Turin TCR Series User manual

1
TCR SERIES COOPERATIVE ROBOT
USER MANUAL
TCR030 TCR050 TCR100
Shanghai Turin Smart Robot Co.,Ltd

2
Before using the robot, please read the safety instructions
carefully and use the robot based on the understanding of the
instructions.
We are committed to continuously improving the quality of our
products. The specifications and information related to our
products in this manual are subject to change without prior
notice. All statements, information and advice in this manual
have been carefully treated but are not guaranteed to be accurate.
The Company is not responsible for any direct or indirect losses
arising from the use of this manual and the products described in
it. Users must take full responsibility for the use of any
products and must use this manual and products with care.
Shanghai Turin Smart Robot Co.,Ltd has the right to interpret
all the contents of this manual.
Without the permission of TURIN, any reproduction, copy or
reprint of this Manual and any contents thereof is strictly
prohibited, and any contents of this Manual shall not be
disclosed to any third party.
All Rights Reserved:Shanghai Turin Smart Robot Co.,Ltd.
Service hotline:400-778-9969
Company address:Room 1001, Building 33, No. 258 Xinzhuan Road,
Songjiang District, Shanghai (R&D Centre)
Building 10, No. 169, Lifa Avenue, Hai'an City,
Jiangsu Province (Factory Address)
Website:http://www.turinrobot.com
E-mail:sa[email protected]m

3
Safety Instructions
This chapter describes the requirements for safe use of robots. Before
using the robot, be sure to read and understand all the information in this
chapter and other auxiliary manuals.
Companies and individuals using TURIN robots should familiarize
themselves with local and national standards and laws, and properly install
safety facilities to protect robot users. Before use (including but not
limited to installation, operation, maintenance and overhaul), please be
sure to read and fully master this manual and other ancillary materials, and
start using it after familiarizing yourself with all equipment knowledge,
safety knowledge and precautions (please refer to 《TURIN Industrial Robot
Application Technical Manual》 for safety precautions). However, TURIN
cannot guarantee that users will not be harmed even if they follow all the
safety information provided in the manual.
Users (including but not limited to operators, program personnel and
maintenance personnel) must pay attention to safety when using the robot,
and should at least wear appropriate work clothes, safety shoes and safety
hats for the operation.
Because the robot system is complex and dangerous, at any time, any
operation of the robot must pay attention to safety. Any time you enter the
robot's working area, it can cause serious injury. Only trained and
certified personnel should enter the area. (For more information about the
training, please consult Shanghai Turin Smart Robot Co.,Ltd.)
The maintenance manual diagram is for illustrative purposes only and may
require removal of the cover or safety cover. It's important to restore the
cover or safety cover before operating the parts and follow the manual's
instructions.
Please note that the drawings and photos in the instructions are
provided as representative examples only. They may differ from the product
you have purchased.

4
The specifications of the product may be modified at times to improve the
product or enhance its ease of use. It's essential to keep this in mind
while using the product. Any unauthorized modifications made by the customer
will not be covered under warranty, and the company will not be responsible
for any damages incurred.
PREFACE
This manual is applicable to the following robot models:
Type the name
Payload
TCR030/TCR050/TCR100
3kg/5kg/10kg
List of Relevant Instructions:
《TURIN Industrial Robot Application Technical Manual》
《General Industrial Robot Technology training manual》

1
DIRECTORY
1. Safety Precautions.....................................................1
1.1 Introduction to Safety Precautions....................................1
1.2 General safety precautions............................................1
1.2.1 Safety considerations for robotic systems...........................1
1.2.2 Security risks......................................................1
1.2.3 Safety behavior.....................................................4
1.2.4 Scram...............................................................6
1.3 Robot safety precautions..............................................7
1.3.1 Introduction to Safety Labels.......................................7
1.3.2 Potentially deadly danger...........................................7
1.3.3 The test work can be dangerous......................................8
1.3.4 Electrical hazards..................................................8
2. Product introduction...................................................9
2.1 Robot component composition...........................................9
2.2 Body of robot........................................................10
2.3 Control cabinet......................................................13
2.4 Button box...........................................................13
3. Mechanical body specification.........................................14
3.1 Product specification................................................14
3.2 Dimensions and range of motion.......................................16
3.3 Origin position and range of motion ..................................17
4. Robot handling and installation.......................................18
4.1 Handle...............................................................19
4.2 Installation.........................................................20
4.3 Installation and storage conditions ..................................22
5. Connection to control device..........................................23
6. Mounting dimensions of external fittings..............................24
6.1 End flange mounting dimensions.......................................24
7. List of finished collaborative robots.................................26

2
8. TURIN-TeachTool software Introduction.................................26
8.1 Overview.............................................................26
8.2 Function.............................................................26
8.3 Operating environment................................................26
9. TURIN-TeachTool Basic operation.......................................27
9.1 Connected robot......................................................27
9.2 APP preliminary understand...........................................29
9.2.1 Interface..........................................................29
9.2.2 Language...........................................................32
9.2.3 Password...........................................................33
9.3 Basic robot parameters...............................................34
9.3.1 Robot joint parameters.............................................34
9.3.2 Robot collision protection.........................................35
9.4 Robot file management................................................42
9.5 Robot Log Information................................................42
10. Hand operated robot..................................................44
10.1 Set up the coordinate system........................................44
10.1.1 Set up tool coordinate system.....................................44
10.1.2 Create user coordinates...........................................45
10.2 Manual operation....................................................45
10.2.1 Joint movement....................................................45
10.2.2 Linear motion.....................................................46
10.2.3 Point movement....................................................47
11. Programming operation................................................48
11.1 Introduction........................................................48
11.2 Program management..................................................49
11.2.1 New program.......................................................49
11.2.2 To run the program................................................50
12. Maintenance..........................................................53
12.1 Daily Inspection....................................................53
12.2 Quarterly Inspection................................................53
12.3 Annual Inspection...................................................54
12.4 Battery Replacement.................................................54
13. Zero calibration.....................................................55
13.1 Mechanical zero calibration.........................................56
13.2 Twenty-point Calibration............................................57

1
1.Safety Precautions
1.1 Introduction to Safety Precautions
This chapter includes two parts:
The first part is the general safety precautions, which are
generally applicable to all types of robots. For details, see 1.2
General safety Precautions!
The second part is the safety precautions for the robot, mainly
introduces the safety precautions for the robot operation and usage,
see 1.3 safety precautions for the robot operation!
1.2 General safety precautions
1.2.1 Safety considerations for robotic systems
This section does not cover how to design and install the robot,
nor does it cover peripherals that affect the safety of the robot. In
order to protect the user, the robot should be designed to comply
with the local and national standards and laws.
TURIN Robotics companies and individuals should familiarize
themselves with local and national standards and laws, and install
appropriate safety facilities to protect the people using the robots.
The user should be familiar with the instructions of the robot system.
But even if the operator followed all the safety information given in
the manual, TURIN could not guarantee that the operator would not
come to any harm.
1.2.2 Security risks
Overview: This section covers the dangers that may arise during the
installation and service of robots.
Safety risks when installing and serving robots:
1、See the section on Installation and Maintenance for details
on robot safety precautions;
2 、 The emergency stop button of the system must be in an
accessible position to stop the robot in case of an accident;
3、The operator must ensure that the installed safety measures
are available;
4 、 Operators must be trained to install, operate and repair
robots。
The specification of TURIN robots must also comply with
regional and national standards and legal rules.
Non voltage risk
1 、 The safety zone needs to be confirmed before the robot is
installed. The safety zone needs to be demarcated before the
robot is installed;

2
2 、 Protective measures or fences should be used to keep the
operator out of the robot's working area (signs such as "no trespass",
"no trespass", "High voltage hazard" should be placed in the relevant
area);
3 、 There SHOULD be NO hanging objects above the robot to
prevent it from falling and damaging the robot and other equipment;
4 、 The spring in the balance cylinder may spring out of the
failure of other parts and cause injury;
5、When DIS assembling the robot, pay attention to objects that
may fall from the robot and injure the person;
6、 Be careful of being scalded by high-temperature components
in the electric control cabinet;
7、When REPAIRING THE ROBOT, DO NOT USE THE ROBOT AS A LADDER,
DO NOT climb THE robot, in case of falling;
8、The high temperature in the reducer and the splashing of the
high temperature oil may cause injury to the human body;
9、It is strictly prohibited to pull any axis of the robot;
10 、 It is strictly forbidden to rely on the electric control
cabinet or touch the button at will, in case the robot has unexpected
action, which may cause personal injury or equipment damage.
Safety considerations for integrators:
1 、 The integration vendor must verify that all safety circuits
are interlocked with safety circuits for external applications;
2 、 The integration vendor must confirm that the emergency
emergency stop safety circuit and the external application safety
circuit are interlocked.
Integrated robot
Security risks
Detailed description
High temperature parts
The servo motor and reducer will
produce high temperature after a long
time operation, and it is easy to burn
by touching these parts. In high
temperature environment, the
temperature of the robot rises faster,
and the scald is more likely to happen.
Removing certain components
can cause the robot to
collapse
Take SOME NECESSARY MEASURES TO ENSURE
THAT THE ROBOT DOES NOT COLLAPSE WHEN
REMOVING SOME PARTS FOR EXAMPLE, when
removing the 2-axis motor, the arm and
forearm should be fixed to prevent the
robot from FALLING over
Cable
Security risks
Detailed description

3
Cables are fragile and easily
damaged
Cables are vulnerable to mechanical
damage, so special care should be taken
when transporting, storing and using
cables, especially the joints.
Motor reduction gear
Security risks
Detailed description
Reducer is easy to damage
under improper external force
Whether in the split motor reducer, or
in the installation of motor reducer,
reducer is easy to damage under
excessive improper external force.
1.2.2.1 Pay attention to hot parts in the robot
In normal work, many parts of the robot will get hot, especially
the servo motor and reducer. Sometimes the parts close to these two
parts will also get hot. Touching these places will easily cause
burns. As the ambient temperature becomes higher, more robot surfaces
will become hot and easily scalded.
Avoid measures:
1、Feel the temperature of the parts before touching them with
your hands to prevent burns.
2、Wait enough time for the hot part to cool down after the
shutdown before performing maintenance and other work.
1.2.2.2 Safety precautions for removing parts
Safe OPERATION: OPEN the cover or protection device after
confirming that the internal parts such as gears are no longer
rotating or moving. Do not open the protection device when gears and
bearings are rotating.
Safety DESIGN: If necessary, use auxiliary devices to keep
internally unsecured parts from their original positions.
1.2.2.3 Pneumatic/hydraulic safety precautions
Overview: This section is about the safety of the
pneumatic/hydraulic systems associated with robots
Residual energy: after turning off the air or hydraulic pump,
pneumatic/hydraulic system exists in the residual gas/liquid, the
gas/liquid has a certain energy, we should take some measures to
prevent the residual energy and equipment damage to human body,
before repair pneumatic and hydraulic components, need to put the
remaining energy release in the system.
Safety design: prevent components from falling and hydraulic oil
from flowing out;Safety valves are required to prevent accidents;
Maintenance tools need to be prevented from falling.
1.2.2.4 Risk during operation

4
Overview: Industrial robot is a flexible system, can be applied
in many industrial fields, all the work must be operated by
professional personnel, and abide by certain safety standards. Care
must be taken at all times when operating.
Highly Qualified operators: Industrial robots must be operated by
professionals who are familiar with the whole system and understand
the risks involved in the individual subsystems.
Risk of anomalies: Be especially careful if an anomaly occurs
during normal operating procedures.
1.2.2.5 Risk of electric
Overview:
1、Although it is necessary to turn on the power supply
for fault diagnosis in many cases, it is necessary to turn off the
power supply and cut off other power connections during the actual
maintenance of the robot.
2、The main power supply of the robot needs to be installed outside
the operating range of the robot, so that the operator can shut down
the robot outside the operating range even if the robot loses control.
Electrical hazard to operator:
High voltage hazard for operators to be aware of:1.Servo motor power
line;2. Power lines connecting fixtures and other devices Electrical
hazard fixtures, external equipment, etc. After the robot is shut
down, the external equipment of the robot may still be running, so
the power cord of the external equipment will also be injured, or the
power cable will be damaged.
1.2.3 Safety behavior
1.2.3.1 Security measures
Overview:Fences and warning signs should be installed around the
working area of the robot to ensure the safe operation of the robot,
prevent random people from entering and prevent the robot from
injuring people.
Security measures:When setting safety protection measures, it is
necessary to consider that the workpiece held by the robot will cause
harm to personnel.
1.2.3.2 Disassemble the robot arm in case of emergency
Describe:In the event of an emergency, any arm of the robot
gets caught by the operator and needs to be removed. Small robot arms
can be removed manually, but large robots need to be lifted by a
crane or other equipment.
The secondary damage:Before releasing the knuckle lock, the arm
needs to be secured to ensure that the arm does not cause secondary

5
damage to the trapped person due to gravity.
1.2.3.3 Brake test
Why do we test:In normal operation, the lock will usually wear out,
in which case, it is necessary to test the lock。
Check the locking procedure:1.Let the joints of the robot move to
The position where the joints bear the maximum load;
2.Turn off the robot and open the lock;
3.Mark each joint;
4.After a period of time to see whether the robot
joints are moving.
Attention:When the robot is operated in manual declaration
mode, all personnel must stand outside the safe
space to avoid any injury.
Attention:Before the robot releases the brake, the
operator must make a safety check to ensure that the
arm will not move under gravity and cause additional
hazards.
1.2.3.4 Use the button box safely
Attention:ENABLE is a button on the button box, when
pressed, the servo motor is enabled; When disconnected,
the servo motor is disconnected enabled.
To ensure safe use of the button box, follow the following
rules:
1.The enable button must not fail at any time;
2.During programming or testing, the enable needs to be
disconnected in time;
3.When the trainer enters the working area of the robot, he
or she is required to carry a button box and tablet, so that
others cannot move the robot without the programmer's
knowledge.
enable:When temporarily stopping the robot or programming or testing,
turn off the enable in time。
1.2.3.5 Work within the scope of the robot
Dangerous: If the work must be carried out within the
scope of the robot, the following rules should be followed:

6
1.This function can be enabled only when the mode is set to
manual, and other automatic controls such as computer control are
disconnected;
2.When the robot is in manual mode, the speed must be limited
to less than 250mm/s; When the robot needs to be set to full
manual speed, only professionals who are fully aware of the
risks should operate it;
3.Pay attention to the revolute joints of the robot to prevent
hair and clothes from being involved in the joints; At the
same time, attention should be paid to other dangers caused
by the movement of the robot, or other ancillary equipment;
4.Test whether the motor lock is working properly to prevent
personal injury caused by abnormal robot;
5.Consider the contingency plan when the robot suddenly moves
towards its prescribed position;
6.Make sure you have shelter, just in case。
Dangerous:Under no circumstances should you stand under
any robot arm in case the robot moves abnormally or
someone else moves to enable it.
1.2.4 Scram
Definition of emergency stop:
The emergency stop is independent of all robot
electrical control and can stop all robot movements,
An emergency stop means that all the power connected
to the robot is disconnected, but the power to the lock on
the servo motor is not disconnected. You must release the
emergency stop button and restart the robot so that the
robot can operate again.
Emergency stops for robotic systems need to be
distinguished:
1.An uncontrolled emergency stop stops the robot by
cutting power to all servomotors;
2.A controlled emergency stop stops the robot by
giving commands to the servo motor so that the robot can
complete its path, and when it completes its path, the
servo motor stops supplying power.

7
Attention:An emergency stop should only be used
when it's really needed, it's really urgent
Cases.
Attention:Emergency stop can not be used for
normal procedures to stop, shut down the robot
etc.
Scram button
There are several emergency stop buttons in the
robot system to stop the robot. There is a red
button on the teaching box and the electric
control cabinet (as shown in the picture below).
1.3 Robot safety precautions
Before use (installation, operation, maintenance, overhaul),
please be sure to read and fully master this manual and other
ancillary data, after familiar with all equipment knowledge, safety
knowledge and precautions before starting to use. The safety
precautions in this manual are classified into four categories:
"Danger", "Caution", "Mandatory" and "Prohibition" respectively.
1.3.1 Introduction to Safety Labels
1
Sign
Explanation
2
Danger
Sign used to indicate that
there is a risk of death or
serious injury if mishandled.
3
Caution
Sign used to indicate that
there is a risk of moderate
injury, minor injury, or damage
to objects if mishandled.
4
Mandatory
Actions that must be strictly
followed.
5
Prohibition
Actions that are strictly
prohibited.
1.3.2 Potentially deadly danger

8
Overview:Any working robot is a potentially deadly machine.
When operating, the robot may have unpredictable actions. All the
movements have strong forces that may cause serious injury to people
in the early working range or damage to equipment.
Avoid to:Before preparing the robot for work, test the
reliability of each safety measure (switch).
Security measures include:Fence gate, lock, safety indicator
light.
Avoid measures:Before starting the robot, ensure that there are
no other idle people in the working range of the robot.
1.3.3 The test work can be dangerous
Overview:Since the robot needs to be disassembled for the repair
service work, several risks need to be considered for the first test
work after the repair work is completed.
Measures:The first test after repair, installation, maintenance,
etc., needs to follow the steps below:
Clean all maintenance and installation tools on the robot and within
the scope of the robot;
Install all safety precautions;
Make sure everyone stays out of the safe range of the robot;
Special attention should be paid to the working condition of the
repaired parts during the test.
Attention:When programming a robot, pay special
attention to the potential for interference.
1.3.4 Electrical hazards
Overview:Electric control cabinet is the center to control the
robot. Any misoperation of the electric control cabinet is likely to
produce electric shock and robot misoperation, which will cause harm
to people and equipment.
Dangerous:1. Never lean on electric control cabinets or other control
cabinets; Do not arbitrarily press the operation button. Otherwise,
unexpected actions of the robot may occur, which may cause personal
injury and equipment damage.
2. During operation, do not allow non-working personnel to
touch the electric control cabinet. Otherwise, unexpected actions
of the robot may occur, which may cause personal injury and

9
equipment damage.
3. When wiring and piping between electric control cabinet,
robot and peripheral equipment, take protective measures, such as
passing pipes, wires or cables through pits or covering them with
protective covers to avoid being trampled on or run over by
forklifts. The OPERATOR and other personnel may be caught by the
open wire, cable or pipe, which will cause the abnormal action of
the robot, resulting in personal injury or equipment damage.
4. When installing a tool on the robot, be sure to first cut OFF
the power supply on the control cabinet and installed tools and
lock the power switch, and to hang a warning sign. If the power
supply is connected in the installation process, it may cause
electric shock, or the abnormal movement of the robot, thereby
causing injury.
5.Before operating the robot, press the emergency stop button
on the front door of the electric control cabinet and the upper
right of the teaching programmer to check whether the indicator
light of "Servo ready" Is off and confirm that the power supply is
turned off.
2.Product Introduction
Before using the product, make sure you have read and fully
understood the Safety Specifications in Chapter 1. This chapter will
provide a brief introduction to the basic components and usage of
the TCR series collaborative robot as an initial understanding of
the robot.
2.1 Robot component composition

10
Figure 2-1 Composition of Robot
Body of robot : The body of the robot is an industrial
collaborative robot used for object handling or assembling with
various tools such as grippers.
Control cabinet:The control cabinet includes core computing
components, has various electrical interfaces, and can be connected
to multiple devices and equipment. Users can adjust the robot arm
movement according to edited programs.
Pad:The pad is a device used for the operating system, which
enables the robot to learn specific positions or perform robot
trajectory and programming control.
Button box : The button box is a handheld device used for
manual manipulation of the robot.
2.2 Body of robot
1
2
3
4

11
As shown in Figure 2-2, the body of the robot includes 6 rotating
motion joints (J1 to J6), as well as the base, upper arm, lower arm,
and end effector. The outer side of the tool flange is equipped with
tool I/O and teaching and calibration function buttons.
Figure 2-3 shows a schematic diagram of the robot's end effector,
and Table 2-1 shows the name and description of the robot's end
effector components.
Figure 2-2 Body of Robot
J3
J2
J4
J5
J6
J1

12
Figure 2-3 Robot End Effector
Name and Description of Robot End Effector Components
Number
Name
Description
1
Flange
The location for installing tools on the
robot.
2
I/O
Input/output interface used to control the
tool.
3
Drag teaching
switch
Push down to put the robot in zero force
control mode, allowing the user to directly
move the robot to any reachable posture.
4
Command
adding switch
Push down to add a motion command that
includes the current robot position to the
current program. The motion type, motion
speed, and joint motion are the same as the
previous command (if there is no motion
command in the current program, the speed of
the joint motion is added at 50%).
Usage of the drag teaching button:
1、Ensure that the robot installation posture, end
effector load, and Tool Center Point (TCP) parameters
are correctly set.
2、Fully evaluate potential hazards in the surrounding
area, otherwise it may cause personal injury or
equipment damage.
1
2
3
4

13
2.3 Control cabinet
1
2
3
4
567
8
Control Cabinet Description
Number
Name
Description
1
Power cable
Power cable for the robot.
2
Power cable
Used to connect power and turn on the
robot.
3
Handle
Convenient for moving.
4
Communication cable
Signal cable.
5
Reserved wiring
hole
Reserved for customer wiring.
6
Teaching pendant
interface
Used to connect the control cabinet to
the teaching pendant (optional).
7
USB
Input/output interface.
8
E/NET
Local area network (LAN) for general
use.
2.4 Button box

14
1
2
3
4
5
6
Button Box Description
Number Name Description
1Emergency
stop switch
Shuts off the servo power and stops robot
operation.
2Start button Used to start the robot in automatic mode.
3Enable button
Ensures the safety of the operator. Only
when in the "click to open" state, can the
enable button be pressed to perform manual
operation and program debugging of the
robot.
4Pause button Pauses robot operation with servo closed.
5Appointment
button
Starts the program of various fixtures
according to the appointment order.
6
Mode
selection
button
Used to switch between manual and automatic
modes.
3.Mechanical body specification
3.1 Product specification
This manual suits for next models
3
Table of contents
Other Turin Robotics manuals
Popular Robotics manuals by other brands
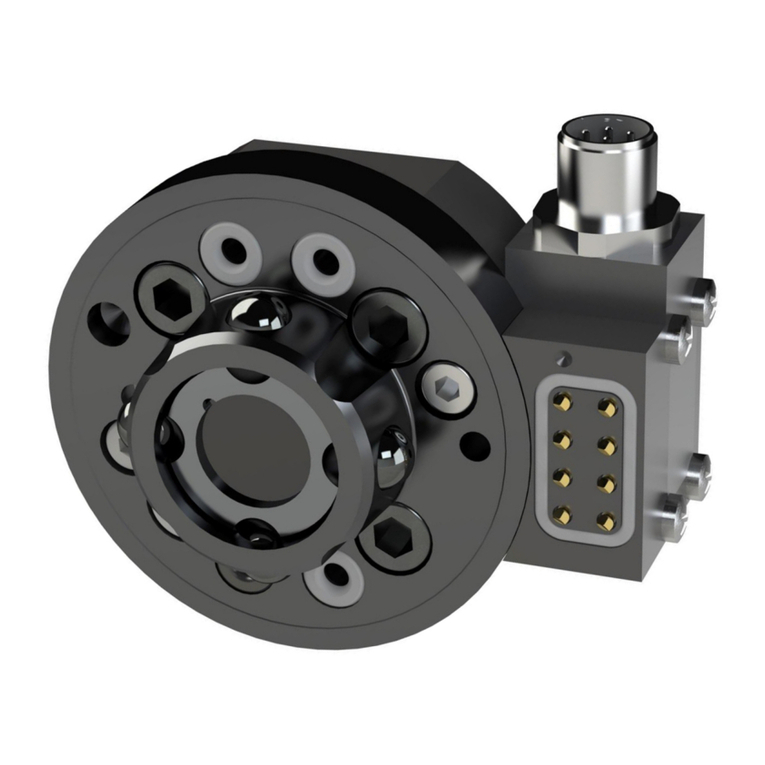
RSP
RSP TC5 Installation and Maintenance
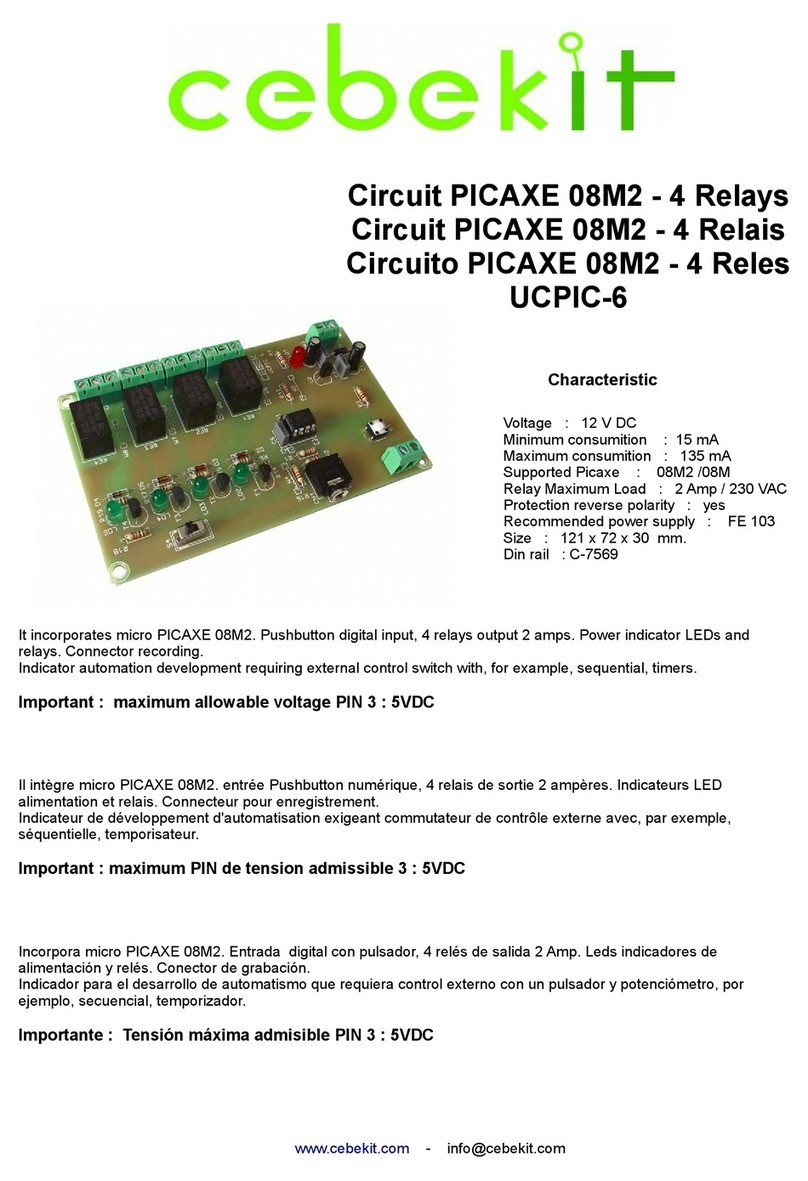
Cebekit
Cebekit UCPIC-6 manual
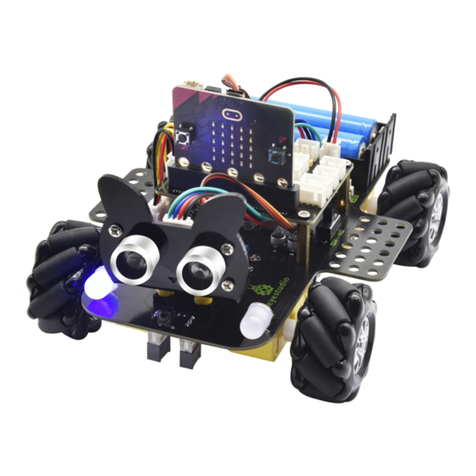
Keyestudio
Keyestudio 4WD Bluetooth Multi-functional Car manual

AndyMark
AndyMark Rover am-4100 PN8 Series user guide
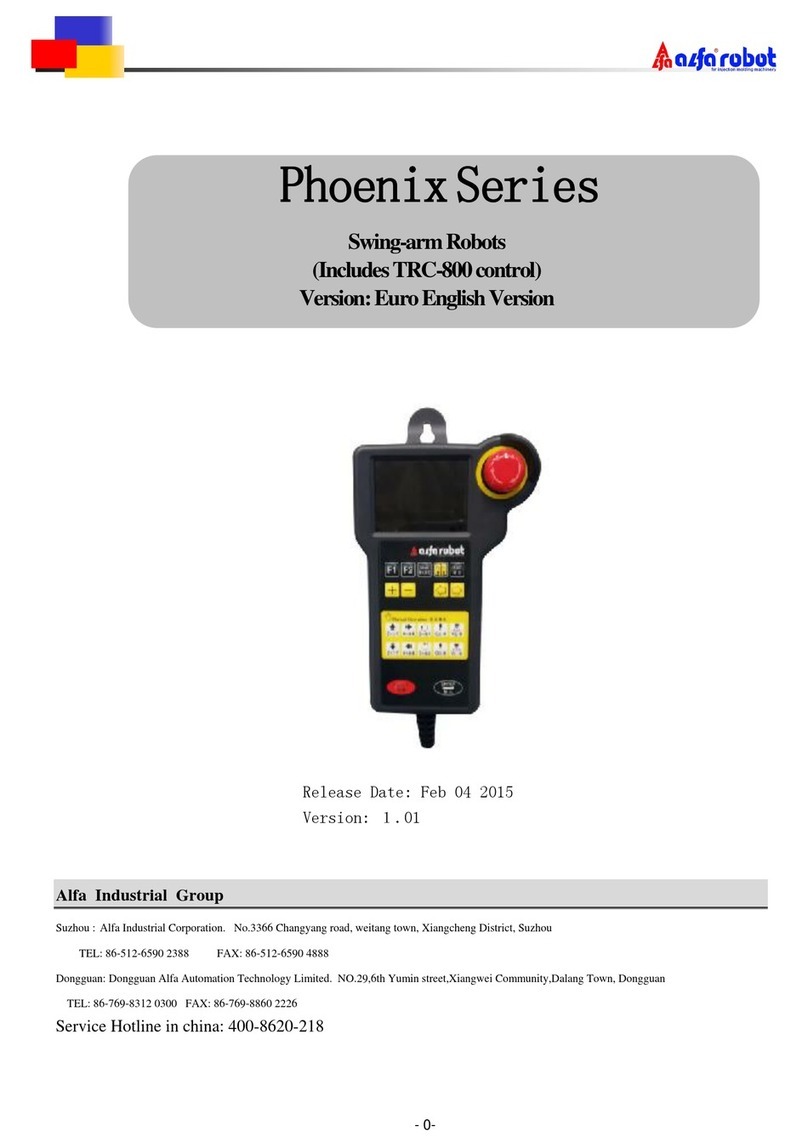
alfa robot
alfa robot Phoenix Series manual
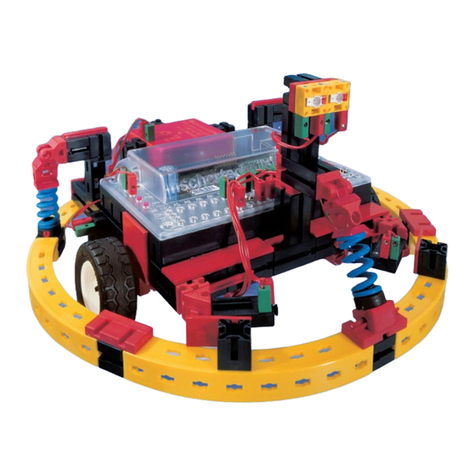
fischertechnik
fischertechnik COMPUTING ROBO MOBILE SET Assembly instructions