before test operation·······································································5-1
5.2 Turning on the power ··································································································5-2
6. Test operation··················································································································6-2
6.1 Check items related to manual operation ·········································································6-2
6.2 Check items related to automatic operation······································································6-3
7. Basic operations and indications/settings···············································································7-1
7.1 Pump Operation·········································································································7-1
7.2 Selecting a receiver tank······························································································7-2
7.3 Selecting the operation of the inflow solenoid valve····························································7-3
7.4 Indications on the display ·····························································································7-4
7.5 Parameter settings ·····································································································7-7
8. Maintenance and inspection································································································8-1
8.1 Precautions for maintenance and inspection ····································································8-1
8.2 Inspection mode·········································································································8-2
8.3 Maintenance check list ································································································8-3
9. How to handle troubles ······································································································9-1
9.1 Alarm handling ··········································································································9-1
9.2 Troubleshooting ·········································································································9-2
10. Special specification····································································································· 10-1
10.1 Negative suction type ································································································ 10-1
10.2 Models with outdoor cover·························································································· 10-2

1-1
1. Safety precautions
Before using the unit, thoroughly read this “Safety precautions” to properly use the product. Information
described below is vital to safe and proper use of the unit and prevention of hazard and/or damage.
1.1 Explanation of safety indications and graphic symbols
This instruction manual divides safety indications into four categories according to the level of hazard (the
extent of damage/losses and the urgency). In addition, the type of user instructions is indicated with a
graphic symbol.
This manual uses the following signs. Fully understand these terms and symbols before reading this manual
further.
Explanation of the safety indications Explanation of the graphic symbols
Indications Meaning
Danger
Indicates an imminently hazardous
situation. Failure to observe this will result
in death or serious injury.
Don’ts Do not touch Do not
disassemble
Do not touch
with wet hand
Do not expose
to water
These graphic symbols indicate prohibited actions
(that must not be done).
Warning
Indicates a potentially hazardous
situation. Failure to observe this will result
in death or serious injury.
Do’s
This graphic symbol indicates mandatory actions
(that must be done).
Caution
Indicates a potentially hazardous
situation. Failure to observe this will result
in minor or moderate injury or property
damage. Caution Electric shock
hazard
Rotation
hazard
Hot surface
Note
Indicates information that is in particular
to be noted or emphasized.
These graphic symbols indicate existing hazards
to beware of.
1.2 Safety precautions
The following are important instructions about safety. Be sure to observe these precautions.
Danger
Once the main power is turned on, do not touch any live parts inside or outside the control panel.
A high voltage applied to live parts causes a serious electric shock.
Warning
Properly move the unit according to lifting
instructions.
Otherwise, the unit may fall, resulting in injury and/or
damage.
Do not carry out any work by/on the water supply
unit that is being lifted.
Otherwise, the unit may fall, resulting in injury and/or
damage.
Only those who are authorized by the site
manager may operate the water supply unit.
Operation by unskilled personnel may lead to an unforeseen
accident.
Only those who are trained to handle the water
supply unit may install, maintain, and inspect it.
Operation by unskilled personnel may lead to an unforeseen
accident.
Only qualified personnel, such as licensed
electrical engineers, are allowed to carry out any
electric work.
Otherwise, it may lead to an electric shock, fire, failures,
and/or other problems.
Use the wiring equipment and devices compliant
with the use conditions, and carry out wiring work
safely and securely according to the technical
standards for electrical facilities, as well as the
indoor wiring regulations.
Otherwise, it may lead to an electric shock, fire, and/or other
problems.
Before starting wiring work, be sure to turn off the
main power and confirm that the pilot lamp is
turned off. Take measures to prevent erroneous
power supply.
Otherwise, it may lead to an electric shock.
At the power supply source, be sure to install a
ground fault interrupter dedicated to this unit.
Otherwise, it may lead to an electric shock, fire, and/or other
problems.

1-2
Warning
Securely install the ground wire and ensure to
carry out grounding work.
Otherwise, it may lead to an electric leak and/or electric
shock.
Do not connect the ground wire to a gas pipe or
water pipe.
Such a connection is illegal and leads to an electric shock,
explosion and/or fire.
Ensure that all electric wires are securely
connected.
Otherwise, it may lead to fire and/or an electric shock.
Before starting the maintenance or inspection
work, be sure to stop the pump and turn off the
main power of the panel board.
Otherwise, it may lead to an electric shock, injury, damage,
water leakage, and/or other problems.
Before starting the unit or carrying out
maintenance/inspection work, ensure that all the
relevant workers are informed of the operation and
that there are no workers in the dangerous zone
around the unit.
Otherwise, it may lead to an unforeseen accident.
Before rotating the pump shaft by hand to check its
smooth rotation, be sure to disconnect the main
power supply.
Otherwise, it may lead to injury and/or damage.
After turning on the power, do not touch any parts
of the water supply unit other than those required
for operation.
Otherwise, it may lead to an electric shock, injury, and/or
other problems.
Ensure to keep the cover of the control panel
closed during operation.
Otherwise, it may lead to an electric shock, fire, and/or other
problems.
Do not put your fingers or foreign objects into any
openings or rotating part of the motor during
operation.
Otherwise, it may lead to injury and/or damage.
Do not perform shutoff operation for more than one
minute continuously.
Otherwise, the temperature and pressure will increase inside
the pump, which may damage the pump and/or cause steam
to blow off.
Do not operate the unit if abnormal condition is
observed in any actions and movement or in any
parts, components, and others.
Otherwise, it may lead to injury, failures and/or various
accidents.
If you need to carry out work that requires
disassembly of the unit—such as replacement of
parts, repairs, or inspection, ask the vendor or the
service center specified by Teral inc.
If unskilled personnel carry out the work that requires special
knowledge, it may lead to an accident and/or failures.
Caution
Do not use the unit outside the range of the
product specifications.
Otherwise, it may lead to an electric shock, fire, water
leakage, failures, and/or other problems.
Do not use the unit at the power voltage other than
the specification.
An incorrect voltage may damage the control panel.
Do not use a single unit as the only means of
directly operating key facilities or sustaining life.
In the event of a failure, the water supply may stop. Ensure
to make a backup unit readily available.
Do not use the unit to deliver pure water.
Otherwise, pure water may be contaminated with impurities.
Pay special attention to nails when opening the
delivered container.
Otherwise, it may lead to injury and/or damage.
As for the installation environment of the unit,
strictly observe the installation instructions.
Otherwise, it may lead to premature failure.
Ensure that the floor at the unit’s installation place
is waterproofed and fitted with drainage.
Otherwise, it may lead to serious damage in the event of
leakage.
Only after detaching a companion flange from
each pump, screw a pipe into it.
Otherwise, it may lead to damage or water leakage.
Do not merge suction pipes.
Otherwise, it may hinder the normal operation.
Do not use any piping materials that are prone to
rust.
Otherwise, it may damage the unit.
Do not install different or other cables or control
wires in one pipe or duct.
Otherwise, it may damage the unit and/or other equipment.
Provide a ground electrode dedicated to the inflow
solenoid valve.
Otherwise, it does not function normally.
Do not step on the control panel, pump, or pipes.
Otherwise, it may lead to injury, damage, and/or other
problems.
Try to prevent the control panel and the motor from
being sprayed water.
Otherwise, it may lead to an electric shock, electric leak,
failures, and/or other problems.

1-3
Caution
Implement each operation carefully.
Otherwise, it may lead to injury and/or damage.
Properly make each setting of the control panel
depending on the conditions of use.
Otherwise, it may hinder the normal operation.
Before operation, thoroughly clean (flush) the
inside of the piping.
Otherwise, the piping system may be contaminated with
foreign matter, thus leading to an accident or a pump failure.
Do not run the pump without priming.
Otherwise, it may damage the sliding parts inside the pump.
Do not perform automatic operation with the TJ
valve shut.
Otherwise, it may hinder the normal operation and damage
the unit.
Do not touch the motor body or the cooling fins for
the control panel while the unit is running or
immediately after the unit has stopped.
Otherwise, you may get burns from the hot surface.
Do not cover the motor or the control panel with
cloths or other objects.
Otherwise, it may lead to overheat and/or ignition.
Do not place anything on the water supply unit or
do not step on the unit.
Otherwise, it may lead to injury and/or damage.
In the event of an alarm or abnormal condition that
cannot be resolved, immediately contact Teral Inc.
or its service provider.
Otherwise, it may lead to an accident.
Ensure to carry out inspection according to the
maintenance checklist.
Otherwise, you cannot prevent potential failures, thus
leading to a higher risk of accidents.
Replace the packing and O-rings during inspection
involving disassembly.
Otherwise, it may lead to water leakage.
Before disassembling, shut the suction and
discharge sluice valves, and then discharge
pressured water from the pump and the piping.
Otherwise, water may spurt out, thus leading to an accident.
Do not perform an insulation resistance test on the
control panel. (Before performing an insulation
resistance test on the motor, disconnect electric
wires and cables from the control panel.)
Otherwise, it may damage the control panel.
If you do not use the unit for a long time, turn off
the power, drain water from the inside, and then
store the unit.
Otherwise, it may lead to insulation degradation, freeze
cracking, and/or other problems.
When the water supply unit is used outdoors, fit
the outdoor cover in the special accessories.
Failure to observe this may cause damage to the unit.
If negative suction is necessary, adopt the unit
specified for negative suction.
Failure to observe this may cause discharge pressure drop
and lead to a water cutoff.
Do not fit an advance phase capacitor to the
secondary wiring in the control panel.
Failure to observe this may damage the unit.
To operate the pump, close the bypass of the
check valve.
If not followed, the check valve will not function.

2-1
2. Before using the water supply unit
Caution
Make sure that the delivered package is placed right-side up before
unpacking. Pay special attention to nails especially when opening a
wooden crate or you may get injured.
Note
After unpacking, ask the vendor to dispose of packaging materials that
are no longer necessary.
2.1 Points to be checked
When you receive the water supply unit, check the following points immediately after unpacking.
(1) Check the nameplate to verify that the delivered product is exactly what you ordered.
(2) Check that no part of the unit has been damaged during transportation.
(3) Check all fastening parts including bolts and nuts are securely tightened.
(4) Check all the accessories that you ordered have been completely delivered.
2.2 Model type description
᳒Ყ᳐᳀ᲽᲧ Ყ᳟
ijĬĭĮįİı IJ
Ĭ0: 2WOR
ĭ 7PKVFKUEJCTIG PQOKPCNFKCOGVGT
Į'UVKOCVGFVGTOKPCNRTGUUWTGEQPUVCPVEQPVTQN
QHYCVGTUWRRN[WPKV
į2WOR
PQOKPCNFKCOGVGT
İ 0QQH
R
WO
R
UVC
I
G
ı 1WVRWV
IJ1RGTCVKQP
OQFG
ij/QVQT
GHHKEKGPE[
9:
6:
6:
(:
(:
):
0QPG
G
᳑:
RWOR2CTCNNGNRWOR4QVCVKQP
RWOR2CTCNNGNRWOR4QVCVKQP
RWOR2CTCNNGNRWOR4QVCVKQP
RWOR2CTCNNGNRWOR4QVCVKQP
RWOR2CTCNNGNRWOR4QVCVKQP
RWOR2CTCNNGNRWOR4QVCVKQP
5VCPFCTFGHHKEKGPF[+'GSWKXCNGPV
6QR4WPPGTGHHKEKGPE[+'GSWKXCNGPV
Indicated by 8-digits
alphanumeric
Control panel model
e.g. BQNXC-233-3.7/2
Indicated by 10-digits alphanumeric
Motor output
e.g. 3.7kW
Unit discharge bore
(mm)
Pump suction bore
(mm)
Unit model
e.g. NX-65VFC502-3.7WX3-e
Pump model
e.g. UNX502-3.7-e
Pump suction/discharge
bore (mm)
Pump rated current (A)
Indicated by 10-digits
alphanumeric
Motor bearing model
Unit nameplate
(Affixed to the base)
Pump nameplate
(Affixed to the motor)
Control panel nameplate
(Affixed to the control panel)
Fig. 2-1 Information inscribed on the nameplates
Indicated by 10-digits alphanumeric

3-1
3. Configuration and overview of the water supply unit
This chapter describes standard specifications of the water supply unit. If you have purchased a customized
product, some information in this chapter may not be applicable to your unit. Refer to the separately supplied
delivery specifications and other documents to check the product specifications in such a case.
3.1 Specifications of the water supply unit
Caution
Do not use this unit under any conditions other than those provided in
the specifications. Otherwise, electric shock, fire, water leakage, or
property damage may occur.
Note
If the inflow pump head is 5m or more, contact Teral for consultation.
Table 3-1 Standard specifications of water supply unit
Operation mode
WX3 : 2-pump Parallel, 3-pump Rotation
TX3 : 3-pump Parallel, 3-pump Rotation
TX4 : 3-pump Parallel, 4-pump Rotation
FX4 : 4-pump Parallel, 4-pump Rotation
FX5 : 4-pump Parallel, 5-pump Rotation
GX5 : 5-pump Parallel, 5-pump Rotation
Control method Estimated terminal pressure constant control / Discharge pressure constant control
by frequency control
Applicable
liquid
Liquid
property Fresh water
Temperature 0 to 40°C
Installation location Indoors (0 to 40°C, Max. RH85%, no condensation), Altitude: Max. 1,000m
Suction conditions Inflow (Inflow pump head: Max. 5 m)*
Pump
(Material)
NX model stainless steel horizontal multistage centrifugal pump
(Impeller: SUS304, Casing: SCS13, Main shaft: SUS304)
Motor
Type Totall
y
-enclosed fan-cooled type for indoor use
Protection
class IP44
Number of
poles 2 poles
Flange Suction:Dedicated companion flange, Discharge: JIS Flange
Power supply 1.1 to 7.5 kW: 3-phase 200/200-220 V (50/60 Hz)
Paint color Common base: Munsell N-5
Pressure tank: Munsell 10Y5.5/0.5
Pressure tank Model DPT20 (20L diaphragm tank)
Pressure detection device Pressure transmitte
r
: Transmission system: 5 VDC, 3-wire system
Output voltage: 0.5 to 3.5 V DC
Control
panel
Model BQNXC type
Motor
Protection Inverter (with electronic thermal protection)
Normal
indications
Indicator lamp:
Power supply, Pump operation (per pump), Pump operation inhibition (per pump), Failure (all)
Other indications:
Discharge pressure, Voltage, Current (per pump), Operating frequency (per pump), Cumulative
operation time (per pump), Cumulative number of starts (per pump), Number of start times of the
unit on the previous day, Alarm log (last 5 alarms)
Alarm
indications
Receiver tank full, Receiver tank low, Dry-run prevention, Electrode failure, Start frequency failure,
Pressure transmitter 1 failure, Control panel high temperature, EEPROM error, Overload (per
pump), Discharge pressure abnormal drop (per pump), Electric leak (per pump), High temperature
(per pump), Flow switch failure (per pump), Overcurrent (per pump), Overvoltage (per pump),
Stall prevention (per pump), Inverter overload (per pump), Open-phase output (per pump), Inverter
overheat (f per pump), Communication failure (per pump), Inverter trouble 1 (per pump), Inverter
trouble 2 (per pump)
External
outputs
Powe
r
supply for alarm (at power voltage), Inflow solenoid valve output (at power voltage),
Operation/alarm signal (No-voltage a-contact)
External
inputs External stop signal (interlock): supports a/b-contacts
*The negative suction models support up to 4 m in the actual pump head and up to 6 m in the total pump head (at 20°C water
temperature).
*If a flush valve or the like is used, a sudden pressure drop may occur, thus leading to the problems such as insufficient water
supply, noise, premature damage of the pressure tank, or others. Contact us for such cases.

3-2
3.2 Names and functions of each part
3.2.1 Names and functions of the components of the water supply unit
䐟Control panel
The control panel controls the pump and supplies the power to the motor.
It enables to start/stop the pump, detects the operating status of the pump and automatically switch the No.
of the pump to run.
Also it enables pump variable speed control by a pressure transmitter signal and thereby estimated
terminal pressure constant control is conducted.
䐠Pump
Its motor rotates an impeller to generate pressure for delivering water.
䐡Pressure transmitter
The pressure transmitter converts pressure into an electric signal so as to use it for control.
䐢Pressure tank
The pressure tank maintains the pressure in the piping and reduces the number of start/stop and pressure
fluctuations of the pump.
䐣Junction pipe
The junction pipe joins the discharge pipes of the two pumps into one pipe.
䐤Discharge elbow
The discharge elbow has a built-in cushion check valve and is equipped with the flow switch㻌䐦
. Inside the
elbow, a bypass is provided so as to make the water reverse-flow during maintenance by opening.
䐥Gate valve
The gate valve is used for maintenance and is provided for each pump.
䐦Flow switch
The flow switch outputs a signal to stop the pump when the water flow rate is not higher than the setup
(stop) flow rate.
䐧High temperature sensor
If the water temperature is not lower than the setup temperature due to zero-discharge operation, the high
temperature sensor outputs a signal to stop the pump.
䐨Priming plug
This plug is used to prime the pump.
䐩TJ valve
This is a three-way valve used to discharge water from the pressure tank when you carry out the
maintenance of the pressure tank and the pressure transmitter.
䐪Air vent plug of pump
This plug is used to release air from the pump.
䐫Pump drain
This drain is used to discharge water from the pump.
1
23
4
5
67
9
10
8
11
1312
Fig.3-2-1 NX-VFC-e Multiple pump control water supply unit
(This figure shows for 3 pumps unit)

3-3
3.2.2 Names and functions of control panel elements
ձDisplay
It displays a variety of information
about the water supply unit. (ĺsee
7.4)
ղOperation selector switch
The switch is to change the
operation mode of the water supply
unit. (ĺsee 7.1)
ճCurrent mode indicator lamp
The lamp is to display the operation
mode currently selected.
մTank selector switch
Press this switch to select the
receiver tank(s) to be used. (ĺsee
7.2)
յCurrent tank indicator lamp
The indicator lamp will be on for the
receiver tank currently selected.
նSolenoid valve operation selector
switch
Press this switch to change the
solenoid valve operation mode. (ĺ
see7.3)
շCurrent solenoid valve operation indicator lamp
The indicator lamp will be on for the solenoid valve operation currently selected.
ոOperation indicator lamp
The indicator lamp will be on while the pump is running. The lamp blinks during checking for low flowrate in
automatic mode.
չOperation inhibition indicator lamp (per pump)
The indicator lamp will be on when the operation parameter is set to “Operation inhibition” mode.
(ĺsee 7.5)
պPower indicator lamp
The indicator lamp will be on while the power is turned ON. It blinks in inspection mode (ĺsee 8.2).
ջFailure indicator lamp
The indicator lamp blinks when an alarm occurs.
ռNo. 1 Manual/Confirm switch
Press the switch to run the pump No.1 in the manual mode. The switch is also used as the “Confirm” switch
in the setting and other modes.
սNo.2 Manual/Back switch
Press the switch to run the pump No.2 in the manual mode. The switch is also used as the “Back” switch in
the setting and other modes.
վManual switch (No. 3 to 5)
The switch is to manually operate the pumps No. 3 to 5.
տReset switch
The switch is used to reset an alarm.
Generated alarms can be reset by pressing the switch once the cause of the alarm is eliminated.
րBuzzer stop switch
The switch is used to manually stop the buzzer when an alarm occurs. The switch is also used in
combination with the cursor switch 1 to switch the basic information items on the display.
ցSetting switch
The switch is used to switch to or to exit from the setting mode (ĺsee 7.5).
ւCursor switch 1
The operating frequency can be changed by pressing the switch in the manual mode of Pump no.1.
The switch is used to switch the indication items, make the settings, and switch the indication items of the
pump No.1.
փCursor switch (No. 2 to 5)
The operating frequency can be changed by pressing this switch in the manual mode of the pumps No.2 to
5. The switch is used to switch the indication items of the pump No.2 to 5.
#1
Manual
Reset
Buzzer
stop
Setting
ššššššššššš
Confirm
#2
Manual
$CEM
#1 operation
#1 Block
#2 operation
#2 Block
Power
Failure
Manual Stop Auto
No.1 No.2
Man.
Open
Man.
Close Auto
Com
mon
#3 operation
#3 Block
#4 operation
#4 Block
#5 operation
#5 Block
#3
Manual
#4
Manual
#5
Manual
12
3
4
5
7 6 18
1312
11
10
17
16
15
8
9
19
14
Operation
selector
Tank
selector
Solenoid
valve
operation
selector
Fig.3-2-2 Operation panel on the control panel
(This figure shows for 5 pumps unit)

3-4
3.2.3 Configuration of the control panel
Warning
While the power is on, high voltage is applied inside the control panel,
which is very dangerous. Any person other than the one authorized to
do so must not open cover of the control panel. if not followed, it may
cause an electric shock.
(1) Components
&%4
ᲢښᲣ
&%4
ᲢښᲣ
&%4
ᲢښᲣ
&%4
ᲢښᲣ
&%4
ᲢښᲣ Сࣂؕெ
+08 +08 +08 +08 +08
'.%$ '.%$ '.%$ '.%$ '.%$
6$
Ტ᩿Უ
40( 40( 40( 40( 40(
ŠᚡӭƷᛟଢ
6$ ᩓเᇢ܇Ө
+08 ǤȳȐȸǿ
'.%$ ᩓȖȬȸǫ
&%4 щྙોծȪǢǯȈȫǪȗǷȧȳ
40( ȩǸǪȎǤǺȕǣȫǿ
СࣂႴƷನᢿԼ
ᲢƸȝȳȗӨૠӨƷȦȋȃȈƷNjƷưƢᲣ
DCR5
(Back side)
DCR4
(Back side)
DCR3
(Back side)
DCR2
(Back side)
DCR1
(Back side)
TB1
(Side wall)
Control
board
䕔Description of Codes
TB1 Power terminal
INV1,2,3,4,5 Inverter
ELCB1,2,3,4,5 Earth leakage
DCR1,2,3,4,5 Power-factor improvement reactor (option)
RNF1,2,3,4,5 Radio noise filter
Fig 3-2-3 Control panel components
(This figure shows for 5 pumps unit)

3-5
3.2.4 Control board
The following are the details of the control board.
Warning
Do not remove the protective cover on the control board or the cover of
the I/O terminal block when the power is turned on.
Otherwise, it may lead to an electric shock.
Table 3-2-4 (a) Connector assignments
No. Connection point No. Connection point No. Connection point
CN1
Equipment inside the control panel
CN11
Flow switch for pump No. 4
CN21
Equipment inside the control panel
CN2
Equipment inside the control panel
CN12
Flow switch for pump No. 5
CN22
Equipment inside the control panel
CN3
Equipment inside the control panel
CN13
(Unused)
CN23
Equipment inside the control panel
CN4
Equipment inside the control panel
CN14
(Unused)
CN24
Equipment inside the control panel
CN5
Equipment inside the control panel
CN15
(Unused)
CN25
Equipment inside the control panel
CN6
Control panel high-temperature
sensor
*1
CN16 High temperature sensor No. 1 CN26
Equipment inside the control panel
CN7 Pressure transmitter
CN17 High temperature sensor No. 2 CN27
(Unused)
CN8 Flow switch for pump No. 1
CN18 High temperature sensor No. 3 CN29
Equipment inside the control panel
CN9 Flow switch for pump No. 2
CN19 High temperature sensor No. 4
CN10
Flow switch for pump No. 3
CN20 High temperature sensor No. 5
*1 For models fitted with outdoor cover, this sensor is connected depending on the specifications.
Table 3-2-4 (b) Codes and application of input/output terminal block
Code Application Code Application
IL1 and IL2
Interlocking signal B1 to B8 Alarm signal output
1E0 to 1E4
Receiver tank water level detector electrode No. 1
BC Alarm signal output common
2E0 to 2E4
Receiver tank water level detector electrode No. 2 VR and VT
Power supply for alarm (200V)
1N1 and 1N2
Receiver tank solenoid valve control
electrode No.1
RH and TH
(Unused)
2N1 and 2N2
Receiver tank solenoid valve control
electrode No.2
SVC and SV1
Receiver tank solenoid valve No. 1
(200V)
M1 to M5 Pumps No. 1 to pump No. 5 operation
signal
SVC and SV2
Receiver tank solenoid valve No. 2
(200V)
MC Operation signal common
㻌
㻌
㻌
㻌
㻌
㻌
㻌
㻌
㻌
㻌
㻌
㻌
㻌
㻌
㻌
㻌
㻌
Fig.3-2-4 Control Board Arrangement
I/O terminal block
TH
RH
SV1
SVC
SV2
SVC
VR
VT
M5
M4
M3
M2
M1
MC
B8
B7
B6
B5
B4
B3
B2
B1
BC
2N2
2N1
2E4
2E3
2E2
2E1
2E0
1N2
1N1
1E4
1E3
1E2
1E1
1E0
IL2
IL1
Operating power switch
Operating
power
switch
OFF
ON
CN1
CN2
CN10
CN9
CN8
CN7
CN6
CN5
CN4
CN3
CN21
CN15
CN20
CN19
CN18
CN17
CN16
CN14
CN13
CN12
CN11
CN22 CN23 CN24 CN25
CN26
CN27
CN29
Output terminal block

3-6
3.3 Specifications of control panel
Table 3-3 Specifications of control panel
Item Specifications 1 Specifications 2
Control panel model BQNXC
Operation mode Automatic rotational operation
(WX3/TX3/TX4/FX4/FX5/GX5)
Material and external color of casing Steel plate (Munsell 5Y7/1 semigloss/baking finish)
Output range Three-phase 200/200-220 V (50/60 Hz) 1.1 to 7.5 kW
Circuit
configuration
Ground fault interrupter Individual pump systems S
Power-factor correcting reactor (DCR) Individual pump systems 㸫S
Motor protection 㸫Inverter (electronic thermal protection)
Double receiver tank circuit Can be switched on the operation panel S
Inflow solenoid valve circuit Can be operated on the operation panel S
Electrode 5P circuit 㸫S
Functions
Dry-run prevention 㸫S
Automatic switching upon failure 㸫S
Pump continuous operation prevention function 㸫S
Pump operation time equalization function 㸫S
External stop signal (interlock) available a/b-contact available S
Buzzer stop timer setting 1 to 60 min, , no buzzer S
Full/low water alarm automatic recovery setting 㸫S
Inflow solenoid valve automatic alternation setting 㸫S
Inspection mode 㸫S
Alarm buzzer 㸫S
Buzzer stop switch 㸫S
Energy-saving operation setting 㸫S(for the products equipped with a Top runner motor)
Indications on control panel
Indicat
o
r lamp
Power 㸫S
Operation (per pump) 㸫S
Inhibition (per pump) 㸫S
Failure (collective) 㸫S
Various indications
Discharge pressure Unit: mH2O S
Power voltage Unit: V S
Operation current (per pump) Unit: 0.1 A S
Operation frequency (per pump) Unit: 0.1 Hz (only automatic) S
Cumulative operation time (per pump) Unit: Hour S
Cumulative number of starts (per pump) Unit: times S
Number of start times of the unit Number of starts on the previous day S
Alarm log 5 latest alarms S
Interlocking in operation 㸫S
Alarm indications
Receiver tank full No: E001 S
Receiver tank low No: E002 S
Dry-run prevention No: E003 S
Electrode failure No: E004 S
Start frequency failure No: E006 S
Pressure transmitter 1 failure No: E051 S
Control panel high temperature No: E070 O
EEPROM error No: E080 S
Overload (per pump) No: E#01 S
Discharge pressure abnormal drop (per pump) No: E#02 S
Electric leak (per pump) No: E#03 S
High temperature (per pump) No: E#04 S
Flow switch failure (per pump) No: E#05 S
Overcurrent (per pump) No: E#11 S
Overvoltage (per pump) No: E#12 S
Stall prevention (per pump) No: E#14 S
Inverter overload (per pump) No: E#15 S
Open-phase output (per pump) No: E#16 S
Inverter overheat (per pump) No: E#17 S
Inverter communication failure (per pump) No: E#18 S
Inverter trouble 1 (per pump) No: E#19 S
Inverter trouble 2 (per pump) No: E#20 S
External
output
Power for alarm Power voltage S
Inflow solenoid valve output Power voltage S (Open/closed selectable when the power is supplied)
Operation signal No-voltage a-contact S (per pump)
Fault signal No-voltage a-contact S (5 points: patterns 0 to 4)
“S” indicates standard features, and “O” indicates optional features.
*1 Power voltage and operation current values are estimated values. There is an error of approximately 10% with
respect to the full scale.
*2 “E006” and “E#04” can be disabled using settings. Refer to “7.5 Parameter setting.”
*3 The character “#” is replaced by the corresponding pump number.
*4 The open-phase output error is detected by only the units with the rated output of 5.5 kW or more.
*5 For the fault signal external output pattern, refer to “7.5 Parameter setting.”
*6 Energy-saving operatin setting is available only for the products equipped with a Top runner efficiency motor (IE3
equivalent).

3-7
3.4 Specification tables
3.4.1 Standard models (positive suction type)
Table 3-4-1 Specification list (positive suction type)
Suction
condition
Operation
method
Nominal dia. mm
Type Output
kW
Phase/
Voltage
V
Standard specification Spec. range Charged
pressure in
pressure tank
MPa(kgf/cm2)
Pump
suction
Unit
discharge
Max. water
supply
amount
m3/min
Total pump
head
m
Min. pump
head
m
Stop pressure
(rough value)
MPa(kgf/cm2)
Water supply
amount
m3/min
Discharge
pump head
range
m
positive suction type
2-pump Parallel, 3-pump Rotation
40
65
NX-65VFC401-1.1W x 3-e 1.1
3-phase䡡
200
(50Hz)
3-phase
200/220
(60Hz)
0.4 18 15 0.20 (2.0) 0.04 to 0.48 15 to 25 0.13 (1.3)
NX-65VFC402-1.5W x 3-e 1.5 0.4 28 24 0.28 (2.9) 0.04 to 0.54 21 to 35 0.18 (1.8)
NX-65VFC402-2.2W x 3-e 2.2 0.4 40 34 0.39 (4.0) 0.04 to 0.54 30 to 51 0.25 (2.6)
NX-65VFC402-3.7W x 3-e 3.7 0.4 56 48 0.55 (5.6) 0.04 to 0.60 37 to 64 0.31 (3.2)
NX-65VFC403-3.7W x 3-e 3.7 0.4 64 54 0.63 (6.4) 0.04 to 0.60 45 to 79 0.39 (4.0)
NX-65VFC403-5.5W x 3-e 5.5 0.4 77 65 0.76 (7.7) 0.04 to 0.60 50 to 90 0.44 (4.5)
50
NX-65VFC502-2.2W x 3-e 2.2 0.6 25 21 0.25 (2.6) 0.04 to 0.74 18 to 30 0.16 (1.6)
NX-65VFC502-3.7W x 3-e 3.7 0.6 47 40 0.46 (4.7) 0.04 to 0.87 30 to 52 0.25 (2.6)
NX-65VFC503-5.5W x 3-e 5.5 0.6 64 54 0.63 (6.4) 0.04 to 0.87 41 to 71 0.35 (3.6)
NX-65VFC503-7.5W x 3-e 7.5 0.6 74 63 0.73 (7.4) 0.04 to 0.90 50 to 90 0.44 (4.5)
65 80
NX-80VFC652-3.7W x 3-e 3.7 1.0 22 19 0.24 (2.4) 0.04 to 1.11 18 to 30 0.15 (1.5)
NX-80VFC652-5.5W x 3-e 5.5 1.0 35 30 0.34 (3.5) 0.04 to 1.22 25 to 42 0.22 (2.2)
NX-80VFC653-7.5W x 3-e 7.5 1.0 51 43 0.50 (5.1) 0.04 to 1.15 41 to 71 0.35 (3.6)
3-pump Parallel, 3 (4) -pump Rotation
40 80
NX-80VFC401-1.1T x 3(4) –e 1.1
3-phase䡡
200
(50Hz)
3-phase
200/220
(60Hz)
0.6 18 15 0.20 (2.0) 0.06 to 0.72 15 to 25 0.13 (1.3)
NX-80VFC402-1.5T x 3(4) –e 1.5 0.6 28 24 0.28 (2.9) 0.06 to 0.81 21 to 35 0.18 (1.8)
NX-80VFC402-2.2T x 3(4) –e 2.2 0.6 40 34 0.39 (4.0) 0.06 to 0.82 30 to 51 0.25 (2.6)
NX-80VFC402-3.7T x 3(4) –e 3.7 0.6 56 48 0.55 (5.6) 0.06 to 0.90 37 to 64 0.31 (3.2)
NX-80VFC403-3.7T x 3(4) –e 3.7 0.6 64 54 0.63 (6.4) 0.06 to 0.90 45 to 79 0.39 (4.0)
NX-80VFC403-5.5T x 3(4) –e 5.5 0.6 77 65 0.76 (7.7) 0.06 to 0.90 50 to 90 0.44 (4.5)
50 100
NX-100VFC502-2.2T x 3(4) –e 2.2 0.9 25 21 0.25 (2.6) 0.06 to 1.10 18 to 30 0.16 (1.6)
NX-100VFC502-3.7T x 3(4) –e 3.7 0.9 47 40 0.46 (4.7) 0.06 to 1.30 30 to 52 0.25 (2.6)
NX-100VFC503-5.5T x 3(4) –e 5.5 0.9 64 54 0.63 (6.4) 0.06 to 1.30 41 to 71 0.35 (3.6)
NX-100VFC503-7.5T x 3(4) –e 7.5 0.9 74 63 0.73 (7.4) 0.06 to 1.35 50 to 90 0.44 (4.5)
65 125
NX-125VFC652-3.7T x 3(4) –e 3.7 1.5 22 19 0.24 (2.4) 0.06 to 1.66 18 to 30 0.15 (1.5)
NX-125VFC652-5.5T x 3(4) –e 5.5 1.5 35 30 0.34 (3.5) 0.06 to 1.83 25 to42 0.22 (2.2)
NX-125VFC653-7.5T x 3(4) –e 7.5 1.5 51 43 0.50 (5.1) 0.06 to 1.72 41 to 71 0.35 (3.6)
4-pump Parallel, 4 (5) -pump Rotation
40 80
NX-80VFC401-1.1F x 4(5) –e 1.1
3-phase䡡
200
(50Hz)
3-phase
200/220
(60Hz)
0.8 18 15 0.20 (2.0) 0.08 to 0.97 15 to 25 0.13 (1.3)
NX-80VFC402-1.5F x 4(5) –e 1.5 0.8 28 24 0.28 (2.9) 0.08 to 1.08 21 to 35 0.18 (1.8)
NX-80VFC402-2.2F x 4(5) –e 2.2 0.8 40 34 0.39 (4.0) 0.08 to 1.10 30 to 51 0.25 (2.6)
NX-80VFC402-3.7F x 4(5) –e 3.7 0.8 56 48 0.55 (5.6) 0.08 to 1.20 37 to 64 0.31 (3.2)
NX-80VFC403-3.7F x 4(5) –e 3.7 0.8 64 54 0.63 (6.4) 0.08 to 1.20 45 to 79 0.39 (4.0)
NX-80VFC403-5.5F x 4(5) –e 5.5 0.8 77 65 0.76 (7.7) 0.08 to 1.20 50 to 90 0.44 (4.5)
50 100
NX-100VFC502-2.2F x 4(5) –e 2.2 1.2 25 21 0.25 (2.6) 0.08 to1.47 18 to 30 0.16 (1.6)
NX-100VFC502-3.7F x 4(5) –e 3.7 1.2 47 40 0.46 (4.7) 0.08 to 1.74 30 to 52 0.25 (2.6)
NX-100VFC503-5.5F x 4(5) –e 5.5 1.2 64 54 0.63 (6.4) 0.08 to 1.74 41 to 71 0.35 (3.6)
NX-100VFC503-7.5F x 4(5) –e 7.5 1.2 74 63 0.73 (7.4) 0.08 to 1.80 50 to 90 0.44 (4.5)
65 125
NX-125VFC652-3.7F x 4(5) –e 3.7 2.0 22 19 0.24 (2.4) 0.08 to 2.22 18 to 30 0.15 (1.5)
NX-125VFC652-5.5F x 4(5) –e 5.5 2.0 35 30 0.34 (3.5) 0.08 to 2.43 25 to 42 0.22 (2.2)
NX-125VFC653-7.5F x 4(5) –e 7.5 2.0 51 43 0.50 (5.1) 0.08 to 2.30 41 to 71 0.35 (3.6)
5-pump Parallel, 5-pump Rotation
40 100
NX-100VFC401-1.1G x 5-e 1.1
3-phase䡡
200
(50Hz)
3-phase
200/220
(60Hz)
1.0 18 15 0.20 (2.0) 0.10 to 1.21 15 to 25 0.13 (1.3)
NX-100VFC402-1.5G x 5-e 1.5 1.0 28 24 0.28 (2.9) 0.10 to 1.35 21 to 35 0.18 (1.8)
NX-100VFC402-2.2G x 5–e 2.2 1.0 40 34 0.39 (4.0) 0.10 to 1.36 30 to 51 0.25 (2.6)
NX-100VFC402-3.7G x 5–e 3.7 1.0 56 48 0.55 (5.6) 0.10 to 1.50 37 to 64 0.31 (3.2)
NX-100VFC403-3.7G x 5–e 3.7 1.0 64 54 0.63 (6.4) 0.10 to 1.50 45 to 79 0.39 (4.0)
NX-100VFC403-5.5G x 5–e 5.5 1.0 77 65 0.76 (7.7) 0.10 to 1.50 50 to 90 0.44 (4.5)
50 125
NX-125VFC502-2.2G x 5–e 2.2 1.5 25 21 0.25 (2.6) 0.10 to 1.84 18 to 30 0.16 (1.6)
NX-125VFC502-3.7G x 5–e 3.7 1.5 47 40 0.46 (4.7) 0.10 to 2.18 30 to 52 0.25 (2.6)
NX-125VFC503-5.5G x 5–e 5.5 1.5 64 54 0.63 (6.4) 0.10 to 2.17 41 to 71 0.35 (3.6)
NX-125VFC503-7.5G x 5–e 7.5 1.5 74 63 0.73 (7.4) 0.10 to 2.25 50 to 90 0.44 (4.5)
65 150
NX-150VFC652-3.7G x 5–e 3.7 2.5 22 19 0.24 (2.4) 0.10 to 2.78 18 to 30 0.15 (1.5)
NX-150VFC652-5.5G x 5–e 5.5 2.5 35 30 0.34 (3.5) 0.10 to 3.04 25 to 42 0.22 (2.2)
NX-150VFC653-7.5G x 5–e 7.5 2.5 51 43 0.50 (5.1) 0.10 to 2.88 41 to 71 0.35 (3.6)
*Above specifications also apply to standard models without “-e” at the end of the model.

3-8
3.4.2 Special models (negative suction type)
Table 3-4-2 Specification list (negative suction type)
Suction
condition
Operation
method
Nominal dia. mm
Type
Output
kW
Phase/
Voltage
V
Standard specification Spec. range Charged
pressure in
pressure tank
MPa(kgf/cm2)
Pump
suction
Unit
discharge
Max. water
supply
amount
m3/min
Total pump
head
m
Min. pump
head
m
Stop pressure
(rough value)
MPa(kgf/cm2)
Water supply
amount
m3/min
Discharge
pump head
range
m
negative suction type
2-pump Parallel, 3-pump Rotation
40
65
NX-65VFC401-1.1W x 3-e 1.1
3-phase䡡
200
(50Hz)
3-phase
200/220
(60Hz)
0.4 18 15 0.23 (2.3) 0.04 to 0.55 12 to 25 0.10 (1.0)
NX-65VFC402-1.5W x 3-e 1.5 0.4 27 23 0.32 (3.3) 0.04 to 0.55 19 to 37 0.16 (1.6)
NX-65VFC402-2.2W x 3-e 2.2 0.4 39 33 0.46 (4.7) 0.04 to 0.55 28 to 54 0.25 (2.5)
NX-65VFC402-3.7W x 3-e 3.7 0.4 55 47 0.54 (5.5) 0.04 to 0.60 34 to 63 0.29 (3.0)
NX-65VFC403-3.7W x 3-e 3.7 0.4 63 54 0.67 (6.8) 0.04 to 0.60 42 to 79 0.36 (3.7)
NX-65VFC403-5.5W x 3-e 5.5 0.4 76 65 0.74 (7.6) 0.04 to 0.60 47 to 88 0.41 (4.2)
50
NX-65VFC502-2.2W x 3-e 2.2 0.6 24 20 0.27 (2.8) 0.04 to 0.78 15 to 30 0.13 (1.3)
NX-65VFC502-3.7W x 3-e 3.7 0.6 46 39 0.46 (4.7) 0.04 to 0.88 28 to 54 0.25 (2.5)
NX-65VFC503-5.5W x 3-e 5.5 0.6 63 54 0.63 (6.4) 0.04 to 0.88 39 to 73 0.34 (3.5)
NX-65VFC503-7.5W x 3-e 7.5 0.6 73 62 0.74 (7.6) 0.04 to 0.93 47 to 88 0.41 (4.2)
65 80
NX-80VFC652-3.7W x 3-e 3.7 1.0 21 18 0.28 (2.9) 0.04 to 1.15 16 to 31 0.14 (1.4)
NX-80VFC652-5.5W x 3-e 5.5 1.0 34 29 0.41 (4.2) 0.04 to 1.19 25 to 48 0.22 (2.2)
NX-80VFC653-7.5W x 3-e 7.5 1.0 50 43 0.65 (6.6) 0.04 to 1.13 41 to 77 0.35 (3.6)
3-pump Parallel, 3 (4) -pump Rotation
40 80
NX-80VFC401-1.1T x 3(4) –e 1.1
3-phase䡡
200
(50Hz)
3-phase
200/220
(60Hz)
0.6 18 15 0.23 (2.3) 0.06 to 0.83 12 to 25 0.10 (1.0)
NX-80VFC402-1.5T x 3(4) –e 1.5 0.6 27 23 0.32 (3.3) 0.06 to 0.83 19 to 37 0.16 (1.6)
NX-80VFC402-2.2T x 3(4) –e 2.2 0.6 39 33 0.46 (4.7) 0.06 to 0.83 28 to 54 0.25 (2.5)
NX-80VFC402-3.7T x 3(4) –e 3.7 0.6 55 47 0.54 (5.5) 0.06 to 0.90 34 to 63 0.29 (3.0)
NX-80VFC403-3.7T x 3(4) –e 3.7 0.6 63 54 0.67 (6.8) 0.06 to 0.90 42 to 79 0.36 (3.7)
NX-80VFC403-5.5T x 3(4) –e 5.5 0.6 76 65 0.74 (7.6) 0.06 to 0.90 47 to 88 0.41 (4.2)
50 100
NX-100VFC502-2.2T x 3(4) –e 2.2 0.9 24 20 0.27 (2.8) 0.06 to 1.17 15 to 30 0.13 (1.3)
NX-100VFC502-3.7T x 3(4) –e 3.7 0.9 46 39 0.46 (4.7) 0.06 to 1.32 28 to 54 0.25 (2.5)
NX-100VFC503-5.5T x 3(4) –e 5.5 0.9 63 54 0.63 (6.4) 0.06 to 1.31 39 to 73 0.34 (3.5)
NX-100VFC503-7.5T x 3(4) –e 7.5 0.9 73 62 0.74 (7.6) 0.06 to 1.39 47 to 88 0.41 (4.2)
65 125
NX-125VFC652-3.7T x 3(4) –e 3.7 1.5 21 18 0.28 (2.9) 0.06 to 1.73 16 to 31 0.14 (1.4)
NX-125VFC652-5.5T x 3(4) –e 5.5 1.5 34 29 0.41 (4.2) 0.06 to 1.79 25 to 48 0.22 (2.2)
NX-125VFC653-7.5T x 3(4) –e 7.5 1.5 50 43 0.65 (6.6) 0.06 to 1.70 41 to 77 0.35 (3.6)
4-pump Parallel, 4 (5) -pump Rotation
40 80
NX-80VFC401-1.1F x 4(5) –e 1.1
3-phase䡡
200
(50Hz)
3-phase
200/220
(60Hz)
0.8 18 15 0.23 (2.3) 0.08 to 1.10 12 to 25 0.10 (1.0)
NX-80VFC402-1.5F x 4(5) –e 1.5 0.8 27 23 0.32 (3.3) 0.08 to 1.11 19 to 37 0.16 (1.6)
NX-80VFC402-2.2F x 4(5) –e 2.2 0.8 39 33 0.46 (4.7) 0.08 to 1.11 28 to 54 0.25 (2.5)
NX-80VFC402-3.7F x 4(5) –e 3.7 0.8 55 47 0.54 (5.5) 0.08 to 1.20 34 to 63 0.29 (3.0)
NX-80VFC403-3.7F x 4(5) –e 3.7 0.8 63 54 0.67 (6.8) 0.08 to 1.20 42 to 79 0.36 (3.7)
NX-80VFC403-5.5F x 4(5) –e 5.5 0.8 76 65 0.74 (7.6) 0.08 to 1.20 47 to 88 0.41 (4.2)
50 100
NX-100VFC502-2.2F x 4(5) –e 2.2 1.2 24 20 0.27 (2.8) 0.08 to 1.55 15 to 30 0.13 (1.3)
NX-100VFC502-3.7F x 4(5) –e 3.7 1.2 46 39 0.46 (4.7) 0.08 to 1.76 28 to 54 0.25 (2.5)
NX-100VFC503-5.5F x 4(5) –e 5.5 1.2 63 54 0.63 (6.4) 0.08 to 1.74 39 to 73 0.34 (3.5)
NX-100VFC503-7.5F x 4(5) –e 7.5 1.2 73 62 0.74 (7.6) 0.08 to 1.85 47 to 88 0.41 (4.2)
65 125
NX-125VFC652-3.7F x 4(5) –e 3.7 2.0 21 18 0.28 (2.9) 0.08 to 2.31 16 to 31 0.14 (1.4)
NX-125VFC652-5.5F x 4(5) –e 5.5 2.0 34 29 0.41 (4.2) 0.08 to 2.38 25 to 48 0.22 (2.2)
NX-125VFC653-7.5F x 4(5) –e 7.5 2.0 50 43 0.65 (6.6) 0.08 to 2.27 41 to 77 0.35 (3.6)
5-pump Parallel, 5-pump Rotation
40 100
NX-100VFC401-1.1G x 5-e 1.1
3-phase䡡
200
(50Hz)
3-phase
200/220
(60Hz)
1.0 18 15 0.23 (2.3) 0.10 to 1.38 12 to 25 0.10 (1.0)
NX-100VFC402-1.5G x 5-e 1.5 1.0 27 23 0.32 (3.3) 0.10 to 1.38 19 to 37 0.16 (1.6)
NX-100VFC402-2.2G x 5–e 2.2 1.0 39 33 0.46 (4.7) 0.10 to 1.39 28 to 54 0.25 (2.5)
NX-100VFC402-3.7G x 5–e 3.7 1.0 55 47 0.54 (5.5) 0.10 to 1.50 34 to 63 0.29 (3.0)
NX-100VFC403-3.7G x 5–e 3.7 1.0 63 54 0.67 (6.8) 0.10 to 1.50 42 to 79 0.36 (3.7)
NX-100VFC403-5.5G x 5–e 5.5 1.0 76 65 0.74 (7.6) 0.10 to 1.50 47 to 88 0.41 (4.2)
50 125
NX-125VFC502-2.2G x 5–e 2.2 1.5 24 20 0.27 (2.8) 0.10 to 1.95 15 to 30 0.13 (1.3)
NX-125VFC502-3.7G x 5–e 3.7 1.5 46 39 0.46 (4.7) 0.10 to 2.20 28 to 54 0.25 (2.5)
NX-125VFC503-5.5G x 5–e 5.5 1.5 63 54 0.63 (6.4) 0.10 to 2.18 39 to 73 0.34 (3.5)
NX-125VFC503-7.5G x 5–e 7.5 1.5 73 62 0.74 (7.6) 0.10 to 2.32 47 to 88 0.41 (4.2)
65 150
NX-150VFC652-3.7G x 5–e 3.7 2.5 21 18 0.28 (2.9) 0.10 to 2.88 16 to 31 0.14 (1.4)
NX-150VFC652-5.5G x 5–e 5.5 2.5 34 29 0.41 (4.2) 0.10 to 2.98 25 to 48 0.22 (2.2)
NX-150VFC653-7.5G x 5–e 7.5 2.5 50 43 0.65 (6.6) 0.10 to 2.83 41 to 77 0.35 (3.6)
*Above specifications also apply to special models (negative suction type) without “-e” at the end of the model.

4-1
4. Installation
4.1 Precautions for installation
Warning
When moving or installing the unit, never lift it in an unstable condition
or with any load applied to the pressure tank, pipes, or control panel.
Otherwise, the unit may fall, resulting in injury and/or damage.
Before lifting the unit, refer to the catalog, the external dimensions
drawing, or other documents to check the weight of the unit, and use an
appropriate lifting device of which rated load is over the the unit.
Otherwise, the unit may fall, resulting in injury and/or damage.
Caution
For the installation environment, follow the precautions described
below. Otherwise, it may lead to failures and/or other problems as well
as a shorter life of the units.
Caution
This water supply unit is designed for indoor use. For outdoor use,
install the outdoor hood, which is available as a special accessory.
Otherwise, it may lead to failures.
Caution
To suck up water from a lower position, use a water supply unit
designed for lifting operation.
Otherwise, discharge pressure may drop, thus leading to disruption of
water supply.
(1) Install the unit at a place that meets the following conditions:
· a place that meets the requirements in Section “3.1 Specifications of the water supply unit “;
· a place that is not exposed to the wind or rain;
· a dry, well-ventilated environment, which as free of dust or moisture as possible;
· a location where unauthorized persons cannot easily enter or operate the product;
· a location as close to the water source as possible so that the suction pipe can be short.; and
· a location where mainance can be conducted easily and abnormality can be readily coped with.
(2) Fix the water supply unit firmly on a level concrete foundation with anchor bolts.
(3) Be sure to provide a drain ditch around the water supply unit, and waterproof the floor.
(4) If the system could be exposed to the freezing temperature in winter, be sure to take measures to prevent
freezing in the pump room or prevent the pump, valves, piping, pressure transmitter, pressure tank, and
other devices from freezing. We can offer the special models designed to prevent freezing. Contact us.
(5) Use sound insulating materials for the door and walls of the pump room. Particularly when generated noise
may pose a problem, take necessary measures against the noise.
(6) When lifting the water supply unit, use the lifting holes in the common base as shown in the figure below.
Also apply pads so as not to damage the unit body. Do not remove the cap of the control panel for
attaching hanging bolts to lift the unit.
Lifting hole
Fig.4-1 Lifting hole position

4-2
4.2 Precautions for piping work
Caution
Do not screw a pipe into the pump with the companion flange attached
to the pump. Otherwise, it may damage the pump.
Caution
Do not merge the suction pipes. Do not install the piping with a shape
of upward bend (i.e. providing the piping with a rising slope and then a
descending slope).
Otherwise, it may hinder the normal operation.
Caution
Do not use any piping materials that are prone to rust.
Otherwise, it may damage the unit.
Caution
After work, thoroughly clean (flush) the inside of the receiver tank and
piping.
(1) Attach a companion flange cto the water supply unit after connecting the pipe.
(2) Install an adequate pipe support dso that the weight of the piping system will not be applied to the main
unit.
(3) For test operation and adjustments, be sure to attach sluice valves fand a test pipe gto the discharge
pipe e.
(4) Ensure to install a suction pipe hto each pump.
(5) The suction pipes hmust be as short and straight as possible with minimal bends.
(6) To minimize the piping loss, the bore of the suction pipes hmust be equal to or one size larger than that of
the pump. Pay special attention because the flow rate of the subsequently activated pump exceeds the
value devided the maximum water usage by the maximun number of paralleled units.
(7) For maintenance, be sure to attach sluice valves ito the suction pipes h.
(For negative suction type, do not attach sluice valves ito the suction pipes.)
(8) Ensure to attach strainers jto the ends of the suction pipes hin order to block the entrance of foreign
matter.
(9) After piping work, be sure to clean the inside of a receiver tank kto prevent the entry of foreign matter into
the pumps.
<Piping work example>
Maintenance space
600mm or more
Vibration isolation
frame base
(Special attachment)
Drainage
ditch
Receiver
tank
9
1
2
8
6
7
54
3
Vibration
isolation fitting
Drainage
ditch
7
6 2
Maintenance space
600mm or more
Maintenance space
600mm or more
Maintenance space
600mm or more
Note) Maintenance space indicates manufacturer’s
recommendations.
Fig. 4-2 Piping work example (for positive suction type)

4-3
4.3 Precautions for wiring work
Warning
Use the wiring equipment and devices compliant to use conditions, and
carry out wiring work safely and securely according to the technical
standards for electrical facilities, as well as the indoor wiring
regulations.
Only qualified personnel such as licensed electrical engineers are
allowed to carry out electric wiring work.
Incomplete wiring work by unqualified persons is prohibited by law.
4.3.1 Wiring work for power supply
Warning
Be sure to install a ground fault interrupter dedicated to this unit at the
primary power supply. Otherwise, it may lead to an electric shock
and/or fire.
Warning
Ensure to securely install a ground wire to the control panel. Ensure to
perform grounding work.
Warning
Connecting a ground wire to gas or water pipes is not only prohibited
by law but also extremely dangerous.
Caution
Do not install different or other cables or control wires in one pipe or
conduit.
Caution
Do not attach a phase advance capacitor to the secondary wiring of the
control panel.
Otherwise, it may lead to failures in the inverter or the phase advance
capacitor.
(1) On the primary power supply side of the water supply unit, be sure to install a ground fault interrupter
dedicated to this unit.
Check the capacity of the ground fault interrupter fitted inside the control panel, and then select a ground
fault interrupter on the power supply side in consideration of protection coordination.
(2) Be sure to attach a ground wire to prevent an electric shock.
Connect the ground wire to the ground terminal inside the control panel.
(3) Connect the primary power line to the power terminal block inside the control panel.
Pass each wire through a metal tube or a metal conduit for shielding, and ground the covering of the tube.
(4) Control the fluctuation of the voltage within ±10% of the rated voltage, and the frequency within ±5% of the
rated frequency.
Keep in mind that if you use the unit at a voltage or frequency out of the range, the unit may break down.
Also note that if the power voltage is lower than the rated voltage, an overload may occur even if the flow
rate is within the specified range.
(5) Before running the pump, check the following points again:
xAn appropriate ground fault interrupter is installed.
xWiring is correct.
xThe unit is securely grounded.
xNone of the three wires (two wires for single-phase power) of the motor has come loose or is
disconnected.
Note that poor or incorrect connection of motor terminals may burn out the motor.

4-4
4.3.2 Instrumentation
Carry out wiring work for instrumentation according to the following procedure.
Note
Insert the instrumentation wires into the inlet ports for instrumentation
wires, secure the wires by passing the binding band through the clamps
on the right side face inside the control panel and under the contorl
board, and then connect them to the board. If the clamps are not used
for binding the wires, it may cause some trouble in the maintenance of
the unit.
Caution
Attach grommets (22 mm in diameter) to the wire inlet ports to protect
the wires, or use conduit tubes.
(1) Wiring work for water level control
Referring to the following table, connect wires to receiver tank electrodes.
· Ball tap type ··································Table 4-3-2(a)
· Inflow solenoid valve type ·················Table 4-3-2(b)
Note
· The Tank Selection setting is set to “No tank” before shipment. Before
starting the operation of the pumps with receiver tank electrodes connected,
select water tank(s) you use on the operation panel. (ĺsee 7.2.)
· When using an inflow solenoid valve, check the type of the solenoid valve
(normally open or normally closed), and set the type (parameter P103).
(ĺsee 7.5.)
· Set the Solenoid Valve Operation setting to “Auto” on the operation panel
before use. (ĺsee 7.3.)

4-5
Table 4-3-2 (a) Wiring patterns (ball tap type)
Single receiver tank Double receiver tank
4P type electrode
Settings
Tank Selection setting: No.1
Solenoid Valve Operation setting:
Man. Close
Parameter P101: 4
Tank Selection setting: Common
Solenoid Valve Operation setting: Man. Close
Parameter P101: 4
Wiring pattern
Terminal block for receiver tank No.1
Electrodes for receiver tank
Terminal block for receiver tank No.1
Electrodes for receiver tank No.1
Terminal block for receiver tank No.2
Electrodes for receiver tank No.2
5P type electrode
Settings
Tank Selection setting: No.1
Solenoid Valve Operation setting:
Man. Close
Parameter P101: 5
Tank Selection setting: Common
Solenoid Valve Operation setting: Man. Close
Parameter P101: 5
Wiring pattern
Terminal block for receiver tank No.1
Electrodes for receiver tank
Terminal block for receiver tank No.1
Electrodes for receiver tank No.1
Terminal block for receiver tank No.2
Electrodes for receiver tank No.2
Wires
Full water level
Dry-run recovery
Dry-run prevention
Low water level
Wires
Full water level
Dry-run recovery
Dry-run prevention
Low water level
Wires
Full water level
Dry-run recovery
Dry-run prevention
Low water level
Wires
Full water level
Dry-run recovery
Dry-run prevention
(low water level)
Wires
Full water level
Dry-run recovery
Dry-run prevention
(low water level)
Control panel
City water
Level regulating
valve
Ball tap
Receiver tank
Water supply unit
Control panel
City water
City water
Level regulating
valve
Ball tap Ball tap
Receiver tank #1 Receiver tank #2
Level regulating
valve
Water supply unit
Wires
Full water level
Dry-run recovery
Dry-run prevention
(low water level)
This manual suits for next models
1
Table of contents
Other Teral Control Unit manuals
Popular Control Unit manuals by other brands

YASKAWA
YASKAWA IM 053PN manual
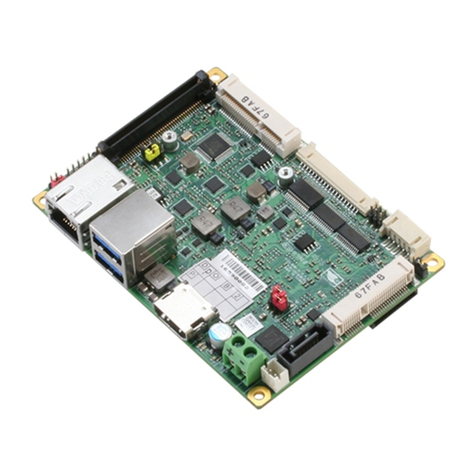
Aaeon
Aaeon PICO-BSW1 user manual
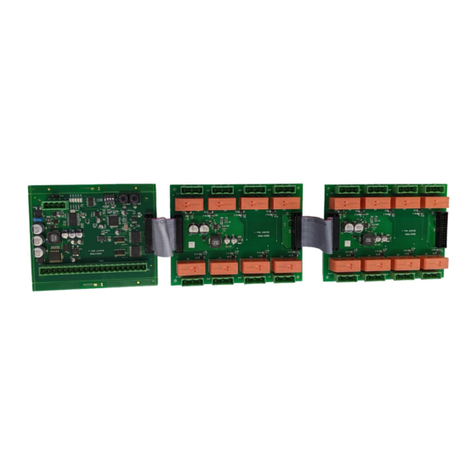
Sensitron
Sensitron STG/OUT16-S2 instruction manual

Kessel
Kessel Staufix FKA Standard Installation and operating manual
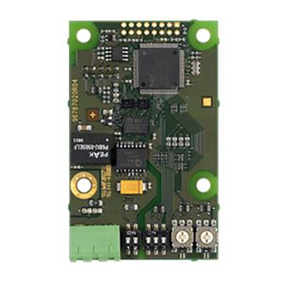
Grundfos
Grundfos CIM 200 Functional profile and user manual
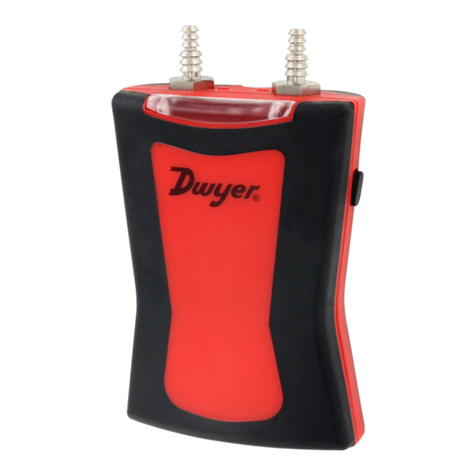
Dwyer Instruments
Dwyer Instruments DP3 Series Installation and operating instructions