Advanced Instruments 3D3 User manual

4D35SM Rev25 082714
Advanced®Osmometer Model 3D3
Advanced®Cryoscope Model 4D3
Service Manual


3he Advanced®3D3/4D3 Service Manual
1. Introduction
Specifications . . . . . . . . . . . . . . . . . . . . .7
General Description and Purpose . . . . .9
Service Assistance . . . . . . . . . . . . . . . . .9
Safety/Regulatory Information . . . . . .11
Symbol onventions . . . . . . . . . . . . . .11
General autions . . . . . . . . . . . . . . . . .11
Service & Maintenance autions . . . .12
Hazardous Material autions . . . . . . .13
Regulatory Notices . . . . . . . . . . . . . . .13
Symbol onventions . . . . . . . . . . . . . .14
2. General Overview
Major onfiguration hanges . . . . . . .17
System control electronics . . . . . . . . .17
Motor control relays . . . . . . . . . . . . . .17
Operator/Supervisor keyswitch . . . . . .17
General Overview (Intel) . . . . . . . . . . .18
Removing the over . . . . . . . . . . . . . .19
alibration . . . . . . . . . . . . . . . . . . . . . .20
3D3/4D3 ircuit Description (Intel) . .21
Power Supply . . . . . . . . . . . . . . . . . . . .21
Front End . . . . . . . . . . . . . . . . . . . . . . .21
3D3605/4D3605 ontrol Board Set . .21
3D3620/4D3620 Processor Board . . . .22
P B605 Application Board . . . . . . . . .23
3D3/4D3 ircuit Description (Hitachi)27
Power Supply . . . . . . . . . . . . . . . . . . . .27
Front End . . . . . . . . . . . . . . . . . . . . . . .27
3D3600/4D3600 Main ontrol Board .27
Design hanges . . . . . . . . . . . . . . . . . .30
Replacement Parts . . . . . . . . . . . . . . . .32
Supplies & Accessories . . . . . . . . . . . .32
3. Maintenance
leaning and Maintenance . . . . . . . . .37
Osmometer/ ryoscope Well leaning 39
4. roubleshooting
Introduction . . . . . . . . . . . . . . . . . . . . .43
Freeze Amplitude . . . . . . . . . . . . . . . . .44
Stir Driver Noise . . . . . . . . . . . . . . . . .45
Head Sensor Adjustment . . . . . . . . . . .46
Head Up/Down Test . . . . . . . . . . . . . .47
Power On Diagnostics . . . . . . . . . . . . .48
A/D Tests . . . . . . . . . . . . . . . . . . . . . . .48
Sample Bin Setting . . . . . . . . . . . . . . .49
Block Bin Setting . . . . . . . . . . . . . . . .50
Stir Amplitude . . . . . . . . . . . . . . . . . .50
Display/Printer Test . . . . . . . . . . . . . . .51
Beeper Test . . . . . . . . . . . . . . . . . . . . .51
Keypad Test . . . . . . . . . . . . . . . . . . . . .51
Barcode Test . . . . . . . . . . . . . . . . . . . .51
Reset Serial Number . . . . . . . . . . . . . .52
Instrument Software Updates . . . . . . .53
Performing FLASH firmware update .53
Troubleshooting Table . . . . . . . . . . . . .55
5. Replacement Instructions
Block Probe (4D3340) . . . . . . . .4SP340
lapper (3 2241R) . . . . . . . .3 2P241R
ontrol Board Set (3D3605/4D3605),
Application Board (P B605R),
Processor Board (3D3620R/4D3620R)
. . . . . . . . . . . . . . . . . . . . . . .4D3P620
ooling Assembly (3D3300/4D3300)
. . . . . . . . . . . . . . . . . . . . . . .4D3P300
ooling Fan (4D3360) . . . . . . . .4DP360
Display Board and Harness (4D3851)
. . . . . . . . . . . . . . . . . . . . . . .4DP851R
EPROM (716811R) . . . . . . . . .71P811R
EPROM (716824R) . . . . . . . . .71P824R
EPROM (716825R) . . . . . . . . .71P825R
Ferrite Bead Rework (91035) . . .4SP475
Fuse (70011/70022) . . . . . . . . . . .700P11
Head Up Relay or Head Down Relay
(3D3109) . . . . . . . . . . . . . . . .3DP109
Heat Transfer Fluid Pump Assembly
(4D3690), Fluid Filter (4D3710),
One-way heck Valve (4D3705/
99133R) . . . . . . . . . . . . . . . . .4DP690
ISO 5764 Upgrade Kit (4D3101)4D3P01
ISO 5764 Upgrade Kit (4D3104 4D3P04
Keypad (3D3511/4D3511) . . . . .4DP511
Load Resistor (425150R) . . . . .42P150R
Mandrel (3LH500) . . . . . . . . . .3LHP500
Motor (4D3350) . . . . . . . . . . . . .4DP350
NVRAM Battery (71027R) . . . .71P27R
Power Supply Assembly (4D3950/
325950R) . . . . . . . . . . . . . . . .325P950
Power Supply Assembly (3D3950)
. . . . . . . . . . . . . . . . . . . . . . . .4DP950
Table of Contents

4
The Advanced®3D3/4D3 Service Manual
Probe Alignment Tool Kit
(3LA700) . . . . . . . . . . . . . . . .3LP700
Sample Probe (4D3700) . . . . . . .4DP700
Sample Probe (3D3700) . . . . . . .3DP700
Sample Probe (4D3102) . . . . . . .4D3P02
Sample Probe Versions FAQ . . .4DP002
Stir/Freeze Coil (3D2404) . . . . .3DP404
Stir/Freeze ire (3LH243/
4LH243) . . . . . . . . . . . . . . . .4LHP243
Transistor (PCB520) . . . . . . . .PCP520R
Transistor (PCB522) . . . . . . . .PCP522R
Tube Ejector Spring (3D3312/
4D3312) . . . . . . . . . . . . . . . 4DP312
Yoke (3LH230) . . . . . . . . . . . .3LHP230
6. Printer User Manual
7. Schematics
Hitachi Processor Board
PCB600 Assembly Drawing
PCB600 Main Board Schematic
Interconnection Schematic - Hitachi
Intel Processor Board
PCB605 Assembly Drawing
PCB605 Application Board Schematic
4D3605 Assembly Drawing
PCB620 Assembly Drawing
PCB620 Processor Board Schematic
Interconnection Schematic - Intel
APPENDICES
A: Symbol Definitions
B: Product Disposal and Recycling
C: Service Log
Inde

1. Introduction


7he Advanced®3D3/4D3 Service Manual
Model 3D3 Osmometer Specifications
Electrical:
Voltage: 100 to 130 VA or 200 to 250 VA
Frequency: 50 or 60 Hz
Fuses: 2-Amp time delay for 100-130 VA ;
1-Amp time delay for 200-250 VA
Power: 150 Watts
Memory Backup: integral lithium cell;
10 years typical
Sample Volume: 0.20 or 0.25 mL
Sample Capacity: Single sample
Readout: 20-character digital display
Units: mOsm/kg H2O
Range:
Low: 0 to 2000 mOsm/kg H2O
High: 1400 to 4000 mOsm/kg H2O
Linearity: Less than ±0.5% from a straight line
Resolution: 1 mOsm/kg H2O
Repeatability:
0 to 400 mOsm ±2 mOsm/kg (1 S.D.)
400 to 4000 mOsm ±0.5% (1 S.D.)
Communications:
DTE RS-232 , parallel printer, barcode
Storage Temperature: - 40° to +45°
(- 40°F to +113°F)
Operating Temperature
(ambient): 18° to 35°
(64°F to 95°F)
Room umidity: 5 to 80% R.H.
(non-condensing)
Drift: Less than 1 digit per month
Ambient Temp. 1 digit for every 5° (9°F)
Effect: ambient temperature change.
Start-up Time: From stand-by: immediately
From power on: under 5 minutes
Test Time: Approximately 2 minutes per sample
in 0 to 2000 mOsm range; moderately
longer in high range.
Dimensions inches centimeters
Width: 12.5 32
Depth: 16.5 42
Height: 11.5 29
With Head Up: 16 41
Weight pounds kilograms
Net: 27 12
Shipping: 38 18
Warranty: One-year limited warranty on work-
manship and all parts except glass,
plastic and parts warranted by their
makers.
Certification:
Refer to Regulatory Notices (see page 11) for appli-
cable standards.

he Advanced®3D3/4D3 Service Manual 8
Model 4D3 Cryoscope Specifications
Electrical:
Voltage: 100 to 130 VA or 200 to 250 VA
Frequency: 50 or 60 Hz
Fuses: 2-Amp time delay for 100-130 VA ;
1-Amp time delay for 200-250 VA
Power: 150 Watts
Memory Backup: integral lithium cell;
10 years typical
Sample Volume: 2.0 to 2.5 mL
Sample Capacity: Single sample
Readout: 20-character digital display
Units: -m° or -m°H
Range: 0 to -1000 m° or m°H
Linearity: Typically ±0.5% from a straight line
Resolution: ±1 m° or m°H
Repeatability: ±2 m° or m°H (1 S.D.)
Communications:
DTE RS-232 , parallel printer, barcode
Storage Temperature: - 40° to +45°
(- 40°F to +113°F)
Operating Temperature
(ambient): 18° to 35°
(64°F to 95°F)
Room umidity: 5 to 80% R.H.
(non-condensing)
Drift: Less than 1 digit per month
Ambient Temp. 1 digit for every 5° (9°F)
Effect: ambient temperature change.
Start-up Time: From stand-by: immediately
From power on: under 5 minutes
Test Time: Approximately 90 seconds in
30-second timed mode
Dimensions inches centimeters
Width: 12.5 32
Depth: 16.5 42
Height: 16 41
Weight pounds kilograms
Net: 27 12
Shipping: 38 18
Warranty: One-year limited warranty on work-
manship and all parts except glass,
plastic and parts warranted by their
makers.
Certification:
Refer to Regulatory Notices (see page 11) for appli-
cable standards.

he Advanced®3D3/4D3 Service Manual
9
General Description and Purpose
Advanced® Osmometers and ryoscopes
determine the concentration of solutions
through freezing-point depression measure-
ment. Osmometers are used primarily to
measure body fluids such as serum and urine,
and cryoscopes are used to determine the
freezing points of various liquids and to
detect added water in milk. Application infor-
mation is available upon request.
Except for different cooling assemblies,
stir/freeze wires, sample sizes and software,
the 3D3 and the 4D3 are identical to one
another. For clarity when replacing parts or
troubleshooting, the instructions indicate any
significant differences between the two instru-
ments.
he Service Manual
This Service Manual contains:
• instructions for performing repairs.
• guides for troubleshooting operational and
mechanical problems.
• circuit system illustrations.
• information about replacement parts and
service repairs.
This manual is designed to assist
service technicians, and does not
imply a license to perform repairs
without proper qualifications.
Service Assistance
To contact Advanced Instruments Product
Service:
• all (800) 225-4034 (toll-free within the
USA and anada; after normal business
hours, dial extension 2191)
• all +US (781) 320-9000 (elsewhere)
• Or fax (781) 320-3669
When calling Advanced Instruments, have the
model and serial number from the label on the
back of the instrument, and a description of
the problem. Use a telephone as close to the
instrument as possible in order to facilitate
making recommended diagnostic checks.
A service technician may assist in making
minor repairs over the phone, providing you
with recommended parts (or part numbers), or
may issue an authorization (RMA) to ship the
instrument for factory repair.
The RMA procedure is as follows:
1. ontact Advanced Instruments to obtain
an RMA.
2. Pack and ship the instrument in its origi-
nal carton. Do not send instrument sup-
ply items.
3. Prepay shipment to the factory. Advanced
Instruments cannot accept collect ship-
ments. Insure the shipment or accept the
damage risk.

10
he Advanced®3D3/4D3 Service Manual
Notes:

he Advanced®3D3/4D3 Service Manual
11
To reduce the risk of bodily injury,
electric shock, fire, and damage to
your instrument, please read and
observe the following precautions.
• If the product is used in a manner not in
accordance with the equipment design,
operating instructions or manufacturer's
recommendations, the operation of the
product may be impaired to the extent that
a safety hazard is created.
• Do not attempt to perform electrical work
if you are not fully qualified. This manual
is not a substitute for electrical training.
Symbol Conventions
The exclamation point within an
equilateral triangle is intended to
alert the user to the presence of
important operating and maintenance
(servicing) instructions in the litera-
ture accompanying this product.
The lightning flash with arrowhead
symbol within an equilateral triangle
is intended to alert the user to the
presence of uninsulated dangerous
voltage within the product's enclo-
sure that may be of sufficient magni-
tude to constitute risk of electric
shock to persons.
The static symbol within an equilat-
eral triangle is intended to alert the
user to the presence of internal com-
ponents that could be damaged by
static electricity.
This static symbol is intended to
alert the user to the presence of a
specific component that could be
damaged by static electricity.
This symbol indicates the presence
of alternating current (A ).
This symbol indicates the presence
of a fuse.
This symbol indicates the presence
of protective earth ground.
This symbol indicates the power is
ON.
This symbol indicates the power is
OFF.
General Cautions
• This product should be operated only with
the type of power source indicated on the
product’s electrical ratings label. Refer to
the installation instructions included with
the product.
• If the power cord provided is replaced for
any reason or if an alternate cord is used,
the cord must be approved for use in the
local country. The power cord must be
approved for the product’s listed operating
voltage and be rated at least 20% greater
than the ampere ratings marked on the
product’s electrical ratings label. The cord
end that connects to the product must have
an IE 60320 connector.
• Plug the product into an approved ground-
ed electrical outlet.
• Do not disable the power cord’s grounding
plug.
• If an extension cord or power strip is used,
make sure that the cord or strip is rated for
the product, and that the total ampere rat-
ings of all products plugged into the exten-
sion cord or strip do not exceed 80% of the
cord’s or strip’s rating limit.
• Route power cords so that they will not be
walked on, tripped on, or pinched by items
placed upon or against them. Pay particu-
Safety / Regulatory Information

he Advanced®3D3/4D3 Service Manual 12
lar attention to the plug, electrical outlet,
and the point where the cord exits the
product.
• Do not pull on cords and cables. When
unplugging cords or cables, grasp the cor-
responding connector.
• Do not install or use this product in any
area subject to extreme short-term temper-
ature variations, or locations that exceed
the specified operating environment tem-
peratures.
• Never use this product in a wet area.
• To avoid injury or fire hazard, do not oper-
ate this product in an explosive atmos-
phere.
• Do not install or use the product on an
unstable, non-level work surface.
• Do not operate this product with the covers
removed or unsecured.
Service & Maintenance Cautions
•Unplug the power cord prior to opening or
removing covers, or else you may be
exposed to electric shock, excessive tem-
peratures, or mechanical hazards.
•Performing service or maintenance not
detailed in the User’s Guide, with or with-
out this Service Manual, should only be
done by a qualified service technician.
•Never restrict airflow into or out of the
product. Occasionally, check the air vents
for blockage.
•Wipe the exterior of the product with a
soft, damp cloth as needed. Using cleaning
products other than those specified, may
discolor or damage the finish.
•If the product requires service for any of
the following reasons, unplug the product
from the electrical outlet and refer service
to a qualified service technician.
- The power cord, extension cord, power
strip or power input module is damaged.
-Liquid has been spilled into the interior
of the product.
-A foreign object has fallen into the
product.
-The product has been dropped or dam-
aged by a falling object.
-There are noticeable signs of overheat-
ing or a burning odor.
-The product does not operate normally
when you follow the operating proce-
dures.
-The main supply fuse(s) or any internal
fuse(s) continually fail.
•A discharge of static electricity from con-
tact with the human body or other conduc-
tor may damage system boards or static
sensitive devices. Never perform internal
maintenance without following recom-
mended static protection procedures.
• The product is equipped with operator
accessible fuses. If a fuse blows, it may be
due to a power surge or failure of a com-
ponent. Replace the fuse only once. If the
fuse blows a second time, it is probably
caused by failure of a component part. If
this occurs, refer service to qualified serv-
ice personnel. Always replace the fuse
with one of the same rating, voltage, and
type. Never replace the fuse with one of a
higher current rating.
• When servicing the product, use only
factory-specified parts.
• WARNING: When returning this product
for service, or shipping this product to a
second location, remove all hazardous
specimens and decontaminate the product
before packaging for shipment. If the
product cannot be decontaminated, consult
with your shipping agent on appropriate
packaging and marking.

he Advanced®3D3/4D3 Service Manual
13
Hazardous Material Cautions
• WARNING: Handle all biohazardous mate-
rials according to established good laborato-
ry practices and follow your institution’s
exposure control plan. Persons handling
human blood and body fluid samples must
be trained in blood-borne hazards and
observe universal precautions. Universal pre-
cautions is an approach to infection control,
where all human blood and body fluids are
treated as if known to be infectious. Use per-
sonal protective equipment such as gloves,
gowns, etc., to prevent exposure. Store bio-
hazardous materials in regulated waste con-
tainers and dispose of these materials in a
safe and acceptable manner that is in com-
pliance with all country, state and local
requirements.
•If a biohazardous material is spilled on or
inside the equipment, decontaminate the
equipment using a 1% bleach solution, or as
outlined by those policies and procedures
established within your institution.
•To avoid injury or fire hazard, do not operate
this product in an explosive atmosphere.
Regulatory Notices
•This product has been designed and manu-
factured in accordance with U.S., anadian,
and European regulatory requirements as
outlined below. Modifications made to this
product that are not expressly approved in
writing by the manufacturer will void the
user’s authority to operate this product, pre-
viously issued factory approvals, and the
user’s rights under the warranty.
•The distributor or dealer may have applied
additional local, national, or international
approvals to this product. onsult the dis-
tributor or dealer for more information and
documentation.
•onnections to this product must be made
with shielded cables. Use of non-shielded
cables may violate RFI/EMI limits.
U.S. Safety This product has been listed by
ETL testing laboratories as being
in compliance with the require-
ments of UL 3101-1, 1st Edition,
"Electrical Equipment for
Laboratory Use; Part 1: General
Requirements". The "US" in the
lower right of the ETL mark
demonstrates this listing.
anadian Safety This product has been listed by
ETL testing laboratories as being
in compliance with the require-
ments of AN/ SA 22.2
No.1010.1-92, "Safety
Requirements for Electrical
Equipment for Measurement,
ontrol and Laboratory Use;
General Requirements";
Including Amendment Two. The
" " in the lower left of the ETL
mark demonstrates this listing.
E Declaration of This product meets the intent of
onformity - EM Directive 89/336/EE for
Electromagnetic ompatibility.
ompliance was demonstrated
using the following standards, as
listed in the Official Journal of
the European ommunities:
onsult the Declaration of on-
formance certificate shipped with
the product for the latest update.
• EN 61326: 1998, Group 1,
lass B, "Electrical Equipment
for Measurement, ontrol, and
Laboratory Use".
E Declaration of: This product meets the intent of
onformity - Low Directive 73/23/EE , the Low
Voltage Voltage Directive. ompliance
was demonstrated using the fol-
lowing standards as listed in the
Official Journal of the European
ommunities: onsult the
Declaration of onformance cer-
tificate shipped with the product
(if required) for the latest update.
·EN 61010-1 (1993), "Safety
Requirements for Electrical
Equipment for Measurement,
ontrol and Laboratory Use -
General Requirements";
Including Amendment Two
(1995).
Regulatory
approval type Description

The Advanced®3D3/4D3 Service Manual 14
Symbol Conventions
This symbol indicat s conformity to
r l vant Europ an dir ctiv s.
This symbol indicat s th product
was t st d to conform to r l vant
Canadian and U.S. saf ty standards
by Int rt k T sting S rvic s NA,
Inc. Th ETL mark is approv d in
th Unit d Stat s as a Nationally
R cogniz d T sting Lab (NRTL) by
OSHA, and in Canada by th
Standards Council of Canada.
Regulatory
approval type Description
EC D claration of This product m ts th int nt of
Conformity - WEEE Dir ctiv 2002/96/EC as am nd d
by 2003/108/EC for Wast
El ctrical and El ctronic
Equipm nt (WEEE). Consult th
D claration of Conformanc c r-
tificat shipp d with th product
(if r quir d) for th lat st updat .

2. General Overview


17 he Advanced®3D3/4D3 Service Manual
Over the years, Advanced Instruments, Inc.
has made several improvements to the
3D3/4D3 system. It is important to identify
some of these changes to properly service
your instrument. Although every attempt has
been made to cover all the configurations,
some descriptions may vary from what is
present in your particular situation. If you are
having difficulty comparing your system to
this manual, consult the factory for assistance.
Please refer to the applicable system photo-
graphs and circuit descriptions once you have
identified your configuration. You may also
refer to suffix history chart located in the
Design hanges section of this manual, but
keep in mind that many of these changes were
backward-compatible, so use the chart only as
a reference.
System control electronics
1. The original main control board was a
single board located on the right side,
containing a Hitachi 63A03 microproces-
sor and a 256K Byte EPROM. This
board can be identified by the heat sink
mounted component in the upper left cor-
ner of the main control board. This board
and firmware are no longer supported, as
of October 1, 2001.
2. The second main control board was a sin-
gle board located on the right side, also
containing a Hitachi 63A03 microproces-
sor, but had a 512K Byte EPROM. This
board can be identified by the lack of a
heat sink mounted component in the
upper left corner of the main control
board. This board and firmware are no
longer supported, but can be replaced
with the Intel configuration. All refer-
ences to this configuration will use the
term main control board.
3. The third and current control board, locat-
ed on the right side, is a two-board set.
The larger board is called the application
board, and the smaller board is called the
processor board. The processor board
contains an Intel 80 186 microprocessor
and two field-programmable Flash
EPROM's. All references to this configu-
ration will use the terms control board
set, application board, or processor
board.
Motor control relays
1. The original configuration used two chas-
sis-mounted relays located on the center
rear interior wall.
2. The second configuration used two P B-
mounted relays located on the center rear
interior wall. This version may be used
as a replacement for the first configura-
tion.
Operator/Supervisor keyswitch
1. The first configuration had no keyswitch.
All references to keyswitch position in
this manual should be ignored.
2. The second configuration used a black
plastic keyswitch located on the rear of
the instrument. This keyswitch, when in
the operator position, locked the user out
of these features: setup, diagnostic test
utilities, and calibration.
3. The third and current configuration uses a
metal keyswitch located on the rear of the
instrument. This keyswitch, when in the
operator position, locks the user out of
these features: setup and calibration.
Note:If you have configuration number 2
(above) and you replace the main con-
trol board with the control board set,
the operator and supervisor positions
will be reversed, and your keyswitch
will now only lock out the setup and
calibration features.
Major Configuration Changes

he Advanced®3D3/4D3 Service Manual 18
General Overview
A. Head
B. Motor
. Driver Transistors (Stir, Thermoelectric)
D. Motor apacitor
E. Head Up/Head Down Relays
F. Power Entry Module
G. RS-232 Port
H. Printer Port
I. Printer Power Outlet
J. Supervisor/Operator Keyswitch
K. Barcode Port
(Intel Processor Systems)
A
B
Q
T
S
D
F
G
R
H
E
P
L
I
MNO
K
J
U
L. Sample Probe Plugin
M. Block Probe Plugin
N. Main Board Set (Application/Processor)
O. Power Supply
P. Keypad Transition Board
Q. Keypad
R. Display
S. Deck
T. Heat Transfer Return Tube
U. Heat Transfer Inlet Tube

19 he Advanced®3D3/4D3 Service Manual
Removing the Instrument Cover & the Head Cover
Tools Needed: Flat-bladed screwdriver,
Phillips screwdriver.
Warning-Hazardous Voltage
Warning-Internal components ma
be damaged b static electricit .
CAUTION: Improper connections
may cause damage to the instrument.
The following instructions refer to 4D3
cryoscopes with suffix "A" or later, and to
all 3D3 osmometers:
1. Turn off the power and unplug the instru-
ment.
2. Remove the two sets of screws from the
side panels (A) and the two screws from
the rear panel (B).
3. Slide the instrument cover up and off.
4. Remove the two screws from the head
cover ( ) and lift off the head cover.
The following instructions refer to 4D3
cryoscopes without a suffix:
1. Turn off the power and unplug the instru-
ment. Remove the heat transfer fluid
from the front cover.
2. Remove the two screws from the rear
panel of the back cover (B) and lift off
the back cover.
3. Remove the four screws from underneath
the front cover, lift the front cover slightly
up and then slide it forward and off.
4. Remove the keypad display connectors
from the keypad on the front cover.
5. Remove the two screws from the head
cover ( ) and lift off the head cover.
A
B

20
he Advanced®3D3/4D3 Service Manual
The 3D3 has two ranges, each with its own
calibration. To calibrate the low range, three
freezing-point tests are required at the 100
mOsm/kg level, and six tests are required at
the 1500 mOsm/kg level. To calibrate the
high range, six freezing-point tests are
required at both the 1500 mOsm/kg level and
the 3000 mOsm/kg level.
The 4D3 allows timed or plateau-seeking cali-
bration in either the Hortvet (m°H) or the
elsius (m° ) scale. Six freezing-point tests
are required at each of the 4D3s two calibra-
tion levels:
-408 m° (-422 m°H), and
-600 m° (-621 m°H).
Note: On instruments using the Intel proces-
sor and control board set, your cali-
bration may vary slightly from that
mentioned here. If you see the mes-
sage “Recalibration Needed”, follow
the instrument prompts to complete the
initial calibration.
alibrate the instrument according to the
instructions below:
1. Turn the instrument on.
2. If there is a Supervisor/Operator key-
switch, turn it to the Supervisor position.
It must remain there throughout calibra-
tion.
3. Press CALIB to begin the calibration
sequence.
4. The display will prompt you at each cali-
bration level. Place a sample of the first
calibration standard into the freezing
chamber and press START.
5. ontinue loading and testing samples at
the first calibration level until the display
prompts you for samples at the second
calibration level.
6. Place the sample of the second calibration
standard into the freezing chamber and
press START.
7. When the instrument has completed cali-
bration, the display will read
"Calibration Complete".
Calibration
This manual suits for next models
1
Table of contents
Other Advanced Instruments Test Equipment manuals
Popular Test Equipment manuals by other brands
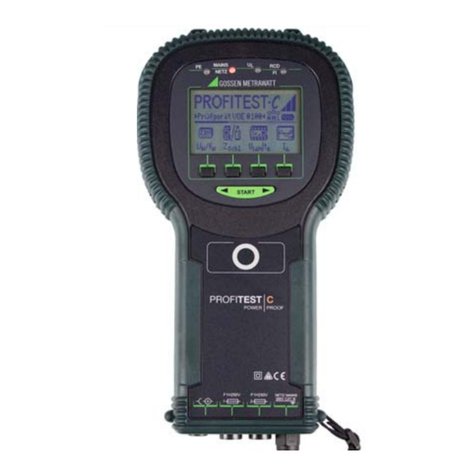
Gossen MetraWatt
Gossen MetraWatt ProFiTEST C-GB int. operating instructions
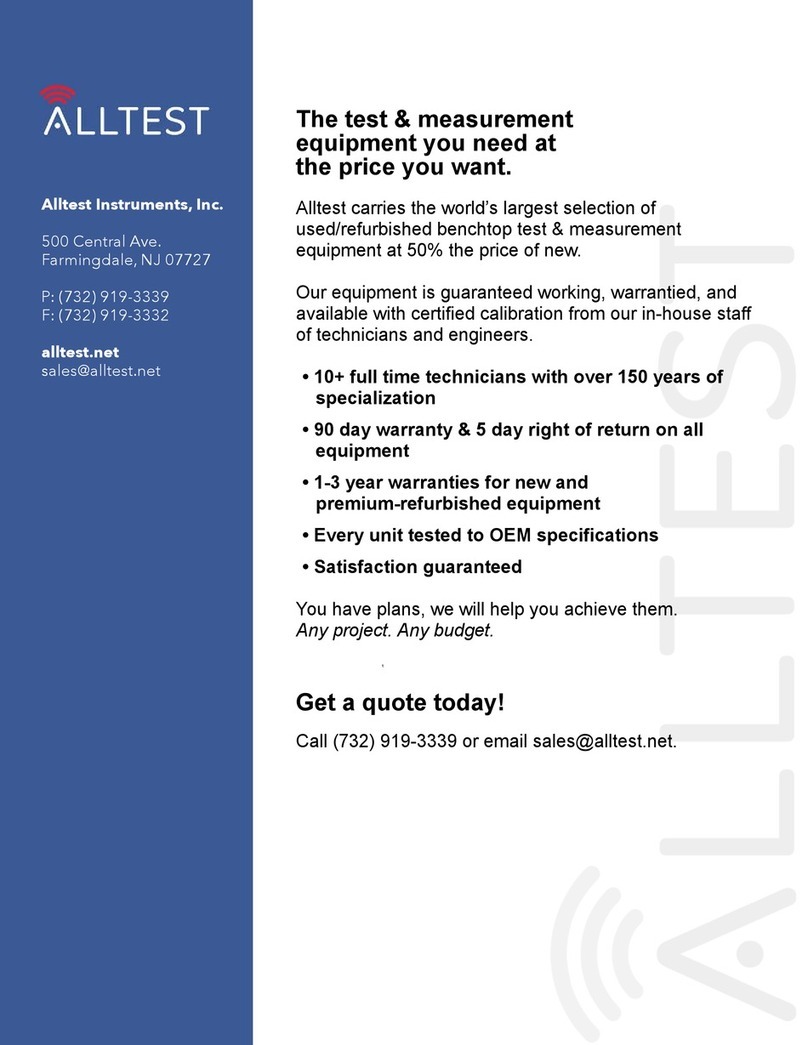
Tektronix
Tektronix 1725 instruction manual
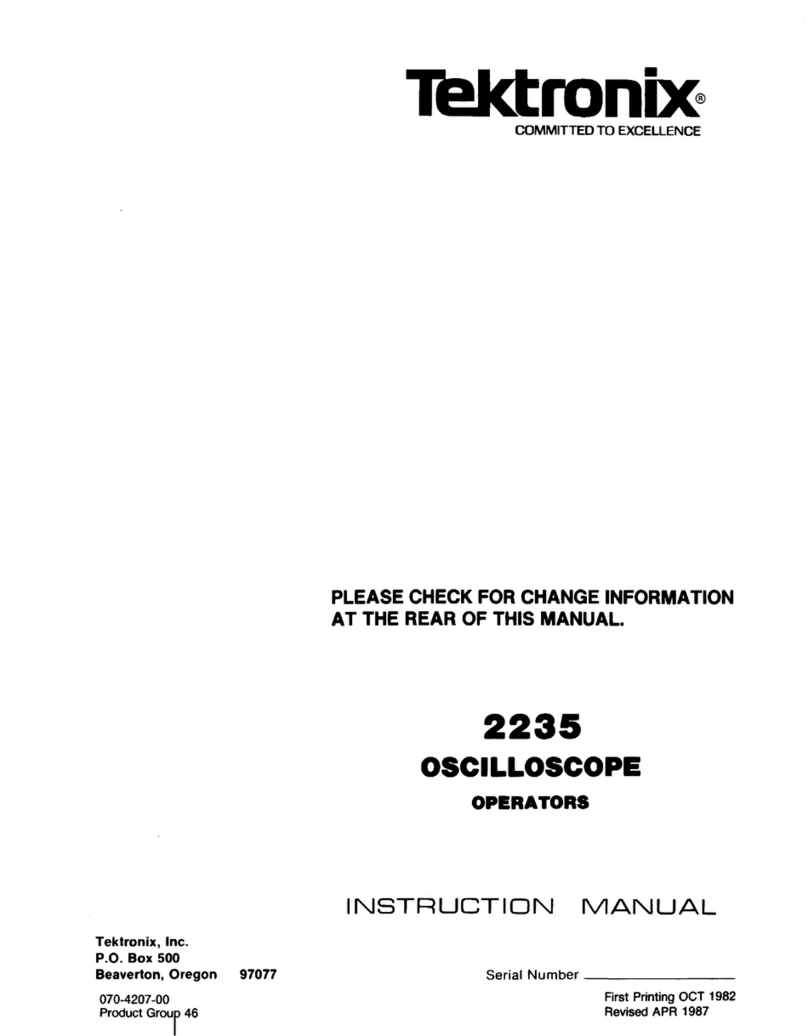
Tektronix
Tektronix 2235 instruction manual
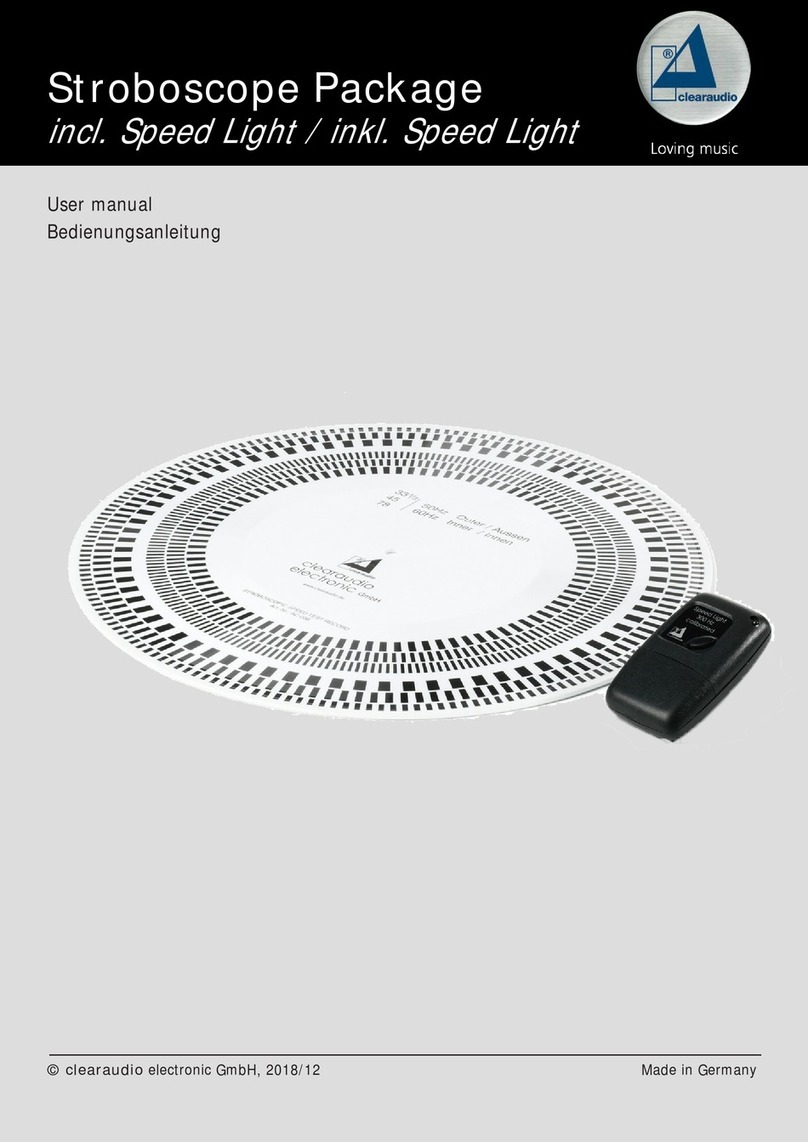
Clearaudio
Clearaudio AC039 user manual
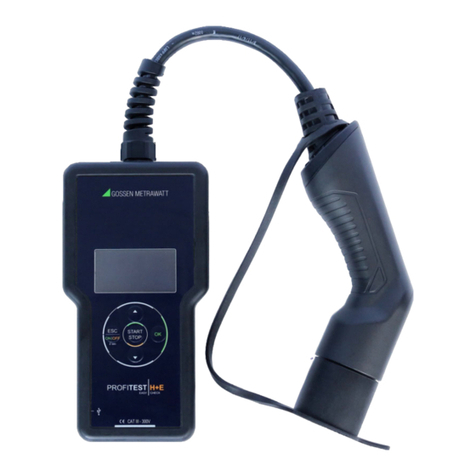
Gossen MetraWatt
Gossen MetraWatt PROFITEST H+E EASY CHECK operating instructions
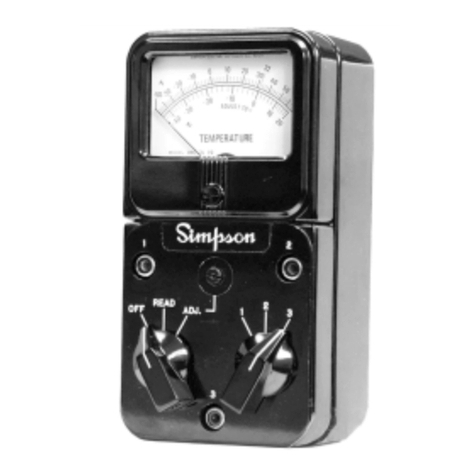
Simpson
Simpson 385-3L Operator's manual