Titan HD4P-12000 Instruction manual

INSTALLATION, OPERATION,
& MAINTENANCE MANUAL
MODEL:
HD4P-12000 4-POST LIFT
FOLLOW THIS MANUAL CAREFULLY TO ENSURE THE EQUIPMENT WILL
FUNCTION CORRECTLY AND PROVIDE MANY YEARS OF DEPENDABLE SERVICE.
FAILURE TO FOLLOW THESE INSTRUCTIONS AND SAFETY WARNINGS MAY
RESULT IN PERSONAL INJURY OR PROPERTY DAMAGE. KEEP THIS MANUAL IN A
SAFE DRY PLACE FOR FUTURE REFERENCE.
®

Products May Be
Upgraded Without Notice
Please Visit
WWW.TITANLIFTS.COM
For The Latest Version Of
This Manual
P.O. Box 7069 • Greenwood, IN 46142 • Ph. 888-908-4826 • Fx. 317-215-2770 • www.titanlifts.com

CONTENTS
1-SAFETY .....................................................................................................................1
1.1 INTRODUCTION........................................................................................................................ 1
1.2 SAFETY INSTRUCTIONS FOR COMMISSIONING...................................................................... 1
1.3 SAFETY INSTRUCTIONS FOR OPERATION............................................................................... 1
1.4 SAFETY INSTRUCTIONS FOR MAINTENANCE ......................................................................... 3
1.5 RISKS....................................................................................................................................... 3
2-UNPACKING & SET-UP...............................................................................................4
2.1 DELIVERY AND CHECK OF PACKAGES ..................................................................................... 4
2.2 LIFTING AND HANDLING.......................................................................................................... 4
3-SPECIFICATIONS ......................................................................................................5
4-FLOOR REQUIREMENTS ............................................................................................6
4.1 SELECTING THE SITE AREA ..................................................................................................... 6
4.2 FLOOR REQUIREMENTS ........................................................................................................... 6
4.3 ANCHORING TIP SHEET........................................................................................................... 7
5-INSTALLATION INSTRUCTIONS................................................................................8
ASSEMBLY VIEW............................................................................................................................ 8
POWER UNIT LOCATION ................................................................................................................ 8
COLUMN & CROSSBEAM INSTALLATION ...................................................................................... 9
RAISING THE CROSSBEAMS ........................................................................................................10
RUNWAY INSTALLATION ..............................................................................................................10
CYLINDER AND CABLE INSTALLATION ........................................................................................10
POWER UNIT INSTALLATION........................................................................................................12
ROUTING HYDRAULIC HOSE.........................................................................................................12
LIFT START UP / FINAL ADJUSTMENTS.......................................................................................12
ANCHORING THE COLUMNS.........................................................................................................13
FINAL ASSEMBLY .........................................................................................................................15
LEVELING/SYNCHRONIZING.........................................................................................................15
BLEEDING .....................................................................................................................................16
6-OPERATION INSTRUCTIONS...................................................................................17
6.1 DEFECTS/MALFUNCTIONS .....................................................................................................17
6.2 CONTROLS..............................................................................................................................17
6.3 OPERATION............................................................................................................................18
7-MAINTENANCE........................................................................................................19
7.1 MAINTENANCE SCHEDULE .....................................................................................................19
7.2 MAINTENANCE BY OPERATOR ...............................................................................................21
7.3 CLEANING ...............................................................................................................................22
7.4 TROUBLESHOOTING GUIDE ....................................................................................................22
8-DIAGRAMS & PARTS LIST .......................................................................................28
8.1 PARTS LIST.............................................................................................................................33

To Our Valued Customers:
Thank you for purchasing a Titan Lifts® product. We hope this high quality equipment provides you with years of
dependable service.
It is unfortunate that rare situations may occur with the products you purchase from Titan Lifts®. We value your
business as well as the trust you have and need to maintain your relationship with us. Titan Lifts® carries liability
coverage that may protect our customers if a situation does occur. However, as in all accidents there must be
proof of liability for a claim to be made. Our insurance company requires the following procedures be observed in
order to consider a claim:
A. The claimant must contact the Titan Lifts® distributor immediately with the facts of the situation.
B. If any equipment is damaged, including vehicles or shop equipment, Titan Lifts® must be given the
opportunity to send and impartial representative to the site for proper assessment of the situation.
C. The Vehicle cannot be moved until either an impartial representative has reviewed the accident or clear
and precise pictures are taken that reect all the pertinent information for an impartial representative to be able
to access the information from a distance. Titan Lifts® or its representatives must approve the pictures before
anything can be moved.
D. If any potential liability is determined on behalf of Titan Lifts®, two estimates must be submitted for
damages to be reimbursed.
It is imperative that the claimant complies with these procedures, because without proper assessment of the sit-
uation a claim will be denied.
ARBITRATION NOTICE
The installation or use of this equipment shall constitute an acknowledgement that the user agrees to resolve any
and all disputes or claims of any kind whatsoever, which relate in any way to the equipment, by way of binding
arbitration, not litigation. No suit or legal action may be led in any state or federal court. Any arbitration shall be
governed by the Federal Arbitration Act, and administered by the American Mediation Association, Indianapolis
Indiana. The maximum amount that an arbitrator may award and all damages shall not exceed the retail value of
this equipment.
WARRANTY NOTICE
This equipment must be installed by a “Professional Installer” assembled and used in the manner according to
the documentation provided to be covered by warranty.
Damaged or missing components must be reported within 72 hours of receipt to your freight carrier and to the
distributor. Claims must be led to cover cost.
If you have any questions or if we can be of any further assistance, please don’t hesitate to contact a Titan Lifts®
representative at 1-888-908-4826. Thank you for the opportunity to continue to serve your lift equipment needs.
PO Box 7069 Greenwood, IN 46142
1.888.908-4826 FAX (317) 215.2770
www.titanlifts.com
TITAN MARKETING, LLC
®

1
1-SAFETY
INSTRUCTIONS
1.1 INTRODUCTION
• The lift may be installed and commissioned by authorized service personnel only.
• The standard lift version may not be installed and commissioned in the vicinity of
explosives or ammable liquids, outdoors or in moist rooms (e.g. car wash).
• Read this entire manual.
• Load should not exceed rated capacity for this lift – 12,000 lb
• Only trained authorized personnel over the age of 18 years should operate the lift.
• Indoor use recommended.
• Always lift the vehicle using all four arms.
• Never use the lift to raise one end or one side of vehicle.
FAILURE TO COMPLY WITH INSTRUCTIONS COULD RESULT IN
PROPERTY DAMAGE.
WARNING: READ ENTIRE MANUAL AND COMPLY WITH ALL SAFETY AND SERVICE
PRECAUTIONS. DEATH, PERSONAL INJURY AND / OR PROPERTY DAMAGE MAY OCCUR IF
INSTRUCTIONS ARE NOT FOLLOWED CAREFULLY.
Personal injury and property damage incurred due to non-compliance with these safety
instructions are not covered by the product liability regulations.
FAILURE TO COMPLY WITH INSTRUCTIONS COULD RESULT IN PERSONAL
INJURY.
SYMBOLS
IMPORTANT INFORMATION
1.2 SAFETY INSTRUCTIONS FOR COMMISSIONING
1.3 SAFETY INSTRUCTIONS FOR OPERATION

2
WARNING: Use this lift only in well ventilated areas. Carbon monoxide exhausted
from running vehicle engines is a colorless, odorless fume that, if inhaled, can cause
serious personal injury or death.
WARNING: People with pacemakers should consult their physician(s) before using
this product. Operation of electrical equipment in close proximity to a heart pacemaker
could cause interference or failure of the pacemaker.
WARNING: This product contains or produces a chemical known to the State of
California to cause cancer and birth defects (or other reproductive harm). (California Health
& Safety Code 25249.5 et seq.)
• Maintain a safe working environment. The work area should be clean, dry, clutter free, and
sufciently lit.
• Vehicle doors should be closed during the raising and lowering cycles.
• Closely watch the vehicle and lift during the raising and lowering cycles.
• Do not operate the lift in explosive atmospheres, such as in the presence of ammable
liquids, gases, or dust. Power equipment can create sparks which may ignite ammables.
• Keep hands, tools, and other extremities from under carriage and moving parts.
• Never operate this lift with someone on it.
• Do not allow anyone on the lift or inside a raised vehicle.
• Keep children and bystanders away from work area. Do not let children operate or play
on lift.
• Wear proper safety attire. Do not wear loose tting clothing while operating lift. Long hair,
jewelry and sleeves should be secured.
• Never leave the lift unattended while under a load.
• Do not operate this lift if under the inuence of drugs, alcohol, or medication. Operator
must be alert at all times when using heavy lift equipment.
• Comply with all applicable accident prevention regulations.
• Only use the vehicle manufacturer’s recommended lifting points.
• After positioning the vehicle, apply the parking brake.
• Use caution when removing or installing heavy vehicle components which may result in
center-of-gravity displacement.
• Use this lift only for the work it is intended. Do not use this product for an application for
which it was not designed. Misuse can lead to personal injury and/or property damage.

3
TILTING RISK
Use caution when lowering the lift and make sure the tracks stay level with the safety locks.
• Maintenance or repair work should be done by authorized service personnel only.
• Work on the electrical equipment should be done by certied licensed electricians only.
• Ensure that ecologically harmful substances are disposed of in accordance with the
appropriate regulations.
• To prevent the risk of damage, do not use high pressure / steam jet cleaners or caustic
cleaning agents.
• Do not replace or override the safety devices.
WARNING: Risks the personnel could encounter, due to an improper use of the lift, are
described in this section.
CRUSHING RISK
During lowering of runways and vehicles, personnel must not be within the area
covered by the lowering trajectory. The operator must be sure no one is in danger before
operating the lift. Stay clear of the lift when lowering or raising vehicles. Keep hands and
feet away from moving parts and especially points that could pinch. Keep your feet clear of
the lift when raising and lowering vehicles.
BUMPING RISK
When the lift is stopped at relatively low working height, the risk of bumping against
projecting parts increases. Always be aware of your surroundings and avoid bumping your
head or body on the lift or the vehicle.
1.4 SAFETY INSTRUCTIONS FOR MAINTENANCE
1.5 RISKS

4
2-UNPACKING & SET-UP
Only skilled personnel who are familiar with the lift and this manual shall be allowed to
carry out, lifting, handling, transport and unpacking operations.
When the lift is delivered, carefully unpack the lift making sure all the parts have been
included. Check for possible damages due to transport and storage; verify that what is
specied in the conrmation of order is included. In case of damage in transit, the customer
must immediately inform the carrier of the problem.
Remove the lift and all parts from delivery pallet and place on a clean, solid, at surface.
Packages must be opened paying attention not to cause damage to people (keep a safe
distance when opening straps) and parts of the lift (be careful the objects do not
drop from the package when opening.)
LIFT AND HANDLE ONLY ONE PACKAGE AT A TIME
2.1 DELIVERY AND CHECK OF PACKAGES
2.2 LIFTING AND HANDLING
When loading/unloading or transporting the equipment to the site, be sure to use suitable
loading (e.g. cranes, trucks) and hoisting means. Be sure to hoist and transport the
components securely so that they cannot drop, taking into consideration the package’s
size, weight, center of gravity, and its fragile parts.

5
IMPORTANT: THE PROPERTIES INDICATED APPLY TO LIFTS RUNNING AT
OPERATING TEMPERATURE.
IMPORTANT: COMPONENTS AND SPECIFICATIONS ARE SUBJECT TO
CHANGE WITHOUT NOTICE.
3-SPECIFICATIONS
Specications HD4P-12000
Overall Height 88” (2225mm)
Overall Width 137” (3480mm)
Overall Length 195 1/4” (4960mm)
Raising / Lowering time Approx. 51s
Max Lifting Height 67” (1700mm)
Lowered Runway Height 6” (170mm)
Width Between Columns 118 1/2” (3009.9mm)
Max Drive-Through Clearance 104 1/2” (2654mm)
Max Clearance Under Runway 63” (1600mm)
Runway Width 19 1/4” (489mm)
Width Between Runways 48” (219mm)
Runway Length (no ramp) 191 1/4” (4858mm)
Ramp Length 38” (970mm)
Load capacity 12,000 lbs” (5500kg)
Concrete grade min. 6” Thick Reinforced/ 3,000 PSI
Motor power 2.2KW
Power supply Single Phase 220V Grounded
Sound pressure level ≤75dB(A)

6
4-FLOOR REQUIREMENTS
WARNING: SPECIFICATIONS OF CONCRETE MUST BE ADHERED TO. FAILURE
TO DO SO COULD CAUSE LIFT FAILURE RESULTING IN PERSONAL INJURY
OR DEATH. THE FLOOR SHOULD BE A REINFORCED CONCRETE SLAB NOT
LESS THAN 6” (101.6MM) THICK WITH THE COMPRESSIVE STRENGTH OF THE
CONCRETE NO LESS THAN 3,000 PSI (20.68MPA).
DANGER: FOR CORRECT INSTALLATION OF THE LIFT, THE FLOOR MUST
BE FLAT AND LEVEL. CHECK WITH STRAIGHT EDGE AND LEVEL. IF A FLOOR IS
OF QUESTIONABLE SLOPE, CONSIDER A SURVEY OF THE SITE AND/OR THE
POSSIBILITY OF POURING A NEW LEVEL CONCRETE SLAB.
4.1 SELECTING THE SITE AREA
4.2 FLOOR REQUIREMENTS
1. Make sure that adequate space and height is available.
2. Check for ceiling clearance (lifting height plus vehicle height).
3. Check for clearance in front and rear of vehicle on lift.
4. Check for overhead garage door clearance.
Do not use the lift on any asphalt surface. Make sure the lift is used on a dry, oil/grease
free, at level CONCRETE surface capable of supporting the weight of the lift, the vehicle
being lifted, and any additional tools and equipment. The concrete oor surface should
have a minimum thickness of 6”. The concrete must have a minimum strength of 3,000 PSI,
and should be aged at least 30 days prior to use. Do not use the lift on concrete expansion
seams or on cracked, defective concrete.
IMPORTANT: NEW CONCRETE MUST BE ADEQUATELY CURED AT LEAST 30
DAYS MINIMUM. NO LIABILITY FOR ANY DAMAGES WILL BE ACCEPTED SHOULD
YOU INSTALL THE LIFT ON AN UNSUITABLE FLOOR.

7
4.3 ANCHORING TIP SHEET
1. Use a concrete hammer drill with a carbide tip, solid drill bit the same diameter as the
anchor, 3/4”. (.775 to .787 inches diameter). Do not use excessively worn bits or bits
which have been incorrectly sharpened.
2. Keep the drill perpendicular to the concrete while drilling.
3. Let the drill do the work. Do not apply excessive pressure. Lift the drill up and down
occasionally to remove residue to reduce binding.
4. Drill the hole for anchor bolt completely through the concrete. If an error is made during
the installation of these anchors, this will allow for the anchor bolt to be driven down
into the ground, so that a new anchor may be installed in place (g.1).
5. Be sure to clean all dust from hole. (g. 2).
6. Place a at washer and hex nut over threaded end of anchor, leaving approximately 1/4
inch of thread exposed above the nut (g.3). Carefully tap anchor into the concrete until
nut and at washer are against base plate. Be sure to only tap the top of the anchor and
not the nut. This could cause damage to the threads of the anchor.
7. Tighten the nut (g. 4) to 85 ft-lbs of torque.
DO NOT USE AN IMPACT WRENCH TO TIGHTEN ANCHORS!

8
5-INSTALLATION INSTRUCTIONS
IMPORTANT: BEFORE ATTEMPTING TO ASSEMBLE THIS LIFT TO MAKE SURE
THAT THERE IS ENOUGH ROOM FOR ALL COMPONENTS. THE SAFETY ROD
ASSEMBLY WILL TAKE UP ADDITIONAL SPACE WHILE BEING INSTALLED. KEEP
THE FLOOR AREA CLEAR OF THE LIFT COMPONENTS UNTIL THEY ARE READY TO
BE INSTALLED.
ASSEMBLY VIEW
POWER UNIT LOCATION
1) The power unit should be located at SAME SIDE as the POWERSIDE runway (with
cylinder.) Utility rails on the side of each runway MUST be installed to the inside. For
the remainder of this instruction manual we will illustrate the power unit mounted at
the DRIVER-SIDE (LEFT) FRONT column.

9
COLUMN & CROSSBEAM INSTALLATION
2) Install the latch bar (safety lock ladders) into columns with threaded stud end exposed
through the hole in top plate. DO NOT tighten the top nut and DO NOT secure the
bottom of latch bar at this time. (See Fig. A)
Fig. A
Latch Bar
Bolt and Nut
Threaded Stud
Nut
3) Place a chalk line on the oor according to the oor plan layout. Stand the columns
at their respective locations. DO NOT BOLT columns down at this time. Use caution to
prevent the columns from falling over. Place one crossbeam next to their appropriate
columns with cable sheave window positioned inward. Hold the threaded stud and
raise the Latch Bar to clear space for assembling crossbeams into columns (making
sure the plastic slide blocks are still in position,) then drop down the latch bar through
the slide block guide slots on crossbeams until the ladders come to rest on the base
plates. Tighten the top nut on top plate and secure the bottom latch bar with bolt, nut
and washer. Complete the same process for the other crossbeam.

10
RAISING THE CROSSBEAMS
RUNWAY INSTALLATION
CYLINDER AND CABLE INSTALLATION
4) Raise the crossbeams until the primary safety locks engage to facilitate Cable routing
and nal assembly.
5) The COLUMNS and CROSSBEAMS will now be in position and spaced properly for the
runways. Be careful not to disturb the Columns and Crossbeams at this time as they
may tip over causing personal injury or harm.
6) Position the POWERSIDE RUNWAY on top of the Crossbeams with the UTILITY RAIL
towards the center. The tting holes located at the side of the Powerside Runway
should be adjacent the POWER UNIT COLUMN. Align the holes in the runway with the
holes on the Crossbeams and bolt together (torque to 35-45 PSI) using hex head bolts
and nuts. (Refer to Fig. B) Complete the same process for the offside runway.
Fig. B
Bolt runway to the
crossbeams using hex
head bolts and nuts.
7) Locate the POWERSIDE RUNWAY easily identied by the Cylinder and Sheave
roller mounting structures welded on the underside. The Powerside Runway will be
positioned on the left of the lift where the Power Unit is installed.
8) In order to install the cables, it is necessary to rst extend the HYDRAULIC CYLINDER.
Install Cylinder and Cables as shown in Fig. C.
Steel Cable
Cable
Block

11
Fig. C
Cylinder Loop
9) Install the SHEAVES with AXLES under the Powerside Runway and route cables. (Refer
to Fig. D)
Fig. D
10) Route the Cable ends through the ends of each Crossbeam over the SLACK SAFETY
PIN by removing the pulley assembly, then to the top of each column. Reinstall pulley
after cable has been routed. Tighten the nut using Hex Nuts and Flat Washers at the
ends of the cable. (See Fig. E)
Crossbeam Pulley Removal Crossbeam Pulley Re-installation

12
Fig. E Fig. E
SLACK
SAFETY PIN
All cables MUST remain in sheave grooves. Before lift start-up,
check all of the cables for proper routing.
11) After routing the Cables double-check to make sure all are properly positioned and
REMAIN WITHIN THE GROOVES of ALL pins. (See Fig. E)
POWER UNIT INSTALLATION
ROUTING HYDRAULIC HOSE
LIFT START UP / FINAL ADJUSTMENTS
12) Mount the POWER UNIT to the Mounting Bracket using the M8 Hex Bolts and nuts
(torque to 35-45 PSI) then FILL THE RESERVOIR with 20-quarts of premium quality ISO-
32, AW-46 Hydraulic oil.
13) Install the hydraulic ttings to the power unit and base end of the cylinder under
runway, run the power unit hose through the front crossbeam tube to the cylinder base.
(refer to Fig. F) NOTE: BE SURE THAT THE HOSE IS CLEAR OF MOVING PARTS.
14) Be sure to grease all (6) zerk ttings. (See Fig. G)
Fig. F
Hydraulic
Fitting
Hose
Fig. G

13
15) Make sure the POWER UNIT RESERVOIR is full. Fill the oil tank with a premium quality
ISO-32, AW-46 Hydraulic Oil.
16) Spray a light lubricant to the inside and outside of the columns where the slide blocks
glide.
17) Test the power unit by pressing “UP” button. If the motor sounds like it is operating
properly, raise the lift and check all hose connections for leaks. If the motor gets hot or
makes unusual sounds, stop and check all electrical connections.
18) Before proceeding, double-check to make sure all cables are properly positioned within
the grooves of ALL sheaves. Make sure all cable sheave retaining pins and/or clips are
secure.
19) Check to make sure that all slack safety locks are cleared and free.
20) Continue pressing the “UP” button until the cables get taught and the lift starts to
move.
21) RAISE LIFT UNTIL THE CYLINDER BOTTOMS OUT AND THE LIFT STOPS. ADJUST
EACH CABLE SO THAT EACH SAFETY LOCK RESTS ABOVE THE TOP SAFETY LOCK
POSITION. It may be necessary to tighten or loosen each cable to reach the proper
height. The cable nuts MUST be tightened until there is at least one inch of threads
protruding through the nut.
ANCHORING THE COLUMNS
22) Before proceeding, DOUBLE CHECK MEASUREMENTS and make certain that the bases
of each column are square and aligned with the chalk line. Raise the lift up and down
and make sure it operates properly at the locations prescribed by the markings on the
oor. (See Fig. H)
Fig. H
Fig. I
23) Using the BASE PLATE on each column as a guide, drill each
anchor hole approximately 5” deep using a rotary hammer
drill and 3/4” concrete bit. ( See Fig. I)

14
24) After drilling, REMOVE DUST thoroughly from
each hole using compressed air and/or bristle
brush. Make certain that the columns remain
aligned with the chalk line.
25) Assemble the washers and nuts on the anchors
then tap into each hole with a hammer until the
washer rests against the base plate. Be sure that
if shimming is required, enough THREADS ARE
LEFT EXPOSED. ( See Fig. J)
Fig. J
Tap anchor bolts into each
hole with a hammer until
the washer rests against
the baseplate.
Fig. K
Fig. L
Tighten each anchor nut to 80 ft. lbs.
26) If shimming is required, insert the shims as
necessary under the base plate so that when the
anchor bolts are tightened, the columns will be
plumb. (See Fig. K)
27) After any necessary shims are installed, tighten
each anchor nut to 80 ft. lbs. IMPORTANT - If
anchor bolts do not hold when torqued to required
amount, concrete must be replaced. Saw cut
and remove 24” x 24” square area under each
column base then repour with reinforced 3000 PSI
concrete to a depth of six inches minimum, keying
new concrete under existing oor. (See Fig. L)

15
Fig. M
28) Install the front tire stops at the forward side of the lift using hex bolts, nuts and
washers. Torque to 35-45 ft. lbs. (See Fig. N)
Fig. N
Pin
Runway
Approach Ramp
Front Tire Stop
Hex
Bolt
FINAL ASSEMBLY
LEVELING/SYNCHRONIZING
29) Install the approach ramps on the entry side of the lift. (See Fig. M)
INSTALLATION HINT: Remove C-clip from ramp pin, slide pin through ramp and runway,
replace C-clip.
30) Using an engineer’s automatic Level (transit), locate the Level, at a convenient location
in the shop that allows an unobstructed view of all four corners of the runways.
31) Follow the Level manufacturer’s instructions for proper setup of the Level. Be sure it is
ADJUSTED LEVEL in all directions.
32) Raise the lift approximately 30”- 40”. Then lower lift until all locking latches are engaged
in each column and the runways are in full down position on locks.
33) Place a Level target on the right/front corner of the runway. (See Fig. O)
34) Beginning with “A” position, sight the level to the target and mark the number or the
graduation on the inch scale of the target that aligns to the cross hairs of the level (See
Fig. O)

16
BLEEDING
35) Next, move the target and place it at point “B” on the runway. (See Fig. O)
36) Rotate the Level and focus on the target scale.
37) Adjust the adjustment nut on the safety ladder bar at the top of the Column at “B” until
the cross hair of the Level align to reference mark on the target scale. (See Fig. O)
38) Repeat steps locating the target assembly at points “C” and “D” and adjusting safety
ladders at each corresponding column until the reference mark on the target scale is on
the cross hair of the Level. The runways are now level at all four points.
Fig. O
39) To complete the leveling procedures, TIGHTEN EACH SAFETY LADDER TOP NUT
against the bottom of the Column Top Plate. Torque to 35-45 ft. lbs.
40) Next, load vehicle onto the lift.
41) Raise the lift to full height. Listen and watch as the locking latches click in place.
SYNCHRONIZE BY ADJUSTING THE CABLES so that all four latches click at the same
time. Make necessary adjustments to the cables allowing COMPENSATION FOR
STRETCH.
42) Lift must be fully lowered before changing or adding uid.
43) Raise and lower lift six times. The cylinder is self-bleeding. After bleeding system, uid
level in power unit reservoir may be down. Add more uid if necessary to raise lift to full
height. It is only necessary to add uid to allow full height raise.
44) To pressure test, run lift to full rise and run motor for approximately 3-seconds after lift
stops. This will place pressure on the hydraulic system. Stop and check all ttings and
hose connections. Tighten or reseal if required.
Table of contents
Other Titan Lifting System manuals
Popular Lifting System manuals by other brands
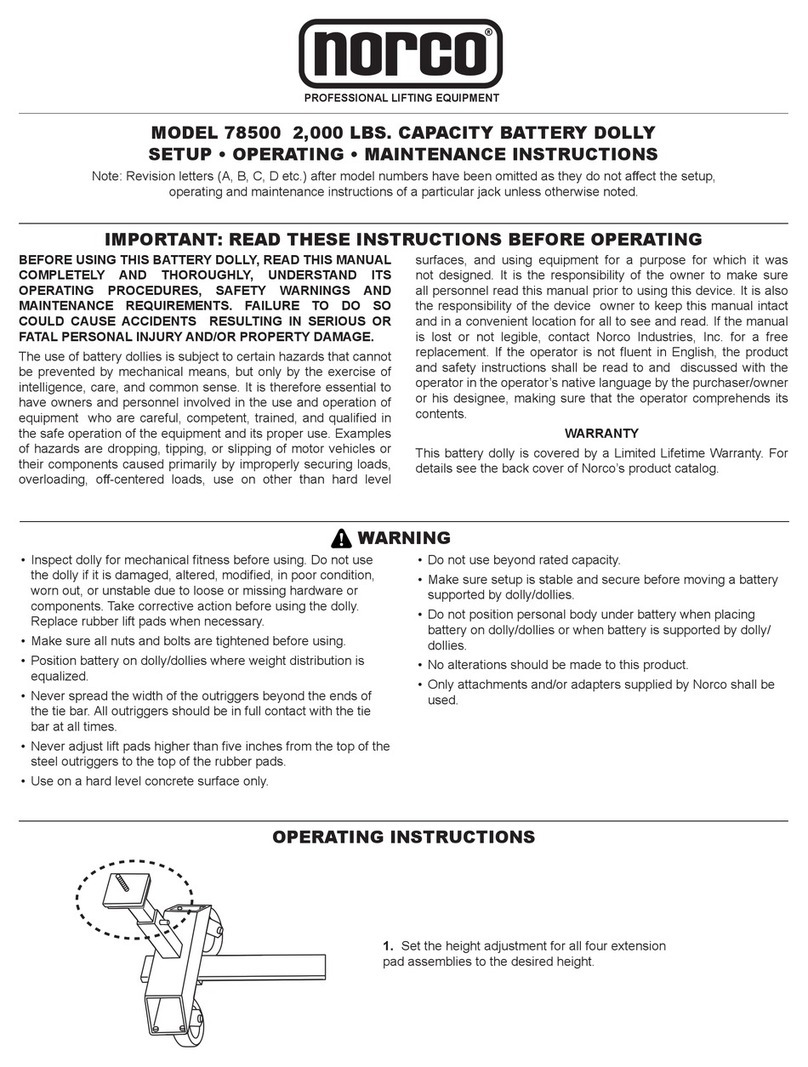
Norco
Norco 78500 Setup, operating, maintenance instructions
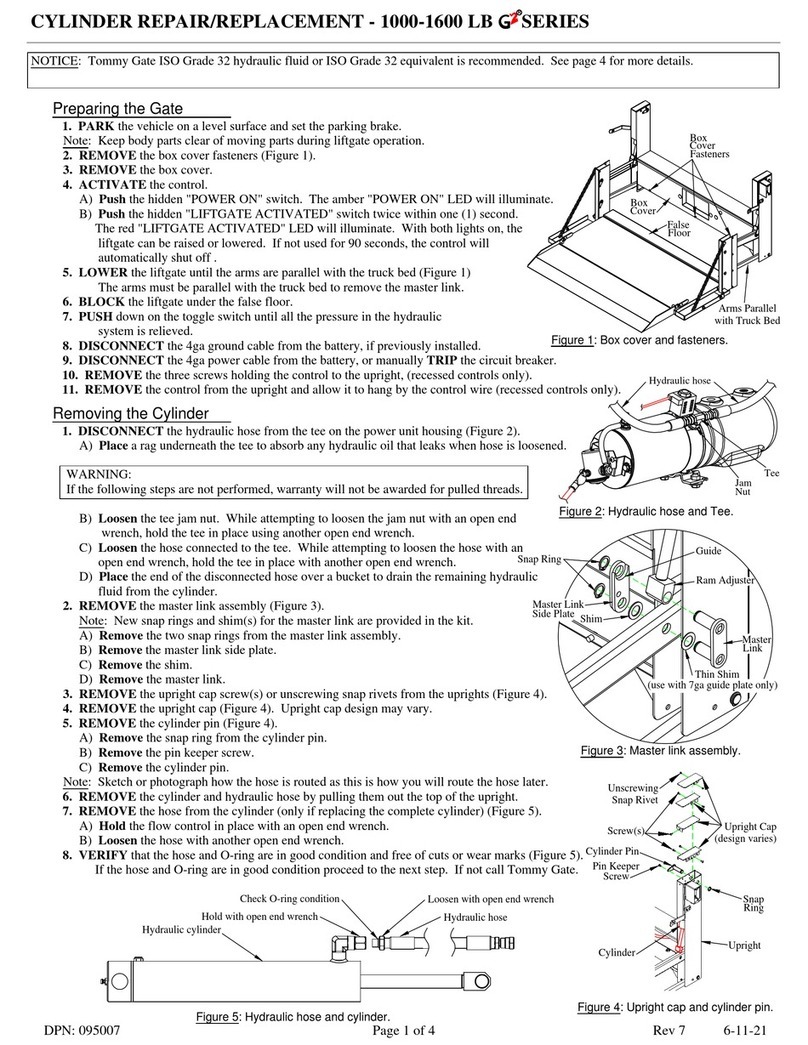
Tommy Gate
Tommy Gate Railgate 1600 Series quick start guide
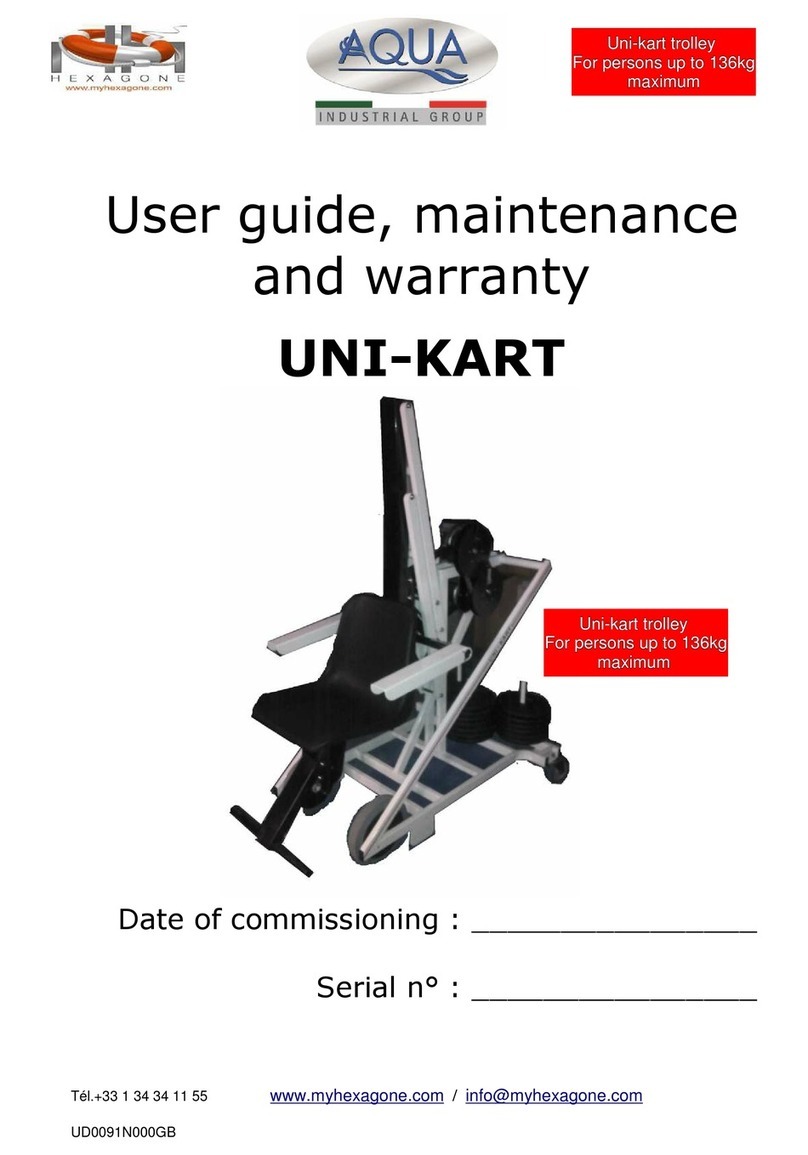
Aqua
Aqua Hexagone UNI-KART User guide, maintenance and warranty
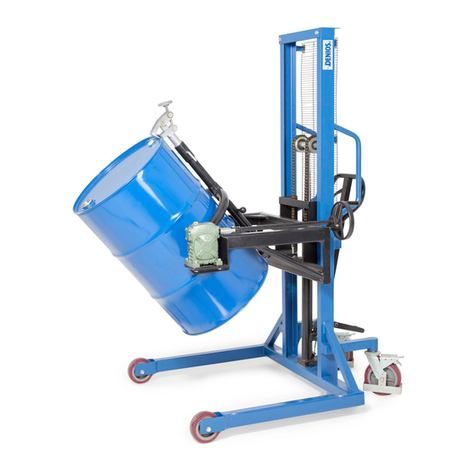
Denios
Denios FW-D user manual
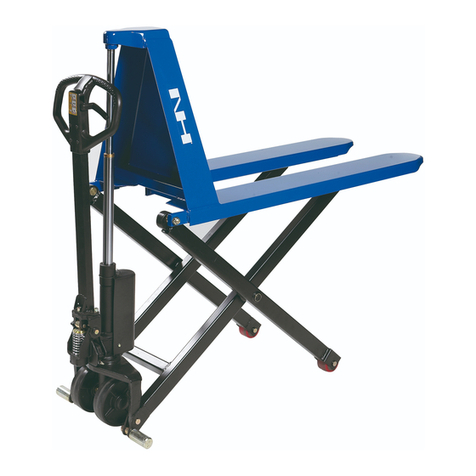
NH Handling
NH Handling SLP1000 user guide
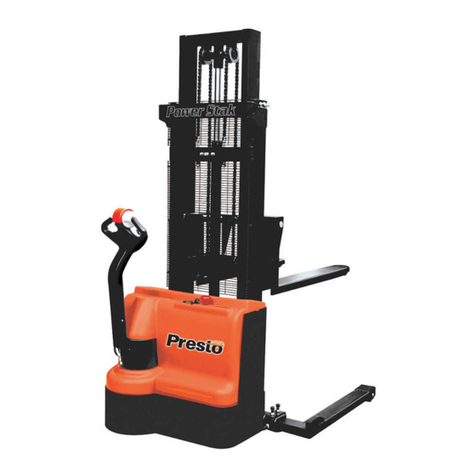
Presto Lifts
Presto Lifts Power Stak PPS2200-125AS Installation, operation and service manual