YOKOGAWA F3SP71-4S User manual

User’s
Manual
Sequence CPU - Modbus/TCP Functions
IM 34M06P15-03E
Applicable Modules:
Model Code Model Name
F3SP71-4S Sequence CPU Module (with network functions)
F3SP76-7S Sequence CPU Module (with network functions)
IM 34M06P15-03E
2nd Edition
Yokogawa Electric Corporation

Blank PageBlank Page

i
Media No. IM 34M06P15-03E (CD) 2nd Edition : Jan. 31, 2012 (YHQ) IM 34M06P15-03E 2nd Edition: Jan. 31, 2012-00
All Rights Reserved Copyright ©2011, Yokogawa Electric Corporation
Applicable Product
Range-free Multi-controller FA-M3
Model code Name
F3SP71-4S Sequence CPU Module (with network functions)
F3SP76-7S Sequence CPU Module (with network functions)
The document number and document model code for this manual are given below.
Refer to the document number in all communications, including when purchasing
additional copies of this manual.
Document No. : IM 34M06P15-03E
Document Model Code : DOCIM

ii
IM 34M06P15-03E 2nd Edition: Jan. 31, 2012-00
Important
About This Manual
- This Manual should be passed on to the end user.
- Before using the controller, read this manual thoroughly to have a clear
understanding of the controller.
- This manual explains the functions of this product, but there is no guarantee that
they will suit the particular purpose of the user.
- Under absolutely no circumstances may the contents of this manual be transcribed
or copied, in part or in whole, without permission.
- The contents of this manual are subject to change without prior notice.
- Every effort has been made to ensure accuracy in the preparation of this manual.
However, should any errors or omissions come to the attention of the user, please
contact the nearest Yokogawa Electric representative or sales office.
Safety Precautions when Using/Maintaining the Product
- The following safety symbols are used on the product as well as in this manual.
Danger. This symbol on the product indicates that the operator must follow the
instructions laid out in this user’s manual to avoid the risk of personnel injuries,
fatalities, or damage to the instrument. Where indicated by this symbol, the manual
describes what special care the operator must exercise to prevent electrical shock
or other dangers that may result in injury or the loss of life.
Protective Ground Terminal. Before using the instrument, be sure to ground this
terminal.
Function Ground Terminal. Before using the instrument, be sure to ground this
terminal.
Alternating current. Indicates alternating current.
Direct current. Indicates direct current.

iii
IM 34M06P15-03E 2nd Edition: Jan. 31, 2012-00
The following symbols are used only in the user’s manual.
WARNING
Indicates a “Warning”.
Draws attention to information essential to prevent hardware damage, software
damage or system failure.
CAUTION
Indicates a “Caution”
Draws attention to information essential to the understanding of operation and
functions.
TIP
Indicates a “TIP”
Gives information that complements the present topic.
SEE ALSO
Indicates a “SEE ALSO” reference.
Identifies a source to which to refer.
- For the protection and safe use of the product and the system controlled by it, be
sure to follow the instructions and precautions on safety stated in this manual
whenever handling the product. Take special note that if you handle the product in
a manner other than prescribed in these instructions, the protection feature of the
product may be damaged or impaired. In such cases, Yokogawa cannot guarantee
the quality, performance, function and safety of the product.
- When installing protection and/or safety circuits such as lightning protection devices
and equipment for the product and control system as well as designing or installing
separate protection and/or safety circuits for fool-proof design and fail-safe design of
processes and lines using the product and the system controlled by it, the user
should implement it using devices and equipment, additional to this product.
- If component parts or consumable are to be replaced, be sure to use parts specified
by the company.
- This product is not designed or manufactured to be used in critical applications
which directly affect or threaten human lives and safety — such as nuclear power
equipment, devices using radioactivity, railway facilities, aviation equipment,
shipboard equipment, aviation facilities or medical equipment. If so used, it is the
user’s responsibility to include in the system additional equipment and devices that
ensure personnel safety.
- Do not attempt to modify the product.
Exemption from Responsibility
- Yokogawa Electric Corporation (hereinafter simply referred to as Yokogawa Electric)
makes no warranties regarding the product except those stated in the WARRANTY
that is provided separately.
- Yokogawa Electric assumes no liability to any party for any loss or damage, direct or
indirect, caused by the use or any unpredictable defect of the product.

iv
IM 34M06P15-03E 2nd Edition: Jan. 31, 2012-00
Software Supplied by the Company
- Yokogawa Electric makes no other warranties expressed or implied except as
provided in its warranty clause for software supplied by the company.
- Use the software with one computer only. You must purchase another copy of the
software for use with each additional computer.
- Copying the software for any purposes other than backup is strictly prohibited.
- Store the original media that contain the software in a safe place.
- Reverse engineering, such as decompiling of the software, is strictly prohibited.
- Under absolutely no circumstances may the software supplied by Yokogawa Electric
be transferred, exchanged, or sublet or leased, in part or as a whole, for use by any
third party without prior permission by Yokogawa Electric.

v
IM 34M06P15-03E 2nd Edition: Jan. 31, 2012-00
General Requirements for Using the FA-M3 Controller
Avoid installing the FA-M3 controller in the following locations:
- Where the instrument will be exposed to direct sunlight, or where the operating
temperature exceeds the range 0°C to 55°C (32°F to 131°F).
- Where the relative humidity is outside the range 10 to 90%, or where sudden
temperature changes may occur and cause condensation.
- Where corrosive or flammable gases are present.
- Where the instrument will be exposed to direct mechanical vibration or shock.
- Where the instrument may be exposed to extreme levels of radioactivity.
Use the correct types of wire for external wiring:
- Use copper wire with temperature ratings greater than 75°C.
Securely tighten screws:
- Securely tighten module mounting screws and terminal screws to avoid problems
such as faulty operation.
- Tighten terminal block screws with the correct tightening torque as given in this
manual.
Securely lock connecting cables:
- Securely lock the connectors of cables, and check them thoroughly before turning
on the power.
Interlock with emergency-stop circuitry using external relays:
- Equipment incorporating the FA-M3 controller must be furnished with emergency-
stop circuitry that uses external relays. This circuitry should be set up to interlock
correctly with controller status (stop/run).
Ground for low impedance:
- For safety reasons, connect the [FG] grounding terminal to a Japanese Industrial
Standards (JIS) Class D (earlier called Class 3) Ground*1 . For compliance to CE
Marking, use braided or other wires that can ensure low impedance even at high
frequencies for grounding.
*1 Japanese Industrial Standard (JIS) Class D Ground means grounding resistance of 100 Ωmax.
Configure and route cables with noise control considerations:
- Perform installation and wiring that segregates system parts that may likely become
noise sources and system parts that are susceptible to noise. Segregation can be
achieved by measures such as segregating by distance, installing a filter or
segregating the grounding system.
Configure for CE Marking Conformance:
-For compliance to CE Marking, perform installation and cable routing according to
the description on compliance to CE Marking in the “Hardware Manual”
(IM 34M06C11-01E).

vi
IM 34M06P15-03E 2nd Edition: Jan. 31, 2012-00
Keep spare parts on hand:
- We recommend that you stock up on maintenance parts including spare modules.
- Preventive maintenance (replacement of the module or its battery) is required for
using the module beyond 10 years. For enquiries on battery replacement service
(for purchase), contact your nearest Yokogawa Electric representative or sales
office. (The module has a built-in lithium battery. Lithium batteries may exhibit
decreased voltage, and in rare cases, leakage problems after 10 years.)
Discharge static electricity before operating the system:
- Because static charge can accumulate in dry conditions, first touch grounded metal
to discharge any static electricity before touching the system.
Never use solvents such as paint thinner for cleaning:
- Gently clean the surfaces of the FA-M3 controller with a cloth that has been soaked
in water or a neutral detergent and wringed.
- Do not use volatile solvents such as benzine or paint thinner or chemicals for
cleaning, as they may cause deformity, discoloration, or malfunctioning.
Avoid storing the FA-M3 controller in places with high temperature or
humidity:
- Since the CPU module has a built-in battery, avoid storage in places with high
temperature or humidity.
- Since the service life of the battery is drastically reduced by exposure to high
temperatures, take special care (storage temperature should be from -20°C to
75°C).
- There is a built-in lithium battery in a CPU module and temperature control module
which serves as backup power supply for programs, device information and
configuration information. The service life of this battery is more than 10 years in
standby mode at room temperature. Take note that the service life of the battery
may be shortened when installed or stored at locations of extreme low or high
temperatures. Therefore, we recommend that modules with built-in batteries be
stored at room temperature.
Always turn off the power before installing or removing modules:
- Failing to turn off the power supply when installing or removing modules, may result
in damage.
Do not touch components in the module:
- In some modules you can remove the right-side cover and install ROM packs or
change switch settings. While doing this, do not touch any components on the
printed-circuit board, otherwise components may be damaged and modules may fail
to work.
Do not use unused terminals:
- Do not connect wires to unused terminals on a terminal block or in a connector.
Doing so may adversely affect the functions of the module.

vii
IM 34M06P15-03E 2nd Edition: Jan. 31, 2012-00
Waste Electrical and Electronic Equipment
Waste Electrical and Electronic Equipment (WEEE), Directive 2002/96/EC
(This directive is only valid in the EU.)
This product complies with the WEEE Directive (2002/96/EC) marking requirement.
The following marking indicates that you must not discard this electrical/electronic
product in domestic household waste.
Product Category
With reference to the equipment types in the WEEE directive Annex 1, this product is
classified as a “Monitoring and Control instrumentation” product.
Do not dispose in domestic household waste.
When disposing products in the EU, contact your local Yokogawa Europe B. V. office.
How to Discard Batteries
The following description on DIRECTIVE 2006/66/EC (hereinafter referred to as the EU
new directive on batteries) is valid only in the European Union.
Some models of this product contain batteries that cannot be removed by the user.
Make sure to dispose of the batteries along with the product.
Do not dispose in domestic household waste.
When disposing products in the EU, contact your local Yokogawa Europe B. V. office.
Battery type: Lithium battery
Note: The symbol above means that the battery must be collected separately as
specified in Annex II of the EU new directive on batteries.

viii
IM 34M06P15-03E 2nd Edition: Jan. 31, 2012-00
Introduction
Overview of the Manual
This manual explains the commands and responses for communication control with
higher-order computers via Modbus/TCP and with the sequence CPU module used with
the FA-M3 (F3SP71-4S, F3SP76-7S).
Related User’s Manuals
Depending on the type of the CPU module, you should refer to different user's manuals.
zAbout functions
- Sequence CPU Instruction Manual - Functions (for F3SP71-4N/4S, F3SP76-7N/7S)
(IM 34M06P15-01E)
- Sequence CPU - Network Functions (for F3SP71-4N/4S, F3SP76-7N/7S)
(IM 34M06P15-02E)
zTo create ladder programs
- FA-M3 Programming Tool WideField3 (IM 34M06Q16-E)
Refer to the following manuals, if required.
zFor FA-M3 specifications and configuration*1, installation and wiring,
test run, maintenance and inspection or system-wide restrictions on
module installation
*1: For specification of products other than the power supply module, base module, input/output module, cable, and
terminal unit, refer to the respective product manuals.
- Hardware Manual (lM 34M06C11-01E)
F3SP71
F3SP76

ix
IM 34M06P15-03E 2nd Edition: Jan. 31, 2012-00
Copyrights and Trademarks
Copyrights
Copyrights of the programs and online manual included in this CD-ROM belong to
Yokogawa Electric Corporation.
This online manual may be printed but PDF security settings have been made to prevent
alteration of its contents.
This online manual may only be printed and used for the sole purpose of operating this
product. When using a printed copy of the online manual, pay attention to possible
inconsistencies with the latest version of the online manual. Ensure that the edition
agrees with the latest CD-ROM version.
Copying, passing, selling or distribution (including transferring over computer networks)
of the contents of the online manual, in part or in whole, to any third party, is strictly
prohibited. Registering or recording onto videotapes and other media is also prohibited
without expressed permission of Yokogawa Electric Corporation.
Trademarks
- Ethernet is a registered trademark of XEROX Corporation.
- Modbus is a registered trademark of Schneider Electric.
- The trade and company names that are referred to in this document are either
trademarks or registered trademarks of their respective companies.

Blank Page

TOC-1
IM 34M06P15-03E 2nd Edition
FA-M3
Sequence CPU - Modbus/TCP Functions
CONTENTS
Applicable Product ....................................................................................i
Important ...................................................................................................ii
Introduction............................................................................................viii
Copyrights and Trademarks ...................................................................ix
1. Overview ....................................................................................... 1-1
1.1 Overview of Modbus/TCP Slave Function ............................................ 1-1
1.2 System Configuration of Modbus/TCP Slave Function....................... 1-2
2. Modbus/TCP Slave Function ....................................................... 2-1
2.1 Specifications .......................................................................................... 2-1
Functional Specifications.................................................................... 2-1
Communication Functions.................................................................. 2-1
2.2 Communication Protocol........................................................................ 2-1
2.3 Data Frames ............................................................................................ 2-2
2.4 Function Codes ....................................................................................... 2-3
Support Function Codes .................................................................... 2-3
PDU Configuration ............................................................................. 2-4
2.5 Response Error Code ............................................................................. 2-5
2.6 Modbus Device Allocation Specifications ........................................... 2-6
Modbus Device List............................................................................ 2-6
Modbus Device Associations ............................................................. 2-7
2.7 Specifying Devices in Commands....................................................... 2-12
List of Supported Devices ................................................................ 2-12
2.8 Modbus/TCP Slave Function Settings................................................ 2-13
Required Settings............................................................................. 2-13
Settings Specified as Necessary...................................................... 2-14
2.9 Using Modbus/TCP Slave Function via Ethernet .............................. 2-15
Connecting to a Monitor ................................................................... 2-15
Connecting to a PC .......................................................................... 2-15
3. Command/Response Details ....................................................... 3-1
3.1 Read Coils ($01) ...................................................................................... 3-1
3.2 Read Discrete Inputs ($02) ..................................................................... 3-2
3.3 Read Holding Registers ($03) ................................................................ 3-3
IM 34M06P15-03E 2nd Edition: Jan. 31, 2012-00

TOC-2
IM 34M06P15-03E 2nd Edition: Jan. 31, 2012-00
3.4 Read Input Registers ($04) ..................................................................... 3-4
3.5 Write Single Coil ($05)............................................................................. 3-5
3.6 Write Single Register ($06)..................................................................... 3-6
3.7 Write Multiple Coils ($0F) ....................................................................... 3-7
3.8 Write Multiple Registers ($10) ................................................................ 3-8
3.9 Read File Record ($14)............................................................................ 3-9
3.10 Write File Record ($15) ......................................................................... 3-11
3.11 Mask Write Register ($16)..................................................................... 3-13
3.12 Read/Write Multiple Registers ($17) .................................................... 3-14
3.13 Read FIFO Queue ($18)......................................................................... 3-15
Revision Information .................................................................................i

1-1
IM 34M06P15-03E 2nd Edition: Jan. 31, 2012-00
1. Overview
This manual describes only the Modbus/TCP server (slave) function (hereinafter
referred to as "Modbus/TCP slave function").
CAUTION
F3SP7-S does not have the Modbus/TCP client (master) function.
1.1 Overview of Modbus/TCP Slave Function
The Modbus/TCP slave function is for connecting FA-M3 to a Modbus network. It
enables Modbus communication to receive process requests from a master
device via Ethernet lines under Modbus commands. As no programming is
required on the module end, this greatly simplifies creation of SCADA
applications on the monitor or PC.
In this module, the Modbus/TCP slave function can be used via the 10BASE-T
/100BASE-TX connector located on its front panel.
Ethernet
SCADA
FA-M3
Modbus Command
F010101.VSD
Ethernet
FA-M3
Modbus Command
Monitor (Touch Panel)
10BASE-T/100BASE-TX
Connector
Figure 1.1.1 Example Configuration of Modbus/TCP Slave Function

1-2
IM 34M06P15-03E 2nd Edition: Jan. 31, 2012-00
1.2 System Configuration of Modbus/TCP
Slave Function
This section describes the system configuration of the Modbus/TCP slave
function.
zConfiguration via Ethernet
In this system configuration, connection is via the 10BASE-T/100BASE-TX connector
located on the front panel of the module. A monitor or PC is connected using
Modbus/TCP application protocol.
F010102.VSD
FA-M3
Modbus Command
Ethernet
SCADA
10BASE-T/100BASE-TX
Connector
Figure 1.2.1 Example Configuration of Modbus/TCP Slave Function via Ethernet
Table 1.2.1 Supported Modbus Slave Functions
Function Description Support
Serial communication Modbus communication via Serial communication No
Ethernet communication Modbus communication via Ethernet Yes
Write-protect function Function that prohibits device writing using
Modbus commands.
Yes
1.

2-1
IM 34M06P15-03E 2nd Edition: Jan. 31, 2012-00
2. Modbus/TCP Slave Function
This chapter describes the Modbus/TCP slave function via Ethernet.
2.1 Specifications
This section describes the functional and communication specifications of the
Modbus/TCP slave function.
Functional Specifications
The following table shows the functional specifications of the Modbus/TCP slave
function.
Table 2.1.1 Supported Modbus Slave Functions
Function Description Support
Serial communication Modbus communication via Serial
communication
No
Ethernet communication Modbus communication via Ethernet Yes
Write-protect function Function that prohibits device writing
using Modbus commands.
Yes
Communication Functions
The following table shows the communication specifications of the Modbus/TCP slave
function.
Table 2.1.2 Specifications of Higher-level Link Service Provided by Modbus/TCP Slave
Function (Ethernet)
Specification Item Specification
Communications
protocol
TCP/IP
Maximum number of
connections
8
(Total amount of TCP/IP connections of higher-level link
services)
Port number 502 ($01F6)
Command data format Binary
2.2 Communication Protocol
In Modbus/TCP frame, the module returns one response to each request received from
a higher-level computer (monitor or PC).
F020201.VSD
MBAP
Header Data
Sending
station
Receiving
station
Modbus/TCP Application Protocol
Function Code
MBAP Header : Modbus Application Header
MBAP
Header Data
Function Code
Figure 2.2.1 Communication Protocol

2-2
IM 34M06P15-03E 2nd Edition: Jan. 31, 2012-00
2.3 Data Frames
The specifications of the Modbus/TCP data frames are as shown below.
F020301.VSD
Ethernet
Header
IP
Header
TCP
Header
Application Data
(Modbus/TCP ADU) FCS
MBAP Header PDU
Transaction
ID
Protocol
ID Length Unit ID Function
Code Data
Figure 2.3.1 Modbus/TCP Data Frames
zMBAP Header
The Modbus Application Protocol (MBAP) header consists of seven bytes.
Table 2.3.1 MBAP Header
Name Size Description
Transaction ID 2-byte Freely selected value is specified to identify transactions of the master device.
The slave returns the received value.
Protocol ID 2-byte "0" is specified if using the Modbus/TCP application protocol.
Length 2-byte Byte count from after the unit ID.
Unit ID 1-byte Used by the master when specifying the slave connected to another line via a
gateway or similar method.
Specifies the CPU number (1 to 4) executing commands.*1
The slave returns the received value.
*1: The CPUs that can be specified are the sequence CPU F3SP22/28/38/53/58/59/66/67/71/76. It cannot be executed
for other CPUs.
Tip
"1" is specified for the unit ID if the access target is the CPU inserted into slot 1.
"2" is specified for the unit ID if the access target is the CPU inserted into slot 2 with the CPU
connected using Modbus/TCP is inserted in slot 1.
zPDU
The Protocol Data Unit (PDU) is configured as follows.
Table 2.3.2 PDU
Name Size Description
Function code 1-byte Processing contents for the slave from the master.
Data 1 to 252 bytes Parameters for the function code.

2-3
IM 34M06P15-03E 2nd Edition: Jan. 31, 2012-00
2.4 Function Codes
This section describes the Modbus function codes.
Support Function Codes
The functions codes supported by this module are as shown below.
Table 2.4.1 Function Code List
Function
Code
Name Description Supported
01 ($01) Read Coils Consecutively reads the status of a max. of
2,000 coils.
Yes
02 ($02) Read Discrete Inputs Consecutively reads the status of a max. of
2,000 inputs.
Yes
03 ($03) Read Holding Registers Consecutively reads the status of a max. of 125
holding registers.
Yes
04 ($04) Read Input Registers Consecutively reads the status of a max. of 125
input registers.
Yes
05 ($05) Write Single Coil Writes a single coil. Yes
06 ($06) Write Single Register Writes a single register. Yes
15 ($0F) Write Multiple Coils Consecutively writes the status of a max. of
1,968 coils.
Yes
16 ($10) Write Multiple Registers Consecutively writes the status of a max. of 123
registers.
Yes
20 ($14) Read File Record Reads a max. of 124 file records. Yes
21 ($15) Write File Record Writes a max. of 122 file records. Yes
22 ($16) Mask Write Register Mask a single register with AND or OR. Yes
23 ($17) Read/Write Multiple Registers Reads and writes multiple registers. Yes
24 ($18) Read FIFO Queue Reads FIFO tables. Yes

2-4
IM 34M06P15-03E 2nd Edition: Jan. 31, 2012-00
PDU Configuration
This subsection describes the configuration of function codes and data.
zSpecifying Device Numbers in PDU
"(Device number) - 1" is specified in the PDU for setting a device number.
The above does not apply to file and record numbers specified at Read/Write File
Record command.
F020401.VSD
Example: If the status of holding register no. 32 is single-word read at Read Holding
Registers ($03).
Function Code Data
$03 Starting Holding Register No.
$001F
Read Points
$0001
31 ($001F) is specified as the starting
address of the holding register for reading
holding register no.32.
Figure 2.4.1 Specifying Device Numbers
Device numbers stored in responses are request command device numbers.
Tip
$0000 is used in the PDU for specifying the starting coil number 00001 corresponding to I0001.
zHow to Read the Format
This subsection explains how to read the request/response format block diagram.
F020402.VSD
Function Code Data
$01
1-byte 2-byte 2-byte
Starting Coil Nos.
($0000 to $FFFF)
Read Points
($0001 to $07D0)
Area Name
Frame Contents
Settings/Storage
Range
Area Size
Figure 2.4.2 How to Read Format
This manual suits for next models
1
Table of contents
Other YOKOGAWA Computer Hardware manuals
Popular Computer Hardware manuals by other brands
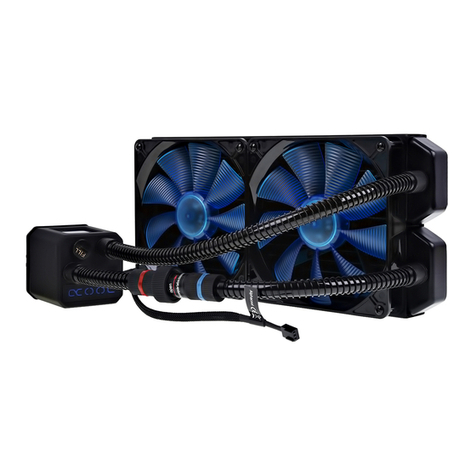
Alphacool
Alphacool Eisbaer 280 manual
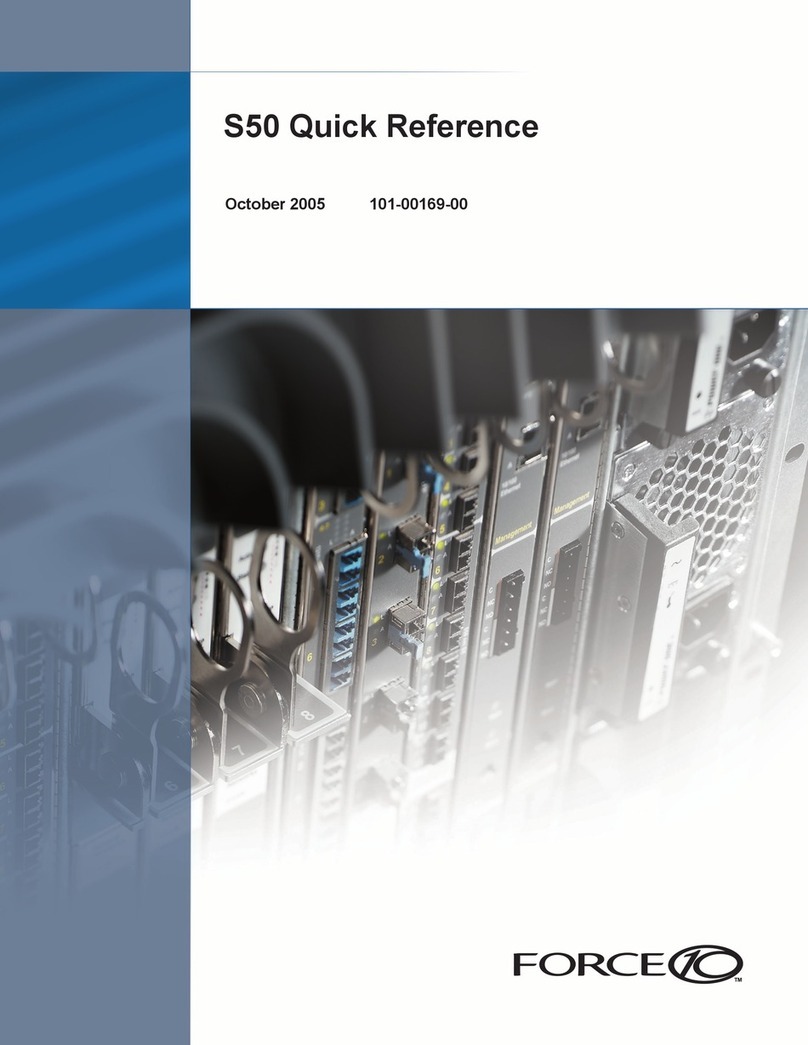
Force 10
Force 10 S50 quick reference
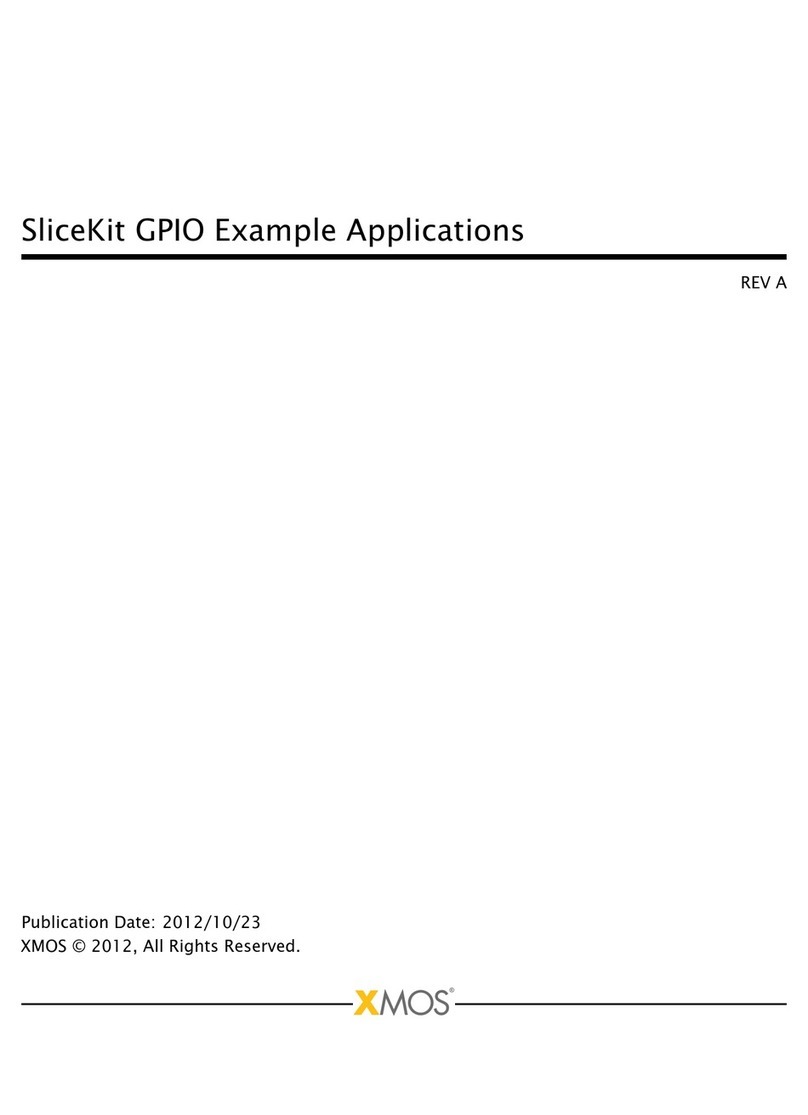
XMOS
XMOS SliceKit GPIO GPIO Example Applications
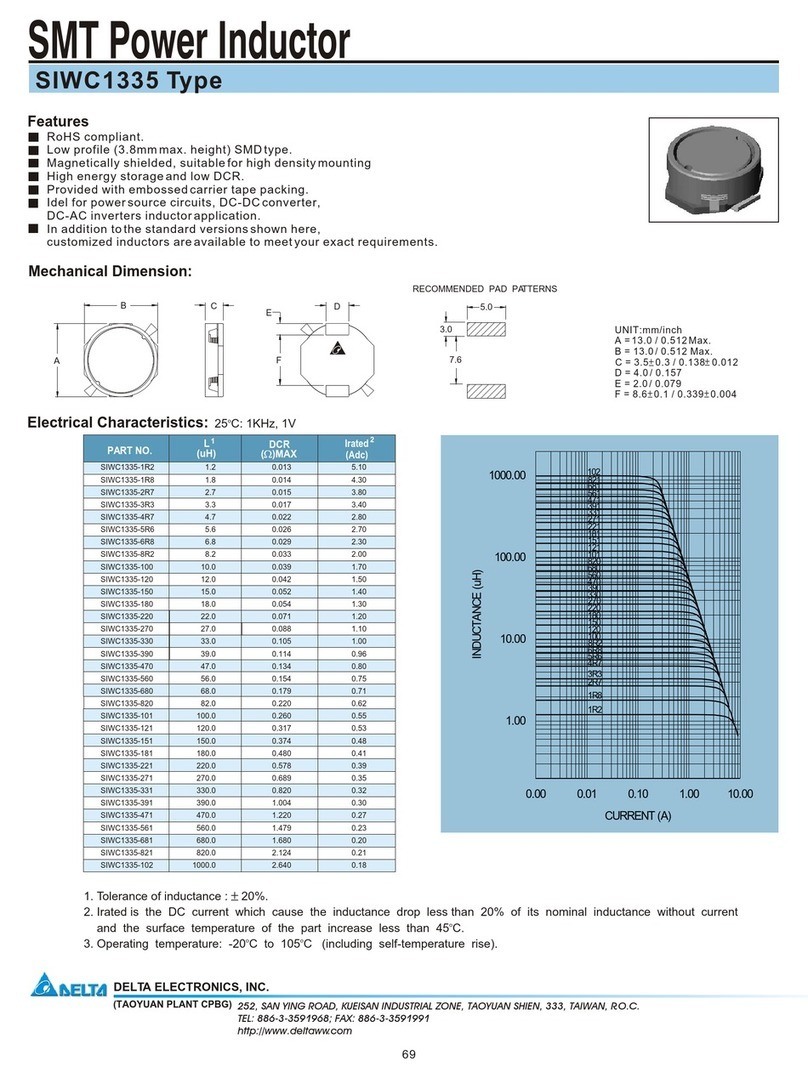
Delta Electronics
Delta Electronics SMT Power Inductor SIWC1335 Specifications

aquilar
aquilar AquiTron AT-MZA-EXP installation instructions
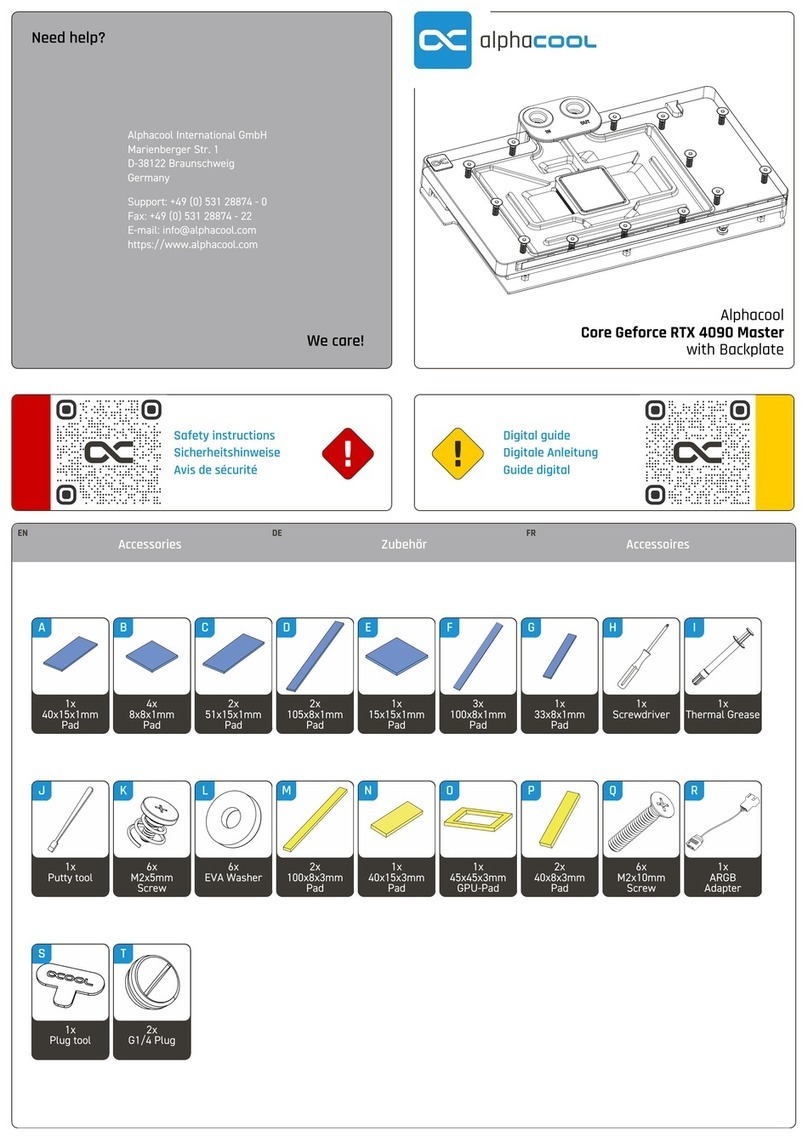
Alphacool
Alphacool Core Geforce RTX 4090 Master quick start guide