Wachendorff URDR001A User manual

Controller
User manual
URDR001A

2 - URDR001A - User manual

3 - URDR001A - User manual
Table of contents
1 Safety guidelines.......................................................................................................................................................... 5
1.1 Organization of safety notices.................................................................................................................. 5
1.2 Safety Precautions ....................................................................................................................................... 5
1.3 Precautions for safe use.............................................................................................................................. 6
1.4 Environmental policy / WEEE .................................................................................................................... 7
2 Model Identification.................................................................................................................................................... 7
3 Technical Data.............................................................................................................................................................. 7
3.1 General Features .......................................................................................................................................... 7
3.2 Hardware Features ...................................................................................................................................... 7
3.3 Software Features ........................................................................................................................................ 7
3.4 Programming mode.................................................................................................................................... 8
4 Dimensions and Installation..................................................................................................................................... 8
5 Electrical wirings .......................................................................................................................................................... 8
5.1 Wiring diagram............................................................................................................................................. 9
5.1.a Power Supply...................................................................................................................................... 9
5.1.b Analogue Input AI1........................................................................................................................... 9
5.1.c CT input ............................................................................................................................................. 10
5.1.d Digital inputs.................................................................................................................................... 10
5.1.e Serial input........................................................................................................................................ 10
5.1.f Digital output................................................................................................................................... 10
5.1.g Analogue output AO1 .................................................................................................................... 10
5.1.h Relays output Q1 - Q2..................................................................................................................... 10
5.1.i Relay output Q3............................................................................................................................... 11
6 Display and Key Functions....................................................................................................................................... 11
6.1 Meaning of Status Lights (Led)................................................................................................................ 11
6.2 Keys................................................................................................................................................................ 12
7 Controller Functions.................................................................................................................................................. 12
7.1 Modification of main and alarm setpoint value ................................................................................ 12
7.2 Automatic Tune .......................................................................................................................................... 12
7.3 Manual Tune................................................................................................................................................ 12
7.4 Tuning once ................................................................................................................................................. 13
7.5 Synchronized tuning ................................................................................................................................. 13
7.6 Digital input functions.............................................................................................................................. 14
7.7 Automatic / Manual regulation for % output control....................................................................... 14
7.8 Heater Break Alarm on CT (Current Transformer) .............................................................................. 15
7.9 Dual Action (Heating-Cooling)............................................................................................................... 15
7.10 LATCH ON Function ................................................................................................................................... 16
7.11 Soft-Start Function..................................................................................................................................... 17
7.12 Pre-Programmed cycle ............................................................................................................................. 17
7.13 Retransmission function on analogue output.................................................................................... 17
7.14 Timer functions........................................................................................................................................... 18
8 Serial communication .............................................................................................................................................. 19
8.1 Serial compatibility with URDR0001 .....................................................................................................23
9 Reading and configuration through NFC ............................................................................................................25
9.1 Configuration through memory card ...................................................................................................25
9.2 Memory card creation/update................................................................................................................26
9.3 Configuration loading from memory card..........................................................................................26
10 Loading default values.............................................................................................................................................26
11 Access configuration .................................................................................................................................................26
11.1 Parameters list functioning .....................................................................................................................27
12 Table of configuration parameters........................................................................................................................27

4 - URDR001A - User manual
13 Alarm Intervention Modes....................................................................................................................................... 51
13.a Absolute or threshold alarm active over (par. 123
A L .1 . F .
=
A b . u P. A .
)........................................................... 51
13.b Absolute or threshold alarm active below (par. 123
A L .1 . F .
=
A b . u P. A .
)........................................................ 51
13.c Absolute or threshold alarm referred to command setpoint active over (par. 123
A L .1 . F .
=
Ab . c. u .A.
) 52
13.d Absolute or threshold alarm referred to command setpoint active below (par. 123
A L .1 . F .
=
Ab . c.L.A.
)52
13.e Band alarm (par. 123
A L .1 . F .
=
band
)..................................................................................................................52
13.f Asymmetric band alarm (par. 123
A L .1 . F .
=
A.band
)........................................................................................52
13.g Upper deviation alarm (par. 123
A L .1 . F .
=
up.dev.
)..........................................................................................53
13.h Lower deviation alarm (par. 123
A L .1 . F .
=
Lo.dev.
)..........................................................................................53
13.1 Alarms label................................................................................................................................................. 53
14 Fault reporting table .................................................................................................................................................54

5 - URDR001A - User manual
Introduction
The process controller URDR001A is specifically conceived for application on control panels with DIN
rail mounting. It stands out for the bright display which ensures optimal visibility and increased level
of information for the operator beside a scrolling help function.
URDR001A relies on Wachendorff flagship programming mode by NFC/RFID technology with
dedicated Wachendorff EMG App for Android devices (same already used for OLED-Wachendorff
indicators) not requiring wirings and power supply, allowing quick set-up/updates on site.
The outputs can be selected as command/multiple alarm modes/analogue retransmission. Serial
communication RS485 is avaiable with Modbus RTU/Slave protocol. Useful power supply with
extended range 24 to 220VAC / VDC with galvanic insulation.
1 Safety guidelines
Read carefully the safety guidelines and programming instructions contained in this manual before
connecting/using the device.
Disconnect power supply before proceeding to hardware settings or electrical wirings to avoid risk of
electric shock, fire, malfunction.
Do not install/operate the device in environments with flammable/explosive gases.
This device has been designed and conceived for industrial environments and applications that rely
on proper safety conditions in accordance with national and international regulations on labour
and personal safety. Any application that might lead to serious physical dama ge/ life risk or involve
medical life support devices should be avoided. Device is not conceived for applications related to
nuclear power plants, weapon systems, flight control, mass transportation systems.
Only qualified personnel should be allowed to use device and/or service it and only in accordance to
technical data listed in this manual.
Do not dismantle/modify/repair any internal component.
Device must be installed and can operate only within the allowed environmental conditions.
Overheating may lead to risk of fire and can shorten the lifecycle of electronic components.
1.1 Organization of safety notices
Safety notices in this manual are organized as follows:
Safety notice Description
Danger! Disregarding these safety guidelines and notices can be life-threatening.
Warning! Disregarding these safety guidelines and notices can result in severe injury or
substantial damage to property.
Information! This information is important for preventing errors.
1.2 Safety Precautions
CAUTION - Risk of Fire and Electric Shock
This product is UL listed as DIN-rail mounting process control equipment. It must be
mounted in an enclosure that does not allow fire to escape externally.
Danger!
If the output relays are used past their life expectancy, contact fusing or burning may
occasionally occur. Always consider the application conditions and use the output
relays within their rated load and electrical life expectancy. The life expectancy of
output relays varies considerably with the output load and switching conditions.
Danger!
Loose screws may occasionally result in fire.
For screw terminals of relays and of power supply, tighten screws to tightening torque
of 0,51 Nm. For other terminals, tightening torque is 0,19 Nm
Warning!
A malfunction in the Digital Controller may occasionally make control operations
impossible or prevent alarm outputs, resulting in property damage. To maintain safety
in the event of malfunction of the Digital Controller, take appropriate safety measures,
such as installing a monitoring device on a separate line.
Warning!

6 - URDR001A - User manual
1.3 Precautions for safe use
Be sure to observe the following precautions to prevent operation failure, malfunction, or adverse
affects on the performance and functions of the product. Not doing so may occasionally result in
unexpected events. Do not handle the Digital Controller in ways that exceed the ratings.
• The product is designed for indoor use only. Do not use or store the product outdoors or in any of
the following places.
- Places directly subject to heat radiated from heating equipment.
- Places subject to splashing liquid or oil atmosphere.
- Places subject to direct sunlight.
- Places subject to dust or corrosive gas (in particular, sulfide gas and ammonia gas).
- Places subject to intense temperature change.
- Places subject to icing and condensation.
- Places subject to vibration and large shocks.
• Installing two or more controllers in close proximity might lead to increased internal temperature
and this might shorten the life cycle of electronic components. It is strongly recommended to
install cooling fans or other air-conditioning devices inside the control cabinet.
• Always check the terminal names and polarity and be sure to wire properly. Do not wire the
terminals that are not used.
• To avoid inductive noise, keep the controller wiring away from power cables that carry high voltages
or large currents. Also, do not wire power lines together with or parallel to Digital Controller
wiring. Using shielded cables and using separate conduits or ducts is recommended. Attach a
surge suppressor or noise filter to peripheral devices that generate noise (in particular motors,
transformers, solenoids, magnetic coils or other equipment that have an inductance component).
When a noise filter is used at the power supply, first check the voltage or current, and attach the
noise filter as close as possible to the Digital Controller. Allow as much space as possible between
the Digital Controller and devices that generate powerful high frequencies (high-frequency
welders, high-frequency sewing machines, etc.) or surge.
• A switch or circuit breaker must be provided close to device. The switch or circuit breaker must be
within easy reach of the operator, and must be marked as a disconnecting means for the controller.
• The device must be protected by a fuse T1A, 250 VAC, time lag, low shut-off capacity.
•
Wipe off any dirt from the Digital Controller with a soft dry cloth. Never use thinners, benzine, alcohol,
or any cleaners that contain these or other organic solvents. Deformation or discoloration may occur.
• The number of non-volatile memory write operations is limited. Therefore, use EEprom write mode
when frequently overwriting data, e.g.: through communications.
• Chemicals/solvents, cleaning agents and other liquids must not be used.
• Non-respect of these instructions may reduce performances and safety of the devices and cause
danger for people and property.
For CT (Current Transformer) input:
• Warning: To reduce risk of electric shock, always open or disconnect circuit from power-distribu-
tion system (or service) of building before installing or servicing current transformers
• For use with Listed Energy-Monitoring Current Transformers
• The current transformers may not be installed in equipment where they exceed 75 percent of the
wiring space of any cross-sectional area within the equipment
• Restrict installation of current transformer in an area where it would block ventilation openings
• Restrict installation of current transformer in an area of breaker arc venting
• Not suitable for Class 2 wiring methods
• Not intended for connection to Class 2 equipment
• Secure current transformer and route conductors so that the conductors do not directly contact
live terminals or bus.

7 - URDR001A - User manual
1.4 Environmental policy / WEEE
Do not dispose electric tools together with household waste material.
According to European Directive 2012/19/EU on waste electrical and electronic equipment and its
implementation in accordance with national law, electric tools that have reached the end of their life
must be collected separately and returned to an environmentally compatible recycling facility.
2 Model Identification
Power supply 24..220 VAC/VDC ±10% 50/60 Hz – 3 Watt
URDR001A 1 A.I. + 1 relays 5 A + 1 relays 3 A + 1 relay 2 A + 2 SSR + 2 D.I. + 1 A.O. V/mA +
RS485 + CT
3 Technical Data
3.1 General Features
Displays 4 digits 0,52’’, 5 digits 0,30’’
Operating temperature Temperature: 0-45° C -Humidity 35..95 uR%. Max. altitude: 2000m
Sealing Open type, IP20 (not UL evaluated)
Material Box and front panel PC UL94V0
Weight Approx. 210 g
3.2 Hardware Features
Analogue
inputs
AI1: configurable via software.
Input: Thermocouple type K, S, R, J,T,E,N,B.
Automatic compensation of cold junction
from -25..85° C.
Thermoresistances: PT100, PT500, PT1000,
Ni100, PTC 1K, NTC 10K (β 3435K)
Input V/mA: 0-1 V, 0-5 V, 0-10 V, 0-20 o 4-20
mA, 0-60 mV.
Pot. Input: 1...150 KΩ.
CT: 50 mA.
Tolerance (25° C)
± 0.2% ±1 digit (on F.s.) for thermocou-
ple, thermoresistance and V/mA.
Cold junction accuracy 0.1° C/°C.
Impedence:
0-10 V: Ri>110 KΩ
0-20 mA: Ri<5 Ω
0-40 mV: Ri>1 MΩ
Relay outputs Config. as command and alarm output
Contacts:
Q1: 5 A - 250 VAC for resistive load.
Q2: 3 A - 250 VAC for resistive load.
Q3: 2 A - 250 VAC for resistive load.
SSR outputs Config. as command and alarm output 12/24 V, 25 mA.
Analogue
output
Configurable as command
and alarm output or as retransmission of
process / setpoints.
Configurable:
0-10 V with 40000 points +/-0.2% (on
F.s.) @25 °C; load >= 1 KΩ
4-20 mA with 40000 points +/-0.2% (on
F.s.) @25 °C; load <= 250Ω
Power-supply Extended power-supply 24..220 VAC/VDC
±10% 50/60 Hz Consumption: 3 Watt
3.3 Software Features
Regulation algorithms ON-OFF with hysteresis.
P, PI, PID, PD with proportional time
Proportional band 0..9999°C o °F
Integral time 0,0..999,9 sec (0 excludes)
Derivative time 0,0..999,9 sec (0 excludes)
Controller functions Manual or automatic Tuning, selectable alarm, protection of command
and alarm setpoints.

8 - URDR001A - User manual
3.4 Programming mode
by keyboard ..see paragraph
software LabSoftview ..on
“Download section”
of www.wachendorff-prozesstechnik.de
Wachendorff EMG-App
..through download the App on Google Play Store®, see paragraph
When activated by a reader/interrogator supporting NFC-V protocol,
controller URDR001A is to be considered a VICC (Vicinity Inductively
Coupled Card) according to ISO/IEC 15693 and it operates at a frequency
of 13.56 MHz. The device does not intentionally emit radio waves.
4 Dimensions and Installation
Extractable terminal blocks
Morsettiere Estraibili
Ausfahrbare Klemmen
72 mm
90 mm
64 mm
DIN rail mounting guide EN50022
Attacco a guida DIN EN50022
Hutschienenmontage EN50022
Memory Card USB
(optional)
Cod. 2100.30.013
24 23 22
24...230V
AC/DC
B (+)
RS485 CT
PT100
TC
NI100 A\V
PTC
NTC
A (-) DO2
(PNP) DI2
(PNP) DI1
(PNP) +V
21 20 19
1
NO C
Q1 Q2 Q3
NC NO NO 0V (PNP)
DO1 AO1
V/mA
C CNC
2 3 4 5 6 7 8 9 10 11 12
18 17 16 15 14 13
FNC
SET
C1
C2 A1 A2 A3 TUN MAN REM
5 Electrical wirings
This controller has been designed and manufactured in conformity to Low Voltage Directive 2006/95/
EC, 2014/35/EU (LVD) and EMC Directive 2004/108/EC, 2014/30/EU (EMC). For installation in industrial
environments please observe following safety guidelines:
• Separate control line from power wires.
• Avoid proximity of remote control switches, electromagnetic contactors, powerful engines.
• Avoid proximity of power groups, especially those with phase control.
• It is strongly recommended to install adequate mains filter on power supply of the machine where
the controller is installed, particularly if supplied 220VAC.
The controller is designed and conceived to be incorporated into other machines, therefore
CE marking on the controller does not exempt the manufacturer of machines from safety and
conformity requirements applying to the machine itself.
• Wiring of pins: use crimped tube terminals or flexible/rigid copper wire with diameter 0.2 to 2.5
mm² (min. AWG30, max. AWG14, Minimum temperature rating of the cable to be connected to the
field wiring terminals, 75°C). Cable stripping lenght 7 to 8 mm. Tighten screws to tightening torque
of 0,51 Nm.
• Use Copper or Copper-Clad Aluminum Conductors Only or AL-CU or CU-AL.

9 - URDR001A - User manual
5.1 Wiring diagram
URDR001A
24 23 22
24...220V
AC/DC
B (+)
RS485 CT PT100
TC
NI100 A\V
PTC
NTC
A (-) DO2
(PNP) DI2
(PNP) DI1
(PNP) +V
21 20 19
1
NO C
Q1 Q2 Q3
NC NO NO 0V (PNP)
DO1 AO1
V/mA
C CNC
2 3 4 5 6 7 8 9 10 11 12
18 17 16 15 14 13
5.1.a Power Supply
SUPPLY
24...220
VAC/DC
24
23
Switching power supply 24..220 VAC/VDC ±10% 50/60 Hz - 3 Watt
Galvanic insulation (2500V).
5.1.b Analogue Input AI1
AI1 TC
Shield/Schermo
13
14
For thermocouples K, S, R, J, T, E, N, B.
• Comply with polarity
• For possible extensions, use compensated cable and terminals suitable for
the thermocouples used (compensated).
• When shielded cable is used, it should be grounded at one side only.
AI1
PT/NI100
Shield/Schermo
Rosso
Red
Bianco
White
Rosso
Red
13
14
15
For thermoresistances PT100, Ni100.
• For the three-wire connection use wires with the same section.
• For the two-wire connection short-circuit terminals 13 and 15
• When shielded cable is used, it should be grounded at one side only.
RED/ROSSO
RED/ROSSO
WHITE/BIANCO
AI1
Shield/Schermo
PTC/NTC
15
14
For thermoresistances NTC, PTC, PT500, PT1000 and linear potentiome-
ters.
When shielded cable is used, it should be grounded at one side only to avoid
ground loop currents.
AI1 V
mA
+V
Shield/Schermo
16
14
13
For linear signals in Volt and mA
• Comply with polarity
• When shielded cable is used, it should be grounded at one side only to
avoid ground loop currents.
• It’s possible to select +V at 12Vdc or 24Vdc, by configuring parameter 282
V.out (GROUP R - di S P. - Display and interface).

10 - URDR001A - User manual
5.1.c CT input
CT
18
19
To enable CT input, modify parameter 287 ct F.
• Input for 50 mA amperometric transformer.
• Sampling time 100 ms.
• Configurable by parameters.
5.1.d Digital inputs
0V
DI1
(PNP)
17
+V
16
9
Digital inputs can be enabled by parameters.
Close pin
“DIx”
on pin
“+V”
to enable digital input.
It is possible to put in parallel the digital inputs of different devices joining
together the 0V pins (9).
5.1.e Serial input
RS485
Shield/Schermo
(B)
(A)
21
20
Modbus RS485 communication.
RTU Slave with galvanic insulation.
It is recommended to use the twisted and shielded cable for communica-
tions.
5.1.f Digital output
0V
DO1
(PNP)
9
10 Digital output PNP (including SSR) for command or alarm.
Range 12 VDC/25 mA or 24 VDC/15mA selectable by parameter 282 v.out.
5.1.g Analogue output AO1
AO1
V/mA
12
11
Linear output in mA or V(galvanically isolated) configurable as command,
alarm or retransmission of process-setpoint.
The selection mA or Volt for the linear output depends on the parameters
configuration.
5.1.h Relays output Q1 - Q2
3
2
1
Q1
5A
220V
6
5
4
Q2
3A
220V
Capacity 5 A (3 A for Q2) / 250 VAC for resistive loads.
See chart below.
Electrical endurance Q1, Q2:
• 5 A (3 A for Q2), 250 VAC, resistive loads, 105operations.
• 20/2 A, 250 VAC, cosφ = 0.3, 1.2x105operations.

11 - URDR001A - User manual
5.1.i Relay output Q3
Q3 2A 220V
Resistive
7
8
Capacity 2 A / 250 VAC for resistive loads.
See chart below.
Electrical endurance Q3:
• 2A, 250 VAC, resistive loads, 105operations.
• 20/2A, 250 VAC, cosφ = 0.3, 105operations.
6 Display and Key Functions
24 23 22
24...230V
AC/DC
B (+)
RS485 CT
PT100
TC
NI100 A\V
PTC
NTC
A (-) DO2
(PNP) DI2
(PNP) DI1
(PNP) +V
21 20 19
1
NO C
Q1 Q2 Q3
NC NO NO 0V (PNP)
DO1 AO1
V/mA
C CNC
2 3 4 5 6 7 8 9 10 11 12
18 17 16 15 14 13
FNC
SET
C1
C2 A1 A2 A3 TUN MAN REM
3
15 2
1
45 6 7 8 9 10
11
12
13
14
1123.4
Normally displays the process. During the
configuration phase, it displays the parameter
being inserted.
2PRo b e
Normally displays the setpoint. During the
configuration phase, it displays the parameter
value being inserted.
6.1 Meaning of Status Lights (Led)
3C1
ON when the command output 1 is active. In versions with single analog input, it is ON
when the valve is opening. In the versions with two analog inputs, in case of command
1 on the motorized valve, it is permanently ON when the valve is opening and flashing
during the closing phase.
4C2
ON when the command output 2 is active. In versions with single analog input, it is ON
when the valve is opening. In the versions with two analog inputs, in case of command
2 on the motorized valve, it is permanently ON when the valve is opening and flashing
during the closing phase.
5A1 ON when alarm 1 is active.
6A2 ON when alarm 2 is active.
7A3 ON when alarm 3 is active.
8TUN ON when the controller is executing an auto-tuning cycle.
9MAN ON when
“Manual”
function is active.
10 REM ON when the controller communicates through serial. Flashes when the remote setpoint
is enabled.

12 - URDR001A - User manual
6.2 Keys
11
• Increases the main setpoint.
• During configuration allows to scroll the parameters or the groups of parameters.
• Increases the setpoints.
12
• Decreases the main setpoint.
• During configuration allows to scroll the parameters or the groups of parameters.
• Decreases the setpoints.
13 SET
• Allows to visualize command and alarm setpoints.
• During configuration allows to enter the parameter to be modified and confirms the
variation.
14 FNC • Allows to enter the Tuning launch function, automatic/manual selection.
• During configuration works as exit key (ESCAPE).
15
c
• ON during the rising phase of the pre-programmed cycle;
d
• ON during the falling phase of the pre-programmed cycle;
c
d
• Both ON during parameter modification, when this is not a default value.
7 Controller Functions
7.1 Modification of main and alarm setpoint value
Setpoint value can be modified from keyboard as follows:
Press Display Do
1
Value on display 2 changes. Increases or decreases the main setpoint
value.
2SET Visualizes the other setpoints on display 1.
Display 2 shows the setpoint type.
3
Value on display 1 changes. Increases or decreases the alarm setpoint
value.
7. 2 Automatic Tune
Automatic tuning procedure allows a precise regulation without delving into the PID regulation
algorithm. Selecting Auto on par. 73 tun.1 (for the regulation loop 1), or on par. 98 tun.2 (for the
regulation loop 2), the controller analyzes the proces oscillations and optimizes the PID parameters.
Led TUN flashes.
If the PID parameters are not yet selected, at the device switch-on, it is automatically launched the
manual Tuning procedure described into the next paragraph.
7. 3 Manual Tune
Manual procedure allows the user greater flexibility to decide when to update
PID algorithm parameters. During the manual tuning, the device generates a step to analyze the
system inertia to be regulated and, according to the collected data, modifies PID parameters.
After selecting Manu. on par. 73 t u n .1 , or on par. 98 tu n.2, the procedure can be activated in three ways:
• Running Tuning by keyboard:
Press FNC until display 2 shows tunE with display 1 on dis. and then press SET: display 1 shows Enab.
Led TUN switches ON and the procedure starts.
• Running Tuning by digital input:
Select tunE on par. 231 d . i .1 . F. (or on par. 239 d.i.2.F.). At first activation of digital input (commutation
on front panel) led TUN led switches on and at second activation switches off.
• Running Tuning by serial input:
Write 1 on word modbus 1216 (command 1) or 1217 (command 2): led TUN switches ON and the
procedure starts. Write 0 to stop the tuning.

13 - URDR001A - User manual
To avoid an overshoot, the treshold where the controller calculates new PID parameters is determined
by this operation:
Tune threshold = Setpoint -
“Set Deviation Tune”
(par. 74 s.d.t.1 or par. 99 s.d.t.2)
Ex.: if the sepoint is 100.0 °C and the Par.32 s.d.t.1 is 20.0 °C the threshold to calculate PID parameters
is (100.0 - 20.0) = 80.0 °C.
For a greater precision on PID parameters calculation it is suggested to start the manual tuning
procedure when the process deviates from the setpoint.
7.4 Tuning once
Set once on parameter 73 tun.1, or on parameter 98 tun.2.
Autotuning procedure is executed only once at next DRR244 restart. If the procedure doesn’t work,
will be executed at next restart.
7. 5 Synchronized tuning
Set sYNch . on parameter 73 t u n .1 or on parameter 98 tun.2.
This procedure has been conceived to calculate correct PID values on multi-zone systems, where each
temperature is influenced by the adjacent zones.
Writing on word modbus 1216 (for regulation loop 1) or 1217 (for regulation loop 2) the controller
works as follows:
Word value Action
0Tune off
1 Command output OFF
2 Command output ON
3Tune active
4Tune completed: command output OFF (read only)
5Tune not available: softstart function enabled (only reading)
Here below the functioning for regulation loop 1: the master switches-off or turns-on all zones (value
1 or 2 on word 1216) for a time long enough to create inertia on the system.
At this point the autotuning is launched (value 3 on word 1216). The controller executes the procedure
for the calculation of the new PID values. When the procedure ends, the controller switches off the
command output and selects the value 4 on word 1216. The master, who will always read the word
1216, will control the various zones and when all will have finished, will bring to 0 the value of word
1216: the various devices will regulate the temperature independently, with the new calculated values
N.B. The master must read the word 1216 at least every 10 seconds or the controller will automatically
exit the autotuning procedure.
7.6 Digital input functions
The DRR244 functions related to digital inputs, can be enabled by parameters 231 d . i .1 . F. e 239 d.i .2.F..
•
2 t.S w
.: Two threshold setpoint modification: with digital input active the DRR244 regulates on SET2,
otherwise reulates on SET1;
•
2 t.S w.i.
: Modification of 2 setpoints by digital input with impulse command;
•
3 t.S w.i.
: Modification of 3 setpoints by digital input with impulse command,
•
4 t.S w.i.
: Modification of 4 setpoints by digital input with impulse command,
•
s t./S t.
: Start / Stop of the controller by digital input with impulse command,
•
ru n.
: The regulation is enabled only with digital input active,
•
HoLd
: With digital input active the conversion is locked (visualization maintenance function);
•
tune
: Enables/disables the Tuning if par. 73 t u n .1 is selected as manu.;
•
a u . m a .i.
: If par. 48 a.ma.1. is selected as enab. or en.sto. , with impulse command on digital input, the
DRR244 switches the related regulation loop, from automatic to manual and vice versa.
•
a u.m a.c.
: If par. 48 a.ma.1. is selected as enab. or en.sto. the DRR244 switches to manual the related
regulation loop, with digital input active, otherwise the regulation is automatic.
•
A ct.ty.
: DRR244 execute a cooling type regulation with digital input active, otherwise the regulation
is of heating type;

14 - URDR001A - User manual
•
A.i. 0
: Zero tare function: brings the analogue input to 0.
•
M.reS.
: Allows the reset of the output if manual reset is active for the alarms and for the command
outputs;
•
t.1.ru n
: If timer 1 is enabled (par. 328 t m r .1 different from di s a b .), with digital input active, the timer
is switched to RUN, otherwise is kept in STOP;
•
t.1.s.e.
: If timer 1 is enabled (par. 328 t m r.1 different from di s a b .), acting on the digital input, the
status of the timer switches from STOP to RUN e vice versa;• t .1 . s t a . : If il timer 1 is enabled (par.
328 t m r.1 differnet from di s a b .), acting on the digital input, the timer is switched to RUN;
•
t.1. e n d .
: If il timer 1 is enabled (par. 328 t m r .1 differnet from di s a b .), acting on the digital input, the
timer is switched to STOP;
•
t.2.ru n
: If timer 2 is enabled (par. 331 t m r. 2 different from di s a b .), with digital input active, the timer
is switched to RUN, otherwise is kept in STOP;
•
t. 2.s .e.
: If timer 2 is enabled (par. 331 t m r. 2 different from di s a b .), acting on the digital input, the
status of the timer switches from STOP to RUN e vice versa;
•
t. 2.s t a.
: If timer 2 is enabled (par. 331 t m r. 2 different from di s a b .), acting on the digital input, the
timer is switched to RUN;
•
t. 2.en d.
: If timer 2 is enabled (par. 331 t m r. 2 different from di s a b .), acting on the digital input, the
timer is switched to STOP;
•
Lo.cfG.
: With digital input active, the access to setpoint configuration/modification is locked;
•
u p. k e y
: simulate button
operation;
•
d o w n.k.
: simulate button
operation;
•
fnc. k.
: simulate button FNC operation;
•
s et. k.
: simulate button SET operation;
•
EXT.A L.
: External Alarm. The controller goes to STOP and the alarms are disabled. To return to START
condition, one of following events is required:
- switching off and on the controller
- activation of the digital input if the relative parameter is
s t./S t.
- by pressure SET button if par. 286 s.k.s.f. set on
s t./S t.
- START by serial commad on word modbus 1214).
7.7 Automatic / Manual regulation for % output control
This function allows to switch from automatic functioning to manual command of the output
percentage.
With par. 48 A . m a .1 . it is possible to select two modes.
1 First selection (enab.) allows to enable with FNC the writing p.--- on display 1, while on display 2 is
showed autom.
Press SET to visualize manu.; it’s now possible, during the process visualization, modify through the
keys
c
and
d
the output percentage. To back to automatic, with the same procedure, select autom.
on display 2: immediately led MAN switches off and functioning backs to automatic.
2 Second selection (en.sto.) enables the same functioning but with two important variants:
• If there is a temporary power failure or after switch-off, the manual functioning as well as the
previous output percentage value will be maintained at restarting.
• If the sensor breaks during automatic functioning, the controller switches to manual mode while
maintaining the output percentage command unchanged as generated by the PID immediately
before breakage.
Ex: on an extruder the command in percentage of the resistance (load) is maintained also in case of
input sensor failure.

15 - URDR001A - User manual
7.8 Heater Break Alarm on CT (Current Transformer)
This function allows to measure load current to manage an alarm during a malfunctioning with power
in short circuit, always open or partial break of the charge. To enable this function set 50 H z or 60 Hz on
par. 287 ct F. and the value of the connected transfomer, on par. 288 ct v ..
• Select on par. 290 H.b.a.t. the Heater Break Alarm intervention threshold in Ampere.
• Select on par. 291 o cu. t. the intervention threshold in Ampere to control the overcurrent.
• Select on par. 292 H.b.a.d. the delay time in seconds for the Heater Break Alarm intervention.
• It is possible to associate an alarm, selecting H.b.a. on par. 123 a L .1 . F. on par. 141 a L. 2.F. or par. 159 a L . 3 . F.
or par. 177 a L.4 . F. or par. 195 a L. 5 . F. .
It is possible to visualize on display 2 the average current, selecting AMPEr. on par. 278 vi . d . 2.
Selecting 0 on par. 290 H. b .A. t. it is possible to visualize the current consumption without generating
an Heater Break Alarm.
7.9 Dual Action (Heating-Cooling)
DRR244 is suitable also for systems requiring a combined heating-cooling action.
The command output has to be configured as PID for Heating (Par. 38 a c . t .1 = Heat and P. b . 1 greater
than 0), and one of the alarms (A L .1 . F. , AL. 2. f. , AL.3. f. , A L.4 . f . , AL.5. f.) has to be configured as c o o L.
The command output must be connected to the actuator responsible for heating, while the alarm will
control cooling action.
Parameters to be configured for the heating PID are:
a c . t .1 = Heat Command output action type (Heating);
P. b . 1: Heating proportional band;
i . t. 1: Integral time of heating and cooling;
d . t. 1: Derivative time of heating and cooling;
c. t. 1: Heating time cycle.
Parameters to be configured for the cooling PID related to regulation loop 1 and alarm 1 are:
A L .1 . F. = co o L. Alarm 1 selection (Cooling);
p.b.m.1: Proportional band multiplier;
o.d.b.1: Overlapping / Dead band;
c. c. t.1: Cooling time cycle.
Par. p.b.m.1 (that ranges from 1.00 to 5.00) determines the proportional band of
cooling action basing on the formula:
Proportional band for cooling action = p. b. 1 x p.b.m.1.
This gives a proportional band for cooling which will be the same as heating band if p.b.m.1 = 1.00, or 5
times greater if p.b.m.1 = 5.00.
Integral and derivative time are the same for both actions.
Par. o.d.b.1 determines the percentage overlapping between the two actions. For systems in which
the heating output and cooling output must never be simultaneously active a Dead Band (o.d.b.1 ≤ 0),
must be configured, vice versa you can configure an overlapping (o.d.b.1 > 0).
The following figure shows an example of dual action PID (heating-cooling) with i. t. 1 = 0 e d . t. 1 = 0.
1
ACTIVE
ACTIVE
SPV
PV
x = COOL
x = COOL
x = COOL
< 0
= 0
> 0
(HEAT)
(HEAT)
(HEAT)
COMMAND OUTPUT (HEAT)
ALARM OUTPUT (COOL)
COMMAND OUTPUT (HEAT)
ALARM OUTPUT (COOL)
COMMAND OUTPUT (HEAT)
ALARM OUTPUT (COOL)
SPV
PV
ACTIVE
ACTIVE
SPV
PV
ACTIVE
ACTIVE

16 - URDR001A - User manual
2
ACTIVE
ACTIVE
SPV
PV
x = COOL
x = COOL
x = COOL
< 0
= 0
> 0
(HEAT)
(HEAT)
(HEAT)
COMMAND OUTPUT (HEAT)
ALARM OUTPUT (COOL)
COMMAND OUTPUT (HEAT)
ALARM OUTPUT (COOL)
COMMAND OUTPUT (HEAT)
ALARM OUTPUT (COOL)
SPV
PV
ACTIVE
ACTIVE
SPV
PV
ACTIVE
ACTIVE
3
ACTIVE
ACTIVE
SPV
PV
x = COOL
x = COOL
x = COOL
< 0
= 0
> 0
(HEAT)
(HEAT)
(HEAT)
COMMAND OUTPUT (HEAT)
ALARM OUTPUT (COOL)
COMMAND OUTPUT (HEAT)
ALARM OUTPUT (COOL)
COMMAND OUTPUT (HEAT)
ALARM OUTPUT (COOL)
SPV
PV
ACTIVE
ACTIVE
SPV
PV
ACTIVE
ACTIVE
Parameter c. c.T.1 has the same meaning of cycle time for heating action c. t. 1.
Parameter c o . f .1 (Cooling Fluid) pre-selects the proportional band multiplier p.b.m.1 and the cooling PID
cycle time c. c.T.1 according to cooling fluid type:
c o . f .1
Cooling fluid type
p.b.m.1 c. c. t.1
Ai r Air 1.00 10
oi L Oil 1.25 4
H2o Water 2.50 2
Once parameter c o . f .1 has been selected, the parameters p.b.m.1, o.d.b.1 and c. c.T.1 can be however
modified.
7.10 LATCH ON Function
For use with input pot. and with linear input (0..10 V, 0..40 mV, 0/4..20 mA) it is possible to associate start
value of the scale (par. 4 L.L.i .1) to the minimum position of the sensor and value of the scale end (par. 5
u.L.i.1) to the maximum position of the sensor (par. 10 L t c .1 configured as stndr).
It is also possible to fix the point in which the controller will display 0 (however keeping the scale range
between L.L.i .1 and u.L.i. 1using the
“virtual zero”
option by selectin u.0.sto. or u.0.t.on. on par. 10 L t c .1 .
Selecting u.0.t.on. the virtual zero must be reset at each switching on; selecting u.0.sto. the virtual zero
will remain fixed once calibrated. To use the LATCH ON function, configure the par. L t c .1 1
Then refer to the following table for the calibration procedure:
Press Display Do
1FNC Exit parameters configuration. Display 2
visualizes writing La t c.
Place the sensor on minimum operating
value (corresponding to L.L.i .1)
2
Store value on minimum.
Display shows Lo w .
Place sensor on maximum operating value
(corresponding to u.L.i.1).
3
Store value on max.
Display shows Hi G h .
To exit standard proceeding press SET.
For
“virtual zero”
setting, place the sensor to
zero point.
4FNC
Set virtual zero. Display shows zero .
If
“Virtual zero at start”
is selected, point 4
must be repeated at each starting.
To exit procedure press SET.
1 The tuning procedure starts by exiting the configuration after changing the parameter.

17 - URDR001A - User manual
7.11 Soft-Start Function
DRR244 is provided with two types of softstart selectable on parameter 264 SS. tY. (
“Softstart Type”
).
1 First selection (GrA d .) enables gradient softstart. AAt starting the controller reaches setpoint basing
on the rising gradient set on parameter 266 SS. G r. (
“Softstart Gradient”
) in Unit/hour (ex. °C/h). If
parameter 269 SS . ti . (
“Softstart Time”
) is different to 0, at starting when the time selected on par.
269 is elapsed, the controller stops to follow the gradient and reaches setpoint with the maximum
power.
2 Second selection (PErc.) enables output percentage softstart. On par. 268 SS. tH. it is possible to set
the threshold under which starts the softstart (
“Softstart Threshold”
). On par. 267 SS.PE. (
“Softstart
Percentage”
) an output percentage is selectable (from 0 to 100), which controller keeps until the
process exceeds the threshold set on par. 268 or until the time in minutes set on par. 269 S S . ti .
(
“Softstart Time”
word 2084).
If the Sof-Start function is active the automatic/manual Tuning function cannot be activated.
7.12 Pre-Programmed cycle
Pre-programmed cycle function activates by setting
Enab.
on parameter 263 p r. cY. .
Controller reaches setpoint 1 basing on the gradient set on parameter 266 SS .G r. , then it reaches max.
power up to setpoint 2. When the process reaches max. power, this setpoint is maintained for the time
set on parameter 270 m a . t.i . .
At expiry, process will reach ambient temperature according to gradient entered on parameter 271
f a . G r. , then command output will be disabled and display will visualize Sto p.
Setpoint
Time
Setpoint 1
Setpoint 2
Maintenance time
Mantenimento
Cooling
RareddamentoMax Power
Max Potenza
Rising gradient
Gradiente di salita
Cycle starts at each activation of the controller,
or via digital input if it is enabled for this type of
functioning (parameters 231, 239 set as
st./s t.
or
rUn
).
7.13 Retransmission function on analogue output
If not used as command, the analogue output can be used to retransmit process/ setpoint/ current
read by the C.T. input/ output percentage.
Select on parameter 298 r t M .1 (“Retransmission 1”) the value to be retransmitted and on parameter 299
r.1 . t Y . (“Retransmission 1 Type”) the output type.
It is possible also to select on parameters 300 r.1.L.L. and 301 r.1 . u . L . the input value rescale limits.

18 - URDR001A - User manual
7.14 Timer functions
The DRR244 integrates two timers that can be independent, sequential or looped together.
Timer 1 is enabled on parameter 328 t m r .1 . ; timer 2 on parameter 331 t m r. 2. :
EN AB.
the timer starts from the keyboard or digital input (user intervention is required)
EN.StA.
the timer starts counting when the regulator is in RUN.
The timer time-base set in mm.ss or hh.mm by changing parameters 329 t.b. t.1 for timer 1 and 332 t.b.t.2
for timer 2.
In parameter 334 tM r.S. can be define whether the timers should be independent or related to each
other.
Sin G L.
The timers work independently of each other.
S e Q u e.
When timer 1 ends, timer 2 starts. The sequence is active only by starting timer 1. When
timer 2 expires, the sequence is interrupted.
LooP
When a timer ends, another starts: the sequence repeats itself cyclically.
To change the duration of the counting time, follow the steps below:
Press Display Do
1SET Press until ti mE 1 or ti m e 2 visualized on
display 1.
2
Digits on display 1 changes. Increase or decrease time value for the
selected timer.
To start the keyboard count follow the steps below:
Press Display Do
1FNC
Press until ti m e 1 or ti m e 2 visualized on
display 2. Display 1 shows STOP if the
timer is stopped, otherwise it shows the
remaining time.
2SET The timer stops if active or starts counting
if in STOP.
Start/Stop of Timer is possibile also by digital input (see parameters d . i .1 . F ... d .i .4 . F. .)
The alarm outputs can be associated with the timers (parameters A L .1 . F .... A L . 5 . F. ). On parameters 330
A. tM.1 and 333 A. tM.2 is possible to select the activation mode. The proposed solutions are as follows:
Start
Alarm active during timer counting
End
Alarm active when the timer expiry
W A r n.
Alarm active 5 “ before the timer expiry

19 - URDR001A - User manual
8 Serial communication
URDR001A is equipped with RS485 and can receive/broadcast data via serial communication using
MODBUS RTU protocol. The device can only be configured as a Slave. This function enables the control
of multiple controllers connected to a supervisory system / SCADA.
Each controller responds to a Master query only if the query contains the same address as parameter
318 sL. a d . (
“Slave Address”
).
The addresses permitted range from 1 to 254 and there must not be controllers with the same address
on the same line.
Address 255 can be used by the Master to communicate with all the connected equipment (broadcast
mode), while with 0 all the devices receive the command, but no response is expected.
The baud rate is selected on parameter 319 bd . rt. (
“Baud Rate”
).
DRR244 can introduce a delay (in milliseconds) of the response to the master request. This delay must
be set on parameter 321 se. d e. (
“Serial Delay”
).
Each parameter modification is saved by the controller in the EEPROM memory (100000 writing cycles),
while the setpoints are saved with a delay of 10 seconds after the last modification.
Changes made to words that are different from those reported in the following table can lead to
malfunction.
Modbus RTU protocol features
Baud-rate
Selectable on parameter 319 bd . rt.
1200bit/s 28800bit/s
2400bit/s 38400bit/s
4800bit/s 57600bit/s
9600bit/s 115200bit/s
19200bit/s
Format
Selectable on parameter 320 s. p. p.
8N1 8N2
8E1 8E2
8O1 8O2
Supported
functions
WORD READING (max 50 word) (0x03, 0x04)
SINGLE WORD WRITING (0x06)
MULTIPLE WORDS WRITING (max 50 word) (0x10)
Here below a list of all available addresses and supported functions:
RO = Read Only R/W = Read/Write WO = Write Only
Modbus
address Description Read
Write
Reset
value
0Device type RO 474
1Software version RO Flash
2Boot version RO Flash
3 Slave Address RO Eepr/dip
6Baud rate RO Eepr/dip
50 Slave address automatic learning WO -
51 System code comparison for slave address automatic learning WO -
500 Loading default values (write 9999) RW 0
501 Restart DRR244 (write 9999) RW 0
502 Setpoint storing delay time RW 10
503 Parameters storing delay time RW 1
701 First character of the custom alarm message 1 RW “u“
...
723 Last character of the custom alarm message 1 RW 0
751 First character of the custom alarm message 2 RW “u“
...

20 - URDR001A - User manual
Modbus
address Description Read
Write
Reset
value
773 Last character of the custom alarm message 2 RW 0
801 First character of the custom alarm message 3 RW “u“
...
823 Last character of the custom alarm message 3 RW 0
851 First character of the custom alarm message 4 RW “u“
...
873 Last character of the custom alarm message 4 RW 0
901 First character of the custom alarm message 5 RW “u“
...
923 Last character of the custom alarm message 5 RW 0
951 First character of the custom alarm message 6 RW “u“
...
973 Last character of the custom alarm message 6 RW 0
1000 AI1 value (degrees with tenth) RO -
1006 Real setpoint (gradient) of the regulation loop 1 RO 0
1008
Alarms status (0=absent, 1=present)
Bit0 = Alarm 1 Bit3 = Alarm 4
Bit1 = Alarm 2 Bit4 = Alarm 5
Bit2 = Alarm 3 Bit5 = Alarm 6
RO 0
1009
Error flags 1
Bit0 = AI1 process error (sensor 1)
Bit1 = Reserved
Bit2 = Cold junction error
Bit3 = Safety error
Bit4 = Generic error
Bit5 = Hardware error
Bit6 = Error H.B.A. (partial rupture of the load)
Bit7 = Error H.B.A. (SSR in short circuit)
Bit8 = Overcurrent error
Bit9 = Parameters out of range error
Bit10= CPU eeprom writing error
Bit11= RFid eeprom writing error
Bit12= CPU eeprom reading error
Bit13= RFid eeprom reading error
Bit14= Eeprom calibrations bench corrupted
Bit15= Eeprom constants bench corrupted
RO 0
1010
Error flags 2
Bit0 = Missing calibrations error
Bit1 = Eeprom CPU bench parameters corrupted
Bit2 = Eeprom CPU setpoint bench corrupted
Bit3 = RFid memory not formatted
RO 0
1011
Digital inputs status (0=not active, 1=active)
Bit0 = Digital inp. 1
Bit1 = Digital inp. 2
RO 0
1012
Outputs status (0=off, 1=on)
Bit 0 = Q1 Bit 3 = DO1
Bit 1 = Q2 Bit 4 = DO2
Bit 2 = Q3
RO 0
Table of contents
Other Wachendorff Controllers manuals
Popular Controllers manuals by other brands
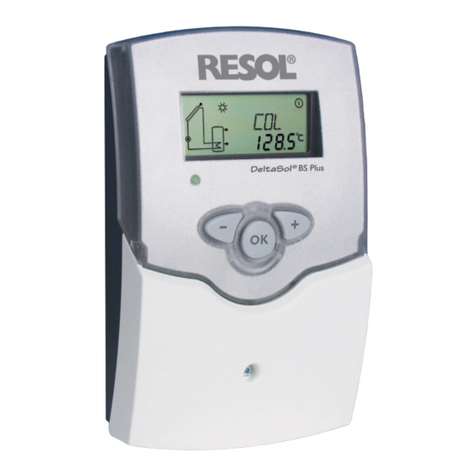
Resol
Resol DeltaSol BS Plus manual
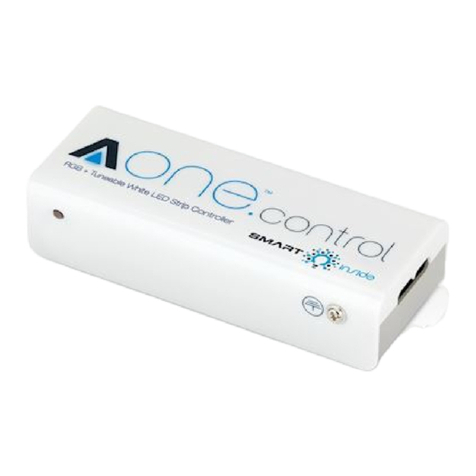
Aurora
Aurora AU-A1ZBSCRGBCX quick start guide
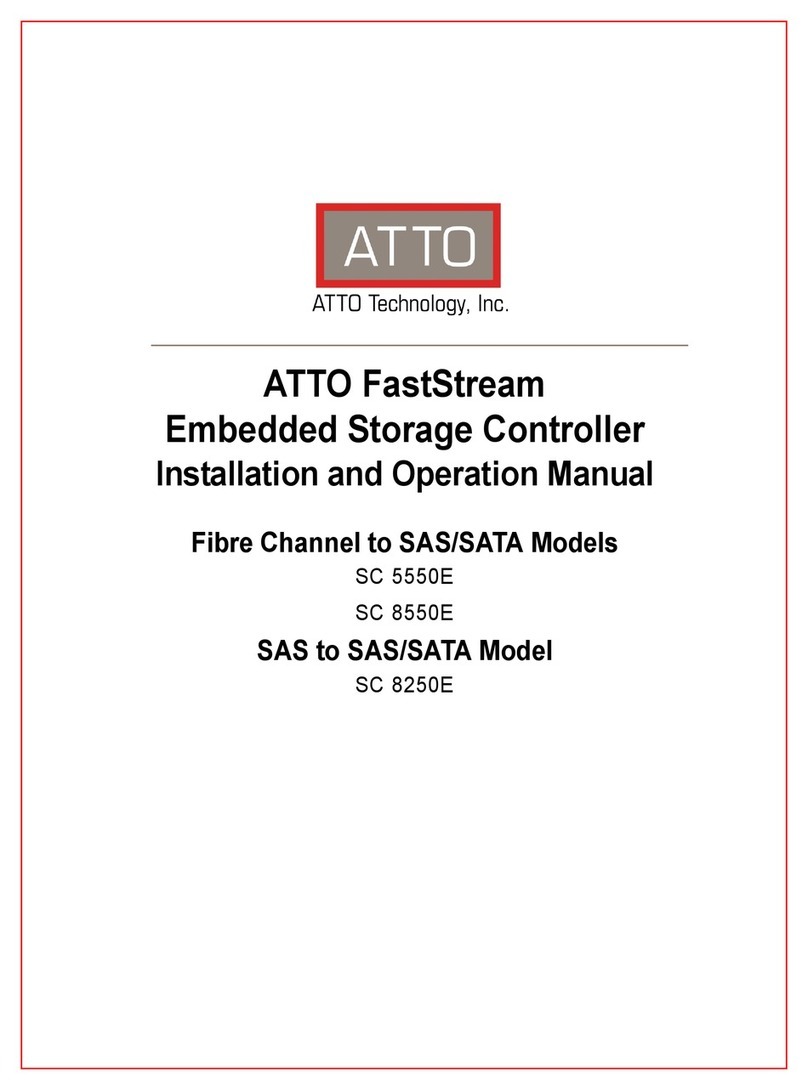
ATTO Technology
ATTO Technology SC 5550E Installation and operation manual
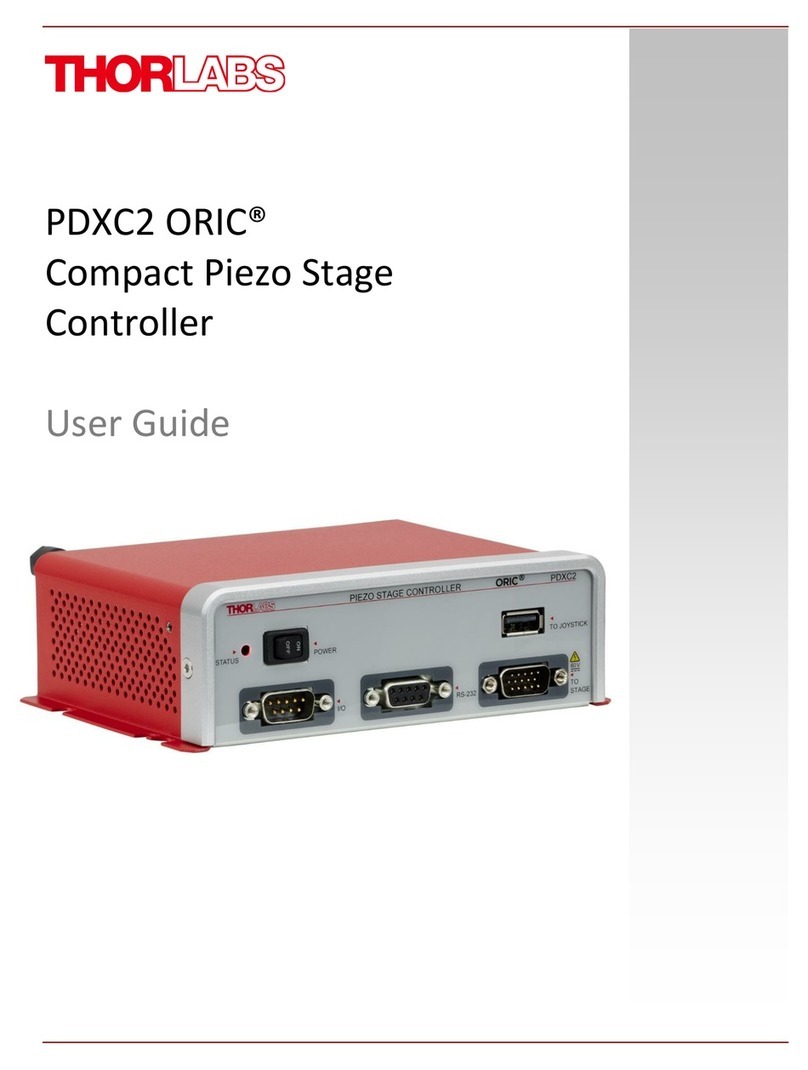
THORLABS
THORLABS ORIC PDXC2 user guide
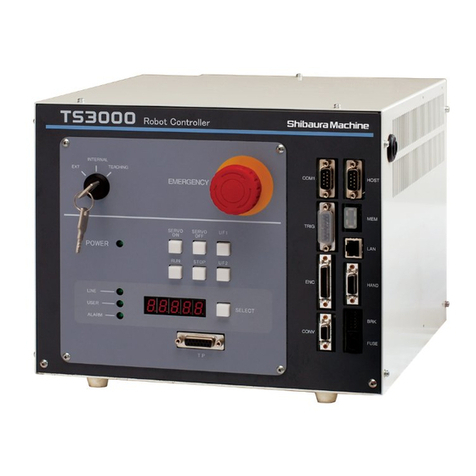
Toshiba
Toshiba TS3000 Series instruction manual
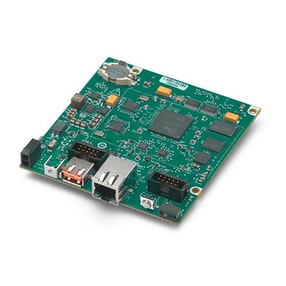
National Instruments
National Instruments sbRIO-9607 user manual