Yamato V User manual

TYPE V Controller
Communication Reference Codes
Instruction Manual
First Edition
Yamato Scientific America Inc.
Santa Clara,CA
Printed on recycled paper
For proper equipment operation, please read this
instruction manual and main unit instruction manual
before use. Also read external communications
terminal instruction manual carefully when ordering
optional external communication function. Always
keep equipment documentation safe and close at
hand for convenient future reference.

Table of contents
1. COMMUNICATION SETTING PROCEDURES ........................................... 1
1.1: Communication setting ............................................................ 1
1.2: Connection ...................................................................... 5
1.3: Multiple connection procedure ...................................................... 6
2. COMMUNICATION INTERFACE ....................................................... 7
2.1: Data transmission system .......................................................... 7
2.2: Frame configuration ............................................................... 7
2.3: Message configuration ............................................................ 7
2.4: Slave address .................................................................... 7
2.5: Function code .................................................................... 8
2.6: Data ............................................................................ 8
2.7: Reference number ................................................................ 8
2.8: Error check ...................................................................... 9
2.9: Function code details ............................................................. 10
2.10: Error processing ................................................................ 12
2.11: Transmission error codes ........................................................ 12
3. REMOTE OPERATION VIA COMMUNICATION ......................................... 13
3.1: Start remote mode ............................................................... 13
3.2: End remote mode ................................................................ 13
3.3: Remote operation start/stop ....................................................... 13
3.4: Operation mode change in remote mode ............................................ 13
3.5: Key operation in remote mode ..................................................... 14
3.6: Recovery from power outage in remote mode ........................................ 14
4. COMMUNICATION REFERENCE TABLE .............................................. 15
4.1: Function code 03/06 ............................................................. 15
4.2: Function code 04 ................................................................ 22
5. COMMUNICATION SAMPLE MESSAGE .............................................. 28
5.1: ASCII .......................................................................... 28
5.2: RTU ........................................................................... 29
6. PRECAUTIONS .................................................................... 30

1
1. COMMUNICATION SETTING PROCEDURES
1.1: Communication setting
Make appropriate settings to master device (workstation PC etc.) and to TYPE V controller on
main unit (hereafter, “main unit”)
The following table shows the communication setting items for TYPE V controller.
Set values on master device to match items 1-6 below on main unit
The following settings can be made by key operation.
Item Item display
name Communication settings
1 Communication
protocol PRTCL MODBUS-ASCII/RTU
2 Data length DATA 7/8 bit
3 Parity PARI Non/odd/evn
4 Stop bit length STOPB 1/2 bit
5 Communication rate BPS 9600/19200/38400bps
6 Response delay time DELAY 0, 10, 20-250 msec
7 Communication
address ADDRS 1-99
8 Communication mode
CMODE RW/R
: Factory defaults
Communication settings by key operation
1
Controller power should be turned off, showing only
the time.
If control panel shows anything other than time in the
sub (lower) display, press & hold to turn off
the controller
So it only shows the time.
2
Press & hold until "UPASS" shows in the sub
display and "00" shows in the main (upper) display.
Enter "11" using and press .
* Password is fixed at 11 and cannot be changed.

2
1. COMMUNICATION SETTING PROCEDURES
3
Press repeatedly until "COM" shows in the
sub display.
Press .
4
Communication protocol setting; default is "ASCI".
"PRTCL" shows in the sub display and "ASCI" in the
main display.
Press . Main display content flashes.
can now be used to select "ASCI" or
"rtU". Select either one and press . .
5
Data length setting; default is "7BIT"
Press to show "DATA" in the sub display and
"7BIT" in the main display.
Press . Main display content flashes.
can now be used to select "7BIT" or "8BIT". Select
either one and press . .
6
Parity setting; default is "EVN"
Press to show "PARI" in the sub display and
"EVN" in the main display.
Press . Main display content flashes.
can now be used to select "NON", "ODD", or "EVN".
Select one and press . .

3
1. COMMUNICATION SETTING PROCEDURES
7
Stop bit length setting; default is "1BIT"
Press to show "STOPB" in the sub display
and "1BIT" in the main display.
Press . Main display content flashes.
can now be used to select "1BIT" or "2BIT"
Select either one and press .
8
Communication rate setting; default is "9.6".
Press to show "BPS" in the sub display and
"9.6 (kbps)" in the main display.
Press . Main display content flashes.
can now be used to select "9.6 (kbps)", "19.2 (kbps)",
or "38.4 (kbps)". Select one and press .
9
Response delay time setting; default is "0".
Press to show "DELAY" in the sub display and
"0 (msec)" in the main display.
Press . Main display content flashes.
can now be used to select "0 (msec)", "10 (msec)",
or "20-250 (msec)" Select one and press .
10
Communication address setting; default is "1".
Press to show "ADDRS" in the sub display
and "1" in the main display.
Press . Main display content flashes.
can now be used to set address from 1-99. Select
one and press .

4
1. COMMUNICATION SETTING PROCEDURES
11
Communication mode setting; default is "RW".
Press to show "CMODE" in the sub display
and "RW" in the main display.
Press . Main display content flashes.
can now be used to select "RW" or "R". Select either
one and press .
12
When all settings are completed, press & hold
to turn TYPE V controller "OFF".
Sub display shows current time, which completes the
communication settings.
Change value can be recovered by using during setting change. (Effective before pressing
)
With the controller turned “OFF”, operation mode can be switched to remote mode by external
communication.
"REMOTE" LED illuminates while in remote mode.All keys except are disabled. Pressing
the other keys shows "REMOT" in the sub display.
By holding down during remote operation, main unit will quit remote mode and revert to
idle with the controller "OFF".

5
1. COMMUNICATION SETTING PROCEDURES
1.2: Connection
■Workstation PC
・A USB interface is used.
■USB-RS485 converter unit
・For the converter, System Sacom's "USB-RS485I RJ45-T4P" is recommended.
・By purchasing optional "external communication adapter USB-RS485I RJ45-T4P"
(product code 211880), the following connection can be made (workstation not
included).
■Communication cable connection
パソコン Ⅴ型コントローラ
USB-RS485変換アダプタ
USB-485I
通信ケーブル USB ケーブル
USBポート
本 器
Note: "External communication adapter kit" (product code 211880) includes the following:
1. USB cable: connects workstation and USB-RS485 converter unit. 1.8 m.
2. Comm cable: connects USB-RS485 converter unit to main unit terminal block. UL2464TASB
2-leadAWG20 cable.
3. USB-RS485 converter unit: System Sacom USB-485I RJ45-T4P.
Workstation PC
USB-RS485 adapter TYPE V controller
USB cable Comm cable
Main unit
USB port USB-485I

6
1. COMMUNICATION SETTING PROCEDURES
1.3: Multiple connection procedure
Shown below is an example of multi-drop wire connection.
パソコン Ⅴ型コントローラ
USB-RS485 変換アダプタ
通信ケーブル
通信ケーブル
ID:01
Ⅴ型コントローラ
Ⅴ型コントローラ
ID:02
ID:31
100Ω1/4W
終端抵抗
本 器
最大 31 台まで接続できます
Note: Terminating resistor: custom-made item.
If you prepare a terminating resistor yourself, connect a fixed resistor of 100 Ωand 1/4 W or
over in parallel to the last cable appliance terminal block.
Workstation PC
USB-RS485 converter
Comm cable
Main unit
TYPE V controller
TYPE V controller
TYPE V controller
Up to 31 units can be
connected
Comm cable
Terminating resistor
100Ω1/4W

7
2. COMMUNICATION INTERFACE
ԂCommunication protocol conforms to MODBUS and the protocol can be selected from RTU and
ASCII.
Refer to MODBUS standard specification and commercial reference manuals for details on
MODBUS.
2.1: Data transmission system
Transmission system: half-duplex asynchronous data transfer (polling/selecting)
Transmission distance: Max 500m (results may vary depending on environment)
Connection method: Multi-drop system (max 31 units)
Start bit: 1 bit
Transmission code: ASCII (ASCII mode)
Binary (RTU mode)
Error check: LRC (ASCII mode)
CRC-16 (RTU mode)
2.2: Frame configuration
In RTU mode, frame is composed of message portion only.
In ASCII mode, frame consists of start character ": (colon, 3AH)", message and end character
"CR (carriage return, ODH) + LF (line feed, 0AH)".
RTU mode: message
ASCII mode: : | message | CR | LF
2.3: Message configuration
MODBUS messages are composed of the following in both RTU andASCII modes.
Slave address
Function code
Data
Error check
2.4: Slave address
Slave address can be set from 1-99. Master normally communicates with one slave device. All
slave devices receive any message sent from the master in common, however, only the device
with slave address corresponding to the directive message responds.

8
2. COMMUNICATION INTERFACE
2.5: Function code
The function code communicates to the slave device what to execute. Function code data is
classified by type below.
Analog setting: each setting information type. Numerical value within 16 bits:
-32768 to 32767
Analog input data: measurement, status and other data. Numerical value within 16 bits.
Code
Function Unit MODBUS original function (reference)
03
Read analog settings
16 bit
Read content of maintenance register
04
Read analog input data
16 bit
Read content of input register
06
Write analog settings
16 bit
Write to single maintenance register
2.6: Data
Data configuration varies according to function code.
At the time of request from the master, data is composed of code number, data count, etc. of
target data to be read and written.
Response from the slave consists of data in relation to the request.
Basic MODBUS data is all integers of 16-bit, and the presence or absence of a sign is defined for
each data. Accordingly, by assigning a decimal to another address to convert into an integer or
fixing the decimal position, it is normalized and expressed on scale upper/lower limits.
2.7: Reference number
A reference number is assigned to data and it is necessary for reading and writing the data.
Reference number range is categorized as "analog input data" and "analog setting value"
according to data type.
Data type Reference number Relative number
Analog input data 30001-40000 Reference number -30001
Analog setting value 40001-50000 Reference number -40001
Relative number is the address number used during actual communication.

9
2. COMMUNICATION INTERFACE
2.8: Error check
Transmission frame error check differs by mode.
RTU: CRC-16
ASCII: LRC
2.8.1 CRC-16 calculation
CRC divides the information to be sent with the generating polynomial, adds the remainder
behind the information to send.
Generating polynomial is as follows:
1 + x2 + x15 + x16
Use the following procedure to calculate from slave address to final data.
1. CRC-16 data (if x) initialization (= FFFFH)
2. Exclusive OR (EX-OR) of data 1 and x. →x
3. Shift x 1 bit to the right. →x
4. If carrier appears, take A001H and EX-OR. Otherwise, go to step 5. →x
5. Repeat steps 3 and 4 until shifted 8 times
6. EX-OR of x and following data. →x
7. Same as steps 3-5
8. Repeat final data
9. Create a message of the calculated 16-bit data, ordering low to high
Example: if data is [02H] [07H], CRC-16 is 1241H; so error check data will be [41H] [12H].
2.8.2 LRC calculation
Use the following procedure to calculate from slave address to final data.
1. Create message using RTU mode
2. Add up data from heading to end. →x
3. Take the complement of x. →x
4. Add 1. (x = x+1)
5. Add x to end of message as LRC.
6. Convert in entirety to ASCII characters.
Example: if data is [02H] [07H], LRC is [F7H]; so binary message will be [02H] [07H] [F7H] and
ASCII message will be [30H] [32H] [30H] [37H] [46H] [37H].

10
2. COMMUNICATION INTERFACE
2.9: Function code details
The following is a function code exclusive response:
2.9.1Analog setting value reading
[Function code: 03 (03H)]
Only a specific quantity from the specified number "continuous number analog setting value
(2-byte: 16-bit) data" is read. The data is split into high 8-bit and low 8-bit, arranged in numerical
order and composed into response message data.
Example: readout for fixed temp operation SV setting, fixed temp auto start SV setting, fixed temp
auto start time/timer select setting for slave 1.
(slave 1 analog setting value reference numbers are 40001 to 40003 in above cases.)
Reference number
(Relative number) 40001
(0000H) 40002
(0001H) 40003
(0002H)
Data 650
(028AH) -50
(FFCEH) 0
(0000H)
<RTU mode>
<ASCII mode error check>
LRC F9H
LRC 9DH
Note: start number (relative number) is "reference number minus 40001".
Note: the number of data is the number of bytes in data; the number of requests is 3 and the
number of data is 6 in the example above.
Master →device
Device →master (normal)
Slave address 01H
Slave address 01H
Function code 03H
Function code 03H
Start number (H) 00H
Number of data 06H
Start number (L) 00H
Fixed temp SV (H) 02H
Quantity (H) 00H
Fixed temp SV (L) 8AH
Quantity (L) 03H
Fixed temp AT STA SV (H)
FFH
CRC (L) 05H
Fixed temp AT STA SV (L) CEH
CRC (H) CBH
Fixed temp timer select (H)
00H
Fixed temp timer select (L)
00H
CRC (L) E8H
CRC (H) A3H

11
2. COMMUNICATION INTERFACE
2.9.2Analog input data read-out
[Function Code: 04(04 H)]
Only a specific quantity from the specified number "continuous number analog input (2 byte : 16-bit)
data" is read.
The data is split into high 8-bit and low 8-bit, arranged in numerical order and composed into
response message data.
Response example: Same as "function code 03", only the start number (relative number) is
"reference number minus 30001".
2.9.3Analog setting value write
[Function code: 06(06 H)]
Assign analog setting value for given number to specified value.
Example: set fixed temp operation temp setting to 100 for slave 1.
<RTU mode>
Master →device Device →master (normal)
Slave address 01H Slave address 01H
Function code 06H Function code 06H
Setting value No. (L) 00H Setting value No. (L) 00H
Setting value No. (L) 00H Setting value No. (L) 00H
Setting data (H) 00H Setting data (H) 00H
Setting data (L) 64H Setting data (L) 64H
CRC (L) 88H CRC(L) 88H
CRC (H) 21H CRC(H) 21H
<ASCII mode error check>
LRC 95H LRC 95H
Note: setting value number (relative number) is "reference number minus 40001".
Note: Response will be the same as master message under normal response.

12
2. COMMUNICATION INTERFACE
2.10: Error processing
No response error
In the following cases, message is ignored and no response is sent.
1. When message transmission error (overrun, framing, parity, CRC or LRC) is detected.
2. When slave address in message is not for receiving device.
3. When message data interval is too long.
RTU...When less than 9600bps: 20msec or more
When over 9600bps: 5msec or more
ASCII...1sec or more
4. When transmission parameters are not in agreement.
5. When receiving message exceeds maximum allowable bytes.
Response error
When master message contains no error, but the following problems (see table below) occur, a
code signifying error content is sent in response as an "error message".
Slave address
Function code Function code + 80H
Function code + 80H
Error codes
CRC (L)
03 83H
CRC (H)
04 84H
06 86H
2.11: Transmission error codes
Transmission error codes are as follows:
Error Codes Description
01H Function code error
Irregular/incorrect function code is received
02H Relative number (reference number) error
Irregular/incorrect start number or setting value number is received
03H
Incorrect number of data pieces
・Number of data exceeds the specified number for data to be transmitted
in response to received message
・The number of request is 0
・Number of specified data received and actual number of data are not in
agreement
11H Setting value out of range
Setting value is outside the range defined in the reference table
12H Setting not available

13
3. REMOTE OPERATION VIA COMMUNICATION
3.1: Start remote mode
・Remote mode can start only when the controller is OFF state.
・Start remote mode by specifying operation mode (fixed temp operation, program operation, auto
start, auto stop, or program auto start). However, when program operation or program auto start
is selected, remote mode cannot be started unless the following condition is satisfied.
Operation mode Remote mode start conditions
Program operation
Program patterns for the operation are specified.
Program auto start
Program pattern for auto start is specified.
3.2: End remote mode
・When remote mode ends, regardless of the remote operation state (standby/running/end) main
unit terminates operation and set remote operation state in standby, then quit remote mode.
After remote mode ends, the controller will be turned OFF (shows power OFF screen).
3.3: Remote operation start/stop
・When starting remote operation during standby or at the end of operation, main unit starts
remote operation with operation mode and setting value set at that point.
・Remote operation is stopped by transmitting remote operation stop command during remote
operation.
3.4: Operation mode change in remote mode
・The operation mode can be changed to another during standby or at the end of operation.
However, when changing the operation mode to program operation or program auto-start, the
mode change cannot be completed unless the following condition is satisfied.
Operation mode Operating mode change conditions
Program operation
Program patterns for the operation are specified.
Program auto start
Program pattern for auto start is specified.

14
3. REMOTE OPERATION VIA COMMUNICATION
3.5: Key operation in remote mode
・All key operations on the controller are disabled in remote mode except power OFF operation
by holding down the POWER key. When pressing any keys other than the POWER key,
display indicates that main unit is in remote mode and buzzer sounds. This indication will show
for one second, and then the display returns to the previous screen.
3.6: Recovery from power outage in remote mode
・The power recovery operation in remote mode is the same as that in local mode.

15
4. COMMUNICATION REFERENCE TABLE
External communication
When using external communication option on any unit, access by anything other
than the following reference addresses, may cause equipment malfunction. Do not
attempt to use any reference address, code or utility other than those given below
or as recommended by Yamato Scientific Co., Ltd. Do not access functions that are
not mentioned in the controller keys operation (see main unit instruction manual).
Unit may malfunction or become out of control.
4.1: Function code 03/06
TYPE V Controller Communication Reference table; items with “*” are not applicable by model
Reference
No. FNC
Code
R/W
Data name Setting range
(in-transmission)
Initial
value
Remarks
40001 03
06 R
W
Fixed temp operation
SV setting SLL-SLH 0.0℃
◆Corrected within the
range between SLL and
SLH
40002 03
06 R
W
Fixed temp auto start
SV setting SLL-SLH 0.0℃
◆Corrected within the
range between SLL and
SLH
40003 03
06 R
W
Fixed temp auto start
time/timer select Timer/time
(0/1) Timer
40004 03
06 R
W
Fixed temp auto start
time setting (H) 00-99
(0-99) 00 H: hour
40005 03
06 R
W
Fixed temp auto start
timer setting (L) 00-59
(0-59) 00 L: minute
40006 03
06 R
W
Fixed temp auto start
time setting (H) 00-23
(0-23) 00 H: hour
40007 03
06 R
W
Fixed temp auto start
time setting (L) 00-59
(0-59) 00 L: minute
40008 03
06 R
W
Fixed temp auto stop
SV setting SLL-SLH 0.0℃
◆Corrected within the
range between SLL and
SLH
40009 03
06 R
W
Fixed temp auto stop
timer/time select Timer/time
(0/1) Timer
40010 03
06 R
W
Fixed temp auto stop
timer setting (H) 00-99
(0-99) 00 H: hour

16
4. COMMUNICATION REFERENCE TABLE
Reference
No. FNC
Code
R/W
Data name Setting range
(in-transmission)
Initial
value
Remarks
40011 03
06 R
W
Fixed temp auto stop
timer setting (L) 00-59
(0-59) 00 L: minute
40012 03
06 R
W
Fixed temp auto stop
time setting (H) 00-23
(0-23) 00 H: hour
40013 03
06 R
W
Fixed temp auto stop
time setting (L) 00-59
(0-59) 00 L: minute
40014 03
06 R
W
Fixed temp quick auto
stop timer/time select Timer/time
(0/1) Timer
40015 03
06 R
W
Fixed temp quick auto
stop timer setting (H) 00-99
(0-99) 00 H: hour
40016 03
06 R
W
Fixed temp quick auto
stop timer setting (L) 00-59
(0-59) 00 L: minute
40017 03
06 R
W
Fixed temp quick auto
stop time setting (H) 00-23
(0-23) 00 H: hour
40018 03
06 R
W
Fixed temp quick auto
stop time setting (L) 00-59
(0-59) 00 L: minute
40019 03
06 R
W
Program operation
pattern no. setting 0-99
(0-99) 0 ◆Setting not available
while program operation
is running
40020 03
06 R
W
Program operation auto
start pattern no. setting
0-99
(0-99) 0 ◆
Setting not available while
auto start timer is
counting
40021 03
06 R
W
Program auto start
timer/time select Timer/time
(0/1) Timer
40022 03
06 R
W
Program auto start timer
setting (H) 00-99
(0-99) 00 H: hour
40023 03
06 R
W
Program auto start timer
setting (L) 00-59
(0-59) 00 L: minute

17
4. COMMUNICATION REFERENCE TABLE
Reference
No. FNC
Code
R/W
Data name Setting range
(in-transmission)
Initial
value
Remarks
40024 03
06 R
W
Program auto start time
setting (H) 00-23
(0-23) 00 H: hour
40025 03
06 R
W
Program auto start time
setting (L) 00-59
(0-59) 00 L: minute
40027 03 R
Accumulated power
consumption (KW/h) 0-999KW/h
(0-999) 0 KW/h
40028 03 R
Accumulated power
consumption (MW/h) 0-999MW/h
(0-999) 0
MW/h
40029 03 R
Accumulated CO2
emissions (Kg) 0-999Kg
(0-999) 0 Kg
40030 03 R
Accumulated CO2
emissions (t) 0-999t
(0-999) 0 t
40031 03 R
Output MV 0.0-100.0%
(0-1000) 0.0%
40032 03 R
Accumulated time:
total power-on time Max: 65535h
(0-65535) 0h
40033 03 R
Accumulated time:
total operation time Max: 65535h
(0-65535) 0h
40034 03 R
Present power
consumption 0.0-999.9KW/h
(0-9999) 0 KW/h

18
4. COMMUNICATION REFERENCE TABLE
Reference
No. FNC
Code
R/W
Data name Setting range
(in-transmission)
Initial
value Remarks
41001 03
06 R
W
Keypad lock setting OFF/MLOC/
FLOC/ON
(0/1/2/3) OFF
41002 03
06 R
W
Buzzer sound setting
ON/
CLK (click off)/
OFF
(0/1/2)
ON
41003 03
06 R
W
Calendar setting
(Year) 2010-2099
(10-99) 2010
41004 03
06 R
W
Calendar setting
(Month) 1-12
(1-12) 1
41005 03
06 R
W
Calendar setting
(day) 1-31
(1-31) 1
41006 03
06 R
W
Calendar setting
(Hour) 0-23
(0-23) 0
41007 03
06 R
W
Calendar setting
(minute) 0-59
(0-59) 0 ◆Seconds are fixed at 0
41008 03
06 R
W
Refrigerator control
function select
NON/2P/
CYC/CNT
(0/1/2/3) 2P *
41009 03
06 R
W
Refrigerator cycle
operation ON-time
setting
0-120min
(0-120) 30min *
41010 03
06 R
W
Refrigerator cycle
operation OFF-time
setting
0-120min
(0-120) 10min Restart protective time ≦
OFF-time*
41011 03
06 R
W
Defrost operation mode
setting
NON (none)/
CLK (time)/
TIME (time)
(0/1/2)
NON Auto setting*
41012 03
06 R
W
Defrost operation start
time setting (H) 00-23
(0-23) 00 H: hour*
41013 03
06 R
W
Defrost operation start
time setting (L) 00-59
(0-59) 00 L: minute*
Table of contents
Popular Controllers manuals by other brands
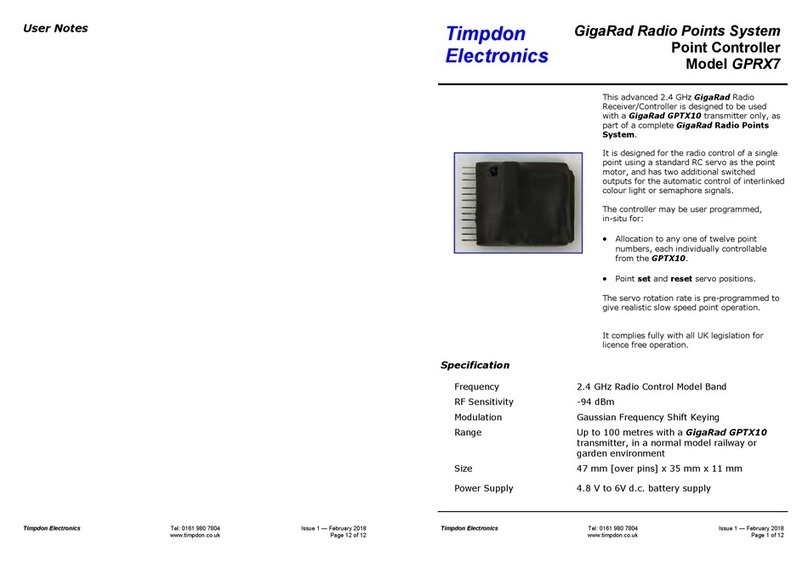
Timpdon Electronics
Timpdon Electronics GPRX7 quick start guide

Johnson Controls
Johnson Controls VMA1615 installation instructions
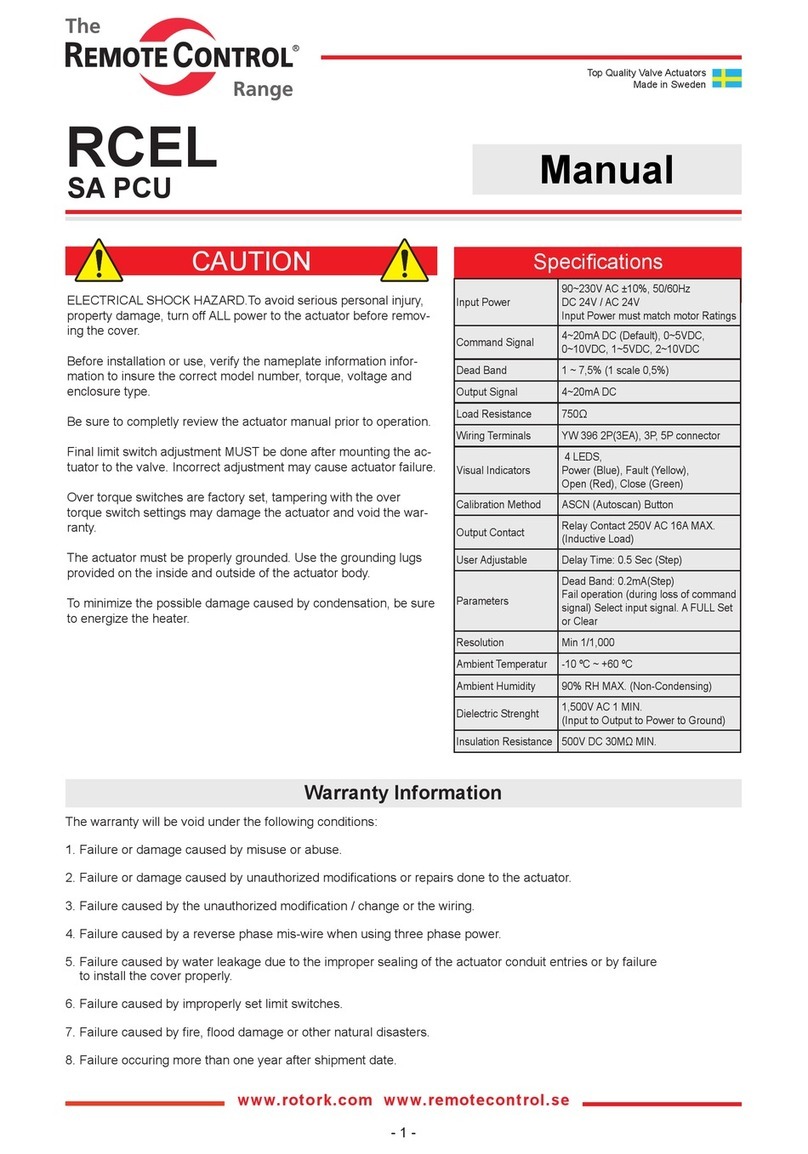
rotork
rotork Remote Control Series manual
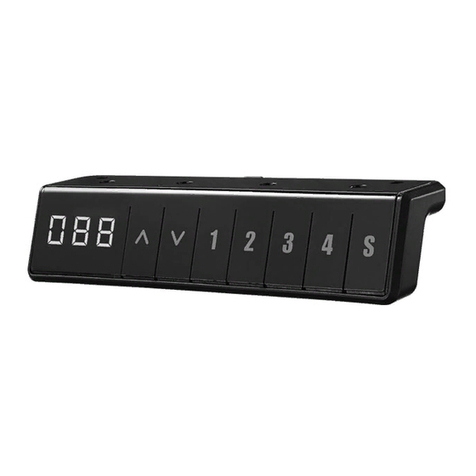
Timotion
Timotion TDH6 user manual

Safeline
Safeline ProLink manual
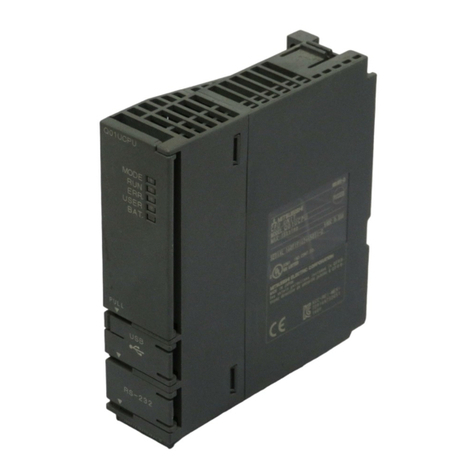
Mitsubishi Electric
Mitsubishi Electric MELSEC-Q00U(J)CPU user manual