AEROCET 3400 Installation and user guide

ISSUE DATE:
8/12/03
Incorporated
PAGE
1 of 107
TITLE: Service & Maintenance Manual
FILE NO.
A-10031
REVISION
DATE:
2/6/2020
SUBTITLE: Model 3400 Amphibious Floats
REVISION
8
SERVICE MANUAL
AND
INSTRUCTIONS FOR CONTINUED AIRWORTHINESS
FOR
AEROCET 3400 AMPHIBIOUS SEAPLANE FLOATS
Aerocet, Inc.
P.O. Box 2119
265 Shannon Lane
Priest River, Idaho 83856
Phone: (208) 448-0400
Fax: (208) 448-1644
This ICA must be followed when Aerocet 3400 Floats are installed in
accordance with Supplemental Type Certificate (STC) No. SA01257SE.
The information contained in this document supplements or supersedes the
basic manuals only in those areas listed herein. For limitations, procedures, and
performance information not contained in this manual, consult the basic
aircraft ICA or maintenance manual.

ISSUE DATE:
8/12/03
Incorporated
PAGE
2 of 107
TITLE: Service & Maintenance Manual
FILE NO.
A-10031
REVISION
DATE:
2/6/2020
SUBTITLE: Model 3400 Amphibious Floats
REVISION
8
This page intentionally left blank.

ISSUE DATE:
8/12/03
Incorporated
PAGE
3 of 107
TITLE: Service & Maintenance Manual
FILE NO.
A-10031
REVISION
DATE:
2/6/2020
SUBTITLE: Model 3400 Amphibious Floats
REVISION
8
Log of Revisions Page
REV. PAGES
AFFECT.
DESCRIPTION DATE
0
ALL
Initial Release
8/12/03
1
2, 15, 22-25
Calendar time added to inspection schedule,
editorial.
9/25/04
2
27
Corrected tire ply from 6 to 8 ply rating
8/1/06
3
Incorporated changes to the lower nose gear
assembly, keel and wear strip installation, main gear
and edited troubleshooting in gear advisory/hydraulic
pump.
3/17/08
TH
4
10
15-17
11, 13, 16,
17.
Added 35A-45700 Wheel Installation & references
to A-10036 CMM.
Added Ni8U-EM12E-AN6X2-H1141 Sensor to main
gear section.
Added Figures 5.2.10; 5.3; 5.6; 5.7a, 5.7b; .
7/06/09
TH
5
5, 59-68
7
8
9
11
12
12-15
17
23
32-34
38
40, 48
51
69
Added Section 11. Troubleshooting.
Added note Re: K-66 compatibility.
Added 1.1 Availability of this manual.
Added 1.2 Applicable CMM’s
Added 1.3 Dimensions, Locations and
Nomenclature.
Deleted “UHMW Plastic” from Keel Strip
description.
Added Figure 2.1.
Added “(for old style plugs only)”
Added 2.1, 2.2, and 2.3 for Fasteners.
Added Figure 3.1.1.
5.2.11 Expanded Axle Nut Installation.
Added Figures 6.2.1, 6.2.2, 6.2.3, 6.2.4, & 6.2.5.
Added Figure 6.7 to differentiate between old and
new Gear Advisories.
Added Note to define text applicable to only the K-
65 Gear Advisories.
Added 6.8 with illustrations for Spot Mirror.
Added “removal” to Para. 2 & 3.
Changed title of Section 9 from “Continued
Airworthiness Schedule…” to “Recommended
Airworthiness Schedule…”
Added Section 12. Airworthiness Limitations to
comply with 14 CFR Part 23, Appendix G.
8/17/09
T. Hamilton
6
43-527, 30-
3179-80
Added new section 8 on installation of floats to
aircraft including weights of remaining components.
Other changes to include 206
Added Appendix with Install drawings for CPL
8/27/2010
MHH

ISSUE DATE:
8/12/03
Incorporated
PAGE
4 of 107
TITLE: Service & Maintenance Manual
FILE NO.
A-10031
REVISION
DATE:
2/6/2020
SUBTITLE: Model 3400 Amphibious Floats
REVISION
8
REV. PAGES
AFFECT.
DESCRIPTION DATE
7
9
10
19
49, 51-53
66, 71, 77
85, 86
87
Added 206 image to Figure 1.3.1.
Added 182 image to Figure 1.3.1.
MS20426AD4-xxx was MS203426AD4-xxx
Added T206H References.
Added Inspection, troubleshooting and repair of
main gear actuator housing.
Added listings to Appendices A & B.
Added Appendix C, for T206H
9/23/15
8
ALL
Minor changes, such as punctuation or formatting are
not marked. Subsections that follow newly inserted
subsections are remarked sequentially without
marks. Updated or added cross references to
sections and figures without marks.
2/6/2020
7
Copy/pasted relevant WARNING from Section 2.
17 thru 30
Expanded Section 2 to include general cleaning, salt
removal, corrosion prevention, lubrication, locker
subsections, & bilge cup subsections.
34 thru 35
Added splash guards to nose gear removal.
37
Added “and Brake” to Aerocet Wheel and Brake.
50
Added 35A-60200 hydraulic power unit.
51
Added “108 Series” to clarify accumulator tube use.
53
Added 6.7 General Service of Hydraulic System.
59
Added 7.5 Water Rudder Anodes.
61
Added Section 8 Anodic Systems.

ISSUE DATE:
8/12/03
Incorporated
PAGE
5 of 107
TITLE: Service & Maintenance Manual
FILE NO.
A-10031
REVISION
DATE:
2/6/2020
SUBTITLE: Model 3400 Amphibious Floats
REVISION
8
Table of Contents
Section Topic .........................................................................................................................................................Page
Log of Revisions Page...................................................................................................................................................3
Table of Contents...........................................................................................................................................................5
1Introduction and General Float Information....................................................................................................7
2Float Hull and General Maintenance.............................................................................................................17
3Float Handling and Jacking...........................................................................................................................31
4Nose Gear......................................................................................................................................................33
5Main Gear......................................................................................................................................................37
6Landing Gear Retraction System...................................................................................................................45
7Water Rudder Retraction and Steering System.............................................................................................59
8Anodic Systems.............................................................................................................................................61
9Float Installation and Removal to Aircraft....................................................................................................63
10 Repairing Composite Float Hulls..................................................................................................................77
11 Recommended Service Schedule, General Practices and Product Listings for Service................................85
12 Tire Pressures................................................................................................................................................91
13 Troubleshooting ............................................................................................................................................93
14 Airworthiness Limitations...........................................................................................................................103
Installation Drawings for Aerocet Model 3400 Amphibious Floats:.........................................................................105

ISSUE DATE:
8/12/03
Incorporated
PAGE
6 of 107
TITLE: Service & Maintenance Manual
FILE NO.
A-10031
REVISION
DATE:
2/6/2020
SUBTITLE: Model 3400 Amphibious Floats
REVISION
8
This page intentionally left blank – except this line

ISSUE DATE:
8/12/03
Incorporated
PAGE
7 of 107
TITLE: Service & Maintenance Manual
FILE NO.
A-10031
REVISION
DATE:
2/6/2020
SUBTITLE: Model 3400 Amphibious Floats
REVISION
8
1Introduction and General Float Information
This service and maintenance manual is applicable to Aerocet Model 3400 Amphibious Seaplane Floats and their
general application to a variety of airplanes. The Customer Parts List in the appendix provides pertinent data
referenced to in the text of this manual. Strut geometry, boxing (flying) wires, specific hydraulic line routing, pump
mounting – electric and emergency, specific wiring, water rudder retract routing, and landing gear advisory
mounting are unique for each STC or TC application to aircraft. Installation of the Aerocet Model 3400
Amphibious Seaplane Floats should be done according to the FAA approved drawings supporting these different
applications.
The Aerocet Model 3400 Amphibious Seaplane Floats are twin all composite float hulls separated by spreader bars,
which incorporate hydraulically operated retractable landing gear allowing for landing on either water or land. An
airplane-mounted electric-hydraulic pump, with a backup hand pump operates the hydraulics. The float utilizes a
double fluted bottom contour from the step forward and has a flat top deck design with built-in antiskid. Each float
offers a single large storage locker. Each float has six compartments for safety. Access to the inside of these
compartments is through screwed on access panels on the deck or through the storage locker hatch cover. Water
rudders are mounted on the stern of each float for water taxi operations. The floats are mounted to various airplanes
by aerodynamic aluminum struts. These are rigidly mounted. Boxing (flying) wires are used to stabilize the
mounting of the floats to the airplane.
The floats incorporate pump locations into each compartment, and these are used to remove any excess water
through condensation, leakage from the access panel gaskets, bolts, or pump-out plugs, or leakage from a damaged
float hull. These pump locations will also show hydraulic leakage, which is red in color.
The main landing gear utilizes a trailing arm link design using a 6.00 X 6 tire and an oleo shock strut. The nose gear
is full swiveling, has a centering device, and uses a composite strut for absorbing the landing loads. Steering of the
airplane is done through differential braking.
A panel mounted landing gear advisory and gear position switch is used. It includes an up and down lever, lights for
each gear and their position, a pump operation light, and an audio output to advise the pilot of gear position when
triggered at a set speed. An optional smaller, dash mounted, landing gear position light system is available giving
the pilot more heads-up awareness of the landing gear condition prior to landing.
WARNING:
If the pilot, when on the water, strikes rocks or debris, assess the damage as soon as possible. Continuing into a
high-speed situation with the floats, will typically exaggerate the damage due to high water pressure. If the pilot
makes a hard landing on the runway, stop and examine the landing gear parts and supporting structure for
damage. The composite nose strut should not have any delamination, the main gear truck should not have any
sheared rivets and all the metal should have no distortion. The drag brace (the metal part which connects the
oleo strut to the step bulkhead) should not be bent (especially in the area of the over center stop contact point).
NOTE:
The K-66 “auxiliary” unit is only available with the K-65 Gear Advisory, and is not
useful or compatible with the newer, Model GC600 Gear Advisory units.

ISSUE DATE:
8/12/03
Incorporated
PAGE
8 of 107
TITLE: Service & Maintenance Manual
FILE NO.
A-10031
REVISION
DATE:
2/6/2020
SUBTITLE: Model 3400 Amphibious Floats
REVISION
8
1.1 Availability
One complete hard (paper) copy of this manual shall be provided with each new set of Model 3400 Twin Amphibian
Floats. Additional copies and minor revisions shall be available via email, U.S.P.S. (mail), UPS or FedEx by
request. Fees and delivery charges may apply.
Notification of any changes that require service for airworthiness shall be distributed to all applicable Aerocet
owners on record with Aerocet, Inc. In such a case, copies of the applicable, revised portions of this manual shall be
provided.
Aerocet, Inc. maintains record of purchasers and/or owners, collected at the time of purchase in order to comply
with the above, as well as to maintain a high standard of service. If you have moved since your original purchase,
have purchased a used product or otherwise have reason to believe that the contact information on file is incorrect,
please provide the following information to Aerocet, Inc: (Aerocet contact information is on the front of this
document.)
Float Information:
Float Model: _________________________________
Float S/N (R/L) _______________________________
Aircraft Information:
Aircraft Make/Model __________________________
Aircraft Registration ___________________________
Aircraft S/N _________________________________
Owner Information: (as applicable)
Previous Owner ______________________________
Previous Address _____________________________
Present Owner _______________________________
Present Address ______________________________
Present Phone Number ________________________
Present Email Address _________________________
1.2 Component Maintenance Manuals
Certain accessories that are more complex, that require additional inspection and maintenance procedures are
described in Component Maintenance Manuals (CMM) or Maintenance Manuals (MM). References to the
necessary manuals are placed in relevant areas of this manual. Depending upon the optional equipment you have
installed on your Aerocet Model 3400 floats, you may also require the following CMM’s, MM’s or Parts Catalogs:
1) Cleveland Wheels and Brakes, AWBCMM0001-7 (or later) Maintenance Manual.
2) Cleveland Wheels and Brakes, AWBPC0001-7 (or later) Product Catalog
3) Aerocet A-10036, Component Maintenance Manual [Aerocet 6.00-6 Wheel Assembly, Aerocet Brake
Assembly]
4) Aerocet A-10037, Component Maintenance Manual [Aerocet Model GC600 Gear Advisory]

ISSUE DATE:
8/12/03
Incorporated
PAGE
9 of 107
TITLE: Service & Maintenance Manual
FILE NO.
A-10031
REVISION
DATE:
2/6/2020
SUBTITLE: Model 3400 Amphibious Floats
REVISION
8
1.3 Dimensions, Locations and Nomenclature
Figure 1.3.1 Showing Model 3400 Amphibious Float installation on a Cessna 180 Aircraft (185 similar).
Figure 1.3.2 Showing Model 3400 Amphibious Float installation on a Cessna 206 Aircraft.

ISSUE DATE:
8/12/03
Incorporated
PAGE
10 of 107
TITLE: Service & Maintenance Manual
FILE NO.
A-10031
REVISION
DATE:
2/6/2020
SUBTITLE: Model 3400 Amphibious Floats
REVISION
8
Figure 1.3.3 Showing Model 3400 Amphibious Float installation on a Cessna 182 Aircraft.
Figure 1.3.4 Showing Front View of Model 3400 Floats.

ISSUE DATE:
8/12/03
Incorporated
PAGE
11 of 107
TITLE: Service & Maintenance Manual
FILE NO.
A-10031
REVISION
DATE:
2/6/2020
SUBTITLE: Model 3400 Amphibious Floats
REVISION
8
Figure 1.3.5
Figure 1.3.6

ISSUE DATE:
8/12/03
Incorporated
PAGE
12 of 107
TITLE: Service & Maintenance Manual
FILE NO.
A-10031
REVISION
DATE:
2/6/2020
SUBTITLE: Model 3400 Amphibious Floats
REVISION
8
1.4 Fastener Torque
Torque Value Conversion:
To convert in.-lb. to ft.-lb: Value (ft.-lb.) x 12 = Value (in-lb.)
To convert ft.-lb. to in.-lb: Value (in-lb.) x 0.0833 = Value (ft.-lb.)
1.4.1 Tooling Requirements:
Calibrated torque wrench
Adapters that affect the length of the torque wrench will affect the required torque indication and must be calculated
according to Figure 1.5.3.
1.4.2 Hardware Cleanliness:
All hardware is to be free of dirt, grit and grease. All dirty hardware shall be thoroughly cleaned and lubricated with
a dry film lubricant such as LPS 1, or Teflon products per manufacturer instructions. It is recommended that all
stainless hardware be thoroughly lubricated with anti-seize lubricant of good quality to prevent galling upon
assembly.
1.4.3 Torque Procedure
Assure that hardware is clean and properly prepared for installation. Assemble nuts to bolts, measuring the tension
required to turn the nut and add this to the required final torque. Where possible apply torque to the nut, and not to
the fastener head. Apply a smooth, even pressure, stopping and re-torqueing if chattering or premature loading
occurs. This may warrant disassembly and subsequent inspection for burrs or galling. Replace any damaged
hardware.
Access panels should be torqued only to "hand tight", the fiberglass should exhibit only mild deformation. A
portable hand drill could be used, provided that the clutch is set properly. Do not apply more pressure to the hatch
screws than is necessary to engage the tool to the fastener head as this will risk damaging the Tinnerman style nuts
below.
All other nuts shall be torqued per 1.5 Fastener Torque Values unless otherwise noted.

ISSUE DATE:
8/12/03
Incorporated
PAGE
13 of 107
TITLE: Service & Maintenance Manual
FILE NO.
A-10031
REVISION
DATE:
2/6/2020
SUBTITLE: Model 3400 Amphibious Floats
REVISION
8
1.5 Fastener Torque Values
Figure 1.5.1 Recommended Torque Values (inch-pounds) (From AC43.13-1B, Table 7-1)
(Except where otherwise noted, such as Deck Fitting bolts – see installation drawings)
Figure 1.5.2 Minimum Prevailing Torque Values for Re-used Self-Locking Nuts
(from AC43.13-1B, Table 7-2)
Self-Locking Nuts:
Self-locking nuts, when re-used, must have at
least the minimum prevailing torque listed in
figure to the left. Nuts that are smaller than those
listed in the table shall not be used if they can be
run up by hand.

ISSUE DATE:
8/12/03
Incorporated
PAGE
14 of 107
TITLE: Service & Maintenance Manual
FILE NO.
A-10031
REVISION
DATE:
2/6/2020
SUBTITLE: Model 3400 Amphibious Floats
REVISION
8
Figure 1.5.3 Torque Wrench with Various Adapters

ISSUE DATE:
8/12/03
Incorporated
PAGE
15 of 107
TITLE: Service & Maintenance Manual
FILE NO.
A-10031
REVISION
DATE:
2/6/2020
SUBTITLE: Model 3400 Amphibious Floats
REVISION
8
1.6 Fastener Use and Discretion
1.6.1 Fastener Lengths
Rivets: Where replacement or repair of rivets is required, use rivets of proper specifications only, for instance,
MS20426AD4-xxx. Lengths may be determined by measuring the thickness of the material(s) to be assembled and
adding 1.5" X Diameter of the rivet to be used. Over-sized rivets may be substituted where holes have been drilled
out.
Bolts and screws shall have a minimum of one thread visible through the nuts upon final torque.
Washers may be rearranged if necessary, to accommodate proper fit, up to two washers beneath the nut and one
beneath the fastener head. Typically, Aerocet intends to put one thin washer beneath the fastener head and one
thicker washer beneath the nut.
1.6.2 Fastener Reuse
Fasteners are to be inspected for condition, per Section 11 of this manual. Such fasteners that are acceptable may be
cleaned, re-lubricated and re-installed as determined. Self-locking nuts shall meet the minimum prevailing torque as
listed in Figure 1.5.2 Minimum Prevailing Torque Values for Re-used Self-Locking Nuts, or shall be replaced.

ISSUE DATE:
8/12/03
Incorporated
PAGE
16 of 107
TITLE: Service & Maintenance Manual
FILE NO.
A-10031
REVISION
DATE:
2/6/2020
SUBTITLE: Model 3400 Amphibious Floats
REVISION
8
This page intentionally left blank – except this line

ISSUE DATE:
8/12/03
Incorporated
PAGE
17 of 107
TITLE: Service & Maintenance Manual
FILE NO.
A-10031
REVISION
DATE:
2/6/2020
SUBTITLE: Model 3400 Amphibious Floats
REVISION
8
2Float Hull and General Maintenance
The following is a general instruction set to
2.1 Cleaning
Seaplanes operating in saltwater or brackish water should be thoroughly hosed down or flushed with fresh water
each day, including the landing gear bays.
The float’s design, which uses an all-composite structure, basically eliminates hull corrosion and leakage. The floats
should be kept clean with biodegradable soap and water. The sides and the bottoms from the step aft can be waxed
to help in the cleaning process. The bottoms of the floats from the step forward should not be waxed, as this gives
unpredictable water performance. Stains from the waterline down may be removed using marine fiberglass stain
remover. FSR (Fiberglass Stain Remover), manufactured by Davis, is recommended. Do not use abrasive cleaners
or pads—these will scratch the white gel-coat surface. The gel-coat color surface should always be maintained on
the floats for ultraviolet radiation protection.
Properly bathing a saltwater-operated seaplane immediately after EVERY day of saltwater operation is critical to
maintaining the aircraft. Failure to do so can result in severe corrosion. Different bodies of saltwater with their
varying salt concentration, air temperature, and humidity of the operating environment play a significant role in
determining how badly the aircraft may corrode if salt removal and corrosion prevention practices are not followed.
High salt content, high temperatures, and high humidity are the most corrosive conditions.
Be aware of the quality of the fresh water supply. It may be advisable to test your water supply for acidity/alkalinity
and dissolved solids. It is recommended that water have a pH between 6.5 and 7.5, and less than 200 parts per
million dissolved solids. If you practice a strict bathing routine but continue to note abnormal corrosion, the quality
of water may be a problem.
Use of a product like Salt-Away®in accordance with manufacturer’s instructions and provided in part further in this
section will prove helpful in removing fresh salt and help with removing some of the old as well. This is a
water-based compound specifically designed for this purpose. It is distributed Internationally, and application
devices are readily available as well.
Pressure washers are not recommended for salt removal. They tend to push salt around the aircraft surface, rather
than to dissolve the salt and let it sheet off of the aircraft. The high pressures can deposit salt into areas of the
aircraft that are not normally salted during aircraft landings and takeoffs. The goal is to use high flow, but low
pressure, gravity-flow of freshwater to sheet water off of the aircraft. Use a high-quality adjustable hose nozzle, and
wide bore hose, that can put a large volume of water on the aircraft without blasting salt and soap into cracks and
crevices.
Brushing of the belly, sides, and tail with a soft bristle brush on a 6-foot (2-meter) pole is advised. There tends to be
more salt on the aft and lower portions of the aircraft, but in some conditions, many other areas of the aircraft can
become salted.
WARNING:
DO NOT SPRAY WATER INTO INTRUMENTATION ORIFICES. This will render them ineffective or cause
damage.Refer to aircraft Maintenance Manual and use prescribed processes.
NOTE:
Applying rinse water in a methodical, front to back, top down manner is intended to avoid forcing contaminates
and salt into skin seams and overlaps, while maintaining the most efficient and complete coverages, and
gravity-driven sheeting action.

ISSUE DATE:
8/12/03
Incorporated
PAGE
18 of 107
TITLE: Service & Maintenance Manual
FILE NO.
A-10031
REVISION
DATE:
2/6/2020
SUBTITLE: Model 3400 Amphibious Floats
REVISION
8
Soap can be used during the bathing process, particularly for removing oils. Zep Aviation Aircraft Cleaner II, part
number R50335, is a proven product for this purpose. Follow the manufacturer’s instructions and reduce the
recommended amount of soap by as much as 50% if there is very little or no oily residue on the aircraft. Check the
belly for oil before preparing soap concentrations. Soap can cause corrosion the same as saltwater and must be
rinsed quickly and thoroughly just like the salt.
If washing in direct sunlight, it may be advisable to wash in sections. Do not allow soap to dry on the aircraft, or it
will become difficult to remove.
2.2 Bathing Procedure for Aerocet 3400 Amphibian Floats Installations
Remove any fairings that cover float gear at least once per week during bathing, or any time the aircraft will sit un-
used for more than a week.
Prepare a 5-gallon (20 liter) bucket with soapy water as described above.
Assure plenty of hose length to reach all sides of the aircraft. Using a tall ladder as needed, thoroughly rinse the
aircraft from the top down, from front to back. Make the water sheet down the aircraft: Do not blast the aircraft so
that water bounces off of it. The water should stick and flow down the surfaces.
Using a pole brush, apply soap working from top to bottom, front to back, scrub the sides and rinse, leaving the most
oily, soiled portions of the aircraft for last. It only takes a small amount of agitation to remove the salt that remains
after a good rinsing. Prolonged scrubbing is not needed. Avoid scrubbing metallic items that are coated with
preservative oils, such as float hardware. Rinse thoroughly. Do not allow soap to dry on surfaces.
Scrub the horizontal stabilizer and the vertical stabilizer. Rinse thoroughly.
Scrub and rinse the belly last. If it is oily it may take more scrubbing than the sides. Agitate the soapy water in the
bucket with the brush often to clean off the brush. Change the water as often as may be necessary. It is
recommended to change water between baths when washing multiple aircraft.
If the strut fairings have been removed, the unpainted metallic parts underneath will need rinsing. Take care not to
blast water into the aircraft fuselage. Scrubbing is not recommended where heavily coated with grease and other
preservative oils.
Wash out the back side of the main gear bulkhead. There is a deflector shield that is intended to keep rocks and
debris out of the keel cavity in that area. As the floats may be beached backwards during operations, it is important
to remove any clay, sand or rocks that might remain. If water does not freely flush through the opening, then lift and
secure the floats, retract the gear and disassemble the deflector shield to allow removal of collected debris.
Thoroughly rinse all soap starting at the top and working downward and front to back, including the float landing
gear.
WARNING:
DO NOT SPRAY WATER INTO INTRUMENTATION ORIFICES. This will render them ineffective or will
damage them. Refer to aircraft Maintenance Manual and use prescribed processes.

ISSUE DATE:
8/12/03
Incorporated
PAGE
19 of 107
TITLE: Service & Maintenance Manual
FILE NO.
A-10031
REVISION
DATE:
2/6/2020
SUBTITLE: Model 3400 Amphibious Floats
REVISION
8
2.3 Salt Removal
We recommend the regular use of Salt-Away®to emulsify and remove salt deposits when operating in a marine
environment. This inexpensive product is readily available from marine suppliers and internet vendors
internationally, and it is considered safe to use in wide variety of environments.It is not a soap. It contains
proprietary ingredients to safely remove salt and some ingredients to inhibit corrosion. Except in areas of salt
accumulation, results are immediate. Salt accumulation can be broken apart by regular, frequent applications and
leaving the product in the accumulated areas. Corrosion inhibitors are active on inaccessible surfaces that stay wet.
Water-based Salt-Away®is not a coating and does not bond to surfaces. Highly concentrated; it must be diluted.
Retailers that sell Salt-Away®may offer a kit that includes a hose dispenser, similar to a garden sprayer. The mix
ratio starts more highly concentrated and gradually dilutes as the mix is used. The following methods of using
Salt-Away®are derived from the manufacturer’s instructions. Please consult with Salt-Away directly for more
specific applications and uses.
Immersion: Immersing items in a bath of a Salt-Away®solution is accomplished by dipping the item into the
solution until completely covered by the liquid. Removing it allows gravity to cause the liquid containing the
dissolved salt to flow off the surfaces. Unless there is salt accumulation on the surface, there is no need to soak the
item in the solution. The length of time to allow the item to soak in the Salt-Away®solution to break apart salt
accumulation depends on the amount of accumulation. Re-using the same solution is not recommended. The
recommended dilution ratios for an immersion solution with fresh water can range from 1.5% to 5.0% by volume.
A richer solution greater than 10.0% by volume is not recommended. Rinsing the item with fresh water after the
immersion process is required.
Application by pressure methods: There are 2 conditions necessary for Salt-Away®to remove salt: 1) the pressure
and velocity of the water source must be consistent and great enough for gravity to cause flow; and 2) complete and
thorough flowing of the solution to the exit areas of the surface must occur. Except for salt accumulation areas,
results are immediate. If conditions 1 and 2 do not exist, the Salt-Away solution will dissolve the salt, but the salt
will remain on the surface.
Vertical Surface: Upon application to the surface to be treated, the Salt-Away®solution immediately dissolves any
soluble contaminant. If the pressure is not strong enough to cause complete flow from the surface, the solution will
dissolve the soluble contaminants, the flowing will begin, then slow to a drizzle, and eventually stop before reaching
the removal area. If this situation occurs, the salt is not removed.
Horizontal Surface: The method for removal is more difficult but can be accomplished by "pushing" the dissolved
contaminants with pressurized spray or stream velocity of the Salt-Away solution until they are pushed off the
surface to some other location.
Horizontal Surface, No Outlet: Example: salt-contaminated floors where there is no drain. Pressure is not
necessary to apply the Salt-Away®solution, and the recommended solution is 5.0% Salt-Away®by volume. The
best equipment to use to apply the solution is a compression pump sprayer. The area must be covered with enough
solution to cause standing liquid. If the surface is porous, continue to add solution until it is saturated, and a
standing liquid condition exists. Allow the solution to stand at least 10 minutes, but do not allow it to evaporate.
Salt removal must be accomplished by vacuuming all the standing liquid. The most commonly used vacuum device
is known as a "wet-vacuum machine". Since it is not physically possible to vacuum 100% of the moisture from the
surface, any dissolved salt residing in the remaining moisture will not be removed. This process may need to be
repeated several times depending on porosity and condition of the surface. Do not apply with mop, sponge, or rag as
this will simply transfer salt to other locations. Remove with wet-vacuum machine. Repeat application.

ISSUE DATE:
8/12/03
Incorporated
PAGE
20 of 107
TITLE: Service & Maintenance Manual
FILE NO.
A-10031
REVISION
DATE:
2/6/2020
SUBTITLE: Model 3400 Amphibious Floats
REVISION
8
2.4 Corrosion Preventatives water-displacing oils (ACF 50®)
Water-displacing, corrosion inhibiting oils like ACF 50®have proven themselves very reliably in marine
environments. If the product evaporates or is removed, then it becomes ineffective, so it is important to develop a
continuing regimen in which it is periodically reapplied when and where necessary. Areas of heat, humidity and salt
are extremely prone to corrosion, while generally drier areas might not require as much attention over time.
These products are commonly available through aviation retailers in pails, sprays or bottles.
Some less accessible areas of the seaplane or amphibian may be easier to apply in a fog. “ACF 50®” may be fogged
into areas using a compressed air, venturi type spray gun. It can also be sprayed directly onto the area needing
protection. The advantage of the fog system is that tiny airborne particles of the oil will stay airborne and continue
to apply and migrate several hours after spraying. The system consists of a compressed air supply, spray gun, pick-
up tube, and product container. Air pressure between 60-120 psi is needed to properly atomize the liquid.
Open the forward and middle hatches of both floats which are secured by screws. Check hydraulic lines and fittings
for cleanliness, leaks and corrosion. Liberally fog/spray all four of these compartments with ACF 50®, and
immediately screw down the hatches. Take care while closing the middle hatches to place the float pump pickup
tube in its retainer at the bottom of the compartment. The fog of oil will float in the air, coating parts and displacing
water.
The mechanic should address the strut fairings area at this time. Inspect for heavy salt deposits that do not rinse
away and remove as needed. Inspect for corrosion. If corrosion is apparent, let the area dry of water. Remove
preservative oil on affected areas with an appropriate solvent, treat the corrosion per standard practices, and reapply
grease (AGC-2 aluminum complex grease works well) over all the hardware that is normally covered by the
fairings. Spray directly with ACF 50®. Generally, heavier greases should be applied before the lighter oils.
Reinstall the fairings and wipe off any excess oil or grease.
Float nose gear slide box assembly should be fogged or sprayed liberally with ACF 50®or equivalent. Slide tracks
should be wiped free of any wet lubricant, however, and then lubricated with a PTFE dry-film lubricant. (See
Products Listing)
Main landing gear truck may be fogged internally using provided holes. Remaining landing gear may be treated
externally.
NOTE:
Avoid treating zinc anodes. If oil is applied to them, then remove all residue with solvent.
(See Section 8 Anodic Systems)
Table of contents
Other AEROCET Aircraft manuals
Popular Aircraft manuals by other brands
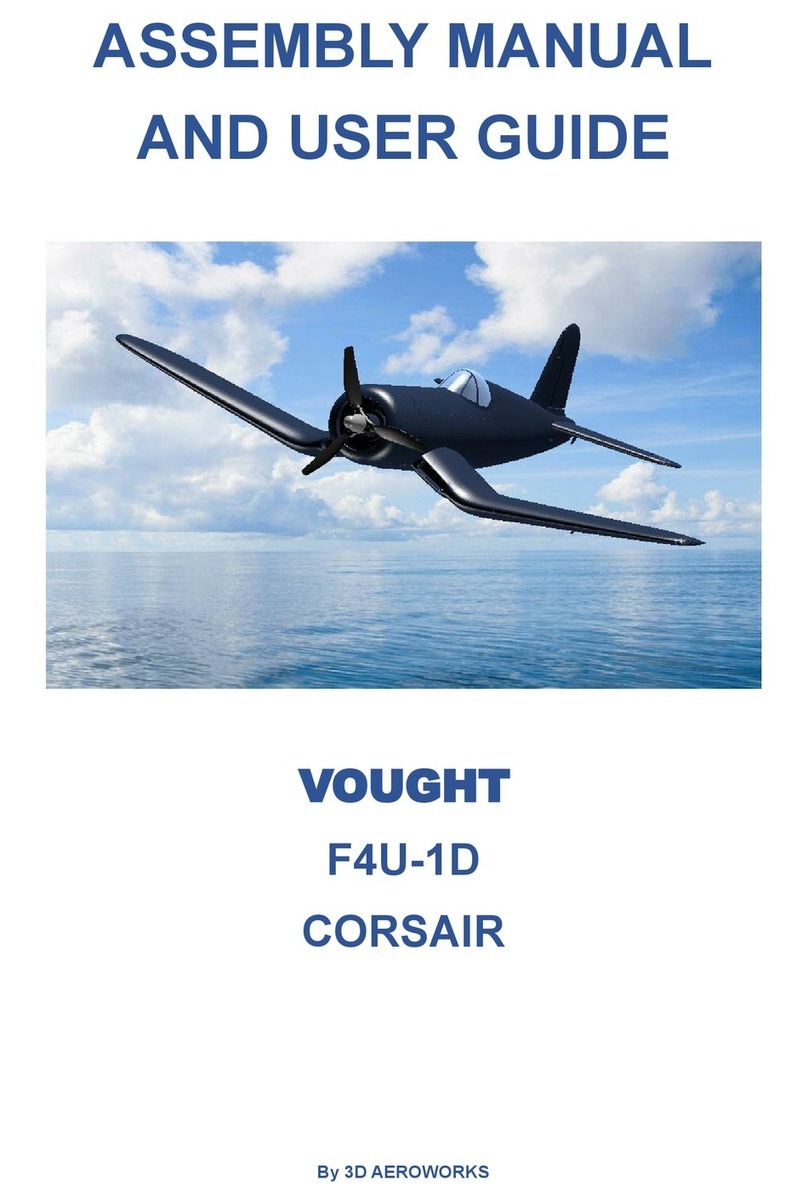
3D AEROWORKS
3D AEROWORKS VOUGHT F4U-1D CORSAIR Assembly manual and user guide
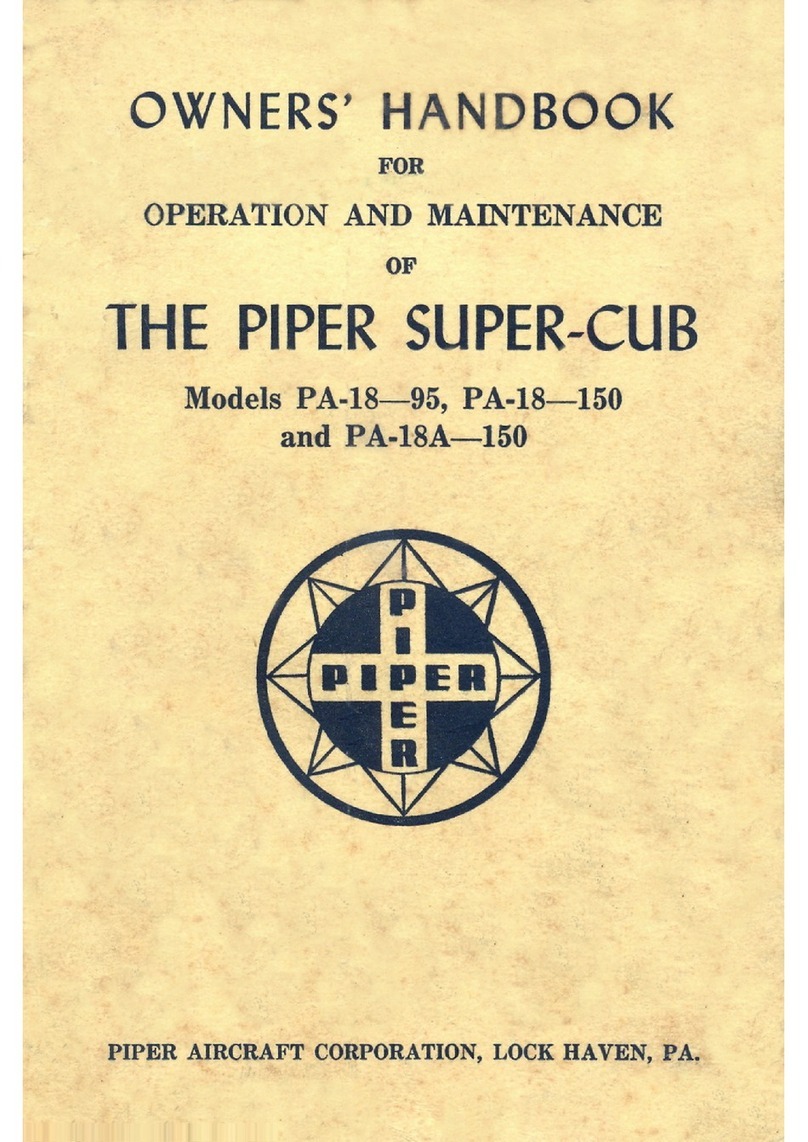
Piper
Piper Super-Cub PA-18A-150 Operation and maintenance

Gin
Gin Bolero 7 user manual
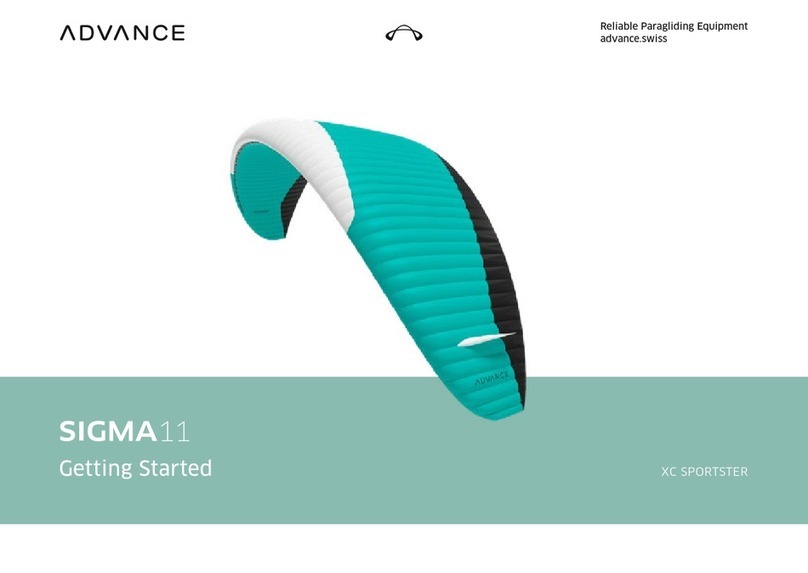
Advance acoustic
Advance acoustic SIGMA11 Getting started

Aeros
Aeros Aeros-2 Service manual
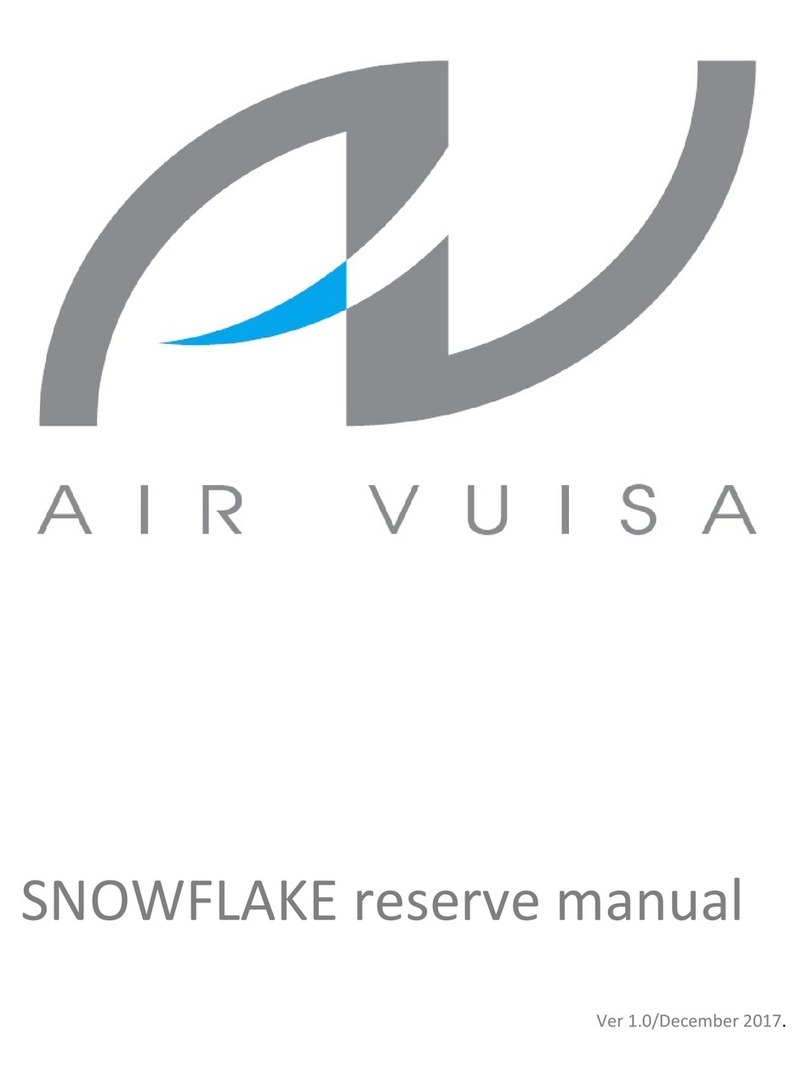
Air Vuisa
Air Vuisa SNOWFLAKE reserve series manual