ABB M3LK 250 User manual

—
ADDITIONAL MOTOR MANUAL
Low voltage Water-cooled motors,
motor type M3LK 250

2
3GZF500725-144 EN 03-2023 | ABB IEC LV MOTORS

3
3GZF500725-144 EN 03-2023 | ABB IEC LV MOTORS
Contents
1. Validity........................................................................................................................................ 4
2. Safety Instructions .................................................................................................................... 4
2.1. General .......................................................................................................................................... 4
2.2. Intended Use................................................................................................................................ 4
2.3. Transport storage....................................................................................................................... 4
2.4. Installation.................................................................................................................................... 5
3. Electrical connection..................................................................................................................5
4. Operation.................................................................................................................................... 6
5. Maintenance and servicing ........................................................................................................ 7
6. Handling.......................................................................................................................................7
7. Lifting.......................................................................................................................................... 8
8. Water cooling ............................................................................................................................. 9
9. Connection ................................................................................................................................. 9
9.1. Requirements for cooling water .............................................................................................. 9
9.2. Filling or draining cooling water.............................................................................................10
10. Consendation drain holes ........................................................................................................10
11. Water leakage detector............................................................................................................10
12.Figures ....................................................................................................................................... 11
Contact us .......................................................................................................................................13

4
3GZF500725-144 EN 03-2023 | ABB IEC LV MOTORS
1. Validity
This additional installation, operation, and maintenance manual is valid for water cooled mo-
tors (M3LK 250) and is to be read together with the main manual (Low Voltage Motors/Man-
ual). Additional information may be required for some machines due to special application
and/or design considerations.
Usage:
Normally, water cooled motors are manufactured to specific customer requirements. How-
ever, these instructions refer to ’standard’ water cooled motor versions.
2. Safety Instructions
2.1. General
General safety regulations, safety precautions and specific agreements made for each work
site shown in this document must be observed all times.
2.2. Intended Use
Electric machines have dangerous live and rotating parts and may have hot surfaces. All oper-
ations serving transport, storage, installation, connection, commissioning, operation and
maintenance should be carried out by skilled personnel (in conformity with EN 50 110-1 / DIN
VDE 0105 / IEC 60364). Improper handling may cause serious personal injury and damage to
property.
These machines are intended for use as components for industrial and commercial installa-
tions as defined in the Machinery Directive (MD) 89/392/EEC. Commissioning is prohibited
until conformity of the end product with this directive has been established (follow particular
local safety and installation rules e.g. EN 60204).
These machines comply with the harmonized series of standards EN 60034 / DIN VDE 0530.
Their use in hazardous areas is prohibited unless they are expressly designed for such use.
Air-cooled models are typically designed for ambient temperatures of -20°C or -25°C up to
+40°C and altitudes of 1000 m above sea level, (Please refer to product specific instructions.
Ambient temperature for air-/water-cooled models should be no lower than +5°C without wa-
ter/glycol-based mixture for coolant. Do take note of deviating information on the rating
plate. Field conditions must conform to all rating plate markings. NOTE – Delete this section
once done!
2.3. Transport storage
Report damage immediately to the transport company if damage is discovered upon delivery
and stop commissioning, if necessary. Lifting eyes are only dimensioned for the weight of the
machine, therefore do not apply extra loads. Ensure the use of correct lifting eyes and if
needed, use suitable lifting equipment (e.g.rope guides). Remove shipping braces (e.g. bear-
ing locks, vibration dampers) before commissioning and store these for further use.
When storing machines make sure that the location is dry, and free from dust and vibration
to avoid bearing damage. Measure insulation resistance before commissioning. Limit values

5
3GZF500725-144 EN 03-2023 | ABB IEC LV MOTORS
for the insulation resistance can be found from the product specific manuals. If limit values
are not reached, dry the winding according to the manufacturer's instructions.
2.4. Installation
Ensure even support, solid foot or flange mounting and exact alignment in the case of direct
coupling. Avoid resonances with rotational and double mains frequency as a result of assem-
bly. Turn rotor and listen for abnormal slip noises and check direction of rotation in uncou-
pled state.
Follow the manufacturer’s instructions when mounting or removing couplings or other drive
elements and cover them with a touch guard. To do a trial run without output elements, lock
or remove the shaft end key. Avoid excessive radial and axial bearing loads (note manufactur-
er's documentation). The type of balancing is indicated in the shaft,( see product specific
manuals). In case of protruding, visible part of the shaft end key, establish mechanical bal-
ance.
Make the necessary ventilation and cooling system connections making sure that the ventila-
tion does not get obstructed and that exhaust air either from the current machine or other
machines, is not drawn into the ventilation intake.
The terminals of a machine with frequency converter supply may be energized even when the
machine is at a standstill.
Beware of reverse-power when working at the supply system.
Machines covered by this instruction are not suitable for direct online use (DOL).
3. Electrical connection
When the machine shaft is rotating, a permanent magnet machine induces voltage to the ter-
minals. The induced voltage is proportional to the rotational speed and can be hazardous
even at low speeds. Prevent any rotation of the shaft before opening the terminal box and/or
working at the unprotected terminals.
The terminals of a machine with frequency converter supply may be energized even when the
machine is at a standstill.
Beware of reverse-power when working at the supply system.
Machines covered by this instruction are not suitable for direct online use (DOL).

6
3GZF500725-144 EN 03-2023 | ABB IEC LV MOTORS
Operations must only be carried out by skilled persons while the machine is non-operational.
Before starting work, the following safety rules must be strictly applied:
•De-energize!
•Provide safeguard against reclosing!
•Prevent any rotation of the shaft before opening the terminal box and/or working
at the unprotected terminals.
•Verify safe isolation from supply!
•Connect to earth and short!
• Cover or provide barriers against neighbouring live parts!
•De-energize auxiliary circuits (e.g. anti-condensation heating)!
Rating plate markings and connection diagrams must be followed. Check the compatibility of
the machine and the frequency converter.
The connection must be made so that a permanent safe electrical connection is maintained.
Use appropriate cable terminals. Establish and maintain safe equipotential bonding.
No foreign bodies, dirt or moisture is allowed in the terminal box. Always close unused cable
entrance holes and the box itself in a dust and watertight manner. Lock the key when the ma-
chine is run without coupling. For machines with accessories, check that they function before
commissioning.
The proper installation (e.g. segregation of signal and power lines, screened cables etc.) lies
within the installer's responsibility.
4. Operation
Do not exceed the maximum allowed speed of the machine. See product specific manuals.
Check the vibration level of the machine regularly. In case of deviations from normal opera-
tion - e.g. elevated temperature, noises, vibrations - disconnect the machine. If necessary, es-
tablish cause and consult manufacturer, if necessary.
Do not override protective devices, not even in trial run. In case of heavy dirt deposits, clean
the cooling system at regular intervals.
Make sure that condensation drain plugs are open and clean. Drain plugs, if requested, are
located at the lower part of the end shields to allow condensation to escape from the motor.
Open the drain plug by turning it counter- clockwise. Tap it to check its free operation and
close it by pressing and screwing it clockwise. Drain plugs should be operated in regular in-
tervals (see figure 1).

7
3GZF500725-144 EN 03-2023 | ABB IEC LV MOTORS
5. Maintenance and servicing
Only qualified personnel familiar with the relevant safety requirements are allowed to open
and maintain permanent magnet synchronous machines.
It is not allowed to remove the rotor of a permanent magnet synchronous machine without
the special tools designed for this purpose.
Magnetic stray fields, caused by an open or disassembled permanent magnet synchronous
machine or by a separate rotor of such a machine, may disturb or damage other electrical or
electromagnetic equipment and components, such as cardiac pacemakers, credit cards and
equivalent.
Loose metallic parts and waste must be prevented from entering the interior of the perma-
nent magnet synchronous machine as well as getting into contact with the rotor.
Before closing an opened permanent magnet synchronous machine, all parts which does not
belong to the machine and wastes must be removed from the interior of the machine.
Note!
Beware of magnetic stray fields and possible induced voltages when rotating the separate
rotor of a permanent magnet synchronous machine as they may cause damage to surround-
ing equipment, for example lathes or balancing machines.
Permanent magnet synchronous machines must only be serviced by repair shops qualified
and authorized by ABB. For more information concerning service of permanent magnet syn-
chronous machines, please contact ABB.
Follow manufacturer’s operating instructions. For further details see product specific manu-
als or contact ABB.
Motor has special encoder and bearings system which requires a special care during a
maintenance. Separate service instruction needs to be observed.
Note, that motor interfaces have been sealed with special compound for sealing and corro-
sion protection purposes. This needs to be re-applied during re-assembly process. Please
contact ABB for assembly instructions.
Grease the bearings during commissioning before start-up. Follow the regreasing and oil-
change instructions mentioned in the product specific manuals. If the machine is equipped
with grease automate or oil supply system, make sure the system is working.
6. Handling
Should the motor be used or stored in environments with the risk of sub-zero temperatures,
freezing of the water inside the motor must be prevented. This can be done either by empty-
ing the water jacket or by using anti- freeze additives.
Before emptying the water jacket, protect it with a corrosion-protective emulsion, e.g. Esso
Cutwell 40, Shell Dromus Oil BS, or equivalent, in accordance with the instructions given by
the emulsion manufacturer. If the motor has been standing for a long period of time with no

8
3GZF500725-144 EN 03-2023 | ABB IEC LV MOTORS
water, ensure that water can circulate freely before using the motor again. Remove possible
rust blockages by dissolving them with oxalic acid:
1. Empty the frame of water.
2. Fill the frame with water mixed with oxalic acid (100 g/ liter).
3. Let the acid take effect for approximately 10 minutes.
4. Empty the frame and wash it with pressurized water.
5. Repeat the treatment if necessary.
If the motor is equipped with a separate bearing fan, ensure that there is free ventilation air-
flow. Installation of a motor with a bearing fan in a closed flange construction (i.e. flange-
mounted motor) is not recommended.
Cleaning of motor cooling system helps to restore system efficiency. ABB recommends using
regular flushing and cyclonic or magnetic filters, which should be regularly maintained. Flush-
ing can be done as described above.
Check that water in the system is neutral or near neutral pH after flushing.
7. Lifting
Only the main high strength (360° adjustable in force direction) lifting eyebolts provided with
the motor must be used for lifting the motor. They must not be used to lift the motor when it
is attached to other equipment.
Lifting lugs for auxiliaries (e.g. brakes) or terminal boxes must not be used for lifting the mo-
tor. Because of different output, mounting arrangements and auxiliary equipment, motors
with the same frame may have a different center of gravity.
Damaged lifting lugs must not be used. Check that eyebolts or integrated lifting lugs are un-
damaged before lifting.
Lifting eyebolts must be tightened before lifting. If needed, the position of the eyebolt can be
adjusted using suitable washers as spacers.
Ensure that proper lifting equipment is used and that the sizes of the hooks are suitable for
the lifting lugs.
Care must be taken not to damage auxiliary equipment and cables connected to the motor.
Remove eventual transport jigs fixing the motor to the pallet.
After motor installation protected tapped holes with yellow plugs provided in document
package.
Specific lifting instructions are available from ABB.
During lifting, mounting or maintenance work, all necessary safety considerations shall be in
place and special attention to be taken that nobody will be subject to lifted load.

9
3GZF500725-144 EN 03-2023 | ABB IEC LV MOTORS
8. Water cooling
In motors type M3LK, waste heat is drawn off by water circulating inside the motor housing.
The water circulates around the motor in a jacket inside the housing and flows out through
an outlet.
Motor frame has one water inlet and one outlet with R 1" threads (see figure 2).
Note!
Read the cooling water instruction plate as well as the markings for inlet and outlet pipes on
the motor!
9. Connection
9.1. Requirements for cooling water
Cooling water must be tap water quality. Sea water or water with a proportion of chloride
above 120 mg/l should not be used. The
highest allowed pressure for cooling water is 5 bar, with a recommended maximum input wa-
ter temperature of 45 °C. Steel frame water- cooled construction is only to be used with a
closed fresh-water circulation. The cooling water circulates in ducts integrated in the machine
frame. The material of the frame and ducts is carbon steel according to the standard EN
10025-S235_ or -S355. This material is prone to corrosion in saline and foul water.
The corrosion products and fouling deposits might block the water flow in the ducts. That’s
why it is important to use pure water in the cooling system.
Standard values for the cooling water to be used in the cooling system:
• pH 6.5–9.5
• Alkalinity (CaCO3) > 1 mmol/l
•Chloride (Cl) < 120 mg/l
•Conductivity < 1500 μS/cm
In most cases, normal tap water, i.e. water for domestic consumption, meets all these
requirements.
The cooling water can also be inhibited with an agent protecting the cooling system against
corrosion, fouling, and, when necessary, against freezing. All materials in contact with the
cooling water (pipes, heat exchanger, etc.) must be considered when selecting a suitable in-
hibitor.
Use only suitable and high-class connection parts and seals to connect the machine to the
water circuit.
In environments with risk of sub-zero tempera- tures, a glycol/water mixture can be used
with 40/60 mixture (glycol/water), with a recom- mended minimum environment tempera-
ture of -20 °C.
The lower the cooling water input temperature, the better the cooling of the motor.

10
3GZF500725-144 EN 03-2023 | ABB IEC LV MOTORS
For some cases a higher input temperature can be allowed when requested and checked by
the manufacturer.
The outlet water temperature rise is from 5–10 K.
The minimum pressure and amount of cooling water for the basic construction of a water-
cooled motor is shown in the following table. Please check the requirements for pressure and
the amount of cooling water in the case of special constructions.
If the amount of water varies, its temperature rise will be inversely proportional to the flow
rate.
Frame type
Number of
inlets
Cooling water
flow rate
(l/min)
Water pres-
sure min .
(bar)
Water temp .
rise (K)
Heat transfer of thermal
loss in (approx .) ratio
air/water at room temper-
ature (20°C)
Temperature of inlet cool-
ing water
Water-space of st .
frame (l)
25 °C 40 °C
250 KH_
126 25-10 10/90 30/70 3.8
250 SM_
9.2. Filling or draining cooling water
When filling, open the air vent plug on top of the motor (see figure 2). Let the cooling water
flow into the motor until it comes out of the air gap. Close the air gap with a plug and seal
the joint with sealing tape or strip. Filling must be done carefully so that no air is left in the
motor’s cooling channels. Check for possible leaks after the piping and joints have been con-
nected.
Emptying can be done with pressurized air. After emptying, the plugs must be re-fitted, and
the seals of the joints must be checked.
10. Consendation drain holes
It is of special importance with water cooled motors that the condensation drain holes are lo-
cated in the correct position (fig. 1). Check that the condensation drain holes face down-
wards, especially when the mounting arrangement differs from standard.
11. Water leakage detector
This motor is equipped with float type leakage detector in non-drive end (see figure 2 and 3).
The leakage detector has a magnetic float switch. The magnetic float switch is positioned on
a non-magnetic guide tube. When a specified water level is reached, the magnetic field pro-
duced by the magnet in the float actuates a reed switch (sealed contact) inside the guide
tube.
This closes the electric circuit that transmits the alarm signal to the control board.

11
3GZF500725-144 EN 03-2023 | ABB IEC LV MOTORS
The detector is connected in the lowest part of the motor and vertically installed accord- ing
to the mounting arrangement of the motor. The maximum deviation from the vertical axis
line is ±30°.
Electrical connection of float switch
12. Figures
Figure 1. Condensation drain hole locations. Open and
close position of plugs.
max. voltage max. current 1 A switch capacity
230 V DC/AC 100 VA
Drain hole plugs (condensation)

12
3GZF500725-144 EN 03-2023 | ABB IEC LV MOTORS
Figure 2. Cooling water system.
1…4 Float switch Kubler EVEB-GN1-SVK27A-_NO
(closed contact at alarm)
Figure 3. Sectional view of water leakage detector and
typical connection diagram of float switch.
Bleeding plug (water cooling system)
Water leakage detector (water
cooling system)
Water outlet - EN10556-Rp 1” (water cooling
system)
Water inlet - EN10556-Rp 1”
(water cooling system)

—
Contact us
—
abb .com/motors&generators
© Copyright 2023 ABB. All rights reserved.
Specifications subject to change without notice.
3GZF500725
-
144
EN 03
-
2023
Table of contents
Other ABB Engine manuals
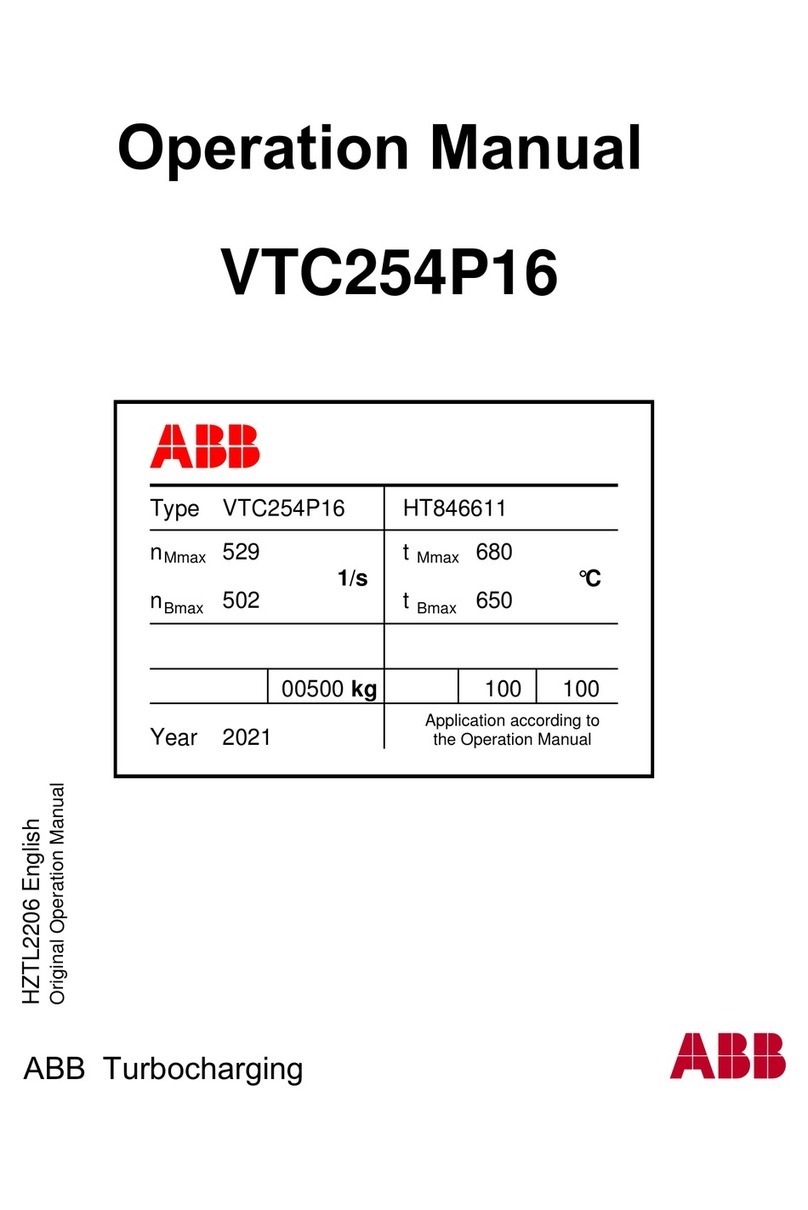
ABB
ABB HT846611 User manual
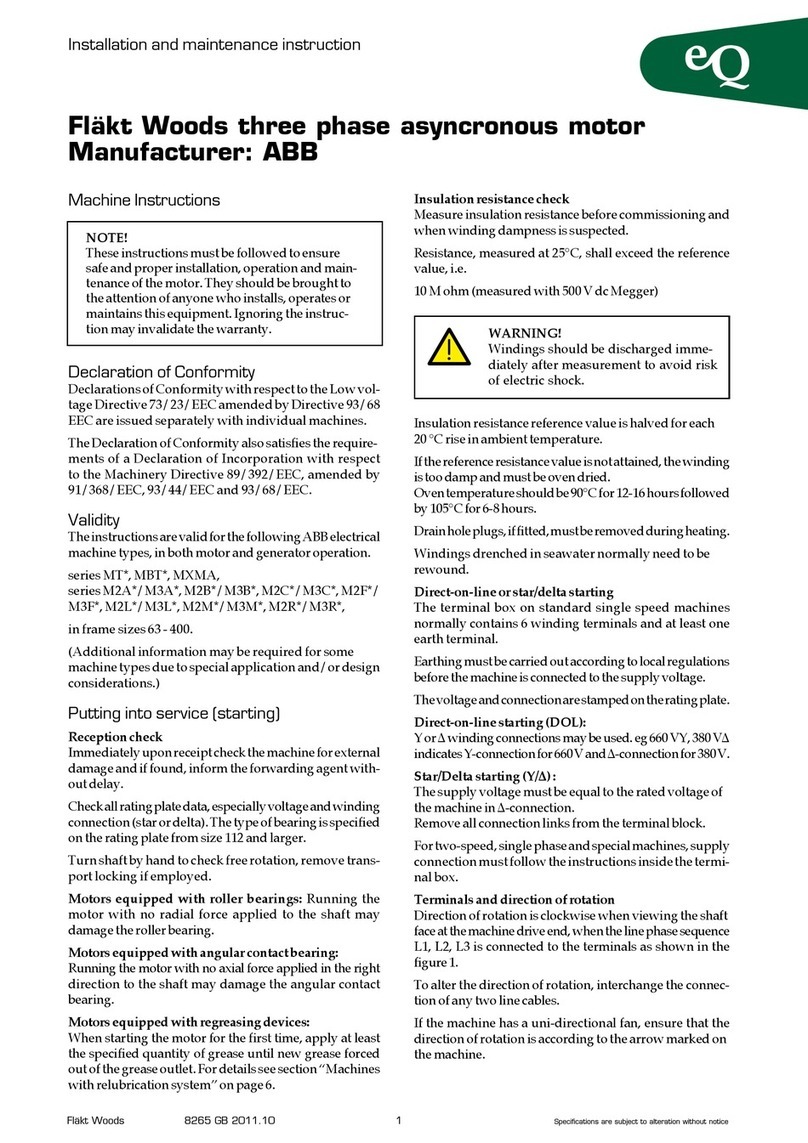
ABB
ABB MT series Technical specifications

ABB
ABB HT576190 User manual

ABB
ABB HT574399 User manual
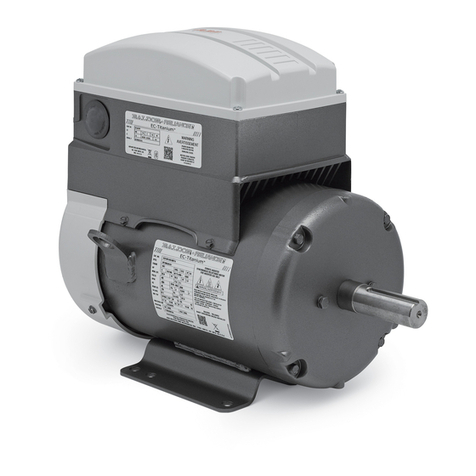
ABB
ABB Baldor-Reliancer EC Titanium User manual

ABB
ABB HT605172 User manual
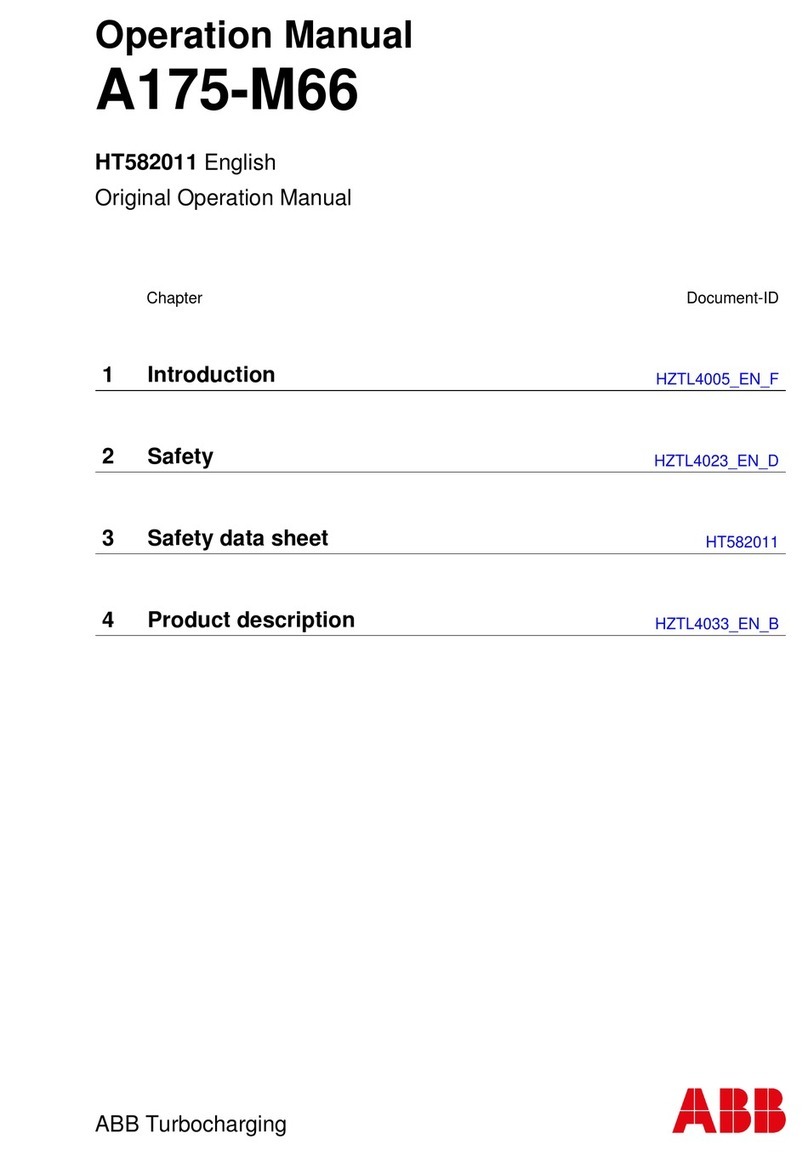
ABB
ABB HT582011 User manual
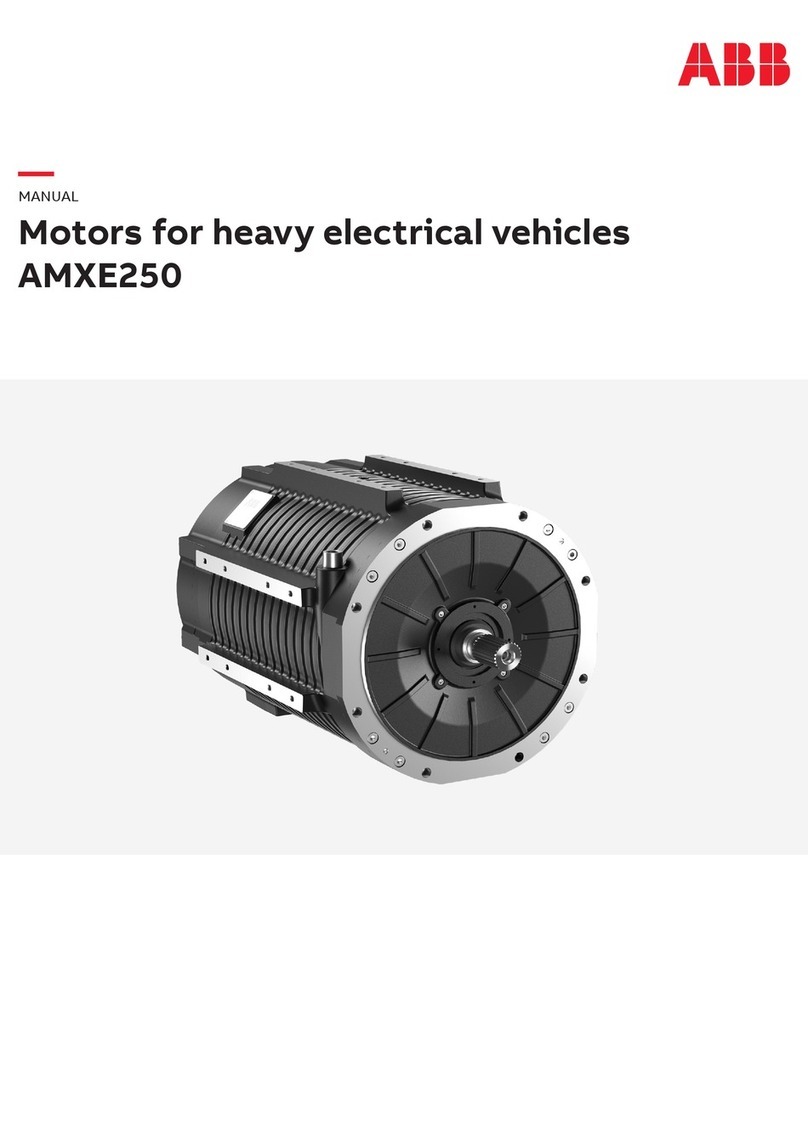
ABB
ABB AMXE250 User manual
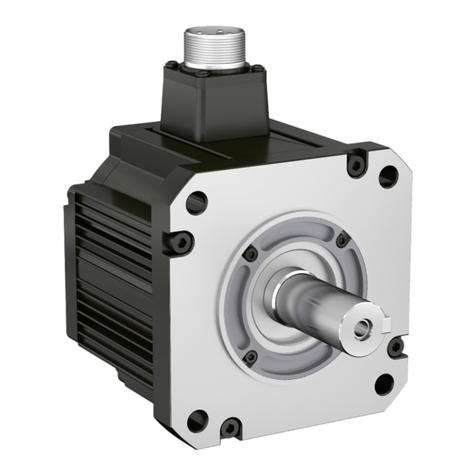
ABB
ABB ESM Series User manual

ABB
ABB HT575729 User manual