THORLABS Kinesis MLJ050 User manual

MLJ050
Motorized Lab Jack
Kinesis User Guide
Original Instructions

2 HA0276T Rev Bk Jan 2017
Contents
Chapter 1 Safety ............................................................................................ 3
1.1 Safety Information .................................................................................. 3
1.2 General Warnings .................................................................................. 3
Chapter 2 Overview ........................................................................................4
2.1 Introduction ............................................................................................. 4
Chapter 3 Mechanical Installation ................................................................ 8
3.1 Unpacking .............................................................................................. 8
3.2 Environmental Conditions ...................................................................... 8
3.3 Mounting to a Work Surface ................................................................... 8
3.4 Transportation ...................................................................................... 10
3.5 Dimensions ........................................................................................... 10
Chapter 4 Software & Electrical Installation ..............................................11
4.1 Installing Software ................................................................................ 11
4.2 Electrical Installation ............................................................................. 11
4.3 Connecting The Hardware ................................................................... 12
4.4 Verifying Software Operation ............................................................... 13
Chapter 5 Standalone Operation ................................................................ 14
5.1 Introduction ........................................................................................... 14
5.2 Top Panel Controls and Indicators ...................................................... 14
5.3 Potentiometer Operation ...................................................................... 15
5.4 Button Operation .................................................................................. 15
Chapter 6 PC Operation ............................................................................... 16
6.1 Introduction ........................................................................................... 16
6.2 Using the Kinesis Software .................................................................. 16
6.3 Homing Motors ..................................................................................... 17
6.4 Stopping the Stage ............................................................................... 17
6.5 Changing Motor Parameters and Moving to an Absolute Position ....... 18
6.6 Jogging ................................................................................................. 19
6.7 Setting Move Sequences ..................................................................... 20
6.8 Changing and Saving Parameter Settings ........................................... 20
Chapter 7 Software Reference ....................................................................21
7.1 Introduction ........................................................................................... 21
7.2 GUI Panel ............................................................................................. 21
7.3 Settings Panel ...................................................................................... 23
Appendices
Appendix A Preventive Maintenance ......................................................... 33
Appendix B Specifications .......................................................................... 34
Appendix C Stepper Motor Operation ........................................................ 35
Appendix D Regulatory ................................................................................ 40
Appendix E Thorlabs Worldwide Contacts ................................................ 44

3
Chapter 1 Safety
1.1 Safety Information
For the continuing safety of the operators of this equipment, and the protection of the
equipment itself, the operator should take note of the Warnings, Cautions and Notes
throughout this handbook and, where visible, on the product itself.
The following safety symbols may be used throughout the handbook and on the
equipment itself.
1.2 General Warnings
Shock Warning
Given when there is a risk of injury from electrical shock.
Warning
Given when there is a risk of injury to users.
Caution
Given when there is a risk of damage to the product.
Note
Clarification of an instruction or additional information.
Warnings
If this equipment is used in a manner not specified in the handbook, the
protection provided by the equipment may be impaired. In particular,
excessive moisture may impair operation.
Spillage of fluid, such as sample solutions, should be avoided. If spillage does
occur, clean up immediately using absorbant tissue. Do not allow spilled fluid
to enter the internal mechanism.
The equipment is for indoor use only.
When running custom move sequences, or under fault conditions, the stage
may move unexpectedly. Operators should take care when working inside the
moving envelope of the stage.

4
Chapter 2 Overview
2.1 Introduction
The MLJ050 series are a range of stepper-motor driven lab jacks. The integrated
electronic controller can either be driven via a PC or can be controlled manually via
the buttons and velocity potentiometer on the control key pad. These Motorized Lab
Jacks provide a rugged, height adjustable platform ideal for mounting optomechanical
sub-assemblies requiring height adjustment. The MLJ050 Motorized Lab Jack offers
excellent rigidity and platform parallelism while providing smooth, quiet motion.
Integral limt switches prevent overdriving. The large 5.6" x 4.9" (125 mm x 142 mm)
mounting platform supports up to 44 lbs (20 kg) with a smooth vertical adjustment
range of 2" (50 mm). Both the top and bottom plates offer a generous array of 1/4" -
20 (M6) tapped holes and clearance slots for general mounting requirements.
Fig. 2.1 MLJ050 Motorized Lab Jack

5
MLJ050 Motorized Lab Jack
2.1.1 Introduction
The MLJ050 stages share many of the benefits of the Thorlabs range of motor
controllers. These include USB connectivity (allowing multiple units to be used
together on a single PC), fully featured Graphical User Interface (GUI) panels, and
extensive software function libraries for custom application development.
The Kinesis software suite provides a flexible and powerful PC based control system
both for users of the equipment, and software programmers aiming to automate its
operation.
The User Interface allows full control of all settings and operating modes enabling
complete ‘out-of-box’ operation without the need to develop any further custom
software. It provides all of the necessarysystem software services such as generation
of GUI panels, communications handling for multiple USB units, and logging of all
system activity to assist in hardware trouble shooting. The Kinesis server is also used
by software developers to allow the creation of advanced automated positioning
applications very rapidly and with great ease.
2.1.2 Kinesis Server
Kinesis controls are re-usable compiled software components that supply both a
graphical user interface and a programmable interface. Many such Controls are
available for Windows applications development, providing a large range of re-usable
functionality. For example, there are Controls available that can be used to
manipulate image files, connect to the internet or simply provide user interface
components such as buttons and list boxes.
With the Kinesis system, .Net Controls are deployed to allow direct control over (and
also reflect the status of) the range of electronic controller units, including the MLJ050
stages. Software applications that use .Net Controls are often referred to as 'client
applications'. A .Net Control is a language independent software component.
Consequently the controls can be incorporated into a wide range of software
development environments for use by client application developers. Development
environments supported include Visual Basic, Labview, Visual C++, C++ Builder,
HPVEE, Matlab, VB.NET, C#.NET
and, via VBA, Microsoft Office applications such as
Excel and Word.

6 HA0276T Rev Bk Jan 2017
Chapter 2
Consider the control supplied for the MLJ050 integrated Labjack & controller.
This Control provides a complete user graphical instrument panel to allow the stage
to be manually operated, as well as a complete set of software functions (often called
methods) to allow all parameters to be set and motor operations to be automated by
a client application. The instrument panel reflects the current operating state of the
controller unit to which it is associated (e.g. such as motor position). Updates to the
panel take place automatically when a user (client) application is making software
calls into the same Control. For example, if a client application instructs the
associated stage to move, the progress of that move is reflected automatically by
changing position readouts on the graphical interface, without the need for further
programming intervention.

7
MLJ050 Motorized Lab Jack
The Kinesis Controls collection provides a rich set of graphical user panels and
programmable interfaces allowing users and client application developers to interact
seamlessly with the Kinesis hardware. Each of the Kinesis controllers has an
associated .Net Control and these are described fully in the handbooks associated
with the controllers.
Fig. 2.2 System Architecture Diagram
Refer to the main Kinesis Software online help file, for a complete programmers guide
and reference material on using the Kinesis Controls collection. This is available
either by pressing the F1 key when running the Kinesis server, or via the Start menu,
Start\Programs\Thorlabs\Kinesis\Kinesis Help.
2.1.3 Software Upgrades
Thorlabs operate a policy of continuous product development and may issue software
upgrades as necessary.

8 HA0276T Rev Bk Jan 2017
Chapter 3
Chapter 3 Mechanical Installation
3.1 Unpacking
3.2 Environmental Conditions
Location Indoor use only
Maximum altitude 2000 m
Temperature range 5oC to 40oC
Maximum Humidity Less than 80% RH (non-condensing) at 31°C
To ensure reliable operation the unit should not be exposed to corrosive agents or
excessive moisture, heat or dust.
If the unit has been stored at a low temperature or in an environment of high humidity,
it must be allowed to reach ambient conditions before being powered up.
The unit must not be used in an explosive environment.
3.3 Mounting to a Work Surface
3.3.1 General
When mounting the lab jack close to other equipment, ensure that the travel of the
moving platform is not obstructed. If equipment mounted on the moving platform is
driven against a solid object, damage to the internal mechanism could occur. The
range of travel is 2.0” (50 mm) vertically.
Note
Retain the packing in which the unit was shipped, for use in future
transportation.
Caution
Once removed from its packaging, the MLJ050 lab jack is easily damaged
by mishandling. The unit should only be handled by its base, not by the
motor or any attachments to the moving platform.
Warning
Operation outside the following environmental limits may adversely
affect operator safety.
Warning
The safety of any system incorporating this equipment is the
responsibility of the person performing the installation.

9
MLJ050 Motorized Lab Jack
3.3.2 Mounting the Stage to the Work Surface
The MLJ050 lab jack is mounted to the working surface by four M6 (1/4-20) screws
through the base as shown in Fig. 3.1.. .
Fig. 3.1 Installation
Note
The mounting holes are accessible with the lab jack fully retracted. The
unit must be powered down or disabled before fixing to the work surface.
4 Bolts M6 (1/4-20)
(2 each side)

10
3.4 Transportation
3.5 Dimensions
Fig. 3.2 Dimensions - MLJ050
Caution
When packing the unit for shipping, use the original packing. If this is not
available, use a strong box and surround the unit with at least 100 mm of
shock absorbent material.
all dimensions in mm (in.) 142.0 (5.59)
25.0 (1.0)
25.0 (1.0)
25.0 (1.0)
125.0
(4.92)
100.0
(3.94)
210.5
(8.29)
25 x M6 (1/4”-20) Tapped
Holes for Mounting
116.0
(4.57)
MAXIMUM EXTENDED
POSITION
MAXIMUM RETRACTED
POSITION
65.00
(2.56)

11
MLJ050 Motorized Lab Jack
Chapter 4 Software & Electrical Installation
4.1 Installing Software
DO NOT CONNECT THE STAGE TO YOUR PC YET
1) Download the software from www.thorlabs.com.
2) Locate the downloaded setup.exe file and move to a suitable file location.
3) Double-click the setup.exe file and follow the on-screen instructions.
4.2 Electrical Installation
4.2.1 Connecting To The Supply
Caution
Some PCs may have been configured to restrict the users ability to load
software, and on these systems the software may not install/run. If you are
in any doubt about your rights to install/run software, please consult your
system administrator before attempting to install.
Ifyou experienceanyproblems when installingsoftware, contactThorlabson
+44 (0)1353 654440 and ask for Technical Support.
Shock Warning
The PSU unit must be connected only to an earthed fused supply of 100 to 240V.
Use only the power supply supplied by Thorlabs, other units may not be rated
to the same current.
The unit is shipped to the UK, Europe and the USA, with the appropriate
power plug already fitted. When shipped to other territories the appropriate
power plug must be fitted by the user. Cable identification is as follows:
Brown: Live Blue: Neutral Green/Yellow: Earth/Ground
When connecting the power and USB cables, ensure they are routed clear
of the moving platform.

12 HA0276T Rev Bk Jan 2017
Chapter 4
4.3 Connecting The Hardware
1) Perform the mechanical installation as detailed in Section 3.
2) Install the Software - see Section 4.1.
3) Using the USB cable supplied, connect the stage unit to your PC.
4) Connect the stage to the power supply - see Section 4.2.1.
5) Connect the PSU to the main supply and switch ‘ON’.
6) Wait for the unit to initialize (about 5 sec). Do not press any controls during this
time. The ACTIVE LED is extinguished or flashing when the unit is ready for use.
7) WindowsTM should detect the new hardware. Wait while WindowsTM installs the
drivers for the new hardware - see the Getting Started guide for more information.
Fig. 4.1 Power and USB Connectors
Note
The USB cable should be no more than 3 metres in length. Communication
lengths in excess of 3 metres can be achieved by using a poweredUSB hub).
_
+

13
4.4 Verifying Software Operation
4.4.1 Initial Setup
1) Run the Kinesis softwareand check that the Graphical User Interface (GUI) panel
appears and is active.
Fig. 4.2 Gui panel showing jog and ident buttons
2) Click the ‘Identify’ button. The POWER LED on the control keypad flashes. This is
useful in multi-channel systems for identifying which driver unit is associated with
which GUI.
3) Click the jog buttons on the GUI panel and check that the associated stage moves.
The position display for the associated GUI should increment and decrement
accordingly.

14 HA0276T Rev Bk Jan 2017
Chapter 5
Chapter 5 Standalone Operation
5.1 Introduction
The MLJ050 lab jack offers a fully featured motion control capability including velocity
profile settings, limit switch handling, and homing sequences. When the unit is
connected to the PC, these parameters are automatically set to allow “out of the box”
operation with no further “tuning” required. However, further adjustment is possible
via the Kinesis Server software - see Chapter 6.
The following brief overview explains how the top panel controls can be used to
perform a typical series of motor moves.
In conjunction with this chapter, it also may be useful to read the background on
stepper motor operation contained in Appendix C .
5.2 Top Panel Controls and Indicators
Fig. 5.1 Front Panel Controls and Indicators
MOVE Controls - These controls allow all motor moves to be initiated.
Jog Buttons - Used to jog the motors and make discrete position increments in
either direction (left button up, right button down) - see Section 6.6. for more
details on jogging.
Slider Potentiometer - Used to drive the motor at a pre-defined speed in either
forward or reverse directions for full and easy motor control - see Section 5.3.
ACTIVE LED - The Active LED will flash when the motor reaches a forward or reverse
limit switch, and is lit when the motor is moving.
Warning
As the unit is raised and lowered, items can become trapped in the
mechanism. During operation, keep fingers, clothing and tools away from
any moving parts.
Motorized Labjack
VELOCITY
ACTIVE
MOVE/JOG
POWER

15
MLJ050 Motorized Lab Jack
POWER LED - When the stage is enabled, this LED is lit. Furthermore, this LED will
flash when the ‘Ident’ button is clicked on the Kinesis GUI panel.
5.3 Potentiometer Operation
The potentiometer slider is sprung such that when released it returns to it’s central
position. In this central position the motor is stationary. As the slider is moved away
from the centre, the motor begins to move. Bidirectional control of the motor is
possible by moving the slider in both directions.
5.4 Button Operation
The keypad can be used to control the motor in a number of ways, as follows.
5.4.1 Homing
A ‘Home’ move is performed to establish a datum from which subsequent absolute
position moves can be measured (see Section 6.3. and Section C.2.2. for further
information on the home position).
To initiate a ‘Home’ move, press and hold both buttons for 2 seconds.
5.4.2 Jogging
The front panel buttons can also be used to ‘jog’ the motor. The jogging parameters
for the buttons are taken from the ‘Jog’ parameters on the ‘Move/Jogs’ settings tab -
see Section 7.3.
Note
The two buttons and the slider on the user top panel can be disabled if
required. To do this, hold down both buttons and tehn power up the unit.
Continue to hold down the buttons until the green POWER LED is lit. This
setting is then persisted, and the buttons will remain disabled until the user
again holds down both buttons on power up, at which point the user interface
becomes operable again.

16
Chapter 6 PC Operation
6.1 Introduction
The following brief tutorial guides the user through a typical series of moves and
parameter adjustments performed using the Kinesis software. It assumes that the unit
is electrically connected as described in Section 4.2. and that the software is already
installed - see Section 4.1.
6.2 Using the Kinesis Software
The Kinesis software application allows the user to interact with any number of
hardware control units connected to the PC USB Bus. This program allows multiple
graphical instrument panels to be displayed so that multiple units can be controlled.
All basic operating parameters can be set through this program, and all basic
operations (such as motor moves) can be initiated. Parameter settings can be saved,
which simplifies system set up whenever the software is run up.
Fig. 6.1 Typical Kinesis User Screen
1) Run the Kinesis software - Start/All Programs/Thorlabs/Kinesis/Kinesis

17
MLJ050 Motorized Lab Jack
6.3 Homing Motors
Homing the motor moves the actuator to the home limit switch and resets the internal
position counter to zero. The limit switch provides a fixed datum that can be found
after the system has been powered up.
Fig. 6.2 Motor Controller Software GUI
1) Click the ‘Home’ button. Notice that the led in the button lights to indicate that
homing is in progress and the displayed position for both channels counts down
to 000.000, i.e the home position.
2) When homing is complete, the ‘Homed’ LED is lit as shown above.
See Appendix C , Section C.2.2. for background information on the home position.
6.4 Stopping the Stage
The drive channel is enabled and disabled by clicking the ‘Enable’ button on the GUI
panel. The green indicator in the button center is lit when the drive channel is enabled.
Disabling the channel removes the drive power.
During operation, the stage can be stopped at any time by clicking the ‘Stop’ button
on the GUI panel. Using this button does not remove power to the drive channel. .

18 HA0276T Rev Bk Jan 2017
Chapter 6
6.5 Changing Motor Parameters and Moving to an Absolute Position
Absolute moves are measured in real world units (e.g. millimetres), relative to the
Home position.
Moves are performed using a trapezoidal velocity profile (see Appendix C , Section
C.1.3.). The velocity settings relate to the maximum velocities at which a move is
performed, and the acceleration at which the motor speeds up from zero to maximum
velocity.
1) On the GUI panel, click the Move arrow to show the Settings panel.
Fig. 6.3 Move Settings Panel
2) Enter the required absolute position and/or parameter values.
3) To move to the position entered click the arrow
4) Click ‘Apply’ to save the parameter settings and close the window, click Reset to
return to the previously saved values.

19
6.6 Jogging
During PC operation, the motor actuators are jogged using the GUI panel arrow keys.
There are two jogging modes available, ‘Single Step’ and ‘Continuous’. In ‘Single
Step’ mode, the motor moves by the step size specified in the Step Distance
parameter. If the jog key is held down, single step jogging is repeated until the button
is released - see Fig. 7.3. In ‘Continuous’ mode, the motor actuator will accelerate and
move at the jog velocity while the button is held down.
1) On the GUI panel, click the word ‘Jog’ to display the Settings panel.
Fig. 6.4 Jog Settings Panel
2) Make parameter changes as required.
3) Click ‘Apply’ to save the settings and close the window, click Reset to return to the
previously saved values.
Note
In current versions of software, the ‘Min Vel’ parameter is locked at zero
and cannot be adjusted.

20 HA0276T Rev Bk Jan 2017
Chapter 6
6.7 Setting Move Sequences
The Kinesis software allows move sequences to be programmed, allowing several
positions to be visited without user intervention. For more details and instructions on
setting move sequences, please see the Kinesis Helpfile.
6.8 Changing and Saving Parameter Settings
During operation, certain settings (e.g. max velocity, jog step size etc) can be
changed as required. Other settings (e.g. PID parameter values) cannot be changed
so easily. When the Kinesis Server is run up and the stage/acuator association made,
suitable default settings are loaded and these values have been chosen to provide
safe performance in the majority of applications. However, for applications where
these settings need to be changed, a new set of Device Start Up settings', must be
created which can then be applied and/or uploaded on subsequent start up. See the
Kinesis Helpfile for more details.
Table of contents
Popular Jack manuals by other brands

Cattini Oleopneumatica
Cattini Oleopneumatica YAK 215/N Operating and maintenance manual
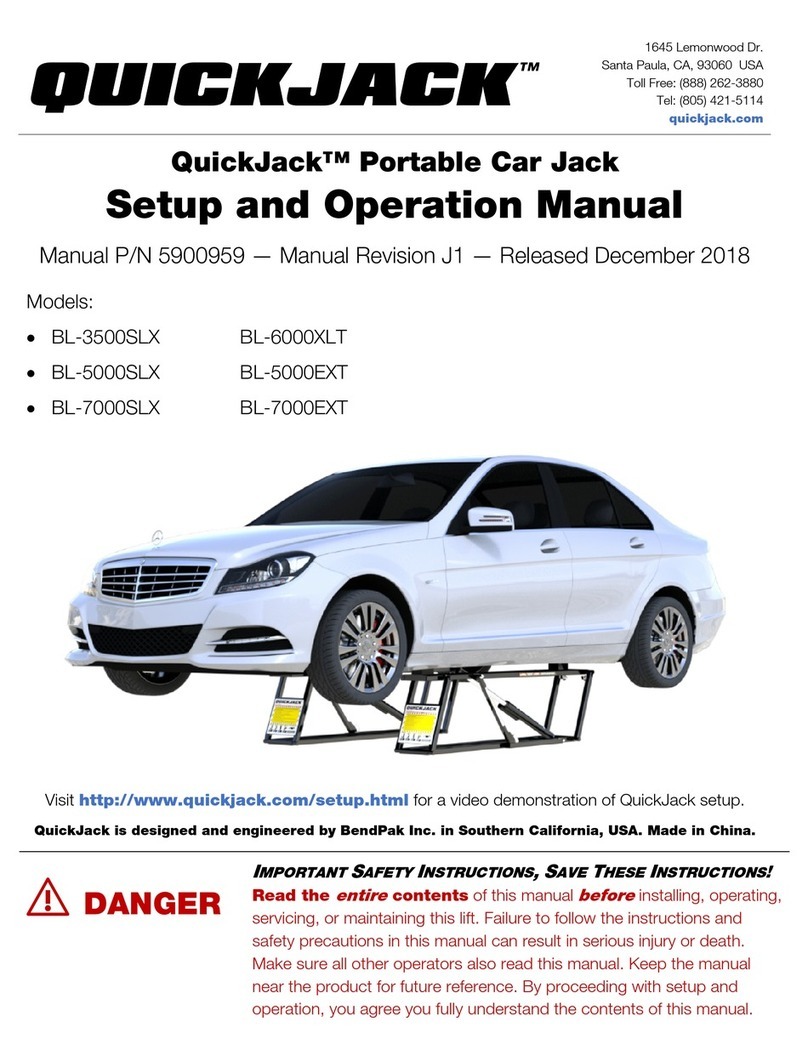
QuickJack
QuickJack BL-3500SLX Setup and operation manual

Meganex
Meganex MEG37 instruction manual
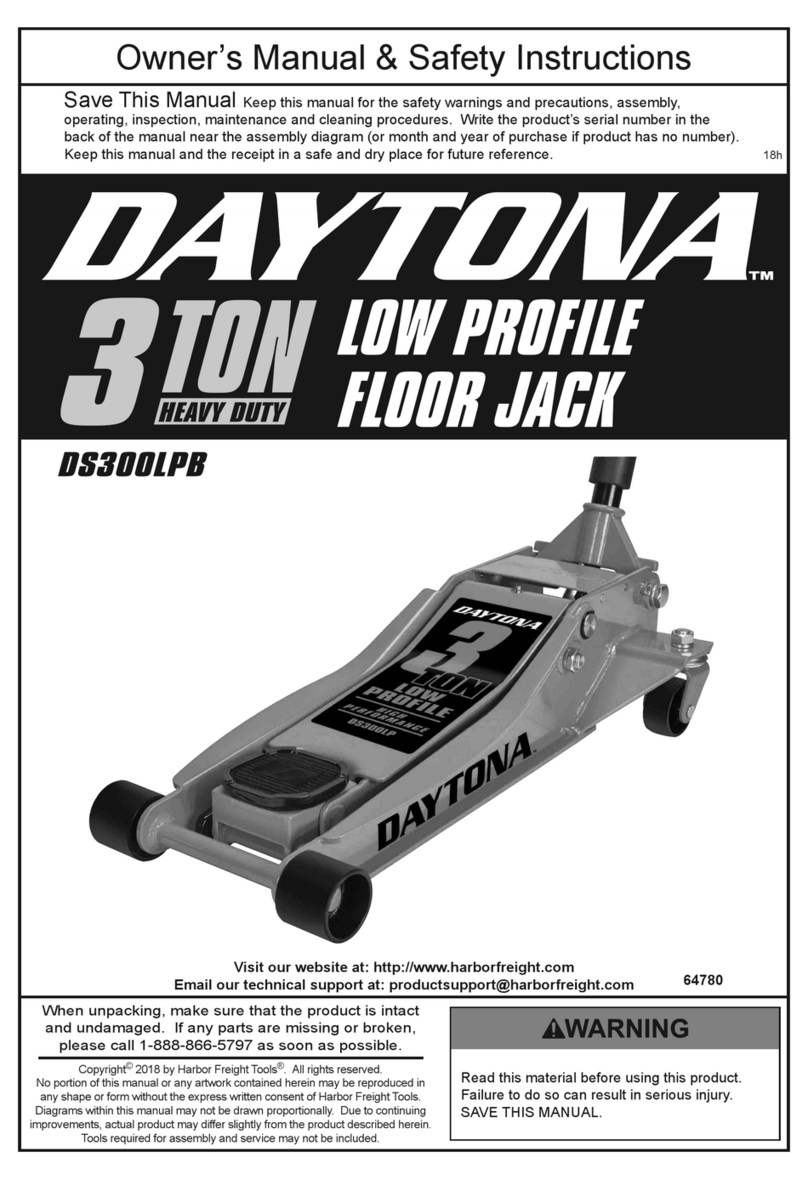
Daytona
Daytona DS300LPB Owner's manual & safety instructions
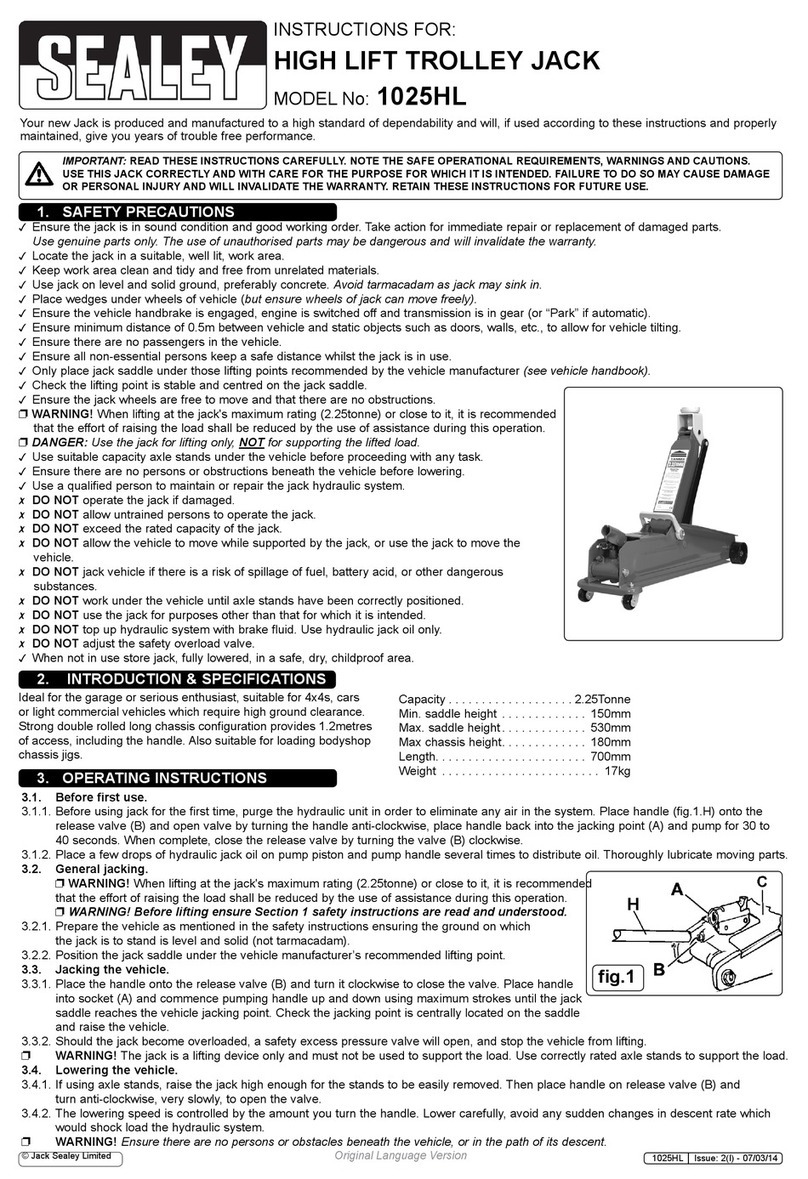
Sealey
Sealey 1025HL instructions
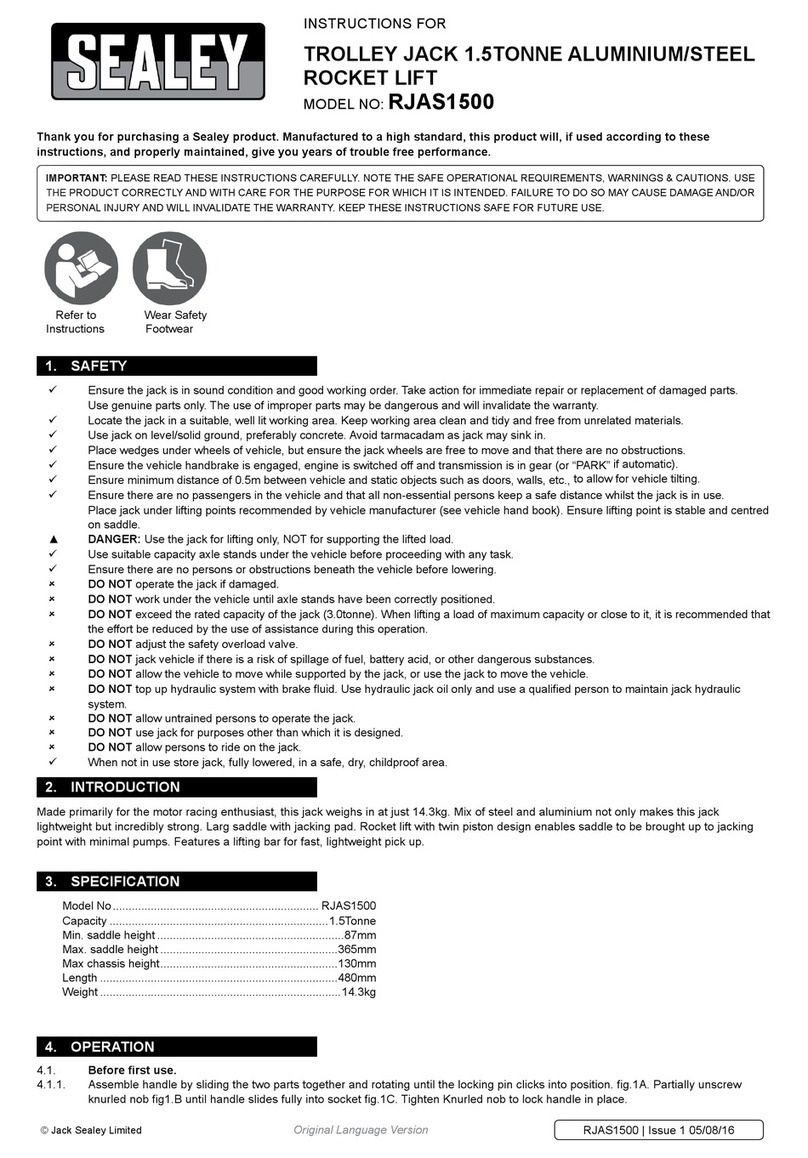
Sealey
Sealey RJAS1500 instructions

BGS technic
BGS technic 2884 instruction manual
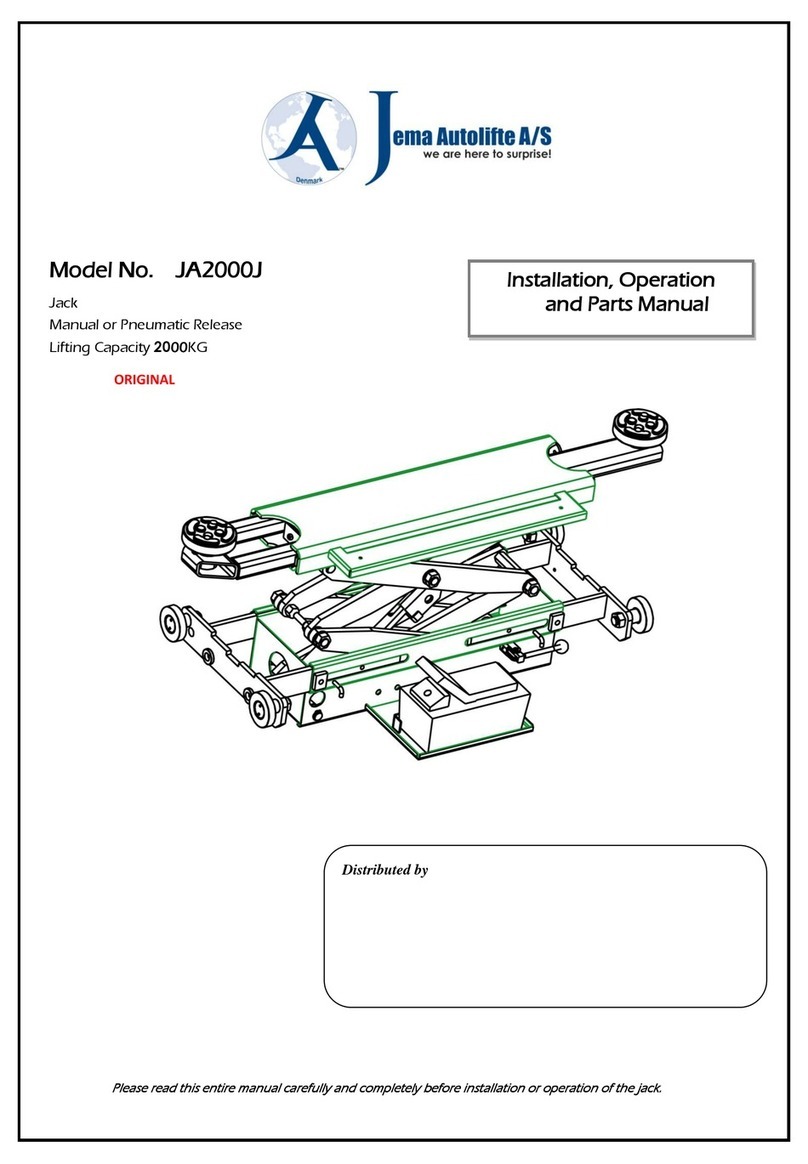
Jema Autolifte
Jema Autolifte JA2000J Installation, operation, and parts manual

Chicago Pneumatic
Chicago Pneumatic CP9420 Instruction manual/safety instruction
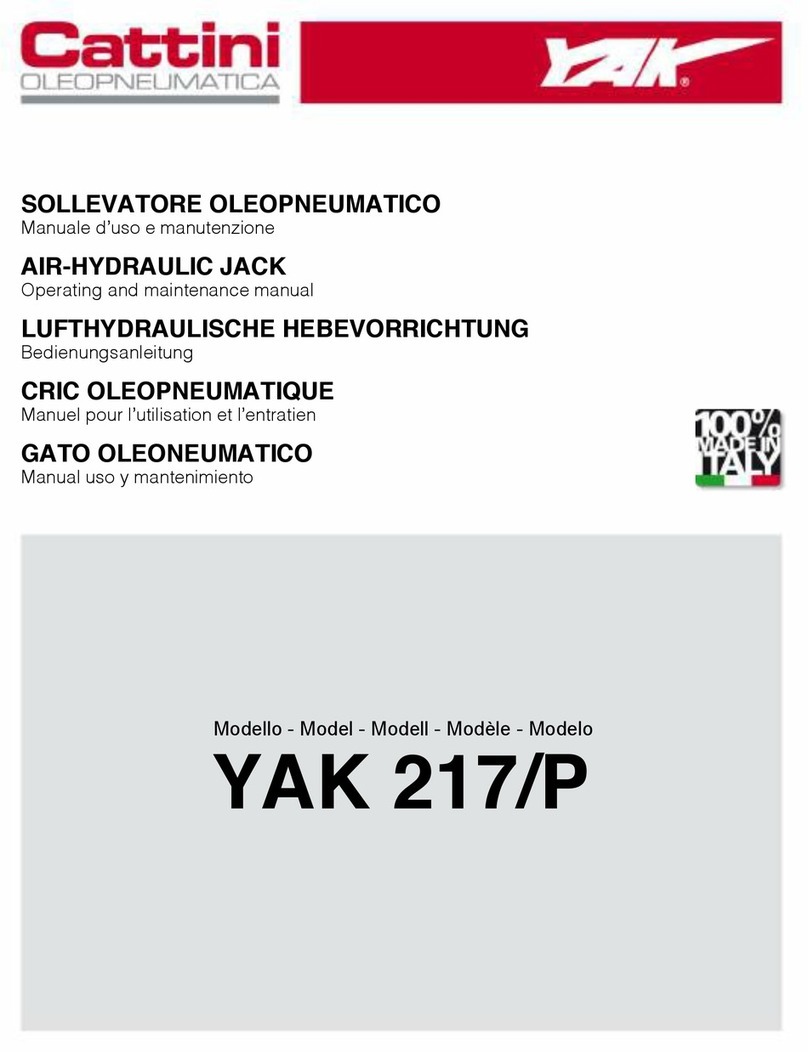
Cattini Oleopneumatica
Cattini Oleopneumatica YAK 217/P Operating and maintenance manual
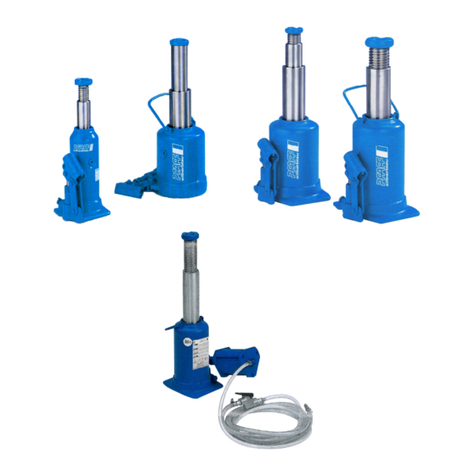
PFAFF silberblau
PFAFF silberblau PROLINE HWH KS 2,0 operating instructions
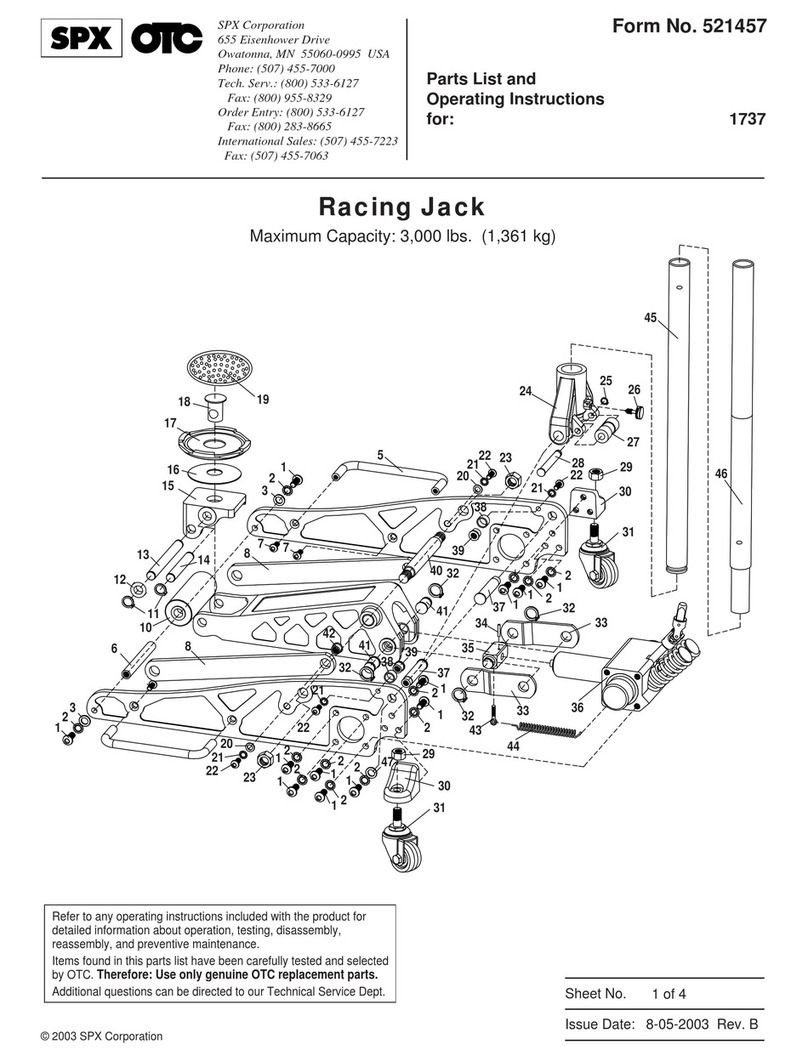
SPX
SPX OTC 1737 Parts list and operating instructions