ABB CIRCUIT SHIELD 87T User manual

ABB
IB
7.6
.
1.7
-
4
Issue
B
INSTRUCTIONS
Transformer
Differential
Relay
©
CIRCUIT
&
SHIELD
Catalog
Series
219
Standard
Case
TYPE
87
T
Catalog
Series
419
Drawout
Test
Case
TYPE
87
T
PIFFEBENT
]
?
0
8
-
0
Ji
MINIMUM
RtSTBAM
’
%
niFKESfcNTIM
ASEABBOWBOfWj
BFSTRA
'
N
'
;
.
:
s
vo
c
HARMONIC
.
yCl
is
MEBTZ
£
£
,
«
PF
*
/
’
CAT
TWO
WINDING
RELAY
Courtesy of NationalSwitchgear.com

IB
7.6
.
1.7
-
4
Page
2
Transformer
Differential
Relay
TABLE
OF
CONTENTS
Introduction
Precautions
Placing
Relay
into
Service
App
1
ication
Data
Maintenance
and
Testing
.
..
Page
2
Page
2
Page
2
Page
5
Page
14
INTRODUCTION
These
instructions
contain
the
information
required
to
properly
install
,
operate
,
and
test
the
ABB
Circuit
-
Shield
Type
87
T
single
-
phase
Transformer
Differential
Relay
.
These
mounting
.
the
case
and
clearly
numbered
.
relays
are
housed
in
a
case
suitable
for
conventional
semi
-
flush
panel
All
connections
to
the
relay
are
made
at
terminals
located
on
the
rear
of
Relays
with
catalog
numbers
starting
with
419
are
similar
in
function
to
relays
of
the
earlier
219
series
,
but
offer
totally
drawout
construction
with
integral
test
faci
1
ities
.
and
blade
assembly
upon
removal
of
the
relay
from
its
case
,
are
of
partial
drawout
construction
,
with
the
input
transformers
remaining
in
the
case
upon
withdrawal
of
the
lower
electronic
circuit
board
.
Current
transformer
shorting
is
accomplished
by
a
direct
-
acting
spring
Units
of
the
219
series
PRECAUTIONS
The
following
precautions
should
be
taken
when
applying
these
relays
:
1
.
Incorrect
wiring
may
result
in
damage
,
diagram
before
energizing
,
correct
polarity
.
Be
sure
wiring
agrees
with
the
connection
Be
sure
that
the
dc
control
voltage
is
applied
in
the
2
.
Apply
only
the
rated
dc
control
voltage
marked
on
the
front
panel
.
3
.
Do
not
attempt
to
change
a
current
tap
setting
while
the
relay
is
in
service
.
This
wi
11
likely
cause
the
relay
to
trip
due
to
the
mismatch
created
.
(
Pulling
the
tap
pin
does
not
open
the
ct
circuit
.
)
If
a
control
wiring
insulation
test
is
4
.
High
voltage
tests
are
not
recommended
,
required
,
withdraw
the
unit
from
its
case
before
applying
the
test
voltage
.
5
.
Follow
test
instructions
to
verify
that
the
relay
is
in
proper
working
order
.
CAUTION
:
since
troubleshooting
entails
working
with
energized
equipment
,
care
should
be
taken
to
avoid
personal
shock
.
Only
competant
technicians
familiar
with
good
safety
practices
should
service
these
devices
.
PLACING
THE
RELAY
INTO
SERVICE
1
.
RECEIVING
.
HANDLING
.
STORAGE
Upon
receipt
of
the
relay
(
when
not
included
as
part
of
a
switchboard
)
examine
for
shipping
damage
.
If
damage
or
loss
is
evident
,
file
a
claim
at
once
and
promptly
notify
Asea
Brown
Boveri
.
Use
normal
care
in
handling
to
avoid
mechanical
damage
.
Keep
the
relay
clean
and
dry
.
2
.
INSTALLATION
the
outline
dimensions
and
panel
drilling
are
given
in
Figure
1
.
Mounting
:
Courtesy of NationalSwitchgear.com

Transformer
Differential
Relay
IB
7.6
.
1.7
-
4
Page
3
Connections
:
Typical
connection
diagrams
for
two
and
three
Internal
connections
in
Figure
2
.
winding
transformers
are
shown
in
Figures
3
and
4
.
Special
care
should
be
taken
to
connect
the
dc
control
power
in
the
proper
polarity
.
These
relays
have
a
metal
front
panel
which
is
connected
through
printed
circuit
board
runs
to
a
rear
terminal
marked
"
G
"
.
In
all
applications
this
terminal
should
be
wired
to
ground
.
The
87
T
relay
includes
an
external
resistor
which
is
supplied
mounted
to
the
case
and
wired
between
terminals
9
and
operation
.
This
resistor
must
be
connected
for
proper
10
.
Note
:
Connections
are
critical
in
this
application
.
Most
problems
experienced
during
commissioning
are
due
to
incorrect
connections
:
interchanged
phases
,
or
ct
polari
-
ties
,
or
incorrect
make
-
up
of
the
delta
ct
connections
.
Using
the
transformer
nameplate
drawing
as
the
reference
,
a
phasing
-
check
should
be
made
to
be
sure
that
the
ct
secondary
connections
are
made
up
properly
properly
for
the
particular
transformer
winding
configuration
.
In
case
of
difficulty
during
commissioning
,
a
plug
-
in
test
unit
is
available
on
loan
from
the
factory
as
an
aid
in
analyzing
connection
problems
;
however
,
significant
load
current
must
be
flowing
to
use
this
device
.
3
.
SETTINGS
Procedures
for
calculating
settings
for
a
particular
installation
are
given
in
the
Application
section
.
CURRENT
TAPS
:
The
ct
secondary
currents
seen
by
the
relay
are
usually
unequal
due
to
the
primary
to
secondary
ct
’
s
on
the
primary
and
secondary
sides
of
the
transformer
.
ratio
of
the
transformer
being
protected
and
the
choice
of
ratios
for
the
The
tap
settings
are
selected
to
equalize
the
input
currents
seen
by
the
differ
-
ential
measurement
unit
of
the
relay
.
The
tap
values
and
ratios
provided
are
shown
in
Table
1
.
Setting
calculations
will
determine
the
tap
selection
required
for
the
high
-
side
and
low
-
side
ct
inputs
.
It
is
important
to
identify
which
input
terminals
of
the
relay
are
connected
to
the
high
-
side
ct
’
s
and
to
the
low
side
ct
’
s
.
these
Then
when
making
settings
,
to
relate
the
front
panel
tap
to
the
input
current
terminals
it
affects
:
the
left
side
tap
for
input
terminals
1
-
2
,
the
right
side
tap
for
terminals
5
-
6
,
and
the
center
tap
(
on
3
winding
units
)
for
input
terminals
3
-
4
.
%
DIFFERENTIAL
:
The
ABB
Circuit
-
Shield
Type
87
T
relay
operates
when
its
input
currents
differ
in
magnitude
(
vectorial
1
y
)
.
The
operating
point
occurs
when
the
difference
,
expressed
as
a
percentage
of
the
smaller
,
exceeds
the
setting
.
The
percentage
differential
or
"
slope
"
setting
is
made
with
the
left
-
hand
front
panel
dial
.
illustrated
in
the
graphs
of
Figures
6
and
7
.
the
operate
current
relative
to
the
tap
value
,
This
continuously
adjustable
control
allows
settings
from
15
to
40
%
,
and
is
In
these
plots
the
vertical
axis
is
Mo
=
(
Ii
/
T
1
)
-
(
I
2
/
T
2
)
and
the
horizontal
axis
is
the
smaller
restraint
current
relative
to
tap
value
MR
=
I
2
/
T
2
The
Percent
Differential
is
D
=
MO
/
MR
where
i
nto
and
i
nto
11
is
the
1
arger
restraint
current
T
1
the
tap
value
,
12
is
the
smaller
restraint
current
T
2
the
tap
value
.
Note
:
MR
=
R
when
I
2
/
T
2
<
R
where
R
(
adjustable
)
Minimum
Restraint
Courtesy of NationalSwitchgear.com

Transformer
Differential
Relay
IB
7.6
.
1.7
-
4
Page
4
MINIMUM
RESTRAINT
(
Minimum
Operating
Current
)
:
The
minimum
operating
current
is
set
by
the
right
-
hand
dial
on
the
front
panel
,
which
is
continuously
adjustable
.
The
minimum
operating
current
value
is
determined
by
the
following
relationship
between
the
restraint
dial
setting
,
the
percent
differential
setting
,
and
the
current
tap
setting
:
(
D
/
(
100
+
D
)
)
x
R
x
T
Im
D
=
%
differential
setting
R
=
adj
min
restraint
setting
T
=
tap
setting
Im
=
minimum
operating
current
in
amperes
where
For
example
,
with
D
=
25
%
,
R
=
2.3
and
T
=
5
A
:
(
25
/
125
)
x
2.3
x
5
46
%
X
5
A
2.3
A
Im
effect
of
varying
the
Minimum
Restraint
adjustment
is
graphically
illustrated
in
The
Figure
7
and
tabulated
in
this
chart
:
Restraint
Dial
Setting
Minimum
Operate
Current
Percent
Differential
Setting
30
%
of
tap
1
.
05
40
%
1
.
5
43
%
65
%
2.3
21
%
25
%
1
.
05
30
%
1
.
5
45
%
2.3
1
.
05
14
%
15
%
1
.
5
20
%
30
%
2.3
The
setting
that
provides
a
30
-
40
%
minimum
operating
current
would
be
typical
for
most
applications
.
INSTANTANEOUS
:
The
instantaneous
element
operates
directly
on
magnitude
of
the
measured
current
difference
.
This
internal
adjustment
is
factory
set
at
10
x
tap
,
but
may
be
adjusted
from
8
to
20
x
as
may
be
required
by
the
application
.
This
element
must
be
set
by
test
.
Refer
to
the
section
on
Testing
for
the
calibration
procedure
.
HARMONIC
RESTRAINT
:
The
harmonic
restraint
unit
blocks
relay
operation
on
transformer
energization
by
detection
of
the
second
harmonic
content
of
the
inrush
current
.
This
element
is
factory
set
to
restrain
on
15
%
second
harmonic
,
which
is
appropriate
for
most
applications
.
An
internal
calibration
adjustment
provides
a
range
of
approximately
10
-
20
%
,
and
may
be
set
by
test
.
Refer
to
the
section
on
Testing
for
the
calibration
procedure
.
Courtesy of NationalSwitchgear.com

Transformer
Differential
Relay
IB
7.6
.
1.7
-
4
Page
5
APPLICATION
DATA
The
ABB
Circuit
-
Shield
Type
87
T
provides
high
-
speed
differential
protection
for
power
transformers
.
The
Type
87
T
is
a
single
-
phase
relay
.
A
set
of
three
relays
is
required
for
the
pro
-
tection
of
one
power
transformer
.
The
relay
is
offered
in
models
for
the
protection
of
two
winding
and
three
winding
transformers
.
The
relay
has
a
linear
percentage
differential
characteristic
in
order
to
accomodate
ct
ratio
mismatch
,
the
operation
of
on
-
load
tap
changers
,
and
ct
errors
at
high
fault
currents
external
to
the
protected
zone
.
Controls
are
provided
on
the
front
panel
to
adjust
the
slope
(
15
-
40
%
)
,
and
the
minimum
operate
current
.
A
second
-
harmonic
restraint
unit
prevents
relay
operation
on
transformer
magnetizing
inrush
current
.
content
,
but
may
be
adjusted
if
required
.
This
unit
is
factory
calibrated
to
restrain
on
15
%
second
harmonic
An
unrestrained
instantaneous
unit
which
operates
on
the
magnitude
of
the
difference
current
is
provided
to
back
up
the
percentage
differential
unit
.
The
instantaneous
unit
is
factory
set
at
10
x
tap
,
but
may
be
adjusted
(
8
-
20
x
)
in
the
field
.
The
relay
has
ratio
correcting
taps
,
therefore
,
external
auxiliary
ct
’
s
will
not
The
high
continuous
rating
of
each
tap
gives
the
user
more
The
low
burden
of
the
relay
(
see
table
3
)
provides
usually
be
required
,
flexibility
in
selecting
taps
,
improved
ct
performance
.
A
procedure
for
calculating
the
relay
settings
for
a
particular
application
follows
on
page
10
.
MOTE
t
DIMENSIONS
ARE
-
^
5
^
-
MM
8.36
213
6.56
6.66
1.19
175
167
30.2
t
PANEL
r
tt
16
o
4.68
3
124
£
J
2.44
62
L
?
o
FRONT
VIEW
(
4
)
^
|
-
0
IA
HOLES
D
.
O
SIDE
VIEW
*
T
•
n
7
n
•
*
n
4
n
3
n
2
o
>
0
0
[
0
i
3.69
0
00
0
|
PANEL
CUTOUT
94
0
6
T
T
0
0
0
0
000
0
1.64
£
IS
13
ii
Uio
i
«
H
12
“
47
~
iias
.
9
*
52.4
i
DRAMfOUT
TEST
CASE
STUD
NUMBERS
(
BACK
VIEW
)
3.19
81.0
6.62
168
Figure
1
:
Relay
Outline
and
Panel
Drilling
Courtesy of NationalSwitchgear.com

IB
7.6
.
1.7
-
4
Page
6
Transformer
Differential
Relay
Specifications
Input
Circuits
:
Ratio
Matching
Taps
:
Continuous
rating
:
1
Second
rating
:
Burden
:
see
Table
1
.
see
Table
2
.
200
Amperes
,
any
tap
.
see
Table
3
.
Percentage
Restraint
Element
:
Minimum
operate
current
:
adjustable
13
-
65
*
of
tap
setting
.
Slope
:
adjustable
15
-
40
*
.
Refer
to
Figures
6
and
7
.
Instantaneous
Element
:
Internally
adjustable
8
-
20
x
tap
.
Factory
set
at
10
x
tap
.
Harmonic
Restraint
Element
:
Restrain
on
2
nd
harmonic
.
Internally
adjustable
approximately
10
*
-
20
*
.
Factory
setting
-
15
*
.
Operating
Time
:
See
Figure
5
.
Output
Contact
Rating
:
@
125
vdc
@
250
vdc
closing
/
tripping
continuous
break
30
A
30
A
5
A
5
A
0.3
A
0.1
A
Operating
Temperature
Range
:
-
20
to
+
70
°
C
models
available
for
125
vdc
@
0.05
A
max
.
drain
110
vdc
@
0.05
A
max
.
drain
250
vdc
@
0.05
A
max
.
drain
220
vdc
@
0.05
A
max
.
drain
48
vdc
@
0.05
A
max
.
drain
32
vdc
and
24
vdc
:
Control
Voltage
:
(
allowable
range
100
-
140
vdc
)
(
allowable
range
88
-
125
vdc
)
(
allowable
range
200
-
280
vdc
)
(
allowable
range
176
-
250
vdc
)
(
allowable
range
38
-
58
vdc
)
see
note
2
below
,
and
page
22
.
TABLE
4
:
CATALOG
NUMBERS
-
COMMON
.
UNITS
Control
Voltage
Catalog
Numbers
Std
Case
Test
Case
System
Freq
.
Type
Windings
87
T
48
vdc
11
Ovdc
125
vdc
250
vdc
Two
60
Hz
.
219
T
2431
219
T
2401
219
T
2441
219
T
2451
419
T
2431
419
T
2401
419
T
2441
419
T
2451
48
vdc
11
Ovdc
125
vdc
220
vdc
50
Hz
.
219
F
2431
219
F
2401
219
F
2441
219
F
2421
419
F
2431
419
F
2401
419
F
2441
419
F
2421
48
vdc
11
Ovdc
125
vdc
87
T
Three
60
Hz
.
219
T
3431
219
T
3401
219
T
3441
419
T
3431
419
T
3401
419
T
3441
50
Hz
.
48
vdc
11
Ovdc
125
vdc
219
F
3431
219
F
3401
219
F
3441
419
F
3431
419
F
3401
419
F
3441
Select
419
series
units
for
new
applications
due
to
the
the
improved
testing
features
.
Notes
:
1
.
2
.
Contact
factory
for
availability
of
units
for
control
voltage
ratings
not
listed
.
Type
96
dc
/
dc
inverter
and
48
vdc
rated
87
T
:
see
page
22
.
For
24
or
32
vdc
control
use
Courtesy of NationalSwitchgear.com

Transformer
Differential
Relay
IB
7.6
.
1.7
-
4
Page
7
Type
87
T
Tap
Ratios
TABLE
1
3.2
4.0
2.9
3.6
4.5
5.0
8.7
2.9
1.00
1.10
1.24
1.38
1
.
72
3.00
1
.
55
3.2
1
.
00
1
.
25
1.13
1
.
41
1.56
2.72
3.6
1
.
00
1.11
1.39
2.42
1
.
25
4.0
1.00
1.13 1.25
2.18
4.5
1.00
1.11
1.93
5.0
1
.
00
1.74
8.7
1.00
Continuous
Current
Ratings
TABLE
2
TABLE
3
Burden
Data
Tap
Setting
Continuous
Rating
Tap
Setting
Ohms
P
.
F
.
2.9
A
3.2
A
3.6
A
4.0
A
4.5
A
5.0
A
8.7
A
1
0
A
2.9
A
3.2
A
3.6
A
4.0
A
4.5
A
5.0
A
8.7
A
0.05
0.05
0.04
0.04
0.04
0.04
0.04
1.0
10
A
1.0
10
A
1.0
1
OA
1
.
0
1
OA
1.0
1
OA
1
.
0
17
A
1.0
Figure
2
:
Internal
Connection
Diagrams
16
D
419
B
Transformer
Differential
Relay
Drawout
Test
Case
Type
87
T
Type
87
T
Transformer
Differential
Relay
Standard
Case
16
D
219
B
++
1
06
O
5
o
3
02
ol
fccJ
fee
?
1
5
a
I
T
T
T
T
G
JT
°
G
r
°
ii
i
i
$
1
E
$
15
OlH
Oja
$
12
$
11
10
?
q
ID
9
*
Notes
:
1
.
Omit
coil
3
-
4
for
two
winding
relays
.
2
.
The
tap
block
associated
with
coil
1
-
2
is
on
left
hand
side
,
when
viewed
from
the
front
of
the
relay
.
3
.
The
tap
block
for
coil
5
-
6
is
on
the
right
hand
side
.
4
.
If
provided
,
the
tap
block
for
coil
3
-
4
is
in
the
center
.
5
.
The
external
resistor
shown
connected
between
terminals
9
and
10
is
supplied
mounted
on
the
relay
and
must
be
in
place
for
proper
operation
.
6
.
The
diode
shown
between
terminals
15
and
16
is
used
for
testing
only
.
See
test
procedures
.
Courtesy of NationalSwitchgear.com

Transformer
Differential
Relay
IB
7.6
.
1.7
-
4
Page
8
Connections
shown
for
Phase
Rotation
a
-
b
-
c
Connections
shown
for
Phase
Rotation
a
-
b
-
c
Delta
-
Wye
Transformer
Delta
-
Delta
Transformer
b
a
c
b
a
c
52
-
1
52
-
1
H
2
r
;
;
ii
m
r
?
n
rt
-
A
„
,
Hi
DLJL
|
»
y
LhJL
nnr
!
£
2
2
2
2
2
JT
|
<
i
6
6
6
6
6
6
6
-
C
£
J
fsjt
:
!
<
5
!
£
!
"
5
j
®
I
|
oo
L
.
_
J
®
L
)
i
*
1
CM
CO
*
3
£
I
?
5
£
?
5
£
co
|
_
J
co
I
J
oo
L
_
t
5
J
52
-
2
52
-
2
*
+
<
>
87
T
-
3
1
*
87
T
-
2
"
S
4
=
rM
87
T
-
1
8
7
8
7
12
11
10
9
\
6
ovo
12
11
10
9
h
6
o
^
o
12
11
10
9
<
Hki
ovo
D
.
C
.
Control
Power
ft
5
f
r
~
r
.
86
86
X
X
52
-
2
86
52
-
1
a
a
^
86
52
-
1
52
-
2
TC
TC
+
Typical
Connections
for
Differential
Protection
Two
-
Winding
Three
-
Phase
Power
Transformer
Figure
3
:
Note
:
using
the
transformer
nameplate
drawing
as
a
reference
,
a
"
phasing
-
check
"
should
be
made
to
insure
that
the
ct
secondary
connections
are
made
up
properly
for
the
particular
transformer
winding
configuration
.
Courtesy of NationalSwitchgear.com

I
2
3
2
3
H
3
52
-
1
52
-
3
93
!
92
94
3
I
92
94
96
'
6
2
94
961
o
>
Irirta
CSJ
IO
,
I
I
I
I
o
K
H
I
H
I
N
-
I
3
K
I
CO
1
±
N
3
!
00
®
I
I
®
I
3
45
*
1
9.5
J
3
&
3
o
“
b
~
b
Y
2
®
"
5
(
D
YI
3
r
+
Y
3
93
n
_
p
..
p
ZO
®
0
)
v
:
52
-
2
XI
X
3
+
4
C
IW
=
1
'
87
T
-
2
87
T
-
3
87
T
-
1
[
M
H
8
7
12
1110
9
o
4
W
ovo
12
11
10
9
0
-
4
KJ
OVO
12
11
10
9
y
6
o
+
*
o
D
.
C
.
ff
Sr
r
Control
Power
“
X
xlx
“
i
52
-
3
86
52
-
1
aa
a
^
86
52
-
1
52
-
3
52
-
2
M
2
3
TC
TC
TC
CO
-
J
O
)
“
O
*
0
)
CD
•
®
-
J
Figure
4
:
Typical
Connections
for
Differential
Protection
-
Three
-
Winding
Three
-
Phase
Transformer
to
Courtesy of NationalSwitchgear.com

Transformer
Differential
Relay
IB
7.6
.
1.7
-
4
Page
10
CALCULATION
OF
SETTINGS
:
A
procedure
for
calculating
the
relay
settings
follows
,
end
of
the
procedure
.
An
example
is
given
at
the
1
.
Determine
the
maximum
load
currents
of
the
transformer
,
on
the
high
-
side
IH
and
the
1
ow
-
side
II
.
2
.
Determine
the
maximum
through
-
fault
currents
,
IHF
and
ILF
.
3
.
Choose
the
ct
ratio
in
accordance
with
step
1
to
give
approximately
5
A
secondary
current
at
the
maximum
load
current
;
and
,
also
so
that
the
maximum
external
fault
current
is
less
than
100
amperes
secondary
.
others
,
check
that
they
meet
the
requirements
above
.
applications
,
through
-
fault
current
is
limited
by
the
transformer
impedance
.
)
If
the
ct
ratios
have
been
specified
by
(
Note
that
for
2
winding
4
.
Calculate
the
load
currents
on
the
ct
secondary
side
,
IHS
and
ILS
.
remembering
to
multiply
by
for
ct
5
.
Calculate
the
relay
currents
,
IHR
and
ILR
secondaries
connected
in
delta
.
6
.
Calculate
the
ratio
of
the
relay
currents
taking
the
1
arger
/
smal
1
er
A
.
7
.
Referring
to
Table
1
,
choose
the
taps
so
that
the
tap
ratio
(
T
)
is
closest
to
the
relay
current
ratio
(
A
)
.
Properly
assign
the
larger
and
smaller
value
tap
selections
to
the
high
-
side
and
low
-
side
relay
currents
culated
in
step
7
.
in
the
same
manner
as
(
A
)
was
cal
-
if
more
than
one
selection
of
taps
is
available
for
the
tap
ratio
desired
usual
practice
to
choose
tap
values
closest
to
the
normal
relay
currents
IHR
and
ILR
.
I
t
i
s
8
.
Check
that
the
relay
currents
are
within
the
continuous
rating
of
the
relay
refer
to
Table
2
.
|
(
T
-
A
)
/
(
sma
11
er
of
T
or
A
)
|
10
.
Select
the
slope
(
percentage
differential
)
setting
.
Both
the
mismatch
and
transformer
’
s
load
tap
changer
range
must
be
considered
.
S
=
M
+
LTC
.
security
,
the
25
%
setting
should
be
used
for
calculated
slopes
of
15
%
and
below
,
the
40
%
setting
for
calculated
slopes
of
15
-
30
%
.
M
=
Mismatch
9
.
Calculate
the
mismatch
:
the
For
and
11
.
Select
the
Instantaneous
setting
.
This
internal
adjustment
is
factory
set
at
10
x
tap
value
.
The
recommended
setting
is
approximately
10
times
the
power
transformers
self
-
cooled
load
current
rating
:
(
a
)
Calculate
the
relay
current
at
the
transformers
self
-
cooled
rating
.
(
b
)
Divide
by
the
high
-
side
relay
tap
value
.
(
c
)
Multiply
by
1.2
for
margin
.
Set
the
internal
potentiometer
R
119
using
the
calibration
procedures
given
in
the
section
on
Testing
.
The
maximum
burden
presented
to
a
ct
is
given
by
the
12
.
CT
performance
check
:
following
equations
:
2.3
RL
+
RB
+
RA
for
wye
-
connected
ct
’
s
.
3.4
RL
+
3
RB
+
3
RA
for
delta
-
connected
ct
’
s
.
(
this
includes
a
correction
factor
for
the
increased
resistance
of
the
leads
due
to
self
-
heating
effects
)
R
R
RL
is
the
one
-
way
lead
resistance
from
ct
to
the
relay
.
RB
is
the
relay
burden
.
RA
is
the
burden
of
other
devices
in
series
with
the
relay
.
where
(
See
Table
3
)
CT
performance
should
be
satisfactory
if
the
maximum
external
fault
current
flowing
through
R
does
not
require
a
voltage
higher
than
one
-
half
the
ANSI
Class
C
accuracy
rating
of
the
ct
.
Therefore
Vc
>
2
x
RIFS
must
be
satisfied
for
both
the
high
-
side
and
low
-
side
ct
’
s
.
(
Note
:
if
a
multi
-
ratio
ct
is
being
used
,
and
if
the
full
secondary
winding
is
not
being
used
,
then
adjust
the
"
C
"
rating
by
the
factor
NS
/
NT
to
account
for
the
lower
effective
"
C
“
rating
.
(
Ns
=
secondary
turns
used
;
NT
-
total
secondary
turns
.
)
13
.
Minimum
operating
current
:
a
setting
giving
25
-
40
%
minimum
operating
current
would
be
usual
practice
.
See
chart
on
page
4
.
Courtesy of NationalSwitchgear.com

Transformer
Differential
Relay
IB
7.6
.
1.7
-
4
Page
11
Example
:
SETTINGS
CALCULATION
The
following
transformer
is
assumed
for
this
example
:
12
/
16
/
20
MVA
OA
/
FA
/
FA
,
115
kv
delta
,
13.8
kv
wye
,
8.5
%
impedance
,
on
-
load
tap
changer
range
+
/
-
10
%
.
Low
.
..
S
.
ide
13.8
kv
wye
)
Hl
9
b
„
SJ
.
de
_
X
1
L
§
_
Jsy
_
jdeltal
1
.
Maximum
load
current
(
at
20
MVA
)
:
IH
=
20000
/
(
115
*
/
3
)
=
100.4
A
II
=
20000
/
(
13.8
*
y
/
3
)
837
A
2
.
Maximum
through
fault
currents
(
assuming
infinite
bus
)
:
IH
F
12000
/
(
13.8
*
V
3
*
0.085
)
5907
A
12000
/
(
115
*
^
3
*
0.085
)
709
A
ILF
3
.
Choose
ct
ratios
:
=
100
:
5
multiratio
1200
:
5
set
on
1000
:
5
tap
.
CT
secondary
currents
at
maximum
through
fault
:
IH
F
s
(
5907
/
1000
)
*
5
=
29.5
A
(
ok
)
(
709
/
100
)
*
5
=
35.5
A
(
ok
)
ILFS
4
.
Load
currents
on
ct
secondary
side
at
maximum
transformer
rating
(
20
MVA
)
:
IH
S
(
837
/
1000
)
*
5
=
4.19
A
(
100.4
/
100
)
*
5
II
s
5.0
2
A
5
.
Relay
currents
at
maximum
load
current
:
High
-
side
ct
secondaries
in
wye
IH
P
Low
side
ct
secondaries
in
delta
II
R
4.19
*
s
/
3
7.26
A
5.02
A
6
.
Ratio
of
relay
currents
:
1
arger
/
sma
11
er
=
7.26
/
5.02
low
side
/
high
side
1
.
446
A
7
.
Select
taps
from
Table
1
:
Closest
ratio
is
1.41
using
taps
4.5
/
3.2
.
Assign
taps
in
proper
relationship
as
calculated
in
step
6
:
Larger
value
for
low
side
ct
’
s
=
4.5
A
tap
.
Smaller
value
for
high
side
ct
’
s
-
3.2
A
tap
.
(
see
notes
on
Figure
2
page
7
for
physical
relationship
of
of
tap
settings
to
input
terminals
)
8
.
Check
continuous
ratings
of
taps
from
Table
2
:
Both
taps
selected
are
rated
10
A
continuous
-
ok
.
9
.
Calculate
the
mismatch
:
1
(
1.41
-
1
.
446
)
|
/
1.41
|
(
T
—
A
)
|
/
(
smaller
of
T
or
A
)
0.036
/
1.41
M
0.025
2.5
%
.
10
.
Select
percentage
differential
setting
(
slope
)
:
S
=
M
+
LTC
=
2.5
+
10
=
12.5
%
.
Use
25
%
setting
.
11
.
Select
the
instantaneous
setting
:
High
-
side
relay
current
at
self
-
cooled
rating
(
12000
/
(
115
*
y
/
3
)
*
5
/
100
=
3.01
A
30.1
/
3.2
9.4
(
x
tap
)
11.3
(
x
tap
)
.
(
3.01
*
10
)
/
(
high
side
tap
)
Multiply
by
1.2
for
margin
=
9.4
*
1.2
Calibrate
relay
to
give
instantaneous
setting
11
x
tap
.
12
.
CT
performance
check
:
Determine
the
approximate
lead
lengths
and
wire
size
used
for
the
ct
secondary
connections
.
Determine
the
one
way
lead
resistance
,
and
the
burden
of
any
other
devices
connected
.
For
this
example
we
assume
the
high
-
side
ct
’
s
(
100
:
5
)
are
ANSI
class
C
200
and
the
low
-
side
ct
’
s
(
1200
:
5
multiratio
)
are
C
400
.
ILFS
29.5
A
IH
F
s
35.5
A
Effective
C
rating
of
low
side
ct
=
400
*
1000
/
1200
=
333
Maximum
allowable
burdens
are
:
RH
S
(
333
v
/
2
)
/
29.5
A
(
200
v
/
2
)
/
35.5
A
5.64
ohms
2.82
ohms
RL
S
(
example
continues
on
next
page
)
Courtesy of NationalSwitchgear.com

Transformer
Differential
Relay
IB
7.6
.
1.7
-
4
Page
12
12
.
CT
performance
check
(
continued
)
:
Assuming
only
the
relay
is
connected
to
the
ct
’
s
:
High
side
ct
’
s
in
wye
2.82
ohms
Low
side
ct
’
s
in
delta
5.64
ohms
2.3
RL
H
+
RB
3.4
RL
L
+
3
RB
Relay
Burdens
from
Table
3
:
RBH
0.04
ohms
(
4.5
A
tap
)
0.05
ohms
(
3.2
A
tap
)
Calculate
maximum
allowed
one
-
way
lead
resistance
:
RL
H
RB
L
(
2.82
(
5.64
-
3
*
0.04
)
/
3.4
1.62
ohms
max
.
0.05
)
/
2.3
1.20
ohms
max
.
R L
L
13
.
Select
minimum
operating
current
setting
:
For
a
minimum
operating
current
of
25
%
relative
to
full
load
current
:
IH
S
High
side
tap
=
(
25
%
x
5.02
J
/
3.2
5.02
A
(
from
step
4
)
3.2
A
(
from
step
7
)
=
39
%
of
tap
.
(
D
/
(
100
+
D
)
)
x
R
X
T
From
page
4
:
Im
WT
.
39
.
39
*
(
100
+
D
)
/
D
.
39
*
(
125
/
25
)
=
D
=
25
%
from
step
10
1.95
(
Minimum
Restraint
setting
)
R
R
Ca
1
culations
for
Three
-
Winding
Transformers
:
Tap
selections
are
calculated
two
at
a
time
,
based
on
the
primary
rating
of
the
transformer
-
and
not
on
the
ratings
of
the
individual
secondary
windings
.
For
the
following
example
assume
transformer
ratings
:
Tertiary
12.4
kv
,
7.5
/
10
Mva
de
1
ta
Secondary
69
kv
,
30
/
40
Mva
wye
Primary
161
kv
,
30
/
40
Mva
OA
/
FA
wye
1200
:
5
C
200
ct
’
s
:
(
all
are
multiratio
)
ct
connections
:
600
:
5
C
200
1200
:
5
C
800
de
1
ta
de
1
ta
wye
primary
to
tertiary
-
16
%
primary
to
secondary
-
9.5
%
impedances
:
(
based
on
OA
rating
)
Tertiary
Primary
Secondary
S
amp
1
e
.
c
a
.
1
c
u
J
.
a
t
i
o
.
n
:
465
A
(
@
1
OMva
)
(
1862
A
@
40
Mva
)
2
.
Max
through
fault
currents
(
assuming
only
source
is
infinite
bus
on
primary
side
)
11640
A
335
A
(
@
40
Mva
)
143
A
(
@
40
Mva
)
1
.
Max
load
currents
3523
A
1
509
A
1000
:
5
600
:
5
3
.
Choose
ct
ratios
400
:
5
2.32
A
(
9.31
A
@
40
Mva
)
2.79
A
1
.
79
A
4
.
CT
secondary
currents
at
maximum
load
2.32
A
(
9.31
A
@
40
Mva
)
4.83
A
3.10
A
5
.
Relay
currents
at
maximum
load
6
.
Ratio
of
relay
currents
(
Note
:
for
this
calculation
,
the
same
transformer
rating
must
-
be
used
for
all
windings
;
in
this
case
the
40
Mva
rating
.
)
1
arger
/
smal
1
er
=
secondary
/
primary
=
4.83
/
3.10
1.558
.
Ai
2
9.31
/
3.10
tertiary
/
primary
3.003
.
1
arger
/
smal
1
er
Ai
3
tertiary
/
secondary
=
9.31
/
4.83
1.928
.
1
arger
/
smaller
A
2
3
(
Example
continued
on
page
23
)
Courtesy of NationalSwitchgear.com

Transformer
Differential
Relay
IB
7.6
.
1.7
-
4
Page
13
.
6
CL
<
.
5
H
-
X
z
.
4
LU
tr
CL
3
O
.
3
Hi
<
GC
LU
a
.
.
2
O
.
1
00
SMALLER
RESTRAINT
CURRENT
IN
MULTIPLES
OF
TAP
SETTING
Figure
5
:
Typical
Operating
Time
0
.
<
X
H
z
LU
DC
GC
3
O
<
cr
LU
CL
O
SMALLER
RESTRAINT
CURRENT
IN
MULTIPLES
OF
TAP
SETTING
o
.
<
X
z
Ui
cr
cr
3
O
LU
2
Ui
0
.
O
SMALLER
RESTRAINT
CURRENT
IN
MULTIPLES
OF
TAP
SETTING
Figure
6
:
Percentage
Differential
Operating
Characteristic
Figure
7
:
Percentage
Differential
Characteristics
at
Low
Currents
for
15
%
,
25
%
,
and
40
%
Settings
showing
minimum
operate
current
as
a
function
of
R
.
(
see
Figure
7
for
detail
at
low
restraint
currents
)
Minimum
Restraint
Dial
(
R
)
adjustable
from
1.0
to
2.3
.
Courtesy of NationalSwitchgear.com

Transformer
Differential
Relay
IB
7.6
.
1.7
-
4
Page
14
TESTING
1
.
MAINTENANCE
AND
RENEWAL
PARTS
No
routine
maintenance
is
required
on
these
ABB
Circuit
-
Shield
solid
-
state
relays
.
Follow
test
instructions
to
verify
periodically
that
the
relay
is
in
proper
working
order
.
We
recommend
that
an
inoperative
relay
be
returned
to
the
factory
for
repair
;
however
,
a
schematic
diagram
is
available
on
request
.
Renewal
parts
will
be
quoted
on
request
to
the
factory
.
219
Series
Units
:
Drawout
circuit
boards
of
the
same
catalog
number
are
interchangible
.
identified
by
the
catalog
number
stamped
on
the
front
panel
and
by
a
serial
number
stamped
on
the
bottom
side
of
the
drawout
circuit
board
.
The
board
is
removed
using
the
metal
pull
knobs
on
the
front
panel
.
Removing
the
board
does
not
open
-
circuit
the
ct
secondaries
;
however
,
a
nuisance
operation
is
possible
if
removed
or
inserted
while
in
service
.
A
unit
is
An
18
point
extender
board
,
catalog
200
X
0018
is
available
for
use
in
calibrating
or
troubleshooting
.
419
Series
Units
:
Metal
handles
provide
leverage
to
withdraw
the
relay
assembly
from
the
case
.
The
assembly
is
identified
by
a
catalog
number
stamped
on
the
front
panel
of
the
relay
and
a
serial
number
stamped
on
the
bottom
of
the
circuit
board
.
Test
connections
are
readily
made
to
the
drawout
relay
unit
by
means
of
standard
banana
plugs
.
Current
connections
are
made
to
the
vertical
posts
at
the
blade
assemblies
.
Control
power
and
output
connections
are
made
at
the
rear
vertical
circuit
board
.
This
rear
board
is
marked
for
easier
identification
of
the
connection
points
.
temporari
1
y
The
value
1400
ohms
for
A
25
watt
resistor
is
suitable
for
IMPORTANT
:
in
order
to
test
the
drawout
unit
a
suitable
resistor
must
be
connected
between
terminals
9
and
10
on
the
rear
vertical
circuit
board
,
of
this
resistor
depends
on
the
control
voltage
rating
of
the
relay
:
units
rated
125
vdc
,
200
ohms
for
48
vdc
units
,
testing
.
If
no
resistor
is
readily
available
,
the
resistor
mounted
on
the
rear
of
the
relay
case
could
be
removed
and
used
;
however
,
be
sure
to
remount
the
resistor
on
the
case
at
the
conclusion
of
testing
.
Should
separation
of
the
upper
and
lower
circuit
boards
be
necessary
,
remove
the
(
2
)
screws
holding
the
handle
assemblies
in
place
.
Some
units
may
also
the
removal
of
(
2
)
screws
from
the
underside
of
the
unit
near
the
rear
The
lower
circuit
board
may
then
be
withdrawn
forward
from
the
printed
circuit
connector
.
An
18
point
extender
board
,
catalog
200
X
0018
is
available
to
provide
access
to
the
lower
circuit
board
for
calibration
or
trouble
-
shooting
.
Pisassembly
:
require
vertical
circuit
board
.
Test
Plug
:
test
units
,
a
1
1
Instruction
Book
IB
7.7
.
1.7
-
8
for
details
on
the
use
of
this
device
.
plug
assembly
,
catalog
400
X
0001
is
available
for
use
with
the
419
series
This
device
plugs
into
the
relay
case
on
the
switchboard
and
allows
access
to
the
external
circuits
wired
to
the
case
including
the
ct
secondaries
.
See
A
2
.
HIGH
POTENTIAL
TESTS
High
potential
tests
are
not
recommended
.
A
hi
-
pot
test
was
performed
at
the
factory
before
shipping
.
If
a
control
wiring
insulation
test
is
required
,
withdraw
the
drawout
element
from
the
case
before
applying
the
test
voltage
.
Courtesy of NationalSwitchgear.com

Transformer
Differential
Relay
IB
7.6
.
1.7
-
4
Page
15
3
.
BUILT
-
IN
TEST
FUNCTION
A
built
-
in
test
function
is
provided
for
convenience
in
running
a
test
on
the
relay
and
associated
trip
circuits
.
The
test
button
is
labelled
TRIP
,
and
depressing
the
button
will
cause
an
immediate
trip
.
tests
should
be
made
with
the
main
circuit
de
-
energized
.
If
tests
must
be
CAUTION
:
made
on
an
energized
circuit
,
take
all
necessary
precautions
.
4
.
ACCEPTANCE
TESTS
and
adjust
the
operating
characteris
-
The
following
procedures
can
be
used
to
verify
tics
of
the
Type
87
T
relay
.
A
.
Minimum
Operating
Current
and
%
Differential
Tests
:
Connect
the
relay
in
the
test
circuit
shown
in
Figure
8
.
Apply
control
voltage
per
the
relay
’
s
rating
as
marked
on
the
front
panel
.
Select
and
make
settings
from
the
listing
in
Table
5
.
Minimum
Operating
Current
:
Increase
the
I
2
current
until
the
87
T
operates
.
(
11
=
0
)
Compare
with
the
expected
value
from
Table
5
.
Pifferential
Characteristic
:
Set
the
I
2
current
for
5.8
amps
.
Increase
the
I
1
current
to
5.8
amps
.
The
87
T
output
contact
should
now
be
open
.
Reset
the
target
to
black
.
Increase
the
I
1
current
until
the
87
T
operates
.
The
I
1
current
should
be
within
the
limits
shown
.
Remember
:
since
the
%
Differential
and
Minimum
Restraint
dials
are
continuously
adjustable
,
you
may
trim
their
positions
if
desired
to
obtain
more
precisely
the
required
operating
values
.
Important
note
:
Some
commercial
test
sets
that
have
2
independent
sources
are
not
suitable
for
the
differential
test
shown
above
because
there
is
a
phase
-
shift
between
the
sources
.
If
you
are
using
such
a
set
,
then
an
alternative
test
for
the
differential
element
using
a
single
source
is
as
follows
:
a
.
Connect
the
relay
as
shown
in
Figure
9
.
b
.
Set
%
Diff
dial
to
40
%
,
taps
to
3.6
A
.
c
.
Apply
7.2
A
test
current
.
The
relay
should
not
trip
.
d
.
Move
one
tap
pin
to
2.9
A
position
.
Apply
7.2
A
and
then
rotate
the
%
Diff
dial
counterclockwise
slowly
until
the
relay
trips
.
The
dial
position
should
be
21
-
27
%
.
Suggested
Settings
for
the
Acceptance
Test
Table
5
:
(
D
)
(
R
)
Min
Restraint
Min
Operate
Lim
Differential
Test
Set
I
2
I
1
limits
I
2
%
Diff
Taps
2.9
A
2.9
A
2.9
A
15
%
2.3
0.75
0.75
0.75
1.0
A
1
.
0
A
1.0
A
5.8
A
5.8
A
5.8
A
6.4
6.9
A
7.5
A
8.4
A
25
%
1
.
5
7.0
40
%
1
.
0
7.8
The
suggested
settings
selected
for
Table
5
use
the
lowest
tap
value
(
2.9
A
)
to
minimize
the
currents
required
for
the
tests
.
If
you
must
check
the
values
to
be
used
in
your
application
,
the
following
formulas
apply
:
1
.
Minimum
operating
current
:
Im
D
=
%
Diff
setting
,
R
=
Minimum
Restraint
Setting
Increase
the
test
current
to
one
input
of
the
relay
.
The
relay
should
trip
within
+
/
-
15
%
of
the
value
calculated
.
(
Trim
dial
position
as
rqd
.
)
(
D
/
(
100
+
D
)
x
R
x
T
tap
value
T
2
.
Differential
characteristic
:
apply
test
currents
of
2
times
the
tap
value
to
each
of
two
current
inputs
.
The
output
contact
should
be
open
.
Increase
one
source
until
the
output
contact
closes
.
The
current
at
which
the
contact
closes
should
be
within
+
/
-
5
%
of
the
value
calculated
from
:
1
=
T
x
(
2
D
+
2
)
T
=
tap
of
"
increased
D
=
%
Diff
setting
.
source
Courtesy of NationalSwitchgear.com

Transformer
Differential
Relay
IB
7.6
.
1.7
-
4
Page
16
B
_
.
Instantaneous
Unit
Tests
:
in
the
testing
and
calibration
of
the
instantaneous
unit
,
high
currents
are
Apply
test
current
for
only
a
short
time
in
order
to
avoid
thermal
damage
.
shut
off
the
current
source
and
review
Selection
lowest
tap
value
(
2.9
A
)
for
the
initial
testing
will
reduce
the
test
current
CAUTION
:
required
.
If
the
expected
operation
is
not
obtained
,
your
connections
and
procedures
.
Wait
30
seconds
before
repeating
a
test
,
of
the
required
.
Typical
test
connections
are
shown
in
Figure
10
.
If
you
are
using
an
electronic
current
source
test
set
it
may
be
necessary
to
place
two
of
the
independent
sources
in
parallel
in
order
to
obtain
the
necessary
current
level
.
Be
sure
that
both
sources
are
set
for
the
same
phase
angle
and
connected
with
the
same
polarity
so
the
currents
add
together
at
the
relay
input
terminals
.
(
Alternate
method
:
for
test
sets
with
limited
capacity
,
the
required
test
current
will
be
reduced
to
one
-
half
of
normal
by
connecting
two
relay
input
windings
in
series
:
test
current
into
terminal
1
,
out
2
,
into
5
,
and
out
terminal
6
.
)
To
verify
the
factory
tting
of
10
x
tap
,
it
is
not
necessary
to
separate
the
upper
and
lower
circuit
boards
;
however
,
if
you
plan
to
recalibrate
the
relay
,
the
adjust
-
ment
potentiometer
R
119
is
located
on
the
lower
circuit
board
as
shown
in
the
circuit
board
layout
on
page
19
.
Use
of
the
18
point
extender
board
will
allow
easier
access
to
this
adjustment
.
-
a
Locate
the
connector
pins
labelled
1
through
5
on
the
module
board
-
see
circuit
board
layouts
on
page
19
.
To
defeat
the
operation
of
the
main
differential
unit
,
a
jumper
must
be
connected
temporarily
between
pins
3
and
5
.
(
Take
care
to
prevent
shorting
to
any
of
the
other
pins
.
)
Only
the
instantaneous
unit
will
remain
active
.
Apply
rated
dc
control
voltage
to
the
relay
.
The
relay
is
If
the
2.9
A
Increase
the
test
current
until
the
relay
operates
and
note
the
value
,
factory
calibrated
for
an
operating
point
of
10
x
tap
(
tolerance
+
/
-
15
%
)
.
tap
is
being
used
,
a
trip
should
be
obtained
at
25
-
33
A
.
and
repeat
the
test
until
the
desired
operating
point
is
obtained
.
If
necessary
,
readjust
R
119
At
the
completion
of
this
test
,
remove
the
temporary
jumper
.
C
.
Harmonic
Restraint
Tests
:
The
Type
87
T
uses
2
nd
harmonic
restraint
to
block
relay
operation
on
transformer
inrush
upon
energization
.
The
factory
calibration
is
restraint
for
2
nd
harmonic
content
of
15
%
and
above
.
and
it
is
not
necessary
to
separate
the
upper
boards
;
however
,
if
you
plan
to
recalibrate
the
relay
,
the
adjustment
potentiometer
R
217
is
located
on
the
module
board
of
the
lower
circuit
board
as
shown
Use
of
the
18
point
extender
board
will
To
verify
the
factory
setting
of
15
%
lower
circuit
in
the
circuit
board
layouts
on
page
19
.
allow
easier
access
to
this
adjustment
.
The
procedure
to
be
used
to
verify
the
harmonic
restraint
function
depends
on
the
type
of
test
set
being
used
:
the
more
modern
electronic
current
-
source
,
or
,
the
older
style
voltage
-
source
.
Most
electronic
current
-
source
units
can
be
set
up
to
provide
one
output
current
at
the
fundamental
and
another
output
at
the
second
-
harmonic
frequency
.
When
using
voltage
-
source
sets
,
the
relay
’
s
built
-
in
diode
is
used
to
generate
second
-
harmonic
.
1
,
Electronic
_
current
-
source
testing
:
a
.
Connect
the
relay
as
shown
in
Figure
11
.
Apply
rated
dc
control
volts
.
b
.
Set
the
taps
at
2.9
A
.
%
Diff
and
Minimum
Restraint
:
any
settings
.
c
.
Apply
4.0
amperes
of
fundamental
current
.
The
relay
should
close
its
output
contact
.
d
.
Apply
2
nd
harmonic
current
and
increase
its
value
until
the
output
Iznd
/
Ifund
X
100
.
Percent
2
nd
for
restraint
contact
drops
out
.
For
the
4.0
A
fundamental
,
restraint
should
occur
for
hnd
The
2
nd
harmonic
current
may
be
increased
and
decreased
to
determine
the
restraint
and
release
points
,
and
R
217
may
be
readjusted
as
needed
to
obtain
the
desired
restraint
point
.
0.58
-
0.66
A
.
continued
on
page
20
.
2
.
.
.
.
.
.
Vo
1
tage
-
source
testing
:
Courtesy of NationalSwitchgear.com

Transformer
Differential
Relay
IB
7.6
.
1.7
-
4
Page
17
TEST
SET
Contact
Monitor
O
a
Figure
8
:
Typical
Test
Connections
a
Current
Source
#
1
II
60
HZ
Phase
=
o
deg
O
r
Minimum
Operating
Current
and
Pet
Differential
Characteristic
Tests
.
O
Current
Source
#
2
12
60
Hz
Phase
-
o
deg
a
Connection
shown
dotted
optional
depending
on
test
set
.
(
+
)
i
(
-
)
o
7
6
'
8
oo
13
14
13
)
16
12
11
9
Note
:
use
50
Hz
sources
if
relay
has
50
Hz
nameplate
rating
.
Apply
dc
control
power
per
relay
’
s
nameplate
rating
.
Resistor
required
between
terminals
9
and
10
.
See
page
14
.
TEST
SET
Contact
Monitor
O
o
+
o
Current
Source
#
I
60
HZ
O
Figure
9
:
Typical
Test
Connections
Alternate
Method
for
Pet
Differential
CharacteriStic
Test
(
+
)
87
T
i
(
-
)
8
^
7
6
6
i
o
o
13
14
13
o
16
12
11
10
9
Courtesy of NationalSwitchgear.com

Transformer
Differential
Relay
IB
7.6
.
1.7
-
4
Page
18
TEST
SET
Contact
Monitor
a
STOP
a
Figure
10
:
Typical
Test
Connections
+
O
Current
Source
#
t
II
60
HZ
Phase
=
o
deg
O
T
Instantaneous
Unit
Pickup
Test
+
o
-
j
Current
Source
#
2
iz
If
second
source
required
in
parallel
to
obtain
needed
current
levels
,
connect
as
shown
by
dotted
lines
.
60
HZ
Phase
-
o
deg
O
_
j
CM
+
HH
I
(
+
)
87
T
l
(
-
)
^
a
^
xx
4
'
,
8
o
°
o
o
13
14
13
Note
use
50
Hz
and
100
Hz
sources
if
relay
has
a
50
Hz
nameplate
rating
.
Apply
dc
control
power
per
relay
’
s
nameplate
rating
.
Resistor
required
between
terminals
9
and
10
.
page
14
.
See
TEST
SET
Contact
Monitor
a
a
-
CD
-
Current
Source
*
t
60
HZ
Phase
-
o
deg
Q
-
+
a
Current
Source
#
2
120
HZ
Phase
-
0
deg
a
Figure
11
:
Typical
Test
Connections
Harmonic
Restraint
Test
using
Electronic
Current
Source
.
(
+
)
87
T
J
(
-
)
o
7
6
<
5
^
6
8
o
°
o o
13
14
13
U
12
11
lO
9
Courtesy of NationalSwitchgear.com

Transformer
Differential
Relay
IB
7.6
.
1.7
-
4
Page
19
\
R
217
Percent
-
second
-
harmonic
calibration
potentiometer
R
228
R
230
S i
Q
O
U
203
R
229
l
Turn
R
217
clockwise
to
reduce
the
percentage
of
second
harmonic
required
to
restrain
relay
operation
.
H
R
226
h
o
-
tzn
C
203
C
210
RZSk
t
—
I
R
219
R
227
in
R
217
"
+
i
Connect
jumper
between
pins
3
and
5
for
test
of
87
T
Instantaneous
Unit
80
S
•
T
C
211
•
CM
C
209
R
20
B
•
w
U
201
R
201
H
H
C
201
R
2
B
2
1
H
R
205
R
203
088
Typical
Layout
-
Type
87
T
Harmonic
Restraint
Module
Board
C
2
SB
Q
O
o
R
22
M
R
2
W
Type
87
T
Typical
Layout
Main
Lower
Circuit
Board
R
11
9
Instantaneous
Unit
Pickup
Calibration
Potentiometer
Turn
R
119
clockwise
to
increase
pickup
.
Courtesy of NationalSwitchgear.com

Transformer
Differential
Relay
IB
7.6
.
1.7
-
4
Page
20
C
.
Harmonic
Restraint
Tests
(
continued
from
page
16
)
2
.
Voltage
-
source
testing
:
A
typical
test
circuit
is
shown
in
Figure
13
a
.
In
this
method
,
the
built
-
in
diode
between
terminals
15
and
16
is
used
to
generate
2
nd
harmonic
content
in
the
current
waveform
,
this
method
.
)
(
Do
not
use
an
electronic
current
source
test
set
with
Set
the
%
Diff
dial
to
15
%
and
the
MinRestraint
dial
to
1.0
.
(
if
these
settings
have
already
been
calibrated
,
mark
the
positions
so
you
can
return
to
the
calibrated
positions
at
the
end
of
this
test
.
)
a
.
Place
the
tap
pins
in
the
2.9
A
tap
.
b
.
Apply
rated
dc
control
voltage
to
the
relay
.
c
.
Set
the
Branch
B
current
at
zero
.
With
the
switch
closed
across
the
diode
,
increase
the
current
in
Branch
A
to
1.0
ampere
.
The
87
T
output
contact
should
close
since
the
input
current
is
all
fundamental
.
d
.
Open
the
contact
across
the
diode
,
thus
causing
significant
2
nd
harmonic
content
in
the
current
waveform
.
The
apparent
current
on
the
Branch
A
ammeter
will
drop
,
but
that
is
proper
.
The
87
T
relay
should
be
restrained
(
output
contact
open
)
,
target
-
reset
button
to
reset
the
target
.
e
.
Do
not
readjust
the
Branch
A
source
.
Actuate
the
increasing
the
fundamental
content
.
f
.
Slowly
raise
the
current
in
Branch
B
The
87
T
will
return
to
the
trip
condition
(
output
contact
closed
,
target
displayed
)
when
the
percentage
of
2
nd
harmonic
falls
below
the
set
value
.
This
value
may
be
read
directly
from
the
curve
in
Figure
13
b
.
Branch
A
current
was
originally
set
to
1.0
A
,
the
vertical
scale
may
be
read
as
the
current
in
Branch
B
.
Since
the
For
the
factory
calibration
of
15
%
nominal
,
the
Branch
B
current
should
be
between
0.8
and
1.0
ampere
for
acceptance
testing
.
The
Branch
B
current
may
be
raised
and
lowered
to
determine
the
"
restrain
"
and
"
unrestrained
"
values
.
Example
:
Assume
the
relay
restrained
with
a
Branch
B
current
of
0.92
amps
.
Reading
the
curve
at
0.92
gives
15
%
2
nd
harmonic
on
the
horizontal
scale
.
internal
potentiometer
R
217
may
be
used
to
adjust
the
value
of
2
nd
harmonic
that
causes
restraint
,
board
layouts
on
page
19
for
the
location
of
R
217
.
Adjustment
:
Refer
to
the
circuit
Note
:
a
change
in
the
restraint
point
may
occur
if
the
polarity
of
the
current
in
winding
1
-
2
is
reversed
.
This
is
due
to
internal
amplifier
offset
.
The
operating
point
should
be
within
the
limits
of
0.8
-
1.0
A
as
given
above
.
D
.
Additional
Tests
for
3
Winding
Relays
:
When
a
3
winding
relay
is
being
tested
,
the
Differential
Characteristic
Test
should
be
repeated
so
that
the
third
input
is
also
tested
.
Referring
to
either
Figure
8
or
Figure
9
as
appropriate
,
the
wire
on
terminal
5
should
be
moved
to
terminal
3
,
and
the
wire
on
terminal
6
moved
to
terminal
4
.
E
.
Note
on
Target
Operation
:
The
relay
’
s
target
may
drop
on
loss
of
dc
control
power
,
even
though
the
relay
has
not
closed
its
output
contact
.
Upon
reapplication
of
control
power
,
the
target
should
be
reset
if
required
.
Courtesy of NationalSwitchgear.com
This manual suits for next models
28
Table of contents
Other ABB Relay manuals
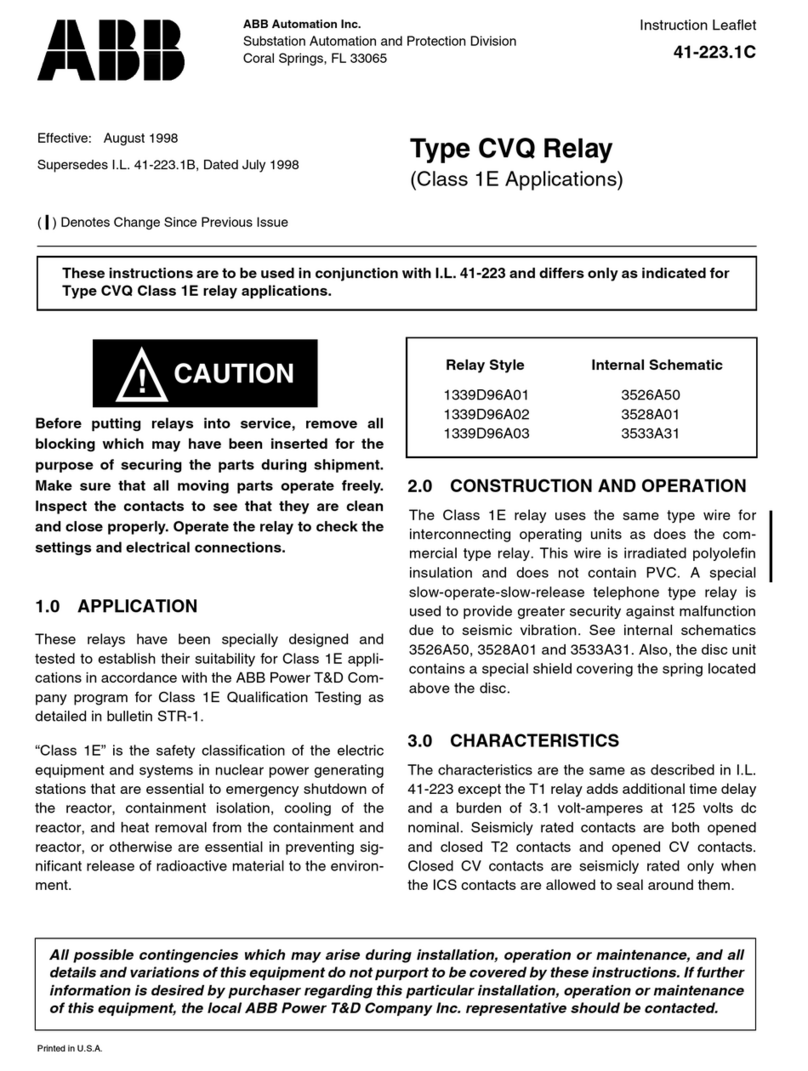
ABB
ABB CVQ Manual

ABB
ABB REU 523 Product manual
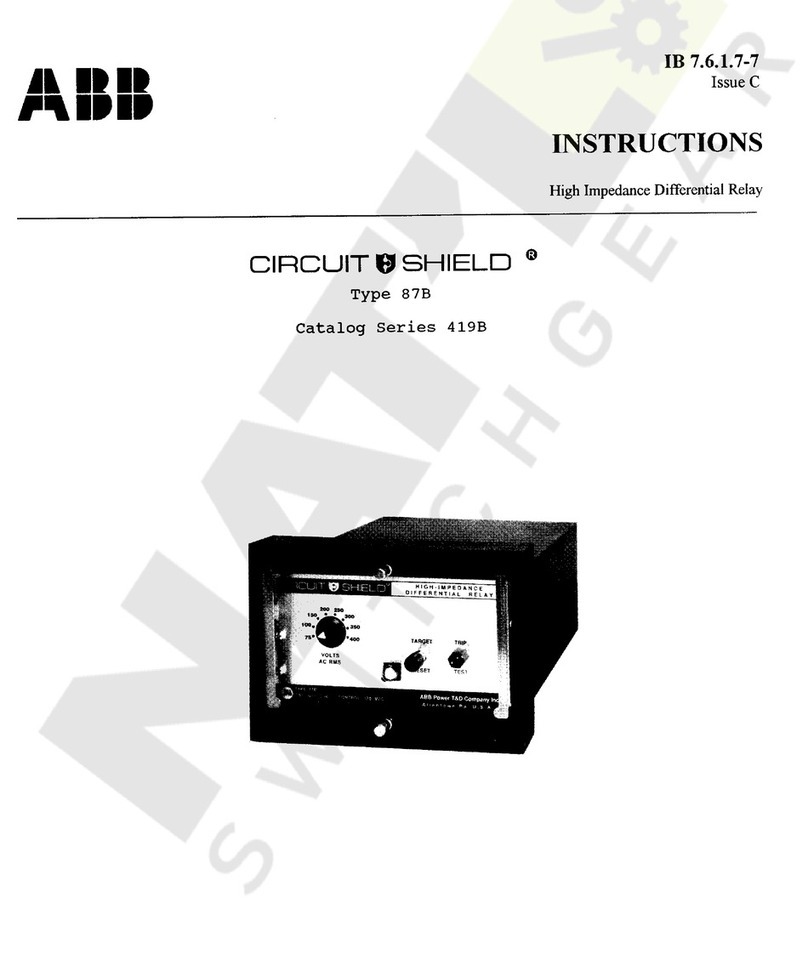
ABB
ABB Circuit Shield 87B User manual

ABB
ABB Rellon 620 Series User manual

ABB
ABB RELION 650 SERIES User manual

ABB
ABB RED670 Relion 670 series Quick start guide
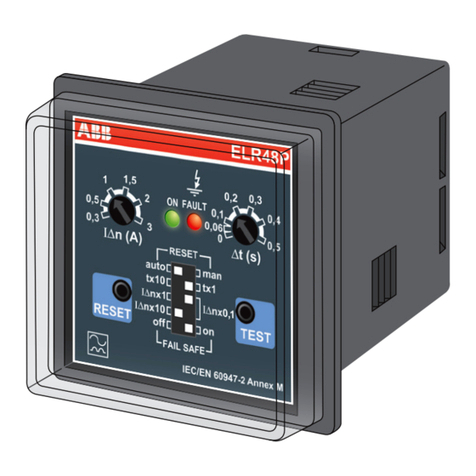
ABB
ABB ELR48P User manual
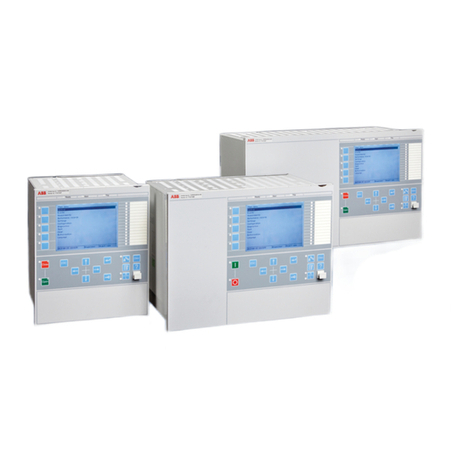
ABB
ABB Relion REC670 Quick start guide
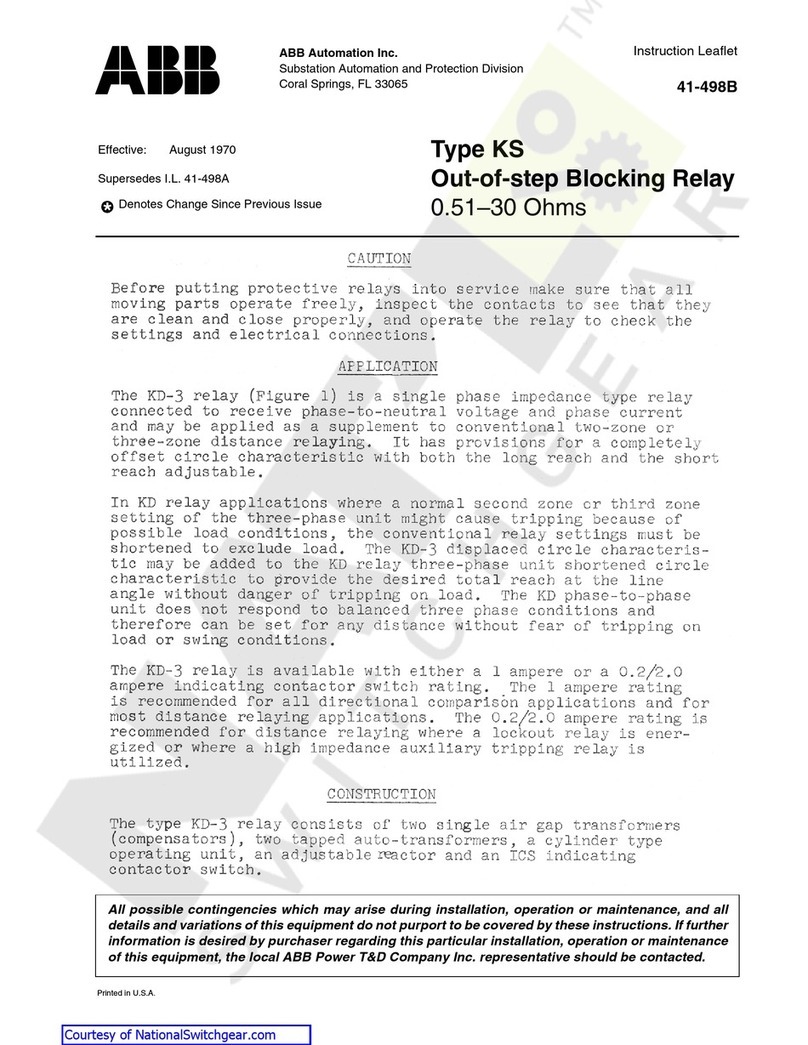
ABB
ABB KS Manual
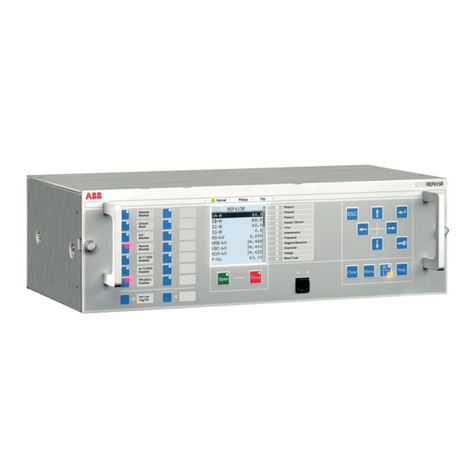
ABB
ABB RELION REF615R User manual