Acrel ARD2F User manual

444
444
444
444
ARD2F
Intelligent motor Protector
Operating Manual
V1. 1
ACREL Co., Ltd

DeclarationAll rights reserved. Without the written permission of the Company, the contents of
any paragraph or section in this manual shall not be copied, copied or disseminated in
any form. Otherwise, all consequences shall be borne by the violator.
Our company reserves all legal rights.
Our company reserves the right to modify the product specifications described in this
manual without prior notice. Before placing an order, please consult your local agent
for new specifications of this produ ct

Catalog
1、Overview ............................................................................................... 1
2、Product Features .................................................................................... 1
3
、
Model Description ................................................................................ 1
4
、
M ain parameters .................................................................................... 3
5、Overall dimensions and installation ...................................................... 5
6、Protection function description ........................................................... 11
7、Function setting and description ......................................................... 26
8、Communication Settings and instructions .......................................... 45
9
、
Typical applications ............................................................................ 8 3
10
、
Features and Functions ..................................................................... 8 7
11
、
Examples of ordering ........................................................................ 8 9

1
1
1
1
1 Overview
Overview
Overview
Overview
The ARD 2F intelligent motor protector (hereinafter referred to as the protector) is suitable for
low-voltage motor circuits with rated voltage up to 660V and integrates protection, measurement,
control, communication, operation and maintenance.Its perfect protection function ensures the
safe operation of the motor, with logic programmable function, can meet a variety of control
methods.
The product adopts split structure, which is composed of main body, display unit, mutual
inductor and optional communication module, and can adapt to the installation of various cabinets.
Product Implementation standards:
—— GB 14048.4-2010 Low-voltage switchgear and control gear -- Part 4-1: Contactors and
motor starters -- Electromechanical contactors and motor starters (including motor protectors);
—— JB / T 10736-2007 Low voltage motor protector.
2
2
2
2 Product
Product
Product
Product Features
Features
Features
Features
■ Support fundamental and full-wave power parameter measurement (U, I,
P,
Q, S,
PF,
F,
EP,
EQ), voltage and current imbalance degree, voltage and current positive sequence, negative
sequence, zero sequence component, three-phase voltage phase Angle, residual current.
■ Protection functions include overload inverse time, overload definite time, grounding, starting
timeout, leakage, underload, locked-rotor, obstruction, short circuit, phase, overflow, imbalance
(current, voltage, power, less power, overvoltage, undervoltage, phase sequence, temperature,
external fault, tE time , running time alarm, fault alarm.
■ 9 channels programmable DI input, the default use of DC24V power supply, or external active
wet contact can be selected (see the selection table).
■ 5 programmable DO output, to meet the direct starting, star - triangle starting,
auto-transformer starting, and other starting modes, can be through the communication bus to
achieve the master station to the motor remote control "start/stop".
■ Optional anti-shaking function: support immediate restart of shaking power and restart of
voltage loss.
■ MODBUS_RTU and PROFIBUS DPV1 communication modules are available for selection.2
MODBUS_RTU communication channels or MODBUS _RTU + PROFIBUS DPV1
communication modules can be chosen.
■ Optional 1 channels DC 4-20MA analog output interface, connected with DCS system, can
realize the monitoring of field equipment.
■ With fault record, start record, stop record, DI displacement record, restart record and other
records of various events, you can view a number of motor operation and maintenance
information.
■ The display interface supports Chinese/English LIQUID crystal display
3
3
3
3 Model
Model
Model
Model Description
Description
Description
Description

2
ARD 2 F
/ +
Display module (Table 3 )
Additional functions (Table 2 )
Current Specification (Table 1 )
Split
D esign serial number
Enterprise code
The corresponding relation between ARD 2F current specification and the rated current and power
of the applicable motor is shown in Table 1 :
Table 1
Protector current
specification (A)
Ratio
setting
Primary side coil
number of transformer
Applicable scope
of motor (kW)
Suitable for motor
Rated current range (A)
1
Support
5circle
0.12- 999 0.1- 5000
5
1circle
0.12- 999 0. 5 - 5000
1.6
Does
not
support
1circle
0.12-0.55 0.4-1.6
6.3
1circle
0.75-2.2 1.6-6.3
25
1circle
3-11 6.3-25
100
1circle
15-45 25-100
250
1circle
55-132 63-250
800
1circle
160-250 250-800
Additional features of ARD 2F are shown in Table 2 :
Table 2
Additional f unction Code Additional f unction Code
Starting control (including K
function)
Q Leakage protection L
Switching input K 4-20mA analog output M
Temperature protection T Anti - electric shock function SU
Alarm (Programmable output) J SOE event record SR
1 channel
communication
Modbus_RTU C
2 channels
communication
2路M odbus_RTU 2C
Profibus _DP CP Modbus+Profibus CCP
Voltage function (phase sequence,
power, power factor)
U t E time protection tE
Energy metering Ep
See Table 3 for the ARD 2F display module:
Table 3
Display module code
90L
LCD display , module size 98 × 60, opening 92 × 55 (unit : mm)
Remarks :
(1)、 Current measuring and 2 channels of relay output DO4(97 、98) 、DO5(95 、96 、94) are

3
standard for ARD2F.
(2)、 When equipped with starting control, the protector provides no more than 2 starting relay
for the sequence control of the closing/opening of two external contactors to realize different
starting ways of motor (such as
Y-
Δ
transformation starting, positive and negative rotation control,
and self-coupling reduced-voltage starting, etc.)
(3)、 The additional function SU and Q should be chosen together.Additional function SU is
including U(voltage function) and SR(SOE event record).
(4) 、 The current specifications of 100A and below shall be the same type of current transformer.
The transformer is equipped with a secondary line of about 1m. If you need special line length,
please contact the manufacturer.The 250A and 800A current specifications use two other types of
transformers with no secondary wires.See "External Dimensions and Installation" for the
dimensions of the transformer .
(5)、The standard display cable is a network cable with a length of 1.5m. 3 meters and 5 meters
are available for optional configuration.
You
can place an order and remark the corresponding
cable length.
(6)、 For customers who do not need display modules, a batch of optional several display
modules can be used as a programmer, or the configuration software provided by the manufacturer
can be used to configure parameters through computer software.
(7)、 The temperature measurement support sensor type is PTC or NTC. 。
(8)、 After selecting the leakage function (L), each protector shall be equipped with a leakage
transformer. Please refer to the "External Dimensions and Installation" section for the dimensions
of the leakage transformer.The leakage transformer is equipped with a secondary wire of
2m ± 10cm. If other lengths are needed, please contact the manufacturer.
4
4
4
4 M
M
M
M ain
ain
ain
ain parameters
parameters
parameters
parameters
4.1 Technical indicators
ARD 2F technical indicators are shown in Table 4 :
Table 4
Technical parameters Technical indicators
Protector auxiliary
power supply
AC85-265V/DC100-350V
Rated working voltage
of the motor
AC220V / 380V / 660V ,50Hz / 60Hz
Rated operating current
of the motor
1 (0.1A- 5000 A)
External current transformer
5 (0.1A- 5000 A)
1.6A(0.4A-1.6A)
6.3A (1.6A-6.3A )
25 (6.3A-25A )
100 (25A-100A )
250 (63A-250A )
800 (250A-800A )
Relay output contact
capacity
Impedance load AC250V 、10 A

4
Switching input
9 channels of passive dry contact (active DC110V , DC220V, AC220V
input can be optional)
C ommunication RS485 Modbus_RTU,Profobus_DP
E nvironment
Working temperature -10 º C ~55 º C
Storage temperature -25 º C ~70 º C
Relative humidity
≤ 95 % No condensation, no corrosive
gas
A ltitude ≤ 2000m
Pollution levels Class 3
Protection grade
Main body IP20, split display module IP54 (installed on the cabinet
panel)
Install ation category Level III
4.2 Functional configuration
The ARD 2F functional configuration is shown in Table 5
Table 5
Type
Function
Functional configuration
S tandard function Optional function
Protection
function
Fixed time overload √
Inverse time overload √
Starting timeout √
Phase loss √
V
oltage unbalance √
C urrent unbalance √
Locked-Rotor √
underload √
External fault √
B lock √
Temperature protection (PTC/NTC )√
R esidual current
grounding √
leakage √ (leakage )
Phase sequence √
Under voltage √
Over voltage √
Under powe r √
Over powe r √
tE Time protect √
Overflow protection √
Alarm of starting times √
Running time alarm √
Fault frequency alarm √
C ontrol
mode
Protection mode √
Direct start mode
√Two-step mode

5
Two-speed mode
Y-
△start mode
Voltage loss restart √
Communica
tion
1 channel Modbus-RTU communication √
2 channel Modbus-RTU communication √
1 channel Profibus-DP communication √
1 channel Modbus-RTU+1 channel
Profibus-DP
√
Switching
input
9 channel DI (programmable) √
Relay
output
2 channel DO (programmable) √
5 channel DO (programmable) √
Analog
output
1 channel DC4-20mA √
E vent
record
Start record, stop record, DI
displacement record, restart record,
(support communication transmission
and U disk export)
√
Display unit
Liquid
crystal
display
(LCD)
Black and white dot
matrix LCD display
√
5
5
5
5 Overall
Overall
Overall
Overall dimensions
dimensions
dimensions
dimensions and
and
and
and installation
installation
installation
installation
5.1 The product composition of ARD 2F is shown in Figure 1, Figure 2
FIG. 1 Composition of products with 100A and below specifications

6
FIG. 2 Composition of 250A and 800A
5 . 2 Panel size and opening (Unit :mm )
The shape and opening size of the black and white liquid crystal display unit are shown in Figure 4:
Front view Side view Back view
Hole size
Fig .3 T he shape and hole size of 90L display unit
5 . 3 Size of main body module (unit: mm)
The ARD 2F main body is installed with 35mm guide rail, and its external dimensions are shown
in Figure 4 :

7
Front view Side view
Fig .4 ARD 2F main body dimensions
5 . 4 The external dimensions of current transformers of 100A and the following specifications are
shown in FIG. 5 (unit: mm) : :
5.4.1 The current transformer with the current specification of the protector is 100A, with the
standard secondary connection line length of 1m ± 10cm. If other lengths are needed, please contact
the manufacturer, for example, 3m and 5m lines are optional.The secondary lines of yellow, blue,
red and black correspond to the correlation of current A, B, C and the common end of the
transformer.
A
protector is equipped with a set of transformer.
F ig . 5 External dimensions of current transformers with specifications below 100A
5.4 .2 T he external dimensions of the 250A current transformer are shown in FIG. 6 (unit: mm) :
The current specification of the protector is the current transformer matched at 250A. There is no
secondary connection wire. One protector is equipped with three transformers.

8
F ig . 6 External dimensions of current transformer 250A
5.4 .3 The external dimensions of the current transformer (800A) are shown in FIG. 7 (unit: mm) :
The current specification of the protector is 800A and the current transformer is not equipped with
secondary connection. One protector is equipped with three transformers.
F ig . 7 External dimensions of current transformer 800A
5.4 .4 The external dimensions of the leakage current transformer are shown in Figure 8 and Table
6 (unit: mm) :
The protectors with current specifications of 100A and below are equipped with leakage current
transformers with specifications of L-45.250A and current protector with specifications
L-80 leakage current transformer;800A and current specification protector with L-150 leakage
current transformer.The leakage transformer is equipped with a secondary wire of 2m ± 10cm. If
other lengths are needed, please contact the manufacturer.

9
F ig . 8 External dimensions of leakage current transformer
Table 6
Dimmen
sion
Spec.
Overall
size (mm)
Go through
size (mm)
Installation
size (mm)
T
olerance
(mm)
W
eight (g)
W H D Φ M N Φ 2
L-45 75 75 22 46 65 65 4
± 1
200 ± 10
L-80 120 120 23 81 105 105 4 380 ± 20
L-150 196 205 24 150 175 180 6 850 ± 50
5.5
T
erminal
The wiring terminal arrangement of the ARD 2F main body is shown in Figure 9 :

10
Fig . 9 ARD 2F terminal arrangement
See Table 7 for the ARD 2F terminal number and function definition:
Table 7
Terminals
NO .
Function definition Remark
1 Power input L (+ at DC time)
The auxiliary power supply is
connected to the two terminals2 Power input N (- at DC time)
3 Un input
Three-phase voltage input4 Ua Phase voltage input
5 Ub Phase voltage input
6 Uc Phase voltage input
7、8 DO1 ,Start 1 output
5 -channel programmable relay
output (DO)
(The function is defined as factory
default setting, which can be set by
users according to their needs)
9、10 DO2 ,Start 2 output
11 、12 DO3 ,Alarm output
97 、98 DO 4 ,Trip output, normally open point signal
95 、96 、94
DO 5 ,Trip output, normally closed + normally
open with common end
14 DI 1 ,Stop signal input
9 - channel programmable Switching
input (DI)
(The function is defined as factory
default setting, which can be set by
users according to their needs)
15 DI 2 ,Start 1 signal input
16 DI 3 ,Start 2 signal input
17 DI 4 ,Emergency stop signal input
18 DI 5 ,Reset signal input
19 DI 6 ,Control permission 1 input
20 DI 7 ,Control permission 2 input
21 DI 8 ,External fault signal input
22 DI9 ,ordinary DI
23 COM2 ,DI Input common terminal
35 A nalog output AO+
4-20mA analog output36 Analog output common end AO-

11
25 A1
F irst channel MODBUS
communication26 B1
28 A2
Second channel MODBUS
communication29 B2
32 T1 (PTC input A )
Temperature protection (thermistor
input)33 T2 (PTC input B )
41 I O * Leakage current measurement
42
COM3(common terminal of current 、leakage
current input )
Three phase current input43 Ia Phase current input
44 Ib Phase current input
45
Ic Phase current input
6
6
6
6 Protection
Protection
Protection
Protection function
function
function
function description
description
description
description
The default action stages of each protection are shown in Table 8 :
Table 8
Protection type
Default active
period
Overvoltage, undervoltage, voltage imbalance, phase sequence, external
fault, overflow protection, starting times, fault times, running time,
PTC/NTC temperature protection
whole course
Reverse time overload, locked rotor , phase break, leakage, grounding,
starting timeout, short circuit, overflow protection,
Overvoltage, undervoltage, voltage imbalance, phase sequence, external
fault, number of starts, number of faults, running time, PTC/NTC
temperature protection, fixed time overload
When starting
Reverse time-limit overload, blocking, phase break, current imbalance,
leakage, grounding, constant time-limit overload, underload, short circuit,
overflow protection, overvoltage, undervoltage, voltage unbalance, phase
sequence, underpower, overpower, external fault, PTC/NTC temperature
protection, number of starts, number of faults, running time
In operation
6.1 Inverse time overload protection
When the motor runs for a long time in excess of its rated current under excessive load, it
will overheat the motor, reduce insulation and burn it out. The protector calculates the heat
capacity of the motor according to its heating characteristics and simulates its heating
characteristics to protect the motor.
The starting condition of reverse time-limit overload protection is that the maximum
three-phase current reaches the set overload starting value, and the default overload starting value
is 1.2 times the motor's rated current.
The current-time comparison table of overload protection is shown in Table 9 , and the
overload characteristic curve (K curve) is shown in Figure 1 0 :

12
Table 9
Optional
tripping curve
grade K
1 2 3 5 10 15 20 25 30 35 40
Tripping delay
(S)tolerance
± 10%
Three - phase balanced load, starting from the cold state
Rated value
Ie × 1.2
25 50 75 125 250 375 500 625 750 875 1000
× 1.5 16 32 48 80 160 240 320 400 480 560 640
× 2 9 18 27 45 90 135 180 225 270 315 360
× 3 4 8 12 20 40 60 80 100 120 140 160
× 4 2.26 4.52 6.78 11.3 22.5 33.8 45 56.3 67.5 78.8 90
× 5 1. 44 2.88 4.32 7.2 14.4 21.6 28.8 36 43.2 50.4 57.6
× 6 1 2 3 5 10 15 20 25 30 35 40
× 7.2 0.7 1.4 2.1 3.5 6.9 10.4 13.9 17.4 20.8 24.3 27.8
0
100
200
300
400
500
600
700
800
900
1000
Ie × 1.2 × 1.5 × 2 × 3 × 4 × 5 × 6 × 7.2 × 8
F ig . 1 0 Characteristic curve of overload (K curve)
Inverse time overload protection improves manual and automatic reset options.When "automatic"
is selected, after the overload trip of the motor, the heat capacity will be automatically reset to less
than 15%, and the restart operation can be allowed without the need for further reset
operation;When "manual" is selected, after the motor overload trip, the heat capacity will be
reduced to less than 15%. Manual manual reset is required, otherwise the restart operation is not
allowed.

13
Note :
Imax :Maximum three-phase current
Is :Overload starting fixed value
Heat :Percentage heat capacity
Hs :Heat capacity alarm value
TS :Starting shield time
t E Time protect ion
For the increased safety type motor, after the ac winding reaches the rated operating stable
temperature at the highest ambient temperature, the time required from the beginning of passing
through the blocking current until it rises to the limit temperature is tE time.The tE time of the
increased safety motor is usually provided by the motor manufacturer, and the user can find this
data on the motor nameplate.
It provides thermal overload protection of disconnecting the power supply of the motor within tE
time during lock-in. It is only put in after the motor is started, with an independent delay timer.The
motion delay comparison of tE protection characteristic curve is shown in Table 1 0 , and the curve
is shown in Figure
1
1 :
2 3 4 5 987
2
3
5
8
2
5
10
20
50
t(S)
tEp(S)
15
12
100
A
I /I

14
Fig .
1
1 tE Protection delay to blocking current ratio IA/Ie Current-time characteristic curve
I nstructions : tEp :7 times of the rated current allowed lock-in time ; IA :Locked-rotor current ;
Ie :Rated current of the motor.
Table10
t
Ep
Set
IA/Ie
2(S)3(S)4(S)5(S)6(S)8(S)10 (S)12 (S)15 (S)
2.0 32 48 64 80 96 128 160 192 240
2.2 20.27 30.4 40.54 50.67 60.81 81.08 101.35 121.62 152.02
2.4 14.75 22.12 29.5 36.87 44.25 59 73.75 88.5 110.63
2.6 11.54 17.32 23.09 28.87 34.64 46.19 57.74 69.29 86.62
2.8 9.46 14.19 18.92 23.65 28.39 37.85 43.31 56.78 70.97
3.00 8 12 16 20 24 32 40 48 60
3.20 6.91 10.37 13.83 17.29 20.75 27.67 34.59 41.51 51.88
3.40 6.08 9.13 12.17 15.22 18.26 24.35 30.44 36.52 45.66
3.60 5.43 8.14 10.86 13.58 16.29 21.72 27.16 32.59 40.74
3.80 4.9 7.35 9.8 12.25 14.7 19.6 24.5 29.41 36.76
4.00 4.46 6.69 8.93 11.16 13.39 17.86 22.32 26.79 33.48
4.20 4.09 6.14 8.19 10.24 12.29 16.39 20.49 24.59 30.74
4.40 3.79 5.68 7.58 9.47 11.37 15.06 18.95 22.74 28.42
4.60 3.52 5.28 7.05 8.81 10.57 14.1 17.62 21.15 26.43
4.80 3.29 4.94 6.59 8.24 9.88 13.08 16.48 19.77 24.72
5.00 3.09 4.64 6.19 7.74 9.29 12.38 15.48 18.58 23.22
5.20 2.92 4.38 5.84 7.3 8.76 11.68 14.6 17.53 21.91
5.40 2.76 4.15 5.53 6.91 8.3 11.07 13.83 16.6 20.75
5.60 2.63 3.94 5.26 6.57 7.89 10.52 13.15 15.78 19.73
5.80 2.5 3.76 5.01 6.27 7.52 10.03 12.54 15.05 18.81
6.00 2.4 3.6 4.8 6 7.2 9.6 12 14.4 18
6.20 2.3 3.45 4.6 5.75 6.9 9.2 11.51 13.81 17.26
6.40 2.21 3.32 4.42 5.53 6.64 8.85 11.07 13.28 16.6
6.60 2.13 3.2 4.27 5.33 6.4 8.54 10.67 12.81 16.01
6.80 2.06 3.09 4.12 5.16 6.19 8.25 10.32 12.38 15.48
7.00 2 3 4 5 6 8 10 12 15
8.00 2 3 4 5 6 8 10 12 15
9.00 0.2 0.2 0.2 0.2 0.2 0.2 0.2 0.2 0.2
N ote :
(1)The action time of tE protection = the action time /2 × t
Ep
when t
Ep
is 2 (S)
(2)When tE is set at 5 (S), the tE value determined according to the starting current ratio IA/ Ie
is in accordance with iEC79-7 and GB3836.3-2000 standards. When it is used for tE time
protection of increased safety motor, its inverse time overload protection can be set according to
this characteristic curve.In order to ensure that the power is disconnected before tE time during the
motor's lock-in, the inverse time curve of the overload protection device should be lowered by

15
about 15%.
(3)The action time of tE protection is achieved by setting "motor type" and "trip level", and the
corresponding trip curve is selected by setting tEp (trip level) according to Table 9.(When the
motor type is selected as "increased security motor", the tripping level will automatically change
to tEp setting;Otherwise, the trip curve is the reverse time-limit overload trip curve of ordinary
motor.
Note :
Imax :Maximum three-phase current
In :Rated current
Heat :Percentage heat capacity
Hs :Heat capacity alarm value
6.2 Start timeout protection
When the starting time of the motor reaches the starting time set by the user, the average
three-phase current does not drop below the set tripping threshold, trigger the starting timeout
protection, issue tripping command, and stop the motor operation.For the increased safety motor,
the starting time setting shall not exceed 1.7 times tE time.
Note :
Iav :Three-phase mean current
Is :Set trip threshold
T
s:S tarting time

16
6.3 Locked-rotor protection
In the process of starting, if the motor shaft is stuck due to excessive load or mechanical reasons,
and the fault is not removed in time, the motor will overheat and the insulation will be reduced
and the motor will be burned out.The lock ed-rotor protection is applicable to the motor when such
faults occur in the starting stage. When the average current percentage reaches the set threshold,
the protector will trip or alarm within the set time in time to avoid the motor burning out.
Note :
Iav :Three-phase mean current
Is1 :Alarm action threshold
Is2 :Tripping threshold
Ts1 :Alarm action delay time
Ts2 :Delay time of trip action
6.4 Blocking protection
During the operation of the motor, if the motor shaft is stuck due to excessive load or mechanical
reasons, and the fault is not removed in time, the motor will be overheated and the insulation will
be reduced and the motor will be burned out.The blocking protection is applicable to protect the
motor when such faults occur in the running stage. When the average current reaches the set
threshold, the protector will trip or alarm within the set time in time to avoid the motor burning
out 。

17
Note :
Iav :Three-phase mean current
Is1 :Alarm action threshold
Is2 :Tripping threshold
Ts
:Alarm action delay time
6.5 Underload protection
The protector provides underload protection when the motor is loaded with pumping load. When
the average three-phase current is lower than the set value, the protector should trip or alarm
within the set time.
Note:
Iav: Three-phase mean current
Is1: Alarm action threshold
Is2: Tripping threshold
Ts1: Delay time of alarm action
Ts2: Delay time of trip action
6.6 、Underpower protection
When the load power is lower than the set action value, the protector will trip or alarm during the
set action time.
Table of contents
Other Acrel Protection Device manuals
Popular Protection Device manuals by other brands
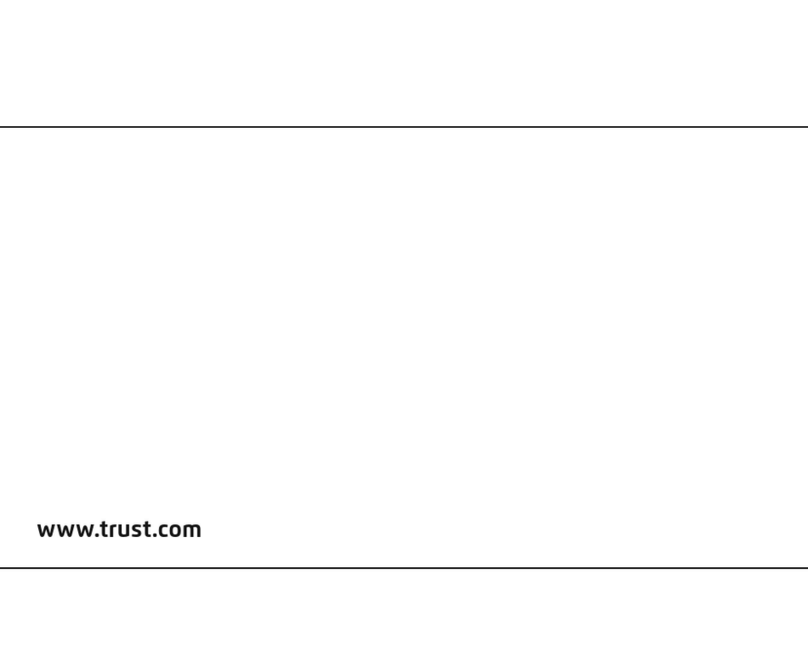
Trust
Trust START-LINE OWH-002 user manual
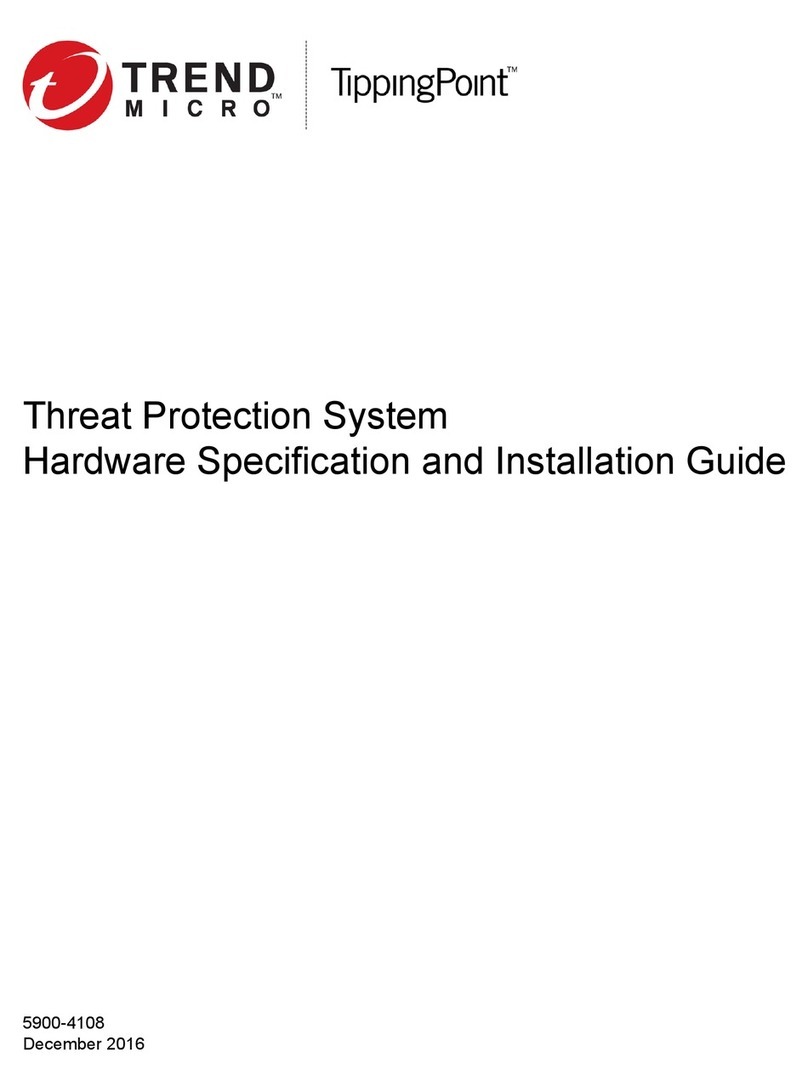
Trend Micro
Trend Micro TippingPoint 2200T Hardware Specification and Installation Guide
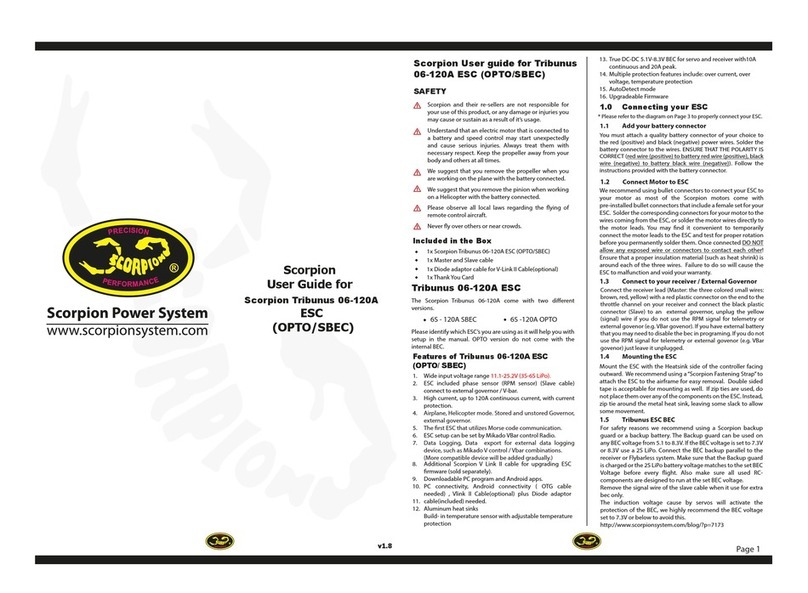
Scorpion Power System
Scorpion Power System Tribunus 06-120A ESC user guide
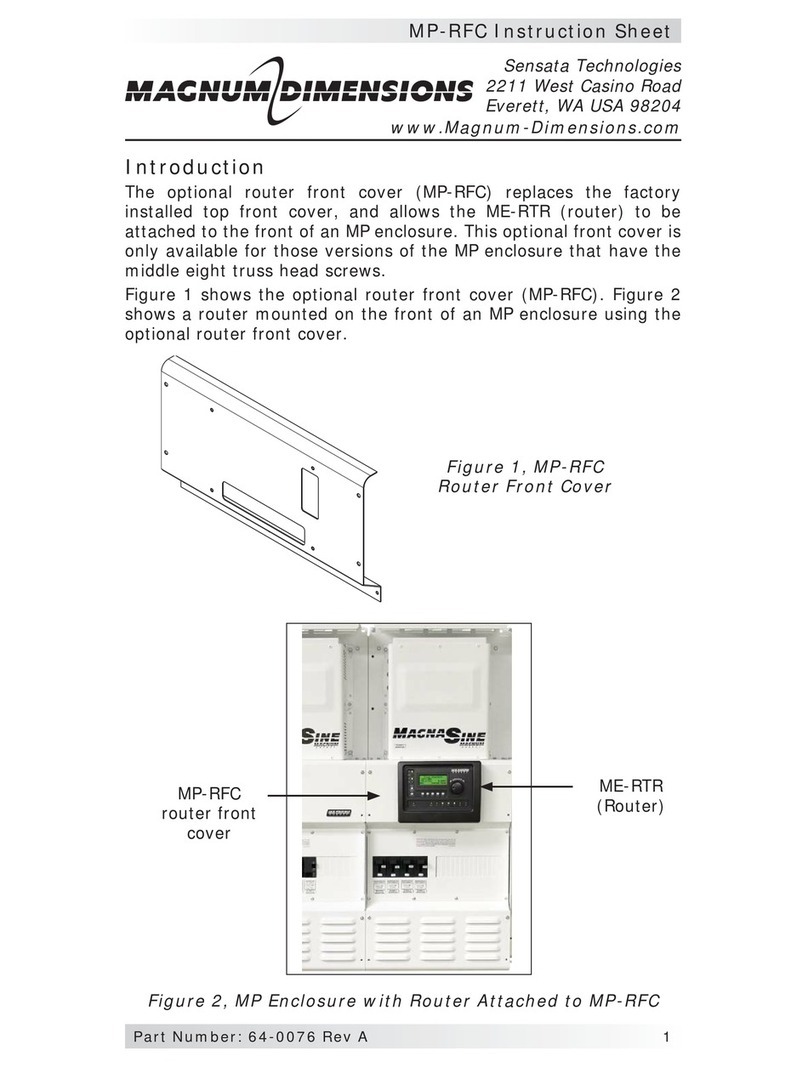
Magnum Dimensions
Magnum Dimensions MP-RFC instruction sheet

Sony
Sony BKM-PP25 Mounting instructions
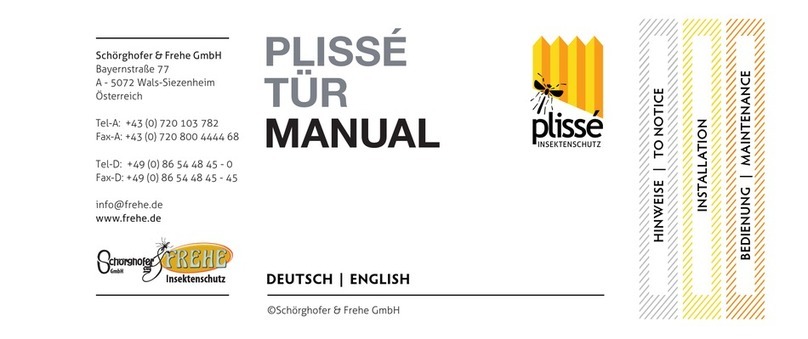
Schörghofer & Frehe
Schörghofer & Frehe Plisse manual