WABCO 1200E User manual

Maintenance Manual 34
System Saver Series Single Cartridge Air
Dryers
System Saver Series
•1200E, P, U
•1800E, P, U
•1200 Plus, MCP
Revised 03-16

Service Notes
Information contained in this publication was in effect at the time the publication
was approved for printing and is subject to change without notice or liability.
Meritor WABCO reserves the right to revise the information presented or to
discontinue the production of parts described at any time.
Meritor WABCO Maintenance Manual 34 (Revised 03-16)
About This Manual
This manual contains maintenance procedures for Meritor WABCO’s
System Saver Series single cartridge air dryers.
Before You Begin
1. Read and understand all instructions and procedures before
you begin to service components.
2. Read and observe all Warning and Caution hazard alert
messages in this publication. They provide information that can
help prevent serious personal injury, damage to components,
or both.
3. Follow your company’s maintenance and service, installation,
and diagnostics guidelines.
4. Use special tools when required to help avoid serious personal
injury and damage to components.
Hazard Alert Messages and Torque
Symbols
WARNING
Warnings are included to alert the user that possible hazards
are associated with the processes/procedures described.
These may cause death or injury in any form, if the
instructions in the operational or procedural task are not
followed precisely. Warnings describe the potential hazards
and possible impact that could occur if the warnings are not
observed.
CAUTION
Cautions are included to alert the user than damage to the
equipment is possible if the instructions in the operational or
procedural task are not followed precisely. Cautions describe
the hazards and possible impact that could occur if the
cautions are not observed.
@This symbol alerts you to tighten fasteners to a specified torque
value.
NOTE: Notes are included to provide the user with supplemental
information, which is helpful but does not necessarily belong in the
core text. Many operational and procedural tasks are easier with the
addition of notes.
How to Obtain Additional Maintenance,
Service and Product Information
Visit Literature on Demand at meritor.com to access and order
additional information.
Contact the Meritor OnTrac™ Customer Call Center at
866-668-7221 (United States and Canada); 001-800-889-1834
(Mexico); or email OnTrac@meritor.com.
If Tools and Supplies are Specified in
This Manual
Contact Meritor’s Commercial Vehicle Aftermarket at
888-725-9355.

Contents
pg. pg.1Section 1: Introduction
Overview
Other Publications Related to Meritor WABCO System
Saver Series Single Cartridge Air Dryers
Air Dryer Identification
2 How the Air Dryer Works
3 Air Dryer Cycle
7 Air Dryer Components
10 Dryer Identification
Description of Components
14 Section 2: Component Removal and
Installation
Component Replacement
Requirements
15 Component Removal and Installation
Desiccant Cartridge
16 Outlet Check Valve Assembly
Heater Assembly
17 Turbo Cut-Off Valve Assembly
18 System Saver 1200 Plus Governor
Regeneration Valve Assembly
19 Purge Valve Assembly
20 Pressure-Controlled Check Valve (PCCV)
21 Bypass Valve
22 Pressure Relief Valve
Purge Silencer (Muffler)
23 Air Dryer Assembly
24 Section 3: Troubleshooting and Testing
Maintenance
25 Maintenance Tips
26 Troubleshooting
31 Tests
Heater Resistance
Electric Power to Dryer
Leak Test
Air Pressure Checks
Operational Test for System Saver Series Air Dryers —
Regeneration and Purge Style
32 Pressure-Controlled Check Valve Test — Regeneration
Style Only
34 Section 4: Appendix I — Glossary
Definitions
Basic Air System/Air Dryer Terms
35 Section 5: Appendix II — Application Info
Requirements
Operating Environment
36 System Saver Series Installation Criteria
37 Section 6: Appendix III — Special
Applications
Description
Holset E-Type Compressor Systems
38 ECON Valve
40 Alcohol Evaporator
41 Combo Tank Installation for Regeneration-Style Air Dryers
42 Combo Tank Installation for Regeneration-Style Air Dryers
43 Meritor WABCO System Saver Series Single Cartridge Air
Dryer Component Replacement Guide — Dedicated
Purge
44 Meritor WABCO System Saver Series Single Cartridge Air
Dryer Component Replacement Guide
45 Section 7: Appendix IV — Exploded View of
System Saver 1200 Plus Series Air Dryer
46 Section 8: Appendix V — Temporary Air
Dryer Bypass
Bypass Procedure
47 Section 9: Appendix VI — Exploded View of
System Saver 1200 Plus Series with Multi
Circuit Protection

Notes

1 Introduction
1
Meritor WABCO Maintenance Manual 34 (Revised 03-16)
1 Introduction
Overview
Maintenance Manual 34 contains troubleshooting steps and service
information for the Meritor WABCO System Saver Series (1200 and
1800) single cartridge air dryers.
NOTE: If you have a System Saver TWIN air dryer, use Maintenance
Manual 35, Meritor WABCO System Saver TWIN Air Dryer. To obtain
this publication, refer to the Service Notes page on the front inside
cover of this manual.
Other Publications Related to Meritor WABCO
System Saver Series Single Cartridge Air
Dryers
TP-92116, Installing the Meritor WABCO System Saver Series Air
Dryer, provides complete installation instructions.
PB-8857AS contains a complete listing of air dryer replacement
parts.
TP-97101 is a troubleshooting guide. There is also a poster-sized
troubleshooting guide, TP-9772, available.
TP-9672, Air Dryer Application Guide, provides an in-depth look at
System Saver Series air dryer applications.
T-20102V, Air System Troubleshooting video Stopping With Air and
T-97105V, System Saver 1200 videotapes are also available.
TP-1033, System Saver 1200 Plus Series Air Dryers, provides
installation instructions.
TP-1343, Troubleshooting and Repairing System Saver 1200 Plus
Air Dryers with Turbo Cut-off Valves on Vehicles with Cummins
Engines, provides service instructions.
TP-09133, Replacing a Bendix AD9 Air Dryer with a System Saver
1200 Plus Air Dryer, provides replacement instructions.
TP-0579, Installation Instructions for Meritor WABCO’s Dessicant
Cartridge Replacement Kit, provides installation instructions.
TP-9610, Using an Alcohol Evaporator with Meritor WABCO System
Saver 1000, 1200, and 1200 E Series Single Cartridge, provides air
dryer instructions.
TP-9557, Pressure Relief Valve Installation Instructions for Meritor
WABCO System Saver 1000, 1200 and 1200E Series and System
Saver TWIN Air Dryers, and Modification Instructions for Units
Equipped with Alcohol Evaporators, provides installation
instructions.
To order literature, visit our website at meritorwabco.com.
Air Dryer Identification
Alphabetical designations of the System Saver Series family of air
dryers have specific meanings:
P Indicates an external purge tank is used for desiccant
regeneration
U Indicates discharge line — unloaded compressor
E Indicates a Holset style compressor function
G Indicates integral governor for air compressor control
UP Indicates discharge line — unloaded compressor (with external
purge tank)
System Saver 1200/1800: System regeneration valve assembly on
side of dryer
System Saver 1200E: Tubing and banjo fitting at front of dryer
System Saver 1200P/1800P: Uses dedicated purge tank. Port 22
drilled and tapped
System Saver 1200U/1800U: Small regeneration hole visible in
back of Port 1 when fitting is removed. No spring in turbo cut-off
valve assembly.
System Saver 1200UP/1800UP: Port 22 drilled and tapped. Small
regeneration hole visible at back of Port 1 when fitting is removed.
No spring in turbo cut-off valve assembly. Dedicated purge tank.
The air dryer base is the same for both the 1200 and 1800 Series
air dryers, however the 1800 Series canister is 3.2 inches taller
than the 1200. This larger canister contains 50% more desiccant,
which makes the 1800 ideal for applications calling for frequent
starts, stops and long compressor cycles. System Saver 1200 and
System Saver 1800 Series air dryers are illustrated in Figure 1.1.
System Saver 1200P and System Saver 1800P, which are used with
a dedicated purge tank, are illustrated in Figure 1.2.
System Saver 1200 Plus: Has the governor integrated into the
body of the air dryer and also has an integrated purge tank.
Figure 1.3.
System Saver 1200 Plus MCP: Has the governor and pressure
protection elements integrated into the body of the air dryer. Also
has an integrated purge tank. Figure 1.4.

1 Introduction
2Meritor WABCO Maintenance Manual 34 (Revised 03-16)
Figure 1.1
Figure 1.2
Figure 1.3
Figure 1.4
How the Air Dryer Works
During system pressure build-up, compressed air passes into the air
dryer where the filter system removes contaminants and passes the
air into the drying stage.
Moisture-laden air passes through the desiccant bed in the air dryer
cartridge and moisture is retained by the desiccant. Moisture that
condenses out also collects in the base of the dryer. When the
compressor unloads, the water is expelled and dried air flows back
through the dryer, drying the desiccant for the next cycle.
NOTE: For further information about System Saver E air dryers and
components, refer to Section 4 and Section 5. For special
applications, refer to Section 6.
Figure 1.1
SYSTEM SAVER 1200 AND 1800 SERIES
Figure 1.2
SYSTEM SAVER 1200P AND 1800P
Figure 1.3
SYSTEM SAVER 1200 PLUS
4003875a
4003876a
4007638a
Figure 1.4
SYSTEM SAVER 1200 PLUS MCP
4011898a

1 Introduction
3
Meritor WABCO Maintenance Manual 34 (Revised 03-16)
Air Dryer Cycle
A single cartridge air dryer cycle is illustrated in Table A.
Table A
The governor turns the compressor on when supply tank pressure
drops below cut-in pressure, between 100 psi and 110 psi
(689-758 kPa) depending on governor settings.
Compressed air passes into the air dryer at the inlet port:
앫Moisture-laden air and contaminants pass through the
desiccant.
앫Moisture is retained by desiccant; moisture also collects in the
base of the dryer.
앫Contaminants are removed as air passes through the desiccant
bed.
The governor turns the compressor off when system reaches
cut-out pressure, between 120 psi and 130 psi (827-896 kPa)
depending on governor settings.
1002142a
CONTROL
“WET” AIR
“DRY” AIR
CONTROL/DRY
LINES
ENGINE TURBO
BOOST PRESSURE
1002143a
1002145a
CONTROL
“WET” AIR
“DRY” AIR
CONTROL/DRY
LINES
ENGINE TURBO
BOOST PRESSURE

1 Introduction
4Meritor WABCO Maintenance Manual 34 (Revised 03-16)
When the compressor unloads, the purge valve opens:
앫On 1200E, P, U, 1800E, P, U, the dryer purges the desiccant
cartridge and expels any water collected in the dryer base.
— Regeneration valve opens.
앫On 1200 regeneration models, when the regeneration valve
opens.
— Dry system air flows back through the dryer, 10 psi (69 kPa)
is taken from the supply and secondary tanks for the
regeneration.
— Back flow dries desiccant, preparing it for the next cycle.
앫On 1200 P, UP, 1800 P and UP:
— Dry air flows from the separate purge tank back through the
air dryer.
앫On 1200 Plus:
— Dry air flows from the integrated purge tank back through
the air dryer. Air can be felt and heard flowing from the
purge valve for an extended period of time.
— Dry system air flows back through the air dryer to
regenerate the desiccant.
1002144b
1200E, P, U
1800E, P, U
1200 PLUS
TO
CANISTER
FROM
CANISTER
IN
OUT TO TANKS

1 Introduction
5
Meritor WABCO Maintenance Manual 34 (Revised 03-16)
Typical System
A typical Meritor WABCO System Saver 1200 or 1800 Series air
dryer installation is illustrated in Figure 1.5. A System Saver 1200
Plus system is shown in Figure 1.6. Illustrations for Combo Tank
installations appear in Section 6.
Figure 1.5
Figure 1.5
1002141c
PURGE
VALVE
(EXHAUST)
COMPRESSOR
DISCHARGE
LINE
COMPRESSOR
CONTROL
(PURGE) PORT
COMPRESSOR
INTAKE LINE
PRESSURE-
CONTROLLED
CHECK VALVE
SUPPLY
TANK
SYSTEM
RESERVOIRS
ONE-WAY
CHECK
VALVE
DRYER
OUTLET
PORT
SYSTEM SAVER SERIES
REGENERATION
STYLE AIR DRYER
DRYER
INLET
PORT
UNLOADER
LINE
RESERVOIR-
TO-GOVERNOR
LINE
1800
1200
SUPPLY
LINE
PURGE
TANK
PURGE
VALVE
(EXHAUST)
P SERIES WITH DEDICATED
PURGE TANK
BOTTOM VIEW
OF AIR DRYER
REGENERATION
VALVE
GOVERNOR
UNLOADER
PORT

1 Introduction
6Meritor WABCO Maintenance Manual 34 (Revised 03-16)
Figure 1.6
Figure 1.6
4012522a
COMPRESSOR
DISCHARGE
LINE PURGE VALVE
(EXHAUST)
COMPRESSOR
CONTROL
(PURGE)
PORT
DRYER
INLET PORT
COMPRESSOR
INTAKE LINE
SUPPLY
TANK
SYSTEM
RESERVOIRS
ONE-WAY
CHECK
VALVE
SYSTEM SAVER
1200 PLUS
AIR DRYER
UNLOADER
LINE
SUPPLY
LINE

1 Introduction
7
Meritor WABCO Maintenance Manual 34 (Revised 03-16)
Air Dryer Components
Meritor WABCO single cartridge air dryers contain replaceable
component parts. Standard air dryer components are illustrated in
Figure 1.7. For 1200 Plus Series air dryers, refer to Figure 1.8.
Refer to Figure 1.9 for 1200 Plus Series air dryers with Multi Circuit
Protection. Refer to Section 2 for instructions for removal of old
parts and installation of new parts.
Figure 1.7
Figure 1.7
1002146b
SYSTEM SAVER 1200 OR 1800
COALESCINGDESICCANT
CARTRIDGE
PRESSURE
RELIEF
VALVE
PURGE
VALVE
ASSEMBLY
REGENERATION VALVE ASSEMBLY
(FOR REGENERATION STYLE AIR
DRYERS)
O-RING
12- OR 24-VOLT
HEATER ASSEMBLY
1200
1800
PURGE
TANK
Port 22 drilled
and tapped for
dedicated purge
style.
TURBO
CUT-OFF
VALVE
ASSEMBLY
OUTLET
CHECK
VALVE
ASSEMBLY

1 Introduction
8Meritor WABCO Maintenance Manual 34 (Revised 03-16)
Figure 1.8
Figure 1.8
4007692a
PRESSURE
RELIEF
VALVE
DESICCANT
CARTRIDGE
SYSTEM SAVER 1200 PLUS SERIES AIR DRYER
OUTLET
CHECK
VALVE
ASSEMBLY GOVERNOR
O-RING
PURGE VALVE
ASSEMBLY
TURBO
CUT-OFF
VALVE
ASSEMBLY
HEATER
ASSEMBLY

1 Introduction
9
Meritor WABCO Maintenance Manual 34 (Revised 03-16)
Figure 1.9
Figure 1.9
4011774a
PURGE VALVE
ASSEMBLY
HEATER ASSEMBLY
GOVERNOR
OUTLET CHECK
VALVE ASSEMBLY
O-RING
TURBO
CUT-OFF
VALVE
ASSEMBLY
PRESSURE
RELIEF VALVE
DRAIN
VALVE
DESICCANT
CARTRIDGE
SYSTEM SAVER 1200 PLUS SERIES AIR DRYER
WITH MULTI CIRCUIT PROTECTION

1 Introduction
10 Meritor WABCO Maintenance Manual 34 (Revised 03-16)
Dryer Identification
The identification tag on the face of the dryer provides important
information about the air dryer — information you will need when
servicing or replacing components. Figure 1.10.
Figure 1.10
Description of Components
Replacement components for single canister air dryers are
described below.
Desiccant Cartridge: A cylindrical steel housing containing the
filter elements and desiccant needed to filter and dry system air.
Spin-on/spin-off design allows quick and easy maintenance. The
System Saver 1800 Series cartridge is 3.2-inches (81 mm) taller
than the 1200 Series cartridge [6.4-inches (164 mm) tall].
Figure 1.11.
Always replace cartridges with authentic Meritor WABCO brand
cartridges.
Figure 1.11
Figure 1.10
1696
1002147c
SYSTEM
SAVER
1200/1200U
DATE CODE
FIRST TWO DIGITS = BUILD WEEK
LAST TWO DIGITS = BUILD YEAR
MANUFACTURING
LOCATION CODE
SYSTEM
SAVER
1800/1800U
SYSTEM
SAVER
1200 PLUS
SYSTEM
SAVER
1200E
PART
NUMBER
SYSTEM
SAVER
1200P/1200UP
OR
1800P/1800UP
Figure 1.11
1002148b
1800
1200

1 Introduction
11
Meritor WABCO Maintenance Manual 34 (Revised 03-16)
Coalescing Cartridge: Utilizes a filter element added to the
standard desiccant to remove aerosols and oil particles.
Heater: Located in the air dryer base, the heater prevents water
that collects in the air dryer from freezing. It consists of a cylindrical
resistive-type heating element and a small circular thermostat.
Heater is available for 12- and 24-volt air dryers. Figure 1.12.
Figure 1.12
Bypass Valve: A valve located between the inlet and outlet ports of
the dryer. It allows air to flow into the dryer and go directly to the
outlet port, bypassing the desiccant cartridge. The 1200 and 1200E
Series with date codes later than 0894 do not use a bypass valve.
Figure 1.13.
Figure 1.13
Outlet Check Valve: A valve located in the outlet port (port 21) of
the air dryer. It prevents air from flowing back through the air dryer
and escaping out the purge valve during a compressor unload cycle.
Figure 1.14.
Figure 1.14
Pressure-Controlled Check Valve (PCCV): Used with System
Saver Series regeneration style air dryers. The PCCV is usually
mounted on the secondary air tank in place of an inlet check valve. It
lets air backflow from the secondary tank to the supply tank as long
as system pressure remains between the normal cut-in and cut-out
range of the governor. It allows additional air volume for generation
during the air dryer purge cycle. Not used with integrated or
separate purge tank style air dryers. Figure 1.15.
Figure 1.15
Pressure Relief Valve: A valve that protects the air dryer from
over-pressurization. On dryers with date codes earlier than 2295, it
is installed in the inlet port of the dryer (port 1) using a Street-Tee
fitting. On dryers with date codes later than 2295, the pressure
relief valve is attached directly to the air dryer. Figure 1.16.
Figure 1.16
Figure 1.12
Figure 1.13
1002149a
HEATER MAY BE STAINLESS
STEEL CLAD OR CERAMIC
1002150a
Figure 1.14
Figure 1.15
Figure 1.16
1002151a
1002152b
AIR FLOW
DIRECTION
1002153a

1 Introduction
12 Meritor WABCO Maintenance Manual 34 (Revised 03-16)
Purge Valve: A valve located on the bottom of the air dryer base
that remains open during a compressor unload cycle. It allows
collected moisture, condensation, and contamination to be expelled
from the air dryer during a purge cycle. Figure 1.17.
Figure 1.17
Regeneration Valve: The valve that controls regeneration of the
desiccant. It allows air from the supply and secondary tanks to
bypass the outlet check valve. The air expands and backflushes
moisture off of the desiccant, then out through the dryer’s purge
valve. Figure 1.18.
Used with 1200 Series air dryers only.
Figure 1.18
ECON Valve Replacement Part: This valve is used on System
Saver Series 1200E single cartridge air dryers used with Holset
E-type compressors. Figure 1.19.
Figure 1.19
ECON Valve: This valve must be installed if System Saver 1200
Series air dryers NOT DESIGNATED E are used with Holset E-type
compressors. This valve is not required on System Saver 1200 E air
dryers. Figure 1.20.
Figure 1.20
Turbo Cut-off Valve: A valve located in the inlet port of the air dryer.
It closes the path between the air compressor and the air dryer
purge valve during compressor unload. This prevents a loss of
turbocharger boost pressure during a compressor unload cycle,
thereby maintaining boost pressure for maximum engine
horsepower. Figure 1.21 and Figure 1.22 (used exclusively on the
1200 Plus model).
There is no spring in the turbo cut-off valve assemblies used on U
Series air dryers.
The System Saver E Series air dryers use a special turbo cut-off
valve. Refer to the air dryer parts book PB-8857AS for part number
information.
Figure 1.17
Figure 1.18
1002154a
1002155a
Figure 1.19
Figure 1.20
4003877a
4003878a

1 Introduction
13
Meritor WABCO Maintenance Manual 34 (Revised 03-16)
Figure 1.21
Figure 1.22
Heater Power Harness: Twelve-inch cable with Metri-Pack plug
provides electrical connection to air dryer heating unit. Figure 1.23.
Figure 1.23
Purge Silencer: Optional part for all Meritor WABCO air dryers. It is
used to reduce the noise level of an air dryer purge. Figure 1.24.
Figure 1.24
Pressure Protection Elements: Ports that are located directly on
the air dryer. The eight ports are directly connected to the primary,
secondary and any auxiliary air tanks. The function of the pressure
protection elements is to protect the air tanks from a loss of
pressure in the air system. These pressure protection elements are
not serviceable. Figure 1.25.
Figure 1.25
Figure 1.21
Figure 1.22
Figure 1.23
1002156a
TOP
SPRING
4007691a
SYSTEM SAVER
1200 PLUS
1002157a
Figure 1.24
Figure 1.25
1002158a
4011899a

2 Component Removal and Installation
14 Meritor WABCO Maintenance Manual 34 (Revised 03-16)
2 Component Re moval and Installation
Hazard Alert Messages
Read and observe all Warning and Caution hazard alert messages in
this publication. They provide information that can help prevent
serious personal injury, damage to components, or both.
WARNING
To prevent serious eye injury, always wear safe eye protection
when you perform vehicle maintenance or service.
Remove all pressure from the air system before you
disconnect any component, including the desiccant cartridge.
Pressurized air can cause serious personal injury.
Park the vehicle on a level surface. Block the wheels to
prevent the vehicle from moving. Support the vehicle with
safety stands. Do not work under a vehicle supported only by
jacks. Jacks can slip and fall over. Serious personal injury and
damage to components can result.
NOTE: The pressure protection elements are not serviceable on the
System Saver 1200 Plus with MCP. The entire air dryer needs to be
replaced if these parts are not operating effectively.
Component Replacement
Requirements
Refer to Table B for component replacement requirements. If
necessary, you may also refer to Table D for System Saver Series air
dryer troubleshooting. Before replacing any air dryer component,
verify that the air compressor and air governor are working correctly,
then drain the air tanks. Repair or replace these parts, if necessary.
Check the entire air system for leaks, and repair as necessary.
When draining air tanks before servicing the air dryer, check for
water and/or oil that may have accumulated in the tanks. Water
and/or oil in the air tanks could indicate a problem with the dryer or
compressor.
Table B
Replacement Requirements
Component When to Replace Why
Cartridge Every two to three years for standard dessicant.
Every one to two years for coalescing.
Preventative maintenance.
When compressor is replaced. Contaminated cartridge.
Water in supply tank. Saturated or contaminated cartridge, high duty cycle
(wrong application of air dryer).
Bypass Valve (dryers with date
codes earlier than 0894)
Valve leaking, inlet to outlet. Cut O-ring, bad seat.
Heater Assembly Water collecting in air dryer is freezing —
electrical power to dryer is O.K.
Heater assembly not working (internal short or open
circuit).
Outlet Check Valve Air continues to flow from purge valve after
purge cycle, but stops flowing when the
compressor load cycle begins.
Valve is stuck in the open position, or not functioning
properly.
No pressure build-up in system, everything else
is O.K.
Valve is stuck in closed position.
Purge Valve No purge cycle when compressor unloads —
normal pressure at dryer control port 4 (governor
port).
Valve is stuck in the closed position, or not
functioning properly.
Air flows from purge valve during compressor’s
load cycle — no pressure at dryer control port.
Valve is stuck in the open position, or not functioning
properly.
Pressure Protection Valve Pressure protection valves will not open (air
dryer must be replaced).
Valves are stuck in closed position.

2 Component Removal and Installation
15
Meritor WABCO Maintenance Manual 34 (Revised 03-16)
NOTE: When replacing air dryer components, use only Meritor
WABCO replacement parts.
The exploded view of the air dryer in Section 1 shows the location of
the various air dryer components.
Component Removal and Installation
Desiccant Cartridge
NOTE: Replacement cartridges are marked “System Saver
Series.”
1. Replacement kit contains one cartridge and one O-ring.
Figure 2.1.
Figure 2.1
2. Loosen and remove the old cartridge. Use strap wrench if
necessary.
3. Remove and discard O-ring from dryer base.
Turbo Cut-Off Valve Air compressor stuck pumping, TCU remains
open. System will build pressure until safety
valve opens in system.
Signal line loss.
Air flows from purge valve during compressor
unload cycle after purge cycle, and flow is
noticeably stronger at high engine RPM,
especially under load.
Turbo cut-off valve leaking.
No pressure build-up in system — high
compressor discharge line pressure.
Valve stuck in closed position.
Regeneration Valve Regeneration cycle continues after compressor
begins, and secondary tank pressure drops 15
psi (103 kPa) or more.
Regeneration valve allowing too much air to come
back into cartridge.
Purge cycle is too short (five seconds or less) —
pressure-controlled check valve is O.K., no leak
in governor control line.
Regeneration valve not allowing enough air to come
back into cartridge.
Air dryer purges — but no regeneration, no
check valve between air dryer and supply tank,
and purge valve has not closed.
Regeneration valve not allowing any air to come back
into cartridge.
Pressure-Controlled Check
Valve
Regeneration cycle too short; may result in
water in tank.
Valve checks (stops airflow) too high.
Replacement Requirements
Component When to Replace Why
Figure 2.1
1002163b
1800
1200

2 Component Removal and Installation
16 Meritor WABCO Maintenance Manual 34 (Revised 03-16)
NOTE: If seats are damaged so badly that a tight seal cannot
be maintained, replace the air dryer.
4. Inspect and clean seal seat. Repair any minor damage.
5. Lubricate and install new O-ring on stem.
6. Lubricate cartridge seal.
7. Thread replacement cartridge onto the base until the seal
touches the base. Then, tighten the cartridge ONE additional
turn. DO NOT OVERTIGHTEN. Figure 2.2.
Figure 2.2
Outlet Check Valve Assembly
1. Review Figure 2.3 to ensure you have all of the parts required
to replace the outlet check valve. Use the grease included with
the replacement kit to lubricate the O-ring seal.
Figure 2.3
2. Remove the snap ring, washer, spring, valve body and O-ring.
3. Clean and inspect the valve bore. If the bore is damaged so
that a tight seal cannot be maintained, replace the air dryer.
4. Install the new O-ring on the valve body. Figure 2.4.
Figure 2.4
5. Apply a thin layer of grease to the valve bore and the O-ring.
6. Install the new valve body with its long end in the bore.
7. Install the new spring with its small end around the “Y”-shaped
fins on the valve body.
8. Install the new washer and the new snap ring to hold the
components in place.
Heater Assembly
1. Review Figure 2.5 to ensure you have all of the parts required
to replace the heater assembly.
Figure 2.5
2. Disconnect the plug.
Figure 2.2
Figure 2.3
1002164a
SEAL
SEAL SEAT
O-RING
1002165a
O-RING
SPRING
GREASE
WASHER
SNAP
RING
VALVE
BODY
Figure 2.4
Figure 2.5
1002166a
SNAP RING
WASHER
SPRING
O-RING
VALVE
BODY
1002167a
THERMOSTAT
RECEPTACLE
O-RING
HEATER
ELEMENT
This manual suits for next models
7
Table of contents
Other WABCO Other manuals
Popular Other manuals by other brands
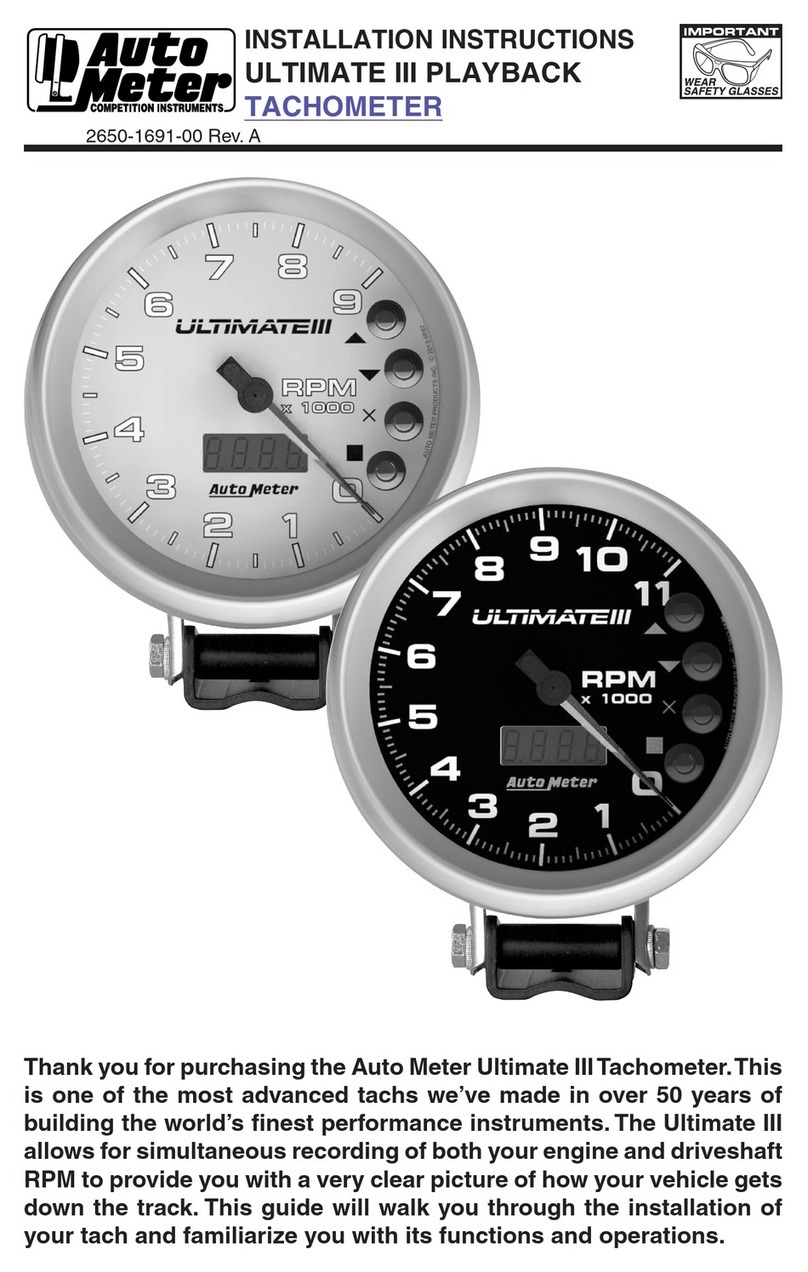
AutoMeter
AutoMeter ULTIMATE III Installation instructions manual
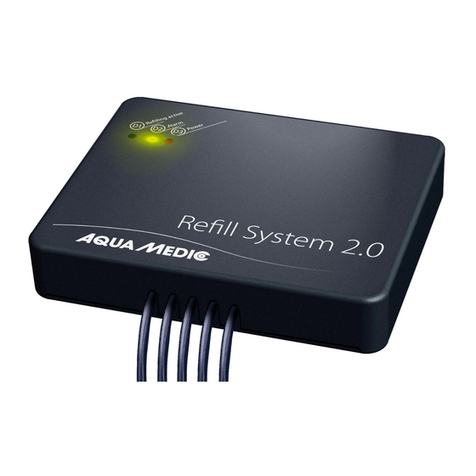
Aqua Medic
Aqua Medic Refill System 2.0 Operation manual
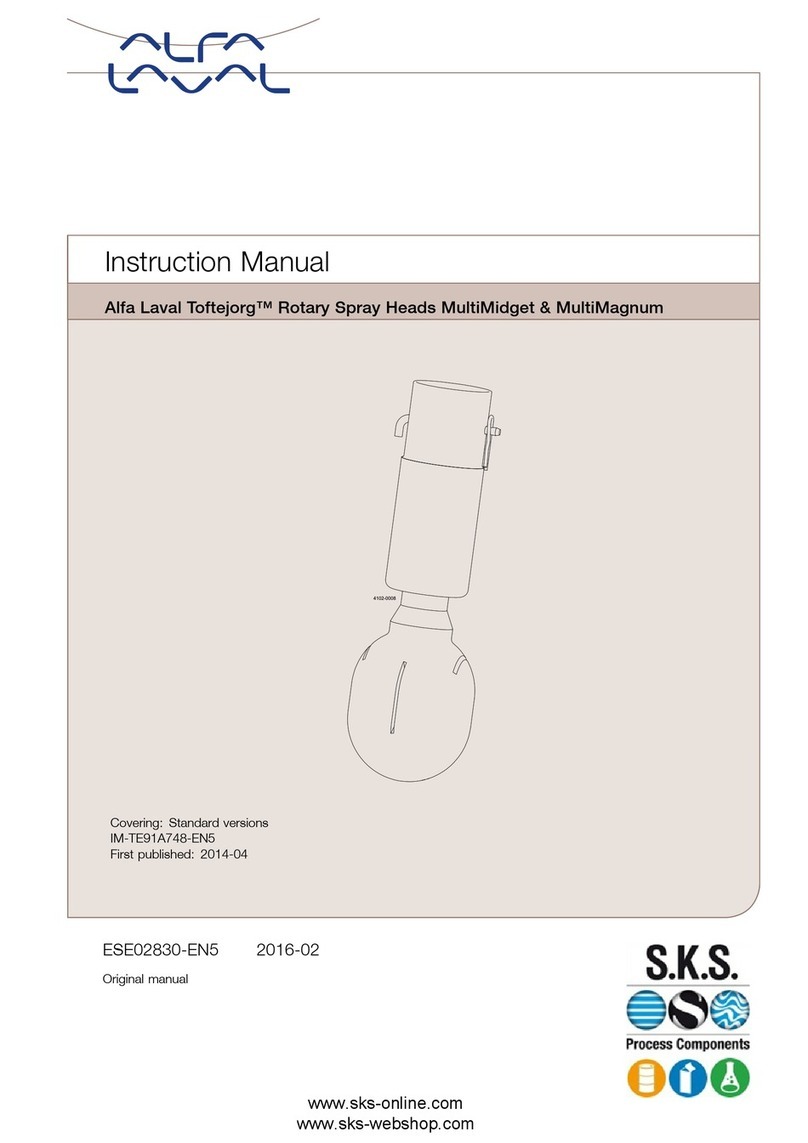
Alfalaval
Alfalaval Toftejorg instruction manual

Aqua Medic
Aqua Medic Turboflotor Percula Operation manual
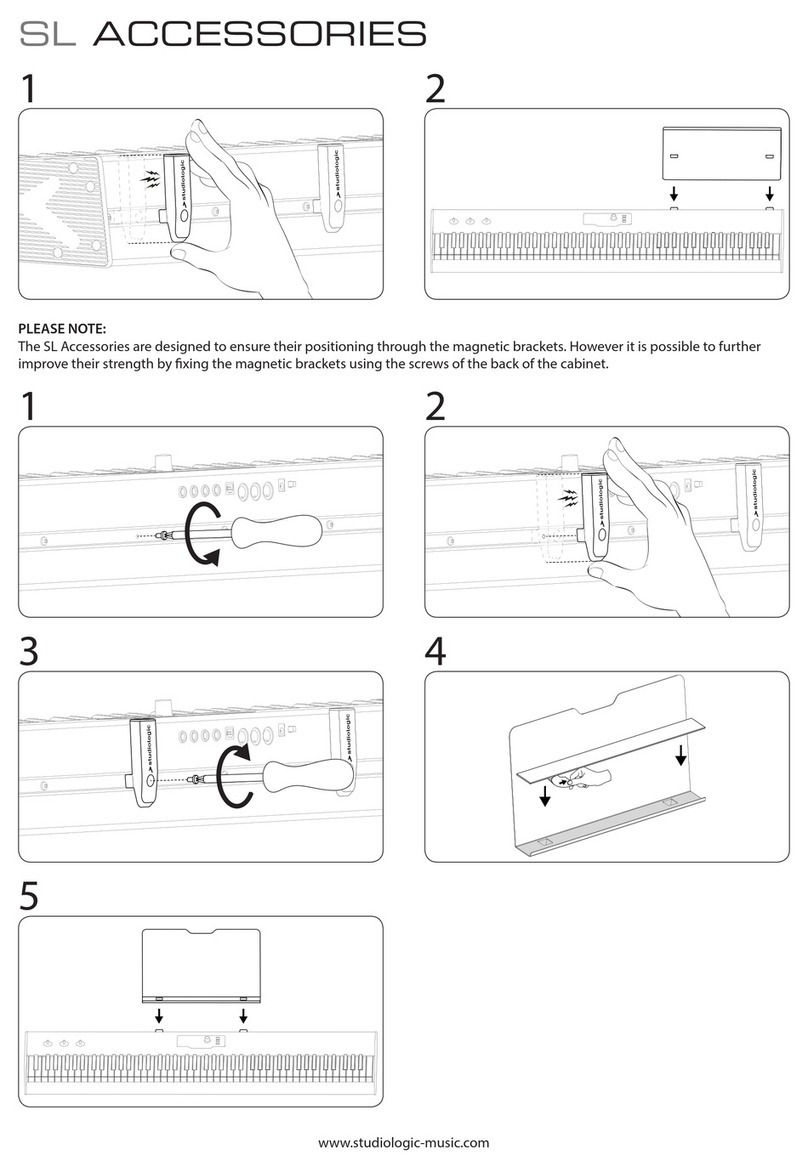
Studio Logic
Studio Logic SL Magnetic Computer Plate manual

Aqua One
Aqua One AquaReef 525 manual

OEM Tools
OEM Tools 24936 Operating instructions and parts manual

Aqua Medic
Aqua Medic Calciumreactor KR 400 Operation manual

Iron logic
Iron logic Matrix III MF-I user manual

Aqua Medic
Aqua Medic Anthias 130 Operation manual
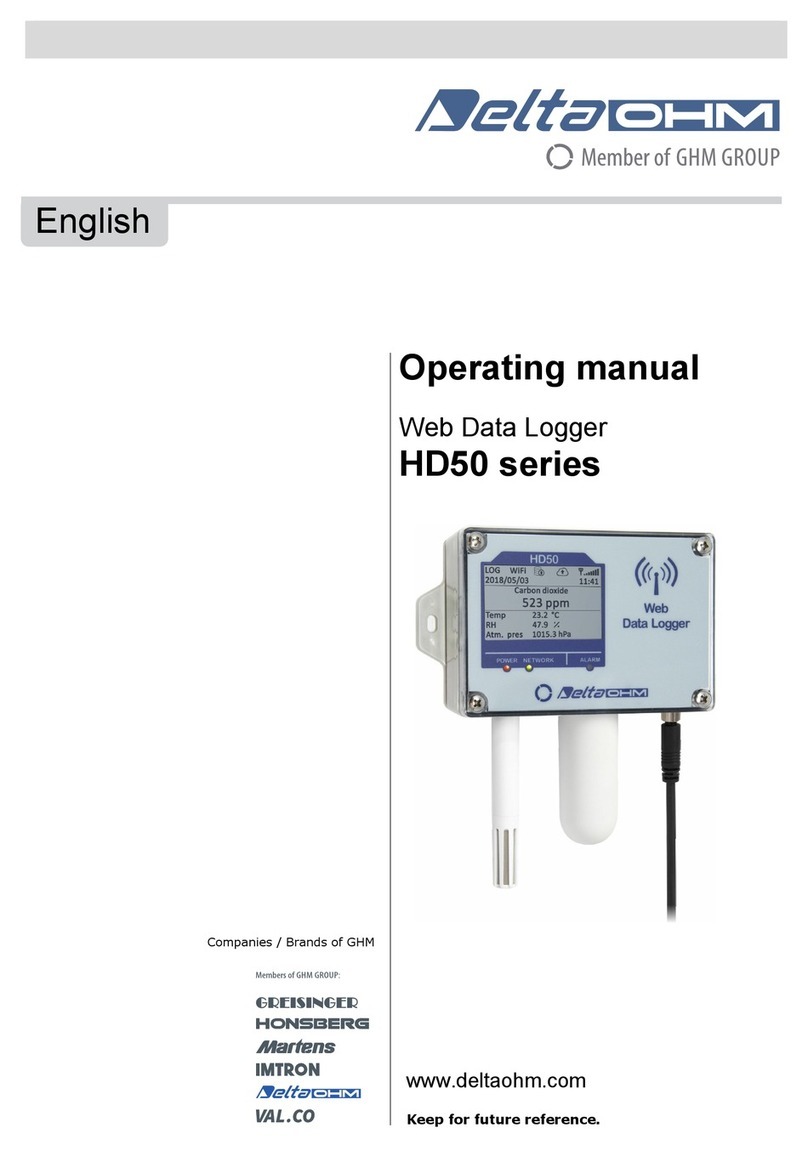
Delta OHM
Delta OHM HD50 N/1 TC operating manual

Aqua Medic
Aqua Medic Mistral 200 Operation manual