Vanair Reliant RS45 User manual

INSTALLATION, OPERATION, MAINTENANCE AND PARTS MANUAL
45 CFM / 150 PSIG HYDRAULIC-DRIVEN, OPEN
CENTER & CLOSED CENTER, 12V & 24V, (OPTIONAL)
COLD-WEATHER, ROTARY SCREW COMPRESSOR
Read this manual before
installing, operating or
servicing this equipment.
Failure to comply with the
operation and maintenance
instructions in this manual
WILL VOID THE EQUIPMENT
WARRANTY.
NOTE
Use only Vanair Vanguard™
Premium Synthetic Oil and
Genuine Vanair Parts.
Inspect and replace
damaged components
before operation.
Substituting non-Vanair oil
or non-genuine Vanair filter
components WILL VOID THE
COMPRESSOR
WARRANTY!
NOTE
Making unauthorized
modifications to the system
components WILL VOID THE
WARRANTY!
Always inform Vanair
Manufacturing, Inc., before
beginning any changes to
the RS45 system.
KEEP THE MANUAL
WITH THE VEHICLE
NOTE
This publication contains the
latest information available
at the time of preparation.
Every effort has been made
to ensure accuracy.
Vanair Manufacturing, Inc.
reserves the right to make
design change modifications
or improvements without
prior notification.
Vanair Manufacturing, Inc.
10896 West 300 North
Michigan City, IN 46360
Telephone (toll free): (800) 526-8817
Service (toll free): (844) VAN-SERV
(844) 826-7378
Telephone: (219) 879-5100
Service Fax: (219) 879-5335
Parts Fax: (219) 879-5340
Sales Fax: (219) 879-5800
www.vanair.com
©2018 Vanair Manufacturing, Inc.
All rights reserved
P/N: 090126-OP_r0
Effective Date:
JANUARY-2018

MOBILE POWER SOLUTIONS
This limited warranty supersedes all previous Vanair warranties
and is exclusive with no other guarantees or warranties
expressed or implied.
LIMITED WARRANTY—Subject to the expressed terms and
conditions set forth below, Vanair Mfg., Inc. (“Vanair”), of
Michigan City, Indiana (USA), warrants to the original retail
purchaser of new Vanair equipment that such equipment is
free from defects in materials and workmanship when shipped
by Vanair.
For warranty claims received by Vanair within the applicable
warranty periods described below, Vanair will repair or replace
any warranted equipment, parts or components that fail due to
defects in material or workmanship or refund the purchase
price for the equipment, at Vanair’s discretion. Vanair is not
responsible for time or labor to gain access to the machine to
preform work. WARRANTY WILL BE VOID IF GENUINE VANAIR
PARTS AND FLUIDS ARE NOT USED.
Vanair must be notified in writing within thirty (30) days of any
such defect or failure. No warranty work or returns without
prior authorization is allowed. Vanair will provide instructions
on the warranty claim procedures to be followed.
Warranty will commence upon receipt of the Warranty
Registration Card. If the Warranty Registration Card is not
received within six (6) months of shipment from Vanair, the
warranty commencement date shall be thirty (30) days from
the date of shipment from Vanair. Records of warranty
adherence are the responsibility of the end user.
1. Lifetime Warranty Parts – 3 Years Labor
• Rotary Screw Air Compressor AirEnd
2. 6 Years Parts – 3 Years Labor
• Vanair Super Capacitor (VSC)
3. 3 Years Parts – 1 Year Labor
• Reciprocating Compressor Air End
• Generators
•Welders
4. 2 Years Parts – 1 Year Labor
•HydraulicMotors
•HydraulicPumps
5. 1 Year Parts – 1 Year Labor
• All electronics including, but not limitedto:
i) I/O Boards
ii) Modules
iii) Panel Boxes
iv) Instrumentation
v) Clutches
vi) Solenoids
vii) Running Gear/Trailers
viii) Compressor/Hydraulic Coolers, including Fan and
RadiatorCore
This Limited Warranty shall not apply to:
1. Consumable components, such as shaft seals, valves, belts,
filters, capacitors, contactors, relays, brushes or parts that
fail due to normal wear and use.
2. Items furnished by Vanair, but manufactured by others,
such as engines and trade accessories (these items are
covered by the manufacturer’s warranty, if any).
3. Equipment that has been modified by any party other than
Vanair or equipment which has not been used and
maintained in accordance with Vanair’s specifications.
4. Equipment which has been improperly installed and/or
improperly operated, based upon Vanair’s specifications
for the equipment or industry standards.
5. Equipment installed by non-authorized or third party
personnel.
Vanair products are intended for purchase and use by
commercial/industrial users and persons trained and
experienced in the use and maintenance of industrial
equipment.
In the event of a warranty claim covered by this Limited
Warranty, the exclusive remedies shall be, at Vanair’s sole
discretion: (i) repair; or (ii) replacement; (iii) where authorized in
writing by Vanair in appropriate cases, the reasonable cost of
repair or replacement at an authorized Vanair service facility; or
(iv) payment of (or credit for) the purchase price (less
reasonable depreciation based upon actual use) upon return of
the equipment at the warranty claimant’s risk and expense.
Vanair will pay standard ground freight for any warranty item
shipped to and from Vanair or (Vanair designated facility)
within the first year of the applicable warranty period. Any
additional expedited freight cost is the responsibility of the
purchaser.
TO THE GREAT EXTENT PERMITTED BY APPLICABLE LAW, THE
REMEDIES PROVIDED HEREIN ARE THE SOLE AND EXCLUSIVE
REMEDIES APPLICABLE TO THE VANAIR EQUIPMENT. IN NO
EVENT SHALL VANAIR BECOME LIABLE FOR DIRECT, INDIRECT,
SPECIAL, PUNITIVE, INCIDENTAL OR CONSEQUENTIAL
DAMAGES (INCLUDING LOSS OF PROFIT OR LOST BUSINESS
OPPORTUNITY), WHETHER BASED ON CONTRACT, TORT OR
ANY OTHER LEGAL THEORY. IN NO EVENT SHALL VANAIR
BECOME OBLIGATED TO PAY MORE ON ANY WARRANTY CLAIM
THAN THE PURCHASE PRICE ACTUALLY PAID BY THE ORIGINAL
RETAIL PURCHASER.
THIS LIMITED WARRANTY IS MADE IN LIEU OF ALL OTHER
WARRANTIES, EXPRESS OR IMPLIED, INCLUDING THE
WARRANTIES OF MERCHANTABILITY AND/OR FITNESS FOR A
PARTICULAR PURPOSE, OR ANY OTHER WARRANTY OR
GUARANTY ARISING BY OPERATION OF LAW. ANY WARRANTY
NOT EXPRESSLY PROVIDED HEREIN, IMPLIED WARRANTY,
GUARANTY AND ANY REPRESENTATION REGARDING THE
PERFORMANCE OF THE EQUIPMENT, AND ANY REMEDY FOR
BREACH OF CONTRACT, IN TORT, OR ANY OTHER LEGAL
THEORY WHICH, BUT FOR THIS PROVISION, MIGHT ARISE BY
IMPLICATION, OPERATION OF LAW, CUSTOM OF TRADE, OR
COURSE OF DEALING ARE EXCLUDED AND DISCLAIMED BY
VANAIR.
Some states in the United States of America do not allow
limitations of how long an implied warranty lasts, or the
exclusion of incidental, indirect, special or consequential
damages, and as such, the above limitations and exclusions
may not apply to you. This warranty provides specific legal
rights. Other rights may be available to you, but may vary from
state to state.
In Canada, legislation in some provinces provides for certain
additional warranties or remedies other than as stated herein,
and to the extent that they may not be saved, the limitations
and exclusions set out forth above may not apply. This Limited
Warranty provides specific legal rights, and other rights may be
available, but may vary from province to province.
AIR N ARC®
ALL-IN-ONE POWER-SYSTEMS®
RELIANT™ SERIES
POWERFLEX™ SERIES
PRO SERIES
CONTRACTOR SERIES
VIPER™ SERIES
FST™ SERIES
(844) VAN - SERV
SERVICE@VANAIR.COM
PARTS@VANAIR.COM
10896 W. 300 N.
MICHIGAN CITY, IN 46360
(800) 526-8817
VANAIR.COM
EFFECTIVE: JAN 8, 2016
090088_r1

RELIANT RS45 AIR COMPRESSOR TABLE OF CONTENTS
090126-OP_R0 (JAN-2018) PAGE - I
TABLE OF
CONTENTS
VANAIR MANUFACTURING, INC.
(800) 526-8817 • www.vanair.com
WARRANTY ..............................................BEHIND COVER
TABLE OF CONTENTS...................................................... I
WARRANTY CLAIMS PROCEDURE ................................ V
CLAIMS PROCESS FOR WARRANTED PARTS..................................................................................... V
PROCEDURE ........................................................................................................................................... V
Figure W-1: Serial Plate / Serial Number Location......................................................................................................VI
SECTION 1: SAFETY .....................................................1
1.1 GENERAL INFORMATION ......................................................................................................1
1.2 DANGERS, WARNINGS CAUTIONS AND NOTES ................................................................1
1.2.1 DANGERS........................................................................................................................................................1
1.2.2 WARNINGS......................................................................................................................................................1
1.2.3 CAUTIONS.......................................................................................................................................................2
1.2.4 NOTES...................................................................................................................................................................3
1.3 SAFETY DECALS ....................................................................................................................3
1.4 DISPOSING OF MACHINE FLUIDS .......................................................................................3
SECTION 2: SPECIFICATIONS..........................................5
TABLE 2A: VANAIR RS45 SPECIFICATIONS...........................................................................................5
TABLE 2B: PRIME LUBRICANT CHARACTERISTICS .............................................................................6
TABLE 2C: RECOMMENDED TORQUE SPECIFICATIONS ....................................................................5
SECTION 3: INSTALLATION..............................................7
3.1 MACHINE PACKAGE RECEIPT/INSPECTION............................................................................7
3.2 GENERAL INSTRUCTIONS .........................................................................................................7
3.3 DETERMINING THE COMPRESSOR UNIT MOUNTING LOCATION.........................................8
Continued on next page...

TABLE OF CONTENTS RELIANT RS45 AIR COMPRESSOR
PAGE - II 090126-OP_R0 (JAN-2018) VANAIR MANUFACTURING, INC.
(800) 526-8817 • www.vanair.com
SECTION 3: INSTALLATION (CONTINUED)
3.4 HYDRAULIC SYSTEM OVERVIEW............................................................................................. 8
3.4.1 HYDRAULIC SYSTEM FILTRATION......................................................................................................................8
3.4.2 HYDRAULIC OIL RESERVIOR..............................................................................................................................9
3.4.2.1 DETERMINING RESERVOIR SIZE...............................................................................9
3.4.2.2 DETERMINING RESERVOIR SHAPE...........................................................................9
3.4.2.3 MANDATORY RESEROIR FEATURES .........................................................................9
3.4.2.4 RECOMMENDED RESERVOIR OPTIONS.................................................................10
3.4.2.5 RESERVOIR FEATURES TO AVOID ..........................................................................10
3.4.3 RECOMMENDED HYDRAULIC SYSTEM SPECIFICATIONS............................................................................10
3.4.4 STANDARDS GUIDELINES.................................................................................................................................10
3.5 INSTALLATION............................................................................................................................11
3.5.1 MACHINE LOCATION...........................................................................................................................................11
3.5.2 CLEARANCES......................................................................................................................................................11
3.5.3 MOUNTING...........................................................................................................................................................11
3.5.4 SERVICE CONNECTIONS...................................................................................................................................11
3.5.5 ELECTRICAL CONNECTIONS.............................................................................................................................11
3.5.6 HYDRAULIC SUPPLY CIRCUIT...........................................................................................................................11
3.5.7 ROUTING..............................................................................................................................................................11
Figure 3-3A: Dimension Diagram - RS45 Open Center Without Thermal Valve ........................................................12
Figure 3-3B: Dimension Diagram - RS45 Open Center With Thermal Valve .............................................................13
Figure 3-3C: Dimension Diagram - RS45 Closed Center Without Thermal Valve......................................................14
Figure 3-3D: Dimension Diagram - RS45 Closed Center With Thermal Valve...........................................................15
SECTION 4: OPERATION................................................17
4.1 GENERAL INFORMATION.........................................................................................................17
4.2 PURPOSE OF CONTROLS ....................................................................................................... 17
Figure 4-1: Main Machine Component Locations.......................................................................................................18
4.3 NORMAL OPERATION .............................................................................................................. 19
4.3.1 INITIAL START-UP PROCEDURE: PRE-CHECKS.............................................................................................19
4.3.2 ROUTINE START-UP PROCEDURE...................................................................................................................20
Figure 4-5: Controller Screen Identification and Navigation.......................................................................................21
4.3.3 ROUTINE SHUT-DOWN PROCEDURE..............................................................................................................22
4.3.4 OPERATING CONDITIONS.................................................................................................................................22
4.3.5 EXTREME OPERATING CONDITIONS...............................................................................................................22
Continued on next page...

RELIANT RS45 AIR COMPRESSOR TABLE OF CONTENTS
090126-OP_R0 (JAN-2018) PAGE - III
VANAIR MANUFACTURING, INC.
(800) 526-8817 • www.vanair.com
SECTION 5: MAINTENANCE ...........................................23
5.1 GENERAL INFORMATION.........................................................................................................23
5.2 MACHINE MAINTENANCE SCHEDULE....................................................................................24
5.3 REPLACEMENT PARTS ............................................................................................................24
TABLE 5A: MAINTENANCE SCHEDULE TABLE - COMPRESSOR INTERVALS..................................25
TABLE 5B: ROUTINE REPLACEMENT KIT ORDER INFORMATION ....................................................25
5.4 PARTS REPLACEMENT AND ADJUSTMENT PROCEDURES ................................................29
5.4.1 ALIGNMENT.........................................................................................................................................................29
5.4.2 SETTING THE MINIMUM PRESSURE VALVE....................................................................................................30
5.4.3 COMPRESSOR THERMAL VALVE......................................................................................................................30
5.4.4 SERVICING THE SYSTEM CIRCUIT BREAKER, FUSES AND RELAY.............................................................30
5.4.5 SAFETY SHUTDOWN SYSTEMS.......................................................................................................................30
5.4.6 PRESSURE RELIEF VALVE................................................................................................................................31
5.4.7 REPLACING THE DRIVE COUPLING.................................................................................................................31
5.4.7.1 REPLACING THE DRIVE COUPLING ELEMENT ...................................................... 32
5.4.7.2 COUPLING ASSEMBLY.............................................................................................. 32
5.4.7.3 HUB ALIGNMENT CHECK.......................................................................................... 33
5.4.7.4 COUPLING MAINTENANCE....................................................................................... 33
5.4.8 STORAGE AND INTERMITTENT USE................................................................................................................34
5.4.8.1 INTERMITTENT USE......................................................................................................... 34
5.4.8.2 LONG TERM STORAGE .................................................................................................... 34
SECTION 6: TROUBLESHOOTING .................................35
6.1 GENERAL INFORMATION.........................................................................................................35
6.2 TROUBLESHOOTING GUIDE - MACHINE OPERATION..........................................................36
6.3 TROUBLESHOOTING GUIDE - HYDRAULICS .........................................................................38
SECTION 7: ILLUSTRATED PARTS LIST.......................45
7.1 PARTS ORDERING PROCEDURE ............................................................................................45
TABLE 7A: RECOMMENDED SPARE PARTS LIST...............................................................................46
7.2 COMPRESSOR AND PARTS - OPEN CENTER MODEL..........................................................48
7.3 COMPRESSOR AND PARTS - CLOSED CENTER MODEL .....................................................50
7.4 COOLER ASSEMBLY (NO THERMAL VALVE)..........................................................................52
7.5 COOLER ASSEMBLY (WITH THERMAL VALVE) ......................................................................53
7.6 FRAME AND CANOPY...............................................................................................................54
Continued on next page...

TABLE OF CONTENTS RELIANT RS45 AIR COMPRESSOR
PAGE - IV 090126-OP_R0 (JAN-2018) VANAIR MANUFACTURING, INC.
(800) 526-8817 • www.vanair.com
SECTION 7: ILLUSTRATED PARTS LIST (CONTINUED)
7.7 HOSE & TUBE ASSEMBLY- OPEN CENTER; NO THERMAL VALVE...................................... 56
7.8 HOSE & TUBE ASSEMBLY- OPEN CENTER; WITH THERMAL VALVE .................................. 58
7.9 HOSE & TUBE ASSEMBLY- CLOSED CENTER; NO THERMAL VALVE ................................. 60
7.10 HOSE & TUBE ASSEMBLY- CLOSED CENTER; WITH THERMAL VALVE ............................. 62
7.11 THERMAL VALVE ASSEMBLY - CLOSED CENTER ................................................................ 64
7.12 DISPLAY AND CONTROLLER ASSEMBLY .............................................................................. 65
7.13 HYDRAULIC MANIFOLD ASSEMBLY - OPEN CENTER .......................................................... 66
7.14 HYDRAULIC MANIFOLD ASSEMBLY - CLOSED CENTER ..................................................... 67
7.15 DECALS - PART 1 OF 2, IDENTIFICATION .............................................................................. 68
7.15 DECALS - PART 2 OF 2, LOCATIONS...................................................................................... 70
7.16A SCHEMATIC DIAGRAM - HYDRAULIC OIL FLOW, CLOSED CENTER .................................. 71
7.16B SCHEMATIC DIAGRAM - HYDRAULIC OIL FLOW,
CLOSED CENTER WITH THERMAL VALVE ............................................................................ 72
7.16C SCHEMATIC DIAGRAM - HYDRAULIC OIL FLOW, OPEN CENTER....................................... 73
7.16D SCHEMATIC DIAGRAM - HYDRAULIC OIL FLOW, OPEN CENTER
WITH THERMAL VALVE ............................................................................................................ 74
7.17 ELECTRICAL SCHEMATIC........................................................................................................ 75
7.18 HOSE INSTALLATION GUIDE ................................................................................................... 76
TABLE 7C: MAINTENANCE TRACKING LOG ....................................................................................... 77

RELIANT RS45 AIR COMPRESSOR WARRANTY CLAIMS PROCEDURE
090126-OP_r0 (JAN-2018) PAGE - V
VANAIR MANUFACTURING, INC.
(844) VAN-SERV • www.vanair.com
CLAIMS PROCESS FOR
WARRANTED VANAIR
PARTS
This process must be used by owners of
Vanair® equipment in situations where a
warranted item needs repair or replacement
under the terms of the purchase warranty.
Do not return items to Vanair without prior
authorization from the Vanair Warranty
Administrator.
PROCEDURE:
When a customer needs assistance in
troubleshooting a system and/or returning
parts, follow the steps below.
1. Locate the machine’s serial number:
The machine package serial number plate is
located inside the machine compartment on
the underside of the hood (see Figure W-1).
The hydraulic motor and the compressor
unit both also have their own individual serial
number/serial plates (see Figure W-1). For
issues particularly involving either the
hydraulic motor or the compressor unit,
these serial numbers may also be helpful for
conveying information. In any case, the
machine serial number can be used to
confirm and process any issue regarding the
machine overall, including the motor and the
compressor.
2. Have a list of the symptoms/condition/
malfunctions along with any applicable
temperature and pressure readings, and
also the number of operational hours
available:
Note that the above information will also
need to be included on the Return Material
Authorization Form (per Step #6); this form
is necessary for warranty processing if the
warranty claim is deemed valid by the
service case review.
3. Contact the Vanair® Service Department
by phone (1-844-VANSERV) to speak with
a Service Technician.
4. Vanair Service will troubleshoot the
problem based on the information
provided by the customer, and attempt to
return the unit to service as quickly as
possible.
5. If the unit cannot be returned to service,
and Vanair determines this matter is a
warranty issue, the Service Technician
will assign an RMA (Return Material
Authorization) number that will provide
for the return of the item to Vanair for
analysis and a final determination as to
the item’s warranty status.
6. Warranty Claims are solicited via a
Return Material Authorization (RMA)
Form. This form can be obtained by
request directly from the Vanair Service
Department:
Once a current form has been obtained,
follow the instructions given on the form to fill
in the information needed. This form is used
for the purpose of soliciting a warranty case.
Customers have 30 days after the RMA
number is issued to return the item. If the
NOTE
The RMA number must be placed on the
outside of the package being returned.
WARRANTY CLAIMS
PROCEDURE

WARRANTY CLAIMS PROCEDURE RELIANT RS45 AIR COMPRESSOR
PAGE - VI 090126-OP_r0 (JAN-2018) VANAIR MANUFACTURING, INC.
(844) VAN-SERV • www.vanair.com
part is not returned within this period, the
RMA is void and any claims will be denied.
Before sending a warranty part to a
customer, Vanair® will need a P.O. or credit
card number to cover the cost of the part and
shipping. After the part is analyzed and
deemed to be covered under warranty,
Vanair will issue credit to the customer. All
parts eligible for warranty must have the
RMA number on the invoice at the time of
purchase.
No items can be returned “freight collect”.
Freight costs will be addressed at the time
the claim is closed. The customer pays any
additional costs for warranty parts delivered
through expedited services (i.e., Next Day,
Second Day).
VANAIR WILL NEVER ACCEPT ANY
INVOICES FOR PARTS RETURNED: ANY
PARTS RETURNED VIA INVOICE WILL BE
RETURNED FREIGHT COLLECT: NO
PARTS ARE TO BE RETURNED FREIGHT
COLLECT!
Vanair Mfg., Inc. strives to continuously
improve its customer service. Please forward
any questions, comments, or suggestions to
Vanair Service (844-VANSERV) or e-mail us
(warranty@vanair.com).
NOTE
All labor claims or invoices must be
approved by the Vanair Warranty
Administrator prior to starting repair work
along with the cost of the repair. All
paperwork associated with the returned
item and warranty repair cost must
reference the RMA number issued against
the part, and be forwarded to Vanair
within 30 days of the completion of work.
KEY DESCRIPTION KEY DESCRIPTION
AMACHINE SERIAL PLATE / SERIAL NUMBER LOCATION CCOMPRESSOR UNIT SERIAL
PLATE / SERIAL NUMBER
LOCATION
B HYDRAULIC MOTOR SERIAL PLATE / SERIAL NUMBER
LOCATION
Figure W-1: Serial Plate / Serial Number Locations
UNDERSIDE OF HOOD
A
B
C

RELIANT RS45 AIR COMPRESSOR SECTION 1: SAFETY
090126-OP_r0 (JAN-2018) PAGE - 1
VANAIR MANUFACTURING, INC.
(800) 526-8817 • www.vanair.com
1.1 GENERAL INFORMATION
The products provided by Vanair® Mfg., Inc.
are designed and manufactured for safe
operation and maintenance. But it is
ultimately the responsibility of the users and
maintainers for safe use of this equipment.
Part of this responsibility is to read and be
familiar with the contents of this manual
before operation or performing maintenance
actions.
1.2 DANGERS, WARNINGS,
CAUTIONS AND NOTES
These boxes are labeled clearly with the title
block listing either Danger, Warning,
Caution, or other non-safety issue. They
draw attention to specific issues that are
pertinent to the safe and correct operation of
the machine.
The symbols shown and defined in Section
1: Safety are used throughout this manual
and on the machine to call attention to, and
identify, possible hazards.
The international warning symbol (shown
above) is used on all decals, labels and
signs that concern information pertaining to
bodily harm. When you see the international
warning symbol, pay extremely careful
attention, and follow the given instructions
or indications to avoid any possible hazard.
1.2.1 DANGERS
• Keep tools or other conductive objects away
from live electrical parts.
• Never touch electrical wires or components
while the machine is operating. They can be
sources of electrical shock.
1.2.2 WARNINGS
•DO NOT EVER use this compressor as a
breathing air source. Vanair disclaims any
and all liabilities for damage or loss due to
fatalities, personal injuries resulting from the
use of a Vanair compressor to supply
breathing air.
•DO NOT perform any modifications to
this equipment without prior factory
approval.
•DO NOT operate the compressor or any
of its systems if there is a known unsafe
condition. Disable the equipment by
disconnecting it from its power source.
Install a lock-out tag to identify the
equipment as inoperable to other
personnel.
•DO NOT operate the compressor with
any by-pass or other safety systems
disconnected or rendered inoperative.
•DO NOT operate the equipment while you
are under the influence of alcohol or drugs.
•DO NOT operate the equipment while you
are feeling ill.
•DO NOT attempt to service the equipment
while it is operating.
• Before performing maintenance, or replacing
parts, relieve the entire system pressure,
after the system has blown down, by opening
a service valve which will vent all pressure to
the atmosphere. After that, remove any
remaining residual pressure by slowly
DANGER
Identifies actions or conditions which will
cause death, severe injury, or equipment
damage or destructive malfunctions.
WARNING
Identifies actions or conditions which may
cause death, severe injury, or equipment
damage or destructive malfunctions.
SECTION 1:
SAFETY

SECTION1: SAFETY RELIANT RS45 AIR COMPRESSOR
PAGE - 2 090126-OP_r0 (JAN-2018) VANAIR MANUFACTURING, INC.
(800) 526-8817 • www.vanair.com
opening the fill cap. Remove all electrical
power.
•DO NOT use the compressor for
purposes other than for which it is
intended. High pressure air can cause
serious and even fatal injuries.
•DO NOT operate the compressor
outside of its specified pressure and
speed ratings. (See Section 2:
Specifications or refer to the equipment
data plate.).
•DO NOT use flammable solvents or
cleaners for cleaning the compressor or
its parts.
•DO NOT operate the compressor in
areas where flammable, toxic, or
corrosive fumes, or other damaging
substance can be ingested by the
compressor intakes.
• Keep arms, hands, hair and other body
parts, and clothing away from fans, drive
shafts, and other moving parts.
•DO NOT wear jewelry, unbuttoned cuffs,
ties, or loose-fitting clothing when you are
working near moving/rotating parts.
•ALWAYS confine long hair when working
near moving/rotating parts.
•NEVER operate the equipment while
wearing a headset to listen to music or the
radio.
• Wear personal protective equipment such as
gloves, work shoes, and eye and hearing
protection as required for the task at hand.
•DO NOT operate the compressor with
any guards removed or damaged, or
other safety devices inoperative.
•DO NOT operate the compressor in
enclosed or confined spaces where
ventilation is restricted or closed-off.
• Ensure that hoses connected to service
valves are fitted with correctly sized and
rated flow limiting devices which comply
with applicable codes. Pressurized
broken or disconnected hoses can whip,
causing injuries or damage.
•DO NOT use tools, hoses, or equipment
that have maximum ratings below that of
this compressor.
• Keep metal tools, and other conductive
objects away from live electrical
components.
• Before performing maintenance or repair
operations on the compressor, ensure
that all power has been removed and
been locked out to prevent accidental
application.
•DO NOT assume that because the
compressor is in a STOPPED condition
that hydraulic power has been removed.
• Use this compressor only to compress
atmospheric air. Use of this equipment
as a booster pump and/or to compress
any other gaseous or aerosol substance
constitutes improper use. It can also
cause damage or injuries. Such misuse
will also void the warranty.
• Install, operate, and maintain this
equipment in full compliance with all
applicable OSHA, other Federal, state,
local codes, standards, and regulations.
• When lifting objects, be aware of proper
lifting techniques to avoid injury.
•ALWAYS read and follow safety related
precautions found on containers of
hazardous substances.
1.2.3 CAUTIONS
• Check all safety devices for proper
operation on a routine basis.
• Ensure that no tools, rags, or other
objects are left on compressor drive
systems or near intakes.
• Keep the equipment clean when
performing maintenance or service
actions. Cover openings to prevent
contamination.
•DO NOT operate the compressor if
cooling air is not available (fan/cooler not
operating) or if lubricant levels are below
their specified minimum levels.
• Ensure all plugs, hoses, connectors,
covers, and other parts removed for
maintenance actions are replaced
before applying power to the
compressor.
NOTE
Slowly remove fill cap to vent compressor
sump pressure.
CAUTION
Identifies actions or conditions which will
or can cause injuries, equipment damage or
malfunctions.

RELIANT RS45 AIR COMPRESSOR SECTION 1: SAFETY
090126-OP_r0 (JAN-2018) PAGE - 3
VANAIR MANUFACTURING, INC.
(800) 526-8817 • www.vanair.com
• Avoid touching hot surfaces and
components.
• Ensure that electrical wiring, terminals;
hoses and fittings are kept in serviceable
condition through routine inspections
and maintenance. Replace any
damaged or worn components.
1.2.4 NOTES
Note boxes are usually listed to convey and
give focus to a distinct piece of information,
which is not directly related to a safety issue,
but is necessary to understand machine
function and operation. Special note referrals
in the manual may be contained in a box
titled with an IMPORTANT banner, as shown
below, and may also contain the WARNING
symbol, should the information be linked to a
safety issue:
1.3 SAFETY DECALS
Safety decals are placed onto, or located
near, system components that can present a
hazard to operators or service personnel. All
pertinent decals listed in Section 7.15,
Decals, are located near a component which
is subject to respect in terms of safety
precautions. Always heed the information
noted on the safety decals.
1.4 DISPOSING OF MACHINE
FLUIDS
Always dispose of machine fluids under the
guidance of all applicable local, regional and/
or federal law.
Vanair® encourages recycling when allowed.
For additional information, consult the
container label of the fluid in question.
NOTE
Additional information (or existing
information) which should be brought to the
attention of operators/maintainers affecting
operation, maintenance, or warranty
requirements.
IMPORTANT
Additional, CRUTIAL information (or existing
information) which should be brought to the
attention of operators/maintainers affecting
operation, maintenance, or warranty
requirements.
WARNING
DO NOT REMOVE OR COVER ANY
SAFETY DECAL. Replace any safety decal
that becomes damaged or illegible.

SECTION 1: SAFETY RELIANT RS45 AIR COMPRESSOR
PAGE - 4 090126-OP_r0 (JAN-2018)
BLANK PAGE
VANAIR MANUFACTURING, INC.
(800) 526-8817 • www.vanair.com

RELIANT RS45 AIR COMPRESSOR SECTION 2: SPECIFICATIONS
090126-OP_r0 (JAN-2018) PAGE - 5
VANAIR MANUFACTURING, INC.
(844) VAN-SERV • www.vanair.com
SECTION 2:
SPECIFICATIONS
TABLE 2A: VANAIR RS45 SPECIFICATIONS
GENERAL SYSTEM INFORMATION SPECIFICATION
RATINGS
Capacity (CFM @ 150 psig): 45
Air pressure rating (psig): 150
Speed of compressor (RPM @ 100 psig): 4500
Hydraulic motor RPM 4500
Hydraulic flow (gpm @ 120°F hydraulic oil temperature): 11.0
Hydraulic pressure (psig @ 100/150 compressor psig): 2150 @ 100 / 2550 @ 150 II
Maximum compressor oil temperature 240°F
Maximum hydraulic oil temperature 160°F
COMPRESSOR
Type: Encapsulated, Oil-injected, Rotary Screw
Compressor oil tank capacity: 4 U.S. Quarts (3.7L)
Compressor overheating protection: Shut Down at 240°F
Air inlet system: Dry-type, Single Stage Filter
Drive coupling: Direct Drive, Flex Jaw Coupling
Hydraulic motor: Gear Type
PACKAGE
Main frame: Formed Aluminum with Bolt-down Provision
Electrical supply: 12V Standard; 24V Optional
Electrical connections: Deutsch 6-pin Round
Supply connections (customer hook-up): Hydraulic: Oil In = #12 3/4”, 37° JIC
Hydraulic: Oil Out = #16 1”, 37° JIC
Case Drain: #6 3/8” JIC
Air Out: #12 3/4” JIC
Electrical: 12V DC (Standard)
24V DC (Optional)
I Refer to Section 3.4, Hydraulic System Requirements, for additional speed requirement information.
II Hydraulic relief valve setting is 3200 psi. Recommended hydraulic system pressure: 2600 psi continuous, 3000 psi
intermittent.
Table continued on next page

SECTION 2: SPECIFICATIONS RELIANT RS45 AIR COMPRESSOR
PAGE - 6 090126-OP_r0 (JAN-2018) VANAIR MANUFACTURING, INC.
(844) VAN-SERV • www.vanair.com
PACKAGE (continued)
Enclosure: Sheet Metal with Service Access
Cooler: Hydraulic Oil Cooler/Radiator Core - Electric Fan
Dimensions: 33.6" L x 21.00" W x 22.81” H
Weight: 196 lbs (dry)
NOTE: For cold weather machines: Cracking Pressure: 50 PSI
NOTE: Shift Temperature: 100°F
NOTE: For machine installation clearances, refer to Figure 3-2, Minimum Installation Clearances, in Section 3,
Installation.
NOTE: Specifications are subject to change without notice.
TABLE 2B: PRIME LUBRICANT CHARACTERISTICS
Viscosity 178 SUS at 100°F (38°C)
Flash point 457°F (236°C)
Pour Point -49°F (-45°C)
Contains Rust and Oxidation Inhibitors and Detergents
TABLE 2C: RECOMMENDED TORQUE SPECIFICATIONS
TYPE DESCRIPTION: SAE 5
3 line ID marks SAE 8
6 line ID marks
Bolt Diameter Thread / inch Dry Oiled Dry Oiled
1/4 20 8 6 12 9
5/16 18 17 13 25 18
3/8 16 30 23 45 35
1/2 20 90 65 120 90
TABLE 2A: VANAIR RS45 SPECIFICATIONS
GENERAL SYSTEM INFORMATION SPECIFICATION

RELIANT RS45 AIR COMPRESSOR SECTION 3: INSTALLATION
090126-OP_r0 (JAN-2018) PAGE - 7
VANAIR MANUFACTURING, INC.
(844) VAN-SERV • www.vanair.com
3.1 MACHINE PACKAGE
RECEIPT/INSPECTION
Upon receipt of the machine package,
inspect the exterior of the shipping crate for
signs of shipping/transit damage. Any
damage should be reported immediately to
the shipping company.
Access the roof panel to inspect the
component parts and supports. Remove
manual from inside of canopy.
Should any damage be discovered during
package inspection, contact the shipping
company immediately.
3.2 GENERAL INSTRUCTIONS
This section provides general guidance for
locating and preparing the Vanair RS45
compressor package for operation. Each
installation is unique and can be affected by
location, ventilation, and other factors such
as electrical and hydraulic power supply
availability and location.
NOTE
Before fully unpacking the unit, inspect the
component parts, supports and loose-
packed parts to ensure that there have been
no internal movements of assemblies or
components, which may have been
damaged during shipment.
WARNING
Before performing maintenance or repair
operations on the compressor, ensure that
all power has been removed and locked
out to prevent accidental application.
DO NOT assume that because the
compressor is in a STOPPED condition
that power has been removed.
WARNING
Install, operate, and maintain this
equipment in full compliance with all
applicable OSHA, other Federal, state,
local codes, standards, and regulations.
WARNING
Do not install in any enclosed space
without first contacting Vanair.
WARNING
Grounding must consist of a minimum two
(2) gauge wire between the instrument
panel, the machine, and the truck chassis.
NOTE
Although much of the information given in
this installation section is detailed, these
guidelines should be considered as
referential material only, due to the diverse
possibilities of the end user’s vehicle
make, model and year, and the unit model
specifications.
NOTE
Install electrical components (circuit
breakers, pressure switches, toggle
switches, etc.) in locations where
exposure to water or moisture will be most
minimized.
NOTE
Contact Vanair® at
(219) 879-5100 / (844) VAN-SERV
Service Fax: (219) 879-5335
www.vanair.com
to report missing items, incorrect part
numbers, or other discrepancies.
SECTION 3:
INSTALLATION

SECTION 3: INSTALLATION RELIANT RS45 AIR COMPRESSOR
PAGE - 8 090126-OP_r0 (JAN-2018) VANAIR MANUFACTURING, INC.
(844) VAN-SERV • www.vanair.com
3.3 DETERMINING THE
COMPRESSOR UNIT
MOUNTING LOCATION
When determining the location to mount the
RS45 unit, the following criteria must be
taken into consideration:
• Refer to Section 3.5, Installation. The
location must allow for the machine
dimensions (Figures 3-3A through 3-3D),
and additional space requirements for
minimum cooling, access and
maintenance.
• The mounting surface must be level and
able to accommodate the four [4]
mounting bolts of the base frame. Refer
to Figures 3-3A through 3-3D for
mounting hole location dimensions.
• The mounting surface must be able to
support the units weight (196 lbs.).
• The external display must be easily
visible to the operator.
It is recommended, for most installations, to
mount the compressor on the driver’s side of
the vehicle. The unit should be situated in
such a manner that the fan (rear) and intake
side (front) are not obstructed. Do not place
the compressor in any location where it can
intake exhaust fumes, dust or debris.
3.4 HYDRAULIC SYSTEM
OVERVIEW
Refer to Figures 3-3A through 3-3D for
hydraulic pump system connections.
Please take into consideration the following:
• The hydraulic flow and pressure
requirements of the system.
• A continuous hydraulic load is necessary
when compressor is running.
• The duty cycle and ambient operating
temperatures.
• Other hydraulic equipment which may
share that same hydraulic supply system
(Vanair® recommends a dedicated pump
and hydraulic circuit).
The hydraulic hoses must be run to the
machine. Verify that hoses are hooked up
properly to ensure proper flow. Also, verify
that the hoses are laid out properly so that
no chafing or kinking of the hoses is
possible. Refer to Section 7.18, Hose
Installation Guide, for assistance with
proper hose layout and connecting functions.
3.4.1 HYDRAULIC SYSTEM FILTRATION
Vanair recommends using a 10 micron oil
filter on the hydraulic oil return line. Flow
rating of the filter must be equal to, or greater
than,
the maximum GPM at which the
system will be operated.
IMPORTANT
Vanair® highly recommends consulting a
hydraulic supply expert for specifying the
correct hydraulic supply components for
vehicle-side integration (including oil
reservoir size, hydraulic pressure relief,
hose size, etc.) for your application.
IMPORTANT
Contaminated hydraulic fluid allowed to
enter the pump will cause malfunction of the
pump controls. Hydraulic system hoses
must be flushed and cleaned prior to being
connected to the unit.
WARNING
Follow all applicable safety
recommendations as outlined in Section 1:
Safety of this manual.
WARNING
Improperly, or non-connected lines will
damage the equipment.
NOTE
The temperature of the hydraulic oil should
not exceed 160°F due to the rating of the
Vanair-supplied hydraulic motor.

RELIANT RS45 AIR COMPRESSOR SECTION 3: INSTALLATION
090126-OP_r0 (JAN-2018) PAGE - 9
VANAIR MANUFACTURING, INC.
(844) VAN-SERV • www.vanair.com
3.4.2 HYDRAULIC OIL RESERVOIR
3.4.2.1 DETERMINING RESERVOIR SIZE
In a conventional hydraulic system, minimum
tank size, in gallons, should be equal to the
maximum GPM flow rate, times two (x 2).
3.4.2.2 DETERMINING RESERVOIR
SHAPE
The reservoir structure should be tall and
narrow rather than shallow and broad
(Figure 3-1). A tall, narrow tank is
recommended because:
1. The oil level is well above suction line
opening, avoiding the
possibility of
drawing air into the pump due to a vortex
or
“whirlpool” effect within the tank during
operation flow.
2. Allows for better oil level tolerance level
of the system if vehicle operates at an
unusual (slightly off level) vehicle angle.
3. To keep return flow well below the
surface so it does not break the surface
and cause aeration (cavitation) of the oil.
3.4.2.3 MANDATORY RESERVOIR
FEATURES
• The reservoir should incorporate the
following design features:
• In terms of location of the reservoir tank
within the hydraulic system, note that the
hydraulic pump’s inlet line (suction line
out from the reservoir to the pump)
should be located near the bottom of the
tank, well below the oil level. The suction
line should protrude a minimum of two
(2”) inches into the reservoir to keep it
away from potential contaminant surface
buildup.
• A baffle or baffles should be included to
prevent sloshing, or centrifugal motion of
the oil; the goal is to break up direct flow
of the oil from the return point to the
suction point. This allows for the cooling
action contact with the tanks’ inner
surfaces, and promote separation of any
air or contaminants that interact with the
flowing oil.
• An ideal baffle design would position
several (but not too many) baffles to
promote an ‘S’ shape flow within the
reservoir, as viewed from above. The
area of the end gaps should be at least
twice the area of the suction line
diameter.
• A drain port with plug, situated at the
lowest point of the reservoir, is needed to
assure complete draining. It should be
installed using an
adapter or housing
which does not protrude above the inner
surface of the floor of the tank. It should
be visible and
accessible for removal,
with sufficient space available for
catching the waste oil.
• If the return line entrance to the tank is
located near the top, it should be
extended downward within the tank to
minimize foaming and aeration of the
circulating oil. This extends oil integrity,
which in turn helps to maintain system
performance and reliability.
IMPORTANT
Use only a filter that is specifically intended
for hydraulic systems.
KEY DESCRIPTION
A PREFERRED SHAPE: TALL AND NARROW
B SHAPE TO AVOID: BROAD AND SHALLOW
Figure 3-1: Reservoir Design Shape
A
B

SECTION 3: INSTALLATION RELIANT RS45 AIR COMPRESSOR
PAGE - 10 090126-OP_r0 (JAN-2018) VANAIR MANUFACTURING, INC.
(844) VAN-SERV • www.vanair.com
• An in-line filter on the return line is
needed to protect the system against
contaminants being introduced into the
oil. The filter should be mounted
externally from the reservoir in a location
that allows for easy of service access.
• A breather and fill cap is needed at the
oil fill port, which needs to be located
above the system oil level. The breather
cap acts to both filter air that is drawn
into the reservoir as the oil level
diminishes, and bleeds air out as the
level is regained. This maintains
constant atmospheric pressure in the air
volume within the reservoir.
• A sight-glass provides a direct visual
indication of the oil level without having
to open, or otherwise access, the
reservoir.
3.4.2.4 RECOMMENDED RESERVOIR
OPTIONS
Although not essential for an adequately
functioning reservoir, the following
components will contribute to maximize the
hydraulic system’s efficiency and maintain a
quality operational level.
• Magnetic drain plug: Attracts and
concentrates ferrous contaminants at the
drain plug source for easier accessibility
and removal when cleaning tank interior.
• A temperature gauge: Located in
approximation to, or built in to, the sight
glass assembly allows for temperature
reading at a glance.
• Filler port strainer: Prevents large
contaminant particles from blending with
system oil when adding new oil.
• Return line diffuser (splash) plate reduces
velocity of oil flow before return oil
stream merges with the main reservoir
oil volume.
• A reservoir heater: For those systems that
are exposed to cold climate ambients,
having the ability to preheat the hydraulic
oil prior to start up will make for easier
startups, and reduce the strain of
warming up the system under adverse
cold conditions.
3.4.2.5 RESERVOIR FEATURES TO
AVOID
A strainer used to screen the suction line is
not recommended for systems designed for
mobile equipment use. Having equipment
that likely experiences long suction lines,
cold startups and non-tracked or infrequent
maintenance practices may cause this
strainer to potentially promote system strain
(cavitation) than prolong fluid integrity
through filtration.
A pressurized reservoir is not recommended
for vehicles, as its complexity invites too
much potential for loss of system reliability if
it is not properly maintained.
3.4.3 RECOMMENDED HYDRAULIC
SYSTEM SPECIFICATIONS
Refer to Figures 3-3A through 3-3D.
• Flow controller is optional to reduce flow if
necessary. Consult Vanair®.
HYDRAULIC LINES
The following is a minimum requirement and
NO quick disconnects may be used. Lines
are to be kept as straight and short as
possible.
• Pressure port = Standard, #12, 3/4” hose
(located at manifold block)
• Load sense = #4 JIC = 1/4” hose (Used for
closed center system only)
• Pressure relief/case drain = #6 JIC = 3/8”
hose
• Hydraulic suction = Standard, #16, 1”
hose
3.4.4 STANDARDS GUIDELINES
• Hydraulic pressure relief factory set at
3200 psi.
WARNING
Do not operate machine without hydraulic
system completely assembled.

RELIANT RS45 AIR COMPRESSOR SECTION 3: INSTALLATION
090126-OP_r0 (JAN-2018) PAGE - 11
VANAIR MANUFACTURING, INC.
(844) VAN-SERV • www.vanair.com
3.5 INSTALLATION
3.5.1 MACHINE LOCATION
It is vital to locate the machine so that there
is no restriction of cooling air through the
enclosure (Refer to Figure 3-2). Cooling air
enters the enclosure at the rear (cooler)
package end of the machine, passes through
the cooler and exits through vents in the
upper sides and the front.
3.5.2 CLEARANCES
Refer to Figure 3-2. Ensure that adequate
surrounding clearance space exists around
the machine to allow for adequate cooling
ventilation through the canopy shroud,
unobstructed service access, and a clear
view of the control panel. An approximate
recommendation of ten (10) inches
clearance, minimum, is needed for proper
cooling circulation, plus any additional
service access room included where
needed.
3.5.3 MOUNTING
Mounting surface or support should be
adequate for the weight of the machine (196
lbs.), and should be level for normal
operation. Mounting holes are located in the
frame footing for four (4) 1/2” hold down
bolts.
3.5.4 SERVICE CONNECTIONS
Refer to Figure 3-3A through 3-3D. Service
connections are conveniently grouped at the
lower rear section of the unit in the base
frame.
3.5.5 ELECTRICAL CONNECTIONS
Refer to Figure 3-3A through 3-3D. This
system is offered with either 12V DC or 24V
DC circuits.
3.5.6 HYDRAULIC SUPPLY CIRCUIT
Refer to the hydraulic flow schematic
drawings (Sections 7.16A through 7.16D). It
is recommended that the compressor unit
possesses a separate pump/flow/return
hydraulic circuit to other hydraulic
equipment. This is to prevent the possibility
of pressure/flow drops that may occur if
other hydraulically-powered equipment is
activated during compressor operation,
which may in turn, cause the compressor to
stall out. Alternatively, use of a diverter valve
will permit hydraulics to power different
equipment selectively.
3.5.7 ROUTING
Refer to Figures 3-3A through 3-3D, and the
wiring diagram. Ensure that all supply hoses
and electrical wiring are correctly specified,
adequately supported, and do not touch or
rest on any sharp edges. Wiring should be
protected with split loom to prevent
corrosion, and consequently, loss due to
down time.
KEY DESCRIPTION
ABACK SIDE CLEARANCE = 10” MINIMUM
BLEFT SIDE CLEARANCE = 10” MINIMUM
CFRONT SIDE CLEARANCE = 10” MINIMUM I
DRIGHT SIDE CLEARANCE = 10” MINIMUM
ETOP SIDE (OVER HEAD) CLEARANCE = 42.63” MINI-
MUM, FOR (OPENED) HOOD ACCESS
I
Thefront(controlpanel)sidemayneedadditionalclearancefor
both access to the service panel there, and/or access to view
the controller panel.
Figure 3-2: Minimum Installation Clearances
A
B
D
C
E

SECTION 3: INSTALLATION RELIANT RS45 AIR COMPRESSOR
PAGE - 12 090126-OP_r0 (JAN-2018) VANAIR MANUFACTURING, INC.
(844) VAN-SERV • www.vanair.com
Figure 3-3A: Dimension Diagram - RS45 Open Center Without Thermal Valve
28.38
1.52
OIL DRAIN
COMPRESSOR
(TO TANK)
OIL RETURN
HYDRAULIC
CASE DRAIN
HYDRAULIC MOTOR
OIL FILL
FILTER
OIL
21.00
OIL DRAIN HOSE
22.81
DISPLAY MODULE
(TO MOTOR)
OIL SUPPLY
HYDRAULIC
DISCHARGE
AIR
SCALE 3/16
VIEW A-A
A
A
PARTS REMOVED FOR CLARITY
CLEARANCE
HOOD
19.82
REMOVED FOR CLARITY
ACCESS PANEL
27.00
19.25
(4x)0.56
33.60
AIR FILTER INTAKE
2.25
5.13
DISCLAIMER
If machine package is to be mounted
within a confined space such as
beneath a canopy, the unit must have a
minimum of ten (10) inch clearances on
the front and back sides for ventilation.
051598ID_r1
Table of contents
Other Vanair Compressor manuals
Popular Compressor manuals by other brands

Gude
Gude 50066 Instructions for use

Ingersoll-Rand
Ingersoll-Rand centac C950 Planning and installation manual
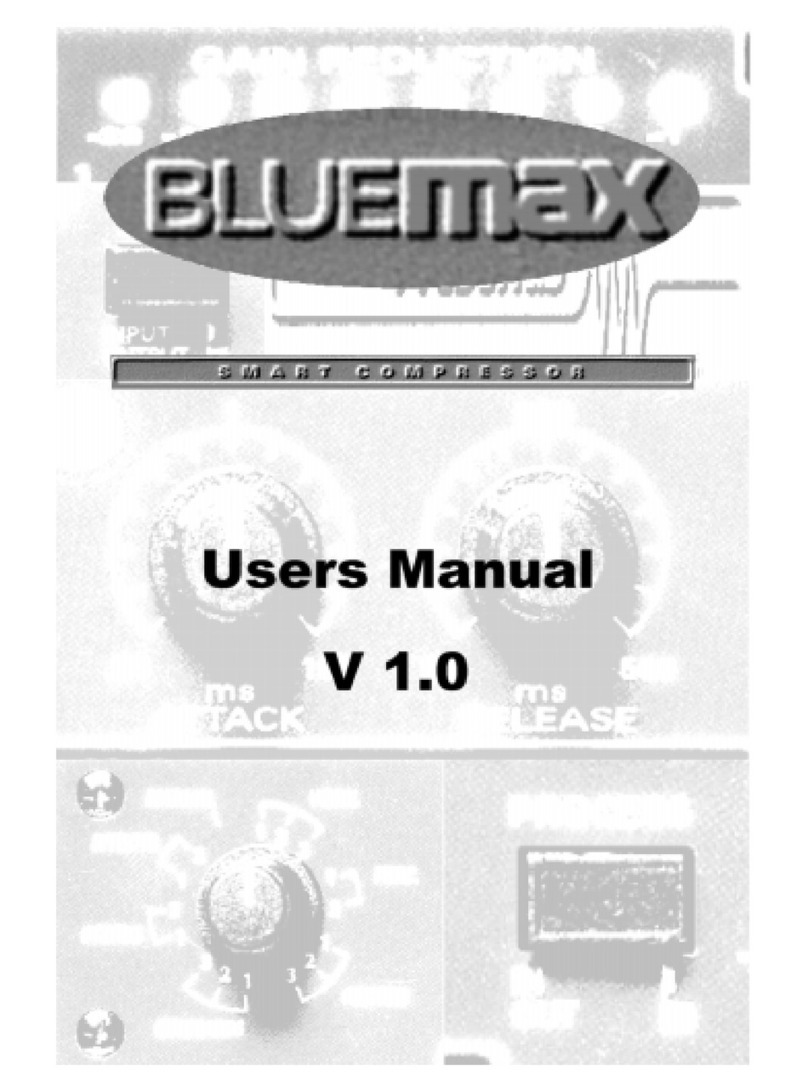
PRESONUS
PRESONUS Smart Compressor user manual
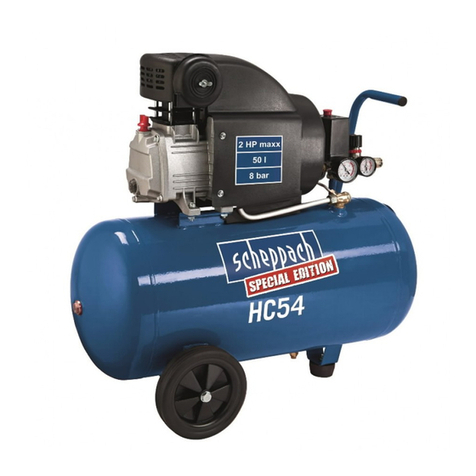
Scheppach
Scheppach HC54 Translation of original instruction manual

Panasonic
Panasonic Matsushita QA51K13GAU6 Specification sheet
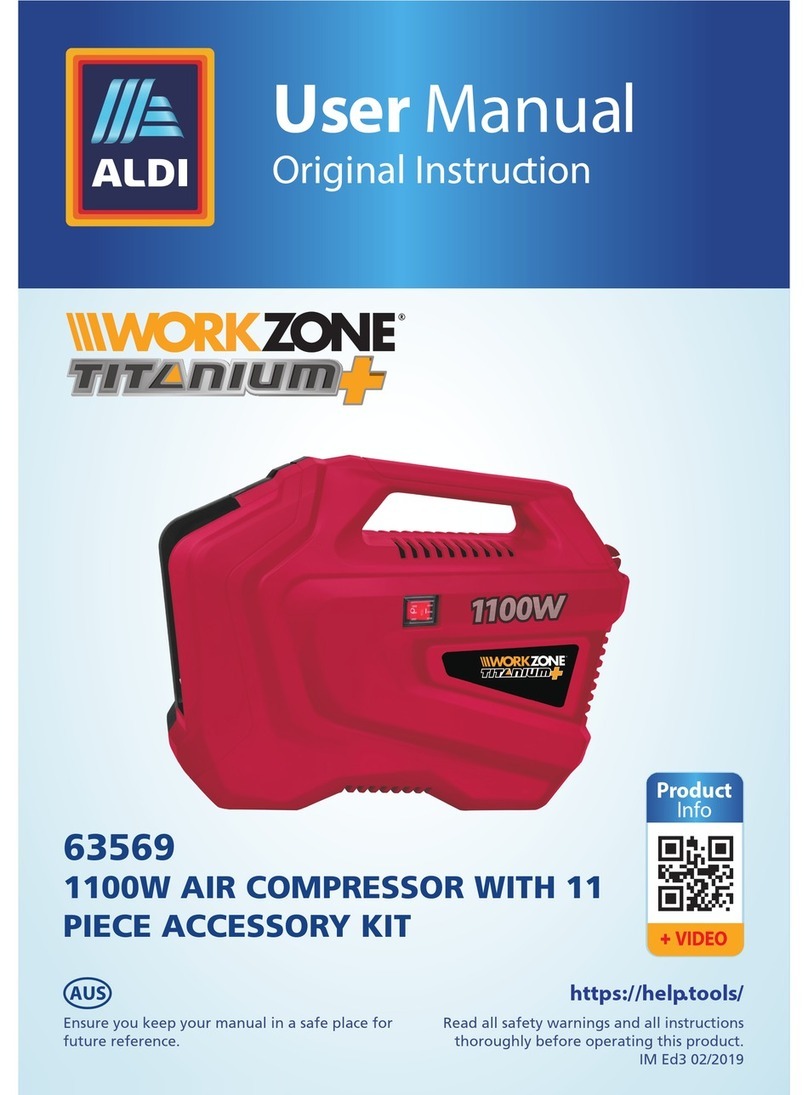
WORKZONE TITANIUM
WORKZONE TITANIUM PAP110 user manual