THORLABS OSW8 Series User manual

___________________________________________________________________
__________________________________
Operation Manual
Thorlabs Instrumentation
PRO8000 (-4) / PRO800
Optical Switches OSW8xxx
2010

0 Safety
________________________________________________________________________________
______________________________________________________________________________________________________
© 2010 Thorlabs
Version: 3.1
Date: 16.09.2010
Copyright© 2010, Thorlabs

Safety 1
________________________________________________________________________________
______________________________________________________________________________________________________
© 2010 Thorlabs
Contents Page
1General description 3
1.1 Safety 3
1.2 Features 5
1.3 Technical data 5
1.3.1 General data 5
1.3.2 OSW8102 5
1.3.3 OSW8104 6
1.3.4 OSW8108 6
1.3.5 OSW8202 7
2Operating the OSW8xxx 8
2.1 Display 8
2.2 Selecting a module 8
3Communicating with a control computer 10
3.1 General information 10
3.1.1 Nomenclature 10
3.1.2 Data format 10
3.1.3 Selecting the module slot 11
3.1.4 Querying the module type 11
3.1.5 Changing the optical switch setting 12
3.2 Status reporting 13
3.2.1 Standard event status register (ESR) 14
3.2.2 Standard event status enable register (ESE) 14
3.2.3 Status byte register (STB) 15
3.2.4 Service request enable register (SRE) 15
3.2.5 Reading the STB by detecting SRQ 15
3.2.6 Reading the STB by "*STB?" command 15
3.2.7 Reading the STB by serial poll 15
4Service and Maintenance 16
4.1 General remarks 16
5Appendix 16
5.1 Warranty 16
5.2 Thorlabs “End of Life” policy (WEEE) 17
5.2.1 Waste treatment on your own responsibility 17
5.2.2 Ecological background 18
5.3 Certifications and compliances 19
5.4 Copyright 20
5.5 Addresses 21

2 Safety
________________________________________________________________________________
_____________________________________________________________________________________________________
© 2010 Thorlabs
We aim to develop and produce the best solution for your application in the
field of optical measurement technique. To help us to come up to your
expectations and develop our products permanently we need your ideas and
suggestions. Therefore, please let us know about possible criticism or ideas.
We and our international partners are looking forward to hearing from you.
In the displays shown by the PRO8 you may find the name PROFILE.
PROFILE was the name of the manufacturer before it was acquired by Thorlabs
and renamed to Thorlabs.
Thorlabs
This part of the instruction manual contai ns every specific information on how to
operate an opt ical switch OSW8xxx. A gener al description is f ollowed by
explanations of how to oper ate the unit manually. You will also find every information
about remote control via the IEEE 488 / RS232C computer interface.
Attention
This manual contains “WARNINGS” and “ATTENTION” label in this
form, to indicate dangers for persons or possible damage of equip-
ment.
Please read these advises carefully!
NOTE
This manual also contains “NOTES” and “HINTS” written in this form.

Safety 3
________________________________________________________________________________
______________________________________________________________________________________________________
© 2010 Thorlabs
1 General description
1.1 Safety
Attention
All statements regarding safety of operation and technical data in
this instruction manual will only apply when the unit is operated
correctly.
Before applying power to your PRO8000 (-4) / PRO800 system, make
sure that the protective conductor of the 3 conductor mains power
cord is correctly connected to the protective earth contact of the
socket outlet!
Improper grounding can cause electric shock with damages to your
health or even death!
Modules may only be installed or removed with the mainframe
switched off.
All modules must be fixed with all screws provided for this purpose.
Modules of the 8000 series must only be operated in the mainframe
PRO8000, PRO8000-4 or PRO800.
All modules must only be operated with duly shielded connection
cables.
Only with written consent from Thorlabs may changes to single
components be carried out or components not supplied by Thorlabs
be used.
This precision device is only dispatchable if duly packed into the
complete original packaging including the plastic form parts. If
necessary, ask for a replacement package.

4 Safety
________________________________________________________________________________
_____________________________________________________________________________________________________
© 2010 Thorlabs
Attention
Semiconductor laser modules can deliver up to several 100mW of
(maybe) invisible laser radiation!
When operated incorrectly, this can cause severe damage to your
eyes and health!
Never switch on connected laser modules with the output connec-
tors of the optical switch open!
Be sure to pay strict attention to the safety recommendations of the
appropriate laser safety class!
This laser safety class is marked on your PRO8000 (-4) / PRO800
plug-in module or on your external laser source used.
Attention
Mobile telephones, handy phones or other radio transmitters are not
to be used within the range of three meters of this unit since the
electromagnetic field intensity may then exceed the maximum
allowed disturbance values according to EN 50 082-1.

Features 5
________________________________________________________________________________
______________________________________________________________________________________________________
© 2010 Thorlabs
1.2 Features
General functions
The Thorlabs optical switches of the OSW8xxx series are ultra-fast MEMS
(Micro Electro-Mechanical System) based fiber optic switches with low insertion loss,
designed for the Thorlabs PRO8000(-4) / PRO800 mainframe.
1.3 Technical data
(All technical data are valid at 23 ± 5°C and 35±15% humidity)
1.3.1 General data
Operating temperature 0 … +35°C
Storage temperature -10 … +60°C
1.3.2 OSW8102
Switching configuration 1 x 2
Wavelength range 1240 … 1610 nm
Insertion loss 1) typ. 0.7 dB, max. < 1.5 dB
Crosstalk, min. - 50 dB
Back reflection, max. - 50 dB
PDL 2) < 0.1 dB
Switching time typ. 0.5 ms. max. < 1ms
Input power, max. +17 dBm (50 mW)
Fiber type 9/125/900, Corning SMF28e
Connectors 3) FC/APC
Lifetime 109 switching cycles without degradation of performance
1) measured at output port
2) measured at 1550 nm
3) other connectors on request

6 Technical data
________________________________________________________________________________
_____________________________________________________________________________________________________
© 2010 Thorlabs
1.3.3 OSW8104
Switching configuration 1 x 4
Wavelength range 1240 … 1610 nm
Insertion loss 1) typ. 1.2 dB, max. < 2.1 dB
Crosstalk min. - 60 dB
Back reflection, max. - 50 dB
PDL 2) < 0.15 dB
Switching time typ. 0.5 ms, max. < 1ms
Input power max. + 17 dBm (50 mW)
Fiber type 9/125/900, Corning SMF28e
Connectors 3) FC/APC
Lifetime 109 switching cycles without degradation of performance
1.3.4 OSW8108
Switching configuration 1 x 8
Wavelength range 1240 … 1610 nm
Insertion loss 1) typ. 1.6 dB, max. <2.6 dB
Crosstalk min. - 60 dB
Back reflection, max. - 45 dB
PDL 2) < 0.2 dB
Switching time typ. 0.5 ms, max. < 1ms
Input power, max. + 17 dBm (50 mW)
Fiber type 9/125/900, Corning SMF28e
Connectors 3) FC/APC
Lifetime 109 switching cycles without degradation of performance
1) measured at output port
2) measured at 1550 nm
3) other connectors on request

Technical data 7
________________________________________________________________________________
______________________________________________________________________________________________________
© 2010 Thorlabs
1.3.5 OSW8202
Switching configuration 2 x 2
Wavelength range 1240 … 1610 nm
Insertion loss 1) typ. 0.7 dB, max. < 1.5 dB
Crosstalk min. - 50 dB
Back reflection, max. - 50 dB
PDL 2) < 0.15 dB
Switching time typ. 0.5 ms, max. < 1ms
Input power (max.) + 17 dBm (50mW)
Fiber type 9/125/900, Corning SMF28e
Connectors 3) FC/APC
Lifetime 109 switching cycles without degradation of performance
1) measured at output port
2) measured at 1550 nm
3) other connectors on request

8 Display
________________________________________________________________________________
_____________________________________________________________________________________________________
© 2010 Thorlabs
2 Operating the OSW8xxx
2.1 Display
The main menu shows the channel numbers of the inserted modules and their main
parameters. In the case of the OSW8xxx this is t he fiber output connected to the
common port.
Channel no. Cursor Switch settings
CH1 COM -> 2
CH2
CH3
CHANGE
2.2 Selecting a module
Select a module for further input by setting the cursor to the c hannel number of the
desired module.
Use the soft keys and .
CH1
Pressing will lead to the channel menu
Pressing again or will lead back to the main menu.
CH1 COM -> 2
CH2
CH3
CHANGE

Selecting a module 9
________________________________________________________________________________
______________________________________________________________________________________________________
© 2010 Thorlabs
In the channel menu (just as also in the main menu) you can toggle between the
different switch settings by pressing “CHANGE” and further selecting up or down by
the corresponding soft-keys. In the case of the 2 -> 2 switch OSW8202 the word
“TOGGLE” is displayed, to indicate the back and forward switching of the two
configurations.
CH1 COM -> 3
CH2
CH3
CHANGE: down up

10 General information
________________________________________________________________________________
_____________________________________________________________________________________________________
© 2010 Thorlabs
3 Communicating with a control computer
3.1 General information
The description of the mainframe of the PRO8000 (-4) / PRO800 includes all
instructions of how to prepare and exec ute the programming of the system via
IEEE 488 computer interface.
Special operation features of an OSW8xxx optical switch module are described here.
(Refer to chapter 2, “Operating the OSW8xxx" starting on page 8)
3.1.1 Nomenclature
Program messages (PC ⇒ PRO8000 (-4)) are written in inverted commas:
"*IDN?"
Response messages (PRO8000 (-4) ⇒ PC) are written in brackets:
[:SLOT 1]
There is a decimal point: 1.234
Parameters are separated with comma: "PLOT 2,0"
Commands are separated with semicolon: "*IDN?;*STB?"
3.1.2 Data format
According to the IEEE 488.2 specifications all data variables are divided into 4
different data formats:
Character response data (<CRD>)
Is a single character or a string. Examples:
A or ABGRS or A125TG or A1.23456A
(Refer to IEE488.2 (8.7.1))
Numeric response data Type 1 (<NR1>)
Is a numerical value with sign in integer notation. Examples:
1 or +1 or -22 or 14356789432
(Refer to IEE488.2 (8.7.2))
Numeric response data Type 2 (<NR2>)
Is a numerical value with or without sign in floating poi nt notation without exponent.
Examples:
1.1 or +1.1 or -22.1 or 14356.789432
(Refer to IEE488.2 (8.7.3))

General information 11
________________________________________________________________________________
______________________________________________________________________________________________________
© 2010 Thorlabs
Numeric response data Type 3 (<NR3>)
Is a numerical value with or without sign in floating poi nt notation with exponent with
sign . Examples:
1.1E+1 or +1.1E-1 or -22.1E+1 or 143.56789432E+306
(Refer to IEE488.2 (8.7.4))
3.1.3 Selecting the module slot
":SLOT <NR1>" Selects a slot for further programming
<Nr1>=1…8 (PRO8000), 1…2 (PRO800)
":SLOT?" Queries the selected slot
[:SLOT <NR1><LF>]
3.1.4 Querying the module type
Reading:
":TYPE:ID?" Reads the module ID (here 227)
[:TYPE:ID 227<LF>]
":TYPE:SUB?" Reads module subtype:
0: 1 x 8 switch
1: 2 x 2 switch
2: 1 x 2 switch
3: 1 x 4 switch
[:TYPE:SUB <NR1><LF>]
":TYPE:TXT?" Reads the module identification in text form, e.g.:
[:TYPE:TXT "OSW8202 2x2"<LF>]
":TYPE:SN?" Reads the module serial number, e.g:
[:TYPE:SN 1234-567<LF>]

12 General information
________________________________________________________________________________
_____________________________________________________________________________________________________
© 2010 Thorlabs
3.1.5 Changing the optical switch setting
Programming:
":OSW <NR1>" Set the desired switch configuration:
OSW8102:
<NR1>=1: connect COM with output 1
<NR1>=2: connect COM with output 2
OSW8104:
<NR1>=1: connect COM with output 1
<NR1>=2: connect COM with output 2
<NR1>=3: connect COM with output 3
<NR1>=4: connect COM with output 4
OSW8108:
<NR1>=1: connect COM with output 1
<NR1>=2: connect COM with output 2
<NR1>=3: connect COM with output 3
<NR1>=4: connect COM with output 4
<NR1>=5: connect COM with output 5
<NR1>=6: connect COM with output 6
<NR1>=7: connect COM with output 7
<NR1>=8: connect COM with output 8
OSW8202:
<NR1>=1: connect port 1 with 3 and 2 with 4
<NR1>=2: connect port 1 with 4 and 2 with 3
Reading:
":OSW?" Reads the OSW switch configuration
[:OSW <NR1><LF>]

Status reporting 13
________________________________________________________________________________
______________________________________________________________________________________________________
© 2010 Thorlabs
3.2 Status reporting
The OSW8xxx has no own device er ror registers. You can only use t he PRO8000 (-
4) / PRO800 mainframe status registers shown here.
Figure 1 The PRO8000 (-4)/ PRO800 register ESR, ESE, STB and SRE
Output buffer
ERROR Queue
or serial poll
Service
Request
Generation
{
{
{
{
{
{

14 Status reporting
________________________________________________________________________________
_____________________________________________________________________________________________________
© 2010 Thorlabs
3.2.1 Standard event status register (ESR)
The bits of this register represent the following standard events:
Power on This event bit indicates, t hat an off to on transition has
occurred in the power supply. So it is high after turning on
the device for the first time.
User request (Not used)
Command error A command error occurred.
Execution error An execution error occurred.
Device dependent error A device dependent error occurred.
Query error A query error occurred.
Request control (Not used)
Operation complete Can be set with "*OPC".
The ESR can be read dire ctly with the command "*ESR?". This read command
clears the ESR. The content of the ESR can not be set.
The bits are active high.
3.2.2 Standard event status enable register (ESE)
The bits of the ESE are used to select, wh ich bits of the ESR shall influence bit 5
(ESB) of the STB. The 8 bits of the ESE are combined with the according 8 bits of
the ESR via a wired “AND”-function. These 8 results are combined with a logical
“OR”-function, so that any "hit" leads to a l ogical 1 in bit 5 (ESB) of the STB. As any
bit of the STB can assert an SRQ, every event (bit of the ESR) can be used to assert
an SRQ.

Status reporting 15
________________________________________________________________________________
______________________________________________________________________________________________________
© 2010 Thorlabs
3.2.3 Status byte register (STB)
The bits of this register are showing the status of the PRO8000 (-4) / PRO800.
RQS RQS: Request service message: Shows, that this device
has asserted SRQ (read via serial poll).
MSS Master summary status: Shows that this device requests a
service (read via "*STB?").
MAV (Message AVailable) This bit is high after a query request,
as a result "waits" in the output queue to be fetched. It is
low, if the output queue is empty.
DES (Device Error Status) This bit is high after a device error
occurred. Which device errors will set this bit is defined
with the EDE.
EAV (Error AVailable) This bit is high as long as there are
errors in the error queue.
FIN (command FINished) This bit is high, after a command has
finished and all bits of the STB have been set.
The STB can be read directly with the command "*STB?". The content of the STB
can not be set. The bits are active high.
All bits except bit 6 of the STB can be used to assert a service request (SRQ)
(Please refer to 3.2.5). Alternatively the SRQ can be recognized using the command
"*STB?" (Please refer to 3.2.6) or by serial poll (Please refer to 3.2.7).
3.2.4 Service request enable register (SRE)
The bits of the SRE are used to select, which bits of the STB shall assert an SRQ.
Bit 0, 1, 2, 3, 4, 5 and 7 of the STB are re lated to the according 7 bits of the SRE by
logical “AND”. These 7 results are combined by a logical "OR", so that any "hit" leads
to a logical 1 in bit 6 of the STB and asserts an SRQ.
3.2.5 Reading the STB by detecting SRQ
If an SRQ is asserted (see 3.2.4) bit 6 of t he STB is set to logical 1, so that the
controller can detect which device asserted the SRQ by auto serial polling.
3.2.6 Reading the STB by "*STB?" command
If the controller does not "listen" to SRQ’s at all, the service request can be detected
by reading the status byte with the command "*STB?".
If bit 6 is logical 1, a service request was asserted.
3.2.7 Reading the STB by serial poll
If the controller does not suppor t auto serial poll, the service request can also be
detected via manual serial poll.
If bit 6 is logical 1, a service request was asserted.

16 General remarks
________________________________________________________________________________
_____________________________________________________________________________________________________
© 2010 Thorlabs
4 Service and Maintenance
4.1 General remarks
The OSW8xxx modules don’t need any regularly maintenance by the user.
If the fiber optic connectors are changed very frequently and if an increased insertion
loss is registered, standard cleaning procedure for fiber connectors should be
applied.
5 Appendix
5.1 Warranty
Thorlabs warrants material and production of the OSW8xxx for a period of 24 months
starting with the date of shipm ent. During this warranty period Thorlabs will see to
defaults by repair or by exchange if these are entitled to warranty.
For warranty repairs or service the unit must be sent back to Thorlabs (Germany) or
to a place determined by Thorlabs. The customer will carry the shipping costs to
Thorlabs, in case of warranty repairs Thorlabs will carry the shipping costs back to
the customer.
If no warranty repair is applicable the customer also has to carry the costs for back
shipment.
In case of shipment from outside EU duties, taxes etc. which should arise have to be
carried by the customer.
Thorlabs warrants the hard- and software determined by Thorlabs for this unit to
operate fault-free provided t hat they are handled accordi ng to our requirements.
However, Thorlabs does not warrant a faulty free and uninterrupted operation of the
unit, of the soft- or firmware for special app lications nor this instruction manual to be
error free. Thorlabs is not liable for consequential damages.
Restriction of warranty
The warranty mentioned before does not cover errors and defects being the result of
improper treatment, software or interface not supplied by us, modification, misuse or
operation outside the defined ambient c onditions (refer to the PRO8000(-4) /
PRO800 mainframe operation manual) stated by us or unauthorized maintenance.
Further claims will not be consent ed to and will not be acknowledged. Thorlabs does
explicitly not warrant the usability or the economical use for certain cases of
application.
Thorlabs reserves the right to change this instru ction manual or the technical data of
the described unit at any time.

Thorlabs “End of Life” policy (WEEE) 17
________________________________________________________________________________
______________________________________________________________________________________________________
© 2010 Thorlabs
5.2 Thorlabs “End of Life” policy (WEEE)
As required by the WEEE (Was te Electrical and Electronic Equipment Directive) of
the European Community and the corresponding national laws, Thorlabs offers all
end users in the EC the possibility to retu rn “end of life” units without incurring
disposal charges.
This offer is valid for Thorlabs electrical and electronic equipment
• sold after August 13th 2005
• marked correspondingly with the crossed out “wheelie bin” logo (see Figure 2)
• sold to a company or institute within the EC
• currently owned by a company or institute within the EC
• still complete, not disassembled and not contaminated
As the WEEE directive applies to self cont ained operational electrical and electronic
products, this “end of life” take back se rvice does not refer to other Thorlabs
products, such as
• pure OEM products, that means assemblies to be built into a unit by the user
(e. g. OEM laser driver cards)
• components
• mechanics and optics
• left over parts of units disassembled by the user (PCB’s, housings etc.).
If you wish to return a Thorlabs unit for wa ste recovery, please contact Thorlabs or
your nearest dealer for further information.
5.2.1 Waste treatment on your own responsibility
If you do not return an “end of life” unit to Thorlabs, you must hand it to a company
specialized in waste recovery. Do not dispose of the unit in a litter bin or at a public
waste disposal site.

18 Thorlabs “End of Life” policy (WEEE)
________________________________________________________________________________
_____________________________________________________________________________________________________
© 2010 Thorlabs
5.2.2 Ecological background
It is well known that WEEE pollutes the environment by releasing toxic products
during decomposition. The aim of the Eu ropean RoHS directive is to reduce the
content of toxic substances in electronic products in the future.
The intent of the WEEE dire ctive is to enforce the re cycling of WEEE. A controlled
recycling of end of live products will t hereby avoid negative impacts on the
environment.
Figure 2 Crossed out “wheelie bin” symbol
This manual suits for next models
1
Table of contents
Other THORLABS Switch manuals
Popular Switch manuals by other brands
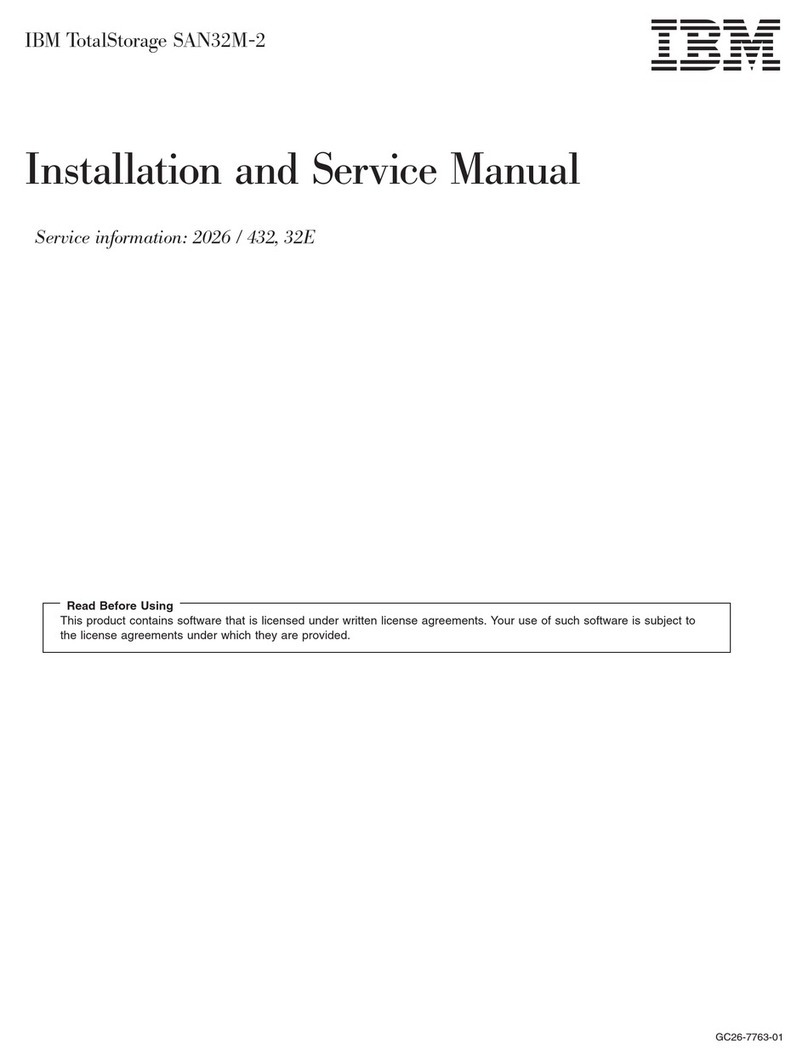
IBM
IBM SAN32M-2 Installation and service manual
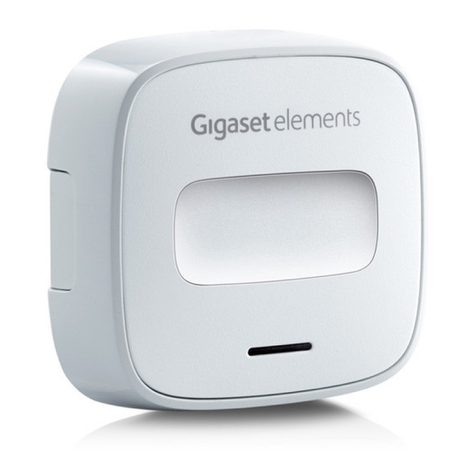
Gigaset
Gigaset Elements Button quick start guide
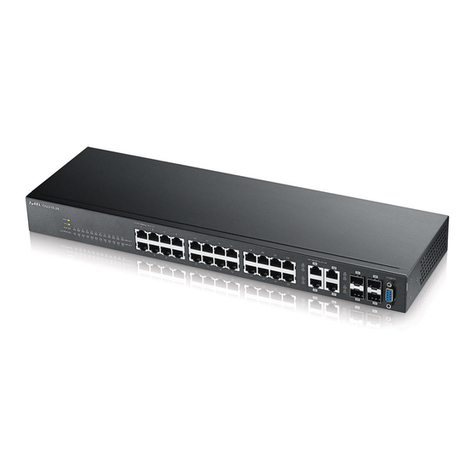
ZyXEL Communications
ZyXEL Communications GS2210 Series user guide
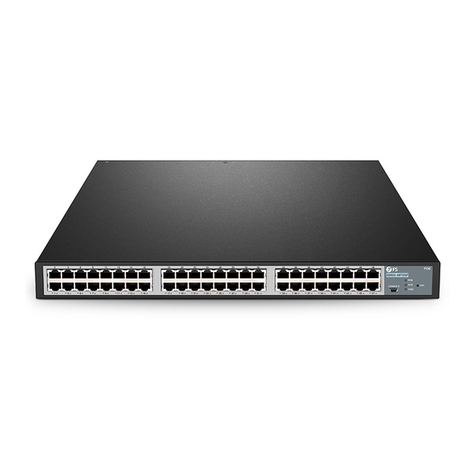
FS
FS S5500-48T8SP Configuration guide
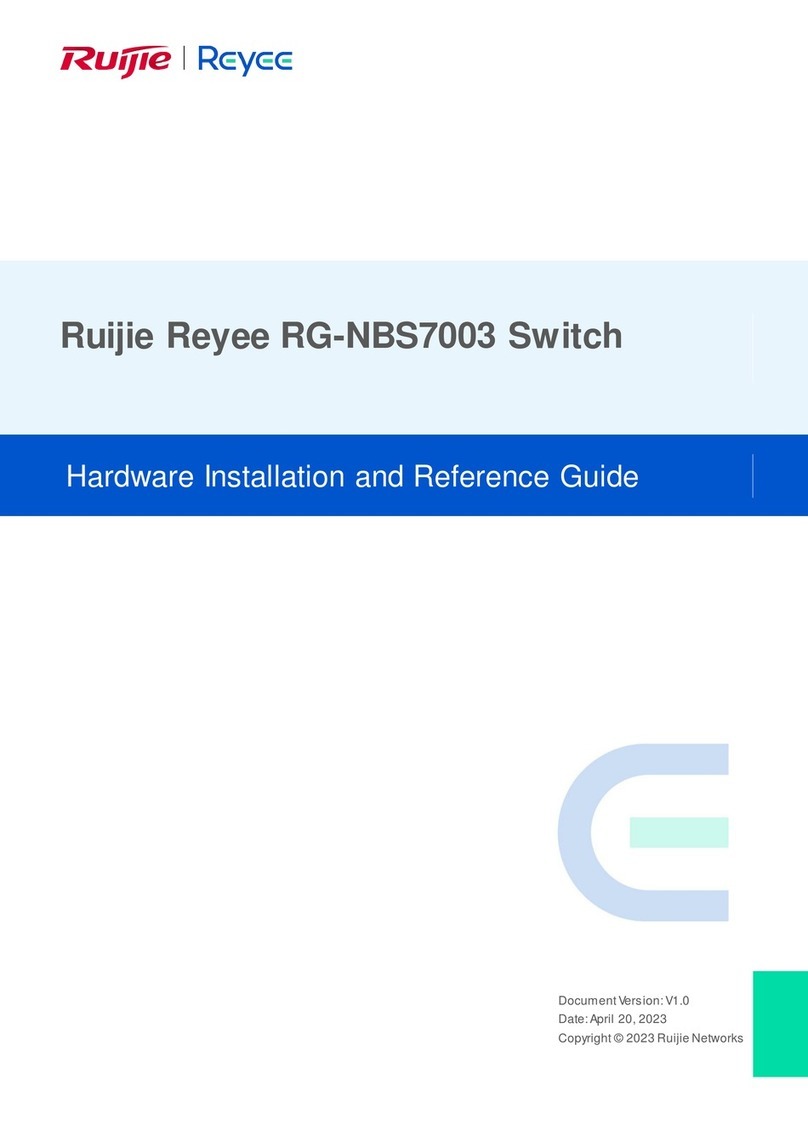
Ruijie
Ruijie Reyee RG-NBS7003 Hardware installation and reference guide
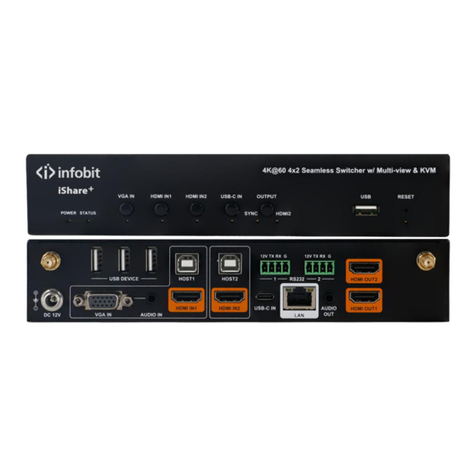
infobit
infobit iShare+ user manual
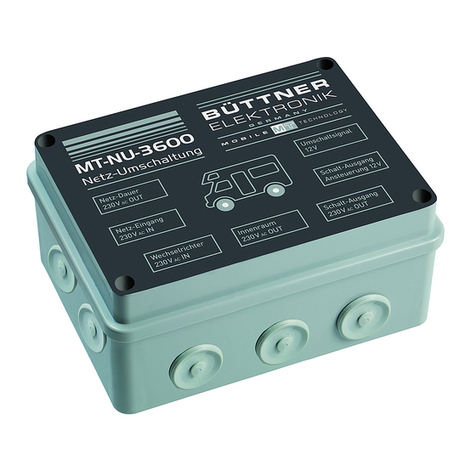
Dometic
Dometic MT NU 3600 Installation and operating manual

NETGEAR
NETGEAR GS724Tv1 - ProSafe Gigabit Smart Switch Specifications
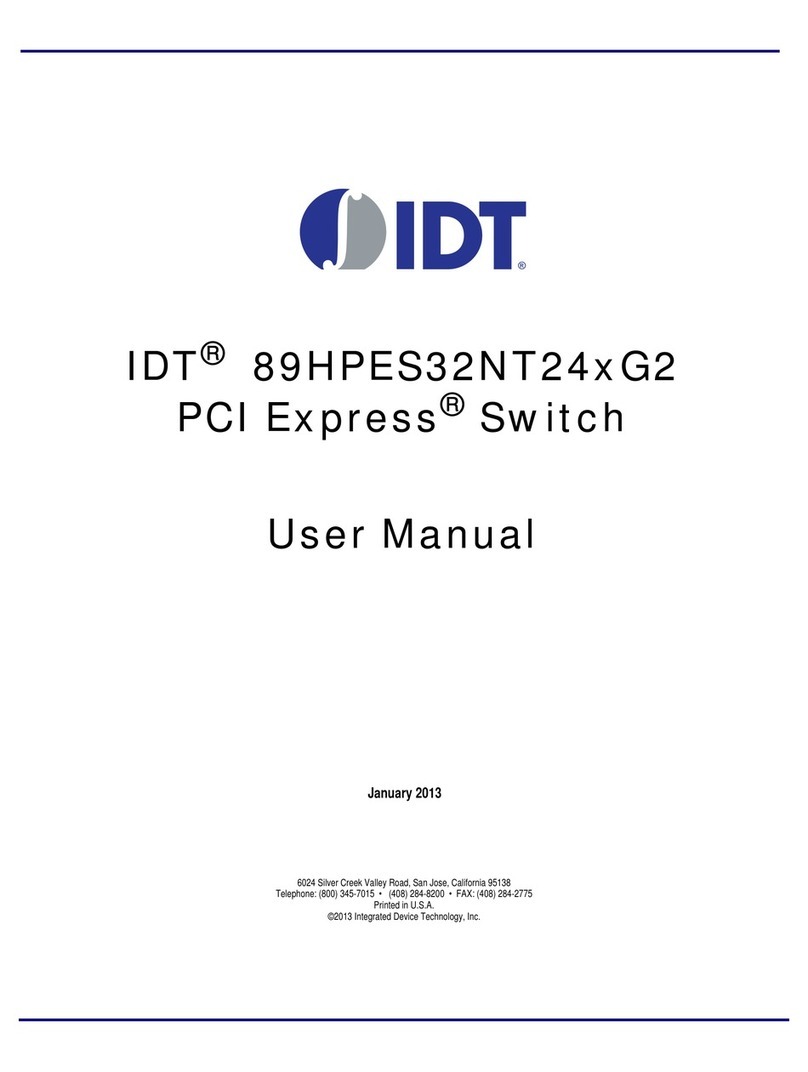
IDT
IDT PCI Express 89HPES32NT24xG2 user manual

ABB
ABB OTM C Series Installation and operating instructions
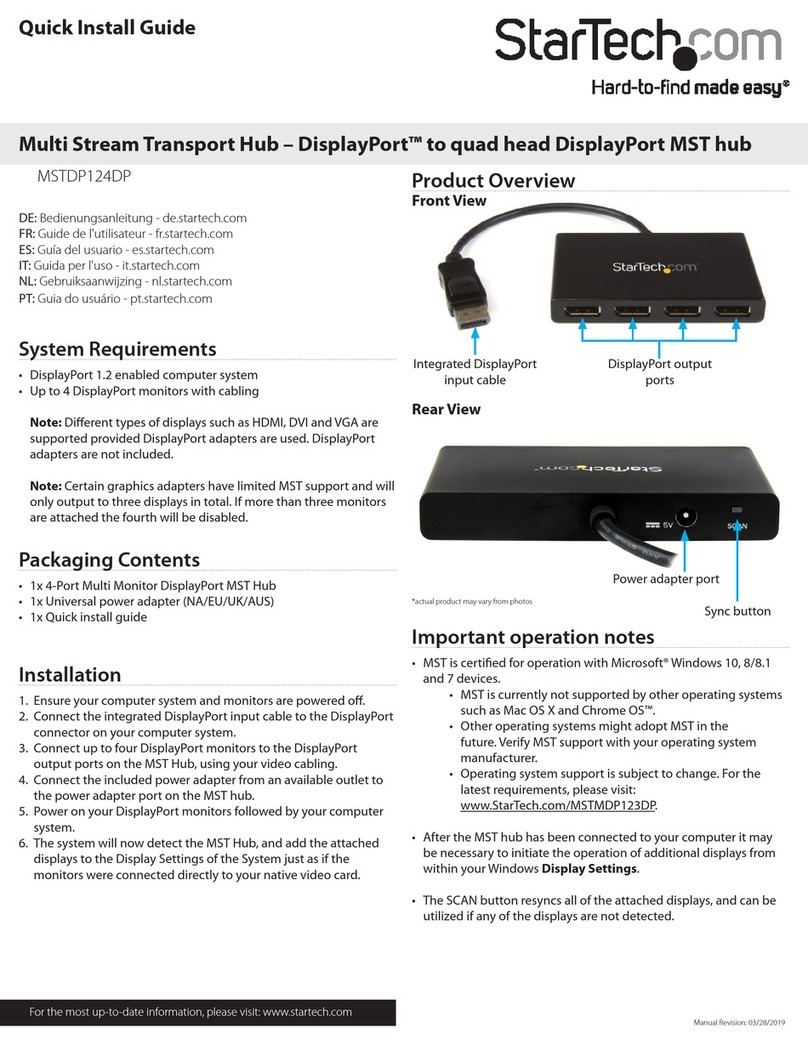
StarTech.com
StarTech.com MSTDP124DP Quick install guide
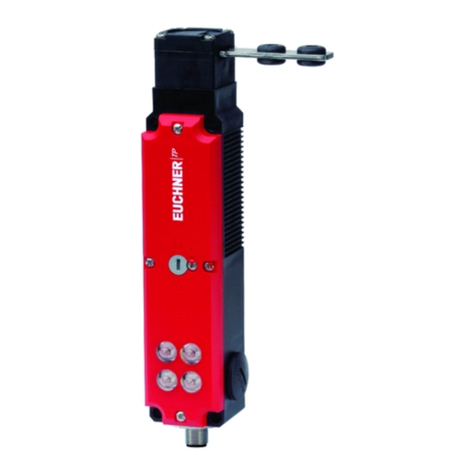
EUCHNER
EUCHNER TP AS2 Series operating instructions