AAON RSMD-CM Quick start guide

RSMD-CM
Technical Guide

AAON
2425 South Yukon Ave.
Tulsa, OK 74107-2728
www.aaon.com
Factory Technical Support Phone: 918-382-6450
AAON®Controls Support: 866-918-1100
It is the intent of AAON®to provide accurate and current product
information. However, in the interest of product improvement,
AAON® reserves the right to change pricing, specications, and/
or design of its product without notice, obligation, or liability.
AAON Part Number: G102430, Rev. A
Copyright December 2021 AAON, Inc.
AAON®is a registered trademark of AAON, Inc., Tulsa, OK.
Copeland Scroll™ is a registered trademark of Emerson
Electric Co., Sidney, OH
AAON®assumes no responsibility for errors or omissions in
this document. This document is subject to change without
notice.
RSMD-CM REVISION LOG
REVISION AND DATE CHANGE
Rev. A, December 22, 2021 First edition
www.aaon.com
RSMD-CM PARTS REFERENCE
PART DESCRIPTION PART NUMBER
Refrigerant System Module for Digital Compressors with
Condenser Fans with Microchannel Coils (RSMD-CM) ASM06709
VCCX2 Controller ASM01698
Prism 2 ASM02533
IP Module Kit ASM01902
CommLink 5 ASM01874
E-BUS Cable Assembly E-BUS Power and Comm
1.5 ft., 3 ft., 10 ft., 25 ft., 50 ft., 75 ft.,
100 ft., 150 ft., 250 ft., and 1000 ft. spool
G029440 (1.5 ft.), G012870 (3 ft.), G029460 (10 ft.), G045270 (25 ft.),
G029510 (50 ft.), G029530 (75 ft.), G029450 (100 ft.), G029470 (150 ft.),
V36590 (250 ft.), G018870 (SPOOL)
Modular Service Tool SD - Operator Interface ASM01895
All manuals are also available for download from
www.aaon.com/controlsmanuals.

3
RSMD-CM Technical Guide
TABLE OF CONTENTS
OVERVIEW ................................................................................................................................................. 5
Features and Applications....................................................................................................................................... 5
Dimensions ............................................................................................................................................................. 6
INSTALLATION AND WIRING.................................................................................................................. 7
Electrical and Environmental Requirements .......................................................................................................... 7
WIRING ....................................................................................................................................................... 8
Inputs Wiring ........................................................................................................................................................... 8
Outputs Wiring ........................................................................................................................................................ 9
INPUTS AND OUTPUTS ......................................................................................................................... 10
Inputs/Outputs Map............................................................................................................................................... 10
Inputs and Outputs.................................................................................................................................................11
SEQUENCE OF OPERATIONS .............................................................................................................. 12
Cooling Mode, Dehumidication, and Head Pressure Control.............................................................................. 12
LCD SCREENS ........................................................................................................................................ 13
LCD Display Screen and Navigation Keys............................................................................................................ 13
Main Screens Map ................................................................................................................................................ 14
Module Screens .................................................................................................................................................... 15
System Status Screens......................................................................................................................................... 16
Sensor Status Screens ......................................................................................................................................... 17
Setpoint Status Screens ....................................................................................................................................... 18
Alarms Screens..................................................................................................................................................... 19
Alarms History Screens and Protected Screens Map........................................................................................... 21
Conguration Screens .......................................................................................................................................... 22
Diagnostic Screens ............................................................................................................................................... 23
Alarm Counts and Address Screens ..................................................................................................................... 25
TROUBLESHOOTING ............................................................................................................................. 26
LED Diagnostics ................................................................................................................................................... 26
Suction Pressure Transducer Testing ................................................................................................................... 27
CopelandTM Discharge Thermistor Temperature Sensor Testing .......................................................................... 28
Temperature Sensor Testing ................................................................................................................................. 29
Head Pressure Transducer ................................................................................................................................... 30
APPENDIX A: CONDENSER OPTIONS ................................................................................................ 31
Two Condensers Per Module (Default)................................................................................................................. 31
Single Condenser Per Module .............................................................................................................................. 33
Single Condenser Per Two Modules..................................................................................................................... 35
Single Condenser for Three Modules ................................................................................................................... 37
A1/B1 and A2/B2 Condenser Conguration.......................................................................................................... 39
ON/OFF Condenser Options ................................................................................................................................ 42

4RSMD-CM Technical Guide
FIGURES AND TABLES
TABLES
Table 1: RSMD-CM Module Electrical and Environmental Requirements.......................................................................7
Table 2: RSMD-CM Inputs and Outputs .............................................................................................................................10
Table 3: Navigation Key Functions.......................................................................................................................................13
Table 4: Suction Pressure Transducers Coil Pressure/Temperature/Voltage Chart for R410-A Refrigerant ........... 27
Table 5: Discharge Thermistor Temperature/Resistance .................................................................................................28
Table 6: 0-5V Temperature Sensor - Voltage and Resistance for Type III Sensors.....................................................29
Table 7: Head Pressure Transducer Chart .........................................................................................................................30
FIGURES
Figure 1: RSMD-CM Dimensions ............................................................................................................................................6
Figure 2: RSMD-CM Inputs Wiring ..........................................................................................................................................8
Figure 3: RSMD-CM Outputs Wiring.......................................................................................................................................9
Figure 4: LCD Display and Navigation Keys........................................................................................................................13
Figure 5: RSMD-CM LED Locations .....................................................................................................................................26
Figure 6: Two Condenser Operation (Default).....................................................................................................................31
Figure 7: Prism 2 Condenser Conguration - Two Condenser Operations (Default) ....................................................32
Figure 8: Single Condenser Per Module...............................................................................................................................33
Figure 9: Prism 2 Condenser Conguration - Single Condenser Per Module................................................................34
Figure 10: Single Condenser Per Two Modules ....................................................................................................................35
Figure 11: Prism 2 Condenser Conguration - Single Condenser Per Two Modules......................................................36
Figure 12: Single Condenser for Three Modules...................................................................................................................37
Figure 13: Prism 2 Condenser Conguration - Single Condenser for Three Modules....................................................38
Figure 14: A1/B1 Wiring.............................................................................................................................................................39
Figure 15: A2/B2 Wiring.............................................................................................................................................................40
Figure 16: Prism 2 Condenser Conguration - A1/B1 and A2/B2 Condenser Conguration .........................................41
Figure 17: Prism 2 Condenser Conguration - ON/OFF Condenser Options...................................................................42

5
RSMD-CM Technical Guide
OVERVIEW
Features and Applications
Features and Applications
The Refrigerant System Module for Digital Compressors with
Condenser Fans with Microchannel Coils (RSMD-CM) can
monitor and control up to two compressors and condensers.
The compressors can be in either a tandem or non-tandem
conguration. The module is designed for R410-A refrigerant.
The RSMD-CM is for units that match all of the following
criteria:
1. One or two circuits.
2. Compressors may be any mix of xed, two-step, and
digital.
3. Reheat is present on the rst circuit.
The RSMD-CM must be connected to a VCCX2 Controller. Up
to four RSMD-CM Modules can be connected, depending on the
size of the system. There are two E-BUS expansion ports which
allow the use of communicating sensors and E-BUS modules.
The RSMD-CM Module provides the following:
• Modulates the compressors to satisfy the Suction Coil
(Saturation) Temperature. The Suction Coil (Saturation)
Temperature Setpoint is reset by the VCCX2 Controller
to maintain the Supply Air Temperature during Cooling
Mode. During Dehumidification Mode, it controls
the compressors to directly maintain the Suction
(Saturation) Temperature Setpoint.
• When the Heat Pump is in Heating Mode, the RSMD-CM
modulates and stages the compressors to maintain a
given Supply Air Temperature Setpoint.
• Modulates the condenser to maintain the Head Pressure
Setpoint.
• Provides alarms and safeties for the compressor and
condenser operation.
• For convenience on split systems, with the proper
communication cable installed, the RSMD-CM
provides a port for connecting the Modular Service
Tool SD to the VCCX2.
• Provides a 2 x 8 LCD character display and four buttons
that allow access to system status, setpoints, alarms and
some conguration settings.

6RSMD-CM Technical Guide
OVERVIEW
Dimensions
Figure 1: RSMD-CM Dimensions
1.33 1.50
1.50
0.45
6.15
3.09
3.07
4.96
5.26
5.55
0.75 4.10 0.74
5.05
1.50
0.52
1.33
1.50
GND
TEMP3
TEMP2
TEMP1
TB9
GND +5V
D12
BIN4
D11
BIN3
D10
BIN2
D9
BIN1
TB12
GND
HP-2
+5V
TB8
GND
J1 C
C
SP-2
+5V
TB6
GND
HP-1
+5V
TB3 POWER
COMM
ALARM
STATU
GND
SP-1
+5V
TB4
YS102632 REV 1
R30 4751
R1
R34 4751
R2
4751 R38
R3
4751 R42
R4
4751 R58
R5
COM
V6
TB7
COMP1
24VAC
P6
COMP2
TB11
AOUT 1
AOUT 2
GND
P2
HH485
R+
GND
T-
TB2
C20
.01uF
I
O
I
O
OMRON
G5Q-1A4
DC12V
SA
5A30VDC
CHINA 10A250VAC~
R14
R27
R28 R31
R32 R35
R36 R39
R40 R44
R43
C43
R49
R48
R56
R54
1002
1002
1002
1002
1002
1002
.1uF
1002
1002
.1uF
1002
1002
.1uF
1002
1002
.1uF
1002
1002
.1uF
1002
1002
SERIAL #
ALARM
UP
DOWN
ENTERMENU
AAON P/N:ASM06709
+24 VAC
GND
RELAY CONTACT
RATING IS 1 AMP
MAX @ 24 VAC
CONDENSER 1
COMP 1
COMP 2
ANALOG OUT
REVERSING VALV E
COMMON
RELAY OUTPUT
TERMINALS
LABEL P/N:
G102070
COND 1
COND 2
GND
24 VAC
POWER ONLY
WARNING!
POLARITY
MUST BE
OBSERVED
OR THE
CONTROLLER
WILL BE
DAMAGED
CONDENSER 2
HEAD PRES 1
+5 V
+5 V
COMP DIS 1
COMP 1
SP-1
HP-1
COMP DIS 2
COMP 2
GND
GND
OA COIL/POWF
EMER SHDN
GND
LEAVING H20
GND
SUCTION PRES 2
HEAD PRES 2
+5 V
+5 V
SP-2
HP-2
GND
GND
R+
SHD
T-
R+ SHD T-
E-BUS DUAL E-BUS
EXPANSION
RSMD-CM
www.aaon.com
SUCTION PRES 1
Note: All dimensions are in inches.

7
RSMD-CM Technical Guide
Table 1: RSMD-CM Module Electrical
and Environmental Requirements
INSTALLATION AND WIRING
Electrical and Environmental Requirements
General
Correct wiring of the AAON controller and its modules is the
most important factor in the overall success of the installation
process. The AAON controller and modules are factory
installed and wired at the AAON factory. Some of the following
information may not apply to your installation if it was pre-wired
at the factory. However, if troubleshooting of the controller or
modules is required, it is a good idea to be familiar with the
system wiring.
Wiring
The modules must be connected to an 18-30 VAC power source
of the proper size for the calculated VA load requirements. All
transformer sizing should be based on the VA ratings listed in
Table 1, this page.
NOTE: If the temperature at the controller is below -4ºF
(-20ºC), the display refresh rate could be less
responsive.
WARNING: When using a single transformer to power
more than one controller or expansion
module, the correct polarity must always
be maintained between the boards. Failure
to observe correct polarity will result in
damage to the unit controller, RSMD-CM,
and any associated module.
Please carefully read and apply the following information when
wiring the unit controller, RSMD-CM, and any associated
module.
1. All wiring is to be in accordance with local and
national electrical codes and specications.
2. All 24 VAC wiring must be connected so that all
ground wires remain common. Failure to follow this
procedure can result in damage to the controller and
connected devices.
3. Minimum wire size for 24 VAC wiring should be
18-gauge.
4. Minimum wire size for all sensors should be 24-gauge.
Some sensors require two-conductor wire and some
require three-or four-conductor wire.
5. Minimum wire size for 24 VAC thermostat wiring
should be 22-gauge.
6. Be sure that all wiring connections are properly
inserted and tightened into the terminal blocks. Do
not allow wire strands to stick out and touch adjoining
terminals which could potentially cause a short circuit.
7. When communication wiring is used to interconnect
HVAC unit controllers together or to connect to other
communication devices, all wiring must be plenum-
rated, minimum 18-gauge, two-conductor, twisted pair
with shield. AAON can supply communication wire
that meets this specication and is color coded for
the network or local loop. Please consult your AAON
distributor for information. If desired, Belden #82760
or equivalent wire may also be used.
8. Before applying power to the HVAC unit controller,
RSMD-CM Modules, and any associated modules,
be sure to recheck all wiring connections and
terminations thoroughly.
Powering Up
When the controller and modules are rst powered up, the
POWER LED should light up and stay on continuously. If it does
not light up, check to be sure that you have 24 VAC connected
to the controller, that the wiring connections are tight, and that
they are wired for the correct polarity. The 24 VAC power must
be connected so that all ground wires remain common. If after
making all these checks, the POWER LED does not light up,
please contact AAON Controls Support for assistance.
Control
Device
Voltage
VA Load
Operating
Temperature
Humidity
(Non-
Condensing)
RSMD-CM
Module
18-30VAC 18 -22°F to 158°F
-30ºC to 70ºC 0-95% RH
Inputs
Resistive Inputs require 10KΩ
Type 3 Thermistor
24VAC Inputs provide 4.7kΩ
Load
Outputs Relay Outputs: 1 amp
maximum per output.

8RSMD-CM Technical Guide
WIRING
Inputs Wiring
RSMD-CM Wiring
The RSMD-CM provides three analog inputs, four binary inputs,
ve relays, and two analog outputs. See Figure 2, this page, for
inputs wiring and Figure 3, page 9, for outputs wiring.
WARNING: Observe polarity! All boards must be wired
with GND-to-GND and 24-VAC-to-24
VAC. Failure to observe polarity will result
in damage to one or more of the boards.
Expansion modules must be wired in such
a way that the expansion modules and the
controller are always powered together. Loss
of power to the expansion module will cause
the controller to become inoperative until
power is restored to the expansion module.
Suction Pressure Transducer Wiring
The Suction Pressure Transducers must be wired as shown
in Figure 2, this page. It is typically required for all VCCX2
applications.
The Suction Pressure Transducers are used to measure suction
pressure at the HVAC unit’s DX evaporator coil suction line.
This suction line pressure is converted to saturated refrigerant
temperature. The saturated refrigerant temperature is used to
properly control the compressors to maintain a given Suction
Coil (Saturated) Temperature Setpoint. In Cooling Mode,
the VCCX2 resets the Suction Coil (Saturated) Temperature
Setpoint to maintain a given Supply Air Temperature Setpoint.
In Dehumidification Mode, the Suction Coil (Saturated)
Temperature Setpoint is a user congurable setpoint that can be
reset based on indoor humidity levels.
Figure 2: RSMD-CM Inputs Wiring
GND 18-30
VAC
Head Pressure 2
Transducer (by others)
Comp. Discharge
Temp 1 Sensor
Comp. Discharge
Temp 2 Sensor
Leaving Water
Temp Sensor
Comp Status 1
Comp Status 2
Outside Coil Temp/POWF
Emergency Shutdown
Suction Pressure 1
Transducer
RD
WT
BL
Head Pressure 1
Transducer (by others)
Suction Pressure 2
Transducer
Line Voltage
ALARM
UP
DOWN
ENTERMENU
AAON P/N:ASM06709
+24 VAC
GND
RELAY CONTACT
RATING IS 1 AMP
MAX @ 24 VAC
CONDENSER 1
COMP 1
COMP 2
ANALOG OUT
REVERSING VALV E
COMMON
RELAY OUTPUT
TERMINALS
LABEL P/N:
G102070
COND 1
COND 2
GND
24 VAC
POWER ONLY
WARNING!
POLARITY
MUST BE
OBSERVED
OR THE
CONTROLLER
WILL BE
DAMAGED
CONDENSER 2
HEAD PRES 1
+5 V
+5 V
COMP DIS 1
COMP 1
SP-1
HP-1
COMP DIS 2
COMP 2
GND
GND
OA COIL/POWF
EMER SHDN
GND
LEAVING H20
GND
SUCTION PRES 2
HEAD PRES 2
+5 V
+5 V
SP-2
HP-2
GND
GND
R+
SHD
T-
R+ SHD T-
E-BUS DUAL E-BUS
EXPANSION
RSMD-CM
www.aaon.com
SUCTION PRES 1
RD
WT
BL
RD
WT
BL
RD
WT
BL

9
RSMD-CM Technical Guide
WIRING
Outputs Wiring
Head Pressure Control
The Head Pressure Transducers are used to measure Head
Pressure at the discharge line. This Head Pressure is used to
drive the condenser fans with a 0-10 VDC output signal or
valve with a 2-10 VDC output signal to maintain a given Head
Pressure Setpoint.
Compressor Discharge Sensors
The Digital Compressor Discharge Temperature Sensor monitors
the discharge temperature from the digital compressor to protect
against overheating.
Leaving Water Temperature Sensor
The Leaving Water Temperature Sensor is used to measure the
Leaving Water Temperature when used on a water source heat
pump unit.
CAUTION: Suction pressure transducers should
be installed in a vertical portion of the
suction line to prevent refrigerant oil from
accumulating in the sensor.
NOTE: If there are two compressors on a single circuit (a
tandem circuit), Suction Pressure 2, Head Pressure
2, and Condenser Signal 2 would not be used.
Figure 3: RSMD-CM Outputs Wiring
GND 18-30
VAC
Line Voltage
Actuator
NOTE:
All relay outputs are normally open
and rated for 24 VAC power only.
1 Amp maximum load.
24 VAC ONLY
COMPRESSOR 1 ENABLE
COMPRESSOR 2 ENABLE
CONDENSER 1 ENABLE
CONDENSER 2 ENABLE
REVERSING VALVE
Digital Compressor 1 Unloader
Digital Compressor 2
Signal 1
Condenser
Condenser
Signal 2
WSE Bypass
Valve Actuator
Wires to VCCX2
Loop Communications
connector when used on
a split system.
GND
+
GND
+
COM
+
COM
+
GND
TEMP3
TEMP2
TEMP1
TB9
GND +5V
D12
BIN4
D11
BIN3
D10
BIN2
D9
BIN1
TB12
GND
HP-2
+5V
TB8
GND
J1 C
C
SP-2
+5V
TB6
GND
HP-1
+5V
TB3 POWER
COMM
ALARM
STATU
GND
SP-1
+5V
TB4
YS102632 REV 1
R30 4751
R1
R34 4751
R2
4751 R38
R3
4751 R42
R4
4751 R58
R5
COM
V6
TB7
COMP1
24VAC
P6
COMP2
TB11
AOUT 1
AOUT 2
GND
P2
HH485
R+
GND
T-
TB2
C20
.01uF
I
O
I
O
OMRON
G5Q-1A4
DC12V
SA
5A30VDC
CHINA 10A250VAC~
R14
R27
R28 R31
R32 R35
R36 R39
R40 R44
R43
C43
R49
R48
R56
R54
1002
1002
1002
1002
1002
1002
.1uF
1002
1002
.1uF
1002
1002
.1uF
1002
1002
.1uF
1002
1002
.1uF
1002
1002
SERIAL #
ALARM
UP
DOWN
ENTERMENU
AAON P/N:ASM06709
+24 VAC
GND
RELAY CONTACT
RATING IS 1 AMP
MAX @ 24 VAC
CONDENSER 1
COMP 1
COMP 2
ANALOG OUT
REVERSING VALV E
COMMON
RELAY OUTPUT
TERMINALS
LABEL P/N:
G102070
COND 1
COND 2
GND
24 VAC
POWER ONLY
WARNING!
POLARITY
MUST BE
OBSERVED
OR THE
CONTROLLER
WILL BE
DAMAGED
CONDENSER 2
HEAD PRES 1
+5 V
+5 V
COMP DIS 1
COMP 1
SP-1
HP-1
COMP DIS 2
COMP 2
GND
GND
OA COIL/POWF
EMER SHDN
GND
LEAVING H20
GND
SUCTION PRES 2
HEAD PRES 2
+5 V
+5 V
SP-2
HP-2
GND
GND
R+
SHD
T-
R+ SHD T-
E-BUS DUAL E-BUS
EXPANSION
RSMD-CM
www.aaon.com
SUCTION PRES 1
Actuator must be 0-10 VDC with
24 VAC power. Confirm wiring
terminations with manufacturer's
wiring instructions.
1 COM
2 +
3 Y1

10 RSMD-CM Technical Guide
INPUTS AND OUTPUTS
Inputs/Outputs Map
Inputs/Outputs Map
See Table 2, this page, for the RSMD-CM inputs and outputs.
Table 2: RSMD-CM Inputs and Outputs
REFRIGERATION SYSTEM MODULE
FOR DIGITAL COMPRESSORS
Analog Inputs
1Suction Pressure 1 (SP-1)
2Head Pressure 1 (HP-1)
3Suction Pressure 2 (SP-2)
4Head Pressure 2 (HP-2)
5Compressor Discharge Temperature 1 Sensor (TEMP1)
6Compressor Discharge Temperature 2 Sensor (TEMP2)
7Leaving Water Temperature Sensor (TEMP3)
Binary Inputs
1Compressor Status 1 (BI1)
2Compressor Status 2 (BI2)
3Outdoor Coil Temperature / Proof of Water Flow (BI3)
4Emergency Shutdown (BI4)
Analog Outputs
1Condenser 1 Signal (AO1)
2Condenser 2 Fan Signal (0-10 VDC) or WSE Bypass
Actuator (2-10 VDC) (AO2)
Relay Outputs (24 VAC)
1Compressor 1 Enable Relay (RLY1)
2Compressor 2 Enable Relay (RLY2)
3Condenser 1 Enable Relay (RLY3)
4Condenser 2 Enable Relay (RLY4)
5Reversing Valve Relay (RLY5)
NOTE: AO1 Fan is 0-10 VDC and water valve is 2-10 VDC.
Inputs and Outputs
+5V - VDC Power
This output is a 5 VDC output that supplies power to the Suction
Pressure Transducers.
SP-1 and SP-2 - Suction Pressure Transducers
The Suction Pressure Transducers are used to measure suction
pressure at the HVAC unit’s DX evaporator coil suction line.
This suction line pressure is converted to saturated refrigerant
temperature. The saturated refrigerant temperature is used to
properly control the compressors to maintain a given Suction
Coil (Saturated) Temperature Setpoint. In Cooling Mode,
the VCCX2 resets the Suction Coil (Saturated) Temperature
Setpoint to maintain a given Supply Air Temperature Setpoint.
In Dehumidification Mode, the Suction Coil (Saturated)
Temperature Setpoint is a user congurable setpoint that can be
reset based on indoor humidity levels.
+5V - VDC Power
This output is a 5 VDC output that supplies power to the Head
Pressure Transducers.
HP-1 and HP-2 - Head Pressure Transducers
The Head Pressure Transducers are used to measure Head
Pressure at the discharge line. This Head Pressure is used to drive
the condenser fans to maintain a given Head Pressure Setpoint.
TEMP1 and TEMP2 - Compressor Discharge
Temperature Sensor 1 and Sensor 2 Input
The Digital Compressor Discharge Temperature Sensors monitor
the discharge temperature from the digital compressor to protect
against overheating.
TEMP3 - Leaving Water Temperature Sensor Input
This input monitors the condenser leaving water temperature
and determines if the water source condenser is operating in a
safe water temperature range.
BI1 - Compressor Status 1
When this wet contact input closes, a 24 volt signal to BI1
indicates Compressor 1 is running. If BI1 (Compressor Status
Input) becomes de-energized while the compressor is running,
a high pressure alarm is triggered. The high pressure switch
and low pressure switch are in series. Check both switches if an
alarm occurs. The alarm will de-energize the compressor output
for two minutes and then re-energize the output.

11
RSMD-CM Technical Guide
INPUTS AND OUTPUTS
Inputs and Outputs
BI2 - Compressor Status 2
If wired non-tandem: When this wet contact input closes, a 24
volt signal to BI2 indicates Compressor 2 is running. If BI2
(Compressor Status Input) becomes de-energized while the
compressor is running, a high pressure alarm will be triggered.
The high pressure switch and low pressure switch are in
series. Check both switches if an alarm occurs. The alarm will
de-energize the compressor output for two minutes and then
re-energize the output.
If wired in tandem: When this wet contact input closes, a 24
volt signal to BI2 indicates that Compressor 2 is running. If
BI2 (Compressor Status Input) becomes de-energized while the
compressor is running, a compressor alarm will be triggered
and the compressor will de-energize RLY2, shutting down the
compressor, and lock it out.
BI3 - Outdoor Coil Temperature/Proof of Water Flow
Status
This input can be used for the following two options:
• Air to Air Heat Pump: This wet contact input monitors
a Defrost Coil Temperature Switch on air to air heat
pump units. If the compressors are operating in the
Heating Mode and this switch closes, it will initiate a
Defrost Mode.
• Water Source Heat Pump: This wet contact input is for
the Water Proof of Flow Switch. If the Water Proof of
Flow Switch contact opens while the condenser valve is
operating, the controller will react to protect the system
depending on the current mode of operation.
BI4 - Emergency Shutdown
This wet contact input is used to initiate shutdown of the HVAC
unit when a normally closed Smoke Detector (by others), Firestat
(by others), or other shutdown condition (by others) contact is
opened. The controller remains active and can initiate alarm
relays.
NOTE: The binary inputs require wet contacts (24 VAC
only) to recognize an active input. If you provide
dry contacts, the contact closure will not be
recognized.
AO1 - Condenser 1 Fan Signal
This 0-10 VDC output is used to control/modulate the Condenser
1 Fan /Valve to maintain the Head Pressure Setpoint.
AO2 - Condenser 2 Fan Signal or Waterside
Economizer Bypass Actuator Valve
This 0-10 VDC output is used to control/modulate the Condenser
2 Fan /Valve to maintain the Head Pressure Setpoint or this output
signal is a Direct Acting 2-10 VDC output signal that is used to
modulate the waterside Economizer Bypass Actuator.
RLY1 - Compressor 1 Enable
This relay enables Compressor 1.
RLY2 - Compressor 2 Enable
This relay enables Compressor 2.
RLY3 - Condenser 1 Enable
This relay enables the Condenser 1 Fan/Water Valve.
RLY4 - Condenser 2 Enable
This relay enables the Condenser 2 Fan/Water Valve.
RLY5 - Reversing Valve Enable
This relay enables the Reversing Valve.

12 RSMD-CM Technical Guide
SEQUENCE OF OPERATIONS
Cooling Mode, Dehumidication, and Head Pressure Control
Cooling Mode Operation
In the Cooling Mode, as Supply Air Temperature (SAT) rises
above the Active SAT Cooling Setpoint, the compressors will
stage on and modulate to maintain the Active Evaporator Coil
Suction (Saturation) Temperature Setpoint. Two compressors are
controlled per RSMD-CM. Multiple RSMD-CM Modules are
needed when there are more than two compressors.
Modules with One Digital and One Fixed Compressor
If the digital compressor modulates to 100% and the SAT is
still above the SAT Cooling Setpoint for the Cooling Stage
Up Delay, then the xed compressor will stage on. The digital
compressor will then be allowed to modulate as necessary
to maintain the Active Evaporator Coil Suction (Saturation)
Temperature Setpoint. Minimum o times must also be met
before compressors can stage on.
Modules with Multiple Digital Compressors
If the rst digital compressor modulates to 100% and the SAT is
still above the SAT Cooling Setpoint for the Cooling Stage Up
Delay, then the second digital compressors will enable and the
two digital Compressors will then modulate together to maintain
the Active Evaporator Coil Suction (Saturation) Temperature
Setpoint.
Staging Down Compressors
If the digital compressor(s) have modulated down to 30% for
the Stage Down Delay period and the SAT has fallen below the
SAT Cooling Setpoint minus the Stage Control Window, then the
last compressor to have staged on (digital or xed) will stage o
assuming its Minimum Run Time has been met. Any remaining
digital compressors are then allowed to modulate as needed. If
the last remaining digital compressor reaches 0% for the Stage
Down Delay, it will stage o.
Dehumidication Operation
The RSMD-CM activates the Cooling Stages based on the
Evaporator Coil Temperature compared to the Evaporator Coil
Suction (Saturation) Temperature Setpoint. The Evaporator
Coil Suction (Saturation) Temperature is calculated by using
the Suction Pressure Transducer and converting the pressure to
temperature.
For Copeland™ Digital Scroll Compressor units, the RSMD-CM
will modulate the Copeland Digital Scroll™ Compressor to
maintain the Evaporator Coil Suction (Saturation) Temperature
Setpoint and activate the compressors as necessary.
On units that have one digital and one xed capacity compressor,
if the xed capacity compressor is activated, the Copeland™
Digital Scroll Compressor will only be allowed to modulate
within the range of 70-100% in order to prevent the loss of reheat
capacity during low load conditions. If, with both compressors
on, the rst digital compressor has modulated down to its 70%
minimum and the Coil Suction Temperature falls below the Coil
Temperature Setpoint minus the Cooling Stage Control Window,
then the second compressor will stage o once its Compressor
Minimum Run Time and the Stage Down Delay Times have been
met. At that point, the Copeland™ Digital Scroll Compressor
can modulate down as needed to maintain the Coil Temperature
Setpoint.
If the RSMD-CM has two digital compressors, the first
compressor will be locked at 100% and the second compressor
will modulate.
Head Pressure Control
The RSMD-CM can monitor a Head Pressure Transducer and
control a condenser fan or water valve to maintain a Head
Pressure Setpoint.
A condenser relay is commanded on when the rst compressor
is enabled (except if the unit Heat Pump is in Defrost Mode).
On an air cooled unit, the condenser fan will be controlled with
0-10 VDC output signal. On a water cooled unit, the water valve
will be controlled with a 2-10 VDC signal.
When the Condenser Signal rst activates, it maintains at 100%
for 10 seconds.
In the Cooling Mode, the Condenser Signal will modulate to
maintain the Cooling Head Pressure Setpoint. On units with a
condenser fan, the signal can modulate between 15% and 100%.
On a unit with a condenser water valve, the signal can modulate
between 25% and 100%. If the Head Pressure exceeds 550 psig,
the Condenser Control Signal will immediately go to 100% and
a High Head Pressure Alarm will be generated. The alarm will
be deactivated when the Head Pressure drops below 540 psig.
In the Dehumidication Mode, the Condenser Output Signal
controls to the Reheat Head Pressure Setpoint. High Head
Pressure conditions produce the same eects as in the Cooling
Mode.
If no Head Pressure Transducer is detected, the Condenser Output
Signal will be maintained at 100%.

13
RSMD-CM Technical Guide
LCD SCREENS
LCD Display Screen and Navigation Keys
LCD Display Screen and Navigation Keys
The LCD display screens and buttons allow you to view status
and alarms, and enable force modes. See Figure 4, this page,
and refer to Table 3, this page, for descriptions.
Navigation
Key Key Function
MENU Use the MENU key to move through screens
within Main Menu categories and return to the
Main Menu while at other screens.
UP Use this key to adjust setpoints and change
congurations.
DOWN Use this key to adjust setpoints and change
congurations.
ENTER Use the ENTER key to navigate through the
Main Menu Screen categories.
ALARM
UP
DOWN
ENTERMENU
Figure 4: LCD Display and Navigation Keys
Table 3: Navigation Key Functions

14 RSMD-CM Technical Guide
LCD SCREENS
Main Screens Map
Main Screens Map
Refer to the following map when navigating through the LCD
Main Screens. To scroll through the screens, press the <MENU>
button.
RSMD
1067vxxx
Press to scroll through REFRIG MODULE screens.
Press to go to SYSTEM STATUS screens.
SYSTEM
STATUS
Press to scroll through SYSTEM STATUS screens.
Press to go to SENSOR STATUS screens.
SENSOR
STATUS
Press to scroll through SENSOR STATUS screens.
Press to go to ALARMS screens.
ALARMS
Press to scroll through ALARMS screens.
Press to go to ALARM HISTORY screens.
ALARM
HISTORY
Press to scroll through ALARM HISTORY screens.
Press to go to SETPOINT STATUS screens.
SETPOINT
STATUS
Press to scroll through SETPOINT STATUS screens.

15
RSMD-CM Technical Guide
LCD SCREENS
Module Screens
Module Screens
Refer to the following map when navigating through the
RSMD-CM Screens. From the RSMD-CM Screen, press
<ENTER> to scroll through the screens.
RSMD
1067vxxx
EBUS COMM
PACKETS
E-BUS COMMUNICATION DIAGNOSTICS
Number of COMM packets received.
SOFTWARE
1067vXXX
CURRENT SOFTWARE VERSION
You can access the protected screens from this screen by holding
the <UP> button for ve seconds.
BOARD/EBUS
ADDRESS
CURRENT BOARD ADDRESS
#COMP
CONFIGURED
# OF COMPRESSORS CONFIGURED
#COND
CONFIGURED
# OF CONDENSERS CONFIGURED
COMP A1-B1
FIXED OR DIG
COMPRESSOR A1 or B1 - FIXED or DIGITAL
COMP A2-B2
FIXED OR DIG
COMPRESSOR A2 or B2 - FIXED or DIGITAL

16 RSMD-CM Technical Guide
LCD SCREENS
System Status Screens
System Status Screens
Refer to the following map when navigating through the System
Status Screens. From the SYSTEM STATUS Screen, press
<ENTER> to scroll through the screens.
SYSTEM
STATUS
MODE OF
OPERATION
SYSTEM MODE OF OPERATION
Possible Choices are:
OFF, COOL, HEAT, DEHUMID, FORCE
COMP A1-B1
OFF/
MODULATING %
COMPRESSOR A1, B1
(based on board address)
OFF / MOD POSITION
OFF: Compressor is o.
MODULATING PERCENTAGE: 0-100%
COMP A2-B2
ON/OFF
COMPRESSOR A2, B2
(based on board address)
ON, OFF, FORCED
OFF: Compressor is o.
ON: Compressor is on.
COND 1 FAN
OFF/
MODULATING %
CONDENSER FAN 1
OFF / MOD POSITION
OFF: Condenser is o.
MODULATING PERCENTAGE: 0-100%
COND 2 FAN
OFF/
MODULATING %
CONDENSER FAN 2
OFF / MOD POSITION
OFF: Condenser is o.
MODULATING PERCENTAGE: 0-100%
BYPS VLV
CLOSED OR
% VALVE
WATERSIDE ECONOMIZER BYPASS VALVE
CLOSED or MOD POSITION
CLOSED: Valve is closed.
VALVE PERCENTAGE: 0-100%
DEFROST
# MINUTES
DEFROST INTERVAL TIMER
# of MINUTES
OR
If congured for Water Source Heat Pump
H2O FLOW
YES/NO
WATER FLOW
YES/NO

17
RSMD-CM Technical Guide
LCD SCREENS
Sensor Status Screens
Sensor Status Screens
Refer to the following map when navigating through the Sensor
Status Screens. From the SENSOR STATUS Screen, press
<ENTER> to scroll through the screens.
SENSOR
STATUS
SUCTION 1
XXX PSI
SUCTION PRESSURE 1 READING FROM INPUT
HEAD PR1
XXX PSI
HEAD PRESSURE 1 READING FROM INPUT
SUCTION 2
XXX PSI
SUCTION PRESSURE 2 READING FROM INPUT
HEAD PR2
XXX PSI
HEAD PRESSURE 2 READING FROM INPUT
CALC CT1
XX DEG
CALCULATED COIL TEMPERATURE 1 FROM SUCTION
PRESSURE 1 INPUT
CALC CT2
XX DEG
CALCULATED COIL TEMPERATURE 2 FROM SUCTION
PRESSURE 2 INPUT
COMPTMP1
XX DEG
COMPRESSOR TEMPERATURE 1 READING FROM HEAD
PRESSURE 1 INPUT
COMPTMP2
XX DEG
COMPRESSOR TEMPERATURE 2 READING FROM HEAD
PRESSURE 2 INPUT
OR
If congured for Water Source Heat Pump
H2O TEMP
XX DEG
WATER TEMPERATURE READING FROM LEAVING WATER
TEMPERATURE SENSOR

18 RSMD-CM Technical Guide
LCD SCREENS
Setpoint Status Screens
Setpoint Status Screens
Refer to the following map when navigating through the Setpoint
Status Screens. From the SETPOINT STATUS Screen, press
<ENTER> to scroll through the screens.
SETPOINT
STATUS
COILT SP
35 DEG
COIL TEMPERATURE SETPOINT STATUS
Valid range is 35ºF to 70ºF. Default is 35ºF.
IF CONFIGURED FOR MODULATING CONDENSER, THE
FOLLOWING SCREEN WILL DISPLAY
HEADPRSP
340 PSI
HEAD PRESSURE SETPOINT STATUS
Valid range is 275 to 475 psi. Default is 340 psi.
IF CONFIGURED FOR FAN CYCLE, THE FOLLOWING
TWO SCREENS WILL DISPLAY
FAN ON
XX PSI
HEAD PRESSURE READING WHEN FAN CYCLE IS ON
FAN OFF
XX PSI
HEAD PRESSURE READING WHEN FAN CYCLE IS OFF
IF CONFIGURED WATER SOURCE HEAT PUMP, THE
FOLLOWING THREE SCREENS WILL DISPLAY
GLYCOL %
%
GLYCOL PERCENTAGE STATUS
LOW SUCT
95 PSI
LOW SUCTION PRESSURE SETPOINT STATUS
Default is 95 psi.
LOW H2O
37 DEGF
LOW LEAVING WATER TEMPERATURE SETPOINT STATUS
Default is 37ºF.
IF CONFIGURED FOR AIR TO AIR HEAT PUMP, THE
FOLLOWING SCREEN WILL DISPLAY
DEFR INT
30 MIN
DEFROST INTERVAL SETPOINT STATUS
Default is 30 minutes.

19
RSMD-CM Technical Guide
LCD SCREENS
Alarms Screens
Alarms Screen
If an alarm is present, the ALARM LED above the LCD display
will light up red and blink. The Alarms will display and scroll
automatically from the ALARMS screen when alarms are present.
The alarms are as follows:
NO ALARMS: This will be shown if there are no current alarms.
EBUS SLAVE (SLV) TIMEOUT: This alarm indicates that
communication has been lost between the RSMD-CM and the
Main controller or other E-BUS modules that may be connected.
This can be the result of a bad cable, a missing cable, or the
module not being congured properly.
NO SUCTION PRESSURE TRANSDUCER 1 (SUCT1)
DETECTED: This alarm indicates the Suction Pressure Transducer
1 is not detected by the system. There is no compressor failure
from this alarm. The failure will be unsafe suction pressure.
NO SUCTION PRESSURE TRANSDUCER 2 (SUCT2)
DETECTED: This alarm indicates the Suction Pressure Transducer
2 is not detected by the system. There is no compressor failure
from this alarm. The failure will be unsafe suction pressure.
NO HEAD PRESSURE TRANSDUCER 1 (HEAD1) DETECTED:
This alarm indicates the Head Pressure Transducer 1 is not
detected by the system. This will cause the condenser fan/valve
to go to 100%.
NO HEAD PRESSURE TRANSDUCER 2 (HEAD2) DETECTED:
This alarm indicates the Head Pressure Transducer 2 is not
detected by the system. This will cause the condenser fan/valve
to go to 100%.
HIGH HEAD PRESSURE 1 (HP1) DETECTED: This alarm
indicates when the Head Pressure 1 rises above 550 psig. This
will cause the condenser to go to 100%.
HIGH HEAD PRESSURE 2 (HP2) DETECTED: This alarm
indicates when the Head Pressure 2 rises above 550 psig. This
will cause the condenser to go to 100%.
LOW SUCTION PRESSURE 1 (SP1) FAILURE: This alarm will
occur if Suction Pressure 1 stays below the Low Suction Pressure
Setpoint for one minute or falls below 40 psi for ve seconds.
This alarm will shut down the system. Power must be cycled to
clear the alarm.
LOW SUCTION PRESSURE 2 (SP2) FAILURE: This alarm will
occur if Suction Pressure 2 stays below the Low Suction Pressure
Setpoint for one minute or falls below 40 psi for ve seconds.
This alarm will shut down the system. Power must be cycled to
clear the alarm.
LOW SUCTION PRESSURE 1 (SP1) DETECTED: This alarm
will occur if Suction Pressure 1 falls below the Low Suction
Pressure Setpoint for 20 seconds. The system will try to protect
itself by lowering compressor modulation percentage.
LOW SUCTION PRESSURE 2 (SP2) DETECTED: This alarm
will occur if Suction Pressure 2 falls below the Low Suction
Pressure Setpoint for 20 seconds. The system will try to protect
itself by lowering compressor modulation percentage.
COMPRESSOR 1 (COMP1) HPS FAULT: This alarm occurs if the
relay is energized and the binary input is energized but the binary
input de-energizes within the rst 15 minutes of the compressor
call. The module allows four retries but locks out on the fth
fault. This sequence is intended to help the startup of units with
microchannel coils and prevent nuisance lockouts when the coil is
cold. If a fault occurs after the rst 15 minutes of the compressor
call, the module will allow one retry, and will lock out if another
fault occurs within two hours. If any faults have occurred, but
the module is not locked out, the fault counter will reset to zero
if the RSMD-CM goes to O Mode OR the compressor has run
successfully for two hours since the last fault.
COMPRESSOR 1 (COMP1) FAULT: If the relay energizes but the
binary input never energizes, this alarm occurs if the compressor
fails to run 45 seconds after the relay is activated. This causes an
alarm and de-energizes the compressor enable relay. The system
will retry after ve minutes.
COMPRESSOR 2 (COMP2) FAULT (if wired in tandem): If the
relay energizes but the binary input never energizes: This alarm
occurs if the compressor fails to run 45 seconds after the relay is
activated. This causes an alarm and shuts down the compressor
(relay). The system will retry after ve minutes.
COMPRESSOR 2 (COMP2) HPS FAULT (if not in tandem): If
the relay is energized and the binary input is also energized: If
the binary input de-energizes within the rst 15 minutes of the
compressor call, the module will allow four retries, and will lock
out on the fth fault. This sequence is intended to help the startup
of units with microchannel coils and prevent nuisance lockouts
when the coil is cold. If a fault occurs after the rst 15 minutes
of the compressor call, the module will allow one retry, and will
lock out if another fault occurs within two hours. If any faults
have occurred, but the module is not locked out, the fault counter
will reset to zero if the RSMD-CM goes to O Mode OR the
compressor has run successfully for two hours since the last fault.
ALARMS

20 RSMD-CM Technical Guide
LCD SCREENS
Alarms Screens
COMPRESSOR 2 (COMP2) FAULT (if not in tandem): If the
relay energizes but the binary input never energizes, this alarm
occurs if the compressor fails to run 45 seconds after the relay is
activated. This causes an alarm and de-energizes the compressor
enable (relay). The system will retry after ve minutes.
COMPRESSOR 1 (COMP1) BAD TEMPERATURE: This alarm
will occur if the Discharge Temperature Sensor 1 measures less
than -40ºF or more than 356ºF. This causes an alarm and de-
energizes the compressor enable (relay).
COMPRESSOR 2 (COMP2) BAD TEMPERATURE: This alarm
will occur if the Discharge Temperature Sensor 2 measures less
than -40ºF or more than 356ºF. This causes an alarm and de-
energizes the compressor enable (relay). The system will retry
after ve minutes.
COMPRESSOR 1 (COMP1) CUTOFF: This alarm will occur if
the Discharge Temperature Sensor 1 measures more than 265ºF.
This causes an alarm and de-energizes the compressor enable
(relay). The system will can be restarted after 30 minutes.
COMPRESSOR 2 (COMP2) CUTOFF: This alarm will occur if
the Discharge Temperature Sensor 2 measures more than 265ºF.
This will cause an alarm and will shut down the compressor
(relay). The system will can be restarted after 30 minutes.
COMPRESSOR (COMP) 1 or 2 LOCKOUT: If active cuto
occurs ve times within a four-hour period, the compressor will
be locked out. Power must be cycled and the compressor restarted
to clear the alarm.
• If a circuit’s Suction Pressure twice within a two-hour
window falls below the Low Suction Pressure Setpoint
for longer than one minute, the compressor on that
circuit will be locked out. Manual reset or change of
mode is required to return to normal operation.
• If the Suction Pressure falls below the Unsafe Suction
Setpoint for ve seconds, that circuit’s compressor will
be locked out. Power will need to be cycled to restart
the unit.
• If the Leaving Water Temperature falls below the
setpoint, the last compressor will be locked out until the
Leaving Water Temperature rises 6ºF above setpoint.
• The Leaving Water Temperature remains below the
setpoint for one minute or falls 3ºF below the setpoint.
This alarm will disable when the Leaving Water
Temperature rises 12ºF above the setpoint.
NO PROOF OF WATER FLOW: This alarm occurs when there
is a call for a compressor and the Proof of Flow input is o for
more than three minutes or, if during Heat Pump heating mode,
the Proof of Flow input is open for more than two seconds. This
alarm will disable when the Proof of Flow is enabled.
LOW WATER TEMPERATURE: If both compressors are on and
water temperature goes below the setpoint, Compressor 2 will
fail. If both compressors are on and water temperature goes 3ºF
below the setpoint, both compressors will fail. If Compressor 2
is o or failed and water temperature is still low for one minute,
the Compressor 1 will also fail. This alarm will disable when the
leaving water temperature rises 6ºF above the setpoint.
EMERGENCY SHUTDOWN: If the Emergency Shutdown binary
input is not activated, the compressors will shut o.
COMPRESSOR 1 FALSE ACTIVE INPUT: If the compressor
relay is o but the compressor status binary input is activated
for 60 seconds, it will cause an alarm.
COMPRESSOR 2 FALSE ACTIVE INPUT: If the compressor
relay is o but the compressor status binary input is activated
for 60 seconds, it will cause an alarm.
WSHP HEATING OUT OF ENVELOPE FAULT: If the circuit
is running below the envelope consecutively for one minute,
the compressor(s) on the circuit will fail and an alarm will be
generated. The system will retry after ve minutes.
Table of contents
Other AAON Control Unit manuals
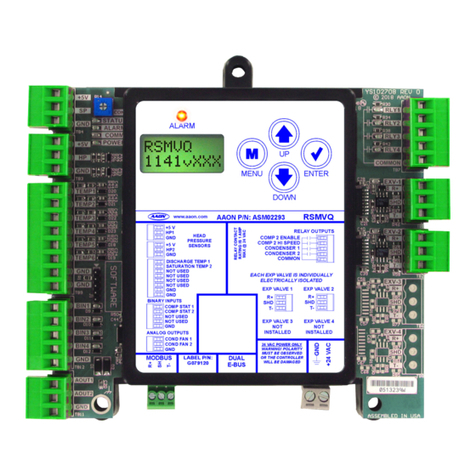
AAON
AAON RSMVQ Quick start guide
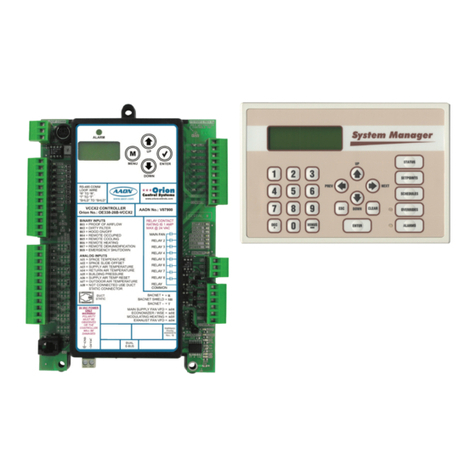
AAON
AAON SS1068 User manual
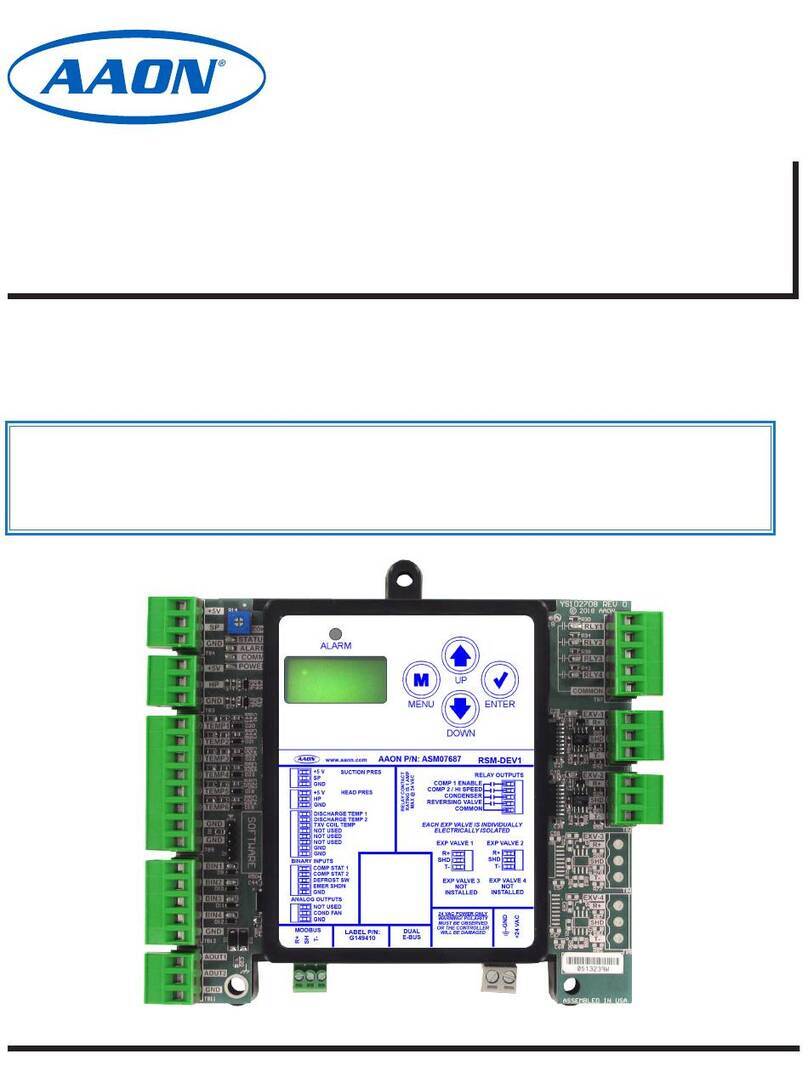
AAON
AAON RSM-DEV1 Quick start guide
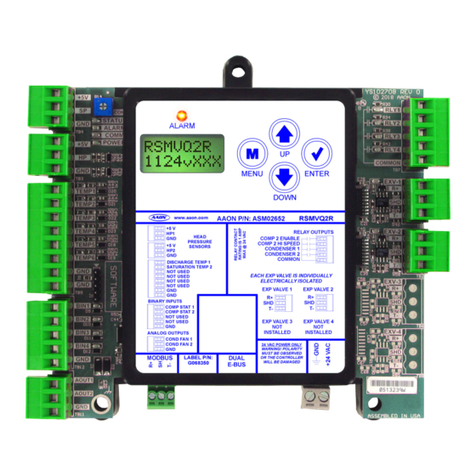
AAON
AAON RSMVQ2R Quick start guide
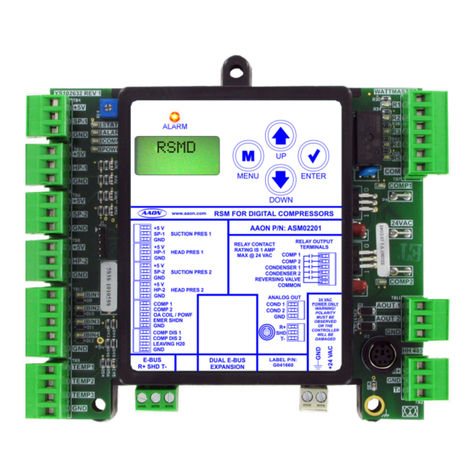
AAON
AAON RSMD Quick start guide
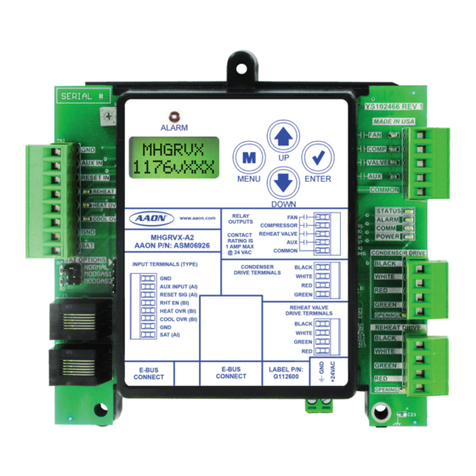
AAON
AAON MHGRVX-A2 Quick start guide
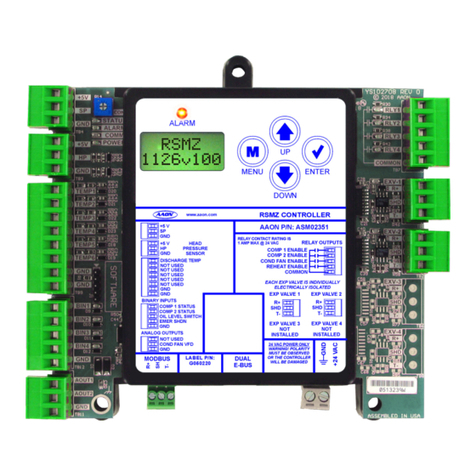
AAON
AAON RSMZ Quick start guide

AAON
AAON HP2C2 Quick start guide

AAON
AAON MODGAS-XWR2 Quick start guide
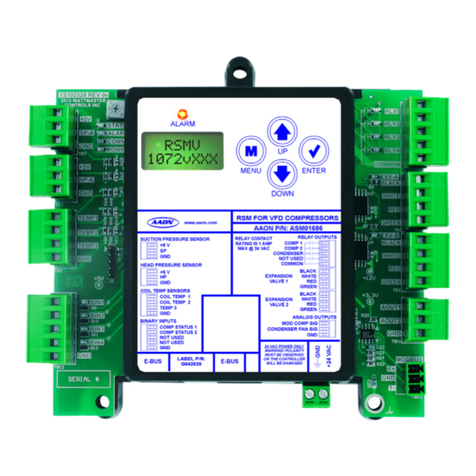
AAON
AAON RSMV ASM01686 Quick start guide