VAF instruments 667 Programming manual

Technical Manual
Instructions for installation, operation and maintenance
Publication nr TIB-667-GB-1121
Supersedes TIB-667-GB-0918
667
PEM4 +SPU3 SYSTEM
For T-Sense®, TT-Sense®and PT2 Flowmeters

1
TABLE OF CONTENTS
1. PREFACE......................................................................................3
1.1 General........................................................................................................3
1.2 Symbols.......................................................................................................3
1.3 Copyright......................................................................................................3
2. SYSTEM DESCRIPTION...............................................................4
2.1 PEM4 Propulsion Efficiency Monitoring System ..........................................4
2.2 System security............................................................................................4
3. TECHNICAL SPECIFICATIONS ....................................................5
4. SAFETY INSTRUCTIONS..............................................................7
5. UNPACKING..................................................................................7
6. INSTALLATION AND FIRST USE..................................................7
6.1 Record PEM4 + SPU3 system data.............................................................8
6.2 Installation diagrams of the PEM4 + SPU3 system......................................9
6.3 Installation instruction of the PEM4 + SPU3 system..................................10
6.4 Configuration and connection of the SPU3................................................11
6.5 Cable specifications...................................................................................12
6.6 Modbus input for T-Sense®and TT-Sense®...............................................13
6.7 Analogue input for torque-, speed- and power...........................................13
6.8 Analogue or Modbus input for shaft generator...........................................14
6.9 Analogue or Modbus input for auxiliary power...........................................15
6.10 Analogue input for ViscoSense®3D –Density, temp. and Viscosity........15
6.11 Modbus output to external system ..........................................................16
6.12 Modbus connections...............................................................................17
7. OPERATING PRINCIPLES..........................................................18
7.1 General......................................................................................................18
7.2 Displayed parameter and engineering units...............................................18
7.3 Explanation of parameters.........................................................................19
7.3.1 Shaft torque ......................................................................................19
7.3.2 Shaft speed.......................................................................................19
7.3.3 Shaft power.......................................................................................19
7.3.4 Shaft thrust (option)...........................................................................19
7.3.5 Shaft generator (option) ....................................................................19
7.3.6 Fuel oil consumption.........................................................................19
7.3.7 Fuel oil temperature..........................................................................19
7.3.8 Speed over ground (SOG) via NMEA0183 .......................................20
7.3.9 Speed through water (STW) via NMEA0183.....................................20
7.3.10 Speed through water (STW) via pulse signal from speed log ...........20
7.3.11 Density..............................................................................................20
7.3.12 Draft..................................................................................................20
7.3.13 Inclino................................................................................................20
7.4 How to operate...........................................................................................21
7.5 Explanation of the menus...........................................................................22
7.5.1 Operating menus...............................................................................22
7.5.2 Settings menu Users.........................................................................24
7.5.3 Settings menu Advanced..................................................................24
7.6 Explanation of the menus...........................................................................25
7.6.1 Home menu ......................................................................................25
7.6.2 Engine menu.....................................................................................26
7.6.3 Propulsion menu...............................................................................31

2
7.6.4 Alarms menu.....................................................................................34
7.6.5 Signals (raw) menu...........................................................................35
7.6.6 Settings menu...................................................................................36
7.7 Method of calculations ...............................................................................39
8. MAINTENANCE...........................................................................44
9. REPAIR........................................................................................44
10. TAKE OUT OF SERVICE.........................................................44
11. REMOVAL AND STORAGE OF EQUIPMENT.........................44
12. MALFUNCTION AND SEND FOR REPAIR..............................44
13. ENVIRONMENT.......................................................................44
14. DISPOSAL...............................................................................44
15. TROUBLE SHOOTING ............................................................45
16. EMC CLASSIFICATIONS OF THE PEM4 + SPU3 SYSTEM ...45
16.1 Certificates..............................................................................................45
17. DRAWINGS .............................................................................46
18. ABBREVIATIONS ....................................................................52
19. SPARE PARTS........................................................................52
20. WARRANTY CONDITIONS......................................................53

3
1. PREFACE
1.1 GENERAL
The PEM4 Propulsion Efficiency Monitoring system is a microprocessor based instrument for use with
the T-Sense®Optical Torque Measuring System and TT-Sense®Optical Thrust and Torque Measuring
System. The T-Sense®is providing torque, shaft speed and power as input for the PEM4 system. The
TT-Sense®additionally provides thrust measurements as input.
The PEM4 system is supplied with a robust SPU3 Signal Processing Unit, which can be connected to a
large number of extra inputs like flowmeters, GPS, speed log, or one additional T-Sense® or TT-Sense®
in case of twin screw vessels.
This completely unique and compact total solution can be used for simple to very complicated
configurations.
To ensure safe and correct installation and operation, read this manual completely before
installing the equipment and starting operations.
The (micro) SD card should not be exposed to computer viruses, since this could
contaminate the (micro) SD card. Contamination could disturb good working of the system.
For any additional information contact:
VAF Instruments B.V.
Tel.
+31 78 618 3100
Vierlinghstraat 24, 3316 EL Dordrecht
Fax
+31 78 617 7068
P.O. Box 40, NL-3300 AA Dordrecht
E-mail
The Netherlands
Internet
www.vaf.nl
Or your local authorized VAF dealer.
Their addresses can be found on www.vaf.nl
1.2 SYMBOLS
The following symbols are used to call attention to specific types of information.
A warning to use caution! In some instances, personal injury or damage to the instrument
or control system may result if these instructions are not followed properly.
An explanation or information of interest.
1.3 COPYRIGHT
This Technical Manual is copyrighted with all rights reserved.
While every precaution has been taken in the preparation of this manual, no responsibility for errors or
omissions is assumed. Neither is any liability assumed for damages resulting from the use of the
information contained herein. Specifications can be changed without notice.

4
2. SYSTEM DESCRIPTION
2.1 PEM4 Propulsion Efficiency Monitoring System
The PEM4 system is a modular propulsion efficiency system. This manual describes the combination of
the PEM4 with the SPU3 (Signal Processing Unit). The PEM4 stand alone system is able to calculate
torque, speed and poweroutput data. The PEM4 stand alone is describedin a separate technicalmanual,
(TIB-669 T-Sense®and PEM4 stand alone). The PEM4 system in combination with the SPU3 can
manage a maximum of 12 Flowmeter inputs in with PT100 temperature inputs related to a maximum of
8 consumers. Furthermore a maximum of 6 ViscoSense®3D inputs, a speed log pulse, GPS NMEA
signal, draft meter and inclino meter can be added as input to the system.
The SPU3 converts all these input signals to one RJ45 Ethernet signal for monitoring purposes through
a PEM4 touch screen or using the IVY®Propulsion Performance Management system.
A RS485 Modbus signal is available for connectionan external system like Alarm and Monitoring System
(AMS) or to connect a separate PC running the optional SPU3 datalogger software.
Functions, which can be performed with the PEM4 + SPU3 system are:
•Measurement and display of the torque, thrust, shaft speed and power.
•Calculation of the average shaft power, shaft speed and torque during the last 1, 4 and 24 hours.
•Calculation of the total energy, total revolutions and total CO2emissions including reset.
•Calculation of the fuel consumption in kg per nautical mile, fuel consumption in kg per hour, fuel
consumption in gram per kWh (Specific Fuel Oil Consumption - SFOC), average fuel consumption per
nautical mile, fuel temperature compensation and calculation of the total mass per fuel type per
consumer including reset.
•Calculation of thrust, thrust power quotient, when a TT-Sense®sensor is installed.
•Displaying of parameters, engine load diagram and power/speed diagram.
•Above mentioned calculations for twin screw vessels when an additional T-Sense®or TT-Sense®
system is installed.
The SPU3 can be installed in the vicinity of the flow meter(s) and/or booster unit or in the engine control
room (ECR). The PEM4 touch screen can be installed in a control cabinet or control panel in the ECR
and/or on the bridge.
2.2 SYSTEM SECURITY
Besides checking the status of the torque measurement system and/or flowmeters the PEM4 + SPU3
system also checks itself continuously for program and configuration data integrity, normal program flow
and power supply conditions. All alarm messages will be logged in a dedicated alarm screen.

5
3. TECHNICAL SPECIFICATIONS
SPU3
Drawing 0815-1120 (section 17)
Supply voltage
115 - 230 VAC
Power consumption
30 W max.
Protection class
IP65
Net weight
Approx. 10 kg
Operating temperature
Lower than 55⁰C
Dimensions
660 x 300 x 165 mm (w x h x d)
CPU
Beagle Bone, Sitara AM3359AZCZ100, 1GHz, SDRAM 512MB
DDR3L 800 MHZ, On board flash 2GB, 8bit embedded MMC
Flowmeter pulse inputs
(backplanes)
Number of pulse inputs
12 flowmeters (max. 8 engines/boilers)
Input type
VAF Instruments PT2 sensor or Namur
Max. freq. pulse input
1000 Hz
Threshold voltage
3 V
Maximum pulse voltage
8,2 V
Flowmeter temperature inputs
(backplanes)
Number of temp. inputs
12
Input type
3 wire PT100
Range
0⁰C to 200⁰C
Accuracy
± 1⁰C
Update time
1 Hz
Analogue inputs
(backplanes)
Max. 9x optional analogue inputs
(3 analogue modules with 3 analogue inputs each)
Range per analogue input 4-20mA each. Ri = 100Ω
Used for:
•Max. 2 shaft generators
(1 analogue input each)
•Max. 2 torque meters e.g. VAF-Palco - Torque/speed/power
(3 analogue inputs each)
•Max. 6 auxiliary power - Total auxiliary power
(1 analogue input each)
•Max.6ViscoSense®3D-Density, Temperature andViscosense
(3 analogue inputs each)
•Max. 4 draft meters –Front, Middle SB, Middle PS, Back
(1 analogue input per meter)
•Max. 1 Inclino meter –Pitch, Roll, Yaw
(1 analogue input per signal)
Signal input
(J1) T1 or T1+T2
Input signal from T-Sense®,TT-Sense®sensors or Auxiliary Engines.
RS485 (2-wire), Baud rate: 19200, Data bits: 8, Parity: none, Stop bits:
2,
Flow control: None
(max1200m cable length)
Signal input
(J2) T2 or Aux1
Input signal from T-Sense®, TT-Sense®sensors or Auxiliary Engines
RS485 (2-wire), Baud rate: 19200, Data bits: 8, Parity: none, Stop bits:
2,
Flow control: None
(max1200m cable length)
Modbus output
(J3)
Modbus connection
For data transfer to an external system like AMS or for connection to a
separate PC running (optional) SPU3 data logger software.
RS485 (2-wire) Baud rate: 57600, Data bits: 8, Parity: none, Stop bits:
1,
Flow control: None,Function code 3(Holding Registers), Modbus slave
address 1
(max1200m cable length)

6
NMEA input
(J4)
NMEA 0183, used for GPS*
PEM4 is reading following strings:
•$--VTG sentence (“speed over ground” - SOG)
•$--VBW sentence (“longitudinal water speed” – STW)
RS422 (2-wire), Baud rate: 4800, Data bits: 8, Parity: none, Stop bits:
1,
Flow control: None (max1200m cable length)
*systems in combination with IVY®are able to read more
information available through NMEA
Ship’s speed log input
(J6)
Pulse input for speed log. 1-999p/NM
Ethernet output
(J10)
One RJ45 Ethernet connection to the PEM4 touch screen, the IVY®
Propulsion Performance Management system, or to a PC/network on
board.
(max100m cable length)
Optional a RJ45 Ethernet switch for connecting e.g. a second PEM4
touch screen.
Figure 1 SPU3 Signal Processing Unit
PEM4.7 Touch Screen
Drawing 0815-1023 (section 17)
Supply voltage
115-230 VAC to power supply unit
Dimensions
235 x 150 x 44 (w x h x d)
Cut out
217,6 x 128,6 mm (w x h)
Cut out depth
38 mm
Front panel thickness
6 mm
Connections
RJ45 Ethernet connection on the back-bottom side of the panel
Temperature range
-20ºC up to +60ºC
Display
Color TFT LCD, PCAP
Touch screen 7,0” (1024 x 600 dots) with adjustable LED backlight
Net weight
1,3 kg

7
PEM4.8 Touch Screen
Drawing 0815-1025 (section 17)
Supply voltage
115-230 VAC to power supply unit
Dimensions
218,16 x 162,67 x 46,5 mm (w x h x d)
Cut out
167 x 116 mm (w x h)
Cut out depth
32 mm
Front panel thickness
17 mm
Connections
RJ45 Ethernet connection on the back-bottom side of the panel
Temperature range
-10ºC up to +50ºC
Display
Color TFT LCD, Touch screen 8” (1024 x 600 dots) with
adjustable backlight
Net weight
940 g
PEM4.10 Touch Screen
Drawing 0815-1026 (section 17)
Supply voltage
115-230 VAC to power supply unit
Dimensions
260 x 178 x 44 mm (w x h x d)
Cut out
246,5 x 164,5 mm (w x h)
Cut out depth
46 mm
Front panel thickness
3,20 mm
Connections
RJ45 Ethernet connection on the back-bottom side of the panel
Temperature range
0ºC up to +50ºC
Display
Color TFT LCD, Touch screen 10.1” (1280 x 800 dots) with
night view
Net weight
2 kg
4. SAFETY INSTRUCTIONS
There are no special safety instructions for the equipment.
5. UNPACKING
Let the equipment acclimatize inside the closed box for at least one hour at the location where the system
will be installed.
When the equipment is taken out of the box, please leave the special protection supplied with the
equipment as long as possible in place to avoid any damage.
The special protection should be stored for the unlikely event the equipment has to be sent for repair.
Dispose of the packing material should be done according to the laws of the country where the equipment
is installed, or according to the rules that are applicable on the vessel.
•Be careful when unpacking the electronic equipment. The content is fragile.
•Do not press on the PEM4 touch screen.
•Be careful not to damage any of the connectors, control modules or wiring.
6. INSTALLATION AND FIRST USE
The PEM4 + SPU3 system will be delivered with the software and correct data settings installed. First
connect all the inputs and outputs to the components. Connect for the PEM4.10 version a grounding
cable to the grounding screw on the backside of the screen, see section 17 drawing 0815-1126.
The power supply wires should be connected at last.
Note: There is an ON/OFF switch on PEM4 touch screen. When the power switch is switched ON the
screen will turn on.

8
Check if the inputs are connected correctly through menu <ALARMS> <Signals(raw)>.
In case of any errors the connection(s) or connected equipment(s) should be checked and corrected.
6.1 RECORD PEM4 + SPU3 SYSTEM DATA
This information is required when contact the supplier for any reason.
SPU3 nameplate:
Type No.
SPU3
Serial No.
Supply voltage
V
Frequency
Hz
Var.No.
Power Cons.
W
PEM4 system info:
Software
Version
Serialnumber
Hullnumber
Delivery date

9
6.2 INSTALLATION DIAGRAMS OF THE PEM4 + SPU3 SYSTEM
The PEM4 + SPU3 system, consisting of SPU3 signal processing unit and PEM4 touch screen, can be
connected to the T-Sense®or TT-Sense®stator control box as shown in below figures.
Figure 2 –Example of PEM4.7 + SPU3 system including T-Sense®torque sensor and 2 Touch Screens
Figure 3 –Example of PEM4.8 + SPU3 system including T-Sense®torque sensor and 2 Touch Screens
Figure 4 –Example of PEM4.10 + SPU3 system including T-Sense®torque sensor and 2 Touch Screens

10
6.3 INSTALLATION INSTRUCTION OF THE PEM4 + SPU3 SYSTEM
The propulsion efficiency monitoring system consists of a SPU3 and a PEM4 touch screen, T-Sense®
or TT-Sense®sensors, flowmeters, speed log/GPS/NMEA input and draft/inclino meters will be
connected to the SPU3. The SPU3 will perform all calculations and data processing to the PEM4
touch screen.
1. Always install the SPU3 with cable glands facing downwards. Do not take electronics out of the
cabinet.
Figure 5 –SPU3 positioning
2. Install the SPU3 in the engine room (ER), engine control room (ECR) or near to the HFO booster
units, but as much as possible free from moisture, free from large fluctuations of temperature and
particularly free from vibration and shock. Also influences such as large magnetic fields must be
avoided. Ambient temperature should under all circumstances be lower than 55°C. External
dimensions drawings of the SPU3 can be found in section 17.
3. Connect the RS485 Modbus output from the stator control box of one T-/TT-Sense®sensor to the
SPU3 in accordance with drawing 0815-2019 in section 17.
When available, the second T-/TT-Sense®sensor cable needs to be connected as well.
4. Connect the signal outputs of the flow meters, speed log and/or shaft generator to the SPU3 in
accordance with drawing 0815-2019 in section 17.
Cable shields of the flowmeter cables should always be connected to the SPU3 side only.
5. Connect the RJ45 Ethernet output from the SPU3 to the PEM4 touch screen in accordance with
drawing 0815-2019 in section 17.
6. Ensure that all relevant signal cables are properly connected and grounded.
7. Connect the power supply to the SPU3 and PEM4 touch screen(s) in accordance with drawing 0815-
2019 in section 17.
8. Check if the output data is available on the touch screen(s) through menu <ALARMS> <Signals(raw)>.
If any applicable output data is not available on the touch screen a pop-up alarm screen describing
the failure(s) will show up.
Important notes
•Never connect cable shields at both ends to ground, but at one end only, to avoid
earth loops.
•Avoid interference on the signal cables by installing them as far as possible away
from electric power cables.
•Ensure that the ambient temperature at the SPU3 never exceeds 55⁰C.

11
6.4 CONFIGURATION AND CONNECTION OF THE SPU3
The propulsion efficiency monitoring system is a modular system. Every system is specifically build and
programmed.
The table “Flowmeter numbers, description and position” at the inside of the SPU3 cabinet, provides
information regarding flow meter (TAG) numbers, configuration of the flow meters, speed log or GPS at
the SPU3. The number of backplanes differs per SPU3 configuration.
Figure 6 –Example table “Flowmeter numbers, description and position”
Figure 7 –SPU3 Cabinet layout
PT2 Flowmeters should be connected to the SPU3 according drawing/table 0815-2019 in
section 17.
Processor module
Backplanes (max. 4pcs) with
ABCD-input modules.
Power supply
Network switch (optional)

12
6.5 CABLE SPECIFICATIONS
Specification of the input, output and power supply cables used for connecting the PEM4 + SPU3 system.
Figure 8 –Specification of input/output cables at Control box, SPU3 and PEM 4 touch screen(s)
1) Number of flowmeters can add up to max. 12 for 8 engines or consumers
2) Optional
3) When used with VAF Datalogger, please refer to SIG 918 for PC settings and connections
4) Pulse and PT100 signals should not be joined within 1 pair
Cable specification
IC-01
Integrated antenna cable 5m
VAF supply
IC-02
Integrated stator cable 5m
VAF supply
IC-03
Power supply (115 / 230 VAC) cable
3 x 1,5 mm2
IC-04
Modbus connection cable
1 x 2 x 0,50 mm2, twisted pair, braid shielded
IC-05
Flowmeter cable for pulse and PT100
(3m integrated),
2 x 3 x 0,50 mm2or 4 x 2 x 0,50 mm2, individual screened twisted pair,
braid shielded 4)
IC-06
Connection cable GPS or speed log
1 x 2 x 0,50 mm2twisted pair, braid shielded
IC-07
Connection cable shaftgen. 4-20mA input
1 x 2 x 0,50 mm2twisted pair, braid shielded
IC-08
Ethernet cable
CAT5e braid shielded, RJ45 plug
IC-09
From Power Supply Unit 24 VDC cable 5)
2 x 0,50 mm2
All screens to be connected under the cable gland on the SPU3 side only.
Cable glands are M20 for cable dia. 7-12 mm.
Note: The maximum number of analogue inputs is 9 inputs, depending on the system
configuration.

13
6.6 MODBUS INPUT FOR T-SENSE®AND TT-SENSE®
The T-Sense®or TT-Sense®signal will be connected to the J1 Modbus input connection (Channel 1).
When a second T-Sense®or TT-Sense®is installed the signal will be connected to the J2 Modbus input
connection (Channel 2).
Both the J1 and J2 Modbus input connections (resp. channel 1 and 2) can also be used for connection
of Auxiliary Engines (AE) input. See section 6.9.
In such situation two, or more, Modbus input signals can be connected to the J1 and/or J2 Modbus input
connection.
Therefore the inputs will be set on “Channel 1” or “Channel 2”, with each input a different slave address
equal to the slave address of the connected device.
The T-Sense®or TT-Sense®stator box slave address is factory set by VAF Instruments.
6.7 ANALOGUE INPUT FOR TORQUE-, SPEED- AND POWER
It is possible to connect a torque-, speed- and power-meter to the SPU3 system. This torque-, speed and
power-meter needs to be equipped with analogue 4–20mA outputs.
The analogue 4–20mA signals can be connected to the SPU3 (Backplane-X) representing the
torque-, speed- and power-signal.
Analog input
Signal
Type of input
signal
Terminal number on SPU3
Backplane-`X`
Shaft torque signal
4–20mA - active
Terminal nr. X1 and X2
Shaft speed signal
4–20mA - active
Terminal nr. X3 and X4
Shaft power signal
4–20mA - active
Terminal nr. X5 and X6
The number of Backplane-“X” might differ per configuration, depending on the total system.
Please refer to the connection diagram what comes with the project.
Make sure that the torque meter settings in the SPU3 system itself are set correctly. You are able to
adjust these torque meter settings in the “Settings menu”(advanced level only).
When passive analogue outputs have to be connected to the SPU3 system please contact VAF
Instruments.

14
6.8 ANALOGUE OR MODBUS INPUT FOR SHAFT GENERATOR
The PEM4 + SPU3 system is able to calculate the total power generated by the main engine(s) when
shaft generators are incorporated in the vessel’s propulsion system. When the generators are positioned
at the propeller shaft line (inline or tunnel gear type) or connected to the gearbox as a Power Take Off
(PTO) the PEM4 + SPU3 system can add up both propulsion power and the measured generator power
in order to calculate the correct SFOC values per engine.
Please be aware that the efficiency of the generators themselves is decreasing the overall
SFOC value by a certain percentage.
A maximum of 2 input signals (4–20mA or Modbus) can be connected to the SPU3 representing the shaft
generator power level(s).
Analog input
Signal
Type of input
signal
Terminal number on SPU3
Backplane-‘X’
Shaft generator one
4–20mA - active
Terminal nr. X1 and X2
Shaft generators two
4–20mA - active
Terminal nr. X1 and X2 + X3 and X4
Shaft generator one
4–20mA - passive
Terminal nr. X5 and X6
The number of Backplane-“X” might differ per PEM4 configuration, depending on the total
system. Please refer to the connection diagram what comes with the project.
Modbus input
Signal
Type of input
signal
Terminal number on SPU3
Shaft generator one
Modbus
Terminal nr. J1 (see section 6.12)
Shaft generators two
Modbus
Terminal nr. J2 (see section 6.12)
Make sure that the shaft generator settings in the PEM4 + SPU3 system itself are set correctly. You are
able to adjust these shaft generator settings in the PEM4 Settings menu (advanced user only).
When 2 passive shaft generator outputs have to be connected to the PEM4 + SPU3 system please
contact VAF Instruments.

15
6.9 ANALOGUE OR MODBUS INPUT FOR AUXILIARY POWER
When Auxiliary Engines (AE) are monitored by VAF PT2 flow meters, it is possible to measure the
Specific Fuel Oil Consumption (SFOC) of the AE driving the generators.
In order to measure the electric power supplied by the generators to the boardnet, 4–20mA signals or
Modbus signals representing the power level of the generators can be connected to an input inside of
the SPU3. A maximum of 6 AE’s can be connected.
A maximum of6 input signals (4–20mA or Modbus) can be connected to the SPU3 representing the AE’s
power level.
Analog input
Signal
Type of input
signal
Terminal number on SPU3
Backplane-‘X’
Auxiliary power 1
4–20mA - active
Terminal nr. X1 and X2
Auxiliary power 2
4–20mA - active
Terminal nr. X3 and X4
Auxiliary power …
4–20mA - active
Terminal nr. X… and X…
The number of Backplane-“X” might differ per PEM4 configuration, depending on the total
system. Please refer to the connection diagram what comes with the project.
Modbus input
Signal
Type of input
signal
Terminal number on SPU3
Auxiliary power 1
Modbus
Terminal nr. J1 (see section 6.12)
Auxiliary power 2
Modbus
Terminal nr. J2 (see section 6.12)
Auxiliary power …
Modbus
Terminal nr. J1 (see section 6.12)
6.10 ANALOGUE INPUT FOR VISCOSENSE®3D –DENSITY, TEMP. AND VISCOSITY
A ViscoSense®3D can be connected to the SPU3. Therefore the 4–20mA output signals of the
ViscoSense®3D interface box, density, temperature and viscosity, will be connected to the analogue input
inside of the SPU3.
Using the density and temperature input the mass flow within the fuel system can be calculated and be
shown on the PEM4 screen.
Because the ViscoSense®3D measurement and the volume flow measurement possibly have different
temperatures, both measurements (mass and volume) will be calculated at reference temperature and
accordingly be multiplied with each other to get the mass flow.
Analog input
Signal
Type of input
signal
Terminal number on SPU3
Backplane-`X`
Density
4–20mA - active
Terminal nr. X1 and X2
Temperature
4–20mA - active
Terminal nr. X3 and X4
Viscosity
4–20mA - active
Terminal nr. X5 and X6
The number of Backplane-“X” might differ per PEM4 configuration, depending on the total
system. Please refer to the connection diagram what comes with the project.

16
6.11 MODBUS OUTPUT TO EXTERNAL SYSTEM
If applicable the PEM4 + SPU3 system can be connected to an external system like an Alarm and
Monitoring System (AMS) or SPU3 Datalogger software through the J3 Modbus slave output, which is at
the processor module in the SPU3 cabinet.
COM-port settings for reading out the J3 Modbus signal at SPU3
Communication protocol
Modbus RTU
Serial interface
RS485 (2-wire)
Baud rate
57600
Data bits
8
Parity
None
Stop bits
1
Flow control
None
Function code
3 (Holding registers)
Modbus slave address
1
The Modbus output data is made available at two 16 bits integers which will have to be converted to 32
bits float according IEEE754. IEEE754 is a standard for binary floating point arithmetic.
Modbus address list
To receive a full list containing the available standard SPU3 Modbus addresses (ASL-668
SPU3 Modbus registers list) or in case your AMS system is programmed for 16 or 32 bit
integer input signals, please contact VAF Instruments for additional information.
In case more than one (1) SPU3 is connected in the same MODBUS-loop, the slave
addresses of these SPU3’s are factory set resp. slave-“1”, slave-“2”, etc.

17
6.12 MODBUS CONNECTIONS
For connection of multiple slaves to J1 and/or J2 Modbus SPU3 master input, following
“multidrop” connection and settings need to be taken into account.
Figure 9 –Multidrop connection diagram
The connection loop needs to be “closed” with termination resistors.
In example Figure 9 the termination resistor needs to be placed at the first device (SPU3/master) and
at the last connected device (slave n).
Figure 10 –Termination resistor switch
The SPU3 termination resistor can be set by way of a jumper switch in “on”-position.
The termination resistor of the last device depends on the device. This can be done using a
resistor or by way of a switch. Please contact your supplier.
NOTE:
Do not connect the signal ground to the ship hull.
Termination resistor switches.
Set the switch in “on”-position to activate
the termination resistor for the
corresponding connection.

18
7. OPERATING PRINCIPLES
7.1 GENERAL
A zero setting procedure is always necessary in order to obtain a correct measurement and reading of
the T-Sense®Torque sensor or TT-Sense®Thrust & Torque sensor.
For more detailed information see section 6.4 of TIB-661 T-Sense®or TIB-664 TT-Sense®.
The PEM4 + SPU3 system is an integrated solution for monitoring engine power, fuel consumption and
a wide selection of additional data and indicators. The PEM4 + SPU3 system will display the engine load
diagram and the actual load of the main engine. The menu structure of the PEM4 + SPU3 system is self-
explaining and the system is easy to operate.
A number of conditional messages will inform you about error/fault conditions if applicable.
Setups determining functionality are subdivided in two levels and access is only possible via a right-of-
access code. All setups and computations are stored in a battery backup RAM. The PEM4 + SPU3
system is self-checking as for correct functioning of its memories, program run and existence of supply
voltage.
7.2 DISPLAYED PARAMETER AND ENGINEERING UNITS
The following parameters are available
Unit
•Shaft torque
kNm
•Shaft speed
rpm
•Shaft power
kW
•Shaft thrust
kN
•Total energy
kWh, MWh, GWh
•Total mass
kg
•Time-base
hours, minutes, seconds
•Shaft generator power (to calculate total power)
kW or MW
•Fuel oil flowmeters, max. 12x (*)
l/min
•K-factors flowmeters
pulses/litre
•Fuel temperature sensors, max. 12x (*)
°C
•GPS NMEA Ship’s SOG
knots
•GPS NMEA Ship’s STW
knots
•Speed log (input)
pulses/NM
•Fuel oil consumption
kg/h, ltr/h or kg/NM, ltr/NM
•Specific gravity
kg/l
•Thermal expansion
%/°C
•Ref. Temperature
°C
•Caloric value
MJ/kg
•Specific Fuel Oil Consumption (SFOC)
g/kWh
•Propeller thrust
kN
•Thrust power quotient
kN/MW
(*) for a maximum of 8 engines/consumers

19
7.3 EXPLANATION OF PARAMETERS
7.3.1 Shaft torque
The shaft torque is measured in the T(T)-Sense®rotor part and sent wireless to the control box. The shaft
torque output of the control box is connected to SPU3 via RS485 Modbus. *) **)
7.3.2 Shaft speed
The shaft speed is measured via a gravity sensor in the T(T)-Sense®rotor part and sent wireless to the
control box. The shaft speed output of the control box is connected to SPU3 via RS485 Modbus. *) **)
7.3.3 Shaft power
The measured torque and shaft speed are the input values to the power calculation, which is performed
in the T(T)-Sense®stator control box. The shaft power output of the control box is connected to SPU3
via RS485 Modbus. *) **)
7.3.4 Shaft thrust (option)
When a TT-Sense®is installed, which additionally measures shaft thrust, the measured thrust is sent
wireless to the control box. The shaft thrust output of the control box is connected to SPU3 via RS485
Modbus. *) **)
*) Adjustment of the bar-graph-ranges (“Engine Consumption” and “Engine Power”) and the
horizontal/vertical axis (“Propulsion Power/Speed diagram”) at the PEM4 touch screen are
programmed at VAF location.
**) Zero torque adjustment will be done during commissioning of the T(T)-Sense®rotorand control
box. For more detailed information see section 6.4 of TIB-661 T-Sense®or TIB-664 TT-Sense®.
7.3.5 Shaft generator (option)
The shaft generator output signal should be an active 4–20mA or Modbus signal. The input range is
programmed at VAF location.
The total power delivered by the main engine can be calculated by:
Total power main engine = Shaft power + shaft generator power.
Specific Fuel Oil Consumption (SFOC) value is calculated by dividing the engine’s fuel consumption by
above mentioned Total power.
7.3.6 Fuel oil consumption
Up to 12 flowmeters, each with a pulse and temperature output, can be connected to the SPU3. The
SPU3 can handle a maximum of 8 engines and/or consumers. Please refer to section 3for the flowmeter
pulse and temperature specifications.
The K-factor of each flowmeter is programmed at VAF location or can be set via the settings menu by
VAF authorised representatives through the PEM4 touch screen.
7.3.7 Fuel oil temperature
For an accurate calculation of fuel oil consumption, it is recommended to connect PT100 temperature
sensors within the system. Temperature sensors are strongly recommended when a supply/return
system is programmed. VAF type PT2 flowmeters are as a standard equipped with PT100 temperature
sensors. The PT100 sensors are connected to the SPU3.
The PT100 range is programmed in the SPU3. No further settings are needed.
Table of contents
Other VAF instruments Computer Hardware manuals
Popular Computer Hardware manuals by other brands
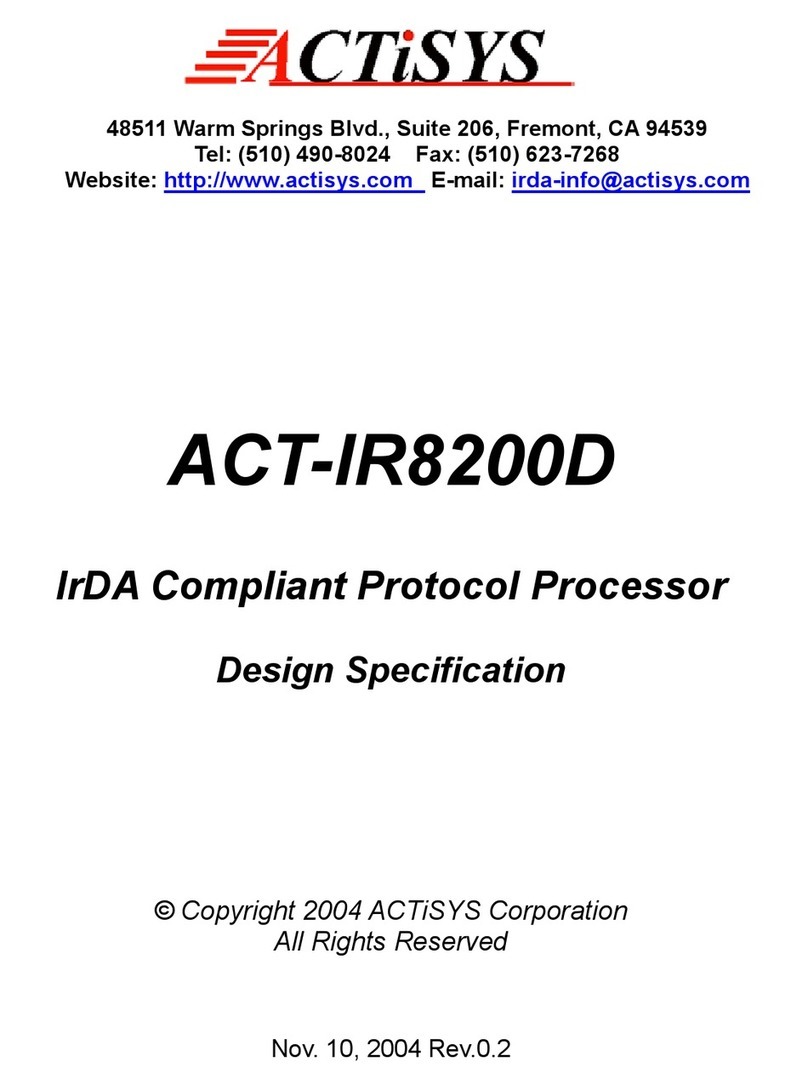
ACTiSYS
ACTiSYS IR8200D Design specification
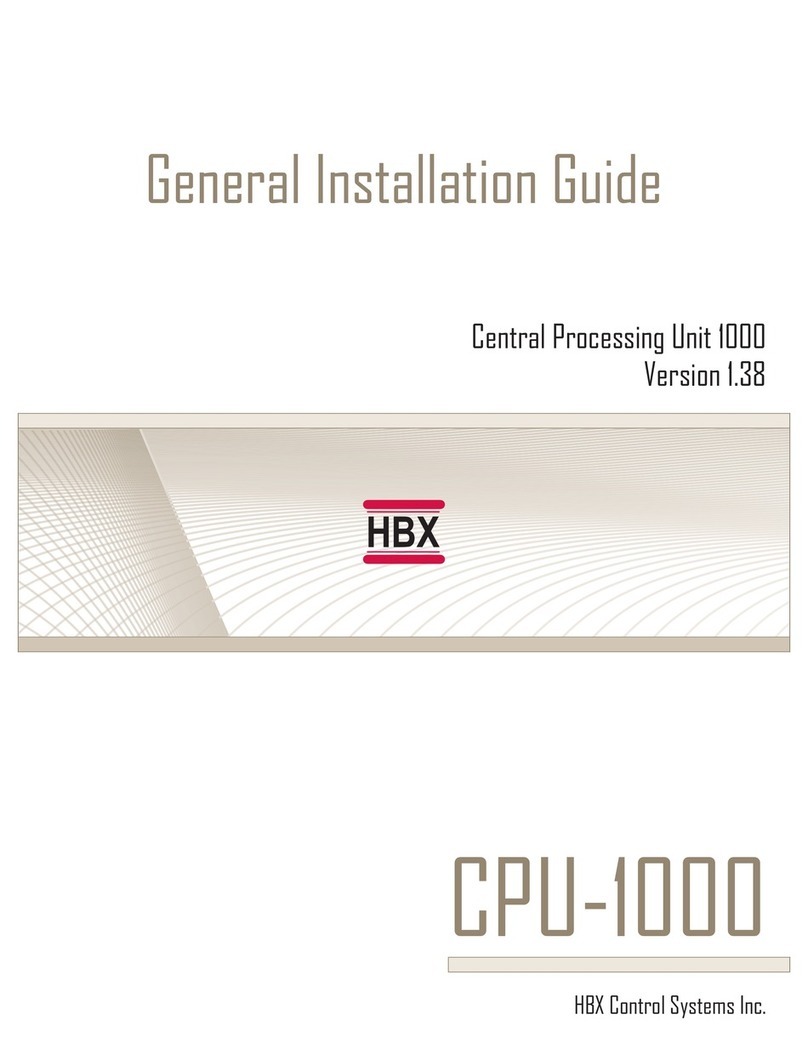
HBX
HBX CPU-1000 installation guide
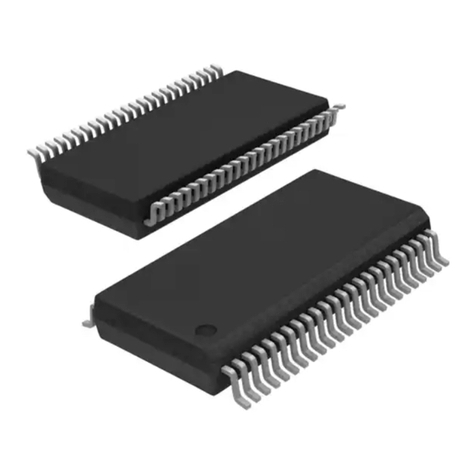
Cypress
Cypress AutoStore STK17T88 Application note
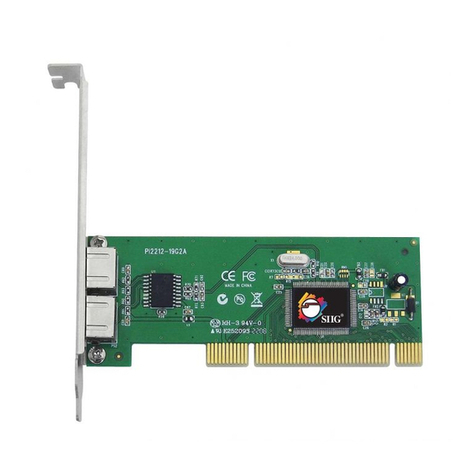
SIIG
SIIG DP PCI-to-PS/2 Quick installation guide
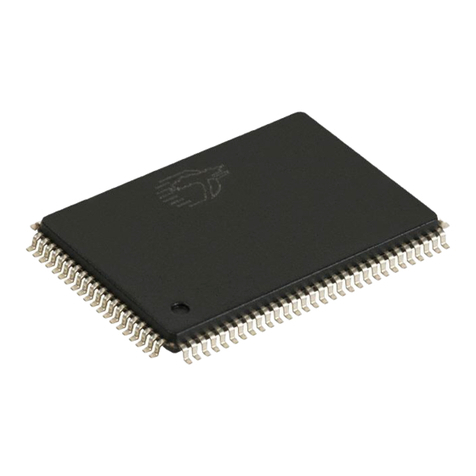
Cypress Semiconductor
Cypress Semiconductor CY7C1339G Specification sheet
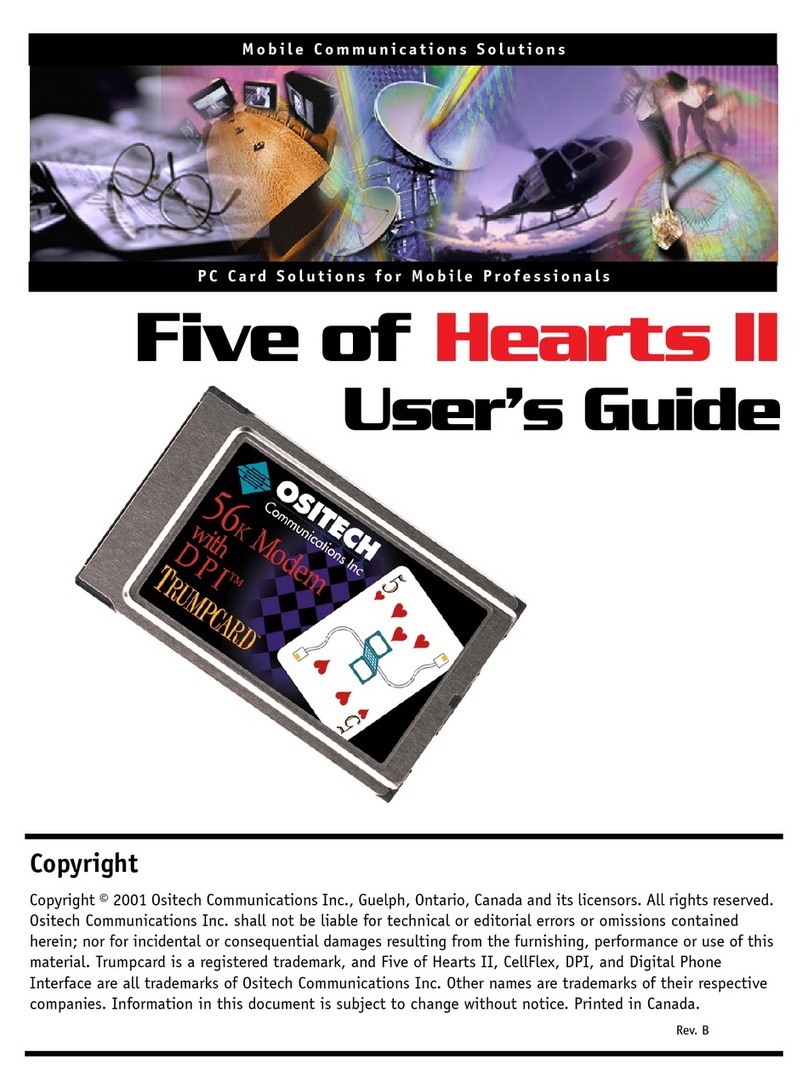
Ositech Communications
Ositech Communications Five of Hearts II user guide