Water Soft ISOBAR II User manual

Greensand PlusManual
Installation / Operation Manual

2
www.watersoftinc.com
Online at
Register Your Product
General Specifications............................................................ Page 3
Installation Requirements....................................................... Page 4
Programming the Control Valve............................................... Page 7
Master Programming............................................................... Page 11
Utilizing Bluetooth................................................................... Page 12
Control Valve Powerhead Assy. ISO II & ISO III.................... Page 15
Valve Body Assembly ISO II.................................................... Page 16
Bypass Assembly ISO II........................................................... Page 18
Valve Body Assembly ISO III................................................... Page 19
Bypass Assembly ISO III.......................................................... Page 21
Service Instructions................................................................. Page 22
Troubleshooting........................................................................ Page 23
Error Codes.............................................................................. Page 24
Warranty Information............................................................... Page 25
FCC Compliance Statement:
http://www.chandlersystemsinc.com/files/FCC_Compliance_Statement.pdf
Industry Canada Compliance Statement:
http://www.chandlersystemsinc.com/files/Industry_Canada_Compliance_Statement.pdf

3
WARNING
Lubricants
Do NOT use Vaseline, oils, hydrocarbon lubricants or spray silicone anywhere! Petroleum base lubricants will cause
swelling of o-rings and seals. The use of other lubricants may attack plastic Noryl®. It is recommended that Dow
Corning® silicone grease be used as a lubricant for all control valves. Dow Corning® 7 Release Compound is used in the
manufacture of Chandler Systems control valves. (Part # LT-150)
Sealants
Pipe dope and liquid thread sealers may contain a carrier that attacks some plastic materials. It is recommended that
Teflon® tape be used to seal plastic Noryl® threaded fittings.
Greensand Plus Iron Specifications
General Specifications G9I
G9I-3
G10I
G10I-3
G12I
G12I-3
Filter Media Greensand Plus ™
Filter Media Capacity (cu ft) 1.00 1.50 2.00
Garnet Sand Underbed (lbs) 20 30 50
Mineral Tank (Vortech ™) 9 x 48 10 x 54 12 x 52
Potassium Permanganate Solution Tank Size 10 x 16
Removal Capacities Iron / Sulfur 10 ppm / 3 ppm 10 ppm / 3 ppm 10 ppm / 3 ppm
Service Flow Rate - Continous (gpm) 456
Service Flow Rate - Intermittent (gpm) 678
Backwash Flow Rate (gpm) 5.0 5.0 6.0
Gallons Used / Regeneration 128 130 173
Space Required 9 x 21 x 57 10 x 22 x 62 13 x 24 x 60
Approximate Shipping Weight (lbs) 157 215 305

4
Installation
Greensand Plus Iron Filter is capable of removing dissolved iron, manganese and hydrogen sulfide from water through
oxidation and filtration. The maximum practical limit of iron (Fe) and / manganese (Mn) in raw water is 10 ppm. The
maximum practical limit of hydrogen sulfide (h2S) is 3ppm. Raw water pH should be 6.8 to 8.8.
Manganese treated greensand works as an oxidizing filter to remove the dissolved minerals above. The manganese
oxides convert the soluble ferrous minerals in the water into ferric (or floating particles) minerals. As the ferric hydroxide
forms, it is filtered from the water by the granular material in the tank.
When the oxidizing capacity of the filter media becomes exhausted, regeneration is necessary. First the filter valve
bypasses the raw water to the system to provide uninterrupted service. The valve then reverses the flow of the water
through the filter bed to produce a backwash to the drain. Because of the density of the media bed, it is very important to
size the filter to the pump volume thus insuring adequate supply for backflushing.
The valve then brings in dissolved potassium permanganate from the small feeder tank and rinses it slowly through the
greensand media. The introduction of this oxidizing agent replaces the oxygen lost during normal service and restores the
managanese dioxide coating on the filter material renewing it for further service. A fast rinse then follows to settle the
media and insure that the chemical is rinsed away. The valve then refills the potassium permanganate tank to make solu-
tion for the next time. Service flow is downward through the filter media and up through the distributor tube in the center of
the tank.
It is recommended that the greensand media be vigorously regenerated when new and that it be regenerated before it is
exhaused while it is in service.
CITY WATER
INLET
WELL
INLET
RELIEF VALVE
MUST BE
INSTALLED
PRESSURE
TANK
WATER
METER
GREEN-
SAND
PLUS
FILTER
SOFTENER
BRINE TANK
WATER
HEATER
PRESSURE RELIEF VALVE
(To drain)
PUMP
HARD WATER
TO OUTSIDE FAUCETS
HOT SOFT WATER
COLD SOFT WATER
SERVICE
GREENSAND PLUS FILTER
(Incoming Water from Left-Side)
GROUNDED & UNSWITCHED
115- VOLT OUTLET
DRAIN LINES
DRAIN LINES
REQUIRED
4" AIR GAP
FEED POT
TANK

5
InstallationInstallation
-Installation Requirements-
Feed Pot Tank
• A level floor position between the well pump and pressure tank. (See Typical Installation Diagram.)
• DO NOT install in an area of direct sunlight or where freezing temperatures may occur!
Filter Tank
• A level floor position ahead of piping into water heater.
• Unit must be installed at least 10’ ahead of the inlet to a water heater to prevent damage due to back-up of hot water.
• DO NOT install the unit in an area of direct sunlight or where freezing temperatures may occur! (See Typical Installation
Diagram.)
-Filter Location / Other Requirements-
• Locate the unit near an unswitched, 120 volt / 60 Hz grounded electrical outlet.
• Check for distance and proper drain installation (e.g. floor drain, washing machine standpipe).
• Determine type and size of piping required for softener connection (e.g. copper, galvanized, PVC plastic).
Note: Where the drain line is elevated above the control valve or exceeds 20 feet in length to reach the drain, use 3/4”
I.D. drain line tubing of 1/2” I.D. Drain line tubing is not included.
Caution: If sweat soldering copper pipe, (remember to always use lead free solder and flux) cover yoke and bypass valve
with wet rags to prevent heat damage to connections and control valve! If using PVC or plastic pipe, primers
and solvent cements specifically recommended for use with potable water are required.
Note: All plumbing lines not requiring soft water should be connected upstream of the filter. (See Typical Installation
Diagrams.)
-Installation Procedure-
-Water Supply Connection and Bypass Valve-
To allow for filter servicing, swimming pool filling or lawn sprinkling, a manual bypass valve has been installed at the
factory. The bypass allows raw water to be manually routed around the filter.
1. Position filter at desired location for installation. If a water softener is to be installed, the filter should be positioned first
and then the softener. (See Installation Diagrams.)
2. The filter material is shipped separately from the mineral tank. The tank must be loaded with material after tank has
been placed at the desired location.
a. Remove the control valve by unscrewing from the tank.
b. Remove and inspect distributor tube and bottom basket.
c. Replace distributor tube and use cap provided to place over top of distributor tube to prevent mineral from
entering tube while filling.
d. Place mineral funnel in hole on top of tank.
e. Pour several gallons of water in the tank.
Caution: Not following this procedure can cause damage to distributor tube or basket when loading material!
f. First pour in the filter material.
Note: The required quantity of gravel is in the tank already.
g. After filling the tank with material, use a garden hose or several buckets to fill the tank with water.
Note: This will permit the filtering material to become soaked while preparing the installation and will prevent the control
valve from being plugged with floating material on initial backwash.
h. Remove funnel and clean filter material from tank threads.
i. Remove cap from distributor tube.
j. Replace control valve on mineral tank.
Caution: Be extremely careful to position distributor tube into control valve distributor tube pilot hole.
3. Turn off main water supply and open nearest faucet to relieve pressure.
4. Cut main line and install elbows and extensions.

6
Installation
Caution: Raised arrows located on the sides of control valve body and bypass valve indicate proper direction of
water flow. Install inlet and outlet piping in direction of arrows. It is recommended that a vacuum breaker be
installed on the inlet plumbing.
Bypass - Shown
5. Rotate handle on bypass valve to the bypass position (position of handle is across inlet/outlet piping).
6. Turn the main supply line on to restore water service to the home.
7. Open nearest faucet to evacuate air and repressurize plumbing lines.
8. Check for leaks!
- Drain Line Connection -
1. The drain line flow control assembly is pre-assembled for your convenience. Should you choose to hard plumb the
drain line, please remove the barb fitting. The flow control housing can be removed by removing the clip and pulling
straight out on housing.
Note: When re-installing the drain line flow control housing, be sure you hear and feel the O-Ring pop into place before
inserting the clip.
2. Install 1/2” I.D. drain line tubing (not included) from hose barb to an open drain. A 4” gap between end of the drain line
and the open drain is required to prevent waste water backflow. Keep the drain line as short as possible. An overhead
drain line can be used if necessary, but should discharge below the control valve. A syphon trap (taped loop) at the
outlet of the drain line is advisable to keep the drain line full and assure correct flow during backwash. Elbows or other
fittings must be kept at a bare minimum.
Note: Where the drain line is elevated above the control valve or exceeds 20 feet in length, 3/4” I.D. drain line tubing
should be used.
-Potassium Permanganate Feed Rate-
The amount of potassium permanganate fed during regeneration is automatically controlled by the float assembly located
inside the feed tank. This is an adjustable float, which must be set at a minimum of 4 1/4”, but not higher than 5 1/2”. This
distance is measured between the bottom of chemical feed valve and the bottom of the float with the valve closed (float
UP position). The float settings for each model are as follows:
Model # Float Setting Media Amount
G9I / -3 4 1/4” 1.0 cu. ft.
G10I / -3 4 1/2” 1.5 cu. ft.
G12I / -3 5” 2.0 cu. ft
1. To measure and set the float, remove the chemical well cap and float assembly.
2. Remove rubber band from float valve.
3. Measure distance from bottom of chemical feed valve to the bottom of float with the float in the UP position. To move
float, slide rubber grommets up and down float shaft. Make certain both upper and lower grommets are
tightly against float body. Replace float assembly and chemical well cap.
WARNING: After adjustment, ensure that the float maintains proper up and down travel, otherwise, overfilling of the feed
tank could occur!

7
Installation Installation
-Chemical Feed Line and Overflow Connections-
1. Position Potassium Permanganate Tank (KMNO4) on a smooth, level surface near the filter media tank. If necessary,
the KMNO4 tank can be placed at a higher level than the resin tank, but never at a lower level.
2. Install one end of 3/8” O.D. by 1/4” I.D. chemical line tubing (included with unit) to compression fitting located on right
side of control valve, behind backplate.
3. Remove KMNO4 tank cover.
4. Insert opposite end of chemical line through outer hole in KMNO4 tank.
5. Connect chemical line to compression fitting on float valve located on top of chemical well.
6. Install 1/2” I.D. drain line tubing (not included) to the overflow fitting on KMNO4 tank located just below the chemical
line.
7. Run the opposite end of KMNO4 tank drain line to a suitable drain.
Note: The KMNO4 tank drain is gravity flow and must discharge below the overflow fitting.
Caution: Do not tee to the main drain line from control valve.
NOTICE: The KMNO4 overflow is provided as a back-up in the event the float shut-off should fail, allowing the KMNO4
tank to overfill. This drain connection would then carry the excess chemical to the drain and prevent flooding of the floor,
which could be hazardous to health or damage furniture or carpets. Therefore, no liability will or can be assumed by the
manufacturer of the filter should this occur.
Electronic Connections
P - Power Supply
B - Powered in Backwash Step Only
(Cycle #1)
S - Powered in Entire Regeneration Cycle
P B S
- Electrical Connection -
1. Connect the power supply to the control valve and plug into a 115 volt / 60 Hz receptacle.
Note: Do not plug into an outlet controlled by a wall switch or pull chain that could inadvertently be turned off.

8
Installation
-Pressurizing The System -
2. Slowly rotate handle of the bypass valve to the SERVICE position.
3. Open the nearest faucet to evacuate air from plumbing lines.
4. Check for leaks! If water is observed leaking from bypass, o-rings on valve body may not be seated properly. Exercise
bypass valve.
5. After air is evacuated from plumbing lines, turn off faucet.
- Initial Control Valve Operation -
1. Advance control valve to BACKWASH (cycle 1) position and allow water to run to drain for 3 to 4 minutes.
Warning: Close handle on bypass prior to selecting the backwash position. After backwash position has been
established, slightly open valve on bypass to evacuate air from the media tank. Fully open bypass valve when
all air is depleted. This procedure will prevent media form being uplifted into control valve.
2. Advance control valve to RAPID RINSE (cycle 3) position and allow water to run to drain for 3 to 4 minutes.
3. Advance control valve to SERVICE (cycle 0) position.
- Final Checkout -
1. Be certain that the bypass valve is in Service position and main valve is completely on.
2. Check electrical supply to be certain the cord is connected to an uninterrupted 115 volt outlet.
3. Be sure to REGISTER YOUR PRODUCT online at www.csiwater.com
4. Leave this manual with the homeowner.
Important Notice - The plumbing system, piping, pressure tank, hot water tanks, softeners, etc. that have been exposed to
iron bearing water may need to be cleaned of the precipitated iron that has been collected in them or iron bleed thru may
be a problem. We suggest all tanks be drained and flushed thoroughly.
- Programming The Control Valve -
1. Set time of day.
2. Set a.m. or p.m.
3. Set number of days between backwash. (This generally will be every 4 to 6 days.)
1. Set regeneration time if other than 12:00 a.m. is desired.

9
Installation
Main Menu
12:00
1. To enter Main Menu, press the Menu/Enter button.
(Time of Day will flash)
2. To set the Time of Day, press the Set/Change button.
(First digit will flash) Example (12:00)
To change digit value, press the Set/Change button.
- To accept the digit value, press the Menu/Enter button.
- Next digit will flash to begin setting.
- Once the last digit display is accepted, all digits will flash.
3. To set A.M. or P.M., press the Menu/Enter button.
- To change digit value, press the Set/Change button. Example ( A )
- To accept the digit value, press the Menu/Enter button.
- Once A.M. or P.M. is accepted, the next menu item will flash.
4. a. To set the Number of Days between Backwash Cycles (A), press the Set/Change button. -
Repeat instructions from step (2). Example ( A - 06 )
Notes: 1) Maximum value is 29.
2) If value set to 0, Automatic Backwash will never occur.
3) Default setting is 6 days for filters.
5. To Exit Main Menu, press the Menu/Enter button.
Note: If no buttons are pressed for 60 seconds, the Main Menu will be exited automatically.
Programming the Control Valve
Normal Operation
1. Home Display
a. Alternates between the display of Time of Day and Number of Days until the Next Backwash. (Metered
Softeners will alternate between time of days and gallons remaining until next regeneration)
- Days Remaining until the Next Backwash will count down from the entered value until it reaches 1 day
remaining.
- A Backwash Cycle will then be initiated at the next designated regeneration time.
2. Battery Back-Up (Uses a standard 9-volt alkaline battery.)
Features of Battery Back-Up:
• During power failures, the battery will maintain the time of day as long as the battery has power. The
display is turned off to conserve battery power during this time. To confirm that the battery is working,
press either button and the display will turn on for five (5) seconds.
• If power failure occurs while system is regenerating, the Signature 2 will motor to a shut off position to
prevent constant flow to drain. Depending upon system pressure and other factors, it is possible to
observe a reduced flow to drain during this step. After power is restored, the Signature 2 will return
and finish the cycle where it left off prior to the power interruption.
• When used without battery back-up, during a power failure, the unit stops at its current point in the
regeneration position and then restarts at that point when the power is restored. The time will be offset
by the increment of time the unit was without power, so it is necessary to reset the time of day on the
unit. No other system will be affected.

10
Filters Default (Min)
Step 1 Backwash 10
Step 2 Brine Draw 60
Step 3 Rapid Rinse 10
Step 4 Refill 4
Programming the Control Valve
Starting Extra Regeneration Cycle
1. To Start Delayed Extra Cycle Example ( 1)
If Days Remaining Until Next Backwash does not read ‘1’, press and hold the
Set/Change button for 3 seconds until the display reads ‘1’.
- Backwash cycle will initiate at the next designated backwash time.
2. To start Immediate Extra Cycle First complete above step.
- With Days Remaining Until Next Regeneration at ‘1’.
- Press and hold the Set/Change button.
- After 3 seconds, the backwash cycle will begin.
3. To Fast Cycle thru regeneration First complete above 2 steps.
Note:Press and hold the Set/Change button for 3 seconds to advance to the next cycle step. Fast Cycle is not
necessary unless desired to manually step through each cycle step. (Repeat until valve returns to the
home display)

11
Master Programming Mode
Master Programming Mode
To enter Master Programming Mode, press and hold both buttons for 5 seconds.
Note: All Master Programming functions have been preset at the factory. Unless a change is desired, it is
NOT necessary to enter Master Programming Mode.
1. Regeneration Time ( r ) Example ( r 12A )
- The time of day at which backwash may take place is designated by the letter “r”.
- Default regeneration time settings is 12a
- The first display digit indicates A.M. or P.M. To change the value, press the Set/Change button.
- Press Menu/Enter button to accept the value and move to the next digit.
- The second and third display digits indicate the hour at which the backwash will occur.
- Change the digits with the Set/Change button and accept with the Menu/Enter button.
- After the entire display flashes, press the Menu/Enter button to move to the next menu item.
2. Regeneration Cycle Step Times (Steps 1, 2, 3, 4)
Example ( 3 - 10)
- The next 4 displays set the duration of time in minutes for each backwash cycle step.
- The step number which is currently modifiable is indicated on the far left of the display screen.
- The number of minutes allotted for the selected backwash step is displayed on the far right.
- Change the digit values using the Set/Change and Menu/Enter buttons as described above.
3. Bluetooth Enabled BE - 1 (ON)
BE - 0 (OFF)
4. Bluetooth Password BBPP is displayed for one second, then password is displayed.
5. To Exit the Master Programming Mode, press the Menu/Enter button until time of day returns.
Note: If no buttons are pressed for 60 seconds, the Master Programming Mode will be exited automatically.

12
For simplified set up and control, please install the Legacy View on a compatible Bluetooth 4.0+ enabled smart phone or
tablet.
1. Download and install the Legacy View app from the Google Play Store, Apple App Store
2. Open the Legacy View app
• Choose a valve device at any time from the list of available devices to connect to by clicking on it.
• If the valve you want to connect to doesn’t show up, or there is a problem connecting to a device you can
press the “Scan for Devices” button or the Legacy View logo at any time to refresh the list and start the
process over.
• If the valve device is a BTLE valve and it has a password other than the default password, the first time you
connect to it the app will ask you to enter the password. After entering it the first time you should not need to
enter it again unless it changes.
3. BTLE Valve devices can be updated by the App. When the app is updated from the Google Play Store or the Apple
App Store, it may contain an updated firmware program for the valve devices. These updates could contain new
features or operational improvements. It is up to the user to allow these updates to be sent to the valve device.
Uploading a new program takes approximately 1 minute.
Dashboard
NOTE: Consult your dealer before making any changes
From the Dashboard, all items in ORANGE can be changed, while blue fields are informational only.
If you are unsure about the function of the field click the for more information.
Utilizing Bluetooth Control

13
Utilizing Bluetooth Control Set Up Utilizing Bluetooth App
Advanced Settings
NOTE: Consult your dealer before making any changes. We do not recommend changing Advanced Settings unless you
have a good understanding of the system operation.
From the Advanced Settings, all items in ORANGE with a “set” button can be changed.
For Filters:
Set Backwash Frequency
This sets the amount of day between backwash cycles
Change Time of Day (Press “SET” to set time automatically based on device).
Set Regeneration Time
Example: For 2a.m., just type 2, choose a.m., and press ‘OK’
Note: If you have a filter and a softener the valves should be set to regenerate
at different times. Factory default times are 12a.m. for filters, and 2 a.m. for
softeners.

14
Status and History
From the Status and History, all items in ORANGE can be reset.
1. Start a regeneration or backwash cycle
Option 1: Click the “Regenerate Unit Now.”
Once a regeneration has been started, if you would like to force the unit into the
next cycle step click “Go to Next Regeneration Step”.
Option 2:
Touch any graph to enlarge and see
details. Enlarged graphs are able to
be zoomed in by pinching with two
fingers.
(Enlarged graph shown below)
“Regenerate Unit at Next Regen Time” button
This will take the system into a backwash cycle at the next regeneration time.
Set Up Utilizing Bluetooth App
Pressing the .csv logo in the corner
will allow the graph data to be
exported and shared.
Enlarged graph showing water usage
Pressing this icon will show a list of
the data that is in the graph.

15
Control Valve Powerhead Assembly
3
4
5
6
7
8
9
10
11
12
13
14
15
16
17
18
E
M
*"F" Port is for softener flow meter connection (flow meter not shown)
LETTERS IN DIAGRAM REPRESENT WIRING CONNECTIONS
19
1
E
P
P
M
F
Ref Description Part Number Qty
0 Power Head Assy. 20943C100 1
1 Softener Circuit Boad Assy. 20943C102 1
2 Encoder 20001X124 1
3 Front Plate 20001X004 1
4 Encoder Wheel 20001X007 1
5 Main Gear 21001X120 1
6 Power Supply 20001X125 1
7 Back Plate 20001X005 1
8 Lower Front Base For Cover 20111X002 1
9 Motor 20016X006 1
10 Lower Back Base for Cover 20111X003 1
11 Valve Cover 20111X001 1
12 Piston Screw 20001X003 1
13 Screw SC10 3
14 Screw SC9 2
15 Piston Washer 20001X002 1
16 Washer Circuit Board 20111X014 1
17 Screw Motor SC2 1

16
Valve Body Assy.
Ref
#Description Part # Qty.
1 Piston Assembly 20001X231 1
2 10-24 x 13/16 Screw 20001X226 3
3 Seal & Spacer Kit 20561X253 1
4 End Spacer N/S 1
Flow Control Button 5.0 GPM 20251X272 1
Flow Control Button 6.0 GPM 20251X274
Flow Control Button 7.0 GPM 20251X273 1
6 Plastic Flow Control Housing 20017X100 1
6a Flow Control Assembly – Specify GPM Incl. (1)
Flow Control Assy. 5.0 GPM-
PVC
20017X262 1
Flow Control Assy. 6.0 GPM-
PVC
20017X263 1
Flow Control Assy. 7.0 GPM-
PVC
20017X264 1
7 Drain Line Fitting
1/2” NPT X 1/2” Tubing
20017X255 1
8 Drain Retainer 20017X214 1
9 Brine Assembly 20561X225 1
10 BLFC Assembly .5 GPM 20001X228 1
Ref
#Description Part # Qty.
11 Brine Line Ferrule 20251X305 1
12 Brine Line Compression Nut N/S 1
13 10-24 X 1 Hex Screw 20001X226 1
14 Injector Cap 20001X223 1
14a Injectory Kit-Specify Size- Inc.
(1) ea #14, #15, #16, #17 &
(2) #13
20001X220 1
15 Injector Seal 20001X224 1
16 Injector Assy. Specify Size 20001X219 1
17 Injector Screen 20001X222 1
18 Injector Plug & O-Ring Assy. 20001X217 1
19 Valve O-Ring 20561X205 1
20 Dist. O-Ring 20561X204 1
Items #21 thru #24 used ONLY with Signature 2
21 Mounting Clip 20561X201 2
22 8-18 X 5/8” Screw 20561X217 2
23 Adapter Coupling N/S 2
23a Adapter Coupling & O Ring
Assy. Incl. (1) #40 & (2) # 41
20561X215 1
24 O-Ring 20561X216 4

17
Valve Body Assy. Bypass Assembly
Ref # Description Part # Qty
1Plastic Bypass Valve Assembly 20561X292 1
2
Bypass Valve 3/4” Stainless Steel 20561X270 1
Bypass Valve 1” Stainless Steel 20561X283 1
(1)
(2)

18
Valve Body Drive Assy.
2
9
1
3
13 14
12
16
17 18
19
21/22
10
11
45
6
7
6A
8
15
20

19
Valve Body Drive Assy. Valve Body Drive Assy.
Ref Description Part No. Qty
1 Piston Assembly 20001X231 1
2 10-24 X 13/16 Hex Head 20001X226 5
3 Seal and Spacer Kit 20561X253 1
4 Bottom Spacer N/S 1
5a DLFC 5.0 Button 20251X272 1
DLFC 6.0 Button 20251X274 1
DLFC 7.0 Button 20251X273 1
6a Flow Control Assembly 5.0 20017X262 1
Flow Control Assembly 6.0 20017X263 1
Flow Control Assembly 7.0 20017X264 1
6 Drain Line Flow Control Housing - Blank 20017X100 1
7 Drain Line Hose Barb, Straight 20017X255 1
8 DLFC Clip 20017X214 1
9 Brine Valve 20561X225 1
10 Brine Line Flow Control Assy. 20001X228 1
11 Brine Line Ferrule 20251X305 1
12 10-24 X 1 Hex Screw 20001X226 2
13 Injector Cover 20009X001 1
14 Injector Seal 20001X224 1
15 Injector w/ Check Ball 200017X219 1
16 Injector Screen 20001X222 1
17 Injector Plug 20001X217 1
18 Valve O-Ring 20561X205 1
19 Distributor Pilot O-Ring 20561X204 1
20 Flow Meter 20017X203 1
21/22 Valve Body Complete VH1-B-D15 1

20
Ref Description Part No.
1 D15 Bypass 20017X283
2 1” Female Straight Slip Set (optional) 20017X288
3 1” NPT Elbow Set 20017X284
4 1” NPT Straight Set (optional) 20017X289
5a Elbow, Vertical Adapter Blank (optional) 20017X295
5b Elbow, Vertical Adapter 1/4” NPT Tapped (optional) 20017X294
Other manuals for ISOBAR II
1
This manual suits for next models
1
Table of contents
Other Water Soft Control Unit manuals
Popular Control Unit manuals by other brands
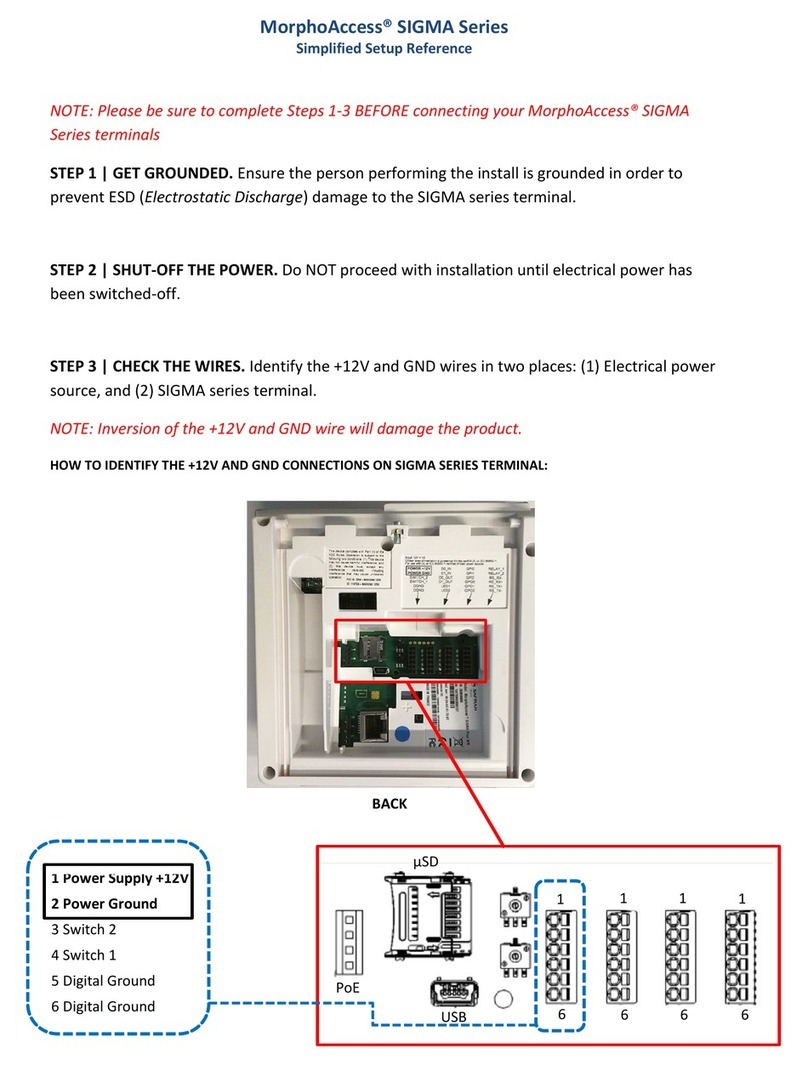
MorphoAccess
MorphoAccess SIGMA Series Simplified Setup Reference

Fluke
Fluke 80TK instruction sheet
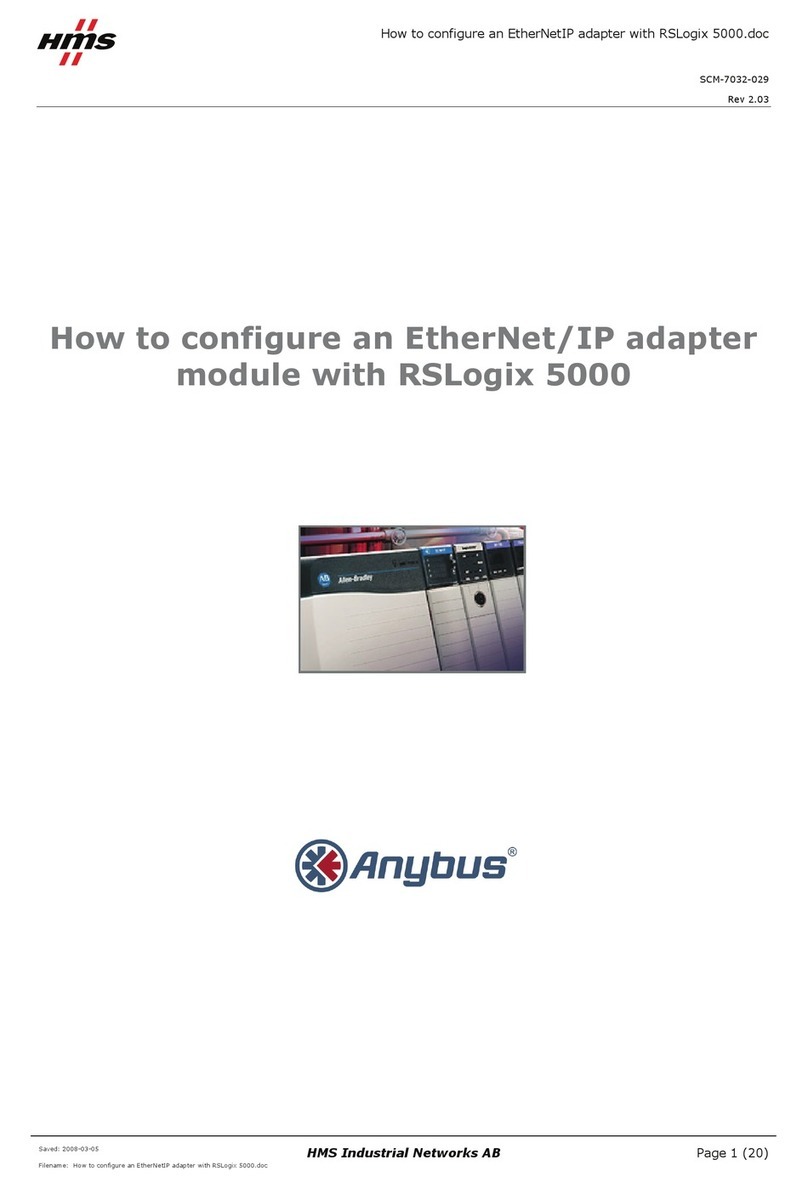
HMS
HMS Anybus EtherNet/IP How to configure
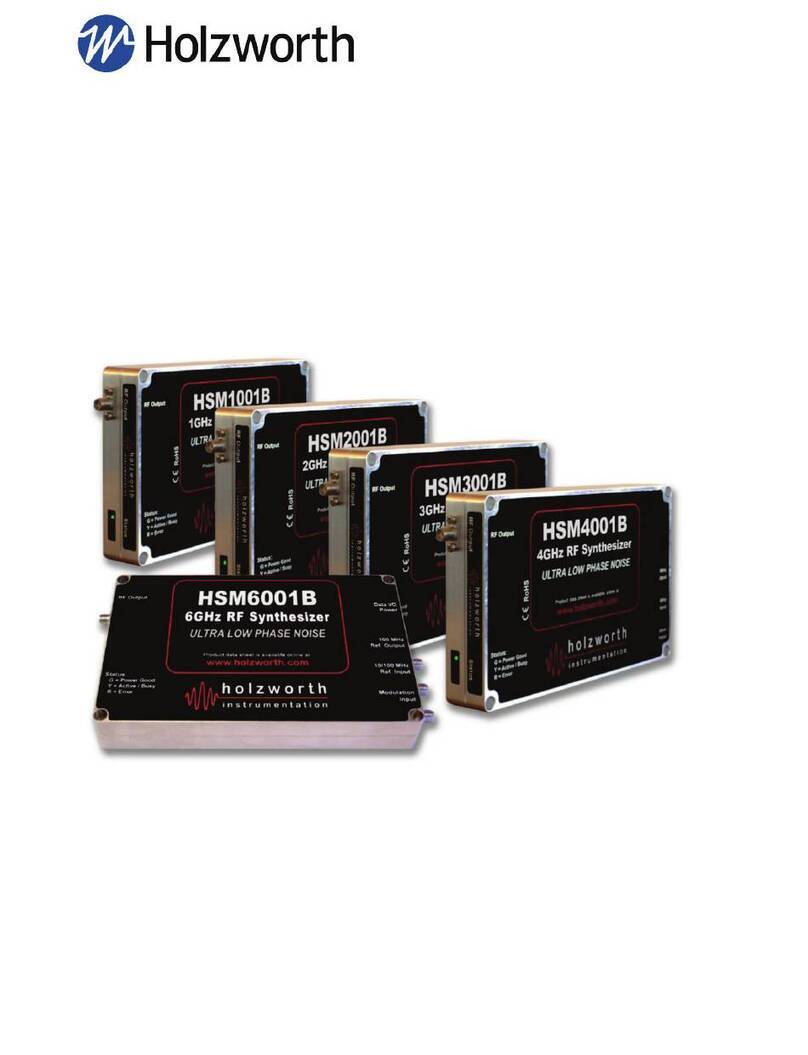
Holzworth Instrumentation
Holzworth Instrumentation HSM Series Quick start operation guide
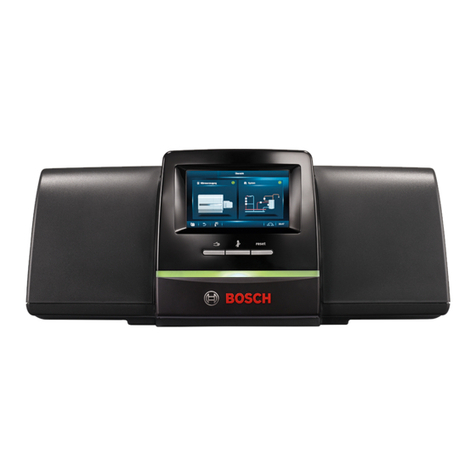
Bosch
Bosch Control 8313 Service instructions for contractors

Valcom
Valcom V-119RTHF instruction manual