Texas Instruments bq51020EVM User manual

User's Guide
SLUUB03–April 2014
bq51020EVM (5-W WPC) Integrated Wireless Receiver
Power Supply
The bq51020EVM-520 (PWR520-002) wireless power receiver evaluation kit (EVM) from TI is a high
performance, easy-to-use development kit for the design of wireless power solutions. It helps designers to
evaluate the operation and performance of the bq51020 IC, a secondary-side receiver device for wireless
power transfer in portable applications. The bq51020 device is a fully-contained, wireless power receiver
capable of operating in WPC v1.1 protocol which allows a wireless power system to deliver up to 5 W to
the system when used with a Qi inductive transmitter. The bq51020 device provides a single device power
conversion (rectification and regulation) as well as the digital control and communication for WPC
specification. The kit enables designers to speed up the development of their end-applications.
Contents
1 Introduction ................................................................................................................... 2
2 Considerations with this EVM.............................................................................................. 2
3 Modifications.................................................................................................................. 3
4 Recommended Operation Condition ...................................................................................... 3
5 Equipment and EVM Setup................................................................................................. 4
5.1 Schematic............................................................................................................ 4
5.2 Connector Descriptions ............................................................................................ 5
5.3 Jumpers and Switches............................................................................................. 5
5.4 Test Point Descriptions ............................................................................................ 5
5.5 Pin Description of the IC .......................................................................................... 6
6 Test Procedure............................................................................................................... 6
6.1 Definition............................................................................................................. 6
6.2 Recommended Test Equipment .................................................................................. 7
6.3 Equipment Setup.................................................................................................... 7
6.4 Procedure............................................................................................................ 8
7 Test Results................................................................................................................. 11
7.1 Steady-State Operation with bq2425x Charger .............................................................. 11
7.2 Load Step .......................................................................................................... 12
7.3 Start Up............................................................................................................. 12
7.4 Efficiency Data..................................................................................................... 13
7.5 AD Insertion and Removal ...................................................................................... 13
7.6 Thermal Performance............................................................................................. 14
8 Layout and Bill of Material ................................................................................................ 15
8.1 bq51020 Traces .................................................................................................. 15
8.2 Layout Guidelines ................................................................................................. 15
8.3 Printed-Circuit Board Layout Example ......................................................................... 15
8.4 bq51020EVM-520 Layout ........................................................................................ 17
8.5 Bill of Materials (BOM)............................................................................................ 20
List of Figures
1 bq51020EVM-520 Schematic .............................................................................................. 4
2 bq51020 in Steady State Operation with bq24250 .................................................................... 11
3 Load Step ................................................................................................................... 12
4 Start Up With 500 mA ..................................................................................................... 13
5 System Efficiency Versus Output Power ............................................................................... 13
1
SLUUB03–April 2014 bq51020EVM (5-W WPC) Integrated Wireless Receiver Power Supply
Submit Documentation Feedback Copyright © 2014, Texas Instruments Incorporated

Introduction
www.ti.com
6 Adapter Insertion and Removal .......................................................................................... 14
7 Thermal Image (1000-mA Load) ........................................................................................ 14
8 bq51020EVM-520 Layout Example ..................................................................................... 16
9 bq51020EVM-520 Top Assembly ....................................................................................... 17
10 bq51020EVM-520 Layer 1 ................................................................................................ 17
11 bq51020EVM-520 Layer 2 ................................................................................................ 18
12 bq51020EVM-520 Layer 3 ................................................................................................ 18
13 bq51020EVM-520 Layer 4 ................................................................................................ 19
List of Tables
1 bq51020EVM-520 Electrical Performance Specifications.............................................................. 3
2 Pin Description............................................................................................................... 6
3 bq51020EVM-520 Bill of Materials ...................................................................................... 20
1 Introduction
The bq51020 is an advanced, flexible, secondary-side device for wireless power transfer in portable
applications. The bq51020 device integrates an ultra-low-impedance synchronous rectifier, a very-high-
efficiency post regulator, digital control, and accurate voltage and current loops. The bq51020 devices
provide the AC/DC power conversion while integrating the digital control required. The IC complies with
the WPC v1.1 communication protocol.
Together with the bq500xxx primary-side controller transmitter, the bq51020 enables a complete
contactless power transfer system for a wireless power supply solution. By utilizing near-field inductive
power transfer, the secondary coil embedded in the mobile device can pick up the power transmitted by
the primary coil. The voltage from the secondary coil is then rectified and regulated to be used as a power
supply for down-system electronics. Global feedback is established from the secondary to the primary in
order to control the power transfer process.
A WPC system communication is digital -– packets are transferred from the secondary to the primary.
Differential bi-phase encoding is used for the packets. The bit rate is 2Kbps. Various types of
communication packets have been defined. These include identification and authentication packets, error
packets, control packets, power usage packets and efficiency packets, among others.
2 Considerations with this EVM
The bq51020EVM-520 evaluation module (PWR520-002) demonstrates the receiver portion of the
wireless power system. This receiver EVM is a complete receiver-side solution that produces 5-W output
power at up to 1-A load with adjustable output voltage.
• The receiver can be used in any number of low-power battery portable devices as a power supply for a
battery charger. With contact-free charging capability, no connections to the device are needed.
• Highly-integrated wireless power receiver solution
– Ultra-efficient synchronous rectifier
– Very-high efficiency post regulator
– WPC v1.1-compliant communication and control
– Only one IC required between RX coil and DC output
• Programmable output voltage to optimize performance for application
• Adaptive Communication current limit (CM_ ILIM) for robust communication.
• Supports 20-V max input
• Low-power dissipative overvoltage clamp
• Overvoltage, overcurrent, overtemperature protection
• Low-profile, external pick-up coil
• Frame is configured to provide correct receiver to transmitter spacing
2bq51020EVM (5-W WPC) Integrated Wireless Receiver Power Supply SLUUB03–April 2014
Submit Documentation Feedback
Copyright © 2014, Texas Instruments Incorporated

www.ti.com
Modifications
• Room above coil for testing with battery, key for Foreign Object Detection (FOD) tuning
• Options to adjust the input current limit and output voltage using resistors
• Flexibility for Foreign Object Detection (FOD) tuning
• Adjustable resistor that can be used to set RFOD
• Temperature sensing can be adjusted using external resistors
• Micro-USB connector for adapter testing configuration
• WPG LED indicator (turns on as VOUT goes high)
• PD_DET LED indicator --turns on as the RX is on TX pad
3 Modifications
See the data sheet (SLUSBX1) when changing components. To aid in such customization of the EVM, the
board was designed with devices having 0402 and 0603 or larger footprints. A real implementation likely
occupies less total board space.
Note that changing components can improve or degrade EVM performance.
4 Recommended Operation Condition
Table 1 provides a summary of the bq51020EVM-520 performance specifications. All specifications are
given for an ambient temperature of 25°C.
Table 1. bq51020EVM-520 Electrical Performance Specifications
PARAMETER TEST CONDITION MIN TYP MAX UNIT
VIN RECT input voltage range 4.0 10.0 V
IAD_EN_sink Sink current 1 mA
IIN Input current range 1.5 A
IOUT Output current range Current limit programming range 1.5 A
VOUT(REG) Programmable output voltage(1) POUT = 5 W 4.5 8 V
fsSwitching frequency WPC 110 205 kHz
TJJunction temperature 125 °C
(1) The output voltage can be adjusted using VOUT(REG) resistors. Also the coil needs to change for different voltage for optimal
operation of the EVM.
3
SLUUB03–April 2014 bq51020EVM (5-W WPC) Integrated Wireless Receiver Power Supply
Submit Documentation Feedback Copyright © 2014, Texas Instruments Incorporated

GND
1800pF
C4
0.068µF
C2
0.068µF
C1
BOOT1
RECTBOOT2
BOOT2
OUT
BOOT1
CLMP1
AD
FOD
VTSB/VIREG
CLMP2
COMM1
AD_EN
/WPG
COMM2
VO_REG
CM_ILIM
TS
CLMP1
0.47µF
C9
0.47µF
C12
CLMP2
COMM2
COMM1 GND
GND
VO_REG
1
2
J5
GND
0.1µF
C19
GND
TS
GND
VTSB/VIREG
TP1
DNP
TP2
DNP
2.00k
R13
DNP
GND
1.50k
R7
RECT
/WPG
GND
GND
0.1µF
C18
150
R2
FOD
TP5
1
2
3
JP1
110
R4
TP4
ADJ
TS
GND
ILIM
FIX
RECT
56.2k
R1
1
2
J3
1
2
J4
1
2
3
JP2
GND
CM_ILIM
High
Low
CM_ILIM
GND
GND
0.1µF
C16
TP3
GND
GND
0.1µF
C6
OUT
GNDGND
AD_EN
Rect
1µF
C17
GND
GND
GND
Out
ILIM
FOD
AC1
AC2
Orange
D2
Green
D1
1
2
3
4
5
6
7
8
9
10
11
J1
1 2
3 4
5 6
7 8
9 10
J2
GND
Q1
CSD75301W1015
OUT
AD
GND
20k
R15
10.0k
R11
5.11k
R16
0.047uF
C3
100pF
C5
10µF
C14
10µF
C15
1µF
C20
0
R3
OUT
0.015µF
C10
0.015µF
C11
0.022µF
C8
0.022µF
C13
3.3µF
C7
1.50k
R20
DNP
Green
D3
DNP
GND
102k
R17
DNP
102k
R14
11.3k
R18
DNP
11.3k
R10
102k
R19
DNP
5.6Meg
R12
27k
R21
DNP
100pF
C22
DNP
GND
PGND
A1
PGND
A2
PGND
A3
PGND
A4
PGND
A5
PGND
A6
AC1
B1
AC1
B2
AC1
B3
AC2
B4
AC2
B5
AC2
B6
BOOT1
C1
RECT
C2
RECT
C3
RECT
C4
RECT
C5
BOOT2
C6
OUT
D1
OUT
D2
OUT
D3 OUT D4
OUT D5
OUT D6
CLAMP1 E1
AD E2
AD_EN E3
EN1/SCL E4
VIREG E5
CLAMP2 E6
COMM1 F1
FOD F2
LPRBEN and TERM F3
EN2/SDA F4
LPRB1 and WPG F5
COMM2 F6
VO_REG G1
ILIM G2
CM_ILIM G3
TS G4
TMEM G5
LPRB2 and PD_DET G6
U1
bq51020
2.2µF
C21
200
R9
200
R8
5 K
R5
DNP
500 Ohm
R6
1
2
3
JP3
1
2
3
JP4
TP6
Ext
GND
GND
Hi
Low
Hi
Low
EN1
EN2
102k
R22
5.1V
D4
BZT52C5V1T-7
GND
Equipment and EVM Setup
www.ti.com
5 Equipment and EVM Setup
5.1 Schematic
Figure 1 shows the bq51020 schematic.
Figure 1. bq51020EVM-520 Schematic
4bq51020EVM (5-W WPC) Integrated Wireless Receiver Power Supply SLUUB03–April 2014
Submit Documentation Feedback
Copyright © 2014, Texas Instruments Incorporated

www.ti.com
Equipment and EVM Setup
5.2 Connector Descriptions
The connections points are described in the following paragraphs.
5.2.1 J1 – AD External Adapter Input
Power can be provided to simulate an external adapter applied to the receiver in this bq51020EVM-520
(PWR520-002).
5.2.2 J2 – Programming Connector
This connector is populated and is for factory use only
5.2.3 J3 – Output Voltage
Output voltage in wireless power mode up to 1 A; the adapter option is also supported in this PWR520-
002.
5.2.4 J4 –GND
Ground return
5.2.5 J5 – TS/CTRL and Return Connector
External connection for temperature sense resistor, see data sheet for additional information. Not
populated in this spin.
5.3 Jumpers and Switches
The control jumpers are described in the following paragraphs.
5.3.1 JP1– ILIM (FIX or ADJ)
Maximum output current is set by the ILIM pin. In the FIX position, the current is set to a fixed value of R4
plus RFOD. In the ADJ position, current is set by R5. Note that R5 is not populated in this EVM.
5.3.2 JP2 – CM_ILIM
Enables CM_ILIM feature when pulled low and disable when pulled up.
5.3.3 JP3 – EN1 (Low and High)
EN1 pin, set High using external power supply connected to TP6 .
5.3.4 JP4 – EN2 (Low and High)
EN2 pin, set High using external power supply connected to TP6.
5.4 Test Point Descriptions
The test points are described in the following paragraphs.
5.4.1 TP1 and TP2 – AC1 and AC2 Inputs
This are not populated, they can be used for measuring AC voltage applied to the EVM from the receiver
coil.
5.4.2 TP3– Rectified Voltage
The input AC voltage is rectified into unregulated DC voltage (VRECT); additional capacitance is used to
filter the voltage before the regulator.
5
SLUUB03–April 2014 bq51020EVM (5-W WPC) Integrated Wireless Receiver Power Supply
Submit Documentation Feedback Copyright © 2014, Texas Instruments Incorporated

Equipment and EVM Setup
www.ti.com
5.4.3 TP4– ILIM
Programming pin for overcurrent limit protection, pin G2 of the IC.
5.4.4 TP5 – FOD
Input for rectified power measurement for FOD feature in WPC, pin F2 of the IC. TP5 is the FOD pin for
the bq51020.
5.4.5 TP6 – Ext
Connect to 5-V external power supply. Used to pull EN1 and EN2 high. Any voltage level above 7 V may
damage the IC.
5.5 Pin Description of the IC
Table 2. Pin Description
PIN Number (WCSP) bq51020
A1, A2, A3, A4, A5, A6 PGND
B1, B2, B3 AC1
B4, B5, B6 AC2
C1 BOOT1
C2, C3, C4, C5 RECT
C6 BOOT2
D1, D2, D3, D4, D5, D6 OUT
E1 CLAMP1
E2 AD
E3 AD_EN
E4 EN1
E5 VTSB
E6 CLAMP2
F1 COMM1
F2 FOD
F3 TERM
F4 EN2
F5 WPG
F6 COMM2
G1 VO_REG
G2 ILIM
G3 CM_ILIM
G4 TS/CTRL
G5 TMEM
G6 PD_DET
6 Test Procedure
This procedure describes test configuration of the bq51020EVM-520 evaluation board (PWR520-002) for
bench evaluation.
6.1 Definition
The following naming conventions are followed.
6bq51020EVM (5-W WPC) Integrated Wireless Receiver Power Supply SLUUB03–April 2014
Submit Documentation Feedback
Copyright © 2014, Texas Instruments Incorporated

www.ti.com
Test Procedure
VXXX : External voltage supply name (VADP, VTS, VOUT)
LOADW: External load name (LOADR, LOADI)
V(TPyy): Voltage at internal test point TPyy. For example, V(TP02) means the voltage at TP02.
V(Jxx): Voltage at header Jxx
V(TP(XXX)): Voltage at test point XXX. For example, V(ACDET) means the voltage at the test
point which is marked as ACDET.
V(XXX, YYY): Voltage across point XXX and YYY.
I(JXX(YYY)): Current going out from the YYY terminal of header XX.
Jxx(BBB): Terminal or pin BBB of header xx.
JPx ON : Internal jumper Jxx terminals are shorted.
JPx OFF: Internal jumper Jxx terminals are open.
JPx (-YY-) ON: Internal jumper Jxx adjacent terminals marked as YY are shorted.
Assembly drawings have locations for jumpers, test points, and individual components.
6.2 Recommended Test Equipment
The following equipment is needed to complete this test procedure:
Power Supplies
• Power Supply #1 (PS #1) capable of supplying 19 V at 1 A is required
• Power Supply #2 (PS #2) capable of supplying 5 V at 1 A is required
• Power Supply #3 (PS #3) capable of supplying 5 V at 1 A is required
Loads
• A resistive load or electronic load that can be set to 5 Ω/1000 mA, 10 Ω/500 mA, and 5 kΩ/1 mA. The
power rating should be 5 W.
Meters
• Two DC voltmeters and two DC ammeters
Oscilloscopes
• Not required
bqTesla Transmitter
• The HPA689 transmitter or equivalent is used for the final test.
Recommended Wire Gauge
• For proper operation, TI recommends 22-AWG wire.
6.3 Equipment Setup
The following items ensure proper equipment setup:
Test Set Up
• The final assembly will be tested using a bqTesla transmitter – provided (HPA689). Input voltage to the
transmitter is set to 19 VDC ±200 mV, with a current limit of 1.0 A.
• Connect power supply to J1 and J2 of the transmitter, HPA689
• Set power supply to OFF
• Place unit under test (UUT) on the transmitter coil
• UUT will be placed in the center of the HPA689 TX coil. Other bqTesla transmitter base units are also
acceptable for this test (ensure the correct input voltage is applied).
Load
• The load is connected between J3-OUT and J4-GND of the UUT
7
SLUUB03–April 2014 bq51020EVM (5-W WPC) Integrated Wireless Receiver Power Supply
Submit Documentation Feedback Copyright © 2014, Texas Instruments Incorporated
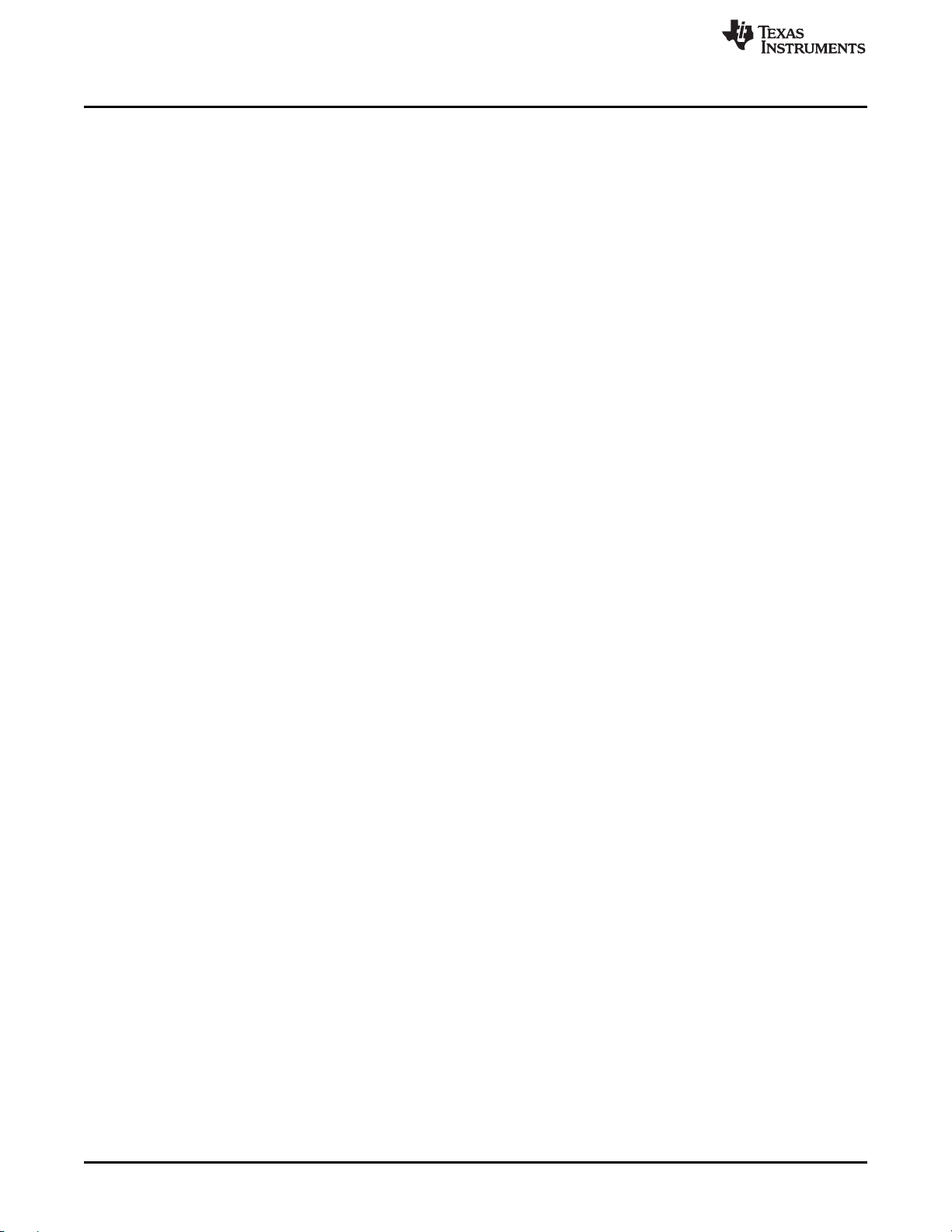
Test Procedure
www.ti.com
• A DC ammeter is connected between UUT and load
• Set the load for 5 Ω/1000 mA
Jumper Settings
• JP1 →ILIM and FIX are shorted
• JP2 →CM_ILM and High are shorted
• JP3 →EN1 and Low are shorted
• JP4 →EN2 and Low are shorted
Voltage and Current Meters
• Connect the ammeter to measure 19-V input current to the transmitter. Connect the voltmeter to
monitor the input voltage at J1 and J2 of TX unit. On UUT a voltmeter is used to measure output
voltage at J3 with ground at J4. Connect the ammeter to measure load current.
RFOD: R6 Set Up
• Connect the ohmmeter between JP5 (FOD) and J4 (GND). Adjust R6 to a 495 Ωreading on the
ohmmeter.
•NOTE: Sometimes the multimeter cannot read the more than 430 Ωfrom the FOD resistor due to
charged up capacitors in the board. If that happens, use a twizer and short C15 for few seconds, then
measure again.
6.4 Procedure
The following operating procedures are provided at a variety of operating loads:
Turn ON Operation and Operation at 1000-mA Load
• Turn ON transmitter power supply (19 V)
• Transmitter – Verify LED D2 is ON
• UUT – Adjust load current to 1000 mA ±50 mA
• Put the receiver EVM on the transmitter coil and align them correctly
• After 5 seconds verify that:
– Transmitter – Status LED D5 should be green, flashing approximately every 1 second
– The transmitter should beep
– Transmitter – LED D2 still ON
– Receiver – LED D1 is ON
– UUT – Verify that VOUT is 4.9 V to 5.15 V (between J3 and J4)
– UUT – Verify that the rectified voltage is 5 V to 5.4 V (between TP3 and GND) NOTE: a modulation
signal is present on this voltage every 250 ms and may cause fluctuation in the reading: use lower
value or baseline.
Efficiency Test (1000-mA Load)
• Verify that input current to the TX is less than 500 mA with input voltage at 19 VDC
• Turn OFF the transmitter power supply (19 V)
Turn ON Operation and Operation at 500-mA Load
• Turn ON the transmitter power supply (19 V)
• Transmitter – Verify LED D2 is ON
• UUT – Adjust load current to 500 mA ±50 mA
• Put the receiver EVM on the transmitter coil and align them correctly
• After 5 seconds verify that:
– Transmitter – Status LED D5 should be green, flashing approximately every 1 second.
– The transmitter should beep
– Transmitter – LED D2 still ON
8bq51020EVM (5-W WPC) Integrated Wireless Receiver Power Supply SLUUB03–April 2014
Submit Documentation Feedback
Copyright © 2014, Texas Instruments Incorporated

www.ti.com
Test Procedure
– Receiver – LED D1 is ON
– UUT – Verify that VOUT is 4.9 V to 5.2 V (between J3 or TP7 and J4)
– UUT – Verify that the rectified voltage is 5 V to 5.4 V (between TP3 and GND) NOTE: a modulation
signal is present on this voltage every 250 ms and may cause fluctuation in the reading: use lower
value or baseline.
Efficiency Test (500-mA Load)
• Verify that input current to the TX is less than 260 mA with an input voltage at 19 VDC
• Turn OFF the transmitter power supply (19 V)
Operation (1-mA Load)
• Turn ON the transmitter power supply (19 V)
• Transmitter – Verify LED D2 is ON
• UUT – Adjust load current to 1 mA ±200 µA
• Put the receiver EVM on the transmitter coil and align them correctly
• After 5 seconds verify that:
– Transmitter – Status LED D5 should be green, flashing approximately every 1 second.
– The transmitter should beep
– Transmitter – LED D2 still ON
– Receiver – LED D1 is ON
– UUT – Verify that VOUT is 4.9 V to 5.2 V (between J3 and J4)
– UUT – Verify that the rectified voltage is 6.9 V to 8.6 V (between TP3 and GND) NOTE: a
modulation signal is present on this voltage every 250 ms and may cause fluctuation in the reading:
use lower value or baseline.
Efficiency Test (1-mA Load)
• Verify that input current to the TX is less than 80 mA with input voltage at 19 VDC
• Turn OFF the transmitter power supply (19 V)
• Remove UUT from transmitter
Adapter Test (500-mA Load)
• Connect 5 V ±250 mV adapter on J1 on the bq51020EVM-520 receiver
• Adjust the load current to 500 mA ±50 mA (J3 OUT and J4 GND)
• Verify that:
1. UUT – LED D1 is OFF
2. UUT – VOUT is 5.0 V ±600 mV (J3)
3. Transmitter – Status LED D5 is OFF
4. Put external +5 V power supply to TP6 (Ext) and GND (J4)
5. Set the EN1 and EN2 jumper as follows:
• JP3: EN1 and Low are shorted
• JP4: EN2 and High are shorted
6. Put the receiver EVM on the transmitter coil and align them correctly while still having the adapter
connected to J1 and the external +5 V on TP6.
• After 5 seconds verify that:
– Transmitter – Status LED D5 should be green, flashing approximately every 1 second.
– The transmitter should beep
– Transmitter – LED D2 is still ON
– Receiver – LED D1 is ON
– UUT – Verify that VOUT is 4.9 V to 5.2 V (between J3 and J4)
– UUT – Verify that the rectified voltage is 5V to 5.6V (between TP3 and GND). NOTE: a
9
SLUUB03–April 2014 bq51020EVM (5-W WPC) Integrated Wireless Receiver Power Supply
Submit Documentation Feedback Copyright © 2014, Texas Instruments Incorporated

Test Procedure
www.ti.com
modulation signal is present on this voltage every 250 ms and may cause fluctuation in the
reading: use lower value or baseline.
– This disables wired power and prioritizes wireless power
7. Set the EN1 and EN2 jumper as follows:
• JP3: EN1 and High are shorted
• JP4: EN2 and High are shorted
8. Put the receiver EVM on the transmitter coil and align them correctly while still having the adapter
connected to J1 and the external 5 V on TP6.
9. Verify that:
• UUT – LED D1 is OFF
• UUT – VOUT is 0 V ±600 mV (J3)
• Transmitter – Status LED D5 is ON
• This means both wired and wireless power are disabled
10 bq51020EVM (5-W WPC) Integrated Wireless Receiver Power Supply SLUUB03–April 2014
Submit Documentation Feedback
Copyright © 2014, Texas Instruments Incorporated

www.ti.com
Test Results
7 Test Results
7.1 Steady-State Operation with bq2425x Charger
With the power supply off, connect the supply to the bqTESLA transmitter.
• Set up the test bench as described in Section 6.
• Power TX with 19 V.
• Connect the output of RX to a battery charger (bq24250) to charge a battery.
• Set the VBAT to 3.8 V.
• Set the charger current to 1.2 A.
• Set input current limit on the charger to 1 A.
• Monitor the IOUT and VOUT from the RX after putting the receiver EVM on the transmitter coil and align
them correctly.
•Figure 2 shows the VOUT and IOUT from the RX as the battery charges.
Figure 2. bq51020 in Steady State Operation with bq24250
11
SLUUB03–April 2014 bq51020EVM (5-W WPC) Integrated Wireless Receiver Power Supply
Submit Documentation Feedback Copyright © 2014, Texas Instruments Incorporated
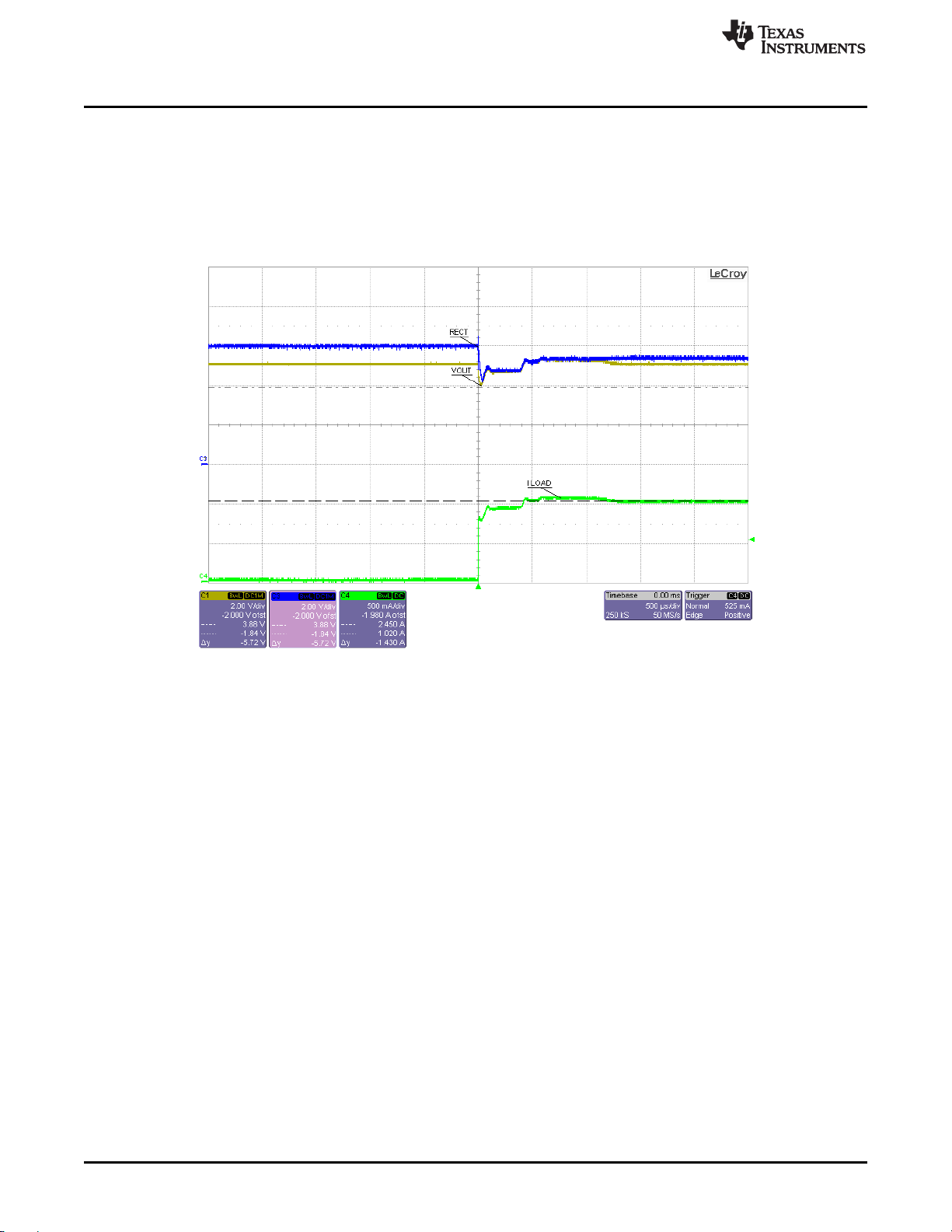
Test Results
www.ti.com
7.2 Load Step
The procedure for load step is as follows:
• Set up the test bench as described in Section 6.
• Power WPC TX (bq500210) with 19 V.
• Provide a load step from no-load (high impedance) to 1000 mA (if using current source load).
• Monitor on side RX: load current, rectifier voltage, and output voltage as shown in Figure 3.
Figure 3. Load Step
7.3 Start Up
The procedure for start-up test with load:
• Set up the test bench as described in Section 6.
• Power the WPC TX
• Apply 10 Ωacross J3 and J4, put the receiver EVM on the transmitter coil, and align them correctly
• Monitor the RECT pin, IOUT, and output voltage, as shown in Figure 4.
12 bq51020EVM (5-W WPC) Integrated Wireless Receiver Power Supply SLUUB03–April 2014
Submit Documentation Feedback
Copyright © 2014, Texas Instruments Incorporated

20
30
40
50
60
70
80
90
100
0 1000 2000 3000 4000 5000
Efficiency (%)
Power (mW)
TX-bq500211A
TX-bq500212A
C001
www.ti.com
Test Results
Figure 4. Start Up With 500 mA
7.4 Efficiency Data
7.4.1 Efficiency Versus Output Power (AC-DC)
Figure 5 illustrates the system (DC-DC) efficiency of the bq51020EVM-520 under different transmitters.
Figure 5. System Efficiency Versus Output Power
7.5 AD Insertion and Removal
Figure 6 illustrates the behavior of the bq51020EVM-520 when the AD is inserted while the EVM is on the
transmitter pad. There is some off time during the transition between wireless power and wired power
modes.
13
SLUUB03–April 2014 bq51020EVM (5-W WPC) Integrated Wireless Receiver Power Supply
Submit Documentation Feedback Copyright © 2014, Texas Instruments Incorporated

Test Results
www.ti.com
Figure 6. Adapter Insertion and Removal
7.6 Thermal Performance
This section shows a thermal image of the bq51020EVM-520. A 1-A load is used and the output voltage is
set to 5 V. There is no air flow and the ambient temperature is 25°C. The peak temperature of the device
(39°C in WPC) is well below the maximum recommended operating condition listed in the data sheet.
Figure 7. Thermal Image (1000-mA Load)
14 bq51020EVM (5-W WPC) Integrated Wireless Receiver Power Supply SLUUB03–April 2014
Submit Documentation Feedback
Copyright © 2014, Texas Instruments Incorporated

www.ti.com
Layout and Bill of Material
8 Layout and Bill of Material
8.1 bq51020 Traces
The bq51020 device pins can be classified as follows:
•Signal/Sensing Traces
– TS/CTRL, EN1, EN2, PD_DET, WPG, COMM, ILIM, AD, ADEN, FOD, TMEM, CM_ILIM, VO_REG,
VTSB, Term.
– Make sure these traces are not interfered by the noisy traces
•Noisy Traces
– AC1, AC2, BOOT, COMM
– Make sure these traces are isolated from other traces, use ground plan
•Power Traces
– AC1, AC2, OUT, CLAMP, PGND
– Make sure to use the correct width for the right current rating.
8.2 Layout Guidelines
Use the following layout guidelines:
• The traces from the input connector to the inputs of the bq51020 IC pin should be as wide as possible
to minimize the impedance in the lines. Otherwise, this causes a voltage drop and thermal issue.
• Keep the trace resistance as low as possible on AC1, AC2, OUT, and PGND.
• Use the appropriate current rating traces (width) the AC, OUT and PGND.
• The PCB should have a ground plane (return) connected directly to the return of all components
through vias (At least two vias per capacitor for power-stage capacitors, one via per capacitor for
small-signal components).
• The dissipation of heat path is important. Adding internal layers increases the thermal performance.
Multiple vias in the PGND pins of the IC is recommended to decrease the thermal resistance in the
board and allow much easier thermal dissipation through inner layer and power ground layers.
• The via interconnect is important and must be optimized near the power pad of the IC and the GND.
• 2-oz copper, or greater, is recommended
• For high-current applications, the balls for the power paths should be connected to as much copper in
the board as possible. This allows better thermal performance because the board conducts heat away
from the IC.
• It is always good practice to place high frequency bypass capacitors next to RECT and OUT.
8.3 Printed-Circuit Board Layout Example
The primary concerns when laying a custom receiver PCB are as follows:
• AC1 and AC2, GND return trace resistance
• OUT trace resistance
• GND connection
• Copper weight ≥2 oz
For a 1-A fast charge current application, the current rating for each net is as follows:
• AC1 = AC2 = 1.2 A
• BOOT1 = BOOT2 = 1 A
• RECT = 50 mA
• OUT = 1 A
• COMM1 = COMM2 = 300 mA
• CLAMP1 = CLAMP2 = 500 mA
15
SLUUB03–April 2014 bq51020EVM (5-W WPC) Integrated Wireless Receiver Power Supply
Submit Documentation Feedback Copyright © 2014, Texas Instruments Incorporated

Layout and Bill of Material
www.ti.com
• ILIM = 10 mA
• AD = AD_EN = TS/CTRL = EN1 = EN2 = TERM = FOD = 1 mA
• PWR = 10 mA
TI also recommends having the following capacitance on RECT and OUT:
• RECT ≥10 μF
• OUT ≥1μF
It is always good practice to place high-frequency bypass capacitors next to RECT and OUT of 0.1 μF.
Figure 8 illustrates an example of a WCSP layout:
Figure 8. bq51020EVM-520 Layout Example
16 bq51020EVM (5-W WPC) Integrated Wireless Receiver Power Supply SLUUB03–April 2014
Submit Documentation Feedback
Copyright © 2014, Texas Instruments Incorporated

www.ti.com
Layout and Bill of Material
8.4 bq51020EVM-520 Layout
Figure 9 through Figure 13 show the bq51020EVM-520 PCB layout.
Figure 9. bq51020EVM-520 Top Assembly
Figure 10. bq51020EVM-520 Layer 1
17
SLUUB03–April 2014 bq51020EVM (5-W WPC) Integrated Wireless Receiver Power Supply
Submit Documentation Feedback Copyright © 2014, Texas Instruments Incorporated

Layout and Bill of Material
www.ti.com
8.5 Bill of Materials (BOM)
Table 3 lists the BOM for the EVM.
Table 3. bq51020EVM-520 Bill of Materials
Designator Qty Value Description Package Part Number Manufacturer
Reference
!PCB 1 Printed Circuit Board PWR520 Any
C1, C2 2 0.068µF CAP CER 0.068UF 50V 10% X7R 0603 0603 GRM188R71H683KA93D MuRata
C3 1 0.047uF CAP CER 0.047UF 50V 10% X7R 0603 0603 GRM188R71H473KA61D MuRata
C4 1 1800pF CAP CER 1800PF 50V 10% X7R 0603 0603 GRM188R71H182KA01D MuRata
C5 1 100pF CAP, CERM, 100pF, 50V, +/-10%, X7R, 0402 0402 CC0402KRX7R9BB101 Yageo America
C6 1 0.1uF CAP, CERM, 0.1uF, 50V, +/-10%, X7R, 0402 0402 C1005X7R1H104K050BB TDK
C7 1 3.3uF CAP, CERM, 3.3uF, 25V, +/-10%, X5R, 0603 0603 C1608X5R1E335K080AC TDK
C8, C13 2 0.022uF CAP CER 0.022UF 25V 10% X7R 0603 0603 C0603C223K3RACTU Kemet
C9, C12 2 0.47uF CAP, CERM, 0.47uF, 25V, +/-10%, X5R, 0603 0603 GRM188R61E474KA12D MuRata
C10, C11 2 0.015uF CAP, CERM, 0.015uF, 50V, +/-10%, X7R, 0402 0402 GRM155R71H153KA12D MuRata
C14, C15 2 10uF CAP, CERM, 10uF, 25V, +/-10%, X5R, 0805 0805 C2012X5R1E106K125AB TDK
C16, C19 2 0.1uF CAP, CERM, 0.1uF, 50V, +/-10%, X7R, 0603 0603 GCM188R71H104KA57B MuRata
C17 1 1uF CAP, CERM, 1uF, 50V, +/-10%, X7R, 0805 0805 GRM21BR71H105KA12L MuRata
C18 1 0.1uF CAP, CERM, 0.1uF, 16V, +/-10%, X7R, 0402 0402 GRM155R71C104KA88D MuRata
C20 1 1uF CAP, CERM, 1uF, 25V, +/-10%, X7R, 0603 0603 GRM188R71E105KA12D MuRata
C21 1 2.2uF CAP, CERM, 2.2uF, 16V, +/-10%, X5R, 0603 0603 GRM188R61C225KE15D MuRata
D1 1 Green LED, Green, SMD 1.6x0.8x0.8mm LTST-C190GKT Lite-On
D2 1 Orange LED, Orange, SMD 1.6x0.8x0.8mm LTST-C190KFKT Lite-On
D4 1 5.1V Diode, Zener, 5.1V, 300mW, SOD-523 SOD-523 BZT52C5V1T-7 Diodes Inc.
H1 1 Tape segment, Low Static Polyimide Film. Cut tape section from 36 yard roll 1.5" x 2.3" 5419-1 1/2" 3M
H2 1 Case Modified Polycase LP-11B with 4 screws J-6838A Polycase
H3 1 Coil, RX with Attractor IWAS4832FFEB9R7J50 Vishay
H4, H5, H6, H7 4 #4 x 3/8" pan head phillips screw #4 x 3/8" PSMS 004 0038 PH BandF Fastener
H8, H9, H10, H11 4 Spacer, 0.100" Thk x 0.25" OD x 0.147" ID 0.1" THK 905-100 Bivar
J1 1 Receptacle, Micro-USB-B, Right Angle, SMD Micro USB receptacle 105017-0001 Molex
J2 1 Connector, 100mil Shrouded, High-Temperature, Gold, TH 5x2 Shrouded header N2510-6002-RB 3M
J3, J4, J5 3 Header, 100mil, 2x1, Tin plated, TH Header, 2 PIN, 100mil, PEC02SAAN Sullins Connector
Tin Solutions
JP1, JP2, JP3, JP4 4 Header, 100mil, 3x1, Tin plated, TH Header, 3 PIN, 100mil, PEC03SAAN Sullins Connector
Tin Solutions
LBL1, LBL2 2 Thermal Transfer Printable Labels, 0.650" W x 0.200" H - 10,000 per roll PCB Label 0.650"H x THT-14-423-10 Brady
0.200"W
Q1 1 -20V MOSFET, P-CH, -20V, -1.2A, 2x3 DSBGA 2x3 DSBGA CSD75301W1015 Texas Instruments
R1 1 56.2k RES, 56.2k ohm, 1%, 0.063W, 0402 0402 CRCW040256K2FKED Vishay-Dale
R2 1 150 RES, 150 ohm, 5%, 0.063W, 0402 0402 CRCW0402150RJNED Vishay-Dale
R3 1 0 RES, 0 ohm, 5%, 0.063W, 0402 0402 CRCW04020000Z0ED Vishay-Dale
R4 1 110 RES, 110 ohm, 1%, 0.063W, 0402 0402 CRCW0402110RFKED Vishay-Dale
20 bq51020EVM (5-W WPC) Integrated Wireless Receiver Power Supply SLUUB03–April 2014
Submit Documentation Feedback
Copyright © 2014, Texas Instruments Incorporated
Table of contents
Other Texas Instruments Receiver manuals
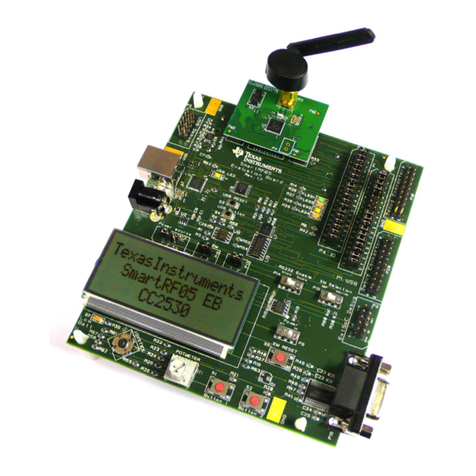
Texas Instruments
Texas Instruments CC2530 ZigBee Development Kit User manual
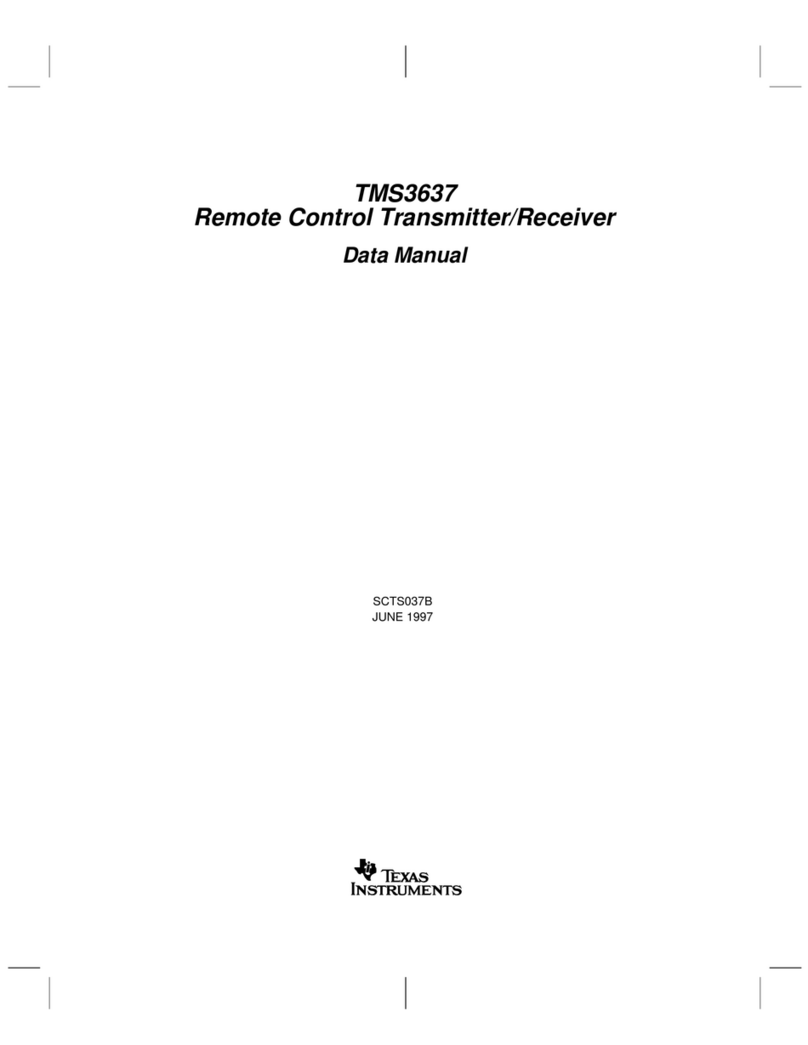
Texas Instruments
Texas Instruments TMS3637 Installation and user guide
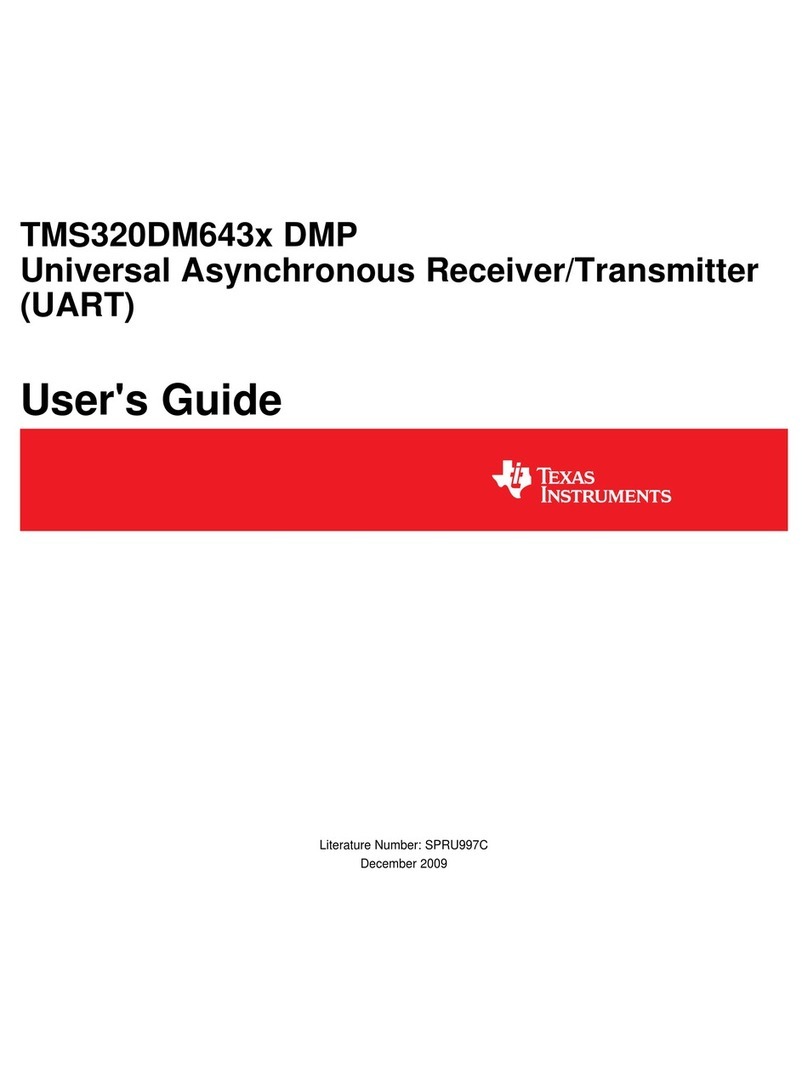
Texas Instruments
Texas Instruments TMS320DM643x User manual
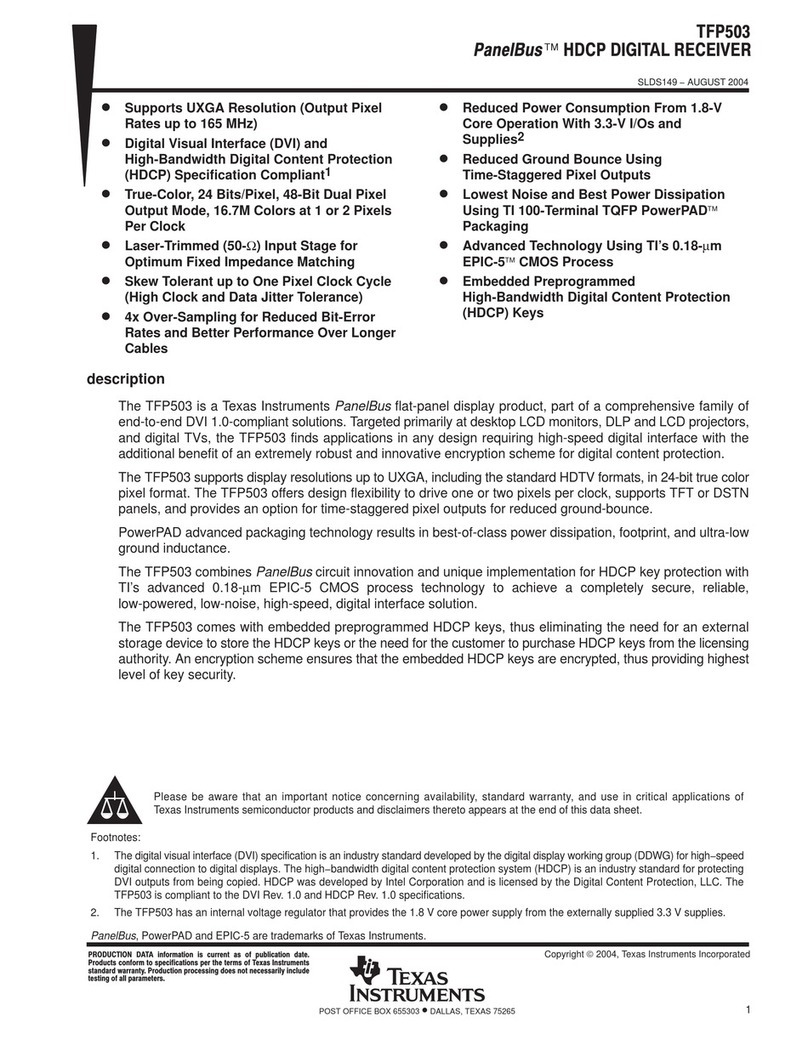
Texas Instruments
Texas Instruments PanelBus TFP503 User manual
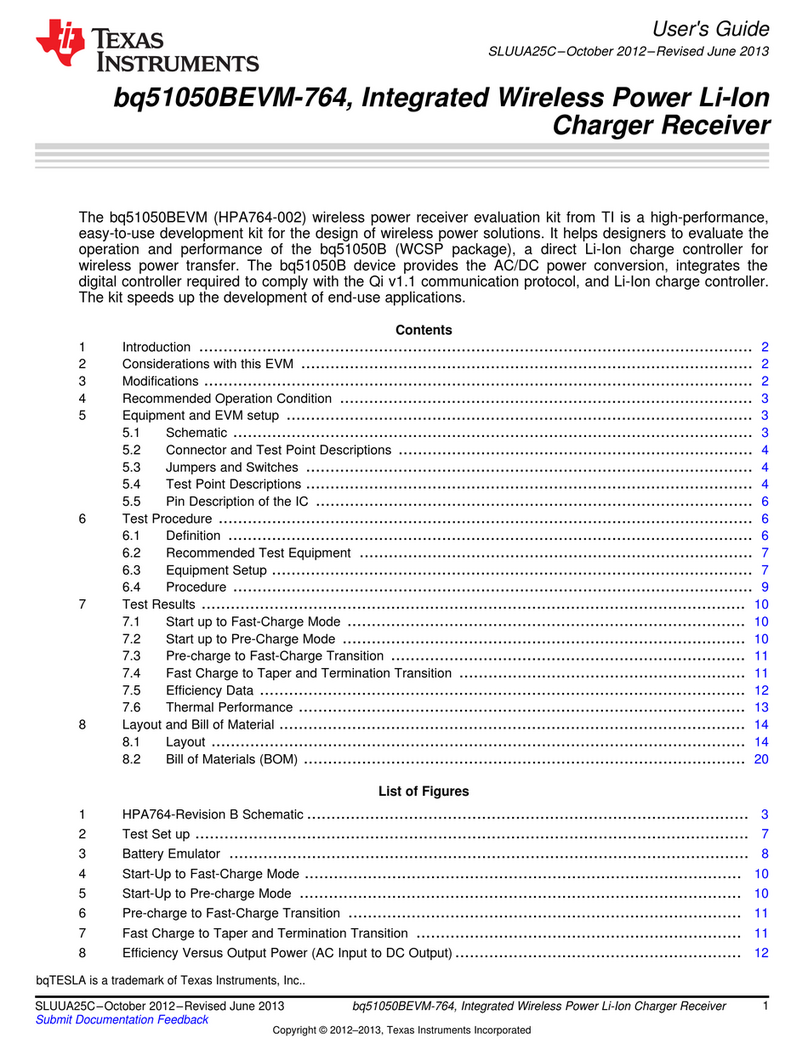
Texas Instruments
Texas Instruments bq51050BEVM-764 User manual

Texas Instruments
Texas Instruments TRF1500 Operator's manual

Texas Instruments
Texas Instruments bq51221EVM-520 User manual