Texas Instruments bq51221EVM-520 User manual

User's Guide
SLUUAX6B–February 2014–Revised June 2014
Dual Mode (WPC and PMA) Integrated Wireless Receiver
Power Supply
The bq51221EVM-520 (PWR520-001) wireless power receiver evaluation kit (EVM) from Texas
Instruments is a high performance, easy-to-use development kit for the design of wireless power solutions.
It helps designers to evaluate the operation and performance of the bq51221 IC, (also, this EVM can be
used to evaluate the bq51021 IC, a WPC-only receiver) a secondary-side receiver device for wireless
power transfer in portable applications. The bq51221 device is a fully contained wireless power receiver
capable of operating in both the WPC and PMA protocols which enables a system to not be confined to
one standard. The bq51221 provides a single stage power conversion while integrating the digital control
and communication. The bq51221 complies with the WPC v1.1 and PMA communication protocol. The kit
enables designers to speed up the development of their end-applications.
Contents
1 Introduction ................................................................................................................... 3
2 Considerations with this EVM.............................................................................................. 3
3 Modifications.................................................................................................................. 4
4 Recommended Operation Condition ...................................................................................... 4
5 Equipment and EVM Setup................................................................................................. 5
5.1 Schematic............................................................................................................ 5
5.2 Connector and Test Point Descriptions.......................................................................... 6
5.3 Jumpers/Switches .................................................................................................. 6
5.4 Test Point Descriptions ............................................................................................ 7
5.5 Pin Description of the IC........................................................................................... 7
6 Test Procedure............................................................................................................... 8
6.1 Definition............................................................................................................. 8
6.2 Recommended Test Equipment .................................................................................. 8
6.3 Equipment Setup.................................................................................................... 8
6.4 Procedure............................................................................................................ 9
7 Test Results................................................................................................................. 11
7.1 Steady State Operation with bq2425x Charger ............................................................... 11
7.2 Load Step .......................................................................................................... 12
7.3 TS Control Function............................................................................................... 14
7.4 Efficiency Data..................................................................................................... 15
7.5 AD Insertion and Removal ....................................................................................... 15
7.6 Thermal Performance............................................................................................. 16
8 Dual Mode Coil Design Consideration................................................................................... 17
8.1 Shielding............................................................................................................ 17
8.2 Receiver Detection: Attraction and Alignment................................................................. 17
8.3 Inductor Value ..................................................................................................... 17
9 Layout and Bill of Materials ............................................................................................... 18
9.1 bq5122x Traces ................................................................................................... 18
9.2 Layout Guidelines ................................................................................................. 18
9.3 Printed-Circuit Board Layout Example ......................................................................... 18
9.4 bq51221EVM-520 Layout ........................................................................................ 20
9.5 Bill of Materials .................................................................................................... 23
List of Figures
1
SLUUAX6B–February 2014–Revised June 2014 Dual Mode (WPC and PMA) Integrated Wireless Receiver Power Supply
Submit Documentation Feedback Copyright © 2014, Texas Instruments Incorporated

www.ti.com
1 bq51221EVM-520 Schematic .............................................................................................. 5
2 bq51221 in Steady State Operation with bq24250EVM............................................................... 11
3 Load Step (PMA) with VIN_DPM ........................................................................................ 12
4 Load Step (WPC)........................................................................................................... 13
5 TS Control Function ....................................................................................................... 14
6 System Efficiency versus Output Current .............................................................................. 15
7 AD Insertion and Removal ............................................................................................... 15
8 Thermal Image in WPC Transmitter (1000-mA Load) ................................................................ 16
9 Thermal Image in PMA Transmitter (1000-mA Load) ................................................................. 16
10 Dual Mode Coil Example.................................................................................................. 17
11 bq51221EVM-520 Layout Example ..................................................................................... 19
12 bq51221EVM-520 Top Assembly........................................................................................ 20
13 bq51221EVM-520 Layer 1 ................................................................................................ 20
14 bq51221EVM-520 Layer 2 ................................................................................................ 21
15 bq51221EVM-520 Layer 3 ................................................................................................ 21
16 bq51221EVM-520 Layer 4 ................................................................................................ 22
List of Tables
1 bq51221EVM-520 Electrical Performance Specifications.............................................................. 4
2 Pin Description............................................................................................................... 7
3 bq51221EVM-520 Rev. B Bill of Materials ............................................................................. 23
2Dual Mode (WPC and PMA) Integrated Wireless Receiver Power Supply SLUUAX6B–February 2014–Revised June 2014
Submit Documentation Feedback
Copyright © 2014, Texas Instruments Incorporated

www.ti.com
Introduction
1 Introduction
The bq5122x is an advanced, flexible, secondary-side device for wireless power transfer in portable
applications. The bq5122X devices integrate an ultra-low-impedance synchronous rectifier, a very high
efficiency post regulator, digital control, and accurate voltage and current loops. The bq5122X devices
provide the AC/DC power conversion while integrating the digital control required. The IC complies with
both WPC v1.1 and PMA communication protocol.
Together with the bq50xxx primary-side controller or any type-1 PMA transmitter, the bq5122X enables a
complete contactless power transfer system for a wireless power supply solution. By utilizing near-field
inductive power transfer, the secondary coil embedded in the mobile device can pick up the power
transmitted by the primary coil. The voltage from the secondary coil is then rectified and regulated to be
used as a power supply for down-system electronics. Global feedback is established from the secondary
to the primary in order to control the power transfer process.
In WPC, the system communication is digital - packets are transferred from the secondary to the primary.
Differential bi-phase encoding is used for the packets. The bit rate is 2 Kbits/s. Various types of
communication packets have been defined. These include identification and authentication packets, error
packets, control packets, power usage packets and efficiency packets, among others.
A PMA-compliant receiver communicates based on continuous transmission of signals from the receiver to
the transmitter. The PMA system defines six different communications symbols. These are PMA INC,
PMA DEC, PMA NoCHG, PMA EOC, PMA MsgBit and PMA TBD (proprietary for future use). The PMA
receiver will transmit these signals back to back with no gaps between them to control the operation point.
Each PMA receiver will have a unique PMA RXID, transmitted in the RXID message. Note that the first
build of these EVMs do not have RX ID implemented.
2 Considerations with this EVM
The bq51221EVM-520 evaluation module (PWR520-001) demonstrates the receiver portion of the
wireless power system. This receiver EVM is a complete receiver-side solution that produces 5-W output
power at up to 1-A load with adjustable output voltage.
• The receiver can be used in any number of low-power battery portable devices as a power supply for a
battery charger. With contact-free charging capability, no connections to the device are needed.
• Highly integrated wireless power receiver solution
– Ultra efficient synchronous rectifier
– Very high efficiency post regulator
– WPC v1.1- and PMA-compliant communication and control
– Only one IC required between RX coil and DC output
• Programmable output voltage to optimize performance for any application
• Adaptive communication current limit (CM_ILIM) for robust communication in WPC mode
• Supports 20-V max input
• Low-power dissipative over voltage clamp
• Over voltage, over current , over temperature protection for both PMA and WPC modes
• Low-profile, external pick-up coil
• Frame is configured to provide correct receiver to transmitter spacing
• Room above coil for testing with battery, key for Foreign Object Detection (FOD) tuning.
• Options to adjust the input current limit and output voltage using resistor or I2C
• Flexibility for FOD tuning
• Adjustable resistor that can be used to set RFOD
• Temperature sensing can be adjusted using external resistors
• Micro-USB connector for adapter testing configuration
• I2C connector (USB-TO-GPIO “HPA172” kit for I2C communication through computer is required)
• WPG LED indicator (turns on as the VOUT goes high)
3
SLUUAX6B–February 2014–Revised June 2014 Dual Mode (WPC and PMA) Integrated Wireless Receiver Power Supply
Submit Documentation Feedback Copyright © 2014, Texas Instruments Incorporated

Modifications
www.ti.com
3 Modifications
See the bq51221 data sheet (SLUSBS9) when changing components. To aid in such customization of the
EVM, the board was designed with devices having 0402 and 0603 or larger footprints. A real
implementation likely occupies less total board space.
Note that changing components can improve or degrade EVM performance.
4 Recommended Operation Condition
Table 1 provides a summary of the bq51221EVM-520 performance specifications. All specifications are
given for an ambient temperature of 25°C.
Table 1. bq51221EVM-520 Electrical Performance Specifications
Parameter Test Condition MIN TYP MAX Unit
Vrect Rect voltage range 4 10 V
IAD_EN_sink Sink current 1 mA
IIN Input current range 1.5 A
IOUT Output current range Current limit programming range 1.5 A
VOUT(REG) Programmable Output Voltage(1) POUT = 5 W 4.5 8 V
FsSwitching Frequency WPC 110 205 kHz
PMA 235 275
TJJunction Temperature 125 °C
(1) The output voltage can be adjusted using I2C or the VIREG and VOREG resistors. Also the coil needs to be changed for
different voltage for optimal operation of the EVM.
4Dual Mode (WPC and PMA) Integrated Wireless Receiver Power Supply SLUUAX6B–February 2014–Revised June 2014
Submit Documentation Feedback
Copyright © 2014, Texas Instruments Incorporated

1
1
2
2
3
3
4
4
5
5
6
6
D D
C C
B B
A A
2 3
3/5/2014
PWR520B.SchDoc
Sheet Title:
Size:
Mod. Date:
File:
Sheet: of
Bhttp://www.ti.com
Contact: http://www.ti.com/support
bq51221EVM-520Project Title:
Designed for: Public Release
Assembly Variant:001
© Texas Instruments 2014
Drawn By:
Engineer:
T. Allag
T. Allag
Te xas Instruments and/or its licensors do not warrant the accuracy or completeness of this specification or any information contained therein. Texas Instruments and/or its licensors do not
warrant that this design will meet the specifications, will be suitable for your application or fit for any particular purpose, or will operate in an implementation. Texas Instruments and/or its
licensors do not warrant that the design is production worthy. You should completely validate and test your design implementation to confirm the system functionality for your application.
Not in version controlSVN Rev:
PWR520Number: Rev: B
GND
2700pF
C4
0.056uF
C2
0.1uF
C1
BOOT1
RECTBOOT2
BOOT2
OUT
BOOT1
CLMP1
AD
FOD
VTSB/VIREG
CLMP2
COMM1
AD_EN
LPRB1
COMM2
VO_REG
CM_ILIM
TS
CLMP1
0.47µF
C9
0.47µF
C12
CLMP2
COMM2
COMM1 GND
GND
VO_REG
1
2
J5
DNP
GND
0.1µF
C19
GND
TS
GND
VTSB/VIREG
TP1
DNP
TP2
DNP
2.00k
R13
GND
1.50k
R7
DNP
RECT
LPRB1
GND
GND
0.1µF
C18
150
R2
FOD
TP5
1
2
3
JP1
110
R4
TP4
ADJ
TS
GND
ILIM
FIX
RECT
56.2k
R1
1
2
J3
1
2
J4
1
2
3
JP2
GND
CM_ILIM
High
Low
CM_ILIM
GND
GND
0.1µF
C16
TP3
GND
GND
0.1µF
C6
OUT
GNDGND
AD_EN
Rect
1µF
C17
GND
GND
GND
Out
ILIM
FOD
AC1
AC2
Orange
D2
DNP
Green
D1
DNP
1
2
3
4
5
6
7
8
9
10
11
J1
1 2
3 4
5 6
7 8
9 10
J2
GND
A2
A1
B2
C2
C1
B1
Q1
CSD75301W1015
500 Ohm
R6
5k ohm
R5
DNP
OUT
AD
GND
20k
R15
DNP
10.0k
R11
1.50k
R16
DNP
0.082uF
C3
100pF
C5
10µF
C14
10µF
C15
1µF
C20
0
R3
OUT
0.015µF
C10
0.015µF
C11
0.082µF
C8
0.082µF
C13
3.3µF
C7
1.50k
R20
Green
D3
GND
102k
R17
102k
R14
11.3k
R18
11.3k
R10
102k
R19
27k
R21
DNP
100pF
C22
DNP
GND
PGND
A1
PGND
A2
PGND
A3
PGND
A4
PGND
A5
PGND
A6
AC1
B1
AC1
B2
AC1
B3
AC2
B4
AC2
B5
AC2
B6
BOOT1
C1
RECT
C2
RECT
C3
RECT
C4
RECT
C5
BOOT2
C6
OUT
D1
OUT
D2
OUT
D3 OUT D4
OUT D5
OUT D6
CLAMP1 E1
AD E2
AD_EN E3
EN1/SCL E4
VIREG E5
CLAMP2 E6
COMM1 F1
FOD F2
LPRBEN and TERM F3
EN2/SDA F4
LPRB1 and WPG F5
COMM2 F6
VO_REG G1
ILIM G2
CM_ILIM G3
TS G4
TMEM G5
LPRB2 and PD_DET G6
U1
bq51221
2.2µF
C21
200
R9
200
R8
5.6Meg
R12
www.ti.com
Equipment and EVM Setup
5 Equipment and EVM Setup
5.1 Schematic
Figure 1 illustrates the bq51221EVM-520 schematic.
Figure 1. bq51221EVM-520 Schematic
5
SLUUAX6B–February 2014–Revised June 2014 Dual Mode (WPC and PMA) Integrated Wireless Receiver Power Supply
Submit Documentation Feedback Copyright © 2014, Texas Instruments Incorporated

Equipment and EVM Setup
www.ti.com
5.2 Connector and Test Point Descriptions
The connections points are described in the following paragraphs:
J1 – AD External Adapter Input
Power can be provided to simulate an external adapter applied to the receiver in the bq51221EVM-520
(PWR520-001).
J2 – Programming Connector
This connector is populated and is used for I2C communication using the USB-TO-GPIO “HPA172” kit.
J3 – Output Voltage
Output voltage in wireless power mode up to 1 A; the adapter option is also supported in this PWR520-
001.
J4 –GND
Ground return
J5 – TS and Return Connector
External connection for temperature sense resistor, see the bq51221 data sheet (SLUSBS9) for additional
information. Not populated in this spin.
5.3 Jumpers/Switches
The control jumpers and switches are described in the following paragraphs:
JP1– ILIM - Fix or ADJ
Max output current is set by ILIM pin. In the FIX position, the current is set to a fixed value of R4. In the
ADJ position current is set by R5. Note that R5 is not installed in this EVM.
JP2 – CM_ILIM
Enables the CM_ILIM feature when pulled low and disables when pulled up (High).
6Dual Mode (WPC and PMA) Integrated Wireless Receiver Power Supply SLUUAX6B–February 2014–Revised June 2014
Submit Documentation Feedback
Copyright © 2014, Texas Instruments Incorporated

www.ti.com
Equipment and EVM Setup
5.4 Test Point Descriptions
The test points are described in the following paragraphs:
TP1 & 2 – AC1 and AC2 Inputs
These are not populated, they can be used for measuring AC voltage applied to the EVM from the
receiver coil.
TP3– Rectified Voltage
The input AC voltage is rectified into unregulated DC voltage (RECT); additional capacitance is used to
filter the voltage before the regulator.
TP4– ILIM
Programming pin for over current limit protection, pin G2 of the IC.
TP5 – FOD
Input for rectified power measurement for Foreign Object Detection feature in WPC, pin F2 of the IC. FOD
pin for the bq51221.
5.5 Pin Description of the IC
Table 2. Pin Description
Pin Number (WCSP) bq5122x
A1, A2, A3, A4, A5, A6 PGND
B1, B2, B3 AC1,
B4, B5, B6 AC2,
C1 BOOT1
C2, C3, C4, C5 RECT
C6 BOOT2
D1, D2, D3, D4, D5, D6 OUT
E1 CLAMP1
E2 AD
E3 AD_EN
E4 SCL
E5 VIREC
E6 CLAMP2
F1 COMM1
F2 FOD
F3 LPRB_EN and TERM
F4 SDA
F5 LPRB1 and WPG
F6 COMM2
G1 VO_REG
G2 ILIM
G3 CM_ILIM
G4 TS
G5 TMEM
G6 LPRB2 and PD_DET
7
SLUUAX6B–February 2014–Revised June 2014 Dual Mode (WPC and PMA) Integrated Wireless Receiver Power Supply
Submit Documentation Feedback Copyright © 2014, Texas Instruments Incorporated

Test Procedure
www.ti.com
6 Test Procedure
This procedure describes test configuration of the bq51221EVM-520 evaluation board (PWR520-001) for
bench evaluation.
6.1 Definition
The following naming conventions are used:
VXXX : External voltage supply name (VAD, VOUT, VTS)
LOADW: External load name (LOADR, LOADI)
V(TPyy): Voltage at internal test point TPyy. For example, V(TP02) means the voltage at TP02.
V(Jxx): Voltage at header Jxx
V(TP(XXX)): Voltage at test point XXX. For example, V(ACDET) means the voltage at the test point which
is marked as ACDET.
V(XXX, YYY): Voltage across point XXX and YYY.
I(JXX(YYY)): Current going out from the YYY terminal of header XX.
Jxx(BBB): Terminal or pin BBB of header xx.
JPx ON : Internal jumper Jxx terminals are shorted.
JPx OFF: Internal jumper Jxx terminals are open.
JPx (-YY-) ON: Internal jumper Jxx adjacent terminals marked as YY are shorted.
Assembly drawings have location for jumpers, test points, and individual components.
6.2 Recommended Test Equipment
The following equipment is needed to complete this test procedure:
Power Supplies
Power Supply #1 (PS #1) capable of supplying 19 V at 1 A is required power plug to supply the PMA
transmitter (An adapter usually included on the PMA TX module).
Loads
A resistive load or electronic load that can be set to 5 Ω/1000 mA, 10 Ω/500 mA, and 5 kΩ/1 mA power
rating should be 5 W.
Meters
Two DC voltmeters and two DC ammeters are required.
Oscilloscopes
Not required.
bqTesla Transmitter and PMA Transmitter
• The transmitter HPA689 or equivalent will be used to test WPC mode
• PMA to test PMA mode (Duracell Powermat for 2 Devices “PMA compatible”—M2PB1)
• For proper operation, 22-AWG wire is recommended
6.3 Equipment Setup
6.3.1 Test Set Up
• The final assembly will be tested using a bqTesla transmitter (HPA689). Input voltage to the transmitter
is set to 19 VDC ±200 mV with current limit of 1.0 A.
• Connect power supply to J1 and J2 of transmitter, HPA689
• Set power supply to OFF
• Place Unit Under Test (UUT) on transmitter coil
8Dual Mode (WPC and PMA) Integrated Wireless Receiver Power Supply SLUUAX6B–February 2014–Revised June 2014
Submit Documentation Feedback
Copyright © 2014, Texas Instruments Incorporated

www.ti.com
Test Procedure
• UUT will be placed in the center of HPA689 TX coil. Other bqTesla transmitter base units are also
acceptable for this test (Just make sure to apply the right input voltage).
• A PMA (Duracell Powermat TX) transmitter is needed to test the PMA compliance
6.3.2 Load
• The load is connected between J3-OUT and J4-GND of the UUT
• A DC ammeter is connected between UUT and Load
• Set the load for 5 Ω/1000 mA
6.3.3 Jumper Settings
JP1 →ILIM and FIX are shorted
JP2 →CM_ILIM and high are shorted
6.3.4 Voltage and Current Meters
Connect ammeter to measure 19-V input current to transmitter. Connect voltmeter to monitor input voltage
at J1 and J2 of TX unit. On UUT a voltmeter is used to measure output voltage at J3 with ground at J4.
Connect ammeter to measure load current.
6.3.5 RFOD : R6 Set Up
Connect an ohmmeter between TP5 (FOD) and J4 (GND). Adjust R6 to 480 ohm reading on the
ohmmeter.
6.4 Procedure
6.4.1 Turn ON Operation and Operation at 1000-mA Load
• Turn ON Transmitter power supply (19 V)
• Transmitter—Verify LED D2 is “ON”
• UUT—Adjust load current to 1000 mA ±50 mA
• Put the receiver EVM on the Transmitter coil and align them correctly
• After 5 seconds verify that:
• Transmitter—Status LED D5 should be green flashing ~ 1 sec
• You should hear a beep from the transmitter
• Transmitter—LED D2 still ON
• Receiver—LED D1 is ON
• UUT—Verify that Vout is 4.9 V to 5.1 V ( Between J3 and J4)
• UUT—Verify that rectified voltage should be 5 V to 5.4 V (between TP3 and GND) (note: a modulation
signal is present on this voltage every 250 ms and may cause fluctuation in the reading use lower
value or base line)
6.4.2 Efficiency Test (1000-mA Load)
• Verify that input current to TX is less than 500 mA with input voltage at 19 VDC
• Turn OFF Transmitter Power Supply (19 V)
6.4.3 Turn ON Operation and Operation at 500-mA Load
• Turn ON Transmitter power supply (19 V)
• Transmitter—Verify LED D2 is “ON”
• UUT—Adjust load current to 500 mA ±50 mA
• Put the receiver EVM on the Transmitter coil and align them correctly
9
SLUUAX6B–February 2014–Revised June 2014 Dual Mode (WPC and PMA) Integrated Wireless Receiver Power Supply
Submit Documentation Feedback Copyright © 2014, Texas Instruments Incorporated

Test Procedure
www.ti.com
• After 5 seconds verify that:
• Transmitter—Status LED D5 should be green flashing ~ 1 sec
• You should hear a beep from the transmitter
• Transmitter—LED D2 still ON
• Receiver—LED D1 is ON
• UUT—Verify that Vout is 4.9 V to 5.2 V ( Between J3 or TP7 and J4)
• UUT—Verify that rectified voltage should be 5 V to 5.4 V (between TP3 and GND) (Note: a modulation
signal is present on this voltage every 250 ms and may cause fluctuation in the reading use lower
value or base line)
6.4.4 Efficiency Test (500-mA Load)
• Verify that input current to TX is less than 260 mA with input voltage at 19 VDC
• Turn OFF Transmitter Power Supply (19 V)
6.4.5 Operation (1-mA Load)
• Turn ON Transmitter power supply (19 V)
• Transmitter—Verify LED D2 is “ON”
• UUT—Adjust load current to 1 mA ±200 µA
• Put the receiver EVM on the Transmitter coil and align them correctly
• After 5 seconds verify that:
• Transmitter—Status LED D5 should be green flashing ~ 1 sec.
• You should hear a beep from the transmitter
• Transmitter—LED D2 still ON
• Receiver—LED D1 is ON
• UUT—Verify that Vout is 4.9 V to 5.2 V ( Between J3 and J4)
• UUT—Verify that rectified voltage should be 6.6 V to 8.6 V (between TP3 and GND) (Note: a
modulation signal is present on this voltage every 250 ms and may cause fluctuation in the reading use
lower value or base line)
6.4.6 Efficiency Test (1-mA Load)
• Verify that input current to TX is less than 80 mA with input voltage at 19 VDC
• Turn OFF Transmitter Power Supply (19 V)
6.4.7 PMA Test (1000-mA Load)
• Turn ON PMA Transmitter power supply(18 V) or by using the adapter that comes with the PMA
transmitter
• Put the receiver EVM on the Transmitter coil and align them correctly
• After 5 seconds verify that:
1. You should hear a beep from the transmitter
2. Receiver—LED D3 is ON
• UUT—Adjust load current to 1000 mA ±50 mA
• UUT—Verify that Vout is 4.9 V to 5.2 V ( Between J3 and J4)
• UUT—Verify that rectified voltage should be 5 V to 5.4 V (between TP3 and GND) (Note: a modulation
signal is present on this voltage every 250 ms and may cause fluctuation in the reading use lower
value or base line)
10 Dual Mode (WPC and PMA) Integrated Wireless Receiver Power Supply SLUUAX6B–February 2014–Revised June 2014
Submit Documentation Feedback
Copyright © 2014, Texas Instruments Incorporated

www.ti.com
Test Results
6.4.8 Adapter Test (500-mA Load)
• Connect 5-V ±200 mV adapter on J1 on the PWR520-001 Receiver
• Adjust load current to 500 mA ±50 mA (J3 “OUT” and J4 “GND”)
• Verify that:
1. UUT—LED D3 is ON
2. UUT—Vout is 5.0 V to 6 V (J3)
3. Transmitter—Status LED D5 is off
7 Test Results
7.1 Steady State Operation with bq2425x Charger
With the power supply off, connect supply to the PMA transmitter.
• Set up the test bench as described in Section 6
• Power PMA TX with 18 V or with the PMA power adapter
• Connect the output of RX to a battery charger (bq24250EVM-150) to charge a battery
• Set the VBAT to 3.8 V
• Set the charger current to ~1.2 A
• Set input current limit from the charger to 1 A
• Monitor the IOUT and VOUT from the RX after putting the receiver EVM on the transmitter coil and
align them correctly
•Figure 2 shows the VOUT and IOUT from the RX as the battery charges
Figure 2. bq51221 in Steady State Operation with bq24250EVM
11
SLUUAX6B–February 2014–Revised June 2014 Dual Mode (WPC and PMA) Integrated Wireless Receiver Power Supply
Submit Documentation Feedback Copyright © 2014, Texas Instruments Incorporated

Test Results
www.ti.com
7.2 Load Step
The procedure for load step in PMA mode is as follows:
• Set up the test bench as described in Section 6
• Power PMA TX with 18 V or with the PMA power adapter
• Connect the output of RX to a battery charger (bq24250EVM-150) to charge a battery
• Set the VIN_DPM of the charger to 4.6 V
• Set a battery voltage to full charge state and connect system load to system output of the charger.
Then, put the receiver EVM on the transmitter coil and align them correctly.
• Provide a load step from no-load (high impedance) to 1000-mA on the system load
• Monitor on side RX: load current, rectifier voltage, and output voltage as shown in Figure 3
Figure 3. Load Step (PMA) with VIN_DPM
12 Dual Mode (WPC and PMA) Integrated Wireless Receiver Power Supply SLUUAX6B–February 2014–Revised June 2014
Submit Documentation Feedback
Copyright © 2014, Texas Instruments Incorporated

www.ti.com
Test Results
The procedure for load step in WPC mode is as follows:
• Set up the test bench as described in Section 6 for a WPC transmitter
• Power WPC TX with 19 V. Then put the receiver EVM on the transmitter coil and align them correctly.
• Provide a load step from no-load (high impedance) 1000 mA (if using current source load)
• Monitor on side RX: Rectifier voltage, and output voltage as shown in Figure 4
Figure 4. Load Step (WPC)
13
SLUUAX6B–February 2014–Revised June 2014 Dual Mode (WPC and PMA) Integrated Wireless Receiver Power Supply
Submit Documentation Feedback Copyright © 2014, Texas Instruments Incorporated

Test Results
www.ti.com
7.3 TS Control Function
The procedure for temperature sensing (TS) control functions when the TS pin is held high:
• Set up the test bench as described in Section 6
• Power the PMA TX. Then put the receiver EVM on the transmitter coil and align them correctly.
• Drive the TS pin high (2 V) using external power supply
• Monitor the TS pin, PMA signal (If a test fixture is used—to see End of Charge), WPG, and output
voltage as shown in Figure 5
Figure 5. TS Control Function
14 Dual Mode (WPC and PMA) Integrated Wireless Receiver Power Supply SLUUAX6B–February 2014–Revised June 2014
Submit Documentation Feedback
Copyright © 2014, Texas Instruments Incorporated

0.00
0.10
0.20
0.30
0.40
0.50
0.60
0.70
0.80
0.90
0.05 0.25 0.45 0.65 0.85 1.05
Efficiency
IOUT tA
WPC-bq500210_Vin_19 V
WPC-bq500210_Vin_5 V
WPC-bq500410_Vin_12 V
PMA - 18 V
C001
www.ti.com
Test Results
7.4 Efficiency Data
The plot shown in Figure 6 illustrates the system (DC-DC) efficiency of the bq51221EVM-520 under
different transmitters.
Figure 6. System Efficiency versus Output Current
7.5 AD Insertion and Removal
The plot shown in Figure 7 illustrates the behavior of the bq51221 when the AD is inserted while the EVM
is on the transmitter pad. There is a 36-ms off time during the transition between wireless power and wired
power modes.
Figure 7. AD Insertion and Removal
15
SLUUAX6B–February 2014–Revised June 2014 Dual Mode (WPC and PMA) Integrated Wireless Receiver Power Supply
Submit Documentation Feedback Copyright © 2014, Texas Instruments Incorporated

Test Results
www.ti.com
7.6 Thermal Performance
This section shows a thermal image of the bq51221EVM-520 in both WPC and PMA. A 1-A load is used
and output voltage is set to 5 V. There is no air flow and the ambient temperature is 25°C. The peak
temperature of the IC (39°C in WPC and 37°C in PMA) is well below the maximum recommended
operating condition listed in the data sheet.
Figure 8. Thermal Image in WPC Transmitter (1000-mA Load)
Figure 9. Thermal Image in PMA Transmitter (1000-mA Load)
16 Dual Mode (WPC and PMA) Integrated Wireless Receiver Power Supply SLUUAX6B–February 2014–Revised June 2014
Submit Documentation Feedback
Copyright © 2014, Texas Instruments Incorporated

www.ti.com
Dual Mode Coil Design Consideration
8 Dual Mode Coil Design Consideration
8.1 Shielding
Implementation of a shielding mechanism is recommended as part of receiver device. Shielding provides
protection from possible bi-directional interference between wireless charging system and consumer
electronic device. The interference causes may include coupling interference causing development of heat
due to eddy currents, impact on wireless charging data transfer, and so forth. It is recommended to apply
the shield on all the magnetically active area (between the secondary coil and the electronic device).
8.2 Receiver Detection: Attraction and Alignment
When a PMA Transmitter is in standby phase and a receiver is placed on the charging surface, the
transmitter detects the presence of the receiver by using either passive method with a “Hall Effect Sensor”
or by active method with digital pinging.
In the passive method, the transmitter uses a Hall Effect Sensor to detect the presence of a receiver coil.
It measures the voltage difference between no coil on TX and a full aligned coil on TX. If the difference in
the hall sensor measurements between the two cases is above 200 mV, the power transfer phase will
start as required by PMA. In the active method, it uses a digital pinging method instead. This detection
method uses a periodic short pulse or short burst of pulses applied to the primary coil. By measuring the
resultant interference on the primary coil, the presence of a receiver can be detected.
For both methods, a PMA-compliant receiver coil design shall include materials that can trigger the Hall
Effect Sensor and create enough interference on the digital pinging on the PMA transmitters. The
implementation is vendor specific and may rely on the magnetic material used for alignment aid, the
shielding, or any other material designers select.
The alignment aid ferrite should have no more than 2 mm distance from charged device outer surface.
The recommended shielding ferrite placed on the receiver antenna and the alignment aid fit into the hole
at the center of the shielding ferrite as indicated in Figure 10.
Figure 10. Dual Mode Coil Example
8.3 Inductor Value
A PMA-compliant receiver operating frequency is between 232 kHz and 278 kHz. For best efficient PMA
only systems, the recommended coil self-inductance is around 4-µH range and coil self-resistance is
around 300 mΩ. The operating frequency for PMA is higher than WPC. Thus, for dual mode solution the
inductance has to be increased to meet WPC requirements. For dual mode applications, a recommended
coil self-inductance is about 7.5 µH and coil self-resistance is around 300 mΩ.
In this EVM, the 760308102210 coil from Wurth electronics is used as an example for dual mode solution.
Other coils also can be used such as KNCWZ08C409 from Panasonic and ASC-353583M08-S0 V1.0 from
Amotech. The resonant capacitors are not required for PMA mode only. To support WPC and PMA, tuning
resonant caps according to WPC requirement and with the final configuration of the board is a must. Note
that the coil inductance and the required shielding may vary from application to application depending on
the final configuration of the board.
17
SLUUAX6B–February 2014–Revised June 2014 Dual Mode (WPC and PMA) Integrated Wireless Receiver Power Supply
Submit Documentation Feedback Copyright © 2014, Texas Instruments Incorporated

Layout and Bill of Materials
www.ti.com
9 Layout and Bill of Materials
9.1 bq5122x Traces
The bq5122x device pins traces can be classified as follows:
•Signal/Sensing Traces
TS/CTRL, SDA, SCL, LPRB2/PD_DET, LPRB1/WPG ,COMM, CHG, ILIM, AD, AD_EN, FOD, TMEM,
CM_ILIM, VO_REG, VIREG, LPRB_EN/TERM.
Make sure these trace are not being interfered by the noisy traces.
•Noisy Traces
AC1, AC2, BOOT, COMM
Make sure to isolated these traces from other traces, you can use ground plan.
•Power Traces
AC1, AC2, OUT, CLAMP, PGND
Make sure to use the right width for the right current rating.
9.2 Layout Guidelines
• The traces from the input connector to the inputs of the bq5122x IC pin should be as wide as possible
to minimize the impedance in the lines. Otherwise, a voltage drop and thermal issue will be caused.
• Keep the trace resistance as low as possible on AC1, AC2, and OUT.
• Use the appropriate current rating traces (width) on the AC, OUT, CLAMP and GND.
• The PCB should have a ground plane (return) connected directly to the return of all components
through vias (At least two vias per capacitor for power-stage capacitors, one via per capacitor for
small-signal components).
• The dissipation of heat path is important. Adding internal layers increases the thermal performance.
Multiple vias in the PGND pulls of the IC is recommended to decrease the thermal resistance in the
board and allow much easier thermal dissipation through inner layer and power ground layers.
• The via interconnect is important and must be optimized near the power pad of the IC and the GND.
• 2-oz copper or greater is recommended
• For high-current applications, the balls for the power paths should be connected to as much copper in
the board as possible. This allows better thermal performance because the board conducts heat away
from the IC.
• It is always a good practice to place high frequency bypass capacitors next to RECT and OUT.
9.3 Printed-Circuit Board Layout Example
The primary concerns when doing a layout for a custom receiver PCB are as follows:
• AC1 and AC2, GND return trace resistance
• OUT trace resistance
• GND connection
• Copper weight ≥2 oz
For a 1-A fast charge current application, the current rating for each net is as follows:
• AC1 = AC2 = 1.2 A
• BOOT1 = BOOT2 = 1 A
• RECT = 10 mA
• OUT = 1 A
• COMM1 = COMM2 = 300 mA
• CLAMP1 = CLAMP2 = 500 mA
• ILIM = 10 mA
18 Dual Mode (WPC and PMA) Integrated Wireless Receiver Power Supply SLUUAX6B–February 2014–Revised June 2014
Submit Documentation Feedback
Copyright © 2014, Texas Instruments Incorporated

www.ti.com
Layout and Bill of Materials
• AD = AD_EN = TS-CTRL = SCL = SDA = TERM = FOD = 1 mA
• CHG = 10 mA
It is also recommended to have the following capacitance on RECT and OUT:
• RECT ≥10 µF
• OUT ≥1 µF
It is always good practice to place high frequency bypass capacitors next to RECT and OUT of 0.1 μF.
Figure 11 illustrates an example of a WCSP layout.
Figure 11. bq51221EVM-520 Layout Example
19
SLUUAX6B–February 2014–Revised June 2014 Dual Mode (WPC and PMA) Integrated Wireless Receiver Power Supply
Submit Documentation Feedback Copyright © 2014, Texas Instruments Incorporated

Layout and Bill of Materials
www.ti.com
9.4 bq51221EVM-520 Layout
Figure 12 through Figure 16 illustrate the bq51221EVM-520 layout views.
Figure 12. bq51221EVM-520 Top Assembly
Figure 13. bq51221EVM-520 Layer 1
20 Dual Mode (WPC and PMA) Integrated Wireless Receiver Power Supply SLUUAX6B–February 2014–Revised June 2014
Submit Documentation Feedback
Copyright © 2014, Texas Instruments Incorporated
This manual suits for next models
1
Table of contents
Other Texas Instruments Receiver manuals

Texas Instruments
Texas Instruments bq51020EVM User manual
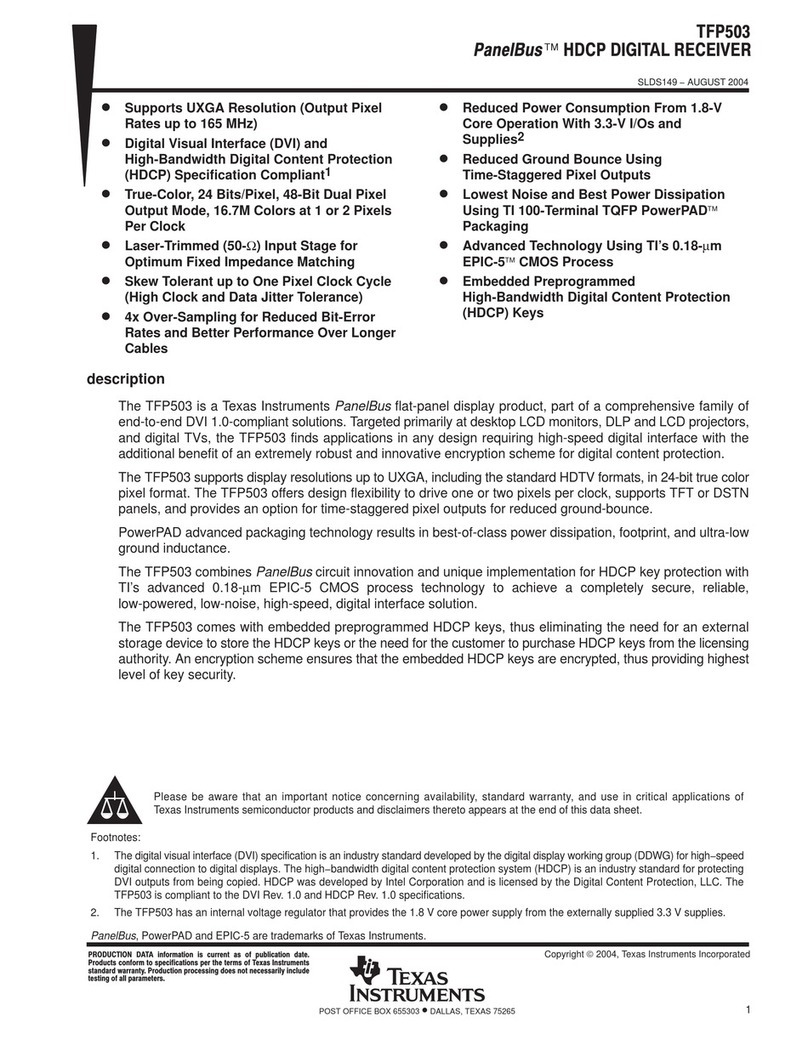
Texas Instruments
Texas Instruments PanelBus TFP503 User manual
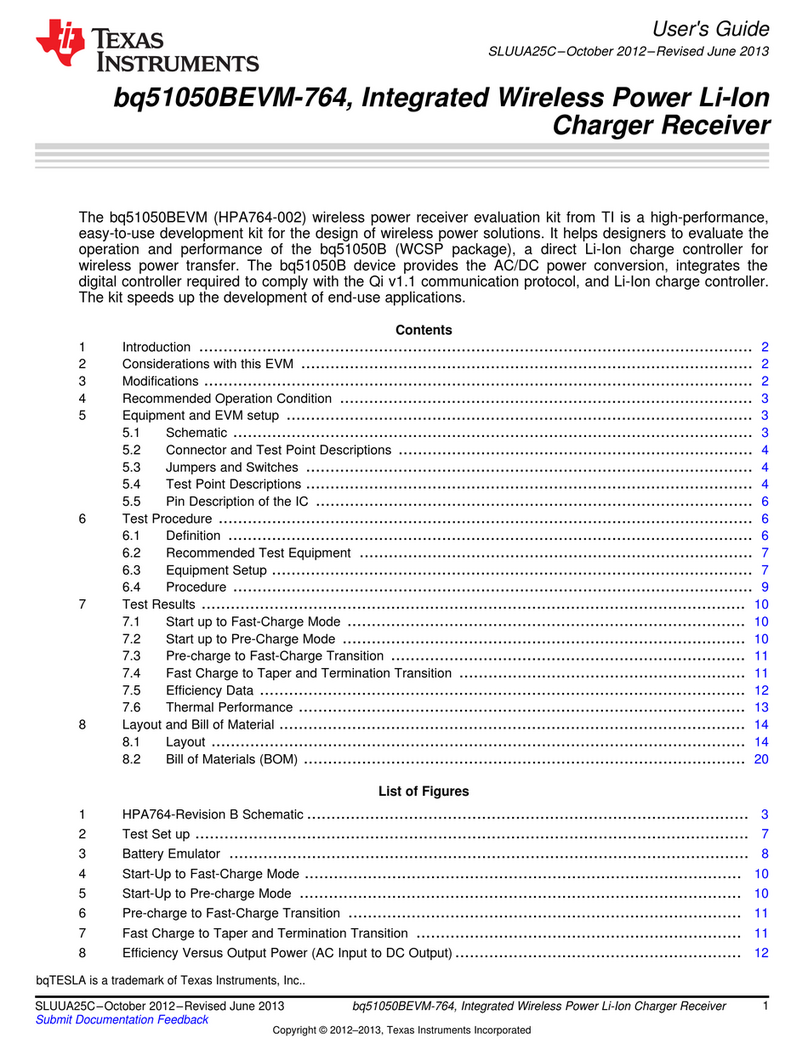
Texas Instruments
Texas Instruments bq51050BEVM-764 User manual
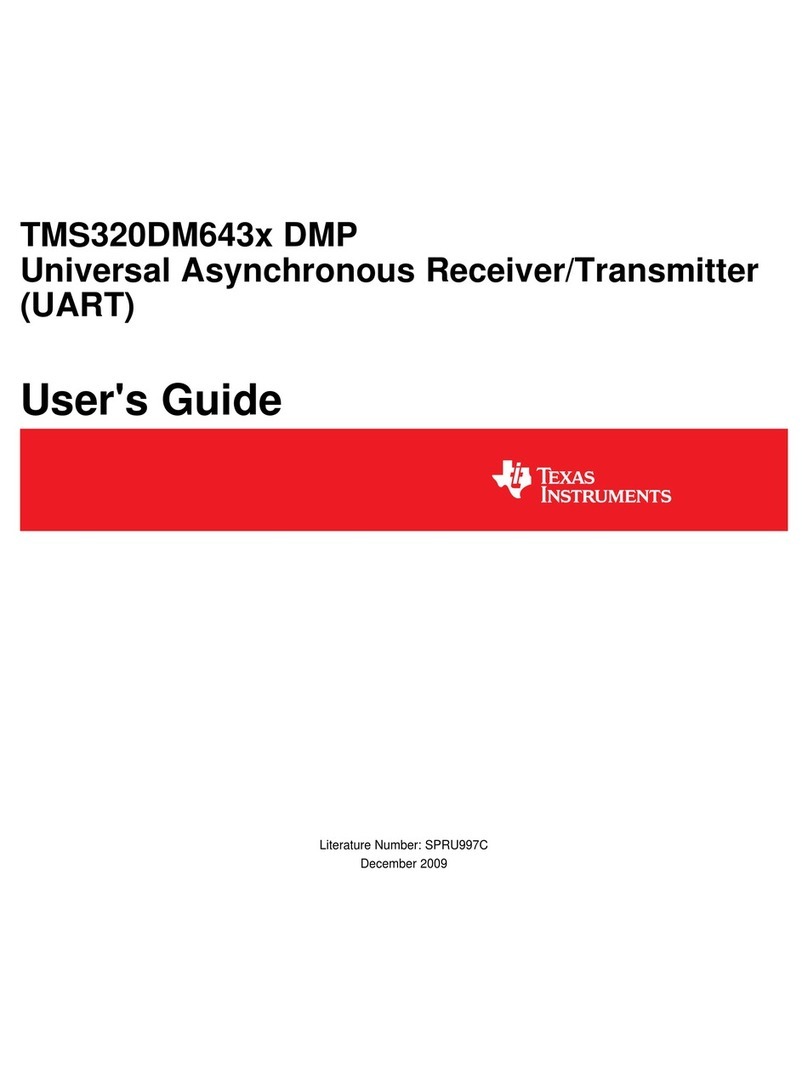
Texas Instruments
Texas Instruments TMS320DM643x User manual
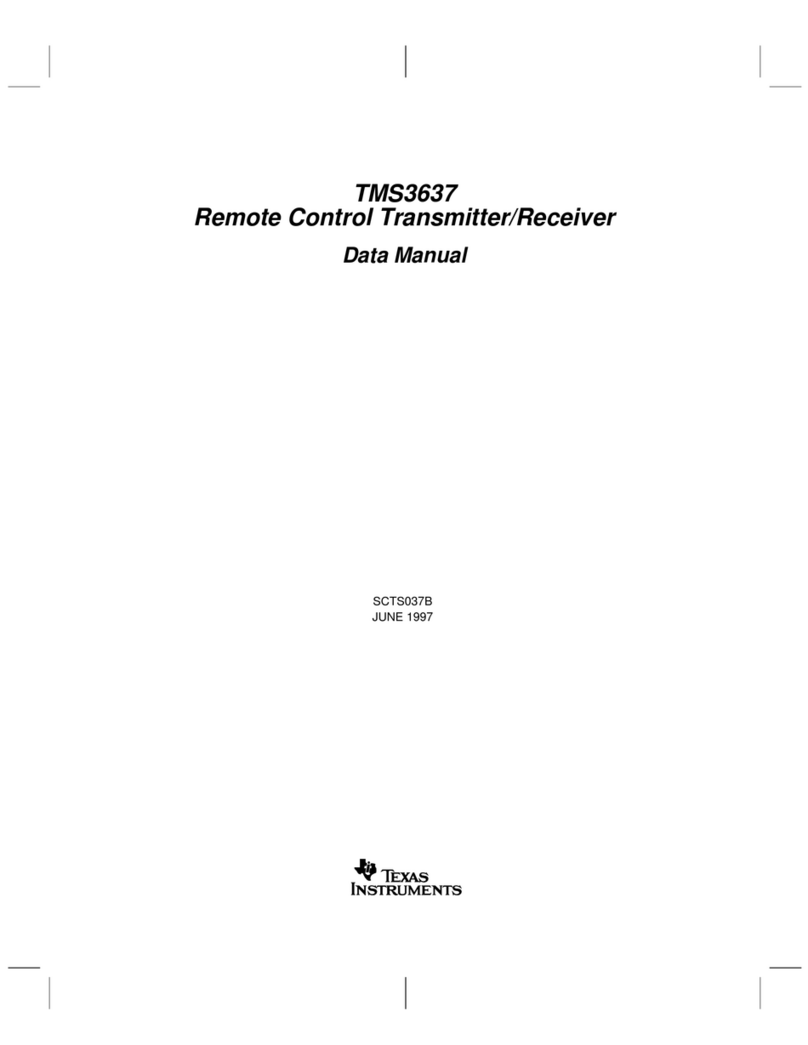
Texas Instruments
Texas Instruments TMS3637 Installation and user guide

Texas Instruments
Texas Instruments TRF1500 Operator's manual
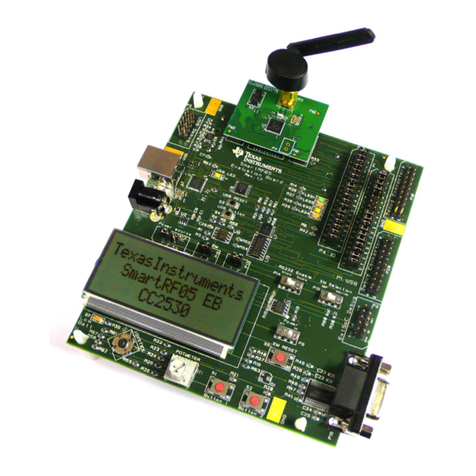
Texas Instruments
Texas Instruments CC2530 ZigBee Development Kit User manual