Wheel Horse D-250 Operating instructions

D-250 REPAIR MANUAL
Table of Contents – Page 1 of 5
FOREWORD...
CHAPTER 1: PRE-DELIVERY SERVICE
REMOVE THE TRACTOR FROM THE SHIPPING CARTON
INSTALL FRONT WHEELS
INSTALL REAR WHEELS
ADJUST TIRE PRESSURE
MOUNT STEERING WHEEL
CHECK ENGINE OIL
CHECK HYDRAULIC FLUID
CHECK TRANSAXLE FLUID
CHECK COOLING SYSTEM
CHECK WIRING
SERVICE THE BATTERY
FILL THE FUEL TANK
LUBRICATE TRACTOR
TEST TRACTOR'S OPERATION
CHECK FRONT WHEEL ALIGNMENT
ATTACH OWNER'S MANUAL TO TRACTOR
CHAPTER 2: GENERAL MAINTENANCE
LUBRICATION CHART
MAINTENANCE CHART
MAINTENANCE SCHEDULE
CHANGE ENGINE OIL
CHANGE TRANSAXLE FLUID
CLEAN ENGINE AIR FILTER
CHECK GOVERNOR OIL
BODY LUBRICATION
CHECK STEERING GEAR OIL
CHAPTER 3: TUNE-UP
SPARK PLUGS
DISTRIBUTOR MAINTENANCE - DISTRIBUTOR CAP
DISTRIBUTOR MAINTENANCE - DISTRIBUTOR WIRES
DISTRIBUTOR MAINTENANCE - ROTOR
DISTRIBUTOR MAINTENANCE - POINTS AND CONDENSER REPLACEMENT
ENGINE TIMING - MARKING THE FLYWHEEL
ENGINE TIMING - STROBE LIGHT METHOD
ENGINE TIMING - TEST LIGHT METHOD
CARBURETOR ADJUSTMENT - ADJUSTING ENGINE IDLE
CARBURETOR ADJUSTMENT - ADJUSTING AIR/FUEL
CARBURETOR ADJUSTMENT - ADJUSTING MAXIMUM RPM
TUNE-UP SPECIFICATIONS

D-250 REPAIR MANUAL
Table of Contents – Page 2 of 5
CHAPTER 4: ENGINE
ENGINE SPECIFICATIONS
ENGINE TROUBLESHOOTING - ENGINE IS OVERHEATING
ENGINE TROUBLESHOOTING - ENGINE RUNS -- BUT MISFIRES
ENGINE TROUBLESHOOTING - STARTER WORKS -- BUT ENGINE DOES NOT
ENGINE, REMOVAL FROM TRACTOR
ENGINE, INSTALLING IN TRACTOR
CYLINDER BLOCK - DISASSEMBLY
CYLINDER BLOCK - REASSEMBLY OF ENGINE BLOCK
PISTONS/LINERS - REMOVAL
PISTONS/LINERS - SERVICING
PISTONS/LINERS - REASSEMBLY
CYLINDER HEAD - VALVE SPRING REPLACEMENT
CYLINDER HEAD - REMOVAL OF CYLINDER HEAD
CYLINDER HEAD - DISASSEMBLY
CYLINDER HEAD - REASSEMBLY
CYLINDER HEAD - INSTALLATION
CYLINDER HEAD - VALVE ADJUSTMENT
COOLING SYSTEM - FLUSHING
COOLING SYSTEM - WATER PUMP REPLACEMENT
COOLING SYSTEM - RADIATOR REPLACEMENT
COOLING SYSTEM - RESERVOIR BOTTLE - REMOVAL
COOLING SYSTEM - RESERVOIR BOTTLE - INSTALLATION
DRIVE BELTS (CRANKSHAFT - HYDRAULIC PUMP - GOVERNOR)
DRIVE BELTS (WATERPUMP - CAMSHAFT)
DRIVE BELTS (WATERPUMP - GENERATOR)
DRIVE BELTS (FRONT PTO)
CARBURETOR - REMOVAL
CARBURETOR - INSTALLATION
CARBURETOR - CLEANING
CARBURETOR - CHOKE ADJUSTMENT
GOVERNOR - REMOVAL
GOVERNOR - INSTALLATION
GOVERNOR - GOVERNOR LINKAGE ADJUSTMENT
GOVERNOR - GOVERNOR/THROTTLE LINKAGE ADJUSTMENT
GOVERNOR - GOVERNOR SPEED ADJUSTMENT
GOVERNOR - MAINTENANCE
DISTRIBUTOR - DRIVE PINION AND DRIVE GEAR REPLACEMENT
CLUTCH - REMOVAL
CLUTCH - INSTALLATION
CHAPTER 5: TRANSAXLE
SPECIFICATIONS
TRANSAXLE REMOVAL
TRANSAXLE REPLACEMENT

D-250 REPAIR MANUAL
Table of Contents – Page 3 of 5
CHAPTER 5: TRANSAXLE - Continued
TRANSAXLE INSTALLATION
TRANSAXLE REBUILD/DISASSEMBLY - DISASSEMBLY
TRANSAXLE REBUILD/DISASSEMBLY - REAR PTO ASSEMBLY REMOVAL
TRANSAXLE REBUILD/DISASSEMBLY - REDUCTION GEAR ASSEMBLY
TRANSAXLE REBUILD/DISASSEMBLY - GEARSHIFT HOUSING
TRANSAXLE REBUILD/DISASSEMBLY - LEFT GEAR HOUSING REMOVAL
TRANSAXLE REBUILD/DISASSEMBLY - PROBLEM IDENTIFICATION
TRANSAXLE REBUILD/DISASSEMBLY - COUNTERSHAFT ASSEMBLY
TRANSAXLE REBUILD/DISASSEMBLY - WORM WHEEL/WORM SHAFT
TRANSAXLE REBUILD/DISASSEMBLY - REVERSE IDLER GEAR
TRANSAXLE REBUILD/DISASSEMBLY - REAR PTO SHIFT LEVER
TRANSAXLE REBUILD/DISASSEMBLY - DIFFERENTIAL ASSEMBLY
TRANSAXLE REBUILD/DISASSEMBLY - WORM SHAFT ASSEMBLY
TRANSAXLE REBUILD/DISASSEMBLY - REAR PTO DRIVE
TRANSAXLE REBUILD/DISASSEMBLY - PARKING BRAKE
TRANSAXLE REBUILD/REASSEMBLY - ADJUSTING THE WORM WHEEL
TRANSAXLE REBUILD/REASSEMBLY - REVERSE IDLER GEAR
TRANSAXLE REBUILD/REASSEMBLY - COUNTERSHAFT ASSEMBLY
TRANSAXLE REBUILD/REASSEMBLY - LEFT GEAR HOUSING
TRANSAXLE REBUILD/REASSEMBLY - REDUCTION GEAR (SERVICING)
TRANSAXLE REBUILD/REASSEMBLY - REAR PTO COVER
AXLE TUBES - REMOVAL OF AXLE TUBE
AXLE TUBES - DIFFERENTIAL LOCK DISASSEMBLY (RIGHT TUBE ONLY)
AXLE TUBES - DISASSEMBLY
AXLE TUBES - REASSEMBLY
AXLE TUBES - DIFFERENTIAL LOCK REASSEMBLY (RIGHT TUBE ONLY)
AXLE TUBES - INSTALLING AXLE TUBE
AXLE TUBES - ON-VEHICLE AXLE SHAFT/BEARING REPLACEMENT
GEARSHIFT BOX REBUILD - DISASSEMBLY
GEARSHIFT BOX REBUILD - ASSEMBLY
CHAPTER 6: POWER TAKE OFF
FRONT/MID PTO
REAR PTO
CHAPTER 7: ELECTRICAL
TROUBLESHOOTING STARTING CIRCUIT
STARTING CIRCUIT - STARTER REPLACEMENT
STARTING CIRCUIT - IGNITION SWITCH REPLACEMENT
TROUBLESHOOTING CHARGING CIRCUIT
CHARGING CIRCUIT - GENERATOR REPLACEMENT
CHARGING CIRCUIT - REGULATOR REPLACEMENT
FUSES
WIRING SCHEMATIC

D-250 REPAIR MANUAL
Table of Contents – Page 4 of 5
CHAPTER 8: HDYRAULIC SYSTEM
GENERAL SPECIFICATIONS
CHANGING HYDRAULIC FLUID
BLEEDING HYDRAULIC SYSTEM
HYDRAULIC LIFT CYLINDER REPLACEMENT
HYDRAULIC PUMP REPLACEMENT
CHAPTER 9: CHASSIS
FRONT AXLE ASSEMBLY - REMOVAL
FRONT AXLE ASSEMBLY - INSTALLATION
FRONT AXLE ASSEMBLY - FRONT AXLE REPLACEMENT
STEERING (WHEEL) SPINDLE - REMOVAL
STEERING (WHEEL) SPINDLE - INSTALLATION
STEERING GEAR ASSEMBLY - REMOVAL
STEERING GEAR ASSEMBLY - INSTALLATION
FRONT WHEEL BEARING REPLACEMENT
REAR DRUM BRAKES - REMOVAL
REAR DRUM BRAKES - REPLACEMENT
REAR DRUM BRAKES - ADJUSTMENT
PARKING BRAKE
GAS TANK REPLACEMENT
CHAPTER 10: TOOLS - SPECIAL TOOLS
SPECIAL TOOLS - VALVE SPRING COMPRESSOR
SPECIAL TOOLS - CYLINDER HEAD HOLDER
SPECIAL TOOLS - EXTRACTOR FOR DISTRIBUTOR DRIVE PINION
SPECIAL TOOLS - SOCKET FOR CYLINDER HEAD BOLTS
SPECIAL TOOLS - CYLINDER LINER HOLDER
SPECIAL TOOLS - VALVE ADJUSTING WRENCH
SPECIAL TOOLS - EXTRACTOR FOR ROCKER ARM SHAFT
SPECIAL TOOLS - TOOL TO CHANGE VALVE SPRING WITHOUT REMOVING CYLINDER
SPECIAL TOOLS - OIL PRESSURE GAUGE
SPECIAL TOOLS - LIFTING HOOP FOR ENGINE
SPECIAL TOOLS - CENTERING BOLT FOR CYLINDER HEAD
SPECIAL TOOLS - SET OF REAMERS FOR VALVE GUIDES (7MM DIAMETER)
SPECIAL TOOLS - PUNCH FOR VALVE GUIDE (7MM DIAMETER)
SPECIAL TOOLS - TOOL TO COMPRESS RINGS WHEN INSTALLING PISTONS IN
SPECIAL TOOLS - HOLDER FOR DIAL GAUGE
SPECIAL TOOLS - PLATE TO MEASURE CYLINDER LINER PROTRUSION
SPECIAL TOOLS - MOUNTING PLATE FOR PISTON PIN
SPECIAL TOOLS - PUNCH FOR PISTON PIN
SPECIAL TOOLS - EXTENSION FOR DIAL GAUGE
SPECIAL TOOLS - VALVE SPRING COMPRESSOR (SINGLE)
SPECIAL TOOLS - TOOLS TO REMOVE DISTRIBUTOR PINION
SPECIAL TOOLS - CENTERING BOLT FOR CLUTCH DISC

D-250 REPAIR MANUAL
Table of Contents – Page 5 of 5
CHAPTER 10: TOOLS - SPECIAL TOOLS - Continued
SPECIAL TOOLS - PULLER FOR CRANKSHAFT PULLEY (251667)
SPECIAL TOOLS - PULLER FOR CRANKSHAFT PULLEY (251668)
SPECIAL TOOLS - PULLER FOR CAMSHAFT GEAR
SPECIAL TOOLS - PULLER CLAWS FOR B. VI. 28
SPECIAL TOOLS - ENGINE STAND
SPECIAL TOOLS - MOUNTING DEVICE FOR ENGINE STAND
SPECIAL TOOLS - ENGINE HOLDER FOR STAND
SPECIAL TOOLS - EXTENSION FEET FOR ENGINE STAND
SPECIAL TOOLS - WRENCH FOR OIL DRAIN PLUG
SPECIAL TOOLS - CALIBRATION BEARING FOR TRANSAXLE COUNTERSHAFT
SPECIAL TOOLS - CALIBRATION BEARING FOR TRANSAXLE WORM WHEEL (251677)
SPECIAL TOOLS - CALIBRATION BEARING FOR TRANSAXLE WORM WHEEL (251678)
SPECIAL TOOLS - FUNNEL TO ADD ENGINE COOLANT

lawn
&
garden
tractors
PRINTEDIN
U.S.A.
8/76
50
Repair
Manual-
PART
NO.
A-1431

n
Foreword
The main objective of this repairmanual is to provide to the reader sufficient technical information to set up and/or
repair the D-250 tractor with speed and skill. Themanualalso provides information regarding the generalmaintenance
ofthe unit.
Since the D-250 tractor is a unique innovation within the lawn and garden industry, every Wheel HorseServiceTechnician
will want to beaware of the latest recommended procedures for
all
possible repairs for theD-250.
Please note: Although a section hasbeen provided for the repair of the transaxle(Chapter 5) Wheel Horse currently
is
not authorizing it's internal repair. If the transaxle is a suspected failure immediately contact your Distribution Centeror
the factory for assistance. This does not mean that the axle tubes (including brakes) cannot be repaired
-
just the internal
components of the transaxle itself. You, as,a servicing dealer,
will
be notified by mail when you will beauthorized to
make internal repairson this component.
i
How
to
Use
This
Manual
1.
If
the general subject is known:
1.1 Turn to the general table of contents.
1.2 Scan until you come to the subject area.
1.3
Turn to the selected chapter index page.
1.4 Scan the indexpage for the specific subject area.
1.5 Turn to the specific subject.
2. Ifthe specific subject area is known:
2.1 Turn to the general chapter required.
2.2 Scan chapter indexpage for the specific subject.
2.3
Turn to the specific subject.
3.
If replacement parts are required:
3.1 Consult with the D-250 parts manual.
3.2
Turn to the "How to use
..."
section and follow
the directions.

GENERAL TABLE
OF
CONTENTS
CHAPTER
1
-
PREDELIVERYSERVICE.1-1
CHAPTER
2
-
GENERAL MAINTENANCE..2-1
CHAPTER
3
-
TUNE-UP.. 3-1
CHAPTER
4
-
ENGINE4-1
CHAPTER
5
-
TRANSAXLE5-1
CHAPTER
6
-
POWERTAKE
OFF..
6-1
CHAPTER7
-
ELECTRICAL7-1
CHAPTER
8
-
HYDRAULICSYSTEM8-1
CHAPTER
9
-
CHASSIS.. 9-1
CHAPTER 10
-
SPECIALTOOLS10-1
CHAPTER 11 SERVICEBULLETINS..
CHAPTER
12
MISCELLANEOUS
iii

Figure 1-1
Figure 1-2
Figure 1-3
Figure 1-4
Figure 1-5
Figure 1-6
Figure 1-7
Figure 1-8
Figure 1-9
Figure 1
-
10
Figure 1-11
Figure 1-12
Figure 1
-
13
Figure 2-1
Figure 2-2
Figure 2-3
Figure 2-4
Figure 2-5
Figure 2-6
Figure 2-7
Figure 2-8
Figure 2-9
Figure 2- 10
Figure 3-1
Figure 3-2
Figure 3-3
Figure 3-4
Figure 3-5
Figure 3-6
Figure 3-7
Figure 3-8
Figure 3-9
Figure 3- 10
Figure 3-11
Figure 3-12
Figure 3- 13
Figure 3- 14
Figure 3-15
Figure 3- 16
Figure 3-17
Figure 4-1
Figure 4-2
Figure 4-3
Figure 4-4
Figure 4-5
Figure 4-6
Figure 4-7
Figure 4-8
Figure 4-9
Figure
4-
10
Figure 4-11
Figure 4-12
Figure 4-13
Figure 4- 14
Figure 4-15
Figure 4-16
Figure 4-17
Figure 4- 18
Figure 4-19
Figure 4-20
Figure 4-21
Figure 4-22
Figure 4-23
Figure 4-24
Figure 4-25
iv
ILL
U
STRATION
S
D-250 Tractoron Shipping Skid
..
1-3
Front Wheel Castle Nut and Cotter
Pin Installation
...............
1-4
Lug Nut Tightening
............
1-4
Steering Wheel Installation
......
1-4
Dipstick Removal
.............
1-5
Dipstick FULL andADD Marks
...
1-5
HydraulicFluidReservoir Location
.
1-5
TransaxleFiller Plug
...........
1-5
TransaxleFillerPlugOilLevel Mark 1-5
Coolant System Reservoir Bottle
-
CoolantLevel Marks
...........
1-6
Battery Location
..............
1-6
Mid-Hydraulic Lift Cylinder
......
1-7
PowerTake
Off
(PTO) Clutch
....
1-7
EngineOilDrainPlug
..........
2-4
TransaxleFiller Plug
...........
2-4
TransaxleDrainPlugs
..........
2-4
EngineAirFilter (Oil-bath)
......
2-4
EngineAirFilter Cartridge
.......
2-5
Lower Portion of AirFilter
with Insert
..................
2-5
EngineGovernor Dipstick Location 2-5
EngineGovernor Dipstick
.......
2-5
Lubrication Points
.............
2-6
Steering GearReservoir Plug
.....
2-6
SparkPlugRemoval
...........
3-3
Distributor Cap Interior
.........
3-3
Distributor Rotor
..............
3-3
Condenser
..................
3-3
Ignition Points
...............
3-4
Ignition Point Adjustment
.......
3-4
Distributor Identification Numbers
.
3-4
Flywheel Timing Marks
.........
3-4
Marking Flywheel Timing Mark
...
3-5
Distributor RetainingClamp Nut
.
.
3-5
Flywheel Timing Marks
.........
3-5
Flywheel Timing Marks
.........
3-5
Connecting Test Light to Distributor
Terminal
....................
3-6
CarburetorIdle Screw
..........
3-6
Carburetor Air/Fuel Screw
.......
3-6
Throttle Cables
...............
3-6
EngineGovernor Adjustment
.....
3-7
Tractor Front End
.............
4-7
Dashboard Panel
..............
4-7
GrilleRemoval
...............
4-7
RadiatorAssembly
............
4-8
Water Pump
.................
4-8
Throttle Linkages
.............
4-8
Clutch Rod Attachment
........
4-8
Belt Guard
..................
4-8
HydraulicPump
..............
4-9
Horn Mounting Bolt
...........
4-9
Regulator MountingBolts
.......
4-9
Front Engine Mount Bracket
.....
4-9
Lifting Hoop Installation
........
4-9
Driveshaft Coupling
............
4-
10
Hydraulic Lift Cylinder
..........
4-10
HydraulicPump
..............
4-10
Belt Guard
..................
4-10
Throttle Linkages
.............
4-10
Water Pump
.................
4-11
RadiatorAssembly
............
4-1 1
DashboardPanel
..............
4-11
Tractor Front End
.............
4-11
HydraulicPumpRemoval
.......
4- 12
Hydraulic Lift Cylinder
..........
4-9
Driveshaft Positioning Arrows
....
4-12
Figure 4-29
Figure 4-27
Figure 4-28
Figure 4-29
Figure 4-30
Figure 4-3
1
Figure 4-32
Figure 4-33
Figure 4-34
Figure 4-35
Figure 4-36
Figure 4-37
Figure 4-38
Figure 4-39
Figure
4-40
Figure
4-4
1
Figure 4-42
Figure 4-43
Figure 4-44
Figure 4-45
Figure 4-46
Figure
4-47
Figure
4-48
Figure 4-49
Figure 4-50
Figure 4-5
1
Figure 4-52
Figure 4-53
Figure 4-54
Figure 4-55
Figure 4-56
Figure 4-57
Figure 4-58
Figure 4-59
Figure 4-60
Figure 4-61
Figure 4-62
Figure 4-63
Figure 4-64
Figure 4-65
Figure 4-66
Figure 4-67
Figure 4-68
Figure 4-69
Figure 4-70
Figure 4-7
1
Figure 4-72
Figure 4-73
Figure 4-74
Figure 4-75
Figure 4-76
Figure 4-77
Figure 4-78
Figure 4-79
Figure 4-84
CylinderHead Bolt Removal
.....
4-12
CylinderHeadRemoved from
Engine
.....................
4-
12
CylinderLiner Hold-down Tool
...
4-13
Distributor Drive Pinion Removal
..
4-13
Camshaft Removal
............
4-13
OilPumpRemoval
............
4-13
Connecting Rod and Cap
Numbering
..................
4-
14
Engine, Bottom View
..........
4- 14
Liner/Piston/ConnectingRod Assembly
Removal
....................
4- 14
SpacerPlateRemoval
..........
4-15
Connecting Rod Journal Regrinding4-15
Crankshaft Fillets
.............
4- 15
Crankshaft Axial Play
Measurement
................
4-15
CylinderLinerClearanceMeasurement,
FeelerGauge
................
4-16
CylinderLiner Clearance Measurement,
Dial Gage
...................
4-16
Liner Installation
..............
4-16
Liner/Piston/ConnectingRod Assembly
Installation
..................
4-
16
CylinderLiner Hold-down Tool
...
4-17
OilPump installation
...........
4-17
Camshaft Installation
...........
4-17
Timing Chain Installation
........
4-17
Camshaft Flange Mounting Bolts
.
4-17
ChainTensioner Installation
......
4-18
CylinderHead Bolt Removal
.....
4-18
OilPump
...................
4-18
CylinderLiner Hold-down Tool
...
4-19
Piston PinRemoval
...........
4-19
Piston/Connecting Rod Assembly
.
4-
19
Piston Pin Centering
...........
4-19
Piston Ring Installation
.........
4-19
CylinderLiner Clearance Measurement,
FeelerGauge
................
4.20
CylinderLiner Clearance Measurement,
Dial Gauge
..................
4-20
Piston Liner Installation
.........
4-20
Special Tool
(P/N
90.45.287)
Installation
..................
4-21
Valve Spring (Special Tool)
Compressor
.................
4-21
Water PumpRemoval
..........
4-22
Rocker Arm Retaining Clip and
Spring
.....................
4-22
Rocker Arm Shaft
............
4-22
Pulling Rocker Arm Shaft
.......
4-22
Valve Spring Compressor
Installation
..................
4-22
ValveKeepers
...............
4-23
Rocker Arm Shaft
............
4-23
Rocker Arm Retaining Clipand
Spring
.....................
4-23
Water Distributor Tube
.........
4-23
Valve Numbering Layout
........
4-24
Valve Adjustment Tool
.........
4-24
Radiator Petcock
..............
4-25
Water Pump
.................
4-25
Water PumpPulley
............
4-25
Water Pump, Detail
...........
4-25
Thermostat Installation
.........
4-26
Tractor Front End
.............
4-26
Crankshaft Sprocket Removal
....
4-13
Crankshaft Main Bearing Caps
...
4-15
CylinderHead Bolt Removal
.....
4-21

LIST
OF
ILLUSTRATIONS
Figure 4-81 Dashboard Panel 4-26
Figure 4-82 HydraulicPumpBracket Bolts
....
4-27
Figure 4-83 IdlerPulley Bracket Bolt
........
4-27
Figure 4-84 Generator Mounting Bracket Bolt
.
4-27
Figure 4-85 Carburetor
..................
4-27
Figure 4-86 Carburetor Components
.........
4-28
Figure 4-87 Throttle PlateOpening
Measurement
................
4-28
Figure 4-89 Throttle andCarburetorLinkages
. .
4-29
Figure 4-91 GovernorLinkage
.............
4-29
Figure 4-92 Throttle Cables
...............
4-29
Figure 4-94 Distributor Bushingand Drive Gear
..............
Figure 4-88 Carburetor Adjustment Rod
......
4-28
Figure 4-90 Governor MountingBolts
.......
4-29
Figure 4-93 EngineGovernor Adjustment
.....
4-30
SpecialTools
................
4-30
Figure 4-95 Distributor BushingRemoval
.....
4-30
Figure 4-96 Distributor Drive Gear Removal
...
4-30
Figure 4-98 Distributor Bushing Installation
...
4-31
Figure 4-97 Distributor. Drive Gear, and Pinion 4-30
Figure 4-99 Distributor Bushing Clearance
Measurement
................
4-3 1
Figure 4-100 Distributor Drive Pinion Installation 4-31
Figure 4- 102 Tractor Undercarriage
..........
4-32
Figure 4-103 Engine.Rear View
............
4-32
Figure 4-104 Clutch Housing Assembly Removal 4-32
Figure 4-105 Clutch Disk and Pressure Plate
Removal
....................
4-32
Figure 4- 101 Distributor Installation
..........
4-31
Figure 4-106 Clutch Plate with Special Tool
...
4-32
Figure 4-107 Clutch Housing Assembly
.......
4-32
Figure 4-108 Clutch HousingPlate
..........
4-32
Figure 5-1 Seat Mounting Brackets
........
5-3
Figure 5-2 GasTankRear Mounting Brackets 5-4
Figure 5-3 GasTankRemoval
............
5-4
Figure 5-5 SpeedRange Linkage
..........
5-4
Figure 5-6 Jack Stands Installed under
Chassis
....................
5-5
Figure 5-8 TransaxleSide Mounting Brackets
.
5-5
Figure 5-4 TransaxleDisassembly Points
....
5-4
Figure 5-7 Transaxle Front Mounting Bolts
...
5-5
Figure 5-9 TransaxleAssembly Points
......
5-6
Figure 5-1
0
Transaxle in Upright Position
....
5-6
Figure 5-12 Transaxle RearSpacer Plate
.....
5-7
Figure 5-14 Transaxle with PTO Removed
....
5-7
Figure 5-15 PTO Countershaft Snap Ring
....
5-7
Figure 5-11 Transaxle.Rear View
..........
5-6
Figure 5-13 PowerTakeOff(PTO)Removal
..
5-7
Figure 5-16 Transaxle, Front View
..........
5-7
Figure 5-17 Reduction Gear Front Cover
Removal
....................
5-8
Figure 5-18 Reduction Gear Housing
........
5-8
Figure 5-19 Housing/RollerBearing Shim
.....
5-8
Figure 5-21 TransaxleCase Bolt Location
....
5-8
Figure 5-22 TransaxleGear Train
-
Neutral
...
5-9
Figure 5-23 TransaxleGear Train
-
First
.....
5-9
Figure 5-24 TransaxleGear Train
-
Second
...
5-9
Figure 5-25 TransaxleGear Train
-
Third
.....
5-9
Figure 5-26 Transaxle Gear Train
-
Fourth
....
5-9
Figure 5-27 TransaxleGear Train
-
Reverse
...
5-9
Figure 5-20 GearshiftHousing Bolt Location
. .
5-8
Figure 5-28 Countershaft Assembly Removal
.
.
5-10
Figure 5-29 Loosening Worm Wheel and
Shaft
......................
5- 10
Figure 5-30 Worm Shaft Removal
..........
5-10
Figure 5-31Worm Gear
.................
5-10
Figure 5-32 ReverseIdler Gear Removal
.....
5-10
Figure 5-33 RearPTO Shift LeverRemoval
...
5-1
0
Figure 5-34 Marking Worm Gear
...........
5-11
Figure 5-35 Straightening Differential Locking
Tabs
......................
5-11
Figure 5-36 Differential Shaft Removal
.......
5-11
Figure 5-37 Differential Components
........
5-11
Figure 6-38 Worm Shaft Disassembly
.......
5-12
Figure 5-39 Idler GearSnap Ring Removal
...
5-12
Figure 5-40 Straightening Worm Gear Locking
Figure 5-41 Worm Shaft Components
.......
5-12
Tabs
......................
5-12
Figure 5-42Measuring Bearing
to
Idler Gear
Clearance
...................
5-12
Figure 5-43 Intermediate Shaft Components
...
5-13
Figure 5-44 Power Take Off (PTO) Shaft
Components
.................
5- 13
Figure 5-45 PTO Shaft Installation
..........
5-13
Figure 5-46 Intermediate Shaft Installation
....
5-13
Figure 5-47 BrakeCam Assembly
..........
5-13
Figure 5-48 Parking BrakeLeverRemoval
....
5-14
Figure 5-49 Axial Play Measurement
........
5-14
Figure 5.50.1Worm Gear Outside Caliper
Measurement
................
5-14
Figure 5.50.2 Inside Caliper Measurement
......
5-14
Figure 5-51
Figure 5-52
Figure 5-53
Figure 5-54
Figure 5-55
Figure 5-56
Figure 5-57
Figure 5-58
Figure 5-59
Figure 5-60
Figure 5-61
Figure 5-62
Figure 5-63
Figure 5-64
Figure 5-65
Figure 5-66
Figure 5-67
Figure 5-68
Figure 5-69
Figure 5-70
Figure 5-71
Figure 5-72
Figure 5-73
Figure 5-74
Figure 5-75
Figure 5-76
Figure 5-77
Figure 5-78
Figure 5-79
Figure 5-80
Figure 5-81
Figure 5-82
Figure 5-83
Figure 5-84
Figure 5-85
Figure 5-86
Figure 5-87
Figure 5-88
Figure 5-89
ReverseIdler Installation
........
5-15
Countershaft Installation
........
5-15
Countershaft AxialPlay
Measurement
................
5- 15
Transaxle Gear Train
-
Neutral
...
5-15
Intermediate Shaft to Casing
Measurement
................
5- 16
Reduction Gear Housing Centering
Protrusion Measurement
........
5-16
Shim Installation/Removal
.......
5-16
ChangeGear
................
5-16
PTO Countershaft ShimWashers
.
5-17
Cluster Gear Removal
..........
5-17
Drive Shaft Input GearSnap Ring
.
5-17
Shift Lever Components
........
5- 17
Countershaft Gear to Casing
Measurement
................
5-17
PTO Countershaft ShimWashers
.
5-18
Alignment of Gear Tops
........
5-18
ChangeGear
................
5-18
Housing/RollerBearing Shim
.....
5-18
Reduction Gear Housing
........
5-18
Reduction Gear Front Cover
Installation
..................
5-18
Transaxle,Rear View
..........
5-19
PTOGears
..................
5-19
PTO Output Shaft Measurement
.
.
5-19
PTOCover Measurement
.......
5-19
PTO Countershaft Measurement
.
.
5-20
.
Wheel Hub Removal
...........
5-20
Brake Backing Plate Mounting
Axle Tube MountingBolts
......
5-20
Differential Lock
..............
5-20
Axle Components
.............
5-21
Axle Shaft Removal
...........
5-21
Gearshift Box Adjusting Screws
..
5-21
Gear Housing with Selector Shaft
Components
.................
5-22
Shift Gate Assembly
...........
5-22
Shift Lever Assembly
..........
5-22
Shift Lever Assembly
..........
5-22
Shift Gate Installation
..........
5-22
Fork and Selector Shaft
Relationships
.................
5-23
Shift Rails
..................
5.23
Shift Installation Special Tool
....
5-23
Bolts
......................
5-20
V

LIST
OF
ILLUSTRATIONS
Figure 5-90 Installation of Spring and Bearing
.
5-23
Figure 5-91 Fabricated Tool in Use
.........
5-23
Figure 5-92 Selector Shaft Installation
.......
5-23
Figure 5-93 Shifting Forks Installation
.......
5-24
Figure 6-1 PTO.Rear View
...............
6-3
Figure 6-3 PTO Clutch Cable AdjustingNuts
.
6-3
Figure 6-4 RearPTOSpline
..............
6-3
Figure 7-2 Starter Removal
..............
7-3
Figure 7-3 Ignition Switch
...............
7-3
Figure 7-4 Generator. Installed
............
7-5
Figure 7-5 Voltage Regulator. Installed
......
7-5
Figure 7-6 FuseBox(Cover Removed)
......
7-5
Figure 7-7 D-250 Wiring Schematic
.......
7-6
Figure 6-2 PTO IdlerPulley
..............
6-3
Figure 7-1 Muffler and Exhaust Manifold
....
7-3
..............
Figure 8-1 HydraulicPump 8-3
Figure 8-2 Hydraulic Lift Cylinder
..........
8-3
Figure 8-3 HydraulicPump. Bottom View
...
8-3
Figure 9-1 Front Axle Mounting Bolts
......
9-3
Figure 9-3 PTOSnap Ring and Washers
....
9-3
Figure 9-4 Turning the Locking Collar
......
9-3
Figure 9-6 Front Axle Support
............
9-4
Figure 9-8 PTO Shaft (Rear View) 9-4
i
Figure 9-11 Steering Spindle Components
....
9-4
Connection
..................
9-5
Figure 9-13 WheelHubRemoval
...........
9-5
Figure 9-14 BrakeShoeRemoval
...........
9-5
Figure 9-16 Parking Brake Adjustment
.......
9-6
Figure 9-2 Front PTOPulley
.............
9-3
........
Figure 9-5 Front AxleComponents 9-3
Figure 9-7 Shim Installation
..............
9-4
Figure 9-9 Turning the Locking Collar 9-4
Figure 9-1
0
Axle Adjusting Bolt 9-4
Figure 9-12 Steering Spindle/Tie Rod
.........
......
...........
Figure 9-15
Rear
BrakeTurnbuckle
.........
9-5
Figure 9-17 Seat Mounting Brackets
........
9-6
Figure 9-18 GasTankRear Mounting Brackets 9-7
Figure 9-19 GasTankRemoval
............
9-7
Figure 10-2 Cylinderheadholder
...........
10-3
Figure 10-3 Extractor for distributor drive
pinion
.......................
10-3
Figure 10-4 Socket for cyl.
.
head bolts
......
10-3
.Figure 10-5 Cylinderlinerholder
...........
10-3
Figure 10-6 Valve adjusting wrench
.........
10-4
Figure 10-7 Extractor for rocker arm shaft
...
10-4
Figure 10-8 Tool to changevalve spring without
removing cylinderhead
.........
10-4
Figure 10-9 Oilpressuregauge
............
10-4
Figure 10-10 Lifting hoop for engine
.........
10-4
Figure 10-11 Centering bolt for cyl.
.
head
.....
10-5
Figure 10-12Setof reamers for valve guides
(7mm
diameter)
..............
10-5
Figure 10-13 Punch for valveguide (7mm dia.) 10-5
Figure 10-1
4
Tool
to compress ringswhen installing
Figure 10-15 Holder for dialgauge
..........
10-5
Figure 10-16 Plate to measure cylinder liner
protrusion
...................
10-6
Figure 10-18 Punch for piston pin
..........
10-6
Figure 10-19 Extension fordial gauge
........
10-6
Figure 10-20 Valve spring compressor (single)
.
.
10-6
Figure 10-21 Tools to remove distributor pinion 10-7
Figure 10-1 Valve spring compressor
........
10-3
pistons in cylinders
............
10-5
Figure 10-17Mounting plate for pistonpin
....
10-6
Figure 10-22 Centering bolt for clutch disc
....
10-7
Figure 10-23 Puller for crankshaft pulley
......
10-7
Figure 10-24 Puller for crankshaft pulley
......
10-7
Figure 10-26 Puller claws for B
.
Vi
.
28
......
10-8
Figure 10-25 Puller for camshaft gear
........
10-7
vi
Figure 10-27 Engine stand
................
10-8
Figure 10-28 Mounting device for engine stand
.
10-8
Figure 10-29 Engineholder for stand
........
10-8
Figure 10-30 Extension feet for engine stand
.
.
10-8
Figure 10-32 Calibrationbearing for transaxle
Figure 10-33 Calibrationbearingfortransaxle worm
Figure 10-34 Calibrationbearingfortransaxle worm
Figure
10-31
Wrench for oil drain plug
.......
10-9
countershaft
.................
10-9
wheel
......................
10-9
wheel
......................
10-9
Figure 10-35 Funnel to add engine coolant
....
10-9

CHAPTER
1
PRE-DELIVERY
SERVICE
PRE-DELIVERYSERVICE
CHAPTER CONTENTS
RemoveTractorFromShippingCarton
,
.
.
..
.
.
.
1-3
Install Front Wheels
.
. .
..
.
... .
.
.
.
.
.
.
.
.
. . .
.
1-4
Install Rear Wheels
.
.
.
.
.
.
.
.. .
.
.
. .
. .
.
. .
.
.
.
1-4
Adjust TirePressure
.
.
.
.
. .
. .
..
..
.
.
.
.
.
.
,
..
.
1-4
Mount SteeringWheel
.
.
.
.
.
. . .
.
.
.
. .
.
.
.
.
.
.
.
1-4
CheckEngineOil
.
.
.
.
.
.
...
.
. .. . .
.
. .
..
.
.
.
.
1-5
CheckHydraulicFluid
.
.
.
...
.
.
.
..
.
.
.
.
,
.
.
.
. .
1-5
CheckTransaxleFluid
.
. .
..
.
..
.
..
.
.
.
.
.
. .
.
.
.
1-5
Check CoolingSystem
...
.
. ..
.
.
.
. .
.
.
.
.
.
.
.
.
1-6
Check Wiring
.
.
.
.
.. .
..
.
.
.
.
. .
.
... . .
.
..
. .
.
1-6
ServiceThe Battery
.
.
.
,
..
.
. .
,
.
..
. .
.
.
. .
.
.
.
1-6
Fill
TheFuelTank
.
.
..
.
.
. .
..
,
.
.
.
.
.
.
.
.
. .
.
.
1-6
LubricateTractor
. .
. .
.. .
.
. .
.
.
.
.
.
.
.
.
.
.
.
.
.
.
1-6
Test Tractor’s Operation
... ..
.
.
.
. .
.
. .
. .
.
. .
.
1-6
Check Front Wheel Alignment
.
.. .
..
.
..
..
.
.
.
1-7
LIST
OF
ILLUSTRATIONS
Figure 1-1
Figure 1-2
Figure 1-3
Figure 1-4
Figure 1-5
Figure 1-6
Figure 1-7
Figure
1-8
Figure 1-9
Figure 1
-
10
Figure 1-11
Figure 1
-
12
Figure 1
-
13
0-250 Tractor on Shipping Skid
. .
1-3
Front Wheel Castle Nut and Cotter
Pin Installation
.
.
.
. . ..
.
.
.
. .
.. .
1-4
Lug Nut Tightening.
. . ..
.
.
.
.
.
. .
1-4
Steering Wheel Installation
.
..
.
.
.
1-4
Dipstick Removal
.
...
.
..
.
.
.
,
.
.
1-5
Dipstick FULL and
ADD
Marks.
.
.
1-5
HydraulicFluidReservoir Location
.
1-5
TransaxleFillerPlug
.
.
. . .
.
.
.
. .
.
1-5
TransaxleFillerPlugOilLevel Mark1-5
Coolant System Reservoir Bottle
-
CoolantLevel Marks
.
..
. ... .
.
.
.
1-6
Battery Location
..
.
..
.
.
.
.
.
. ...
1-6
Mid-Hydraulic Lift Cylinder
.
..
.
.
.
1-7
Power Take
Off
(PTO)Clutch
.
.
.
.
1-7
1-1

'CHAPTER
1
PRE-DELIVERY
SERVICE
CHAPTER
1
PRE-DELIVERYSERVICE
Figure
1-1
D-250
Tractor
onShippingSkid
REMOVETHETRACTORFROMTHESHIPPINGCARTON
Quantity Parts
1.
Cut the bands which hold the carton to the shipping
skid.
2.
Remove the cardboard carton.
3. Cut the wires holding the axles
of
the tractor to the
skid.
4.
The parts to be installed are located in the box. The
following is
a
list
of
the loose parts you should have.
1 Steering Wheel
1
Steering Wheel Insert
1
1 Steering Wheel Nut (ontractor)
Washer (on tractor)
1
1
10
.2
2
2
2
1
1
1
1
Lockwasher (ontractor)
Woodruff Key (ontractor)
Rear Wheel LugNuts
Castle Nuts
Washer
Cotter Pins
HubCap
Draw Bar Hitch Pin
Owners Manual
New Products Registration Card
(in card pack)
Warranty Card (on tractor)
1-3

CHAPTER
1
PRE-DELIVERYSERVICE
INSTALL FRONT WHEELS
1.Raise thefrontof the tractor with a suitable hoist or
jack.
a) If a floor jack is being used, locate the jackunder
thefront axle support casting.
b) If a chain hoist is being used, attachthehoist to
the front axle and take care not to scratch thehood or
axle.
2.Place a front wheel on the spindle with the valve
stem on the outside.
3.
Install thethrust washer, followed by a castle nut and
a cotter pin (SeeFigure 1-2). The castle nut should be
tight enough thatthe wheel does not wobble, but loose
enough thatthe wheel rotates freely.
Figure
1-2
Front Wheel Castle Nut and Cotter Pin
Installation
4.
Install the wheel on the other side.
5. Lower the front of tractor and remove jackor hoist.
INSTALL REAR WHEELS
1. Block the front wheels to prevent the tractor from
rolling.
2.
Raise the rear of the tractor using
a
suitable jackor
hoist. If using a floor jack,center
it
under the transaxle.
Place
a
block of wood between the jack and the transaxle
to prevent damage to the transaxlecase.
3.
Mount eachrear wheel assembly with the valve stem
facing toward the outside.
4.
Install the five lug nuts on each wheel and tighten
by hand.
5.
Then tighten
by
torquing every other lugnut
in
increments until they are
all
tightened to
65
ft-lbs (See
Figure 1-3).
1
I
Figure
1-3
Lug Nut Tightening
6.
Lower the tractor and remove jackor hoist.
ADJUST TIREPRESSURE
1.
Adjust the front tires with a low pressure tire gauge
to15 psifor normal operation,or 21 psi when using a
heavy front attachment.
2.
Adjustthe rear tires with a
low
pressure tire gauge
to11 psi for normal operation, or 18 psi when using a
heavyrear attachment.
MOUNT STEERINGWHEEL
1.Check to see that the front wheels are pointing straight
ahead.
2. Using the key taped to steering wheel shaft, Place
the steering wheel onthe shaft.
3. Install the flat washer, followed by the lockwasher
and then thenut (SeeFigure 1-4).
Figure
1-4
SteeringWheel Installation
4.
Snap the steering wheel insert into place.

CHAPTER
1
PRE-DELIVERY SERVICE
V
CHECKENGINE OIL
1.
Remove the dipstick andcheck the engine oil level
(SeeFigure 1-5).
Figure
1-5
DipstickRemoval
2. The top of the flattened out portionisthe full mark
and the bottom is the add mark (See Figure 1-6).
ADD
OIL
Figure
1-6
Dipstick FULL and ADDMarks
3. Add oil if necessary, but
neveroverfill.
Use only API
Service SC oils. The chart below indicates the viscosity
to use for your climate.
Engine Oil
Temperature
-
Viscosity Chart
Air Temperature Oil Viscosity
Above 86°F(30°C) SAE
HD
20W40
86°F(30°C) or 10W40
10°F (-12°C) to SAE
HD
10W30
Below 10°F(-12°C)SA€ 5W20
CHECK HYDRAULIC FLUID
1.
Check the hydraulic fluid level in the reservoir tank
(SeeFigure 1-7).
Figure
1-7
Hydraulic Fluid Reservoir Location
2.
The fluid level should be between the top and the
bottom of the tank neck.
CHECK TRANSAXLE FLUID
1.
Remove the transaxle filler plug and check thefluid
level on the dipstick (See Figure 1-8).
Figure
1-8
Transaxle FillerPlug
2.
The level should be above the line on the dipstick
(SeeFigure
1-9).
Figure
1-9
Transaxle FillerPlug Oil Level Mark

CHAPTER
1
PRE-DELIVERY
SERVICE
3.Add transaxle fluid
if
necessary,
but
do
not overfill.
Use SAE 9O/Hypoid fluid only.
CHECKCOOLING SYSTEM
1.
The coolant level
in
the reservoir bottle should be
betweenthe max. and min. marks (See Figure 1-1
0).
Figure
1-10
CoolantSystemReservoir Bottle
-
Coolant
Level Marks
2.
If
there isno fluid
in
the reservoir bottle, remove the
radiator cap and check to see if there is coolant in the
radiator.
3. Before adding anycoolant,check the coolant in the
engine with a hydrometer. The system should be protected
to-31°F (-35°C).
4.
If necessary,add coolant to ensureadequate protection
from freezing.
CHECK WIRING
1.
Visually inspect for any loose connections and tighten
as required.
2.
Check the routing of wires to make sure they
will
not
be cut by moving parts or burned by the exhaust system.
SERVICE THE BATTERY
Electrolyteor battery
fluid are poisonousand can be injurious
to eyes,skin and clothing.In theevent
of an accident, flush immediately with
asolutionofone part baking soda to
fourpartswater and callaphysician
immediately. If baking soda is not available,
flush affectedareawithwater and call
physician immediately.
NOTE:
Never install electrolyte
in
battery
with the battery in the tractor. Use only
an electrolyte with a specific gravityof
1.265.
1. Remove the batteryholddown strap and cover (See
Figure 1-11).
2.
Remove the battery cable from the negative terminal.
3. Remove the cable
from
the positive terminal and
lift
thebattery from the tractor.
Figure
1-11
BatteryLocation
Remove the caps and fill eachcell until the electrolyte
(battery acid) is 1/4 inch (6mm) above the top edge of
the plates or 1/8 inch (3mm) above the top ofthe
separators.
5.
Allow thebattery to stand for
5
to
6
hours. During
thistimethe acid level will drop,and should be restored
to
the original level.
6.
For the first time, charge the batteryat
1
amp for
about 15 hours.
NEVER CHARGE WITH A BOOSTER
CURRENT
FOR THE FIRST
CHARGE.
The battery caps
should always be
off
when charging.
7.
Two hours after charging, restore the fluid level with
distilled water.
NOTE:
After the battery hasbeen in service,
add 'only distilled water.
DONOTADD
ELECTROLYTE TO A USED BATTERY.
8.
Install thebattery in the tractor with the terminal post
side toward the front, or closest to the engine.
9.
Connect the positive battery cable first.
10. Connect the negative battery cable.
11.Coat the exposed metal portions with battery grease.
12. Install 'thebattery coverand hold down strap.
FILL
THE
FUEL
TANK
1. Fill the fuel tank with regulargasoline (90 octane or
higher).
2.
Check fuel hoses and fittings for leaks.
LUBRICATETRACTOR
1. Grease 'all the lube pointsmentioned inthe Body
Lubrication section on page
2-6.
TESTTRACTOR'S OPERATION
1.
Start
the
engine. The starting procedures are given in
detail on page
4
ofthe Owner's Manual.
2.Check the operation of all gauges and indicator lights.

3. Check to see that the parking brake light comes on
whenthe
key
is pushed in and the parking brake lever
is positively engaged.
4.
Test the operation of the lights,
5.
Check thelift cylinder to see if the mid hydraulic
lift
is operating
(See
Figure 1-1
2).
Figure
1
-
12
Mid-HydraulicLiftCylinder
6.
Test the PTO clutch (See Figure 1-13).
Figure
1-1
3
Power
Take
Off
(PTO) Clutch
7.
Test drive the tractor, using boththeforward and
reversegears.
CHECK FRONT WHEEL ALIGNMENT
1.Set the front wheels pointing straight ahead.
2.
Each wheel should have approximately 3/64 inch of
"toe
in".
ATTACHOWNER'SMANUAL
TO
TRACTOR
1.
Attachtheowner's manualand the manual of
attachments and accessories to the tractor.
CHAPTER
1
PRE-DELIVERY
SERVICE

CHAPTER
2
GENERALMAINTENANCE
CHAPTER CONTENTS
Maintenance Schedule.
.
.
.
.
.
.
.
.
... .
.
.
.
.
.. .
.
2-3
ChangeEngineOil
.
.
.
. .
.
.
.
.
.
.
. ..
.
.
.
.
...
.
.
2-4
ChangeTransaxleFluid
...
. ... .
. .
.
.
. .
.
....
.
2-4
CleanEngineAirFilter
.
..
.
.
.
.
.
.
.
.
.
.
.
.
.
.
.
.
.2-4
CheckGovernorOil
.
. . .
. .
.. . .
.
. ..
.
.
.
.
.
.
.
.2-5
Body Lubrication.
.
.
. .
.
..
.
.
..
.
.
.
.
..
.
.
..
. ..
2-5
Check Steering Gear Oil
.
.
.
.
. .
.
.
.
.
.
.... .
.
.
.
2-6
LIST
OF
ILLUSTRATIONS
Figure 2-1
Figure
2-2
Figure
2-3
Figure
2-4
Figure 2-5
Figure
2-6
Figure
2-7
Figure
2-8
Figure
2-9
Figure
2-
10
EngineOilDrainPlug
.
.
..
.
.
..
.
.
2-4
TransaxleFillerPlug
......
.
.
.
.
.
2-4
TransaxleDrainPlugs
.
.
....
.
.
.
.
2-4
EngineAirFilter(Oil-bath)
.
.
..
.
.
2-4
EngineAirFilter Cartridge.
..
.
..
.
2-5
Lower Portion
of
AirFilter
with
Insert
..
.
.
.
..
...
.
.
..
.
..
.2-5
EngineGovernorDipstick Location
2-5
EngineGovernor Dipstick
.
.
..
.
..
2-5
Lubrication Points
..
..
.
..
.
.
..
. .
2-6
Steering GearReservoir Plug.
.
...
2-6

CHAPTER
2
GENERAL
MAINTENANCE
i-
LUBRICATIONCHART
o
o
o o
o
ENGINELUBRICATIONPOINTS
1.
2.
3.
4.
5.
6.
7.
8.
Oilfiller cap
Dipstick
Oil drainplug
Governor
Airfilter
Hydraulic system drainplug
Hydraulic reservoir
Hydraulicpump
TRANSMISSION
9. Oildipstick/fill cap
10. Oildrainplug
11. Oildrainplug
STEERING
12. Steering gear
COOLINGSYSTEM
13. Radiator
14. Overflow (compensating) bottle
15.
Front
axle
bearing (1)
20.
Gear Shift
lever
16. Universal shaft (3) 21. Stub
axles
17.
Front wheel hubs
22.
Front PTO
18.
Brake
axle'
23. Mid PTO
19.Brakepedal bearing 24.RearPTO
25.
Front spindles
SAEHD 20W-40 2.5 liters
B.
10°F(-12°C) to
(2.6
qts.)
Engine 86°F (30°C) Daily30
60
100
(Change)
SAE
HD 10W-30 Check Check
C. Below 10°F Dipstick
SAE 5W-20
(-12°C)
Governor HDSAE 10
0.05
liters
(.053
qts.)
100
(at the start
of
each season)
60
Hydraulic SystemHDSAE 10
Air Filter
2.5 liters
(2.6 qts.) Dailyorwhen hoses
500
x
cm above
removed
Same
as
Engine
Retainer
Ring 10-20 30
30
30
Transmission
SAE
90/Hypoid
(5.5
qts.) 10-20 30
Steering Gear SAE 90/Hypoid
5.25
liters
.1
liter 200
100
When the engine
is
cold the
bottle should bebetweenthe
4
Pints
Coolant
to
7.5
Pints Water min. and max. mark.
orHighGrade
All
Daily The fluidin the system should
Year Anti-Freeze bereplacedtotallyat least
every two (2) years after the
system has been flushed.
Cooling System
Grease Fittings Regular lubrication Grease Replace Defective Zerks Immediately
2-2

CHAPTER
2
GENERALMAINTENANCE
CHAPTER
2
GENERALMAINTENANCE
!
MaintenanceSchedule
CHANGEENGINEOIL(Seepage 2-4)
CHANGETRANSAXLEFLUID(Seepage2-41
CHANGEHYDRAULICFLUID(Seepage
8-3)
CHANGEENGINEAIRFILTEROIL(Seepage 2-4)
CHECKGOVERNOROIL(Seepage 2-4)
FLUSHCOOLINGSYSTEM(Seepage 4-25)
BODYLUBRICATION(Seepage 2-5)
ENGINETUNE-UP(Seepage
3-1)
CHECKSTEERINGGEAR
OIL
(See page 2-5)
CHECK DRIVEBELTS(Seepage 4-27)
Change oil after first
30
hours,
60
hours and then every
100
operating hours thereafter.
Change fluid after first
30
hours, and then every 200
hours thereafter.
Change hydraulic fluid after first
60
hours, and then
every
500
hours thereafter.
Change after every
30
hours of operation.
Checkgovernor
oil
every
100
hours of operation.
Flush the system and add new coolant every two years.
Grease all lube pointsshown on page 2-6 after every
100
hours.
Perform anengine tune-up every
150-200
hours.
Check steering gear oil every
100
hours.
Check conditionof drive belts every
100
hours.
CHECK ALLENGINE AND CHASSIS NUTS
&
BOLTSCheck for tightness of nuts and bolts every
30
-
50
FOR
TIGHTNESS hours.
2-3
Table of contents
Other Wheel Horse Tractor manuals

Wheel Horse
Wheel Horse 1-3745 User manual

Wheel Horse
Wheel Horse 854 Troubleshooting guide

Wheel Horse
Wheel Horse 208-4 User manual

Wheel Horse
Wheel Horse 1-7441 User manual
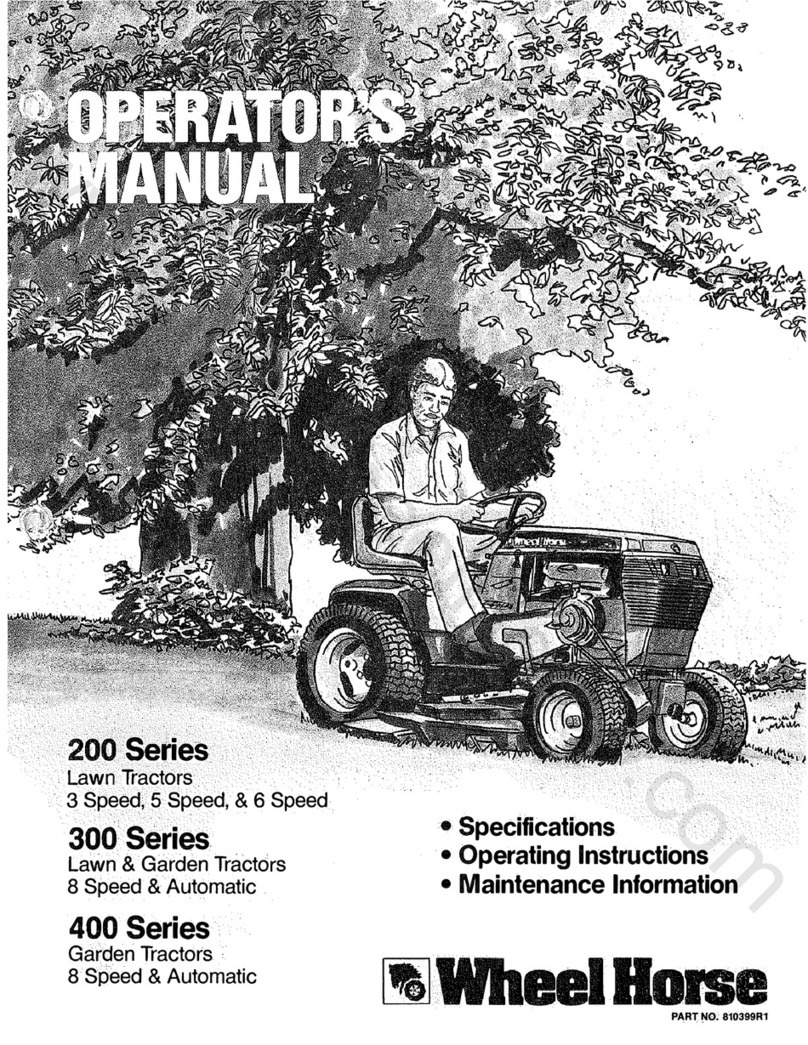
Wheel Horse
Wheel Horse 200 Series User manual

Wheel Horse
Wheel Horse B-81 User manual

Wheel Horse
Wheel Horse 1067 User manual

Wheel Horse
Wheel Horse B-81 User manual

Wheel Horse
Wheel Horse B-81 Reference manual
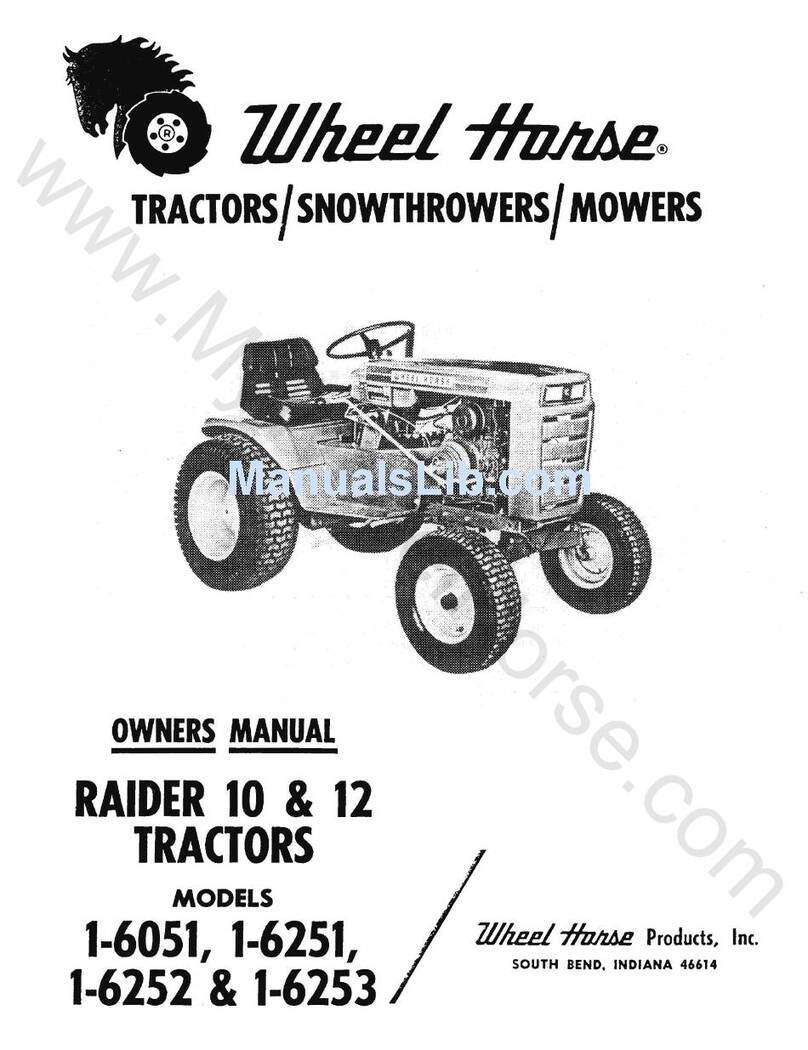
Wheel Horse
Wheel Horse 1-6051 User manual