Thermal Care Vactherm RV Instruction Manual



Table of Contents
Foreword .................................................................................................................................................................................................................. 1
Safety Guidelines .................................................................................................................................................................................................. 1
Pre-Installation....................................................................................................................................................................................................... 2
Receiving Inspection............................................................................................................................................................................................2
Unit Storage............................................................................................................................................................................................................ 2
Installation - Mechanical....................................................................................................................................................................................2
Foundation .............................................................................................................................................................................................................. 2
Unit Location .......................................................................................................................................................................................................... 2
Rigging......................................................................................................................................................................................................................2
Fluid Distribution Piping ....................................................................................................................................................................................2
Installation - Electrical......................................................................................................................................................................................... 3
Controller Operation ...........................................................................................................................................................................................4
Figure 1 –Control Panel ........................................................................................................................................................................... 4
Start............................................................................................................................................................................................................................ 4
Stop............................................................................................................................................................................................................................4
Temperature Adjust .............................................................................................................................................................................................4
Display Set Point Temperature .............................................................................................................................................................. 4
Setting Set Point Temperature............................................................................................................................................................... 4
Increase..................................................................................................................................................................................................................... 4
Decrease................................................................................................................................................................................................................... 4
Date & Time............................................................................................................................................................................................................ 4
Displaying Pump Running Hours.......................................................................................................................................................... 5
Resetting Pump Running Hour Counter ............................................................................................................................................ 5
Displaying Clock Time ............................................................................................................................................................................... 5
Setting Clock Time ......................................................................................................................................................................................5
Displaying Day of the Week....................................................................................................................................................................5
Setting Day of the Week...........................................................................................................................................................................5
Timer On/Off .......................................................................................................................................................................................................... 5
Display Status of Timer .............................................................................................................................................................................5
Turning Timer On/Off ................................................................................................................................................................................5
Setting Start Time........................................................................................................................................................................................ 5
Setting Timer Stop Time...........................................................................................................................................................................6
Setting Timer Days for Automatic Start/Stop .................................................................................................................................. 6
Deviation Alarm.....................................................................................................................................................................................................6
Setting Deviation Alarm Temperature ................................................................................................................................................ 7
Activating Deviation Alarm......................................................................................................................................................................7
Deactivating Deviation Alarm................................................................................................................................................................. 7
Tank Temperature ................................................................................................................................................................................................ 7
Password Entry....................................................................................................................................................................................................... 7
Entering or Changing Password ............................................................................................................................................................ 7
Deleting Password ...................................................................................................................................................................................... 7
Pump Status Indicator ........................................................................................................................................................................................8
Heating Status Indicator .................................................................................................................................................................................... 8
Cooling Status Indicator ....................................................................................................................................................................................8
Low Level Alarm Indicator.................................................................................................................................................................................8
Deviation Alarm Indicator .................................................................................................................................................................................8
Automatic Timer Status Indicator .................................................................................................................................................................. 8

Controller Control Fault Logic ......................................................................................................................................................................... 8
Draining the Mold ................................................................................................................................................................................................ 8
Start-up..................................................................................................................................................................................................................... 8
Step 1 –Connect Main Power ......................................................................................................................................................................... 9
Table 1 - Fill Water Chemistry Requirements.................................................................................................................................10
Table 2 –Recommend Glycol Solutions...........................................................................................................................................10
Step 3 –Start the Unit.......................................................................................................................................................................................10
Step 4 –Check Pump Rotation......................................................................................................................................................................10
Step 5 –Enter Set Point Temperature ........................................................................................................................................................10
Setting Set Point Temperature.............................................................................................................................................................10
Step 6 - Adjusting the Vacuum.....................................................................................................................................................................11
Preventive Maintenance...................................................................................................................................................................................11
Once a Week ........................................................................................................................................................................................................11
Once a Month ......................................................................................................................................................................................................11
Once a Year...........................................................................................................................................................................................................11
General Troubleshooting.................................................................................................................................................................................12
Charts and Drawings .........................................................................................................................................................................................13
Figure 1 –Pump Performance (60 Hz)..............................................................................................................................................13
Figure 2 –Cooling Capacity ..................................................................................................................................................................14
Figure 3 –High Voltage Wiring Diagram..........................................................................................................................................15
Figure 4 –Low Voltage Wiring Diagram ..........................................................................................................................................16
Figure 5 –Control Board Details .........................................................................................................................................................17
Figure 6 –Heating Element Details....................................................................................................................................................18
Figure 7 –Principle of Operation ........................................................................................................................................................19

1
Foreword
The temperature control unit is a packaged unit that
typically includes a fluid pump, electric immersion
heater, and temperature control valve in a cabinet.
The purpose is to provide circulation and
temperature control of a cooling fluid.
This manual is to serve as a guide for installing,
operating, and maintaining the equipment. Improper
installation, operation, and maintenance can lead to
poor performance and/or equipment damage. Use
qualified installers and service technicians for all
installation and maintenance of this equipment.
This manual is for our standard product. The
information in this manual is general in nature. Unit-
specific drawings and supplemental documents are
included with the equipment as needed. Additional
copies of documents are available upon request.
Due to the ever-changing nature of applicable
codes, ordinances, and other local laws pertaining to
the use and operation of this equipment, we do not
reference them in this manual.
Safety Guidelines
Observe all safety precautions during installation,
start-up, and service of this equipment. The
following is a list of symbols used in this manual and
their meaning.
General Warning
Electricity Warning
Sharp Element Warning
Hot Surface Warning
Flammable Material Warning
Explosive Material Warning
General Mandatory Action
Wear Eye Protection
Wear Protective Gloves
Wear Ear Protection
Disconnect Before Carrying Out Maintenance or
Repair
Connect an Earth Terminal to Ground
Only qualified personnel should install, start-up, and
service this equipment. When working on this
equipment, observe precautions in this manual as
well as tags, stickers, and labels on the equipment.
WARNING: Any use or misuse of this equipment
outside of the design intent may cause injury or harm.
WARNING: This equipment contains hazardous
voltages that can cause severe injury or death.
WARNING: This equipment contains hot oil and water
or coolant under pressure. Accidental release of hot
water or coolant under pressure can cause personal
injury and or property damage.
WARNING: This equipment may contain fan blades or
other sharp edges. Make sure all fan guards and other
protective shields are securely in place.
WARNING: The exposed surfaces of motors, piping,
and other fluid circuit components can be very hot
and can cause burns if touched with unprotected
hands.
CAUTION: Disconnect and lock out incoming power
before installing, servicing, or maintaining the
equipment. Connecting power to the main terminal
block energizes the entire electric circuitry of the unit.
Shut off the electric power at the main disconnect
before opening access panels for repair or
maintenance.
CAUTION: Wear eye protection when installing,
maintaining, or repairing the equipment to protect
against any sparks, debris, or fluid leaks.

2
CAUTION: The equipment will exceed 70 dBA sound
pressure at 1 meter distance and 1 meter elevation
when operating. Wear ear protection as required for
personal comfort when operating or working in close
proximity to the chiller.
CAUTION: Wear protective gloves when installing,
maintaining, or repairing the equipment to protect
against any sparks, debris, or fluid leaks.
Pre-Installation
Receiving Inspection
When the unit arrives, verify the information on the
unit nameplate agrees with the order
acknowledgement and shipping papers. Inspect the
equipment for any visible damage and verify all
items shown on the bill of lading are present. If
damage is evident, document it on the delivery
receipt by clearly marking any item with damage as
“unit damage” and notify the carrier. In addition,
notify our Customer Service Department and they
will provide assistance with preparing and filing
freight damage claims, including arranging for an
estimate on repair costs; however, filing the shipping
damage claim is the responsibility of the receiving
party. Do not install damaged equipment without
getting the equipment repaired.
Shipping damage is the responsibility of the carrier.
To protect against possible loss due to damage
incurred during shipping and to expedite payment
for damages, it is important to follow proper
procedures and keep records. Photographs of
damaged equipment are excellent documentation
for your records.
Start unpacking the unit, inspect for concealed
damage, and take photos of any damage found.
Once received, equipment owners have the
responsibility to provide reasonable evidence that
the damage did not occur after delivery. Photos of
the equipment damage while the equipment is still
partially packed will help in this regard. Refrigerant
lines can be susceptible to damage in transit. Check
for broken lines, oil leaks, damaged controls, or any
other major component torn loose from its
mounting point.
Record any signs of concealed damage and file a
shipping damage claim immediately with the
shipping company. Most carriers require concealed
damages be reported within 15 days of receipt of
the equipment. In addition, notify our Customer
Service Department and they will provide assistance
with preparing and filing freight damage claims,
including arranging for an estimate on repair costs;
however, filing the shipping damage claim is the
responsibility of the receiving party.
Unit Storage
When storing the unit it is important to protect it
from damage. Blow out any water from the unit;
cover it to keep dirt and debris from accumulating
on or getting in and store in an indoor sheltered
area that does not exceed 145°F.
Installation - Mechanical
Foundation
Install the unit on a rigid, non-warping mounting
pad, concrete foundation, or level floor suitable to
support the full operating weight of the equipment.
When installed the equipment must be level within
¼ inch over its length and width.
Unit Location
The unit is available in many different configurations
for various environments. Refer to the proposal and
order acknowledgement document for the
equipment to verify the specific design conditions in
which it can operate.
To ensure proper airflow and clearance space for
proper operation and maintenance allow a minimum
of 12 inches of clearance between the sides of the
equipment and any walls or obstructions. Avoid
locating piping or conduit over the unit to ensure
easy access with an overhead crane or lift to lift out
heavier components during replacement or service.
Rigging
The unit has a base with casters to facilitate easy
movement and positioning. Follow proper rigging
methods to prevent damage to components. Avoid
impact loading caused by sudden jerking when
lifting or lowering the unit. Use pads where abrasive
surface contact may occur.
Fluid Distribution Piping
Ensure all piping and fittings are suitable for the
maximum operating temperature and pressure of

3
the unit. Proper insulation of chilled process fluid
piping is crucial to prevent condensation. The
formation of condensation adds a substantial heat
load to the cooling system.
The importance of properly sized piping cannot be
overemphasized. See the ASHRAE Handbook or
other suitable design guide for proper pipe sizing. In
general, run full size piping out to the process and
then reduce the pipe size to match the connections
on the process equipment. One of the most
common causes of unsatisfactory unit performance
is poor piping system design. Avoid long lengths of
hoses, quick disconnect fittings, and manifolds
wherever possible as they offer high resistance to
water flow. When manifolds are required, install
them as close to the use point as possible. Provide
flow-balancing valves at each machine to assure
adequate water distribution in the entire system.
Install shut-off valves at each machine to allow for
isolation of the unit.
Installation - Electrical
All wiring must comply with local codes and the
National Electric Code. Minimum Circuit Amps (MCA)
and other unit electrical data are on the unit
nameplate. A unit specific electrical schematic ships
with the unit. Measure each leg of the main power
supply voltage at the main power source. Voltage
must be within the voltage utilization range given on
the drawings included with the unit. If the measured
voltage on any leg is not within the specified range,
notify the supplier and correct before operating the
unit. Voltage imbalance must not exceed two
percent. Excessive voltage imbalance between the
phases of a three-phase system can cause motors to
overheat and eventually fail. Voltage imbalance is
determined using the following calculations:
% Imbalance = (Vavg –Vx) x 100 / Vavg
Vavg = (V1 + V2 + V3) / 3
Vx = phase with greatest difference from Vavg
For example, if the three measured voltages were
442, 460, and 454 volts, the average would be:
(442 + 460 + 454) / 3 = 452
The percentage of imbalance is then:
(452 –442) x 100 / 452 = 2.2 %
This exceeds the maximum allowable of 2%.
There is a terminal block for main power connection
to the main power source. The main power source
should be connected to the terminal block through
an appropriate disconnect switch. There is a separate
lug in the main control panel for grounding the unit.
Check the electrical phase sequence at installation
and prior to start-up. Operation of the unit with
incorrect electrical phase sequencing will result in
improper pump performance. Check the phasing
with a phase sequence meter prior to applying
power. The proper sequence should read “ABC” on
the meter. If the meter reads “CBA”, open the main
power disconnect and switch two line leads on the
line power terminal blocks (or the unit mounted
disconnect). Do not interchange any load leads that
are from the unit contactors or the motor terminals.
WARNING: This equipment contains hazardous
voltages that can cause severe injury or death.
WARNING: This equipment contains hot water or
coolant under pressure. Accidental release of hot water
or coolant under pressure can cause personal injury
and or property damage.
WARNING: This equipment may contain fan blades or
other sharp edges. Make sure all fan guards and other
protective shields are securely in place.
WARNING: The exposed surfaces of motors, piping,
and other fluid circuit components can be very hot
and can cause burns if touched with unprotected
hands.
CAUTION: Disconnect and lock out incoming power
before installing, servicing, or maintaining the
equipment. Connecting power to the main terminal
block energizes the entire electric circuitry of the unit.
Electric power at the main disconnect should be shut
off before opening access panels for repair or
maintenance.
CAUTION: Wear eye protection when installing,
maintaining, or repairing the equipment to protect
against any sparks, debris, or fluid leaks.
CAUTION: Wear protective gloves when installing,
maintaining, or repairing the equipment to protect
against any sparks, debris, or fluid leaks.
CAUTION: Wire the unit ground in compliance with
local and national codes.

4
Controller Operation
Figure 1 –Control Panel
The controller uses a set of digital LED displays to
show various temperatures as well as status and
alarm conditions.
Start
To start the unit press the Start button. If the water
level in the reservoir is below the level required to
satisfy the low level sensor, the controller will initiate
an initial fill sequence. During this sequence, the fill
valve opens and will remain open until the proper
water level is achieved. The automatic fill cycle has a
four-minute timer that will close the fill solenoid
valve and stop the pump. This safety has been
included in case there is a leak present that does not
allow the reservoir to fill up. After the initial fill cycle
is complete, the unit will automatically fill the tank if
the level gets too low. If the fill valve remains open
for more than 20 seconds, the unit will close the fill
solenoid valve and shut off the pump. The display
will show a 1as the first digit followed by the tank
temperature.
Stop
To stop the unit press the Stop button. When the
unit is stops, the status display and the last digital
display on the right will display a dot.
CAUTION: Stopping the unit without cooling the
water in the reservoir can lead to potential user
injury during servicing of the unit. In order to allow
the water in the reservoir to be cooled automatically
during shut down, depress the Temperature Adjust
button and the Password ‘C’ button to initiate an
automatic cool down cycle. The controller will open
the cooling valve and keep it open until the
temperature of the water in the reservoir is below
105°F (40°C). The automatic cool down cycle can be
stopped at any time by depressing the Off button.
Temperature Adjust
The Temperature Adjust button is used to view and
change the set point temperatures.
Display Set Point Temperature
To display the Set Point temperature press and
release the Temperature Adjust button. This will
show the Set Point temperature in the display. If no
other buttons are pressed for 5 seconds, the display
will return to the actual temperature.
Setting Set Point Temperature
To change the Set Point temperature press the
Temperature Adjust button and release to display
the current Set Point temperature and then
immediately used the Increase or Decrease buttons
to change the Set Point temperature until the
desired temperature is displayed. Once the desired
Set Point temperature displays, release all buttons.
After 5 seconds, the display will return to the actual
temperature and the new set point is active.
Increase
Pressing the Increase button increases the value of
the set point, deviation alarm, and timer settings
when those adjustment features are active.
Decrease
Pressing the Decrease button decreases the value of
the set point, deviation alarm, and timer settings
when those adjustment features are active.
Date & Time
Press the Timer button to display and adjust pump
running hours and automatic start/stop timers as
indicated below.

5
Displaying Pump Running Hours
Press the Date & Time button and release and
immediately press the Start button to display the
pump running hours. The pump running hours will
display for 5 seconds. If no other buttons are
pressed for 5 seconds, the display will return to the
actual temperature. The pump running hour counter
counts running hours in intervals of 1 hour up to
9,999 hours.
Resetting Pump Running Hour Counter
Resetting the pump running hour counter requires
three button presses in sequence. Press the Date &
Time button and release, press the Start button and
release, and press the Stop button and release to
reset the pump running hour counter. If no other
buttons are pressed for 5 seconds, the display will
return to the actual temperature.
Displaying Clock Time
Press and release the Date & Time button once to
display the current clock time. The time will display
for 5 seconds. If no other buttons are pressed for 5
seconds, the display will return to the actual
temperature.
Setting Clock Time
The clock timer is used for programming automatic
start and stop times. If the power to the unit is
disconnected, the clock resets to 0 0 0 0 hours (based
on a 24-hour clock with 0000 hours being midnight)
and will begin keeping time from that point forward
until reset. To adjust the time, press the Date & Time
button and release and immediately use the Increase
and Decrease buttons to set the current time.
Releasing all buttons sets the time to the time shown
in the display. After 5 seconds, the display will return
to the actual temperature and the new time is set.
Displaying Day of the Week
Press and release the Date & Time button twice to
display the internal clock timer day of the week. The
day of the week will display for 5 seconds. If no other
buttons are pressed for 5 seconds the display will
return to the actual temperature.
Setting Day of the Week
The day of the week is used for programming
automatic start and stop times. If the power to the
unit is disconnected, the day resets to Monday (Day
1) based on a 24-hour clock and will begin keeping
dates from that point forward until reset. To adjust
the day, press the Date & Time button twice, release,
and immediately use the Increase and Decrease
buttons to set the current day of the week as follows.
Releasing all buttons sets the day to the one shown
in the display. After 5 seconds, the display will return
to the actual temperature and the new day is set.
Timer On/Off
Pressing the Timer On/Off button is used to program
times and days for which the automatic 7 day, 24
hour timer will start and stop the unit. This is an
optional feature; however, it is available for
applications that require automatic preheating and
shutdown. It uses a common start and stop time for
all days of the week programmed to be active for the
timer program. Each day can be included or
excluded; however, all days will have the same start
and stop time. Once programmed, it is possible to
turn the timer on and off as desired.
Display Status of Timer
To display the status of the timer, three keystrokes
are required. Press the Date & Time button and
release, press the Date & Time button again and
release, and press the Timer On/Off button and
release to display the current timer status.
Turning Timer On/Off
To change the status of the timer, four keystrokes
are required. Press the Date & Time button and
release, press the Date & Time button again and
release, press the Timer On/Off button and release,
and if the timer status is not as desired press the On
button to toggle between timer on and timer off
status until the desired status is displayed as shown
in the above examples. Release all buttons after
selecting the timer status. If no other buttons are
pressed for 5 seconds the timer status is set and
display will return to the actual temperature.
Setting Start Time
To change the timer start time, press the Date &
Time button and release, press the Timer On/Off
button once and release. This will reset the display to
0 0 0 0. To adjust the start time, use the Increase and
Decrease buttons to set the desired start time (based
on a 24-hour clock). Releasing all buttons sets the
start time to the time shown in the display. After 5
seconds, the display will return to the actual
temperature and the new start time is set.

6
Setting Timer Stop Time
To change the timer stop time press the Date &
Time button and release, press the Timer On/Off
button and release, press the Timer On/Off button
again and release. This will reset the display to
0 0 0 0. To adjust the stop time, use the Increase and
Decrease buttons to set the desired start time (based
on a 24-hour clock). Releasing all buttons sets the
start time to the time shown in the display. After 5
seconds, the display will return to the actual
temperature and the new start time is set.
Setting Timer Days for Automatic Start/Stop
Depressing the Timer Adjust button twice and then
immediately depressing the Timer On/Off button
once will reset the display to show the settings for
Monday. When reviewing the settings for each day
of the week, the first digit on the left of the display
indicates the day of the week and the remaining four
digits of the display indicate the activation status of
that day. If there is a decimal in the first and third
digits for the day, automatic start/stop is scheduled.
If there is there is a decimal in the second and third
digits for the day, automatic start/stop is not
scheduled.
To change the day of the week, use the Increase and
Decrease buttons. Once the desired day is displayed,
use the On button to toggle the status of the timer
for that day.
Examples of days of week displays
Monday (timer off)
1
.
.
Monday (time on)
1
.
.
Tuesday (timer off)
2
.
.
Tuesday (timer on)
2
.
.
Wednesday (timer off)
3
.
.
Wednesday (timer on)
3
.
.
Thursday (timer off)
4
.
.
Thursday (timer on)
4
.
.
Friday (timer off)
5
.
.
Friday (timer on)
5
.
.
Saturday (timer off)
6
.
.
Saturday (timer on)
6
.
.
Sunday (timer off)
7
.
.
Sunday (timer on)
7
.
.
Starting with Monday, toggle the schedule status
using the On button until the desired status is
reached, and then used the Increase button to move
to the next day and repeat the process until all days
are programed as desired and release all buttons.
After 5 seconds, the display will return to the actual
temperature and the days for automatic start/stop
are set.
Deviation Alarm
Depressing the Deviation Alarm Adjust button will
show the current deviation alarm set point in the
display. The deviation alarm set point is the number
of degrees the tank temperature must rise above the
set point before the alarm horn will activate. When
active and an alarm condition occurs, the Deviation
Alarm light illuminates, the alarm horn sounds, and
voltage will be at terminal XI on the control board.
Note: There is a 45 minute time deviation alarm delay after initial
start-up to minimize the potential for unwanted alarms during
initial start-up as the unit brings the system up to operating
temperature.

7
Setting Deviation Alarm Temperature
To change the deviation alarm temperature press
the Deviation Alarm button and release and use the
Increase and Decrease button to change the degrees
of deviation from the set point temperature at which
the deviation alarm will activate. Once the desired
deviation is displayed release all button to set. After
5 seconds, the display will return to the actual
temperature and the new deviation alarm is set.
Example of deviation set for 20°F off Set Point temperature
A
2
0
Activating Deviation Alarm
To activate the deviation alarm, press the Deviation
Alarm button and release and immediately press the
On button and release. After 5 seconds without a
button push, the display will return to the actual
temperature and the deviation alarm is activate.
Example of deviation alarm activated
A
-
1
-
Deactivating Deviation Alarm
To deactivate the deviation alarm, press the
Deviation Alarm button and release and immediately
press the Off button and release. After 5 seconds
without a button push, the display will return to the
actual temperature and the deviation alarm is
inactive.
Example of deviation alarm deactivated
A
-
0
-
Tank Temperature
Pressing the Tank Temperature button shows the
current tank temperature in the display.
Password Entry
Pressing the Password Entry buttons will allow for
secured access to the control program and will
prevent unauthorized personnel from making
changes. The correct four-letter password will be
required to adjust temperatures or timer functions.
The password remains in memory even if the power
is disconnected.
Entering or Changing Password
To enter or change a password, use the following
steps.
1. Press the Off button to stop the unit.
2. Press and hold the C button until the display
shows the following. This opens the password
menu.
Example of password menu open
C
0
3. Enter four letters in the desire password
sequence using the A, B, and C buttons. The
controller will count the number of letters
entered and will show the number entered in the
far right digital display. When all four letters are
entered, the display shows the following.
Example of deviation alarm activated
C
4
4. Press the Off button to confirm the password.
5. Press the On button to start the unit. The unit
will now require a correct password for a change
in set point temperature to occur.
Deleting Password
To delete the password, use the following steps.
1. Press the Off button to stop the unit.
2. Press and hold the C button until the display
shows the following. This opens the password
menu.
Example of password menu open
C
0
3. Press the Off button to clear the password. The
display shows the following.

8
Example of password deleted, no password entered
C
.
4. Press the On button to start the unit. The set
point temperature can occur without the need
for a password.
Pump Status Indicator
There are two indicating lights in the Pump icon.
When the pump is on the upper LED will be green.
When the pump overloads the lower LED will be
yellow.
Heating Status Indicator
There are two indicating lights in the Heating icon.
When Heater 1 is on the upper LED will be green.
When Heater 2 is on the lower LED will be green.
Cooling Status Indicator
When the cooling valve is open, the LED in the
Cooling icon will be green.
Low Level Alarm Indicator
The LED in the Low Level icon will be yellow when
the oil level in the reservoir is too low.
Deviation Alarm Indicator
The LED in the Deviation Alarm icon will be green
when the Deviation Alarm is active. The LED will not
be on if the Deviation Alarm has been turned off.
Automatic Timer Status Indicator
The LED in the Timer icon will be green when the
Automatic Start/Stop Timer is active. The LED will
not be on if the Automatic Start/Stop Timer is not
active.
Controller Control Fault Logic
Alarm
Condition
Indication
Tank Low Level
Low Level Alarm indicator light on
Temperature display flashing
Alarm horn on and X1 output powered
Temperature
Deviation
Temperature Deviation Alarm indicating light on
Temperature display flashing
Alarm horn on and X1 output powered
Temperature
Sensor Short
Circuit
Temperature display flashing
Alarm horn on and X1 output powered
Temperature
Sensor
Disconnected
Temperature display flashing
Alarm horn on and X1 output powered
Draining the Mold
The temperature control unit is equipped with a
specific program that can automatically cool to
105°F before draining the mold. To initiate a mold
drain sequence depress the Temperature Adjust
button and then immediately depress the On button.
The display will show ‘E’ followed by the actual
temperature in the tank. The cooling solenoid valve
opens and will remain energized unit the tank
temperature drops to 105°F. When the tank
temperature reached 105°F, the alarm horn will
sound to signal the mold is ready for draining.
Once the unit has cooled to 105°F, close the vacuum
adjusting valve and remove the hose on the valve.
The vacuum created will automatically pull the water
through the hoses and the mold back to the unit.
When the unit is finished draining, turn the unit off
by depressing the Off button and remove the hoses.
Start-up
Every unit is factory set to deliver oil in accordance
with the standard operating specifications for that
particular unit. Due to variables involved with
different applications and different installations,
minor adjustments may be required during the initial
start-up to ensure proper operation. Use a qualified
technician to perform the start-up procedure in
sequence. The following serves as a checklist for the
initial start-up and for subsequent start-ups if the
unit is out of service for a prolonged time.
WARNING: This equipment contains hazardous
voltages that can cause severe injury or death.

9
WARNING: This equipment contains hot water or
coolant under pressure. Accidental release of hot water
or coolant under pressure can cause personal injury
and or property damage.
WARNING: This equipment may contain fan blades or
other sharp edges. Make sure all fan guards and other
protective shields are securely in place.
WARNING: The exposed surfaces of motors, piping,
and other fluid circuit components can be very hot
and can cause burns if touched with unprotected
hands.
CAUTION: Disconnect and lock out incoming power
before installing, servicing, or maintaining the
equipment. Connecting power to the main terminal
block energizes the entire electric circuitry of the unit.
Electric power at the main disconnect should be shut
off before opening access panels for repair or
maintenance.
CAUTION: Wear eye protection when installing,
maintaining, or repairing the equipment to protect
against any sparks, debris, or fluid leaks.
CAUTION: Wear protective gloves when installing,
maintaining, or repairing the equipment to protect
against any sparks, debris, or fluid leaks.
CAUTION: Wire the unit ground in compliance with
local and national codes.
Step 1 –Connect Main Power
Connect main power properly ensuring it matches
the voltage shown on the nameplate of the unit.
Check the electrical phase sequence prior to start-
up. Operation of the unit with incorrect electrical
phase sequencing will cause damage to
components. Check the phasing prior to applying
power. The proper sequence is “ABC.” If the phasing
is incorrect, open the main power disconnect and
switch two line leads on the main power terminal
blocks (or the unit mounted disconnect). All
electrical components are in-phase at the factory. Do
not interchange any load leads that are from the unit
contactors or the motor terminals. After making
proper power connection and grounding, turn the
main power on.
Step 2 –Fill Coolant Circuit
Check to make sure all piping connections are secure
and that all lines are suitable for water or the coolant
in the system at the maximum set point temperature
and cumulative pressure rating of the maximum
pump pressure and the unit fill fluid pressure.
NOTE: A cooling source inlet filter ships loose in the crate with the
unit. Install this in the inlet of the chilled water line before
connecting the cooling source line.
Make sure that the cooling source is the appropriate
temperature and pressure for your application. In
most cases, the cooling source is between 40°F and
85°F. The cooling source fluid pressure must be
above the set point of the pressure switch in order
for the unit to start. For most applications, the
design cooling source supply pressure is between 25
psi and 50 psi. Units with the 300°F operating range
option require an inlet cooling source pressure of 75
psi. If the total pressure in the unit (cooling source
inlet pressure plus the pump pressure) exceeds 150
psi, the pressure relief valve in the unit will open. If
this becomes an issue, install a pressure-regulating
valve (Part #9616548 available from our Parts
Department) on the supply line to help regulate the
pressure to ensure it does not exceed the pressure
rating of the pressure relief valve. For further
assistance in installing a pressure-regulating valve,
please contact our Customer Service Department.
System Fill Water Chemistry Requirements
The properties of water make it ideal for heat
transfer applications. It is safe, non-flammable, non-
poisonous, easy to handle, widely available, and
inexpensive in most industrialized areas.
When using water as a heat transfer fluid it is
important to keep it within certain chemistry limits to
avoid unwanted side effects. Water is a “universal
solvent” because it can dissolve many solid
substances and absorb gases. As a result, water can
cause the corrosion of metals used in a cooling
system. Often water is in an open system (exposed
to air) and when the water evaporates, the dissolved
minerals remain in the process fluid. When the
concentration exceeds the solubility of some
minerals, scale forms. The life giving properties of
water can also encourage biological growth that can
foul heat transfer surfaces.
To avoid the unwanted side effects associated with
water cooling, proper chemical treatment and
preventive maintenance is required for continuous
plant productivity.

10
Unwanted Side Effects of Improper Water Quality
•Corrosion
•Scale
•Fouling
•Biological Contamination
Cooling Water Chemistry Properties
•Electrical Conductivity
•pH
•Alkalinity
•Total Hardness
•Dissolved gases
The complex nature of water chemistry requires a
specialist to evaluate and implement appropriate
sensing, measurement and treatment needed for
satisfactory performance and life. The
recommendations of the specialist may include
filtration, monitoring, treatment and control devices.
With the ever-changing regulations on water usage
and treatment chemicals, the information is usually
up-to-date when a specialist in the industry is
involved. The table below shows the list of water
characteristics and quality limitations.
Table 1 - Fill Water Chemistry Requirements
Water Characteristic
Quality Limitation
Alkalinity (HCO3-)
70-300 ppm
Aluminum (Al)
Less than 0.2 ppm
Ammonium (NH3)
Less than 2 ppm
Chlorides (Cl-)
Less than 300 ppm
Electrical Conductivity
10-500µS/cm
Free (aggressive) Carbon Dioxide (CO2)†
Less than 5 ppm
Free Chlorine(Cl2)
Less than 1 PPM
HCO3-/SO42-
Greater than 1.0
Hydrogen Sulfide (H2S)
Less than 0.05 ppm
Iron (Fe)
Less than 0.2 ppm
Manganese (Mn)
Less than 0.1 ppm
Nitrate (NO3)
Less than 100 ppm
pH
7.5-9.0
Sulfate (SO42-)
Less than 70 ppm
Total Hardness (dH)k
4.0-8.5
† Dissolved carbon dioxide calculation is from the pH and total
alkalinity values shown below or measured on the site using a test
kit. Dissolved Carbon Dioxide, PPM = TA x 2[(6.3-pH)/0.3] where TA =
Total Alkalinity, PPM as CaCO3
Table 2 –Recommend Glycol Solutions
Chilled Water Temperature
Percent Glycol By Volume
50°F (10°C)
Not required
45°F (7.2°C)
5 %
40°F (4.4°C)
10 %
35°F (1.7°C)
15 %
30°F (-1.1°C)
20 %
25°F (-3.9°C)
25 %
20°F (-6.7°C)
30 %
CAUTION: When your application requires the use of
glycol, use industrial grade glycol specifically
designed for heat transfer systems and equipment.
Never use glycol designed for automotive
applications. Automotive glycols typically have
additives engineered to benefit the materials and
conditions found in an automotive engine; however,
these additives can gel and foul heat exchange
surfaces and result in loss of performance or even
failure of the chiller. In addition, these additives can
react with the materials of the pump shaft seals
resulting in leaks or premature pump failures.
WARNING: Ethylene Glycol is flammable at higher
temperatures in a vapor state. Carefully handle this
material and keep away from open flames or other
possible ignition sources.
Step 3 –Start the Unit
To start the unit press the Start button. If the water
level in the reservoir is too low, the display will show
F I L L and the Low Level Alarm Indicator light will
turn on. The Low Level Alarm Indicator light will
remain on until the water level is sufficient for
operation.
Step 4 –Check Pump Rotation
Check the rotation of the pump by visually
confirming the motor shaft rotation matches the
directional arrow sticker on the motor case. If the
pump is running backwards, switch two of the main
power leads, after shutting off the disconnect switch.
Step 5 –Enter Set Point Temperature
To display the Set Point temperature press and
release the Temperature Adjust button. This will
show the Set Point temperature in the display. If no
other buttons are pressed for 5 seconds, the display
will return to the actual temperature.
Setting Set Point Temperature
To change the Set Point temperature press the
Temperature Adjust button and release to display

11
the current Set Point and then immediately used the
Increase or Decrease buttons to change the Set
Point until the desired temperature displays. Once
the desired Set Point displays, release all buttons.
After 5 seconds, the display will return to the actual
temperature and the new set point is active.
Step 6 - Adjusting the Vacuum
Adjust the positive/negative flow through the mold
by using the vacuum adjusting valve on top of the
back panel. Start by fully closing this valve so that
the injector makes a vacuum in the return line from
process. The vacuum created allows air to enter the
circuit through any leaks that are present. Opening
the adjusting valve slowly allows water to flow to the
mold and pressurizes the supply line. The leak will
reappear as the pressure increases. Slowly closing
the adjusting valve now eliminates the leak.
The unit is now ready for service.
Preventive Maintenance
Once the unit is in service, we suggest following the
maintenance procedures as closely as possible. The
importance of a properly established preventive
maintenance program cannot be overemphasized.
Taking the time to follow these simple procedures
will result in substantially reduced downtime,
reduced repair costs, and an extended useful lifetime
for the unit. The following is a list of suggested
periodic maintenance.
Once a Week
1. Check to make sure that the To Process
temperature is reasonably close to the Set Point
temperature. If the temperature stays more than
5°F away from the set point, there may be a
problem with the unit. If this is the case, refer to
the General Troubleshooting section of this
manual or contact our Customer Service
Department.
2. Check the pump discharge pressure. Investigate
further if the pressure starts to stray away from
the normal operating pressure.
3. Check the pump for leaks in the seal area.
Replace pump seal if necessary.
Once a Month
Repeat items 1 through 3 listed above and continue
with the following.
4. With the main power shut off, check the
condition of electrical connections at all
contactors, starters, and controls. Check for
loose or frayed wires.
5. Check the incoming voltage to make sure it is
within 10% of the design voltage for the
temperature control unit.
6. Check the amp draws to each leg of the pump
and heaters to confirm that they are drawing the
proper current.
7. Check the heat exchanger inlet strainer and
clean debris out as necessary.
8. Check the condition of the oil and replace as
necessary as instructed by the oil manufacturer.
Once a Year
Repeat items 1 through 8 as listed above and
continue with the following.
9. Carefully inspect the heat exchanger for signs of
scale build-up and carefully clean and remove
scale as necessary.
CAUTION: The amount of scale build-up is
dependent upon the amount of cooling required for
each process along with the quality of the cooling
water supply. We have supplied the unit with a
copper heat exchanger. We recommend you clean
the heat exchanger thoroughly on a periodic basis, or
after each job, to allow for the longest life and
highest heat removal potential of the unit. If the heat
exchanger becomes completely blocked, lime scale
removal will be impossible.

12
General Troubleshooting
Problem
Possible Cause
Remedy
The unit does not start after connection, tank
filling, and pressing the On button
Main fuses blown
Replace blown fuses
Motor defective
Contact factory
Reset tripped
Reset
Control circuit breaker tripped
Reset
Motor buzzes after pressing the On button
and overload trips
Voltage on two of the phases only
Check incoming power supply, check and
replace blown fuse
Motor defective
Contact factory
No water circulation, even though the pump
is rotating
Pump is rotating in the wrong direction
Change two of the incoming power leads
Process water lines clogged
Clean lines
The unit does not heat
Contactor defective
Replace contactor
Thermostat defective
Replace thermostat
Heating element defective
Replace heating element
Safety fuse defective
Replace safety fuse
The unit does not cool
Solenoid valve at “Cooling Water In” defective
Replace solenoid valve
Cooling heat exchanger clogged
Clean coil
Thermostat defective
Replace thermostat
The unit cooling all the time
Dirt in the cooling solenoid valve
Take apart the valve, clean out, replace if
required
Thermostat defective
Replace thermostat
Water comes out the overflow pipe
Tank overfilled
Drain some water
Dirt in the fill solenoid valve
Take apart the valve, clean out, replace if
required
Level sensing probe dirty or defective
Clean probe, replace if required
The unit does not fill the tank, level lamp is
not on
Level sensing probe dirty or defective
Clean probe, replace if required
Defective microprocessor
Contact factory
The unit does not fill the tank, level lamp is on
Water supply not connected
Connect supply
Defective fill solenoid valve
Replace if required

13
Charts and Drawings
Figure 1 –Pump Performance (60 Hz)

14
Figure 2 –Cooling Capacity

15
Figure 3 –High Voltage Wiring Diagram

16
Figure 4 –Low Voltage Wiring Diagram
Table of contents
Other Thermal Care Temperature Controllers manuals
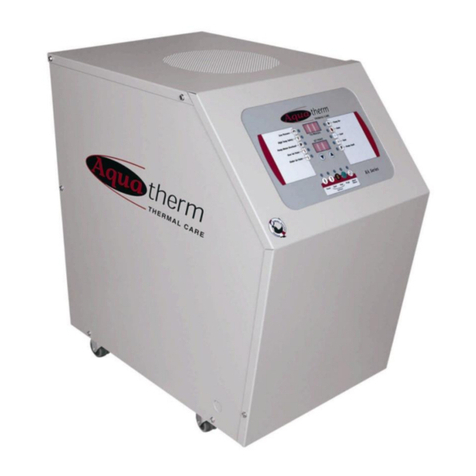
Thermal Care
Thermal Care RA Series User manual
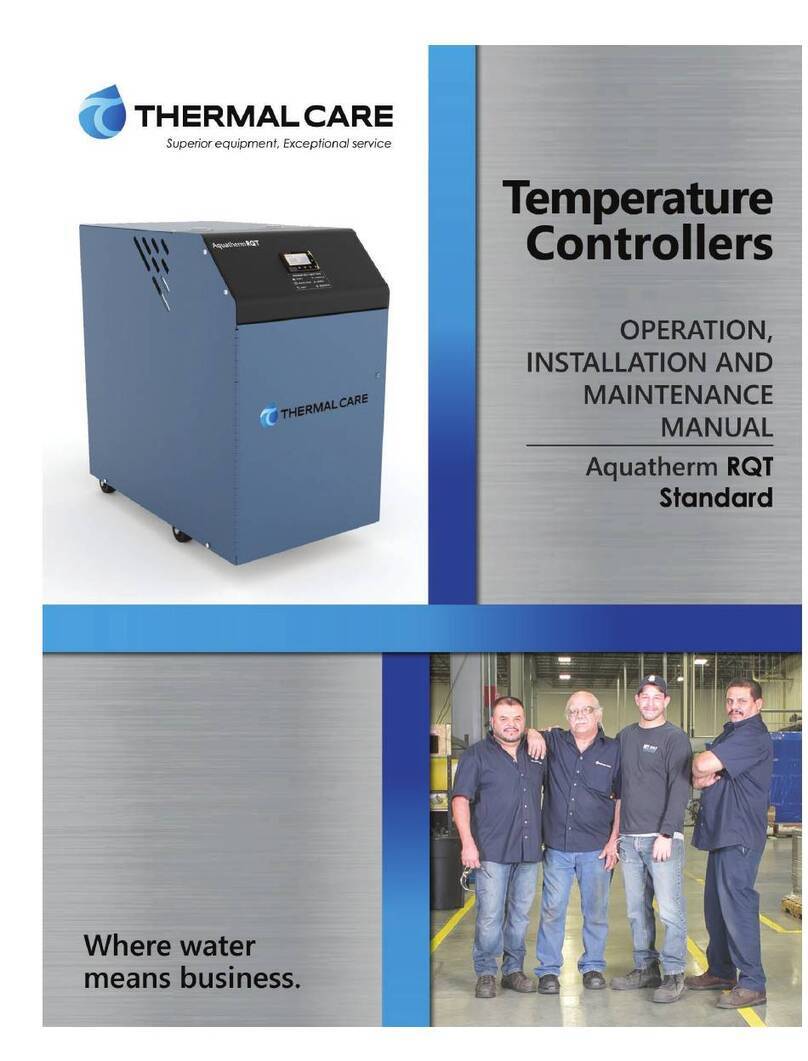
Thermal Care
Thermal Care Aquatherm RQT Standard Instruction Manual
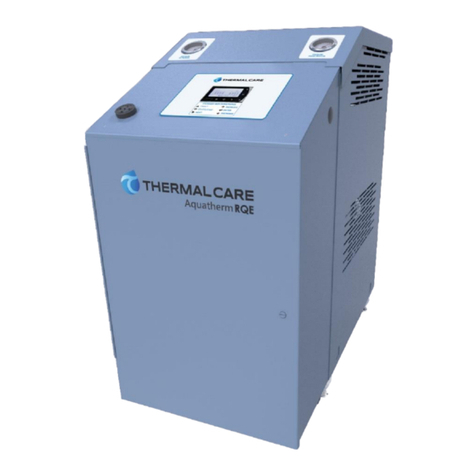
Thermal Care
Thermal Care Aquatherm RQE Instruction Manual
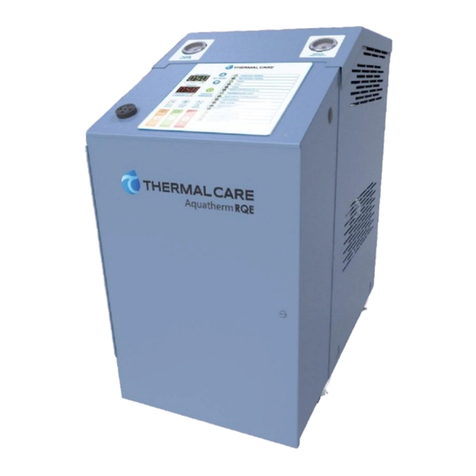
Thermal Care
Thermal Care Aquatherm RQE Instruction Manual
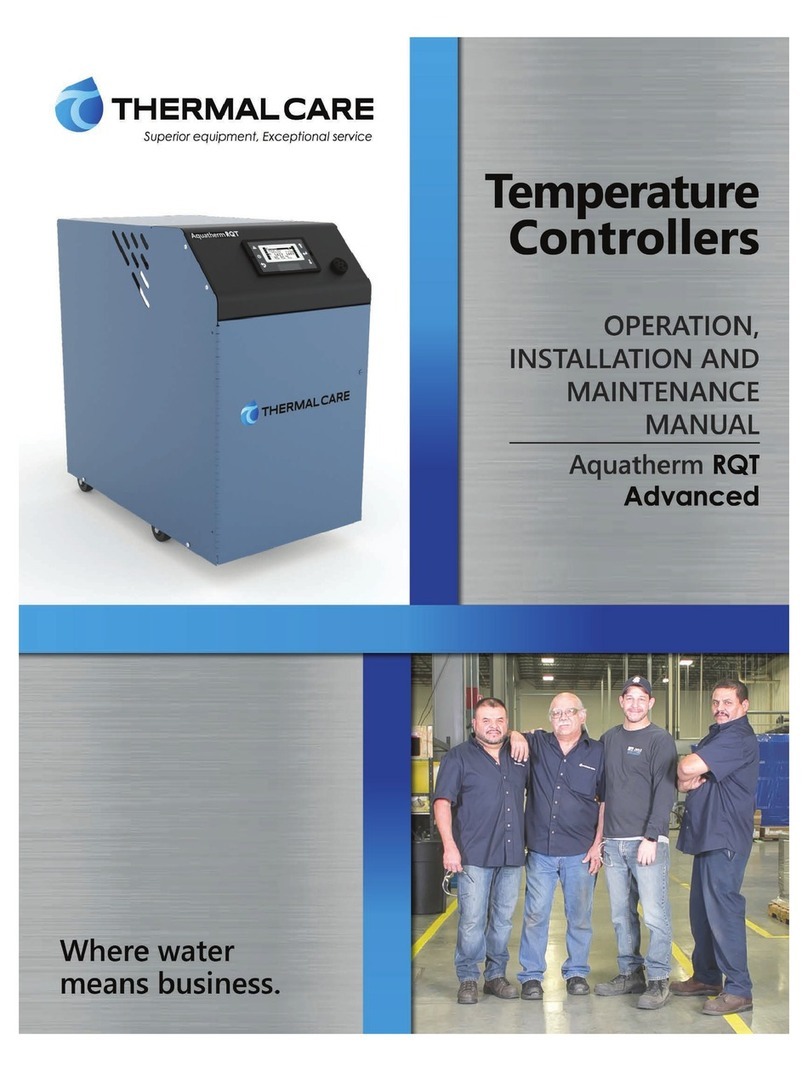
Thermal Care
Thermal Care Aquatherm RQT Advanced Instruction Manual
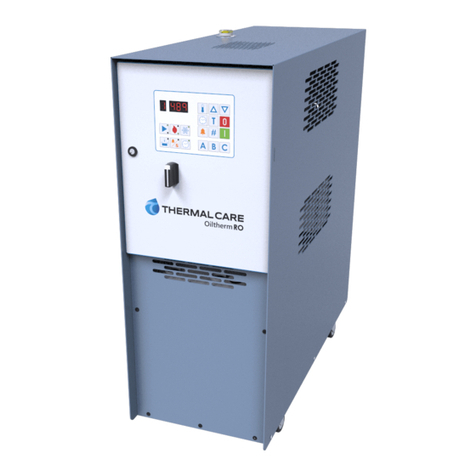
Thermal Care
Thermal Care Oiltherm RO Instruction Manual

Thermal Care
Thermal Care Aquatherm RQT Premium Instruction Manual