Variotech ENA3 User manual

Manual and data sheet for
ENA3 UCM Control
ENA3 UCM Control Manual Version 1.3
Date: 21.04.2017 page 1 of 12
Variotech GmbH, Gewerbeweg 5, 2230 Gänserndorf, Tel +43 2282 60310, https://variotech.com
Manual
UCM safety control in accordance
with EN81-20 5.6.7 - to prevent an
unintended car movement
Manual: ENA3 Version 1.3
All rights to this manual are owned by company Variotech GmbH.
Copies for internal purposes may be made.
In preparing this manual we have used the utmost care, but we cannot guarantee the accuracy of
this manual, because mistakes cannot be avoided 100%.
The contents of this manual can be changed anytime without notice. For improving information we
will be grateful.
This safety control is designed exclusively for use in a lift control system and may be used only as
specified in this manual.
This description contains the information necessary for the intended use of the controller.
Knowledge about the safety of the operating field 'Lift' is assumed.
These skills are fundamental for the understanding of this description.

Manual and data sheet for
ENA3 UCM Control
ENA3 UCM Control Manual Version 1.3
Date: 21.04.2017 page 2 of 12
Variotech GmbH, Gewerbeweg 5, 2230 Gänserndorf, Tel +43 2282 60310, https://variotech.com
INDEX OF CONTENTS:
General: ................................................................................................................................................... 3!
Legend: ................................................................................................................................................ 3!
Safety guidelines: ................................................................................................................................ 3!
Training of the installation and operation personnel: ........................................................................... 4!
Warranty and liability management: .................................................................................................... 4!
Intended use: ....................................................................................................................................... 4!
Protection against electric shock: ........................................................................................................ 4!
Technical description: .............................................................................................................................. 4!
Layout and Connections: ..................................................................................................................... 4!
Technical details: ................................................................................................................................. 5!
Environmental conditions: ................................................................................................................... 5!
Assembly / Fastening: ......................................................................................................................... 5!
Connections and terminal description: ................................................................................................ 5!
Displays, signal transducer and switch: ............................................................................................... 6!
Optimization of the number of necessary traveling cable wires: ......................................................... 7!
Commissioning: ....................................................................................................................................... 8!
Function test UCM-error: ......................................................................................................................... 8!
Actual testing (UCM error tests) .......................................................................................................... 8!
Effects of UCM-error tests: .................................................................................................................. 8!
UCM-error-reset: ................................................................................................................................. 9!
Diagnostic-input ................................................................................................................................... 9!
Error detection: ...................................................................................................................................... 10!
Possible errors: .................................................................................................................................. 10!
Concept for possible error detection and error prevention: ............................................................... 10!
Plausibility check: (Testing of the correct function) ........................................................................... 10!
Self-test of outputs: ............................................................................................................................ 11!
Display the type of error: ................................................................................................................... 11!
Error-Reset: ....................................................................................................................................... 11!
Maintenance: ......................................................................................................................................... 12!
Disposal and Recycling: ........................................................................................................................ 12!
Included in delivery: ............................................................................................................................... 12!
Ordering information and spare parts: ................................................................................................... 12!

Manual and data sheet for
ENA3 UCM Control
ENA3 UCM Control Manual Version 1.3
Date: 21.04.2017 page 3 of 12
Variotech GmbH, Gewerbeweg 5, 2230 Gänserndorf, Tel +43 2282 60310, https://variotech.com
General:
The safety control ENA3 is destined for use in safety circuits by a lift.
It consists of a fail-safe control module and proper sensors or magnetic switches. With an open safety
circuit ENA3 performs a self-test every 20th drive. A new drive is not allowed until the end of this test.
(see document ENA3 self test-timing)
The activation of the brake actuators and a control input to verify the correct operation of the actuators
are implemented in the control module.
The (brake) actuators themselves are not part of this safety control or the description but must be
installed on-site at the lift.
Those stopping brake actuators can be used, which have been examined in accordance with the
requirements of EN81-20 and are able to stop the lift within the required distance.
These include examined traction sheave brake, safety gears in combination with an overspeed
governor rope brakes, guide rail brakes and safety valves that an EN81-20/50 type examination have
been subjected.
The software in the safety control is factory tested and sealed and can not be modified or changed in
any way.
Legend:
Particularly important information in the manual are identified as follows:
DANGER! + WARNING!
This notice must be strictly observed. The sign warns of imminent danger,
which can cause serious injury and death.
ATTENTION!
This note indicates attention to a hazard and informs of appropriate precautions
to prevent minor injuries and property damages.
IMPORTANT! - INFO!
This note presents situations that can lead to damage of equipment or facilities,
and provides tips for proper application and also provides information on key
passages and other special features.
Safety guidelines:
The safety instructions are an important part of the operating manual.
In consequence of non-compliance of the instructions, all warranty claims and
warranties, as well as potential liability claims are lost. Moreover all regulations
on accident prevention for lifts must be observed. All local rules must be taken
into account to prevent damage due to improper handling with voltages and
currents. Especially concerning protection measure and correct earthing.

Manual and data sheet for
ENA3 UCM Control
ENA3 UCM Control Manual Version 1.3
Date: 21.04.2017 page 4 of 12
Variotech GmbH, Gewerbeweg 5, 2230 Gänserndorf, Tel +43 2282 60310, https://variotech.com
Training of the installation and operation personnel:
The operator may only use people for installation and commissioning, which have
the basic rules of accident prevention and safety knowledge and have read and
understood the safety instructions in this manual.
ESD: The operating personnel must ensure that the device is not damaged by an
electrostatic charge / discharge during installation / replacement. A direct contact
with the board / electronic components should be avoided or suitable protective
measures should be taken.
Warranty and liability management:
Warranty and liability claims will be lost if the control is not used as intended or if
any damage due to non-observance of the operating instructions or if the
installation and operating personnel have not been trained properly.
Intended use:
The application of ENA3 safety controls are provided solely lift systems.
The control may not be used in of other systems or particular in industrial plants.
The safety control ENA3 may only be used for the case defined in EN81-20 5.6.7,
to prevent of an unintendend movement of the car from a standstill.
Protection against electric shock:"
The safety control ENA3 must be installed in a grounded or protective insulated
control box.
Technical description:
Layout and Connections:
Variotech GmbH
ENA3 control
Return contactor
safety circuit
LED “S”
Linking to safety
circuit device
Integration into
safety circuit
switching
UCM-brake actuator
fuse T2,5A
1
2
3
4
5
6
7
8
9
LED “ZONE”
LED „µP“
LED „µP“
LED „FB“
Connection
for
feedback switch
+24V supply
-24V supply
protective earth
10
11
12
13
14
15
16
17
Magnet switch
Magnet switch

Manual and data sheet for
ENA3 UCM Control
ENA3 UCM Control Manual Version 1.3
Date: 21.04.2017 page 5 of 12
Variotech GmbH, Gewerbeweg 5, 2230 Gänserndorf, Tel +43 2282 60310, https://variotech.com
Technical details:
Connection: plug-in terminals, no confusion because different numbers of poles.
The terminals are designed for a max. conductor cross section 1 mm² with sleeve, or 1.5 mm² without
sleeve.
The maximum cable length for the safety circuit tapping is limited to a maximum of 200m, in order to
prevent malfunction due to coupling.
If a cable length> 200m is required, this must be additionally protected by suitable measures.
All other cables are not limited in their length.
Connection cables must have a minimum cross-sectional of 0.75 mm², except the magnetic switch.
cable length: there are no prescribed limits
The cables must be routed so that it can come to no damage during operation. (Protected installation).
Shielded cables are not necessary.
Safety Integrity Level: SIL2
Requirements: EN81-20 5.6.7,
EN 13849 part1+part2
EN 61508 part1 to part7,
ISO 22201,
EN12015, EN12016
System response times: 50ms - safety circuit on
Terminal 12/13,
20ms - no monitoring of the
safety circuit (terminal 12/13 free)
Operating ambient temperature: 5°C + 40°C
Humidity (no condensation) < 95 %
Storage temperature: – 25°C + 70°C
Dimensions: 10cm x 10cm x height 7cm
Fatigue strength: according EN81-50
Resistance to shock: according EN81-50
Weight: 400g
Environmental conditions:
The ENA3 security control is designed so that it pollutes the environment as little as possible. It emits
no pollutants and does not contain environmentally harmful substances and consumes very little
power.
Assembly / Fastening:
Installation of security control should preferably be close to the elevator control. If more space is
available in the control box, a free DIN rail width of about 10cm is required. Possible is also mounting
on the car roof.
If there is no space available, it is possible to mount the unit nearby to the control box.
In that case the safety control ENA3 can be delivered in a special industrial plastic housing.
An assembly without housing is not allowed, because a case is required with a protection factor of at
least IP2x.
Connections and terminal description:
Terminals 1, 2, 3: Connection for magnet switches (door zone) according to the schematic
The door zone is defined in each station by means of 2 magnetic tapes.
The dimension of the door zone should correspond to the unlocking zone of the door, and therefore
should be of approximately flush to the top / bottom of each 10cm (20cm total).
Note: For encoders of safety circuits, the requirements of EN 81-50: 2014, 5.6.3.1.1 apply.
Terminals 4, 5, 6: Connection for a feedback contact of the braking device.
( UCM-approved traction sheave brake, or UCM-approved safety gear and over speed governor)

Manual and data sheet for
ENA3 UCM Control
ENA3 UCM Control Manual Version 1.3
Date: 21.04.2017 page 6 of 12
Variotech GmbH, Gewerbeweg 5, 2230 Gänserndorf, Tel +43 2282 60310, https://variotech.com
12
13
Relay contact
The braking system must be monitored.
When the lift is in the station the unit must be in inoperative position and the feedback contact should
be closed (NC contact). This also allows a detection of a line interruption.
However, if only one normally open contact (NO contact) is present it can also be used.
• A normally closed NC contact must be connected to terminal 5, 6
• A normally open contact NO contact must be connected to terminal 4, 5
• If no feedback contact is present, the terminals 5, 6 must be bridged.
Terminal 7 (PLUS), 8 (Minus): connection power supply 24V DC (+/- 10%)
Terminal 9: connection protected earth.
Terminal 10, 11: connection for safety circuit and safety circuit feedback
with wide input voltage range:
This input automatically adjusts to the applied voltage
in a range from 24V to 230V AC / DC.
Terminal 12, 13: Safety relay contact.
This contact is used to test a door zone bypass circuit of the door switches and
is integrated in series in the bypass. If no bypass circuit is present the terminals
12 and 13 remain free. When leaving the door zone the contact is opened so
that the door switch can be tested without any interference from the bypass
circuit. The relay contacts have a switching capacity of 3A, 250V.
Terminal 14, 15: Safety relay contact.
This contact will be integrated in the safety circuit according to the schematic
diagram and serves to switch off the lift on the UCM error. To protect the
contacts of the safety relay and thus to increase the reliability, a fuse in series
with the contacts was implemented directly on the board.
The fuse has a value of 2.5 A.
The relay contacts have a switching capacity of 3A, 250V.
Terminal 16, 17: Safety relay contact.
This contact is for switching off the UCM-braking system and should therefore be
integrated directly in the circuit of the braking device.
The relay contacts have a switching capacity of 3A, 250V.
Note: Assuming that a connected coil with a suitable protective diode (freewheeling diode) is
connected, the relay outputs (terminal 12/13, 14/15, 16/17) switch a maximum DC voltage up to
24VDC, 1A.
Displays, signal transducer and switch:
LEDs: To view certain operating conditions 6 LEDs are available.
• 2 LED labeled with "Zone"
The LED indicates when the car is in a door-zone.
If both LEDs are lighted the car is within the door zone, otherwise it is outside the door zone
If only one LED is lighted a magnetic switch is defective and must be replaced.
10
11
optocoupler
16
17
Relay contact
Relay contact
14
15

Manual and data sheet for
ENA3 UCM Control
ENA3 UCM Control Manual Version 1.3
Date: 21.04.2017 page 7 of 12
Variotech GmbH, Gewerbeweg 5, 2230 Gänserndorf, Tel +43 2282 60310, https://variotech.com
• 2 LED labeled with „µP“ indicate that the safety system is working properly.
The LEDs are usually lighted constantly.
Only after stopping at the level, the LEDs will flash for a few seconds to show that it tests the safety
relay.
If the LED is flashing all the time, an error occurred which is described in more detail in the section
"Displaying the type of error."
If only one LED is on, the safety control system is defective and must be replaced.
• 1 LED labeled with "FB" indicates the correct function of the feedback switch (braking device).
This LED should light when the car is stopped and the UCM-braking system has switched off.
If the LED is not lighted, the UCM-braking device or the switch must be checked.
• 1 LED labeled with "S" indicates when the safety circuit is activated (Door closed).
This LED must be lighted by closed and locked doors or rather closed safety circuit.
Piezo signal transducer (Buzzer):
• The Piezo buzzer is in normal operation without function.
However, if an error occurs the Piezo buzzer starts to beep - the same rate as the indicator of „µP“
LED
Reset button:
• This button has no function during normal operation.
It serves only to restart ENA3 safety control after an error. The button must be pressed briefly. If
the button is jammed or otherwise remains in the pressed state, the safety circuit will not come into
operation again.
Optimization of the number of necessary traveling cable wires:
Especially in the modernization of existing lifts, there is often a lack of free traveling cable wires.
The following 2 tables show the necessary number of traveling cable wires depending on which UCM-
brake actuator is used and where the ENA3 control is located.
Table 1: Shows the required number of traveling cable wires on the assumption that the safety control
is mounted at or near the lift control.
version A:
ENA3 safety control mounted nearby the lift control
At lift box
On the car
roof
Required
traveling
cable wires
Door zone switch
-
x
3
UCM brake actuator, and feedback contact
-
x
4
UCM brake actuator, and feedback contact
x
-
-
supply 24V DC
x
x
-
Safety circuit monitoring
x
-
-
Safety circuit shutdown
x
-
-
re-leveling: test and switch off the bridging of the safety
circuit
x
-
-
Table 2: Shows the required number of traveling cable wires on the assumption that the safety control is
located on the car roof.
Version B:
ENA3 safety control mounted nearby the lift control
at lift box
on the car
roof
required
traveling
cable wires
Door zone switch
x
-

Manual and data sheet for
ENA3 UCM Control
ENA3 UCM Control Manual Version 1.3
Date: 21.04.2017 page 8 of 12
Variotech GmbH, Gewerbeweg 5, 2230 Gänserndorf, Tel +43 2282 60310, https://variotech.com
UCM brake actuator, and feedback contact
x
-
4
UCM brake actuator, and feedback contact
-
x
-
supply 24V DC
x
x
-
Safety circuit monitoring
x
-
2 (1)
Safety circuit shutdown
x
-
2 (1)
re-leveling: test and switch off the bridging of the safety
circuit
x
-
2 (1)
Commissioning:
It is assumed that the magnet switch is properly installed and the
Door zone magnets were installed correctly.
The car must be in a door zone.
• Inspection of the correct mechanical fixation of the safety control
• Inspection of all connections and terminals
• Remove the orange plug and afterwards switch on the unit
• The 2 LEDs „Zone“ must be on (car at level)
• The 2 LEDs „µP“ must be on. Indicate that the safety system is working properly - no fault and all
relays are switched through.
• The LED „FB“ must be on. Indicates the correct function of the feedback switch (braking device).
• The LED „S“ must be on. Indicates when the safety circuit is activated. (Door closed).
• When safety circuit is open, the "S" LED must not light.
In the case of a negative test, one must assume a capacitive coupling in the safety circuit. This is to
be remedied on-site.
The orange plug must be connected again.
Now the lift can be tested.
All functions of the elevator controls should work properly.
Function test UCM-error:
Precondition for a meaningful review of the UCM function is a proper function of the lift itself and the
proper integration of ENA3 safety control.
Check before testing:
• After the correct installation of the ENA3 or pressing the reset button of the elevator
before the function test must make a Normal trip!
• All LEDs on the ENA3 safety control must be lighted.
• All connectors must be plugged correctly
Actual testing (UCM error tests)
• Disconnect the connector with the terminal numbers 10 and 11 (safety circuit).
• The "S" LED must switch off.
• Give a lift call.
• The car should be starting to move.
• As soon as the car leaves the door zone ENA-3 safety control initiates an emergency stop.
Effects of UCM-error tests:
• The car is located near the station with closed doors.
• The distance to the station depends on the effectiveness of the UCM-braking device.
• On the safety control ENA3 the LED „µP“ is flashing and the LED "FB" is lighted.
All other LEDs must be off.
• The LEDs "µP" will flash 2 times with a subsequent pause of about 4 seconds.

Manual and data sheet for
ENA3 UCM Control
ENA3 UCM Control Manual Version 1.3
Date: 21.04.2017 page 9 of 12
Variotech GmbH, Gewerbeweg 5, 2230 Gänserndorf, Tel +43 2282 60310, https://variotech.com
This is the signal for an UCM fault. The piezo buzzer beeps additional to the LED in the same rate.
• Check disconnection of safety circuit terminals (terminals 14, 15) and terminals of the brake
actuator (terminals 16, 17).
UCM-error-reset:
Pressing the reset button on the control board of the safety control clears the error and the lift should
be back in operation mode, as far as the UCM-brake actuator does not require additional steps.
(release safety gear, etc.)
The error cannot be deleted by switching the device off and on.
Diagnostic-input
The function of the UCM-brake actuator or UCM-safety valve is monitored by a diagnostic switch.
The contacts of this switch have to be connected to the diagnostic input of the ENA3 control.
A LED (FB) indicates the correct function.
When multiple switches on the brake actuator are monitored and included, multiple normally closed
contacts can be connected in series or normally open contacts can be connected parallel.
The diagnostic function of the switch can be simulated:
The ENA3 control has a LED (FB) which indicates the correct function of the unit.
If the UCM-brake actuator (brake, overspeed governor, safety valve, etc.) is in non-operating state
(lift stands still with activated brake actuator) the LED “FB” is on.
If the brake actuator is released, the LED switches off.
If there are dual circuit brakes, the function of the diagnostic switch is checked by releasing one part of
the brake. The LED must switch off and by releasing of the part brake the LED should go on again.
The second part of the brake should be tested too.
The instructions of the manufacturer of the UCM-brake actuators must be observed for proper testing
of the diagnostic switch.
The diagnostic switch can be configured as NO or NC contact:
Version: diagnostic switch is a normally closed contact (NC)
Diagnostics switch (NC) on terminal 5 and 6, terminal 4 stays free permanently.
Diagnostic switch as NC contact
Diagnostic switch
LED “FB”
Lift stands still,
UCM-brake actuator in non-operating state
Terminal 5 and terminal 6 are
connected by switch
lighted *
Lift moves
Terminal 5 and terminal 6 are not
connected by switch (because NC)
off
testing of the diagnostic switch,
then give a lift call
Wire from terminal 5 (or terminal 6)
must be disconnected.
off
After the end of drive the function of the
diagnostic switch is tested by ENA3 control.
LED “µP” flashes 3 times
Buzzer beeps 3 times.
off
The ENA3 control detects the error and switches off, thereby the lift is out of service.
Connect wire on terminal 5 or terminal 6 again.
Switch on the device again by pressing the reset-button.
Version: Diagnostic switch is a normally open contact (NO)
Diagnostics switch (NC) on terminal 4 and 5, make a permanently bridge from terminal 5 to terminal 6.

Manual and data sheet for
ENA3 UCM Control
ENA3 UCM Control Manual Version 1.3
Date: 21.04.2017 page 10 of 12
Variotech GmbH, Gewerbeweg 5, 2230 Gänserndorf, Tel +43 2282 60310, https://variotech.com
Diagnostic switch as NO contact
Diagnostic switch
LED “FB”
Lift stands still,
UCM-braking system in non-operating state
Terminal 4 and terminal 5 not
connected by switch
lighted *
Lift moves.
Terminal 4 and 5 connected by
switch (because NO)
off
testing of the diagnostic switch,
then give a lift call
Bridge between terminal 4 and
terminal 5.
off
After the end of drive the function of the
diagnostic switch is tested by ENA3 control.
The LED “µP” flashes 3 times.
Buzzer beeps 3 times.
off
The ENA3 control detects the error and switches off, thereby the lift is out of service.
Remove bridge between terminal 4 and terminal 5.
Switch on the device again by pressing the reset-button.
* If the brake actuator (e.g. coil) is not controlled (on/off) by the lift control and it rest in „on“ position
the LED „FB“ will not be lighted if the lift is in the station!.
Note: There are different types and designs of diagnostic switches on the various UCM-braking
devices. For proper use the manufacturer's instructions of the UCM-braking device must be observed.
This applies to UCM-brake actuators like dual-circuit brake, a limiter with safety gear, cable brake, etc.
as well as for hydraulic lifts with UCM safety valves.
If the UCM-brake actuator has no diagnostic switches or contacts available to connect to the ENA3
control, it can be assumed that the UCM-tested brake actuator already includes other equivalent ways
of self-monitoring. Thus, the terminals 5 and 6 must be bridged, that the ENA3 control will still operate!
Error detection:
The ENA3 safety control is responsible, for detecting a specific error ( UCM-error) and in the case of
an error, to initiate an immediate emergency stop of the lift.
The ENA3 safety control itself has no direct control function of the lift.
Possible errors:
• Error in the ENA3 safety control itself. Such an error is detected by the safety control itself and
always leads to a shutdown of the device, and thus the lift.
• Wiring errors at the inputs of the safety control are also detected and lead also to a shutdown.
• External wiring errors on the safe outputs of the safety control system must be detected during the
installation and must be corrected. The safety control must not be used until all wiring errors (no
missing or incorrect external connections) are corrected.
Concept for possible error detection and error prevention:
• Error indication by LEDs which are not lighted:
In normal operation and when the lift is in the station with closed doors, all LEDs on the board
should be lighted. It is therefore absolutely necessary to monitor the LEDs and in case of a not
lighted LED to find the cause of it.
• Detecting errors using the automatic testing of safety control:
If safety control detects an error, the „µP“ LED starts flashing and the piezo-buzzer starts beeping.
• Prevention of errors by suitable wiring management.
Errors in the output circuit are detected by a functional test.
Plausibility check: (Testing of the correct function)
• Redundant (twice arranged) transmitters and sensors for safety functions are subjected to an
examination for plausibility by ENA3 safety control. The functional test is carried out for all possible
combinations of the two transmitters. If a plausibility-error occurs the safety control shuts down
automatically.

Manual and data sheet for
ENA3 UCM Control
ENA3 UCM Control Manual Version 1.3
Date: 21.04.2017 page 11 of 12
Variotech GmbH, Gewerbeweg 5, 2230 Gänserndorf, Tel +43 2282 60310, https://variotech.com
• The feedback contacts of the brake actuator must be wired and evaluated properly, otherwise the
safety control would also shut down during the plausibility check.
Self-test of outputs:
• On power supply or after a reset, ENA3 performs a self test for the first 5 times when the car is in a
door zone with open safety circuit . After the first 5 trips the self-test is carried out periodically each
20th time.
The relays R1, R2, R3 switch during a test.
o With an open safety circuit (door opens) the test is carried out after about 3 seconds
o With a closed safety circuit the test is not performed
On a new drive the relay R4 switches quickly on/off upon exiting the door zone.
In case of pre-opening of doors it must be ensured that the brake has already fallen before the self-
test is performed.
• Disruptions of the peripheral wiring lead to the shutdown of the lift.
• Errors while switching of safety relay lead to the shutdown of the lift.
Display the type of error:
The ENA3 safety control detects different types of errors. It saves them and displays (report) them
visually and acoustically.
Only by pressing the ENA3 reset button it is possible to clear errors.
• Actual UCM error (unintended car movement).
If the lift is not in the door zone such an error will result in immediate shutdown of the lift.
ENA3 displays the error by 2-time blinking of the LED and peeping of the buzzer.
• Errors of the UCM-brake actuator or feedback contact.
This error will result in an immediate shutdown of the lift in the door zone.
ENA3 displays the error by 3-time blinking of the LED and peeping of the buzzer.
• Error in the microprocessor or in the electronic circuit.
This error will result in an immediate shutdown of the lift in the door zone.
ENA3 displays the error by 4-time blinking of the LED and peeping of the buzzer.
• Malfunction in the control or within an output relay.
This error will result in an immediate shutdown of the lift in the door zone.
ENA3 displays the error by 5-time blinking of the LED and peeping of the buzzer.
Cause of error
Error code
Troubleshooting
Actual UCM error UCM
2-time blinking of the LED
µP and peeping of a buzzer
Push ENA3 Reset button
Errors of the UCM-brake
actuator or feedback
contact
3-time blinking of the LED
µP and peeping of a buzzer
Check the brake actuator and the feedback
contact
Then push ENA3 Reset button
Error in the
microprocessor or in the
electronic circuit
4-time blinking of the LED
µP and peeping of a buzzer
Push ENA3 Reset button
If the error occurs again you have to
change the control unit
Error in the control or
within an output relay
5-time blinking of the LED
µP and peeping of a buzzer
Check the power supply of 24VDC!
Then push ENA3 Reset button.
If the error occurs again you have to
change the control unit.
Error of the magnetic
switches
6-time blinking of the LED
µP and beeping of the
buzzer
Check the magnet switches and if they
were installed correctly. Both magnetic
switches must always switch
simultaneously.
Error-Reset:
It is not possible to bring the unit back in operation (reset) by switching on and off the supply voltage.

Manual and data sheet for
ENA3 UCM Control
ENA3 UCM Control Manual Version 1.3
Date: 21.04.2017 page 12 of 12
Variotech GmbH, Gewerbeweg 5, 2230 Gänserndorf, Tel +43 2282 60310, https://variotech.com
The error is stored permanently. Only by pressing the reset button on the control board the error of the
UCM safety circuit will be cleared and the lift should get back in normal operation, as far as the UCM-
brake actuator does not require additional measures. (for example, release of safety gear, etc.)
Maintenance:
There are no direct services or maintenance measures necessary. The safety control must always be
kept clean and dry. It must be ensured that the safety control is replaced after an operating period of
10 years or 3.5 million drives because the specified product life cycle of the safety relay has been
reached or exceeded.
Disposal and Recycling:
Unusable or irreparable devices and devices which have exceeded their lifecycle have to be disposed
in accordance to the applicable waste disposal regulations for electronic waste. The plastic housing
can be disposed as residual waste.
Included in delivery:
The scope of delivery includes the safety control ENA3, the manual and two special magnetic switches
(Encoder Typ C1511FDA0300S) for monitoring of the door zone.
The ENA3 safety control will be delivered in a plastic housing which can be fixed on a DIN rail and
should be installed in the control box of the lift.
The safety control system needs a power supply of 24 VDC (+ / - 10%).
On request, the necessary magnetic tape (20cm per stop), a power supply for a supply voltage of
115V to 230V can be delivered as well.
In addition the unit can be installed and delivered in an industrial plastic housing (IP65).
Ordering information and spare parts:
Title
Description
Part number
ENA3 Control 24V incl.
magnetic switches
Mounted in a plastic housing for DIN rail
mounting with needed magnet switches
ENA3_V2MS
ENA3 Control 24V excl.
magnetic switches
Mounted in a plastic housing for DIN rail
mounting with needed magnet switches
ENA3_V2XX
suitable industrial box
IP65
Plastic housing with transparent cover
175x150x80
NSYTBS19168T
ENA3 Magnetic switches
2x monostable magnetic switches
(redundant version)
ENA3-MS-RE2
Magnetic tapes
for door zone 20cm
ENA3-MAG20
Power Supply 110V to
230V
DIN rail power supply
ENA3-MDR-6024
Fixation kit for magnetic
tapes
For every door zone 20 cm
2 tapes per stop are necessary
ENA3-MAG-BEF
ENA3 with emergency
power supply
Consists of an ENA3 control device and ENA3-
NSE emergency power supply and extra
functions to supply power to an UCM brake
actuator which needs to be supplied during
power failure (f.e. speed governer).
ENA3-NSE-BOX








Table of contents
Popular Controllers manuals by other brands
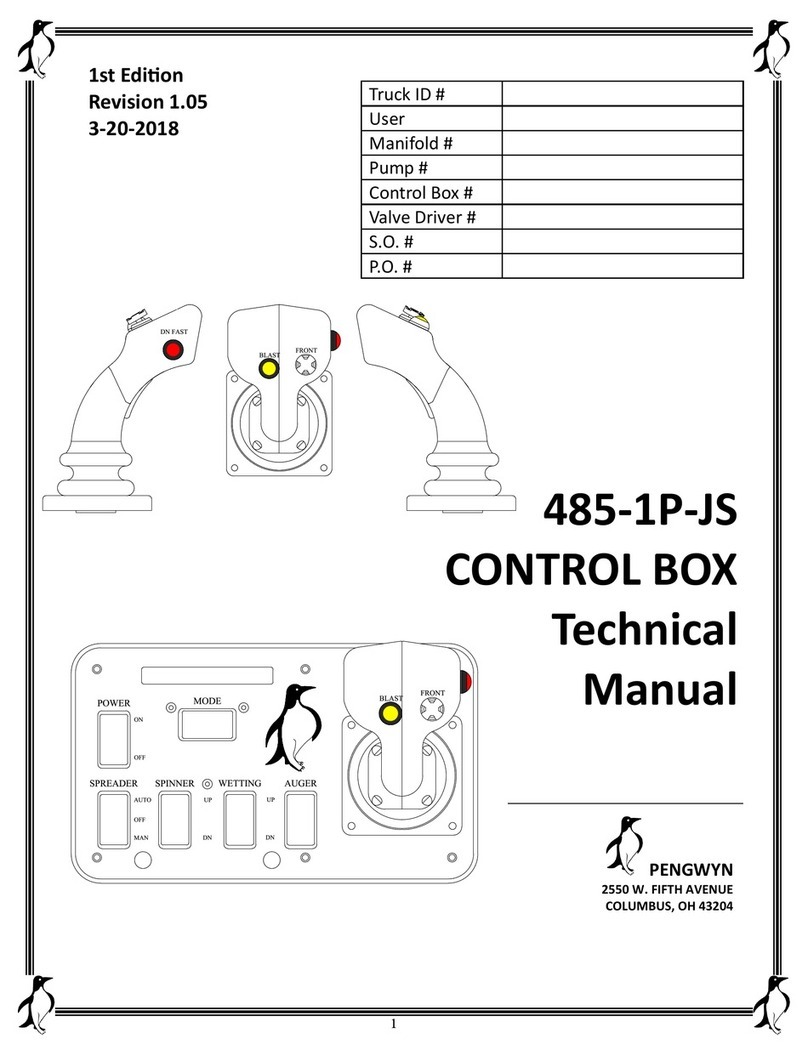
PENGWYN
PENGWYN 485-1P-JS Technical manual
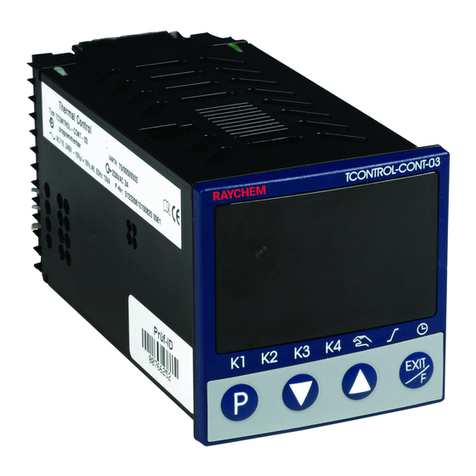
nVent RAYCHEM
nVent RAYCHEM TCONTROL-CONT-03 OPERATING AND INSTALLATION Manual
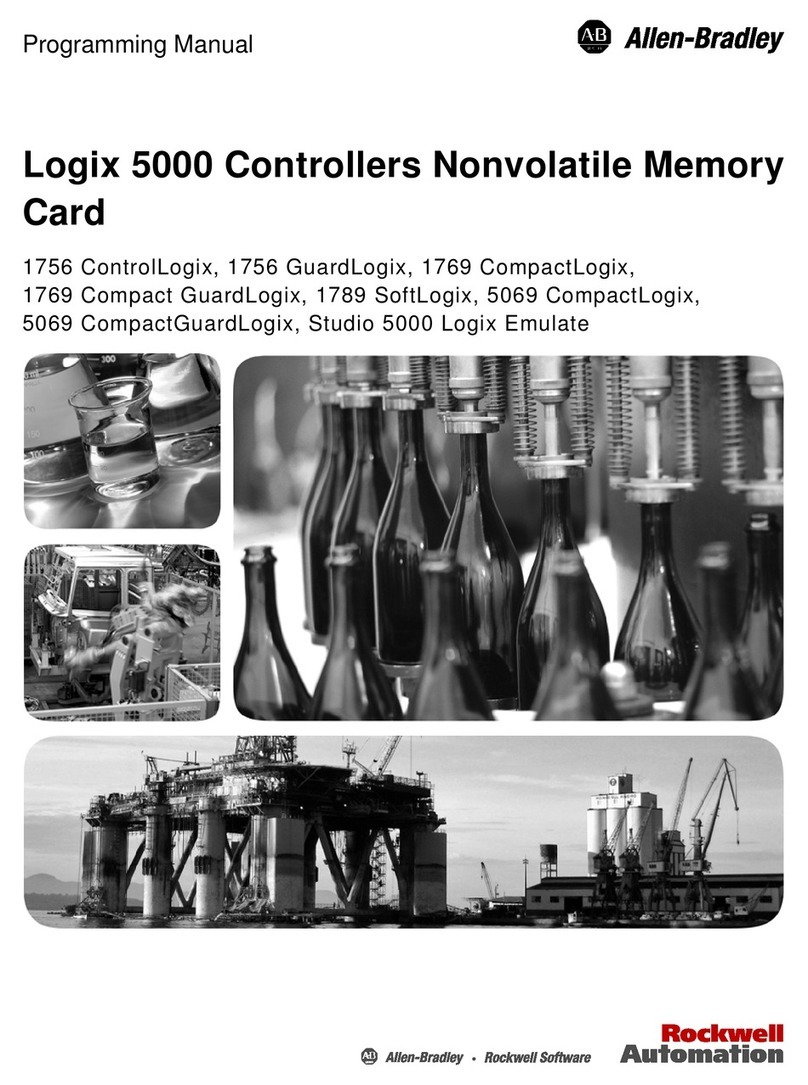
Allen-Bradley
Allen-Bradley Studio 5000 Logix Emulate Programming manual
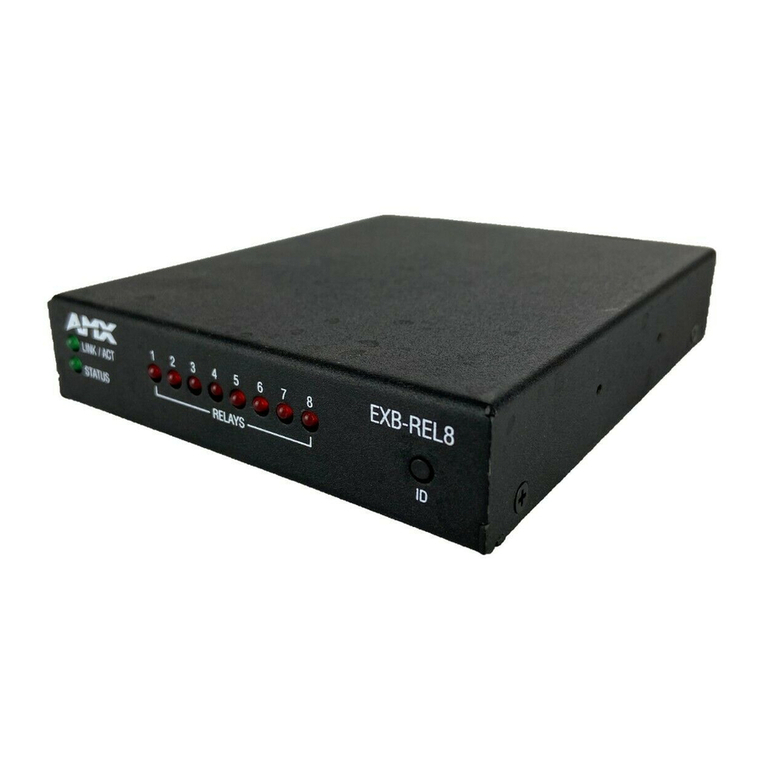
AMX
AMX AXB-REL8 instruction manual
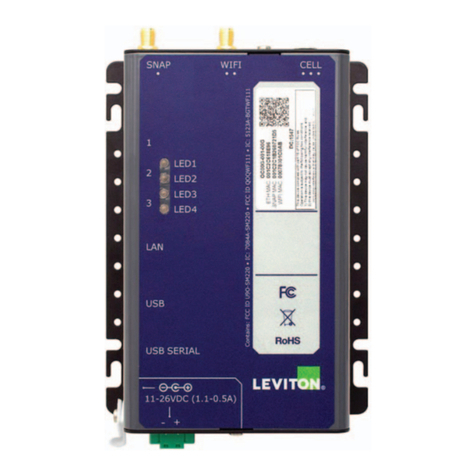
Leviton
Leviton NorthStar Site Controller user guide
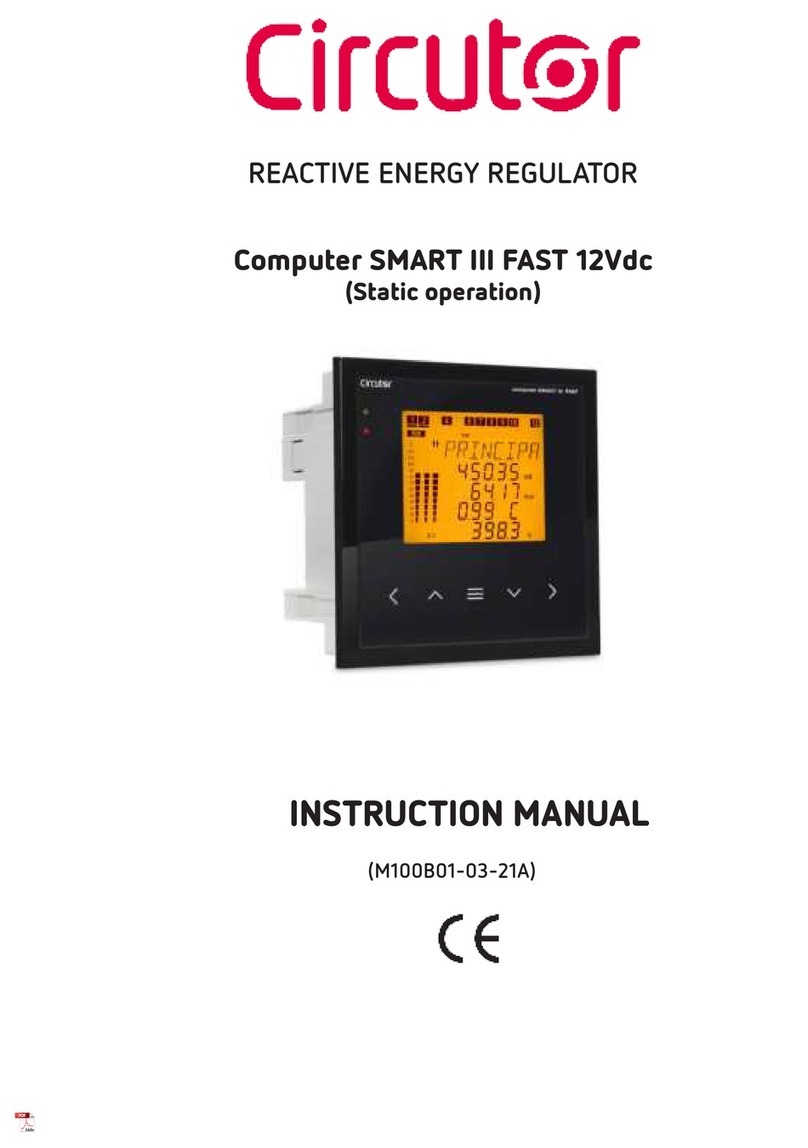
Circutor
Circutor Computer SMART III FAST 12Vdc instruction manual