Zmotion EIO16084 User manual

–––––---

Foreword
The motion controller provides rich interface, and it has excellent motion control performance, which
can meet the expansion requirements of various projects.
This manual is copyrighted by Shenzhen Technology Co., Ltd., without the written permission of the
Zmotion Technology, no person shall reproduce, translate and copy any content in this manual. The
above-mentioned actions will constitute an infringement of the copyright of the company's manual, and
Zmotion will investigate legal responsibility according to law.
For details about the ZMC controller software and the introduction and routine of each command,
please refer to the ZBASIC software manual.
Information contained in this manual is only for reference. Due to improvements in design and
functions and other aspects, Zmotion Technology reserves the final interpretation! Subject to change
without notice!
Pay attention to safety when debugging the machine!
Please be sure to design an effective safety protection device in the machine, and add an error
handling program in the software, otherwise Zmotion has no obligation or responsibility for the loss
caused.
In order to ensure the safe, normal and effective use of the product, please be sure to read this
product manual carefully before installing and using the product.

Safety Statement
⚫This chapter describes the safety precautions required for the correct use of this product. Before
using this product, please read the instructions for use and correctly understand the relevant
information on safety precautions.
⚫This product should be used in an environment that meets the design specifications, otherwise
it may cause equipment damage or personal injury, and malfunctions or component damage
caused by failure to comply with relevant regulations are not within the scope of product quality
assurance.
⚫Zmotion will not take any legal responsibility for personal safety accidents and property losses
caused by failure to comply with the contents of this manual or illegal operation of products.
Safety Level Definition
According to the level, it can be divided into " Danger " and " Caution ". Failure to operate as required
may result in moderate injury, minor injury or equipment damage.
Please keep this guide in a safe place for reading when needed, and be sure to hand this manual to
the end user.
Install
Danger
◆When the controller is disassembled, all external power supplies used by the
system should be disconnected before operation, otherwise it may cause
misoperation or damage to the equipment.
◆It is forbidden to use in the following places: places with dust, oil fume, conductive
dust, corrosive gas and flammable gas; places exposed to high temperature,
condensation, wind and rain; places with vibration and shock. Electric shock, fire
and misuse can cause product damage and deterioration.
Notice
◆Avoid metal shavings and wire ends falling into the hardware circuit board during
installation.
◆After installation, ensure that there are no foreign objects on the hardware circuit
board.
◆When installing, make it tightly and firmly with the mounting frame.

◆Improper installation of the controller may result in misoperation, failure and fire.
Wiring
Danger
◆The specifications and installation methods of the external wiring of the
equipment shall comply with the requirements of local power distribution
regulations.
◆When wiring, all external power supplies used by the system should be
disconnected before operation.
◆When powering on and running after the wiring work is completed, the terminals
attached to the product must be installed.
◆Cable terminals should be well insulated to ensure that the insulation distance
between cables will not be reduced after the cables are installed on the terminal
block.
Notice
◆Avoid metal shavings and wire ends falling into the hardware circuit board during
installation.
◆The cable connection should be carried out correctly on the basis of confirming
the type of the connected interface.
◆It should be confirmed that the cables pressed into the terminals are in good
contact.
◆Do not bundle the control wires and communication cables with the main circuit
or power supply wires, etc., and the distance between the wires should be more
than 100 mm, otherwise noise may cause malfunction.
◆If the controller is not installed properly, it may cause electric shock or equipment
failure or malfunction.

EIO16084 Bus Expansion Module User Manual V1.5
Content
Chapter I Production Information........................................................................................3
1.1. Product Information ..........................................................................................3
1.2. Function Features..............................................................................................3
1.3. System Frame ...................................................................................................3
1.4. Hardware Installment........................................................................................4
Chapter II Product Specification .........................................................................................6
2.1. Interface Definition............................................................................................6
2.2. Order Information..............................................................................................7
2.3. Work Environment .............................................................................................7
Chapter III Wiring, Communication Configuration ..............................................................8
3.1. Power Input .......................................................................................................8
3.2. Power Specification ..........................................................................................8
3.3. IN Digital Input...................................................................................................9
3.3.1. Digital Input Specification......................................................................9
3.3.2. Digital Input Wiring...............................................................................10
3.4. OUT Digital Output ..........................................................................................10
3.4.1. Digital Output Specification .................................................................11
3.4.2. Digital Output Wiring ............................................................................12
3.5. EtherCAT Bus Interface ...................................................................................12
3.6. AXIS Differential Pulse Axis Interface.............................................................14
3.6.1. AXIS Interface Signal Specification & Wiring.......................................16
Chapter IV Expansion Module ...........................................................................................20
4.1. EtherCAT Expansion Wiring Reference............................................................20
4.2. EtherCAT Expansion Module Usage................................................................21
4.3. EtherCAT Bus Expansion Resource Mapping .................................................23
Chapter V Data Dictionary.................................................................................................25

EIO16084 Bus Expansion Module User Manual V1.5
5.1. Input & Output .................................................................................................25
5.2. The First Drive on The First Expansion Module..............................................25
Chapter VI Run and Maintain ............................................................................................28
6.1. Regular Inspection and Maintenance .............................................................28
6.2. Common Problems..........................................................................................29

EIO16084 Bus Expansion Module User Manual V1.5
Chapter I Production Information
1.1. Product Information
EIO16084 bus expansion module is used for EtherCAT bus controller, when IO and
other resources are not enough, an expansion module is needed. And controller can link
with multiple EtherCAT expansion modules through EtherCAT bus at the same time. And
IO and axis resources of EIO16084 can be accessed by mapping Number.
1.2. Function Features
◆Axis expansion: 4-axis pulse-axis expansion.
◆Digital expansion: there are 16 inputs and 8 outputs, each pulse axis has 2 additional
inputs and 2 additional outputs that can be configured.
◆Pulse output mode: pulse / direction or dual pulses.
◆Maximum pulse output frequency of each axis is 10MHZ.
◆The maximum output current of outputs (except pulse-axis) can reach 300mA, which
can directly drive some kinds of solenoid valves.
1.3. System Frame

EIO16084 Bus Expansion Module User Manual V1.5
1.4. Hardware Installment
EIO16084 bus expansion module is installed horizontally with screws, and each controller
should be fastened with 4 screws.
→Unit: mm →Mounting Hole Diameter 4.5mm
Installation
attention
⚫Non-professionals are strictly prohibited to operate. Specifically,
professionals who had been trained related electrical equipment,
or who master electrical knowledge.
⚫Please be sure to read the product instruction manual and safety
precautions carefully before installation.
⚫Before installation, please ensure that the product is powered off.
⚫Do not disassemble the module, otherwise the machine may be
damaged.
⚫Avoid direct sunlight installation.

EIO16084 Bus Expansion Module User Manual V1.5
⚫In order to facilitate ventilation and controller replacement, 2-3cm
should be left between the upper and lower parts of the controller
and the installation environment and surrounding components.
⚫Considering the convenient operation and maintenance of the
controller, please do not install the controller in the following
places:
a) places where the surrounding ambient temperature exceeds
the range of -20°C-60°C
b) places where the ambient humidity exceeds the range of 10%-
95% (non-condensing)
c) places with corrosive gases and flammable gases
d) places with many conductive powders such as dust and iron
powder, oil mist, salt, and organic solvents

EIO16084 Bus Expansion Module User Manual V1.5
Chapter II Product Specification
2.1. Interface Definition
Mark
Interface
Number
Description
POW
The led that indicates
the current state.
1
Power state: it lights when power is
conducted.
RUN
1
Run state: it lights when runs normally
ALM
1
Error state: it lights when runs incorrectly
EtherCAT IN
EtherCAT bus
interface
1
Connect to main controller or former level
expansion module.
EtherCAT OUT
1
Connect to drive equipment or behind level
expansion module.
Digital input
16
NPN type, main power 24V.
Digital output
8
NPN type, main power 24V.

EIO16084 Bus Expansion Module User Manual V1.5
Main power
1
24V DC power supplies for main control area
of expansion module.
Pulse axis
4
Each can be configured as differential pulse
output and differential encoder input.
2.2. Order Information
Model
Axes
Encoder
Inner
IN
Inner
OUT
ECAT IN /
EACT OUT
Functions
EIO1616
-
-
16
16
1/1
Module: EIO1616M
Module + cover:
EIO1616MT
EIO16084
4
4
16
8
1/1
4-axis expansion
EIO24088
8
8
24
8
1/1
8-axis expansion
2.3. Work Environment
Item
Parameters
Work Temperature
-10℃-55℃
Work relative Humidity
10%-95% non-condensing
Storage Temperature
-40℃~80℃(not frozen)
Storage Humidity
Below 90%RH (no frost)
vibration
Frequency
5-150Hz
Displacement
3.5mm(directly install)(<9Hz)
Acceleration
1g(directly install)(>9Hz)
Direction
3 axial direction
Shock (collide)
15g, 11ms, half sinusoid, 3 axial direction
Degree of Protection
IP20

EIO16084 Bus Expansion Module User Manual V1.5
Chapter III Wiring, Communication
Configuration
3.1. Power Input
The power supply input adopts a 3Pin (there are all 3 terminals) screw-type pluggable
wiring terminal. And it is 24V DC power.
→Terminal Definition:
Terminal
Name
Type
Function
E+24V
Input
Positive (+) terminal of DC power input
(connect positive of power to positive of
controller)
EGND
Input
Negative (-) terminal of power input
FG
Earthing
(Grounding)
Protect
3.2. Power Specification
→Specification
Item
Description
Voltage
DC24V(-10%~10%)
The current to open
≤0.5A
The current to work
≤0.4A
Anti-reverse connection
Valid
Overcurrent Protection
Valid

EIO16084 Bus Expansion Module User Manual V1.5
3.3. IN Digital Input
→Terminal Definition
Terminal
Name
Type
Function 1
EGND
/
External power ground
EGND
/
External power ground
IN0
NPN type,
digital inputs
Input 0
IN1
Input 1
IN2
Input 2
IN3
Input 3
IN4
Input 4
IN5
Input 5
IN6
Input 6
IN7
Input 7
EGND
/
External power ground
EGND
/
External power ground
IN8
NPN type,
digital inputs
Input 8
IN9
Input 9
IN10
Input 10
IN11
Input 11
IN12
Input 12
IN13
Input 13
IN14
Input 14
IN15
Input 15
3.3.1. Digital Input Specification
Item
Digital input (IN0-15)
Input mode
NPN type, input is triggered when in low-electric level
Frequency
<5kHz
Impedance
4.7KΩ
Voltage level
DC24V
The voltage to open
<14.5V
The voltage to close
>14.7V
Minimal current
-1.8mA (negative)
Max current
-6mA (negative)

EIO16084 Bus Expansion Module User Manual V1.5
Isolation mode
optoelectronic isolation
Note: the above parameters are standard values when the voltage of expansion
module power supply (E+24V port) is 24V.
3.3.2. Digital Input Wiring
→Wiring Note:
⚫The wiring principle of digital inputs IN (0-15) is shown in the figure above. The
external signal source can be an optocoupler, a key switch or a sensor, etc., all can
be connected as long as the requirements on output of electric level can be achieved.
⚫For the public end, please connect the "EGND" port on the power supply to the "COM"
terminal of the external input device. If the signal area power supply of the external
device and the power supply of the expansion module are in the same power supply
system, this connection also can be omitted.
3.4. OUT Digital Output
→Terminal Definition
Terminal
Name
Type
Function
EGND
/
External power ground
NC
/
Spare
OUT0
NPN leakage,
Output 0

EIO16084 Bus Expansion Module User Manual V1.5
OUT1
digital outputs
Output 1
OUT2
Output 2
OUT3
Output 3
OUT4
Output 4
OUT5
Output 5
OUT6
Output 6
OUT7
Output 7
3.4.1. Digital Output Specification
Item
Digital Output (OUT0-7)
Output mode
NPN leakage type, it is 0V when outputs
Frequency
<8kHz
Voltage level
DC24V
Max output current
+300mA
Max leakage current when off
25μA
Respond time to conduct
12μs
Respond time to close
80μs
Overcurrent protection
Support
Isolation method
optoelectronic isolation
Note:
The times in the form are typical based on the resistive load, and may change
when the load circuit changes.
Due to the leak-type output, the shutdown of the output will be obviously
affected by the external load circuit, and the output frequency should not be set
too high in the application. And it is recommended to set below 8KHz.

EIO16084 Bus Expansion Module User Manual V1.5
3.4.2. Digital Output Wiring
→Wiring Note:
⚫The wiring principle of digital outputs OUT (0-7) is shown in the figure above. The
external signal receiving end can be an optocoupler or a relay or solenoid valve, all
can be connected as long as the input current does not exceed 300mA.
⚫For the connection of the public end, please connect the "EGND" port on the power
supply to the negative pole of the DC power supply of the external input device. If the
DC power supply of the external device and the expansion module power supply are
in the same power supply system, this connection can also be omitted.
3.5. EtherCAT Bus Interface
EIO16084 bus expansion module has 2 100M EtherCAT communication interfaces,
and they support EtherCAT protocol. EtherCAT IN is connected to main controller or
former level expansion module, but EtherCAT OUT is connected to drive equipment or next
level expansion module, they can not be mixed. The pin definition is as follows:

EIO16084 Bus Expansion Module User Manual V1.5
→Specification
Item
Specification
Communication protocol
EtherCAT protocol
Valid service
CoE(PDO, SDO), FoE
Synchronization method
IO adopts input and output synchronization / DC-
distributed clock
Physical level
100BASE-TX
Duplex mode
Full duplex
Topology
linear topology
Transfer media
Cable
Transfer distance
It is less than 100M between 2 nodes
Process data
Maximum 1486 bytes of one single frame
Synchronization shaking
of two slave stations
<1us
Refresh
1000 digital input and output about is 30us, 16 servo
axes is about 100us
→Communication Cable Requirements
EtherCAT communication interface adopts standard Ethernet RJ45 interface.
The network cable adopts Category 5e STP, and the crystal head has a metal shell to
reduce interference and to prevent information from being eavesdropped. As shown below:

EIO16084 Bus Expansion Module User Manual V1.5
Item
Specification
Cable type
Flexible crossover cable, Category 5e
traverse
twisted pair
Line pairs
4
Isolation
cross skeleton
Connector
Crystal head with iron shell
Cable material
PVC
Cable length
Less than 100m
Use RJ45 network cable connection method:
⚫When installing, hold the crystal head that is with the cable and insert it into the RJ45
interface until it makes a "click" sound (kada).
⚫In order to ensure the stability of communication, please fix the cables with cable ties.
⚫When disassembling, press the tail mechanism of the crystal head, and pull out the
connector and the module in a horizontal direction.
Please use tube-type pre-insulated terminals and cables with appropriate wire
diameters to connect the user terminals.
3.6. AXIS Differential Pulse Axis Interface
This product provides 4 local differential pulse axis interfaces, each interface is a
standard DB26 female socket.

EIO16084 Bus Expansion Module User Manual V1.5
→Interface Definition
Interface
Pin
Signal
Description
1
EGND
Negative pole of IO 24V power
2
IN16-
19/ALM
General input (recommended as
driver alarm)
3
OUT8-
11/ENABLE
General output (recommended as
driver enable)
4
EA-
Encoder differential input signal A-
5
EB-
Encoder differential input signal B-
6
EZ-
Encoder differential input signal Z-
7
+5V
Positive pole of 5V power of
pulse/encoder signal
8
Reserved
Reserved
9
DIR+
Servo or step direction output +
10
GND
Negative pole of 5V power of
pulse/encoder signal
11
PUL-
Servo or step pulse output -
12
Reserved
Reserved
13
GND
Negative pole of 5V power of
pulse/encoder signal
14
OVCC
Positive pole of IO 24V power
15
OUT12-
15/CLR
General output, recommended to
clear drive alarms
16
IN20-
23/INP
General input, recommended to do
on-position signal
17
EA+
Encoder differential input signal A+
18
EB+
Encoder differential input signal B+
19
EZ+
Encoder differential input signal Z+
20
GND
Negative pole of 5V power of
pulse/encoder signal
21
GND
22
DIR-
Servo or step direction output -
23
PUL+
Servo or step pulse output +
24
GND
Negative pole of 5V power of
pulse/encoder signal

EIO16084 Bus Expansion Module User Manual V1.5
25
Reserved
Reserved
26
Reserved
Reserved
Note:
ALM, ENABLE, CLR and INP are recommended to be used as axis IO, because the
drive capacity is small.
OVCC, +5V are only used for communication between the controller and the
servo driver, please do not use it as power supply for other places.
3.6.1. AXIS Interface Signal Specification & Wiring
→Specification:
Signal
Item
Description
PUL/DIR
Signal type
Differential output signal
Voltage range
0-5V
Maximum frequency
10MHz
EA/EB/EZ
Signal type
Differential input signal
Voltage range
0-5V
Maximum frequency
5MHz
IN16-23
Input method
NPN leak type, it is triggered
when low electric level is input.
Frequency
<5kHz
Impedance
6.8KΩ
Voltage level
DC24V
The voltage to open
<10.5V
The voltage to close
>10.7V
Minimal current
-1.8mA (negative)
Maximum current
-4mA (negative)
Isolation
optoelectronic isolation
OUT8-15
Output method
NPN leak type, it is 0V when
outputs
Frequency
<8kHz
Voltage level
DC24V
Maximum current
+50mA
Overcurrent protection
No
Table of contents
Other Zmotion Computer Hardware manuals
Popular Computer Hardware manuals by other brands
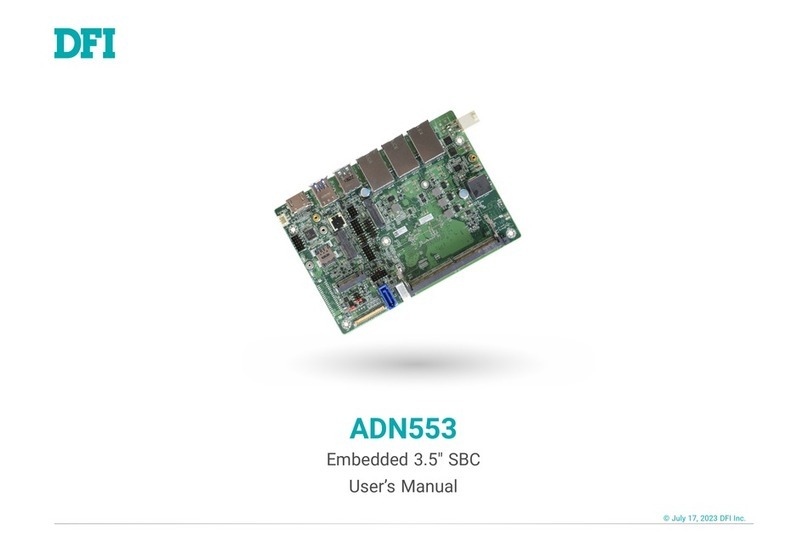
DFI
DFI ADN553 user manual
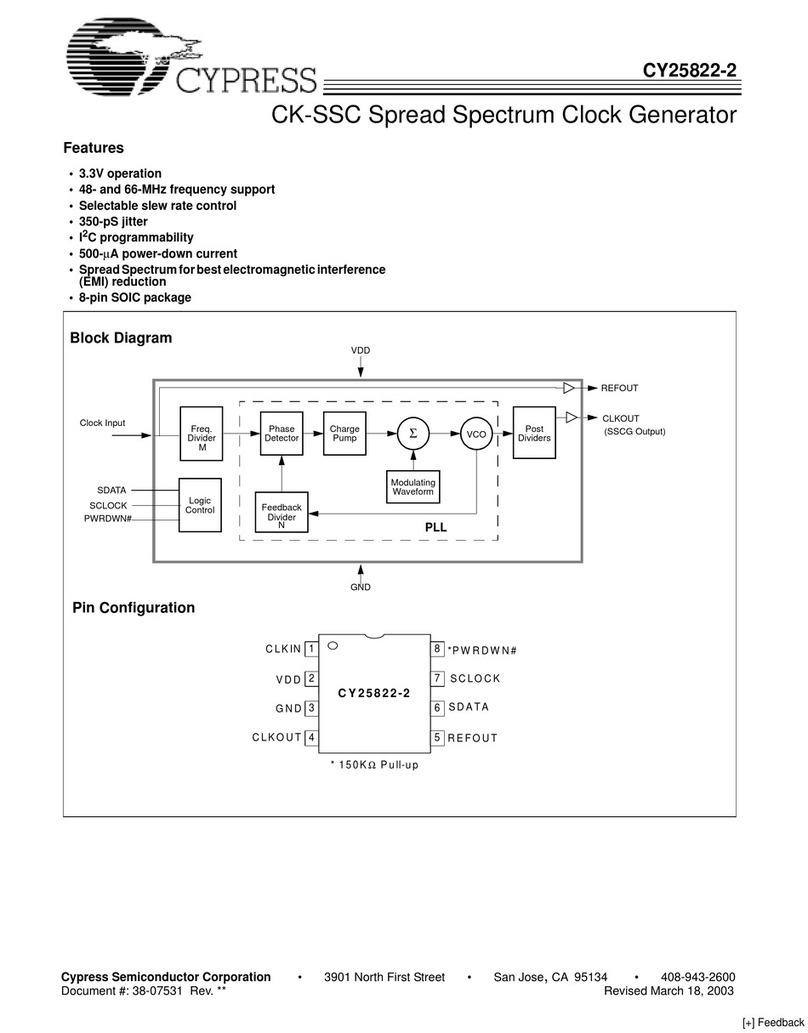
Cypress Semiconductor
Cypress Semiconductor CY25822-2 Specification sheet
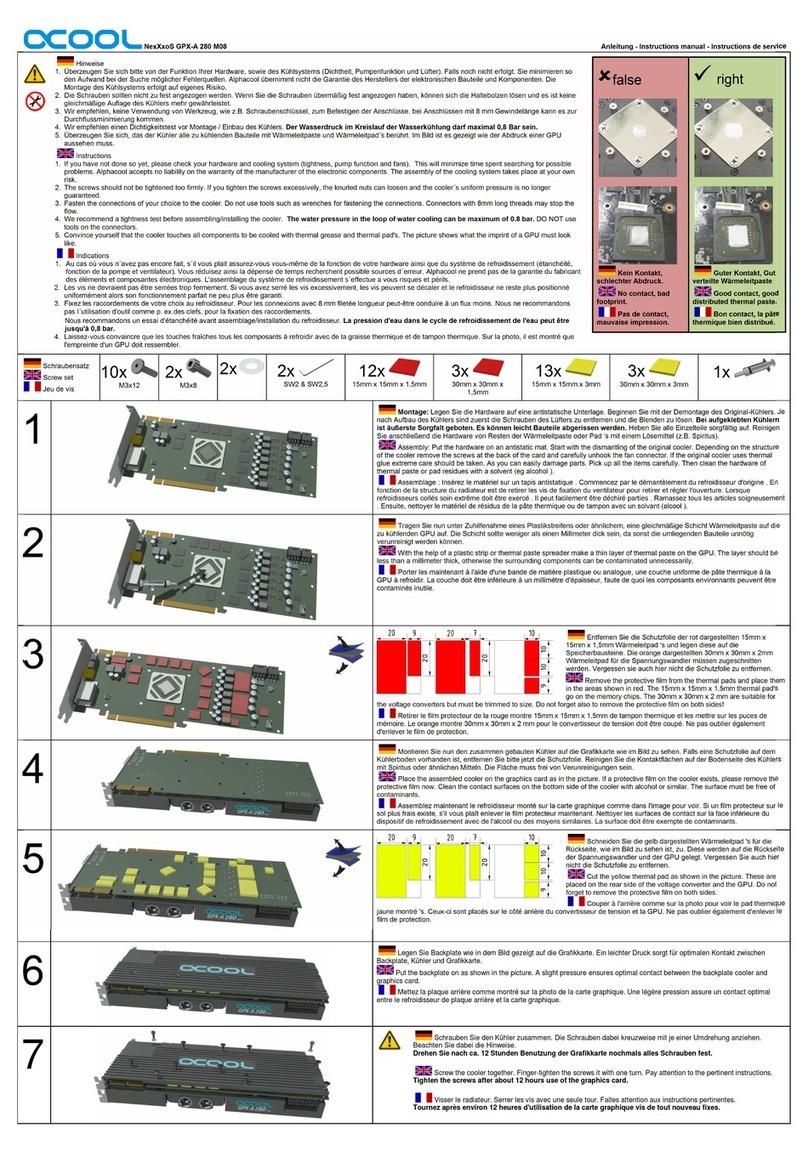
Alphacool
Alphacool NexXxoS GPX-A 280 M08 instruction manual
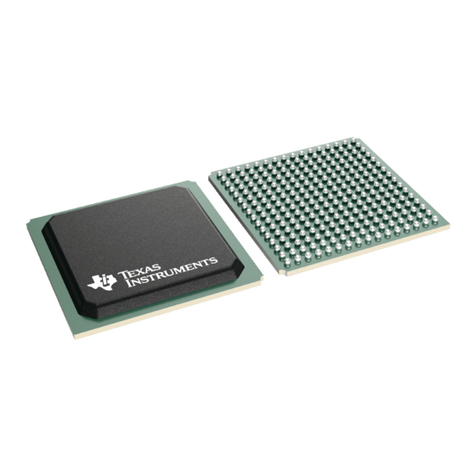
Texas Instruments
Texas Instruments OMAP-L137 EVM user manual
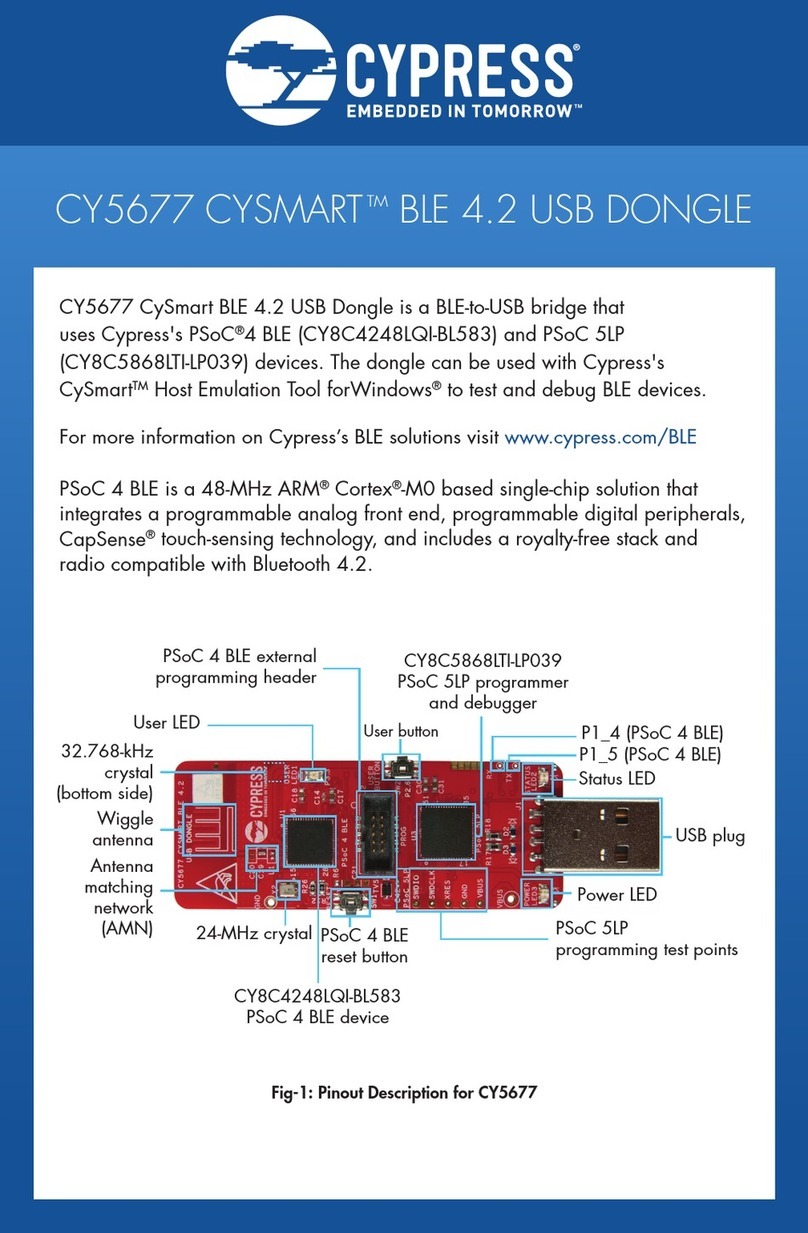
Cypress
Cypress CYSMART CY5677 Installation
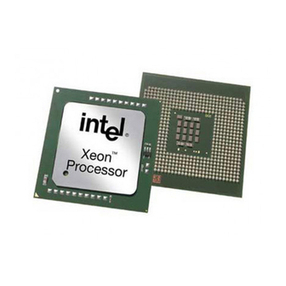
Intel
Intel BFCBASE - Motherboard - 7300 datasheet

Apricorn
Apricorn PEDA Specifications
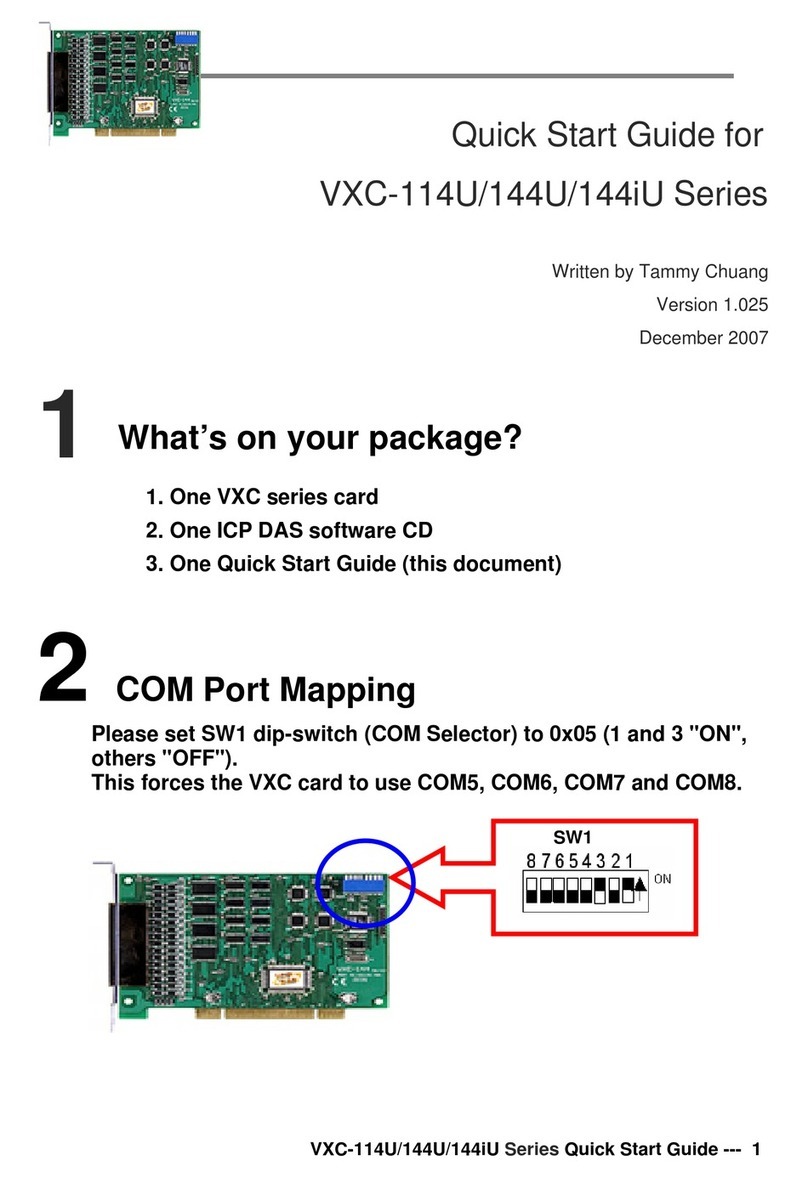
ICP DAS USA
ICP DAS USA VXC-114U Series Quick start guide for
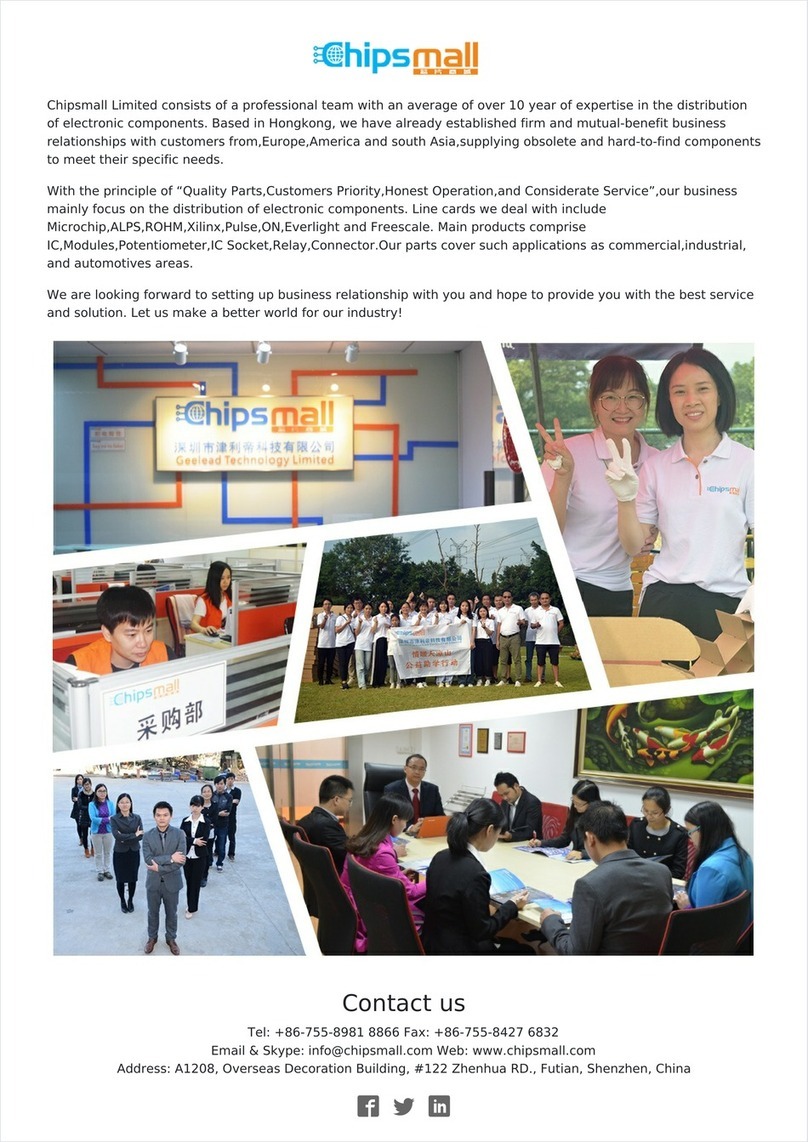
Terasic
Terasic Cypress CapSense P0080 user manual
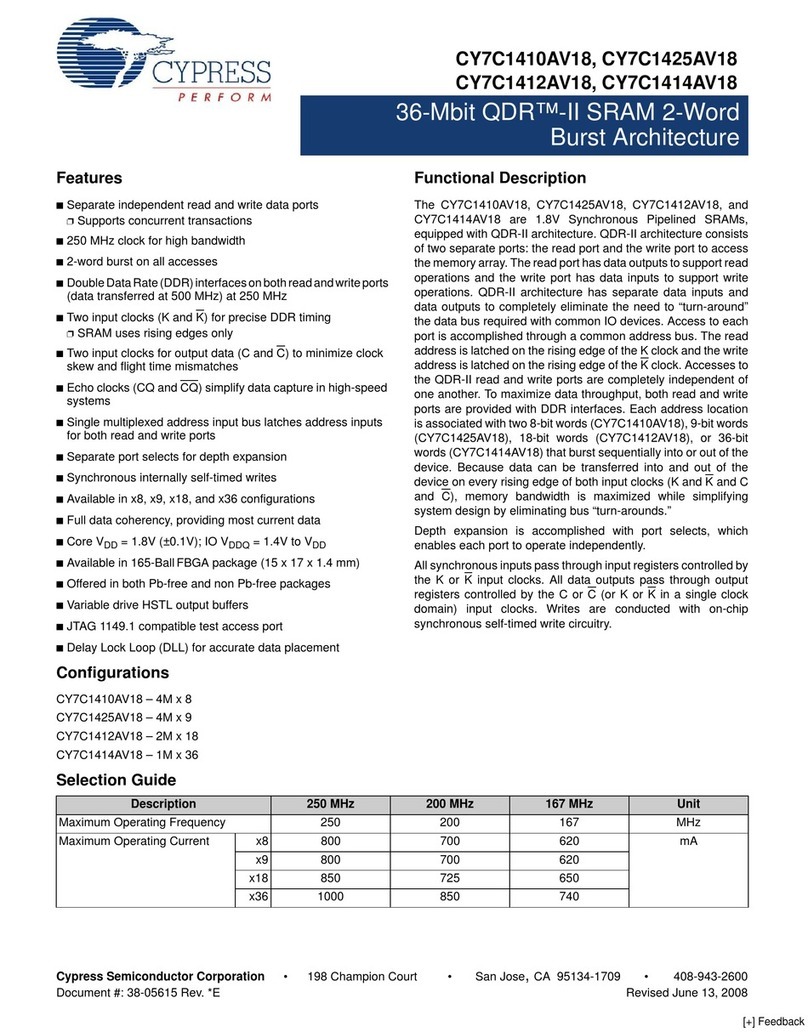
Cypress Semiconductor
Cypress Semiconductor CY7C1410AV18 Specification sheet
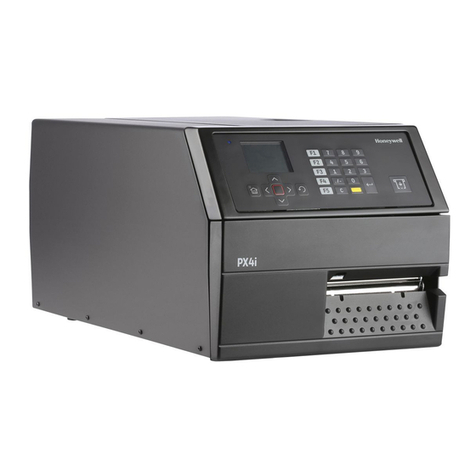
Honeywell
Honeywell PX4ie installation guide
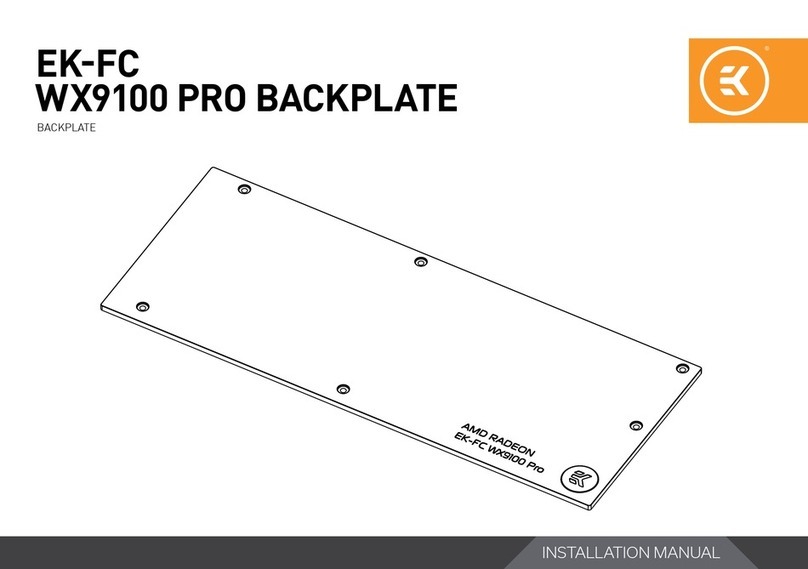
ekwb
ekwb EK-FC WX9100 PRO BACKPLATE installation manual