WASSON-ECE Instrumentation Restek TO-Clean User manual

TO-Clean
Manual
WSN: XXXXX
101 Rome Ct.
Fort Collins, CO 80524
Phone #: (970) 221-9179
Fax #: (970) 221-9364

©Copyright 2010 by Wasson ECE Instrumentation, Inc. (MG 08/10)
All rights reserved worldwide
Printed in the United States of America
This publication is protected by federal copyright law. No part of this publication
may be copied or distributed, transmitted, transcribed, stored in a retrieval
system, or transmitted into any human or computer language, in any form or by
any means electronic, mechanical, magnetic, manual or otherwise, or disclosed
to third parties without the express written permission of Wasson-ECE
Instrumentation, Inc., 101 Rome Court, Fort Collins, CO 80524.
DISCLAIMER OF WARRANTY AND LIMITED WARRANTY
This publication is provided “as is” without warranty of any kind. Wasson-ECE
Instrumentation, Inc. does not warrant, guarantee, or make any representation
regarding the use, or the results of the use, of this publication in terms of
correctness, accuracy, reliability, currentness, or otherwise. Further, Wasson-
ECE Instrumentation, Inc. reserves the right to review this publication and to
make changes from time to time in the content herein without obligation of
Wasson-ECE Instrumentation, Inc., to notify any person or organization of such
revision or changes.
Note to the end user.
This manual should be read in its entirety, prior to use of the applicated
instrument. Once read, please follow the instructions in the “getting started”
section of the manual in setting gas pressures and supplying appropriate power
to the gas chromatograph.

Table of Contents
Table of Contents
Instrument Description ........................................................................... 1
Product Features............................................................................................... 1
Initial Setup.............................................................................................. 2
Gas Supply........................................................................................................ 2
Pack List............................................................................................................ 2
Power Requirements......................................................................................... 3
Hardware Description and Assembly .................................................... 4
Vacuum Pump................................................................................................... 4
Dewar................................................................................................................ 5
Humidification Chamber.................................................................................... 7
Vacuum Valve Assembly .................................................................................. 9
Controller Box ................................................................................................. 10
Plumbing Diagram........................................................................................... 12
Operation................................................................................................ 13
Setting the Oven Temperature – Watlow 988 Series Control ......................... 13
Setting your Watlow Parameters..............................................................................13
Connecting the Canisters................................................................................ 16
Connecting 1 Liter Canisters ....................................................................................16
Software Control ............................................................................................. 16
Method Configuration ...............................................................................................17
Canister Cleaning ..................................................................................................... 20

Table of Contents
Diagnostics ............................................................................................................... 22
Maintenance........................................................................................... 25
Vacuum Pump................................................................................................. 25
Dewar U-Tube Traps....................................................................................... 27
Replacement Parts ................................................................................ 28
Warranty Statement............................................................................... 29
CE Certification – Declaration of Conformity...................................... 30

Instrument Description
1
Instrument Description
TO-Clean is a revolutionary canister cleaning system developed by Wasson-ECE
Instrumentation. The TO-Clean canister cleaner allows for fully automated
canister cleaning. The TO-14/15 compliant TO-Clean system was designed to
take the guess work out of canister cleaning. The twelve 6-liter canister capacity
will increase your lab’s efficiency. The system is fully automated, allowing the
user to start a cleaning cycle and walk away. Using the touch screen controller,
up to ten custom methods can be defined and loaded as needed. The system
also comes with an automated leak check method to ensure system
performance. This provides a high performance system that is easy to use as
well as consistent.
An on-board touch screen embedded controller makes system operation as easy
as pressing start. The controller allows the user to save up to ten different
methods. The user can define each method including: number of cycles,
pressure, and soak times. Once the method has been defined, it is saved and is
accessible for later use.
Product Features
•EPA Method TO-14/15 compliant
•12 canister capacity, expandable to 24 one liter canisters
•Embedded touch screen controller
•30 mTorr vacuum for 12, 6-liter canisters
•Automated system leak test
•Electronic valve control
•Custom-built trays for different canister sizes
•User defined methods
•Save up to ten methods
•Isothermal oven, controllable to 110°C
•Edwards RV-8 vacuum pump

Initial Setup
2
Initial Setup
Gas Supply
Connect all gas lines to the proper fittings, as described in the Hardware section.
Gas bottle regulators should be high quality two stage regulators. Set the gas
bottle pressures leading to the TO-Clean to the following gas pressures:
Gas Minimum Quality Maximum
Set Pressure
Nitrogen Ultra High Purity 60 psig
Valve actuation requires approximately 55 psig dry instrument air or nitrogen.
Industrial compressed “house air” is usually inadequate for valve actuation
without additional treatment. Water and particulates can damage the actuators.
Connect gases as described in the Hardware Description section.
Pack List
Unpack and inspect the system for any damage that may have been incurred
during shipment. Ensure that all of the items found in the pack list are present.
Table 1 lists the items that should be present with your order. This list may vary
depending on your order. Check the shipping pack list which is shipped with the
instrument for a more accurate description of what was shipped with your order.
If there is a variance between your shipped pack list and your order please
contact our shipping department at 970-221-9179 to reconcile these differences.

Initial Setup
3
Table 1: Pack List
Quantity Item Restek
PN Wasson-
ECE PN Check
1 TO-Clean Canister Cleaner (120V, 60Hz) 22916 A3000-120
0 TO-Clean Canister Cleaner (220/230V,
50/60Hz) 22917 A3000-220
1 Power Cord for Pump 1225
1 Bag - ¼“ nuts with caps, qty 12 12910-001
1 Bag - ¼“ vespel ferrules, qty 12 1499
1 Oven Cart 22919 25568-030 (Optional)
1 Humidifier 24282 25568-021 (Optional)
1 Wasson-ECE manual XXXXX
1 Edwards RV-8 Vacuum pump 70218
1 Dewar, Pyrex Brand Glass, 4300 mL 22918 25568-022 (Optional)
1 ½” Stainless Steel U-tube, TO Clean,
vacuum trap A2552-004
1 1/8” Stainless Steel U-tube, TO Clean
pressure trap A2552-002
1 TO-Clean Power cord 1225
1 1/8” Stainless Steel Tubing – 12 ft S0122
1 PVC Vacuum Tubing – 6 ft 25574-003
1 PVC Vacuum Tubing – 3 ft 25574-003
1 Edwards Oil, 1 quart 70487
1 Edwards Oil Mist Filter 70219
1 1L Option, tubing, fittings, and inserts for
24-1L canisters 22920 A3000-001 (Optional)
1 Watlow User Manual CD
Power Requirements
The TO-Clean system and vacuum pump are configured for 120VAC/60
hertz. The TO-Clean requires one dedicated 20-amp circuit and the
vacuum pump requires a 15-amp circuit.

Hardware Description and Assembly
4
Hardware Description and Assembly
Place the TO-Clean on a bench top or on the optional system cart.
Vacuum Pump
The TO-Clean comes with an Edwards BOC RV-8 vacuum pump. Unpack the
pump and place it on the floor next to the canister cleaner. Attach the vacuum
hose to the top of the pump, using the metal clamp, as shown in Figure 1.
The oil mist filter and oil ballast have been pre-assembled at the factory and are
connected by a short piece of tubing. Unscrew the gray oil ballast cap and screw
the oil ballast into the threaded hole until tight. Remove the clear cap from the
black mist filter fitting on the pump. Place the oil mist filter on top of the black
fitting and secure using the metal clamp.
Unscrew the two gray oil caps on the pump and pour the oil that came with the
vacuum in either of the inlets. There is an oil level window on the back of the
vacuum. The oil reservoir should be 1/3 – 1/2 full. You should not need the
entire bottle for the first fill. Screw the oil caps back on before turning the pump
on.
For further information on the Edwards pump see the manual and CD included in
the shipment.

Hardware Description and Assembly
5
Figure 1 – Vacuum Pump
Dewar
The optional Dewar houses the U-Tube where contaminants are trapped. This
cleans the nitrogen entering the system and protects the pump from
contaminants in the canisters. Connect the Dewar brackets to the right side of
the TO-Clean as shown in Figure 2. Slide the Dewar into the brackets and place
both the vacuum and nitrogen U-tubes into the Dewar along with the provided
insulating cap.
Figure 2 - Dewar Bracket
Oil Mist Filter
Mist Filter
Fitting
Oil Ballast
Vacuum Hose
to Dewar U-
Tube
Oil Caps
Dewar
Brackets

Hardware Description and Assembly
6
Attach the vacuum hose from the pump to the Dewar U-Tube using the metal
clamp, as shown in Figure 3. Attach the vacuum hose which goes to the valve
assembly to the other side of the Dewar U-Tube using the metal clamp.
Figure 3 - Dewar Vacuum Hose Connections
Connect the 1/8” line from the compressed nitrogen regulator to the 1/8” Dewar
U-tube fitting as shown in Figure 4. Connect the other side of the 1/8” Dewar U-
Tube line to the bottom of the humidification chamber, described in the next
section. Once the system has been assembled, leak checked, and is ready to
run, the Dewar can be filled with liquid nitrogen or liquid argon. The user should
be able to lift the insulating lid with all the Dewar connections intact.
Vacuum Hose
to Valve
Assembly
Vacuum
Hose to
Pump

Hardware Description and Assembly
7
Figure 4 - Dewar with Nitrogen Charge Gas Connection
Humidification Chamber
The optional humidification chamber is filled with water and humidifies the
nitrogen entering the canisters. This aids in removing volatile organic compounds
from the canisters. If the humidification chamber was shipped separately, it will
need to be attached to the ¼” fittings on the humidifier bracket, shown in Figure
5. If not already connected, attach the 1/8” nitrogen charge gas tubing from the
Dewar to the bottom bracket. Attach the 1/8” tubing on the top bracket to the 1/8”
Nitrogen or
charge gas
through Dewar

Hardware Description and Assembly
8
bulkhead labeled “UHP Nitrogen” on the back of the controller box, shown in
Figure 7.
Figure 5 - Humidification Chamber
Note:
The maximum pressure of the humidification chamber is 90 psig.
To “UHP N2”
bulkhead on back
of controller box
Humidification
Chamber
Humidification
Chamber
Bracket
Connections
To Dewar Nitrogen or
Charge gas 1/8”
fitting

Hardware Description and Assembly
9
Vacuum Valve Assembly
The vacuum valve assembly is located at the back of the TO-Clean and consists
of the vacuum valve and tee fitting, shown in Figure 6. Attach the vacuum valve
hose assembly from the Dewar U-Tube to the bottom of the vacuum valve. If not
already connected, attach the 1/8” vacuum valve actuation air line to the 1/8”
fitting on the vacuum valve. Attach the 1/8” nitrogen charge line from the
bulkhead labeled “To Tee Fitting”, located on the back of the controller box, to
the tee on the vacuum valve assembly.
Figure 6 - Vacuum Valve Assembly
Vacuum
Valve
Valve Actuation Air –
to bulkhead labeled
“Air or N2 – 60 psig
Max”
Nitrogen charge gas
– to bulkhead
labeled “To Tee
Fitting”
Vacuum Hose
to Dewar
U-Tube
Tee Fitting

Hardware Description and Assembly
10
Controller Box
The controller box, located at the upper right side of the TO-Clean, houses the
electrical components, including the Watlow heater controller and the touch
screen controller. Operation of these components is described in the Operation
section of this manual.
There are five 1/8” bulkheads located on the back of the controller box, shown in
Figure 8. If not already connected, attached the tubing show in Figure 6 “Valve
Actuation Air” and “Nitrogen Charge Gas” to the bulkheads labeled “Vacuum
Valve” and “To Tee Fitting”, respectively and connect tubing from the humidifier
shown in Figure 5 to the bulkhead labeled “UHP Nitrogen”.
You will need to connect actuator gas to the bulkhead labeled “Air or Nitrogen -
60 PSIG Max” and the bulkhead labeled “Purge Vent” to a proper vent location.
Figure 7 - Controller Box – Back
Troubleshooting note:
Note: If actuator gas is not attached to the bulkhead labeled “Air or Nitrogen – 60 PSI Max” at a minimum
pressure of 55 psig, the vacuum valve will not actuate.

Hardware Description and Assembly
11
Plug the power cable to the back of the control box. The power switch is located
on the back of the control box. Set the power switch to the “on” position. The fan
on the back of the controller box should start running and the heater and control
screen on the front of the controller box will turn on.

Hardware Description and Assembly
12
Plumbing Diagram
V3
V1
V2

Operation
13
Operation
Setting the Oven Temperature – Watlow 988 Series Control
The oven temperature is controlled by the Watlow controller located on the front
of the control panel. Set the controller temperature to the temperature at which
you wish to clean the canisters. To change the operating temperature, press the
[▼] or [▲] arrow keys on the Watlow controller. The lower display will show the
set temperature; the upper display will show the actual temperature. The oven’s
maximum temperature is 110°C.
The instructions for setting your Watlow parameters are described below. The set
points are also listed in Table 2. Complete information about the Watlow
controller and all default values can be found in the Watlow Series 988 Controller
User’s Manual on the CD included with the shipment.
Setting your Watlow Parameters
1. Reach the setup page by pressing both the arrow [▼] and [▲] keys at the
same time for three seconds. The lower display should read [set]. The
upper display should give you four options. Use the arrow keys [▼] or [▲]
to select between menu options: [InPt], [OtPt], and [COM].
2. Scroll to [GLbL], and hit the [Mode] key. [C_F] should show up in the lower
display, the upper display should be [ºC]. Use the [▼] or [▲] keys to
scroll through the options for the upper display.
3. Hit the [Mode] key until [rP] is shown in the lower display. Arrow through
the options for the upper display until it reads [Strt].
Note:
If you are using Restek canisters, the blue Parker valves can withstand heating to 250°C, but the gauges
on the 3-way valves can only be heated to 80°C. Please verify what type of valve/gauge is on the canister
before setting oven temperature.

Operation
14
4. Hit the [Mode] key until “rate” is in the lower display. The upper display
should read [100].
5. Hit the [Display] key to return to the main display.
6. Use the arrow keys to enter the Setup Menus again (step #1). Scroll to
[InPt] and hit the [Mode] key.
7. Keep pressing the [Mode] key until [ln 1] is in the lower display. The upper
display should show [H] (use the arrow keys to scroll through if it is not
set to [H]).
8. Press the [Mode] key until [rL1] is in the lower display. The upper display
should show [0] (use the arrow keys to scroll through if it is not set to [0]).
9. Press the [Mode] key until [rH1] is in the lower display. The upper display
should show [110] (use the arrow keys to scroll through if it is not set to
[110]).
10. Press the [Mode] key until [ln 2] is in the lower display. The upper display
should be set to [rtd].
11. Press the [Display] key to return to the main display.
12. Use the arrow keys to enter the Setup Menus again (step #1). Scroll to
[OtPt] and hit the [Mode] key.
13. Keep pressing the [Mode] key until [Ot 1] is in the lower display. The
upper display should show [Ht].
14. Press the [Mode] key until [Ot 2] is in the lower display. The upper display
should be set to [Ht].
15. Hit the [Display] key to return to the main display.
16. Press the [Mode] key until [OPer] is shown in the lower display. The upper
display should read [PidA].
17. Press the [Mode] key until [Pb2A] is shown in the lower display. The
upper display should read [0].
18. From the main display hit the Display key until [Pr 2] is shown in the lower
display. Then hit the [Mode] key until [SP 2] is shown in the lower display.
The upper display should read [300].

Operation
15
19. Hit the [Display] key to return to the main display.
Table 2: Watlow Setpoints
Setup Menu
Options
(selected with [▼]
or [▲] keys from
Main Display)
Lower Display
(selected with [Mode] key)
Upper Display
(selected with [▼] or [▲] keys)
GlbL
C_F °C
rP Strt
Rate 100
InPt
Ln 1 H
rL1 0
rH1 110
Ln 2 rtd
OtPt
Ot 1 Ht
Ot 2 Ht
Main Display
Lower Display
(selected with [Mode] key)
Upper Display
(selected with [▼] or [▲] keys)
Oper PidA
Pb2A 0
Main Display
(select with
[Display] key)
Lower Display
(selected with [Mode] key)
Upper Display
(selected with [▼] or [▲] keys)
Pr 2 SP2 300

Operation
16
Connecting the Canisters
Place the 6 liter canisters upside down in the slots in the oven shelves and
connect them to the ¼” Swagelok fittings provided with the steel flex tubing. If
there are any positions that are unused ensure that position is plugged with the
provided ¼” Swagelok plug.
Connecting 1 Liter Canisters
If you purchased the optional upgrade to 24 - 1 Liter Canister capacity, your
system will include 12 sheet metal inserts. These are removable and are
fastened to the standard rack with four screws each. The 1 liter canisters are
placed upside down over the opening in the insert. The steel flex tubing will have
a removable tee with two connections to handle double the canisters. To convert
back to 6 liter canisters, remove the metal inserts by unscrewing the 4 screws,
and remove the tees from the flex tubing lines.
Software Control
When the controller is powered on using the power switch located on the back of
the controller the user is presented with the Start Menu (Figure 8) which allows
the user to select one of three options: Configure Methods, Diagnostics, or
Clean.
Table of contents
Popular Other manuals by other brands

Aqua One
Aqua One Royale 90 Assembly instructions

Bavarian Demon
Bavarian Demon AXON Product information

Aqua Medic
Aqua Medic Mistral 50 ECO Operation manual
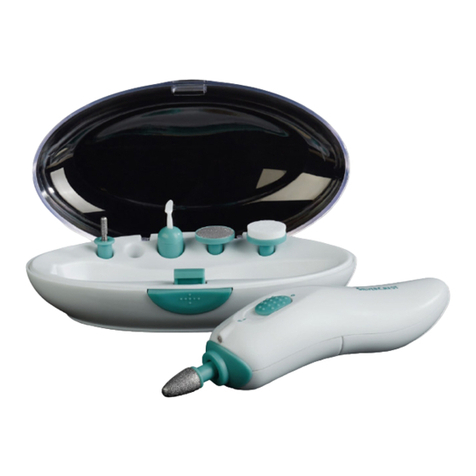
Silvercrest
Silvercrest Manicure & Pedicure Set Original instructions
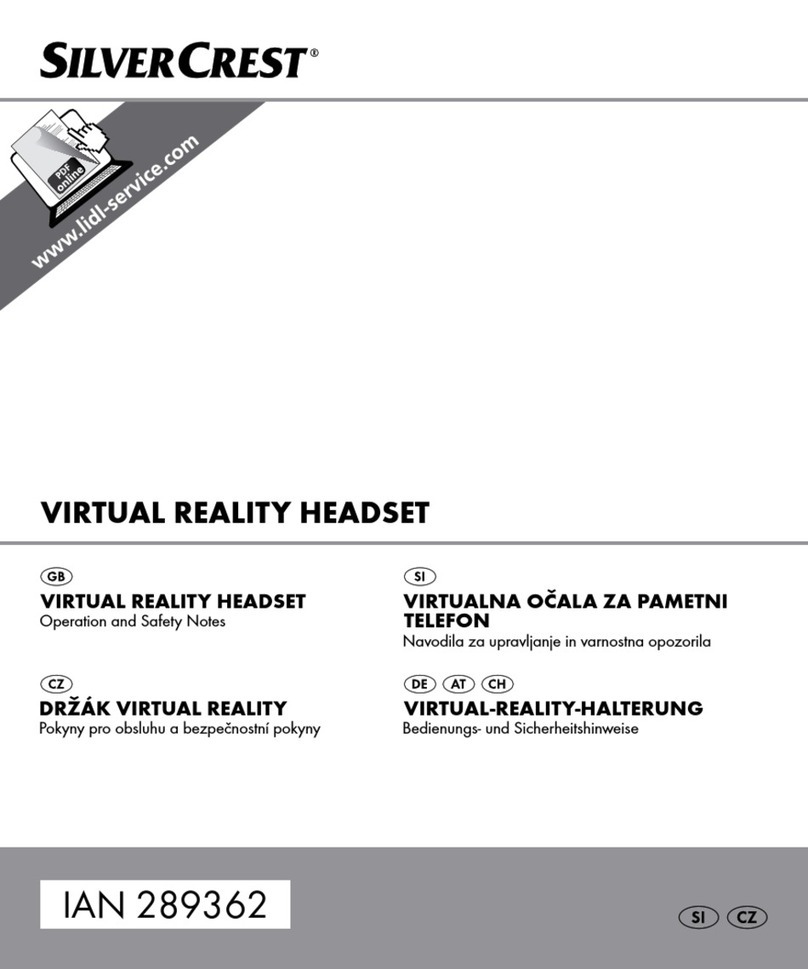
Silvercrest
Silvercrest 289362 Operation and safety notes
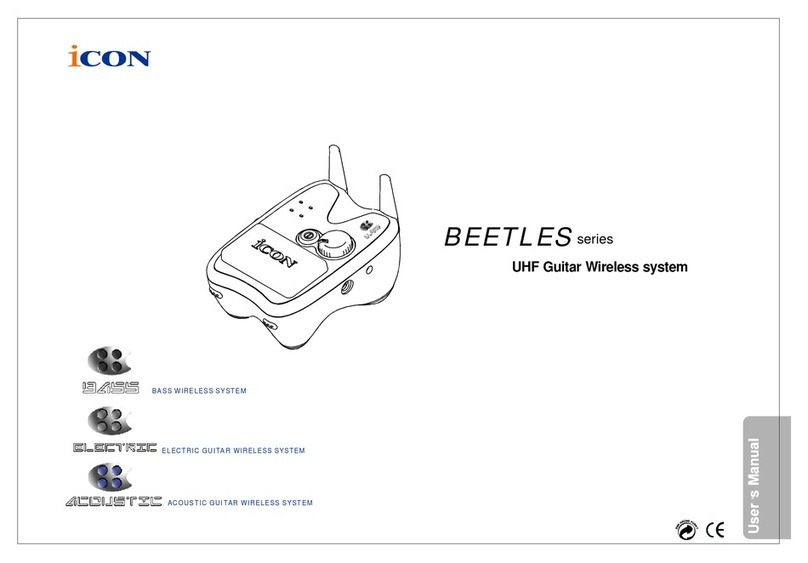
ICON
ICON BEETLES Series user manual