ViscoTec preeflow eco-CONTROL EC200 2.0 Manual

OPERATION &
MAINTENANCE MANUAL
eco-CONTROL EC200 2.0

AB
Power supply A
Inlet pressure
monitoring A
2-component dispenser
eco-DUO
Material feeding A
Material feeding B
Dosing pressure
monitoring A

TABLE OF CONTENTS
3 / 120INST-007080 / E eco-CONTROL EC200 2.0
1Introduction ...................................................................................................... 7
1.1 Scope of delivery ..................................................................................... 7
1.2 Incoming inspection ................................................................................. 7
2Safety ................................................................................................................ 8
2.1 Explanation of symbols used ................................................................... 8
2.2 Intended Use............................................................................................ 9
2.3 Personnel............................................................................................... 10
2.3.1
Operators................................................................................... 10
2.3.2
Maintenance staff ...................................................................... 10
2.4 Informal safety precautions.................................................................... 11
2.5 Preventing damage to equipment .......................................................... 11
2.6 Compressed air supply .......................................................................... 12
2.7 Organisational safety measures ............................................................ 12
2.8 Residual risks......................................................................................... 13
2.9 IT safety ................................................................................................. 14
3Product description ....................................................................................... 15
4Operation ........................................................................................................ 16
4.1 Connections ........................................................................................... 16
4.1.1
1-component dispenser connection........................................... 17
4.1.2
Connection of two 1-component dispensers
(synchronous operation)18
4.1.3
2-component dispenser connection........................................... 19
4.1.4
2-component dispenser connection with dynamic mixer ........... 20
4.2 Initial commissioning.............................................................................. 21
4.3 Switching on / off.................................................................................... 21
4.4 Navigation structure ............................................................................... 22
4.5 Icons ...................................................................................................... 24
4.6 Start-up process..................................................................................... 25
4.7 First-time start-up................................................................................... 26
4.8 Quick start.............................................................................................. 27

TABLE OF CONTENTS
4 / 120 INST-007080 / Eeco-CONTROL EC200 2.0
4.9 Editing a program................................................................................... 28
4.9.1
Volume....................................................................................... 29
4.9.2
Flow rate .................................................................................... 30
4.9.3
Suck-back .................................................................................. 30
4.9.4
Pot life (with 2-component dispenser) ....................................... 31
4.9.5
Blankshot quantity (with 2-component dispenser)..................... 32
4.9.6
Mixing ratio (with 2-component dispenser)................................ 34
4.9.7
Material density.......................................................................... 34
4.9.8
Calibration.................................................................................. 35
4.9.9
Save location ............................................................................. 35
4.9.10
Dosing pressure max. (with dosing pressure sensor)................ 36
4.9.11
Pressure monitoring (with dosing pressure sensor) .................. 36
4.9.12
Dynamic mixer (for 2-component dispensers) ........................... 37
4.9.13
Changing field values ................................................................ 38
4.10 Calibration.............................................................................................. 39
4.11 Duplicating a program/creating a new program ..................................... 42
4.12 Dispense screen .................................................................................... 44
4.12.1
Dispense screen – Selecting parameters.................................. 45
4.12.2
Dispense screen - Changing the view ....................................... 46
4.12.3
Dispensing screen - Selecting the view..................................... 46
4.13 Choosing favourites ............................................................................... 47
4.14 Deleting a program ................................................................................ 48
4.15 Settings .................................................................................................. 48
4.15.1
User management ..................................................................... 49
4.15.2
System Information.................................................................... 52
4.15.3
Program Management............................................................... 55
4.15.4
Error messages ......................................................................... 56
4.15.5
Display & Sounds ...................................................................... 58
4.15.6
Start-Up Window........................................................................ 59
4.15.7
Date & Time............................................................................... 59
4.15.8
Language................................................................................... 60
4.15.9
Units........................................................................................... 60
4.15.10
System Calibration..................................................................... 61

TABLE OF CONTENTS
5 / 120INST-007080 / E eco-CONTROL EC200 2.0
4.15.11
Manual purging.......................................................................... 62
4.15.12
Sensors...................................................................................... 63
4.15.13
External Control unit .................................................................. 65
4.15.14
Interfaces ................................................................................... 67
4.15.15
IO Test (hardware test).............................................................. 68
4.16 Manual purging (start screen) ................................................................ 70
4.17 Help (start screen) ................................................................................. 71
5Dosing pressure monitoring ......................................................................... 72
5.1 Teach-In dosing ..................................................................................... 74
5.2 Monitoring units...................................................................................... 75
5.2.1
Envelope curve ......................................................................... 76
5.2.2
Integral ...................................................................................... 77
5.2.3
Control box ............................................................................. 78
5.3 Teach-In settings ................................................................................... 80
5.4 List of Teach-In dosing operations and monitoring units ....................... 81
5.5 Validity of a dosing operation................................................................. 81
5.6 Component signal .................................................................................. 82
5.7 Dosing window – view with monitoring units.......................................... 83
6Dynamic mixer................................................................................................ 86
7Explanations of the operating modes .......................................................... 88
7.1 Dosing manually .................................................................................... 88
7.2 Dosing with the foot switch (optional) .................................................... 89
7.3 Dosing using external control unit.......................................................... 90
7.3.1
Signal value for external program selection............................... 90
7.3.2
Signal forms and levels.............................................................. 92
7.3.3
Troubleshooting with external control unit ................................. 93
8Maintenance ................................................................................................... 94
8.1 Maintenance intervals ............................................................................ 94
8.2 Troubleshooting / Warning message / Error message........................... 94

TABLE OF CONTENTS
6 / 120 INST-007080 / Eeco-CONTROL EC200 2.0
9Cleaning .......................................................................................................... 99
10 Spare parts ..................................................................................................... 99
11 Technical specifications.............................................................................. 100
11.1 Interface description............................................................................. 100
11.1.1
Interface X1: System I/O.......................................................... 100
11.1.2
Interface X2: Inlet pressure...................................................... 101
11.1.3
Interface X3: External program selection................................. 101
11.1.4
Wiring diagrams for external inputs/outputs ............................ 102
11.1.5
Logical links of the outputs ...................................................... 105
11.2 EU Declaration of Conformity .............................................................. 106
11.3 Technical data...................................................................................... 107
12 Disposal ........................................................................................................ 108
12.1 General principles ................................................................................ 108
12.2 Return and recycling programme for waste equipment in the European
Union108
13 Accessories .................................................................................................. 110
13.1 Mounting of the holder ......................................................................... 111
13.2 Cabinet installation............................................................................... 112
13.3 Installation of the pneumatic unit ......................................................... 114
14 Keyword index.............................................................................................. 115

7 / 120INST-007080 / E eco-CONTROL EC200 2.0
INTRODUCTION
1Introduction
Dear customer,
We are delighted that you have decided to purchase a ViscoTec product. We have no doubt
that this product will meet all your requirements. We wish you trouble-free and successful
operation.
The dosing system consists of the eco-CONTROL EC200 2.0 dosing control unit and a
1- or 2-component dispenser. Simultaneous operation of two identical 1-component
dispensers is possible.
This operation manual describes the dosing control unit. A separate operation and
maintenance manual is supplied for the different dispensers.
1.1 Scope of delivery
eco-CONTROL EC200 2.0 dosing control unit, support, power cable, USB stick and
operation and maintenance manual. The 2-component dispenser also includes a set of
adhesive stickers to label the two motors, the plugs, sensors and the supply line.
1.2 Incoming inspection
Damage in transit can lead to malfunctions, and consequently to personal injury and damage
to property. Damaged components must not be put into operation.
Check the delivery immediately on receipt for damage in transit and damage to the
packaging. Check that the delivery is complete according to the enclosed delivery note.
Make sure you have not left any part of the delivery in the packaging.
Compensation for damage during transport may be claimed only if the carrier is notified
immediately.

8 / 120 INST-007080 / Eeco-CONTROL EC200 2.0
SAFETY
2Safety
2.1 Explanation of symbols used
The following symbols are used in this manual:
The following notices indicate safety instructions and must be followed:
This manual is structured so that text and the related figure are on the same page as far
as possible. In this way the information can be understood quickly. If reference is made to a
component in a figure, the part has a key number.
Work step
• List
Fig. 1 Legend number, reference to a figure
* Reference to a comment
COMMAND Designations of buttons/switches, menu items and input dialogs
indicates a hazardous situation which, if not avoided, will result in death or serious injury.
indicates a hazardous situation which, if not avoided, may result in death or serious injury.
indicates a hazardous situation which, if not avoided, may result in minor injury.
NOTE
indicates a technical tip to avoid damage to property or equipment.
DANGER
WARNING
CAUTION

9 / 120INST-007080 / E eco-CONTROL EC200 2.0
SAFETY
2.2 Intended Use
The dosing control unit controls the dispensers in order to convey and precise dispense
viscose material.
Check the chemical resistance of the materials that are in contact with the material before
commissioning. For information on the equipment materials refer to the dispenser operation
and maintenance manual.
No liability can be accepted for damage caused by failure to observe this operation manual
or due to a lack of maintenance or checks.
Misuse
Any use other than the stipulated intended use shall be considered as misuse.
This includes
• Use outside the permissible operating limits
• Use in explosive environments
• Use underground
• Use outdoors
Misuse also includes the following actions carried out without the explicit written approval of
the manufacturer:
• Conversions and/or extensions
• Use of non-genuine spare parts
• Repairs carried out by unauthorised companies or persons
• Use of non-approved materials
Misuse is not permissible, and will result in voiding of guarantee, warranty and liability claims.

10 / 120 INST-007080 / Eeco-CONTROL EC200 2.0
SAFETY
2.3 Personnel
The operating organisation shall ensure that only appropriately qualified and authorised
personnel work on this machine. It is responsible for ensuring that operators and
maintenance staff possess the necessary qualifications. Personnel must be at least
15 years old.
All personnel working with or on the machine must have read and understood this
operation manual.
The operating company shall document the operators' and maintenance staff's
acknowledgement of this manual, and shall ensure their compliance with it by means of
regular training.
2.3.1
Operators
Before starting work, the personnel assigned as operators must be adequately instructed
regarding the nature and scope of their duties and the potential risks. Training is to be
conducted on a regular basis (at least once a year). Training is to be conducted after any
technical modifications.
2.3.2
Maintenance staff
The maintenance and repair staff must be authorised and
• adequately trained for the relevant activities
• familiar with and comply with the applicable technical rules and safety regulations
Competent personnel are persons who, by virtue of their training, experience and knowledge
of the relevant requirements, standards and safety regulations, can carry out the necessary
activities while recognising and avoiding potential hazards.

11 / 120INST-007080 / E eco-CONTROL EC200 2.0
SAFETY
2.4 Informal safety precautions
The following documents must be read, understood and followed. They must always be
available at the machine's operating location, and must be kept in legible condition:
• The operation manual for this product
• Generally applicable and local accident prevention and environmental protection
regulations
• Safety data sheets for the conveyed materials, as well as for any cleaning products or
lubricants being used
2.5 Preventing damage to equipment
In order to prevent damage to equipment and to ensure precision dosing, ensure that
• the connecting cable for a dispenser may only be connected or disconnected when
the power supply is switched off. Otherwise, the electronics in the drive motor could
be damaged
• only original dosing pressure sensors adapted for the dosing control unit are to be used
• the dispenser must never be operated without material (the stator will be destroyed)
• the material inlet (feed) and the material outlet must never be closed during operation
• the material outlet (e.g. dosing needle or mixer) must not be damaged or blocked
• the dispenser is regularly checked and cleaned
• the specifications in the product data sheet for the material are observed and adhered to

12 / 120 INST-007080 / Eeco-CONTROL EC200 2.0
SAFETY
2.6 Compressed air supply
If the pneumatic unit is used, there must be a maintenance unit (pressure regulator and
cut-off valve) immediately before the dosing system. Compressed air supply max. 6 bar.
2.7 Organisational safety measures
The necessary personal protective equipment must be provided by the operating
organisation. Personal protective equipment must be worn when carrying out all work and
procedures.
To ensure the provision of suitable personal protective equipment, the safety data sheet for
the conveyed material must be observed. Specifications for e.g. cleaning products and
lubricants must also be checked and observed.
All personal protective equipment must be checked to ensure it is working properly before
starting work.
Eye protection Hand protection Body protection Foot protection

13 / 120INST-007080 / E eco-CONTROL EC200 2.0
SAFETY
2.8 Residual risks
Thorough training, observance of the operation manual and compliance with safety
regulations are key to permanently accident-free operation.
The following residual risks may occur when operating this machine:
Danger to life from electrical voltage
There is a risk of fatal electric shock if equipment covers are removed or cables are
defective.
• Work and repairs on live parts may only be carried out by competent maintenance staff.
All applicable standards and safety, directives and regulations (e.g. EN 50110-1) must
be complied with.
Material hazardous to health
The conveyed material may contain constituents which are hazardous to health.
Such constituents may cause serious acute or chronic harm to health if they come
into contact with skin, are inhaled or swallowed.
• Always wear appropriate protective equipment
• Observe the specifications in the safety data sheet for the material
Pressurised material
Depending on the setting of the dosing system, the material is conveyed under very high
pressure. If the feeding rate is not adapted to the dosing needle being used, unwanted
spraying of the material might occur. This may result in serious injury.
• Shut down the machine immediately
• The machine may only be restarted once the correct dosing needle has been installed
or after eliminating the leak
DANGER
WARNING
WARNING

14 / 120 INST-007080 / Eeco-CONTROL EC200 2.0
SAFETY
2.9 IT safety
To protect the eco-CONTROL EC200 2.0 dosing control unit and existing IT systems,
it is essential to adhere to the following:
All USB sticks must be checked for viruses and malware by up-to-date security software
before use.
ViscoTec accepts no liability if a USB stick containing malware or an incorrect update file
is used.
Splashing material
During initial commissioning and after being refilled, air bubbles in the material could
cause an uncontrollable spraying from the conveying area. This may result in injury.
• Always wear appropriate protective equipment
• Fully bleed the system before start of production
CAUTION

15 / 120INST-007080 / E eco-CONTROL EC200 2.0
PRODUCT DESCRIPTION
3Product description
The dosing control unit has been developed and tested for high-precision work with
1-component and 2-component dispensers. Simultaneous operation of two identical
1-component dispensers is possible. For 2-component dispensers, a dynamic mixer can
also be connected.
The dosing system has a wide variety of setting options for the dosing quantity and time.
All the values that are related to production can be saved and changed at any time.
Up to 100 different programs can be stored in the dosing control unit.
Operation is done via an intuitive operator guidance system using a graphic user interface.
Depending on the customer order, the required software licence will come pre-installed on
the dosing control unit. The corresponding software licence is also saved as a “backup” on
the supplied USB stick.
Converting to a different software licence can be done at any time without significant setup
times. Simply install the new chargeable software licence on the dosing control unit using a
USB stick (activation). Different software licences are available (see page 110). You can get
the new USB stick from your contract partner or by contacting the manufacturer, citing the
serial number.
New software licences are encrypted and can therefore only be installed on one dosing
control unit. The serial number (SN) of the associated dosing control unit is therefore printed
on the USB stick. The serial number (SN) of the dosing control unit can be found on the type
plate (see page 99).
The dispensers have been developed and tested for precision dosing of materials ranging
from low to high viscosity with extremely high repeat precision.
Preeflow dispensers are positive displacement pumps. The conveying elements comprise a
rotating part, the rotor, and a stationary part, the stator. The rotor, which is in the form of a
type of knuckle thread, rotates inside the stator, which has one more thread turn and twice
the pitch length of the rotor. As a result, conveying areas are produced between the stator
and the rotor rotating inside the stator. The rotor also moves radially within the stator.
The conveying areas move forwards continuously due to the movement. The flexible shaft
used to drive the rotor compensates for the eccentric movement of the rotor and is completely
maintenance-free.
Since the direction of flow is reversible, the material can be sucked back to allow a clean
thread breakage.
The dispenser can be dismantled very quickly.

16 / 120 INST-007080 / Eeco-CONTROL EC200 2.0
OPERATION
4Operation
4.1 Connections
The following connections can be found
on the rear. All texts are in English.
1Motor 1 Connection for dispenser 1 (component A (resin))
2Motor 2 Connection for dispenser 2 (component B (hardener))
3Motor 3 Connection for dynamic mixer
4Dispensing
Pressure A
Dosing pressure sensor connection for dispenser 1
(component A (resin))
5Dispensing
Pressure B
Dosing pressure sensor connection for dispenser 2
(component B (hardener))
6X1 Interface for system I/O (see page 100)
7X2 Interface for inlet pressure (see page 101)
8X3 Interface for external program selection (see page 101)
9RS232 Interface for external control (see page 67)
10 USB USB connection
11 LAN Connection not used
12 110–230 V AC Mains connection 110–230 V AC 100 VA,
(inc. 2 fuses T2,5L250V (glass fuse 5x20))
13 Pressure Control Pneumatic unit (optional)
14 Pressure IN Compressed air inlet (connection hose Ø 6 mm)
15 Control Regulator for manual adjustment of the compressed air
16 Pressure OUT Compressed air outlet (connection hose Ø 4 mm),
connection to material reservoir / cartridge / tank
17 Power on/off On/off switch
32
547 9
168 10
11 12
14
17
15
16
13
Fig. 1

17 / 120INST-007080 / E eco-CONTROL EC200 2.0
OPERATION
4.1.1
1-component dispenser connection
Illustrated with non-self-levelling liquid (material/high viscosity material)
1. Motor 1, 4. Dispensing Pressure A (optional), 16. Pressure OUT
Illustrated with self-levelling liquid (low viscosity material)
1. Motor 1, 4. Dispensing Pressure A (optional)
116
4
Fig. 2
1
4
Fig. 3

18 / 120 INST-007080 / Eeco-CONTROL EC200 2.0
OPERATION
4.1.2
Connection of two 1-component dispensers
(synchronous operation)
Illustrated with non-self-levelling liquid (material/high viscosity material)
1. Motor 1, 2. Motor 2, 4. Dispensing Pressure A, 5. Dispensing Pressure B,
16. Pressure OUT
Illustrated with self-levelling liquid (low viscosity material)
1. Motor 1, 2. Motor 2, 4. Dispensing Pressure A, 5. Dispensing Pressure B
AB
12
5
4
16
Fig. 4
AB
12
5
4
Fig. 5

19 / 120INST-007080 / E eco-CONTROL EC200 2.0
OPERATION
4.1.3
2-component dispenser connection
Illustrated with non-self-levelling liquid (material/high viscosity material)
1. Motor 1, 2. Motor 2, 4. Dispensing Pressure A, 5. Dispensing Pressure B,
16. Pressure OUT
Illustrated with self-levelling liquid (low viscosity material)
1. Motor 1, 2. Motor 2, 4. Dispensing Pressure A, 5. Dispensing Pressure B
AB
12
5
4
16
Fig. 6
AB
5
4
12
Fig. 7

20 / 120 INST-007080 / Eeco-CONTROL EC200 2.0
OPERATION
4.1.4
2-component dispenser connection with dynamic mixer
Illustrated with non-self-levelling liquid (material/high viscosity material)
1. Motor 1, 2. Motor 2, 3. Motor 3, 4. Dispensing Pressure A, 5. Dispensing Pressure B,
16. Pressure OUT
Illustrated with self-levelling liquid (low viscosity material)
1. Motor 1, 2. Motor 2, 3. Motor 3, 4. Dispensing Pressure A, 5. Dispensing Pressure B
AB
12
5
4
16
3
Fig. 8
AB
1
3
2
5
4
Fig. 9
Table of contents
Other ViscoTec Control Unit manuals
Popular Control Unit manuals by other brands
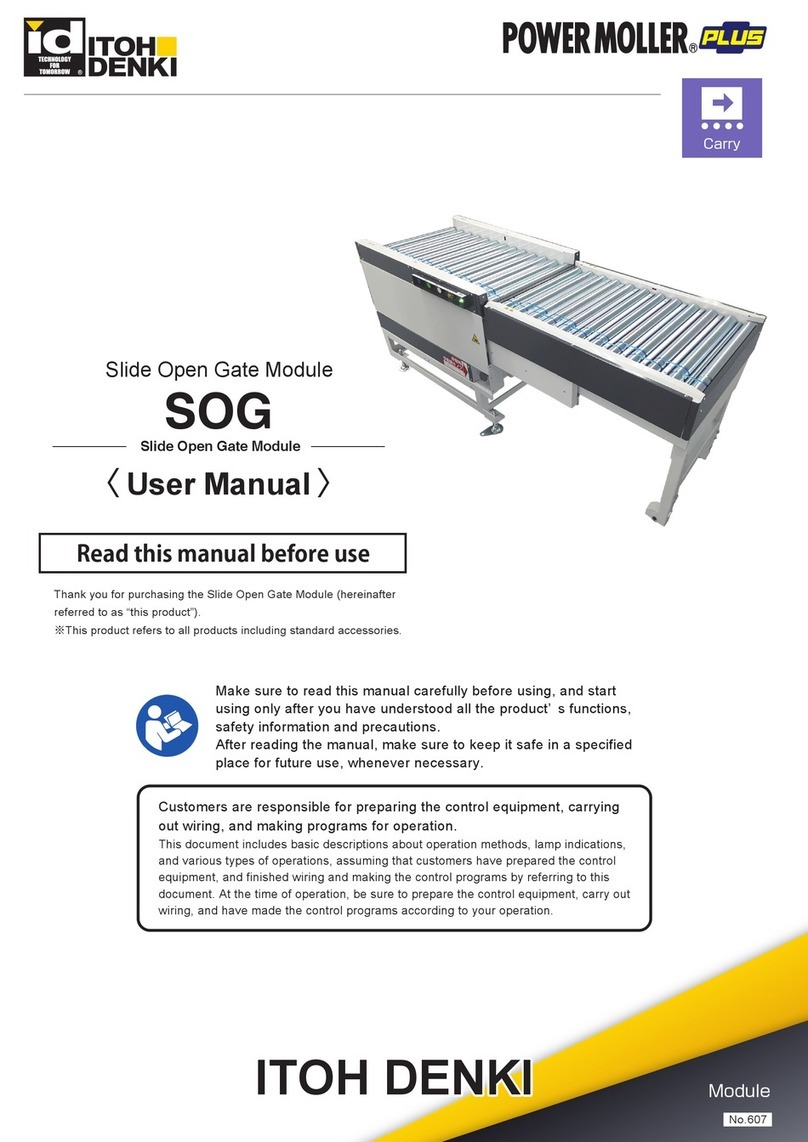
ITOH DENKI
ITOH DENKI POWER MOLLER PLUS SOG user manual
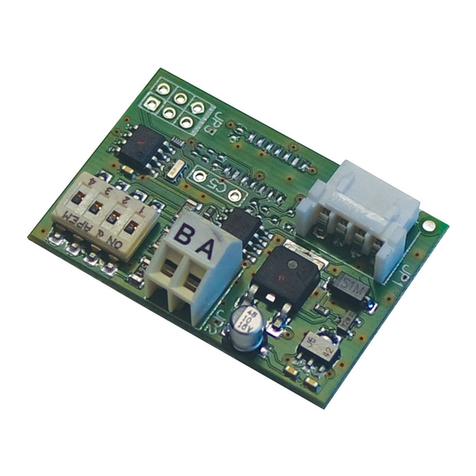
BFT
BFT B EBA RS 485 LINK installation manual
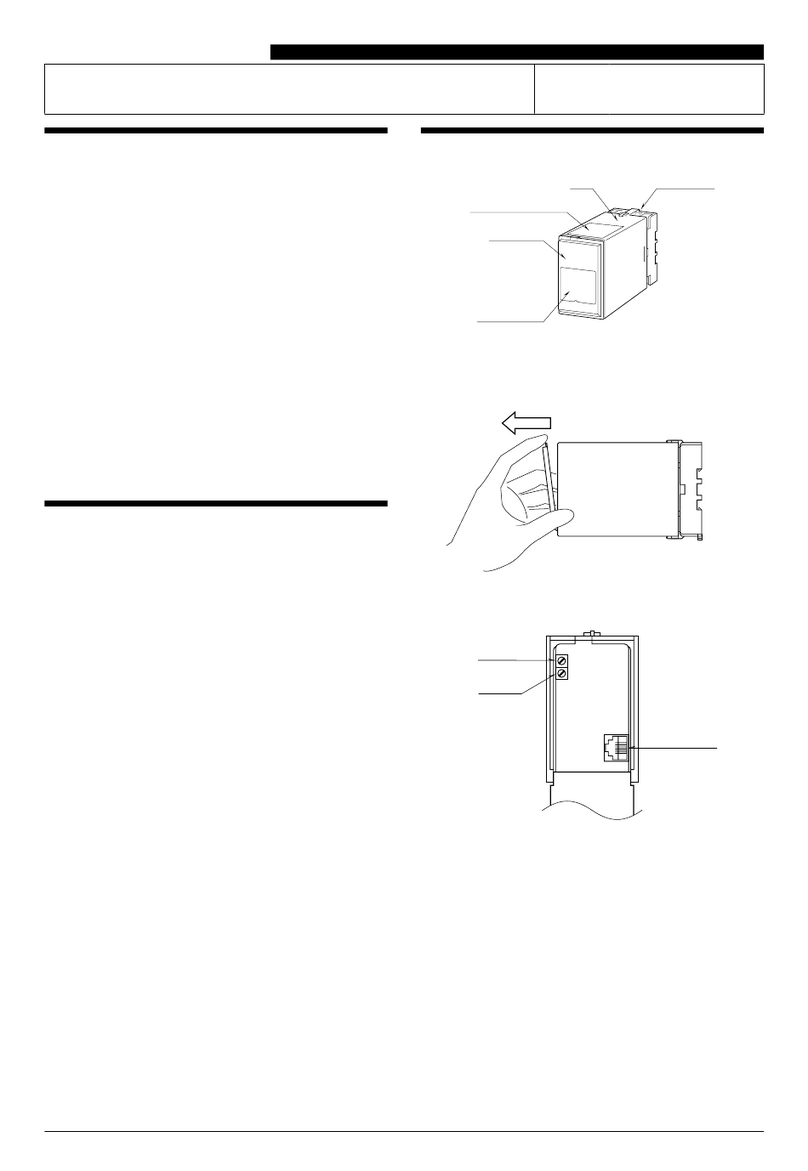
MG
MG JFK instruction manual
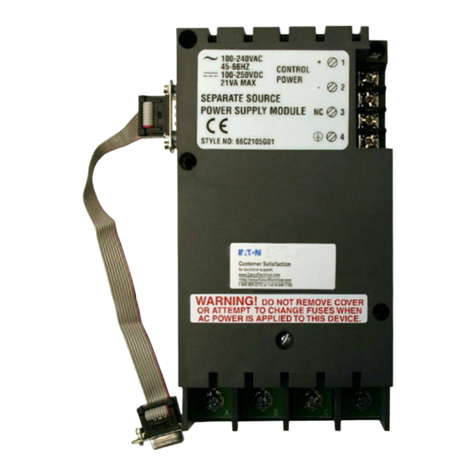
Eaton
Eaton Cutler-Hammer IQMSSPM instructions
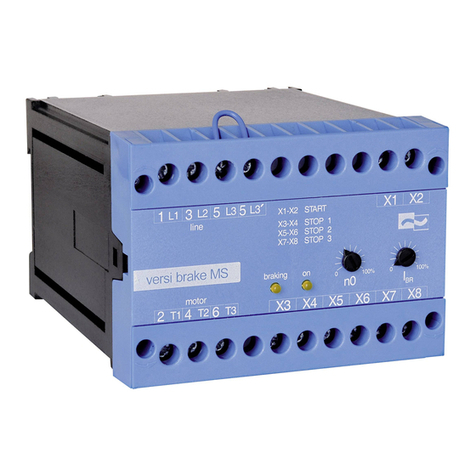
Peter electronic
Peter electronic VBMS Series Assembly and commissioning instructions
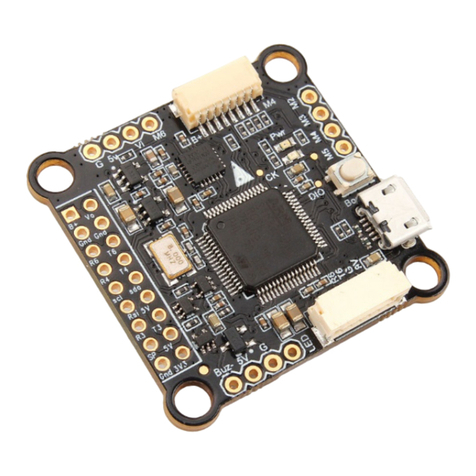
Holybro
Holybro 11048 User manual & installation guide
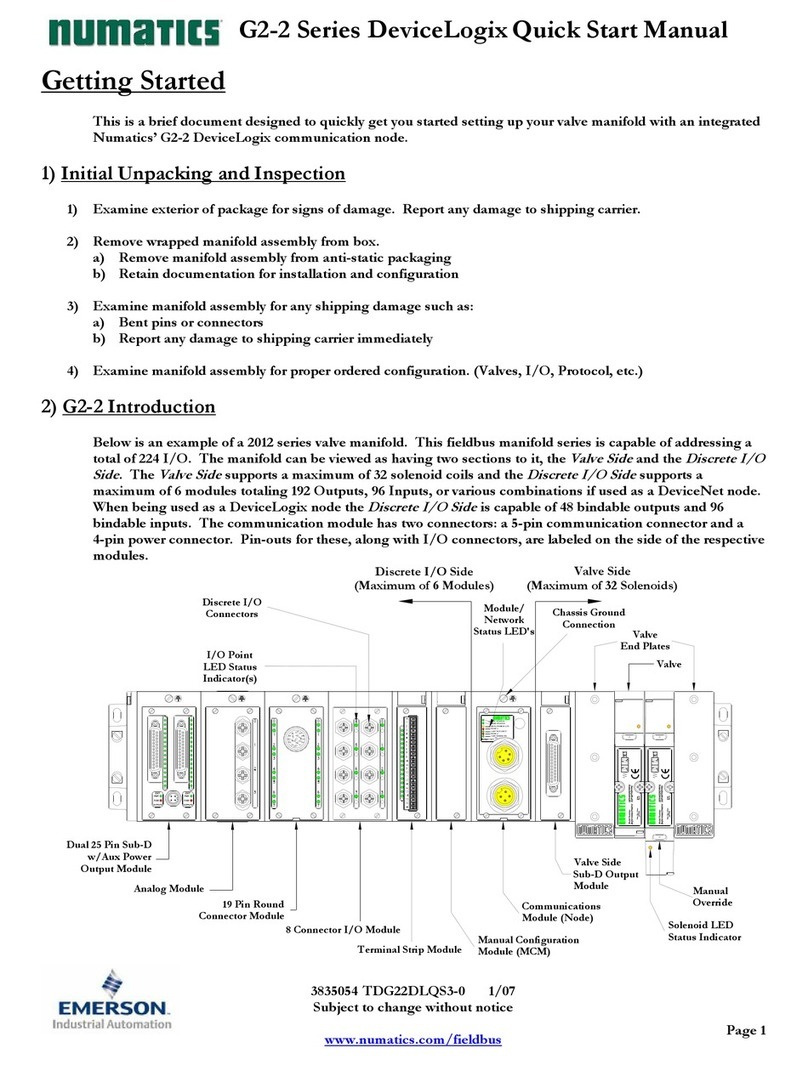
Emerson
Emerson Numatics DeviceLogix G2-2 Series Quick start manual
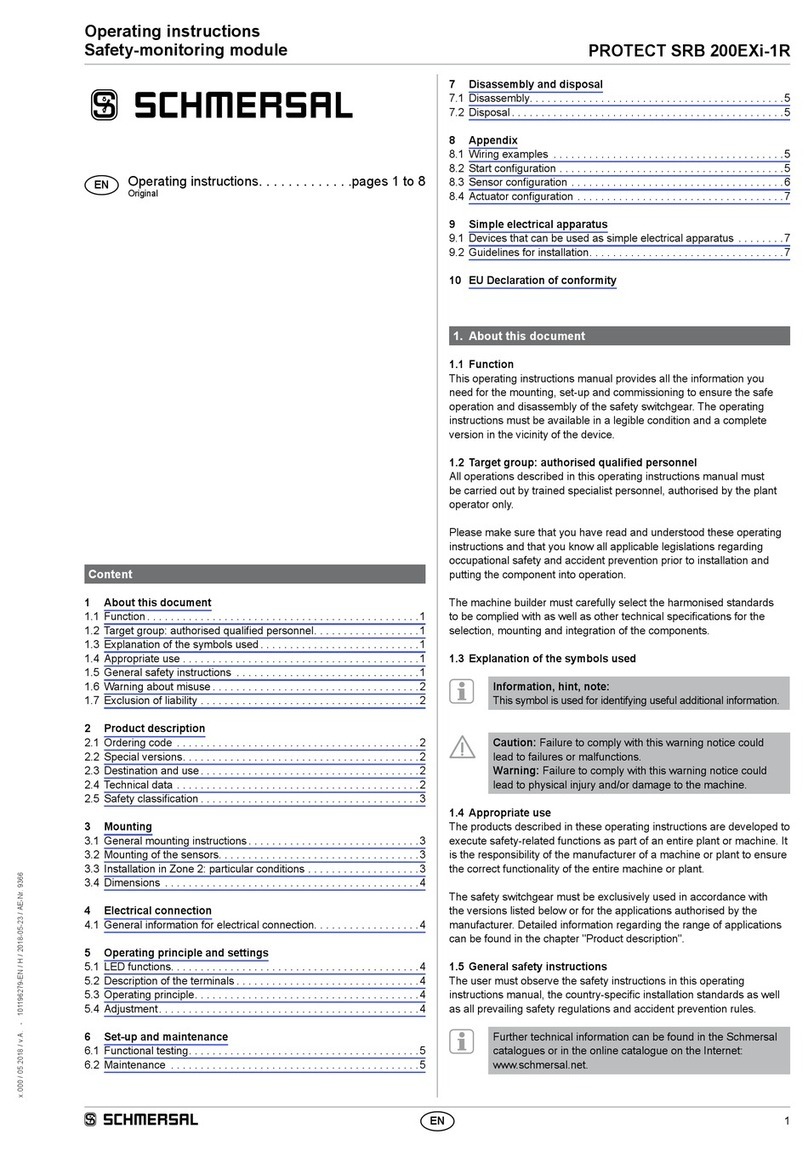
schmersal
schmersal PROTECT SRB 200EXi-1R operating instructions
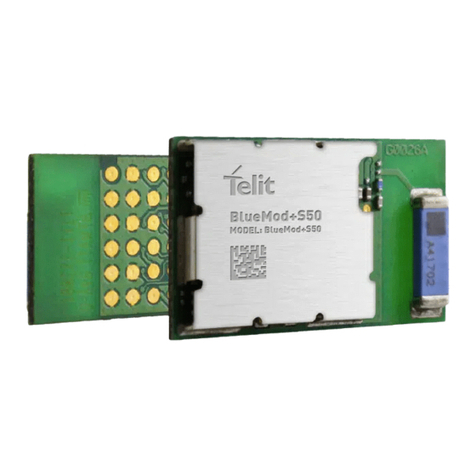
Telit Wireless Solutions
Telit Wireless Solutions BlueMod+S50/AI Hardware user's guide
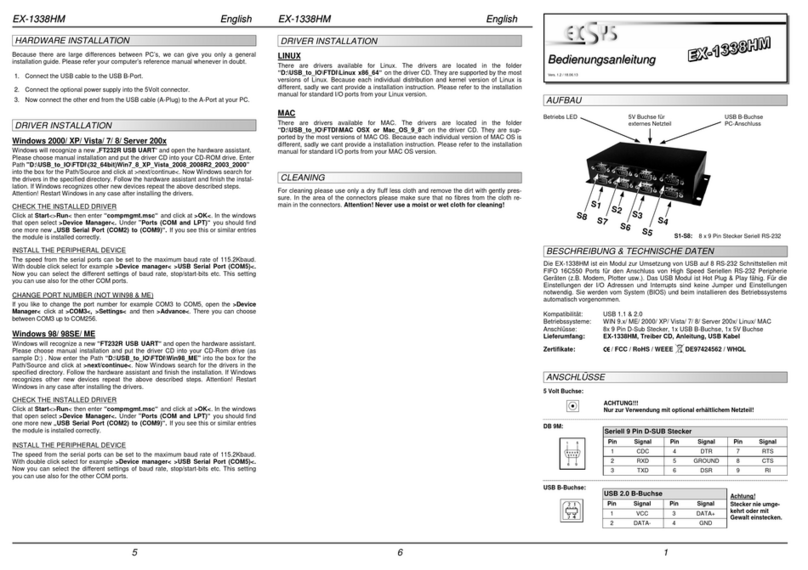
Exsys
Exsys EX-1338HM user manual
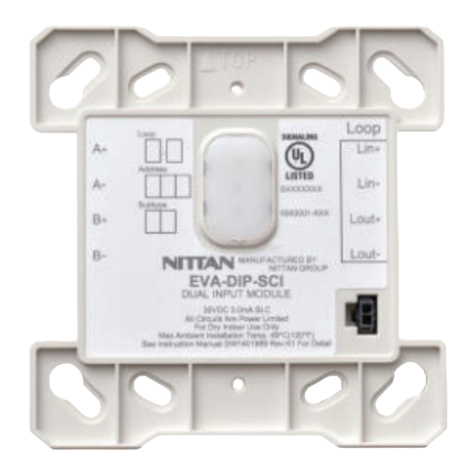
Nittan
Nittan EVA-DIP-SCI instruction manual
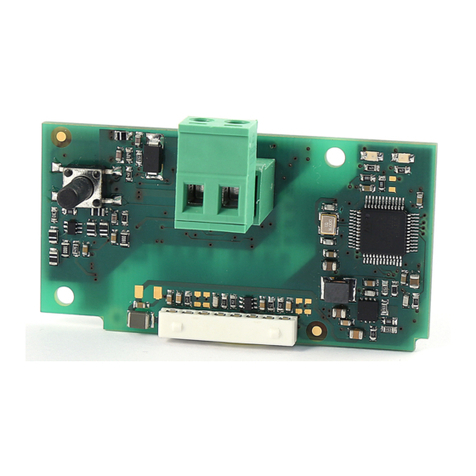
Carel
Carel PCOS00KXN0 user manual