UE 120 Series User manual

EXPLOSION-PROOF SEALING FITTINGS FOR ELEC-
TRICAL WIRE ENTRY. DO NOT MOUNT UNIT IN
AMBIENT TEMPERATURES LOWER THAN -40°F
(40°C) OR HIGHER THAN 160°F (71°C).
Types J120, J120K, H121, H121K, H122,
H122K, H122P
Mount controls vertically (pressure connection facing
down, See Figure 1a) or horizontally (electrical condui
facing up, See Figure 1b). Either mounting position will
properly orient the venting system. Control may be
surface mounted via the four 1/4” screw holes on the
enclosure or mounting bracket. It can also be mouned
directly to a rigid pipe using the pressure connection.
Types J120K, H121K, H122K Opposed Sensor
Differential Pressure Models 36-39, (S)147(B)-(S)157 (B),
367
“Opposed sensor” differential pressure controls should
be mounted with their pressure connection in the
horizontal position (See Figure 2). This will properly ori-
ent the vent holes on the pressure housing as well as
the 1/4” NPT venting conduit at the bottom of the third
compartment (standardly supplied with plastic plug.
GENERAL
MISUSE OF THIS PRODUCT MAY CAUSE
EXPLOSION AND PERSONAL INJURY.
THESE INSTRUCTIONS MUST BE THOR-
OUGHLY READ AND UNDERSTOOD BEFORE
UNIT IS INSTALLED.
The 120 Series pressure and differential pressure
controls are actuated when a bellows, diaphragm or
piston sensor responds to a pressure change. This
response at a pre-determined set point(s) actuates
a SPDT, dual SPDT or DPDT snap-acting
microswitch(es), which converts the pressure signal
into an electrical signal. Control set point(s) may be
varied by turning the internal adjustment hex (J120
models) or the external knob and pointer(s) (H121,
H122, H122P models) according to the procedures
outlined below.
PROOF PRESSURE LIMITS STATED IN THE
LITERATURE AND ON NAMEPLATES MUST
NEVER BE EXCEEDED, EVEN BY SURGES IN
THE SYSTEM. OCCASIONAL OPERATION OF UNIT
UP TO MAXIMUM PRESSURE IS ACCEPTABLE (E.G.
START-UP, TESTING). CONTINUOUS OPERATION
SHOULD NOT EXCEED THE DESIGNATED OVER
RANGE PRESSURE.
Proof Pressure
The highest pressure to which a sensing element may
be occasionally operated without adversely affecting
setpoint calibration and repeatability.
TOOLS NEEDED
Screwdriver
Adjustable Wrench to 11⁄2"
MOUNTING
ALWAYS HOLD A WRENCH ON THE
PRESSURE HOUSING HEX WHEN MOUNT-
ING UNIT. DO NOT TIGHTEN BY TURNING
ENCLOSURE. THIS WILL DAMAGE SENSOR AND
WEAKEN SOLDER OR WELDED JOINTS.
INSTALL UNITS WHERE SHOCK, VIBRA-
TION AND TEMPERATURE FLUCTUATIONS
ARE MINIMAL. ORIENT UNIT TO PREVENT
MOISTURE FROM ENTERING THE ENCLOSURE.
IT IS IMPERATIVE TO USE PROPERLY RATED
UNITED ELECTRIC
CONTROLS
Installation and Maintenance
Instructions
Please read all instructional literature carefully and thoroughly before starting. Refer to the final page for the listing of
Recommended Practices, Liabilities and Warrantees.
UL listed, CSA Certififed,
FM approved (option M415*)
Class I, Division 1, Groups B*, C, D
Class II, Division 2, Groups E, F, G
Class III
*NOTE: CSA, Class I, Division 1, Group B does not apply
to controls with option code 1530 or M450
**Not available with M450
CENELEC approved (Prefix “Q”)
EN50 014 and EN50 018
EEX d IIC T6
Part I - Installation
Potted Conduit
Connection
Breather Drain
(facing down)
Vent Holes
Figure 1a: H121, H121K, H122,
H122K, H122P
120 Series
Explosion-Proof Pressure
and Differential Pressure
Switches
Potted Conduit Connection
Breather Drain (facing down)
Figure 1b: J120, J120K
1/4” NPT
Vent Hole
Vent Holes

Remove cover and wire control (See Figure 3).
Replacing cover hand tight (a minimum of 5 full
threads engaged) is sufficient to maintain proper
protection. Additional tightening is required to fully
engage cover O-ring and seal enclosure to rain-
tight protection.
TOOLS NEEDED
Screwdriver
5/8” Open End Wrench
5/64” Allen Wrench
SOME MODELS HAVE A TWO-PIECE
ADJUSTABLE PLUNGER. THIS FEATURE
IS CHARACTERIZED BY A 3/16” HEX HEAD
SCREW INSTALLED IN THE PLUNGER. THE
LENGTH OF THIS ASSEMBLY IS ADJUSTED AT
OUR FACTORY AND IS CRITICAL TO THE FUNC-
TION OF THE CONTROL. DURING NORMAL
ADJUSTMENT, THESE COMPONENTS SHOULD
NOT BE DISTURBED. HOWEVER, WHEN
REPLACING THE ELECTRICAL SWITCH, IT MAY
BE NECESSARY TO ADJUST THE PLUNGER
LENGTH IN ORDER TO “RE-GAP” THE SWITCH.
REFER TO INSTRUCTIONS IN PART III -
REPLACEMENTS TO DETERMINE IF REGAPPING
IS NECESSARY.
AFTER COMPLETING ADJUSTMENTS ON
TYPE H121 AND H122 CONTROLS, BE
SURE TO RE-INSTALL ADJUSTMENT COVER. DO
NOT OVER TIGHTEN COVER SCREWS.
For set point adjustment and re-calibration, connect
control to a calibrated pressure source.
Types J120 (All) and J120K Models 455-559
Remove cover. Loosen slotted screw adjustment
lock. Adjust set point by turning 5/8” hex adjustment
screw clockwise (IN) to raise set point, or counter-
clockwise (OUT) to lower set point. Secure
adjustment screw by tightening adjustment lock
(see Figure 4a). Internal reference scales are
provided to show at which portion of the range (high
or low) the control is set. Re-calibration of models
50-55, S50B-S55B, 171-174, 183-189, 190-194,
471-474, 483-489, 490-494, 540-567, 680 & 701-
705 may also require the “re-gapping” of the space
between the top of the plunger and the bottom of
the microswitch. Use the flats on the plunger and
plunger hex screw as reference and follow the
gapping instructions on page 3.
Type J120K
Models 36-39,147-S157B, & 367
Remove front cover and gasket from sensor
assembly located below enclosure by unscrewing 4
slotted screws. Loosen slotted screw adjustment
lock (see Figure 4b). Adjust set point by turning
5/8” hex screw clockwise (IN) to increase setting or
counterclockwise (OUT) to decrease setting.
Adjusting screw should be locked by tightening
adjustment lock.
Controls with Breather Drain (Option M450)
Type J120, J120K Models 455-559
Mount with breather drain facing down and conduit con-
nection facing up (See Figure 1b). The conduit connec-
tion must be “potted” for this type of installation.
Types H121, H122 & H122P, All Models
Mount in vertical position with pressure assembly and
breather drain facing down (See Figure 1a).
WIRING
DISCONNECT ALL SUPPLY CIRCUITS
BEFORE WIRING UNIT. WIRE UNITS
ACCORDING TO NATIONAL AND LOCAL
ELECTRICAL CODES. MAXIMUM RECOMMENDED
WIRE SIZE IS 14 AWG. THE RECOMMENDED
TIGHTENING TORQUE FOR FIELD WIRING TERMI-
NALS IS 7 TO 17 IN-LBS.
ELECTRICAL RATINGS STATED IN LITERA-
TURE AND ON NAMEPLATES MUST NOT BE
EXCEEDED—OVERLOAD ON A SWITCH CAN
CAUSE FAILURE ON THE FIRST CYCLE.
TO PREVENT SEIZURE OF ENCLOSURE
COVER, DO NOT REMOVE LUBRICANT
(PETROLATUM). THREADS SHOULD ALSO
BE FREE OF DIRT, ETC.
Part II - Adjustments
Figure 3
Use 75°C copper
conductors only.
Recommended
tightening torque for
field wiring terminals
is 7-17 in-lbs.
Option 1010,
Type J120
Types H121, J120,
H121K, J120K Types H122,
H122K
HIGH
TERMINAL
BLOCK
HIGH SET
(BACK)
LOW SET
(FRONT)
LOW
TERMINAL
BLOCK
Option 1180,
Type H122P

Types H121, H121K
Adjust set point by turning external knob and pointer
to desired setting on scale. Re-calibration (adjusting
set point after replacing microswitch): Slowly turn
adjustment knob until microswitch transfers.
Compare microswitch transfer point to actual pres-
sure. If they do not agree, loosen set screws on
adjustment knob with allen wrench and align pointer
to indicate actual pressure. Tighten knob set screws.
Types H122, H122K
Individual microswitches may be set together or apart
by up to 100% of range. When not set together, the
front microswitch can not be set higher than the rear
microswitch. Turning external knobs will increase or
decrease each switch setting independently. To
re-calibrate, follow procedure for Types H121 above
for each microswitch.
Controls with Options:
Option 1519, Adjustable Deadband Switch
This microswitch has an integral adjustment wheel.
Turning this wheel raises and lowers the pressure
rise set point. The fall set point remains constant.
Consult factory for additional information.
Type J120, Option 1530, Manual Reset
This microswitch, when actuated, remains actuated
until the pressure drops sufficiently to allow the reset
knob (located on the left side of the control) to be
manually turned to reset the microswitch.
Option M210 Indicator for
Differential Pressure Controls, Span Adjustment
(See Figure 5). To adjust indication for maximum
accuracy at any desired set point, follow steps 1 thru
4 listed below.
1) Remove front window and gasket (four screws)
to gain access to span adjustment.
2) Connect control to calibrated gauges and set
required differential pressure.
3) Using a screw driver, slowly turn the span
adjustment to obtain required indication
(See Figure 4).
4) Remount the front gasket and window.
Types H122P
Individual switches may be set together or apart by
up to 60% of range. The front switch is set by turning
the internal calibrating screw to the right for lower set
point and turning to the left for higher set point.
Figure 4a Figure 4b
J120K: Opposed Sensor,
Models 36-39, 147-157,
S147B, S157B, 367
Adjust Screw
Adjust Lock
When not set together, the front switch can not be set
higher than the rear switch. Turning the external
knob will increase or decrease each switch setting
simultaneously without disturbing their relationship.
NOTE: Spanning adjustment will not effect the mid-
range indication. The adjustment is factory calibrated
and sealed to indicate tampering.
DO NOT FORCE SPAN ADJUSTMENT,
SINCE PERMANENT DEFORMATION OF
THE LINKAGE MECHANISM MAY RESULT.
GAPPING PROCEDURE
TOOLS NEEDED
5/8” Open End Wrench
3/16” Open End Wrench (2)
1) Loosen adjustment lock.
2) Turn 5/8” hex adjustment screw IN, to approxi-
mately mid-range. This puts a load on the
sensor and exposes the plunger flats.
3) Using a 3/16” wrench on the plunger flats and a
3/16” wrench on the plunger hex screw, turn hex
OUT from plunger until microswitch actuates. If
microswitch has already actuated, turn plunger
hex screw IN until microswitch deactuates.
4) Continue per following instructions, depending
on model.
Models 50-55, S50B-S55B, 171-174 and 471-474,
521-525, 531-535, 540-548
Turn hex (IN) an additional 2 flats from this point
(approximately 1/3 turn). This will provide a
9-11 mil gap.
Figure 5
Adjustment Procedure for J120/J120K
Figure 6
Window Plexiglass Span Adjust Screw
Window Mounting
Screw
Plunger Screw
Plunger Flat
Adjust Screw
Option M210

Models 680, 701-705, 356-376, 612, 616
Turn hex (IN) 3 flats from this point (approximately
1/2 turn). This will provide for a 14-16 mil gap.
Models 183-189, 190-194, 483-489, 490-494,
565-567
Turn hex (IN) 1 flat from this point. This will provide a
4-7 mil gap.
Models 270, 274
Turn hex (IN) 5 flats from this point. This will provide
a 24-26 mil gap.
CONTACT FACTORY FOR ASSISTANCE
WITH MODELS NOT SHOWN ABOVE.
TOOLS NEEDED
Screwdrivers, Phillips and Standard
5/8” Open End Wrench
5/64” Allen Wrench
3/16” Open End Wrench (2)
The microswitch is the only factory authorized replace-
ment part. Other components are factory replaceable.
ALWAYS DISCONNECT THE ELECTRICAL
SUPPLY CIRCUITS BEFORE REMOVING
EXPLOSION PROOF COVER.
Single Switch Types J120, J120K, H121, H121K
1) Remove cover; (2) microswitch mounting screws;
microswitch and insulator.
2) Disconnect (3) microswitch wires at microswitch
terminals.
3) Install new microswitch. Wire per PART I.
4) Mount microswitch and insulator inside
enclosure.
5) Check gap per Gapping Procedure.
6) Recalibrate per PART II
Dual Switch Types H122, H122K
MICROSWITCHES ARE DIFFERENT FOR
OPERATION PURPOSES AND MUST BE
INSTALLED ACCORDING TO THE FOLLOW-
ING PROCEDURE.
Characteristics between front and rear microswitch
differ in order to maintain consistent differential.
Replace only with the same microswitch type.
Follow wiring diagrams exactly. Incorrect wiring will
cause controls to malfunction.
1) Remove cover, unscrew (4) terminal block
mounting screws and remove terminal blocks
and insulator.
2) Unhook extension spring from conduit wire guide
and remove wire guide.
3) Remove (2) microswitch mounting screws on low
set microswitch and insulator.
4) Loosen (2) set screws on low set adjusting screw
counter clockwise until switch bracket and actuat-
ing lever assembly can be removed. Be sure that
extension spring is on bracket and washer is on
plunger.
5) Turn low set adjusting screw counterclockwise
until the microswitch bracket and actuating lever
assembly can be removed. Be sure the exten-
sion spring is on bracket and the washer is on
the plunger. Note the position of washer, plunger
and lever fingers.
6) Unscrew (2) bias plate screws and remove bias
plate.
7) Remove (2) microswitch mounting screws,
microswitch and insulator.
8) Disconnect (6) wires at microswitch terminals.
Note the difference between high and low
microswitches.
9) Assemble new microswitches and insulators,
mounting high set microswitch to microswitch
bracket and low microswitch to lever assembly.
10) Replace bias plate with flat edge facing conduit
and slot facing sensor assembly.
11) Position low set microswitch bracket and lever
assembly so that fingers of lever are on top of
washer, and turn low set adjustment screw clock-
wise until lever actuates microswitch.
12) Hook extension spring on to wire guide and
replace insulator and terminal blocks.
13) Tighten allen set screws and install terminal
blocks. Wire per Part I.
14) Re-calibrate per Part II.
15) Replace cover.
Types H122P
1) Remove cover, unscrew and remove terminal block
and insulator, letting terminal block hang.
2) Unscrew terminal block supports and remove (2)
switch mounting screws and washers.
3) Lift out dial, switch bank and actuating lever assembly.
4) Disconnect (6) wires at switch terminals.
5) Assemble new switches and insulators to the switch
bank assembly.
Part III - Replacements

Internal Set Point Adjustment
Types J120, J120K
Dimension A
Models Inches mm NPT
Pressure
126-164 8.50 215,9 1/4
S126B-S164B 8.84 244,5 1/2
270-376 7.81 198,4 1/4
450, 452 9.69 246,1 1/4
451, 453, 454 8.94 227,0 1/4
550, 552 9.75 247,7 1/4
551, 553-555 9.31 236,5 1/4
612, 614 8.75 222,3 1/4
701-705 8.31 211,1 1/4
Differential Pressure
147-157 8.44 214,4 1/4
S147B-S157B 8.44 214,4 1/2
456-559 9.31 236,5 1/4
External Set Point
Adjustment
Types H121, H122,
H121K, H122K, H122P
Dimensions
J120 Models 50-55,
S50B-S55B
Models 126-164 Models S126B-
S164B
Models 171-174,
471-474
Models 188-194,
488-494
Models 183-186,
483-486
Pressure
Mounting Bracket
M449, Models 520-535
50-55, 1/4 NPT
S50B-S55B,1/2NPT
Dimension A
Models Inches mm NPT
Pressure
126-164 8.50 215,9 1/4
S126B-S164B 8.84 244,5 1/2
270-376 7.81 198,4 1/4
450, 452 9.69 246,1 1/4
451, 453, 454 8.94 227,0 1/4
520-525 9.06 230,2 1/2
530-535 8.56 217,4 1/2
550, 552 9.75 247,7 1/4
551, 553-555 9.31 236,5 1/4
560-564 7.25 181.4 2” Sanitary
565-567 7.25 181.4 1 1/2” Sanitary
612, 614 8.75 222,3 1/4
701-705 8.31 211,1 1/4
Differential Pressure
147-157 8.44 214,4 1/4
S147B-S157B 8.44 214,4 1/2
456-559 9.31 236,5 1/4
540-543 9.20 232,7 1/8
544-548 9.25 234,4 1/8
4-1/4
MIN. R. (TYP)
6-1/4
1”
MIN. R. (TYP)
2-7/16 1/2 RAD. TYP
.
3-9/16
G-1/62
1-11/38
25/64
45/64
4-13/32
3-6/8
3”
1-1/4 2-1/2 2-3/4 35-1/4
7/32 DIA (2) HOLES
9/32 DIA (12) HOLES

180 Dexter Ave., P.O. Box 9143, Watertown, MA 02471-9143 USA
Telephone: 617 926-1000 Fax : 617 926-2568
http://www.ueonline.com
EMCO10M1200
Models 612-616, 701-705
J120 Models
270-376, 680
H121 Models
270-376
Models 520-525 Models 530-535
Models 450-454,
550-555
fferential Pressure
J120K Models 367 Models 455-457, 559
J120K Models 36-39
Models 147-157 Models S147B-S157B
Models 560-564
RECOMMENDED PRACTICES AND WARNINGS
United Electric Controls Company recommends careful consideration
of the following factors when specifying and installing UE pressure
and temperature units. Before installing a unit, the Installation and
Maintenance instructions provided with unit must be read and
understood.
• To avoid damaging unit, proof pressure and max temperature
limits stated in literature and on nameplates must never be exceeded,
even by surges in the system. Operation of the unit up to proof pres-
sure or max temperature is acceptable on a limited basis (i.e.start-up,
testing) but continuous operation must be restricted to the designated
adjustable range. Excessive cycling at proof pressure or maximum
temperature limits could reduce sensor life.
• A back-up unit is necessary for applications where damage
to a primary unit could endanger life, limb or property. A high or low
limit switch is necessary for applications where dangerous runaway
condition could result.
• The adjustable range must be selected so that incorrect,
inadvertent or malicious setting at any range point can not result in an
unsafe system condition.
• Install unit where shock, vibration and ambient temperature
fluctuations will not damage unit or affect operation. Orient unit so
that moisture does not enter the enclosure via the electrical
connection.
• Unit must not be altered or modified after shipment. Consult UE if
modification is necessary.
• Monitor operation to observe warning signs of possible damage
to unit, such as drift in set point. Check unit immediately.
• Preventative maintenance and periodic testing is necessary for
critical applications where damage could endanger property or
personnel.
• For all applications, a factory set unit should be tested before use.
• Electrical ratings stated in literature and on nameplate must not
be exceeded. Overload on a switch can cause damage, even on the
first cycle. Wire unit according to local and national electrical codes,
using wire size recommended in installation sheet.
• Use only factory authorized replacement parts and procedures.
• Do not mount unit in ambient temp. exceeding published limits.
• For remote mounted temperature units, capillary lengths beyond
10 feet can increase chance of error, and may require re-calibration of
set point and indication.
LIMITED WARRANTY
UE warrants that the product thereby purchased is, upon delivery, free
from defects in material and workmanship and that any such product
which is found to be defective in such workmanship or material will be
repaired or replaced by UE (F.O.B. UE); provided, however, that this
warranty applies only to equipment found to be so defective within a
period of 12 months after installation by buyer but not to exceed 18
months after delivery by the seller. Except for the limited warranty of
repair and replacement stated above, UE disclaims all warranties whatsoev-
er with respect to the product, including all implied warranties of mer-
chantability or fitness for any
particular purpose.
LIABILITY LIMITATION
The sole and exclusive remedy of buyer for any liability or seller
for any claim, including incurred in connection with (I) breach of any
warranty whatsoever expressed or implied, (II) a breach of contract,
(III) a negligent act or acts (or negligent failure to act) committed by
seller, or (IV) an act for which strict liability will be imputed to seller,
is limited to the limited warranty or repair and replacement stated
herein. In no event shall the seller be liable for any special,
indirect, consequential or other damages of a like general nature, including,
without limitation, loss of profits or production, or loss or expenses of any
nature incurred by any third party.
Models 540-543 Models 544-548
UNITED ELECTRIC
CONTROLS
Models 565-567
This manual suits for next models
7
Table of contents
Other UE Switch manuals
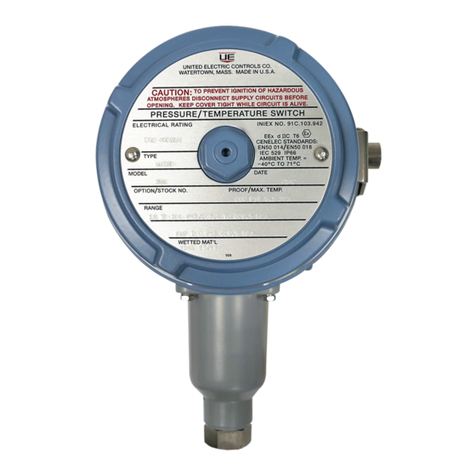
UE
UE 120 Series User manual
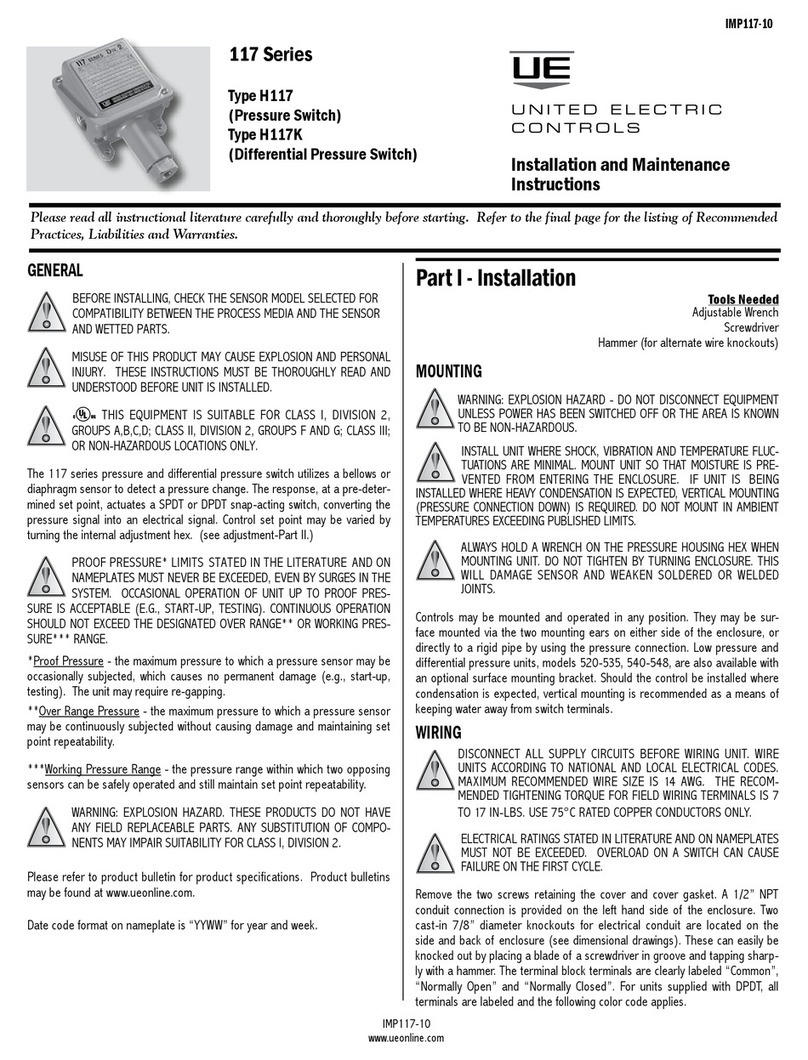
UE
UE 117 Series User manual
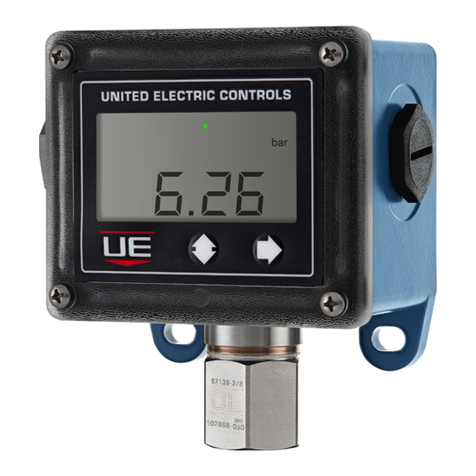
UE
UE ONE Series User manual
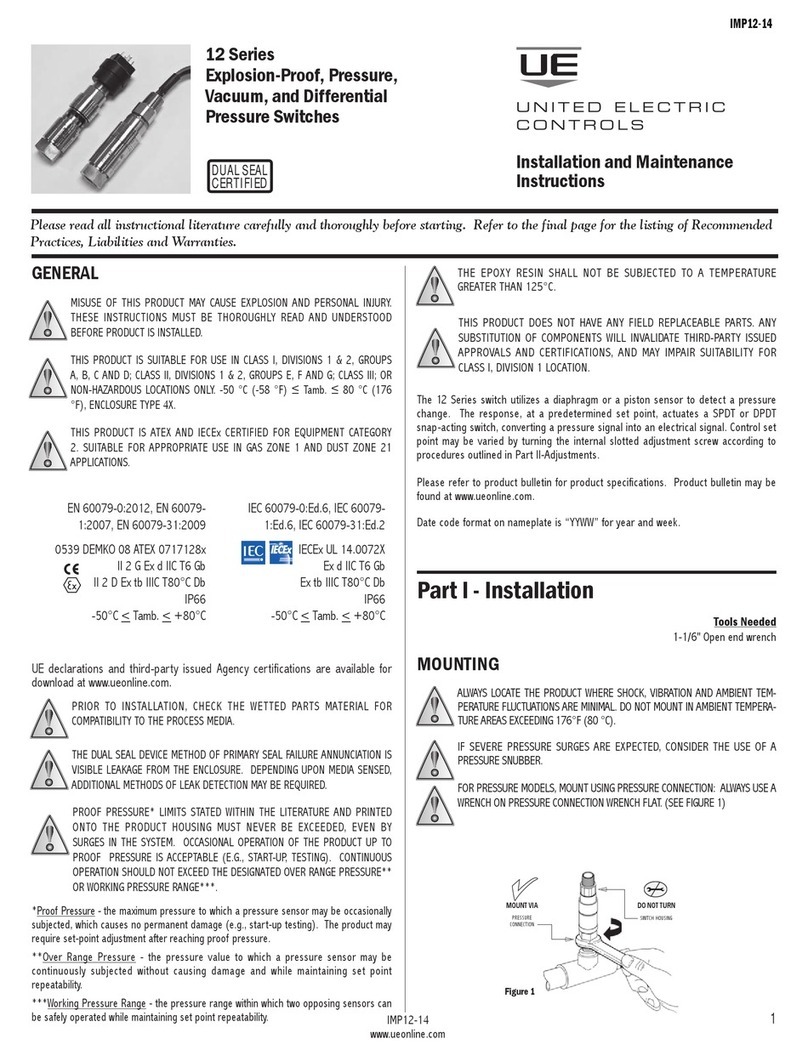
UE
UE 12 Series User manual
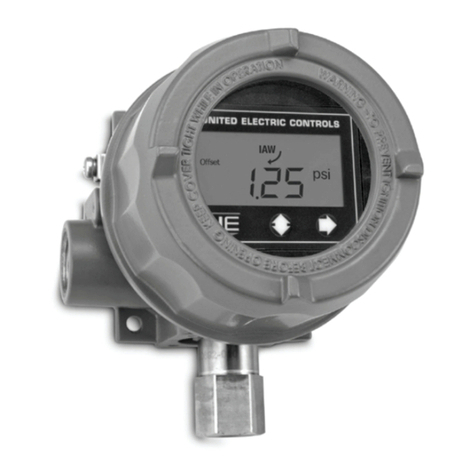
UE
UE ONE Series User manual
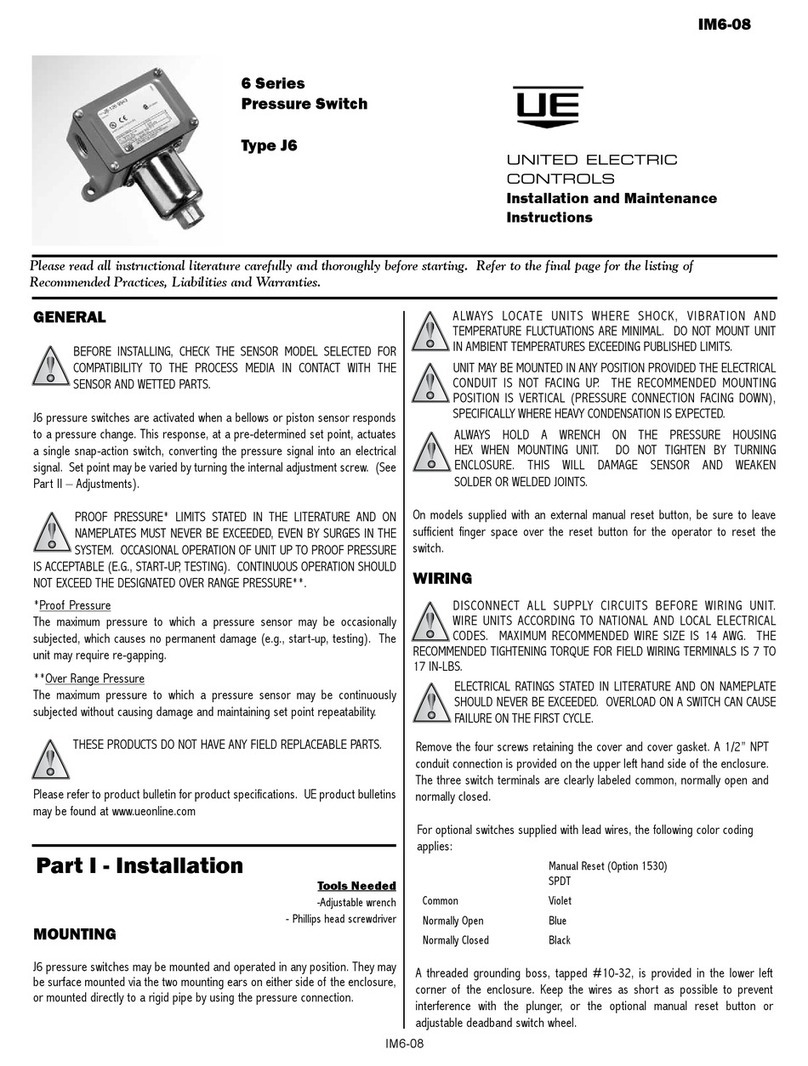
UE
UE 6 Series User manual
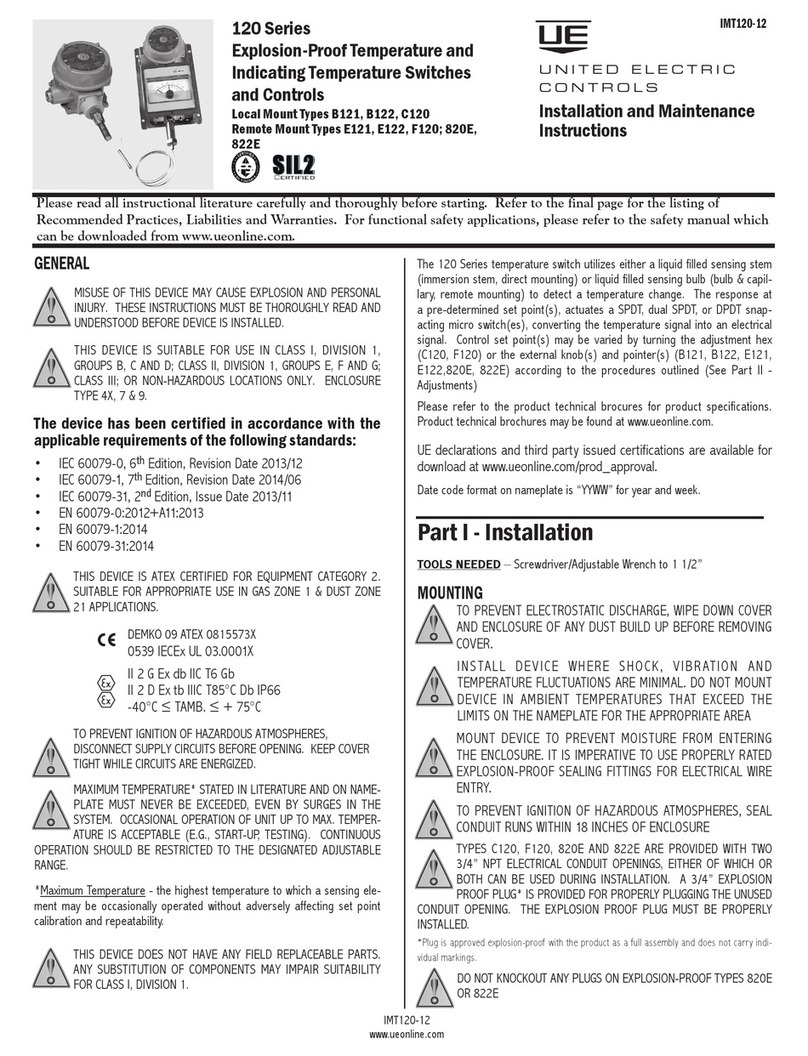
UE
UE B121 User manual
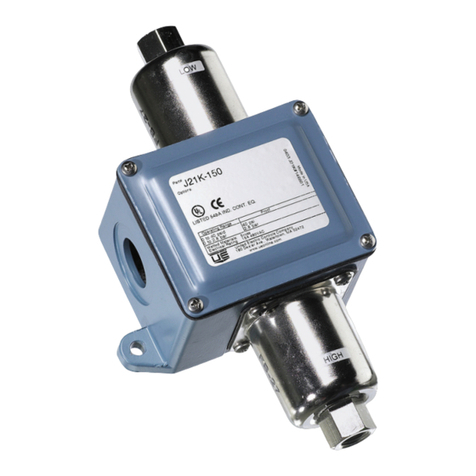
UE
UE J21K User manual
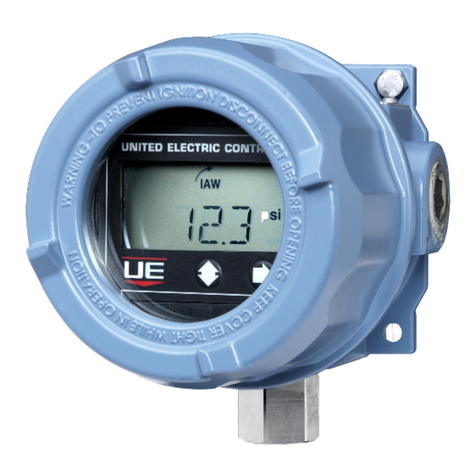
UE
UE Field Safety System One Series User manual
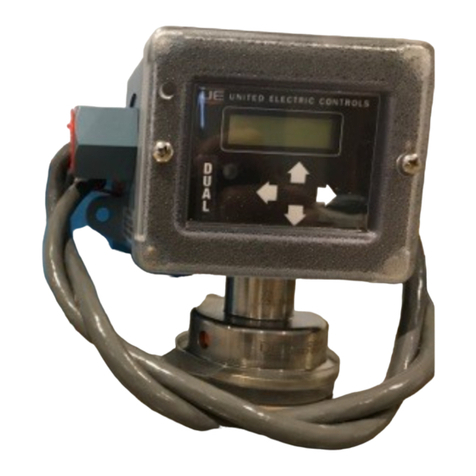
UE
UE ONE Series Installation and operating instructions