UE Systems ULTRAPROBE 201 User manual

Version 1 1
ULTRAPROBE®201
Instruction Manual

Version 1 2
Safetyadvisory
Please read before using your instrument.
Warning
Improper use ofyour ultrasonic detectormay result in death orserious injury. Observe all safety
precautions. Do not attempt to make any repairs or adjustments while the equipment is operating.
Be sure to turn off and LOCK OUT all electrical and mechanical sources before performing any
corrective maintenance. Always refer to local guidelines for appropriate lockout and maintenance
procedures.
SAFETYPRECAUTION: Although your ultrasonic instrument is intended to be used while
equipment is operating, theclose proximity of hot piping, electrical equipment androtating parts
are all potentially hazardous tothe user.Be sure to use extreme caution when using your
instrument around energized equipment. Avoid direct contact with hot pipes or parts, any moving
parts or electrical connections. Do not attempt to check findings bytouching the equipment with
your hands or fingers. Besure to use appropriate lockout procedures when attempting repairs.
Be careful with loose hanging parts such as the wrist strap or headphone cord when inspecting
near moving mechanical devices since they may get caught. Don't touch moving parts with the
contact probe. This may not only damage the part, but cause personal injury as well.
When inspecting electrical equipment, use caution. High voltage equipment can cause death or
severe injury. Do not touch live electrical equipment with your instrument. Use the rubber
focusing probe with thescanning module. Consult withyour safety director before entering the
area and followallsafety procedures. In high voltage areas, keep the instrument close to your
body by keeping your elbows bent. Use recommended protective clothing. Do not get close to
equipment. Your detector will locateproblems at a distance.
When working around high temperature piping, usecaution. Use protective clothing and do not
attempt to touch any piping orequipment while it is hot. Consult withyoursafety director before
entering the area.

Version 1 3
Theory .......................................................................................................................... 4
Monitoring bearing wear.............................................................................................. 5
Component assembly magnetic mount sensor ................................................................ 6
Basic components ....................................................................................................... 6
Component Assembly Instructions................................................................................. 7
UE Systems Grease Caddy Docking Station Mounting Instructions...................................... 7
UE Systems Grease Caddy Docking Station Mounting Instructions...................................... 8
Metered Housing........................................................................................................ 9
Headphones..............................................................................................................10
Using the Ultraprobe 201 Grease Caddy ........................................................................11
Specifications Ultraprobe 201 (Grease Caddy)....................................................................12

Version 1 4
Theory
Ultrasoundconsists ofhigh frequency sound waves that are above the hearing limits of human
perception. Generically ultrasonic frequencies are considered to start at 20,000 cycles per
second ( 20 kilohertz or 20 kHz). Most ultrasonic instrumentation used for equipment condition
analysis includes frequencies that range from 20 to 100 kHz. Instruments such as the Ultraprobe
201 Grease Caddy use an electronic process called “heterodyning” to allow for accurate
translation of ultrasound produced by operating equipment into the audible range where users
can hear thesesounds through headphones andobserve the amplitude ofthesoundon ameter.
The short wave, high frequency nature of ultrasoundoffers many advantages for instruments
used to inspect operating equipment
1. The amplitude of generated ultrasounds will fall off rapidly as the sound travels from its’
source providing a “localized” signal that can be detected and monitored with relative ease
in most noisy environments.
2. The subtle nature ofthis signal provides for early warningof potential failure modes.
3. Increases in friction of rolling elements can be detected and used as an indication oflow
lubrication levels.
4. Using base line information, amplitude levels can be used as a guide for determining when
and when not to lubricatea bearing.
5. The heterodynedsignal helps users hear when grease is entering the bearing and
recognize when to stop lubricating.

Version 1 5
Monitoring bearing wear
In a bearing, normal bearing loads cause an elastic deformation ofthe elements in the contact
area, which give a smooth elliptical stress distribution. But bearingsurfaces are not perfectly
smooth.
For this reason, the actualstress distribution in the contact area will be affected by a random
surface roughness. In the presence of a lubricant film on a bearing surface, there is a dampening
effect on the stress distribution and the acoustic energy produced will be low.
Should lubrication be reduced to a point where thestress distribution is no longer present, the
normal roughspots will make contact with the race surfaces and increase the acoustic energy.
These normal microscopic disuniformities will begin to produce wear and the possibilities of small
fissures may develop which contributes to the „Pre-Failure“ condition. Therefore, a side from
normal wear, the fatigue orservice life of abearing is strongly influenced by the relative film
thickness provided by anappropriate lubricant.
Ultrasonic inspection and monitoring of bearings is by far the most reliable method for detecting
early stages of bearing failure and conditions such as lubrication starvation. The ultrasonic
warning appears priorto a rise in temperature or an increase in lowfrequency vibration levels.
Ultrasonic inspection of bearings is useful in recognizing the beginning stages of fatigue failure
relatedto flooding of orlack of lubricant.
In ball bearings, as the metal in the raceway, roller or ball bearing begins to fatigue, a subtle
deformation begins to occur. This deforming of the metal will produce irregular surfaces, which
will cause an increase in the emission ofultrasonic soundwaves.
As a ball passes over a pit or fault in the race surface, it produces an impact. A structural
resonance of one of the bearing components vibrates or „rings“ by this repetitive impact. The
sound produced is observed as an increase in amplitude in the monitored ultrasonic frequencies
of the bearing.
When listening to a bearing, it is recommendedthat a user become familiar with the sounds ofa
good bearing. A good bearing is heard as a rushing orhissing noise. Crackling or roughsounds
indicate a bearing in the failure stage. Louder rushingsounds similar to that of a good bearing
only slightly rougher,can indicate lack of lubrication.
A change in amplitude from the original base line reading can be an indication of:
a. lack oflubrication or
b. incipient bearing failure.
When a reading exceeds any previous reading by 8-10 dB with no change in the sound quality (a
“rushing” noise) this is an indication of lubrication starvation, an increase of greaterthan 12 dB
can beconsidered to be an indication ofthe beginning of the failure mode.

Version 1 6
Component assembly magnetic mount sensor
Basic components
Your kit consists of the following parts:
A Grease CaddyAssembly
B Clamp
C SensorAssembly –Magnetic Sensorand Cable with Acoustic Shield

Version 1 7
Component Assembly Instructions
1. Attach the Ultraprobe 201 Grease Caddy A to the grease gun, using ClampB.
2. Connect cable from Sensor Assembly to input of Grease Caddy
Before you begintesting, it is advisable to familiarize yourself with the basic components ofyour
kit.
UE Systems Grease Caddy Docking Station Mounting Instructions
Docking Station:
Note the Raised disc with the logo.
This is to face away from the grease gun.
1. Remove tip ofgrease gun 2. Line upindent facing grease gun
3. Srew on Docking Station and tighten 4. Screw on grease gun tip and tighten
NOTE: Do not use Docking Station when using rubber orplastic tubes.

Version 1 8
UE Systems Grease Caddy Docking Station Mounting Instructions
Completed setup
Close up view Ready to use
Keep Magnetic on Docking Station when
greasing
NOTE: Do not use Docking Station when using rubber or plastic tubes.

Version 1 9
Metered Housing
The main component of the Ultraprobe 201 is the metered housing. From back to front, let‘s
examine each part.
On and OFF buttons. To turn the instrument ON, push the ON button in. Once pressed
the instrument will stay on and then automatically turn off after 5 minutes (this will extend
the battery charge and active use of the instrument). To turn the instrument OFF before 5
minutes have elapsed, press the OFF button.
Bar graph Display: The display consists of a ten segment LED bargraph that will indicate
ultrasonic signalstrength. A lownumber of LEDs indicate a lowlevel of ultrasound.
Conversely more intense ultrasonic signals will display moreLEDs.
Battery Level Light: This red light turns on only when the batteries need to be recharged.
Sensitivity Selection Dial: There are eight (8)sensitivity levels which read out in related
decibels of „0“ to „70“. As the dial is turned to the right, to „0“, the sensitivity of the
instrument increases. As the dial is turned to the left, to „70“, the sensitivity decreases. A
low-level ultrasound emission produces low amplitude. To detect low-level ultrasounds,
the instrument should be in a highsensitivity position. 0 is the highest sensitivity position.
For higher amplitude signals, move the sensitivity to the left towards „70“.
The dial dB indications, along with the LED indications in the bar graph may be used to
establish dB levels. To do this, just add 3 dB for each LED bar graph indication to the dB
level set in the sensitivity dial. EX: 0 dB on the sensitivity dial, plus 3 LED bar graph
levels = 9dB (0+9). 40 dB on the sensitivity dial plus 4 bar graphs = 52 dB (40+12)
“Phone” Jack: This is where you plug in the headphones. Be sure to plug it in firmly until
it clicks. Should a recording device be utilized, this is where the cable is inserted. (Use a
miniphone plug).

Version 1 10
Headphones
The standard headphone plugs into the “phone” jack. NOTE: Always use the headphones when
operating the Ultraprobe 201 Grease Caddy. There may be times where stray signals influence
the LED indicator. Using the headset will assure that thesounds being received are coming from
the subject test bearing.
a. Should inspections be performed in areas where either hard hat or hearing protection is
required, there are optional headphones available for both hard hat use and for use in
high noise areas. These heavy duty headphones are designedto block out intense
sounds often found in industrial environments so that the user may easily hear the
sounds received by the ULTRAPROBE 201.
b. For those situations in which it is not possible or difficult to wearthe standard
headphones described above, UE Systems has two other options available: 1. the DHC
1991 Earpiece which loops around the ear, and 2. the SA-2000 Speaker Amplifier which
is a loudspeaker that is compatible with the Ultraprobe headphone output jack.
Front:
A Guide Light
When the unit is on, the guide light automatically is on to help users see in dark locations.
B Wave Guide Connection
C Recharge Jack

Version 1 11
Using the Ultraprobe 201 Grease Caddy
You may use your Ultraprobe 201 Grease Caddy to knowwhen to lubricate by setting a baseline
level. You may choose to lubricate whenever a bearing exceeds a pre-set baseline by 8 dB-12
dB accompanied by a uniform white noise orrushingsound. If a bearing is belowthis level, it
does not need lubrication, therefore do not lubricate bearings with low level readings when
compared to a baseline.
A. When lubricating:
I. Listening while adding lubrication
a. Be sure the greasecoupler issecurely connected to thezerk fitting and that the
magneticsensoris in full contact with the bearing housing.
b. Wear your headphones and besure the head phones are plugged into the
headphone jack.
c. Turn the Ultraprobe 201ON.
d. If the sound is too loud, reduce the sensitivity: turn the Sensitivity Dial LEFT until
the LED’s are at approximately 50% of scale.
e. Apply the lubrication and listen.
II. When toSTOP lubricating:
While applying the lubrication the sound level will begin to drop. You maystop:
a. when thesound level drops off andsuddenly rises or
b. when thesound level approaches a pre determined baseline level which (usually
a drop of 2-3 LED bars on the meter).

Version 1 12
Specifications Ultraprobe 201 (Grease Caddy)
Housing
Attaches directly to the grease gun, gives visual and audible
indicationfor proper lubrication
Construction
Aluminum housing
Dimensions
13.3 x 6.7 x 4.5 cm (LWH)
Operating Temperature
0 °Cto 60°C
Relative
10-95% non-condensing at up to 30 °C
Circuity Humidity
SMD/Solid State heterodyne receiver
Transducer
Magnetically mounted piezoelectric transducer
Frequency Response
Peak response: centered around 38kHz
Indicator
10 Segment LED BarGraph (red)
Bright white LED forillumination oftest area
Sensitivity Selection
8 position precision attenuation
Power
Rechargeable nickel metal hydride
Power off
Time delay after five (5) minutes
Low Batteryindicator
LED
Headset
Deluxe noise isolating headset for hard hat use
Over 23 dB of noise attenuation
Meets or exceedsANSI Specifications and OSHA standards
Attachment
Universal: fits mostcommercially usedcartridge grease guns
Weight
0.45 kg
Warranty
1-year parts/laborstandard,
5 years withcompleted warranty registrationcard.

Version 1 13
Need further support?
Want information regarding products or training?
Contact :
UE SystemsEurope, Windmolen 22, 7609 NN Almelo (NL)
e: info@uesystems.eu w: www.uesystems.eu
t: +31 (0)548 659-011 f: : +31 (0)548 659 010
www.uesystems.eu
Table of contents
Other UE Systems Tools manuals
Popular Tools manuals by other brands
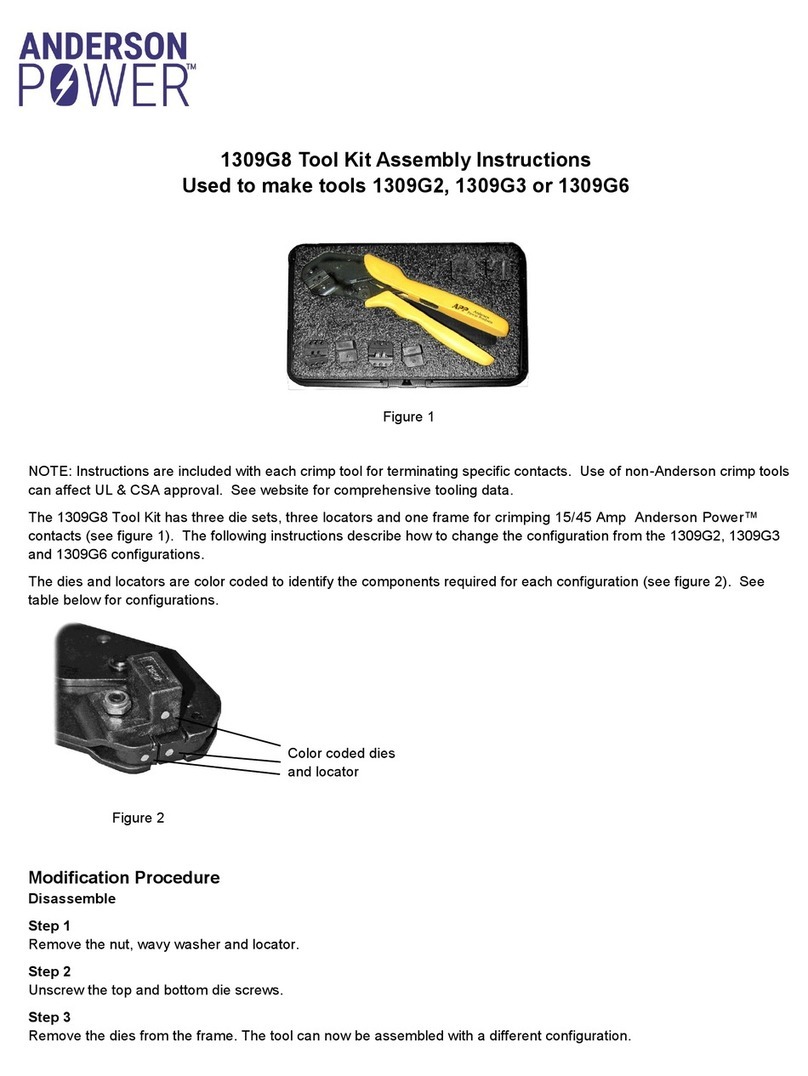
Anderson
Anderson 1309G2 Assembly instructions
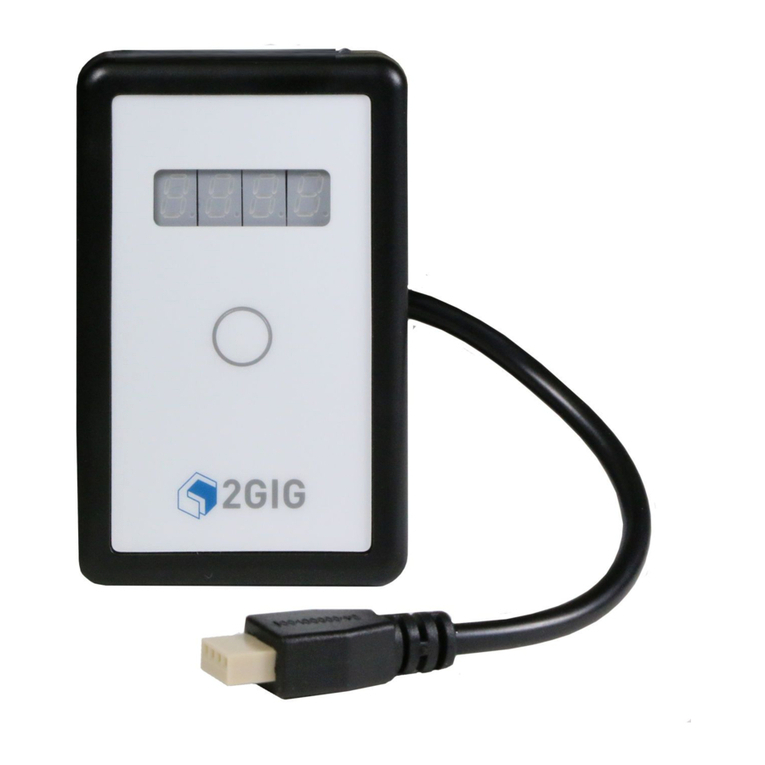
2gig Technologies
2gig Technologies EASY UPDATER quick start guide

OEM Tools
OEM Tools 87009 Operating instructions and parts manual
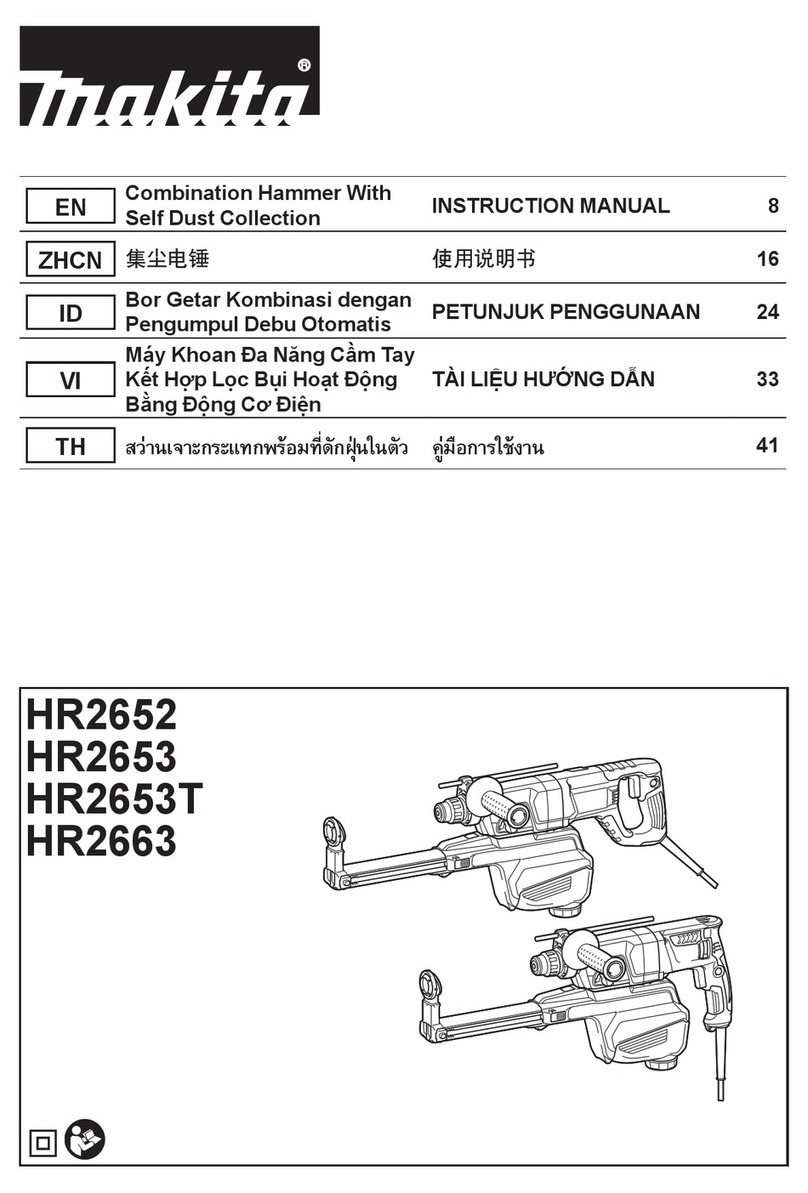
Makita
Makita HR2653T instruction manual

Powerfix Profi
Powerfix Profi PMTR 4 A1 translation of original operation manual
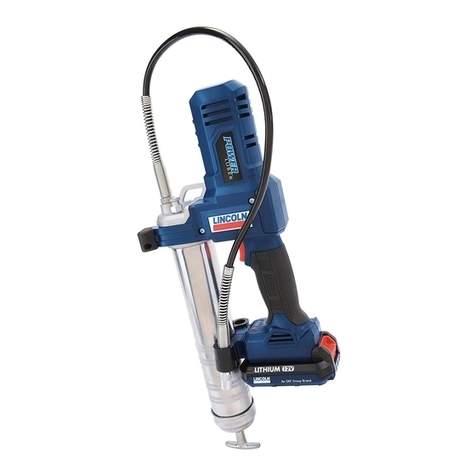
Lincoln
Lincoln SKF A Series Installation and maintenance guide