Aerotech ARMS Series User manual

Revision: 1.03.00
ARMS Series Stage Hardware
Manual

Global Technical Support
Go to www.aerotech.com/global-technical-support for information and support about your Aerotech products. The website
provides downloadable resources (such as up-to-date software, product manuals, and Help files), training schedules, and
PC-to-PC remote technical support. You can also complete Product Return (RMA) forms and get information about repairs
and spare or replacement parts. For immediate help, contact a service office or your sales representative. Have your
customer order number available before you call or include it in your email.
United States (World Headquarters)
Phone: +1-412-967-6440
Fax: +1-412-967-6870
Email: service@aerotech.com
101 Zeta Drive
Pittsburgh, PA 15238-2811
www.aerotech.com
United Kingdom Japan
Phone: +44 (0)1256 855055
Fax: +44 (0)1256 855649
Email: service@aerotech.co.uk
Phone: +81 (0)50 5830 6814
Fax: +81 (0)43 306 3773
Email: service@aerotechkk.co.jp
Germany China
Phone: +49 (0)911 967 9370
Fax: +49 (0)911 967 93720
Email: service@aerotechgmbh.de
Phone: +86 (21) 5508 6731
Email: service@aerotech.com
France Taiwan
Phone: +33 2 37 21 87 65
Email: service@aerotech.co.uk
Phone: +886 (0)2 8751 6690
Email: service@aerotech.tw
This manual contains proprietary information and may not be reproduced, disclosed, or used in whole or in part without the
express written permission of Aerotech, Inc. Product names mentioned herein are used for identification purposes only and
may be trademarks of their respective companies.
Copyright © 2008-2018, Aerotech, Inc., All rights reserved.

ARMS Hardware Manual Table of Contents
Table of Contents
ARMS Series Stage Hardware Manual 1
Table of Contents 3
List of Figures 4
List of Tables 5
Safety Procedures and Warnings 6
EU Declaration of Incorporation 7
Chapter 1: Overview 9
1.1. Environmental Specifications 10
1.2. Accuracy and Temperature Effects 10
1.3. Basic Specifications 11
1.4. Vacuum Operation 14
Chapter 2: Mechanical Specifications and Installation 15
2.1. Unpacking and Handling the Stage 15
2.2. Dimensions 16
2.3. Securing the Stage to the Mounting Surface 25
2.4. Attaching the Payload to the Stage 27
Chapter 3: Electrical Specifications and Installation 29
3.1. Motor and Feedback Connectors 30
3.2. Motor and Feedback Wiring 32
3.3. Motor and Feedback Specifications 33
3.4. Marker and Machine Direction 37
3.5. Motor and Feedback Phasing 38
Chapter 4: Maintenance 41
4.1. Service and Inspection Schedule 41
4.2. Cleaning and Lubrication 41
4.3. Troubleshooting 42
Appendix A: Warranty and Field Service 43
Appendix B: Revision History 45
Index 47
www.aerotech.com 3

Table of Contents ARMS Hardware Manual
List of Figures
Figure 2-1: ARMS150 Dimensions (-TT1, -TT2, -TT3, -TT4) 16
Figure 2-2: ARMS150 Dimensions (-TT5, -TT6, -TT7, -TT8) 17
Figure 2-3: Mounting Pedestal Dimensions for the ARMS150 (-HDP) 18
Figure 2-4: ARMS200 Dimensions (-TT1, -TT2, -TT3, -TT4) 19
Figure 2-5: ARMS200 Dimensions (-TT5, -TT6, -TT7, -TT8) 20
Figure 2-6: Mounting Pedestal Dimensions for the ARMS200 (-HDP) 21
Figure 2-7: ARMS260 Dimensions (-TT1, -TT2, -TT3, -TT4) 22
Figure 2-8: ARMS260 Dimensions (-TT5, -TT6, -TT7, -TT8) 23
Figure 2-9: Mounting Pedestal Dimensions for the ARMS260 (-HDP) 24
Figure 2-10: Standard Mounting Holes 26
Figure 2-11: Side Mount Mounting Holes 26
Figure 2-12: Load Orientation 27
Figure 2-13: ARMS Cantilevered Load Capability 28
Figure 3-1: Motor and Feedback Wiring 32
Figure 3-2: Machine Direction 37
Figure 3-3: Hall Phasing 38
Figure 3-4: Analog Encoder Phasing Reference Diagram 39
4 www.aerotech.com

ARMS Hardware Manual Table of Contents
List of Tables
Table 1-1: Model Numbers and Options 9
Table 1-2: Environmental Specifications 10
Table 1-3: ARMS150 Series Specifications 11
Table 1-4: ARMS200 Series Specifications 12
Table 1-5: ARMS260 Series Specifications 13
Table 2-1: Stage to Mounting Surface Hardware 25
Table 3-1: Motor Wiring Connector 30
Table 3-2: Feedback Connector 31
Table 3-3: Feedback Specifications 33
Table 3-4: S-130 Motor Specifications (for ARMS150) 34
Table 3-5: S-180 Motor Specifications (for ARMS200) 35
Table 3-6: S-240 Motor Specifications (for ARMS260) 36
Table 3-7: Encoder Specifications 36
Table 4-1: Troubleshooting 42
www.aerotech.com 5

Table of Contents ARMS Hardware Manual
Safety Procedures and Warnings
Read this manual in its entirety before installing, operating, or servicing this product. If you do not understand
the information contained herein, contact an Aerotech representative before proceeding. Strictly adhere to
the statements given in this section and other handling, use, and operational information given throughout
the manual to avoid injury to you and damage to the equipment.
The following statements apply wherever the Warning or Danger symbol appears within this manual. Failure
to observe these precautions could result in serious injury to those individuals performing the procedures
and/or damage to the equipment.
D A N G E R : This product contains potentially lethal voltages. To reduce the possibility of
electrical shock, bodily injury, or death the following precautions must be followed.
1. Access to the ARMS and component parts must be restricted while connected to a power
source.
2. Do not connect or disconnect any electrical components or connecting cables while
connected to a power source.
3. Disconnect electrical power before servicing equipment.
4. All components must be properly grounded in accordance with local electrical safety
requirements.
5. Operator safeguarding requirements must be addressed during final integration of the
product.
W A R N I N G : To minimize the possibility of electrical shock, bodily injury or death the
following precautions must be followed.
1. Moving parts can cause crushing or shearing injuries. Access to all stage and motor parts
must be restricted while connected to a power source.
2. Cables can pose a tripping hazard. Securely mount and position all system cables to avoid
potential hazards.
3. Do not expose this product to environments or conditions outside of the listed
specifications. Exceeding environmental or operating specifications can cause damage to
the equipment.
4. The ARMS stage must be mounted securely. Improper mounting can result in injury and
damage to the equipment.
5. Use care when moving the ARMS stage. Lifting or transporting the ARMS stage improperly
can result in injury or damage to the ARMS.
6. This product is intended for light industrial manufacturing or laboratory use. Use of this
product for unintended applications can result in injury and damage to the equipment.
7. If the product is used in a manner not specified by the manufacturer, the protection provided
by the product can be impaired and result in damage, shock, injury, or death.
8. Operators must be trained before operating this equipment.
9. All service and maintenance must be performed by qualified personnel.
N O T E : Aerotech continually improves its product offerings; listed options may be superseded at any
time. All drawings and illustrations are for reference only and were complete and accurate as of this
manual’s release. Refer to www.aerotech.com for the most up-to-date information.
6 www.aerotech.com

ARMS Hardware Manual Table of Contents
EU Declaration of Incorporation
Manufacturer: Aerotech, Inc.
101 Zeta Drive
Pittsburgh, PA 15238-2811
USA
herewith declares that the product:
Aerotech, Inc. ARMS Rotary Stage
is intended to be incorporated into machinery to constitute machinery covered by the Directive 2006/42/EC
as amended;and that the following harmonized European standards have been applied:
EN ISO 12100:2010
Safety of machinery - Basic concepts, general principles for design
EN 60204-1:2010
Safety of machinery - Electrical equipment of machines - Part 1:General requirements
and further more declares that
it is not allowed to put the equipment into service until the machinery into which it is to be
incorporated or of which it is to be a component has been found and declared to be in con-
formity with the provisions of the Directive 2006/42/EC and with national implementing
legislation, i.e., as a whole, including the equipment referred to in this Declaration.
This is to certify that the aforementioned product is in accordance with the applicable requirements of the fol-
lowing Directive(s):
2011/65/EU RoHS2 Directive
Authorized Representative:
Simon Smith, European Director
Address:
Aerotech Ltd
The Old Brick Kiln, Ramsdell, Tadley
Hampshire RG26 5PR
UK
Name
/ Alex Weibel
Position
Engineer Verifying Compliance
Location
Pittsburgh, PA
Date
10/23/2018
www.aerotech.com 7

Table of Contents ARMS Hardware Manual
8 www.aerotech.com
This page intentionally left blank.

ARMS Hardware Manual Overview
Chapter 1: Overview
N O T E : Aerotech continually improves its product offerings; listed options may be superseded at any
time. All drawings and illustrations are for reference only and were complete and accurate as of this
manual’s release. Refer to www.aerotech.com for the most up-to-date information.
Table 1-1: Model Numbers and Options
ARMS Series Rotary Motion Simulator
ARMS150 Rotary motion simulator
ARMS200 Rotary motion simulator
ARMS260 Rotary motion simulator
Tabletop (Required)
-TT1 Metric dimension mounting, engraved scale
-TT2 English dimension mounting, engraved scale
-TT3 Aperture, metric dimension mounting, engraved scale
-TT4 Aperture, English dimension mounting, engraved scale
-TT5 Large diameter tabletop with metric dimension mounting
-TT6 Large diameter tabletop with English dimension mounting
-TT7 Large diameter tabletop, aperture, metric dimension mounting
-TT8 Large diameter tabletop, aperture, English dimension mounting
Motor (Required)
-M1 Direct-drive brushless, slotless motor, standard torque
-M2 Direct-drive brushless, slotless motor, high torque
Integrated Slip-Ring (Required)
-SR01 (1) 12 lines, 2A max current (ARMS150 and ARMS200 only)
-SR02 (1) 24 lines, 2A max current
-SR03 (1,3) 36 lines, 2A max current (ARMS200 only)
-SR04 (1) 48 lines, 2A max current (ARMS260 only)
-SR05 (1,3) 56 lines, 2A max current (ARMS200 only)
-SR06 (1) 72 lines, 2A max current (ARMS260 only)
-SR07 (1) 96 lines, 2A max current (ARMS260 only)
-SR08 (2,3) Low-noise, 12 lines, 1A max current (ARMS150 and ARMS200 only)
-SR09 (2,3) Low-noise, 24 lines, 1A max current with ARMS150 and ARMS200;
2A max current with ARMS260
-SR10 (2,3) Low-noise, 30 lines, 1A max current (ARMS200 only)
-SR11 (2,3) Low-noise, 48 lines, 2A max current (ARMS260 only)
-SR12 (2,3) Low-noise, 70 lines, 2A max current (ARMS260 only)
-SR13 (2,3) Low-noise, 90 lines, 2A max current (ARMS260 only)
(1) Noise Specification:<60 mOhms variation
(2) Noise Specification:<10 mOhms variation
(3)These options are incompatible with all aperture tabletop options (-TT3, -TT4, -TT7, -TT8).
Rotary Union (Optional)
-RU1 One (1) rotary union line for air, vacuum, or non-corrosive gas, 120 psi max
-RU2 Two (2) rotary union lines for air, vacuum, or non-corrosive gas, 120 psi max
NOTE: Rotary union options are incompatible with all aperture tabletop options (-TT3, -TT4, -TT7, -TT8). Rotary unions for
carrying liquids will require customized design, potentially resulting in dimensional changes to the ARMS product.
Mounting Pedestal (Optional)
-HDP Mounting pedestal with adjustable, hard-mount capable leveling feet
www.aerotech.com Chapter 1 9

Overview ARMS Hardware Manual
1.1. Environmental Specifications
W A R N I N G : Do not expose this product to environments or conditions outside of the listed
specifications. Exceeding environmental or operating specifications can cause damage to the
equipment.
Table 1-2: Environmental Specifications
Ambient
Temperature
Operating: 10° to 35° C (50° to 95° F)
The optimal operating temperature is 20° C ±2° C (68° F ±4° F). If at any time the
operating temperature deviates from 20° C, degradation in performance could occur.
Storage: 0° to 40° C (32° to 104° F) in original shipping packaging
Humidity Operating: 20% to 60% RH
Storage: 10% to 70% RH, non-condensing in original packaging.
Altitude Operating: 0 m to 2,000 m (0 ft to 6,562 ft) above sea level
Contact Aerotech if your specific application involves use above 2,000 m or below sea
level.
Vibration Use the system in a low vibration environment. Excessive floor or acoustical vibration
can affect system performance. Contact Aerotech for information regarding your spe-
cific application.
Protection
Rating
The ARMS stages are not suited for dusty or wet environments. This equates to an
ingress protection rating of IP30.
Use Indoor use only
1.2. Accuracy and Temperature Effects
Extreme temperature changes could cause a decrease in performance or permanent damage to the stage.
Aerotech stages are designed for and built in a 20°C (68°F) environment. Any deviation from standard
operating temperature will affect stage accuracy. The severity of temperature effects on all stage
specifications depends on many different environmental conditions, including how the stage is mounted.
Contact the factory for more details.
10 Chapter 1 www.aerotech.com

ARMS Hardware Manual Overview
1.3. Basic Specifications
N O T E : Aerotech continually improves its product offerings; listed options may be superseded at any
time. All drawings and illustrations are for reference only and were complete and accurate as of this
manual’s release. Refer to www.aerotech.com for the most up-to-date information.
Table 1-3: ARMS150 Series Specifications
ARMS Series ARMS150-M1 ARMS150-M2
Width 146 mm
Height (1) 183 mm 246 mm
Aperture(2) 8 mm
Total Travel ±360° Continuous
Motor S-130-39-A S-130-102-A
Bus Voltage Up to 340 VDC
Maximum Torque (Continuous) 2.36 N·m 7.69 N·m
Fundamental Encoder Resolution 16,200 lines/rev
Accuracy (calibrated) (3) ±2.5 arc-sec
Repeatability ±0.5 arc-sec
Max Load (4) Axial 30 kg
Moment 175 N·m
Tilt Error Motion ±1 arc-sec
Maximum Rate (5) 1500°/s
Minimum Rate (6) 0.002°/s
Rate Resolution (6) 0.002°/s
Rate Stability (6)
Over 360° 0.0001%
Over 10° 0.005%
Over 1° 0.05%
Peak Acceleration (7) >20,000°/s2
Inertia (unloaded) (7) 6,600 kg·mm29,700 kg·mm2
Total Mass (7) 9 kg 15 kg
Servo Bandwidth (8) > 70 Hz (-3 dB)
Material Aluminum
Stage Finish Black Anodize
Tabletop Finish Hard Coating (62 Rockwell Hardness)
1. Height may vary with certain slip ring and rotary union options (refer to for more details).
2. Aperture not available with allslip ring and rotary union options (refer to Table 1-1 for more details).
3. Certified with each stage. Requires the use of an Aerotech controller.
4. Maximum loads are mutually exclusive.
5. Maximum rate is based on stage capability. Actual rate may depend on encoder resolution, load, amplifier bus voltage, and motor
(refer to the S-series rotary motor (P/N:EDU166)for more information.
6. Minimum rate, rate resolution, and rate accuracy are based on stage capability. Actual rate, resolution, and accuracy may depend
on encoder resolution.
7. Peak acceleration, inertia, and total mass based on unloaded stage with standard diameter tabletop.
8. Servo bandwidth is based on unloaded stage with standard diameter tabletop. Actual bandwidth may depend on mass and inertia
of stage payload.
www.aerotech.com Chapter 1 11

Overview ARMS Hardware Manual
Table 1-4: ARMS200 Series Specifications
ARMS Series ARMS200-M1 ARMS200-M2
Width 196 mm
Height (1) 224 mm 249 mm
Aperture(2) 8 mm
Total Travel ±360° Continuous
Motor S-180-69-A S-180-94-A
Bus Voltage Up to 340 VDC
Maximum Torque (Continuous) 11.12 N·m 15.93 N·m
Fundamental Encoder Resolution 23,600 lines/rev
Accuracy (calibrated) (3) ±2.5 arc·sec
Repeatability ±0.5 arc·sec
Max Load (4) Axial 140 kg
Moment 425 N·m
Tilt Error Motion ±1 arc·sec
Maximum Rate (5) 1500°/s
Minimum Rate (6) 0.002°/s
Rate Resolution (6) 0.002°/s
Rate Stability (6)
Over 360° 0.0001%
Over 10° 0.005%
Over 1° 0.05%
Peak Acceleration (7) >20,000°/s2
Inertia (unloaded) (7) 33,600 kg·mm239,800 kg·mm2
Total Mass (7) 22 kg 26 kg
Servo Bandwidth (8) > 70 Hz (-3 dB)
Material Aluminum
Stage Finish Black Anodize
Tabletop Finish Hard Coating (62 Rockwell Hardness)
1. Height may vary with certain slip ring and rotary union options (refer to for more details).
2. Aperture not available with allslip ring and rotary union options (refer to Table 1-1 for more details).
3. Certified with each stage. Requires the use of an Aerotech controller.
4. Maximum loads are mutually exclusive.
5. Maximum rate is based on stage capability. Actual rate may depend on encoder resolution, load, amplifier bus voltage, and motor
(refer to the S-series rotary motor (P/N:EDU166)for more information.
6. Minimum rate, rate resolution, and rate accuracy are based on stage capability. Actual rate, resolution, and accuracy may depend
on encoder resolution.
7. Peak acceleration, inertia, and total mass based on unloaded stage with standard diameter tabletop.
8. Servo bandwidth is based on unloaded stage with standard diameter tabletop. Actual bandwidth may depend on mass and inertia
of stage payload.
12 Chapter 1 www.aerotech.com

ARMS Hardware Manual Overview
Table 1-5: ARMS260 Series Specifications
ARMS Series ARMS260-M1 ARMS260-M2
Width 260 mm
Height (1) 229 mm 250 mm
Aperture(2) 25 mm
Total Travel ±360° Continuous
Motor S-240-63-A S-240-83-A
Bus Voltage Up to 340 VDC
Maximum Torque (Continuous) 19.71 N·m 29.09 N·m
Fundamental Encoder Resolution 32,400 lines/rev
Accuracy (calibrated) (3) ±2.5 arc·sec
Repeatability ±0.5 arc·sec
Max Load (4) Axial 230 kg
Moment 650 N·m
Tilt Error Motion ±1 arc-sec
Maximum Rate (5) 1500°/s
Minimum Rate (6) 0.001°/s
Rate Resolution (6) 0.001°/s
Rate Stability (6)
Over 360° 0.0001%
Over 10° 0.005%
Over 1° 0.05%
Peak Acceleration (7) >20,000°/s2
Inertia (unloaded) (7) 115,200 kg·mm2139,000 kg·mm2
Total Mass (7) 39 kg 44 kg
Servo Bandwidth (8) > 70 Hz (-3 dB)
Material Aluminum
Stage Finish Black Anodize
Tabletop Finish Hard Coating (62 Rockwell Hardness)
1. Height may vary with certain slip ring and rotary union options (refer to for more details).
2. Aperture not available with allslip ring and rotary union options (refer to Table 1-1 for more details).
3. Certified with each stage. Requires the use of an Aerotech controller.
4. Maximum loads are mutually exclusive.
5. Maximum rate is based on stage capability. Actual rate may depend on encoder resolution, load, amplifier bus voltage, and motor
(refer to the S-series rotary motor (P/N:EDU166)for more information.
6. Minimum rate, rate resolution, and rate accuracy are based on stage capability. Actual rate, resolution, and accuracy may depend
on encoder resolution.
7. Peak acceleration, inertia, and total mass based on unloaded stage with standard diameter tabletop.
8. Servo bandwidth is based on unloaded stage with standard diameter tabletop. Actual bandwidth may depend on mass and inertia
of stage payload.
www.aerotech.com Chapter 1 13

Overview ARMS Hardware Manual
1.4. Vacuum Operation
Contact the factory for information regarding operation in a vacuum environment.
14 Chapter 1 www.aerotech.com

ARMS Hardware Manual Installation
Chapter 2: Mechanical Specifications and Installation
W A R N I N G : ARMS installation must be in accordance to instructions provided by this
manual and any accompanying documentation. Failure to follow these instructions could result
in injury or damage to the equipment.
2.1. Unpacking and Handling the Stage
D A N G E R / H E A V Y : It is the customer's responsibility to safely and carefully lift and move
the ARMS.
lLift only by the base.
lDo not use the tabletop or cables as lifting points.
lSecure all moving parts before lifting or moving the ARMS to a new location. Unsecured
moving parts could shift and cause bodily injury.
lImproper handling could adversely affect the performance of the ARMS. Use care when
moving the ARMS
Carefully remove the ARMSfrom its protective shipping container. Gently set the ARMS on a smooth, flat,
and clean surface.
Before operating the ARMS, it is important to let it stabilize at room temperature for at least 12 hours.
Allowing it to stabilize to room temperature will ensure that all of the alignments, preloads, and tolerances are
the same as they were when tested at Aerotech. Use compressed nitrogen or clean, dry, oil-less air to
remove any dust or debris that has collected during shipping.
Each ARMS has a label listing the system part number and serial number. These numbers contain
information necessary for maintaining or updating system hardware and software. Locate this label and
record the information for later reference.
N O T E : If any damage has occurred during shipping, report it immediately.
www.aerotech.com Chapter 2 15

Installation ARMS Hardware Manual
2.2. Dimensions
Figure 2-1: ARMS150 Dimensions (-TT1, -TT2, -TT3, -TT4)
16 Chapter 2 www.aerotech.com

ARMS Hardware Manual Installation
Figure 2-2: ARMS150 Dimensions (-TT5, -TT6, -TT7, -TT8)
www.aerotech.com Chapter 2 17

Installation ARMS Hardware Manual
Figure 2-3: Mounting Pedestal Dimensions for the ARMS150 (-HDP)
18 Chapter 2 www.aerotech.com

ARMS Hardware Manual Installation
Figure 2-4: ARMS200 Dimensions (-TT1, -TT2, -TT3, -TT4)
www.aerotech.com Chapter 2 19

Installation ARMS Hardware Manual
Figure 2-5: ARMS200 Dimensions (-TT5, -TT6, -TT7, -TT8)
20 Chapter 2 www.aerotech.com
This manual suits for next models
6
Table of contents
Other Aerotech Control Unit manuals
Popular Control Unit manuals by other brands
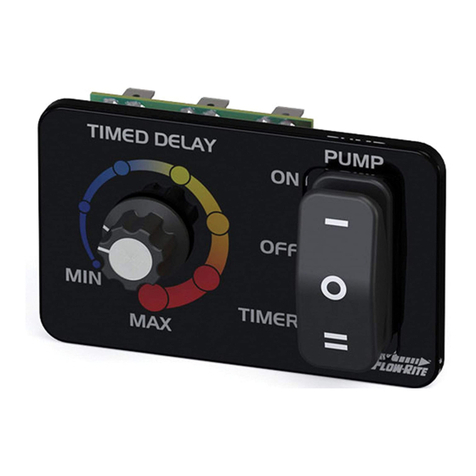
Flow-Rite
Flow-Rite ProTimer Installation and operation instructions
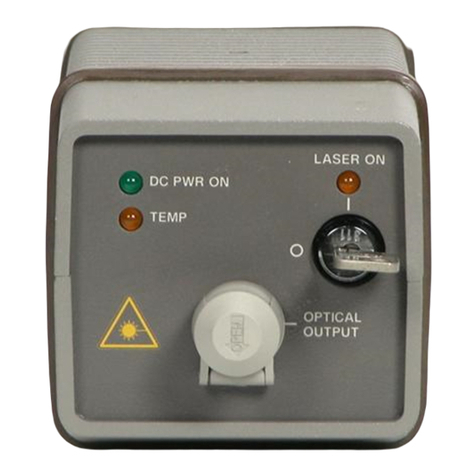
Agilent Technologies
Agilent Technologies 83400 Series user guide
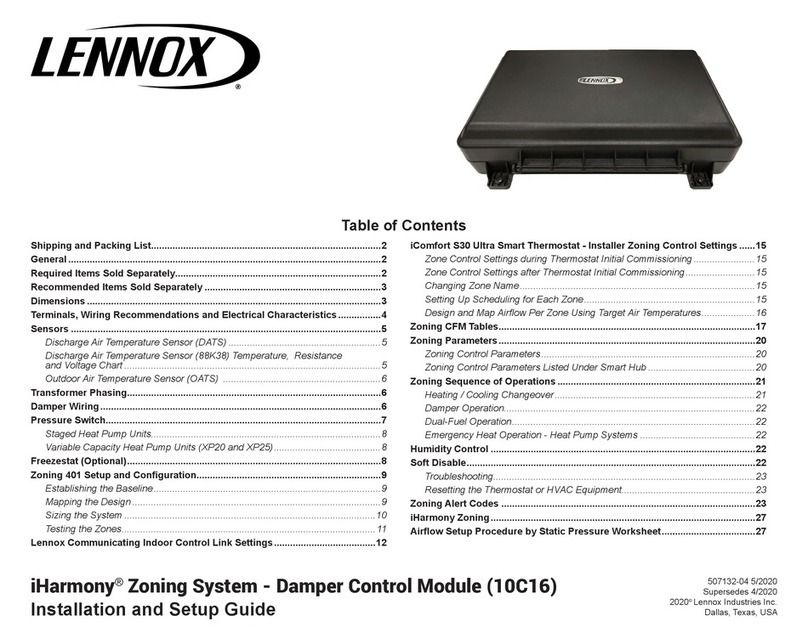
Lennox
Lennox iHarmony 10C16 Installation and setup guide
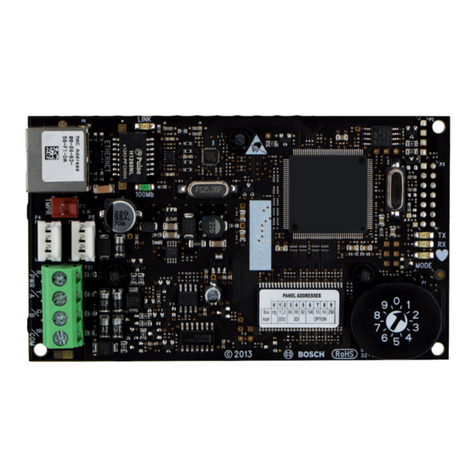
Bosch
Bosch B426 Installation and operation
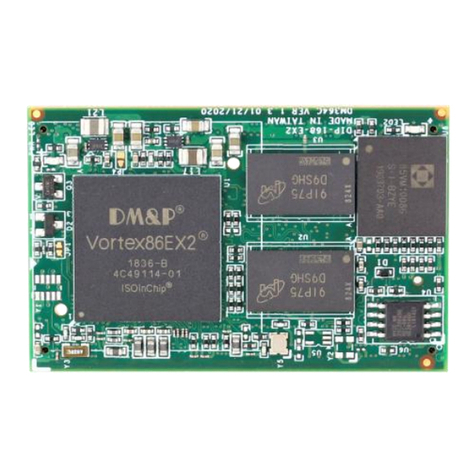
Icop
Icop VEX2-DIP168 user manual
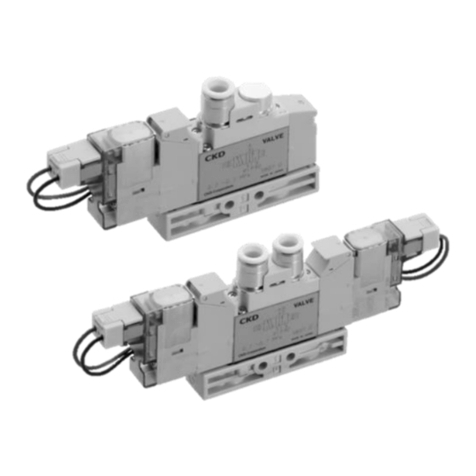
CKD
CKD M3GA/B R Series instruction manual