TEXWRAP 2200SS SIDE SEAL User manual

2200SS
SIDE SEAL
TOUCHSCREEN & PARTS MANUAL
SN: S1005
COPYRIGHT 1999
525 VOSSBRINK DRIVE
WASHINGTON, MO 63090
PH. (636) 239-7424
FX. (636) 2397241
®

2
TABLE OF CONTENTS
I. PREFACE ............................................................................................................................3
II. INSTALLATION.................................................................................................................4
A. Requirements for Machine Operation
B. Uncrating
C. Installation of 2200SS Side Seal Machine
III. MACHINE CONTROLS & LOCATIONS.......................................................................6
A. Manual Controls
B. Touch Screen Display
IV. MACHINE SET-UP ............................................................................................................9
A.Setup for Product Procedure
B. Loading/Routing Film
V. SPECIAL FEATURES........................................................................................................13
A. Using Test Mode
B. Auto Space Feature
C. Film Registration
VI. ENHANCING PERFORMANCE......................................................................................14
VIII. TUNING SIDE SEAL BLADE/ROLLER SYSTEM .......................................................15
IX. CONVEYOR BELT TRACKING .....................................................................................16
X. MAINTENANCE.................................................................................................................17
APPENDICES......................................................................................................................18
XI. APPENDIX A: DEFINITION OF TERMS & MACHINE DIAGRAMS
XII. APPENDIX B: TEXWRAP LIMITED WARRANTY
XIII. APPENDIX C: TOUCHSCREEN MANUAL

3
I. PREFACE
This manual covers the options and features of the 2200SS (Side Seal).
Appendix “A” is the definition of terms. Since these terms may vary from person to person, our
definition is listed for reference.
Whenever a CAUTION or a WARNING is displayed in the manual, observe the warning given.
Failure to do so will result in injury to personnel or damage to the machine.

4
II. INSTALLATION
A. Requirements for Machine Operation
Before beginning installation the machine will need the following:
Power Requirements: 115V dedicated 20 A single-phase circuit required.
DO NOT USE AN EXTENSION CORD
Air Requirements: 12 CFM minimum at 75PSI
This must be clean, dry air.
Machine WILL NOT OPERATE properly if above requirements are not met.
B. Uncrating
Inspect the shipping box for visible damage prior to signing the freight bill. If any damage is found,
contact the carrier immediately. Do not proceed until the carrier’s agent has made an inspection of the
unit. Do not remove the machine from the shipping box.
The following steps are to be taken when removing the machine from the crate:
1) Cut the plastic straps from the box. Use caution when doing so as the straps are under tension.
Remove all fasteners securing the box lid.
2) Lift the box off the crate.
3) Unbolt the lag bolts on each leg.
4) Lift the machine off the crate. Use care not to damage any part of the machine.
5) Adjust leveling feet for desired height of machine. Consider access between floor and frame
for maintenance personnel. 35” between floor and top of conveyor is recommended. NOTE:
Jam nuts on leveling feet must be tightened against frame or excessive machine vibration will
result. Level the machine to ensure smooth operation. Install the air filter/regulator, scrap
winder bail and the exit transfer roller assembly at this time. Untie all moving components and
remove any packing materials.
6) Remove infeed conveyor shipping bracket.

5
C. Installation of 2200SS Machine
Read entire manual before operating.
Qualified personnel with working knowledge of the TEXWRAP 2200SS should perform installation of
a TEXWRAP 2200SS machine. There are rapidly moving parts so observe safety–warning stickers
and keep hands clear of moving parts. Qualified personnel should install all electrical and pneumatic
hookups. Some surfaces are hot so use caution.
1) Level any auxiliary equipment, such as shrink tunnels and/or infeed conveyors to the height of
the Side Seal conveyors.
2) Open the bottom panel boxes and inspect for relays that may have loosened during shipment.
3) Install the air supply. CAUTION: Do Not Exceed 80 PSI at the Side Seal regulator. The
factory recommends 75 PSI.
4) Attach the film folder to the Side Seal and wire it in to the sub-panel (located in the back of the
side seal under the infeed conveyor) according to the film folder wiring diagram.
5) Wire in any auxiliary infeed equipment, such as the Texwrap FC10 (Flighted Conveyor)
following the appropriate wiring diagram(s).
6) Plug the machine into a dedicated 20A, 115V circuit. Make sure that the on/off switch is “off”
at the main lower panel box.
7) Turn on the machine – (the circuit breaker and the on/off switch are located to the right on the
main panel box). CAUTION: Machine parts travel at rapid speeds; make sure all persons,
foreign objects, etc., are clear of the endseal system.
8) Turn on the cross and side heaters. The temperature is preset at the factory. Allow 10 minutes
to warm up. CAUTION: Some surfaces are hot when heaters are on.
9) Depress the red reset button until the light goes off. The machine should reset; the endseal
should return to “home” position.
10) Depress the green run button; the conveyors should run. Manually trip the product sensing
photoeye at the entrance end of the endseal unit. The endseal should cycle at factory settings.
11) The machine is now ready for production, however, first read the entire manual before
operating.

6
III. MACHINE CONTROLS & LOCATIONS
All of the machine controls can be broken down into two general areas; the manual controls and the
display. All 2200SS machines share the same set of manual controls, with only one exception. The
main speed potentiometer is not present on the 2200SS since the machine speed is controlled in the
touch screen display. However, the display will vary.
A) Manual Controls
A listing of the manual controls follows:
Heater On/Off Switch Controls whether or not each individual heater is “on” or “off” .
Green On Turns automatic mode on or off. When the automatic mode is active, the
indicator will be lit.
Red Emergency Stop
Pushbutton Stops the machine in case of an emergency. This disables all power to
the moving parts of the machine.
Red Reset Pushbutton Resets the machine in case of an error condition. This will clear out the
current machine operation, allowing you to restart the machine. If an
error does occur, the indicator will glow red until the button is pushed to
reset the machine. Note: Button must be held in until the machine resets.
Outfeed Speed Control This is used to adjust the speed of the outfeed conveyor. The adjustment
will only affect the outfeed conveyor. If the main speed is changed, then
the outfeed will change in proportion to the main speed. This can be
used to relax the film between tall products before endsealing.
Staging Speed Control This is used to adjust the speed of a staging conveyor tied to the side
seal. If the main speed is adjusted, the staging speed will change in
proportion to the main speed, keeping product spacing uniform over a
range of speeds.
Temperature Controllers Adjusts the temperature of the endseal and the sideseal. To set the
temperature controller for a specific temperature, press the leftmost set
key and press the up or down arrows until the desired temperature is
reached. The recommended settings are 550for the sidesal and 450for
the endseal.

7
B) Touch Screen Display
The touch screen display is where most of machine controls and settings are located. After turning on
the machine power, the following screen will be displayed.
MACHINE
SET-UP NEXT
PRODUCT
LIBRARY
COUNTER
RESET
MANUAL
KEYS
20 36 52 68 84 100
BELTSPEED FT/MIN
PRODUCTS/MINUTE ##.###
SET
#.##
This is considered to be the home panel, and from here, any machine feature or setting can be reached.
Most of the touch screen panels are self-explanatory. Each panel on the touch screen performs a
different function and may contain various types of controls such as a numerical entry key, a slider bar,
buttons, numerical displays, etc. Below is a listing of the different styles of controls that may be
located on the panels and how to use each control. In the appendix are more specific directions on the
touch screen, like how to save a program, how to edit a program, etc.

8
Control Type Function Action Notes
Button Turns on a feature in the PLC
and/or move between panels Pressing the button will
perform an action Two types of operation:
1) Momentary button
OR
2) On/Off switch
Slider Bar Changes a number in the PLC By sliding the position
indicator the value of the
number will change
The position indicator will
not always reflect the
actual value of the number
whenever a numerical
entry pad is used.
Numerical
Entry Pad Allows a change in the PLC
using a calculator type
number pad
When the set button is
pressed a calculator type
numerical pad will be
displayed.
Numerical
Display Displays a value in the PLC This will display a
number, which cannot be
changed.
Button “HOME” – this will go to the
home panel. Pressing the button takes
you directly to home
panel.
All screens should have a
home button.
Button “BACK” – takes you back to
the previous panel Pressing the button takes
you back to previous
panel.
This may not be located
on all panels.

9
IV. MACHINE SET-UP
A. Setup for Product Procedure
1) Unlock handle under infeed conveyor, adjust conveyor to accommodate package width and then
re-lock the handle. The product should sit against the back rail of the infeed conveyor and
should transfer onto the main conveyor without any over hang.
2) Adjust auxiliary infeed conveyor to align with infeed conveyor (if Auxiliary Infeed Conveyor
option is installed) e.g.: Texwrap FC10 Flighted Conveyor.
3) Using the seal height adjustment crank (labeled “A”) set seal height to approximately half the
height of the product above the conveyor surface. Use the top of the sideseal backup roller as a
reference. See diagram below.
ADJUSTMENT OF THE CRANK HANDLES “A” AND “B”
ON ALL TEXWRAP SIDE SEAL MACHINES
CRANK “A” ADJUST THE UP/DOWN CENTERLINE OF THE CROSS SEAL AND SIDE SEAL.
CRANK “B” ADJUST THE DISTANCE BETWEEN THE UPPER AND LOWER SEALBARS, OR
THE OPENING HEIGHT.
When adjusting either crank handle, do so with the air pressure on and keep the lower seal pad
even with the top of the conveyors. If you adjust Crank “A”, monitor the relationship of the lower pad
to the conveyors, adjusting Crank “B” as needed. This also applies to the adjustment of Crank “’B”. As
you adjust, you may have to adjust Crank “A” also in order to keep the lower pad even with the top of
the conveyors. If this is not done, it is possible to run the lower pad down far enough to bind it into the
lower conveyor mounting brackets. You could also run the upper bar into the top mounting brackets.
When this happens, the cranks become difficult to turn and could result in serious damage to machine
components.
Center of Product
Side Seal Backup Roller (Orange)
Mid Conveyor
Infeed Conveyor
Produc
t
Side Seal Unit
Auxiliary Infeed Conveyor
Ad
j
ust Infeed Conve
y
or in this Direction
Back Rail
Locking Handle
Under Conv.

10
IV. MACHINE SET UP (Cont’d)
4) Adjust the endseal opening crank (labeled B) so that the bottom pad of the endseal is slightly
below the surface of the conveyor, the product should also clear under the top bar of the endseal.
5) Adjust the film inverting head to product height using the crank on top of the infeed conveyor.
6) Endseal closure operation will vary with adjustments in endseal opening. With each new product
height setup, adjustments of the flow controls will be necessary to prevent machine “banging”.
Two flow control valves are located together on the main air cylinder, one adjusts the opening
speed of the endseal, and the other adjusts the closing speed of the endseal. Adjust these while
the machine is running, or use the manual seal button on the keypad, until a smooth and quite
operation of the endseal results. The main air cylinder is located beneath the endseal system.
7) The main air regulator should never exceed 80 PSI. The recommended PSI is 75. Exceeding 80
PSI will damage internal mechanisms.
8) “Dry Run” the product without film and check for proper product spacing. In general, the
distance between products, on the middle conveyor, should be 1.5 times the product height.
Tune conveyor speeds and mechanical adjustments. The “Test Mode” can be used to help
establish machine speed. Refer to the “Test Mode” section for a more detailed description.
9) Adjust the sealing position of the cross-seal between packages with end seal lag. Increasing
endseal lag moves cross-seal further from trailing edge of lead package.
10) When satisfied with machine performance, load film (see Section B below).
11) Use the infeed jog key to convey product into the first conveyor from an auxiliary conveyor if
utilized.
12) Press the green automatic on/off button to start operation.
13) Remember to catch scrap bag in front of first product.
14) Any adjustments can be made while the machine is running, both mechanical and touch screen
values.

11
B. Loading/Routing Film
To load the film, follow the steps below. Also refer to film threading diagram on the next page to assist
in loading film. Note: All instructions will assume you are standing to the front of the machine.
1) Load the Centerfolder with film. Refer to FF2200SS Centerfolder Instructions for more details.
2) With both halves of the film still together, loop the film over the topmost roller of the film stand.
3) Feed the film through the middle of the two pin perforated rollers.
4) Loop the film around the backside of the bottom most roller of the film stand.
5) Split the film in half and place the anti-static bar in the middle of the layers of film.
6) For the top layer of film, lay it over the backside of the top film former and fold it under the
slanted side of the top former.
7) For the bottom layer of film, place it under the backside of the bottom film former and fold it
over the slanted side of the bottom former.
8) Pull both halves of the film through to the forward section of the infeed conveyor.
9) Match both free halves of the film together and feed it through the side seal system.
10) Seal the film with the side seal (use “Manual Jog” key) and continue to do so until enough scrap
is created to attach to the scrap winder. Note: Be careful to catch the excess bag at the exit
conveyor while advancing.
11) Channel the scrap film through the Sideseal scrap guide rollers (white). Feed the scrap over the
top of the rightmost roller of the scrap take up system.
12) Loop the scrap under the bottom take up bar and feed over the top of the leftmost scrap take up
roller.
13) Tie the scrap to the scrap winder wheel.
14) Cycle the endseal unit, using the “Manual Endseal” key to cut off the excess bag at the exit
conveyor.

12
Diagram – Film Path

13
V. SPECIAL FEATURES
A. Using Test Mode
This feature is designed to see how fast the machine will run a simulated product for estimation
purposes. The machine will simulate a package of a certain length and height as if there were an actual
physical product. This allows the user to establish a production rate of a particular product. Adjustment
of the input values and the endseal crank adjustments should be made for the simulated package. To get
to the “Test Mode” screen, press the “NEXT” button on the home panel. Next, press the “TEST
MODE” button. Three settings will be displayed: product length, spacing between products, and endseal
lag distance. Once these are set to the desired values, press the “TEST MODE ON/OFF” button,
(remembering to remove the film first). The main speed should be set to the lowest setting and gradually
increase to the maximum achievable for that product. Once the speed is set, allow the “Product Per
Minute Counter” a few minutes to settle and then an accurate count can be achieved. To stop the
machine from continuing the cycle, press the “TEST MODE ON/OFF” button. The machine will stop
and wait for the next user action. With Auto mode off (Green Button), press Test Mode on. Go to
maximize package per minute. Press Go To Max-Speed button. Press to begin the Maximize Speed
Function. Go back to home screen for PPM count and final suggested Maximum Belt Speed.
B. Auto Space Feature
This method of staging eliminates the need in many cases for a separate staging system (such as a
flighted conveyor). By setting a distance between packages, the Auto Space feature will automatically
keep that distance between products. To start Auto Space, press the “MACHINE SET-UP” button on
the home panel. Press the “AUTOSPACE” button. This will ask for a length in inches, enter in the
desired distance between products. Next press the “AUTOSPACE ON/OFF” button. The Auto Space
feature is now on. It will stay on until the buttons are pressed again. To optimize the autospace feature
turn infeed percent to 10
C. Film Registration
Now available. Please call Texwrap technical support for further instructions at 1-800-886-7421.

14
VI. ENHANCING PERFORMANCE
2200
By adjusting certain settings in the machine, the performance (measured in products per minute) can be
increased in some cases up to 15 to 20 packages per minute. The 2200 has a feature allowing an
operator to adjust all the machine settings, which maximize performance. This feature can be reached
by pressing the “MACHINE SETTING” button on the home screen, then the “MAXIMIZE
PACKAGES PER MINUTE” button. Follow the directions on screen.
All Other Models
If the forward MOTION TRIM™ percentage is set too large the machine will seal before the endseal
travels forward. This will not harm the machine, however it will reduce performance. The correct
setting for this depends on the jaw height, product spacing, bag length, and belt speed of the machine.
With each adjustment to the machine this setting may need adjustment as well. Forward MOTION
TRIM™ may also effect the length of the endseal, and if set too large, may cause the machine to act
erratically. To correct this, reduce the forward MOTION TRIM™ or increase bag length. If the return
MOTION TRIM™ percentage is set too short it is possible for the endseal to hit the package directly
behind it, therefore disturbing the spacing between the following two packages. The diagram below
shows how the MOTION TRIM™ affects the endseal cycle time. The return travel distance is
minimized, therefore increasing packages per minute. If this occurs, increase return MOTION TRIM™
until the jaws no longer hit the package.
Stroke Length
Return motion trim @ 100 percent
Forward motion trim @ 0 percent
Stroke Length
Return motion trim @ 100 percent
Forward motion trim @ 100 percent
Stroke Length
Return motion trim @ 0 percent
Forward motion trim @ 100 percent
Notice with each change the stroke length decreases, therefore increasing the packages per minute of the
machine.
Finally, to optimize the Autospace system, a few other settings may be adjusted. One being the sideseal
up time. By increasing this time, the sideseal head will not come up as quickly, therefore reducing the
start up time between staging cycles. The belt speed can also be adjusted to increase the amount of
products per minute. If the speed is set too high products may slip on the belt causing irregular spacing.

15
VIII. TUNING SIDE SEAL BLADE/ROLLER SYSTEM
Sideseal backup rollers will last approximately 40 hours of machine run time. They can be flipped 180
degrees for another 40 hours of operation. This is a quick operation. Adjust the seal height adjustment
crank until the entire sideseal backup roller is visible above the conveyor. Using the palms of your
hands, peel the backup roller off the aluminum hub. Use caution around the round seal blades, they are
hot. Flip seal backup ring and reapply.
Maximizing Life of the Sideseal Backup Roller
Serial number S1029 and earlier:
A) Remove guards covering sideseal.
B) Physically push sideseal arm downward, over-powering the air cylinder until the arm engages the
stop adjustment bolt. Examine the round seal blade system where it contacts the sideseal backup
roller. The blade should barely touch the backup roller with no visible sign of backup roller
compressing under the blade. Adjust sideseal arm stop bolt if necessary.
C) Run a piece of scrap film through the sideseal to ensure temperature is 425-500F. Adjust the
sideseal arm adjustment bolt until the blade cuts the film clean. Excessive blade penetration into
the backup roller will cause premature wearing of the backup roller.
D) When satisfied with seal, lock jam nut on sideseal arm adjustment stop bolt.
E) Replace guards.
Serial number S-1030 and later:
A) Sideseal guard removal is not necessary. The sideseal-adjusting bolt can be accessed through the
stainless cover with a 5/16” Allen wrench. The locking nut is not used on the later machines.
The adjustment procedure is the same as above.

16
IX. CONVEYOR BELT TRACKING
A daily glance at the three conveyor belts for proper tracking is recommended. Sometimes a change in
product size or weight can cause shifts in belt tracking. If any of the three belts has drifted to the edge of
the conveyor, adjustments are necessary. If the machine runs with an untracked belt it will eventually
destroy the belt causing poor machine operation.
Adjust Belt Tracking as follows:
Infeed Conveyor (M1): Locate the two Phillips head machine screws near the entrance. Turning a
screw counter clockwise will cause the belt to track toward that screw. Turning a screw clockwise will
cause the belt to track away from that screw. Turn the screw ¼ turn and wait for the belt to settle as
conveyor runs full speed. Be careful not to over tension the M1 conveyor belt.
Middle and Exit Conveyors (M2/M3): Locate the two Phillips head machine screws. Turning a screw
clockwise will cause the belt to track toward that screw. Turning counter clockwise causes the opposite.
The M2 and M3 conveyor belts are a different material than the M1 belt. The tighter the M2 and M3
conveyors are, the better they track. If there is a tracking problem on the M2 or M3 belt, increase the
tension by turning each screw 3 or 4 full turns clockwise, then track belts turning ¼ turn at a time
between settling. Settling at full speed will take approximately five to ten minutes. There is a break in
period for the M2 and M3 belts. Some initial stretching will occur the first week or so, possibly
requiring retracking.

17
X. MAINTENANCE
To prevent excessive down time and costly repairs a maintenance schedule should be kept (sample
below). The most crucial part being the daily wipe downs. Some films, do to the way they are
processed, leave residue on the inside rollers. By keeping the belts clean, the buildup on the rollers will
be substantially less.
Recommended Maintenance Schedule:
Daily:
1. Check condition of silicon backup rollers on the sideseal. Replace if necessary.
2. Check regulator bowl for water and/or oil.
3. Check the silicon pad beneath the cross seal for wear. Replace if necessary.
4. Check conveyor belts for proper tracking.
Weekly:
1. Wipe down all visible bearings with clean, dry cloth. Do not use any oil.
2. Wipe down the conveyor belts.
Monthly:
1. Check all chain drives for proper tension.
2. Wipe down machine completely.
3. Grease bearings that have grease fitting. Do not grease linear slide bearings.
4. Oil rod ends and main cylinder clevis pin with light oil.
5. Check for proper tension on motion pan drive timing belt, adjust using the two tensioning screws
under exit conveyor. Adjust the two screws together, 1/8 turn each, until white timing belt is taught.
WARNING: If adjustments to belt tension screws are not done in unison, the timing belt may track off
of the timing pulleys, causing belt or pulley failure.

18
APPENDICES

1
APPENDIX “A”
DEFINITION OF TERMS
Endseal Lag - this is also referred to as the “bag length”. It is the excess bag at the end of the product
and is measured from the trailing edge of the product.
Endseal Dwell – also referred to as “seal time”. This is the amount of time the endseal jaws remain
shut in order to seal the film.
Product Jog - this will feed the products up to the staging eyes. The infeed (M1) and staging
conveyors will activate.
Machine Jog - turns all conveyors on, allowing film to be fed through the side seal and take-up unit.
Manual Endseal – this will close the endseal jaws for one seal time.
Auto Space – this is the automatic staging system, which, when enabled will space product between
the infeed and main conveyors.
Max-Speed – allows the machine to speed up to maximum speed for that particular product.
Forward MOTION TRIM – reduces the time of a machine cycle by allowing the jaws to close before
the endseal system travels forward.
Return MOTION TRIM – allows the endseal unit to return to the home position before the jaws are
completely open
Test Mode – a simulated run of a product can be done to measure the machines’ performance on this
application.
Infeed Offset Percent – enables the infeed (M1) to run at a different speed then the main motor drive.
This is based on a percentage difference from the main (M2) drive.

2
Texwrap Limited Warranty
TEXWRAP warrants all manufactured equipment to be free of defects in material and
workmanship for a period of 12 months from date of shipment to the original
purchaser’s facility. This warranty does not cover the replacement of consumable
items, routine maintenance, or alignments.
TEXWRAP will, at their discretion, repair or replace a defective component at no
charge. Transportation and freight charges are not covered under this warranty, but may
be covered by your local TEXWRAP Distributor. Field technician labor is covered by
your local TEXWRAP Distributor on warranted items. Contact your local TEXWRAP
Distributor for their warranty claim procedure and policies.
This warranty will become null and void if it is determined:
The equipment is misused, abused or neglected in any way.
The equipment is altered or modified without prior written approval from
TEXWRAP.
TEXWRAP makes no claims to the fitness of its equipment to perform in any particular application
and therefore will under no circumstances be held liable for any kind of incidental or consequential
losses arising from the use, loss of use, or defective operation of the equipment.
TEXWRAP does not warrant that the equipment conforms to any insurance regulations;
electrical codes or any particular safety features, with the exception of panels
containing UL Stickers, which meet UL Codes. The purchaser assumes liability for
compliance with all applicable statutes, codes and regulations whether federal, state or
local.
This limited warranty applies only to the repair or replacement of defective parts and is extended to the
original purchaser.
form# 00026
Table of contents
Popular Touchscreen manuals by other brands
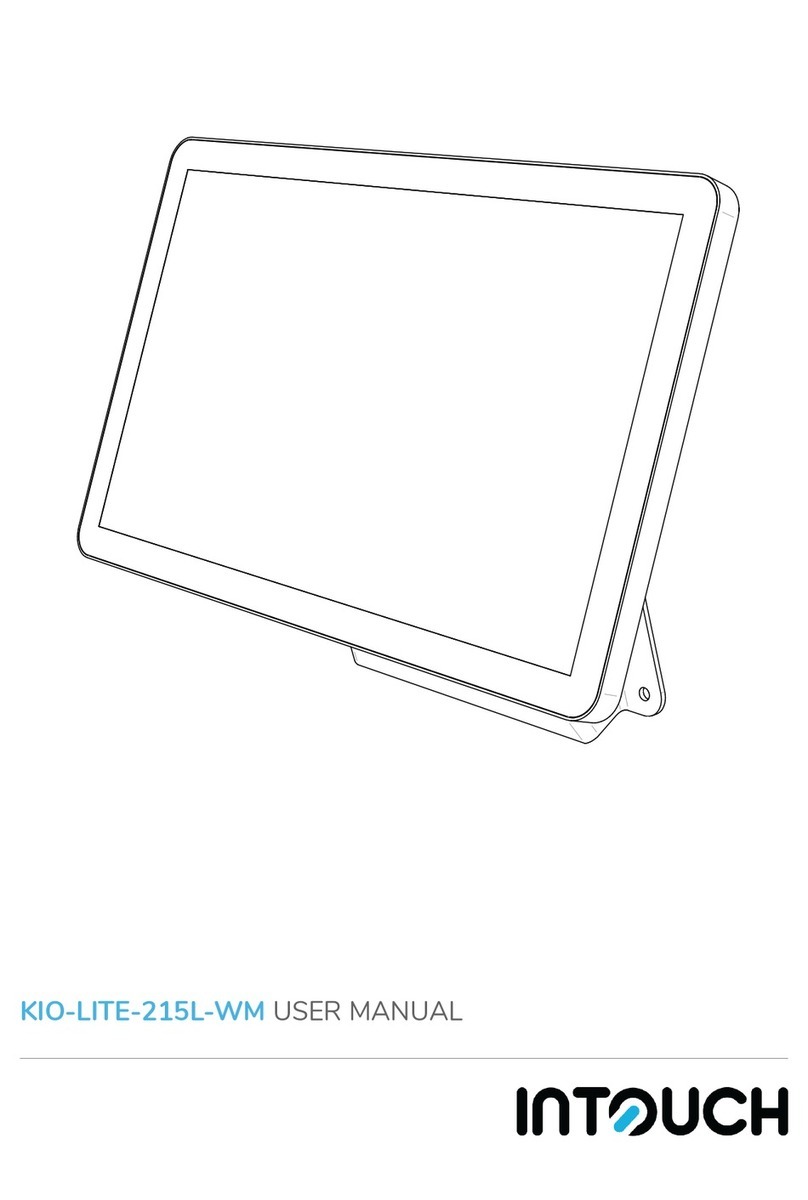
InTouch
InTouch KIO-LITE-215L-WM user manual
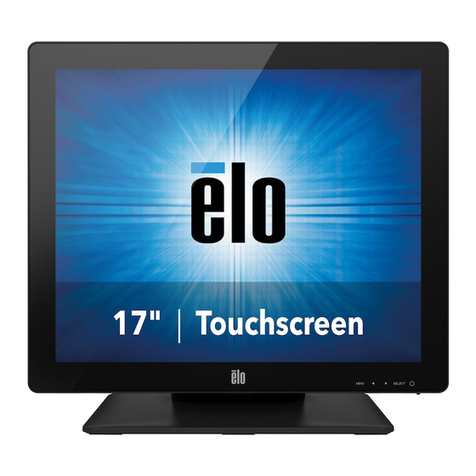
Elo Touch Solutions
Elo Touch Solutions ET1717L user manual
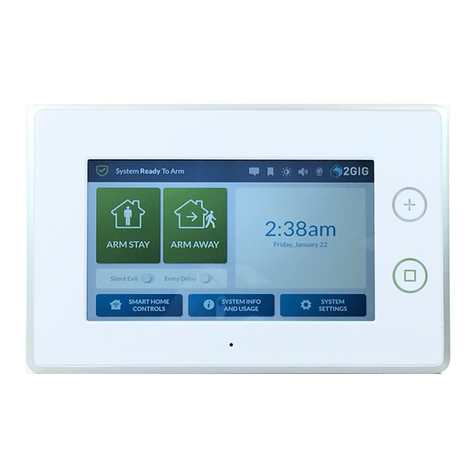
2gig Technologies
2gig Technologies 2GIG-SP1-GC3 instructions
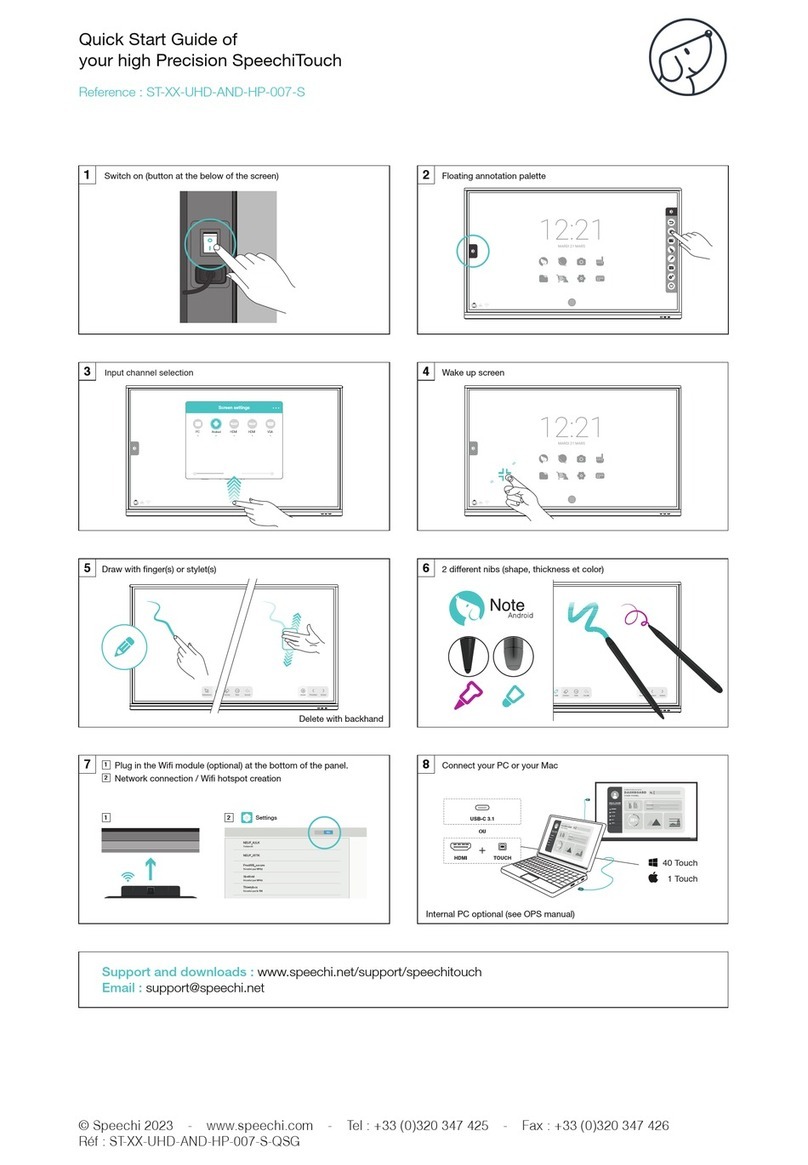
Speechi
Speechi ST-XX-UHD-AND-HP-007-S-QSG quick start guide
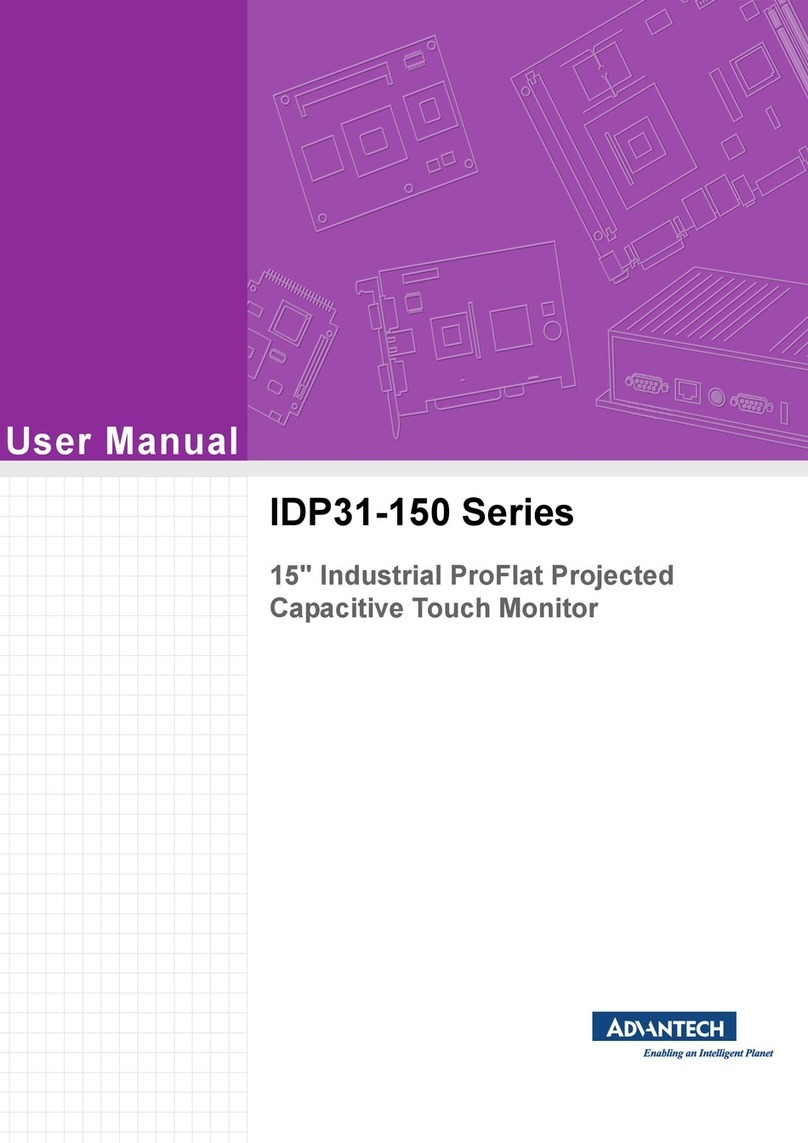
Advantech
Advantech IDP31-150 Series user manual
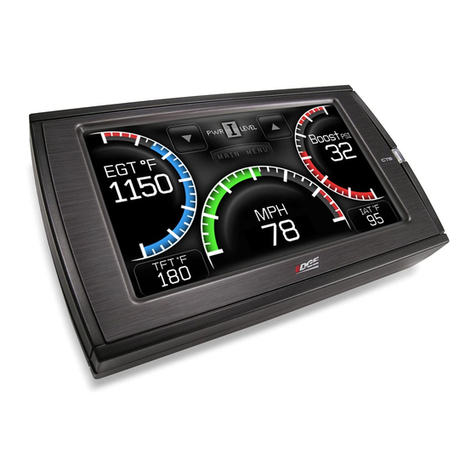
Edge Products
Edge Products CS user guide
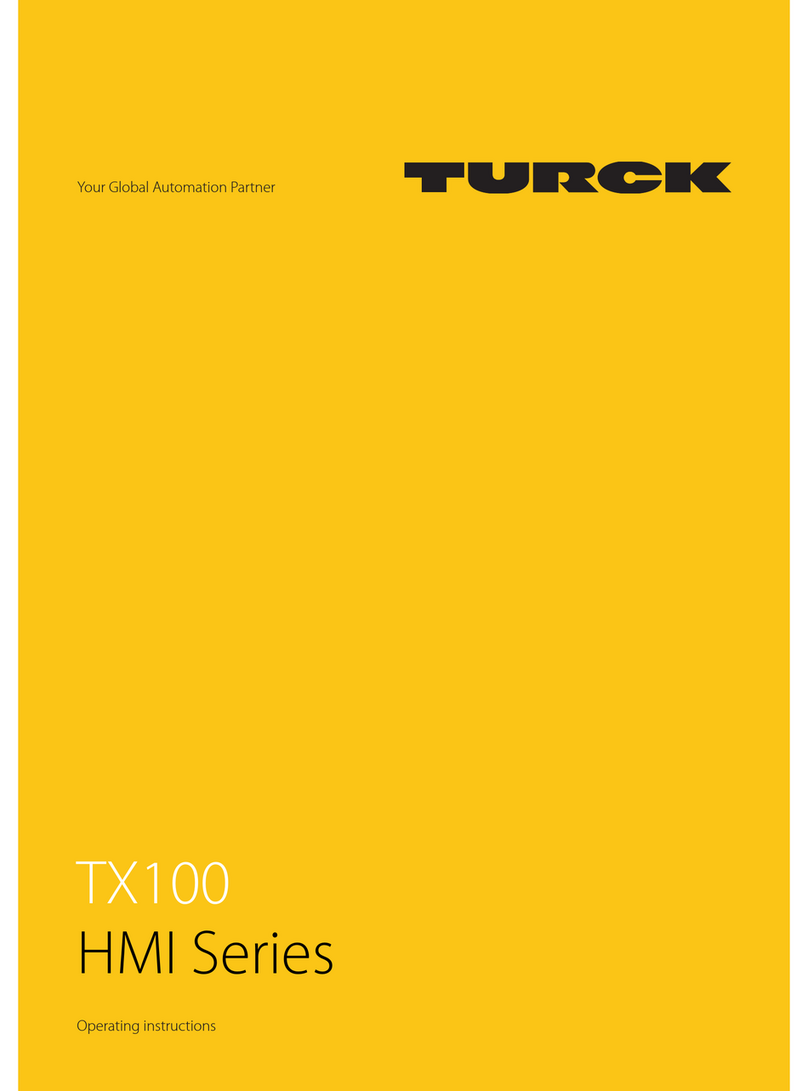
turck
turck HMI Series operating instructions
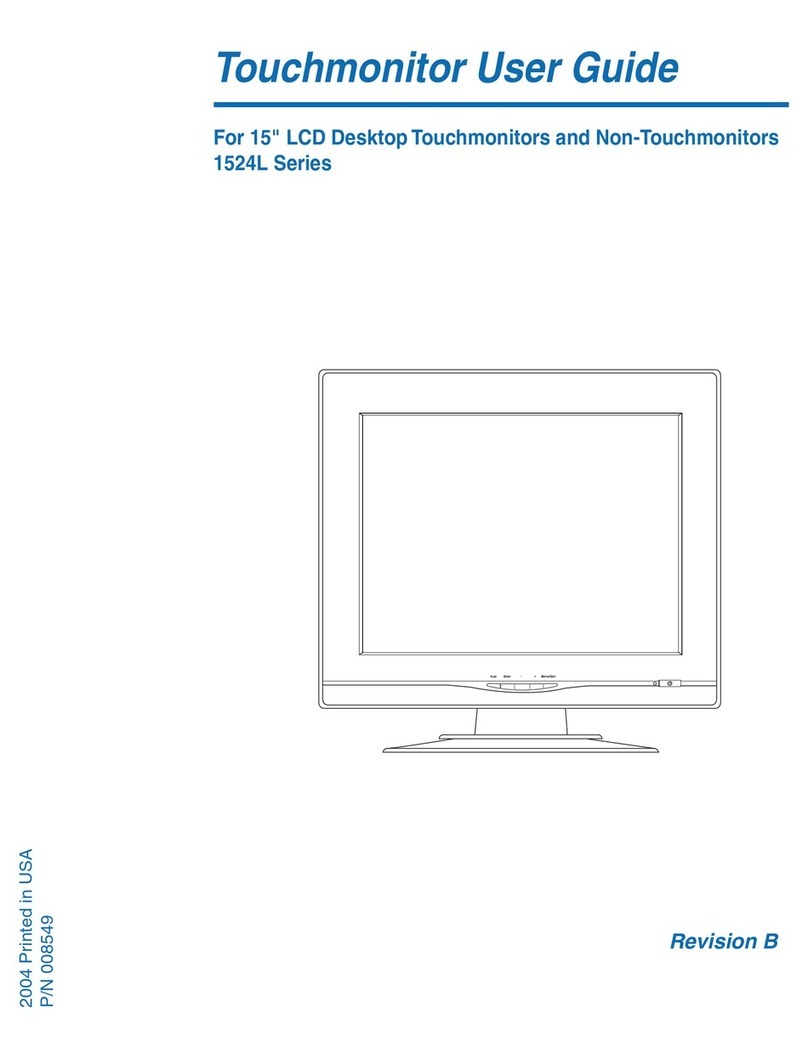
Elo TouchSystems
Elo TouchSystems 1524L user guide
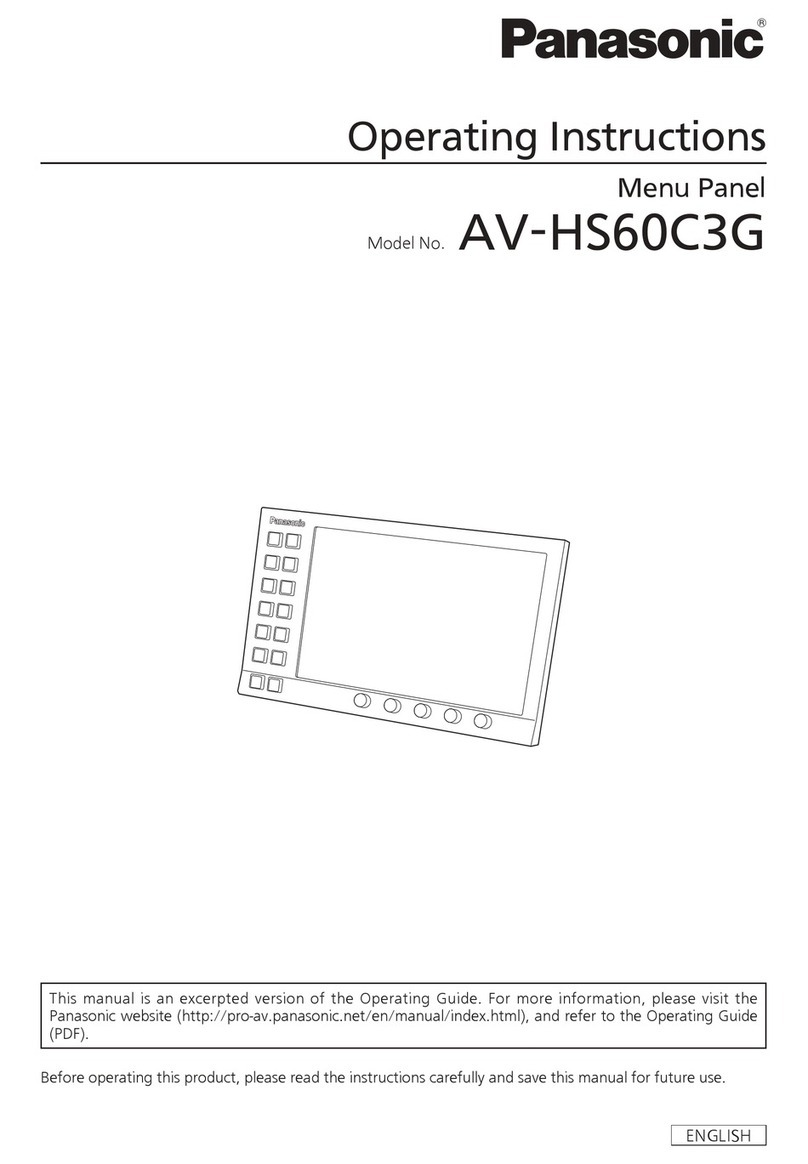
Panasonic
Panasonic AV-HS60C3G operating instructions
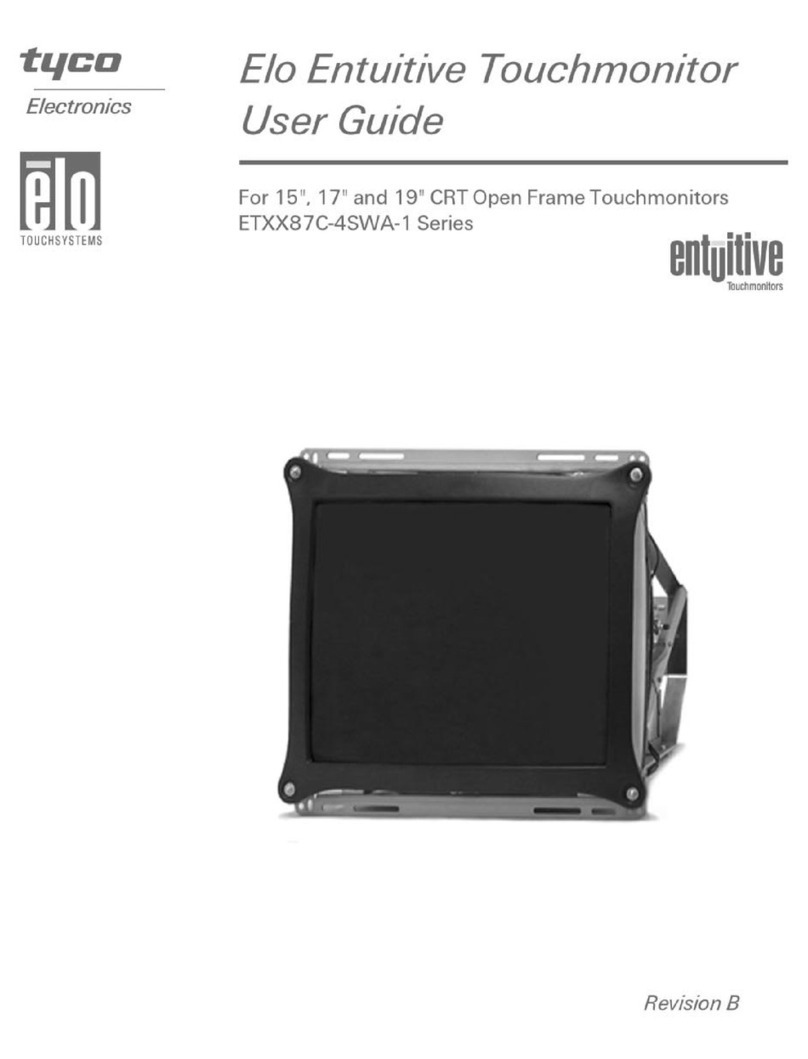
Elo TouchSystems
Elo TouchSystems ETXX87C-4SWA-1 Series user guide

IPO Technologie
IPO Technologie FUTURA 21WQP manual
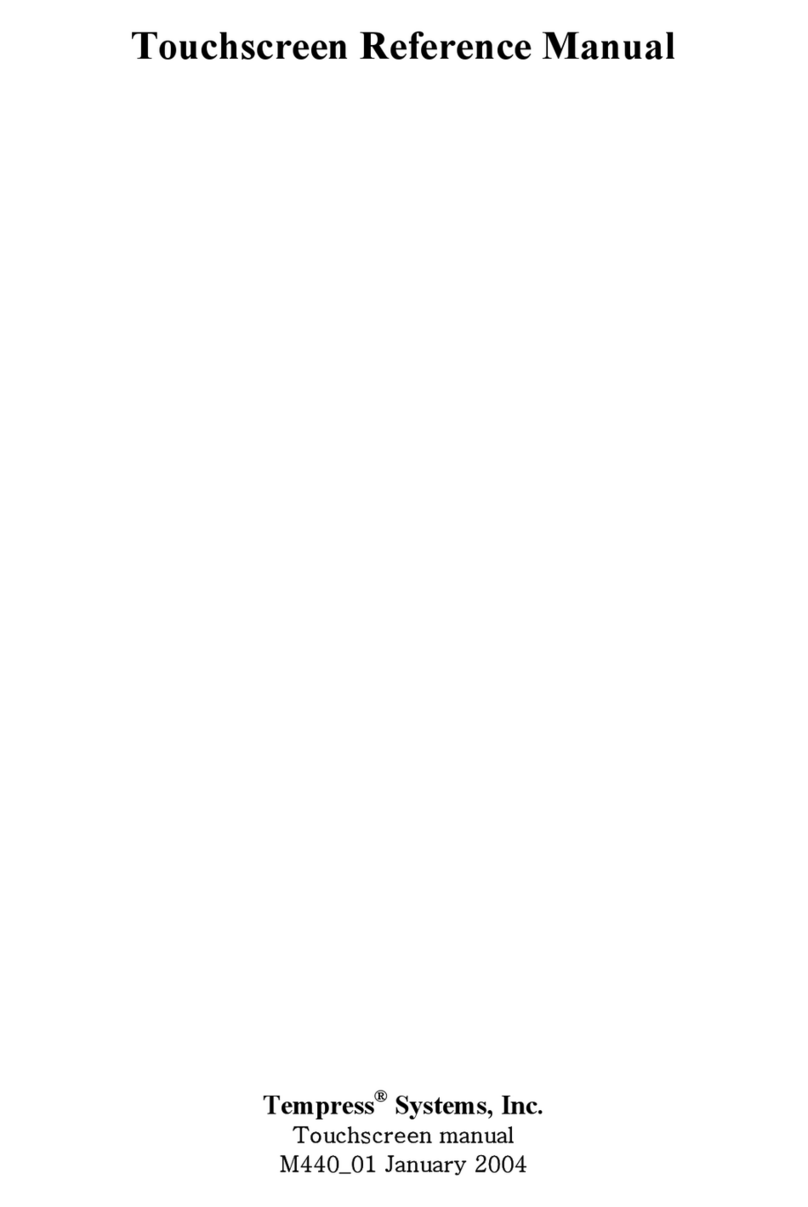
Tempress Systems
Tempress Systems M440-01 Reference manual