VIBROBIT MK40 User guide

EQUIPMENT VIBROBIT 300
Module MK40 Setup Manual
(Ver. 1, module software version 3.0)
ВШПА.421412.304 И1
Rostov-on-Don
2011
SCIENTIFIC-PRODUCTION
ENTERPRISE VIBROBIT LLC
ВИБРО
БИТ

Module MK40 Setup Manual
ВШПА.421412.304 И1
Phone/Fax
+7 863 218-24-75
Phone/Fax
+7 863 218-24-78
E-mail: info@vibrobit.ru
http:// www.vibrobit.ru
Module MK40 Setup Manual are meant for introducing to user (consumer) of operating principles and setting
methods of MK40 Fixed Signal Monitoring Module of Equipment Vibrobit 300.
This Document is an Amendment to
ВШПА.421412.300 РЭ Equipment Vibrobit 300. Operations and Maintenance Manual.
Vibrobit LLC Scientific and Production Enterprise reserves the right to modify parts and accessories without loss of product
performance.
Microsoft and Windows are registered Trade Marks of Microsoft Corporation.
Edition 3 of 26.07.11
2
No revisions

ВШПА.421412.304 И1 SCIENTIFIC-PRODUCTION ENTERPRISE VIBROBIT LLC
CONTENTS
General Information.......................................................................................................................................4
Technical specifications.................................................................................................................................................5
Indication and control equipment...................................................................................................................7
Module operation.........................................................................................................................................10
Switching power on......................................................................................................................................................10
Resetting......................................................................................................................................................................10
Parameters measurement...........................................................................................................................................12
Calibration recommendations......................................................................................................................................18
Logic outputs...............................................................................................................................................................20
Digital Control Interfaces..............................................................................................................................21
RS485 interface...........................................................................................................................................................21
CAN2.0B interface.......................................................................................................................................................24
I2C driven interface......................................................................................................................................................25
Module settings and current state (address tables)....................................................................................................26
Software.......................................................................................................................................................33
Getting started.............................................................................................................................................................34
Measuring channels parameters.................................................................................................................................34
Calibration....................................................................................................................................................................36
Communication interfaces parameters........................................................................................................................37
General parameters.....................................................................................................................................................39
Program close-down....................................................................................................................................................40
Program menu description..........................................................................................................................................41
Maintenance................................................................................................................................................45
Handling and storage...................................................................................................................................45
Manufacturer’s warranty...............................................................................................................................45
ANNEXES....................................................................................................................................................46
А. Controls arrangement on MK40 Module board.......................................................................................................46
B. Connector terminals assignment............................................................................................................................48
C. Module labeling.......................................................................................................................................................49
D. Module (Setup) Order Form example.....................................................................................................................50
No revisions
3

Module MK40 Setup Manual
ВШПА.421412.304 И1
General Information
2-channel MK40 Control Module is designed for measuring of tachometric signals. MK40 is based on high-
performance microcontroller, use of which permits to process signals from sensors in real-time mode (measurement
periods up to 0.1s) and support, in parallel, digital control interfaces.
Measuring channels operate synchronously but independently of one another. Measuring channels basic
functions are:
•
Measurement of sensors DC current and monitoring of sensors and communication line functionality;
•
Measurement period of rotor speed from 0.1 to 1.0 second (equal for both measuring channels);
•
Adjustable number of gear teeth (pulse count per rotor revolution);
•
Selection of sensor signal active front (determined by bridge on the module board);
•
Repetition of basic tachometric pulses for synchronization of control modules, calculating rotational
components and phases (for example, MK20 and M30 modules);
•
Rotor stop block detection and rotor stop block alarm testability (“STOP” mode);
•
Calculated frequency value comparison with set-points (3 set-points for each channel);
•
Calculation of maximum rotor speed;
•
Calculated parameter value transfer to standard current output.
Other MK40 Module features include:
•
Measuring channels input signals: 0(1) – 5mA; 0(4) – 20mA; 0 – 5V.
•
Six logic outputs with adaptable algorithm for alarm and protection circuits implementation;
•
Two standard current outputs with programmed range setup option;
•
Supported communication interfaces: RS485, CAN2.0B, diagnostic interface;
•
Utility software for PC rendering of the module actual state, setting and calibration;
•
Module in several design options:
•
MK40-DC – 20mm 3U narrow front panel, restricted module state alarm system, +24V DC
voltage power supply;
•
MK40-DC-11 – 40mm 3U front panel, bright 7-segment digital display with extended module
indication and control system, +24V DC voltage power supply;
•
MK40-DC-001 - 40mm 3U front panel, a customized alphanumeric LCD with measurement
results displaying capability in all measuring channels simultaneously, +24V DC voltage power
supply;
•
MK40-AC-11-S – 40mm 3U front panel, bright 7-segment digital display with extended module
indication and control system, AC 220V 50Hz power supply and power-on toggle-switch,
installed on the front panel.
•
Transducers (sensors) +24V DC voltage power supply is provided through self-healing 200mA fuse,
installed on MK40 Module board.
•
50Hz test signal generation for MK40-AC-11-S design option.
Overall MK40 Module setting up is implemented by PC or dedicated ПН31 setting unit. In order to setup the
module by means of PC, MK40_setup.exe software should by run on PC and MK40 Module should be connected to
PC via MC01 diagnostic interface board (RS232 PC Interface) or MC01 USB (USB PC interface).
4
No revisions

ВШПА.421412.304 И1 SCIENTIFIC-PRODUCTION ENTERPRISE VIBROBIT LLC
Technical specifications
Table 1. Technical specifications of MK40 Module
Parameter name Value
Number of measuring channels 2
Measuring range and rotor speed alarm, rotations per minute 1 – 10 000
Measuring ranges and input signal alarm:
-Direct current, mA
-DC voltage, V 1-5; 4-20
0.95-4.75
Input resistance, Ohm
-Direct current
-DC voltage 953±2; 232±0,5
not less than 10000
Acceptable tolerance limits of standard output mean percentage error of rotor speed
measuring channels, % ±1,0
Acceptable tolerance limits of digital display mean absolute error of rotor speed measuring
channels, rotations per minute, not greater than ±2,0
Readings updating time, s 0.1 – 1.0
Number of standard DC current signals 2
Output standard DC current signal, mA 0-5;4-20
Output standard DC current signal load resistance, Ohm, not greater than 2000; 500
Number of set-points for each measuring channel 3
Number of digital outputs 6
Output digital signals
-type
-DC voltage, V, not greater than
-output current, mA, not greater than
open collector
24
100
Number of synchronization outputs 2
Output synchronization signals
-type
-DC voltage, V, not greater than
-output current, mA, not greater than
open collector
24
100
Supported digital communication interfaces types RS485 (ModBus)
CAN2.0B
Diagnostic I2C
Power supply voltage, V
-for MK40-AC option
-for MK40-DC options
AC 50Hz 176-242
DC 246-350
+(24±1)
Power consumption, W, not greater than 7
⁰Operating ambient temperature range (inside and out), C +5-+45
No revisions
5

Module MK40 Setup Manual
ВШПА.421412.304 И1
Table 2. Additional specifications of MK40 Module
Parameter name Value
Dimensions, mm
-MK40-DC Module
-MK40-DC-11, MK40-DC-001 and MK40-AC-11-S Modules 20.1 х130 х190
40.3 х130 х190
Weight, kg, not greater than
-MK40-DC option
-MK40-DC-11, MK40-DC-001 options
-MK40-AC-11-S option
0.15
0.20
0.30
Readiness (warm-up) time, min, not greater than 1
Mode of operation continuous
Average life span, years 10
Mean time between failures (calculated), hours, not less than 100000
Acceptable relative humidity, % 80
at a temperature of
⁰+35 C
Insulation resistance in circuits, MOhm, not less than
-in normal operating conditions
-⁰at relative humidity of 80% and temperature of +35 C 40
2
Man-made broadcast interference voltage, dB·mkV, not greater than
-at frequency range from 0.15 to 0.5 MHz
-at frequency range from 0.5 to 2.5 MHz
-at frequency range from 2.5 to 30 MHz
80
74
60
Warranty period, months 24
Handling and transportation conditions in accordance with GOST 23216-78 Ж
Storage conditions in accordance with GOST 15150-69 Ж3
6
No revisions

ВШПА.421412.304 И1 SCIENTIFIC-PRODUCTION ENTERPRISE VIBROBIT LLC
Indication and control equipment
The front panel features of MK40 Module vary depending on design option. Appearance of MK40 Module front
panels is shown in Figure 1.
The following elements are arranged on all front panel types:
•
handle for module installation/dismantling in framework;
•
captured screws;
•
diagnostic interface D.port connector;
•
hidden Reset key for the module resetting;
•
Module state indication Ok LED.
Module state can be assessed based on Ok LED emission color:
▪
Green light – normal module operation;
▪
Yellow light – output logic alarm is disabled by user or after the module resetting;
▪
Red light – fatal error in module operation, module operation is disabled;
▪
Green (yellow) light flashing – sensor test error is detected for one of measuring channels.
MK40-DC
design option
Narrow front panel (width - 20mm) with restricted indication display and control system. Measurement results
review is only possible at reading via digital communication interfaces. Additionally, on the module front panel are
arranged:
•
“Pwr” green LED – module switching on;
•
“Ok” bicolor LED – module status indication;
•
“War” yellow LED – warning (LED operation logic is defined by user);
•
“Alarm” red LED – alarm (operation logic is defined by user).
а) MK40-DC б) MK40-DC-11 в) MK40-AC-11-S г) MK40-DC-001
Figure 1. MK40 Module front panel appearance
No revisions
7
D.port
Reset
об/мин
ВИБРО
БИТ
MK40
С1С2
Stop ∇1∇2∇3
Ok Err Max
Sel
ch Sel
∇Max
freq Logic
off
T-st T-ch
D.port
Reset
Ok
Pwr
War
ВИБРО
БИТ
MK40
Alarm
D.port
Reset
об/мин
ВИБРО
БИТ
MK40
С1С2
Stop ∇1∇2∇3
Ok Err Max
Sel
ch Sel
∇Max
freq Logic
off
T-st T-ch
Power
ON
D.port
Reset
Ok
Pwr War
ВИБРО
БИТ
MK40
Alarm
Mode Sel

Module MK40 Setup Manual
ВШПА.421412.304 И1
MK40-DC-11, MK40-AC-11-S
design option
MK40 Module front panel is provided with 7-segment 4-digit LED display with auxiliary LED’s and control keys.
In these MK40 Module design options only one measuring channel measurement results can be displayed at a time.
On the module front panel are arranged:
•
7-segment digital display for measurement results displaying.
•
Bicolor “Ok” LED – module status indication.
•
Yellow LED’s “C1”, “C2” - for selected measuring channel displaying. Flashing of “C1”, “C2”
LED’s indicates test signal generation at relevant measuring channel output;
•
Yellow “Stop” LED – “STOP” mode, rotor stop block. At “STOP” alarm testing, “Stop” LED
starts flashing;
•
Yellow LED’s “V1”, “V2” - for indication of parameters overrun of relevant set-points. During
displaying of set-point, relevant set-point LED flashes.
•
Red “Err” LED – indication of selected measuring channel fault. “Err” LED flashes, when
measuring channel normalization timeout is being count.
•
Yellow “Max” LED – displaying of rotor maximum speed. During sensor DC current displaying,
“Max” LED starts flashing;
•
Control keys:
•
“Sel ch” – switching between measuring channels. If measuring channel is disabled (during
the module setup), relevant measuring channel information is not displayed;
•
“Sel V” – set-points displaying. If set-point is disabled (during the module setup), relevant set-
point value is not displayed. At pressing and holding down of “Sel V” key, sensor DC current is
displayed;
•
“Max freq” – rotor maximum speed displaying. At pressing and holding down of “Max freq”
key, rotor maximum speed is reset;
•
“Logic off” – when held down for long duration, disables/enables module logic alarm;
•
Power-on toggle-switch “Power” (only for MK40-AC-11-S option).
At displaying of additional information (maximum rotor speed, set-point values etc.), module automatically
switches to rotor speed value displaying after preset timeout is count (30 seconds on default).
2
nd
measuring channel of MK40 Module can be set up in the module +24V supply voltage measuring mode.
After selection of 2
nd
measuring channel displaying, transition to 1
st
measuring channel displaying will be implementer
automatically upon timeout.
At simultaneous pressing of holding down of “Sel V” and “Max freq” keys, “STOP” alarm test is switched on/off
(“STOP” alarm test must be enabled in the module settings). At enabling of “STOP” alarm test “Stop” LED starts
flashing. Module automatically resets “STOP” alarm test during preset timeout (TimeOut_TestStop parameter).
At simultaneous pressing of holding down of “Max freq” and “Logic off” keys, external test signal at measuring
channel input is connected/disconnected (test signal connection must be enabled in the module settings). At
connection of external test signal relevant measuring channel “C1”, “C2” LED starts flashing. Module automatically
disconnects external test signal during preset timeout (TimeOut_TestMode parameter).
8
No revisions

ВШПА.421412.304 И1 SCIENTIFIC-PRODUCTION ENTERPRISE VIBROBIT LLC
MK40-DC-001
design option
MK40 Module front panel is provided with customized alphanumeric LCD, signal LED’s and control keys. All
measuring channel measurement results and measuring channels state can be displayed simultaneously.
On the module front panel are arranged:
•
Customized alphanumeric LCD with backlight;
•
Signal LED’s”
•
“Pwr” green LED – module switching on;
•
“Ok” bicolor LED – module status indication;
•
“War” yellow LED – warning (LED operation logic is defined by user);
•
“Alarm” red LED – alarm (operation logic is defined by user);
Two control keys
•
“Mode” key – display mode selection
•
“Sel” key – displayed data selection
Controlled parameter overrun of set-point is signaled by “V1”, “V2”, “V3” and “V4” symbols
(in frame).
“Er” (in frame) symbol indicates sensor fault detected in actual measuring channel;
measured parameter value is deemed equal to zero (lines are displayed on LCD), actual
measuring channels set-points alarm is inactive.
After measuring channel operation is normalized, “Er” symbol starts flashing, and the unit
counts measuring channel normalization timeout (set by user).
In “STOP” mode rotor speed value is deemed equal to zero, nonsignificant decimal point
is displayed after “0” symbol At “STOP” alarm testing, nonsignificant decimal point, following
rotor speed value, starts flashing.
At test signal connection to measuring channel input, empty frame of non-existing set-point 4 starts flashing on
top right panel of measuring channel data display.
In supply voltage measuring mode of 2
nd
measuring channel, actual supply voltage of the module is displayed
on bottom panel of measuring channel data display, while standard 2
nd
measuring channel data is not displayed.
In order to display maximum rotor speed, press “Mode” key until rotor speed value appears on LCD (in two
channels simultaneously). During maximum rotor speed displaying, measuring unit symbols “rpm” start flashing on
LCD, while symbols of measured parameter value overrun of set-point are not displayed. Return to normal display
mode is implemented by repeated pressing of “Mode” key or automatically upon timeout.
In order to display sensors direct current, press and hold down “Mode” key, until sensor current value appears
on LCD (in two channels simultaneously). During sensor current display, measuring unit symbols “mA” appear on LCD,
while symbols of measured parameter value overrun of set-point are not displayed. Return to normal display mode is
implemented by repeated pressing and holding down of “Mode” key or automatically upon timeout.
For set-points values displaying on LCD, press and hold down “Sel” key, until 1
st
measuring channel sign K1
and first set-point symbol V1 start flashing. By repeated (and short-term) pressing of “Sel” key, all three set-points of
actual measuring channel can be reviewed. Set-points values are displayed instead of measurement results. If set-
point is disabled (in module settings), lines are displayed instead of set-point.
Review of other measuring channel set-points values can be implemented by pressing “Sel” key or
automatically upon timeout.
Logic outputs on and off switching is implemented by simultaneous pressing and holding down of “Mode-Sel”
keys, until logic outputs operation mode is switched. When logic outputs are disabled, “Ok” LED glows yellow, and all
logic outputs are inactive.
No revisions
9
Figure 2. LCD data
display example

Module MK40 Setup Manual
ВШПА.421412.304 И1
Module operation
Switching power on
When switching power on, operating parameters are loaded from volatile memory. Operating parameters are
divided by sections:
•
Measuring channels parameters;
•
Module system parameters and communication interfaces parameter.
Check sum, which permits to ensure validity of loaded data, is added to each operating parameters section of
volatile memory. If calculated check sum is not matching sum, written to volatile memory, data is considered as
corrupted and can’t be used for module operation.
Each section of volatile memory has main and reserve storage. In case, that parameters section of volatile
memory is read with error, attempt is being made data reading from volatile memory reserve storage section.
In case of error occurrence in one of parameters sections, module operation is disabled, active signal level is
present at logic output 7, “Ok” LED glows red.
During standard loading of operating parameters before MK40 Module operation start:
•
MK40-DC option – “Ok” LED glows yellow to indicate module starting initialization.
•
MK40-DC-11, MK40-DC-001 and MK40-AC-11-S options - “Ok” LED glows yellow, module serial
number, and then, module year of manufacture is displayed on 7-segment indication display and MK40
initialization is implemented.
Note. Hot swap of MK40 module in section without disconnection from power supply is not recommended but
allowed for all MK40 Module design options.
After switching power on (resetting), logic outputs function is disabled for preset time. If logic outputs function is
disabled, “Ok” LED glows yellow.
Resetting
For Module resetting, microcontroller hand resetting is fulfilled and series of actions is made which corresponds
to power switching on. Reasons for MK40 Module resetting can be:
•
switching the module power on;
•
resetting upon user’s command (by means of ”Reset” key, located on the front panel or by command via
digital communication interfaces);
•
microcontroller supply voltage reduction (power source failure);
•
resetting by watchdog timer due to microcontroller program “hang up”.
By pressing hidden “Reset” key, installed on MK40 Module board, through the slot in module front panel, user
may implement resetting and “cold start” of the module.
For Module resetting – press “Reset” key for short period of time, and, after that pressing and hold
down “Reset” key until the module is reset.
Note. Module resetting can only be implemented after identification information (Module serial number, year of
manufacturing) is displayed and MK40 Module initialization cycle is complete.
10
No revisions

ВШПА.421412.304 И1 SCIENTIFIC-PRODUCTION ENTERPRISE VIBROBIT LLC
Module cold start
Cold start is meant for writing default operating parameters to volatile memory. This function is beneficial during
initial Module powering on or in the case, when module recalibration is to be carried out or known operating
parameters are to be set.
Switching to “Cold start” mode is implemented by pressing and holding down “Reset” key during entire cycle of
identification information displaying and module initialization after resetting.
If module transfers to Cold start mode, then:
•
MK40-DC option – “Ok” LED starts glowing yellow simultaneously with “War” LED.
•
MK40-DC-11, MK40-DC-001 and MK40-AC-11-S options – “Cold” message starts flashing on 7-
segment display.
After switching to cold start mode, the module “Cold start” mode must be confirmed. Confirmation of “Cold start”
mode is “Reset” key pressing sequence, which is similar to Module resetting sequence in normal operating conditions
(short-term pressing, pressing and holding down of “Reset” key).
At confirmation of the module “Cold start” mode, module settings are initialized by default setup and written to
volatile memory, after which the module is reset. If “Cold start” mode is not confirmed, module does over to normal
operation.
MK40-DC option
During settings writing to volatile memory, “War” LED flashes. Writing results can be determined by “Ok” LED
glowing color:
•
Green – writing is successful and error free.
•
Yellow – one or several data sections has been written to volatile memory at the second attempt.
•
Red – one or several data sections has been written to volatile memory with error.
MK40-DC-11, MK40-DC-001 and MK40-AC-11-S options
During writing “Load” message is displayed. Writing results can be determined by “Ok” LED glowing color (in the
same manner as for “Slim” option) and displayed message:
•
“Good” - writing is successful and error free.
•
“Bad” – one or several data sections has been written to volatile memory at the second attempt.
•
“Err” – one or several data sections has been written to volatile memory with error.
Results of operating parameters writing to volatile memory are displayed for 2 seconds, after which the module
is reset automatically.
No revisions
11

Module MK40 Setup Manual
ВШПА.421412.304 И1
Parameters measurement
MK40 Module operates in real-time mode with measurement results update rate of 250ms.
Module implements the following basic operations:
•
measures sensor current and monitors sensor functionality;
•
measures rotor speed;
•
repeats tachometric pulses for control modules synchronization, calculating variable signals (only for
“slot” reference surface);
•
compares calculated parameter values with set-points and signals overrun;
•
transfers measured values to standard outputs;
•
generates logic alarms;
•
updates data on display equipment;
•
supports data exchange via digital communication interfaces.
At measuring channels outputs resettable fuses and protective stabilitrons (triacs) are provided, which prevent
damage to module input circuits, caused by impulse interference or hazardous voltage level.
Both measuring channels function equally, synchronously and independently of one another. Only several
parameters are common (for detailed description of parameters, refer to Table 16):
•
PeriodMeasur - otor speed measurement period from 0.1 to 1.0 second;
•
TestPointSenseOk - set-points test timeout after sensor function normalization;
•
TimeOut_TestMode - “Measuring channel test” mode timeout;
•
TimeOut_TestStop - “STOP” mode test timeout;
•
SynhroPulse - pulse time of control modules measurements synchronization.
Sensor current measurement
Input current signal must be converted into voltage. For this purpose, precision resistors, corresponding to
sensor signal current range and removable bridge are provided at measurement channels input circuits. Input signals
range by voltage is from 0 to 5V.
Note. During measuring channel function operation with voltage signals, it is recommended to keep margin of
valid signal range in order to implement sensor functionality test function.
Input signal (voltage) passes through low-frequency filter (LFF) and arrives at 10-digit analog-digital convertor
(ADC) input, built in microcontroller. Within 250ms 521samplings of ADC values are implemented in each measuring
channel. ADC mean value is used in further calculations of sensor current. High number of ADC samplings permits to
achieve ADC actual DC resolution of 12bit due to averaging.
Sensor current is calculated by formula:
I
sense
= A
I
+ B
I
⋅ADC
where I
sense
– calculated value of sensor current;
ADC – averaged ADC value;
A
I
, B
I
– linear equation ratios for sensor current calculation.
Sensor current value I
sense
can be displayed (by pressing “Curr sense” key) and is used in sensor test algorithm
for calculation of changing parameter value.
A
I
, B
I
ratios are automatically calculated during module operation initialization by sensor current range data
(20% of RangeCurrMax, RangeCurrMax) and saved ADC values (AdcInMin, AdcInMax), corresponding to
sensor current input range, by which calibration has been carried out.
Note. If one of calibration value pairs (20% of RangeCurrMax, RangeCurrMax or AdcInMin, AdcInMax) is
equal to zero, or they are equal, then A
I
, B
I
ratios are not calculated and taken equal to zero (sensor current value I
sense
is always equal to zero).
12
No revisions

ВШПА.421412.304 И1 SCIENTIFIC-PRODUCTION ENTERPRISE VIBROBIT LLC
Sensor functionality test
Sensor test is carried out by I
sense
calculated value. Sensor is deemed functional, if value falls within acceptable
limits (CurrValidMin, CurrValidMax), setup during the module settings.
Monitoring of minimum/maximum acceptable sensor current can be disabled in the module settings
(EnaValidMin, EnaValidMax respectively). If sensor current monitoring is switched off at one of the limits, sensor
is deemed functional independent of calculated sensor current.
Enabling of sensor current monitoring can be useful, for example, during MK40 Module operation with sensor
signals level 0-5mA; in this case, disabling of sensor current lower limit monitoring is reasonable.
If I
sense
value is lower than minimum acceptable current level CurrValidMin, sensor signal level is deemed too
low (ErrorSenseLow, FlagError flags are activated). In order to normalize measuring channel function, I
sense
value must be higher than CurrValidMin + CurrValidHist (ErrorSenceLow flag is dropped).
If I
sense
value is higher than maximum acceptable current level CurrValidMax, sensor signal level is deemed
too high (ErrorSenseHigh, FlagError flags are activated). In order to normalize measuring channel function,
I
sense
value must be lower than CurrValidMin - CurrValidHist (ErrorSenceHigh flag is dropped).
When any abnormal sensor current level flag is activated (ErrorSenseLow, ErrorSenseHigh), measured
parameter value is taken as equal to zero.
It is not recommended to set sensor current level hysteresis value (CurrValidHist) equal to zero, as the
alarm frequent switch-over effect may occur.
After normalization of sensor function and ErrorSenseLow, ErrorSenseHigh flags are dropped, FlagError
flag is dropped after definite time interval TestPointSenseOK. After FlagError flag drop, calculated value of
measured parameter is compared with set-point.
In Figure 3 is shown an example of sensor test algorithm during sensor constant current decrease below
acceptable level. Sensor current acceptable levels are equal to 0,9mA and 5,1mA respectively, hysteresis – 0,1mA.
Figure 3. Sensor test algorithm during sensor constant
current decrease below acceptable level
After the module resetting, sensor is deemed functional, however timeout is to be counted before comparing
parameter value with set-points value, as FlagError flag is automatically activated after resetting.
No revisions
13
ErrorSenseLow
FlagError
0,9
1,0
5,1
5,0
Time TestPointSenseOk
Malfunction of the sensor is found
out, the parameter is equal to zero Comparing of value of
parameter with set point is authorized
Flag
Logic
level
Sensor
Current,
mA
Sensor operation was normalized,
the measured parameter is calculated
Time
Time

Module MK40 Setup Manual
ВШПА.421412.304 И1
Rotor speed measurement
Rotor speed measurement is implemented, providing that sensor fault was not detected (ErrorSenseLow,
ErrorSenseHigh flags are dropped). If sensor fault was detected (one of ErrorSenseLow, ErrorSenseHigh
flags is activated), rotor speed is not calculated and taken as equal to zero.
Note. Synchronizing pulses are generated (if enabled in the module settings), even if sensor fault was detected.
Definition of rotor speed is implemented by measuring of clock cycles, calculation of leading edge of timing
signal with frequency 10MHz between two clock cycles active fronts.
Clock cycle value is averaged during measurement cycle (determined by PeriodMeasur parameter), then rotor
speed is calculated in rpm (with provision for preset number of pulses per rotor revolution).
If only one clock cycle was detected during measurement cycle, non-averaged clock cycle value is used in rotor
speed calculation.
Minimum measured rotor speed is set by FrequencyMin (not less than 0.9 rpm). If rotor speed is below preset
value, synchronization pulses are deemed non-existing (rotor is stopped).
Synchronizing pulses polarity
Active front polarity of input pulses and repeated synchronizing pulses is determined by bridges on the module
board (see Annex A).
In Figure 4 are shown input/output synchronizing pulses diagrams for 1
st
measuring channel depending on
bridges position on the module board (same for 2
nd
measuring channel).
Synchronizing pulses are generated only if enabled in the module settings (PulseEnabled parameter).
Other ASVM modules synchronization (calculation of rotational components and phases) by MK40 Module input
signals must only be implemented at bridges selected active front, as inactive front of repeated synchronizing pulses
has jitter not greater than ±200mks (output synchronizing pulse duration 800-1000mks).
In order to synchronize simultaneous results acquisition by ASVM control modules, MK40 Module generates
synchronizing pulses with twofold duration and SynchroPulse time (if SynchroPulse is equal to zero, lengthened
synchronizing pulses are not generated).
Figure 4. Polarity of input and output synchronizing pulses
14
No revisions
Широкий импульс
синхронизации измерений (SynhroPulse = 5)
Активный фронт
Вхо ные
импульсы
Выхо ные
импульсы
S3 (2-3)
S3 (1-2)
S7 (1-2)
S7 (2-3)
Note. It is implied, that adjusting resistor is connected to positive supply of pulse output.
Rate of pulse rise is determined by output circuit capacitance and
adjusting circuit parameters (resistor resistance, adjustment voltage).
Rate of pulse rise is determined by output circuit capacitance and
adjusting circuit parameters (resistor resistance, adjustment voltage).

ВШПА.421412.304 И1 SCIENTIFIC-PRODUCTION ENTERPRISE VIBROBIT LLC
Comparing measured parameter value with set-point value
If FlagError flag is dropped (wait timeout is counted after sensor operation normalization), calculated rotor
speed value of is compared with set-points values, set during the module setup.
If sensor fault has been detected (one of ErrorSenseLow, ErrorSenseHigh flags is activated) or
FlagError flag is activated, comparison of calculated D
Param
value with set-points values is not implemented, and all
measured parameter value overrun flags are dropped.
Four set-points are provided for each measuring channel (TestPointData) with individually setup operating
modes (TestPointMode), general hysteresis level (TestPointHist) and overrun response time
(TestPointTime).
Table 3. Set-points operating modes
Mode code Description
0 Set-point is disabled, test is not carried out
1 Test above set-point value
2 Test below set-point value
Operating mode – set-points are disabled
Rotor speed value is not compared with TestPointData set-point, OutPoint flag is always dropped.
Operating mode - test above set-point value
If rotor speed value is higher than TestPointData set-point within TestPointTime time, parameter level is deemed
too high and OutPoint flag is activated. In order to drop OutPoint flag (normal level), rotor speed value must be lower
that TestPointData-TestPointHist within TestPointTime time.
Operating mode - test below set-point value
If rotor speed value is lower than TestPointData set-point value within TestPointTime time, parameter level is
deemed too low and OutPoint flag is activated. In order to drop OutPoint flag (normal level), rotor speed value must be
higher that TestPointData+TestPointHist within TestPointTime time.
Figure 5 shows an example of alarm function at set-point 2400rpm and hysteresis of 100prm.
Set-points test enabling in “STOP” mode is determined by StopEnabled parameter. If StopEnabled parameter is
equal to zero, in “STOP” mode rotor speed value (equal to 0) is not compared with set-points, rotor speed overrun
flags are inactive.
Figure 5. Example of set-point algorithm
(mode – test above set-point level).
No revisions
15
OutPoint
Time TestPointTime
Flag
Logic
level
Detected output value of
the parameter for set point Value of parameter is less set
point taking into account a hysteresis
Time
Time
Signaling switching-on
Signaling switching-off
Short-term surge doesn't
cause signaling switching
Freq, rpm
2400
2500

Module MK40 Setup Manual
ВШПА.421412.304 И1
Module supply voltage measurement
2
nd
measuring channel can be setup for measurement and monitoring of module and sensors supply voltage,
which power circuits are connected to MK40 Module. It is reasonable to use supply voltage measurement in MK40-
AC-11-S Module design option.
Enabling of the module voltage measurement is set during the module setup (ModeWork parameter). In this
mode 2
nd
channel frequency value is taken as equal to zero, all set-points are disabled.
Calculation of the module supply voltage is implemented by sensor current calculation algorithm (voltage value
is available in Current parameter). Voltage calculated value can be compared with sensor test set-points with alarm
generation at logic outputs.
At module supply voltage measurement in 2
nd
measuring channel, bridges on the module board must be set in
positions as follows (position of S4, S8, S5 is of no concern):
S3 – 1-2, 1-5mA current operating mode; S13 – OFF; S9 – ON
2
nd
measuring channel calibration is carried out at 1-5mArange.
Table 4. 2
nd
channel recommended parameters for module supply voltage measurement
Parameter Label Value Notes
Sensor current range lower level RangeCurrMin 8,27
Sensor current range higher level RangeCurrMax 41,36
Sensor lower limit test enabling EnaValidMin 1
Sensor higher limit test enabling EnaValidMax 1
Sensor current lower tolerance limit CurrValidMin 20
Sensor current upper tolerance limit CurrValidMax 28
Sensor test hysteresis CurrValidHist 0,5
Standard output current range lower level CurrOutMin 0
Standard output current range higher level CurrOutMax 0
ADC value of sensor current calibration lower level AdcInMin 1
ADC value of sensor current calibration higher level AdcInMax 1
DAC value of standard output calibration lower level DacOutMin 0
DAC value of standard output calibration higher level DacOutMax 0
Measuring channel enabling Enabled 1 volt
Measuring channel operating mode ModeWork 1
Test signal connection enabling TestEnabled 0
“STOP” alarm test enabling StopEnabled 0
Generate synchronizing pulses PulseEnabled 0
Measured parameter lower range RangeParamMin 0
Measured parameter higher range RangeParamMax 0
Minimum measured rotor speed, rpm FrequencyMin 1
Pulse count per rotor revolution Tooth 1
Data display format FormatOut 0 rpm
Set-points test enabling in “STOP” mode TestPointStop 0
Sensor current range lower level TestPointTime 0 0,5с
Sensor current range higher level TestPointMode_1 0
Sensor lower limit test enabling TestPointMode_2 0
Sensor higher limit test enabling TestPointMode_3 0
Sensor current lower tolerance limit TestPointData_1 0
Sensor current upper tolerance limit TestPointData_2 0
Sensor test hysteresis TestPointData_3 0
Standard output current range lower level TestPointHist 0
Note 1. Determined during calibration of measuring channel input
16
No revisions

ВШПА.421412.304 И1 SCIENTIFIC-PRODUCTION ENTERPRISE VIBROBIT LLC
External test signal
External test signal can be connected to measuring channel input. External signal source can be determined by
S5, S6 bridges.
For MK40-AC-11-S design option 50Hz test signal is generated from mains AC 220V 50Hz voltage.
Connection/disconnection of external timing signal can be implemented by commands via digital communication
interfaces or by user pressing front panel keys for MK40-DC-11 and MK40-AC-11-S design options.
Test signal connection must be enabled during the module setup (TestEnabled).
“STOP” mode test
MK40 Module can generate false “STOP” mode alarm signal at logic outputs. This function can be useful for
“STOP” alarm circuits test before equipment stop block.
Switching on/off of “STOP” mode test can be implemented by commands via digital communication interfaces or
by user pressing front panel keys for MK40-DC-11 and MK40-AC-11-S design options.
“STOP” mode test must be enabled during the module setup (StopEnabled parameter).
Standard output
Standard current output is provided for each measuring channel. Signal level at standard output is proportional
to measured parameter value. Standard output current range, corresponding to measured parameter range, can be
selected randomly during the module setup.
Current setting at standard output is implemented by 12-bit DAC and dynamic current amplifier, designed for
grounded load connection. Protective stabilitrons (breakdown voltage 27V) and 200mA resettable fuse for standard
output circuit protection.
DAC value of standard output is calculated by linear equation formula:
DAC
OUT
= A
O
+ B
O
⋅D
Param
where DAC
OUT
– DAC calculated value;
D
Param
– calculated value of measured parameter;
A
O
, B
O
– linear equation ratios for calculation of standard output DAC value.
A
O
, B
O
ratios are calculated automatically during the module operation initialization by standard output current
range data (CurrOutMin, CurrOutMax), measured parameter range (RangeParamMin, RangeParamMax) and
DAC saved value (DacOutMin, DacOutMax), corresponding to standard output range, at which calibration was
carried out (20% of CurrOutMax, CurrOutMax).
Note. If one of calibration value pairs (20% of CurrOutMax, CurrOutMax or RangeParamMin,
RangeParamMax or DacOutMin, DacOutMax) is equal to zero, or they are equal, then A
O
, B
O
ratios are not
calculated and taken equal to zero (DAC
OUT
value is always equal to zero).
No revisions
17

Module MK40 Setup Manual
ВШПА.421412.304 И1
Calibration recommendations
MK40 Module calibration technique permits to implement recalibration without cold start of the module, and
implement measuring channel range variation without recalibration of measuring channels and standard outputs. If
measuring channel or standard output current range variation is implemented, recalibration is required.
After the module calibration, calibration data must be loaded to module and stored in volatile memory, and the
module must be reset (or ratios recalculation command to be fulfilled).
MK40 Module connection set-up for calibration and test calibration is shown in Figure 6. MK40 Module
calibration is recommended on СП43 calibration bench, which permits to establish indicated test set-up.
Note. The module calibration is carried out by commands via digital communication interfaces by means of
dedicated software.
Вхо
2к
А– МП24 or БП17
В– МК40
R1 – resistance box 100kOhm
R2, R3 - 500±10 Ohm, 0.5V resistors
P1, P2 – DC microammeters 0-20mA, Class 0.2
P2 – DC voltmeter, Class 0.1
Note. P2, R2 are used for voltage measuring channels test.
Figure 6. MK40 Module connection set-up for calibration and test calibration
18
No revisions
R1
мА
VмА
P1
P2 R2
R3
P3
A6, B5,
C6
A2, A32,
B1, B31
+24В
B15
C8
C10
В
A6, B5,
C6
A2, A32,
B1, B31
+24В
А
+
++А16
~220В
~220В
C14
C16
~220В
Pin
Pin
Line
Line
0, Common
0, Common
Unified output 1
Unified output 2
Input 1к
Input 2к

ВШПА.421412.304 И1 SCIENTIFIC-PRODUCTION ENTERPRISE VIBROBIT LLC
Measuring channel input calibration
Measuring channel input calibration sequence is simple enough:
1. Indicate measuring channel current range value (RangeCurrMin, RangeCurrMax);
2. Indicate measured parameter range (RangeParamMin, RangeParamMax);
3. Set 20% of RangeCurrMax current at channel input;
4. Rewrite AdcData value to AdcInMin;
5. Set RangeCurrMax current at channel input;
6. Rewrite AdcData value to AdcInMax;
7. Transfer calibration results to MK40 Module;
8. Implement ratios recalculation.
Alteration of measured parameter range consists in alteration of RangeParamMin, RangeParamMax
parameters.
Calibration wizard is provided in dedicated MK40 Module setting software, which considerably simplifies
calibration process.
Standard output calibration
By measured parameter, standard output range corresponds to input range (RangeParamMin,
RangeParamMax). Standard output calibration consists of the following steps:
1. Indicate standard output current range value (CurrOutMin, CurrOutMax);
2. By writing of value to DacDirectData select current (by means of microammeter), equal to 20% of
CurrOutMax, at standard output;
3. Rewrite DacDirectData value to DacOutMin;
4. By writing of value to DacDirectData select current (by means of microammeter), equal to
CurrOutMax, at standard output;
5. Rewrite DacDirectData value to DacOutMax;
6. Write zero to DacDirectData (switch on calibration mode);
7. Transfer calibration results to MK40 Module;
8. Implement ratios recalculation.
Alteration of input measured parameter range (RangeParamMin, RangeParamMax) automatically changes
parameter range at standard output. Calibration wizard is provided in MK40 setup software for module calibration,
which considerably simplifies calibration process.
Note. Writing of calibration results to MK40 Module and recalculation of ratios can be carried out once after all
calibration steps (input, standard output) are completed.
No revisions
19

Module MK40 Setup Manual
ВШПА.421412.304 И1
Logic outputs
In MK40 Module 6 logic outputs with open collector (active 0) are provided.
Logic outputs circuit design provides for possibility of direct relay coils connection.
Operation of each of 6 logic output is setup by user via digital communication interfaces.
If check sum error has been detected in one of the module operation parameters section, active signal level is
present at logic output 6, while other MK40 Module logic outputs remain in dormant state.
After module resetting, logic outputs are disabled for LogicOffStartUp period of time, counted after module
initialization cycle termination.
Logic outputs operation can be disabled by user, which may be required during module operating parameters
correction or functionality test of the module, without risk of alarm or shutoff protection trip.
MK40 Module includes “OR” matrix (LogicMatrix) for switching of status flags (of measuring channels and
general module status) to logic outputs. If at least one flag, assigned for logic output, is activated, active signal level
will be present at relevant logic output, unless logic outputs are disabled.
Number of logic output, to which it will be assigned, is indicated for each flag. If number of logic output is equal
to o or greater than 6, state of relevant assigned flag will not affect any of logic outputs.
Table 5. Measuring channels status flags StatusCh and their position if logic outputs matrix LogicMatrix
Bit
No. Label Description Code Position in matrix
Channel 1 Channel 2
0OffMode Measuring channel is off Off 8 16
1ErrorSenseLow Sensor current below acceptable level xSL 9 17
2ErrorSenseHigh Sensor current above acceptable level xSH 10 18
3FlagError Measuring channel general fault flag xFE 11 19
4StopMode “STOP” mode xSM 12 20
5OutPoint_1 Parameter value overrun of set-point 1 xS1 13 21
6OutPoint_2 Parameter value overrun of set-point 2 xS2 14 22
7OutPoint_3 Parameter value overrun of set-point 3 xS3 15 23
Note.
In alarm code instead of “x” symbol, channel number should be indicated (for example 1SH).
Table 6. Module status flags StatusSys and their position if logic outputs matrix LogicMatrix
Bit
No. Label Description Code Position
in matrix
0ErrorLoadData Operating parameter readout from volatile memory error ErrLD 0
1LoadDataReserv One or several operating parameters groups are readout
from volatile memory reserve storage ResLD 1
2LogicOffStartUp Logic outputs are disabled after module resetting LgOffSt 2
3LogicOffUser Logic outputs are disabled by user command LgOffU 3
4InterfRS485_Off RS485 Interface is off RS_Off 4
5InterfCAN_Off CAN2.0B Interface is off CAN_Off 5
6AllowOneWrite Single write access is obtained OneWr 6
7CalibrateMode Calibration mode is on for one of standard outputs Calibr 7
Note. For changing module operating parameters, logic outputs must be disabled or permit for single write in
operating parameters must be gained.
20
No revisions
This manual suits for next models
1
Table of contents
Popular Control Unit manuals by other brands
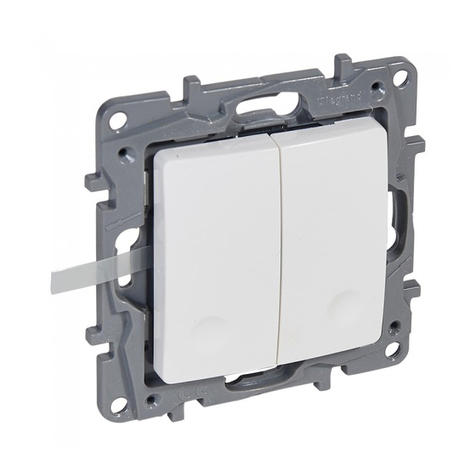
LEGRAND
LEGRAND 0 746 85 manual
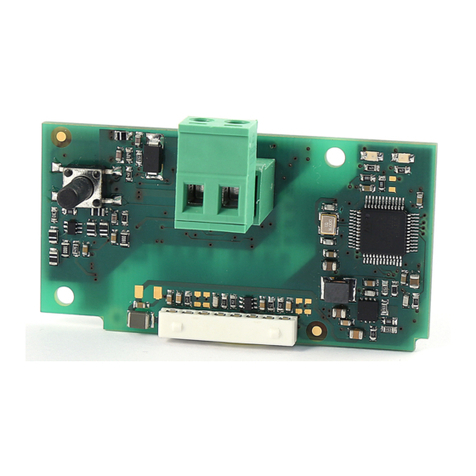
Carel
Carel PCOS00KXN0 user manual
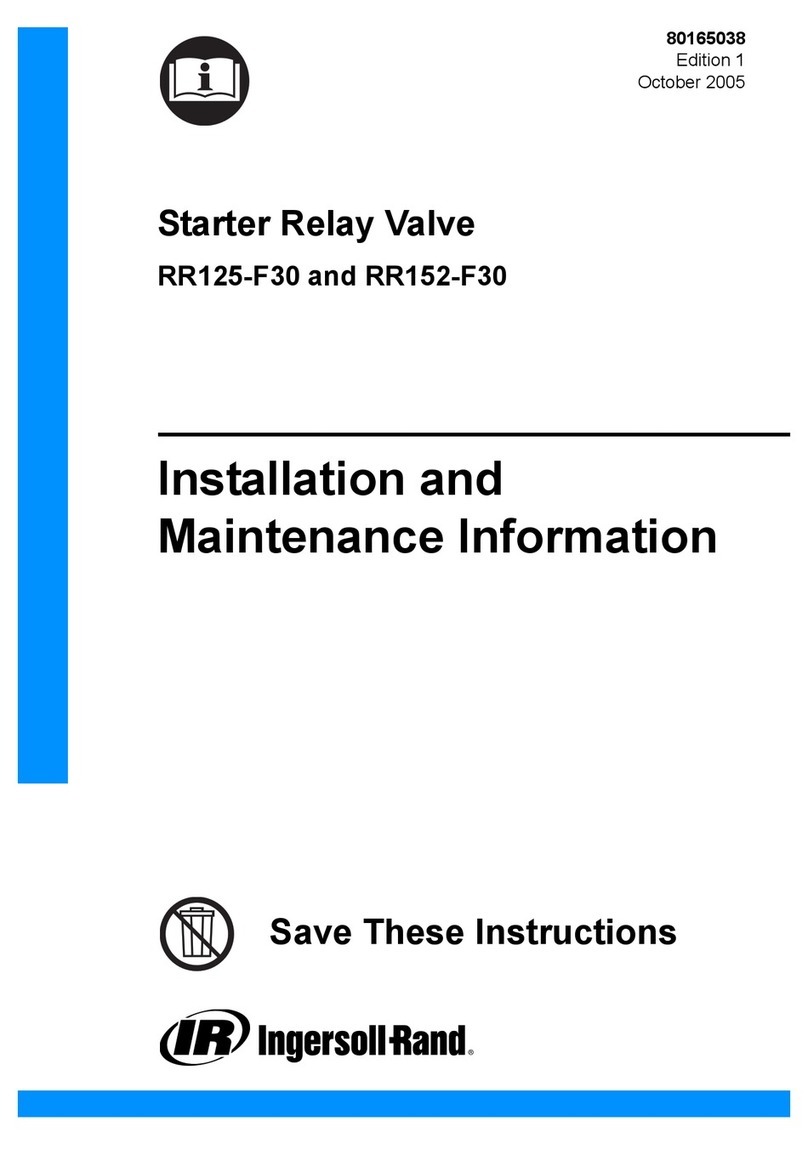
Ingersoll-Rand
Ingersoll-Rand RR125-F30 Installation and maintenance information
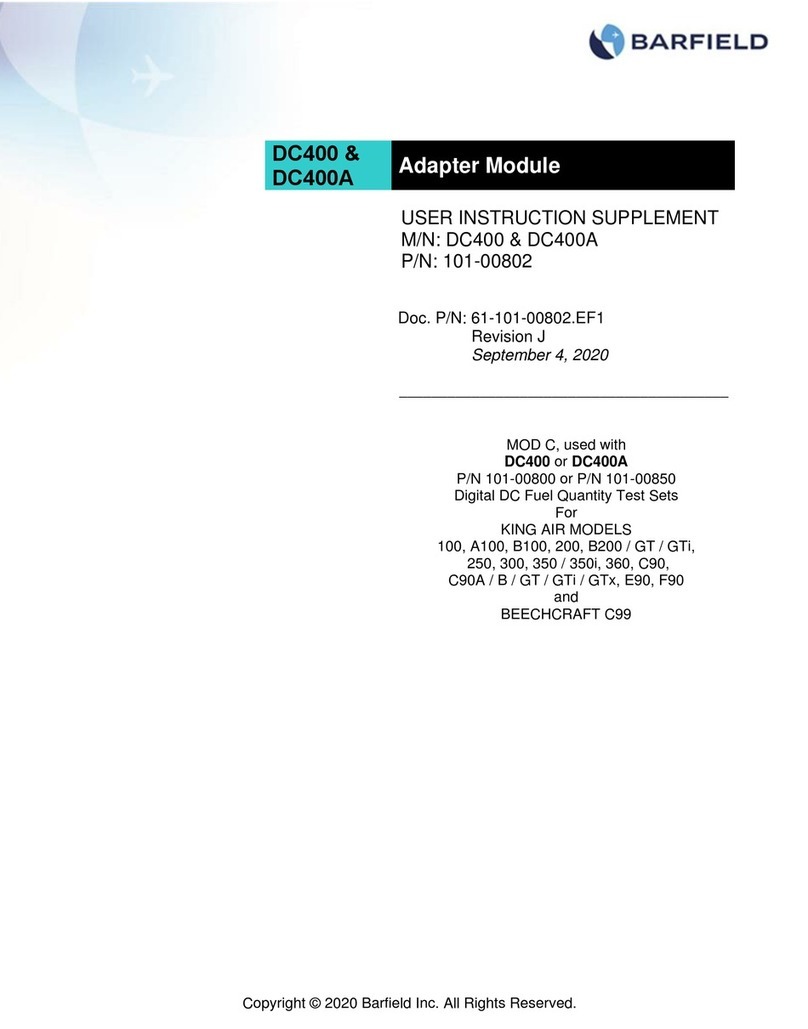
barfield
barfield DC400 User Instruction Supplement
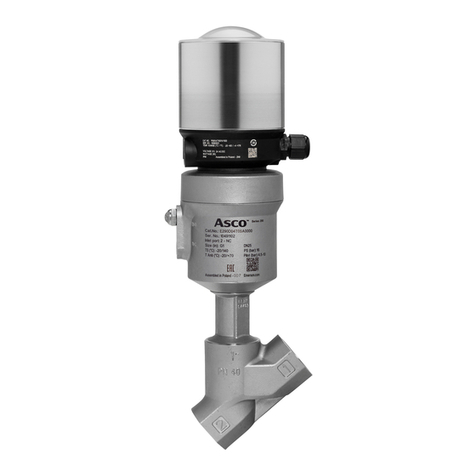
Emerson
Emerson ASCO 290 Series Installation and maintenance instructions
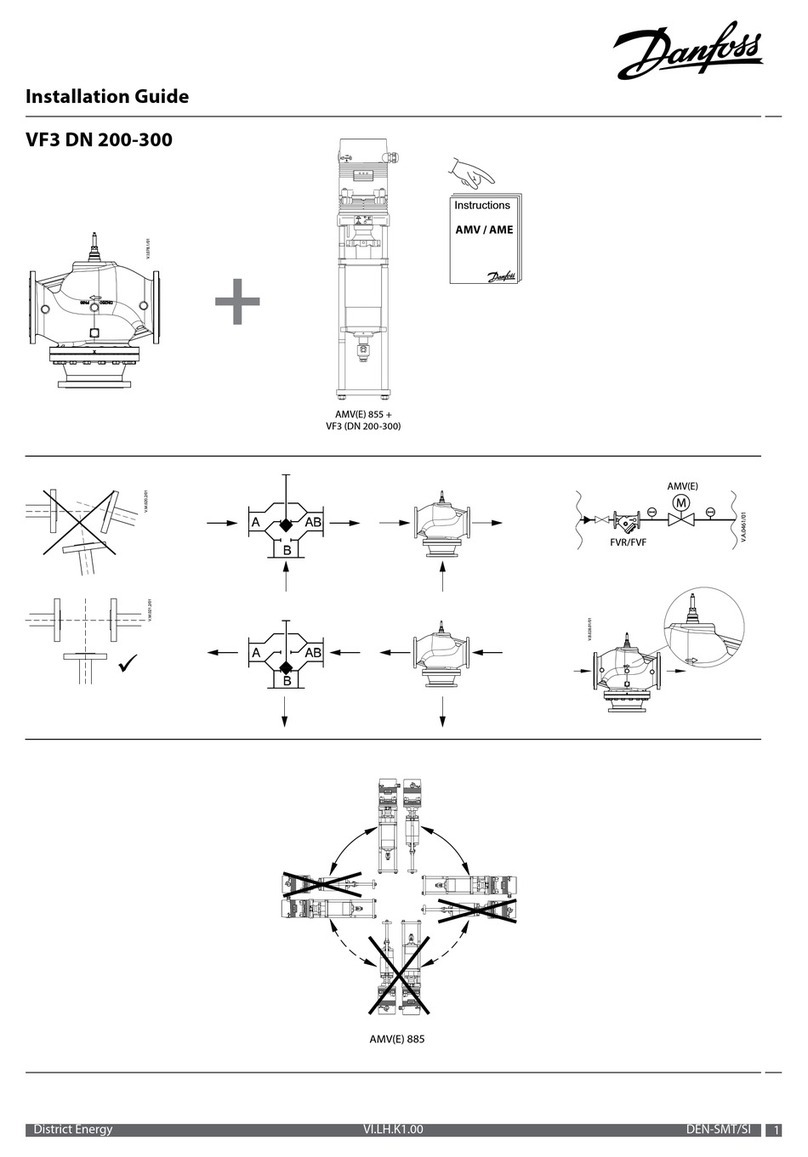
Danfoss
Danfoss VF3 DN 200 installation guide