Weidmuller IE-SW-VL16 Series Manual

Unmanaged Fast Ethernet Switch
ValueLine
IE-SW-VL16 Series
Hardware Installation Guide
8th Edition, March 2018
1243330000/07/04.18
Important note:
This document and additional product information can be
downloaded using following link:
http://www.weidmueller.com
►Select Product Catalogue
Select „Active Industrial Ethernet “
Select „ValueLine unmanaged Switches “
Select Product model
Click and expand section „Downloads “
Download needed software or documentation
Copyright Notice
Copyright 2018 Weidmüller Interface GmbH & Co. KG
All rights reserved.
Reproduction without permission is prohibited.

- 2 -
Overview
The IE-SW-VL16 series of 16-port smart Ethernet switches provides an
economical solution for your Ethernet connections. As a bonus, the
built-in smart alarm function helps system maintainers monitor the health
of your Ethernet network.
IE-SW-VL16 series is available with an operating temperature range of 0
to 60°C or optional with extended operating temperature range from -40
to 75°C. The devices are designed to withstand a high degree of vibration
and shock. The rugged hardware design makes IE-SW-VL16 series
perfect for ensuring that your Ethernet equipment can withstand critical
industrial applications, such as in hazardous locations (Class 1 Division
2/ Zone 2), and complies with FCC, UL and CE Standards.
ATTENTION
This device complies with part 15 of FCC Rules. Operation is
subject to the following two conditions: (1) This device may not
cause harmful interference, and (2) this device must accept
any interference received, including interference that may
cause undesired operation.
Package Checklist
Your Ethernet Switch is shipped with the following items. If any of these
items is missing or damaged, please contact your Weidmüller customer
service for assistance.
Ethernet Switch
Protective caps for unused ports
Hardware Installation Guide (printed)
Features
High Performance Network Switching Technology
10/100BaseT(X) (RJ45), 100BaseFX (SC/ST type, Multimode)
IEEE 802.3/802.3u/802.3x
Store and Forward switching process type, with 4K address entries
10/100M, Full/Half-Duplex, MDI/MDIX auto-sensing
Industrial Grade Reliablity
Power failure, port break alarm by relay output
Redundant dual DC power inputs
Broadcast storm protection to prevent network devices from crashing
Rugged Design
IP30, rugged high-strength case
DIN-Rail or panel mounting ability

- 3 -
Panel Layout
IE-SW-VL16(T)-16TX
1. Grounding screw
2. Terminal block for power input P1/P2
3. Heat dissipation orifices
4. D P Switches
5. Power input PWR1 LED
6. Power input PWR2 LED
7. Fault LED
8. 10/100BaseT(X) Port
9. TP port’s 100 Mbps LED
10. TP port’s 10 Mbps LED
11. Article number
12. Screw hole for wall mounting kit
13. D N-Rail Kit

- 4 -
Panel Layout
IE-SW-VL16(T)-14TX-2SC
1. Grounding screw
2. Terminal block for power input P1/P2
3. Heat dissipation orifices
4. D P Switches
5. Power input PWR1 LED
6. Power input PWR2 LED
7. Fault LED
8. 10/100BaseT(X) Port
9. TP port’s 100 Mbps LED
10. TP port’s 10 Mbps LED
11. Article number
12. 100BaseFX Port
13. FX port’s 100 Mbps LED
14. Screw hole for wall mounting kit
15. D N-Rail Kit

- 5 -
Panel Layout
IE-SW-VL16(T)-14TX-2ST
1. Grounding screw
2. Terminal block for power input P1/P2
3. Heat dissipation orifices
4. D P Switches
5. Power input PWR1 LED
6. Power input PWR2 LED
7. Fault LED
8. 10/100BaseT(X) Port
9. TP port’s 100 Mbps LED
10. TP port’s 10 Mbps LED
11. Article number
12. 100BaseFX Port
13. FX port’s 100 Mbps LED
14. Screw hole for wall mounting kit
15. D N-Rail Kit

- 6 -
Mounting Dimensions
Units: mm (inch)
DIN-Rail Mounting
The aluminum DIN-rail attachment plate should already be fixed to the
back panel of the Ethernet Switch when you take it out of the box. If you
need to reattach the DIN-rail attachment plate, make sure the stiff metal
spring is situated towards the top, as shown in the figures below.
STEP 1
:
Insert the top of the DIN-Rail into
the slot just below the stiff metal
spring.
STEP 2
:
The DIN-Rail attachment unit will
snap into place as shown below.
To remove the DIN-rail from the Ethernet Switch, simply reverse Steps 1
and 2.

- 7 -
Wall Mounting (optional)
For some applications, you will find it convenient to mount the Ethernet
switch on the wall, as shown in the following figures.
STEP 1: Remove the
aluminum DIN-Rail
attachment plate from the
switch rear panel, and then
attach the wall mount plates
as shown in the diagram at
the right.
STEP 2:
Mounting the switch on the wall requires 4 screws.
Use the switch, with wall mount plates attached, as a
guide to mark the correct locations of the 4 screws.
The heads of the screws should be less than 6.0 mm
in diameter, and the shafts should be less than 3.5
mm in diameter, as shown in the figure at the right.
NOTE Before tightening the screws into the wall, make sure the screw
head and shank size are suitable by inserting the screw into one
of the keyhole-shaped apertures of the wall mounting plates.
Do not screw the screws in completely—leave about 2 mm to
allow room for sliding the wall mount panel between the wall and
the screws
STEP 3:
Once the screws are fixed on the wall, insert the four screw heads
through the large parts of the keyhole-
shaped apertures, and then slide
the switch downwards, as indicated. Tighten the four screws for added
stability.
6.0 mm
3.5 mm

- 8 -
ATEX Information
Certificate number DEMKO 11 ATEX 150194X
Ambient range:
-40°C ≤Tamb ≤+75°C for models with suffix of “-T”;
0°C ≤Tamb ≤+60°C for models without suffix of “-T”
Certification string: Ex nA nC IIC T4 Gc
Rated Cable Temperature: ≧100°C
Standards covered:
EN 60079-0:2012+A11:2013, EN 60079-15:2010
The conditions of safe usage:
These devices are to be installed in an ATEX certified IP54
enclosure accessible only with use of a tool and used in an area of
not more than pollution degree 2 as defined by EN 60664-1.
Use a conductor wire of size 0.2 mm² or greater
Conductors suitable for use in an ambient temperature of 93°C
must be used for the Power Supply Terminal.
PROVISIONS SHALL BE MADE, EITHER IN EXTERNAL TO
THE APPARATUS, TO PREVENT THE RATED VOLTAGE
BEING EXCEEDED BY THE TRANSIENTS DISTURBANCES OF
MORE THAN 40 %
.
N
OTE
Suitable for use in Class I, Division 2, Groups A, B, C and D
hazardous locations, or nonhazardous locations only.
WARNING
EXPLOSION HAZARD -
Do not disconnect equipment while the
circuit is live or unless the area is known to be free of ignitable
concentrations.
WARNING
EXPLOSION HAZARD - Substitution of any component may
impair suitability for Class 1, Division 2
WARNING
EXPLOSION HAZARD – Servicing, replacing, and installing the
product can only take place is an area that is non-hazardous.

- 9 -
Wiring Requirements
WARNING
Do not disconnect modules or wires unless the power supply
has been switched off or the area is known to be
non-hazardous. The devices may only be connected to the
supply voltage shown on the type plate.
The devices are designed for operation with a Safety
Extra-Low Voltage. Thus, they may only be connected to the
supply voltage connections and to the signal contact with the
Safety Extra-Low Voltages (SELV) in compliance with
IEC950/ EN60950/ VDE0805.
WARNING
This unit is a built-in type. When the unit is installed in another
piece of equipment, the equipment enclosing the unit must
comply with fire enclosure regulation IEC 60950/EN60950 (or
similar regulation).
WARNING
Safety First!
Be sure to disconnect the power cord before installing and/or
wiring
the Ethernet Switch.
Calculate the maximum possible current in each power wire
and common wire. Observe all electrical codes dictating the
maximum current allowable for each wire size.
If the current goes above the maximum ratings, the wiring
could overheat, causing serious damage to your equipment.
You should also pay attention to the following items:
Use separate paths to route wiring for power and devices. If power
wiring and device wiring paths must cross, make sure the wires are
perpendicular at the intersection point.
NOTE: Do not run signal or communications wiring and power wiring
in the same wire conduit. To avoid interference, wires with different
signal characteristics should be routed separately.
You can use the type of signal transmitted through a wire to determine
which wires should be kept separate. The rule of thumb is that wiring
with similar electrical characteristics can be bundled together.
Keep input wiring and output wiring separated.
It is strongly advised that you label wiring for all devices in the system
when necessary.
Only use copper conductors with 60/75°C capability

- 10 -
Grounding Ethernet Switch
Grounding and wire routing help limit the effects of noise due to
electromagnetic interference (EMI). Run the ground connection from the
ground screw to the grounding surface prior to connecting devices. A 4
mm² conductor must be used when a connection to the external
grounding screw is utilized.
ATTENTION
This product is intended to be mounted to a well-grounded
mounting surface, such as a metal panel.
Wiring the Alarm Contact
The Alarm Contact consists of the two middle contacts of the terminal
block on the Ethernet Switch´s top panel. A typical scenario would be to
connect the Fault circuit to a warning light located in the control room.
The light can be set up to switch on when a fault is detected.
In this section, we explain the meaning of the two contacts used to
connect the Alarm Contact.
FAULT: The two middle contacts of the
6-contact terminal block connector are used
to detect both power faults and port faults.
The two wires attached to the Fault contacts
form an open circuit when:
1. Ethernet Switch has lost power from one
of the DC power inputs.
OR
2. The PORT ALARM DIP Switch for one of
the ports is set to ON, but the port is not
connected properly.
If neither of these two conditions is satisfied,
the Fault circuit will be closed.
ATTENTION
Exposure to some chemicals may degrade the sealing
properties of materials used in the Sealed Relay Device

- 11 -
Wiring the Redundant Power Inputs
Both power inputs can be connected simultaneously to live DC power
sources. If one power source fails, the other live source acts as a backup,
and automatically supplies the Ethernet Switch’s power needs.
The top two contacts and the bottom two contacts of the 6-contact
terminal block connector on the Ethernet Switch’s top panel are used for
the Ethernet Switch’s two DC inputs. Top and front views of the terminal
block connector are shown here.
STEP 1: Insert the negative/positive DC
wires into the V-/V+ terminals.
STEP 2: To keep the DC wires from
pulling loose, use a small flat-blade
screwdriver to tighten the wire-clamp
screws on the front of the terminal block
connector.
STEP 3
: Insert the plastic terminal block
connector prongs into the terminal
block receptor, which is located on
Ethernet Switch’s top panel.
ATTENTION
Before connecting the Ethernet Switch to the DC power
inputs, make sure the DC power source voltage is stable.
ATTENTION
Conductors suitable for use
in an ambient temperature of 93°C
must be used for the power supply terminal.
One individual conductor in a clamping point with 28-12
AWG wire size, and a torque value of 4.5 lb
-in should be
used.
ATTENTION
Transient provisions shall be made to prevent the rated
voltage being exceeded by transient disturbances of more
than 40%.

- 12 -
Communication Connections
The models of IE-SW-VL16 series have 14 or 16 10/100BaseT(X)
Ethernet ports, and 2 or 0 (zero) 100 BaseFX multimode (SC/ST-type
connector) fiber ports.
10/100BaseT(X) Ethernet Port Connection
The 10/100BaseT(X) ports located on Ethernet Switch’s front panel are
used to connect to Ethernet-enabled devices. Below we show pinouts for
both MDI (NIC-type) ports and MDI-X (HUB/Switch-type) ports, and also
show cable wiring diagrams for straight-through and cross-over Ethernet
cables.
10/100Base T(x) RJ45 Pinouts
MDI Port Pinouts
MDI
-
X Port Pinouts
8
-
pin RJ45
Pin
Signal
Pin
Signal
1 Tx+ 1 Rx+
2 Tx- 2 Rx-
3 Rx+ 3 Tx+
6 Rx- 6 Tx-
RJ45 (8-pin) to RJ45 (8-pin) Straight-Through Cable Wiring
RJ45 (8-pin) to RJ45 (8-pin) Cross-Over Cable Wiring

- 13 -
100BaseFX Ethernet Port Connection (Fiber)
Remember to connect the Tx (transmit) port of device 1 to the Rx (receive)
port of device 2, and the Rx (receive) port of device 1 to the Tx (transmit)
port of device 2. Fiber optic connections generally are using the
full-duplex transmission mode.
SC-Port Pinouts SC-Port to SC-Port Cable Wiring
ST-Port Pinouts ST-Port to ST-Port Cable Wiring
ATTENTION
This is a Class 1 Laser/LED product. To avoid causing
serious damage to your eyes, do not stare directly into the
Laser Beam.
DIP Switch Settings
IE
-
SW
-
VL16
Series
DIP Switches
The default setting for each DIP Switch is OFF. The following table
explains the effect of setting the DIP Switches to the ON positions.
DIP Switch
Setting
Description
----
– Serves no function (reserved for future use).
Port Alarm
Function
(P1 to P16)
ON
Enables the corresponding PORT Alarm. If the
port’s link fails, the relay will form an open
circuit and the fault LED will light up.
OFF
Disables the corresponding
PORT Alarm. The
relay will form a closed circuit and the Fault
LED will never light up.
BSP ON
Enables broadcast storm protection (limitation
to 2000 broadcast packets per second and
port)
OFF Disables broadcast storm protection

- 14 -
LED Indicators
The front panel of the Ethernet Switch contains several LED indicators.
The function of each LED is described in the table below.
LED
Color
State
Description
PWR1
AMBER
On Power is being supplied to power input
PWR1.
Off Power is
not
being supplied to power input
PWR1.
PWR2
AMBER
On Power is being supplied to power input
PWR2.
Off Power is
not
being supplied to power input
PWR2.
FAULT
RED
On When the corresponding PORT alarm is
enabled, and the port’s link is inactive.
Off
When the corresponding PORT alarm is
enabled and the port’s link is active, or when
the corresponding PORT alarm is disabled.
10M YELLOW
On Port’s 10 Mbps link is active.
Blinking
Data is being transmitted at 10 Mbps.
Off Port’s 10 Mbps link is inactive
100M
(TP) GREEN
On Port’s 100 Mbps link is active.
Blinking
Data is being transmitted at 100 Mbps.
Off Port’s 100Mbps link is inactive.
100M
(FX) GREEN
On Port’s 100 Mbps link is active.
Blinking
Data is being transmitted at 100 Mbps.
Off Port’s 100Mbps link is inactive.
Auto MDI/MDI-X Connection
The Auto MDI/MDI-X function allows connecting devices to an Ethernet
Switch’s 10/100BaseT(X) port without paying attention to the type of
Ethernet cable being used for the connection. This means that you can
use either a straight-through cable or cross-over cable to connect
devices to the Ethernet Switch.
Auto-Negotiation and Speed Sensing
Each RJ45 Ethernet port independently supports auto-negotiation for
recognizing the transmission speed 10 Mbps or 100 Mbps according to
the IEEE802.3 standard. This means that some of connected Ethernet
devices could operate at 10 Mbps, while at the same time other nodes
are operating at 100 Mbps. Auto-negotiation takes place each time when
a RJ45 cable connection is made and a link will be established. The
Ethernet Switch advertises its capability for using 10 or 100 Mbps
transmission speed to the connected device and expects this also from
the connected device. This procedure results in an agreement to operate
at a speed of either 10 or 100 Mbps.
The fiber optic ports operate at a fixed 100 Mbps speed and full-duplex
mode to provide the best performance.

- 15 -
Auto-Negotiation and Transmission Mode
Besides the transmission speed, each RJ45 port auto-negotiates the
transmission mode (half duplex or full duplex). Typically, if both devices
are set to “auto-negotiation”, the full duplex transmission will be set.
Note about possible loss of data packages in case of “Duplex
mismatching”
If the switch’s auto-negotiation port is connected to a non-negotiating
device, then the Switch will set its port transmission speed same as the
connected device but is unable to correctly detect the duplex mode. As
result the port is set to the correct speed but is using always the half
duplex mode as required by the IEEE 802.3u standard in such cases. For
correct transmission, the non-negotiating port must be set to half-duplex
mode (speed either 10 Mbps or 100 Mbps).
Switching, Filtering, Forwarding, Address
Learning
Each time a packet arrives at one of the switched ports, a decision is
made to either filter or forward the packet. Packets with source and
destination addresses belonging to the same port segment will be filtered,
constraining those packets to one port, and relieving the rest of the
network from the need to process them. A packet with destination
address on another port segment will be forwarded to the appropriate
port, and will not be sent to the other ports where it is not needed.
Packets that are used in maintaining the operation of the network (such
as the occasional multi-cast packet) are forwarded to all ports.
The Ethernet switch operates in the store-and-forward switching mode,
which eliminates bad packets and enables peak performance to be
achieved when there is heavy traffic on the network.
Switches of IE-SW-VL16 series have an address table that can hold up to
4K node addresses, which makes it suitable for use with large networks.
The address tables are self-learning, so that as nodes are added or
removed, or moved from one segment to another, the Ethernet Switch
automatically keeps up with new node locations. An address-aging
algorithm causes the least-used addresses to be deleted in favor of
newer, more frequently used addresses. To reset the address buffer,
power down the unit and then power it back up
WARNING
This equipment is intended to be used in a
restricted access location.
HOT SURFACE!! Before touching it, special
attention or protection is required.

- 16 -
Specifications
Technology
Standards
IEEE 802.3 for 10BaseT,
IEEE 802.3u for 100BaseT(X) and 100Base FX,
IEEE 802.3x for Flow Control
Forward and Filtering
Rate 148,810 pps (100Mbit), 14,881 pps (10Mbit)
Packet Buffer Memory 1.25 Mbit
Processing Type
Store and Forward, with IEEE802.3x full duplex,
back pressure flow control
MAC-address Table
Size 4K uni-cast addresses
Interface
RJ45 Ports 10/100BaseT(X) auto negotiation speed, F/H
duplex mode and auto MDI/MDI-X connection
Fiber Ports 100BaseFX ports (SC/ST connector)
LED Indicators PWR1, PWR2 (Power), 10/100M (TP-Port) and
100M (Fiber port)
DIP Switches Enable/disable broadcast storm protection
Alarm Contact One relay output with current carrying capacity
of 1A @ 24 VDC
Optical Fiber
100Base FX
Multi
-
mode
Fiber Cable Type OM1 50/125 µm
800 MHz*Km
Typical Distance 4 km 5 km
Wavelength
Typical (nm) 1300
TX Range (nm) 1260 to 1360
RX Range (nm) 1100 to 1600
Optical Power
TX Range (dBm) -10 to -20
RX Range (dBm) -3 to -32
Link Budget (dB) 12
Dispersion Penalty
(dB) 3
Typical Distance: To reach the typical distance of a specified fiber
transceiver, please refer to the following formula: Link budget(dB) >
dispersion penalty(dB) + total link loss(dB).
Power
Input Voltage
12/24/48 VDC (9.6 to 60 VDC),
2 redundant inputs
Input Current @ 24
VDC
0.34 A (IE-SW-VL16-16TX)
0.39 A (IE-SW-VL16-14TX-2SC/2ST)
Connection One removable 6-pin terminal block
Inrush current Max. 6.3A @ 24VDC (0.1 - 1ms)
Overload Current
Protection Present
Reverse Polarity
Protection Present
Physical Characteristics
Housing IP30 protection, metal case
Dimension
(W x H x D) 80.5 x 135 x 105 mm
Weight 1,140 g
Installation DIN-rail, Wall Mounting (with optional kit)

- 17 -
Environmenta
l
Operating Temperature
0 to 60°C (32 to 140°F)
-40 to 75°C (-40 to 167°F) for -T models
Storage Temperature -40 to 85°C (-40 to 185°F)
Ambient Relative
Humidity 5 to 95% (non-condensing)
Regulatory Approvals
Safety UL 508, UL 60950-1, EN 60950-1
Hazardous Location
UL/cUL Class I, Division 2, Groups A, B, C, and D;
ATEX Zone 2, Ex nA nC IIC T4 Gc
Maritime DNV/GL
EMI FCC Part 15, CISPR (EN 55032) class A
EMS
IEC 61000-4-2 ESD: Contact: 6 kV; Air: 8 kV
IEC 61000-4-3 RS: 80 MHz to 1 GHz: 20 V/m
IEC 61000-4-4 EFT: Power: 2 kV; Signal: 1 kV
IEC 61000-4-5 Surge: Power: 2 kV; Signal: 2 kV
IEC 61000-4-6 CS: 10 V
IEC 61000-4-8
Shock IEC 60068-2-27
Free Fall IEC 60068-2-32
Vibration IEC 60068-2-6
MTBF
Time 2,290,506 hrs
Database Telcordia (Bellcore), GB
Warranty
Time Period 5 years
Weidmüller gives a 5-year warranty on this product in accordance with
the warranty terms as described in the general conditions of sale of the
Weidmüller company which has sold the products to you. Weidmüller
warrants to you that such products the defects of which have already
existed at the time when the risk passed will be repaired by Weidmüller
free of charge or that Weidmüller will provide a new, functionally
equivalent product to replace the defective one. Safe where expressly
described otherwise in writing in this catalogue/product description,
Weidmüller gives no warranty or guarantee as to the interoperability in
specific systems or as to the fitness for any particular purpose. To the
extent permitted by law, any claims for damages and reimbursement of
expenses, based on whatever legal reason, including contract or tort,
shall be excluded. Where not expressly stated otherwise in this warranty,
the general conditions of purchase and the expressive liability
commitments therein of the respective Weidmüller company which has
sold the products to you shall be applicable.
Contact Information
Weidmüller Interface GmbH & Co. KG
Postfach 3030
32760 Detmold
Klingenbergstraße 16
32758 Detmold / Germany
Phone +49 (0) 5231 14-0
Fax +49 (0) 5231 14-292083
E-Mail info@weidmueller.com
Internet www.weidmueller.com
This manual suits for next models
6
Table of contents
Other Weidmuller Switch manuals
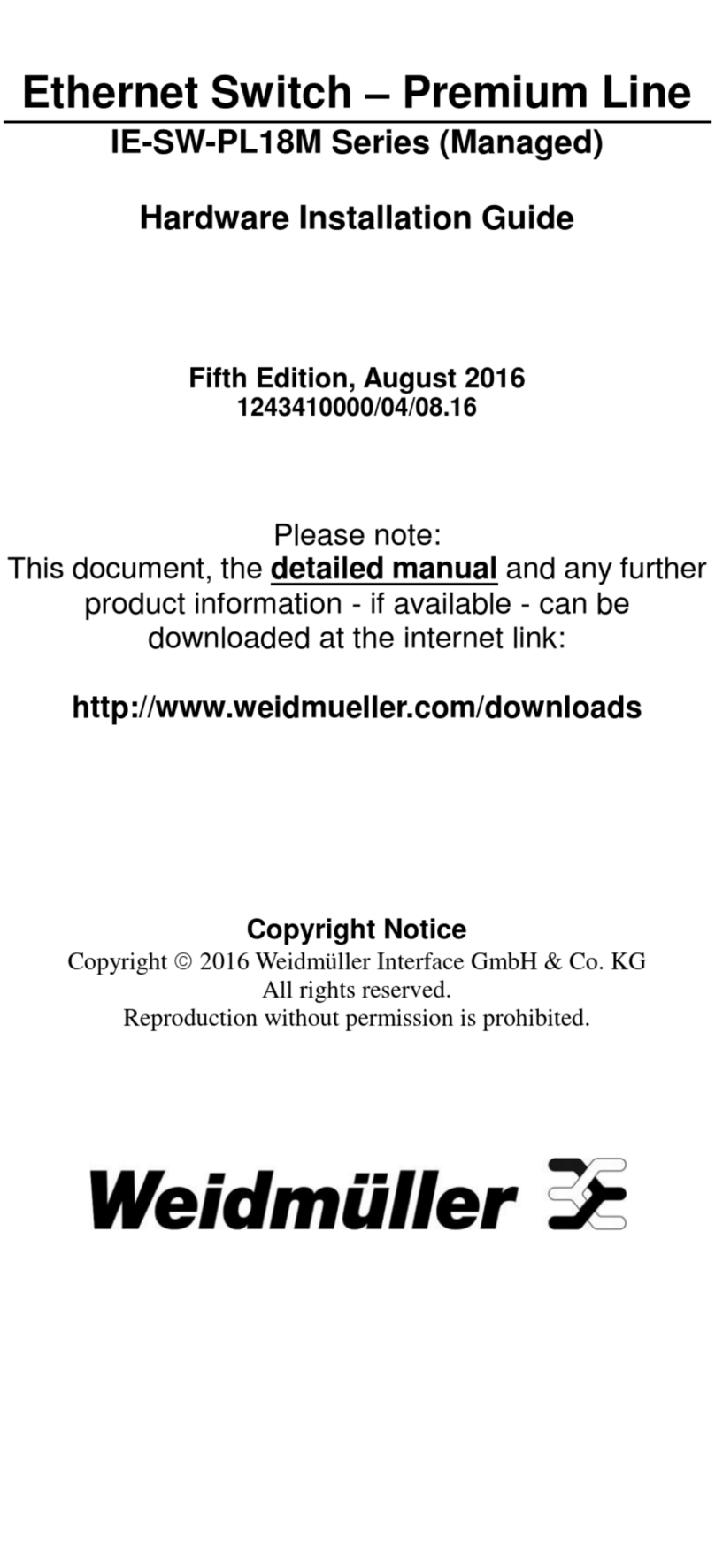
Weidmuller
Weidmuller IE-SW-PL18M Series Manual
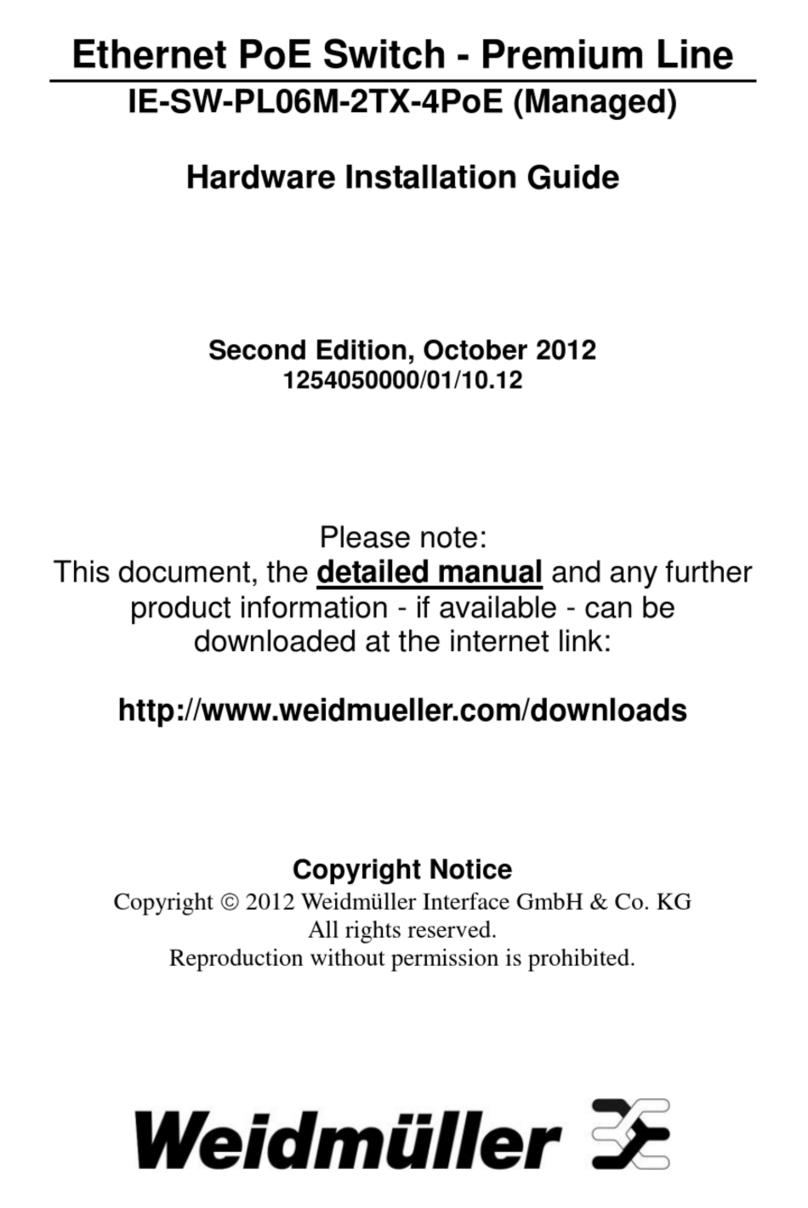
Weidmuller
Weidmuller IE-SW-PL06M-2TX-4PoE Manual

Weidmuller
Weidmuller IE-SW-PL16M Series Manual
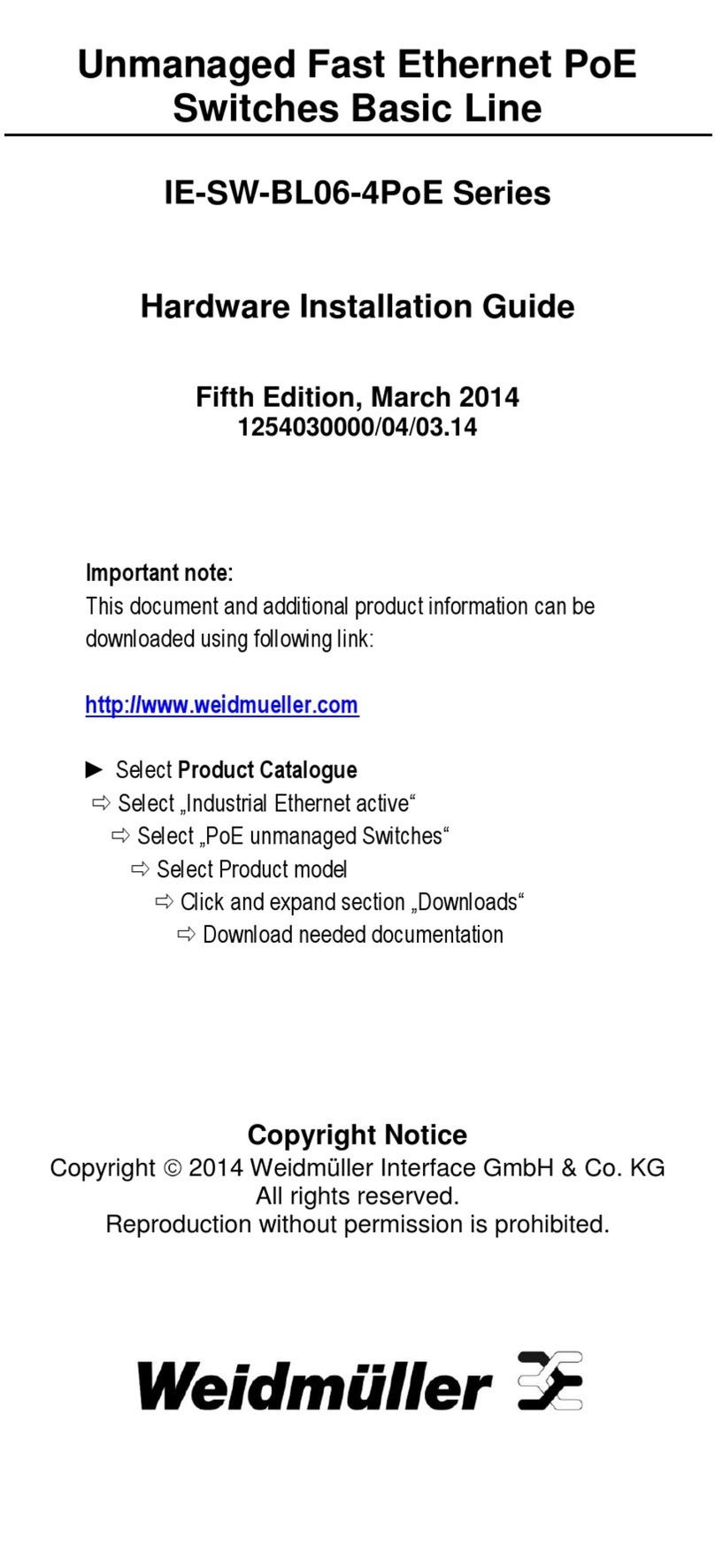
Weidmuller
Weidmuller IE-SW-BL06-4PoE Series Manual

Weidmuller
Weidmuller IE-SW-VL08-8GT Manual
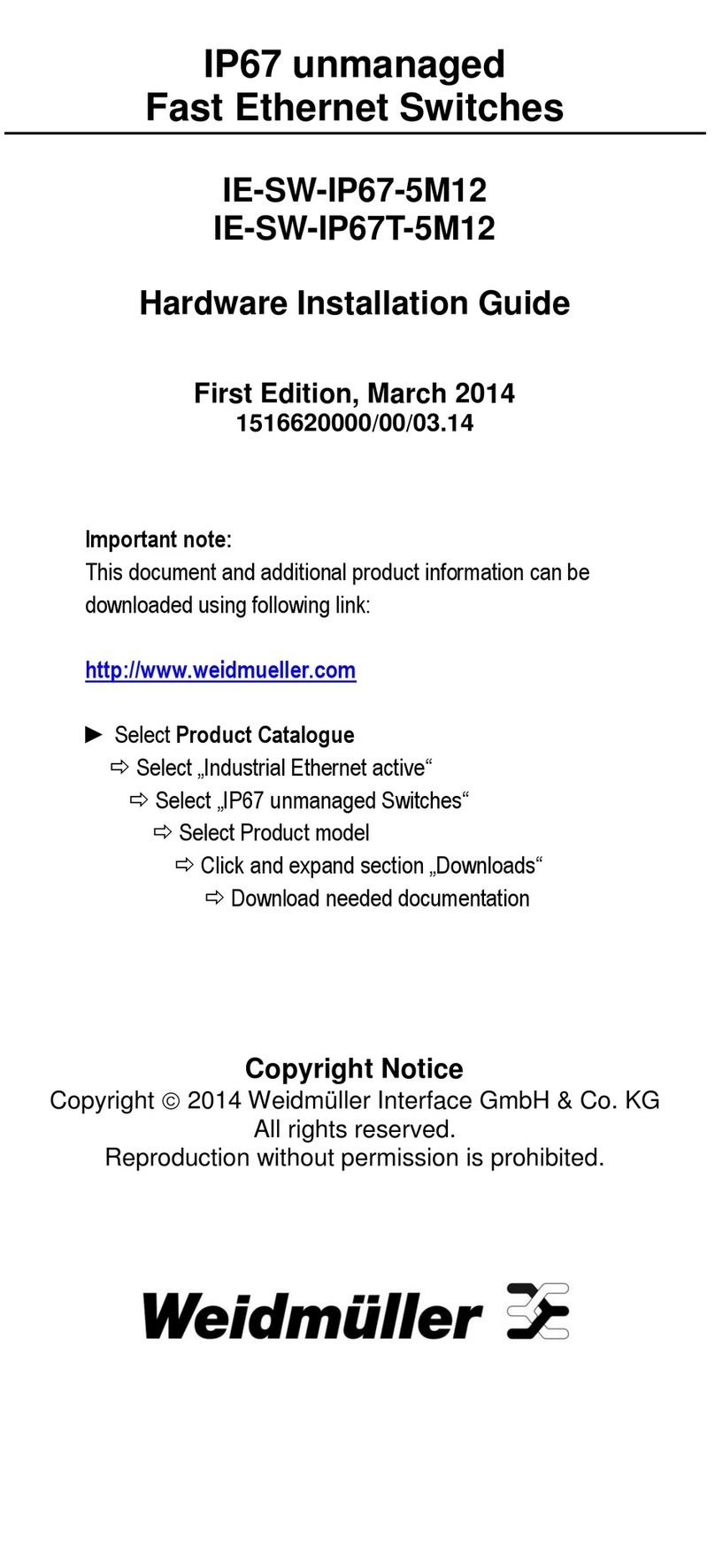
Weidmuller
Weidmuller IE-SW-IP67-5M12 Manual
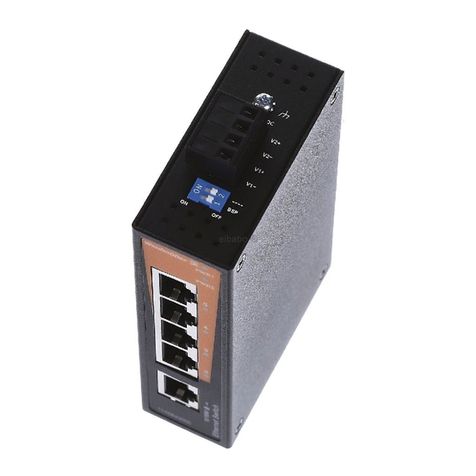
Weidmuller
Weidmuller IE-SW-BL05 Series Manual
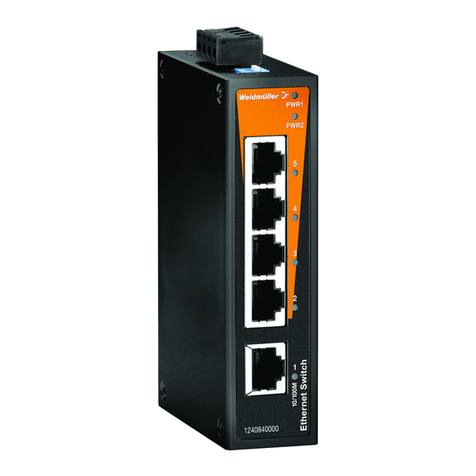
Weidmuller
Weidmuller IE-SW-BL05T-5TX Manual