GEA VP8002 User manual

AutoSelect CowScout
VP8002
DairyRobot
Velos
ID
VP8002 - Control unit for herd management
processes
Operation Manual / Installation Instructions / Parts List
(Original instructions)
7160-9001-560
01. December 2020
gea.com

7160-9001-560
01. December 2020
2 / 74
Contents
1 General 4.................................................................
1.1 Information on the document 4...............................................................
1.2 Manufacturer's address 6....................................................................
1.3 Customer service 6.........................................................................
1.4 EU Declaration of Conformity for Electrical Equipment 7..........................................
2 Safety 8...................................................................
2.1 Use for the intended purpose 8...............................................................
2.2 Owner's obligation of care 8..................................................................
2.3 Subsequent modifications 9..................................................................
2.4 Explanation of the safety symbols 9...........................................................
2.5 General safety instructions and dangers 10......................................................
2.6 Personnel qualifications 10....................................................................
3 Description 11..............................................................
3.1 Technical Data 14...........................................................................
3.2 Default setting 14............................................................................
4 Transport and storage 15...................................................
4.1 Safety Instructions for transportation 15.........................................................
4.2 Storage conditions 15........................................................................
4.3 Disposing of packaging material 15.............................................................
5 assembly and installation 16................................................
5.1 Special Personnel Qualifications 16............................................................
5.2 Safety Instructions 16........................................................................
5.3 Particular hazards 16.........................................................................
5.4 Requirements 16............................................................................
5.5 Preparations before installation 16.............................................................
5.6 Installing the control unit and power supply unit 17................................................
5.7 Electrical Installation 21.......................................................................
5.7.1 Connect control unit (VP8002 - DairyPlan-PC) 22.................................................
6 Commissioning 25..........................................................
6.1 Special Personnel Qualifications 25............................................................
6.2 Particular hazards 25.........................................................................
6.3 Basics of commissioning 26...................................................................
6.3.1 Settings in Device menu (VP8002) 28..........................................................
6.3.2 Settings in the user interface (VP8002) 31.......................................................
6.3.3 User interface menu and function overview (VP8002) 33..........................................
6.4 Checks before commissioning 41..............................................................
6.5 Commissioning the control unit 42..............................................................
6.5.1 Adjusting the control unit for automatic milking systems 43.........................................
6.5.2 Installing a control unit in the DPNet network 44..................................................
6.5.3 Setting up control units individually 49..........................................................
6.6 Checks after commissioning 50................................................................
6.7 Handing over to the owner 51.................................................................
7 Operation 51...............................................................
8 Maintenance 52............................................................
8.1 Special Personnel Qualifications 52............................................................
8.2 Safety Instructions 52........................................................................
8.3 Particular hazards 52.........................................................................
8.4 Firmware update 53..........................................................................
8.5 Restoring the factory setting (VP8002) 55.......................................................

7160-9001-560
01. December 2020 3 / 74
9 Troubleshooting 56.........................................................
9.1 Special Personnel Qualifications 56............................................................
9.2 Particular hazards 56.........................................................................
9.3 Fault messages and troubleshooting help (VP8002) 56............................................
9.3.1 Messages via device LEDs 57.................................................................
9.3.2 Error output via LED display (dE - display Error) - VP8002 58......................................
9.4 Troubleshooting possible errors 60.............................................................
9.4.1 Processing system messages (Dashboard) 60...................................................
9.4.2 Check the behaviour component 61............................................................
9.4.3 Network troubleshooting (Ethernet) 61..........................................................
9.5 Replacing the control unit 62..................................................................
9.5.1 Replacing the control unit (VP8002 with VP8002) 62..............................................
9.5.2 Replacing the control unit (VP8001 with VP8002) 67..............................................
10 Decommissioning 70.......................................................
10.1 Special Personnel Qualifications 70............................................................
10.2 Safety Instructions 70........................................................................
10.3 Final Decommissioning / Disposal 70...........................................................
11 Spare Parts 71.............................................................
12 Appendix 73...............................................................
12.1 Directories 73...............................................................................

General
Information on the document
7160-9001-560
01. December 2020
4 / 74
1 General
1.1 Information on the document
● This manual is supplied with the product.
● This manual should be kept close at hand and remain with the equipment even
when the equipment is sold.
● Reproductions, translations and copies of any kind, even of extracts, require
written authorisation from the manufacturer.
● This edition of this manual is not subject to any amendment service.
● The manufacturer reserves the right to make changes due to technical
developments in the data and images given in this manual.
● In this manual the word ”product” is synonymous with:
Control unit VP8002
Purpose of the manual
This manual describes the control unit in detail (VP8002)
Similarities with the VP8001 control unit and differences are also pointed out
(VP8002 vs. VP8001)
Structure of the manual
● This manual has a modular structure and is intended exclusively for the named
product.
● For more information on the product and its associated components, please
refer to the corresponding documents and manuals.
This applies especially to the safety instructions!
● The abbreviations, units, technical terms, special names or industry-specific
terminology used in this manual are explained in greater detail in the Appendix.
Necessary documents
● Instructions on components associated with the product:
(not a complete list)
Part No. Description
7169-90 . . - . . . Animal segregation AutoSelect ”...” (ethernet)
7160-90 . . -427 Animal identification (neck/leg/ear) VP1801 (ethernet)
7160-90 . . -538 Heat detection and health monitoring
system CowScout
7160-90 . . -540 Per place identification PPID
All the manuals for other installed subsystems.
This applies especially to the safety instructions!
Supply sources
The manuals can be obtained as follows:
● Order the paper version from the manufacturer or dealer.
● Download the file from the Internet (for technical dealers only)
https://extranet.ft.gea.com/

General
Information on the document
7160-9001-560
01. December 2020 5 / 74
Layout elements
Pictograms used
Please note
The signal word indicates information that is important for the product and
environment.
This pictogram refers to an information source.
(chapter, manual, Internet, etc.).
70 . . -90 . . -000 If a manual number is given, the middle 4 figures
indicate the language, as follows:
Language Language Language
-9000- German -9013- Dutch -9032- Serbian
-9001- English (United
Kingdom)
-9015- English (North
American)
-9034- Slovak
-9002- French (France) -9016- Polish -9035- Chinese
-9003- Italian -9018- Japanese -9036- Lithuanian
-9004- Romanian -9021- Danish -9038- Portuguese (Brazil)
-9005- Spanish (Spain) -9022- Hungarian -9039- French (Canada)
-9007- Swedish -9023- Czech -9040- Latvian
-9008- Norwegian -9024- Finnish -9041- Estonian
-9009- Russian -9025- Croatian -9043- Spanish (Central
America)
-9010- Greek -9027- Bulgarian -9046- Vietnamese
-9012- Turkish -9029- Slovene
All of the above languages may not be available.
!A correction bar in the margin indicates changes to the previous edition.
Header
The top line on each page provides information on the
main subject of that page. Main heading
Subheading
Main heading
Subheading
User aids
The character string ”!!” in the search field of the PDF document jumps to
correction bars. !

General
Customer service
7160-9001-560
01. December 2020
6 / 74
1.2 Manufacturer's address
GEA Farm Technologies GmbH
Siemensstraße 25-27
D-59199 Bönen
+49 (0) 2383 / 93-70
+49 (0) 2383 / 93-80
www.gea.com
1.3 Customer service
Authorized Technical Dealer
If necessary, contact your nearest authorized technical dealer.
There is a comprehensive dealer Internet search function on our website at the
following address:
www.gea.com
European Contact Information:
GEA Farm Technologies GmbH
Siemensstraße 25-27
D-59199 Bönen
+49 (0) 2383 / 93-70
+49 (0) 2383 / 93-80
www.gea.com
USA Contact Information:
GEA Farm Technologies, Inc.
1880 Country Farm Dr.
Naperville, IL 60563
+1 630 369 - 8100
+1 630 369 - 9875
www.gea.com

General
EU Declaration of Conformity for Electrical Equipment
7160-9001-560
01. December 2020 7 / 74
1.4 EU Declaration of Conformity for Electrical Equipment
Manufacturer: GEA Farm Technologies GmbH
Siemensstraße 25-27
D-59199 Bönen
We, as manufacturer, declare in sole responsibility that the electrical equipment
Name: Universal control unit
Model: VP8002
Type:
complies to all relevant harmonization provisions of law of this and the following directives:
Relevant EC-Directives: 2014/30/EU EMC Directive
2011/65/EU RoHS Directive to restrict the use of certain hazardous
substances in electrical and electronic equipment
EN 61000-6-2 (2016)
EN 61000-6-3 + A1 (2007+2011) Electromagnetic compatibility (EMC)
Bönen,
16. November 2020
Peter Lauwers
(Managing Director)
i.A. Frank Hölscher
(Head of Milking Equipment)

Safety
Owner's obligation of care
7160-9001-560
01. December 2020
8 / 74
2 Safety
2.1 Use for the intended purpose
The product described has been designed for use in agricultural (mainly milk
producing) environments.
The VP8002 control unit is designed to control the following processes on a dairy
farm:
● Animal identification in the milking parlour
● Animal segregation (AutoSelect - Ethernet)
● System zur Heat detection and health monitoring (CowScout)
● Process control of the DairyNetBox herd management system
Applications which are not listed here are not part of the intended use and are
therefore considered as improper use.
The manufacturer/supplier is not liable for any resulting damage. The user alone
bears the risk.
Use for the intended purpose also includes reading the instructions and observing
the inspection and maintenance conditions.
● We would specifically like to point out that parts or accessories not supplied by
ourselves and setting instructions not provided by GEA Houle are not checked
or released by us either.
● The installation or use of products from other manufacturers may affect the
specified properties of the original parts and lead to injury to persons and
animals.
● The manufacturer does not accept any liability for injury to persons or animals,
or damage to the product, caused by the use of products from other
manufacturers.
2.2 Owner's obligation of care
The product has been designed and constructed taking account of a potential risk
analysis and after careful selection of the compliant harmonized standards and
other technical specifications. It therefore ensures a maximum level of safety.
This safety can only be achieved in practice on the farm, however, if all the
necessary measures have been taken. It is part of the owner's duty of care to plan
these measures and check that they are carried out.
(producing appropriate operating instructions for example)
The owner must ensure the following:
● A complete, legible copy of the manual must always be available at the place
where the product is installed.
● All persons who work with the product must be able to consult the manual at all
times.
● The instructions in the section ”General safety instructions and dangers” must
be followed.
● The legal requirements are observed.
● The product may only be used for its intended purpose.
● The product may only be used if it is in perfect working condition. The safety
equipment, in particular, must be checked regularly to ensure it is working
properly.

Safety
Explanation of the safety symbols
7160-9001-560
01. December 2020 9 / 74
● Work should only be carried out by suitably qualified persons.
● The personnel is regularly instructed in all relevant matters of safety at work and
protection of the environment and is familiar with the manual, particularly the
safety instructions it contains.
2.3 Subsequent modifications
Unauthorized modifications to the product can have a negative impact on the
safety, life span or functionality of the product.
Any modifications not described in the product documentation are deemed to be
prohibited.
For reasons of safety, do not carry out any unauthorized modifications.
Any changes to the product must be approved in writing by the manufacturer.
Any unauthorized modifications to the product will invalidate the warranty and may
invalidate the conformity or installation declaration provided.
2.4 Explanation of the safety symbols
Safety symbols draw attention to the importance of the adjacent text.
The warning signs are designed in accordance with ISO 3864-2 and ANSI535.6.
Safety symbols and signalling word
Warning!
The signal word indicates an immediate danger that could lead to loss of life
or serious physical injury.
Important!
The signalling word indicates hazardous situations that could lead to
damage to property.

Safety
Personnel qualifications
7160-9001-560
01. December 2020
10 / 74
2.5 General safety instructions and dangers
Please note
There are warnings about specific residual hazards in the corresponding
chapters.
● There are risks involved in the operation and maintenance of equipment for
large livestock farms. For your own safety, please carefully read and observe
the instructions (especially the section ”Safety”).
● Do not open or dismantle devices (risk of injury).
● Always observe the warnings given in the product safety data sheets and
operating instructions when using products from other manufacturers!
● Always keep the switchgear cabinet / all electricity supply units / electrical
control units closed. Access is only permitted to authorized personnel with a key
or special tool.
● There are risks involved in the operation and maintenance of equipment for
dairy farms. For your own safety, read and follow the operating manual carefully!
● Protect live and high-voltage components against moisture. Do not use water
or high-pressure cleaners on these electrical products!
2.6 Personnel qualifications
Everyone who performs work or activities in connection with the product must
carefully read and understand the manual and then act accordingly.
● All work on electrical equipment and electrical connections should only be
performed by trained electricians.
In addition, special qualifications are required for the following activities:
● Mounting
● Commissioning
● troubleshooting
● repairs
Please note
If the work requires special qualifications, these are described in the
corresponding chapters.

Description
7160-9001-560
01. December 2020 11 / 74
3 Description
VP8002 vs. VP8001 - Control units in comparison
Please note
The VP8002 control unit is the successor of the VP8001 control unit. Both
control units are almost identical in design and function.
For this reason, the information on the VP8001 control unit in additional
instructions also applies to the VP8002 control unit!
Differences to the VP8001 control unit are explicitly outlined in these
instructions.
Control unit - VP8002
The VP8002 is a universally configurable
control unit.
Functions
● Control of connected systems
● Analysis of animal data and its internal
storage
● Warning messages
VP8002
Features
● The control unit has an internal memory and works independently (independent
of a PC)
● Data backup in the event of a power failure
In the event of a power failure, the built-in capacitor briefly bridges the power
supply. In the event of a longer power failure (approx. 15 seconds), the data is
saved and the control unit is shut down.
● Access to the user interface of the control unit via internet browser,
e.g. from various devices (PC, tablet, ...).
● Simultaneous login of multiple users.
The control unit in the network
● Communication with peripheral devices via CAN bus and ethernet.
Ethernet:
- LAN 1: Communication with the DPNet network, or an external network (e.g.
internet)
- LAN 2: Communication with the internal network for Velos devices
- e.g. VP4102
- Connection only on the VP8002 control unit.
CAN bus:
- Connection of Velos devices with the CAN bus
(e.g. for VP1004 transceivers)
● When used with a herd management system, the control unit uses the animal
and farm data managed there.

Description
7160-9001-560
01. December 2020
12 / 74
Licensed control units for connected systems
VP8002
● ID / PPID
● AutoSelect
● CowScout
● DairyNetBox
LicenceSoftware (section) System (function)
● The control unit controls different processes and functions of connected
systems.
Examples: connected systems
(not a complete list)
- Animal identification in the milking parlour (ID)
- Walk-through identification
- Per place identification (PPID)
- Animal segregation (AutoSelect - Ethernet)
- Walk-through identification
- System zur Heat detection and health monitoring (CowScout)
- Process control of the DairyNetBox herd management system
(corresponds to DPProcessControl in DairyPlan)
For example, in the milking systems: DairyProQ / DairyRobot)
Due to the higher-level control function, the control unit is part of the connected
system.
● The control unit software is divided into system-specific sections that are
activated using licences (corresponds to DairyPlan).
● In the case of new installations, the control units are licensed ex works.
In the case of replacements, the control unit must be licensed.

Description
7160-9001-560
01. December 2020 13 / 74
Examples
Per place identification - PPID (Side-by-Side - CAN-Bus)
LAN1
E
VP8002
A
D
B
LAN2
(CAN-Bus)
VP1004
Animal segregation - AutoSelect 3000 - Ethernet
LAN1
E
VP8002
A
D
B
LAN2
(Ethernet)
VP1801
Item Components
AHerd management PC DairyPlan
BEthernet switch or hub
CControl unit VP8002
DElectrical requirements
EConnected system
Per place identification - PPID (SbS)
● transceiver
● antenna
VP1004
VP6011
Animal segregation - AutoSelect 3000 - Ethernet
● transceiver VP1801

Description
Default setting
7160-9001-560
01. December 2020
14 / 74
3.1 Technical Data
Environment/thermal data (VP8002)
Operating temperature -10 - 45 ºC [14 -113 ºF]
Transport and storage temperature -25 - 70 ºC [-13 -158 ºF]
Relative humidity 10-93%
Electrical specifications (VP8002)
Input voltage range 25 VDC,+10% ,-10%
Output voltage 25 VDC,+10% ,-10%
Power consumption 300mA
Short-circuit protected (power supply)
Inputs 2x digital
Outputs 2 x (250 mA)
2 x (4 A - CAN-Bus)
CAN bus communication 125 kbit/s,2 channels
Communication Ethernet LAN 100/10 Mbps
Firmware / Software downloadable
Protection class IP20
Internal power supply
Maximum current 2 A
Housing (7159-2853-050)
Protection rating IP 65
Geometric data
lengthxWidthxElevation
(without mounting rail)
143 x 127 x 68 mm
weight 400 g
3.2 Default setting
Other settings can be used.
For more information on this subject, please refer to the section on
Commissioning
Important!
Incorrect settings can have a negative effect on the health of the animals,
the quality of the milk and milking results.
► Changes may only be carried out by trained personnel.
► Check all factory settings before commissioning and adjust to the
individual requirements of the installation or animal if necessary.

Transport and storage
Disposing of packaging material
7160-9001-560
01. December 2020 15 / 74
4 Transport and storage
4.1 Safety Instructions for transportation
Special transport hazards
To prevent damage to property and/or life-threatening injury to personnel, always
observe the following:
● Projecting sharp edges may cause cuts.
● If parts are stacked too high, the stack can become unstable and collapse.
● If load suspension devices other than those indicated here are used, this may
lead to serious damage to property and/or life-threatening injury to people.
● The highly inflammable packaging material represents a fire hazard - naked
lights and smoking are prohibited.
4.2 Storage conditions
● Storage temperature range: -25ºC to 70ºC
When storing the goods supplied, the location must provide protection against:
● Humidity/Moisture
● frost
● external damage (bumps, knocks, rodents, insects, . . . )
● Direct sunlight
4.3 Disposing of packaging material
After unpacking, the packing material is to be handled properly and disposed of
carefully in accordance with the valid local regulations on waste disposal and
utilization.

assembly and installation
Preparations before installation
7160-9001-560
01. December 2020
16 / 74
5 assembly and installation
If necessary, contact your nearest authorized technical dealer.
5.1 Special Personnel Qualifications
Installation may only be carried out by specially qualified personnel in accordance
with the safety instructions.
● Participation in corresponding product training is necessary.
See also the section on ”Personnel qualification”.
5.2 Safety Instructions
To prevent damage to property and/or life-threatening injury to personnel always
observe the following:
● The installation must be carried out in accordance with national standards and
regulations.
Example:
Carry out electrical installation work in accordance with the following standards
and requirements:
- EN 60204, Point 14 (Electrical equipment of machines).
- VDE 0100 (Regulations on the erection of power installations)
● Before installation, look for any damage caused by transport. Do not use
damaged components.
● Use only the special tool indicated for assembly.
● In the cases of devices with 24 V direct voltage, the power supplies stipulated
by the manufacturer and approved for the devices must be used, because the
safety of personnel and of the building cannot be ensured otherwise.
● Also read the chapter on Safety.
5.3 Particular hazards
● Electronic components may be damaged by electrostatic processes.
- Only touch the edge of the plug-in contacts and avoid static caused for
example by clothing.
● Before working on electrical installations or equipment (components, housings,
etc.), they must be disconnected from the mains.
Any on/off or emergency stop switches must be fitted with a lock to immobilise
them in the open position and a warning sign should be put up.
● Components which have been incorrectly set down or which have not been
fastened properly may fall off or collapse.
● Parts loosely placed on top of each other can slip and fall off.
● Components with sharp edges which are still exposed and accessible represent
a source of injury.
5.4 Requirements
The product must be installed in a well ventilated frost-free room.
Environmental Specifications
See section: "Technical data"
5.5 Preparations before installation
Necessary documents
For more information on this subject, please refer to the section on
Information on the document

assembly and installation
Installing the control unit and power supply unit
7160-9001-560
01. December 2020 17 / 74
Local purchased items
● Network switch (if more than one VPU)
5.6 Installing the control unit and power supply unit
Installation variants
The control unit can be installed in the following ways:
● In the housing(with an internal power
supply)
- Wall installation
- Installation of the frame
VP8002
SV
● In the housing(with an external power
supply)
- Installation of the frame
Example:
- Per place identification (AR PerFormer)
VP8002
SV
● In the control cabinet (pre-assembled, with an external power supply)
Example:
Per place identification (DairyProQ)
Installation instructions
● For installation variants not described, please refer to the corresponding
instructions for the connected system.
● In the milking parlour, the unit must be installed in a housing with IP65
protection!
● Install network cables at sufficient distances to live cables.

assembly and installation
Installing the control unit and power supply unit
7160-9001-560
01. December 2020
18 / 74
Mounting material
7160-5979-040 7160-5979-050
10
40-70
20
30
7160-5979-060
Item Part -No. Description Quantity
7160-5979-040
Set of accessories
Ø2” -340
7160-5979-050 Ø1,5” -350
7160-5979-060 Ø1” -360
0010 7159-2853-020 retaining plate 111
0020 0019-2227-300 Cheese head screw 444
0030 7019-2209-050 Angle bracket 2 2 -
7019-2209-030 15 - - 2
0040 0019-6933-300 Hexagon bolt M10x20 444
0050 0013-0279-300 Hexagon Nut M10 444
0060 0026-1248-300 Washer 444
0070
7049-3270-000
U-bolt, complete
2” 2 - -
7027-3270-010 Ø1,5” M8 - 2 -
7027-3270-020 Ø1” M8 - - 2
7160-2187-010
10
30,40
20
7160-5979-070 10
40-70
20
30
Item Part -No. Description Quantity
7160-2187-010 Mount, compl. Wall installation x
7160-5979-070 Set of accessories Ø 71-114 mm x
0010 7159-2853-020 retaining plate 276x230x20x2 1 1
0020 0019-2227-300 Cheese head screw M4x35 4 4
0030 0019-5311-050 Wood screw Ø8x70 4 -
0030 7160-5209-110 Angle bracket - 2
0040 0026-2304-890 Rawlplug Ø10 4 -
0040 0019-5550-300 Bolt M6x16 - 4
0050 0013-0276-300 Hexagon Nut M16 - 4
0060 0026-1382-300 Washer 6,4 - 4
0070 0018-3804-300 Hose Clamp Ø 71-114 mm - 2

assembly and installation
Installing the control unit and power supply unit
7160-9001-560
01. December 2020 19 / 74
Installation steps
1. Install the control unit and power supply in
the housing
- Rail (a)
- Control unit (70)
- Electrical Requirements (40)
2. Secure the components with a PPE
terminal block and end plate (20, 30).
40
70
10
Item Part number Description Quantity
Control unit,
complete VP8002 EU GEA x
10 7159-2853-050 Housing (complete) 276x230x136 1
20 0005-4622-890 Series terminal cage clamp 2-wire PE 1
30 0005-4617-890 End Plate for 2 cable terminals 2.5 mm² 1
40 0005-8000-970 Power supply unit 110-240V-AC to 24V-DC 60W 1
50 7160-6942-000 Cable harness
complete CowScout 1
60 7038-9923-000 Kit of expansion parts cable gland M16, M20 1
70 7160-9067-260 Control unit VP8002 1
3. Wire components internally as shown
Warning!
Electrical Hazard!
► Do not connect the power supply until the installation work has been
completed!
Wiring diagram (VP8002)
40
50
70
a b
VP8002
- Connect the control unit to the power supply
- Connect the red and green lamps to the corresponding control outputs with
the cables provided
Indicator lights Out VP8002
aRed I/O1
bgreen I/O2

assembly and installation
Installing the control unit and power supply unit
7160-9001-560
01. December 2020
20 / 74
4. Mounting the assembly using supports
The housing is fitted with a mounting plate suitable for wall and pipe mounting.
7160-5979-040 7160-5979-050 7160-5979-060 7160-2187-010 7160-5979-070
- Mount the control unit on a wall near the PC.
- Observe distances/cable length!
5. Electrical connection (CAN-Bus / Ethernet)
For more information on this subject please see section on:
Section: "Electrical connection"
6. After assembly and wiring, secure the
front flap with a screw.
Table of contents
Other GEA Control Unit manuals
Popular Control Unit manuals by other brands
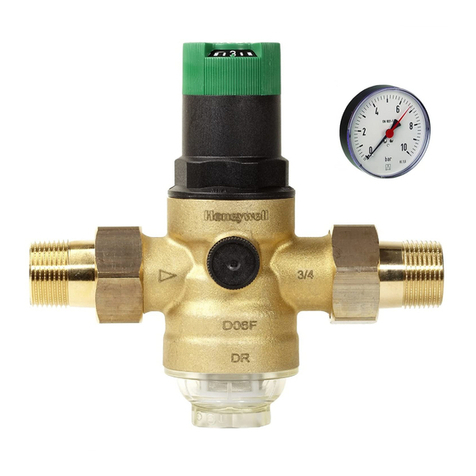
Honeywell
Honeywell D06F installation instructions

Spirax Sarco
Spirax Sarco M80i ISO Installation and maintenance instructions
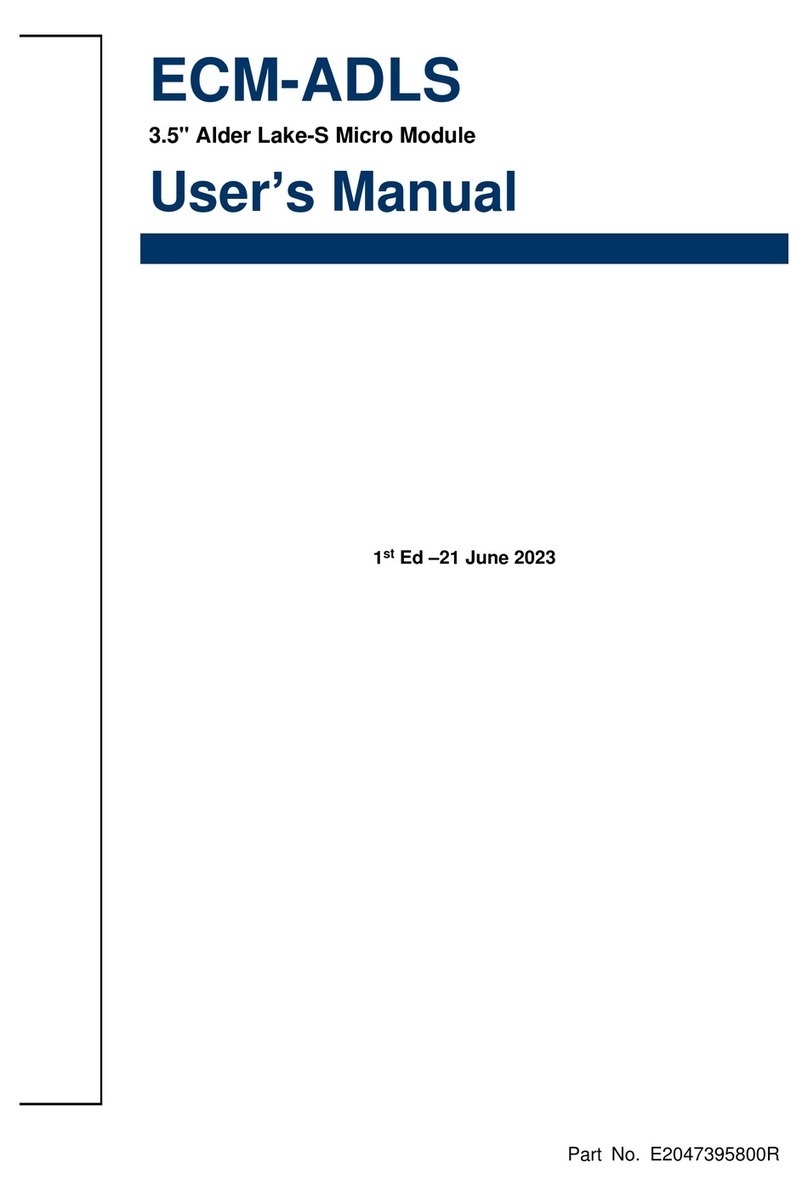
Avalue Technology
Avalue Technology ECM-ADLS user manual
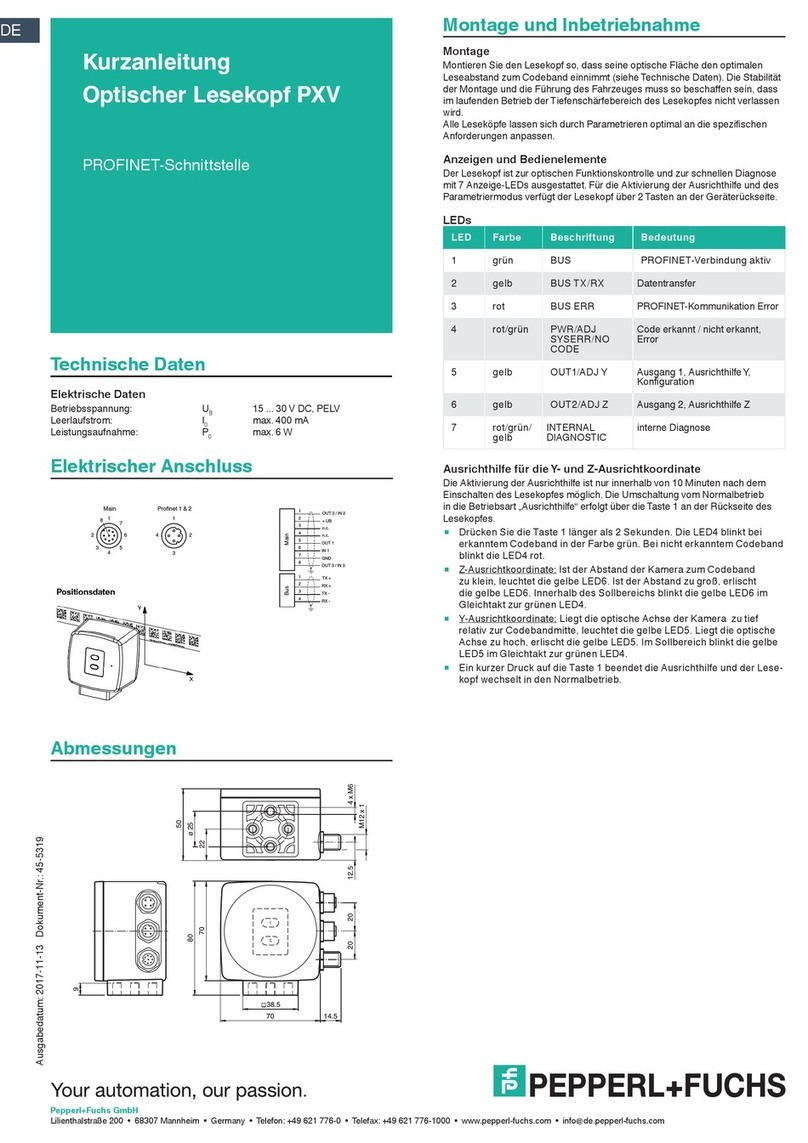
Pepperl+Fuchs
Pepperl+Fuchs PXV Series quick start guide

Sony
Sony HDCU-950 Installation and maintenance manual
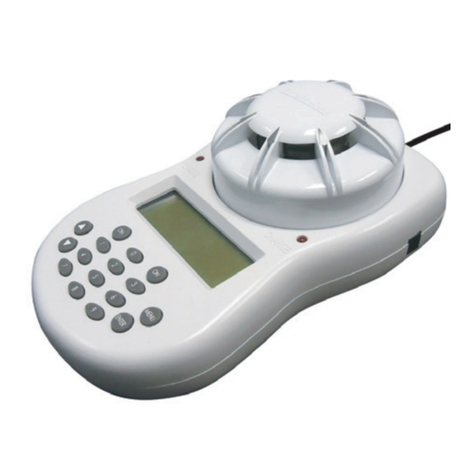
Zeta
Zeta FYREYE MKII ZASC-MI installation guide