Zero RPC-2 User manual

NOTICE TO PURCHASERS AND USERS OF OUR PRODUCTS
AND THIS INFORMATIONAL MATERIAL
The products described in this material, and the information relating to
those products, is intended for knowledgeable, experienced users of
abrasive blasting equipment.
No representation is intended or made as to the suitability of the
products described herein for any particular purpose of application. No
representations are intended or made as to the efficiency, production
rate, or the useful life of the products described herein. Any estimate
regarding production rates or production finishes are the responsibility
of the user and must be derived solely from the user’s experience and
expertise, and must not be based on information in this material.
The products described in this material may be combined by the user in
a variety of ways for purposes determined solely by the user. No
representations are intended or made as to the suitability or
engineering balance of the combination of products determined by the
user in his selection, nor as to the compliance with regulations or
standard practice of such combinations of components or products.
It is the responsibility of the knowledgeable, experienced users of the
products mentioned in this material to familiarize themselves with the
appropriate laws, regulations and safe practices that apply to these
products, equipment that is connected to these products, and materials
that may be used with these products.
It is the responsibility of the user to insure that proper training of
operators has been performed and a safe work environment is
provided.
Our company is proud to provide a variety of products to the abrasive
blasting industry, and we have confidence that the professionals in our
industry will utilize their knowledge and expertise in the safe efficient
use of these products.
RPC-2
REVERSE PULSE DUST COLLECTOR
Clemco Industries Corp. One Cable Car Drive Washington, MO 63090
Phone: (636) 239-4300 Fax: (800) 726-7559
Email: info@clemcoindustries.com
OWNER’S MANUAL
© 2012 Clemco Industries Corp. Stock No.: 22788 Manual No.: 2083-0899 Date of Issue: Aug. 1999, Rev. D, 01-12

RPC-2 REVERSE PULSE DUST COLLECTOR Page 1
© 2012 CLEMCO INDUSTRIES CORP. www.clemcoindustries.com Manual No. 22788
1.0 INTRODUCTION
1.1 Scope of Manual
1.1.1 These instructions cover the assembly,
installation, operation and maintenance of Clemco
RPC-2 Reverse Pulse Dust Collectors.
1.1.2 These instructions also contain important
information required for safe operation of the collector
when used with a blast cabinet. Before using the cabinet
all personnel involved with the cabinet operation must
read this entire manual. Refer to the appropriate manual
for operation of the blast cabinet.
1.2 Safety Alerts
1.2.1 Clemco uses safety alert signal words, based
on ANSI Z535.4-1998, to alert the user of a
potentially hazardous situation that may be
encountered while operating this equipment. ANSI's
definitions of the signal words are as follows:
This is the safety alert symbol. It is
used to alert the user of this equipment
of potential personal injury hazards.
Obey all safety messages that follow this symbol to
avoid possible injury or death.
CAUTION
Caution used without the safety alert symbol
indicates a potentially hazardous situation
which, if not avoided, may result in property
damage.
CAUTION
Caution indicates a potentially hazardous
situation which, if not avoided, may result in
minor or moderate injury.
WARNING
Warning indicates a potentially hazardous
situation which, if not avoided, could result in
death or serious injury.
DANGER
Danger indicates an imminently hazardous
situation which, if not avoided, will result in
death or serious injury.
1.3 General Description
1.3.1 RPC-2 Dust Collectors are dry, reverse pulse jet
cartridge collectors, used to ventilate abrasive blast
cabinets and remove dust from exhausting air. Figure 1
show typical arrangements and call-outs used in the
manual. Silencer may face up or down as shown.
Figure 1
Pulse Manifold
Inlet
Damper
Differential
Pressure
Gauge
Dust Drawer
Exhauster
Sequence
Panel
In-line
Dust Filter
Diaphragm Pulse Valve
Pressure
Regulator
Sequence
Switch
Grounding
Lug
Manifold
Drain
Some items are rotated for clarity
Filter
Cartridges
Damper/
Silencer
Exhaust Stack Damper/
Silencer Assembly

RPC-2 REVERSE PULSE DUST COLLECTOR Page 2
© 2012 CLEMCO INDUSTRIES CORP. www.clemcoindustries.com Manual No. 22788
1.3.2 The exhauster is mounted on the clean-air side
of the filter cartridges, and provides "pull-through" (pulls
air through the reclaimer) air flow, rated at 600, or 900
cfm, depending on the exhauster size. Dust and fines are
drawn through the reclaimer into the dust collector,
trapping dust before discharging clean air.
1.3.3 Filter cartridges are cleaned by a pulse of high
velocity compressed air expanding against the inner
surface of the cartridges. The expanding air momentarily
reverses air flow through the cartridge, releasing dust
that has accumulated on the outer surface. The dust
particles fall away from the cartridges and into the dust
drawer for removal.
1.3.4 The pulse interval is controlled by a timer
located inside the sequence panel. The timer controls
the ON time (the length of time for each pulse) and OFF
time (the length of time between each pulse). The ON
time should never be adjusted. The lower the setting for
the OFF time, the shorter the length of time between
pulses.
CAUTION
Do not pulse new dust collectors or
replacement cartridges until the cartridges are
properly seasoned. See Section 6.2. Pulsing
unseasoned cartridges could cause premature
cartridge failure or decrease the efficiency of
dust collector.
1.3.5 A toggle switch (sequence switch) located on
the sequence panel cover, enables or disables the
timing sequence. The user has an option to connect the
exhauster and sequence panel to the cabinet controls. If
the sequence panel is wired into the exhauster controls,
and the sequence switch is kept ON, the timing
sequence energizes when the exhauster is turned on,
automatically pulsing the cartridges when the exhauster
is running. If the switch is OFF, the timer will not
energize, and the cartridges will not be pulsed.
1.3.6 The differential pressure gauge shows the
pressure difference between the dust side and clean
side of the cartridges. The gauge helps determine the
proper pulse pressure and timer OFF time setting. See
Sections 4.1 and 4.2
2.0 SET-UP AND INSTALLATION
2.1 Push-Through Reclaimer Conversions,
(exhauster mounted on reclaimer), Figure 2
NOTE: If the dust collector replaces an existing filter bag
or dry filter, the reclaimer must be converted to a “pull-
through” style. If a conversion is required, an externally
adjustable vortex cylinder and gasket must be ordered
(stock numbers shown in Figure 2) to replace the
existing exhauster. If the reclaimer is already a “pull-
through” style, skip to Section 2.2.
WARNING
Lock out and tag out the electrical supply
before performing any electrical service.
Shorting electrical components could result in
death, serious electrical shocks, or equipment
damage. All electrical work, or any work done
inside an electrical panel, must be performed by
qualified electricians, and comply with
applicable codes.
2.1.1 Lock-out and tag-out power to the cabinet
control box and reclaimer motor.
2.1.2 Remove the cap screws securing the motor
plate to the exhauster. Lift up on the motor to remove the
motor, motor plate and paddle wheel assembly.
2.1.3 Remove the cap screws located inside the
exhauster housing (save for reuse), and remove the
housing from the top of the reclaimer.
External adjustable vortex cylinder assembly
for 600 cfm Reclaimer ................Stock No. 19080
for 900 cfm Reclaimer ................Stock No. 19084
Gasket, 4 ft. required..................Stock No. 00187
Figure 2
Motor Assembly
Vortex Cylinder
Assembly
Reclaimer
Gasket Exhauster Housing

RPC-2 REVERSE PULSE DUST COLLECTOR Page 3
© 2012 CLEMCO INDUSTRIES CORP. www.clemcoindustries.com Manual No. 22788
2.1.4 Remove the backing from the gasket and place
the gasket along the inside perimeter of the reclaimer
bolt holes. Use cap screws to attach the vortex to the
reclaimer.
2.2 Set-Up
2.2.1 Position the collector in a convenient location
that complies with OSHA and local safety codes. Allow
access to the differential pressure gauge and exhaust
damper. Provide ample space at the top to open the
cover to access the cartridges, and in the front to
remove the dust drawer without tipping it.
2.2.2 Use the four cap screws provided, to attach the
exhauster stack damper assembly to the exhauster
outlet as, shown in Figure 3. NOTE: The silencer may
face up or down as shown in Figure 1.
Figure 3
2.3 Connect Electrical Power
WARNING
Shorting electrical components could result in
serious electrical shocks, or equipment
damage. All electrical work must be performed
by a qualified electrician, and comply with
applicable codes.
NOTE: A wiring schematic for the RPC Collector is
packed in the sequence panel. A schematic for Clemco
cabinets is supplied with the cabinet. After wiring is
completed, keep the schematics and manuals together
for future reference and electrical replacement parts.
Wiring from the user's disconnect to the cabinet controls
must be provided by the user. Conduit and wiring from
the control box (or starter) to the exhauster motor and
115 volts to the RPC Control Panel (Pulse Sequence
Panel), must also be provided by the user.
If the RPC Collector replaces an existing "push through"
collector or dust bag, the exhauster may be wired into
the control box, to the terminal strip or starter where the
conduit from the old reclaimer motor is attached.
2.3.1 Electrical requirements depend on the size and
phase of the motor. Standard dust collectors are
supplied as follows:
600 CFM collectors, 1 HP, 115/230 V., 1 PH, 60 HZ
900 CFM collectors, 2 HP, 230/460 V., 3 PH, 60 HZ
WARNING
Electrical power must be locked out and tagged
out before continuing. Failure to do so could
result in death or serious injury from electrical
shock.
2.3.2 Install conduit, and wire the exhauster motor per
instruction on the motor plate, and the motor starter (for
3 PH wiring), or terminal strip (for 1 PH wiring) as shown
on the schematic.
2.3.3 Install conduit, and wire 115 volt power to the
reverse pulse control panel as shown on the schematic.
2.3.4 After the wiring is completed, observe the
subsequent warning, and check the motor rotation. To
check rotation, jog the starter (momentarily turn switch
on and off). This will cause the motor to rotate slowly.
Look through the slots in the fan housing on top of the
motor where rotation of the fan can easily be observed.
Proper rotation is indicated by the arrow on the
exhauster housing. The fan should rotate toward the
exhauster outlet as shown n Figure 3.
WARNING
Do not look into the exhauster outlet while the
paddle wheel is turning. Injury to the eye or face
could occur from objects being ejected from the
exhauster.
Rotation
Exhauster Outlet
Cap Screws
Exhaust Stack
Damper/Silencer
Assembly

RPC-2 REVERSE PULSE DUST COLLECTOR Page 4
© 2012 CLEMCO INDUSTRIES CORP. www.clemcoindustries.com Manual No. 22788
2.3.5 Check the amperage on initial start up. If the
motor draws excessive amperage, gradually close the
damper until the amperage is within the specifications
shown on the motor plate. The damper is located on the
exhauster outlet.
2.4 Flex Hose Connection
2.4.1 Connect the flexible exhaust hose between the
reclaimer outlet adaptor and dust collector inlet adaptor.
It may be easier to slip the hose over the adaptors, and
create a tighter seal, if the first two or three inches of
wire is removed from the inside of the hose. Use care
not to damage the hose. Secure the hose with worm
clamps. NOTE: The hose wire helps dissipate static in
the conveying hose, and helps ground each segment. In
order for the hose wire to dissipate static electricity, the
wire must touch the metal of each segment.
2.5 Ground Cabinet
2.5.1 To prevent static electricity build up, attach an
external grounded wire from an earth ground to the
grounding lug located on the rear wall of the collector.
2.6 Compressed Air Connections
NOTE: For maximum filter life and efficiency, the pulse
air source should be 30% relative humidity or less, and
be free of any oil contaminants. If line air does not meet
this requirement, an air dryer is recommended.
2.6.1 Connect a 1/2" or larger air hose to the pressure
regulator located on the pulse manifold inlet. An isolation
valve should be installed at the air source to enable
depressurization for service. If rigid pipe is used for the
air line, a flexible section of hose must be used at the
connection, to enable the top access door to swing open
for service.
WARNING
If twist-on type air hose couplings are used,
they must be secured by safety pins or wires to
prevent accidental disconnection while under
pressure. Hose disconnection while under
pressure could cause serious injury.
2.7 Install Manometer, Refer to Section 4.4
3.0 OPERATION
WARNING
All persons operating this equipment must be
made aware of the hazards of abrasive blasting.
Prolonged exposure to any dust could result in
serious lung disease and death. Short term
ingestion of toxic materials, such as lead dust
or dust from other heavy metals and corrosives,
could cause serious respiratory injury or death.
Identify all materials that are to be removed by
blasting, and obtain a Materials Safety Data
Sheet (MSDS) for the blast media. If lead
coating or other toxic materials are being
removed by the blasting process, HEPA after-
filters must be used for those applications.
3.1 Initial Start-up
3.1.1 The dust collector access doors and dust drawer
must be closed when the dust collector is on.
CAUTION
Do not pulse new dust collectors or
replacement cartridges until the cartridges are
properly seasoned. Refer to Section 6.2.
Pulsing unseasoned cartridges could cause
premature cartridge failure or decrease the
efficiency of dust collector.
3.1.2 With the sequence switch OFF, open the
compressed air supply valve to pressurize the pulse
manifold. Check the air line and connections for leaks.
3.1.3 Using the regulator on the manifold inlet, turn
pulse pressure to 20 psi. Turn the sequence switch ON,
and check the air pulse and sequence of the diaphragm
valves, solenoids, and panel timer. After the operation of
the pulse system is confirmed, turn the sequence switch
OFF and increase pressure to 70 psi.
3.1.4 Do not turn the sequence switch ON until the
cartridges are seasoned per Section 6.2.
3.2 Operation Start-Up
3.2.1 Make sure the top access door is secured with
clamps, and that the dust drawer is closed.
3.2.2 Make sure the sequence switch is on. NOTE: Do
not turn the sequence switch ON until the cartridges are
properly seasoned, per Section 6.2.

RPC-2 REVERSE PULSE DUST COLLECTOR Page 5
© 2012 CLEMCO INDUSTRIES CORP. www.clemcoindustries.com Manual No. 22788
3.2.3 Start the exhauster at the control panel, usually
mounted on the blast cabinet.
3.2.4 Check the pulse manifold pressure.
3.3 Shutdown
3.3.1 Run the collector until all media is recovered from
the cabinet, and the cabinet is free of airborne dust.
3.3.2 Turn off the exhauster.
3.3.3 Turn off the compressed air supply valve.
3.3.4 Drain the pulse manifold whenever the
compressed air supply is turned off. The drain petcock is
mounted on the side of the collector. See Figure 1.
3.3.5 Empty contents of the dust drawer into a
suitable container, per Section 5.1.
4.0 Adjustments
4.1 Pulse Manifold Pressure
4.1.1 The pressure regulator located on the pulse
manifold inlet, adjust pulse pressure. Set initial pressure
at 70 psi. Refer to Section 4.2.4.
4.1.2 Do not increase pulse pressure until the pulse
sequence is at maximum intervals as describe in Section
4.2.
4.2 Pulse Sequence Control Panel and Timer
4.2.1 The toggle switch (sequence switch) mounted on
the sequence control panel cover, enables or disables the
timing sequence. When the switch is ON, the pulse
sequence automatically starts when the dust collector
exhauster is started. If the switch is OFF the pulse
sequence will not occur. The switch should be left OFF
(no pulse) until cartridges are seasoned. See Section 6.2.
4.2.2 The timer is factory set at 40 seconds OFF and
15/100 of a second ON. Every 40 seconds the cartridges
are pulsed.
4.2.3 As the cartridges cake with dust, the pulse may
not clean them well enough to bring the differential
pressure gauge below the recommended changeover
pressure of 4". A constant reading higher than 4" is an
indication that more frequent pulse cycles or higher
pressure are needed. When the differential pressure
gauge shows a constant pressure difference greater than
4", adjust the OFF time setting by half. DO NOT ADJUST
ON TIME. Increasing on time will consume more air, but
will NOT increase cleaning efficiency.
4.2.4 When the frequency of the pulse cycles will not
lower the differential pressure to less than 4", or if a
decrease in the efficiency is noted, increase pulse
pressure in increments of 10 psi until the maximum of 100
psi is reached.
4.2.5 When the frequency of the pulse cycles and
higher pulse pressure will not lower the differential
pressure below the changeover pressure of 4" w. c., the
filter cartridges should be replaced, and the timer OFF
time should be reset to 40 seconds, and pressure set to 70
psi. See Section 6.1.
4.3 Damper Setting (Static Pressure)
4.3.1 Static pressure must be adjusted for optimum
reclaimer efficiency. Correct static pressure varies with
size of reclaimer and the size, weight and type of media.
4.3,2 Adjust static pressure using the damper located
on the dust collector exhauster outlet at the base of the
silencer, and the manometer provided with the dust
collector.
4.3.3 Adjust static pressure by further opening the
damper (handle toward vertical) to increase static
pressure or further closing the damper (handle toward
horizontal) to decrease static pressure. Open only as far
as necessary to obtain a balance of dust removal without
media carryover.
4.3.4 If the static pressure is too low, the results will
be dirty media. Dirty media consists of good media, dust,
fines, and blasting by-products.
4.3.5 If the static pressure is too high, it may cause
carryover (usable media carried into the dust collector)
and result in excessive media consumption.
4.3.6 Use the manometer, and adjust the damper to
obtain the pressure in inches of water, as specified below.
The measurements are starting points only. With light-
weight, or finer media the setting may need to be lower;
with heavier and coarse media the setting may need to be
higher.
Media Size Static Pressure
Glass Bead 5 to 7........................3-1/2 to 4 inches
Glass Bead 8 to 13 .....................3 to 3-1/2 inches
Al. Oxide 60 and coarser ..............4 to 5 inches
Al. Oxide 80 and finer ...................3 to 4 inches
Plastic All * .........................2-1/2 to 3 inches
Steel Grit ** ...................................6 to 7 inches
* Non-Aerolyte reclaimers require modification.
Consult the factory.
** Size is limited, and determined by the system’s
application.

RPC-2 REVERSE PULSE DUST COLLECTOR Page 6
© 2012 CLEMCO INDUSTRIES CORP. www.clemcoindustries.com Manual No. 22788
4.3.7 Fine-tuning is required for optimum reclaimer
efficiency. After adjusting the damper to the best
balance of media recovery and media cleaning, carry-
over, or dirty media continues to be a problem, the
adjustable vortex cylinder may need adjustment. Consult
the cabinet manual or reclaimer manual for vortex
adjustment.
4.4 Manometer
NOTE: These instructions show several methods of
taking static pressure readings (negative pressure) on
cabinet reclaimers, using a flexible tube manometer.
Use the method best suited for the application. The
instructions explain the processes for taking periodic
readings and how to permanently install the manometer
for taking frequent readings. Permanent fittings should
be installed when rigid ducting is used, or when the
manometer installation is permanent. Use silicone sealer
or other sealant to seal around the fitting to prevent
leaks. The fitting should be capable of being capped
when the manometer tube is removed. This will prevent
leaks that alter the reclaimer’s separation efficiency.
Taking readings at different locations could produce
different readings. Static pressure readings at the door
are generally .5" to 1" lower than those taken above the
reclaimer. The readings are reference points, so
readings should be taken using the same method each
time the reading is taken.
4.4.1 Refer to directions packed with the manometer
for preparation and operating instructions for the
manometer.
4.4.2 Connect one end of the 3/16" ID tubing to one of
the tubing connectors (elbow) at the top of the
manometer, by pushing it over the barbed adaptor.
4.4.4 Leaving the needle protector on the needle,
insert the needle into the other end of the tubing. The
ends of the tubing must fit tight on the manometer and
needle; leaks will give inaccurate readings.
WARNING
Do not remove the needle shield during the
assembly. The needle is difficult to fit into the
tubing, and the shield protects the installer
from needle punctures.
4.4.5 Open both manometer valves (elbows fittings).
Both valves must be open to obtain a reading. Refer to
the supplement manual supplied with the manometer for
operation.
Figure 4
4.4.6 Place the manometer on the side of the
reclaimer; magnets on the manometer hold it in position.
The manometer must be vertically-plumb so the fluid is
level on both sides of the tube.
4.4.7 Needle placement: Ref. Figure 4.
4.4.7.1 Remove the needle protector, and place the
needle using one of the methods shown in Figure 4.
4.4.8 Turn ON the exhauster. The negative (static)
pressure will move fluid in the tube.
NOTE: Readings must be taken with the cabinet
doors open, and with the exhauster running.
4.4.9 To find the static pressure, add the number of
inches the fluid travels up column one column to the
8
Insert the needle into
straight section of flex
hose, about 8-inches above
the top of the reclaimer.
Place the needle so the
point is inside the door
opening. Carefully close
the door on the needle.
For taking frequent readings,
install a permanent fitting in
the reclaimer wall, just below
the inner cone as shown.
Reclaimers are for reference and
may differ from those shown.

RPC-2 REVERSE PULSE DUST COLLECTOR Page 7
© 2012 CLEMCO INDUSTRIES CORP. www.clemcoindustries.com Manual No. 22788
inches the fluid travels down the other column. Refer to
the example in Figure 5.
4.4.10 After the readings are taken, replace the needle
protector. Close the manometer valves and store the
manometer in the original container in a clean area.
Note: If the manometer installation is permanent, the
manometer may remain on the reclaimer body after the
valves are closed.
Figure 5
5.0 PREVENTIVE MAINTENANCE
WARNING
Always wear a properly fitted and maintained,
NIOSH approved respirator and eye protection
when emptying the dust drawer. Failure to do
so could result in respiratory disease or serious
respiratory and eye irritation. Toxicity and
health risk vary with type of media, and dust
generated by blasting. Identify all material that
is being removed by blasting, and obtain a
Materials Safety Data Sheet for the blast media.
5.1 Daily
5.1.1 With the exhauster turned off, empty the dust
drawer. Heavily contaminated parts or friable media may
require the drawer be emptied more often. Never allow
the drawer to become more than a quarter full.
5.1.2 Check the exhaust air during a pulse cycle. If
dust is emitting from the exhauster, cartridges are
leaking or damaged. Check immediately.
5.1.3 With the exhauster turned on, check the
differential pressure gauge. If reading is high (greater
than 4" above initial reading), adjust pulse pressure
and/or sequence per Section 4.1 and 4.2.
5.2 Weekly
5.2.1 With the exhauster turned off, check the in-line
dust filter dust accumulation. The filter is located on the
side of the collector. See Figure 6.
Figure 6
Cartridge Sheet
Clean side of
cartridge sheet
Dust side of
cartridge sheet
Snubber Fitting
Low pressure line to top
side of cartridge sheet
High pressure line to
bottom side of cartridge
sheet
Dust Filter
The manometer must be vertical when
taking pressure readings.
With the exhauster OFF,
slide the rule to align the
zero with the fluid level.
In the example shown, fluid traveled up
the right column 1-3/4 inch,
and down the left column 1-3/4 inch.
Static pressure is determined by adding
the columns together. In the example,
the static pressure is 3-1/2 inches.
To obtain the pressure reading: With
the exhauster ON, add the number of
inches the fluid travels up the column,
and the number of inches the fluid
travels down the other column. The total
is the static pressure reading.

RPC-2 REVERSE PULSE DUST COLLECTOR Page 8
© 2012 CLEMCO INDUSTRIES CORP. www.clemcoindustries.com Manual No. 22788
6.0 SERVICE MAINTENANCE
WARNING
All maintenance must be done with the
electrical power locked-out and tagged-out, and
the compressed air supply line bled, locked-out
and tagged-out. Failure to do so could result in
death or serious injury from electrical shock,
unintentional actuation of a component, or from
the venting of trapped compressed air.
6.1 Replacing Filter Cartridges
WARNING
Failure to wear properly fitted and maintained,
NIOSH approved respirator and eye protection
when servicing dust laden areas of the dust
collector could result in serious eye irritation
and lung disease or death. Toxicity and health
risk vary with type of media, and dust
generated by blasting. Identify all material that
is being removed by blasting, and obtain a
Materials Safety Data Sheet for the blast media.
6.1.1 Empty the dust drawer, and return the drawer to
its position.
6.1.2 Open the top access door.
6.1.3 Remove the nuts securing the cartridge hold-
down plates.
6.1.4 Remove the hold-down plates and venturi tubes.
6.1.5 Remove cartridges from the top. A small amount
of force may be necessary to loosen the seal of the
cartridge gasket.
6.1.6 When cartridges are removed, clean the inside
of the collector to remove loose or hardened dust,
particularly from the cartridge sealing surface, and the
clean side (top side) of the cartridge sheet.
6.1.7 Install new cartridges; center each cartridge,
install venturi tube, and secure with hold-down plates.
6.1.8 Inspect the access door gasket, replace if worn
or damaged. Close the access door and secure.
6.1.9 Reset timer OFF time to 40 seconds.
6.1.10 Reset pressure to 70 psi.
6.1.11 Season cartridges per Section 6.2.
6.2 Seasoning Cartridges
6.2.1 New cartridges must be seasoned. Cartridges
are seasoned by letting a dust layer develop on the
outside surface of the filter media. The dust layer protects
the filter cartridge, and enhances the filtering efficiency.
6.2.2 Operate the collector without pulsing (sequence
switch off) until the differential pressure gauge reads four
inches (4" w. c.).
6.2.3 After the differential pressure is reached, set the
timer OFF time to 40 seconds, and set the pulse pressure
at 70 psi.
6.2.4 Turn the sequence switch ON to start the pulse
cycle. See Section 4.2.
7.0 TROUBLESHOOTING
WARNING
Shut down the collector immediately if dust is
emitting from the exhauster. Check to make
sure that cartridges are correctly seated and
not worn or damaged. Prolonged breathing of
abrasive dust and blasting by-product dust
could result in serious lung disease or death.
Short term ingestion of toxic dust such as red
lead, poses an immediate danger to health.
Identify all materials that are to be removed by
blasting, and obtain a Materials Safety Data
Sheet for the blast media.
7.1 Collector Not Pulsing
7.1.1 Check the manifold pressure gauge. If the
reading is low, check the regulator adjustment, and
compressed air supply, look for a closed supply valve.
7.1.2 Check to make sure the sequence switch is not
turned off.
7.1.3 Check the fuse in the sequence control panel.
Replace as necessary.

RPC-2 REVERSE PULSE DUST COLLECTOR Page 9
© 2012 CLEMCO INDUSTRIES CORP. www.clemcoindustries.com Manual No. 22788
7.2 One Cartridge Not Pulsing
7.2.1 Solenoid defective. Check continuity for
electrical malfunction.
7.2.2 Check the diaphragm valve. With the
compressed air turned off, remove the four cover
screws, inspect the diaphragm and clean the bleed port.
7.2.3 Check for blockage in the tubing to the
diaphragm valves.
7.3 Pulse is a steady stream of air instead of a
pulse.
7.3.1 Check for a leak in the tubing between the
diaphragm valves and solenoid.
7.3.2 Solenoid remaining in open position. Check
continuity, clean, replace.
7.4 Exhauster Not Running
7.4.1 Exhauster overload could be tripped. Reset and
check for overload.
7.4.2 Make sure that the main disconnect is "on".
7.4.3 Motor defective. Check continuity.
7.5 Excessive Differential Pressure
7.5.1 Valves may not be pulsing properly. See 7.1.
7.5.2 The differential pressure gauge lines may be
plugged with dust. Check and clean.
7.5.3 Make sure the tubing has not been inserted so
far into the tube connection that it blocks the tube ends.
7.5.4 The in-line dust filter may be blocked. Clean or
replace.
7.5.5 Snubber fittings blocked with dust. Clean or
replace. Refer to Figure 6..
7.5.6 The sequence OFF time may need adjusting.
See Section 4.2.
7.5.7 Filter cartridges may need to be replaced. See
Section 4.2 and 6.1.
7.6 No Reading On Differential Pressure Gauge.
7.6.1 Check to make sure the low and high pressure
lines have not been reversed. Refer to Figure 6.
7.7 Dust Emitting From Exhauster.
7.7.1 Check for loose or damaged filter cartridge.
8.0 REPLACEMENT PARTS
8.1 Accessories
Description Stock No.
(-) Vortex cylinder assembly, to convert push-
through reclaimer to a pull-through
for 600 cfm Reclaimer............................19080
for 900 cfm Reclaimer............................ 19084
(-) Manometer kit............................................ 12528
8.2 Sequence Panel, not shown
Item Description Stock No
(-) Sequence control panel assembly.............15788
(-) Sequence control board ............................10261
(-) Solenoid.....................................................10262
(-) Switch, toggle ............................................12127
(-) Boot, toggle switch.....................................14228

RPC-2 REVERSE PULSE DUST COLLECTOR Page 10
© 2012 CLEMCO INDUSTRIES CORP. www.clemcoindustries.com Manual No. 22788
8.3 Collector Assembly, Figure 7
Item Description Stock No.
(-) RPC-2 Collector assembly
600 cfm w/ 1 hp, 115v motor...................15804
600 cfm w/ 1 hp, 230v motor...................15939
900 cfm w/ 2 hp, 230v motor...................20526
1. Filter cartridge, 13" x 36" ...........................15781
2. Venturi tube ...............................................15674
3. Plate, hold-down ........................................16213
4. Valve, 1.5" diaphragm ...............................15818
(-) Repair kit for 1-1/2" pulse valve (above) ...21601
5. Gasket, 5/16" x 1" adhesive backed,
specify feet required ...............................00187
6. Latch ..........................................................10290
7. Fitting, 1/4" NPT bulkhead ........................05605
8. Petcock, 1/4" NPT .....................................01993
9. Gauge, pressure ........................................11826
10. Gauge, differential pressure ......................10188
11. Snubber fitting ...........................................15786
12. Ground lug .................................................11639
13. Tubing, 1/4" nylon, specify feet required ...15892
14. Adaptor, elbow, 1/8" NPT x 1/4" tube ........15787
15. Adaptor, elbow, 1/4" NPT x 1/4" tube ........03428
16. Adaptor, straight, 1/4" NPT x 1/4" tube .....03429
17. Adaptor, straight, 1/8" NPT x 1/4" tube......03430
18. Regulator, 1/2" NPT pressure, w/ gauge ...01902
19. Filter, in-line dust .......................................23415
20. Inlet adaptor
600 cfm, 6" .............................................16362
900 cfm, 7" .............................................16837
21. Clamp, hose ..............................................11576
22. Hose, flex, specify feet required
6" for 600 cfm .........................................12452
7" for 900 cfm..........................................12448
Some items are rotated for clarity
Figure 7
1
23
4
5
5
5
6
6
9
10
11
11
12
13 14
15
17
17
13
18
19
20
21
22
13
8
7
16

RPC-2 REVERSE PULSE DUST COLLECTOR Page 11
© 2012 CLEMCO INDUSTRIES CORP. www.clemcoindustries.com Manual No. 22788
8.4 Exhauster Assembly, Figure 8
Item Description Stock No
1. Motor
600 cfm, 1 Hp, 115-V, 1 Ph, standard.. 12314
600 cfm, 1 Hp, 230-V, 3 Ph ................. 12310
900 cfm, 2 Hp, 230-V, 3 ph, standard.. 12309
900 cfm, 2 Hp, 230-V, 1 Ph ................. 02979
2. Plate, motor mount
600 cfm ................................................ 12004
900 cfm ................................................ 12005
3. Housing, exhauster
600 cfm ................................................ 12272
900 cfm ................................................ 12271
4. Gasket, 5/16" x 1" adhesive-backed,
specify feet required ............................ 00187
5. Paddle wheel
600 cfm ................................................ 12334
900 cfm ................................................ 12335
6. Adaptor, exhauster
600 cfm ................................................ 16836
900 cfm ................................................ 16835
7. Damper assembly, less sound foam
600 cfm, 6" .......................................... 19382
900 cfm, 7" .......................................... 18414
8. Sound foam, 4 sq. ft. req’d., trim to fit .... 12484
Figure 8
1
5
6
4
2
4
3
7, 8
Table of contents
Popular Dust Collector manuals by other brands
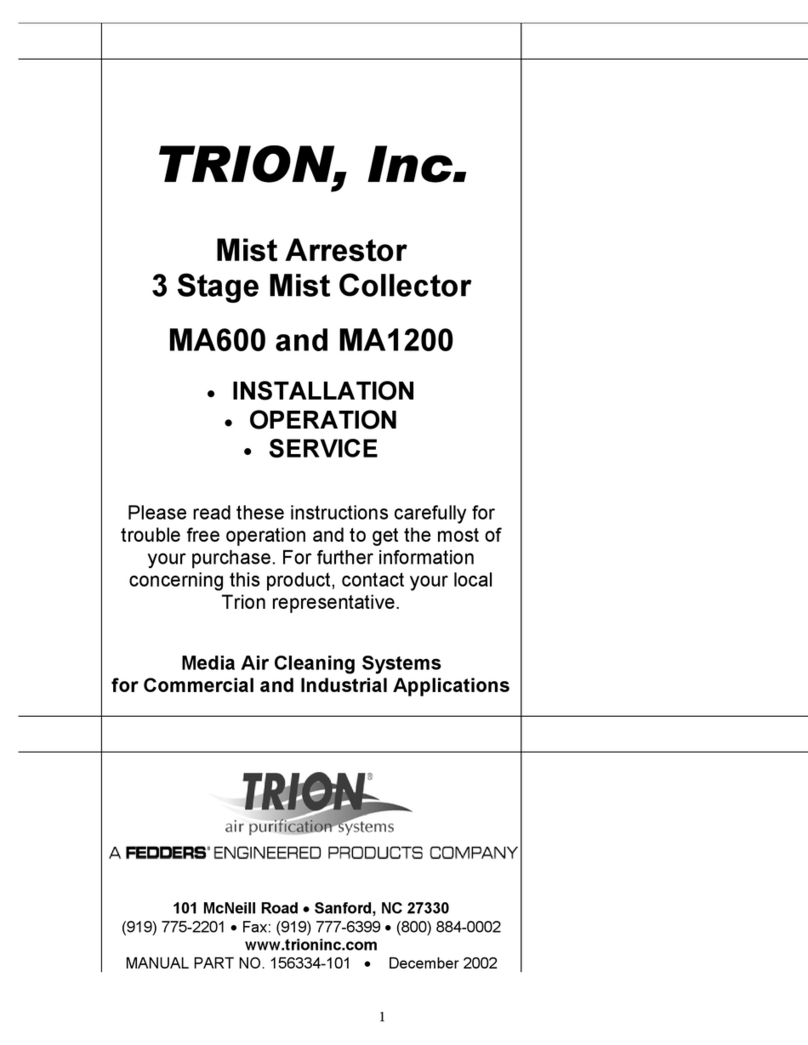
Trion
Trion MA600 Installation, Operation And Service
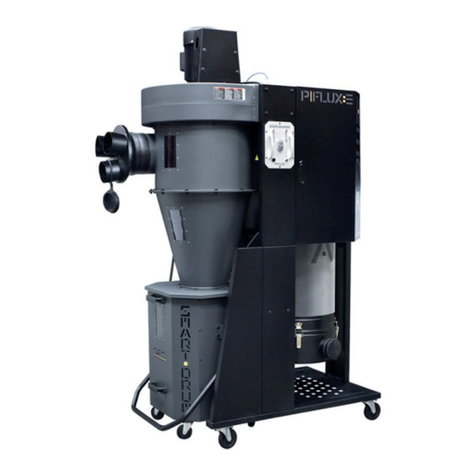
IGM
IGM LAGUNA PFlux3 operating instructions
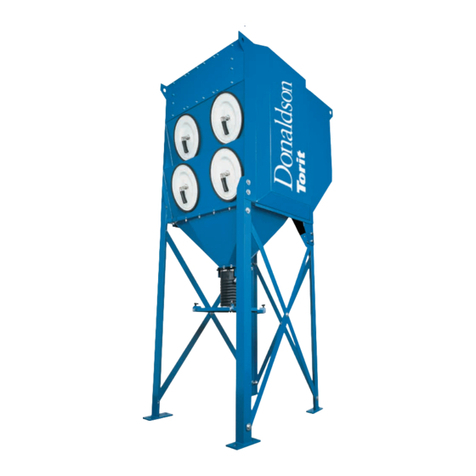
Donaldson Torit
Donaldson Torit DFO 2-4 Installation and operation manual
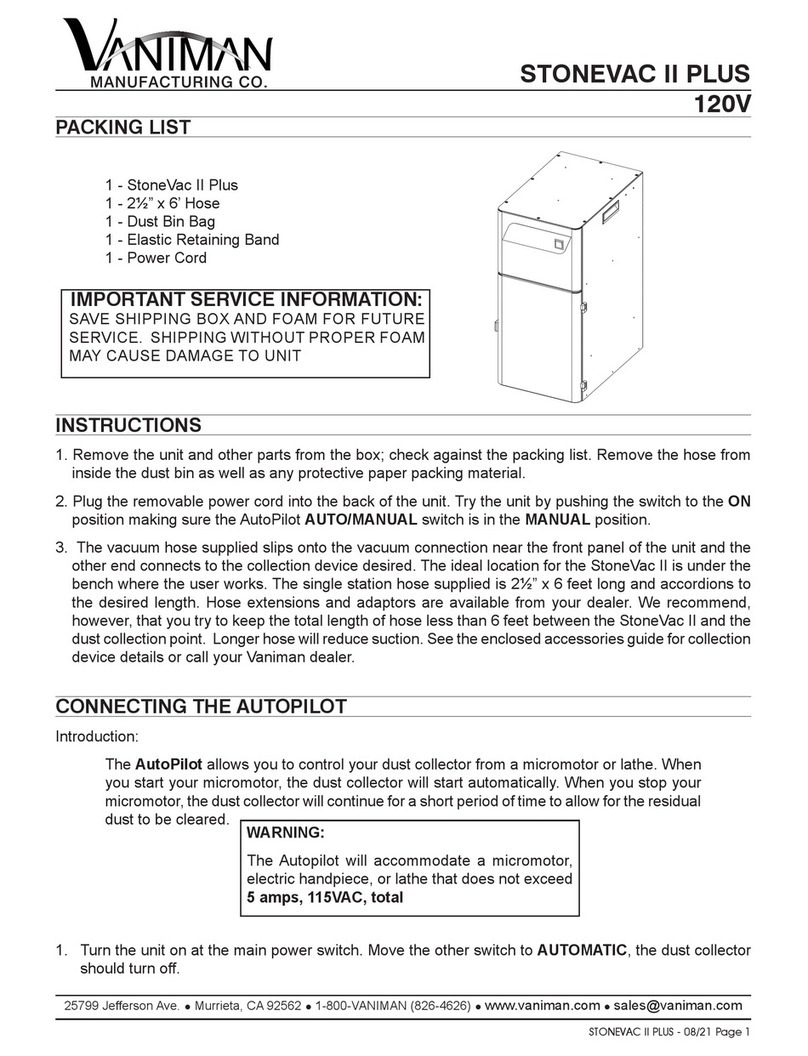
Vaniman
Vaniman STONEVAC II PLUS instructions

HOLZMANN MASCHINEN
HOLZMANN MASCHINEN ABS850DBK user manual
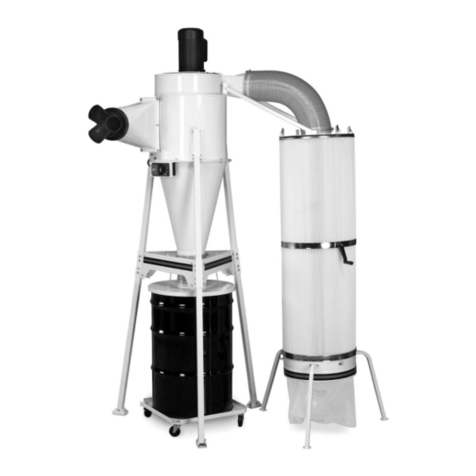
Jet
Jet JC-3BF Operating instructions and parts manual
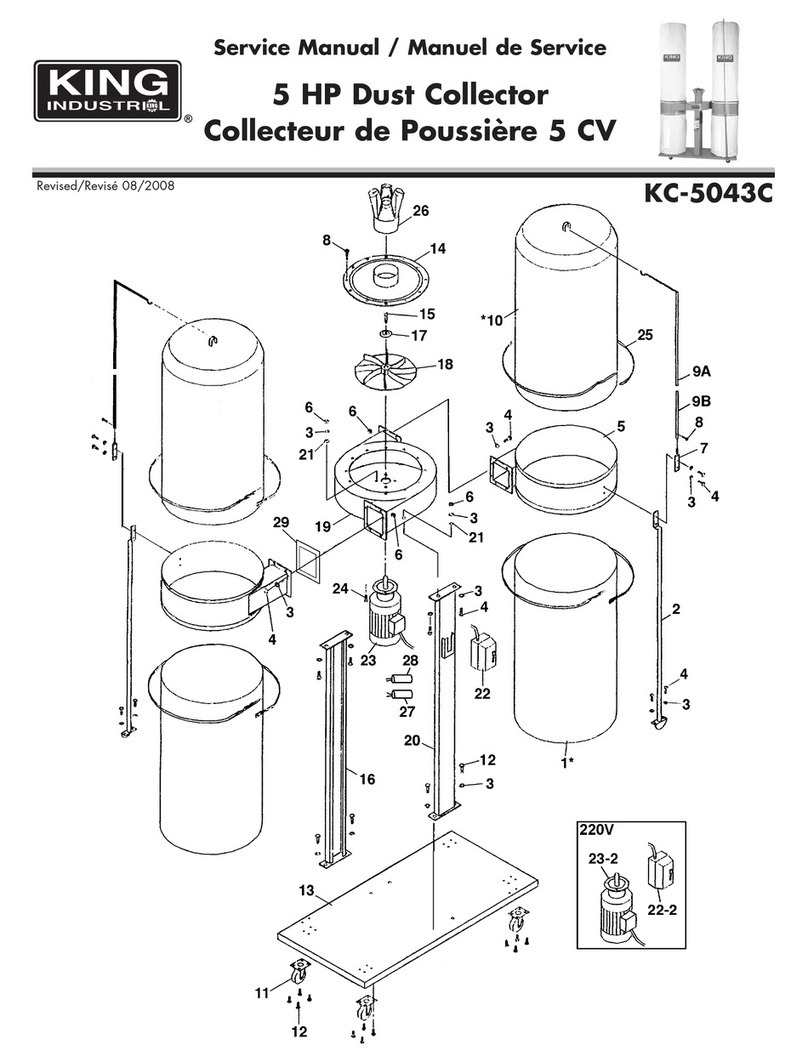
King Industrial
King Industrial KC-5043C Service manual

Powermatic
Powermatic 1792200HK Operating instructions and parts manual

Oneida Air Systems
Oneida Air Systems V1500 owner's manual
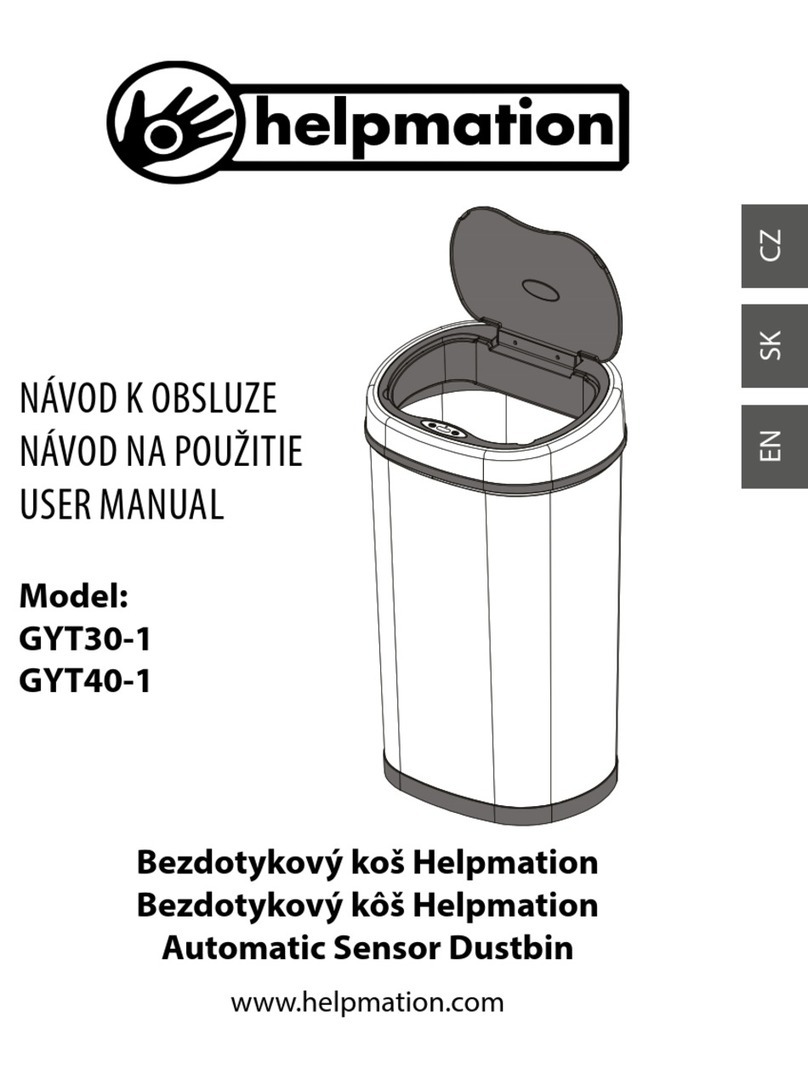
Helpmation
Helpmation GYT30-1 user manual
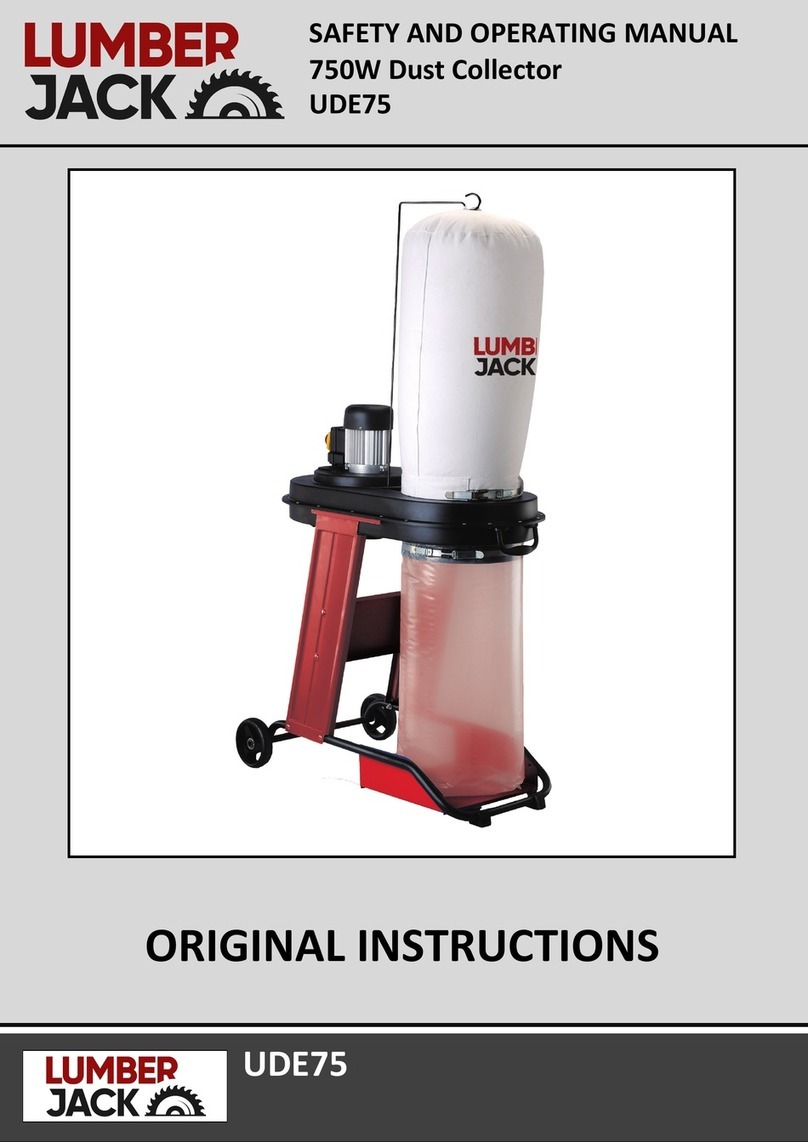
Lumberjack
Lumberjack UDE75 Safety and operating manual
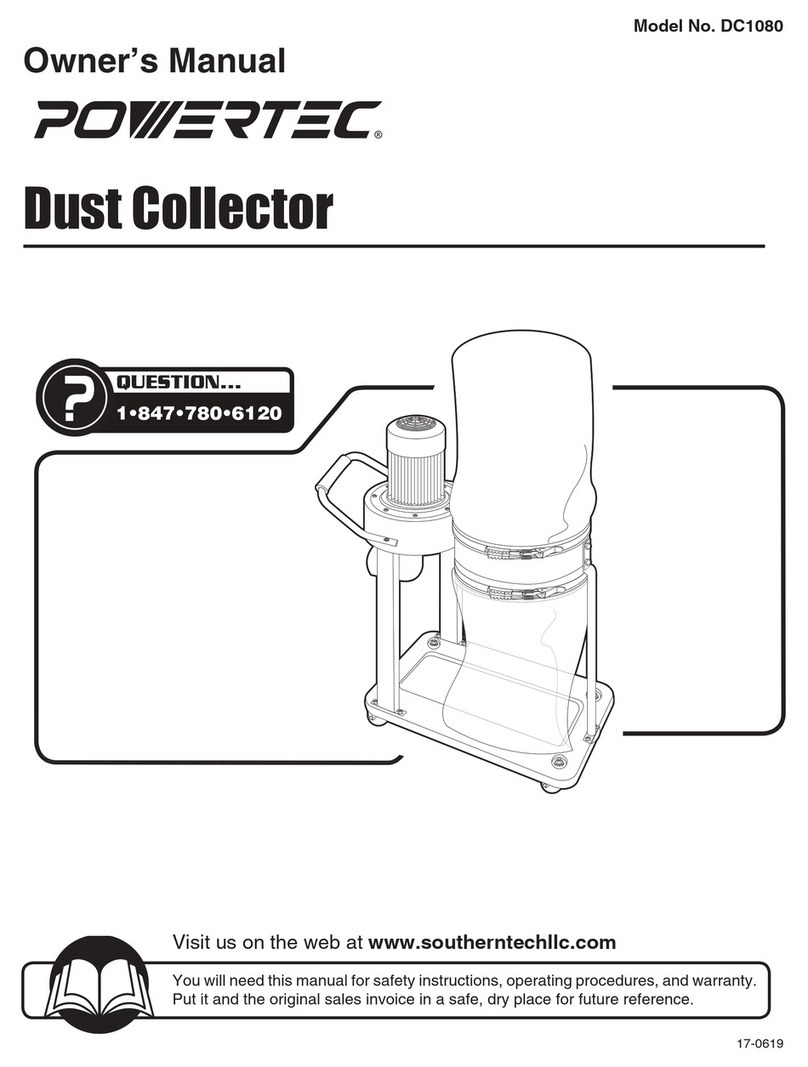
Power Tec
Power Tec DC1080 owner's manual