Vestax WRX-2000 Installation guide


2
TABLE OF CONTENTS
Section 1 - History
Section 2 -Basics
2.1 Difference VRX-Recording Laces
2.2 Mastering
2.3 General
Section 3 – Basic VRX-2000 Set-up and Components
3.1 Set-up
3.2 Handling
3.3 Cutting Head
3.4 Tracking Arm
3.5 Stylus & Heater Life
3.6 Blank Vinyl
Section 4 – Description of VRX-2000 Components
4.1 Top Panel
4.2 Rear View
4.3 Cutting Head Section
Section 5 --Technical Description of VRX-2000
Section 6 – Assembly and Set-up
6.1 Platter Assembly
6.2 Ioniser Assembly
6.3 Tracking Arm/Counter Weight Assembly
6.4 Cutting Stylus Assembly
6.5 Cutting Head Assembly
Section 7 – Final Adjustments
7.1 Stylus pressure Adjustment
7.2 General Adjustment
Section 8– Recording Procedure
Section 9 – Playback
Section 10 – Troubleshooting
10.1 Step by Step
10.2 Start Recording
10.3 Noise
10.4 Distortion
Section 11 - Copyright Issue

3
VESTAX VRX-2000 CUTTING SEMINAR
Section 1 History
Up to now it only was possible to produce vinyl’s with big machines and a room full of equipment. The cost was
tremendous
The new VRX-System now enables a musician to produce his own music on a vinyl in a very short time and
without the necessity of. having a room full of recording equipment.
Also it is possible to perform a recording without having studied this subject or working for several years
with such a equipment.
However working with the VRX-System also technical knowledge and understanding as well as a sufficient
practice is necessary.
This introduction to the VRX recording system will
show you how to use the machine to record music
direct on a vinyl .
You will be guided through all necessary
setups, adjustments and cutting procedures to
create your own vinyl.
As the VRX is an analog machine like a
musical instrument your success depends very
much on your patience to learn and to
practise as well as on your musical understanding.
We often compare this VRX machine with a car.
We can show how to operate this machine
but you have to drive yourself. If you will
become an excellent driver depends on
you, your practice your patience and your skills.
SECTION 2 Basics
The VRX-2000 will give you superb results in the making of long-lasting vinyl records. To achieve such results,
please remember that the mastering process of vinyl records requires skill and a basic understanding of
complicated audio waveforms.
Cutting vinyl from a cassette-based multi-track recording or a stereo cassette recorder should prove to be
straightforward, as the frequency response of cassette-based music is not as intense as that of a CD.
Cutting from professionally mastered CDs that have good equalization and compression should also give
excellent results.
However, recording from some CDs (for example, CDs from home studio set-ups) may provide difficulties. This
is due to the fact that these recordings sometimes have very wide frequency ranges, and have not been
prepared professionally for mass-production or broadcast.
PLEASE
allways refer to the following pages to understand the difference between a big Lace and the VRX-2000.
2.1 VRX-recording

HE AD F R E QUE NC Y E QUAL IS ATION
2.1 VRX-2000RECORDING
The VR X-2000 is an innovative machine for the experienced professional musician.
When us ed with proper training and knowledge, your ability to produce unique, high
quality recordings with the warmth of vinyl is greatly improved.
Although the V R X-2000 is comparable to standard mas ter recording laces (s uch as the
Neuman) there are a number of important differences to be aware of. Two very
important issues to consider are;
HE AD F R E QUE NC Y E QUA L IS ATION
The manner by which the C utting Head reacts to various frequencies will affect the
final output. B asically, the C utting Head is like a very s mall yet powerful speaker
when it reacts to various sound frequencies. (R efer to fig.1& fig.2) E xtreme
frequencies will caus e it to move rather s everely, with that movement being further
reflected in the sound recorded.
G R OOV E P IT C H
-50
-40
-30
-20
-10
0
10
20
30
0 100Hz 1kHz 10kHz
[dB ]
fig.1 : C UT T ING HE AD F R E QUE NC Y R E S P ONS E NE UMANN S x74
V R X-2000 3 B and E Q
NE UMANN Motion F eedback
VR X-2000 C onstant P itch
NE UMANN Variable P itch
950Hz
-50
-40
-30
-20
-10
0
10
20
30
0 100Hz 1kHz 10kHz
[dB ]
fig.2 : C UT T ING HE AD FR E QUE NC Y R E S P ONS E VE S T A X VR X-2000
Though both machines can tolerate such extreme sounds, the way in which they are
handled is completely different. T he proces s of compens ating for these extremes
(peaks & troughs), namely E qualization, involves the flattening / correction of the
incoming curve s ignal. The method by which the Neuman(fig.3) and the VR X-
2000(fig.4) adjust curves is very different. On a big powerful machine, any extreme
incoming signals are compens ated for with an inverted signal, the res ult being a true
sound with a flat signal.(fig.5) This system of compens ation is called motion feedback
and as mentioned above, is used exclusively in large expensive recording lace
systems like the Neuman. T he V R X-2000, however, utilizes a standard graphic E Q
system to compensate for extreme incoming signal curves. T his system is aurally
difficult and requires hours of practice and experimentation to get it perfect over and
over again.
fig.3 : C UT T ING HE AD F R E QUE NC Y R E S P ONS E NE UMANN S x74
950Hz
-50
-40
-30
-20
-10
0
10
20
30
0 100Hz 1kHz 10kHz
[dB ]
950Hz
-50
-40
-30
-20
-10
0
10
20
30
0 100Hz 1kHz 10kHz
[dB ]
cutting drive amp
cutting head
input
driving coil
feadback coil
fig.5 : MOT ION F E E DB AC K C IR C UIT
fig.4 : C UT T ING HE AD FR E QUE NC Y R E S P ONS E VE S TAX VR X-2000
VR X-2000
Advantages
Advantages
* S mall S ys tem
* No cooling s ys tem is needed
* C an us e a small power amplifier
Disadvantages
Disadvantages
* R ecording level is not perfectly flat
* Difficult to adjust the E Q to get a great sound
* T he recorders E Q, needs to be adjusted profess ionally.
* P rofes sional service is needed to replace or tune up
selected parts .
NE UMA NN
* V ery flat frequency response specifications
* True sounding final output
* Needs a very powerful amplifier (600W)
* Head coil gets extremely hot (210•‹C ) and needs to be
cooled down using a helium gas cooling system
* V ery expensive, heavy, high-end professional use only
sound recording device.
Although the V R X-2000 differs greatly from the big machines , such as the Neumann,
attaining high quality recordings time and time again can be eas ily achieved with s tudy
and pers everance. F urthermore, acknowledging the above differences will help you to
unders tand the proces s by which to grasp your pre cutting needs, thereby facilitating
eas ier high end results.
ATT AINING T HE B E S T C UT AG A IN AND A G AIN.
To ensure that your results live up to your expectations of sound quality please follow
the steps below carefully until you have become a consistent producer or amazing,
unique recordings.(fig.6)
C D/MD/P C
comp/limitter
mas ter
comp/limitter
G E 33S A E Q MIXE R AMP
E Q
detec tor loop
input output
fig.5 : VR X-2000 R E C OME NDE D S E T UP
S et up the cutting stylus, making s ure that its position is correct and s ecure.
C heck the stylus connection and pres sure.
Warm up to the heating coil based on your room temperature and desired sound
style. (Y our genre - Jazz, hardcore - will require slightly to greatly different
temperatures )
P erform a one-minute tes t cut to check for irregularities in cutting quality.
Ins pect the cutting blank and the residue (from cutting) for cracks and cutting
precision. T IP : Y ou should watch the "cutting-tip"(offcut) to see that the cutting is
precisely and smoothly.
Assuming that the above check has proved positive, this check is to allow you to
set up for your final recording correctly.
C onnect your input s ource directly to the V R X -2000 - DE F F INAT E LY NO E Q - T his
will help you s ee how your V R X-2000 records and allow you to understand its
recording character.
Make a sample recording - NO E Q - for a few minutes. The longer the recording
the more easily it will be for you to adjust your E Q later to ensure a superior final
cut.
P lay back your recording through an E Q making adjustments to the sound (E Q)
according to your style, tas tes or target result.
Thes e E Q adjustments, that you have made on the playback of the test, are what
will ensure that the final cut is flat and true to your input source.
A frequency range of between 200Hz - 600Hz is the recommended range that will
give you warmth and s ens itivity whilst still being clearly balanced.
Y OUR C UT T ING LE VE L S HOULD NOW BE S E T T O MINIMIS E E XTR E ME 'OVE R '
P E AK S . Use of the input meter on the V R X-2000 is recommended in this case.
This balance is important so as to minimize any chance of damage to your head
and the heating coil of the VR X-2000.
R econnect the V R X-2000 to your input source through your E Q.
E nsure that your input sound is well balanced and the extreme peaks compensated
for.
Make your final cut.
(1) TE S T C UT - T R IAL C UT
A.
B .
C .
D.
E .
(2) S T R AIG HT C UT - S OUND INP UT C HE C K & E Q
A.
B .
C .
(3) P L AY B A C K - E Q ADJ US TME NT
A.
B .
C .
D.
(4) F INA L C UT - UNIQ UE QUA L IT Y E ND R E S ULT S
A.
B .
C .
**NOT E -- T he taking of notes will facilitate an improved unders tanding of the
recording process and help speed up your recording proces s. Thes e notes will also
allow you to perfect your proces s over and over again.

HE AD F R E QUE NC Y E QUA L IS ATION
VR X-2000 R E C OR DING
The VR X-2000 is an innovative machine for the experienced profess ional mus ician.
When us ed with proper training and knowledge, your ability to produce unique, high
quality recordings with the warmth of vinyl is greatly improved.
Although the VR X-2000 is comparable to standard mas ter recording laces (such as the
Neuman) there are a number of important differences to be aware of. Two very
important issues to consider are;
HE AD F R E QUE NC Y E QUA L IS AT ION
The manner by which the C utting Head reacts to various frequencies will affect the
final output. B asically, the C utting Head is like a very small yet powerful speaker
when it reacts to various s ound frequencies. (R efer to fig.1& fig.2) E xtreme
frequencies will caus e it to move rather s everely, with that movement being further
reflected in the sound recorded.
G R OOV E P IT C H
-50
-40
-30
-20
-10
0
10
20
30
0 100Hz 1kHz 10kHz
[dB ]
fig.1 : C UT T ING HE AD F R E QUE NC Y R E S P ONS E NE UMANN S x74
V R X-2000 3 B and E Q
NE UMANN Motion F eedback
VR X-2000 C onstant P itch
NE UMANN Variable P itch
950Hz
-50
-40
-30
-20
-10
0
10
20
30
0 100Hz 1kHz 10kHz
[dB ]
fig.2 : C UT T ING HE AD F R E QUE NC Y R E S P ONS E VE S T AX VR X-2000
Though both machines can tolerate such extreme sounds, the way in which they are
handled is completely different. T he proces s of compens ating for these extremes
(peaks & troughs), namely E qualization, involves the flattening / correction of the
incoming curve s ignal. The method by which the Neuman(fig.3) and the VR X-
2000(fig.4) adjust curves is very different. On a big powerful machine, any extreme
incoming signals are compens ated for with an inverted signal, the res ult being a true
sound with a flat signal.(fig.5) This system of compens ation is called motion feedback
and as mentioned above, is used exclusively in large expensive recording lace
systems like the Neuman. T he V R X-2000, however, utilizes a standard graphic E Q
system to compensate for extreme incoming signal curves. T his system is aurally
difficult and requires hours of practice and experimentation to get it perfect over and
over again.
fig.3 : C UT T ING HE AD F R E QUE NC Y R E S P ONS E NE UMANN S x74
950Hz
-50
-40
-30
-20
-10
0
10
20
30
0 100Hz 1kHz 10kHz
[dB ]
950Hz
-50
-40
-30
-20
-10
0
10
20
30
0 100Hz 1kHz 10kHz
[dB ]
cutting drive amp
cutting head
input
driving coil
feadback coil
fig.5 : MOT ION F E E DB AC K C IR C UIT
fig.4 : C UT T ING HE AD F R E QUE NC Y R E S P ONS E VE S T AX VR X-2000
VR X-2000
Advantages
Advantages
* S mall S ys tem
* No cooling s ys tem is needed
* C an us e a small power amplifier
Disadvantages
Disadvantages
* R ecording level is not perfectly flat
* Difficult to adjust the E Q to get a great sound
* T he recorders E Q, needs to be adjusted profess ionally.
* P rofes sional service is needed to replace or tune up
selected parts .
NE UMA NN
* V ery flat frequency response specifications
* True sounding final output
* Needs a very powerful amplifier (600W)
* Head coil gets extremely hot (210•‹C ) and needs to be
cooled down using a helium gas cooling system
* V ery expensive, heavy, high-end professional use only
sound recording device.
Although the V R X-2000 differs greatly from the big machines , such as the Neumann,
attaining high quality recordings time and time again can be easily achieved with s tudy
and pers everance. F urthermore, acknowledging the above differences will help you to
unders tand the proces s by which to grasp your pre cutting needs, thereby facilitating
eas ier high end results.
ATT AINING T HE B E S T C UT AG AIN A ND AG AIN.
To ensure that your results live up to your expectations of sound quality please follow
the steps below carefully until you have become a consistent producer or amazing,
unique recordings.(fig.6)
C D/MD/P C
comp/limitter
mas ter
comp/limitter
G E 33S A E Q MIXE R AMP
E Q
detec tor loop
input output
fig.5 : VR X-2000 R E C OME NDE D S E T UP
S et up the cutting stylus, making s ure that its position is correct and s ecure.
C heck the stylus connection and pres sure.
Warm up to the heating coil based on your room temperature and desired sound
style. (Y our genre - Jazz, hardcore - will require slightly to greatly different
temperatures )
P erform a one-minute tes t cut to check for irregularities in cutting quality.
Ins pect the cutting blank and the residue (from cutting) for cracks and cutting
precision. T IP : Y ou should watch the "cutting-tip"(offcut) to see that the cutting is
precisely and smoothly.
Assuming that the above check has proved positive, this check is to allow you to
set up for your final recording correctly.
C onnect your input s ource directly to the V R X -2000 - DE F F INAT E LY NO E Q - T his
will help you s ee how your V R X-2000 records and allow you to understand its
recording character.
Make a sample recording - NO E Q - for a few minutes. The longer the recording
the more easily it will be for you to adjust your E Q later to ensure a superior final
cut.
P lay back your recording through an E Q making adjustments to the sound (E Q)
according to your style, tas tes or target result.
Thes e E Q adjustments, that you have made on the playback of the test, are what
will ensure that the final cut is flat and true to your input source.
A frequency range of between 200Hz - 600Hz is the recommended range that will
give you warmth and s ens itivity whilst still being clearly balanced.
Y OUR C UT T ING LE VE L S HOULD NOW BE S E T T O MINIMIS E E XTR E ME 'OVE R '
P E AK S . Use of the input meter on the V R X-2000 is recommended in this case.
This balance is important so as to minimize any chance of damage to your head
and the heating coil of the VR X-2000.
R econnect the V R X-2000 to your input source through your E Q.
E nsure that your input sound is well balanced and the extreme peaks compensated
for.
Make your final cut.
(1) TE S T C UT - TR IAL C UT
A.
B .
C .
D.
E .
(2) S T R AIG HT C UT - S OUND INP UT C HE C K & E Q
A.
B .
C .
(3) P L AY B A C K - E Q ADJ US TME NT
A.
B .
C .
D.
(4) F INA L C UT - UNIQ UE QUA L IT Y E ND R E S ULT S
A.
B .
C .
**NOT E -- T he taking of notes will facilitate an improved unders tanding of the
recording process and help speed up your recording proces s. Thes e notes will also
allow you to perfect your proces s over and over again.

HE AD F R E QUE NC Y E QUA L IS ATION
VR X-2000 R E C OR DING
The VR X-2000 is an innovative machine for the experienced profess ional mus ician.
When us ed with proper training and knowledge, your ability to produce unique, high
quality recordings with the warmth of vinyl is greatly improved.
Although the VR X-2000 is comparable to standard mas ter recording laces (such as the
Neuman) there are a number of important differences to be aware of. Two very
important issues to consider are;
HE AD F R E QUE NC Y E QUA L IS AT ION
The manner by which the C utting Head reacts to various frequencies will affect the
final output. B asically, the C utting Head is like a very small yet powerful speaker
when it reacts to various s ound frequencies. (R efer to fig.1& fig.2) E xtreme
frequencies will caus e it to move rather s everely, with that movement being further
reflected in the sound recorded.
G R OOV E P IT C H
-50
-40
-30
-20
-10
0
10
20
30
0 100Hz 1kHz 10kHz
[dB ]
fig.1 : C UT T ING HE AD F R E QUE NC Y R E S P ONS E NE UMANN S x74
V R X-2000 3 B and E Q
NE UMANN Motion F eedback
VR X-2000 C onstant P itch
NE UMANN Variable P itch
950Hz
-50
-40
-30
-20
-10
0
10
20
30
0 100Hz 1kHz 10kHz
[dB ]
fig.2 : C UT T ING HE AD F R E QUE NC Y R E S P ONS E VE S T A X VR X-2000
Though both machines can tolerate such extreme sounds, the way in which they are
handled is completely different. T he proces s of compens ating for these extremes
(peaks & troughs), namely E qualization, involves the flattening / correction of the
incoming curve s ignal. The method by which the Neuman(fig.3) and the VR X-
2000(fig.4) adjust curves is very different. On a big powerful machine, any extreme
incoming signals are compens ated for with an inverted signal, the res ult being a true
sound with a flat signal.(fig.5) This system of compens ation is called motion feedback
and as mentioned above, is used exclusively in large expensive recording lace
systems like the Neuman. T he V R X-2000, however, utilizes a standard graphic E Q
system to compensate for extreme incoming signal curves. T his system is aurally
difficult and requires hours of practice and experimentation to get it perfect over and
over again.
fig.3 : C UT T ING HE AD F R E QUE NC Y R E S P ONS E NE UMANN S x74
950Hz
-50
-40
-30
-20
-10
0
10
20
30
0 100Hz 1kHz 10kHz
[dB ]
950Hz
-50
-40
-30
-20
-10
0
10
20
30
0 100Hz 1kHz 10kHz
[dB ]
cutting drive amp
cutting head
input
driving coil
feadback coil
fig.5 : MOT ION F E E DB AC K C IR C UIT
fig.4 : C UT T ING HE AD F R E QUE NC Y R E S P ONS E VE S T AX VR X-2000
VR X-2000
Advantages
Advantages
* S mall S ys tem
* No cooling s ys tem is needed
* C an us e a small power amplifier
Disadvantages
Disadvantages
* R ecording level is not perfectly flat
* Difficult to adjust the E Q to get a great sound
* T he recorders E Q, needs to be adjusted profess ionally.
* P rofes sional service is needed to replace or tune up
selected parts .
NE UMA NN
* V ery flat frequency response specifications
* True sounding final output
* Needs a very powerful amplifier (600W)
* Head coil gets extremely hot (210•‹C ) and needs to be
cooled down using a helium gas cooling system
* V ery expensive, heavy, high-end professional use only
sound recording device.
Although the V R X-2000 differs greatly from the big machines , such as the Neumann,
attaining high quality recordings time and time again can be easily achieved with s tudy
and pers everance. F urthermore, acknowledging the above differences will help you to
unders tand the proces s by which to grasp your pre cutting needs, thereby facilitating
eas ier high end results.
ATT AINING T HE B E S T C UT AG AIN A ND AG AIN.
To ensure that your results live up to your expectations of sound quality please follow
the steps below carefully until you have become a consistent producer or amazing,
unique recordings.(fig.6)
C D/MD/P C
comp/limitter
mas ter
comp/limitter
G E 33S A E Q MIXE R AMP
E Q
detec tor loop
input output
fig.5 : VR X-2000 R E C OME NDE D S E T UP
S et up the cutting stylus, making s ure that its position is correct and s ecure.
C heck the stylus connection and pres sure.
Warm up to the heating coil based on your room temperature and desired sound
style. (Y our genre - Jazz, hardcore - will require slightly to greatly different
temperatures )
P erform a one-minute tes t cut to check for irregularities in cutting quality.
Ins pect the cutting blank and the residue (from cutting) for cracks and cutting
precision. T IP : Y ou should watch the "cutting-tip"(offcut) to see that the cutting is
precisely and smoothly.
Assuming that the above check has proved positive, this check is to allow you to
set up for your final recording correctly.
C onnect your input s ource directly to the V R X -2000 - DE F F INAT E LY NO E Q - T his
will help you s ee how your V R X-2000 records and allow you to understand its
recording character.
Make a sample recording - NO E Q - for a few minutes. The longer the recording
the more easily it will be for you to adjust your E Q later to ensure a superior final
cut.
P lay back your recording through an E Q making adjustments to the sound (E Q)
according to your style, tas tes or target result.
Thes e E Q adjustments, that you have made on the playback of the test, are what
will ensure that the final cut is flat and true to your input source.
A frequency range of between 200Hz - 600Hz is the recommended range that will
give you warmth and s ens itivity whilst still being clearly balanced.
Y OUR C UT T ING LE VE L S HOULD NOW BE S E T T O MINIMIS E E XTR E ME 'OVE R '
P E AK S . Use of the input meter on the V R X-2000 is recommended in this case.
This balance is important so as to minimize any chance of damage to your head
and the heating coil of the VR X-2000.
R econnect the V R X-2000 to your input source through your E Q.
E nsure that your input sound is well balanced and the extreme peaks compensated
for.
Make your final cut.
(1) TE S T C UT - TR IAL C UT
A.
B .
C .
D.
E .
(2) S T R AIG HT C UT - S OUND INP UT C HE C K & E Q
A.
B .
C .
(3) P L AY B A C K - E Q ADJ US TME NT
A.
B .
C .
D.
(4) F INA L C UT - UNIQ UE QUA L IT Y E ND R E S ULT S
A.
B .
C .
**NOT E -- T he taking of notes will facilitate an improved unders tanding of the
recording process and help speed up your recording proces s. Thes e notes will also
allow you to perfect your proces s over and over again.

HE AD F R E QUE NC Y E QUA L IS ATION
VR X-2000 R E C OR DING
The VR X-2000 is an innovative machine for the experienced profess ional mus ician.
When us ed with proper training and knowledge, your ability to produce unique, high
quality recordings with the warmth of vinyl is greatly improved.
Although the VR X-2000 is comparable to standard mas ter recording laces (such as the
Neuman) there are a number of important differences to be aware of. Two very
important issues to consider are;
HE AD F R E QUE NC Y E QUA L IS AT ION
The manner by which the C utting Head reacts to various frequencies will affect the
final output. B asically, the C utting Head is like a very small yet powerful speaker
when it reacts to various s ound frequencies. (R efer to fig.1& fig.2) E xtreme
frequencies will caus e it to move rather s everely, with that movement being further
reflected in the sound recorded.
G R OOV E P IT C H
-50
-40
-30
-20
-10
0
10
20
30
0 100Hz 1kHz 10kHz
[dB ]
fig.1 : C UT T ING HE AD F R E QUE NC Y R E S P ONS E NE UMANN S x74
V R X-2000 3 B and E Q
NE UMANN Motion F eedback
VR X-2000 C onstant P itch
NE UMANN Variable P itch
950Hz
-50
-40
-30
-20
-10
0
10
20
30
0 100Hz 1kHz 10kHz
[dB ]
fig.2 : C UT T ING HE AD F R E QUE NC Y R E S P ONS E VE S T A X VR X-2000
Though both machines can tolerate such extreme sounds, the way in which they are
handled is completely different. T he proces s of compens ating for these extremes
(peaks & troughs), namely E qualization, involves the flattening / correction of the
incoming curve s ignal. The method by which the Neuman(fig.3) and the VR X-
2000(fig.4) adjust curves is very different. On a big powerful machine, any extreme
incoming signals are compens ated for with an inverted signal, the res ult being a true
sound with a flat signal.(fig.5) This system of compens ation is called motion feedback
and as mentioned above, is used exclusively in large expensive recording lace
systems like the Neuman. T he V R X-2000, however, utilizes a standard graphic E Q
system to compensate for extreme incoming signal curves. T his system is aurally
difficult and requires hours of practice and experimentation to get it perfect over and
over again.
fig.3 : C UT T ING HE AD F R E QUE NC Y R E S P ONS E NE UMANN S x74
950Hz
-50
-40
-30
-20
-10
0
10
20
30
0 100Hz 1kHz 10kHz
[dB ]
950Hz
-50
-40
-30
-20
-10
0
10
20
30
0 100Hz 1kHz 10kHz
[dB ]
cutting drive amp
cutting head
input
driving coil
feadback coil
fig.5 : MOT ION F E E DB AC K C IR C UIT
fig.4 : C UT T ING HE AD F R E QUE NC Y R E S P ONS E VE S T AX VR X-2000
VR X-2000
Advantages
Advantages
* S mall S ys tem
* No cooling s ys tem is needed
* C an us e a small power amplifier
Disadvantages
Disadvantages
* R ecording level is not perfectly flat
* Difficult to adjust the E Q to get a great sound
* T he recorders E Q, needs to be adjusted profess ionally.
* P rofes sional service is needed to replace or tune up
selected parts .
NE UMA NN
* V ery flat frequency response specifications
* True sounding final output
* Needs a very powerful amplifier (600W)
* Head coil gets extremely hot (210•‹C ) and needs to be
cooled down using a helium gas cooling system
* V ery expensive, heavy, high-end professional use only
sound recording device.
Although the V R X-2000 differs greatly from the big machines , such as the Neumann,
attaining high quality recordings time and time again can be easily achieved with s tudy
and pers everance. F urthermore, acknowledging the above differences will help you to
unders tand the proces s by which to grasp your pre cutting needs, thereby facilitating
eas ier high end results.
ATT AINING T HE B E S T C UT AG AIN A ND AG AIN.
To ensure that your results live up to your expectations of sound quality please follow
the steps below carefully until you have become a consistent producer or amazing,
unique recordings.(fig.6)
C D/MD/P C
comp/limitter
mas ter
comp/limitter
G E 33S A E Q MIXE R AMP
E Q
detec tor loop
input output
fig.5 : VR X-2000 R E C OME NDE D S E T UP
S et up the cutting stylus, making s ure that its position is correct and s ecure.
C heck the stylus connection and pres sure.
Warm up to the heating coil based on your room temperature and desired sound
style. (Y our genre - Jazz, hardcore - will require slightly to greatly different
temperatures )
P erform a one-minute tes t cut to check for irregularities in cutting quality.
Ins pect the cutting blank and the residue (from cutting) for cracks and cutting
precision. T IP : Y ou should watch the "cutting-tip"(offcut) to see that the cutting is
precisely and smoothly.
Assuming that the above check has proved positive, this check is to allow you to
set up for your final recording correctly.
C onnect your input s ource directly to the V R X -2000 - DE F F INAT E LY NO E Q - T his
will help you s ee how your V R X-2000 records and allow you to understand its
recording character.
Make a sample recording - NO E Q - for a few minutes. The longer the recording
the more easily it will be for you to adjust your E Q later to ensure a superior final
cut.
P lay back your recording through an E Q making adjustments to the sound (E Q)
according to your style, tas tes or target result.
Thes e E Q adjustments, that you have made on the playback of the test, are what
will ensure that the final cut is flat and true to your input source.
A frequency range of between 200Hz - 600Hz is the recommended range that will
give you warmth and s ens itivity whilst still being clearly balanced.
Y OUR C UT T ING LE VE L S HOULD NOW BE S E T T O MINIMIS E E XTR E ME 'OVE R '
P E AK S . Use of the input meter on the V R X-2000 is recommended in this case.
This balance is important so as to minimize any chance of damage to your head
and the heating coil of the VR X-2000.
R econnect the V R X-2000 to your input source through your E Q.
E nsure that your input sound is well balanced and the extreme peaks compensated
for.
Make your final cut.
(1) TE S T C UT - TR IAL C UT
A.
B .
C .
D.
E .
(2) S T R AIG HT C UT - S OUND INP UT C HE C K & E Q
A.
B .
C .
(3) P L AY B A C K - E Q ADJ US TME NT
A.
B .
C .
D.
(4) F INA L C UT - UNIQ UE QUA L IT Y E ND R E S ULT S
A.
B .
C .
**NOT E -- T he taking of notes will facilitate an improved unders tanding of the
recording process and help speed up your recording proces s. Thes e notes will also
allow you to perfect your proces s over and over again.

HE AD F R E QUE NC Y E QUA L IS ATION
VR X-2000 R E C OR DING
The VR X-2000 is an innovative machine for the experienced profess ional mus ician.
When us ed with proper training and knowledge, your ability to produce unique, high
quality recordings with the warmth of vinyl is greatly improved.
Although the VR X-2000 is comparable to standard mas ter recording laces (such as the
Neuman) there are a number of important differences to be aware of. Two very
important issues to consider are;
HE AD F R E QUE NC Y E QUA L IS AT ION
The manner by which the C utting Head reacts to various frequencies will affect the
final output. B asically, the C utting Head is like a very small yet powerful speaker
when it reacts to various s ound frequencies. (R efer to fig.1& fig.2) E xtreme
frequencies will caus e it to move rather s everely, with that movement being further
reflected in the sound recorded.
G R OOV E P IT C H
-50
-40
-30
-20
-10
0
10
20
30
0 100Hz 1kHz 10kHz
[dB ]
fig.1 : C UT T ING HE AD F R E QUE NC Y R E S P ONS E NE UMANN S x74
V R X-2000 3 B and E Q
NE UMANN Motion F eedback
VR X-2000 C onstant P itch
NE UMANN Variable P itch
950Hz
-50
-40
-30
-20
-10
0
10
20
30
0 100Hz 1kHz 10kHz
[dB ]
fig.2 : C UT T ING HE AD F R E QUE NC Y R E S P ONS E VE S T A X VR X-2000
Though both machines can tolerate such extreme sounds, the way in which they are
handled is completely different. T he proces s of compens ating for these extremes
(peaks & troughs), namely E qualization, involves the flattening / correction of the
incoming curve s ignal. The method by which the Neuman(fig.3) and the VR X-
2000(fig.4) adjust curves is very different. On a big powerful machine, any extreme
incoming signals are compens ated for with an inverted signal, the res ult being a true
sound with a flat signal.(fig.5) This system of compens ation is called motion feedback
and as mentioned above, is used exclusively in large expensive recording lace
systems like the Neuman. T he V R X-2000, however, utilizes a standard graphic E Q
system to compensate for extreme incoming signal curves. T his system is aurally
difficult and requires hours of practice and experimentation to get it perfect over and
over again.
fig.3 : C UT T ING HE AD F R E QUE NC Y R E S P ONS E NE UMANN S x74
950Hz
-50
-40
-30
-20
-10
0
10
20
30
0 100Hz 1kHz 10kHz
[dB ]
950Hz
-50
-40
-30
-20
-10
0
10
20
30
0 100Hz 1kHz 10kHz
[dB ]
cutting drive amp
cutting head
input
driving coil
feadback coil
fig.5 : MOT ION F E E DB AC K C IR C UIT
fig.4 : C UT T ING HE AD F R E QUE NC Y R E S P ONS E VE S T AX VR X-2000
VR X-2000
Advantages
Advantages
* S mall S ys tem
* No cooling s ys tem is needed
* C an us e a small power amplifier
Disadvantages
Disadvantages
* R ecording level is not perfectly flat
* Difficult to adjust the E Q to get a great sound
* T he recorders E Q, needs to be adjusted profess ionally.
* P rofes sional service is needed to replace or tune up
selected parts .
NE UMA NN
* V ery flat frequency response specifications
* True sounding final output
* Needs a very powerful amplifier (600W)
* Head coil gets extremely hot (210•‹C ) and needs to be
cooled down using a helium gas cooling system
* V ery expensive, heavy, high-end professional use only
sound recording device.
Although the V R X-2000 differs greatly from the big machines , such as the Neumann,
attaining high quality recordings time and time again can be easily achieved with s tudy
and pers everance. F urthermore, acknowledging the above differences will help you to
unders tand the proces s by which to grasp your pre cutting needs, thereby facilitating
eas ier high end results.
ATT AINING T HE B E S T C UT AG AIN A ND AG AIN.
To ensure that your results live up to your expectations of sound quality please follow
the steps below carefully until you have become a consistent producer or amazing,
unique recordings.(fig.6)
C D/MD/P C
comp/limitter
mas ter
comp/limitter
G E 33S A E Q MIXE R AMP
E Q
detec tor loop
input output
fig.5 : VR X-2000 R E C OME NDE D S E T UP
S et up the cutting stylus, making s ure that its position is correct and s ecure.
C heck the stylus connection and pres sure.
Warm up to the heating coil based on your room temperature and desired sound
style. (Y our genre - Jazz, hardcore - will require slightly to greatly different
temperatures )
P erform a one-minute tes t cut to check for irregularities in cutting quality.
Ins pect the cutting blank and the residue (from cutting) for cracks and cutting
precision. T IP : Y ou should watch the "cutting-tip"(offcut) to see that the cutting is
precisely and smoothly.
Assuming that the above check has proved positive, this check is to allow you to
set up for your final recording correctly.
C onnect your input s ource directly to the V R X -2000 - DE F F INAT E LY NO E Q - T his
will help you s ee how your V R X-2000 records and allow you to understand its
recording character.
Make a sample recording - NO E Q - for a few minutes. The longer the recording
the more easily it will be for you to adjust your E Q later to ensure a superior final
cut.
P lay back your recording through an E Q making adjustments to the sound (E Q)
according to your style, tas tes or target result.
Thes e E Q adjustments, that you have made on the playback of the test, are what
will ensure that the final cut is flat and true to your input source.
A frequency range of between 200Hz - 600Hz is the recommended range that will
give you warmth and s ens itivity whilst still being clearly balanced.
Y OUR C UT T ING LE VE L S HOULD NOW BE S E T T O MINIMIS E E XTR E ME 'OVE R '
P E AK S . Use of the input meter on the V R X-2000 is recommended in this case.
This balance is important so as to minimize any chance of damage to your head
and the heating coil of the VR X-2000.
R econnect the V R X-2000 to your input source through your E Q.
E nsure that your input sound is well balanced and the extreme peaks compensated
for.
Make your final cut.
(1) TE S T C UT - TR IAL C UT
A.
B .
C .
D.
E .
(2) S T R AIG HT C UT - S OUND INP UT C HE C K & E Q
A.
B .
C .
(3) P L AY B A C K - E Q ADJ US TME NT
A.
B .
C .
D.
(4) F INA L C UT - UNIQ UE QUA L IT Y E ND R E S ULT S
A.
B .
C .
**NOT E -- T he taking of notes will facilitate an improved unders tanding of the
recording process and help speed up your recording proces s. Thes e notes will also
allow you to perfect your proces s over and over again.

HE AD F R E QUE NC Y E QUA L IS ATION
VR X-2000 R E C OR DING
The VR X-2000 is an innovative machine for the experienced profess ional mus ician.
When us ed with proper training and knowledge, your ability to produce unique, high
quality recordings with the warmth of vinyl is greatly improved.
Although the VR X-2000 is comparable to standard mas ter recording laces (such as the
Neuman) there are a number of important differences to be aware of. Two very
important issues to consider are;
HE AD F R E QUE NC Y E QUA L IS AT ION
The manner by which the C utting Head reacts to various frequencies will affect the
final output. B asically, the C utting Head is like a very small yet powerful speaker
when it reacts to various s ound frequencies. (R efer to fig.1& fig.2) E xtreme
frequencies will caus e it to move rather s everely, with that movement being further
reflected in the sound recorded.
G R OOV E P IT C H
-50
-40
-30
-20
-10
0
10
20
30
0 100Hz 1kHz 10kHz
[dB ]
fig.1 : C UT T ING HE AD F R E QUE NC Y R E S P ONS E NE UMANN S x74
V R X-2000 3 B and E Q
NE UMANN Motion F eedback
VR X-2000 C onstant P itch
NE UMANN Variable P itch
950Hz
-50
-40
-30
-20
-10
0
10
20
30
0 100Hz 1kHz 10kHz
[dB ]
fig.2 : C UT T ING HE AD F R E QUE NC Y R E S P ONS E VE S T A X VR X-2000
Though both machines can tolerate such extreme sounds, the way in which they are
handled is completely different. T he proces s of compens ating for these extremes
(peaks & troughs), namely E qualization, involves the flattening / correction of the
incoming curve s ignal. The method by which the Neuman(fig.3) and the VR X-
2000(fig.4) adjust curves is very different. On a big powerful machine, any extreme
incoming signals are compens ated for with an inverted signal, the res ult being a true
sound with a flat signal.(fig.5) This system of compens ation is called motion feedback
and as mentioned above, is used exclusively in large expensive recording lace
systems like the Neuman. T he V R X-2000, however, utilizes a standard graphic E Q
system to compensate for extreme incoming signal curves. T his system is aurally
difficult and requires hours of practice and experimentation to get it perfect over and
over again.
fig.3 : C UT T ING HE AD F R E QUE NC Y R E S P ONS E NE UMANN S x74
950Hz
-50
-40
-30
-20
-10
0
10
20
30
0 100Hz 1kHz 10kHz
[dB ]
950Hz
-50
-40
-30
-20
-10
0
10
20
30
0 100Hz 1kHz 10kHz
[dB ]
cutting drive amp
cutting head
input
driving coil
feadback coil
fig.5 : MOT ION F E E DB AC K C IR C UIT
fig.4 : C UT T ING HE AD F R E QUE NC Y R E S P ONS E VE S T AX VR X-2000
VR X-2000
Advantages
Advantages
* S mall S ys tem
* No cooling s ys tem is needed
* C an us e a small power amplifier
Disadvantages
Disadvantages
* R ecording level is not perfectly flat
* Difficult to adjust the E Q to get a great sound
* T he recorders E Q, needs to be adjusted profess ionally.
* P rofes sional service is needed to replace or tune up
selected parts .
NE UMA NN
* V ery flat frequency response specifications
* True sounding final output
* Needs a very powerful amplifier (600W)
* Head coil gets extremely hot (210•‹C ) and needs to be
cooled down using a helium gas cooling system
* V ery expensive, heavy, high-end professional use only
sound recording device.
Although the V R X-2000 differs greatly from the big machines , such as the Neumann,
attaining high quality recordings time and time again can be easily achieved with s tudy
and pers everance. F urthermore, acknowledging the above differences will help you to
unders tand the proces s by which to grasp your pre cutting needs, thereby facilitating
eas ier high end results.
ATT AINING T HE B E S T C UT AG AIN A ND AG AIN.
To ensure that your results live up to your expectations of sound quality please follow
the steps below carefully until you have become a consistent producer or amazing,
unique recordings.(fig.6)
C D/MD/P C
comp/limitter
mas ter
comp/limitter
G E 33S A E Q MIXE R AMP
E Q
detec tor loop
input output
fig.5 : VR X-2000 R E C OME NDE D S E T UP
S et up the cutting stylus, making s ure that its position is correct and s ecure.
C heck the stylus connection and pres sure.
Warm up to the heating coil based on your room temperature and desired sound
style. (Y our genre - Jazz, hardcore - will require slightly to greatly different
temperatures )
P erform a one-minute tes t cut to check for irregularities in cutting quality.
Ins pect the cutting blank and the residue (from cutting) for cracks and cutting
precision. T IP : Y ou should watch the "cutting-tip"(offcut) to see that the cutting is
precisely and smoothly.
Assuming that the above check has proved positive, this check is to allow you to
set up for your final recording correctly.
C onnect your input s ource directly to the V R X -2000 - DE F F INAT E LY NO E Q - T his
will help you s ee how your V R X-2000 records and allow you to understand its
recording character.
Make a sample recording - NO E Q - for a few minutes. The longer the recording
the more easily it will be for you to adjust your E Q later to ensure a superior final
cut.
P lay back your recording through an E Q making adjustments to the sound (E Q)
according to your s tyle, tas tes or target res ult.
Thes e E Q adjustments, that you have made on the playback of the test, are what
will ensure that the final cut is flat and true to your input source.
A frequency range of between 200Hz - 600Hz is the recommended range that will
give you warmth and s ens itivity whilst still being clearly balanced.
Y OUR C UT T ING LE VE L S HOULD NOW BE S E T T O MINIMIS E E XTR E ME 'OVE R '
P E AK S . Use of the input meter on the V R X-2000 is recommended in this case.
This balance is important so as to minimize any chance of damage to your head
and the heating coil of the VR X-2000.
R econnect the V R X-2000 to your input source through your E Q.
E nsure that your input sound is well balanced and the extreme peaks compensated
for.
Make your final cut.
(1) TE S T C UT - TR IAL C UT
A.
B .
C .
D.
E .
(2) S T R A IG HT C UT - S OUND INP UT C HE C K & E Q
A.
B .
C .
(3) P L AY B AC K - E Q A DJ US T ME NT
A.
B .
C .
D.
(4) F INA L C UT - UNIQ UE QUA L IT Y E ND R E S ULT S
A.
B .
C .
**NOT E -- T he taking of notes will facilitate an improved unders tanding of the
recording process and help speed up your recording proces s. Thes e notes will also
allow you to perfect your proces s over and over again.

4
2.2 Mastering
Excellent cutting is only possible with excellent mastered records. This Seminar is not intended to
teach mastering and engineering skills. These are a requirement for successful cutting.
However here are some hints about Mastering.
More and more people nowadays are recording in their living room or garage without caring about
monocompatibility or phase continuity and correlation. etc.
Recording this kind of material to a Vinyl (or to a CD) will end up with a terrible sounding result.
Special Studio equipment like studio monitors; VU and peak meters; Multiband Equalizer;
Compressor-Limiter; De-esser; Correlation Meter; Leveler etc. are necessary for a high quality
mastering.
Some good ideas can be found in the booklet “The Secret of the Mastering Engineer” by Bob Katz.
This booklet is downloadable under www.digido.com where also several other interesting information
about recording can be found.
Here are some recommendations from Vinyl Mastering engineers :
To achieve the best results on vinyl following points should be taken care of when a Master Tape or CD
is produced:
•The most powerful tracks should be put to the beginning of a side. Due to the smaller diameters the
performance of high levels decreases when you are recording in the middle of the vinyl.
•Please insert 2 or 3 seconds of silence between each track.
•All tracks should be checked with a correlation meter to prevent the music being in the red area.
•It might be necessary to change the sound of loud, stressed (woman) voices or similar sounds during
the mastering process
•Psychoacoustic sound processing like exciter, enhancer, etc should not be used.
•Extreme bass frequencies must be in phase, check with correlation meter
•Subfrquencies below 15Hz need to be cut. Many playback tonearms have a resonance frequency from
5 to 10Hz.
•Most important is that the mastered material meets the physical limitations of the cutting stylus.
2.3 General
This is a product to cut analog records. It is not like a CD-Recorder where one only needs to push a button.
Cutting records requires experience and technique. If you do not learn how to use the VRX-2000 properly, you
may not get the best possible results.
Especially in the beginning it is very important to learn how to use this machine step by step.
VRX-2000 is a very high-tech creation. Please use great caution in moving and setting up.
Before starting with any work on the VRX-2000 ensure that no magnetic sensitive
material is around.
As magnetic tapes, disks, bank and credit cards, and especially wristwatches.
Please remove your wristwatch !

5
Section 3: BASIC VRX-2000 SET-UP AND COMPONENTS
3.1 SET UP
Please place this unit on a solid, stable and horizontal surface. An unstable surface may pick up external
vibrations, and these unwanted sounds will be recorded on the vinyl. Unstable surfaces may also cause platter
rotation fluctuations.
Please avoid sunlight, dust, humidity, and do not place the unit near heating appliances or sources of heat. If
dust gets on the vinyl recording it will cause additional noise on recording sound.
Please do not place the VRX-2000 near loudspeakers, as any sound with enough volume will be recorded on
the vinyl.
Please also never place the unit near TV, radio, or other equipment which generates electric or magnetic fields.
If the unit is located in such a place it may have an effect on the cutting head and you will not achieve the best
result.
3.2 HANDLING
The VRX-2000 is very heavy. It is recommended that extreme care is taken when moving the unit, and that it is
moved by more than one person. If you are going to ship the unit, please use original packing material.
When transporting, please be sure to disassemble the following parts from the main unit:
1. Cutting head
2. Play back cartridge
3. Platter
N.B. Please also remove the stylus from the cutting head and place both parts in the original case for
transportation.
3.3 CUTTING HEAD
The cutting head is fragile. Please do not drop or force undue power or pressure, and do not touch any place
other than the stylus holding section. If there is any damage inside the cutting head, quality recording will not
be possible.
Please do not place the cutting head in dusty or dirty areas. If dust particles get inside the cutting head, the
head will cease to function properly.
If there is too high a signal applied, the coil may burn or break. In order to avoid such a problem, a limiter circuit
is built-in to the VRX-2000. If you would like to use the unit without internal limiter circuitry, please adjust the
recording levels very carefully, otherwise a high input signal may damage the head.
When you replace the stylus, you will have to assemble and disassemble. Please be careful not to damage the
head on replacement. The cutting head contains a very strong magnet - if steel or other metal is placed near
the cutting head, it will create a very strong magnetic field. Such a damaging strong magnetic field might also
cause a problem with wristwatches, so please remove yours when handling or recording.
Each cutting head is matched to its VRX recorder. Never change heads between different VRX-machines.

6
3.4 TRACKING ARM
The VRX-2000 tracking arm is another sensitive component, and is and very accurately made. Please do not
put pressure on the tracking arm, as it may cause inaccuracies and problems in recording.
If the arm is bent by strong force it will cause the VRX2000 to disfunction totally.
Please also note that the moving parts of the tracking arm require maintenance from time to time.
It is recommended to put some silicone oil on the tracking bar and the other moving parts
every one or two month, depending on the time of usage.
3.5 STYLUS & HEATER LIFE
•The life of the cutting stylus is approximately between 200-300 minutes (depending on the cutting pressure
used and the level of stylus heat). Overusing the stylus reduces the quality of recording. You may initially
notice a reduction in the volume of one side (L/R) of the recording as the cutting stylus wears out. Please
replace the stylus regularly.
•Although the stylus consists of a very hard material, it might be damaged or broken if it is touched or
dropped, mishandled. This will make recording impossible. Please replace the stylus if any of these
instances occur.
•The heater line (wire) is very thin and fragile, therefore please handle very carefully. If the heater line is cut,
please replace the whole stylus immediately.
•If too much current is applied to the heater line, the line may burn and break down. Please be very careful
with adjustments of heater current.
•On assembly of the stylus on the cutting head, please be careful that the heater line does not touch the
vinyl or surrounding parts of the cutting head.
3.6 BLANK VINYL
•The Vinyl’s should be stored in the same room and temperature where the VRX is and where you are
recording.
•Please make sure that the vinyl is perfectly flat when placed on the VRX-2000 for the vinyl cutting
procedure. Vinyl that is not perfectly flat will prevent perfect quality recording.
•If a bent or warped vinyl is used, the depth or width of the groove will be inconsistent. It will cause a
distortion or needle skipping on playback.
•On recording, please make sure the surface of the vinyl is clean. Please do not use thinner or methylated
spirits for cleaning.
•Before recording, please remove the protective sheets on the side of the blank vinyl you intend to record.
•The special vinyl for the VRX-2000 has a similar durability of commercial vinyl, but a record cut in improper
circumstances/condition may have less durability than usual

7
Section 4: Description of VRX-2000 Components
4.1 Top Panel

8
VRX-2000 Components:
1. Ioniser: reduces static build up
2. Slider arm base : mechanism to move the cutting arm
3. Tracking arm: arm to hold cutting head and apply correct pressure
4. Tracking arm weight: adjusts cutting pressure
5. Slider cam: locks the cutting arm in place
6. Release lever (only some special series are equipped with this release lever.)
7. Manual rotation wheel: to set the position of the cutting arm in the correct place on the vinyl
blank
8. Cutting head: Vestax proprietary design high quality stereo cutting head
9. Tracking on/off switch
10. Recording level volume control: to adjust the level of the incoming signal
11. Heater current meter: visual display of the level of heat applied to the cutting stylus
12. Heater current adjustment control: adjusts the level of the heat applied to the cutting stylus.
13. VU level meters: a display of the input level signal left and right
14. Vinyl blank holder: secures blank disc to platter
15. Blank disc
16. Pitch control adjuster: adjusts pitch of platter +/- 10% , only applicable when quartz lock is
disengaged.
17. Quartz lock switch: locks pitch
18. Speed select switch: selects the speed – 33 1/3 rpm or 45 rpm. LED displays 45rpm.
19. Start/stop switch
20. Playback arm height adjustment screw
21. Playback arm counter weight
22. Playback arm headshell
23. Playback arm armrest
24. Playback arm
25. Heavy duty carrying handles
26. Center spindle on turntable platter
27. Turntable platter

9
4.2 Rear View
28. Limiter bypass switch: turns the internal compressor limiter on or off. Must always be in on
position unless external compressor limiter devices are used in the cutting process.
29. Input level select switch: adjusts the input gain +4dB/ 0dB/ -10dB
30. Phono level output jacks: standard RCA left/right output jacks for playback
31. On/off power switch
32. AC power cable
33. Ground terminal
34. XLR balanced left/right audio input sockets PIN1 – ground; PIN2 – hot; PIN3 – cold
35. Unbalanced input jacks: standard left/right RCA audio input sockets. N.B. if both XLR and
RCA audio input sockets have equipment connected, the RCA takes precedence and XLR
becomes disengaged.
36. Connector cable from cutting head to internal mechanisms.

10
4.3 Cutting Head Section
37. Cutting stylus holder (A) 39. Heater wire terminal
38. Cutting stylus holder (B) 40. Multipin connector
Section 5: TECHNICAL DESCRIPTION OF VRX-2000 CUTTING MACHINE
5.1 Description of each Part
•Cutting arm - the cutting arm consists of two parts: the base and the arm. The base has a mechanism
which moves the arm from the outside to inside of the vinyl as you record. The VRX-2000 uses a DC
motor to rotate the gear and move the head in a constant speed. In addition, the arm can be moved
quickly by using the manual rotation wheel, to move the head toward the specific location on the vinyl
blank where you would like to start recording, or to create a tail.
•Turntable - consists of a platter, platter weight, silicone mat, and disc holder. The platter weight is very
heavy, facilitating consistent rotation. The silicone mat and disc holder secure the disc on the turntable
solidly, and prevents shifting of the blank disc. The turntable is driven by high torque direct drive AC
motor and generates a very stable rotation to record the music accurately.
•Cutting Head – the cutting head translates the music signal to the physical movement of the stylus and
cuts the groove on the blank disc. The cutting head of the VRX-2000 uses the same moving coil
technology as top professional cutting machines from the past. The cutting head has 2 magnetic
drivers separated by a 90 degree angle creating a V shape. This layout is optimum for stereo signal
recording with the best possible channel separation, and best balance. The operation of the cutting
head is very similar to that of a loudspeaker – it consists of a coil and a magnet, and the coil moves as
the electric current is applied. The coil is very intricate and fragile – improper handling or overloading
may burn the coil or damage the components. Please be careful not to overload the coil and do not
touch or disassemble the cutting head – damage by improper usage will not be covered by warranty
service.
•Cutting Stylus – the cutting stylus of the VRX-2000 uses a sapphire tip. The sapphire tip is very
delicate and requires careful handling. The cutting head has a heater line to apply heat to the sapphire
tip while recording. The heater line is very thin and easily damaged; it requires careful handling and
setting up. Please do not use this cutting stylus for any other purpose.
Cutting Equalizer – An analogue record is recorded using RIAA equalizer, in order to allow the vinyl to hold a
wide frequency range. The VRX-2000 has an RIAA equalizer built in. This equalizer decreases the low end
and increases the high end for the recording process. On playback, the phono EQ will automatically adjust to
restore the original signal.

11
Section 6: ASSEMBLY AND SET-UP
6.1 Platter assembly
1. Insert platter to center spindle
2. Stick the lower “mirror mat” (2) on the platter with 4 small pcs 2x2 cm of double sided adhesive tape.
2. Also stick the platter weight on “mirror mat” at the same way.
3. Stick the upper “mirror mat” (1) on the platter weight with 4 small pcs 2x2 cm of double sided adhesive
tape
4. Remove the protective sheet of blank disc on the top side, and push the blank disc down on the mirror
mat (1) using a lint-free cloth or the included record cleaner. Apply sufficient pressure to firmly secure
the vinyl blank to the mirror mat.
5. Put on the disc holder to secure the blank vinyl.
•If the blank disc is not dust-free, it may create skipping or noise problems. Ensure your blank is
perfectly clean.
•If the blank disc is not secured to mirror mat, slipping may occur which will render your final cut
unusable.
6.2 Ioniser Assembly
Secure ioniser with 2 screws as per picture below.
(Figure 10.2-A)
FIG10.2-A
6.3 Tracking arm/counter weight assembly
Assemble counter weight on the rear of tracking arm.
(Figure 10.3-A)
FIG10.3-A

12
6.4 Cutting stylus assembly
Cutting stylus components:
•Stylus tip – highest quality sapphire
•Heater line – to heat stylus tip to 40-60 degrees centigrade
•Lifetime of stylus – 200-300 minutes
N.B.
To mount the stylus please only use the screwdriver which
comes with the >VRX-2000 !!
Please be careful of sapphire tip due to its delicate nature.
The lifetime varies, depending on recording conditions,
the applied stylus heat and pressure. Different atmospheric
conditions will dictate different levels of stylus pressure
and heat. Please find optimum conditions for the VRX-2000
to maximize the life of the cutting stylus.
1. Loosen the screw on the stylus holder
2. Carefully insert cutting stylus into stylus receptor.
The shaft of the cutting stylus is half circle, or D shaped.
Please ensure that this is placed into the cutting stylus
receptor correctly.
3. Holding the stylus tip gently, alternatively tighten the
2 stylus screws one rotation each until each of the
2 screws secure the stylus shaft. Do not over tighten
and do not tighten screw a and then screw b independently.
Please make sure that the stylus shaft and cutting stylus
are correctly aligned with the receptor. This is why
the 2 screws must be tightened slowly and alternatively.
Please refer (Figure 10.4-C) (correct stylus installation)
and (Figure 10.4-D) (incorrect stylus installation).
N.B.
The cutting stylus must have an angle of approx 15 degrees
to the surface of the vinyl blank. If the cutting result is not
satisfactory (L&R side not even), please repeat steps 1-3
above using the 2 screws that hold the stylus shaft to achieve
the angle of approximately 15 degrees.
Please refer (Figure 10.4-F) and (Figure10.4-G).
4. Connect the two heater wires to the heater wire terminal. There is no positive or negative polarity here,
so there is no requirement for the wires to be attached in a particular order. To attach the wire to the
terminal, push down, insert wire and release. N.B. please make sure there is no slack in the heating
wire and it totally clears the surface of the vinyl blank.
Right ! WRONG !
FIG10.4
-
C
FIG10.4-D

13
Front View Side View
6.5 Cutting head assembly
•Before the assembly, please ensure that the cutting head is always to the right
•Please assemble the cutting head after installing the stylus.
1. If you lift the cutting arm release lever, the cutting arm lifts up. Please ensure the release lever is
locked. Slide the cutting head into the arm from the front.
2. Secure the cutting head on the cutting arm carefully with supplied two screws
by using a screwdriver !!
N.B.
•Please ensure the cutting head is totally secured or cutting result will be imperfect.
•The magnet on the cutting head is very strong – therefore make sure your wristwatch is
removed.
3. Connect the multipin cutting head cable into the cutting head, ensuring it locks.
4. N.B. when you disconnect, gently pull back the metal sheath.
Before mounting the cutting head to the tracking arm please check the screws on the cutting head.
As the head is vibrating during recording, the screws may get loose and have to be checked
from time to time !
FIG10.4-F FIG10.4-G

14
Section 7: FINAL ADJUSTMENTS
7.10000Stylus pressure adjustment
•Move the cutting arm over the blank disk
•Ensure that the tracking is off.
•Put the cutting arm with the stylus gently on the blank disk
1. Attach the supplied extra fine weight scale
(Figure 11.1-A). to one of the head magnets
2. Holding the scale by the black cylinder and pull gently
upwards until the stylus just lifts of the vinyl. Read
the measure of the scale and adjust if neceessary
7.2 General Adjustment
The above figures should give you a basic setting to start with. As a perfect recording depends very
much on the right adjustment between temperature of the stylus; stylus pressure; and stylus angle
to the disc, you always should find your own proper setting.
A the stylus temperature also is depending on the temperature and humidity of the surrounding air,
the settings also will vary due to this parameters. It is also recommended to make notes about your
settings with your machine.
Section 8: RECORDING PROCEDURE
1. Remove the protective sheet of disc on top side and secure.
2. Secure clean blank disc
3. Select speed N.B. recommended speed for
easiest cutting is 45rpm
4. Adjust pitch
5. Push start button
6. Turn Ioniser on using on/off switch on rear
of Ioniser mechanism.
Select “high”. Please refer (Figure12.1-A).
7. Rotate the slider cam and release lock of the
cutting arm. See (Figure 12.1-B).
8. Set the input level control to minimum
and heater control adjustment to minimum.
9. Turn tracking on/off switch to “on”
N.B.
if the arm starts moving, the lock is in
the incorrect position. Please ensure
lock is released before proceeding.
10. To achieve the desired heat of the cutting
stylus wait 2-4 minutes.
11. Begin play back of the recording source
and increase the input level control, making
sure that the level does not exceed 0db.
12. Peaks of the source material must never exceed 0db.
FIG11.1-A
FIG12.1A
FIG12.1B
Stylus pressure [N] Currentheater[mA]
Kind ofblankdisc rpm
Harmodisc 33 0.45 `0.50 200
Harmodisc 45 0.50 `0.55 500
Lacquerdisc 33,45 0.30 `0.35 300
Condition
Table of contents
Other Vestax Turntable manuals
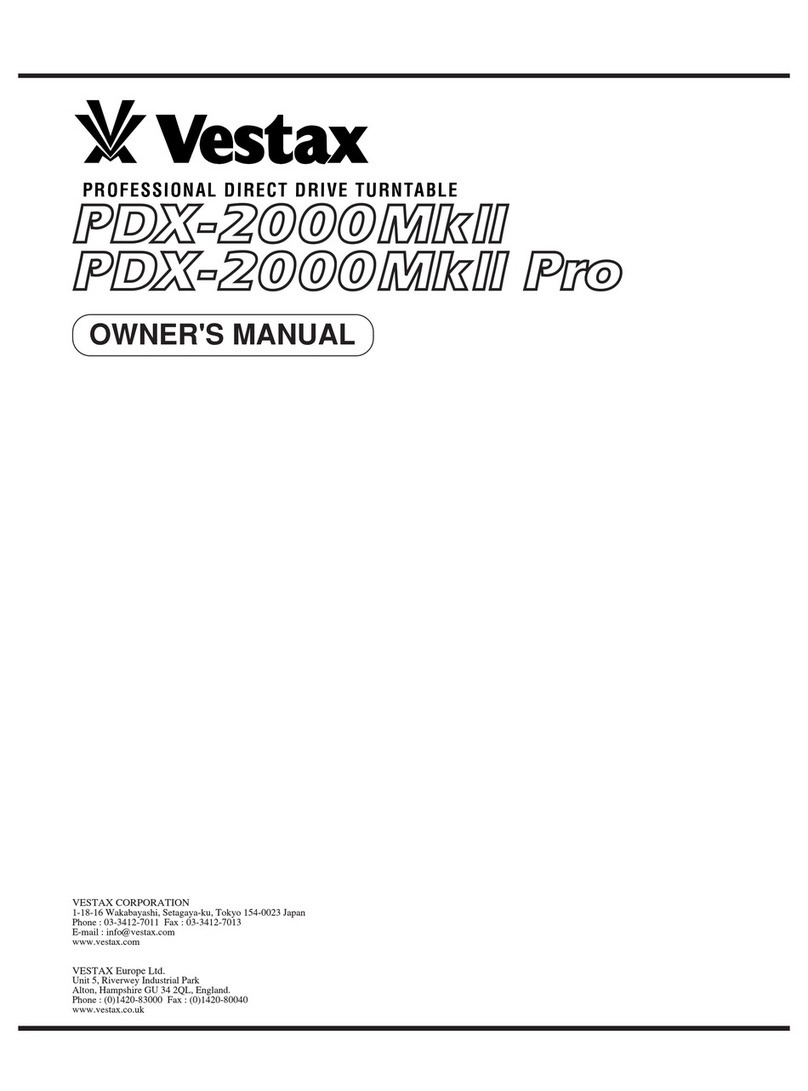
Vestax
Vestax PDX-2000MkII Pro User manual
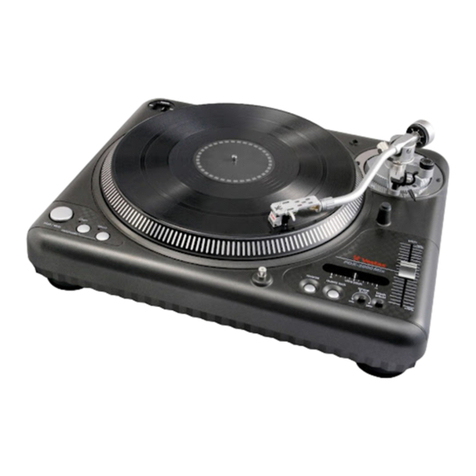
Vestax
Vestax PDX-3000MKII User manual

Vestax
Vestax PDX-a1 User manual
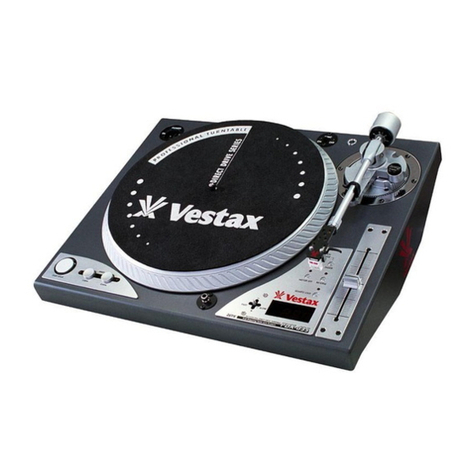
Vestax
Vestax PDX-d3S User manual
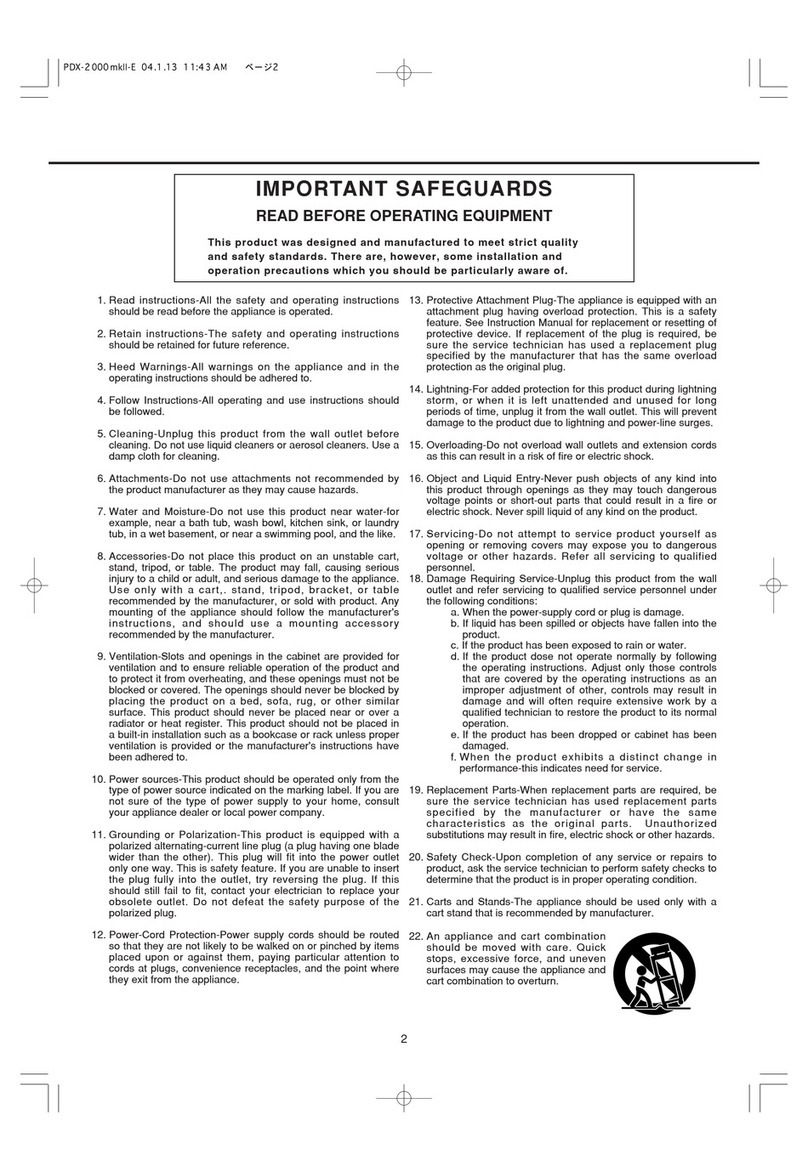
Vestax
Vestax PDX-2000 User manual
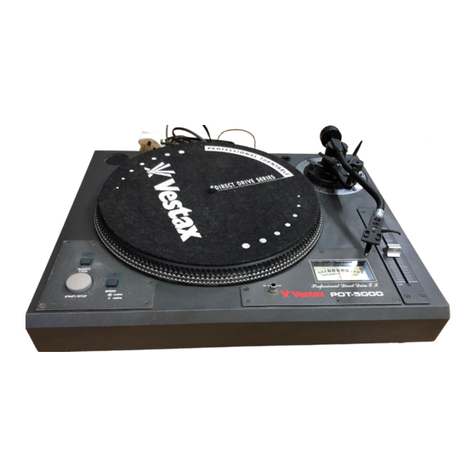
Vestax
Vestax PDT-5000 User manual
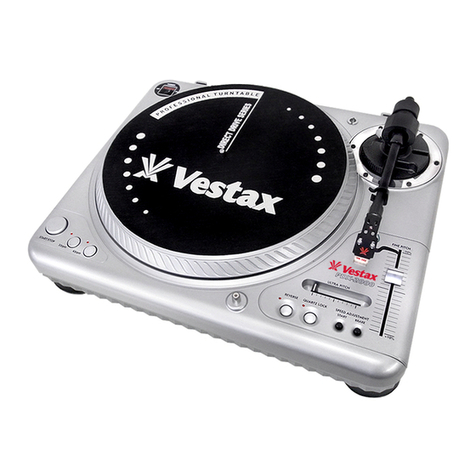
Vestax
Vestax PDX-2000 User manual
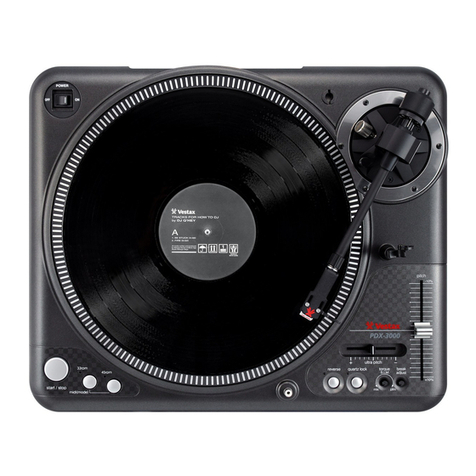
Vestax
Vestax PDX-3000 User manual

Vestax
Vestax HANDY TRAX USB User manual

Vestax
Vestax PDX-2300MkII Pro User manual
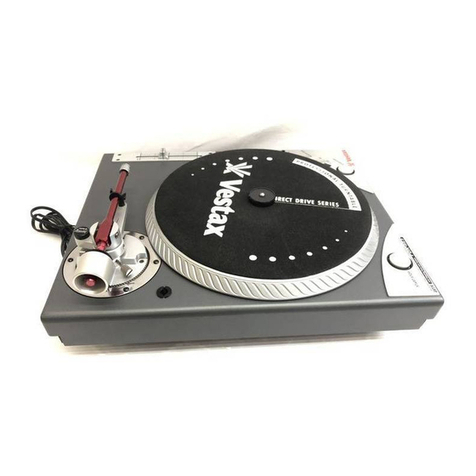
Vestax
Vestax PDX- a2 Quick start guide
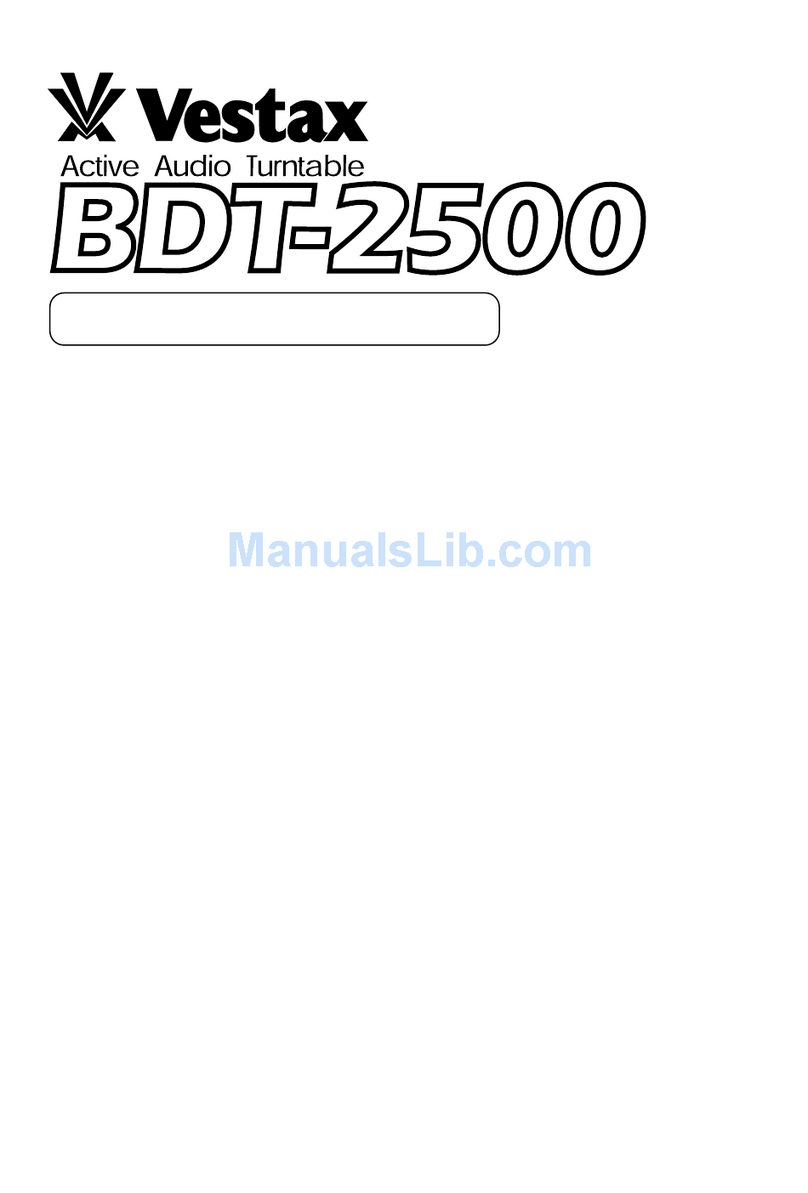
Vestax
Vestax BDT-2500 User manual
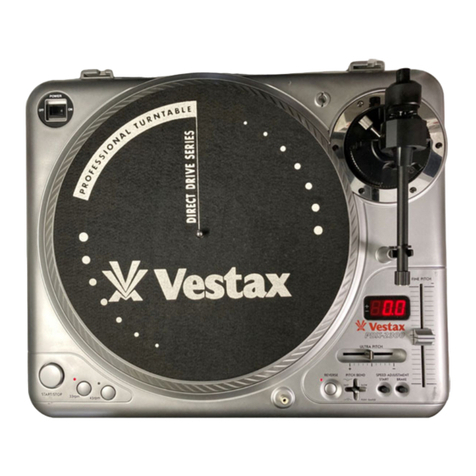
Vestax
Vestax PDX-2300 User manual

Vestax
Vestax PDX-2000 Quick start guide
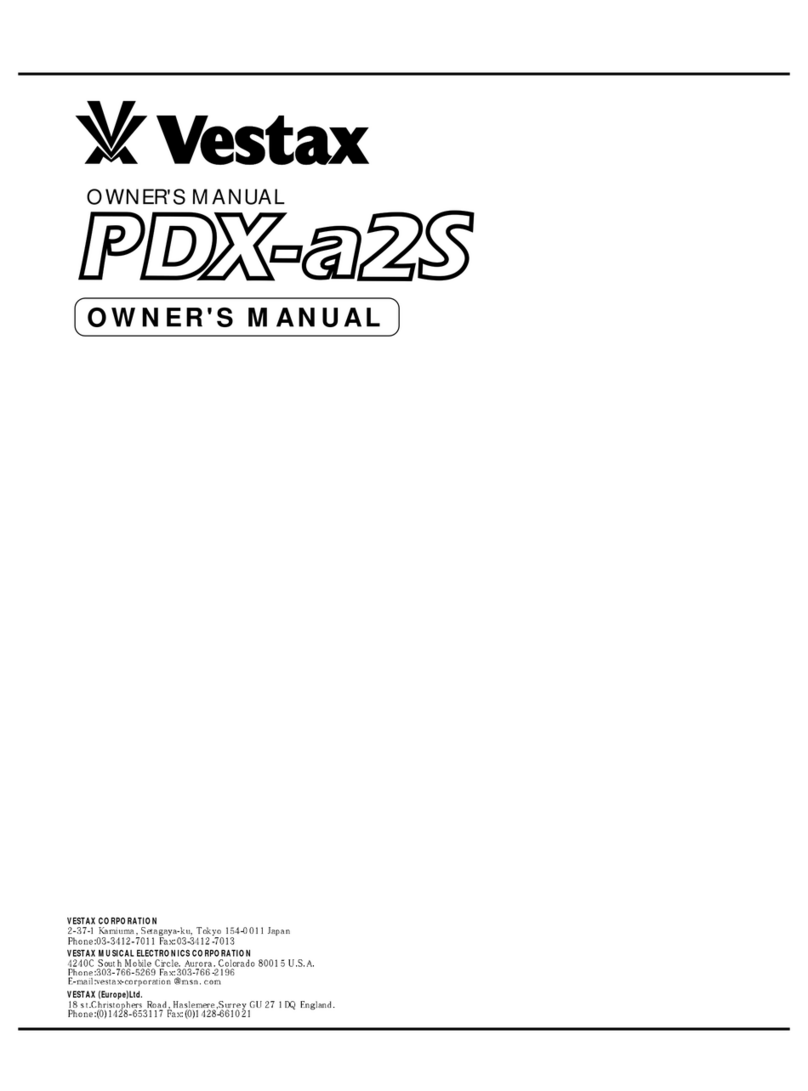
Vestax
Vestax PDX-a2S User manual
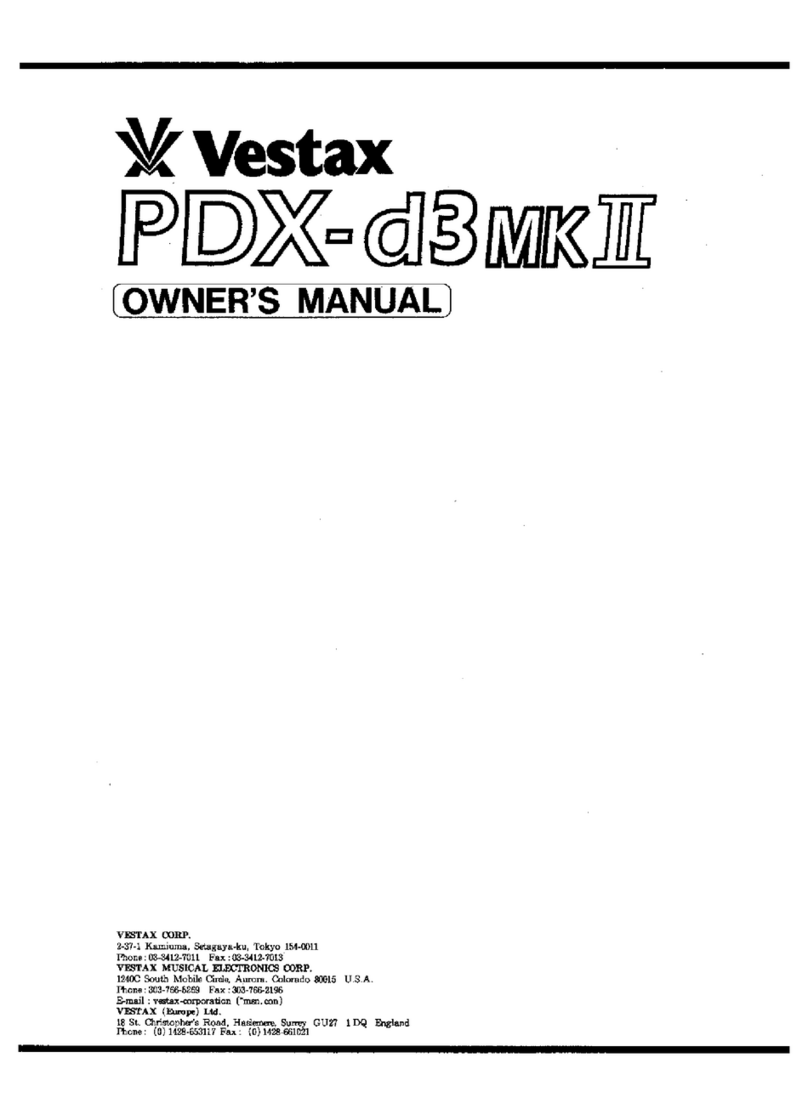
Vestax
Vestax PDX-D3MKII User manual
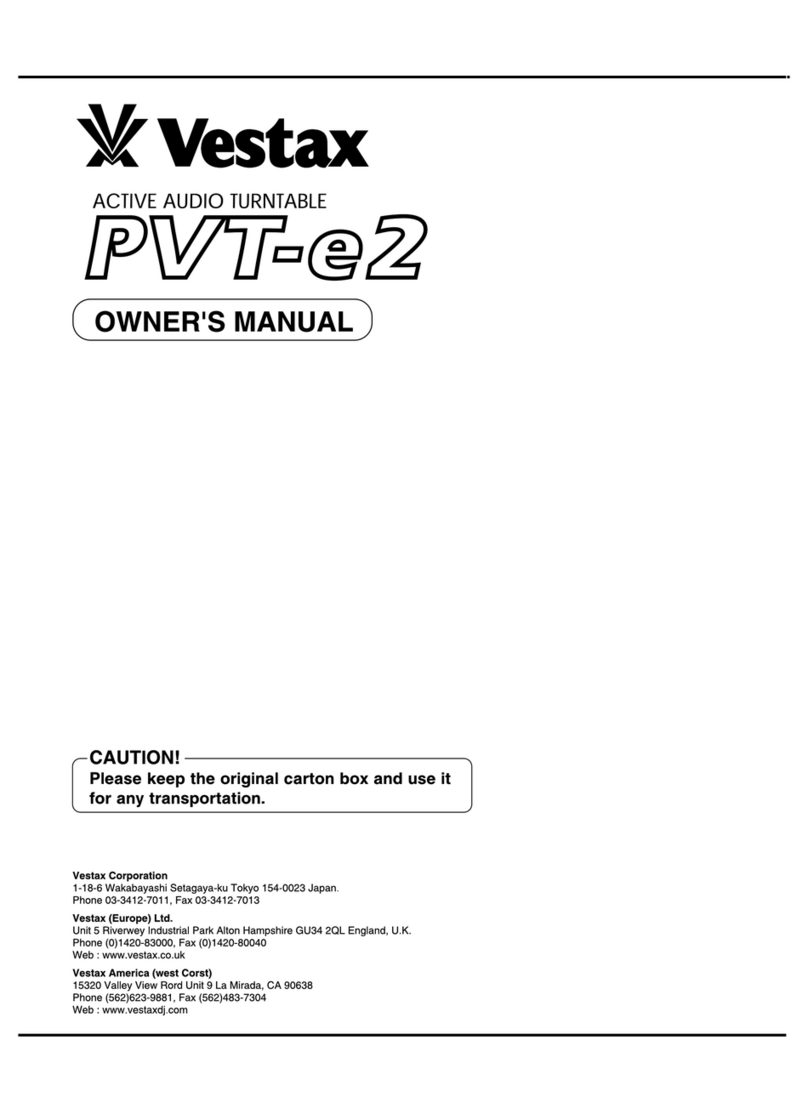
Vestax
Vestax PVT-e2 User manual
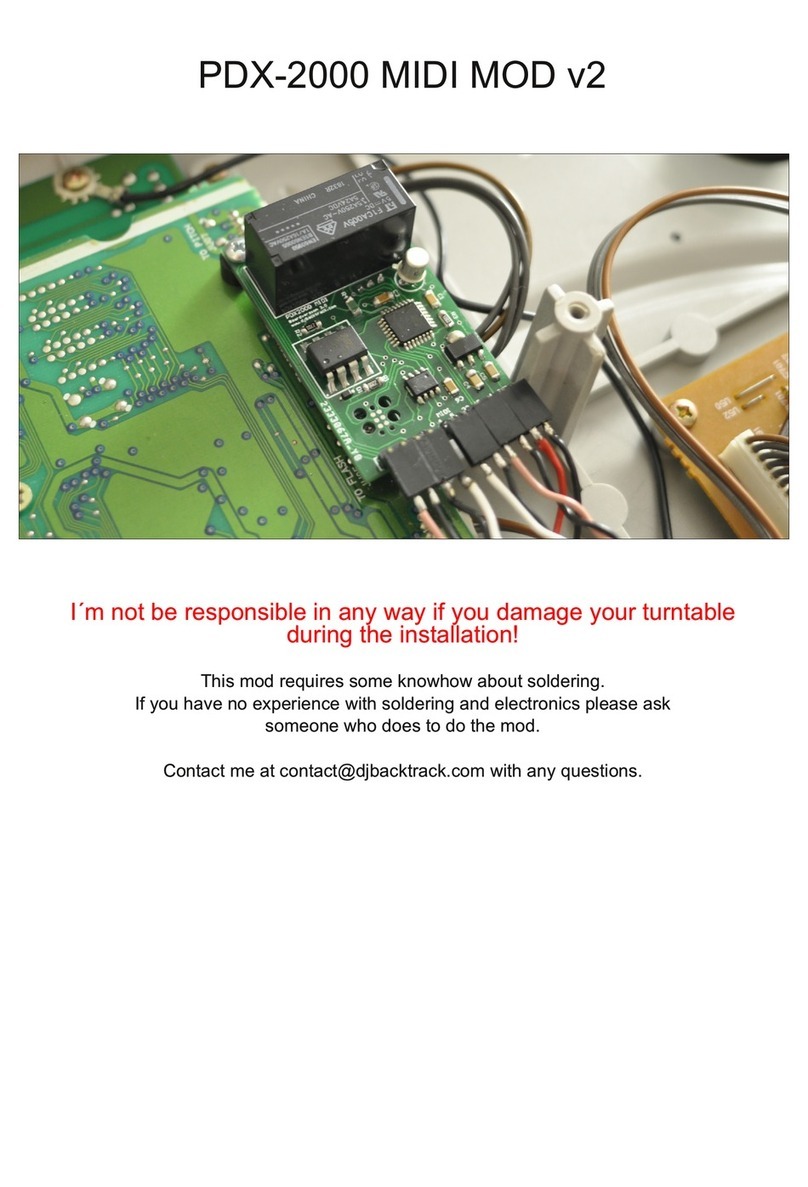
Vestax
Vestax PDX-2000 User manual
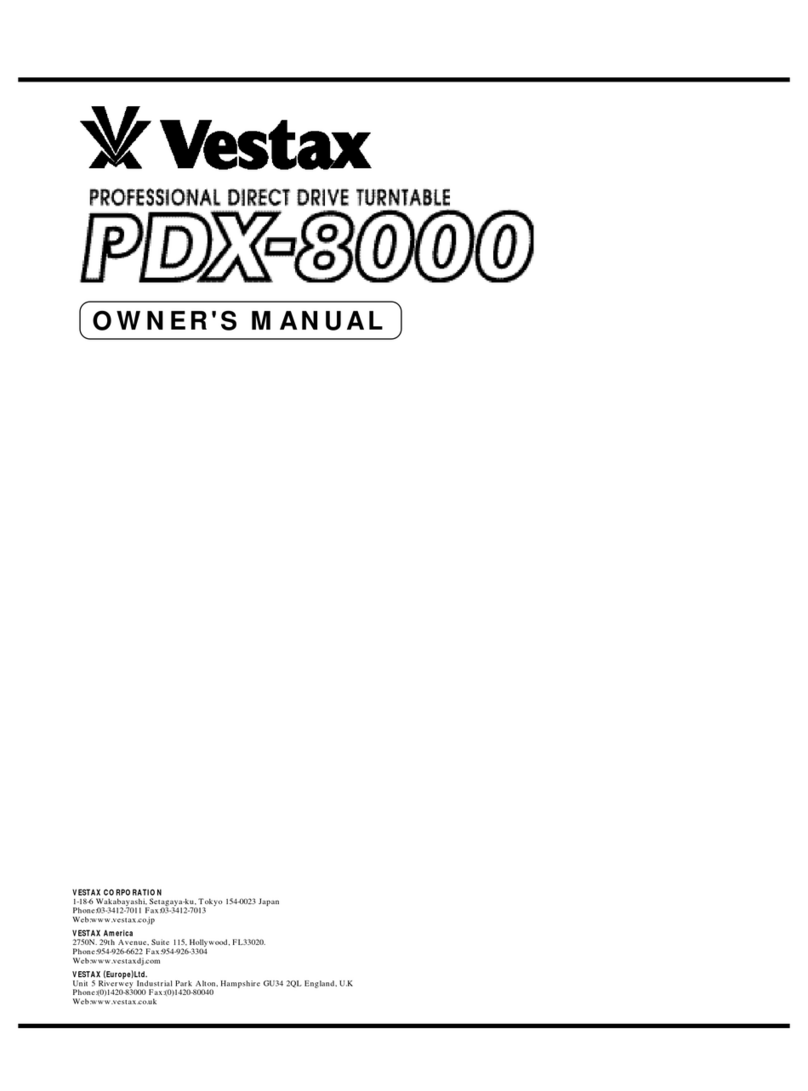
Vestax
Vestax PDX-8000 User manual
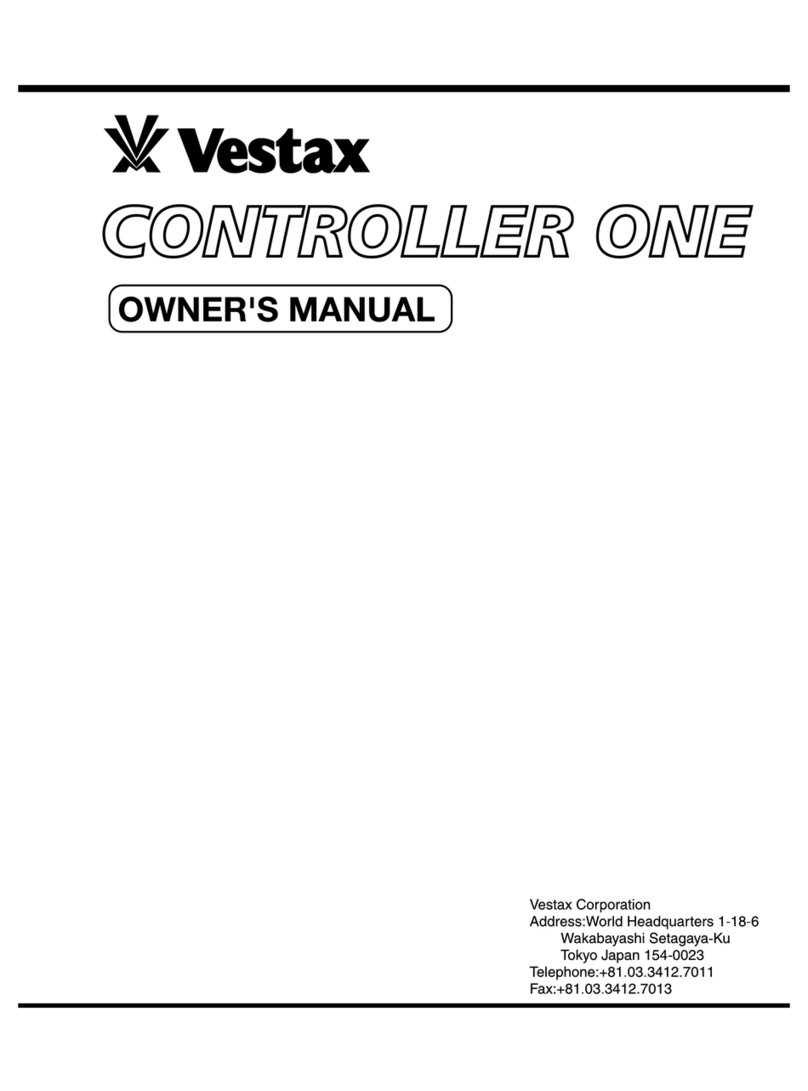
Vestax
Vestax CONTROLLER ONE User manual